Proveedor de PCB de Núcleo de Cobre
South-Electronic
Elija South-Electronic para obtener la mejor calidad, fiabilidad y valor para sus necesidades de PCB. Con nuestros servicios completos de PCB de núcleo de cobre, desde el diseño hasta la producción, garantizamos precisión, durabilidad y cumplimiento con los estándares más exigentes de la industria.
Su Proveedor de Confianza de PCB de Núcleo de Cobre
Welcome to South-Electronic, your source for high-quality Copper Core PCBs known for their superior heat dissipation and robust performance.
Our Copper Core PCBs provide exceptional reliability, making them ideal for high-power applications in demanding sectors. Explore various configurations like 2-layer, 4-layer, or even more complex multi-layer boards, all designed to meet your specific electronic requirements. Whether you’re enhancing the functionality of power electronics or need high-performance boards for automotive applications, our Copper Core PCBs are proven to deliver reliability and precision. Trust South-Electronic for top-notch quality and consistency in your high-tech projects. Our Copper Core PCBs enhance your devices’ performance through exceptional thermal management and increased durability. Partner with us to achieve innovation and success in your field.
¿Por qué elegir South-Electronic?
-
Soluciones Personalizadas
Tu proyecto es único, y tus necesidades también lo son.
En South-Electronic, lo entendemos, por eso ofrecemos soluciones personalizadas de PCB de núcleo de cobre diseñadas específicamente para ti. Obtendrás un producto que cumple exactamente con tus especificaciones, sin concesiones. -
Garantía de Calidad
Te importa la calidad, y a nosotros también.
Con certificación ISO9001 y pruebas rigurosas a lo largo del proceso de producción, puedes confiar en que nuestras PCBs de núcleo de cobre ofrecerán la fiabilidad y la durabilidad que tu proyecto necesita. -
Pedidos Flexibles
Ya sea que necesites un prototipo o una producción a gran escala, tú tienes el control.
Nuestro MOQ flexible te permite pedir desde solo 1 pieza, para que obtengas exactamente lo que necesitas, cuando lo necesitas, y a un precio que se ajuste al tamaño y presupuesto de tu proyecto. -
Profesionalismo y Eficiencia
Te beneficiarás de la vasta experiencia que aporta nuestro equipo.
Con años de conocimiento en la industria, estamos aquí para resolver tus desafíos más difíciles. Desde el diseño hasta la entrega, te guiaremos en cada paso del camino. -
Capacidades de Producción
Entrega rápida para mantenerte en el cronograma.
Por eso hemos optimizado nuestras líneas de producción para asegurarnos de que obtengas tus PCBs de núcleo de cobre rápidamente, sin sacrificar calidad. Tendrás lo que necesitas, cuando lo necesites, manteniendo tu proyecto en marcha. -
Capacidades de Producción
Disfrutarás de una solución integral con nosotros: desde el abastecimiento de componentes hasta el ensamblaje final.
Ya sea soporte técnico, actualizaciones de productos o comunicación oportuna, siempre puedes contar con nosotros para responder a tus necesidades.
Proyectos Relacionados que Hemos Realizado
Opiniones de Clientes
Preguntas Comunes
Preguntas Más Populares
South-Electronic proporciona una variedad de PCBs de núcleo de cobre, incluyendo PCBs de núcleo de cobre de una sola cara y multicapa, diseñados para aplicaciones de alta potencia como iluminación LED, electrónica automotriz y dispositivos de disipación de calor.
South-Electronic ofrece servicios completos de PCB todo en uno, incluyendo prototipos, fabricación de PCB, ensamblaje y abastecimiento de componentes, cubriendo todo el proceso desde el diseño hasta la producción.
South-Electronic sigue un estricto sistema de control de calidad, cumpliendo con los estándares ISO 9001 e IPC para garantizar que cada PCB cumpla con altos requisitos de calidad. Se realizan pruebas funcionales completas y controles de calidad antes del envío.
Sí, South-Electronic ofrece una amplia gama de opciones de personalización, permitiendo a los clientes ajustar el grosor de la placa, el peso del cobre, las capas y los materiales especiales para satisfacer los requisitos específicos del proyecto
Típicamente, el tiempo de producción de South-Electronic varía entre 7 y 15 días laborables, dependiendo de la complejidad y el tamaño del pedido. También se ofrecen servicios urgentes para proyectos con plazos ajustados.
Envíanos un mensaje
Cuanto más detallado completes, más rápido podremos avanzar al siguiente paso.
Guía Completa de PCBs de Núcleo de Cobre
Contenido
Capítulo 1
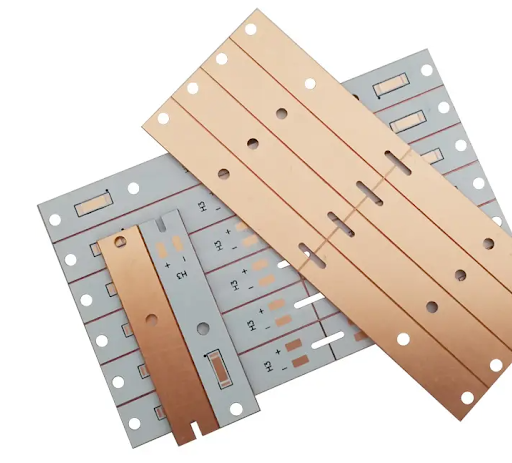
Introducción a los PCBs de Núcleo de Cobre
Los PCBs de núcleo de cobre, también conocidos como PCBs basados en cobre, son un tipo especializado de placa de circuito impreso que utiliza un sustrato de cobre para proporcionar una mejor conductividad térmica y un rendimiento eléctrico mejorado. A diferencia de los PCBs tradicionales que utilizan fibra de vidrio u otros materiales no metálicos, los PCBs de núcleo de cobre están diseñados para gestionar eficientemente la disipación de calor, lo que los hace ideales para aplicaciones de alta potencia.
A medida que la industria electrónica continúa evolucionando, existe una creciente demanda de PCBs que puedan manejar mayores densidades de potencia y desafíos de gestión térmica. Los PCBs de núcleo de cobre se utilizan cada vez más en aplicaciones como iluminación LED, electrónica automotriz y fuentes de alimentación, donde la disipación de calor es fundamental para mantener el rendimiento y prolongar la vida útil de los componentes.
Las principales ventajas de los PCBs de núcleo de cobre sobre los PCBs tradicionales incluyen una mejor gestión térmica, mayor durabilidad y la capacidad de soportar corrientes más altas. Estos beneficios convierten a los PCBs de núcleo de cobre en la opción preferida para industrias que necesitan placas de circuito fiables y de alto rendimiento capaces de manejar condiciones operativas exigentes.
Al incorporar cobre en el diseño de los PCBs, los fabricantes pueden lograr una mejor distribución del calor, reducir los puntos calientes y mejorar la fiabilidad general del sistema, especialmente en entornos de alta frecuencia y alta corriente.
Capítulo 2
¿Qué es un PCB de Núcleo de Cobre?
Un PCB de núcleo de cobre es un tipo de placa de circuito impreso que incorpora un sustrato de cobre para mejorar la disipación de calor y el rendimiento eléctrico general de la placa. Estos PCBs consisten en un núcleo de cobre sólido intercalado entre capas de material dieléctrico y capas conductoras de cobre. El núcleo de cobre actúa como conductor térmico y base estructural, ofreciendo capacidades excepcionales de transferencia de calor en comparación con los PCBs tradicionales.
Estructura de un PCB de Núcleo de Cobre
La estructura típica de un PCB de núcleo de cobre incluye:
- Capa conductora superior: Aquí se montan y conectan los componentes electrónicos mediante trazos de cobre.
- Capa dieléctrica: Situada entre la capa conductora superior y el núcleo de cobre, esta capa proporciona aislamiento eléctrico mientras permite una eficiente transferencia de calor.
- Núcleo de cobre: La capa central de cobre actúa como disipador de calor, absorbiendo y disipando el calor generado por componentes de alta potencia.
- Capa conductora inferior: Opcional en algunos diseños, puede usarse para conexión a tierra o para una mayor disipación de calor.
Diferencias entre los PCBs de Núcleo de Cobre y otros PCBs de Núcleo Metálico
Aunque los PCBs de núcleo de cobre comparten similitudes con otros PCBs de núcleo metálico (MCPCB), como los de núcleo de aluminio o acero, existen diferencias notables:
- Conductividad térmica: El cobre tiene una conductividad térmica significativamente mayor que el aluminio o el acero, lo que lo hace más efectivo para la gestión del calor en aplicaciones de alta potencia.
- Conductividad eléctrica: La superior conductividad eléctrica del cobre permite una mejor distribución de energía y una menor resistencia, crucial para circuitos de alta frecuencia y alta corriente.
- Costo: Los PCBs de núcleo de cobre son generalmente más caros que los de núcleo de aluminio o acero debido al mayor costo del cobre como materia prima. Sin embargo, los beneficios en rendimiento suelen justificar la inversión en aplicaciones donde la disipación de calor es crítica.
- Peso: El cobre es más denso y pesado que el aluminio, por lo que los PCBs de núcleo de cobre tienden a pesar más. Esto puede ser un factor a considerar en aplicaciones donde el peso es importante, aunque a menudo se prioriza el rendimiento.
Los PCBs de núcleo de cobre se utilizan principalmente en aplicaciones donde la alta conductividad térmica y el rendimiento eléctrico fiable son fundamentales, como en iluminación LED, electrónica automotriz y dispositivos de potencia. Su capacidad para gestionar el calor de manera efectiva y soportar componentes de alto rendimiento los convierte en una solución esencial para industrias con exigentes requisitos térmicos y eléctricos.
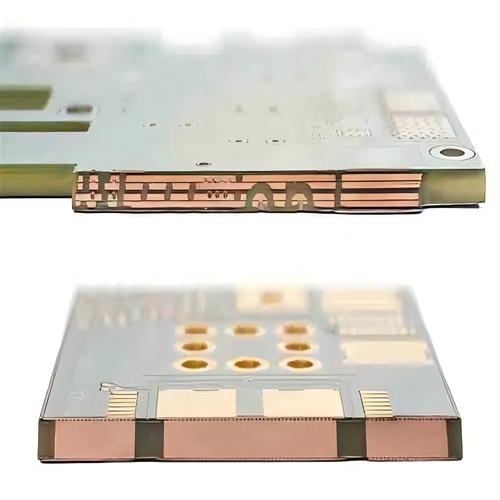
Capítulo 3

Ventajas de Usar PCBs de Núcleo de Cobre
Los PCBs de núcleo de cobre ofrecen varias ventajas sobre los diseños tradicionales de PCBs, lo que los convierte en la opción preferida en aplicaciones que requieren una gestión térmica superior y alta fiabilidad. A continuación, se detallan los beneficios clave:
Conductividad Térmica Superior
Una de las principales ventajas de los PCBs de núcleo de cobre es su excepcional conductividad térmica. El cobre, al ser uno de los materiales más eficientes para la transferencia de calor, permite que estos PCBs disipen el calor mucho más rápido que los PCBs fabricados con núcleos estándar de fibra de vidrio o aluminio. Esta característica es crucial en aplicaciones de alta potencia, donde el calor excesivo puede provocar fallos en los componentes, un menor rendimiento o una vida útil más corta del producto. La capacidad de los PCBs de núcleo de cobre para gestionar y distribuir el calor de manera uniforme ayuda a mantener temperaturas óptimas de funcionamiento para los componentes electrónicos.
Mejor Disipación de Calor para Aplicaciones de Alta Potencia
En industrias como la electrónica automotriz, la iluminación LED y la electrónica de potencia, gestionar el calor es vital para la longevidad y eficiencia de los dispositivos. Los PCBs de núcleo de cobre destacan en disipar el calor lejos de los componentes críticos, reduciendo el riesgo de sobrecalentamiento y mejorando la fiabilidad general del sistema. Esto hace que los PCBs de núcleo de cobre sean particularmente adecuados para aplicaciones de alta potencia donde los PCBs tradicionales pueden tener dificultades para manejar el calor generado. Al distribuir el calor de manera eficiente, los PCBs de núcleo de cobre ayudan a mantener la integridad de los componentes y aseguran un rendimiento consistente a lo largo del tiempo.
Mayor Durabilidad y Fiabilidad
Los PCBs de núcleo de cobre no solo ofrecen un rendimiento térmico superior, sino que también mejoran la durabilidad y la fiabilidad del diseño del circuito en general. El núcleo de cobre proporciona una base estructural sólida, haciendo que el PCB sea más resistente al estrés térmico, al desgaste mecánico y a factores ambientales. Esta mayor durabilidad se traduce en una vida útil más larga para los dispositivos, menores costos de mantenimiento y menos fallos en el campo. Además, la alta conductividad del cobre permite un mejor rendimiento eléctrico, reduciendo la posibilidad de pérdida de señal o interferencia, lo cual es fundamental en aplicaciones de alta frecuencia.
En general, la combinación de una excelente gestión del calor, durabilidad y un rendimiento eléctrico fiable convierte a los PCBs de núcleo de cobre en una solución ideal para industrias que requieren placas de circuito de alta calidad y larga duración capaces de soportar condiciones operativas exigentes.
Capítulo 4
Aplicaciones de los PCBs de Núcleo de Cobre
Los PCBs de núcleo de cobre se utilizan ampliamente en industrias donde la gestión térmica y el rendimiento eléctrico son críticos. Sus propiedades únicas los hacen adecuados para una variedad de aplicaciones de alta potencia y alto rendimiento. A continuación, se presentan algunos de los sectores clave que se benefician de la tecnología de núcleo de cobre:
Electrónica Automotriz
En la industria automotriz, muchos componentes como convertidores de potencia, módulos de control y faros LED generan cantidades significativas de calor. Los PCBs de núcleo de cobre son esenciales en estas aplicaciones, ya que disipan el calor de manera eficiente, asegurando que los componentes electrónicos sensibles funcionen de manera fiable incluso en condiciones extremas de temperatura. Su capacidad para manejar altas corrientes y calor los hace ideales para sistemas de vehículos eléctricos, controladores de motores y unidades de gestión de potencia.
Iluminación LED
Una de las aplicaciones más comunes de los PCBs de núcleo de cobre es en los sistemas de iluminación LED. Los LED generan una cantidad considerable de calor, y los PCBs de núcleo de cobre se utilizan para gestionar ese calor y prolongar la vida útil de los LED. Al disipar el calor de manera más efectiva, los PCBs de núcleo de cobre ayudan a mantener el brillo y la eficiencia de los LED, lo que los hace ideales para soluciones de iluminación de alto rendimiento en los sectores automotriz, industrial y comercial.
Electrónica de Potencia
Los sistemas de electrónica de potencia, como fuentes de alimentación, inversores y convertidores, suelen involucrar altas corrientes y generar mucho calor. Los PCBs de núcleo de cobre son cruciales para estos sistemas, ya que proporcionan una disipación de calor eficiente y mantienen la integridad del circuito bajo cargas eléctricas intensas. En dispositivos de alta potencia como maquinaria industrial y sistemas de distribución de energía, la tecnología de núcleo de cobre ayuda a prevenir el sobrecalentamiento y aumenta la fiabilidad y la longevidad del equipo.
Circuitos de Alta Frecuencia y Aplicaciones de Alta Corriente
En circuitos de alta frecuencia, los PCBs de núcleo de cobre ofrecen una mejor integridad de la señal y reducen las interferencias electromagnéticas (EMI) gracias a la excelente conductividad del cobre. Esto es particularmente importante en telecomunicaciones, sistemas de radar y dispositivos de comunicación inalámbrica. Además, los PCBs de núcleo de cobre son ideales para aplicaciones de alta corriente, ya que pueden manejar cargas eléctricas mayores sin experimentar degradación del rendimiento o sobrecalentamiento.
Otras Industrias que se Benefician de la Tecnología de Núcleo de Cobre
Además de la automotriz, la iluminación y la electrónica de potencia, otras industrias también se benefician de los PCBs de núcleo de cobre. En los sectores aeroespacial y de defensa, los PCBs de núcleo de cobre se utilizan en sistemas críticos donde la fiabilidad y la gestión térmica son primordiales. La industria médica también utiliza PCBs de núcleo de cobre en sistemas de imágenes y equipos de diagnóstico que requieren un rendimiento estable y duradero. Además, la electrónica de consumo, incluidos los sistemas informáticos y de juegos de alto rendimiento, confían cada vez más en la tecnología de núcleo de cobre para gestionar el calor y mejorar la longevidad de los dispositivos.
En resumen, los PCBs de núcleo de cobre desempeñan un papel vital en una amplia gama de industrias, ofreciendo la gestión térmica, durabilidad y rendimiento necesarios para aplicaciones de alta potencia y alto rendimiento.
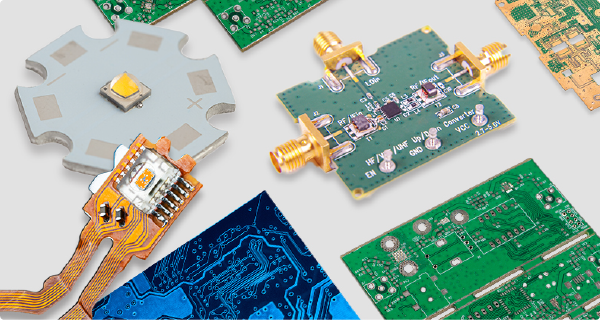
Capítulo 5

Процесс производства печатных плат с медным сердечником
El proceso de fabricación de los PCBs de núcleo de cobre es más complejo que el de los PCBs tradicionales debido a las propiedades térmicas y eléctricas únicas del cobre. A continuación, se presenta una guía paso a paso que describe el proceso de producción, los materiales clave involucrados y los desafíos que enfrentan los fabricantes.
Guía Paso a Paso sobre Cómo se Producen los PCBs de Núcleo de Cobre
Preparación del Núcleo de Cobre
El proceso comienza con la selección de una lámina de cobre de alta calidad, que servirá como el núcleo del PCB. Este núcleo de cobre suele ser más grueso que las láminas de cobre utilizadas en los PCBs estándar para proporcionar una mejor disipación de calor. La lámina de cobre se limpia para eliminar impurezas en la superficie, asegurando una correcta adhesión en los siguientes pasos.Laminado
Una capa dieléctrica, generalmente hecha de materiales térmicamente conductivos y eléctricamente aislantes, se lamina en ambos lados del núcleo de cobre. Esta capa sirve como aislamiento mientras permite la transferencia de calor. El proceso de laminado implica aplicar presión y calor para unir de manera segura el material dieléctrico al núcleo de cobre.Perforación y Grabado
Una vez que la capa dieléctrica está laminada, el PCB pasa por un proceso de perforación para crear agujeros y vías que permiten las conexiones eléctricas entre las diferentes capas de la placa. Después de la perforación, las capas de cobre se graban para formar los patrones del circuito. Este paso utiliza soluciones químicas para eliminar el cobre no deseado, dejando solo las trazas y almohadillas deseadas.Recubrimiento
Después del grabado, los agujeros perforados se recubren con cobre para crear conexiones eléctricas entre las capas superior e inferior del PCB. Este paso asegura que la corriente fluya suavemente a través de la placa. Se pueden agregar capas adicionales de cobre u otros metales para mejorar la conductividad y durabilidad.Aplicación de Máscara de Soldadura y Serigrafía
Se aplica una máscara de soldadura para proteger las trazas de cobre de la oxidación y evitar cortocircuitos. Esta máscara también proporciona aislamiento entre los componentes. Después de la máscara de soldadura, se agrega una capa de serigrafía para etiquetar la placa con las designaciones de los componentes y otras marcas para facilitar el ensamblaje y la resolución de problemas.Acabado Final y Pruebas
El PCB pasa por un acabado superficial final, que puede implicar la aplicación de materiales como oro o plata para mejorar la soldabilidad. Después, el PCB de núcleo de cobre se somete a rigurosas pruebas eléctricas y funcionales para garantizar que cumpla con las especificaciones requeridas. Cualquier defecto se corrige antes de enviar el producto final.
Materiales y Tecnologías Clave Involucradas
- Núcleo de Cobre: El componente principal que proporciona una excelente conductividad térmica e integridad estructural.
- Capa Dieléctrica: Material aislante que también conduce el calor lejos de los componentes de la placa.
- Láminas de Cobre: Se utilizan para crear las trazas del circuito en las capas exteriores.
- Materiales de Recubrimiento: Cobre u otros metales utilizados para recubrir las vías y orificios pasantes para habilitar las conexiones eléctricas.
Tecnologías avanzadas como la perforación con láser y la inspección óptica automatizada (AOI) se utilizan con frecuencia para garantizar precisión durante los procesos de perforación, grabado y pruebas. También se emplean máquinas CNC para un modelado y corte de alta precisión.
Desafíos Comunes y Soluciones Durante la Fabricación
Gestión del Calor: Uno de los principales desafíos en la fabricación de PCBs de núcleo de cobre es mantener un balance adecuado de calor durante los procesos de laminado y soldadura. Un calor excesivo puede provocar deformaciones o delaminado. Los fabricantes mitigan esto utilizando un control preciso de temperatura y materiales de laminado de alta calidad.
Grosor del Cobre: Manejar núcleos de cobre más gruesos es más desafiante que trabajar con PCBs estándar. El mayor peso y densidad del cobre requieren equipos especializados para perforar, grabar y recubrir. El uso de maquinaria CNC con alto par y precisión ayuda a gestionar estos desafíos.
Problemas de Adhesión: Lograr una fuerte adhesión entre el núcleo de cobre y la capa dieléctrica puede ser complicado. Cualquier impureza o superficie irregular puede resultar en un mal enlace. Una limpieza exhaustiva de la superficie y el uso de láminas de alta calidad aseguran una unión más confiable.
Precisión del Grabado: El grabado de capas de cobre más gruesas puede dar lugar a trazas irregulares o sobregrabado. Para solucionar esto, los fabricantes utilizan procesos químicos avanzados y monitoreo en tiempo real para controlar el proceso de grabado.
En conclusión, el proceso de fabricación de PCBs de núcleo de cobre involucra técnicas y materiales avanzados que ayudan a crear placas altamente duraderas y eficientes. A pesar de los desafíos, los fabricantes han desarrollado soluciones que permiten la producción de PCBs de núcleo de cobre con un rendimiento preciso para aplicaciones exigentes.
Capítulo 6
Consideraciones de Diseño para PCBs de Núcleo de Cobre
Consideraciones de Diseño para PCBs de Núcleo de Cobre
El diseño de los PCBs de núcleo de cobre requiere una planificación cuidadosa y la adherencia a reglas de diseño específicas para maximizar sus ventajas térmicas y eléctricas. A continuación, se presentan las principales consideraciones de diseño, mejores prácticas y consejos para garantizar un rendimiento óptimo en los diseños de PCBs de núcleo de cobre.
Reglas de Diseño Específicas y Mejores Prácticas
Espesor del Núcleo de Cobre
El espesor del núcleo de cobre juega un papel crucial en el rendimiento térmico y la integridad estructural del PCB. Los diseñadores deben seleccionar el espesor adecuado del cobre según los requisitos de potencia y las necesidades de disipación de calor de la aplicación. Los espesores comunes del núcleo de cobre varían entre 1.0 mm y 3.0 mm, pero la elección ideal depende de la carga térmica esperada y las restricciones mecánicas.Selección del Material Dieléctrico
Elegir el material dieléctrico correcto entre el núcleo de cobre y las capas conductoras es fundamental para equilibrar la conductividad térmica y el aislamiento eléctrico. Se deben utilizar materiales con alta conductividad térmica, como epoxis térmicamente conductivos o compuestos rellenos de cerámica, para garantizar una transferencia eficiente de calor. El material dieléctrico también debe mantener excelentes propiedades de aislamiento eléctrico para prevenir cortocircuitos.Diseño de Vías y Recubrimiento
Para una óptima disipación de calor y rendimiento eléctrico, el diseño de las vías (agujeros pasantes) debe permitir una transferencia térmica efectiva desde la superficie hacia el núcleo de cobre. Los diseñadores suelen usar vías térmicamente conductoras recubiertas con cobre para canalizar el calor lejos de los componentes calientes. Es importante espaciar adecuadamente las vías y asegurar que las paredes de las vías estén completamente recubiertas para mejorar la fiabilidad y reducir la resistencia.Colocación de Componentes
Los componentes de alta potencia, como transistores de potencia o LEDs, deben colocarse lo más cerca posible del núcleo de cobre para maximizar la disipación térmica. Una colocación adecuada asegura que el calor se transfiera eficientemente al núcleo de cobre, evitando puntos calientes localizados que podrían afectar el rendimiento. Además, los componentes sensibles deben ubicarse estratégicamente para evitar áreas de alto estrés térmico.
Gestión Térmica y Distribución de Potencia
Disipación Efectiva de Calor
Los PCBs de núcleo de cobre se utilizan principalmente por sus propiedades superiores de disipación de calor. Para aprovechar al máximo esto, los diseñadores deben considerar el uso de grandes áreas de cobre, planos de cobre gruesos y disipadores de calor unidos directamente al núcleo de cobre. Al maximizar el área de superficie en contacto con el núcleo de cobre, se puede distribuir más calor de manera uniforme, reduciendo el riesgo de sobrecalentamiento de los componentes de alta potencia.Capas de Distribución de Potencia
La distribución de potencia es otro aspecto crítico en el diseño de PCBs de núcleo de cobre. Para minimizar la caída de voltaje y garantizar una entrega de potencia constante, los diseñadores deben usar trazos anchos y capas gruesas de cobre para los planos de potencia y tierra. Estas capas ayudan a distribuir la corriente eficientemente por toda la placa y reducen la impedancia, lo cual es particularmente importante en aplicaciones de alta corriente.Simulación Térmica
El software de simulación térmica puede utilizarse durante la fase de diseño para predecir cómo fluirá el calor a través del PCB y dónde pueden desarrollarse posibles puntos calientes. Al simular diversas cargas térmicas y ubicaciones de componentes, los diseñadores pueden hacer ajustes antes de la fabricación para garantizar un rendimiento térmico óptimo. Este paso es especialmente importante en diseños de alta potencia donde una gestión inadecuada del calor puede provocar fallos prematuros en los componentes.
Consejos para Garantizar un Rendimiento Óptimo
- Diseño para Fabricabilidad (DFM): Asegúrate de que el diseño cumpla con las capacidades del fabricante. Los núcleos de cobre gruesos pueden ser difíciles de fabricar, por lo que trabajar en estrecha colaboración con tu fabricante para comprender sus limitaciones es esencial para una producción exitosa.
- Minimiza la Longitud de las Trazas: Trazos más cortos entre los componentes de alta potencia reducen la resistencia y mejoran el rendimiento eléctrico general del PCB. Además, minimizar la distancia entre los componentes sensibles al calor y el núcleo de cobre mejora la disipación de calor.
- Usa Almohadillas Térmicas: Para componentes que generan mucho calor, el uso de almohadillas térmicas conectadas al núcleo de cobre a través de vías térmicas puede mejorar significativamente la transferencia de calor. Estas almohadillas ayudan a disipar el calor directamente desde el componente al núcleo de cobre, manteniendo un entorno de operación más fresco.
- Blindaje de Componentes: En aplicaciones con señales de alta frecuencia, los diseñadores pueden necesitar implementar técnicas de blindaje para prevenir interferencias electromagnéticas (EMI). El núcleo de cobre también puede servir como un escudo natural contra EMI, siempre que el diseño incorpore técnicas adecuadas de puesta a tierra y aislamiento.
- Apilado de Capas: Al diseñar un PCB de núcleo de cobre multicapa, la disposición de las capas debe considerar tanto factores térmicos como eléctricos. Las capas de potencia y tierra deben colocarse cerca del núcleo de cobre para aprovechar sus propiedades de disipación de calor, mientras que las capas de señal deben aislarse para evitar interferencias.
En resumen, diseñar PCBs de núcleo de cobre requiere atención a la gestión térmica, la distribución de potencia y la fabricabilidad. Siguiendo estas reglas de diseño y mejores prácticas, los diseñadores pueden crear PCBs de núcleo de cobre eficientes y fiables que funcionen de manera óptima en entornos de alta potencia y alta temperatura.
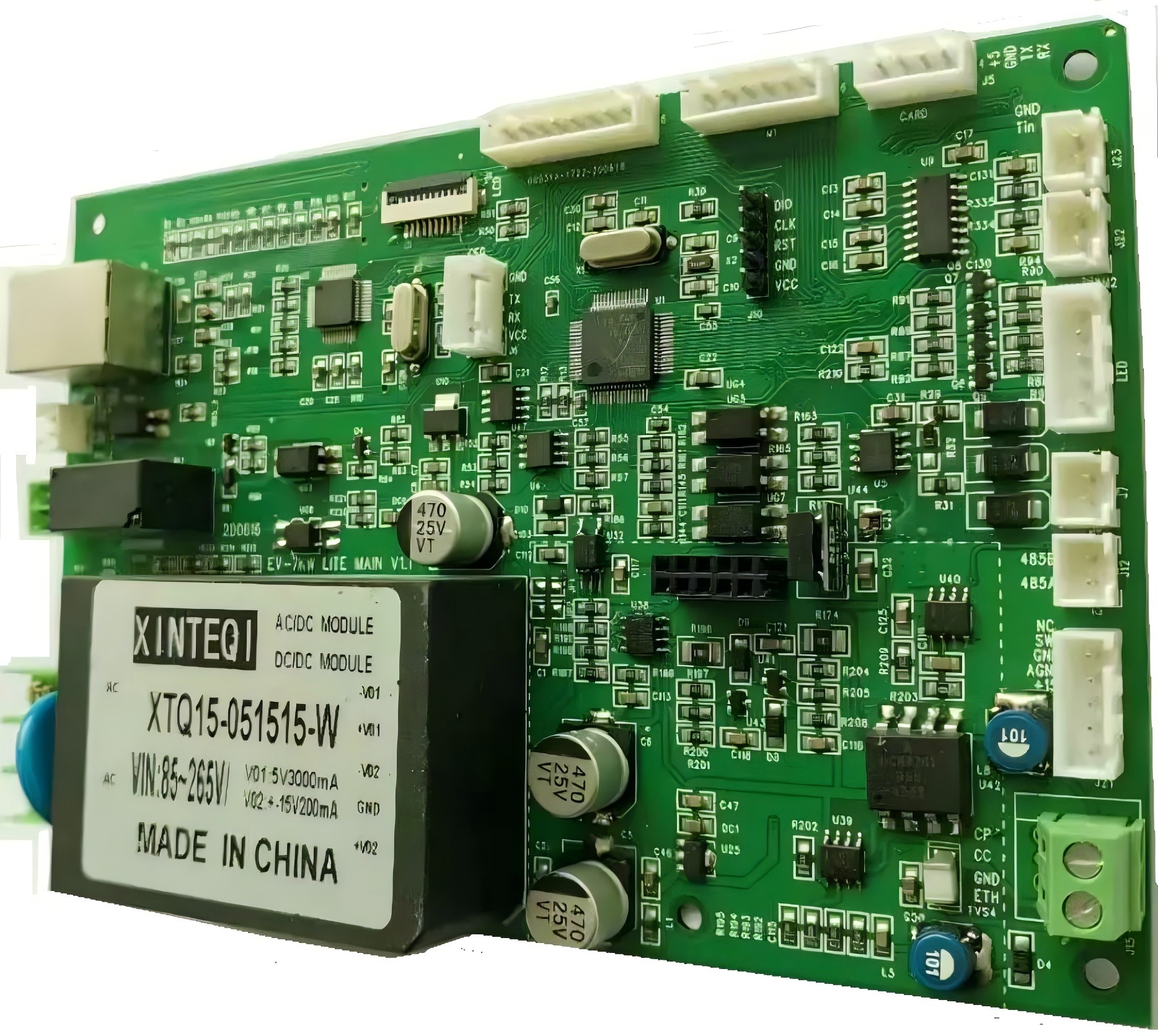
Capítulo 7
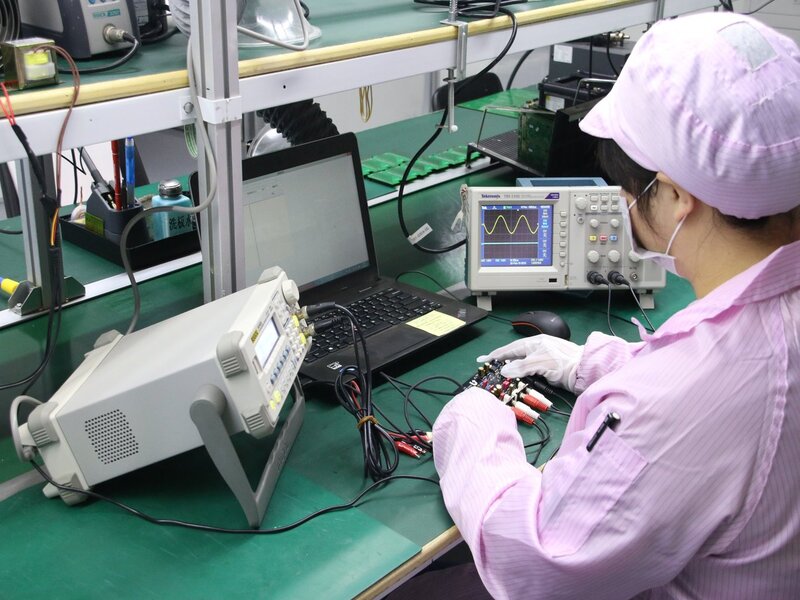
PCB de Núcleo de Cobre vs. PCB de Núcleo de Aluminio
Los PCBs de núcleo de cobre y de núcleo de aluminio se utilizan ampliamente en aplicaciones que requieren una excelente gestión térmica y durabilidad. Sin embargo, difieren significativamente en términos de propiedades de los materiales, rendimiento y costos. Comprender estas diferencias puede ayudarte a elegir el PCB adecuado para tu aplicación específica.
Ventajas y Desventajas de Cada Material
PCB de Núcleo de Cobre
Ventajas:
- Conductividad Térmica Superior: El cobre tiene una conductividad térmica más alta (alrededor de 400 W/mK) en comparación con el aluminio (205 W/mK), lo que hace que los PCBs de núcleo de cobre sean más eficientes en la disipación de calor.
- Mejor Conductividad Eléctrica: La conductividad eléctrica del cobre también es mucho mayor, lo que reduce la resistencia eléctrica y mejora la distribución de potencia en aplicaciones de alta frecuencia y alta corriente.
- Durabilidad: El cobre es más robusto y puede soportar mayores cargas y estrés térmico sin deformarse ni perder rendimiento.
Desventajas:
- Costo: El cobre es significativamente más caro que el aluminio, lo que hace que los PCBs de núcleo de cobre sean más costosos de producir. Este costo más alto puede no estar justificado en aplicaciones de baja potencia donde el aluminio ofrece un rendimiento suficiente.
- Peso: El cobre es más denso y pesado que el aluminio, lo que puede ser una desventaja en aplicaciones sensibles al peso, como la industria aeroespacial y la electrónica portátil.
PCB de Núcleo de Aluminio
Ventajas:
- Menor Costo: El aluminio es más asequible que el cobre, lo que hace que los PCBs de núcleo de aluminio sean una opción rentable para una amplia gama de aplicaciones, especialmente en la electrónica de consumo y la iluminación LED.
- Ligereza: El aluminio es más liviano que el cobre, por lo que es una opción preferida en industrias donde el peso es un factor crítico, como la automotriz y la aeroespacial.
- Gestión Térmica Suficiente: Aunque la conductividad térmica del aluminio es menor que la del cobre, sigue siendo muy superior a la de los sustratos tradicionales FR-4, lo que hace que los PCBs de núcleo de aluminio sean adecuados para muchas aplicaciones sensibles al calor, como las luces LED.
Desventajas:
- Menor Conductividad Térmica: Aunque el aluminio tiene propiedades decentes de disipación de calor, no puede igualar el rendimiento del cobre en aplicaciones de alta potencia.
- Conductividad Eléctrica: La conductividad eléctrica del aluminio es inferior a la del cobre, lo que lo hace menos ideal para circuitos de alta frecuencia o aplicaciones que requieren una distribución eficiente de potencia.
- Menor Durabilidad: El aluminio es menos duradero bajo estrés térmico y mecánico extremo en comparación con el cobre, lo que puede limitar su uso en aplicaciones de alta potencia y alta precisión.
Costo, Rendimiento y Adecuación de Aplicaciones
Costo:
Los PCBs de núcleo de aluminio son generalmente más rentables, lo que los hace adecuados para proyectos con restricciones presupuestarias o aplicaciones donde el rendimiento térmico es importante pero no crítico. Por otro lado, los PCBs de núcleo de cobre son más caros debido al mayor costo del cobre, pero ofrecen un mejor rendimiento tanto en conductividad térmica como eléctrica.
Rendimiento:
En términos de rendimiento, los PCBs de núcleo de cobre ofrecen una disipación de calor superior, mejor conductividad eléctrica y mayor durabilidad. Esto los convierte en la opción preferida para aplicaciones de alta potencia, como convertidores de potencia, electrónica automotriz y sistemas LED de alto rendimiento. Los PCBs de núcleo de aluminio son adecuados para aplicaciones que requieren una buena gestión térmica pero no necesitan el rendimiento térmico o eléctrico de alta gama que proporciona el cobre. Ejemplos incluyen electrónica de consumo, iluminación LED y algunos sistemas automotrices.
Adecuación de Aplicaciones:
- PCBs de Núcleo de Cobre: Más adecuados para aplicaciones de alta potencia donde la disipación extrema de calor y el rendimiento eléctrico son cruciales, como circuitos de alta corriente, dispositivos de potencia, electrónica automotriz y maquinaria industrial.
- PCBs de Núcleo de Aluminio: Ideales para aplicaciones de rango medio donde el costo y el peso son consideraciones importantes, como iluminación LED, electrónica de consumo y sistemas interiores automotrices.
Cuándo Elegir Cobre Sobre Aluminio y Viceversa
Elige PCBs de Núcleo de Cobre cuando:
- Tu aplicación requiere una disipación de calor superior, como en iluminación LED de alta potencia, electrónica automotriz o fuentes de alimentación.
- Necesitas alta conductividad eléctrica para circuitos de alta frecuencia o alta corriente, asegurando una mínima pérdida de energía.
- La durabilidad y el rendimiento a largo plazo son críticos, especialmente en entornos adversos donde los componentes están sujetos a ciclos térmicos y estrés elevado.
Elige PCBs de Núcleo de Aluminio cuando:
- El costo es una consideración clave y la aplicación no requiere la extrema disipación de calor y rendimiento eléctrico que ofrece el cobre.
- El peso es una preocupación y necesitas un PCB más liviano para portabilidad o para reducir el peso total del dispositivo, como en las industrias automotriz y aeroespacial.
- La aplicación implica electrónica de potencia media o sensible al calor, como electrónica de consumo o sistemas LED de baja a media potencia.
En resumen, los PCBs de núcleo de cobre sobresalen en entornos de alta potencia y alto rendimiento donde la gestión térmica y la eficiencia eléctrica son críticas. Los PCBs de núcleo de aluminio, aunque menos capaces en estas áreas, ofrecen una solución rentable y liviana para aplicaciones que no requieren las características de rendimiento extremo del cobre. Elegir entre cobre y aluminio depende de las necesidades específicas de tu proyecto en términos de costo, rendimiento y requisitos de aplicación.
Capítulo 8
¿Cómo Probar PCBs de Núcleo de Cobre?
Probar los PCBs de núcleo de cobre es crucial para garantizar que cumplan con los estándares de rendimiento deseados, particularmente en términos de gestión térmica, rendimiento eléctrico y durabilidad. A continuación, se describen algunos de los métodos y procesos clave para probar los PCBs de núcleo de cobre.
1. Inspección Visual
El primer paso en las pruebas de PCBs de núcleo de cobre es una inspección visual exhaustiva para identificar defectos físicos como capas desalineadas, grabado incompleto o problemas con vías y trazos. Este proceso se realiza manualmente o con sistemas de Inspección Óptica Automatizada (AOI) para detectar problemas que puedan afectar el rendimiento.
Qué buscar:
- Capas de cobre desalineadas.
- Grabado incompleto o irregular de los trazos.
- Defectos en la superficie, como rayones o grietas.
- Aplicación inconsistente de la máscara de soldadura.
2. Prueba de Conductividad Térmica
Dado que la gestión térmica es una característica clave de los PCBs de núcleo de cobre, probar la conductividad térmica es esencial para verificar la eficiencia de la placa en la disipación de calor. Esta prueba se realiza con equipos especializados que miden la transferencia de calor desde componentes de alta potencia al núcleo de cobre.
Cómo funciona:
Un sensor térmico se coloca en el PCB para monitorear la distribución del calor mientras se somete a cargas de potencia. Se evalúa la efectividad de la disipación del calor midiendo la velocidad a la que el calor se transfiere lejos de los puntos calientes.
Métricas clave:
- Velocidad de transferencia de calor.
- Distribución de temperatura en la superficie del PCB.
- Temperatura máxima alcanzada durante la operación.
3. Prueba de Conductividad Eléctrica
Los PCBs de núcleo de cobre son conocidos por su excelente conductividad eléctrica. Probar el rendimiento eléctrico garantiza que los trazos de cobre y el núcleo puedan manejar las cargas de corriente requeridas sin resistencia excesiva, lo que podría causar sobrecalentamiento o pérdidas de energía.
Métodos de prueba:
- Medición de Conductividad: Se utiliza un multímetro o equipo especializado para medir la resistencia en los trazos de cobre y las vías.
- Prueba de Manejo de Corriente: El PCB se somete a cargas de corriente alta, y se mide su capacidad para manejar estas cargas sin degradación del rendimiento.
Métricas clave:
- Resistencia en trazos y vías.
- Caídas de voltaje y pérdidas de energía bajo carga.
- Integridad de las conexiones eléctricas (especialmente en las vías).
4. Prueba de Ciclo Térmico y Resistencia al Estrés
El ciclo térmico es importante para garantizar que los PCBs de núcleo de cobre puedan soportar la expansión y contracción repetida causadas por fluctuaciones de temperatura en aplicaciones reales. Las pruebas de estrés simulan condiciones operativas extremas para verificar la resistencia y durabilidad de la placa.
Cómo funciona:
El PCB se somete a una serie de ciclos de temperatura, alternando entre temperaturas altas y bajas. Este proceso identifica problemas como expansión de materiales, delaminación o fallos mecánicos debido al estrés térmico.
Métricas clave:
- Tasas de expansión térmica.
- Resistencia a la delaminación o grietas.
- Rendimiento bajo ciclos térmicos repetidos.
5. Prueba Funcional
La prueba funcional asegura que el PCB funcione como se espera en su aplicación final. Esto incluye alimentar la placa y someterla a condiciones operativas típicas, como las que se encuentran en electrónica automotriz, iluminación LED o fuentes de alimentación.
Configuración de la prueba:
El PCB se conecta a un banco de pruebas donde opera bajo condiciones simuladas del mundo real. Los sensores miden su rendimiento, incluida la integridad de la señal eléctrica, la distribución de energía y el comportamiento térmico.
Métricas clave:
- Integridad de la señal y niveles de ruido.
- Estabilidad de voltaje y corriente bajo carga.
- Temperaturas operativas en condiciones típicas de uso.
6. Prueba de Carga de Alta Potencia
Para PCBs de núcleo de cobre diseñados para aplicaciones de alta potencia, como convertidores de potencia o sistemas automotrices, la prueba de carga de alta potencia es esencial. Esta prueba verifica la capacidad de la placa para manejar grandes cargas eléctricas sin sobrecalentarse ni sufrir fallos eléctricos.
Configuración de la prueba:
El PCB se somete a cargas de corriente máxima mientras los sensores térmicos y eléctricos monitorean su rendimiento. El objetivo es garantizar que la placa pueda manejar alta potencia sin acumular calor, experimentar caídas de voltaje o fallos de componentes.
Métricas clave:
- Capacidad máxima de carga de corriente.
- Estabilidad térmica a máxima potencia.
- Integridad de la placa y los componentes bajo condiciones de alta tensión.
7. Prueba de Soldabilidad
Las pruebas de soldabilidad se realizan para garantizar que la superficie del PCB permita una soldadura adecuada de los componentes, lo cual es esencial para conexiones fiables en el ensamblaje. Estas pruebas son especialmente importantes para los PCBs de núcleo de cobre, donde la disipación de calor podría afectar la calidad de la soldadura.
Cómo funciona:
El PCB se expone a temperaturas de soldadura, y se evalúa la calidad de las uniones de soldadura. Esta prueba asegura que la superficie de cobre permita una buena humectación y que no existan defectos como uniones frías o mala adhesión.
Métricas clave:
- Resistencia de las uniones de soldadura.
- Propiedades de humectación de la superficie de cobre.
- Ausencia de defectos de soldadura.
8. Pruebas de Fiabilidad
Para verificar la durabilidad y fiabilidad a largo plazo, los PCBs de núcleo de cobre se someten a pruebas ambientales y de fiabilidad. Estas pruebas simulan condiciones operativas adversas, incluyendo humedad, vibración y entornos corrosivos, para garantizar que el PCB pueda soportar un uso prolongado sin fallos.
Pruebas Incluyen:
- Prueba de Humedad: La placa se expone a altos niveles de humedad para evaluar su resistencia a la humedad y la corrosión.
- Prueba de Vibración: Se aplica vibración mecánica para evaluar la integridad estructural del PCB bajo movimiento, crítico en aplicaciones automotrices e industriales.
- Prueba de Salinidad: Para evaluar la resistencia a la corrosión del PCB en aplicaciones marinas o exteriores.
Métricas clave:
- Resistencia a la corrosión.
- Integridad estructural bajo vibración.
- Resistencia a la humedad.
Resumen:
Probar los PCBs de núcleo de cobre implica una combinación de pruebas térmicas, eléctricas, mecánicas y ambientales para garantizar que la placa cumpla con los estándares de rendimiento y fiabilidad. Las pruebas exhaustivas son cruciales para verificar que los PCBs de núcleo de cobre puedan rendir de manera óptima en aplicaciones exigentes donde la disipación de calor y la eficiencia eléctrica son esenciales.
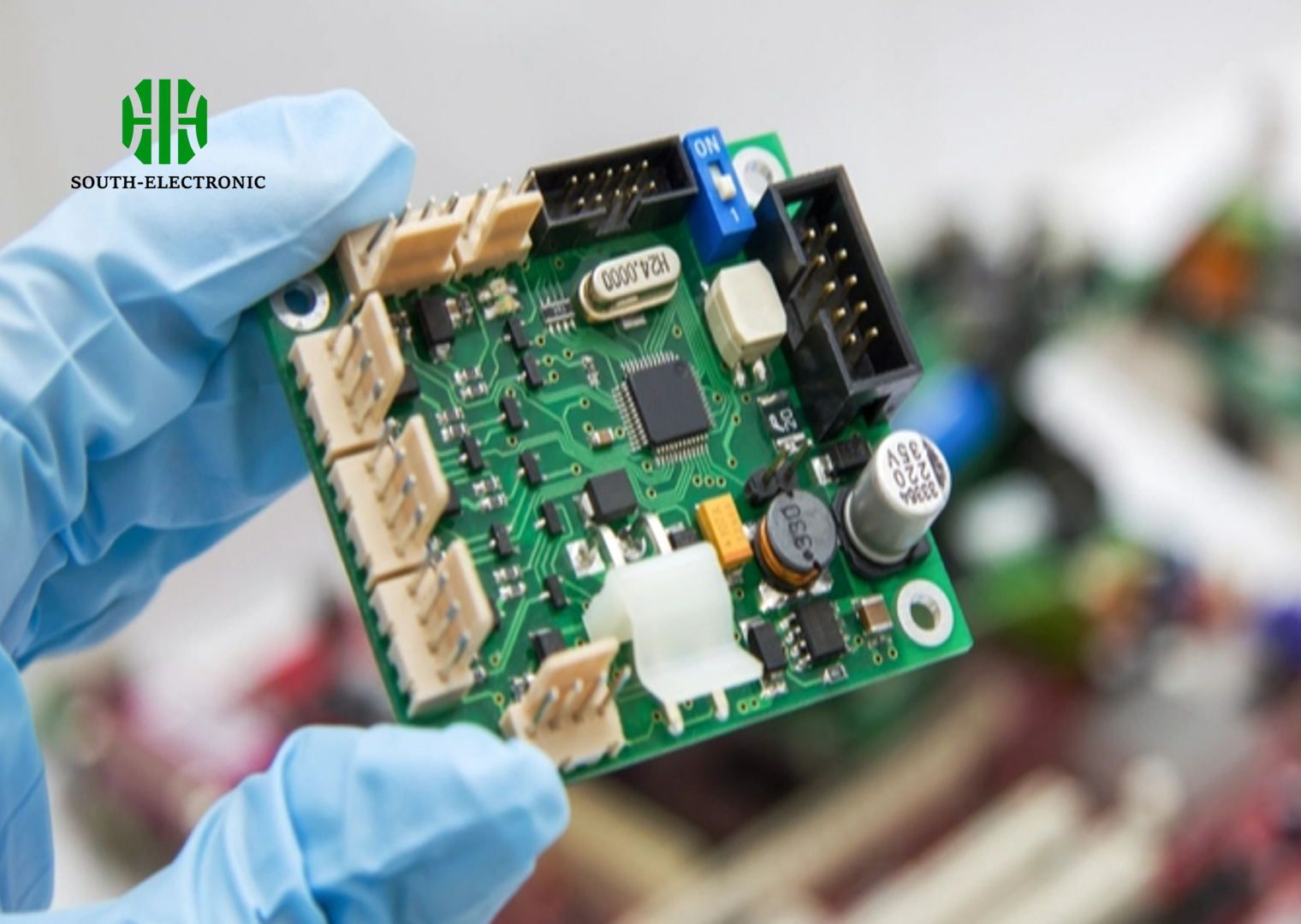
Capítulo 9

¿Cómo Elegir al Proveedor Adecuado de PCB con Núcleo de Cobre?
Elegir al proveedor adecuado de PCB con núcleo de cobre es una decisión crucial que puede impactar la calidad, el rendimiento y la fiabilidad de tu producto final. A continuación, se presentan los factores clave a considerar para asegurarte de que el proveedor cumpla con tus requisitos técnicos y comerciales.
- Experiencia y Experiencia Técnica
Un proveedor con amplia experiencia en la fabricación de PCBs con núcleo de cobre tendrá los conocimientos y la experiencia técnica necesarios para manejar las complejidades de producir placas de alta calidad. Busca proveedores especializados en tecnología de núcleo de cobre con un historial probado en aplicaciones de alto rendimiento como electrónica automotriz, fuentes de alimentación o iluminación LED.
Preguntas para hacer:
- ¿Cuántos años de experiencia tienen en la producción de PCBs con núcleo de cobre?
- ¿Tienen experiencia específica en tu industria o aplicación?
- Estándares de Calidad y Certificaciones
La calidad es primordial cuando se trata de PCBs con núcleo de cobre, especialmente para aplicaciones de alta potencia o sensibles al calor. Asegúrate de que el proveedor cumpla con estándares internacionales de calidad, como ISO 9001 y normas IPC.
Certificaciones a considerar:
- ISO 9001: Certificación del Sistema de Gestión de Calidad.
- Normas IPC: IPC-6012 (Especificación de Rendimiento para PCBs Rígidos) e IPC-A-600 (Aceptación de Placas de Circuitos).
- Certificación UL: Garantiza que los PCBs cumplan con estándares de seguridad eléctrica.
- Capacidades de Fabricación
Evalúa las capacidades de fabricación del proveedor para garantizar que puedan manejar los requisitos específicos de tu proyecto de PCB con núcleo de cobre.
Aspectos clave de fabricación:
- Espesor máximo de cobre que pueden manejar.
- Técnicas avanzadas de laminación para materiales dieléctricos.
- Capacidades de maquinado CNC para perforación y corte precisos.
- Tecnologías avanzadas de recubrimiento para vías y orificios pasantes.
- Pruebas y Control de Calidad
Un proveedor confiable debe contar con estrictas medidas de control de calidad. Esto incluye inspecciones durante el proceso y pruebas del producto final para garantizar el cumplimiento de especificaciones térmicas, eléctricas y mecánicas.
Métodos de prueba esperados:
- Inspección Óptica Automatizada (AOI).
- Pruebas de conductividad térmica.
- Pruebas eléctricas para integridad de señales y manejo de corriente.
- Pruebas de estrés ambiental, como ciclos térmicos y pruebas de vibración.
Personalización y Flexibilidad
El proveedor ideal debe ofrecer opciones de personalización para espesores de cobre, dimensiones de la placa y materiales dieléctricos.Capacidad de Producción y Tiempo de Entrega
Es crucial evaluar la capacidad de producción y tiempos de entrega del proveedor.Soporte Técnico y Comunicación
Elige un proveedor que ofrezca soporte técnico dedicado para ayudarte con el diseño y la fabricación.Precios y Transparencia de Costos
Busca un proveedor con precios competitivos y transparentes.Reputación y Reseñas de Clientes
Investiga la reputación del proveedor mediante testimonios, estudios de caso y valoraciones.Envíos y Logística Global
Asegúrate de que tengan una red de envíos confiable si estás comprando a nivel internacional.
Conclusión
Seleccionar el proveedor adecuado implica evaluar su experiencia, estándares de calidad, capacidades y fiabilidad. Investiga y comunícate con los proveedores para tomar una decisión informada.
Capítulo 10
Tendencias Futuras en las PCBs con Núcleo de Cobre
Las PCBs (Placas de Circuito Impreso) con núcleo de cobre son fundamentales para la electrónica moderna debido a su excelente capacidad de disipación de calor y conductividad eléctrica. A continuación, se presentan algunas tendencias futuras en este campo en evolución:
Aumento de la Demanda para Aplicaciones de Alta Potencia:
A medida que los dispositivos se vuelven más potentes y compactos, aumentará la demanda de PCBs con núcleo de cobre que gestionen el calor de manera eficiente. Esto es especialmente relevante para aplicaciones en vehículos eléctricos, aeroespacial y telecomunicaciones.Avances en la Gestión Térmica:
Es probable que las PCBs con núcleo de cobre del futuro incorporen tecnologías avanzadas de gestión térmica. Estas innovaciones pueden incluir nuevos materiales y diseños arquitectónicos para mejorar aún más la disipación del calor.Miniaturización y Precisión:
La industria sigue avanzando hacia dispositivos más pequeños y eficientes, lo que llevará al desarrollo de PCBs con núcleo de cobre más pequeñas y precisas. Esto requerirá avances en tecnologías de fabricación para mantener el rendimiento mientras se reduce el tamaño.Integración con Electrónica Flexible:
Las PCBs con núcleo de cobre podrían integrarse cada vez más con la electrónica flexible, ofreciendo durabilidad y flexibilidad en el diseño. Esta tendencia es especialmente importante para la tecnología portátil y las pantallas flexibles.Procesos de Fabricación Ecológicos:
Con un enfoque creciente en la sostenibilidad, se fomentará el desarrollo de procesos de fabricación más respetuosos con el medio ambiente. Esto incluye la reducción de residuos, el reciclaje y el uso de materiales ecológicos en la producción de PCBs con núcleo de cobre.Mejora del Rendimiento Eléctrico:
Las PCBs con núcleo de cobre del futuro se centrarán en mejorar el rendimiento eléctrico, soportando mayores tasas de transferencia de datos y mejor integridad de la señal, algo crucial para la electrónica moderna de alta velocidad.Estrategias de Reducción de Costos:
Con el aumento de la demanda, habrá un énfasis en desarrollar procesos de fabricación rentables que mantengan la calidad y el rendimiento, haciendo que las PCBs con núcleo de cobre sean más accesibles para diversas aplicaciones.
Estas tendencias reflejan la innovación y adaptación constantes dentro de la industria electrónica para satisfacer las crecientes demandas de eficiencia, sostenibilidad y rendimiento en los dispositivos modernos.
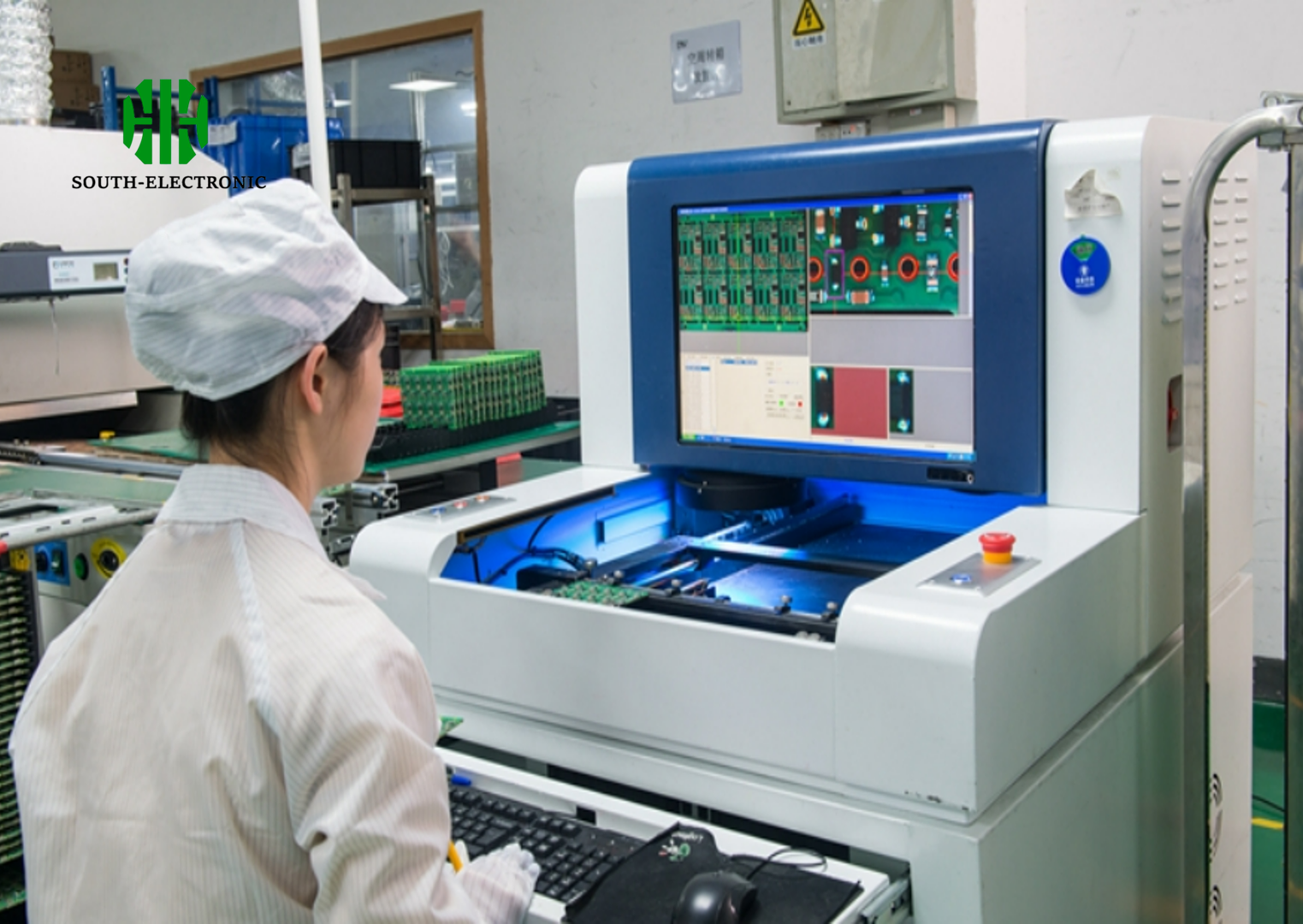
Póngase en Contacto
¿Dónde Estamos?
Parque Industrial, No. 438 Donghuan Road, No. 438, Shajing Donghuan Road, Distrito de Bao'an, Shenzhen, Guangdong, China
Cuarto Piso, Edificio Creativo Zhihui, No.2005 Xihuan Road, Shajing, Distrito de Baoan, Shenzhen, China
Habitación A1-13, Tercer Piso, Centro Industrial Yee Lim, 2-28 Calle Kwai Lok, Kwai Chung, HK
service@southelectronicpcb.com
Teléfono: +86 400 878 3488
Envíanos un mensaje
Cuanto más detallado completes, más rápido podremos avanzar al siguiente paso.
