Cable Harness Manufacturing Services
South-Electronic
Choose South-Electronic for unparalleled quality, reliability, and exceptional value. Discover the difference with our comprehensive cable harness services — from initial design to final production, we guarantee precision, efficiency, and compliance with your specific needs.
Your Trusted Provider of Cable Harness Solutions
Welcome to South-Electronic, where you’ll find superior cable harness manufacturing services renowned for their meticulous construction and rapid execution.
Why Choose South-Electronic?
Select South-Electronic for our specialization in custom, high-quality cable harness manufacturing for diverse applications. Our team offers extensive experience, ensuring top-quality and exceptional service from inception to completion.
-
Unique Customization
Tailored to your specifications, built to your unique needs.
With South-Electronic, you’ll get custom cable assembly solutions that are perfectly tailored to your specific requirements — no compromise, only precision. -
High-Quality Component
Your projects deserve the best.
You can count on durable, reliable components that perform even under the most demanding conditions. -
Flexible Ordering
Enjoy the freedom of flexible minimum order quantities, starting with one piece.
Whether you need a single prototype or a full production run, we make ordering as easy as possible for you. -
Fast Turnaround
We know time is of the essence for your business.
Our streamlined process ensures that you receive your cable assemblies in a timely manner, allowing you to complete your project on time and ahead of schedule. -
Quality Assurance
Quality is our commitment to you.
Every component is thoroughly tested to ensure it meets your standards, giving you confidence in the performance of every product from day one.
Related Project We had Done
Customer Reviews
engineer
thank you, guys, the boards are really good, i am really happy to receive my boards, the components are perfect!
Operation Manager
South-Electronic is my first PCBA supplier in China. The service and quality are excellent, and the after-sales support is also very impressive. Good Job!
Common Questions
Most Popular Questions
South-Electronic makes all sorts of cable harnesses, from simple single-connector jobs to complex multi-connector, multi-conductor assemblies. They work in a bunch of industries, like cars, consumer electronics, and industry.
Yes, South-Electronic will design custom cable harnesses to fit your needs. They'll work with you to make something just for you.
How long it takes to get your cable harness depends on how complicated it is and how many you need. South-Electronic is known for being fast and efficient, so they'll get your order to you as soon as possible.
South-Electronic tests their cable harnesses all the time to make sure they're good. They're an ISO9001-certified factory, so they have to keep their quality high.
South-Electronic tests their cable harnesses all the time to make sure they're good. They're an ISO9001-certified factory, so they have to keep their quality high.
Send us a message
The more detailed you fill out, the faster we can move to the next step.
The Complete Guide For Cable Harness
Contents
Chapter 1
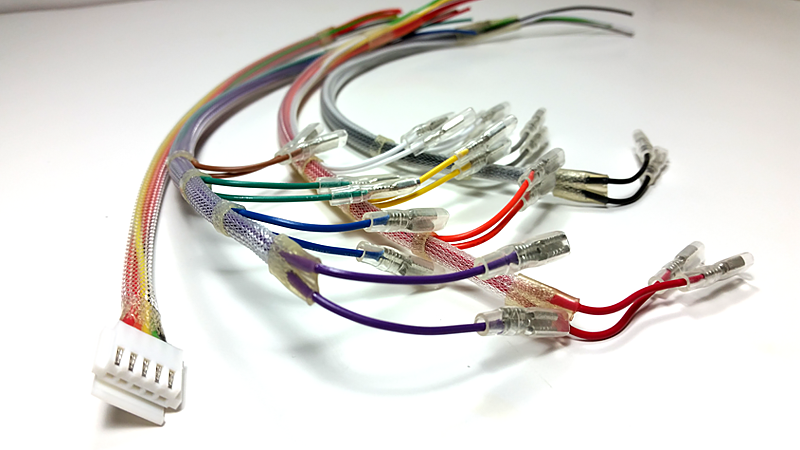
Introduction to Cable Harnesses
Wire harnesses, also known as cable harnesses, are a crucial part of modern electronic and mechanical systems. They organize and bundle electrical wires, cables, or other connections to ensure reliable distribution of power and signals in a wide range of applications. Here’s why they’re important and what they can do for you:
- Organization: Wire harnesses clean up messy wiring systems, making devices and machines look better and work better.
- Safety: By grouping cables together, wire harnesses protect them from damage caused by rubbing, shaking, and other hazards, which can reduce the risk of electrical shorts and fires.
- Durability: They add extra layers of protection to cables, often with protective sleeves or coverings, making them more resistant to things that can hurt them.
- Easy to Install and Maintain: When cables are already put together, installation is faster and less likely to have mistakes, and it’s easier to do maintenance and fix problems.
- Space and Weight: Especially in cars and airplanes, wire harnesses save space and reduce weight, which helps things work better.
Wire harnesses are used in many different industries, from cars and consumer electronics to factories and hospitals, which shows how important and useful they are.
Chapter 2
Understanding Cable Harness
A cable harness is a critical component in electronic and mechanical systems, designed to organize and secure multiple cables into a single structure. Here’s a closer look at what makes cable harnesses indispensable:
- Purpose and Function: Cable harnesses bundle multiple cables together, making them easier to manage and protecting them from damage, thus enhancing overall system performance.
- Protection and Safety: They shield cables from environmental hazards like moisture, heat, vibration, and abrasion, reducing the risk of damage or electrical failure.
- Enhanced Reliability: By minimizing movement and preventing wear, cable harnesses contribute to long-term reliability, ensuring that systems maintain consistent power and signal flow.
- Ease of Installation: Pre-organized cables in a harness simplify the installation process, saving time and reducing the likelihood of installation errors.
- Space Optimization: Cable harnesses allow for organized, compact bundling, which is essential in space-constrained environments, such as in automotive or aerospace applications.
In essence, cable harnesses are engineered to deliver both functionality and protection, making them a crucial part of countless applications across industries.

Chapter 3
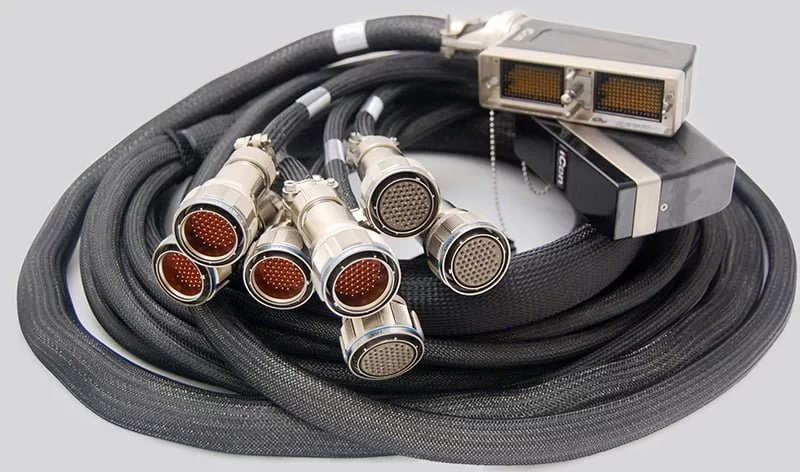
Types of Cable Harnesses
There are many different types of cable harnesses, each designed to meet the specific needs of different applications. Here’s a quick overview of some common types:
- Simple Cable Harnesses: These are basic harnesses with one connector, often used for simple connections in consumer electronics or appliances.
- Multi-Connector Harnesses: These harnesses have multiple connectors and are used in complex wiring systems where different components need to be connected, such as in cars or industrial machinery.
- High-Temperature Harnesses: These harnesses are designed to withstand extreme heat and are used in environments like car engines or industrial equipment where they need to be able to handle high temperatures.
- Shielded Cable Harnesses: These harnesses have shielding to protect against electromagnetic interference (EMI) and are used in sensitive electronics and data transmission systems.
- Flat Cable Harnesses: These harnesses have a flat design and are used in situations where there isn’t a lot of space, like in medical devices or aerospace applications.
- Custom Cable Harnesses: These harnesses are made to order and are designed to meet the specific requirements of a project, ensuring compatibility and optimal performance.
Each type of cable harness is designed to meet specific functional and environmental requirements, making them a versatile and essential component in many different industries.
Chapter 4
Design Considerations for Cable Harnesses
Designing an effective cable harness involves a careful analysis of various factors to ensure optimal performance, durability, and safety. Here are key considerations to keep in mind:
Application Requirements: Understanding the specific application is essential. Factors such as operating environment, space constraints, and functional demands will dictate the harness design. For example, harnesses used in automotive applications may require heat-resistant materials, while those in medical devices might need to be compact and sterile-compliant.
Cable and Connector Selection: Choosing the right types of cables and connectors is crucial. The gauge, insulation, and conductor material of the cables must align with the current, voltage, and signal transmission requirements. Similarly, connectors should be selected based on factors like connection stability, ease of use, and environmental protection.
Environmental Protection: The harness should be designed with adequate protection against environmental factors, such as temperature extremes, moisture, dust, and chemicals. Materials like heat-resistant insulations, protective coatings, and EMI shielding can enhance the harness’s resilience, especially in industrial or automotive environments.
Routing and Flexibility: Proper routing ensures the harness fits well within the device or equipment. Flexible routing is important for components that may experience movement or vibration, as it reduces strain on the cables and extends the lifespan of the harness. Bend radii, entry points, and secure attachment to mounting points are essential for a reliable design.
Safety and Compliance: Safety is paramount in cable harness design. Ensuring compliance with industry standards and regulations (e.g., ISO, UL) is necessary, especially for harnesses used in critical applications like aerospace or medical devices. Safety features such as secure connectors, proper insulation, and strain relief elements are important to prevent accidents.
Ease of Installation and Maintenance: A well-designed cable harness should be straightforward to install and maintain. This can be achieved by clearly labeling cables, simplifying connector placement, and ensuring that harnesses can be accessed easily for repairs or replacements. These features reduce installation time and potential errors.
Cost Efficiency: Balancing quality and cost is important. Selecting cost-effective materials without compromising performance can keep production costs low. Design optimizations, such as minimizing unnecessary components and simplifying the harness layout, can also contribute to cost efficiency.
Testing and Validation: Before finalizing a harness design, rigorous testing should be conducted. Tests for electrical continuity, insulation resistance, and durability under simulated conditions ensure the harness meets all required performance and safety standards.
By considering these factors, designers can create cable harnesses that are not only functional and durable but also tailored to the unique needs of each application, enhancing both the product’s performance and its overall reliability.
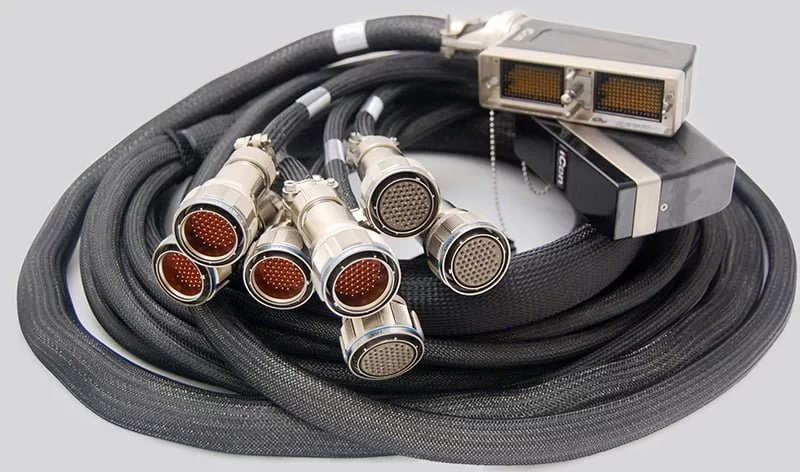
Chapter 5
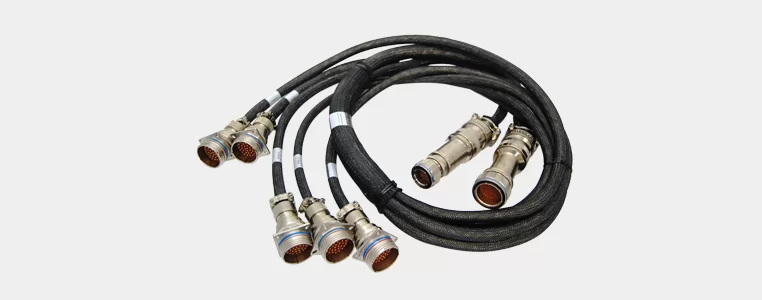
Materials Used in Cable Harness Manufacturing
The materials chosen for cable harness manufacturing are crucial to the performance, durability, and safety of the harness. Here’s a breakdown of key materials commonly used and their specific functions:
Wires and Conductors: The core of any cable harness is the conductor material, typically made of copper due to its excellent electrical conductivity and flexibility. Alternatives like aluminum may be used when weight reduction is essential, such as in aerospace applications, though they offer lower conductivity compared to copper. Silver-plated or tin-coated copper conductors are also common for enhanced corrosion resistance.
Insulation Materials: Insulation protects the conductor from external elements and prevents short circuits. Common insulation materials include:
- PVC (Polyvinyl Chloride): A cost-effective, flexible, and flame-resistant option used in low to medium voltage applications.
- Teflon (PTFE): Offers high-temperature resistance and excellent chemical resistance, making it suitable for demanding environments, such as aerospace or automotive applications.
- Silicone: Known for its flexibility and temperature tolerance, silicone is commonly used in applications that require flexibility and durability at varying temperatures.
Shielding Materials: To protect against electromagnetic interference (EMI) and radio frequency interference (RFI), cable harnesses often include shielding. Shielding materials include:
- Braided Copper or Aluminum: These are the most common options, providing excellent EMI protection while remaining flexible.
- Foil Shielding: Often used in conjunction with braided shields, foil shielding offers additional protection against interference and is lightweight, ideal for applications requiring thin, lightweight harnesses.
Outer Sheath or Jacket: The outer sheath provides an additional layer of protection, guarding against abrasion, chemicals, and environmental factors. Common outer sheath materials include:
- PVC: Used in general-purpose applications for its affordability and resistance to chemicals and moisture.
- Polyurethane (PU): Known for its durability and resistance to oil and abrasion, PU is often used in industrial settings.
- Thermoplastic Elastomer (TPE): Offers flexibility and durability in harsh environments, commonly used in automotive and outdoor applications.
Connectors and Terminals: Connectors join cables within the harness to external components, while terminals provide secure connections. Materials for connectors and terminals often include:
- Brass and Phosphor Bronze: Coated with tin, nickel, or gold to enhance conductivity and resist corrosion. These materials provide a strong electrical connection while withstanding wear and tear.
- Plastic Housings: High-quality plastics like polycarbonate or nylon are used for connector housings, offering durability, insulation, and protection from environmental elements.
Strain Relief and Fasteners: Strain relief components prevent damage to wires by absorbing the stress that may otherwise be transferred to the cable connection points. Fasteners such as zip ties, clamps, or clips are used to organize and secure the cables within the harness. Materials used include:
- Nylon: Lightweight, durable, and resistant to chemicals and heat, making it ideal for securing cables without adding significant weight.
- Silicone or Rubber Strain Reliefs: These provide flexibility and protect cables from bending or pulling damage.
Marking and Labeling Materials: Labels are essential for identifying cables within a harness for ease of installation and maintenance. Labeling materials are usually heat-resistant and durable to withstand the manufacturing process and operational environment. Common options include:
- Heat-Shrink Labels: Shrink to fit securely on cables and resist wear and tear.
- Vinyl or Polyester Labels: Offer high flexibility and durability, and are often used in high-temperature applications.
Each material plays a unique role in the functionality of a cable harness, with selections based on specific performance requirements, environmental conditions, and cost considerations. By choosing the right combination of materials, manufacturers can ensure the cable harness meets both technical and safety standards for a wide range of applications.
Chapter 6
Manufacturing Process of Cable Harnesses
The manufacturing process of cable harnesses involves several precise and carefully monitored steps to ensure quality, durability, and reliability. Here’s a detailed overview of the key stages in cable harness production:
Design and Specification:
The process begins with the design phase, where engineers and designers work closely with clients to determine the harness specifications. This includes the layout, wire types, connectors, protective materials, and labeling requirements. CAD (Computer-Aided Design) software is often used to create detailed blueprints and routing plans for accuracy.Wire Cutting and Stripping:
Once the design is finalized, wires are cut to specified lengths using automated cutting machines. Precision is critical, as any deviation can impact the harness’s functionality. After cutting, the insulation is stripped from each wire end to expose the conductor, preparing it for crimping or soldering. Automated machines are frequently used to maintain consistency and reduce the potential for human error.Terminal and Connector Attachment (Crimping and Soldering):
The exposed ends of wires are then fitted with terminals or connectors. Crimping machines apply pressure to attach terminals securely, ensuring a reliable electrical connection. In some cases, wires may be soldered to connectors or terminals instead. Quality control checks are conducted to verify the strength and integrity of each connection.Cable Assembly:
This stage involves arranging and bundling wires according to the design layout. Using jigs and fixtures helps ensure that the cables are organized properly and follow the intended path. For complex harnesses, cable ties, clamps, or protective sheathing may be added to keep cables secure and organized, preventing tangling and reducing stress on individual wires.Shielding and Protective Sleeving:
To protect the harness from environmental factors such as EMI (Electromagnetic Interference), vibration, and abrasion, shielding or protective sleeving may be applied. Braided shielding or foil shielding is added for EMI-sensitive applications, while outer sheaths, such as PVC or polyurethane, are used to protect against moisture, chemicals, and wear.Testing and Quality Control:
Each cable harness undergoes rigorous testing to ensure it meets safety and performance standards. Testing typically includes:- Continuity Testing: Verifies that electrical signals pass through each wire correctly.
- High-Voltage Testing: Checks insulation integrity to prevent electrical shorts.
- Pull and Flex Tests: Assesses mechanical durability, ensuring wires can withstand bending and stress without damage. Automated testing machines are used to identify any faults or inconsistencies, ensuring each harness is functional and safe.
Labeling and Marking:
Accurate labeling and marking of cables within the harness are essential for installation and maintenance. Heat-shrink labels, tags, or color-coded markers are often used to identify each wire’s purpose, simplifying connection and servicing in the field.Final Assembly and Packaging:
Once tested, harnesses are assembled with any additional components, such as mounting brackets or custom connectors, as specified by the client. The harness is then neatly packaged to protect it during transit. For sensitive applications, like medical or aerospace, additional protective measures may be applied, such as anti-static packaging or environmental barriers.Shipping and Delivery:
After the final quality checks and packaging, cable harnesses are prepared for shipping. Depending on client requirements, manufacturers may offer batch tracking and detailed documentation, ensuring traceability and compliance with industry standards.
Each step in the manufacturing process is integral to producing a high-quality cable harness that meets performance, safety, and durability standards. By following this structured approach, manufacturers can deliver cable harnesses tailored to the demanding needs of various industries, ensuring reliability in every application.

Chapter 7
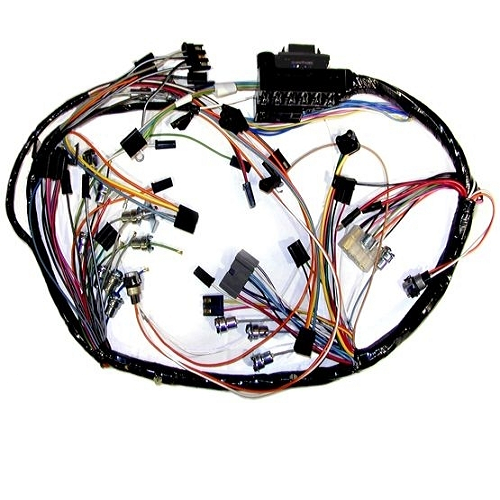
Testing and Quality Assurance for Cable Harnesses
Testing and quality assurance are critical steps in cable harness manufacturing, making sure each harness meets stringent performance and safety standards. These procedures involve multiple testing methods to verify the electrical, mechanical, and environmental reliability of the harness. Key aspects of the quality assurance process include:
- Continuity Testing: This test checks for consistent electrical connections across each wire, confirming that signals pass correctly from one end of the harness to the other without interruptions. Automated testers quickly detect any open or short circuits, helping to identify potential faults before final assembly.
- High-Voltage or Dielectric Withstand Testing: This test subjects the harness to high voltage to ensure the insulation can prevent electrical leaks or breakdowns. Dielectric withstand testing confirms that each harness can handle specified voltage levels without compromising safety, making it essential for harnesses used in high-power applications.
- Insulation Resistance Testing: This test measures the resistance of the harness’s insulation materials, ensuring they effectively prevent current from leaking between adjacent conductors. High insulation resistance is critical for safety and reliability, especially in applications where cables are in close proximity.
- Pull and Flex Testing: To verify the mechanical durability of connections, pull testing applies force to terminals and connectors, ensuring they are firmly attached and will not detach under stress. Flex testing simulates repeated bending and movement to confirm the harness can endure operational strains without damage, an essential check for harnesses used in dynamic environments.
- Environmental and Temperature Testing: Many cable harnesses are tested under simulated environmental conditions, such as extreme temperatures, moisture, and vibration, to ensure they will perform reliably in real-world applications. Harnesses designed for automotive or industrial use often undergo these tests to confirm their resilience against harsh conditions.
- EMI/RFI Shielding Effectiveness Testing: For harnesses in sensitive electronic applications, testing for electromagnetic interference (EMI) and radio frequency interference (RFI) shielding is important. This ensures that the harness can prevent unwanted signals from affecting the performance of nearby electronics.
- Visual Inspection: Trained inspectors conduct thorough visual checks to identify any physical defects, such as improper crimps, damaged insulation, or misaligned connectors. Visual inspection acts as a final quality check to ensure each harness meets visual and mechanical standards before it is shipped.
These testing procedures are integral to quality assurance, ensuring every cable harness is built to last, performs reliably, and meets the specific requirements of the client’s application. By following rigorous testing standards, manufacturers can deliver cable harnesses that stand up to demanding conditions and provide consistent performance across a wide range of industries.
Chapter 8
Common Challenges and Solutions in Cable Harness Production
Cable harness production presents several unique challenges due to the complexity and precision required. Here are some common issues faced during manufacturing, along with solutions that help maintain quality and efficiency:
Complex Design Requirements: Many cable harnesses are custom-made with complex configurations and multiple connectors, often requiring precise layouts and specialized components.
- Solution: Using CAD software and automated design tools can streamline the design process and ensure accuracy. Collaboration between designers and engineers early on helps anticipate challenges and create clear, feasible designs.
Material Selection and Sourcing: Sourcing high-quality, reliable materials like wires, connectors, and protective sheathing can be difficult, especially for specific industry requirements, such as high-temperature resistance in automotive or aerospace applications.
- Solution: Establishing strong supplier partnerships and implementing a rigorous material selection process can ensure a consistent supply of quality materials. Regular audits and quality checks on sourced materials help maintain standards.
Maintaining Quality Control: Ensuring consistent quality across all cable harnesses, especially in high-volume production, can be challenging. Variability in crimping, soldering, and assembly can impact the reliability of the finished product.
- Solution: Automating key steps, such as wire cutting, crimping, and testing, reduces human error. Additionally, implementing standardized quality control procedures and real-time monitoring systems helps maintain uniformity and catch defects early in the process.
Managing Production Time and Costs: Balancing fast turnaround times with cost efficiency can be difficult, especially for custom orders. Extended production times or resource shortages may increase costs and delay delivery.
- Solution: Lean manufacturing techniques and efficient scheduling help optimize resource usage and reduce waste. Clear communication with clients about design feasibility and lead times can also help manage expectations and streamline the production process.
Ensuring Compliance and Reliability: Cable harnesses for sectors like medical, aerospace, or automotive must meet strict regulatory standards for safety and performance. Testing and documentation requirements add to production complexity.
- Solution: Building compliance checks into each stage of production, from material selection to testing, helps ensure products meet regulatory standards. Documenting processes and results allows for traceability and simplifies audits, ensuring both reliability and compliance.
Handling Design Changes and Customization: Client-specific modifications or last-minute design changes can disrupt production schedules and introduce errors.
- Solution: Implementing flexible production systems and agile project management allows manufacturers to accommodate changes with minimal disruption. Using modular design elements where possible also helps adapt to customization without overhauling the entire design.
By addressing these challenges proactively, cable harness manufacturers can improve production efficiency, reduce errors, and deliver reliable products that meet customer specifications and regulatory standards.
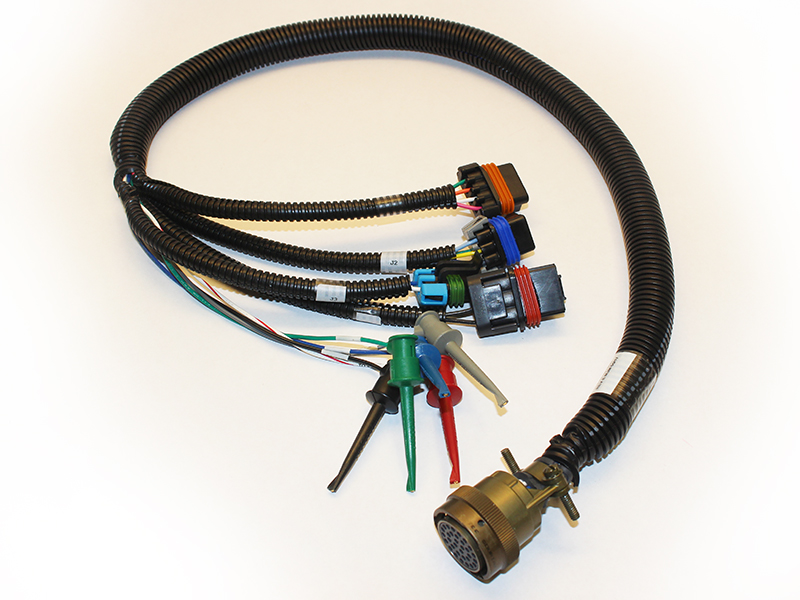
Chapter 9
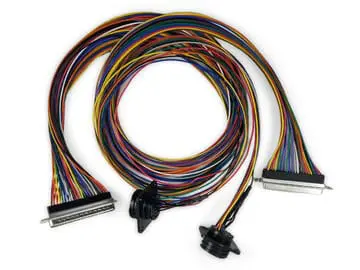
Successful Cable Harness Applications
Cable harnesses are integral to the reliable operation of many industries, providing efficient wiring solutions that enhance performance, safety, and organization. Here are some notable applications where cable harnesses contribute to successful outcomes:
Automotive Industry: Cable harnesses are used extensively in vehicles to manage complex wiring systems for everything from engine controls and lighting systems to infotainment and safety mechanisms. By organizing and protecting wiring, harnesses improve vehicle reliability and simplify assembly processes, ensuring components function smoothly under challenging conditions, such as temperature fluctuations and vibrations.
Aerospace and Defense: In aircraft and defense equipment, where performance and reliability are non-negotiable, cable harnesses help manage essential electrical connections while reducing weight and maximizing space efficiency. They withstand extreme temperatures, pressures, and vibrations, contributing to the safety and operational readiness of aerospace systems, such as navigation, communication, and weaponry.
Medical Equipment: Cable harnesses in medical devices support sensitive operations, ensuring precise connections for imaging equipment, diagnostic tools, and life-support machines. High-quality, durable harnesses are essential to prevent signal interference and ensure uninterrupted performance in equipment that directly impacts patient care.
Industrial Automation: In manufacturing and industrial machinery, cable harnesses enable efficient power distribution and control system integration. They reduce wiring complexity in automated systems, improve safety by securing connections, and provide ease of maintenance, which is essential in environments with continuous, demanding operations.
Telecommunications: In telecommunications infrastructure, cable harnesses support high-speed data transmission and reliable network performance. They organize and protect data and power cables in server racks, communication towers, and data centers, minimizing signal interference and enhancing the stability of telecom networks in all conditions.
Consumer Electronics: In devices like computers, home appliances, and entertainment systems, cable harnesses provide organized, compact wiring solutions that improve device efficiency and durability. They prevent damage to internal components, facilitate repairs, and contribute to streamlined designs that appeal to consumers.
Cable harnesses are critical across these diverse applications, offering tailored solutions that increase operational efficiency, simplify assembly, and extend product longevity. Through the successful use of cable harnesses, industries can achieve reliable performance, simplified maintenance, and enhanced safety in their equipment and products.
Chapter 10
Future Trends and Innovations in Cable Harness Technology
The cable harness industry is evolving to meet the growing demands for efficiency, miniaturization, and reliability across various sectors. Here are some of the emerging trends and innovations shaping the future of cable harness technology:
Smart and Connected Harnesses: As the Internet of Things (IoT) expands, demand for smart cable harnesses with embedded sensors is on the rise. These harnesses monitor data like temperature, humidity, and voltage, enabling predictive maintenance and real-time diagnostics. In industries such as aerospace and automotive, smart harnesses improve safety and reduce downtime by alerting operators to potential issues before they lead to failures.
Miniaturization and Lightweight Materials: With the push toward smaller, lighter devices, particularly in the automotive, aerospace, and consumer electronics sectors, manufacturers are focusing on miniaturizing cable harness components. This trend involves using smaller connectors, thinner wires, and advanced materials like aluminum and lightweight composites, reducing both weight and space requirements. Miniaturization helps improve fuel efficiency in vehicles and frees up valuable space in compact electronics.
Eco-Friendly and Sustainable Materials: Environmental sustainability is becoming a significant concern in cable harness production. Manufacturers are increasingly using recyclable and biodegradable materials, such as eco-friendly plastics and coatings, to reduce environmental impact. Additionally, new production processes aim to minimize waste and energy consumption. By adopting greener materials and practices, companies align with global environmental standards and meet consumer demand for sustainable products.
Automated Manufacturing Processes: Automation is revolutionizing cable harness manufacturing, reducing production time and improving precision. Advanced robotic systems now handle tasks like wire cutting, stripping, crimping, and assembly with minimal human intervention. This shift not only enhances quality by reducing errors but also enables scalability and cost-effectiveness, especially for high-volume production runs. As automation technology advances, cable harness production will become faster and more reliable.
Advanced Testing and Quality Control: Innovations in testing technology allow for more rigorous quality control, ensuring cable harnesses meet increasingly stringent standards. Automated testing systems now conduct real-time monitoring during production, identifying faults and verifying parameters like continuity, insulation resistance, and environmental resilience. Non-destructive testing (NDT) techniques are also improving, allowing for thorough inspection without compromising the harness integrity, which is especially valuable for critical applications like medical devices and aerospace.
Integration of Flexible and Wearable Harnesses: With the rise of wearable technology and flexible electronics, cable harnesses are evolving to become more flexible and adaptable. These harnesses use ultra-thin, flexible wiring that can be embedded within fabrics or curved surfaces without compromising performance. Such technology is particularly promising for medical wearables, fitness trackers, and flexible displays, where traditional wiring would be too rigid or bulky.
High-Speed Data Transmission Capabilities: The increase in data-intensive applications, from 5G networks to autonomous vehicles, requires cable harnesses capable of supporting high-speed data transmission with minimal interference. Innovations in shielding and connector technology are enabling harnesses to handle greater bandwidths while preventing signal loss and electromagnetic interference (EMI). Enhanced data capabilities are critical for applications that require fast, reliable data flow, such as real-time monitoring and communication in autonomous systems.
Modular and Customizable Harness Designs: As industries demand more versatile solutions, modular and customizable cable harness designs are gaining popularity. Modular harnesses allow for easier upgrades, replacements, and repairs, as sections can be swapped out without disrupting the entire system. This approach reduces downtime and enhances flexibility, making modular harnesses ideal for complex machinery, industrial automation, and even consumer electronics where customization is key.
Enhanced Durability for Extreme Environments: The need for cable harnesses that can withstand harsh environmental conditions continues to drive innovation. New materials and protective coatings are making harnesses more resistant to extreme temperatures, moisture, chemicals, and physical wear. For sectors like oil and gas, mining, and outdoor telecommunications, this enhanced durability ensures reliable performance in challenging conditions, extending the lifespan of the harness and reducing maintenance costs.
Augmented Reality (AR) in Assembly and Maintenance: AR is beginning to play a role in the assembly and maintenance of complex cable harnesses, guiding technicians through detailed wiring and connector placements with visual overlays. AR tools can reduce assembly errors and speed up troubleshooting by providing real-time instructions and diagnostic information. This technology is especially useful in industries like aerospace and defense, where cable harnesses are highly complex and assembly precision is paramount.
These trends and innovations are reshaping the cable harness industry, paving the way for more reliable, efficient, and adaptable solutions. As technology continues to evolve, cable harnesses will play an even more critical role in connecting and powering advanced systems across a wide array of applications, from autonomous vehicles to medical wearables and beyond.

Get in touch
Where Are We?
Industrial Park, No. 438 Donghuan Road, No. 438, Shajing Donghuan Road, Bao'an District, Shenzhen, Guangdong, China
Floor 4, Zhihui Creative Building, No.2005 Xihuan Road, Shajing, Baoan District, Shenzhen, China
ROOM A1-13,FLOOR 3,YEE LIM INDUSTRIAL CENTRE 2-28 KWAI LOK STREET, KWAI CHUNG HK
service@southelectronicpcb.com
Phone : +86 400 878 3488
Send us a message
The more detailed you fill out, the faster we can move to the next step.
