Double Layer PCB Supplier
South-Electronic
Go with South-Electronic for the best Double Layer PCBs that are made to order. We'll get them to you fast, we'll make sure they're perfect, and we've been doing this for over ten years. We're accurate, we're dependable, and we're cheap.
Why Choose South-Electronic?
At South-Electronic, we help you get high-quality Double Layer PCBs with fast delivery and competitive pricing. With over a decade of experience and strict quality control, you can trust us to bring your designs to life. Get your custom quote today!
-
Unique Customization
We create the perfect one-stop solution for your project.
You get flexible order quantities, tailored specifically to your needs. Every Double Layer PCB is custom-made to your exact specifications, ensuring it aligns perfectly with your project requirements. -
Fast Turnaround
Save time and keep your project on track.
With our streamlined production process, you’ll enjoy fast delivery without any compromise on quality, helping you meet tight deadlines effortlessly. -
Top-Quality Assurance
Take your project to the next level with our strict quality standards.
You can trust our PCBs, certified by ISO9001, UL, and CE, to meet the highest industry standards. Every PCB we deliver comes with a five-year warranty, ensuring you have peace of mind with free repairs for any issues that arise within that period. -
Lifetime Support
Feel confident with lifetime after-sales care.
Even after delivery, you can rely on us for ongoing support throughout the entire lifespan of your product, giving you long-term peace of mind. -
Global Shipping
Get your PCBs delivered wherever you are.
No matter where your business is located, we offer reliable global shipping, ensuring your PCBs arrive safely and on time, every time.
Related Project We had Done
Customer Reviews
engineer
thank you, guys, the boards are really good, i am really happy to receive my boards, the components are perfect!
Operation Manager
South-Electronic is my first PCBA supplier in China. The service and quality are excellent, and the after-sales support is also very impressive. Good Job!
Common Questions
Most Popular Questions
South-Electronic ensures quality through rigorous testing and strict quality control measures at every stage of production. Each PCB is inspected for durability, precision, and compliance with industry standards, utilizing certifications like ISO9001, UL, and CE to guarantee the best performance.
South-Electronic holds key certifications such as ISO9001, UL, CE, IATF16949, and ISO13485, which reflect its commitment to high-quality production processes that meet global standards in various industries.
The typical lead time for Double Layer PCB orders at South-Electronic ranges from 5 to 10 business days, depending on the complexity and order volume. Rush services are available for urgent projects.
Yes, South-Electronic is highly flexible and capable of managing both small prototype orders and large-scale production runs. Whether you need just one PCB or thousands, we offer customized solutions to meet your specific requirements.
South-Electronic provides a five-year warranty on all Double Layer PCBs, along with lifetime after-sales support. Any issues that arise within the warranty period are covered with free repairs, ensuring long-term reliability.
To place an order, you can send an email via the contact page on the South-Electronic website. Once your order is confirmed, our team will keep you updated with the progress and provide tracking information for shipping, ensuring clear communication throughout the process.
Send us a message
The more detailed you fill out, the faster we can move to the next step.
The Complete Guide For Double Layer PCB
Contents
Chapter 1

Introduction to Double Layer PCB
What’s a Double Layer PCB?
Double Layer PCBs, also known as two-layer PCBs, are printed circuit boards that have two conductive layers, one on each side of the board. These layers are separated by an insulating material, usually FR-4, which provides both electrical insulation and mechanical support. This design allows for more complex and dense circuits compared to single-layer PCBs, while remaining more cost-effective than multi-layer PCBs.
How Do Double Layer PCBs Work?
In a Double Layer PCB, electrical connections can be made through vias—tiny holes that connect the top and bottom layers. These vias allow signals to pass between the two layers, enabling more sophisticated circuit designs and reducing the overall size of the board. This setup provides greater flexibility in routing and placement of components, making Double Layer PCBs ideal for a wide variety of applications.
What’s the Difference Between Single-Layer and Double Layer PCBs?
The main difference between a single-layer PCB and a Double Layer PCB is the number of conductive layers. While a single-layer PCB only has one conductive layer for traces and components, a Double Layer PCB doubles the available space by allowing components and traces on both sides. This allows for more complex circuit paths and improved functionality without increasing the board’s size.
Chapter 2
Key Features of Double Layer PCB
Double Layer PCBs are great for many applications because they offer a lot of features. They have two conductive layers, which means they are more flexible, can hold more components, and perform better, all while being small.
More Components
Double Layer PCBs can hold more components. They have conductive layers on both sides, so you can put more stuff on them. This makes them great for complicated circuits where you don’t have a lot of space, like in smartphones and wearables.
Smaller Size
Double Layer PCBs let you put stuff on both sides, so you can make your design smaller. This is important in industries like consumer electronics and medical devices, where you want things to be small. You can get the same stuff on a Double Layer PCB as you can on a single-layer PCB, but it’s smaller.
Better Performance
The two-layer design lets you route signals better and separate power and ground planes, so your stuff works better. You can make your signals not interfere with each other and not cross over each other, so your circuits work better. This is great for high-frequency stuff and complicated digital systems.
Components on Both Sides
Double Layer PCBs let you put components on both sides, so you can put twice as much stuff on them. This means you can use the space on the board better, especially if you have a lot of components, like microcontrollers, resistors, and capacitors. You can make your layout better and make your stuff work better.
More Flexible Design
Double Layer PCBs let you design more stuff than single-layer boards. You can put traces on both sides, so your design isn’t as complicated and your signals go where they’re supposed to go. This makes it easier to make complicated circuits and meet hard technical requirements without making the board bigger.
Cheap
Double Layer PCBs are more complicated than single-layer boards, but they’re still cheap compared to multi-layer boards. You get a lot more stuff and design flexibility without having to pay for more layers. This is good for medium-complicated projects.
Double Layer PCBs have a lot of features that make them work great, like being flexible, holding more components, and working better, all while being small. This makes them great for a lot of electronic stuff.
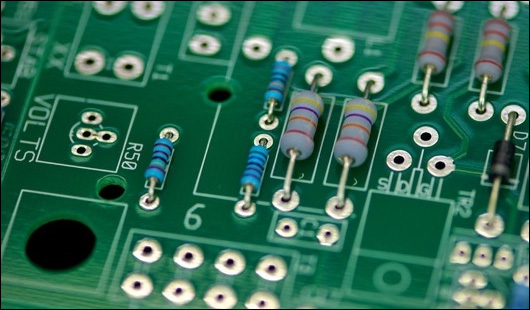
Chapter 3
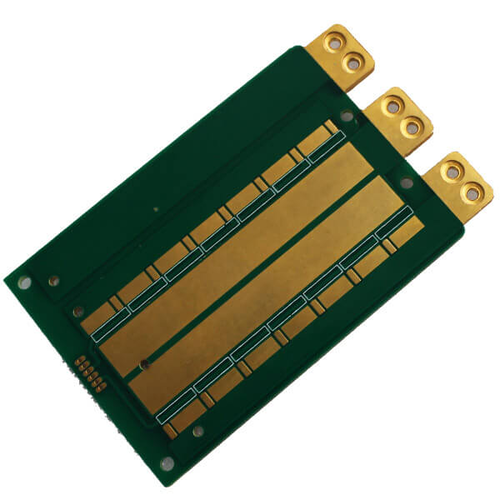
Common Applications of Double Layer PCB
Double Layer PCBs are used in a wide range of industries because they offer a good balance of complexity, performance, and cost. These versatile circuit boards can handle a variety of electronic requirements, making them a popular choice for both everyday devices and advanced systems.
Consumer Electronics
Double Layer PCBs are critical in consumer electronics, where space and functionality are key. You’ll find these PCBs in:
- Smartphones and Tablets: Supporting high-density circuits for processing, communication, and display functions.
- Laptops and Gaming Consoles: Handling complex tasks such as graphics rendering, memory management, and data processing.
- Wearable Devices: Enabling compact designs for smartwatches and fitness trackers while maintaining reliable performance.
Automotive Systems
The automotive industry uses Double Layer PCBs because they can support complex electronics in tight spaces. You’ll find them in:
- Engine Control Units (ECUs): Managing fuel injection, ignition timing, and other critical engine functions.
- Infotainment Systems: Powering multimedia interfaces, navigation systems, and hands-free communication.
- Sensor Modules: Enabling vehicle safety systems such as airbags, anti-lock braking systems (ABS), and tire pressure monitoring.
Medical Devices
Double Layer PCBs are highly reliable and compact, making them ideal for use in medical equipment where precision is crucial. You can find them in:
- Diagnostic Devices: Enabling advanced imaging, blood analysis, and vital sign monitoring.
- Portable Medical Instruments: Powering compact devices like glucose monitors and portable heart rate monitors.
- Implantable Devices: Supporting life-saving equipment such as pacemakers and defibrillators, where size and reliability are key.
Industrial Equipment
In industrial applications, Double Layer PCBs are used in systems that require durability, reliability, and efficient power management. You will find these PCBs in:
- Automation Systems: Supporting programmable logic controllers (PLCs), robotics, and control systems in factory automation.
- Power Supplies: Managing high-power applications such as motor drives, lighting systems, and energy converters.
- Instrumentation and Measurement Equipment: Enabling accurate control and monitoring in production lines and testing equipment.
Telecommunications
In the telecommunications industry, Double Layer PCBs are essential for handling data transmission, signal processing, and communication protocols. You can find them in:
- Routers and Modems: Supporting internet connectivity and data routing functions.
- Base Stations and Antennas: Enabling communication between mobile devices and network infrastructure.
- Switching Systems: Handling call routing, data transfer, and signal switching in telecom networks.
Aerospace and Defense
In aerospace and defense applications, Double Layer PCBs are chosen for their high reliability and performance in harsh environments. You will see them in:
- Avionics Systems: Supporting flight control, navigation, and communication in aircraft.
- Defense Electronics: Enabling radar systems, missile guidance, and electronic warfare systems.
Chapter 4
Materials Used in Double Layer PCB Manufacturing
The choice of materials is critical in determining the performance, durability, and cost of Double Layer PCBs. Each material serves a specific purpose, from the insulating substrate to the conductive layers. Let’s explore the key materials used in manufacturing Double Layer PCBs.
Substrate (Base Material)
The substrate is the foundational layer of the PCB, providing structural support and electrical insulation between the two conductive layers. The most commonly used substrate material is FR-4, a flame-retardant fiberglass-reinforced epoxy laminate.
- FR-4: This material is highly durable, cost-effective, and has excellent insulating properties, making it the industry standard for most Double Layer PCBs. It’s widely used in applications that require strong electrical insulation and mechanical stability.
- Other Substrates: For specialized applications, materials like CEM-1 (a composite of epoxy and paper) or polyimide (a flexible material used in high-temperature environments) may be used. These materials are chosen based on specific performance requirements such as flexibility or heat resistance.
Copper Layers
Copper is used for the conductive traces and pads on both sides of the Double Layer PCB. The thickness of the copper layer, measured in ounces per square foot, directly affects the board’s ability to handle electrical currents.
- Standard Copper Thickness: For most Double Layer PCBs, a thickness of 1 oz/ft² (35 microns) is standard, providing sufficient conductivity for typical applications.
- Thicker Copper: In high-power applications, you might opt for thicker copper, such as 2 oz/ft² or even 3 oz/ft², to improve current handling and reduce heat generation. This, however, increases the overall cost and weight of the PCB.
Solder Mask
The solder mask is a protective layer applied over the copper traces to prevent oxidation and unintended electrical contact. It also gives the PCB its characteristic color, typically green, but it can come in other colors like red, blue, or black.
- Protective Function: Solder masks are essential for protecting the copper layers from corrosion and short circuits during the soldering process. They also help improve the reliability of the PCB by reducing the risk of damage or contamination.
- Solder Mask Types: While epoxy-based solder masks are the most common due to their low cost, liquid photoimageable (LPI) solder masks offer better precision and are often used in high-quality Double Layer PCBs, where more intricate designs are required.
Silkscreen
The silkscreen is the layer that adds labels, component markings, and reference indicators to the PCB surface. It uses a non-conductive ink to print important information on the board, which aids in assembly and troubleshooting.
- Common Silkscreen Colors: White is the most commonly used silkscreen color, but you may also see black, yellow, or other contrasting colors, depending on the solder mask color.
- Material Impact: Although the silkscreen material doesn’t directly impact electrical performance, it plays a crucial role in ensuring that the PCB is assembled accurately and efficiently.
Surface Finish
The surface finish is applied to the exposed copper pads, ensuring that they remain solderable over time. The choice of surface finish impacts the board’s shelf life, solderability, and cost.
- HASL (Hot Air Solder Leveling): This is one of the most affordable surface finishes and involves coating the copper with molten solder. It’s a good option for general-purpose Double Layer PCBs but may not be suitable for fine-pitch components.
- ENIG (Electroless Nickel Immersion Gold): This surface finish provides a smooth and flat surface, making it ideal for complex designs and fine-pitch components. It is more expensive than HASL but offers better reliability and shelf life.
- Other Finishes: OSP (Organic Solderability Preservative) and Immersion Silver are also used for specific applications requiring high-quality finishes at a lower cost than ENIG.
How Material Choice Affects PCB Performance
- Electrical Performance: The choice of copper thickness and substrate directly impacts the PCB’s ability to handle high currents and withstand heat. For high-power or high-frequency applications, selecting the right combination of materials is critical.
- Durability: Materials like FR-4 offer excellent durability for most applications, but if you need a PCB for extreme environments, alternative substrates like polyimide or metal-based options might be necessary.
- Cost Considerations: While standard materials like FR-4 and 1 oz copper are cost-effective, upgrading to thicker copper or premium finishes like ENIG will increase the cost but improve performance and longevity.
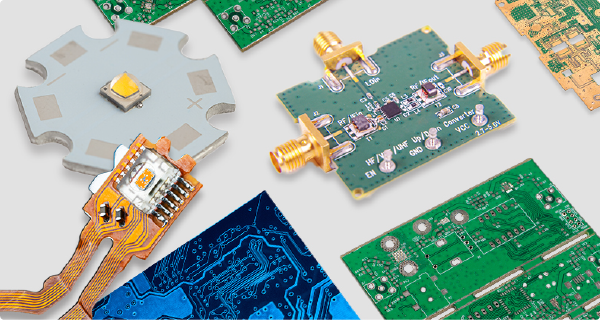
Chapter 5

Applications of Double Layer PCB
Manufacturing Double Layer PCBs involves a series of carefully controlled steps to ensure precision, durability, and functionality. Each phase is essential to delivering a high-quality PCB that meets your exact specifications. Let’s walk through the key stages of the manufacturing process.
1. Design and Layout
The process begins with the design and layout phase, where you or your engineering team creates the PCB blueprint using specialized software like Eagle, Altium, or KiCad. The design includes component placement, routing of traces, and defining the electrical connections between the two layers.
- Schematic Design: Engineers first design the circuit schematic, defining all the connections and components.
- Layout Design: The next step is creating the physical layout, ensuring efficient routing of traces and optimal placement of components.
2. Photolithography (Imaging)
Once the design is finalized, the photolithography process transfers the layout onto the PCB’s copper layers. This involves applying a photosensitive resist to the copper and exposing it to UV light through a mask that represents the circuit design.
- Applying Photoresist: A thin layer of photoresist (light-sensitive material) is applied to the copper-clad board.
- UV Exposure: The PCB is exposed to UV light through a photomask, which hardens the areas of the photoresist that correspond to the circuit traces.
3. Etching
After the photolithography step, the etching process removes the unprotected copper, leaving behind the desired circuit pattern. This step is crucial in defining the conductive paths on both sides of the board.
- Chemical Etching: The PCB is submerged in a chemical solution (usually ferric chloride) that dissolves the excess copper, leaving only the areas protected by the hardened photoresist.
- Cleaning: The remaining photoresist is then removed, revealing the etched copper traces that form the electrical pathways.
4. Drilling
Next, tiny holes known as vias are drilled into the PCB. These holes connect the top and bottom layers of the board, allowing electrical signals to pass between them. This step is critical in Double Layer PCBs, as the two layers rely on vias to complete the circuit.
- Precision Drilling: Automated drilling machines use high-speed drills to create precise holes for vias and component leads. The size and placement of these holes are based on the PCB design.
5. Plating
Once the holes are drilled, the next step is plating, where the inner walls of the vias are coated with a thin layer of copper. This ensures a solid electrical connection between the top and bottom layers.
- Copper Plating: The PCB is submerged in a chemical bath where an electroplating process deposits copper inside the drilled holes, creating conductive vias.
6. Solder Mask Application
A solder mask is then applied to protect the copper traces from oxidation and prevent short circuits during the assembly process. The solder mask also ensures that solder only adheres to the appropriate areas when components are mounted.
- Applying the Mask: The PCB is coated with a layer of solder mask, typically in green but available in other colors like red or blue.
- UV Curing: The solder mask is then hardened using UV light to form a protective barrier over the copper traces.
7. Silkscreen Printing
The next step is applying the silkscreen layer, which includes text, logos, and component labels. This helps with assembly and troubleshooting by providing a clear visual guide for component placement.
- Printing the Silkscreen: Non-conductive ink is printed onto the board, marking important information such as part numbers, reference designators, and company logos.
8. Surface Finish
Before assembly, the PCB undergoes a surface finish treatment to protect the exposed copper pads and ensure reliable soldering. The choice of surface finish—whether it’s HASL, ENIG, or another option—depends on your application and budget.
- Applying Surface Finish: The exposed copper pads are coated with a protective material to prevent oxidation and ensure good solderability during component assembly.
9. Testing and Inspection
Quality control is a critical phase in PCB manufacturing. During testing and inspection, each PCB is thoroughly checked to ensure it meets the design specifications and functions correctly.
- Electrical Testing: The PCB undergoes electrical testing to verify that all connections are working correctly and there are no short circuits or open circuits.
- Visual Inspection: Technicians check for any visible defects, such as misaligned traces, improper drilling, or incomplete etching.
10. Final Cutting and Packaging
Once the PCB passes all quality checks, the final step is cutting the board into its final shape and packaging it for shipment.
- Board Separation: The PCBs are cut out from the larger manufacturing panel using routers or lasers, forming the individual boards.
- Packaging: The boards are carefully packaged to protect them during shipping, ensuring they arrive at your location in perfect condition.
Chapter 6
Benefits of Double Layer PCB
Double Layer PCBs offer numerous advantages that make them a preferred option across various industries and applications. Their two-layer structure allows for increased design flexibility, cost efficiency, improved performance, and the ability to support more complex circuits.
1. Enhanced Design Flexibility
Double Layer PCBs give you the freedom to design more sophisticated circuits without significantly increasing the size of the board. With conductive layers on both sides, you can route more connections and place components more efficiently, making it easier to meet the demands of more complex projects. This flexibility is particularly valuable in industries like consumer electronics, automotive systems, and medical devices, where space is limited but functionality needs to be high.
2. Higher Component Density
One of the key benefits of Double Layer PCBs is their ability to handle higher component densities. You can place components on both sides of the board, effectively doubling the available space for your circuit. This leads to more compact and efficient designs, which are essential in modern applications like smartphones, wearables, and medical instruments.
3. Improved Signal Integrity
With Double Layer PCBs, you can achieve better signal integrity by dedicating one layer for power and ground planes and the other for signal routing. This separation reduces electromagnetic interference (EMI) and minimizes signal noise, resulting in more reliable and stable circuits. This is especially important in high-speed digital applications, where maintaining clean signal paths is critical for proper operation.
4. Cost Efficiency
Compared to multi-layer PCBs, Double Layer PCBs provide you with a cost-effective solution while offering more functionality than single-layer boards. They are easier to manufacture and require fewer materials than multi-layer alternatives, making them a budget-friendly option for medium-complexity projects. You can enjoy the benefits of a more capable PCB without the higher costs associated with multi-layer designs.
5. Support for Complex Circuits
Double Layer PCBs are well-suited for more intricate circuits that require multiple connections and components. The additional conductive layer allows you to design circuits with greater complexity, such as those involving microcontrollers, sensors, and power management systems, without the need for a larger or thicker board.
6. Compact Design
Double Layer PCBs enable you to achieve a compact design without sacrificing performance. By utilizing both sides of the board for components and routing, you can fit more functionality into a smaller space. This is crucial for applications like portable electronics, where every millimeter of space counts.
7. Reduced Cross-Talk
By separating signal traces across two layers, you can reduce cross-talk between adjacent traces, which often leads to signal degradation. This results in a cleaner, more precise signal flow, making Double Layer PCBs ideal for sensitive electronic applications where accuracy is paramount.
8. Efficient Heat Dissipation
Double Layer PCBs offer better heat dissipation compared to single-layer boards. With copper traces on both sides, heat can be distributed more evenly, preventing hotspots and extending the lifespan of your components. This feature is particularly useful in applications that generate a lot of heat, such as power supplies and automotive systems.
9. Versatile Applications
Thanks to their balance of functionality and cost, Double Layer PCBs are versatile enough to be used in a wide range of applications. Whether you need them for simple electronic devices or more complex industrial systems, Double Layer PCBs provide a reliable and adaptable solution.
10. Faster Prototyping and Production
Double Layer PCBs are faster to prototype and manufacture than multi-layer boards. This speed can give you a competitive edge, especially if you are working on time-sensitive projects where fast turnaround is crucial
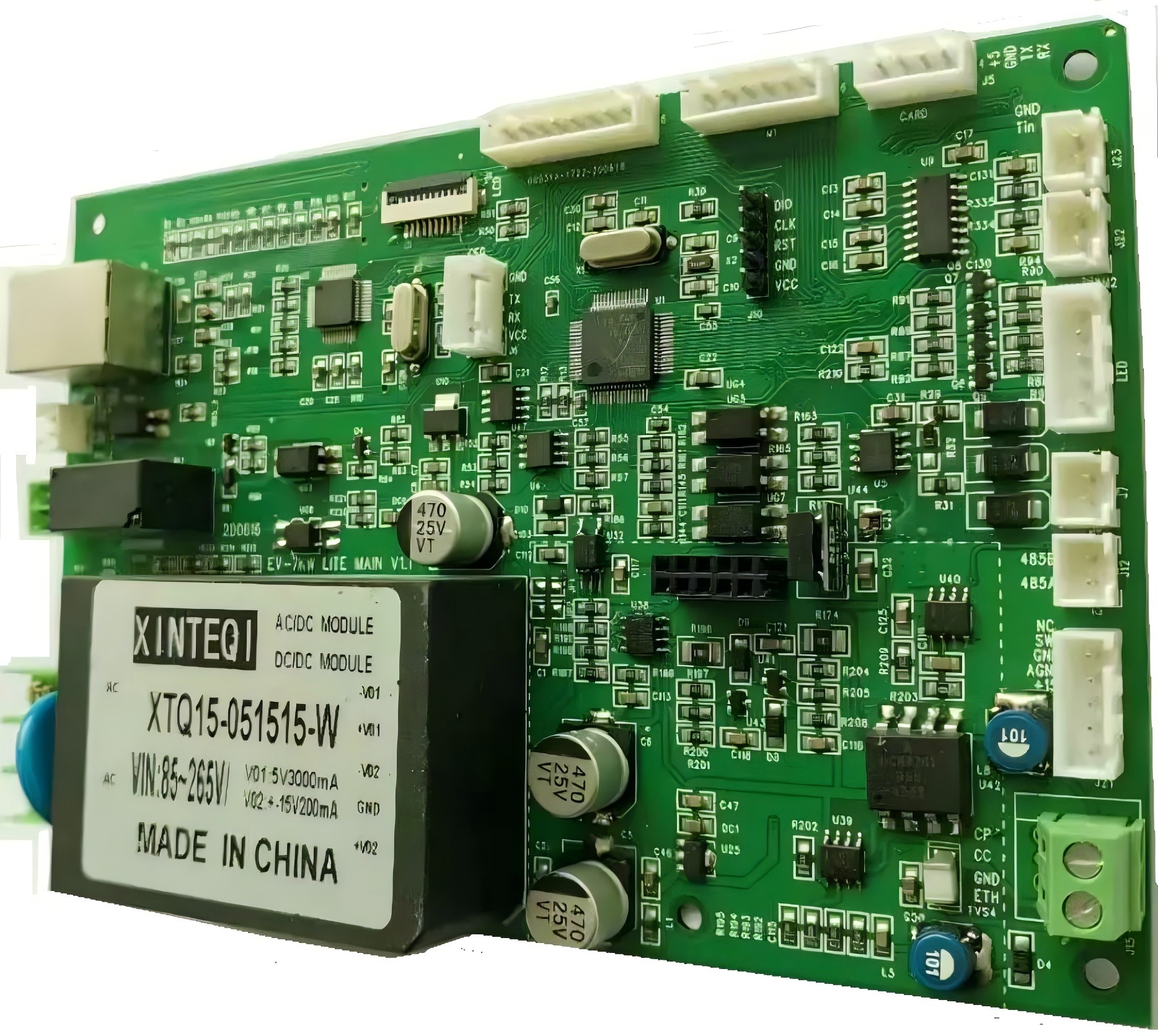
Chapter 7
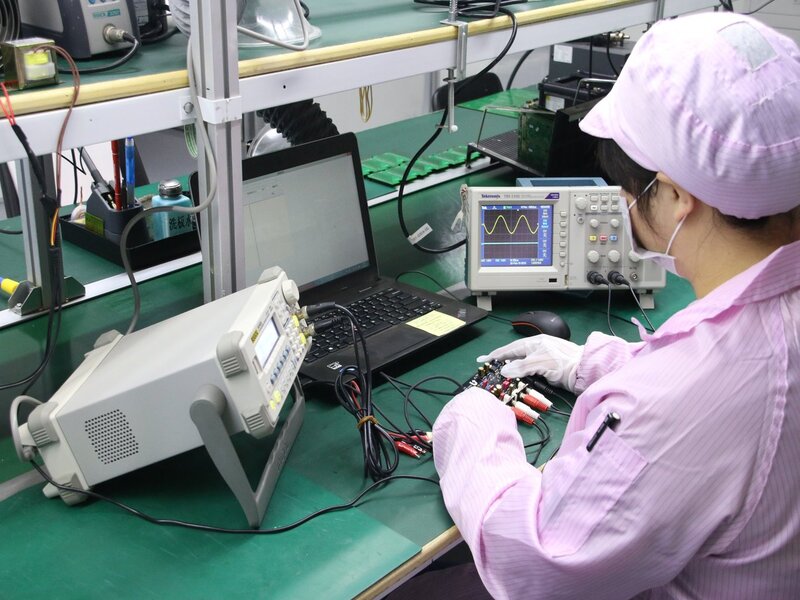
Double Layer PCB Design Tip
Designing Double Layer PCBs requires careful planning to ensure optimal performance, reliability, and manufacturability. Below are some practical tips to help you design effective Double Layer PCBs, focusing on trace layout, component placement, and minimizing noise and interference.
1. Optimize Trace Layout
The trace layout is one of the most critical aspects of Double Layer PCB design. Properly routing traces ensures signal integrity, reduces interference, and allows for efficient power distribution.
- Use Short, Direct Traces: Keep your signal traces as short and direct as possible to minimize resistance and signal delay.
- Separate Signal Types: Place high-frequency and low-frequency signals on different areas of the board or different layers to reduce interference.
- Maintain Proper Trace Widths: Ensure you use appropriate trace widths based on current-carrying requirements. Wider traces are necessary for high-current paths, while thinner traces work for signal routing.
- Avoid 90-Degree Angles: Instead of sharp 90-degree trace bends, use 45-degree angles to reduce signal reflection and improve overall signal flow.
2. Proper Component Placement
Effective component placement is key to achieving a clean, functional design. You want to ensure components are positioned in a way that minimizes trace lengths and facilitates easy assembly.
- Group Related Components: Place components that interact frequently, such as resistors and capacitors, close together. This helps reduce trace lengths and improves signal quality.
- Avoid Overcrowding: Leave enough space between components to allow for heat dissipation and to avoid electrical shorts during the soldering process.
- Plan for Accessibility: Place test points and components like connectors near the edges of the board for easier access during assembly and testing.
3. Minimize Noise and Interference
Double Layer PCBs, with their two conductive layers, can be prone to electromagnetic interference (EMI) and noise if not designed carefully. To minimize this, you can take a few key steps.
- Use Ground and Power Planes: Dedicate one layer (typically the bottom) to ground and power planes. This helps stabilize voltage levels and reduces the risk of noise affecting sensitive signals.
- Add Decoupling Capacitors: Use decoupling capacitors near power pins of ICs to filter out noise and maintain stable voltage levels.
- Shield Critical Signals: If you have sensitive analog or high-frequency signals, route them near ground planes to shield them from interference.
4. Use Vias Efficiently
Vias are crucial in Double Layer PCBs as they connect the top and bottom layers. However, excessive or poorly placed vias can cause performance issues.
- Minimize Via Usage: Use vias sparingly, as each via adds a small amount of resistance and capacitance, which can affect signal integrity.
- Strategic Via Placement: Place vias strategically to create efficient connections between layers, especially for power and ground connections, while keeping signal traces as direct as possible.
5. Plan Power Distribution
Proper power distribution is essential for ensuring the stability of your circuit. In Double Layer PCBs, you have to carefully manage how power flows across both layers.
- Create a Ground Plane: Dedicate an entire layer (or a significant portion of one) to a solid ground plane. This helps reduce noise and provides a reference voltage for all components.
- Use Wide Power Traces: For power traces, use wider traces to handle higher currents without overheating. Ensure that your power distribution network is efficient and well-routed to avoid voltage drops.
6. Choose the Right PCB Design Software
Using the right design software can streamline the entire design process and help you avoid common pitfalls. Some popular software options include:
- Eagle: Known for its user-friendly interface and powerful features, ideal for beginners and professionals alike.
- Altium Designer: Offers advanced tools for PCB design, including high-level schematic capture and simulation capabilities.
- KiCad: A free and open-source PCB design tool with a wide range of features for creating professional-quality PCBs.
7. Simulate and Test Your Design
Before moving into the production phase, you should simulate your PCB design and test it to ensure that it functions as intended.
- Use Simulation Tools: Many PCB design programs offer built-in simulation tools to test the electrical performance of your design. This helps you identify potential issues like crosstalk, signal reflection, or voltage drops.
- Perform Design Rule Checks (DRC): Always run a design rule check to ensure your design meets the manufacturing requirements, such as minimum trace width, clearance, and via size.
Chapter 8
Quality Control and Testing for Double Layer PCB
Ensuring the quality and reliability of Double Layer PCBs is crucial in delivering a product that performs to the highest standards. A thorough quality control process includes multiple testing methods to catch any potential defects early and verify that the PCB meets all design and functional requirements.
Electrical Testing
One of the most important steps in quality control is electrical testing, which ensures that the PCB functions as designed. This involves checking for continuity, short circuits, and proper connections between the top and bottom layers.
- Continuity Testing: This test verifies that all intended connections are made between traces, vias, and components. It checks whether the electrical signals flow correctly across the PCB.
- Short Circuit Testing: This process ensures that no unintended electrical paths or shorts exist between traces or components. Short circuits can cause severe malfunctions or even damage to the entire circuit.
- Impedance Testing: In some cases, especially for high-speed PCBs, impedance testing is conducted to ensure that the PCB maintains consistent electrical resistance, which is vital for proper signal transmission.
Visual Inspection
Visual inspection is another critical step in the quality control process. Technicians and automated systems visually check the PCB for physical defects that might affect performance or assembly.
- Manual Inspection: A trained technician inspects the board for any obvious flaws, such as incorrect trace routing, poor solder mask application, or missing components.
- Automated Optical Inspection (AOI): AOI uses cameras and imaging software to scan the PCB for defects that might not be visible to the naked eye. It quickly identifies issues like misaligned components, incorrect trace widths, or soldering errors, ensuring precision before the next stage.
Functional Testing
Once the PCB has passed electrical and visual inspections, functional testing ensures that the board performs as intended in real-world conditions.
- In-Circuit Testing (ICT): This method checks each individual component to ensure proper placement and functionality. It can also test for open circuits, resistance, and capacitance, giving a comprehensive overview of the PCB’s operational integrity.
- Burn-In Testing: In more critical applications, burn-in testing subjects the PCB to extended periods of electrical load and elevated temperatures. This simulates real operating conditions and identifies any early failures, ensuring long-term reliability.
X-ray Inspection
For more complex Double Layer PCBs, especially those with dense or hidden connections like buried vias, X-ray inspection can be used to check the internal layers and solder joints that aren’t visible through standard inspection methods.
- BGA Inspection: X-ray inspection is particularly useful for checking ball grid array (BGA) components, which have solder joints hidden underneath the component itself, making them impossible to inspect visually.
Automated Test Equipment (ATE)
Automated Test Equipment is used to run a series of electrical and functional tests on the PCB. This process allows for large-scale testing in a shorter time frame, ensuring high-volume production boards meet strict standards.
- Efficiency and Accuracy: ATE can run multiple tests simultaneously, checking for faults such as incorrect voltage levels, open circuits, and faulty components. This is particularly valuable in high-speed production environments where consistency is key.
Solderability Testing
Solderability testing ensures that the PCB’s pads are prepared for proper soldering during assembly. Poor soldering can lead to weak joints, which affect the board’s performance.
- Wet Balance Test: This test evaluates how well the solder adheres to the PCB’s pads, confirming that the surface finish is adequate for the assembly process.
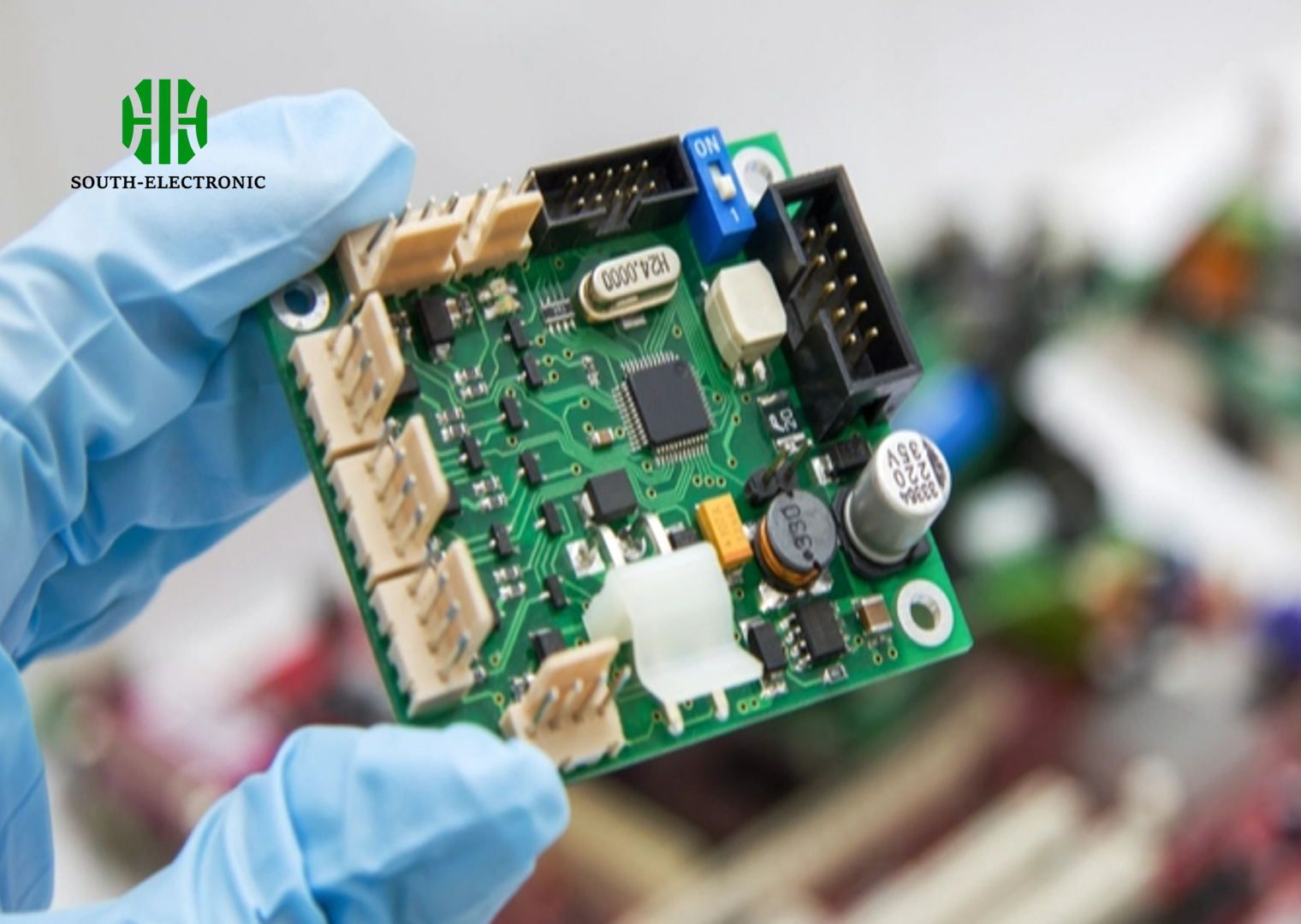
Chapter 9

Choosing the Right Double Layer PCB Supplier
Selecting the right Double Layer PCB supplier is critical to ensuring your project’s success. With so many options available, it’s important to focus on key factors that will help you find a reliable partner who can meet your specific needs. Below are some essential considerations when evaluating suppliers.
1. Certifications and Compliance
A supplier’s certifications are a strong indicator of their commitment to quality and industry standards. Look for suppliers that have internationally recognized certifications such as ISO9001, UL, CE, and IATF16949. These certifications ensure that the supplier follows strict quality management processes, which is crucial for delivering reliable, high-performance PCBs.
- Why it Matters: Certifications guarantee that the supplier’s manufacturing processes meet the necessary safety, reliability, and performance standards, reducing the risk of defects or compliance issues in your products.
2. Production Capacity and Scalability
Your PCB supplier should have the production capacity to handle your order volumes, whether you need a small batch of prototypes or large-scale production. Evaluate their production capabilities, including the number of production lines, lead times, and ability to scale up for larger orders if needed.
- Why it Matters: A supplier with the right capacity can ensure timely delivery, even as your project requirements grow. This flexibility is essential, especially if your business is scaling or requires fast turnarounds.
3. Material Quality
The quality of the materials used in manufacturing the Double Layer PCBs directly impacts their durability, performance, and longevity. Make sure the supplier uses high-grade materials, such as FR-4 substrates, premium copper layers, and reliable solder masks.
- Why it Matters: High-quality materials result in better-performing PCBs that last longer and can withstand demanding environments. Subpar materials may lead to premature failure, increased maintenance costs, and reliability issues.
4. Customer Support and Communication
Strong customer support is vital when dealing with complex PCB orders. Choose a supplier who is easy to communicate with, provides quick responses, and offers technical support throughout the design and production process. The ability to collaborate with engineers and receive updates on production progress is also important.
- Why it Matters: Clear and responsive communication helps prevent misunderstandings, speeds up the resolution of issues, and ensures the supplier aligns with your technical requirements. A supplier that offers ongoing support can help refine your design and address any challenges that arise.
5. Turnaround Time and Delivery
Timely delivery is crucial for keeping your project on schedule. Look for a supplier with a proven track record of meeting deadlines and delivering products within agreed-upon timeframes. Fast turnaround options, without compromising quality, can be a huge advantage, especially for time-sensitive projects.
- Why it Matters: Delayed deliveries can disrupt your production schedules, resulting in missed deadlines and additional costs. A reliable supplier will consistently deliver on time, keeping your operations running smoothly.
6. Flexibility and Customization
A good supplier should offer flexible solutions tailored to your specific needs. Whether you require special materials, unique designs, or small production runs, the supplier should be able to accommodate custom requests. This flexibility ensures your Double Layer PCBs meet the exact specifications of your project.
- Why it Matters: Every project is different, and a supplier that can adapt to your custom requirements will help you achieve the best possible results, even for specialized or niche applications.
Chapter 10
Future Trends in Double Layer PCB Technology
As technology advances, Double Layer PCBs continue to evolve to meet the increasing demands of modern electronics. Future trends in this area are focused on improving materials, manufacturing techniques, and expanding the range of applications. These developments will allow Double Layer PCBs to become even more versatile, efficient, and reliable.
1. Advanced Materials
In the future, we can expect to see the introduction of advanced materials that improve the performance and durability of Double Layer PCBs. High-frequency materials and substrates with better heat resistance will enable more efficient circuit designs for high-power and high-speed applications. The use of environmentally friendly and recyclable materials is also gaining traction, aligning with global sustainability efforts.
- Impact: These materials will open up new possibilities for industries that require higher performance, such as 5G telecommunications, electric vehicles, and aerospace systems, where traditional materials may fall short.
2. Improved Manufacturing Techniques
Manufacturing processes are continuously evolving, and the future of Double Layer PCBs will likely see the adoption of more precise and efficient production methods. Laser drilling, for example, is becoming more common for creating smaller, more accurate vias, which are essential for high-density designs. Additionally, advances in automation and robotics are improving the speed and accuracy of PCB production, leading to reduced costs and faster turnaround times.
- Impact: These advancements will make Double Layer PCBs more accessible to a broader range of applications, providing higher quality at lower costs, especially for industries requiring rapid prototyping and high precision.
3. Miniaturization and High-Density Design
The demand for miniaturization in electronics continues to grow, and Double Layer PCBs will play a key role in enabling smaller, more powerful devices. As components become smaller and more integrated, Double Layer PCBs will evolve to support high-density interconnect (HDI) technologies that allow more connections in a compact space without compromising performance.
- Impact: This trend will drive innovation in consumer electronics, medical devices, and wearables, where space-saving designs are crucial to product success.
4. Enhanced Applications in Emerging Industries
As new industries emerge and existing ones expand, Double Layer PCBs will be used in more specialized applications. For example, electric vehicles (EVs), renewable energy systems, and IoT (Internet of Things) devices are expected to see increased use of Double Layer PCBs due to their balance of performance, cost, and scalability.
- Impact: These applications will push the boundaries of Double Layer PCB design, requiring new configurations, higher reliability, and increased integration of sensors and wireless technologies.
5. Increased Focus on Sustainability
With growing environmental concerns, the PCB industry is likely to place a greater emphasis on sustainable manufacturing practices. Double Layer PCBs will benefit from advancements in energy-efficient production methods, such as reduced chemical usage, recycling of raw materials, and the development of eco-friendly finishes.
- Impact: Future trends in sustainability will not only reduce the environmental footprint of PCB manufacturing but also offer companies a competitive edge by meeting stricter environmental regulations and customer preferences for greener products.
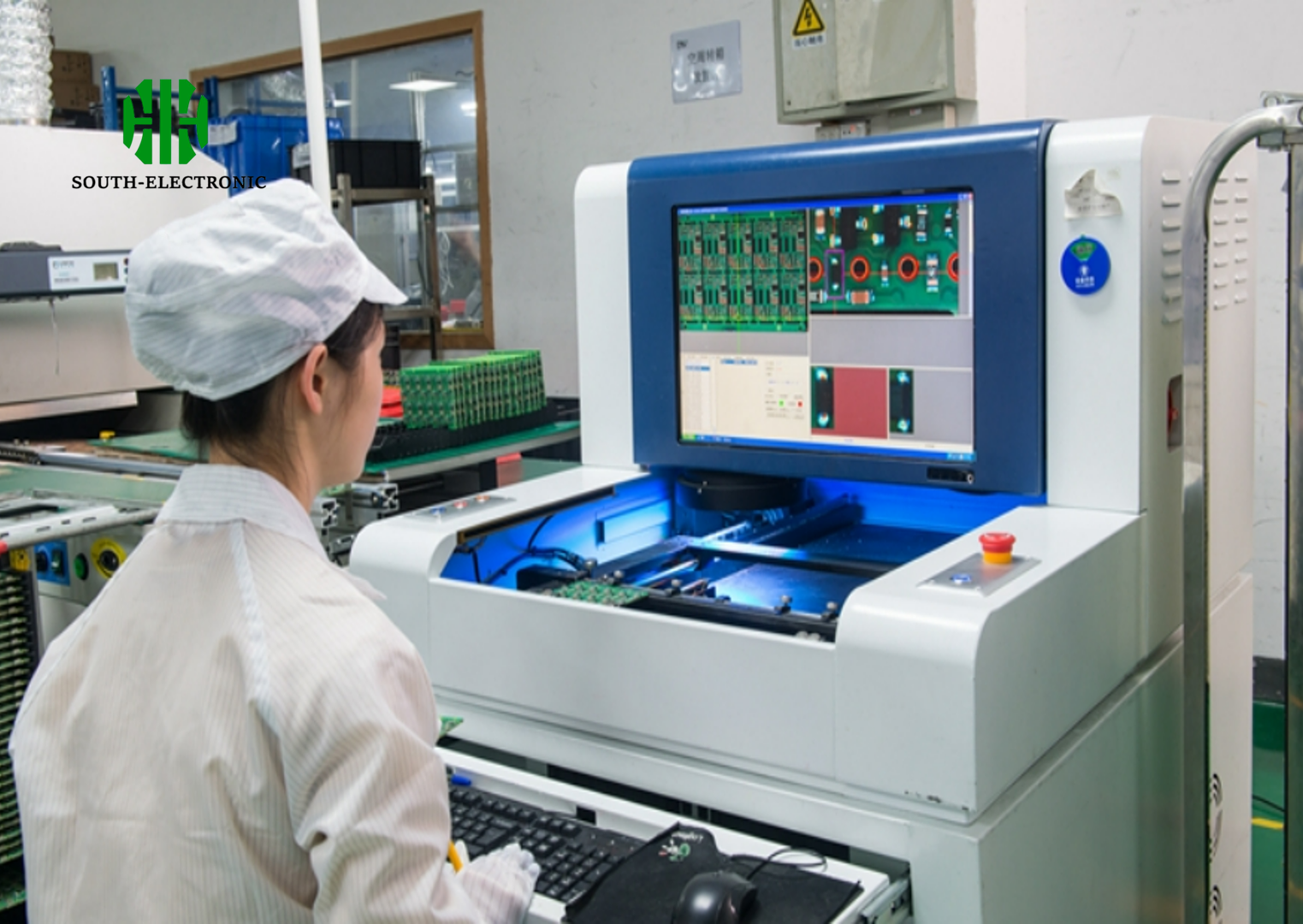
Get in touch
Where Are We?
Industrial Park, No. 438 Donghuan Road, No. 438, Shajing Donghuan Road, Bao'an District, Shenzhen, Guangdong, China
Floor 4, Zhihui Creative Building, No.2005 Xihuan Road, Shajing, Baoan District, Shenzhen, China
ROOM A1-13,FLOOR 3,YEE LIM INDUSTRIAL CENTRE 2-28 KWAI LOK STREET, KWAI CHUNG HK
service@southelectronicpcb.com
Phone : +86 400 878 3488
Send us a message
The more detailed you fill out, the faster we can move to the next step.
