الدوائر المطبوعة المرنة والثابتة
South-Electronic
اختر ساوث-إلكترونيك للحصول على جودة لا مثيل لها، وموثوقية فائقة، وقيمة استثنائية لتلبية متطلباتك في الدوائر المطبوعة. استفد من حلولنا الشاملة للدوائر المطبوعة المرنة والثابتة – من التصميم الأولي إلى الإنتاج النهائي. نحن نضمن الدقة والمتانة والامتثال الصارم لأعلى معايير الصناعة. اكتشف الفرق مع ساوث-إلكترونيك.
شريكك الموثوق لحلول الدوائر المطبوعة المرنة والثابتة!
مرحبًا بك في ساوث-إلكترونيك، وجهتك للحصول على أفضل الدوائر المطبوعة المرنة والثابتة المعروفة بتصميمها المرن وأدائها القوي.
تقدم دوائرنا المطبوعة المرنة والثابتة أداءً استثنائيًا، مما يجعلها مثالية للتطبيقات المتقدمة في البيئات الصعبة. استكشف مجموعة متنوعة من التكوينات، بما في ذلك الطبقة المزدوجة، والطبقات المتعددة، والتصاميم المخصصة المعقدة، والتي تم تصميمها بعناية لتلبية احتياجاتك الإلكترونية الفريدة. سواء كنت تبحث عن لوحات متينة للمجال الجوي أو تصاميم مبتكرة للتكنولوجيا القابلة للارتداء، ستجد الحل المثالي لدينا. استمتع بخدمة مخصصة وتسليم سريع وضمان رضا يركز على احتياجاتك. تعاون معنا لتعزيز الابتكار وتحقيق النجاح في مجالك.
لماذا تختار ساوث-إلكترونيك؟
-
قدرات التصنيع
مع ساوث-إلكترونيك، يمكنك الاستفادة من منشأتنا الحديثة المجهزة بـ 8 خطوط إنتاج.
هذا يعني أنك تستطيع الاعتماد علينا في التعامل مع كل شيء من التصميمات البسيطة إلى المعقدة للدوائر المطبوعة متعددة الطبقات، مما يمنحك المرونة للابتكار والتفوق في سوقك. -
ضمان الجودة
لا يمكنك تحمل التهاون في الجودة، ونحن كذلك.
مصنعنا الحاصل على شهادة ISO9001 يضمن أن كل منتج يمر بعمليات فحص جودة صارمة. يمكنك الوثوق بأن كل دائرة مطبوعة ستلبي أعلى معايير التميز، مما يحررك من القلق بشأن العيوب ويضمن أداءً موثوقًا. -
الخبرة والتجربة
تستحق شريكًا يفهم حقًا تعقيدات الدوائر المطبوعة المرنة والثابتة.
مع ساوث-إلكترونيك، تحصل على أكثر من عقد من الخبرة في الصناعة. نزودك برؤى لا تقدر بثمن وآخر الاتجاهات، لضمان بقاء منتجاتك في طليعة التكنولوجيا. -
الاستجابة السريعة والتسليم
مواعيدك النهائية مهمة بالنسبة لنا.
اختيارك لساوث-إلكترونيك يعني اختيار شريك ملتزم بالوفاء بالمواعيد الضيقة. تضمن عملياتنا المبسطة تصنيع دوائرك المطبوعة المرنة والثابتة بدقة وتسليمها بسرعة، مما يحافظ على سير مشاريعك بسلاسة. -
الدعم الفني مدى الحياة بعد البيع
راحتك هي أولويتنا.
عندما تختارنا، فأنت لا تشتري منتجًا فقط، بل تحصل على دعم فني مدى الحياة بعد البيع. نقف بجانبك في كل مرحلة، لضمان أن تجربتك مع ساوث-إلكترونيك تكون سلسة، موثوقة، وخالية من القلق.
مشاريع ذات صلة قمنا بها
آراء العملاء
الأسئلة الشائعة
أكثر الأسئلة شيوعًا
تشمل شهادات ساوث-إلكترونيك ISO 9001 وقوائم UL، مما يضمن أن كل دائرة مطبوعة مرنة وثابتة نقوم بإنتاجها تلبي معايير دولية صارمة، لتقديم منتجات تتميز بالموثوقية والتميز.
تمر الدوائر المطبوعة المرنة والثابتة من ساوث-إلكترونيك بعملية دقيقة لمراقبة الجودة، تشمل اختبارات متقدمة وفحوصات في كل مرحلة من مراحل الإنتاج. من خلال الاستفادة من التكنولوجيا المتقدمة والالتزام بأنظمة إدارة الجودة الصارمة، نضمن أن كل دائرة مطبوعة تعمل بأفضل أداء في تطبيقاتك.
بكل تأكيد. تتميز ساوث-إلكترونيك بتقديم حلول مخصصة لتلبية متطلبات تطبيقاتك الخاصة. نقدم تصميمات دوائر مطبوعة مرنة وثابتة مخصصة وفقًا لمواصفاتك الدقيقة، مما يضمن تكاملًا سلسًا وأداءً محسنًا ومصداقية عالية لمشاريعك.
تُمكِّن مرافق الإنتاج الواسعة لدى ساوث-إلكترونيك، والتي تضم ثمانية خطوط إنتاج متقدمة، من إدارة الطلبات الكبيرة والمعقدة بكفاءة. نحن مجهزون بالكامل لتوسيع الإنتاج لتلبية متطلباتك دون المساومة على الجودة، مما يضمن التسليم في الوقت المناسب ورضاك التام عن جميع مشاريعك.
مع عقود من الخبرة في تصنيع الدوائر المطبوعة المرنة والثابتة، تمزج ساوث-إلكترونيك بين الخبرة المتعمقة والممارسات المبتكرة. يعكس تواجدنا الطويل في الصناعة التزامنا بالتحسين المستمر وقدرتنا على التكيف مع التطورات التكنولوجية، مما يضمن تقديم حلول عالية الجودة تلبي احتياجاتك.
توفر ساوث-إلكترونيك دعمًا فنيًا شاملاً وخدمات ما بعد البيع القوية. يلتزم فريقنا المتخصص من الخبراء بتقديم الإرشادات اللازمة لتعظيم فعالية الدوائر المطبوعة المرنة والثابتة الخاصة بك. بدءًا من الاستشارة الأولية وحتى المساعدة ما بعد البيع، نضمن حصولك على الدعم اللازم لتحقيق التكامل السلس والأداء الأمثل.
أرسل لنا رسالة
كلما كانت التفاصيل أكثر دقة، كلما تمكنا من المضي قدمًا إلى الخطوة التالية أسرع.
الدليل الشامل للدوائر المطبوعة المرنة والثابتة
الفهرس
سانبتر 1
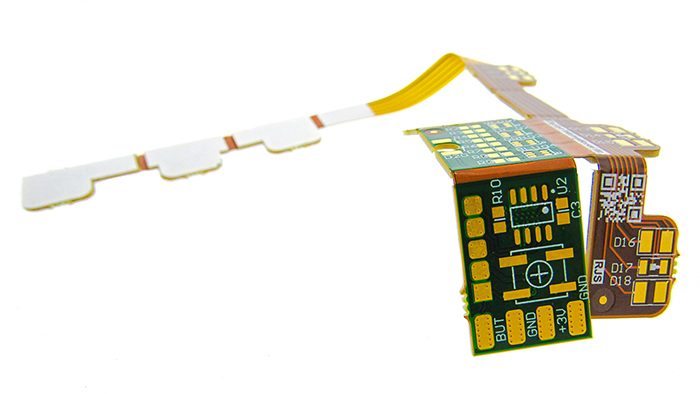
مقدمة عن الدوائر المطبوعة المرنة والثابتة
ما هي الدوائر المطبوعة المرنة والثابتة؟
تتكون الدوائر المطبوعة المرنة والثابتة من طبقات متعددة من الركائز المرنة المرتبطة بلوحة أو أكثر صلبة. يتيح هذا البناء الفريد تحقيق تكوينات معقدة ومدمجة لا يمكن للوحات الدوائر المطبوعة التقليدية تحقيقها. تُمكِّن الطبقات المرنة من الانحناء والطي الديناميكي، مما يوفر لمهندسي التصميم القدرة على تركيب الدوائر في المساحات الضيقة دون التأثير على الأداء الإلكتروني.
تتجاوز أهمية الدوائر المطبوعة المرنة والثابتة الفوائد الهيكلية والميكانيكية. فهي توفر مقاومة محسنة للاهتزازات والضغوط الميكانيكية، مما يجعلها خيارًا مثاليًا للتطبيقات في البيئات الصعبة مثل صناعات الطيران، والأجهزة الطبية، وصناعة السيارات. كما أن قدرتها على تقليل الحاجة إلى الموصلات والواجهات تعزز موثوقية الإشارة وتقلل من مخاطر مشكلات الاتصال الشائعة التي توجد في تجميعات الدوائر المطبوعة التقليدية. ومع استمرار تطور الإلكترونيات، يصبح دور الدوائر المطبوعة المرنة والثابتة أكثر أهمية في دفع حدود قدرات الأجهزة.
سانبتر 2
فوائد استخدام الدوائر المطبوعة المرنة والثابتة
تقدم الدوائر المطبوعة المرنة والثابتة مجموعة من المزايا المقنعة التي تلبي الاحتياجات المتغيرة باستمرار لتصميم الإلكترونيات الحديث. من خلال الجمع بين مزايا تقنيات الدوائر الصلبة والمرنة، توفر حلولًا مبتكرة وعملية. فيما يلي بعض الفوائد الرئيسية:
تعزيز الاستقرار الميكانيكي والمرونة
من أبرز فوائد الدوائر المطبوعة المرنة والثابتة هي قدرتها على تحمل مجموعة واسعة من الضغوط الميكانيكية. تُمكّن الطبقات المرنة الدائرة من الانحناء والالتواء دون الإضرار بالمكونات الإلكترونية، وهو أمر مفيد بشكل خاص في التطبيقات التي تتسم بالحركة والاهتزاز. توفر هذه المرونة أيضًا إمكانية تكوينات التجميع ثلاثية الأبعاد الأكثر تعقيدًا، مما يؤدي إلى حرية تصميم وكفاءة أكبر.تخفيض الحجم والوزن
تلعب الدوائر المطبوعة المرنة والثابتة دورًا حيويًا في تحقيق أجهزة إلكترونية أكثر إحكامًا وخفة وزنًا. من خلال التخلص من الحاجة إلى الموصلات والكابلات بين الأقسام الصلبة المنفصلة، تقلل هذه الدوائر من الحجم والوزن الإجمالي المطلوبين للدوائر. يُعد هذا التخفيض أمرًا حاسمًا في صناعات مثل الطيران والإلكترونيات الاستهلاكية، حيث تُعتبر كل جرام وكل مساحة ذات قيمة كبيرة.زيادة الموثوقية والمتانة
يقلل دمج الطبقات الصلبة والمرنة في لوحة دائرة واحدة من الحاجة إلى نقاط اللحام والموصلات، والتي غالبًا ما تكون نقاط فشل في الدوائر التقليدية. يعزز هذا الحل الموحد الموثوقية العامة للجهاز من خلال تقليل نقاط الفشل المحتملة، مما يؤدي إلى إطالة عمر الجهاز وتقليل احتياجات الصيانة.تبسيط التجميع والاتصال
مع عدد أقل من التوصيلات والمكونات اللازمة لربط اللوحات المتعددة، تبسط الدوائر المطبوعة المرنة والثابتة عملية التجميع. لا يقلل هذا من مخاطر الأخطاء أثناء التصنيع فحسب، بل يعزز أيضًا سلامة الإشارة من خلال تقليل مصادر التداخل المحتملة.أداء كهربائي متفوق
يتيح التصميم السلس للدوائر المطبوعة المرنة والثابتة تحسين التوجيه، مما يمكن أن يحسن الأداء الكهربائي. يمكن أن تؤدي مسارات التوصيل الأقصر إلى تحسين سلامة الإشارة وتقليل زمن الانتقال، مما يجعلها مثالية للتطبيقات التي تتطلب نقل بيانات عالي السرعة.الكفاءة الاقتصادية على المدى الطويل
رغم أن تكاليف الإنتاج الأولية للدوائر المطبوعة المرنة والثابتة قد تكون أعلى مقارنة بالدوائر التقليدية، إلا أن الفوائد طويلة الأمد تؤدي غالبًا إلى توفير في التكاليف. تزيد الموثوقية المحسّنة، وتقليل الحاجة إلى الموصلات، وعملية التجميع المبسطة من خفض تكاليف التصنيع والصيانة بمرور الوقت.
لقد أصبحت الدوائر المطبوعة المرنة والثابتة أداة لا غنى عنها في تصميم الإلكترونيات المتقدم، حيث تقدم فوائد تلبي الاحتياجات الحيوية لمختلف الصناعات. قدرتها على توفير المرونة والموثوقية والكفاءة تجعلها خيارًا مفضلًا للمهندسين الساعين إلى التميز في منتجاتهم المبتكرة.
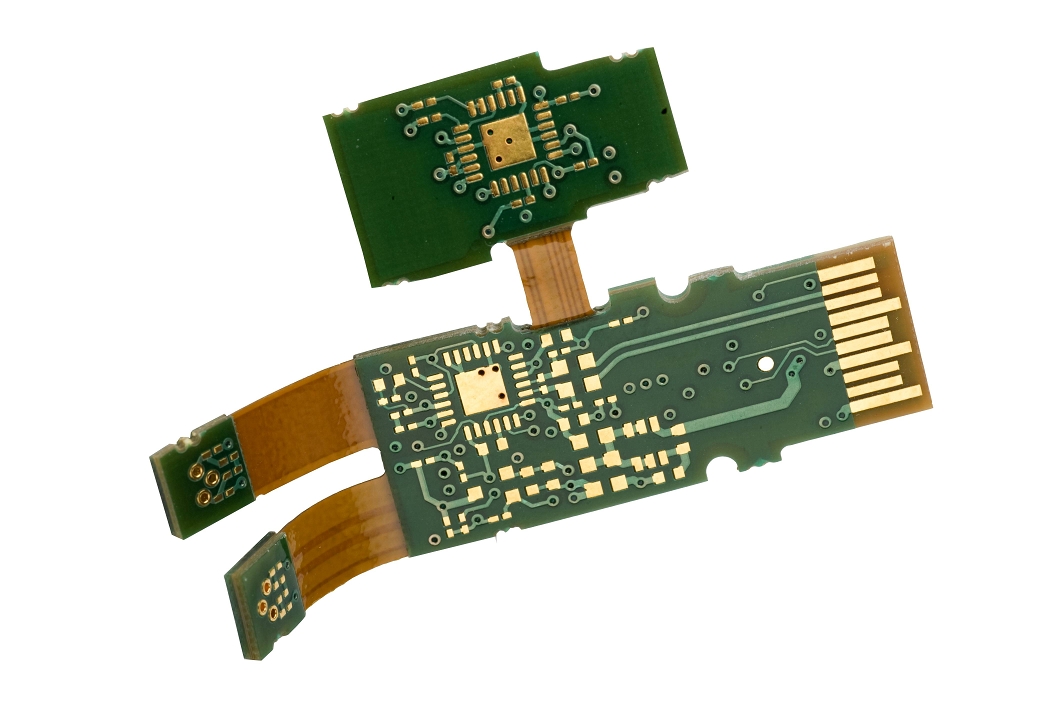
سانبتر 3
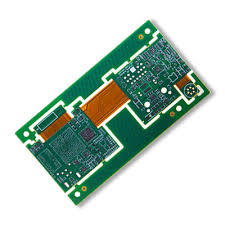
اعتبارات تصميم الدوائر المطبوعة المرنة والثابتة
يتطلب تصميم الدوائر المطبوعة المرنة والثابتة تخطيطًا دقيقًا لاستغلال إمكانياتها الفريدة بالكامل وضمان وظيفتها وموثوقيتها المثلى. فيما يلي العوامل الرئيسية التي يجب مراعاتها أثناء عملية التصميم:
فهم متطلبات التطبيق
تتمثل الخطوة الأولى في تصميم الدوائر المطبوعة المرنة والثابتة في فهم شامل للمتطلبات المحددة للتطبيق. يشمل ذلك مراعاة الظروف البيئية، والإجهاد الميكانيكي، والأداء الكهربائي، والقيود المكانية. سيوجه الفهم الواضح لهذه المتطلبات عملية التصميم، مما يضمن أن المنتج النهائي يلبي المعايير اللازمة.تكديس الطبقات وترتيب الطبقات المرنة
تحديد التكديس الصحيح للطبقات أمر بالغ الأهمية في تصميم الدوائر المطبوعة المرنة والثابتة. يجب تحسين ترتيب الطبقات الصلبة والمرنة لتحقيق الأداء الميكانيكي والكهربائي. التوازن الصحيح بين الطبقات ضروري لتجنب الفشل الميكانيكي وضمان سلامة الإشارة. يجب أيضًا أن يأخذ المصممون في الاعتبار متطلبات الانحناء، والتأكد من وضع الطبقات المرنة لاستيعاب هذه الحركات دون فشل.متطلبات الانحناء والمرونة
واحدة من المزايا الرئيسية للدوائر المطبوعة المرنة والثابتة هي مرونتها، ولكن الانحناء المفرط قد يؤدي إلى إجهاد وأضرار محتملة. من الضروري تحديد مناطق الانحناء وضمان تقليل إجهاد الانحناء. يمكن أن تمنع استخدام نصف قطر انحناء مناسب وتلبية احتياجات الانحناء الديناميكي أو الثابت حدوث أضرار وتطيل عمر الدائرة المطبوعة.وضع المكونات والتوصيل
يعد وضع المكونات بشكل استراتيجي أمرًا أساسيًا لتحسين أداء وموثوقية الدوائر المطبوعة المرنة والثابتة. يجب أن تحتوي الأقسام الصلبة على المكونات الأثقل والموصلات، بينما يجب أن تظل المناطق المرنة خالية من المكونات للسماح بالانحناء. بالإضافة إلى ذلك، يساعد التوصيل الدقيق في الحفاظ على سلامة الإشارة وتقليل التداخل الكهرومغناطيسي.إدارة الحرارة
تعتبر إدارة الحرارة الفعالة أمرًا بالغ الأهمية في تصميم الدوائر المطبوعة المرنة والثابتة، لا سيما للتطبيقات التي تتضمن كثافات طاقة عالية. ضمان تبديد الحرارة بشكل مناسب من خلال المواد وترتيب الطبقات، وربما دمج الفتحات الحرارية أو المشتتات الحرارية، يمكن أن يمنع ارتفاع درجة الحرارة ويحافظ على الأداء.اختيار المواد
يعد اختيار المواد المناسبة لكل من الطبقات الصلبة والمرنة أمرًا أساسيًا لنجاح التصميم. تؤثر اختيارات المواد على الخصائص الكهربائية والحرارية والميكانيكية للدائرة المطبوعة. يجب على المصممين اختيار المواد التي تلبي متطلبات التطبيق المحددة والظروف البيئية.الامتثال للمعايير واللوائح
ضمان امتثال التصميم للمعايير واللوائح الصناعية ذات الصلة، والتي قد تختلف اعتمادًا على التطبيق والموقع الجغرافي. هذا الامتثال ضروري لضمان سلامة المنتج وموثوقيته وقابليته للتسويق.
من خلال مراعاة هذه الجوانب التصميمية بعناية، يمكن للمهندسين استغلال الإمكانيات الكاملة للدوائر المطبوعة المرنة والثابتة، مما يؤدي إلى حلول مبتكرة تلبي المطالب المعقدة للتطبيقات الإلكترونية الحالية والمستقبلية.
سانبتر 4
عملية تصنيع الدوائر المطبوعة المرنة والثابتة
تُعد عملية تصنيع الدوائر المطبوعة المرنة والثابتة رحلة دقيقة تتطلب الدقة والخبرة للحصول على نتائج عالية الجودة. فهم هذه الخطوات أمر أساسي لتصميم دوائر مطبوعة ليست فقط قوية ولكن أيضًا قابلة للتصنيع بكفاءة وبدون أخطاء. فيما يلي تفصيل للمراحل الأساسية في عملية التصنيع:
التصميم والتخطيط المسبق للإنتاج
تبدأ الرحلة بتصميم وتخطيط دقيق. يستخدم المهندسون أدوات برمجية متقدمة لوضع المخططات التفصيلية، وترتيب الطبقات، وتصاميم التخطيط. تشمل هذه المرحلة:- التحقق من قواعد التصميم والقيود
- تحديد متطلبات المواد والتكوينات
- إعداد ملفات CAD للإنتاج
يخضع التصميم لمراجعة وتحقق شاملين للتأكد من أنه يلبي جميع المواصفات ومعايير الأداء.
اختيار المواد والتحضير
يُعد اختيار المواد المناسبة لكل من الأقسام الصلبة والمرنة أمرًا بالغ الأهمية. تشمل المواد الشائعة FR4 للألواح الصلبة والبولييميد للدوائر المرنة. يتم تحضير هذه المواد وقصها وفقًا لمواصفات التصميم، مع مراعاة عوامل مثل مقاومة الحرارة والخصائص العازلة والمرونة.تصنيع الطبقات
يتم تصنيع الطبقات الصلبة والمرنة بشكل فردي:- الطبقات المرنة: يتم تغليف ألواح البولييميد برقائق النحاس، ثم يتم نقشها للكشف عن نمط الدائرة المطلوب.
- الطبقات الصلبة: تشمل هذه العملية طلاء النحاس، وتطبيق الطبقة الحساسة للضوء، والتعريض، والتطوير، والنقش لإنشاء أنماط الدوائر، تمامًا مثل تصنيع الدوائر التقليدية.
التصفيح والربط
بمجرد تصنيع الطبقات الفردية، يتم تصفيحها معًا بدقة. تشمل هذه العملية:- ترتيب الطبقات بالترتيب والتسلسل الصحيح
- استخدام المواد اللاصقة وأفلام الربط لتثبيت الطبقات الصلبة والمرنة
- تطبيق الحرارة والضغط لتصفيح الرزمة بشكل آمن مع تجنب أي انحراف أو فجوات هوائية
الحفر والطلاء
تُستخدم الثقوب المحفورة كفتحات وعناصر تثبيت، مما يتيح التوصيلات الكهربائية بين الطبقات. بعد الحفر، يتم طلاء هذه الثقوب بمادة موصلة، عادة النحاس، لضمان الاتصال الكهربائي الموثوق عبر الدائرة المطبوعة.إضافة القناع اللحامي والتشطيبات السطحية
يتم تطبيق قناع لحام لحماية الدائرة وتحديد نقاط اللحام. يتبع ذلك إضافة تشطيبات سطحية مثل ENIG (نيكل غير كهربائي – ذهب بالانغماس) لتعزيز اللحام وحماية الدائرة من الأكسدة.الاختبار وفحص الجودة
تُجرى اختبارات صارمة وفحوصات للتأكد من أن الدائرة المطبوعة تلبي جميع المواصفات:- الاختبار الكهربائي: يتحقق من استمرارية الدائرة والعزل.
- الفحص البصري: يتحقق من العيوب المادية والعيوب التجميلية.
- الاختبار الوظيفي: يختبر الدائرة المطبوعة في ظروف حقيقية محاكية.
القطع والتجميع النهائي
يتم قص الشكل النهائي للدائرة المطبوعة باستخدام أدوات التوجيه أو الليزر للحصول على أبعاد دقيقة. ثم يتم تجميع أي موصلات أو مكونات إضافية على اللوحة وفقًا للتصميم.
تُعد عملية تصنيع الدوائر المطبوعة المرنة والثابتة عملية معقدة تتطلب تقنية متقدمة وخبرة ماهرة. يجب تنفيذ كل خطوة بدقة لضمان أن تكون الدوائر المطبوعة الناتجة قادرة على الأداء العالي والموثوقية في تطبيقاتها المخصصة.
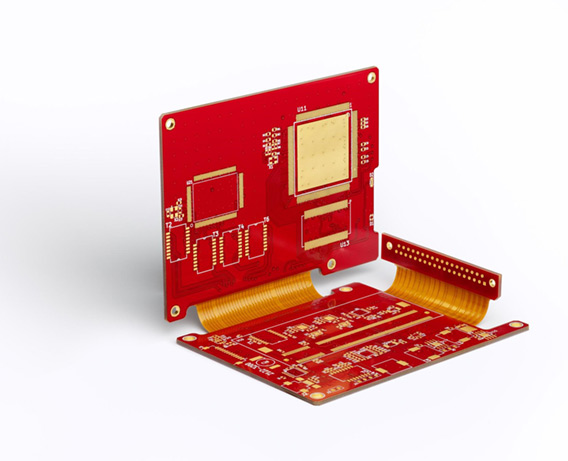
سانبتر 5

تطبيقات الدوائر المطبوعة المرنة والثابتة
أصبحت الدوائر المطبوعة المرنة والثابتة ضرورية في الإلكترونيات الحديثة، بفضل تنوعها وموثوقيتها. يمكّنها مزيجها الفريد من المكونات الصلبة والمرنة من التميز عبر مجموعة واسعة من الصناعات والمجالات التكنولوجية. فيما يلي بعض المجالات الرئيسية التي تتألق فيها الدوائر المطبوعة المرنة والثابتة:
قطاع الطيران والدفاع
يتطلب قطاع الطيران والدفاع إلكترونيات قادرة على تحمل الظروف القاسية، مثل درجات الحرارة العالية، والاهتزازات الشديدة، والضغط الكبير. تتميز الدوائر المطبوعة المرنة والثابتة في:- أنظمة الطيران
- الأقمار الصناعية والمعدات الفضائية
- أجهزة الاتصالات العسكرية
- أنظمة الملاحة والتحكم
تجعل قدرتها على التحمل في البيئات الصعبة، مع كفاءتها في الوزن والمساحة، منها خيارًا مميزًا.
الأجهزة الطبية
تُعد الدقة والموثوقية وصغر الحجم أمورًا حاسمة في التكنولوجيا الطبية. تلعب الدوائر المطبوعة المرنة والثابتة دورًا محوريًا في:- أنظمة التصوير التشخيصي (مثل أجهزة MRI وأجهزة التصوير المقطعي)
- أجهزة مراقبة الصحة القابلة للارتداء
- الأجهزة القابلة للزرع، مثل منظمات ضربات القلب
- الأدوات الجراحية
تساهم مرونتها وتوافقها الحيوي في تطوير أجهزة طبية مدمجة وموثوقة وآمنة.
الإلكترونيات الاستهلاكية
يشهد مجال الإلكترونيات الاستهلاكية تطورًا مستمرًا مدفوعًا بالسعي نحو أجهزة أصغر وأكثر قوة. تُسهّل الدوائر المطبوعة المرنة والثابتة الابتكارات في:- الهواتف الذكية والأجهزة اللوحية
- التكنولوجيا القابلة للارتداء، مثل الساعات الذكية وأجهزة تتبع اللياقة
- الشاشات المرنة والقابلة للطي
- الكاميرات ومعدات الصوت
تجعل قدرتها على دعم التصميمات المعقدة دون التضحية بالوظائف منها حجر الأساس لتكنولوجيا المستهلك الحديثة.
صناعة السيارات
تتطلب إلكترونيات السيارات تحمل الحركة المستمرة والبيئات الصعبة. تُعد الدوائر المطبوعة المرنة والثابتة جزءًا أساسيًا من:- أنظمة المعلومات والترفيه
- أنظمة مساعدة السائق المتقدمة (ADAS)
- أنظمة إدارة المحركات
- أجهزة الاستشعار ووحدات التحكم
يتيح متانتها وقدرتها على التكيف تلبية المتطلبات الصارمة لإلكترونيات السيارات، حيث تتحمل الاهتزازات وتغيرات درجات الحرارة بسهولة.
التطبيقات الصناعية
تعتمد الأتمتة الصناعية والروبوتات على أنظمة إلكترونية متينة وموثوقة. تُعد الدوائر المطبوعة المرنة والثابتة ضرورية في:- الأذرع الروبوتية والآلات
- أنظمة التحكم وأجهزة الاستشعار
- شبكات توزيع الطاقة
- أجهزة إنترنت الأشياء الصناعية
تُساهم قدرتها على تبسيط التجميع وتعزيز الموثوقية في البيئات الصناعية الصعبة في جعلها لا غنى عنها.
تُعد الدوائر المطبوعة المرنة والثابتة في صميم العديد من التطورات التكنولوجية، بفضل تنوعها وموثوقيتها وقدرتها على تلبية احتياجات التصميم المعقدة. مع استمرار الصناعات في دفع حدود الابتكار، سيزداد الطلب على الدوائر المطبوعة المرنة والثابتة، مما يدفع التقدم عبر العديد من المجالات بإمكاناتها الرائدة.
سانبتر 6
التحديات والاعتبارات في تصميم الدوائر المطبوعة المرنة والثابتة
على الرغم من المزايا العديدة للدوائر المطبوعة المرنة والثابتة، إلا أن تصميمها وتصنيعها يواجهان تحديات مميزة يجب إدارتها بعناية لضمان الأداء والموثوقية القصوى. فهم هذه التحديات أساسي لوضع استراتيجيات تصميم وإنتاج أكثر فعالية. فيما يلي التحديات والاعتبارات الرئيسية عند التعامل مع الدوائر المطبوعة المرنة والثابتة:
التعقيد والتكلفة
يتطلب تصميم وإنتاج الدوائر المطبوعة المرنة والثابتة مجموعة من التقنيات المتقدمة، مما يؤدي غالبًا إلى ارتفاع تكاليف التصميم والإنتاج الأولية. تحقيق التوازن بين تعقيد التصميم ومتطلبات المنتج أثناء مرحلة التصميم أمر ضروري للتحكم في النفقات. يمكن أن يساعد التعاون مع شركات تصنيع متمرسة في تقليل التكاليف مع الحفاظ على الجودة.اختيار المواد
يعد اختيار المواد المناسبة أمرًا محوريًا لأداء الدائرة المطبوعة. قد تتطلب الأجزاء الصلبة والمرنة مواد مختلفة، ويجب تقييم توافقها، أدائها الكهربائي، استقرارها الحراري، وقوتها الميكانيكية بعناية. يجب أن تتحمل المواد في الأجزاء المرنة الانحناء المتكرر دون التأثير على الوظيفة.إدارة الإجهاد الميكانيكي
تُعد إدارة الإجهاد الميكانيكي، خاصة في المناطق المرنة، أمرًا بالغ الأهمية. يجب أن يأخذ التصميم في الاعتبار نصف قطر الانحناء ودورات الانحناء لتجنب الإجهاد المفرط الذي قد يؤدي إلى فشل المكونات. تقليل عدد الثقوب الموصلة ونقاط اللحام في مناطق الانحناء أمر ضروري لتقليل تركيز الإجهاد.إدارة الحرارة
تُعد إدارة الحرارة الفعالة أمرًا حيويًا، خاصةً لأن الدوائر المطبوعة المرنة والثابتة قد تعمل في بيئات ذات طاقة ودرجة حرارة عالية. يمكن أن يؤدي ضعف إدارة الحرارة إلى تشوه الدائرة أو تلف المكونات. قد تشمل الحلول التصميمية إضافة مشتتات حرارية، وثقوب حرارية، ومواد واجهة حرارية لتبديد الحرارة بشكل فعال.متطلبات التصنيع والتجميع
يتطلب تصنيع وتجميع الدوائر المطبوعة المرنة والثابتة عمليات أكثر دقة مقارنةً بالدوائر المطبوعة الصلبة القياسية. تتطلب الهياكل المعقدة للطبقات والصفائح تقنيات تصنيع متخصصة ومشغلين ذوي مهارات عالية. عند اختيار شريك التصنيع، تأكد من أن لديهم الخبرة التقنية اللازمة للتعامل مع تحديات الإنتاج المتنوعة.التدقيق والتحقق من قواعد التصميم
نظرًا للخصائص الفريدة للدوائر المطبوعة المرنة والثابتة، يجب إيلاء عناية دقيقة أثناء تدقيق قواعد التصميم (DRC) والتحقق منها. ضمان التوافق مع المواصفات الكهربائية والميكانيكية ومعايير الموثوقية، وكذلك المعايير الصناعية ومتطلبات الشهادات، أمر بالغ الأهمية. تساعد هذه العملية في تحديد ومعالجة المشكلات المحتملة قبل الإنتاج.
من خلال معالجة هذه التحديات بشكل استباقي، يمكن للمهندسين ضمان تلبية تصاميم الدوائر المطبوعة المرنة والثابتة للمتطلبات الفنية مع تحسين التكلفة والموثوقية وقابلية التصنيع.
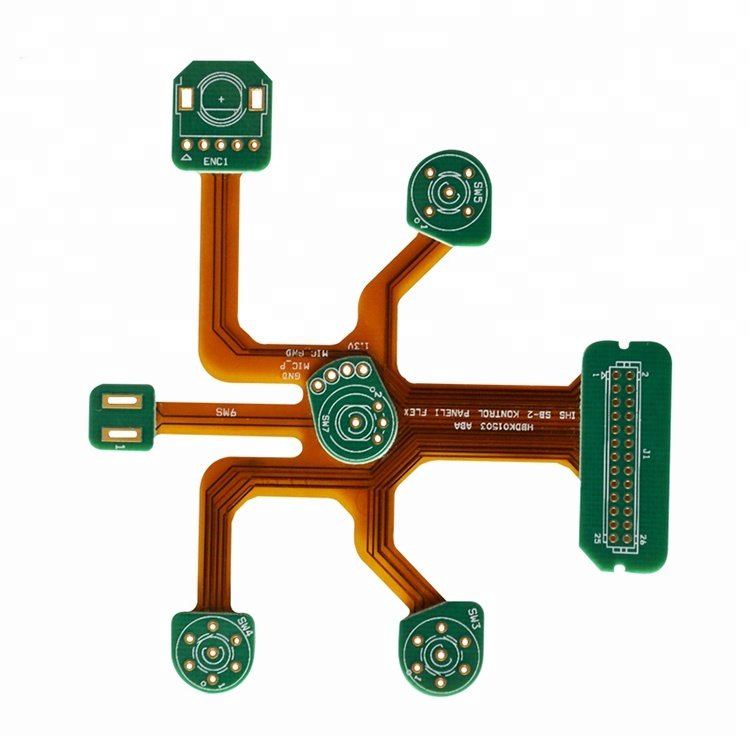
سانبتر 7

نصائح لتصميم الدوائر المطبوعة المرنة والثابتة
يتطلب تصميم الدوائر المطبوعة المرنة والثابتة تخطيطًا وتنفيذًا دقيقين للحصول على أفضل أداء منها. من خلال اتباع أفضل الممارسات، يمكن للمصممين تحسين الأداء والموثوقية وقابلية التصنيع. فيما يلي بعض النصائح الرئيسية لتصميم الدوائر المطبوعة المرنة والثابتة:
التعاون المبكر مع المصنعين
قم بإشراك المصنعين في وقت مبكر من عملية التصميم. يمكنهم مساعدتك في اتخاذ قرارات رئيسية بشأن اختيار المواد، وترتيب الطبقات، وتقنيات التصنيع. يضمن التعاون المبكر أن يكون التصميم قابلاً للتنفيذ وغالبًا ما يؤدي إلى توفير التكاليف وتحسين الأداء في المنتج النهائي.التخطيط الدقيق لترتيب الطبقات
خطط لترتيب الطبقات بعناية لتحقيق التوازن بين المرونة والصلابة. فكر في استخدام ترتيب متماثل للطبقات لتجنب الالتواء وضمان الاستقرار الميكانيكي. يجب أن يأخذ ترتيب الطبقات أيضًا في الاعتبار التحكم في المعاوقة، وإدارة الحرارة، والأداء الكهربائي.تصميم المناطق المرنة والانحناءات
صمم المناطق المرنة لتحمل الإجهاد الميكانيكي:- تأكد من وجود نصف قطر انحناء كافٍ؛ القاعدة العامة هي أن يكون نصف قطر الانحناء عشرة أضعاف سماكة القسم المرن على الأقل.
- تجنب وضع الفتحات أو نقاط اللحام أو المكونات في المناطق المرنة والانحناءات لتقليل تركيز الإجهاد.
- استخدم أشكال نحاسية منقوشة بدلاً من النحاس الصلب في المناطق المرنة لزيادة المرونة وتقليل الوزن دون التضحية بالأداء الكهربائي.
الاهتمام بتخطيط ومسار التتبع
قم بتحسين تخطيط ومسار التتبع لتحسين سلامة الإشارة والأداء الميكانيكي:- حافظ على تناسق عرض التتبع والمسافات، خاصة في مناطق الانحناء، لتجنب نقاط الإجهاد والمشكلات الكهربائية.
- وجه التتبع بشكل عمودي على خط الانحناء لتقليل الإجهاد.
- استخدم مسارات منحنية بدلاً من الزوايا بزاوية 90 درجة لتقليل الإجهاد الميكانيكي أثناء الانحناء.
اختيار المواد اللاصقة والمواد المناسبة
اختر مواد لاصقة توفر روابط قوية بين الطبقات ويمكنها تحمل الإجهادات البيئية. يجب أن تكون للمواد خصائص حرارية وميكانيكية متوافقة مع الدوائر الصلبة والمرنة للحفاظ على الأداء في ظل الظروف المختلفة.مراعاة سلامة الإشارة والتداخل الكهرومغناطيسي
ضع في اعتبارك سلامة الإشارة والتداخل الكهرومغناطيسي (EMI) أثناء مرحلة التصميم:- استخدم تقنيات التوجيه ذات المعاوقة المُتحكم فيها للإشارات عالية السرعة.
- نفذ استراتيجيات التأريض المناسبة ومستويات الأرضية لتقليل EMI.
- ضع المكثفات وفواصل الإشارات بعناية للحفاظ على سلامة الإشارة.
إجراء النماذج الأولية والاختبار
قم ببناء نماذج أولية للتحقق من افتراضات التصميم والأداء. اختبر التصميم بدقة، بما في ذلك اختبارات الإجهاد الميكانيكي، ودورات الحرارة، وتقييمات الأداء الكهربائي، لاكتشاف أي عيوب في التصميم. استخدم بيانات الاختبار لتكرار وتحسين التصميم حسب الحاجة.
من خلال اتباع هذه النصائح، يمكنك تحسين أداء وموثوقية الدوائر المطبوعة المرنة والثابتة وتسهيل عملية التصنيع. يُعد التصميم المدروس والتخطيط المفتاح لإنشاء منتج دوائر مطبوعة مرنة وثابتة قوي وناجح.
سانبتر 8
اختبار وضمان جودة الدوائر المطبوعة المرنة والثابتة
فيما يتعلق بالدوائر المطبوعة المرنة والثابتة، فإن الموثوقية والأداء هما كل شيء. لا يمكن تحمل فشل هذه اللوحات أثناء التشغيل. لذلك، فإن الاختبار وضمان الجودة (QA) هما عنصران حاسمان طوال عملية التصنيع بأكملها. لنلقِ نظرة على طرق الاختبار الرئيسية والمعايير ودور ضمان الجودة في تقديم دوائر مطبوعة مرنة وثابتة عالية الجودة.
طرق الاختبار الرئيسية والمعايير
الاختبار الكهربائي:
- اختبار الاستمرارية: يضمن أن جميع المسارات الكهربائية في الدائرة مكتملة، دون وجود انقطاعات تعيق تدفق الإشارة.
- اختبار العزل: يتحقق من عدم وجود دوائر قصيرة بين المسارات الموصلة، مما قد يؤدي إلى أخطاء في النظام.
- اختبار المعاوقة: ضروري للتطبيقات عالية التردد، حيث يضمن أن تكون المعاوقة ضمن النطاق المحدد للحفاظ على سلامة الإشارة.
الاختبار الحراري:
- اختبار الأداء الحراري: يقيّم كيفية أداء الدائرة في ظل ظروف درجات حرارة مختلفة، وهو أمر بالغ الأهمية للتطبيقات في البيئات القاسية التي تتطلب دورات حرارية.
- التصوير الحراري: يستخدم التصوير بالأشعة تحت الحمراء لاكتشاف النقاط الساخنة وضمان توزيع الحرارة بالتساوي عبر اللوحة أثناء التشغيل.
الاختبار الميكانيكي:
- اختبارات الانحناء والمرونة: تضمن أن الدوائر المطبوعة المرنة والثابتة يمكنها تحمل الانحناءات المتكررة دون تدهور الأداء.
- اختبارات الاهتزاز والصدمات: تُحاكي الظروف الواقعية، خاصة للتطبيقات في صناعات السيارات والطيران التي تتعرض لضغوط ميكانيكية عالية.
الاختبار البيئي:
- اختبار مقاومة الرطوبة: يضمن أن اللوحة تعمل جيدًا في ظروف الرطوبة العالية أو عند تعرضها للرطوبة دون تدهور أو تآكل.
- اختبار الصدمات الحرارية: يختبر قدرة اللوحة على تحمل التغيرات السريعة في درجة الحرارة، وهو أمر ضروري للبيئات ذات التغيرات الحرارية المستمرة.
الاختبار الكيميائي:
- مقاومة المواد الكيميائية: يتحقق من قدرة مواد الدائرة على مقاومة التعرض للمواد الكيميائية، وهو أمر حيوي في التطبيقات الصناعية التي قد تتعرض فيها اللوحة للمذيبات أو المواد المسببة للتآكل.
الفحص البصري والضوئي:
- تستخدم أنظمة الفحص البصري الآلي (AOI) للكشف عن العيوب مثل المكونات غير المصفوفة بشكل صحيح، أو وصلات اللحام السيئة، أو العيوب في المسارات.
الامتثال لمعايير الصناعة:
- الالتزام بمعايير مثل IPC-6013 (مواصفات التأهيل والأداء للدوائر المطبوعة المرنة) و IPC-2223 (معيار تصميم القطاعات للدوائر المطبوعة المرنة) يضمن أن اللوحات تفي بمعايير الجودة والأداء المعترف بها.
أهمية ضمان الجودة في عملية التصنيع
يعد ضمان الجودة عنصرًا أساسيًا في تصنيع الدوائر المطبوعة المرنة والثابتة. يتعلق الأمر بضمان أن كل لوحة يتم إنتاجها تفي بالمواصفات ومعايير الأداء المحددة. فيما يلي الجوانب الرئيسية لضمان الجودة في هذا السياق:
إدارة الجودة الاستباقية:
يبدأ ضمان الجودة بمراجعة تصميم شاملة. الهدف هو تحديد ومعالجة أي مشاكل محتملة في وقت مبكر. يشمل ذلك تقييمات التصميم للتصنيع (DFM) والتصميم للاختبارية (DFT) لجعل عملية الإنتاج والاختبار أكثر سلاسة.التحكم في العمليات:
يجب أن تكون هناك ضوابط قوية على العمليات في جميع مراحل التصنيع لضمان التناسق والقابلية للتكرار. يشمل ذلك مراقبة عوامل مثل درجة الحرارة والرطوبة والضغط في كل خطوة من خطوات التصنيع.إدارة جودة الموردين:
تعتمد الدوائر المطبوعة المرنة والثابتة على مواد ومكونات عالية الأداء. يجب ضمان أن الموردين يلتزمون بمعايير الجودة، وذلك من خلال مراجعات الموردين وشهادات المواد.التحسين المستمر:
يتضمن برنامج ضمان الجودة القوي دورات التغذية الراجعة وتحليل البيانات لتحفيز التحسين المستمر. يشمل ذلك مقارنة نتائج الاختبارات بالمعايير المرجعية والتحقيق في أي انحرافات لتحسين العمليات والمواد بمرور الوقت.الاختبار النهائي والفحص:
يجب أن تكون هناك اختبارات وفحوصات دقيقة في نهاية خط الإنتاج للتأكد من أن كل دائرة مطبوعة تُشحن تلبي معايير الجودة والأداء.التوثيق وإمكانية التتبع:
يجب الاحتفاظ بسجلات مفصلة لكل دفعة تصنيع لضمان إمكانية التتبع. يغطي التوثيق كل شيء بدءًا من استخدام المواد وحتى نتائج الاختبار.
باختصار، يضمن إطار عمل قوي لضمان الجودة تقديم منتج موثوق ودائم، مما يساعد على بناء السمعة والحفاظ على رضا العملاء. من خلال الاستثمار في آليات اختبار وضمان جودة شاملة، يمكن تقليل المخاطر وتعزيز أداء الدوائر المطبوعة المرنة والثابتة في مجموعة واسعة من التطبيقات.
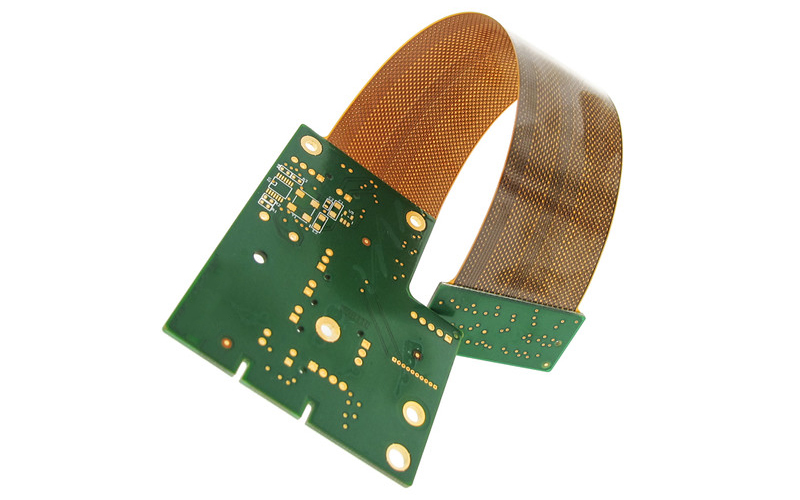
سانبتر 9
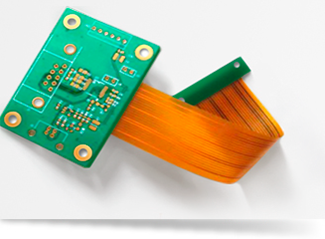
الاتجاهات المستقبلية لتقنية الدوائر المطبوعة المرنة والثابتة
مع استمرار تطور الإلكترونيات، يتم دفع حدود الممكن، وتُعد تقنية الدوائر المطبوعة المرنة والثابتة في طليعة هذه التطورات. مع سعي الصناعات للحصول على أجهزة أصغر وأكثر قوة، تتشكل مستقبل الدوائر المطبوعة المرنة والثابتة من خلال عدة اتجاهات ناشئة:
تصغير الحجم وزيادة التعقيد
يدفع الطلب على الأجهزة الأصغر والأكثر قوة نحو مزيد من التصغير. تتيح الدوائر المطبوعة المرنة والثابتة دمجًا محكمًا للمكونات، مما يسمح بوجود ميزات أكثر ضمن مساحة محدودة. ستُمكن التطورات في تقنيات التصنيع من تحقيق خطوط وأنماط أدق، مما يدعم تصميمات أكثر إحكامًا وزيادة في الوظائف.المواد المتقدمة
سيؤدي تطوير مواد جديدة ذات خصائص محسنة إلى تعزيز إمكانيات الدوائر المطبوعة المرنة والثابتة. ستوفر هذه المواد إدارة حرارية أفضل، ومرونة أكبر، وزيادة في المتانة، مما يمكن الدوائر المطبوعة من الأداء بشكل موثوق في الظروف القاسية. كما ستدعم الابتكارات في المواد الموصلة والركائز أداء كهربائيًا أعلى وكفاءة محسنة.التكامل مع تقنيات إنترنت الأشياء والأجهزة القابلة للارتداء
مع استمرار توسع إنترنت الأشياء (IoT) والتقنيات القابلة للارتداء، ستلعب الدوائر المطبوعة المرنة والثابتة دورًا حاسمًا. قدرتها على التكيف مع أشكال مختلفة ودمج مكونات متعددة يجعلها مثالية للأجهزة القابلة للارتداء، والمنسوجات الذكية، والمستشعرات المتصلة. سيؤدي هذا الاتجاه إلى تطبيقات جديدة في مراقبة الصحة، والأجهزة المنزلية الذكية، والأتمتة الصناعية.أنظمة هجينة ومتعددة اللوحات
سيشهد المستقبل زيادة في الأنظمة الهجينة التي تجمع بين الدوائر المطبوعة المرنة والثابتة وأنواع أخرى من الدوائر المطبوعة لتحسين الأداء والتكلفة. ستستفيد هذه الأنظمة متعددة اللوحات من نقاط القوة لأنواع مختلفة من اللوحات، مما يخلق حلولًا أكثر كفاءة ومخصصة للتطبيقات المعقدة في صناعات مثل الطيران، والسيارات، والاتصالات.ممارسات تصنيع مستدامة
مع تزايد المخاوف البيئية، ستتبنى الصناعة ممارسات تصنيع أكثر استدامة. يشمل ذلك استخدام مواد صديقة للبيئة، وتقليل الهدر أثناء الإنتاج، وتحسين كفاءة استخدام الطاقة. ستصبح إعادة التدوير وإدارة دورة حياة الدوائر المطبوعة المرنة والثابتة أكثر أهمية، مع التركيز على تقليل التأثير البيئي.برامج تصميم ومحاكاة متقدمة
ستحدث التطورات في برامج التصميم وأدوات المحاكاة ثورة في كيفية إنشاء المهندسين لتصميمات الدوائر المطبوعة المرنة والثابتة. ستسمح الأدوات المحسّنة بنماذج أكثر دقة للأداء الميكانيكي والكهربائي، مما يسهل تحسين التصميم وتسريع النماذج الأولية. ستعمل النماذج الافتراضية والنسخ الرقمية على تبسيط عملية التصميم بشكل أكبر، مما يقلل من وقت الوصول إلى السوق وتكاليف التطوير.
مع تطور هذه الاتجاهات، ستصبح الدوائر المطبوعة المرنة والثابتة بشكل متزايد ضرورية لتلبية الطلبات المتزايدة للإلكترونيات الحديثة. من خلال التكيف مع هذه التغيرات، يمكن للمصنعين والمصممين الاستفادة من تقنية الدوائر المطبوعة المرنة والثابتة للابتكار والتميز في مجالاتهم.
سانبتر 10
اختيار الحل الأمثل للدوائر المطبوعة المرنة والثابتة
يتطلب اختيار الحل المناسب للدوائر المطبوعة المرنة والثابتة دراسة متأنية للعديد من العوامل لضمان أن المنتج النهائي يلبي متطلبات الأداء والموثوقية والتكلفة الخاصة بك. فيما يلي الجوانب الرئيسية التي يجب مراعاتها عند اختيار الحل الأمثل للدوائر المطبوعة المرنة والثابتة لمشروعك:
تحديد متطلبات التطبيق
ابدأ بتحديد متطلبات التطبيق بوضوح. ضع في الاعتبار عوامل مثل الأداء الكهربائي، الإجهاد الميكانيكي، بيئة التشغيل، قيود المساحة، والظروف الحرارية. يساعد فهم هذه المتطلبات في تحديد الخصائص والمزايا اللازمة للدوائر المطبوعة المرنة والثابتة.اختيار المواد
اختر المواد المناسبة التي تتماشى مع احتياجات التطبيق البيئية والأداءية. ضع في اعتبارك عوامل مثل المرونة، الثبات الحراري، والخصائص العازلة. يمكن أن يؤثر اختيار الركائز، المواد اللاصقة، والمواد الموصلة بشكل كبير على متانة ووظيفة الدائرة المطبوعة.التعاون مع المصنعين ذوي الخبرة
تعاون مع مصنعين لديهم خبرة واسعة في إنتاج الدوائر المطبوعة المرنة والثابتة. يمكن لخبرتهم أن توجهك نحو اتخاذ قرارات مستنيرة فيما يتعلق بتحسين التصميم، واختيار المواد، والتقنيات التصنيعية ذات التكلفة الفعالة. يمكن للمصنع المتمرس أيضًا المساعدة في التغلب على التحديات المحتملة في عملية التصنيع.تقييم قدرات التصميم
تأكد من أن تصميمك يمكن تصنيعه بسهولة وفعالية. يشمل ذلك التأكد من جدوى التخطيط، والنظر في التحكم في المعاوقة، وتقييم نصف قطر الانحناء لضمان الاستقرار الميكانيكي. يمكن أن تساعد البرامج المتقدمة للتصميم وأدوات المحاكاة في التحقق من صحة هذه العناصر قبل الإنتاج.إجراء النماذج الأولية والاختبار
قم بإنشاء نماذج أولية لاختبار تصميمك في ظروف واقعية. تتيح النماذج الأولية تحديد المشكلات التي قد لا تكون واضحة في مرحلة التصميم ومعالجتها. قم بإجراء اختبارات ميكانيكية وحرارية وكهربائية شاملة للتأكد من أن الدائرة المطبوعة تلبي جميع معايير الأداء.النظر في دورة الحياة والصيانة
ضع في اعتبارك دورة حياة المنتج واحتياجات الصيانة المحتملة. اختر الحلول المرنة والثابتة التي توفر موثوقية طويلة الأمد لتقليل تكرار الإصلاحات أو الاستبدال. هذا مهم بشكل خاص في التطبيقات التي تكون فيها الصيانة محدودة أو مكلفة.موازنة التكلفة مع الأداء
ابحث عن التوازن بين التكلفة والأداء. على الرغم من أن التركيز على توفير التكاليف قد يكون مغريًا، فمن الضروري ضمان عدم المساس بالأداء والموثوقية، خاصة في التطبيقات الحساسة. قم بتقييم التكلفة الإجمالية للملكية على المدى الطويل لاتخاذ قرارات مالية مستنيرة.
من خلال مراعاة هذه العوامل بعناية، يمكنك اختيار حل للدوائر المطبوعة المرنة والثابتة يلبي المطالب الفنية لمشروعك ويتماشى مع قيود الميزانية والجداول الزمنية للتصنيع. يمكن للحل المختار بعناية أن يوفر مزايا كبيرة، مما يدفع النجاح والابتكار في منتجاتك الإلكترونية.
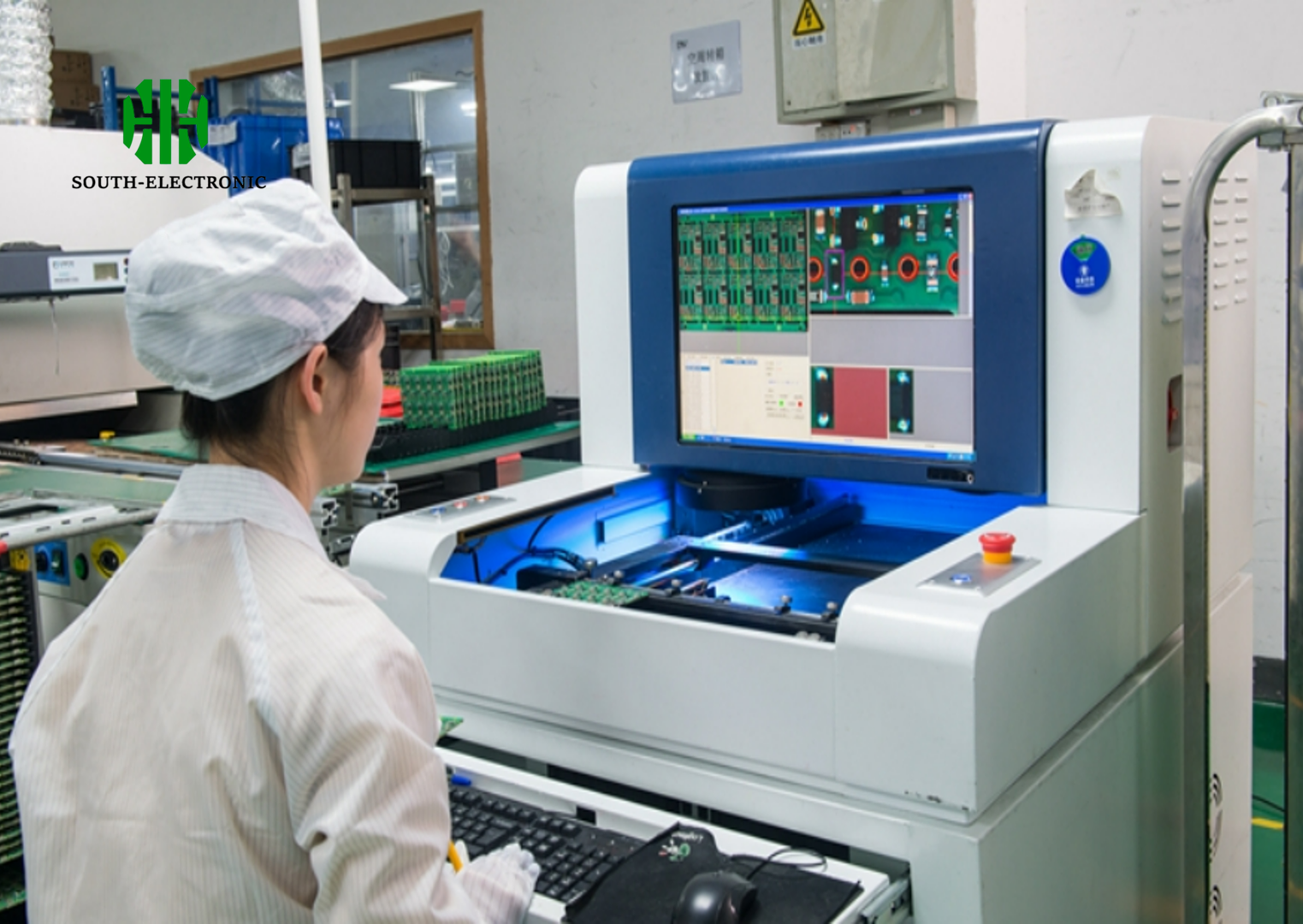
تواصل معنا
أين نحن؟
الحديقة الصناعية، رقم 438 شارع دونغ هوان، رقم 438، شاجينغ دونغ هوان، منطقة باوان، شنتشن، قوانغدونغ، الصين
الطابق 4، مبنى زهيهوي الإبداعي، رقم 2005 شارع شيهوان، شاجينغ، منطقة باوان، شنتشن، الصين
الغرفة A1-13، الطابق 3، مركز يي ليم الصناعي، 2-28 شارع كواي لوك، كواي تشونغ، هونغ كونغ
service@southelectronicpcb.com
الهاتف: +86 400 878 3488
أرسل لنا رسالة
كلما كانت التفاصيل أكثر دقة، كلما تمكنا من المضي قدمًا إلى الخطوة التالية أسرع.
