Automotive PCB Supplier
South-Electronic
At South-Electronic, we specialize in providing high-quality automotive PCBs that deliver reliability, durability, and superior performance.
Discover Unmatched Quality with Our Automotive PCB
Welcome to South-Electronic, your one-stop solution for automotive PCB built to automotive environments. Our PCB is designed to maximize your applications, from safety systems to in-car entertainment.
Rely on South-Electronic for unmatched quality and dependability in your automotive applications. Our automotive PCB boost your projects with consistent, durable performance. Partner with us to drive success in your industry.

Engine Control Units (ECUs)
These circuit boards are central to managing the engine's operations such as fuel injection, ignition timing, and emissions control. They must be highly reliable and able to withstand harsh environmental conditions.
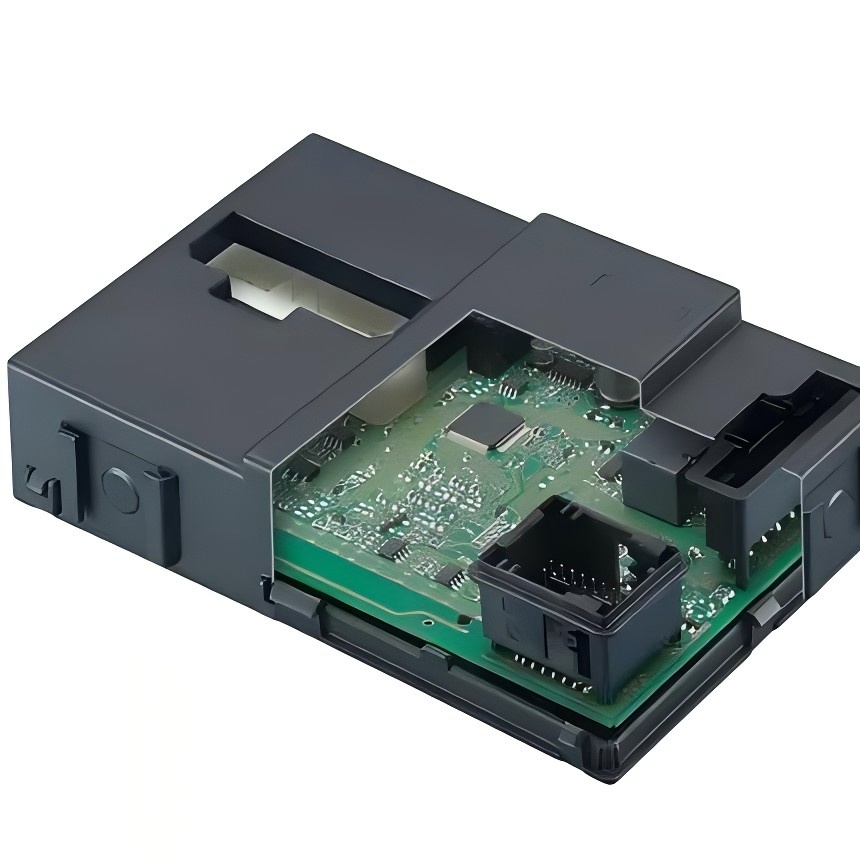
Body Control Modules (BCMs):
Responsible for various body-related functions such as lighting, power windows, central locking, and other convenience features. BCMs often require multiple interfaces for sensors and actuators throughout the vehicle.
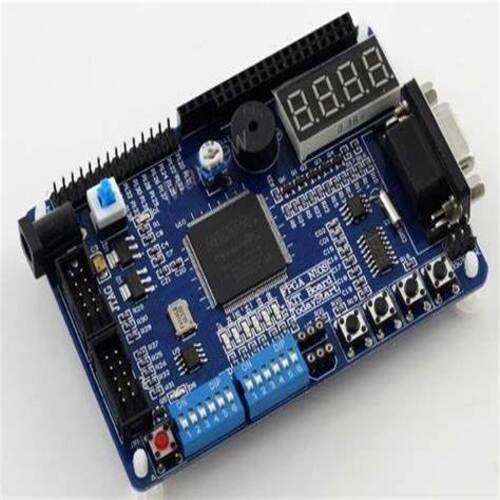
Infotainment System Boards
These handle audio and video entertainment, navigation, and connectivity functions like Bluetooth and Wi-Fi. They often support sophisticated user interfaces and high-speed data processing
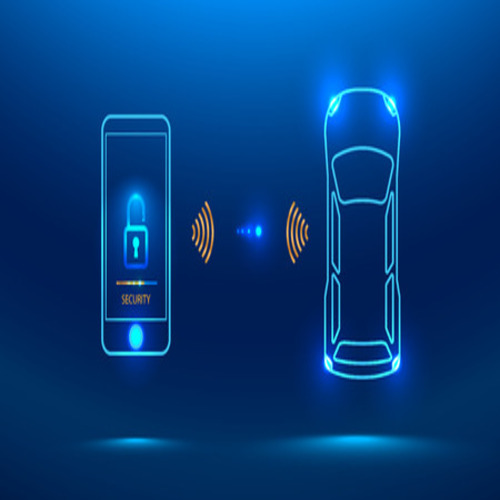
Safety and Security Systems
This category includes circuit boards for airbag systems, antitheft systems, and other safety-related features that require quick response times and fail-safe operation.
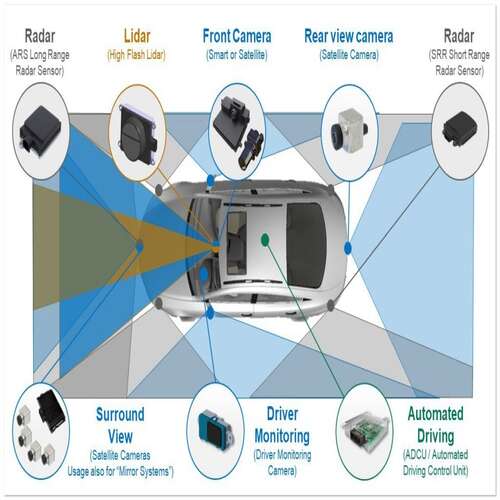
Advanced Driver-Assistance Systems (ADAS)
Involved in controlling the vehicle’s drivetrain components, including transmissions and electric motor controllers, especially in hybrid and electric vehicles.

Power Management Systems
These boards are designed for managing the distribution and quality of power within the vehicle’s electrical system, including battery management systems in electric vehicles.
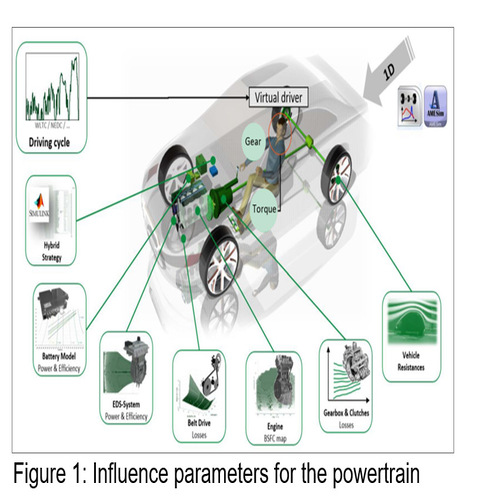
Powertrain and Drivetrain Control
Involved in controlling the vehicle’s drivetrain components, including transmissions and electric motor controllers, especially in hybrid and electric vehicles.
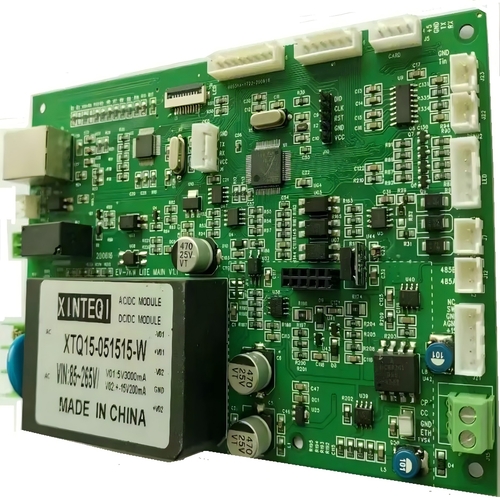
Electric Vehicles and Charging Systems
With the rapid expansion of the electric vehicle market, systems unique to electric vehicles, such as Battery Management Systems (BMS) and charging station communication interfaces, are likely to attract significant search interest.
Why Choose South-Electronic?
At South-Electronic, we understand the critical importance of precise solutions for your automotive projects. We lead in PCB innovation, offering unmatched customization and accuracy to fulfill your specific needs. Our focus is on delivering technical superiority and solutions that ensure project success.
-
Quality Assurance with Extended Warranty
Your automotive projects deserve uncompromising quality, and we deliver.
Every automotive PCB you receive from us is backed by our five-year warranty, ensuring you’re covered with free repairs for any issues that arise during this period. -
Lifetime After-Sales Support
Your peace of mind continues after the sale is complete.
With our lifetime after-sales service, you can count on ongoing support and assistance throughout the lifespan of your products, -
Flexible Ordering without MOQ
Your needs drive our flexibility.
We offer a minimum order quantity of just one piece with no upper limit, providing flexible solutions tailored to your specific demands. -
Rapid Response and Delivery
Your deadlines are important, and we meet them.
With our efficient production processes and optimized logistics, we ensure timely delivery of your orders. -
Transparent and Communicative Client Relations
Your trust in us is reinforced by transparency.
Our end-to-end supply chain visibility allows you to track your orders in real time, ensuring smoother transactions and better communication,
Related Project We had Done
Customer Reviews
engineer
thank you, guys, the boards are really good, i am really happy to receive my boards, the components are perfect!
Operation Manager
South-Electronic is my first PCBA supplier in China. The service and quality are excellent, and the after-sales support is also very impressive. Good Job!
Common Questions
Most Popular Questions
Automotive PCB is used in various applications within vehicles, including engine controls, infotainment systems, navigation systems, and safety features such as airbag deployments and anti-lock braking systems.
Automotive PCB is designed to withstand harsh environments, including high temperatures, vibrations, and moisture. They often require higher standards of durability and reliability due to the critical nature of their applications.
We use a variety of materials, including FR-4, polyimide, and aluminum, to ensure durability and high performance under the extreme conditions typical of automotive environments.
Our automotive PCB passed rigorous testing, including thermal cycling, vibration tests, and moisture resistance checks to ensure they meet the highest standards of quality and reliability.
Absolutely, South-Electronic supports prototyping needs by offering flexible order quantities, allowing you to order as few as one unit to test and validate your designs.
Lead times can vary depending on the complexity and quantity of the order but typically range from 2 to 4 weeks. We strive to meet your schedule requirements while maintaining our quality standards.
Our PCB meet IATF:16949 standards, ensuring a consistent level of quality.
We offer expedited services for urgent orders. Please contact our sales team to discuss your specific requirements and timelines.
South-Electronic provides comprehensive support during the design and manufacturing process, including consultation on design optimization, material selection, and prototype testing to ensure your product meets all expectations and industry standards.
Send us a message
The more detailed you fill out, the faster we can move to the next step.
The Complete Guide For Automotive PCB
Contents
Chapter 1
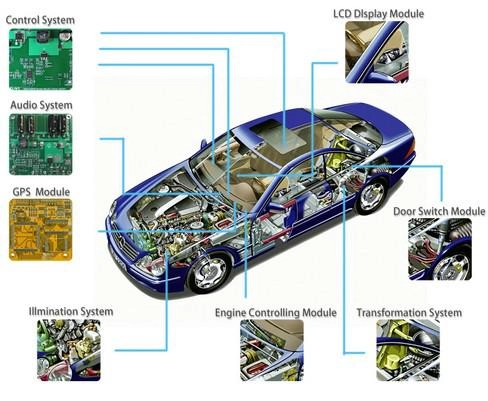
Introduction to Automotive PCB
The Key Role of PCB in Automotive Electronics
When you start your car, what ensures everything from the dashboard to the engine runs smoothly? The answer lies beneath the surface in a compact and powerful printed circuit board (PCB). In the world of automotive electronics, PCB is forming the backbone of nearly every electronic component in a car. From basic functions such as lighting and audio systems to advanced driver assistance systems (ADAS) and electric vehicle management, PCB ensure reliability and efficiency.
As someone deeply involved in the procurement or management of electronic components, you know that the performance of your automotive products depends significantly on the quality and reliability of PCB. They not only provide the electrical connections between components but also must withstand the extreme conditions typical in automotive environments—such as vibrations, high temperatures, and exposure to moisture and chemicals.
The Evolution of Automotive PCB Technology and Its Impact on the Industry
The journey of automotive PCB technology has been marked by significant advancements that have mirrored, and often driven, innovations in the automotive industry itself. From the early days of simple single-layer boards, the evolution towards complex, multi-layered PCBs has been essential to accommodate the increasing demand for functionality and compactness in automotive design.
This evolution has brought forth high-density interconnect (HDI) PCB, flexible PCBs, and rigid-flex PCB, which are crucial for modern vehicles that require highly reliable electronics for safety-critical functions. The shift towards electric vehicles (EVs) and autonomous driving technology has only intensified the demand for more sophisticated, durable, and efficient PCB. As a professional in this industry, you understand that staying ahead means keeping pace with these technological advancements.
As the automotive industry continues to evolve towards smarter, more connected vehicles, the role of PCB is becoming even more critical. Understanding this technology’s past and present will help you navigate its future, ensuring that your business remains at the forefront of the automotive electronics scene. By focusing on quality and innovation in your PCB solutions, you not only meet the industry’s needs but also exceed them, solidifying your reputation as a trusted leader in the automotive PCB market.
Chapter 2
PCB Basics: The Backbone of Automotive Electronics
Definition and Components of PCBs for Automotive Applications
PCB is more than just pieces of fiberglass used to hold electronic components together; they are the vital foundation upon which the functionality and reliability of every automotive electronic system are built. As someone in charge of ensuring the top performance of automotive electronics, you need to understand that a PCB in the automotive industry is engineered to support complex, high-density assemblies that control everything from simple indicators to critical vehicle safety systems.
A typical automotive PCB contains multiple layers of copper sheets laminated together with heat-resistant material, ensuring durability under high thermal and physical stress. These boards are populated with a variety of electronic components including resistors, capacitors, and integrated circuits, all connected through a network of precisely engineered conductive paths, pads, and vias. The choice of components and their layout is meticulously planned to optimize space and maximize functionality, reflecting the high demands of automotive applications.
Differences in Design and Functionality between Automotive PCB and Standard PCB
Understanding the key differences between automotive PCB and standard PCB is crucial for your role, as these distinctions directly impact the performance and reliability of the electronic products you manage or procure. The primary difference lies in the design robustness and functional requirements driven by the unique challenges faced in automotive environments.
Thermal Management: Automotive PCB is
designed to handle extreme temperature swings. Unlike regular PCB, they use materials with higher thermal conductivity and are often designed with thicker copper layers to dissipate heat better, ensuring that they perform consistently under the hood of a car where temperatures can get really high.
Vibration Resistance: Cars are always shaking and getting bumped around, especially when you’re driving in tough conditions. Because of this, automotive PCB is designed with stronger mechanical connections and more rugged mounting techniques than regular PCB. This might mean using through-hole components and special glues to hold the components down tight on the board, so they don’t come loose and break.
Reliability and Longevity: Given that safety is paramount in automotive applications, PCB used in vehicles are subjected to more stringent reliability standards. They are often required to have a longer life expectancy, which is achieved through the use of high-quality materials and rigorous testing protocols that exceed those used for standard PCB.
Complexity and Integration: Automotive PCB generally incorporate more advanced technologies, such as HDI (High Density Interconnect) technology, which allows for a greater number of components in a smaller area. This is critical in modern vehicles where space is at a premium and functionality requirements are high.
As you navigate the complexities of automotive PCB procurement and management, remember that each design decision and material choice affects the overall efficacy and reliability of the end product. By understanding these foundational aspects of automotive PCB, you ensure that the electronics you provide not only meet but exceed the stringent standards required by the industry, catering perfectly to discerning clients who prioritize quality and reliability in their automotive components. This knowledge empowers you to make informed decisions that enhance the value and performance of your automotive electronics offerings.

Chapter 3
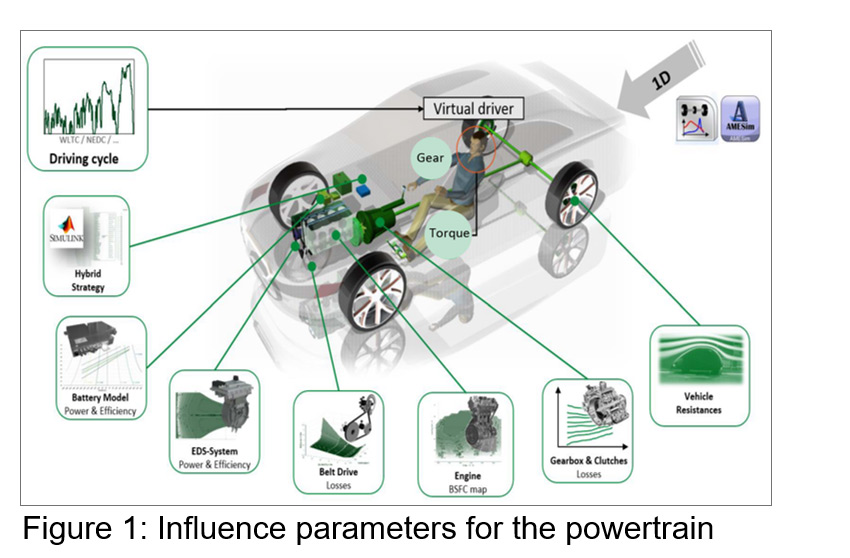
Design Principles for Automotive PCB
Critical Design Considerations Unique to Automotive PCB
There are 3 key considerations that guide automotive PCB design: thermal management, vibration resistance, and miniaturization. These are more than just design parameters; they are benchmarks that define the robustness and functionality of automotive electronics.
Thermal Management: In the compact confines of an automotive environment, managing heat is not just about protecting the PCB; it’s about safeguarding the entire vehicle’s functionality. Advanced thermal management techniques include the use of thermally conductive dielectric materials and heat sinks that are integrated directly onto the PCB. The design may also incorporate thermal vias which help dissipate heat across the board more effectively, thus preventing hotspots that could lead to component failure.
Vibration Resistance: As a professional in automotive electronics, you know that PCB durability under constant vibration is non-negotiable. To enhance vibration resistance, automotive PCB is designed with rugged through-hole components and utilize flexible substrates that can bend without breaking. The layout itself is carefully designed to minimize stress points and place components away from high-vibration areas whenever possible.
Miniaturization: As vehicles incorporate more electronic features into increasingly smaller spaces, the pressure to miniaturize PCB without compromising their performance is tremendous. Techniques such as utilizing HDI (High-Density Interconnect) technology are pivotal. HDI allows for finer lines and spaces, smaller vias, and denser connection pad patterns, which in turn enable more functions per unit area. This not only meets the space constraints but also reduces weight, which is crucial for fuel efficiency and electric vehicle range.
Advanced Design Techniques to Enhance Reliability and Performance
To ensure that your automotive PCB not only meet but exceed the rigorous demands of the automotive industry, integrating advanced design techniques is essential. These methods are designed to enhance both the reliability and performance of your PCB:
Use of Simulation Software: Using PCB simulation software early in the design process can identify potential issues with circuit design, component placement, and thermal distribution. This proactive approach enables optimization before the prototype stage, saving development costs and time.
Component Embedding Technology: This technique involves embedding passive components within the PCB substrate itself, reducing surface clutter and enhancing the thermal stability of the board. This leads to improved signal integrity and a reduction in electromagnetic interference (EMI), which is crucial in the electronically noisy environment of a vehicle.
Signal Integrity Analysis: High-speed signals within the compact space of an automotive PCB require careful management to avoid cross-talk and EMI. Employing signal integrity analysis during design ensures that high-speed data transfers occur without degradation, which is particularly important for safety-critical functions like braking and airbag deployment.
Rigorous Testing and Validation: Incorporating stringent testing and validation phases, including Highly Accelerated Life Testing (HALT) and Highly Accelerated Stress Screening (HASS), ensures that the PCB can withstand the extreme conditions they will face in automotive environments. This not only builds confidence in the reliability of the PCB but also reinforces your commitment to quality to your clients.
By focusing on these sophisticated design principles and techniques, you are not just creating PCB; you are engineering the future of automotive electronics. Each decision you make in the design phase impacts the reliability, efficiency, and overall performance of the automotive systems that depend on your PCB, ensuring that you deliver excellence and innovation to a market that relies on precision.
Chapter 4
Materials and Components Selection
Guide to Choosing the Right Materials for Automotive PCB
When you are tasked with selecting materials for automotive PCB, your choices are pivotal in defining the board’s durability and performance under the extreme conditions typical of automotive environments. These materials must not only ensure the structural integrity of the PCB but also address thermal, mechanical, and chemical challenges.
Substrate Materials: The substrate forms the core of your PCB. For automotive applications, materials like FR-4 are commonly used for their good thermal resistance and mechanical strength. However, for higher performance needs, materials such as Polyimide or PTFE (Polytetrafluoroethylene) are preferred due to their superior heat resistance and electrical insulation properties. These materials are crucial in environments where the PCB is exposed to high temperatures and require a high degree of reliability.
Copper Thickness: Copper layers in automotive PCB typically need to be thicker than those in standard PCB to handle higher currents and enhance thermal conductivity. A thicker copper layer improves the durability and heat dissipation, critical for preventing overheating in compact automotive electronics. The choice of copper thickness should balance electrical performance and thermal management without compromising the physical integrity of the board.
Protective Coatings: Automotive PCB often require additional protective coatings to withstand harsh environmental conditions. Conformal coatings made from materials like silicone, acrylic, or urethane are applied to shield electronic circuits from moisture, dust, chemicals, and extreme temperatures. This not only extends the life of the PCB but also ensures consistent performance in diverse operational conditions.
Insights into High-Quality Component Selection
Choosing the right components is just as critical as selecting the appropriate materials for your automotive PCB. High-quality component selection is essential to meet the rigorous industry standards and ensure the reliability demanded by discerning customers like Bob, who prioritize quality above all.
Choosing Reliable Components: Opt for components from reputable manufacturers known for their high standards and rigorous testing. Components such as capacitors, resistors, and ICs should have proven track records in automotive applications, ensuring they can handle the stresses of high temperatures, vibration, and long-term wear and tear.
Automotive Grade Components: Always use automotive-grade components that are specifically designed and tested for use in vehicles. These components meet stringent automotive reliability standards such as AEC-Q100 for ICs, ensuring they perform under severe conditions. This is crucial for maintaining system integrity and safety, especially in critical systems like braking or steering control.
Testing for Quality Assurance: Before finalizing component selection, ensure that they undergo rigorous testing processes such as temperature cycling, vibration testing, and life testing. This not only confirms their suitability for automotive use but also builds confidence in the reliability of your final product. Implementing a robust testing protocol reflects your commitment to delivering high-quality, dependable products.
Vendor Partnerships: Establish strong relationships with component vendors who understand the automotive market’s demands. This can lead to better support in terms of customization, reliable supply chains, and quick access to the latest technologies and components that meet the evolving standards of the automotive industry.
By meticulously selecting the right materials and components for your automotive PCB, you are not just assembling a product; you are crafting a core element of modern automotive technology that promises reliability and performance.
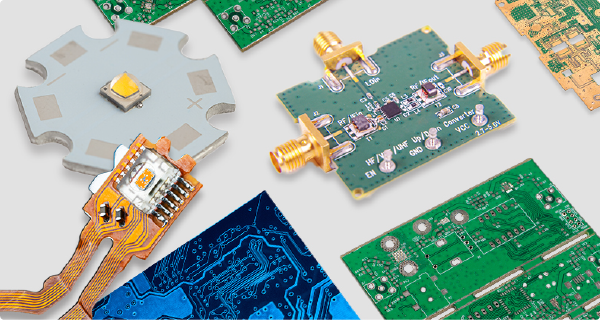
Chapter 5

Manufacturing Processes
In-depth look at automotive PCB manufacturing technology
In the automotive industry, where reliability and precision are paramount, the manufacturing processes for PCB must be meticulously controlled. As you oversee these processes, understanding each step’s nuances ensures that the final product not only meets but exceeds the rigorous demands of automotive applications.
Layering and Lamination: Automotive PCB often require multiple layers to accommodate complex circuits needed for advanced functionalities. The process begins with the stacking of copper and insulating materials, which are then laminated together under high temperatures and pressures. This creates a single, integrated structure where each layer must align perfectly to ensure connectivity and functionality. Special attention is given to the alignment of vias and pads, which are critical for multi-layer boards.
Circuit Patterning and Etching: Once the layers are prepared, photolithography is used to transfer the circuit design onto the board. This involves coating the PCB with a light-sensitive material, exposing it to ultraviolet light through a mask shaped according to the circuit design, and then chemically etching away the unexposed parts. For automotive PCB, this process is refined to achieve high precision and density, which are crucial for managing the complex and compact circuits required in modern vehicles.
Plating and Surface Finish: After etching, the PCB undergoes plating, where additional copper is added to the surface and in the vias. This step enhances the conductivity and strength of the connections. The choice of surface finish—such as ENIG (Electroless Nickel Immersion Gold), HASL (Hot Air Solder Leveling), or OSP (Organic Solderability Preservatives)—depends on factors like reliability, conductivity, and shelf life. Each finish provides different benefits, such as improving solderability or resistance to oxidation, which are vital for the harsh environments encountered in automotive applications.
Emphasis on Quality Control Measures and Testing Processes
Quality control is not just a phase in the manufacturing process; it is an integral part of each step, ensuring that every automotive PCB that leaves your facility is built to last and perform flawlessly.
Automated Optical Inspection (AOI): After each critical manufacturing step, AOI systems are used to check for any defects such as misalignments, insufficient solder, or short circuits. This method uses high-resolution cameras to inspect the boards and is crucial for identifying issues early in the manufacturing process.
Functional Testing: Before the boards are shipped, they undergo functional testing to ensure that every circuit works as intended under conditions that simulate actual automotive environments. This might include power-up tests, in-circuit tests, and system-level tests, ensuring that each component on the PCB performs reliably.
Environmental and Stress Testing: Automotive PCB is subjected to rigorous environmental testing, including temperature cycling, thermal shock tests, and vibration tests. These tests mimic the conditions the PCB will face in real-world automotive settings, highlighting any potential failure points in the manufacturing process.
Continuous Improvement Feedback Loop: Incorporating feedback from the testing phases back into the manufacturing process is crucial for continuous improvement. This approach helps in identifying recurring issues, such as soldering problems, and allows for the adjustment of processes to eliminate these issues in future production cycles.
By maintaining stringent quality control and detailed manufacturing processes, you ensure the reliability and performance of automotive PCB, directly addressing common pain points like soldering issues. This commitment to excellence not only meets the high standards expected by your clients but also positions your products at the forefront of automotive technology, where quality and reliability are non-negotiable.
Chapter 6
Assembly Techniques
Overview of Surface Mount Technology (SMT) and Through-Hole Technology (THT) in Automotive PCB Assembly
In the automotive electronics industry, component robustness and reliability are critical, and two major assembly technologies—surface mount technology (SMT) and through-hole technology (THT)—play a vital role. Understanding the benefits and applications of each technology can significantly impact the performance and durability of a PCB in an automotive environment.
Surface Mount Technology (SMT): SMT has become the dominant assembly process in automotive PCB manufacturing due to its efficiency and ability to accommodate high-density component placement. In SMT, components are mounted directly on the PCB surface without the need for large drilled holes. This technology allows for smaller components and more compact PCB designs, which is critical for space-constrained automotive applications. In addition, SMT allows for faster assembly and typically more robust connections under thermal stress, which is common in automotive environments.
Through-Hole Technology (THT): Although SMT has become very popular, THT is still critical for automotive applications, which require extremely strong mechanical connections between the PCB and the components, especially for connectors or heavy components that may be subjected to great physical stress. In THT, component leads are inserted through pre-drilled holes in the PCB and then soldered to pads on the other side. This technology provides enhanced strength and reliability for components that must withstand high levels of vibration and mechanical stress, making it an ideal choice for high-power or high-stress automotive applications.
Best Practices for Component Placement and Soldering Techniques
To ensure the highest quality and reliability of automotive PCB, meticulous attention must be paid to component placement and soldering techniques. These practices are crucial for mitigating common quality issues such as poor solder joints, component misalignment, and thermal mismatches.
Optimized Component Placement: Strategic component placement is crucial for minimizing stress and enhancing the performance of the PCB. Components sensitive to heat or those generating heat should be placed away from each other to manage thermal profiles effectively. Consider the thermal expansion coefficients of different components to avoid stress and potential damage during temperature fluctuations.
Advanced Soldering Techniques: The soldering process is where many quality issues can arise in PCB assembly. Utilizing advanced soldering techniques such as selective soldering and reflow soldering can help achieve more consistent and reliable solder joints. Selective soldering is particularly useful for THT components where precision is crucial, while reflow soldering is ideal for achieving uniform heat distribution during the soldering of SMT components.
Use of Automated Systems: Implementing automated placement and soldering systems can significantly reduce human error and increase the precision of component placement and soldering. These systems are particularly effective in meeting the stringent quality requirements of automotive PCB.
Regular Inspection and Testing: Incorporating regular inspections during the assembly process, using methods like Automated Optical Inspection (AOI) and X-ray inspection, helps identify and rectify potential defects early. Solder quality tests, such as pull and shear tests, should be routinely conducted to ensure the mechanical integrity of solder joints.
By adhering to these assembly techniques and best practices, you ensure that the automotive PCB you produce are capable of withstanding the rigorous conditions they will face in the field. This commitment to quality not only meets the demands of your discerning clients but also enhances the reliability and longevity of the automotive products that incorporate these PCB, thereby maintaining your reputation as a leader in automotive electronics manufacturing.
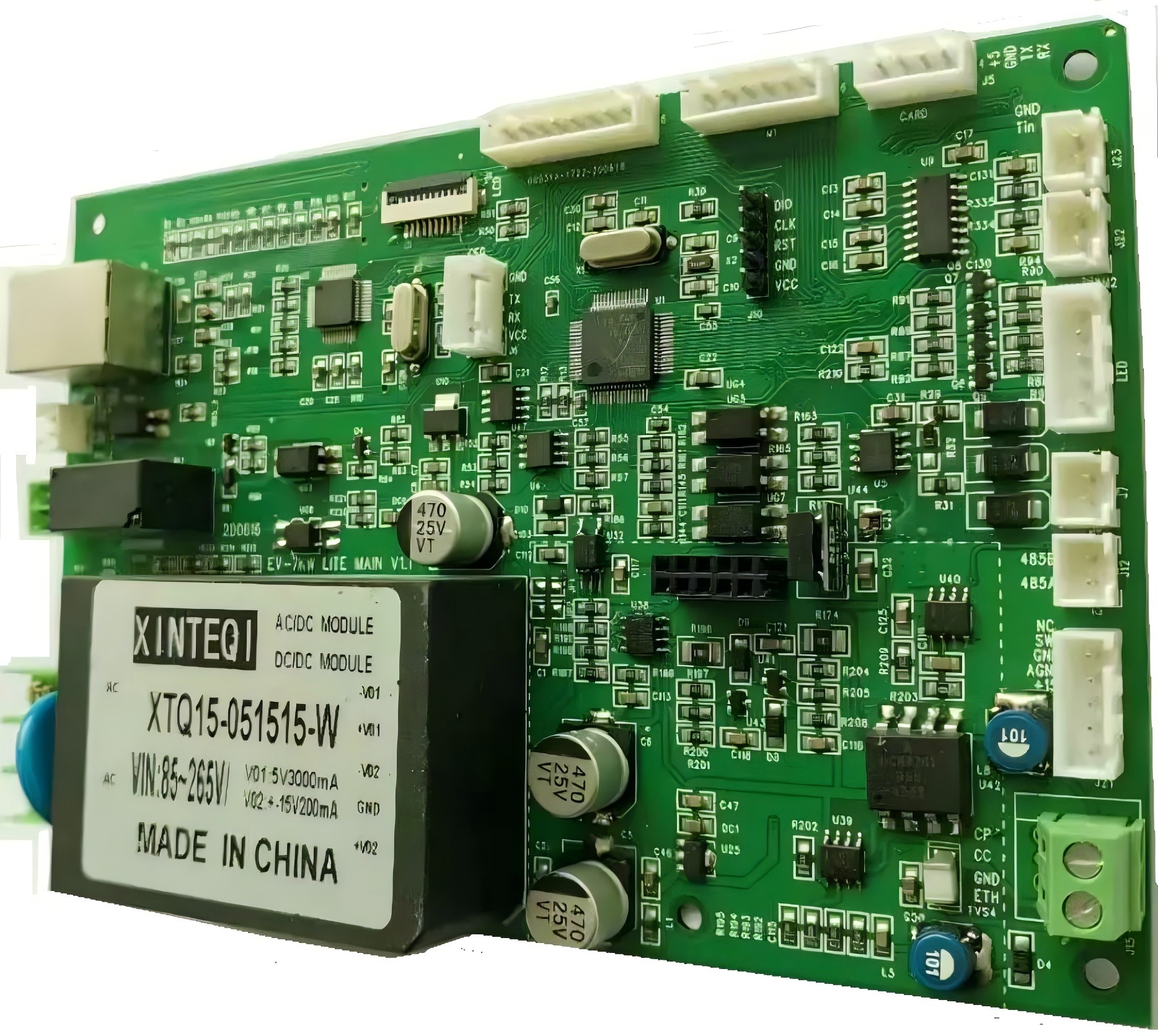
Chapter 7
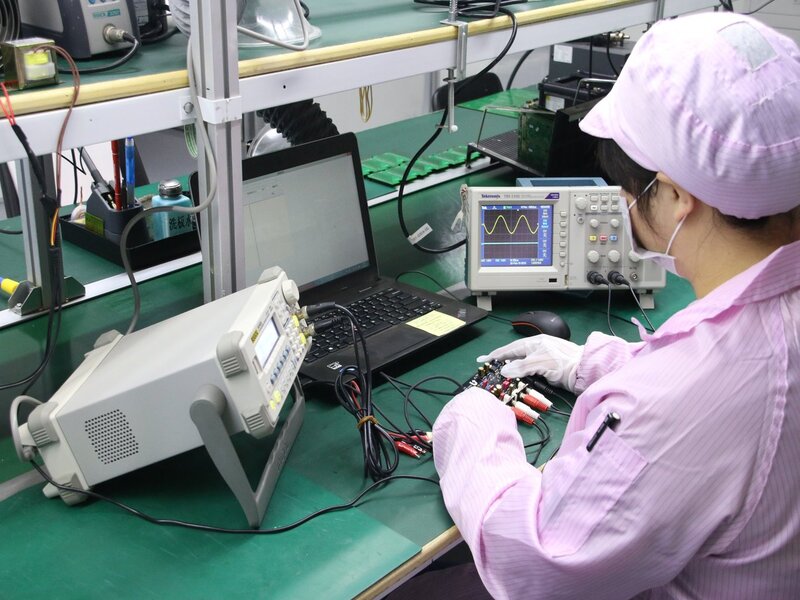
Testing and Quality Assurance
Comprehensive Strategies for Rigorous Testing Phases
In the automotive industry, where the safety and reliability of electronic components can directly impact the functionality and safety of the vehicle, rigorous testing phases are not just a regulatory requirement, but a cornerstone of product development. Implementing comprehensive testing strategies ensures the high quality of automotive PCB, which is paramount for meeting both customer expectations and industry standards.
Pre-assembly Testing: Before assembly begins, raw materials and components are tested to verify their compliance with specifications. This includes testing for material properties such as tensile strength, thermal resistance, and electrical conductivity. Ensuring the quality of these inputs is crucial as they set the foundation for the reliability of the finished PCB.
In-process Testing: During the assembly process, in-process testing is critical to identify any issues early on. This includes Automated Optical Inspection (AOI) for checking solder paste application, component placement, and soldering quality after each step. Additionally, electrical tests such as in-circuit testing (ICT) are performed to check for shorts, opens, and other electrical anomalies.
Functional Testing: After assembly, each PCB undergoes functional testing to ensure it performs as expected under conditions that mimic its intended operational environment. This includes power-up tests, system integration tests, and stress tests that simulate the electrical loads and operational conditions the PCB will face in the vehicle.
Environmental and Durability Testing: Automotive PCB is subjected to environmental stress testing, including temperature cycling, thermal shock tests, humidity tests, and vibration tests. These tests are designed to expose the PCB to extremes of temperature, moisture, and physical stress that it would encounter in its lifetime, ensuring that it can withstand these without failure.
Life Cycle Testing: To ensure longevity, automotive PCB is put through accelerated life testing, where conditions are intensified to induce failures sooner, thus predicting the lifespan of the product under normal operating conditions. This helps in understanding wear-out mechanisms and improving product designs.
Adherence to International Quality Standards
Ensuring compliance with international quality standards is not merely about fulfilling regulatory requirements—it’s about building trust with your customers by consistently delivering products that meet high safety and reliability standards. Here’s how to maintain adherence to these standards:
ISO 9001 and ISO/TS 16949 Certification: These certifications are fundamental for automotive PCB manufacturers, indicating that your quality management system meets the high standards required for automotive parts supply. Maintaining these certifications requires regular audits and continuous improvement of your processes.
IPC Standards for PCBs: Adhering to IPC standards, such as IPC-A-600 for PCB acceptability and IPC-A-610 for electronic assemblies, ensures that your products meet the performance and reliability standards expected in the automotive industry. These standards cover everything from material selection and design to assembly and testing.
Regular Quality Audits and Supplier Reviews: Conduct regular audits of your processes and also review your suppliers to ensure that every component in your supply chain meets the required quality standards. This includes periodic validation of their testing methods and quality control processes.
Documentation and Traceability: Maintain thorough documentation of your testing processes and results. Implement traceability measures that allow you to track each PCB back to its raw materials, production batch, and testing records. This not only aids in quality control but also ensures accountability and facilitates easier root cause analysis in case of defects.
By implementing these rigorous testing phases and adhering to international quality standards, you not only assure the quality of your automotive PCB but also reinforce your commitment to excellence. This dedication to quality assurance is crucial in upholding your reputation and reliability in the competitive automotive industry, meeting the high expectations of clients who prioritize top-tier quality and safety in their products.
Chapter 8
Failure Analysis and Troubleshooting
Common Automotive PCB Failures and Diagnostic Methods
In the rigorous environment of automotive applications, PCB failures can have significant repercussions, from system malfunctions to safety concerns. As a professional responsible for the reliability and safety of automotive electronics, understanding common failures and how to diagnose them is paramount.
Solder Joint Failures: One of the most common issues in automotive PCB is solder joint failure, which can result from poor soldering, thermal cycling, or mechanical stress. Diagnostic methods include visual inspections with high-magnification optics and automated optical inspection (AOI) systems, which can detect cracks, cold joints, or misalignments.
Component Failures: Components on PCB can fail due to overstress, wear out, or manufacturing defects. To diagnose these failures, techniques like electrical testing (using in-circuit tests to check functionality) and thermal imaging to detect overheated areas are essential. For more detailed analysis, advanced methods like Scanning Electron Microscopy (SEM) can identify microscopic failures in component structures.
Conductive Anodic Filament (CAF) Growth: In high-humidity environments, CAF growth can occur within the PCB, leading to electrical shorts between conductive paths. Detection often requires destructive physical analysis (DPA) to examine the internal structure of the PCB layers and identify any unwanted conductive pathways.
Environmental Stress: Exposure to extreme temperatures, moisture, and corrosive substances can lead to PCB delamination, trace corrosion, and other material degradation. Environmental chambers are used to simulate conditions that a PCB might face, identifying potential failure modes under controlled test scenarios.
Preventative Measures and Troubleshooting Guides
To ensure the longevity and reliability of automotive PCBs, implementing preventative measures and establishing robust troubleshooting guides are crucial. These not only help in quickly resolving issues but also in preventing them from occurring in the first place.
Design for Reliability (DfR): Incorporate reliability into the PCB design phase by selecting appropriate materials, optimizing layout for thermal management, and using simulation tools to predict how designs will perform under different stress conditions. This approach helps in minimizing potential failure points right from the start.
Regular Maintenance and Inspection: Implement a schedule for regular maintenance and inspections, including periodic testing of critical PCB functions. This proactive measure can identify potential issues before they lead to failures, significantly reducing downtime and maintenance costs.
Environmental and Stress Testing Protocols: Develop comprehensive testing protocols that subject PCB to environmental and mechanical stresses they will likely encounter. Use the findings from these tests to strengthen the PCB design and assembly processes, enhancing overall durability and performance.
Troubleshooting Guides: Create detailed troubleshooting guides that can be easily followed by technical teams. These guides should include common symptoms of failure, diagnostic steps, and corrective actions. For more complex issues, guides should advise on when to escalate the problem to engineering teams for deeper analysis.
Training and Education: Provide ongoing training for your teams on the latest diagnostic techniques and tools. Knowledgeable personnel are your first line of defense against PCB failures, capable of identifying and mitigating issues efficiently.
By focusing on these areas of failure analysis and troubleshooting, you ensure that automotive PCB is not only designed and manufactured with the highest standards but are also supported through their operational life with effective maintenance and problem-solving strategies. This comprehensive approach is vital for maintaining the integrity and reliability of PCB in automotive applications, thereby upholding your commitment to quality and safety in the demanding automotive industry.
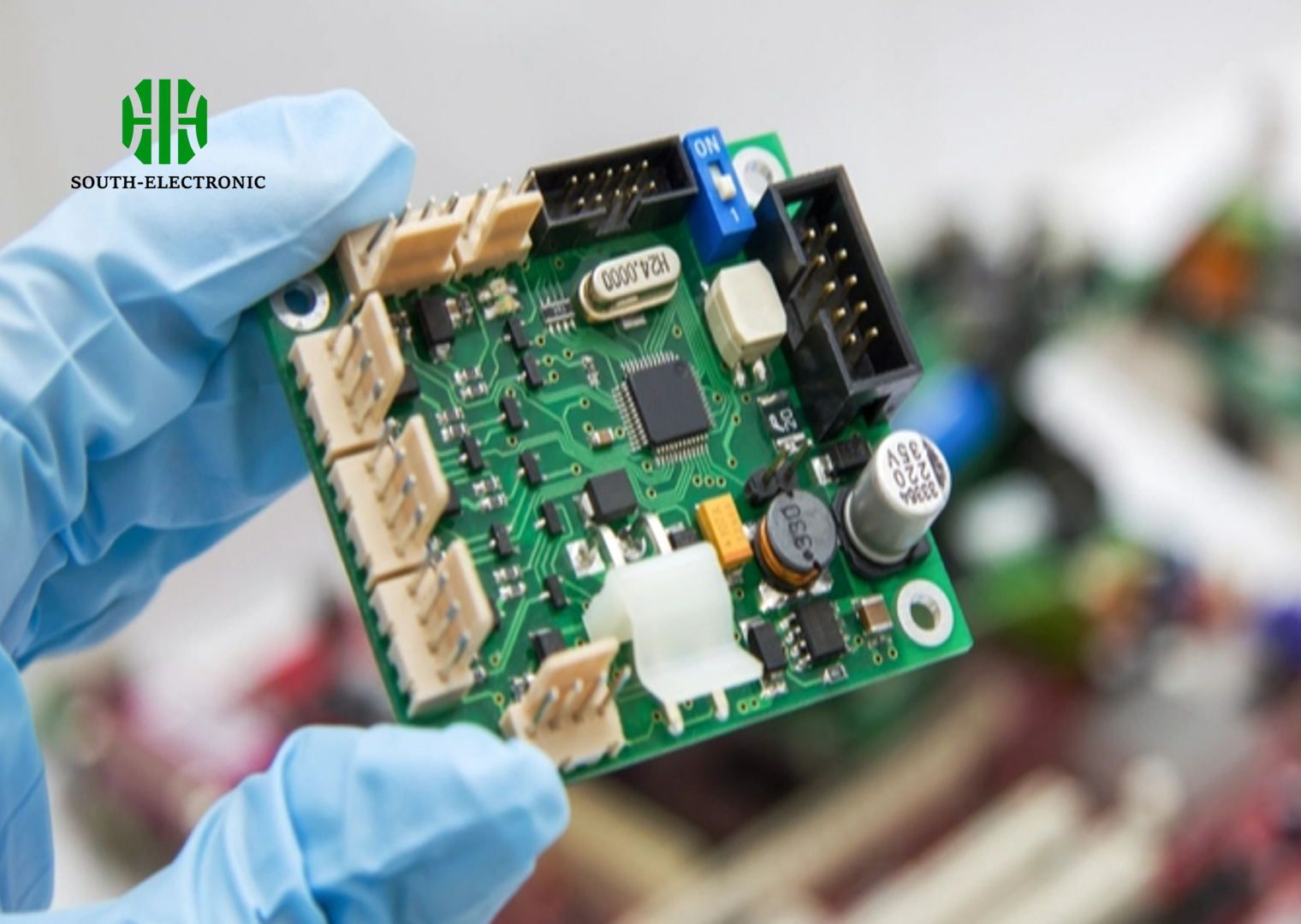
Chapter 9

Innovations and Future Trends
Exploration of Emerging Technologies Such as Flexible PCB for Automotive Use
As you navigate the rapidly evolving landscape of automotive electronics, staying at the forefront of technological advancements, such as flexible printed circuit boards (PCB), is crucial. Flexible PCB are transforming automotive design by offering new possibilities for integrating electronics into spaces where traditional rigid PCB cannot fit.
Advantages of Flexible PCB: Flexible PCB is particularly valuable in automotive applications because of their ability to bend, twist, and fold, allowing them to conform to complex geometries within the vehicle. This flexibility reduces space constraints, enhances the design freedom, and opens up opportunities for innovative applications such as curved instrument panels, connected surfaces, and advanced lighting systems. Moreover, their lightweight nature contributes to overall vehicle weight reduction, which is critical in improving fuel efficiency and battery range in electric vehicles.
Durability and Reliability: Unlike rigid PCB, flexible PCB is built to withstand high levels of vibration and flexing, making them ideal for the dynamic automotive environment. Their durability is enhanced by the use of robust materials like polyimide or polyester, which can endure extreme temperatures and chemical exposures typical in automotive settings.
Integration with Traditional Systems: Combining flexible and rigid PCB technologies, often referred to as rigid-flex PCB, provides the structural stability of rigid PCB with the versatility of flexible circuits. This hybrid approach is particularly effective in space-constrained applications, optimizing the available space while ensuring reliable electrical performance.
Discussion on How Innovations are Shaping the Future of Automotive Electronics
The automotive industry’s shift towards more integrated and intelligent electronics is being significantly influenced by innovations in PCB technology. As you look to the future, understanding these trends can help you anticipate changes and leverage them to maintain a competitive edge.
Smart Surfaces and Interfaces: Innovations in PCB are enabling the transformation of many passive elements of vehicles, like dashboards and door panels, into interactive smart surfaces. These changes enhance user experience by integrating touch sensors and displays directly into the vehicle’s architecture, providing more intuitive controls and information displays.
Autonomous and Connected Vehicles: As vehicles become more autonomous, the demand for sophisticated electronic systems that can communicate with each other and with external networks increases. Advanced PCB support the integration of sensors, controllers, and connectivity modules necessary for autonomous driving technologies, ensuring faster data transmission and enhanced processing capabilities.
Electrification of Vehicles: The global push towards electric vehicles (EVs) is driving the need for more efficient power management systems. PCB in these systems must handle higher currents and provide greater heat dissipation, challenges that are being met with new PCB materials and designs.
Sustainability: With an increasing focus on sustainability, the PCB industry is innovating with recyclable materials and processes that reduce environmental impact. Biodegradable substrates and lead-free solders are examples of how the industry is adapting to environmental regulations and consumer expectations.
By staying informed about these innovations and trends, you position yourself not just as a supplier but as a strategic partner in the automotive electronics industry, capable of meeting the needs of forward-thinking customers who are looking for cutting-edge solutions. This proactive approach not only secures your place in the market but also drives the industry forward, shaping the future of automotive electronics in ways that prioritize efficiency, integration, and sustainability
Chapter 10
Case Studies and Industry Insights
Real-World Examples of Successful Automotive PCB Applications
Exploring successful real-world applications of automotive PCB not only highlights the capabilities of this technology but also demonstrates its impact on automotive innovation and efficiency. As you position yourself within the industry, understanding these applications will help you better communicate the value of your products and services.
Advanced Driver-Assistance Systems (ADAS): One notable example is the use of multilayer PCBs in ADAS, where they facilitate the integration of multiple sensors and cameras. These systems require highly reliable PCB to process and transmit large amounts of data in real-time, ensuring safety and precision. For instance, a leading automotive manufacturer integrated these PCB to enhance their lane-keeping and automatic braking functionalities, significantly reducing road accidents.
Electric Vehicle (EV) Power Systems: In another case, a prominent EV manufacturer utilized high-density interconnect (HDI) PCB to manage the complex power systems required for efficient battery management and power distribution. The PCB supported higher circuit densities and finer lines, optimizing space and improving the performance of the power management systems, leading to longer battery life and increased vehicle range.
Infotainment Systems: Flexible and rigid-flex PCB have revolutionized automotive infotainment systems by allowing for more ergonomic and user-friendly interfaces. A luxury car brand successfully implemented these PCB to create a seamless and aesthetically pleasing dashboard that integrates touch controls and displays, enhancing the user experience without compromising the sophisticated interior design.
Lessons Learned and Best Practices from Industry Leaders
Gleaning insights from industry leaders can provide valuable lessons and best practices that not only refine your processes but also inspire confidence in your potential clients. These insights help in anticipating challenges and fostering innovation within your operations.
Emphasis on Quality Control: A consistent lesson from top manufacturers is the critical importance of stringent quality controls throughout the PCB manufacturing process. Implementing advanced testing and inspection at each stage has been crucial in minimizing defects and ensuring reliability, especially for safety-critical components like those used in ADAS.
Collaborative Design Process: Industry leaders often stress the value of a collaborative approach to PCB design, involving suppliers, designers, and end-users early in the design process. This collaboration ensures that the PCB are not only manufacturable at scale but also meet the specific needs of the application, reducing costly redesigns and enhancing product functionality.
Adaptation to New Technologies: Staying abreast of emerging technologies and materials has been a hallmark of successful PCB manufacturers. For example, the shift towards using environmentally sustainable materials and processes not only complies with regulatory standards but also appeals to the growing market segment concerned with environmental impact.
Focus on Customization: Tailoring solutions to the specific needs of each customer has proven effective. Whether it’s adapting to unique design constraints or developing specialized features for niche applications, customization has enabled manufacturers to differentiate themselves and build strong relationships with their clients.
By incorporating these real-world examples, lessons, and best practices into your business strategy, you not only enhance your operational excellence but also position yourself as a thought leader in the automotive PCB industry. This approach not only attracts potential clients but also fosters long-term partnerships by demonstrating a commitment to quality, innovation, and customer satisfaction.
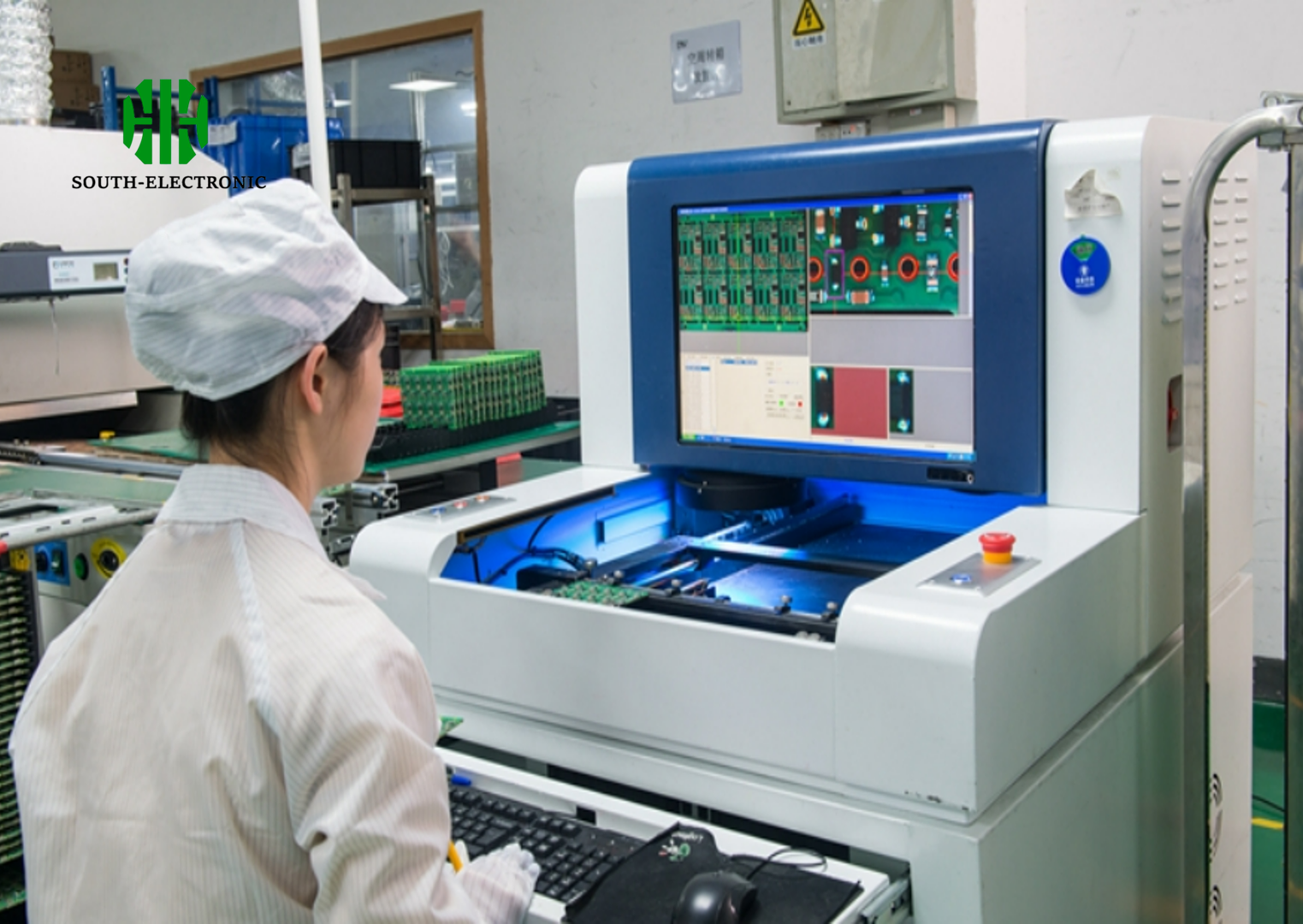
Get in touch
Where Are We?
Industrial Park, No. 438 Donghuan Road, No. 438, Shajing Donghuan Road, Bao'an District, Shenzhen, Guangdong, China
Floor 4, Zhihui Creative Building, No.2005 Xihuan Road, Shajing, Baoan District, Shenzhen, China
ROOM A1-13,FLOOR 3,YEE LIM INDUSTRIAL CENTRE 2-28 KWAI LOK STREET, KWAI CHUNG HK
service@southelectronicpcb.com
Phone : +86 400 878 3488
Send us a message
The more detailed you fill out, the faster we can move to the next step.
