4 Layer PCB Supplier
South-Electronic
Welcome to a world of unparalleled quality and reliability with South-Electronic. If you’re looking for PCBs that combine exceptional electrical performance with mechanical resilience, you’ve found your ideal partner. Your projects deserve high-quality components that deliver consistency and excellence.
Why Choose South-Electronic?
-
Order Flexibility
Order the exact amount you need, starting from just 1 piece.
Whether you’re prototyping or running full-scale production, our flexible ordering process is designed for you. -
Industry Expertise
You get to experience a team with decades of experience.
Working with a professional and efficient team, our experts are always here to support and improve your project. -
Premium Quality Assurance
Get the highest standard PCBs for you.
Our certifications speak for themselves: UL, CE, IATF16949, ISO13485 and ISO9001. Through strict quality control, we ensure that every PCB meets the highest standards without compromise. -
Quick and Reliable Service
Fast delivery and efficient production mean your project can proceed as planned.
Please trust a service that prioritizes your schedule. With 8 advanced production lines, we provide a one-stop service to meet your various needs. -
Global Coverage, Local Support
Your global business will be supported locally.
South-Electronic is headquartered in China and has a strong export business in Europe and the United States. We provide local customer support in these regions, ensuring smooth communication and fast response times.
Related Project We had Done
Customer Reviews
engineer
thank you, guys, the boards are really good, i am really happy to receive my boards, the components are perfect!
Operation Manager
South-Electronic is my first PCBA supplier in China. The service and quality are excellent, and the after-sales support is also very impressive. Good Job!
Common Questions
Most Popular Questions
South-Electronic has robust manufacturing capabilities, able to handle both small batch prototypes and large-scale production. With 8 production lines, they can efficiently manage orders of varying volumes while maintaining high standards of quality.
South-Electronic performs comprehensive testing, including electrical testing such as continuity and impedance checks, to ensure that all 4 Layer PCBs meet required specifications. Detailed test reports are also provided to verify the product’s quality.
The standard lead time for 4 Layer PCBs varies based on order complexity and volume but typically ranges from 7 to 15 business days. Expedited options are available for urgent projects.
Yes, South-Electronic offers global shipping to ensure timely delivery to customers around the world. Their logistics solutions are designed to provide secure and efficient delivery.
South-Electronic provides strong after-sales support, offering warranties on their products. They adhere to strict quality control measures such as ISO and RoHS certifications, ensuring long-term reliability and customer satisfaction.
Send us a message
The more detailed you fill out, the faster we can move to the next step.
The Complete Guide For 4 Layer PCB
Contents
Chapter 1
What is a 4 Layer PCB?
Overview of a 4 Layer PCB
A 4 Layer PCB is a type of printed circuit board that features four distinct copper layers. It is designed with two inner copper layers that are sandwiched between a top and bottom layer, providing more routing options and enhanced functionality compared to a standard 2 Layer PCB.
Why Choose a 4 Layer PCB?
The additional layers in a 4 Layer PCB allow for:
- Higher Component Density: These boards can support more complex designs with a higher number of components in a compact space, making them ideal for advanced electronics.
- Improved Signal Integrity: By separating signal layers with dedicated power and ground planes, 4 Layer PCBs reduce signal interference and cross-talk, ensuring better performance for high-speed circuits.
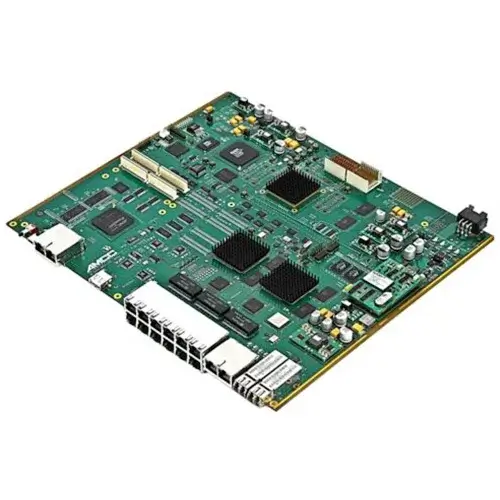
Chapter 2
Structure of a 4 Layer PCB
The structure of a 4 Layer PCB is carefully designed to maximize performance, especially for complex and high-speed circuits. Each layer plays a specific role in managing signals, power, and ground, ensuring reliable operation and minimal interference.
Layer Breakdown
The 4 Layer PCB consists of the following layers:
Top Layer (Signal Layer)
This is the outermost layer where most components are mounted and connected. It is primarily used for signal routing, allowing the transmission of electrical signals between components.Inner Layer 1 (Power Plane)
This inner layer is dedicated to distributing power to various components on the board. By having a separate power plane, the PCB ensures stable voltage levels and reduces noise.Inner Layer 2 (Ground Plane)
The second inner layer acts as a ground plane, providing a return path for electrical currents. It helps in reducing electromagnetic interference (EMI) and enhances signal integrity.Bottom Layer (Signal Layer)
Similar to the top layer, the bottom layer is used for routing additional signals. This layer supports more complex routing and component placement, particularly in high-density designs.
Why This Layer Structure Matters
- Signal Integrity: The separation of power and ground planes between the signal layers minimizes signal interference and reduces cross-talk between circuits. This is essential for high-speed or sensitive applications.
- Improved Performance: The dedicated planes for power and ground help maintain a cleaner electrical environment, leading to more efficient performance, particularly in devices that require fast and accurate signal processing.
- Compact Design: By utilizing both the top and bottom layers for signal routing and reserving the inner layers for power and ground, the design achieves a higher density of components in a compact space without sacrificing performance.
This optimized structure allows 4 Layer PCBs to excel in high-performance applications, providing stable and reliable functionality across various industries.

Chapter 3
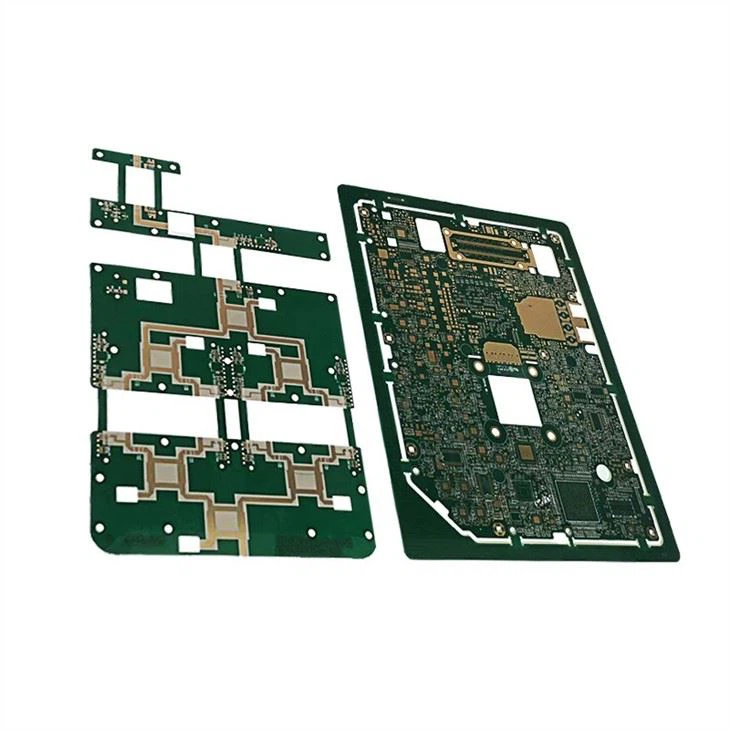
Advantages of 4 Layer PCB
4 Layer PCBs offer several key advantages over traditional 2 Layer PCBs, making them an ideal choice for more complex and high-performance electronic designs.
1. Enhanced Signal Integrity
One of the primary benefits of 4 Layer PCBs is improved signal integrity. The separation of signal layers from the power and ground planes significantly reduces electromagnetic interference (EMI) and cross-talk between signals. This leads to more accurate and stable data transmission, especially in high-speed circuits.
2. Increased Component Density
With the addition of two extra layers, 4 Layer PCBs provide more space for routing and components. This increased layer count allows for more intricate designs, where multiple components need to be interconnected. It is particularly beneficial in modern devices that demand high functionality in a compact form factor.
3. Power and Ground Plane Separation
The dedicated inner layers for power and ground planes improve current flow and power distribution across the board. This separation ensures a clean power supply to the components and reduces noise, making the board more stable and reliable in operation.
4. Compact Design
4 Layer PCBs are ideal for small form factor applications like smartphones, wearables, and IoT devices. Their compact design enables engineers to create high-performance electronics while keeping the overall device size small, which is crucial for portable and space-constrained devices.
These advantages make 4 Layer PCBs a top choice for industries that require high-performance, compact, and reliable electronic solutions.
Chapter 4
Common Applications of 4 Layer PCB
4 Layer PCBs are versatile and widely adopted across various industries due to their compact design, enhanced signal integrity, and ability to support complex electronic systems. Here are some of the key sectors where 4 Layer PCBs are used:
1. Telecommunications
In the telecommunications industry, 4 Layer PCBs are essential due to their ability to handle high-speed signal transmission and maintain signal integrity over long distances. These boards are used in devices such as:
- Networking Equipment: Routers, switches, and servers rely on 4 Layer PCBs to manage large volumes of data and ensure stable network connectivity.
- Wireless Communication Devices: Mobile phones, base stations, and satellite communication systems use 4 Layer PCBs to facilitate efficient signal routing and reduce interference in wireless signals.
The advanced routing and power distribution features of 4 Layer PCBs make them ideal for maintaining the performance and reliability required in communication infrastructure.
2. Medical Equipment
Precision and reliability are paramount in medical devices, and 4 Layer PCBs play a critical role in ensuring that these devices perform safely and accurately. They are used in:
- Diagnostic Equipment: Devices like MRI machines, CT scanners, and blood pressure monitors depend on the high-performance capabilities of 4 Layer PCBs for processing large amounts of data quickly and accurately.
- Wearable Medical Devices: Compact health monitoring systems such as heart rate monitors, glucose meters, and fitness trackers use 4 Layer PCBs to provide high functionality in a small form factor.
The enhanced signal integrity and reliable power distribution of 4 Layer PCBs make them suitable for the demanding environment of medical technology, where accuracy and patient safety are top priorities.
3. Automotive Electronics
Modern vehicles are becoming increasingly reliant on electronic systems, and 4 Layer PCBs are a vital part of this evolution. In automotive electronics, they are used in:
- Engine Control Units (ECUs): 4 Layer PCBs help manage engine functions, fuel injection, and emission controls, ensuring optimal vehicle performance.
- Infotainment Systems: Navigation, audio, and entertainment systems in vehicles are powered by complex PCBs that can support high data transfer rates.
- Advanced Driver Assistance Systems (ADAS): Features such as lane-keeping assist, collision detection, and adaptive cruise control rely on 4 Layer PCBs for processing sensor data in real-time.
The compact design and ability to handle high processing loads make 4 Layer PCBs an essential component in automotive electronics, contributing to both safety and user experience.
4. Consumer Electronics
Consumer electronics demand small, efficient, and powerful PCBs to support the growing complexity of devices. 4 Layer PCBs are widely used in:
- Smartphones and Tablets: These devices require high-density circuit boards to pack powerful processors, memory, and other components into small enclosures.
- Laptops and Wearables: 4 Layer PCBs provide the performance needed for compact designs in laptops, smartwatches, and fitness trackers.
- Home Automation Devices: Smart home products, such as security cameras, smart lighting, and thermostats, utilize 4 Layer PCBs for reliable and compact control systems.
The high component density and signal reliability of 4 Layer PCBs allow consumer electronics to be powerful yet compact, meeting the demands of modern users for faster, smarter, and more connected devices.
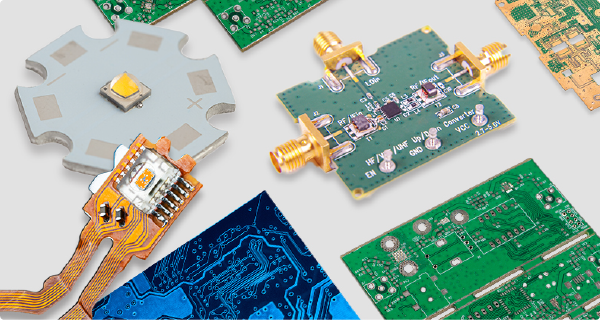
Chapter 5

Materials Used in 4 Layer PCBs
The performance and durability of a 4 Layer PCB are largely determined by the materials used in its construction. These materials are selected to ensure optimal signal transmission, mechanical strength, and thermal stability. Below are the key materials used in a 4 Layer PCB:
1. FR-4 (Base Material)
FR-4 is the most commonly used base material in PCB fabrication. It is a type of glass-reinforced epoxy laminate, providing a solid foundation for the PCB’s structure. Some of the key properties of FR-4 include:
- High Mechanical Strength: FR-4 is known for its excellent durability, ensuring that the PCB can withstand physical stress, vibrations, and harsh environmental conditions.
- Electrical Insulation: This material provides good insulation between conductive layers, reducing the risk of short circuits or signal interference.
- Flame Retardancy: The “FR” in FR-4 stands for Flame Retardant, indicating that it meets certain safety standards for fire resistance, which is especially important in applications where the board may be exposed to heat.
- Thermal Stability: FR-4 exhibits good thermal resistance, ensuring the board performs reliably in environments with varying temperatures.
2. Copper Foil (Conductive Layers)
Copper foil is applied to all conductive layers of the 4 Layer PCB. Copper is used due to its excellent electrical conductivity, which is crucial for maintaining signal integrity and efficient power distribution. The copper foil is typically available in different thicknesses, depending on the application’s current-carrying needs. Some common properties include:
- High Conductivity: Copper allows for minimal resistance in electrical pathways, enabling fast and efficient signal transmission.
- Customizable Thickness: Copper thickness can be adjusted based on the requirements of the PCB. Standard copper thicknesses are 1 oz (35 micrometers), but for boards carrying more current, thicker copper may be used.
- Corrosion Resistance: Copper layers are often treated with protective coatings (like HASL or ENIG finishes) to prevent oxidation and ensure long-term reliability.
- Heat Dissipation: Copper’s excellent thermal conductivity helps dissipate heat generated by high-current components, maintaining board performance.
3. Prepreg (Pre-impregnated Material)
Prepreg is a resin-coated fiberglass sheet that is used between the copper layers to bond them together during the lamination process. Prepreg acts as both a bonding agent and an insulating material. Some critical attributes of prepreg include:
- Bonding Strength: When heated and pressed during lamination, the resin in the prepreg melts and hardens, forming a strong adhesive bond between the copper layers.
- Electrical Insulation: Prepreg provides insulation between the conductive copper layers, ensuring that signals do not interfere with each other.
- Thermal Properties: It is designed to withstand the heat generated during operation, preventing delamination or other structural failures.
- Controlled Thickness: The thickness of prepreg can be precisely controlled, allowing manufacturers to achieve the required distance between layers for optimal performance.
4. Core Material
The core of a 4 Layer PCB is a rigid, FR-4 laminate material that acts as the central foundation of the board. This core is similar to the FR-4 used in the outer layers, but it is pre-laminated with copper on both sides. The core serves the following purposes:
- Mechanical Support: It provides a solid base for the inner copper layers, maintaining the overall rigidity of the PCB.
- Layer Separation: The core separates the inner layers, ensuring proper spacing and alignment during the manufacturing process.
- Electrical Performance: Just like the outer FR-4, the core contributes to the board’s thermal and electrical insulation properties.
5. Additional Materials (Optional)
In some cases, additional materials are used depending on the specific requirements of the application:
- Rogers Material: For high-frequency applications like RF and microwave circuits, Rogers materials are sometimes used instead of FR-4. These materials offer better dielectric performance and are ideal for high-speed signal processing.
- Solder Mask: A solder mask is applied to the outermost layers to protect the copper traces from oxidation and prevent accidental soldering during assembly. It also improves the board’s aesthetics by giving it a uniform green, blue, or red appearance.
- Surface Finishes: Finishes like HASL (Hot Air Solder Leveling), ENIG (Electroless Nickel Immersion Gold), or OSP (Organic Solderability Preservative) are applied to the exposed copper pads to enhance solderability and protect against corrosion.
Chapter 6
Design Process for 4 Layer PCB
The design of a 4 Layer PCB requires careful planning and attention to detail to ensure optimal performance. The process is structured, yet flexible enough to meet the specific needs of different applications, from high-speed communications to compact consumer electronics. Below is a detailed look at the key steps involved in designing a 4 Layer PCB:
1. Schematic Creation
The first step in the design process is creating a schematic, which serves as the blueprint for the PCB’s layout. This involves mapping out all the electrical connections between components, including resistors, capacitors, integrated circuits (ICs), and connectors. A well-designed schematic ensures that all parts are properly connected and that the design will function as intended once manufactured.
- Key Considerations:
- Ensure that the schematic accurately reflects the circuit’s functionality.
- Carefully choose component values and placement to optimize space and performance.
2. Layer Stack-up Configuration
Once the schematic is complete, the next step is determining the layer stack-up configuration. In a 4 Layer PCB, this involves defining the purpose of each layer:
Top and Bottom Layers: These are primarily used for signal routing. Components are placed on the top layer, while the bottom layer is often used for additional routing.
Inner Layer 1: Typically dedicated to the power plane, this layer distributes voltage to various components while minimizing noise.
Inner Layer 2: Reserved as the ground plane, this layer helps with reducing electromagnetic interference (EMI) and provides a return path for signals.
Why Stack-up Matters: A well-optimized stack-up improves signal integrity, enhances power distribution, and minimizes interference between layers.
3. Routing Signals on Top and Bottom Layers
The signal routing phase involves connecting the components placed on the top layer to ensure proper communication between them. Routing is done on both the top and bottom layers, ensuring that traces do not overlap or interfere with one another.
- Best Practices:
- Keep critical signal paths as short as possible to reduce latency.
- Use vias (vertical connections between layers) strategically to maintain signal integrity across the layers.
- Prioritize important signals (such as high-speed data lines) and ensure they are routed on the top layer for better control.
4. Power and Ground Planes on Inner Layers
In a 4 Layer PCB, the inner layers are dedicated to power and ground planes. These planes provide stable power distribution and serve as a return path for signals, which is essential for reducing noise and ensuring reliable operation.
- Power Plane: This layer distributes power from the input source to all components, minimizing voltage drops and ensuring a steady supply.
- Ground Plane: The ground plane acts as a reference point for signals and provides a path for returning currents. Its presence helps in reducing signal interference and noise, leading to improved overall circuit performance.
5. Using Design Software
Modern PCB design software plays a vital role in creating accurate and efficient designs. Popular tools like Altium Designer, Eagle, or KiCAD allow engineers to design, simulate, and optimize PCBs before they are manufactured.
- Benefits of Software:
- Real-time error checking ensures that design flaws, such as signal overlap or incorrect component placement, are identified early.
- Design simulations help test the board’s performance under different conditions, saving time and resources during the manufacturing stage.
The structured approach to designing 4 Layer PCBs ensures that the final product meets high-performance standards while maintaining reliability. For companies like South-Electronic, which focus on high-quality manufacturing and customization, adhering to this detailed process ensures that each PCB is optimized for its specific use, whether in telecommunications, automotive systems, or compact electronics. With a robust design process and the right software tools, you can ensure that your 4 Layer PCB projects are a success.
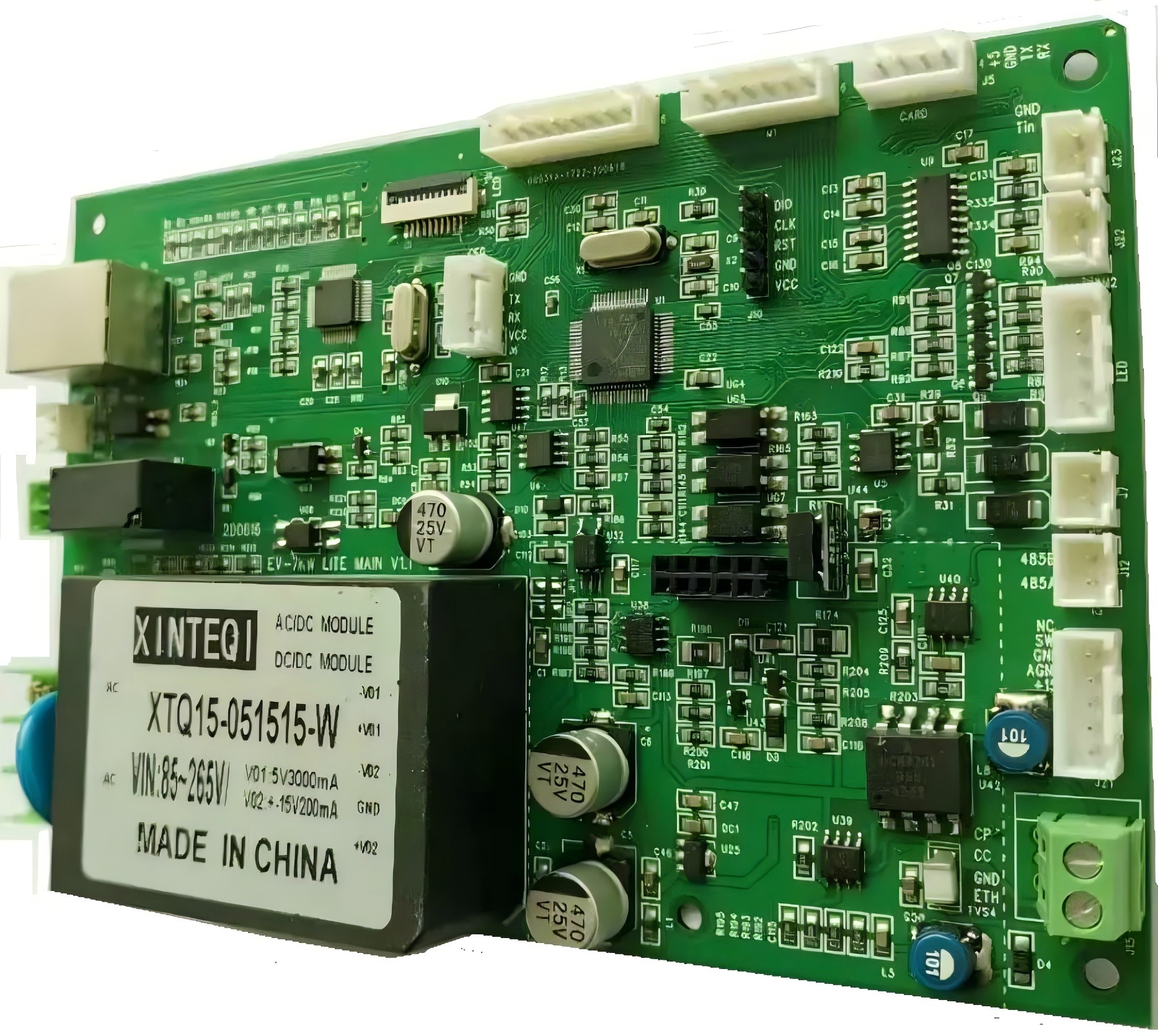
Chapter 7
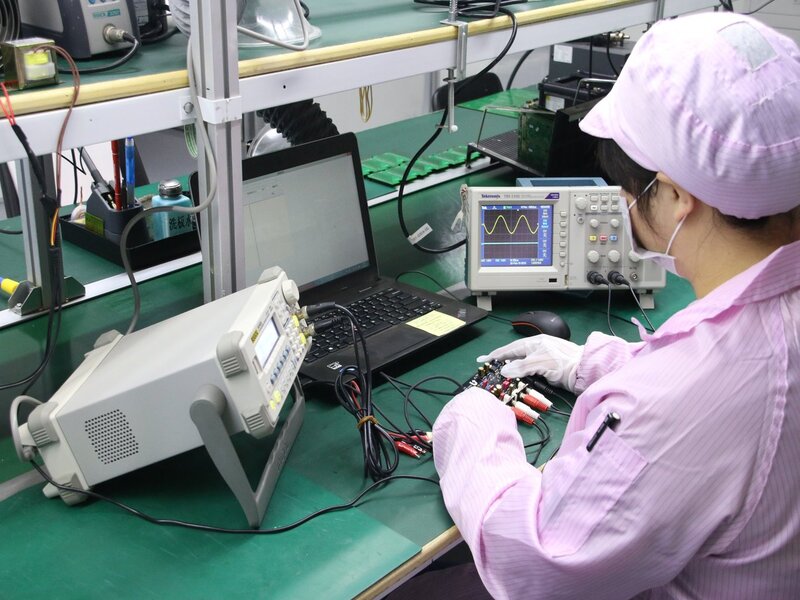
Manufacturing Process of 4 Layer PCB
The manufacturing of a 4 Layer PCB is a precise and multi-step process that requires advanced equipment and techniques to ensure the integrity of the board. Each step is crucial in creating a reliable and high-performance PCB that can meet the demands of modern electronics. Below is a detailed breakdown of the key stages involved in the manufacturing process of a 4 Layer PCB:
1. Lamination
Lamination is the process where the prepreg (pre-impregnated fiberglass) and core materials are pressed together under heat and pressure to form the multilayer structure of the PCB. In a 4 Layer PCB, this involves bonding the four copper layers (two inner and two outer) with insulating layers between them.
- Process Details:
- The copper layers and insulating layers (prepreg) are stacked together in a specific order. The two inner copper layers are sandwiched between layers of prepreg, and the core provides structural support.
- The stack-up is placed in a lamination press, where heat (around 180-200°C) and high pressure are applied. The heat causes the resin in the prepreg to melt and bond the layers together, while the pressure ensures a strong bond without air bubbles or defects.
- Why It’s Important: Lamination forms the essential multilayer structure of the PCB. It ensures the layers are properly aligned and firmly bonded, which is crucial for both electrical performance and the board’s mechanical strength.
2. Drilling
Once the PCB is laminated, the next step is drilling. Drilling creates vias—small holes that allow electrical connections between different layers of the PCB. This step is highly precise, as any misalignment or errors can render the PCB unusable.
Types of Vias:
- Through-hole Vias: These go all the way through the board, connecting all layers.
- Blind Vias: These connect an outer layer to one or more inner layers but do not pass through the entire board.
- Buried Vias: These connect two or more inner layers without reaching the outer layers.
Process Details:
- High-precision CNC machines or laser drills are used to create the vias. The machine reads the drill file generated during the design process, ensuring that each hole is drilled to the correct size and location.
- Drill bits with diameters ranging from 0.1mm to 0.6mm are used, depending on the design requirements.
- After drilling, the holes are inspected for accuracy and any debris or leftover material is removed.
Why It’s Important: Drilling ensures that electrical connections can be made between the PCB layers. Precise drilling is essential to maintain the integrity of these connections and to prevent signal degradation or short circuits.
3. Plating
After drilling, the plating process begins. Plating involves depositing a thin layer of copper on the walls of the drilled holes (vias) and on the surface of the PCB. This step is crucial for creating the conductive pathways that connect the different layers of the PCB.
Process Details:
- The PCB is submerged in a copper plating bath, where a chemical process called electroless copper deposition coats the inner walls of the vias with copper. This allows electrical signals to pass between the layers through the vias.
- The entire surface of the board is also plated with a thin layer of copper to prepare it for the next stage (etching).
- After plating, the copper layer is typically around 1 micron thick, providing a reliable conductive pathway without adding significant thickness to the board.
Why It’s Important: Plating creates the essential conductive connections between the layers of the PCB. The copper in the vias ensures that signals can travel from one layer to another, while the surface plating prepares the board for the creation of copper traces.
4. Etching
Etching is the process of removing excess copper from the surface of the PCB, leaving behind the desired copper traces that will carry electrical signals between components. This is a critical step in defining the PCB’s circuit layout.
- Process Details:
- First, a photoresist layer is applied to the surface of the PCB. The photoresist is a light-sensitive material that covers the areas of copper that should remain intact.
- The PCB is then exposed to UV light through a mask that defines the desired copper pattern. The UV light hardens the photoresist in areas where the copper traces are supposed to stay.
- The PCB is placed in a chemical bath, which dissolves the exposed (unhardened) photoresist and removes the unwanted copper, leaving only the copper traces as defined by the UV mask.
- Why It’s Important: Etching defines the electrical pathways on the PCB. It ensures that only the necessary copper remains on the board, forming the traces that connect components. Accurate etching is vital for maintaining signal integrity and preventing short circuits.
5. Additional Steps (Optional)
After the primary manufacturing steps, additional processes may be performed to enhance the PCB’s durability, appearance, and functionality:
- Solder Mask Application: A protective solder mask is applied to the PCB’s surface to prevent oxidation and accidental short circuits during soldering. The solder mask also gives the board its characteristic green (or other colored) finish.
- Silkscreen Printing: Silkscreening is used to print labels, logos, and reference designators on the PCB, making it easier to identify components during assembly.
- Surface Finishing: Different surface finishes like HASL (Hot Air Solder Leveling), ENIG (Electroless Nickel Immersion Gold), or OSP (Organic Solderability Preservative) are applied to protect exposed copper and ensure good solderability during assembly.
Cahpter 8
Testing and Quality Assurance
Ensuring the reliability and performance of 4 Layer PCBs is critical, especially for applications in industries such as telecommunications, automotive, and medical devices. To guarantee that every board meets the required specifications, several rigorous testing and quality assurance processes are carried out during and after manufacturing. Here’s a breakdown of the key testing methods used for 4 Layer PCBs:
1. Electrical Testing
Electrical testing is one of the most important quality assurance steps for any PCB, including 4 Layer boards. This test ensures that all the electrical connections between the layers are intact and that there are no short circuits or open circuits.
- Continuity Testing: This checks that every trace and via on the PCB is correctly connected and allows the flow of electrical current as intended. If any connection is broken (open circuit), the test will flag the issue for correction.
- Insulation Resistance Testing: This verifies that there is sufficient insulation between different conductive paths on the board. It helps ensure that there is no unintended electrical connection (short circuit) between traces or layers, which could lead to malfunction or damage in the final product.
2. Automated Optical Inspection (AOI)
AOI is a non-contact inspection method that uses high-resolution cameras and advanced algorithms to scan the surface of the PCB for defects. It is an essential step in ensuring the visual and structural integrity of the board.
- Trace and Pad Inspection: AOI detects defects such as broken or incomplete traces, shorts, or misaligned pads, which could compromise the PCB’s performance.
- Via Inspection: The system checks the alignment and quality of the vias to ensure that they are properly formed and free of defects. Since vias play a critical role in connecting the layers of a 4 Layer PCB, even a small defect can cause electrical failures.
- Component Placement Inspection: In PCBs with components already mounted (e.g., during prototyping), AOI can verify that components are placed in the correct position and orientation.
3. Functional Testing
Functional testing simulates real-world operational conditions to ensure that the PCB will perform as expected once assembled into the final product. This test is especially important for PCBs used in critical applications, where failure is not an option.
- Signal Integrity Testing: In high-speed circuits, functional testing checks for signal integrity issues such as noise, jitter, or signal degradation. This is crucial for 4 Layer PCBs that are often used in high-performance devices where signal quality is essential.
- Load Testing: The board is tested under various electrical loads to ensure that it can handle the expected current and voltage levels without failing or overheating.
- Environmental Testing: Some PCBs undergo environmental tests (like temperature cycling or humidity exposure) to ensure they can operate reliably in harsh conditions.
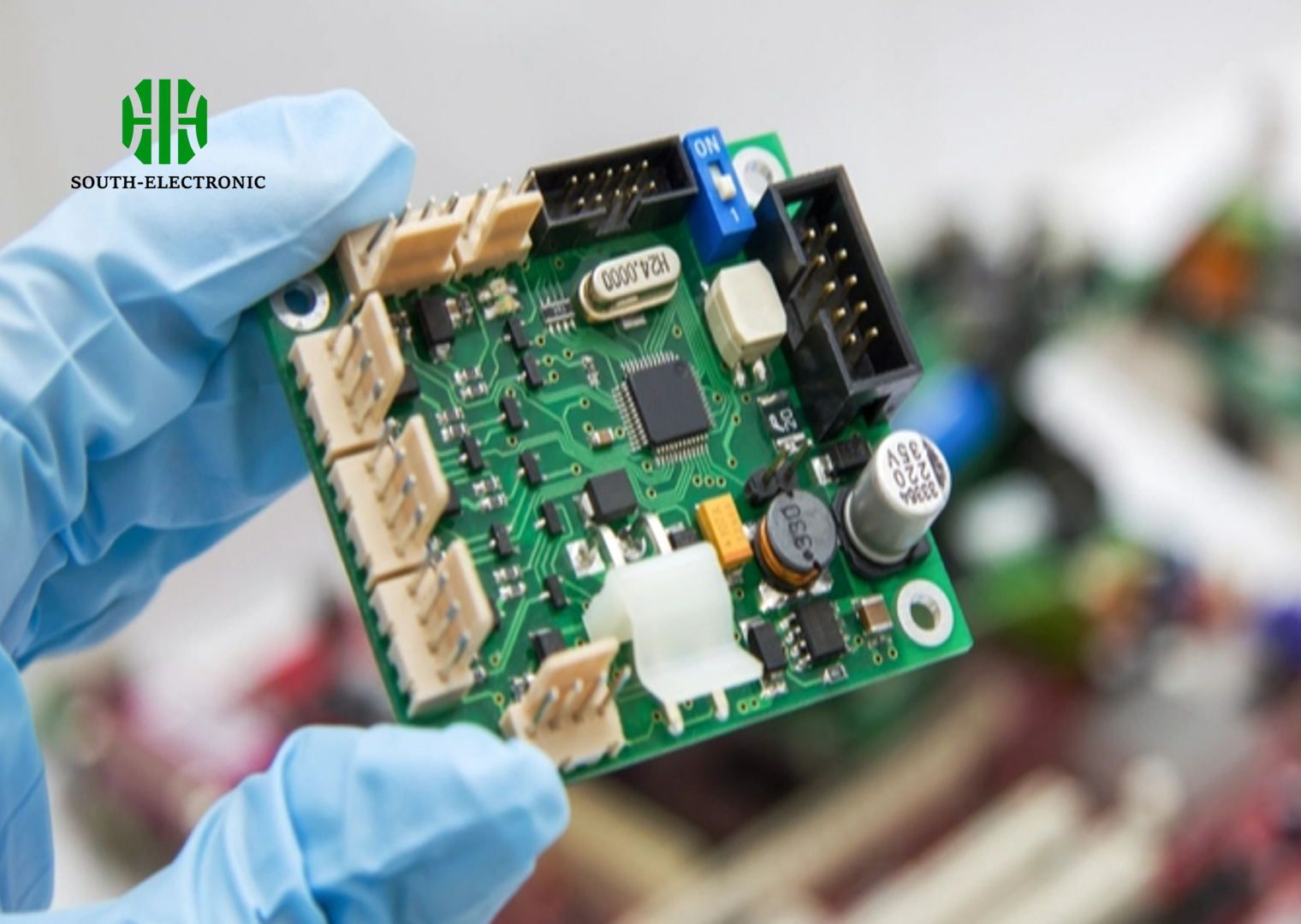
Chapter 9

Cost Factors of 4 Layer PCB
The cost of manufacturing a 4 Layer PCB can vary significantly depending on several key factors. Understanding these cost drivers can help you make informed decisions about your design and production needs. Here are the main elements that influence the cost of 4 Layer PCBs:
1. Material Selection
The choice of materials is one of the most critical factors in determining the cost of a 4 Layer PCB. Different materials offer varying levels of performance, thermal stability, and durability, which can directly impact pricing.
Standard Materials (FR-4): FR-4 is the most commonly used material for 4 Layer PCBs. It offers a balance between cost, performance, and durability, making it suitable for most general applications. FR-4 is relatively affordable, which keeps overall costs lower.
High-End Materials (Rogers, Polyimide): If your design requires superior signal integrity, especially in high-frequency or high-temperature applications, you might need specialized materials such as Rogers or Polyimide. These materials provide better electrical properties, but they come at a higher cost. For example, Rogers is often used in RF and microwave applications but can significantly increase the total production cost due to its advanced properties.
Copper Thickness: The amount of copper used in each layer also affects cost. Thicker copper layers are necessary for boards that will handle higher currents, but they increase both material costs and manufacturing complexity.
2. Layer Stack-up Complexity
The complexity of the layer stack-up is another significant cost driver. In a 4 Layer PCB, the design of the layers, including how signals, power, and ground planes are distributed, can affect manufacturing costs.
Basic 4 Layer Stack-up: A standard stack-up with two signal layers and two power/ground layers is relatively straightforward to manufacture, and costs are kept lower with this simpler configuration.
Complex Stack-ups: If your design requires more intricate routing or specific impedance control, the stack-up may need to be customized. Complex designs often involve additional processing steps, tighter tolerances, and specialized materials, all of which can increase production costs. For example, boards with high-density interconnects (HDI) or fine-pitch components will require more detailed planning and execution, raising costs.
Via Types (Through-hole, Blind, Buried): The use of advanced via technologies, such as blind or buried vias, adds complexity to the manufacturing process and thus increases costs. These vias improve design flexibility but require additional drilling and plating steps.
3. Production Volume
The number of units ordered also plays a significant role in determining the per-unit cost of a 4 Layer PCB. Manufacturers generally offer lower costs per unit for larger production runs due to economies of scale.
Small Batch Orders: For smaller orders, such as prototype or low-volume production, costs per unit are typically higher. This is because setup costs, such as machine calibration and tooling, are spread over fewer boards. Small batch production is ideal for prototyping but can be expensive if used for large-scale deployment.
Large Batch Orders: High-volume production orders tend to have a lower per-unit cost because the setup and material costs are distributed across a larger number of boards. Manufacturers can also optimize production processes when handling larger volumes, further reducing costs. For example, ordering thousands of units in a single run will significantly lower the overall cost compared to ordering just a few dozen units.
4. Additional Factors
There are also other factors that can influence the overall cost of 4 Layer PCBs, including:
- Lead Time: If you need a quick turnaround for your boards, expedited production and shipping will add to the overall cost.
- Testing and Quality Control: Comprehensive testing, such as functional testing, Automated Optical Inspection (AOI), and electrical testing, ensures reliability but adds to the cost, especially for large batches.
- Surface Finishes: The type of surface finish you choose, such as HASL (Hot Air Solder Leveling), ENIG (Electroless Nickel Immersion Gold), or OSP (Organic Solderability Preservative), can also impact the price. Higher-end finishes like ENIG provide better solderability and corrosion resistance but come at a premium.
Chapter 10
How to Choose a 4 Layer PCB Manufacturer?
Choosing the right manufacturer for your 4 Layer PCB is critical to ensure product quality, reliability, and on-time delivery. Given the complexity and precision required in manufacturing multilayer PCBs, there are several key factors to consider when evaluating potential manufacturers. Here’s a guide to help you make the best choice:
1. Experience with Multilayer PCBs
The manufacturer’s experience with multilayer PCBs is a top priority. Not all PCB manufacturers specialize in multilayer designs, so it’s important to select a company with proven expertise in 4 Layer and other complex PCBs.
- Proven Track Record: Look for manufacturers that have a history of successfully producing 4 Layer PCBs for various industries. Ask for case studies or references to verify their experience.
- Technical Know-how: Manufacturers with strong technical knowledge can handle the challenges of multilayer PCB design, such as ensuring signal integrity, impedance control, and heat management.
Why It’s Important: Experienced manufacturers are better equipped to handle the intricate design requirements and potential issues that arise with multilayer PCBs, leading to fewer production errors and better end products.
2. Certifications and Quality Standards
When selecting a 4 Layer PCB manufacturer, it is essential to ensure that they meet established certifications and follow recognized quality standards.
- ISO Certifications: ISO 9001 certification indicates that the manufacturer follows strict quality management systems and procedures. This ensures consistency in manufacturing and product quality.
- UL Certification: UL (Underwriters Laboratories) certification is crucial if your PCBs will be used in products that need to meet specific safety standards, especially for consumer or industrial electronics.
- RoHS Compliance: Make sure the manufacturer complies with RoHS (Restriction of Hazardous Substances) directives, which ensure that the PCBs are free of hazardous materials like lead and mercury.
Why It’s Important: Certifications guarantee that the manufacturer adheres to strict industry standards, ensuring product safety, reliability, and regulatory compliance in different markets.
3. Manufacturing Capabilities
Assess the manufacturer’s production capabilities to ensure they can meet your specific requirements, whether you need large volumes, prototypes, or custom designs.
- Production Volume: Does the manufacturer have the capacity to handle your order size? Whether you need a small batch for prototyping or a large volume for mass production, ensure the manufacturer has the appropriate resources to scale production efficiently.
- Customization Options: Check if the manufacturer can accommodate custom designs, including specialized materials (like Rogers or Polyimide), complex layer stack-ups, or advanced via technologies (e.g., blind or buried vias).
- Technology and Equipment: Advanced equipment such as automated optical inspection (AOI) systems, CNC drilling, and laser cutting machines ensures high precision and reduces errors, especially for complex 4 Layer designs.
Why It’s Important: A manufacturer with robust capabilities can provide flexibility in production, handle complex designs, and ensure that your PCBs meet technical specifications and quality standards.
4. Global Shipping and After-sales Support
Global shipping and strong after-sales support are critical, especially if your business relies on international operations or frequent reorders.
- Global Shipping: Ensure that the manufacturer has a global logistics network and can ship to your location efficiently. They should offer reliable shipping solutions that ensure your PCBs are delivered safely and on time, regardless of your geographic location.
- After-sales Support: Post-delivery support is equally important. Look for manufacturers that offer warranties on their products and provide technical support in case issues arise. A good manufacturer should have a dedicated customer service team that responds promptly to inquiries and helps resolve any concerns with product quality or performance.
Why It’s Important: A manufacturer with dependable shipping services ensures that your products arrive on time, preventing delays in production. Strong after-sales support gives you peace of mind, knowing that any issues will be addressed promptly.
Choosing the right 4 Layer PCB manufacturer involves evaluating their experience, certifications, manufacturing capabilities, shipping options, and commitment to quality assurance. By considering these factors, you can partner with a manufacturer that will provide high-quality, reliable PCBs, tailored to your specific needs.
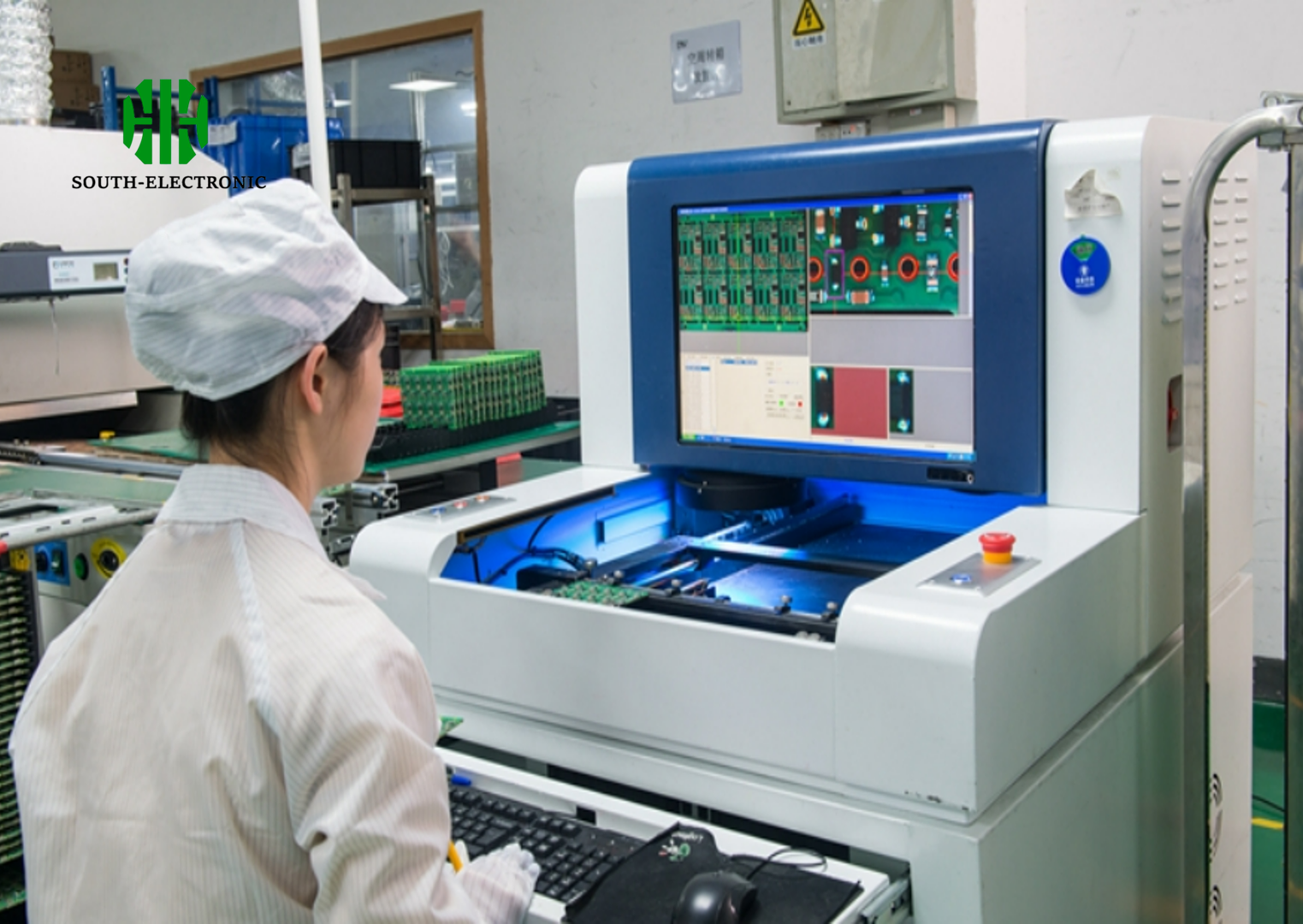
Get in touch
Where Are We?
Industrial Park, No. 438 Donghuan Road, No. 438, Shajing Donghuan Road, Bao'an District, Shenzhen, Guangdong, China
Floor 4, Zhihui Creative Building, No.2005 Xihuan Road, Shajing, Baoan District, Shenzhen, China
ROOM A1-13,FLOOR 3,YEE LIM INDUSTRIAL CENTRE 2-28 KWAI LOK STREET, KWAI CHUNG HK
service@southelectronicpcb.com
Phone : +86 400 878 3488
Send us a message
The more detailed you fill out, the faster we can move to the next step.
