High-Quality 8-Layer PCB
South-Electronic
Go with South-Electronic for the best quality, reliability, and value in your PCB needs. See the difference with our all-in-one 8-layer PCB service – from design to delivery, we guarantee accuracy, durability, and compliance with the highest industry standards.
Your Trusted Partner for High-Quality 8-Layer PCB
Why Choose South-Electronic?
South-Electronic is your go-to solution. With over a decade of expertise, we deliver precision-engineered, custom 8-layer PCBs designed to meet the highest industry standards. Whether you need just one piece or a bulk order, we provide tailored solutions with a fast turnaround time.
-
Customization Flexibility
You’ll have the freedom to order exactly what you need, whether it’s a single prototype or large production volumes.
Our advanced customization capabilities ensure your 8-layer PCB is designed and manufactured to meet even the most intricate specifications, providing you with tailored solutions that align perfectly with your project requirements. -
Experienced Team
You can trust our team of seasoned experts, with over a decade of hands-on experience in PCB manufacturing.
From complex designs to troubleshooting technical challenges, our engineers are well-versed in the latest industry trends and innovations, ensuring your 8-layer PCBs are of the highest quality and precision. -
Strict Quality Control
You’ll be assured that every PCB produced is held to the highest standards, as we are certified by UL, CE, IATF16949, and ISO13485.
These certifications reflect our unwavering commitment to quality, safety, and reliability, giving you peace of mind knowing that your PCBs will perform optimally in even the most demanding environments. -
Comprehensive Service
You’ll experience a truly seamless process from the moment you share your design to the final delivery of your 8-layer PCBs.
We handle every stage of production in-house, from prototyping to assembly, utilizing state-of-the-art equipment that ensures precision, speed, and consistency. Your satisfaction is our priority, and we’re here to support you at every step. -
Fast Delivery
You’ll benefit from our streamlined production processes and advanced machinery that allow us to meet tight deadlines without sacrificing quality.
Whether it’s a time-sensitive project or a high-volume order, you can count on us for fast, reliable delivery that keeps your project on schedule. -
Guaranteed Satisfaction
You’ll appreciate the confidence that comes with working with an ISO9001 certified company.
We prioritize clear, transparent communication and hold ourselves to the highest standards, ensuring that your 8-layer PCBs not only meet but exceed your expectations for performance, durability, and precision.
Related Project We had Done
Customer Reviews
engineer
thank you, guys, the boards are really good, i am really happy to receive my boards, the components are perfect!
Operation Manager
South-Electronic is my first PCBA supplier in China. The service and quality are excellent, and the after-sales support is also very impressive. Good Job!
Common Questions
Most Popular Questions
South-Electronic provides strong after-sales support, offering warranties on their products. They adhere to strict quality control measures such as ISO and RoHS certifications, ensuring long-term reliability and customer satisfaction.
South-Electronic is certified with UL, CE, IATF16949, ISO13485, and ISO9001, so you can be confident that their 8-layer PCBs meet the highest international standards for quality, safety, and performance.
The typical lead time for 8-layer PCBs is between 7 to 15 business days, depending on the complexity and quantity of your order. If you need faster delivery, they also offer expedited options.
To get a quote, you can visit South-Electronic’s website and submit your design specifications through their contact form or email their sales team directly. They’ll respond quickly with a detailed quote based on your requirements.
Yes, South-Electronic offers global shipping to ensure timely delivery to customers around the world. Their logistics solutions are designed to provide secure and efficient delivery.
South-Electronic provides strong after-sales support, offering warranties on their products. They adhere to strict quality control measures such as ISO and RoHS certifications, ensuring long-term reliability and customer satisfaction.
Send us a message
The more detailed you fill out, the faster we can move to the next step.
The Complete Guide for 8-Layer PCB
Contents
Chapter 1
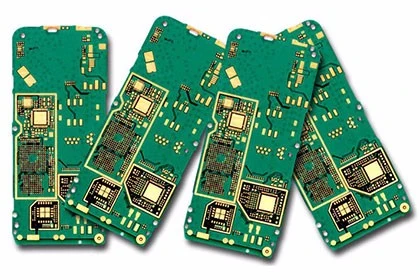
Introduction to 8-Layer PCB
What is an 8-Layer PCB?
An 8-layer PCB is a type of multilayer printed circuit board that has eight layers of conductive material, usually copper, separated by insulating materials (also called dielectrics). These layers are laminated together using heat and pressure to create a compact, sturdy, and efficient structure. The conductive layers allow for intricate routing of electrical signals, while the insulating layers prevent interference between different signals on the board.
In a nutshell, 8-layer PCBs are essential for creating advanced, high-performance electronic systems, making them a cornerstone of many industries, including telecommunications, automotive, medical, and industrial applications.
Importance and Common Uses of 8-Layer PCBs in Electronics
8-layer PCBs play a critical role in modern electronics, especially in applications where space is limited, but performance demands are high. The additional layers provide improved signal integrity, better electromagnetic compatibility (EMC), and enhanced power distribution. These benefits make 8-layer PCBs ideal for applications that require robust performance and reliability.
Key Importance:
- Signal Integrity: With more layers, signal traces can be better separated, reducing cross-talk and interference. This leads to cleaner signals and improved performance, especially for high-speed data transmission.
- Power Distribution: The extra layers allow for more efficient power plane distribution, minimizing voltage drops and ensuring stable power delivery to all components.
- Miniaturization: 8-layer PCBs enable designers to pack more functionality into smaller devices, which is essential for modern electronics like smartphones and wearables.
- Thermal Management: The additional layers can help manage heat more effectively, crucial for high-performance components.
Common Uses:
- Telecommunications: 8-layer PCBs are commonly used in networking devices like routers, switches, and telecommunications equipment, where high-speed data transfer is essential.
- Automotive Electronics: In modern vehicles, 8-layer PCBs are employed for advanced systems like engine control units (ECUs), GPS modules, and infotainment systems that require compact designs and reliable performance.
- Medical Devices: The precision and reliability of 8-layer PCBs make them suitable for medical devices, including diagnostic machines and imaging equipment, where accuracy is critical.
- Industrial Automation: 8-layer PCBs are used in industrial control systems and automation equipment, where durability, signal integrity, and high performance are needed.
In summary, 8-layer PCBs are essential for creating advanced, high-performance electronic systems, making them a cornerstone of many industries, including telecommunications, automotive, medical, and industrial applications.
Chapter 2
Advantages of Using 8-Layer PCB
1. Enhanced Signal Integrity and Reduced Interference
One of the biggest advantages of using an 8-layer PCB is the significant improvement in signal integrity. Signal integrity refers to the quality of the electrical signals as they travel through the PCB. In designs with fewer layers, signal paths can be longer, leading to potential issues such as signal loss, cross-talk, and electromagnetic interference (EMI). These problems can degrade the performance of the device, especially in high-speed applications.
With an 8-layer PCB, additional layers allow for more separation between signal paths, reducing the chance of interference between them. Moreover, specialized layers can be designated for grounding or power distribution, helping to shield sensitive signal traces from interference. As a result, this enhanced layer separation and grounding improve the overall quality of the signals, making the PCB suitable for high-frequency applications like telecommunications, data processing, and RF circuits.
Key Benefits:
- Reduced cross-talk between signals due to better layer management.
- Improved shielding with dedicated ground and power planes.
- Suitable for high-speed and high-frequency applications where signal integrity is critical.
2. Greater Component Density and Space Efficiency
As electronic devices continue to shrink in size while increasing in functionality, the need for compact, high-density PCBs has become more important. An 8-layer PCB provides a significant advantage by allowing designers to accommodate more components and complex routing in a smaller space. This is particularly beneficial for devices where space is at a premium, such as smartphones, tablets, and wearable electronics.
The multiple layers of an 8-layer PCB allow for more efficient routing of signals, reducing the need for long, winding traces on the surface layers. This not only saves space but also shortens the signal paths, which contributes to better performance. Additionally, the higher layer count allows for more flexibility in placing components, enabling designers to pack more functionality into a smaller footprint without compromising the performance or integrity of the circuit.
Key Benefits:
- Higher component density allows for more functionality in compact devices.
- Efficient routing with shorter signal paths improves overall performance.
- Space efficiency enables the production of smaller, more powerful electronics.
3. Improved Heat Dissipation
Thermal management is a critical consideration in PCB design, especially for high-power applications or devices that operate continuously for extended periods. Excessive heat can degrade the performance and lifespan of components, making effective heat dissipation essential.
An 8-layer PCB provides better heat dissipation than boards with fewer layers because the additional layers can help distribute heat more evenly across the board. In multilayer PCBs, thermal vias—small holes filled with conductive material—can be used to transfer heat from the surface layers to the inner layers, where it can be dissipated more effectively. This reduces the concentration of heat in any one area, helping to protect sensitive components from thermal damage.
Moreover, the added layers allow for the inclusion of thicker copper planes dedicated to power distribution, which helps in conducting heat away from critical areas. This is especially important in applications such as industrial machinery, automotive electronics, and power supplies, where excessive heat can compromise reliability and performance.
Key Benefits:
- Better thermal management through even heat distribution across layers.
- Thermal vias improve heat dissipation, protecting components from overheating.
- Suitable for high-power applications and environments where heat is a concern.
Conclusion
In summary, the advantages of 8-layer PCBs make them an ideal choice for high-performance, space-constrained, and heat-sensitive applications. The enhanced signal integrity, greater component density, and improved heat dissipation ensure that these PCBs are well-suited for advanced technologies across industries such as telecommunications, automotive, and industrial automation.

Chapter 3
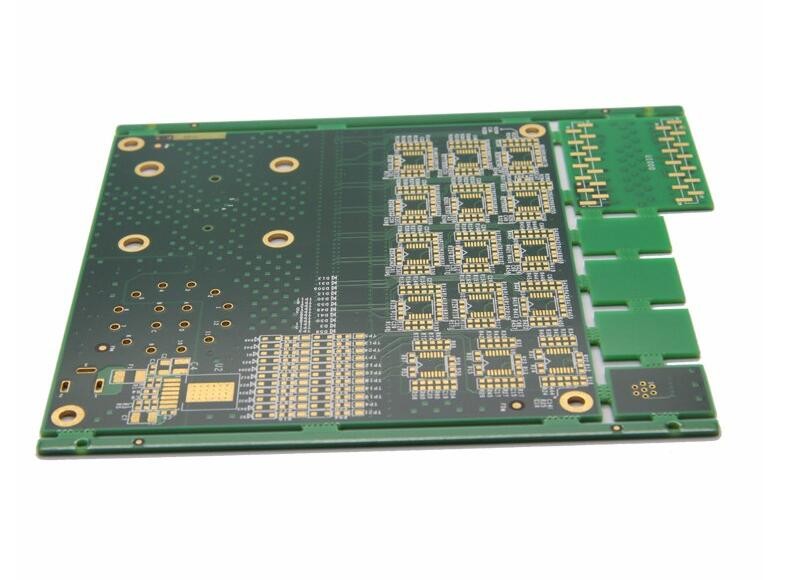
8-Layer PCB Stack-Up Design
Explanation of Stack-Up Structure
The stack-up design of a PCB refers to how the layers of copper (used for routing signals and power) and insulating materials (known as dielectrics) are arranged in the board. In an 8-layer PCB, there are eight conductive layers, typically made of copper, which are separated by layers of insulating material. The stack-up design is crucial because it directly impacts the board’s electrical performance, manufacturability, and cost.
In a standard 8-layer PCB, the layers are arranged in a specific order, usually with signal layers on the outermost layers and power and ground planes in between. This arrangement helps maintain signal integrity, reduce noise, and provide a stable power distribution network. The goal of a well-designed stack-up is to create an optimized structure that minimizes electromagnetic interference (EMI), supports high-speed signals, and efficiently manages power distribution.
A typical 8-layer stack-up consists of alternating layers of signal and power/ground planes:
- Signal Layers: Used for routing electrical signals between components.
- Ground Planes: Provide a reference point for signals, helping reduce noise and EMI.
- Power Planes: Distribute power to the components while minimizing voltage drops and interference.
How to Optimize Layer Arrangement for Signal Integrity, Power Distribution, and Grounding
The arrangement of layers in an 8-layer PCB plays a crucial role in achieving optimal signal integrity, power distribution, and grounding. Here are key strategies to optimize the stack-up:
Signal Integrity:
- Alternating Signal and Ground Planes: Placing signal layers adjacent to ground planes (or power planes) helps shield the signals and reduces electromagnetic interference. This configuration lowers the chances of cross-talk between signals, especially in high-speed circuits.
- Minimize Signal Path Lengths: Keeping signal traces short and placing related signals on the same or adjacent layers can reduce signal delay and loss, improving overall performance.
- Differential Pair Routing: For high-speed signals, use differential pairs (two closely spaced traces carrying equal and opposite signals) on signal layers to enhance noise immunity.
Power Distribution:
- Dedicated Power Planes: Placing a power plane adjacent to a ground plane creates a low-inductance path for power distribution, which reduces voltage fluctuations and ensures stable power delivery. This is particularly important in high-power circuits.
- Optimizing Power and Ground Layer Placement: The power and ground layers should be paired closely to create a “power sandwich,” minimizing impedance and providing a smoother power flow to components.
Grounding:
- Multiple Ground Layers: Having multiple ground layers in the stack-up improves shielding, reduces noise, and provides a stable reference for signals. Ground layers are essential for maintaining signal integrity, particularly in high-frequency applications.
- Ground Vias and Connections: Adding plenty of ground vias (vertical connections between layers) helps ensure proper grounding across all layers, reducing the risk of signal degradation.
Chapter 4
Material Selection for 8-Layer PCB
Choosing the right materials for an 8-layer PCB is critical to achieving the desired performance, durability, and cost-effectiveness for your specific application. The material primarily influences the electrical, thermal, and mechanical properties of the PCB, which in turn affects signal integrity, heat dissipation, and overall reliability. In this section, we will explore the best materials for 8-layer PCBs, their specific uses, and how material choice impacts performance, cost, and durability.
Best Materials for Different Applications
FR4 (Flame Retardant 4)
- Overview: FR4 is one of the most commonly used materials for PCB substrates. It is a glass-reinforced epoxy laminate that provides excellent electrical insulation, mechanical strength, and resistance to moisture and heat.
- Applications: FR4 is widely used in consumer electronics, telecommunications, automotive electronics, and industrial equipment. It’s suitable for low to moderate-frequency applications where cost is a significant factor.
- Advantages:
- Low cost and widely available.
- Good mechanical strength and electrical insulation.
- Suitable for general-purpose applications, including multilayer designs like 8-layer PCBs.
- Disadvantages:
- Limited high-frequency performance due to higher dielectric losses compared to specialized materials like Rogers.
- Lower thermal conductivity, making it less ideal for applications with significant heat generation.
Rogers (High-Frequency Laminates)
- Overview: Rogers is a high-performance material known for its excellent dielectric properties and low signal loss at high frequencies. It is commonly used in applications requiring superior signal integrity, such as RF and microwave circuits.
- Applications: Rogers laminates are used in high-speed digital, RF, microwave, and communication systems, where signal loss must be minimized. It is ideal for advanced applications such as radar systems, 5G networks, and satellite communications.
- Advantages:
- Low dielectric constant and low signal loss, making it ideal for high-frequency and high-speed applications.
- High thermal conductivity, allowing for better heat dissipation.
- Superior stability in environments with high humidity or temperature fluctuations.
- Disadvantages:
- More expensive than FR4, which can significantly increase the cost of production.
- Can be more challenging to process, requiring specialized equipment and techniques.
Polyimide
- Overview: Polyimide is a flexible, high-temperature material known for its excellent thermal and mechanical properties. It is often used in applications requiring both flexibility and durability, such as flex and rigid-flex PCBs.
- Applications: Polyimide is commonly used in aerospace, military, and medical applications where boards need to withstand extreme environments or frequent bending and flexing.
- Advantages:
- Excellent thermal stability and can withstand extreme temperatures.
- High mechanical flexibility, making it ideal for flexible PCBs and applications requiring movement or bending.
- Good electrical insulation properties and chemical resistance.
- Disadvantages:
- Higher cost than FR4, particularly in rigid-flex PCB designs.
- Slightly more complex to manufacture, requiring advanced techniques for production.
PTFE (Polytetrafluoroethylene)
- Overview: PTFE is a synthetic fluoropolymer material known for its low dielectric constant and high-frequency capabilities. It is often used in microwave and RF applications due to its excellent electrical properties.
- Applications: PTFE is used in high-frequency communication systems, antennas, and RF devices where minimal signal loss and interference are critical.
- Advantages:
- Extremely low dielectric constant, making it perfect for high-frequency circuits.
- Chemically inert and resistant to high temperatures and harsh environments.
- Excellent for minimizing signal loss in sensitive RF and microwave applications.
- Disadvantages:
- Expensive compared to other materials like FR4, which can drive up production costs.
- Difficult to process and manufacture, requiring specialized techniques and tools.
The Impact of Material Choice on Performance, Cost, and Durability
Performance
- Signal Integrity: The choice of material has a direct impact on the electrical performance of the PCB. High-frequency applications, such as RF and microwave circuits, require materials with low dielectric constants and low signal loss (e.g., Rogers or PTFE). For general-purpose applications where high-frequency signals are not a concern, FR4 provides a cost-effective option while still offering good signal integrity for low to moderate frequencies.
- Thermal Management: Materials like Rogers and Polyimide have better thermal conductivity than FR4, making them more suitable for applications with high power requirements or those that generate significant heat. Choosing a material with better heat dissipation properties ensures longer component lifespan and reduces the risk of thermal damage.
- Mechanical Properties: Applications requiring flexibility, such as in aerospace or medical devices, benefit from materials like Polyimide, which offers mechanical flexibility and durability in dynamic environments. Stiffer materials like FR4 are better suited for rigid designs where mechanical flexibility is not required.
Cost
- Material Cost: FR4 is generally the most affordable material and is widely available, making it the go-to choice for many general-purpose applications. Rogers, Polyimide, and PTFE are more expensive options, typically used in specialized or high-performance applications where the benefits of enhanced signal integrity, thermal management, or flexibility justify the higher costs.
- Manufacturing Complexity: Some materials, like PTFE and Rogers, require specialized manufacturing processes, which can add to the overall production cost. For example, Rogers materials may need more advanced equipment for lamination and drilling, making it more expensive to produce than FR4 boards. Additionally, complex stack-ups and designs with multiple high-frequency layers may further increase costs due to the precision required.
Durability
- Thermal and Chemical Resistance: Polyimide and PTFE materials offer superior resistance to high temperatures and harsh environments compared to FR4, making them more durable in applications where environmental stress is a concern. For instance, in aerospace or industrial applications, materials that can withstand extreme heat, moisture, or chemical exposure are critical for ensuring the long-term reliability of the PCB.
- Mechanical Strength: For applications that require robust mechanical performance, such as in automotive or industrial electronics, materials like FR4 and Polyimide provide the necessary rigidity or flexibility. Polyimide, in particular, is well-suited for flexible circuits that need to bend without losing structural integrity.
Conclusion
Material selection is one of the most critical decisions in 8-layer PCB design because it directly impacts the performance, cost, and durability of the final product. While FR4 is a cost-effective choice for general-purpose applications, more advanced materials like Rogers, Polyimide, and PTFE are ideal for high-frequency, high-thermal, and flexible applications. Understanding the specific requirements of your project will help you choose the right material, balancing performance needs with cost and manufacturability.
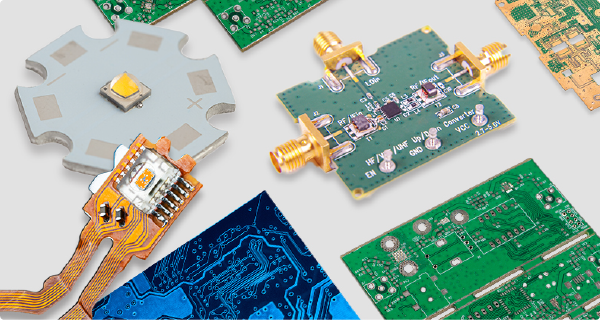
Chapter 5

Applications
8-layer PCBs are a big deal in a lot of advanced electronic systems, especially in industries where high performance, signal integrity, and space efficiency are important. The extra layers give you more flexibility in your circuit design, which means you can do more complex things, better thermal management, and better signal integrity. Here are some of the most common and important places where you’d use an 8-layer PCB.
1. High-Speed Communications
Overview:
The telecommunications industry is one of the primary users of 8-layer PCBs due to the demand for high-speed data transmission and signal integrity. As data rates increase and devices become more complex, maintaining the integrity of signals over long distances and at high speeds becomes crucial. The additional layers in an 8-layer PCB allow for better signal routing, enhanced grounding, and minimized electromagnetic interference (EMI), all of which are critical for communication systems.
Key Uses:
- Networking Equipment: Devices like routers, switches, and modems rely on 8-layer PCBs to handle large amounts of data at high speeds. The extra layers help in separating signal paths, reducing cross-talk, and providing stable power distribution, ensuring reliable performance in networking environments.
- 5G Technology: As the world shifts toward 5G, the need for PCBs that can support high-frequency signals and maintain signal integrity is increasing. 8-layer PCBs play a significant role in the infrastructure behind 5G technology, from base stations to handheld devices.
- Fiber Optics: Fiber-optic communication systems, which require extremely low latency and high-speed data processing, benefit from the signal integrity and efficient power management provided by 8-layer PCBs.
Benefits for High-Speed Communications:
- Reduced signal interference and cross-talk due to better layer separation.
- Improved signal integrity at high frequencies, essential for fast data transmission.
- Greater routing flexibility to accommodate complex circuitry for communication systems.
2. Automotive Electronics
Overview:
The automotive industry increasingly relies on electronic systems to manage everything from engine control units (ECUs) to advanced driver-assistance systems (ADAS). 8-layer PCBs are essential for managing the complexity of modern vehicles, as they allow for greater component density and more sophisticated circuitry in a compact space. Automotive electronics must also withstand harsh environmental conditions, including extreme temperatures and vibrations, making the durability of an 8-layer PCB critical.
Key Uses:
- Engine Control Units (ECUs): ECUs are responsible for controlling various functions of the vehicle’s engine, such as fuel injection, ignition timing, and emissions control. These systems require reliable PCBs with multiple layers to manage the complex data and control systems that ensure engine efficiency and performance.
- Advanced Driver-Assistance Systems (ADAS): ADAS includes features like lane departure warnings, collision avoidance, and adaptive cruise control. These systems rely on multiple sensors, cameras, and radar technologies, all of which require high-performance PCBs to process data quickly and accurately.
- In-Vehicle Infotainment (IVI) Systems: Infotainment systems combine audio, video, and navigation functions. The integration of these various features demands PCBs that can handle high-speed data transfer and provide stable power distribution to ensure smooth operation.
Benefits for Automotive Electronics:
- Enhanced durability and reliability to withstand harsh automotive environments.
- Support for complex, high-density circuitry required by modern automotive systems.
- Improved thermal management, critical in automotive electronics to prevent overheating.
3. Medical Devices
Overview:
Medical devices often require PCBs that can deliver high precision, reliability, and longevity. Many medical applications involve sensitive data processing, where even the slightest signal interference could affect performance. 8-layer PCBs are widely used in medical equipment for their ability to handle complex circuits while maintaining signal integrity and ensuring long-term reliability.
Key Uses:
- Diagnostic Imaging Systems: Medical devices like MRI, CT, and ultrasound machines rely on complex circuits that require precise signal transmission. The multilayer design of 8-layer PCBs helps ensure that these signals are clear and free of interference, which is crucial for accurate diagnostics.
- Portable Medical Devices: Portable devices such as heart monitors, insulin pumps, and handheld diagnostic tools require compact, lightweight PCBs with high reliability. 8-layer PCBs allow for more components to be included in a smaller form factor, making them ideal for portable medical applications.
- Surgical Equipment: High-precision surgical tools often involve electronic components that assist surgeons during procedures. These devices must be incredibly reliable, as any failure could have severe consequences. 8-layer PCBs provide the required complexity and durability for such high-stakes equipment.
Benefits for Medical Devices:
- High reliability and durability for life-critical applications.
- Compact design allows for integration into portable or minimally invasive medical devices.
- Reduced signal interference, essential for precision diagnostic and monitoring tools.
4. Industrial Controls
Overview:
Industrial control systems, such as those used in automation, robotics, and power management, require PCBs that can handle high power loads, complex control algorithms, and harsh operating environments. 8-layer PCBs offer the necessary layer count to accommodate the extensive routing and power management required by modern industrial electronics. Additionally, their enhanced thermal management capabilities make them well-suited for high-power applications.
Key Uses:
- Automation Systems: Factories and industrial plants rely on automation systems to control processes and machinery. These systems need to process large amounts of data in real-time and often operate in challenging environments. 8-layer PCBs provide the durability, signal integrity, and power management needed for such applications.
- Robotics: Robots used in manufacturing, healthcare, and research require complex control systems to manage movement, sensors, and data processing. 8-layer PCBs help integrate multiple subsystems while maintaining the signal integrity needed for precise operation.
- Power Supplies: Industrial-grade power supplies need PCBs that can handle high current and voltage while ensuring efficient heat dissipation. The additional layers in an 8-layer PCB allow for better power plane distribution and help manage thermal loads effectively.
Benefits for Industrial Controls:
- Enhanced power distribution and thermal management for high-current applications.
- Ability to support complex, high-density circuit designs in industrial systems.
- Robustness and durability to withstand harsh industrial environments.
5. Other Applications
8-layer PCBs are also found in several other advanced fields:
- Aerospace Electronics: In aerospace, weight and space are crucial factors. 8-layer PCBs allow for high component density in a compact design while ensuring high reliability under extreme conditions.
- Consumer Electronics: High-end consumer electronics like smartphones, tablets, and gaming consoles require PCBs with advanced routing capabilities and the ability to handle high-speed data. 8-layer PCBs meet these demands while keeping devices compact and lightweight.
- Wearable Technology: As wearable devices become more advanced, they require PCBs that can fit into small, flexible form factors. 8-layer PCBs allow for more functionality in a smaller space, making them ideal for wearable applications like smartwatches and fitness trackers.
Conclusion
8-layer PCBs are a big part of how we design and make modern electronic devices in a bunch of different industries. They let you move data really fast, do complicated things, and manage power really efficiently, which is important in telecom, automotive, medical, industrial, and more. Whether you’re building the next generation of 5G networks or making life-saving medical devices, 8-layer PCBs give you the performance and reliability you need for the toughest applications out there.
Chapter 6
Manufacturing Process for 8-Layer PCB
The manufacturing process for 8-layer PCBs is complex and requires precise control over each stage to ensure high performance and reliability. From initial design to final assembly, each step involves careful planning, execution, and testing. This section provides a detailed breakdown of the key steps involved in manufacturing an 8-layer PCB, the common challenges encountered, and the critical quality checks that ensure the finished product meets industry standards.
Step 1: Design and Layout
The first step in the manufacturing process is the design of the 8-layer PCB, which involves creating a schematic and translating it into a physical layout using PCB design software. The design process includes:
- Schematic Capture: The circuit design is captured in the form of a schematic, which represents the electrical connections between components.
- Layer Stack-Up Design: The arrangement of the 8 layers is determined, optimizing the placement of signal, power, and ground layers for signal integrity and power distribution.
- Routing: Signals are routed between components on different layers using vias (vertical interconnections), ensuring minimal interference and optimized signal paths.
- Design for Manufacturability (DFM): The layout is optimized to meet manufacturing constraints, ensuring that the design can be produced reliably and cost-effectively.
During the design phase, it’s crucial to account for factors like trace width, spacing, and via placement to minimize signal loss and ensure that the final PCB meets performance specifications.
Step 2: Material Selection
Once the design is finalized, the next step is selecting the materials that will be used for the 8-layer PCB. The choice of materials is based on the application’s requirements, including:
- Substrate Material: The base material (often FR4, Rogers, or Polyimide) is selected based on factors like signal integrity, thermal performance, and cost.
- Copper Foil Thickness: The thickness of the copper layers is chosen to handle the required current-carrying capacity.
- Prepreg and Core Materials: Prepreg (fiberglass impregnated with resin) and core materials are used to bond the layers together and provide insulation between conductive layers.
The material selection step is critical to achieving the desired electrical, thermal, and mechanical properties of the PCB.
Step 3: Layer Preparation and Lamination
With the design and materials selected, the manufacturing process begins with the preparation of individual layers:
- Inner Layer Imaging: A layer of photoresist is applied to the copper-clad substrate, and the circuit pattern for each layer is printed using UV light. This process creates the paths that will carry electrical signals.
- Etching: After imaging, the unwanted copper is etched away, leaving only the designed traces on the layer.
- Layer Alignment: Each of the 8 layers is carefully aligned using an optical registration system to ensure that the vias and traces connect properly across layers.
- Lamination: The layers are then stacked together, with insulating layers (prepreg) between them. The stack is placed in a lamination press, where heat and pressure are applied to bond the layers together into a single, solid board.
Step 4: Drilling and Via Formation
After the layers are laminated, the next step is drilling holes to create vias, which connect the different layers of the PCB:
- Drilling: Precision drills are used to create holes through the stack, targeting specific points where connections need to be made between layers. These holes can range from simple through-holes to more complex microvias or buried vias.
- Plating: After drilling, the holes are plated with a thin layer of copper to create an electrical connection between the layers.
This step is particularly challenging for 8-layer PCBs due to the need for precise alignment of the vias and the risk of damaging internal layers during drilling.
Step 5: Outer Layer Imaging and Plating
Once the vias are formed, the outer layers of the PCB are imaged and etched:
- Outer Layer Imaging: A photoresist layer is applied to the outermost copper layers, and the circuit pattern is printed using UV light. The areas that will carry signals are protected, while the rest is exposed for etching.
- Plating: A layer of copper is electroplated onto the exposed areas, including the drilled holes, to create the necessary connections. Additional layers of tin or solder may be applied to protect the copper traces and vias during the final etching process.
- Etching: The excess copper is removed, leaving behind the desired circuit patterns on the outer layers.
At this stage, the PCB begins to take its final form, with all the necessary connections in place.
Step 6: Solder Mask and Silkscreen Application
To protect the PCB and prepare it for component assembly, the following steps are taken:
- Solder Mask Application: A layer of solder mask is applied to the PCB to protect the copper traces from oxidation and prevent solder bridges during assembly. The solder mask is typically green, but other colors like blue, red, and black can also be used.
- Silkscreen Printing: The silkscreen layer is applied to add text, component labels, and reference markings to the PCB, aiding in assembly and troubleshooting.
The solder mask and silkscreen layers are critical for ensuring the PCB is durable and easy to work with during the assembly process.
Step 7: Electrical Testing
Before assembly, the 8-layer PCB undergoes rigorous testing to ensure it meets design specifications:
- Electrical Testing: Automated test systems check for continuity (ensuring all connections are correctly made) and isolation (ensuring no unwanted connections or shorts between different parts of the circuit). Flying probe tests or bed-of-nails testers are commonly used.
- Impedance Testing: For high-speed designs, impedance testing ensures that the PCB maintains the correct impedance values across different layers, which is essential for signal integrity.
Testing is a critical step in ensuring the PCB functions correctly and meets performance standards before components are added.
Step 8: Assembly
Once the PCB passes all testing, it moves on to the assembly phase, where components are mounted on the board:
- Surface Mount Technology (SMT): Components are placed on the surface of the PCB using automated pick-and-place machines. The components are then soldered in place using a reflow oven, which melts the solder and creates a secure connection.
- Through-Hole Assembly: For components that require through-hole mounting, the leads are inserted into the pre-drilled holes and soldered, either manually or using wave soldering machines.
- Inspection: The assembled PCB undergoes visual inspection, automated optical inspection (AOI), and X-ray inspection to ensure all components are correctly placed and soldered.
Common Challenges in 8-Layer PCB Manufacturing
- Layer Registration: Ensuring precise alignment of all 8 layers is critical. Even a slight misalignment can lead to faulty connections or signal integrity issues.
- Drilling Precision: Drilling through multiple layers without damaging inner layers or vias can be challenging. Advanced drilling techniques and tools are required to maintain accuracy.
- Thermal Management: With 8 layers, the PCB can generate significant heat during operation. Proper thermal management techniques, such as the use of thermal vias and efficient power distribution, are essential.
- Signal Integrity: As the number of layers increases, maintaining signal integrity becomes more difficult. Careful planning of the layer stack-up, impedance control, and routing are necessary to avoid cross-talk and interference.
Quality Checks in 8-Layer PCB Manufacturing
To ensure the highest quality standards, multiple quality checks are performed throughout the manufacturing process:
- Visual Inspections: Each layer is visually inspected for defects such as shorts, open circuits, or misalignments.
- Automated Optical Inspection (AOI): Used to automatically detect surface-level defects and ensure component placement is accurate.
- Electrical Testing: Continuity and isolation tests are performed to check for proper electrical connections and ensure there are no shorts.
- Impedance Testing: Ensures the PCB meets the required impedance specifications, which is critical for high-frequency applications.
- Thermal Testing: In some cases, thermal cycling tests are performed to assess the board’s ability to handle temperature variations without delamination or component failure.
Conclusion
The manufacturing process for 8-layer PCBs is a detailed and precise operation that requires careful attention to every step, from design and material selection to fabrication and assembly. By understanding the common challenges and ensuring rigorous quality checks, manufacturers can produce 8-layer PCBs that meet the high-performance demands of modern electronics.
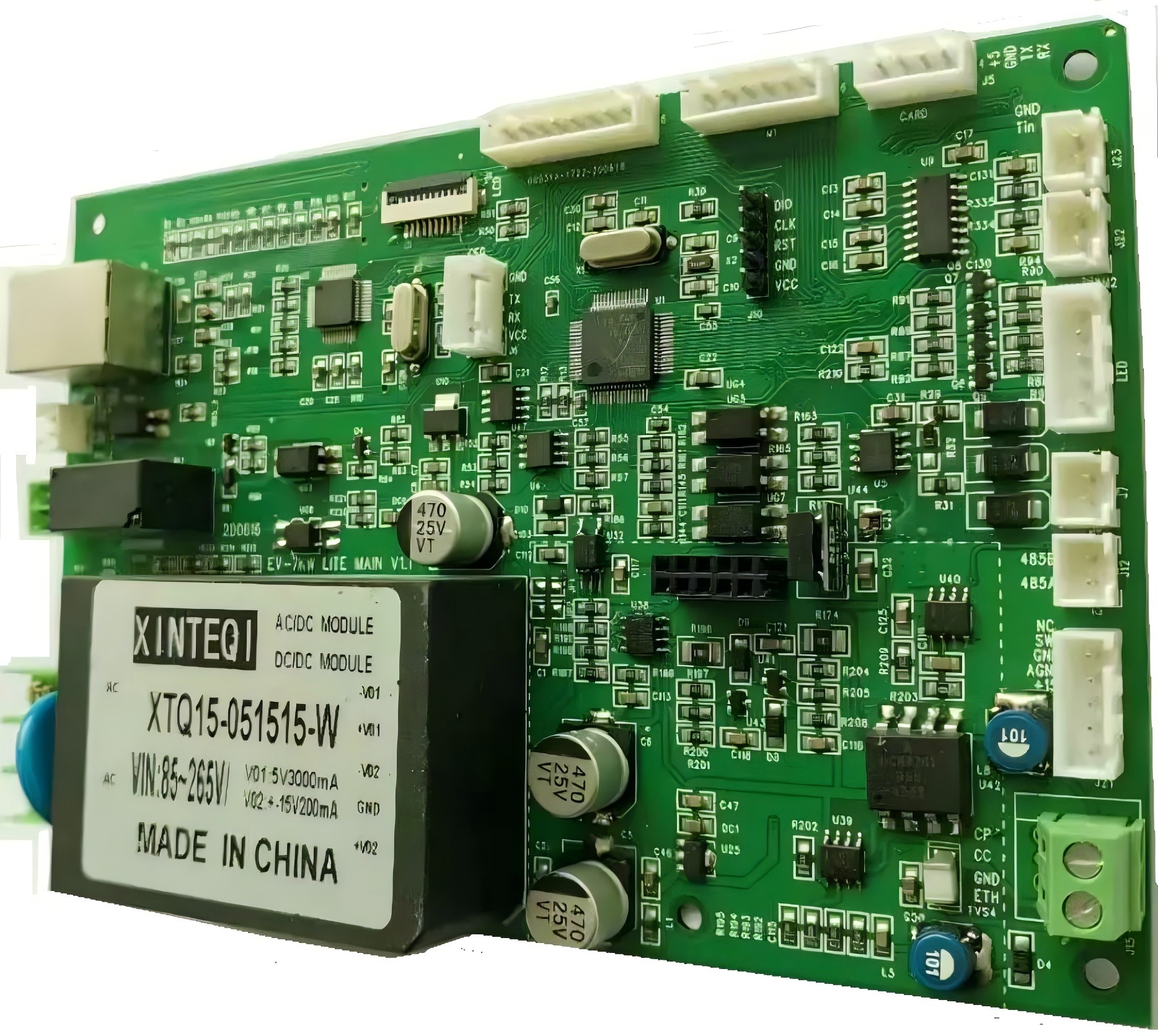
Chapter 7
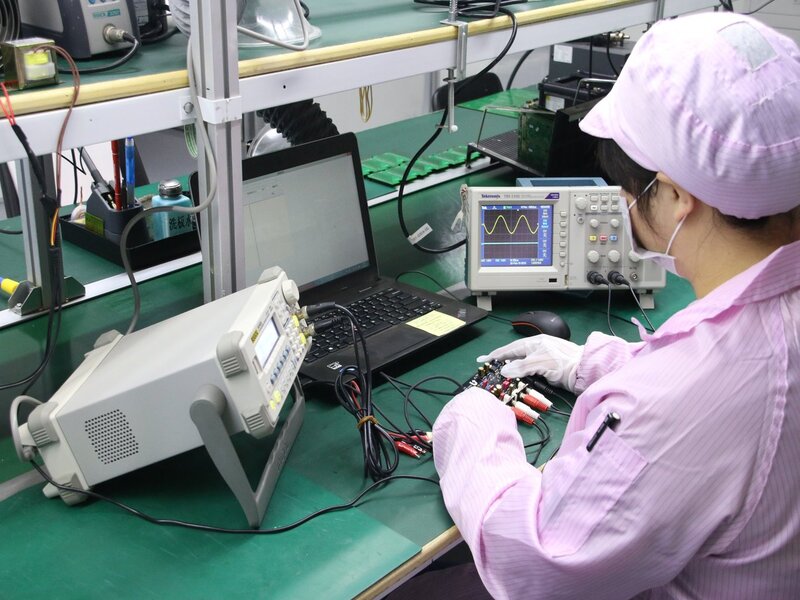
Cost Factors in 8-Layer PCB Production
The cost of producing an 8-layer PCB can vary significantly depending on a range of factors. From the materials used to the complexity of the design, each element plays a role in determining the final price of the board. In this section, we will break down the key cost drivers in 8-layer PCB production and provide tips for reducing costs without sacrificing quality.
Breakdown of Factors Affecting the Cost
Materials
- Substrate Material: The type of substrate material used in an 8-layer PCB has a major impact on cost. Commonly used materials include FR4, which is relatively inexpensive and widely available, and high-performance laminates like Rogers or Polyimide, which are significantly more expensive due to their superior electrical properties and thermal stability. The choice of material depends on the application’s requirements, such as signal integrity, frequency, and environmental conditions.
- Copper Thickness: The thickness of the copper layers also affects the price. Thicker copper is often required for boards that need to handle higher currents or provide better heat dissipation, but it increases material costs. Thicker copper layers (e.g., 2 oz/ft² or more) are more expensive than the standard 1 oz/ft².
- Surface Finishes: The type of surface finish used on the PCB (such as HASL, ENIG, or OSP) affects both performance and cost. For example, ENIG (Electroless Nickel Immersion Gold) offers excellent corrosion resistance and is ideal for high-reliability applications but is more expensive than HASL (Hot Air Solder Leveling).
Layer Count
- Higher Layer Count Equals Higher Costs: Each additional layer increases the complexity of the PCB, requiring more materials, more complex stack-up designs, and additional manufacturing steps. An 8-layer PCB is naturally more expensive than a 4-layer or 6-layer PCB because of the additional inner layers and the more sophisticated lamination process. The more layers required, the higher the manufacturing cost due to increased labor and the need for specialized equipment to align and laminate the layers properly.
- Lamination Process: As the number of layers increases, so does the complexity of the lamination process. In an 8-layer PCB, multiple prepreg (insulating) and core layers must be carefully aligned and laminated under precise conditions to avoid defects like misalignment or delamination, which adds to the cost.
Complexity of the Design
- Advanced Routing and Via Types: Complex routing strategies such as high-density interconnect (HDI), blind vias, buried vias, and microvias can significantly drive up costs. These technologies require advanced equipment and more time to fabricate. Additionally, designs with fine-pitch components or high-speed signal requirements need precise control of trace widths and spacing, which also increases the production cost.
- Impedance Control: PCBs with controlled impedance, often required for high-speed or high-frequency applications, are more expensive to manufacture because they require tighter tolerances during fabrication and careful attention to trace design and stack-up configuration.
- Thermal Management: Some applications require advanced thermal management techniques, such as the use of thermal vias, heat sinks, or special laminates with high thermal conductivity. These measures add complexity and cost to the production process.
Production Volume
- Prototype vs. Mass Production: The production volume significantly impacts the unit cost of an 8-layer PCB. Small batch or prototype runs are much more expensive on a per-board basis because setup costs (such as preparing tooling and performing tests) are spread across fewer units. In contrast, mass production allows for economies of scale, reducing the per-unit cost.
- Setup Costs: Each production run involves setup costs for creating the necessary tooling, configuring the equipment, and preparing materials. For low-volume orders, these setup costs can represent a significant portion of the overall price. Larger production runs allow these fixed costs to be amortized over many units, leading to a lower cost per board.
Tips for Reducing Costs Without Compromising Quality
Choose the Right Material for the Application
- Optimize Material Selection: While high-performance materials like Rogers or Polyimide offer excellent electrical and thermal properties, they may not be necessary for all applications. If your design doesn’t require the advanced characteristics of these materials, choosing a more cost-effective material like FR4 can reduce costs without affecting the board’s performance for lower-frequency or less demanding applications.
- Evaluate Copper Thickness: Use the standard copper thickness of 1 oz/ft² unless your design requires higher current handling or better heat dissipation. Only increase copper thickness if absolutely necessary, as this can significantly add to the material costs.
Simplify the Design Where Possible
- Minimize Via Types: Blind, buried, and microvias are essential for certain high-density designs but can be costly. If your design allows for the use of standard through-hole vias, opt for these instead to reduce the complexity and cost of manufacturing.
- Limit Controlled Impedance: If your application does not require strict impedance control, simplifying the trace design can lower production costs. Controlled impedance requires tighter tolerances during fabrication, which increases costs, so use it only when necessary for high-speed or RF designs.
- Optimize Layer Usage: Ensure that your 8-layer design efficiently utilizes the layers for signal routing, power distribution, and grounding. Avoid adding unnecessary layers, as each additional layer increases both material and manufacturing costs. By optimizing the stack-up design and making the most out of the available layers, you can achieve better cost-efficiency.
Leverage Volume Discounts
- Plan for Mass Production: If possible, consolidate orders to take advantage of the economies of scale offered by larger production runs. Ordering in bulk significantly reduces the per-unit cost, as setup costs are spread across a greater number of boards. If you foresee needing more boards in the near future, it’s often more cost-effective to place a larger order upfront.
- Prototype with Smaller Layer Counts: If you’re in the prototyping stage and your design doesn’t require the full functionality of an 8-layer PCB, consider using a simpler board with fewer layers for initial testing. This can help reduce costs during development while still allowing you to validate the basic functionality of your design.
Work with Experienced PCB Manufacturers
- Choose a Manufacturer with Proven Expertise: Working with a manufacturer that specializes in multilayer PCBs can help you avoid costly mistakes during production. An experienced manufacturer can guide you on how to optimize your design for manufacturability (DFM), potentially saving you both time and money by identifying potential issues early in the process.
- Request Design for Manufacturability (DFM) Reviews: Before finalizing your design, request a DFM review from your manufacturer. This review will help identify potential manufacturing challenges or inefficiencies in your design, such as unnecessary complexity, difficult-to-produce features, or overly tight tolerances, and suggest improvements to make the production process more cost-effective without compromising quality.
Reduce the Number of Customizations
- Standardize Board Specifications: Avoid using highly customized features unless necessary. For example, stick with standard board thicknesses, hole sizes, and surface finishes to reduce costs. Custom specifications often require additional processing steps and specialized materials, increasing both manufacturing time and cost.
Conclusion
The cost of producing an 8-layer PCB is influenced by various factors, including material selection, layer count, design complexity, and production volume. While multilayer PCBs inherently come with higher costs due to their complexity, there are several strategies you can employ to optimize costs without compromising on quality. By selecting the appropriate materials for your application, simplifying your design, leveraging volume discounts, and partnering with an experienced manufacturer, you can achieve a balance between cost-efficiency and high performance in your 8-layer PCB production.
Chapter 8
Key Design Considerations for 8-Layer PCB
When you’re designing an 8-layer PCB, there are several critical factors you need to consider to make sure it performs optimally. These include signal integrity, thermal management, power delivery, and the proper placement of vias and routing strategies. Each of these elements plays a crucial role in determining how efficient, reliable, and functional your final product will be.
Signal Integrity
Signal integrity is especially important, especially in high-speed or high-frequency applications. With 8 layers to work with, you can dedicate specific layers for signal routing and put them next to ground planes, which helps reduce cross-talk and electromagnetic interference (EMI). By keeping trace lengths short and carefully controlling impedance, you can maintain signal integrity, ensuring that your signals transmit accurately and reliably throughout the board.
Thermal Management
Thermal management is another key consideration when designing an 8-layer PCB. As you pack more components and layers into a smaller space, your board generates more heat. To prevent overheating and ensure long-term reliability, you can use techniques like thermal vias, which help transfer heat between layers, and thicker copper planes for better heat dissipation. Properly managing the thermal load ensures that your board operates within safe temperature ranges, even in high-power applications.
Power Delivery
Ensuring stable power delivery across all components is critical, particularly in complex, high-density designs. By dedicating specific layers to power and ground planes, designers can create a low-impedance path for power distribution, reducing voltage fluctuations and noise. Proper power plane placement also improves signal integrity and thermal management, as the power planes can help shield sensitive signals and distribute heat more evenly across the board.
Via Placement and Routing Strategies
Vias, which provide electrical connections between layers, are essential in 8-layer PCB design. Proper via placement is crucial to maintaining signal integrity and ensuring efficient power distribution. Designers must carefully place vias to minimize signal reflection and loss, particularly in high-speed designs. Additionally, using blind or buried vias can help save space and reduce signal interference, allowing for more efficient routing of complex circuits. Optimal routing strategies, such as differential pair routing for high-speed signals and careful planning of trace paths, help avoid signal degradation and ensure reliable operation.
Conclusion
In summary, designing an 8-layer PCB requires careful attention to signal integrity, thermal management, power delivery, and via placement. By addressing these key considerations, designers can ensure that their boards meet performance requirements while maintaining reliability and efficiency, even in complex and high-demand applications.
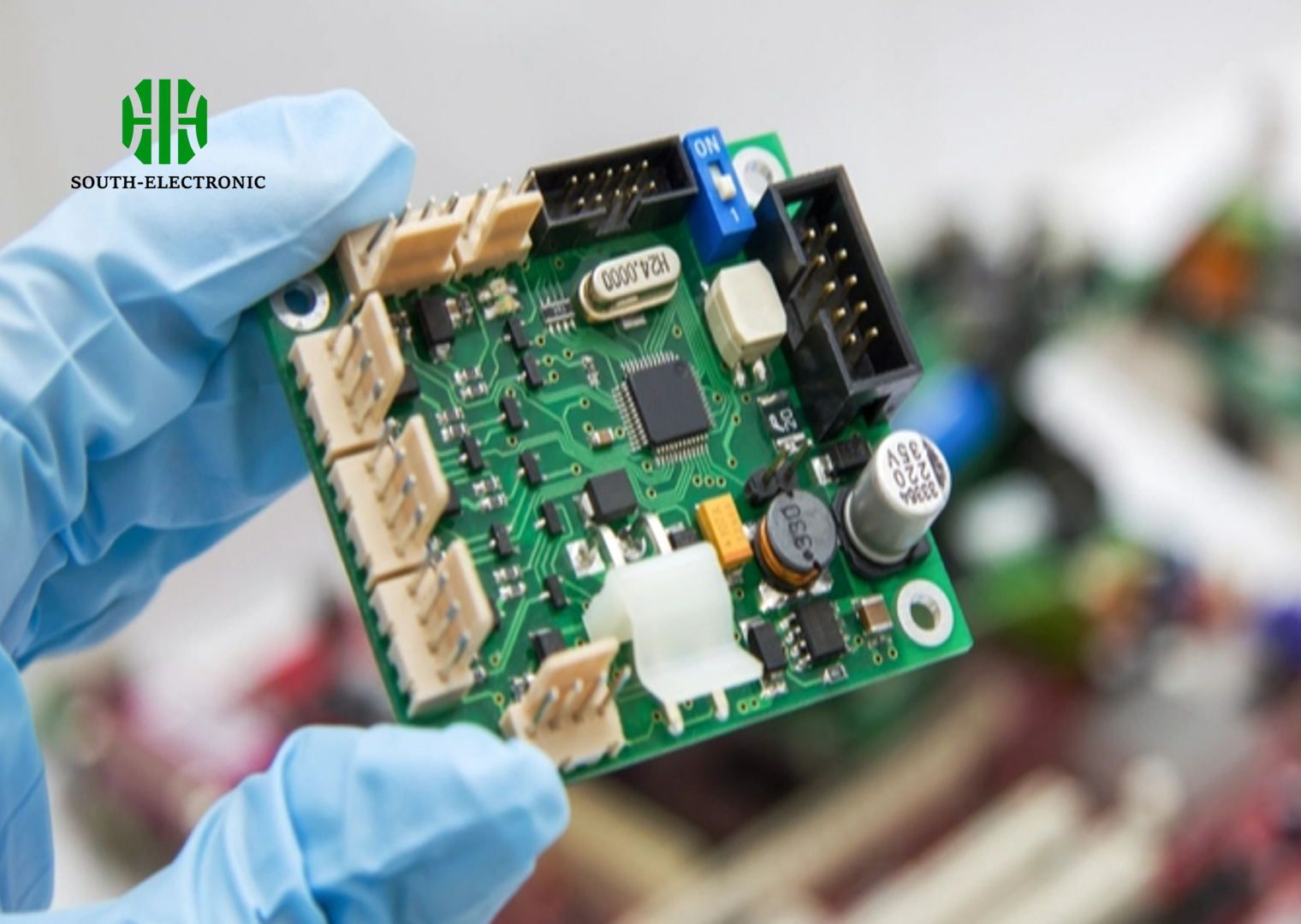
Chapter 9

Testing and Quality Assurance for 8-Layer PCB
Ensuring the quality and reliability of 8-layer PCBs requires a rigorous testing and quality assurance process. Multiple testing methods are employed to verify that the PCB meets design specifications and performs reliably in its intended application.
Common Testing Methods
Electrical Testing: This includes continuity and isolation tests to ensure that all connections are correctly made and that there are no shorts or open circuits. These tests are often performed using automated testing equipment like flying probe testers or a bed of nails to verify the integrity of the electrical pathways across the multiple layers.
Signal Testing: For high-speed and high-frequency PCBs, signal integrity testing is crucial. This involves checking the impedance of traces, assessing signal quality, and verifying that there is no excessive signal loss or interference. Signal testing ensures that the board can handle high data rates without degradation in performance.
Durability Checks: Environmental testing, such as thermal cycling and mechanical stress tests, is performed to ensure the PCB can withstand real-world conditions. These tests evaluate the PCB’s ability to operate under temperature fluctuations, humidity, and mechanical stress, ensuring long-term reliability.
Importance of Certifications
Certifications like UL, CE, and ISO are vital in establishing the quality and safety of 8-layer PCBs:
UL (Underwriters Laboratories) certification ensures that the PCB meets specific safety standards, particularly in terms of flammability and electrical performance, making it crucial for applications where safety is a priority.
CE marking indicates that the PCB complies with the health, safety, and environmental standards required for products sold within the European Economic Area (EEA), ensuring that the board meets stringent regulatory requirements.
ISO (International Organization for Standardization) certifications, such as ISO 9001, demonstrate that the manufacturer follows quality management systems, ensuring consistent production quality and adherence to industry standards.
Conclusion
Testing and quality assurance are critical to ensuring that 8-layer PCBs are both reliable and safe for use in demanding applications. Electrical testing, signal integrity checks, and durability assessments ensure that the boards function as intended, while certifications like UL, CE, and ISO guarantee that they meet recognized industry standards for performance and safety.
Chapter 10
Choosing the Right Supplier
Selecting the right supplier for your 8-layer PCB needs is critical to ensuring high-quality production, timely delivery, and excellent customer support. Several factors should be taken into consideration when evaluating potential suppliers.
Key Factors to Consider
Experience: The supplier’s experience in producing 8-layer and other multilayer PCBs is crucial. A supplier with a strong track record in manufacturing complex, high-performance boards is more likely to deliver reliable products. Look for a supplier that has a proven history in industries such as telecommunications, automotive, and medical devices, where 8-layer PCBs are commonly used.
Certifications: Ensure the supplier holds key industry certifications such as UL, ISO9001, and IATF16949 (for automotive applications). These certifications indicate that the supplier adheres to stringent quality control and safety standards. Certifications like CE are also important if your product is intended for the European market.
Customer Support: Responsive and knowledgeable customer support is essential, especially when dealing with complex PCB designs. Choose a supplier that offers clear communication, timely updates on production status, and post-sale support to address any potential issues quickly.
Delivery Speed: The ability to meet tight deadlines is often crucial in product development. Evaluate the supplier’s production capacity and track record for delivering on time. Suppliers that offer fast prototyping services or expedited production options can be particularly valuable during the early stages of product development.
How to Evaluate a Supplier’s Quality and Reliability
Request Samples or Case Studies: A reliable supplier should be able to provide examples of previous work, either through samples or case studies of similar 8-layer PCB projects. This will give you an idea of their production capabilities and the quality of their output.
Check Reviews and References: Look for reviews or testimonials from other clients who have worked with the supplier. Positive feedback from customers in your industry is a strong indicator of the supplier’s reliability and quality.
Perform a Factory Audit: If possible, visit the supplier’s facility or request a virtual tour to assess their manufacturing processes, equipment, and quality control procedures. A well-maintained and properly equipped factory is a good sign that the supplier can deliver high-quality PCBs.
Conclusion
When choosing a supplier for 8-layer PCBs, it’s essential to consider factors such as experience, certifications, customer support, and delivery speed. Evaluating these elements and reviewing samples or references will help you find a supplier that meets your quality standards and project timelines, ensuring a successful partnership and a high-performing final product.
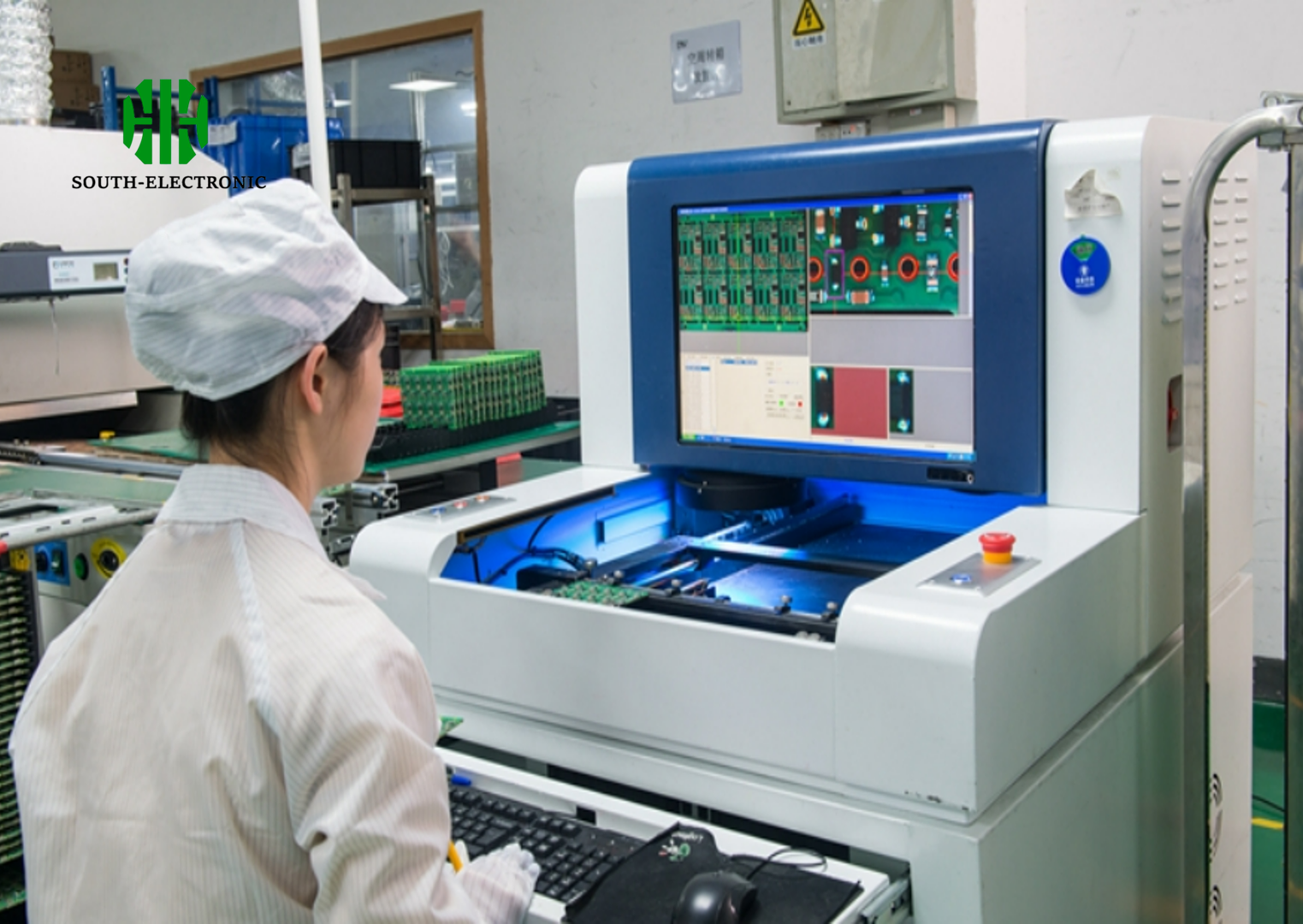
Get in touch
Where Are We?
Industrial Park, No. 438 Donghuan Road, No. 438, Shajing Donghuan Road, Bao'an District, Shenzhen, Guangdong, China
Floor 4, Zhihui Creative Building, No.2005 Xihuan Road, Shajing, Baoan District, Shenzhen, China
ROOM A1-13,FLOOR 3,YEE LIM INDUSTRIAL CENTRE 2-28 KWAI LOK STREET, KWAI CHUNG HK
service@southelectronicpcb.com
Phone : +86 400 878 3488
Send us a message
The more detailed you fill out, the faster we can move to the next step.
