Proveedor de PCB HDI
South-Electronic
Elija South-Electronic para obtener la más alta calidad, fiabilidad y el mejor valor en sus necesidades de PCB. Experimente la diferencia con nuestros servicios completos de PCB HDI: desde el diseño hasta la producción, garantizamos precisión, durabilidad y cumplimiento con los estándares más exigentes de la industria.
Su socio confiable para PCB HDI de alta calidad
Bienvenido a South-Electronic, su fuente de PCB HDI de alta calidad, reconocidos por su tecnología de interconexión de alta densidad y capacidades de miniaturización.
Confíe en South-Electronic para una calidad y consistencia superiores en sus proyectos de alta tecnología. Nuestros PCB HDI mejoran el rendimiento de sus dispositivos a través de una conectividad excepcional y requisitos de espacio reducidos. Colabore con nosotros para lograr innovación y éxito en su campo.

PCB HDI Tipo I
Este tiene microvías ultrafinas con diámetros de menos de 75 micrones y anchos de conductor/aislamiento por debajo de 50 micrones. Es perfecto para dispositivos electrónicos de próxima generación, como equipos médicos avanzados y telecomunicaciones de alta frecuencia.

PCB HDI Tipo II
Este se basa en el Tipo I añadiendo tanto vías ciegas como enterradas para un mejor enrutamiento. Es adecuado para dispositivos electrónicos avanzados que necesitan conexiones de múltiples capas complejas y una mayor densidad.
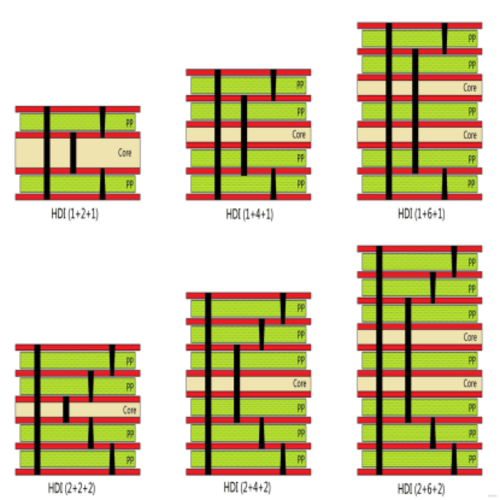
PCB HDI Tipo III
Este cuenta con al menos dos capas de microvías en uno o ambos lados del núcleo, utilizando tanto vías ciegas como enterradas. Es ideal para aplicaciones de alto rendimiento como teléfonos inteligentes y computación avanzada, ya que ofrece un enrutamiento superior.
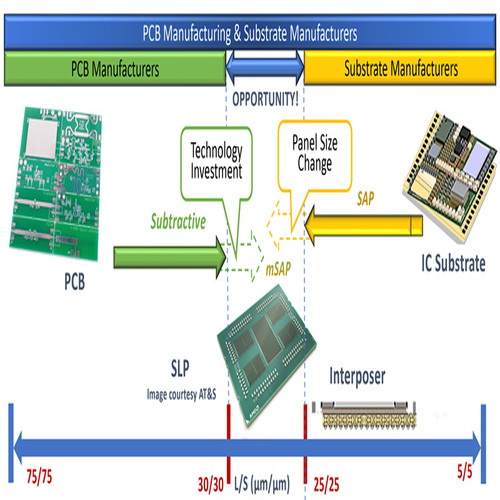
PCB Ultra HDI
Este tiene microvías ultrafinas con diámetros de menos de 75 micrones y anchos de conductor/aislamiento por debajo de 50 micrones. Es perfecto para dispositivos electrónicos de próxima generación, como equipos médicos avanzados y telecomunicaciones de alta frecuencia.
¿Por qué elegir South-Electronic?
Elija South-Electronic por nuestra experiencia en PCBs HDI personalizados y de alta calidad para una variedad de aplicaciones. Nuestro equipo cuenta con una amplia experiencia, asegurando una calidad superior a precios competitivos y un servicio excepcional de principio a fin.
-
Flexibilidad en el Pedido
Puede pedir desde 1 unidad para satisfacer sus necesidades exactas de HDI.
Disfrute de la flexibilidad para probar nuevos diseños o cumplir con los requisitos de lotes pequeños sin complicaciones. -
Equipo Experimentado
Se beneficia de nuestra década de experiencia en la industria.
Entendemos sus desafíos y le brindamos soluciones expertas y soporte confiable en cada paso del proceso. -
Servicio Integral
Obtiene total satisfacción con nuestra amplia gama de equipos.
Nuestro servicio integral garantiza que obtenga todo lo que necesita para una experiencia sin problemas. -
Entrega Rápida
Se beneficia de nuestros tiempos de producción rápidos y eficientes.
Priorizamos la entrega oportuna para cumplir con sus plazos y mantener sus proyectos en marcha. -
Satisfacción Garantizada
Tiene asegurada la calidad y una comunicación clara con nuestra certificación ISO9001.
Su satisfacción es nuestra prioridad, y nos dedicamos a superar sus expectativas con cada pedido.
Proyecto Relacionado que Hemos Realizado
Opiniones de Clientes
Preguntas Comunes
Preguntas Más Populares
South-Electronic tiene una amplia gama de configuraciones de PCB HDI, incluyendo diseños multicapa, microvías, vías ciegas y enterradas, y agujeros perforados con láser. Nos especializamos en ofrecer soluciones de interconexión de alta densidad adaptadas a las necesidades específicas de su proyecto, asegurando un rendimiento óptimo para dispositivos electrónicos complejos.
En South-Electronic, contamos con rigurosas medidas de control de calidad a lo largo del proceso de fabricación. Nuestras PCB HDI se someten a pruebas eléctricas exhaustivas, inspección óptica automatizada (AOI) e inspección por rayos X para detectar cualquier defecto. También estamos certificados por ISO y UL, garantizando que todos los productos cumplen con los estándares internacionales de calidad.
Sí, apoyamos pedidos de lotes pequeños para prototipos. Entendemos la importancia de las pruebas y la validación en la fase de desarrollo, y ofrecemos opciones de fabricación flexibles para satisfacer sus necesidades de prototipado sin requisitos de pedido mínimo.
El tiempo de producción estándar para los PCB HDI en South-Electronic suele ser de 10 a 20 días, dependiendo de la complejidad del diseño y la cantidad del pedido. También ofrecemos opciones para proyectos urgentes con tiempos de entrega más rápidos.
Sí, ofrecemos servicios de prototipado rápido y pedidos urgentes. Para proyectos sensibles al tiempo, ofrecemos opciones de fabricación rápida para asegurar que sus prototipos y pedidos de producción se completen en el menor tiempo posible, sin comprometer la calidad.
Envíanos un mensaje
Cuanto más detallado completes, más rápido podremos avanzar al siguiente paso.
Guía Completa para PCB HDI
Contenido
Capítulo 1
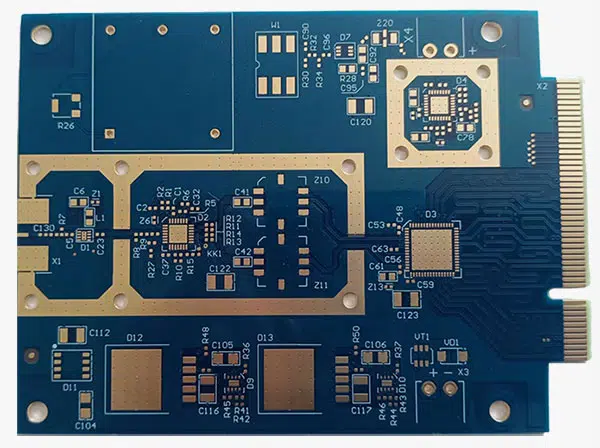
Introducción a PCB HDI
¿Qué es un PCB HDI?
Los PCB HDI (Interconexión de Alta Densidad) son placas de circuitos avanzadas diseñadas para acomodar una mayor densidad de cableado por unidad de área, utilizando trazos más finos y microvías. Esto permite un enrutamiento más complejo y la integración de componentes en un diseño compacto, lo que hace que la tecnología HDI sea ideal para aplicaciones de alto rendimiento.
¿Por qué es importante y dónde se utiliza?
Los PCB HDI son fundamentales en la electrónica moderna, impulsando dispositivos que requieren un procesamiento más rápido, mayor eficiencia y tamaños más pequeños. Se utilizan ampliamente en teléfonos inteligentes, portátiles, dispositivos médicos, sistemas automotrices y equipos avanzados de telecomunicaciones. A medida que las demandas tecnológicas siguen creciendo, los PCB HDI permiten a los fabricantes satisfacer la necesidad de soluciones electrónicas más compactas, eficientes y confiables.
Capítulo 2
Tipos de Configuraciones de PCB HDI
Diferentes Tipos de Configuraciones de PCB HDI
Existen diferentes formas de configurar los PCB HDI, dependiendo de la complejidad y funcionalidad necesarias. La configuración más básica es el diseño HDI de 1 paso, que tiene una sola capa de microvías que proporcionan una conectividad eficiente para aplicaciones menos exigentes, como la electrónica de consumo más pequeña. Un diseño HDI de 2 pasos se basa en esto añadiendo otra capa de microvías o vías escalonadas, lo cual aumenta la densidad de la placa y permite un enrutamiento de señales más complejo. La configuración más avanzada es el diseño HDI de múltiples pasos, que utiliza múltiples vías apiladas o escalonadas a través de varias capas para lograr la máxima densidad y manejar diseños de circuitos altamente complejos. Estas configuraciones son importantes para aplicaciones avanzadas como la computación de alta velocidad, telecomunicaciones y equipos militares, donde el rendimiento, la fiabilidad y la optimización del espacio son críticos.
Microvías, Vías Ciegas y Vías Enterradas Explicadas
La tecnología HDI utiliza tipos avanzados de vías para aumentar considerablemente las opciones de enrutamiento y conectividad entre las capas del PCB. Las microvías son agujeros muy pequeños perforados con láser que normalmente tienen un diámetro inferior a 0.15 mm. Conectan capas adyacentes y permiten una colocación densa de componentes y una alta integridad de la señal. Las vías ciegas conectan la capa exterior del PCB con una o más capas internas sin atravesar toda la placa, lo que ahorra espacio en la superficie del PCB mientras mantiene la eficiencia de enrutamiento. Las vías enterradas solo conectan las capas internas y están completamente ocultas desde el exterior. Esto permite a los diseñadores crear diseños más complejos sin sacrificar espacio en la superficie para componentes adicionales.
Beneficios de las Diferentes Configuraciones de HDI
La configuración que elija para su PCB HDI depende de la aplicación específica y los requisitos de rendimiento. Los diseños HDI de 1 paso son rentables y excelentes para productos con necesidades de rendimiento moderadas, como dispositivos portátiles o productos de electrónica de consumo de nivel básico. Las configuraciones HDI de 2 pasos y múltiples pasos permiten una densidad de componentes mucho mayor y circuitos más sofisticados, lo cual es necesario para aplicaciones de vanguardia como teléfonos inteligentes, tabletas, dispositivos médicos y electrónica automotriz. Además, el uso de microvías, vías ciegas y vías enterradas optimiza el espacio de la placa, reduce la interferencia de señales, mejora la gestión térmica y aumenta el rendimiento general, especialmente en dispositivos que requieren transferencia de datos de alta velocidad y miniaturización, como equipos de telecomunicaciones, sistemas aeroespaciales y dispositivos de computación de alta gama. Mediante el uso de estas diferentes configuraciones y tecnologías de vías, los PCB HDI ofrecen una flexibilidad de diseño inigualable, un mejor rendimiento y beneficios de ahorro de espacio, esenciales para la electrónica moderna.
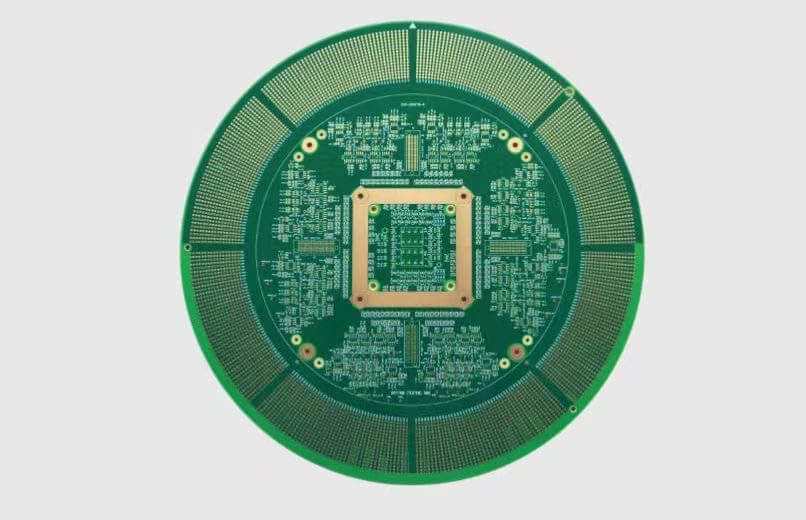
Capítulo 3

Proceso de Fabricación de PCB HDI
La fabricación de PCB HDI es un proceso complejo que implica muchos pasos y tecnologías avanzadas. El objetivo es crear un diseño de alta densidad y múltiples capas que pueda soportar las crecientes demandas de la miniaturización, velocidad y rendimiento de la electrónica moderna. Aquí se presenta un desglose detallado de los pasos clave y las tecnologías utilizadas para fabricar PCB HDI.
Proceso de Fabricación Paso a Paso
El proceso de fabricación de PCB HDI comienza con la creación de una capa central, que sirve de base para las demás capas. Se añaden capas adicionales mediante laminado y grabado para formar las complejas rutas de circuito. Luego, se utilizan tecnologías avanzadas de vías, como microvías, vías ciegas y vías enterradas, para conectar las capas. Después de crear las vías, la placa pasa por perforación, recubrimiento de cobre y acabado de superficie. Finalmente, se inspecciona y prueba para asegurarse de que cumple con las especificaciones y estándares de calidad antes de enviarla al cliente.
- Formación de la Capa Central: El proceso comienza creando las capas centrales del PCB, donde se laminan juntas las capas de cobre y material dieléctrico.
- Perforación Láser: Las microvías se crean mediante perforación láser de alta precisión. Este es un paso crucial en la fabricación de PCB HDI, ya que permite realizar agujeros muy pequeños (generalmente de menos de 150 micrones) que conectan las capas internas y externas.
- Depósito y Recubrimiento de Cobre: Después de perforar las vías, la placa pasa por un proceso de depósito de cobre, en el cual se coloca una capa delgada de cobre en las paredes de las vías perforadas. Este paso asegura la conductividad eléctrica entre las capas. Luego, se recubre toda la superficie con cobre mediante electrodeposición para formar las trazas conductoras.
- Laminación: Las múltiples capas del PCB se apilan y unen mediante laminado. Esto implica aplicar calor y presión para unir las diferentes capas de cobre y material aislante, creando una estructura multicapa que es importante para los diseños de alta densidad.
- Grabado y Formación de Circuito: Las capas de cobre se graban selectivamente para crear el patrón de circuito deseado. Este es un paso crítico para formar los caminos de señal en el PCB.
- Acabado de Superficie y Aplicación de Máscara de Soldadura: Se coloca una máscara de soldadura para proteger las trazas de cobre y evitar cortocircuitos cuando se sueldan los componentes. Luego, se aplica un acabado de superficie, como ENIG (Níquel Electrolítico Inmerso en Oro) o HASL (Nivelación de Soldadura por Aire Caliente), para mejorar la soldabilidad y prevenir la oxidación.
- Inspección y Pruebas: El producto final se somete a pruebas exhaustivas, incluyendo Inspección Óptica Automatizada (AOI), pruebas eléctricas y, a veces, inspección por rayos X, para asegurar que todas las conexiones funcionen y que el PCB cumpla con las especificaciones de diseño.
Tecnologías Involucradas
La fabricación de PCB HDI se basa en varias tecnologías avanzadas que permiten una alta precisión y exactitud:
- Perforación Láser: Utilizada para hacer microvías, que son clave en el diseño de alta densidad de los PCB HDI. La perforación láser permite crear vías extremadamente pequeñas que no pueden hacerse con taladros mecánicos.
- Laminación: Este proceso une las múltiples capas de cobre y material aislante, formando las estructuras multicapa de los PCB HDI. La laminación asegura que la placa sea mecánicamente fuerte y estable.
- Recubrimiento: La electrodeposición se usa para colocar cobre en las vías y trazas, asegurando una buena conexión eléctrica entre las capas. También se aplican acabados especiales en la superficie, como ENIG o OSP (Preservador de Soldabilidad Orgánico), para hacer la placa más duradera y fácil de soldar.
Materiales Clave Utilizados en la Fabricación de PCB HDI
La elección de materiales es importante en la fabricación de PCB HDI tanto para el rendimiento como para la fiabilidad:
- Lámina de Cobre: El cobre se usa para crear las trazas y vías conductoras en el PCB. Su alta conductividad eléctrica lo hace adecuado para asegurar que las señales funcionen bien.
- Materiales Dieléctricos: Materiales como FR-4 (un laminado epoxi reforzado con vidrio) se usan comúnmente como capas aislantes entre las capas de cobre. Para diseños más avanzados, se pueden usar materiales con mayor estabilidad térmica, como el poliimida.
- Prepreg y Laminados: Son importantes para unir las capas. El prepreg (un tejido de vidrio recubierto de resina) se coloca entre las capas de cobre durante el laminado para asegurar que la placa sea mecánicamente fuerte y esté eléctricamente aislada.
- Máscara de Soldadura: Una capa protectora se coloca encima de las trazas de cobre para evitar la oxidación y cortocircuitos durante el ensamblaje.
- Acabados de Superficie: Los acabados comunes como ENIG, HASL o OSP se utilizan para proteger el cobre expuesto y facilitar la soldadura de los componentes.
En conclusión, la fabricación de PCB HDI es un proceso altamente sofisticado que requiere un control cuidadoso de cada paso y el uso de materiales y tecnologías avanzadas. La combinación de perforación láser, laminado multicapa y materiales de alto rendimiento permite la fabricación de placas compactas y de alta densidad, que son importantes para los dispositivos electrónicos modernos.
Capítulo 4
Ventajas de los PCB HDI
Los PCB HDI ofrecen numerosas ventajas sobre los diseños de PCB tradicionales, lo que los hace esenciales en la electrónica moderna, donde el espacio, el rendimiento y la eficiencia son críticos. A continuación, se presentan los principales beneficios que hacen que la tecnología HDI sea la opción preferida para dispositivos compactos, de alto rendimiento y fiables:
Mayor Densidad e Integración de Componentes
Una de las principales ventajas de los PCB HDI es su capacidad para soportar una densidad de componentes mucho mayor que los PCB estándar. Al utilizar microvías, vías ciegas y vías enterradas, los PCB HDI pueden integrar más componentes en un espacio reducido. Esto permite un enrutamiento complejo, especialmente en diseños multicapa, lo que permite a los ingenieros crear circuitos intrincados sin sacrificar espacio o funcionalidad. Esta mayor densidad es crucial para aplicaciones avanzadas, como teléfonos inteligentes, dispositivos portátiles y electrónica automotriz, donde el espacio en la placa es limitado, pero la demanda de funcionalidad es alta.
Mejor Rendimiento Eléctrico e Integridad de Señal
Los PCB HDI están diseñados para manejar señales de alta velocidad con mínima pérdida de señal e interferencia. El uso de trazos más cortos y microvías reduce la longitud del camino de la señal, minimizando la interferencia electromagnética (EMI) y la diafonía. Esto resulta en una mejor integridad de señal, lo cual es vital para aplicaciones de alta frecuencia, como la comunicación 5G, dispositivos IoT y sistemas informáticos. Además, la capacidad de colocar los componentes más cerca acorta los caminos eléctricos, reduciendo la latencia de la señal y mejorando el rendimiento general. Esto es particularmente beneficioso en aplicaciones de datos intensivos, donde la velocidad y precisión son fundamentales.
Factor de Forma Más Pequeño y Diseños Más Compactos
La miniaturización de la electrónica es una fuerza impulsora detrás de la adopción generalizada de la tecnología HDI. Los PCB HDI permiten a los fabricantes crear dispositivos más pequeños, delgados y ligeros sin comprometer la funcionalidad ni el rendimiento. Al maximizar el uso del espacio disponible en la placa con enrutamiento de trazas de alta densidad y estructuras multicapa, los PCB HDI ayudan a reducir el tamaño total de los dispositivos. Esto es especialmente importante en la electrónica de consumo portátil, como teléfonos inteligentes, tabletas y dispositivos portátiles, donde los factores de forma compactos son no solo deseables sino necesarios para la usabilidad práctica.
Mayor Fiabilidad y Durabilidad
La construcción avanzada de los PCB HDI contribuye a una mayor fiabilidad y durabilidad en comparación con los PCB tradicionales. Las vías más pequeñas y el mayor número de interconexiones permiten una mejor gestión térmica, ya que el calor se distribuye de manera más uniforme en la placa. Esto reduce el riesgo de puntos calientes y fallos de componentes debido a un calor excesivo. Además, los materiales utilizados en los PCB HDI, como laminados de alto rendimiento y cobre, proporcionan una mejor resistencia al estrés mecánico, asegurando la integridad de la placa incluso en condiciones ambientales adversas. Esto hace que los PCB HDI sean ideales para industrias como la automotriz, la aeroespacial y la militar, donde la durabilidad y la fiabilidad son esenciales.
Transmisión de Señal Más Rápida y Mejor Rendimiento
Además de una mejor integridad de señal, los PCB HDI ofrecen una transmisión de señal más rápida gracias a su diseño avanzado. Caminos de señal más cortos, menores retrasos de señal y enrutamiento optimizado contribuyen a mayores velocidades de transmisión de datos, que son cruciales en aplicaciones que requieren alta potencia de procesamiento y transferencia rápida de datos. Los PCB HDI se utilizan ampliamente en sectores como las telecomunicaciones, la informática y la automatización industrial, donde el procesamiento y la comunicación de datos a alta velocidad son fundamentales para el rendimiento del sistema.
Flexibilidad en el Diseño y Personalización
La flexibilidad de los diseños de PCB HDI permite a los ingenieros crear placas personalizadas adaptadas a las necesidades específicas de cada aplicación. Con configuraciones de múltiples pasos para las vías y la capacidad de apilar capas de diversas maneras, los PCB HDI ofrecen más libertad de diseño en comparación con los PCB tradicionales. Esto los hace ideales para crear soluciones personalizadas para industrias especializadas como los dispositivos médicos, donde a menudo se requieren diseños únicos para cumplir con estrictos estándares de tamaño y rendimiento. La capacidad de combinar diseños de PCB rígido-flexibles mejora aún más esta flexibilidad, permitiendo diseños complejos en tres dimensiones que pueden ajustarse a dispositivos compactos o de formas irregulares.
Eficiencia en Costos en Producción a Gran Escala
Si bien el costo inicial de producción de PCB HDI puede ser más alto debido a las técnicas avanzadas de fabricación, estos costos se compensan en producciones a gran escala. La capacidad de integrar más funcionalidad en un espacio reducido puede reducir la necesidad de múltiples PCB, componentes e interconexiones, disminuyendo el costo total del producto final. Además, la mayor fiabilidad y rendimiento de los PCB HDI conducen a menos fallos, reduciendo los costos asociados con reparaciones, devoluciones y tiempos de inactividad, lo que hace que la tecnología HDI sea una solución rentable a largo plazo para los fabricantes en gran volumen.
En conclusión, los PCB HDI ofrecen una serie de ventajas que los convierten en la solución preferida para los fabricantes que buscan crear productos electrónicos de alto rendimiento, compactos y fiables. Su capacidad para soportar una mayor densidad de componentes, mejorar la integridad de la señal, ofrecer mayores velocidades y mejorar la flexibilidad de diseño los ha hecho indispensables en sectores como la electrónica de consumo, las telecomunicaciones, la automoción, la aeroespacial y los dispositivos médicos. A medida que la tecnología continúa evolucionando, la demanda de PCB HDI solo aumentará, impulsando la innovación y permitiendo el desarrollo de sistemas electrónicos más avanzados y compactos.

Capítulo 5
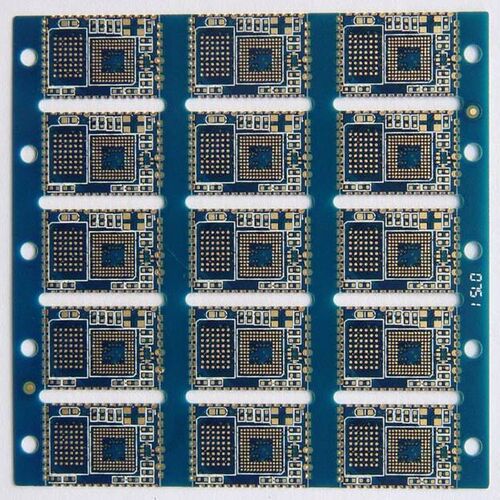
Aplicaciones Comunes de los PCB HDI
Los PCB HDI se han vuelto esenciales en una amplia gama de industrias debido a su capacidad para soportar diseños de alta densidad, mejorar el rendimiento eléctrico y ofrecer formatos más pequeños. Su versatilidad y características avanzadas los hacen ideales para numerosas aplicaciones en varios sectores de alta tecnología. A continuación, se describen algunas de las aplicaciones más comunes de los PCB HDI:
Electrónica de Consumo
El mercado de la electrónica de consumo, en particular dispositivos como teléfonos inteligentes, tabletas, portátiles y dispositivos portátiles, depende en gran medida de los PCB HDI. Con la creciente demanda de dispositivos más pequeños, potentes y con más funciones, la tecnología HDI permite a los fabricantes maximizar la funcionalidad mientras minimizan el tamaño.
- Teléfonos Inteligentes: Los PCB HDI permiten la integración de funciones avanzadas, como cámaras de alta resolución, procesadores rápidos, conectividad 5G y mayor duración de la batería en un espacio extremadamente compacto.
- Tabletas y Portátiles: Estos dispositivos se benefician de los PCB HDI, ya que ofrecen un procesamiento de datos más rápido, mejor gestión de energía y uso más eficiente del espacio, lo que da como resultado diseños más delgados y productos más ligeros.
- Dispositivos Portátiles: Dispositivos como relojes inteligentes y rastreadores de actividad utilizan PCB HDI para incorporar múltiples sensores, procesadores y módulos de comunicación inalámbrica en un paquete pequeño y ligero, haciéndolos cómodos de llevar y ofreciendo funcionalidad robusta.
Dispositivos Médicos y Equipos de Salud
Los PCB HDI desempeñan un papel crucial en el desarrollo de dispositivos médicos, donde la precisión, la fiabilidad y el tamaño compacto son fundamentales. A medida que la industria de la salud adopta tecnologías más avanzadas, como dispositivos de diagnóstico portátiles, equipos médicos implantables y sistemas de monitoreo, el uso de PCB HDI ha aumentado significativamente.
- Dispositivos Implantables: Los PCB HDI se utilizan en marcapasos, neuroestimuladores y audífonos, donde el tamaño reducido y la fiabilidad son esenciales para un uso seguro a largo plazo dentro del cuerpo humano.
- Equipos de Diagnóstico: Dispositivos como máquinas de ultrasonido, escáneres de resonancia magnética y herramientas de diagnóstico portátiles se benefician de la alta potencia de procesamiento y la transmisión eficiente de datos que proporcionan los PCB HDI, lo que garantiza resultados precisos y oportunos.
- Monitores de Salud Portátiles: Los rastreadores de actividad y los dispositivos médicos portátiles que monitorean el ritmo cardíaco, la presión arterial y otros signos vitales requieren PCB HDI compactos y ligeros para ofrecer un rendimiento fiable mientras son cómodos para el paciente.
Industria Automotriz y Aeroespacial
En los sectores automotriz y aeroespacial, los PCB HDI son críticos para crear sistemas fiables y de alto rendimiento que puedan soportar entornos difíciles mientras ofrecen funcionalidad avanzada.
- Electrónica Automotriz: Los PCB HDI se utilizan en sistemas ADAS (Sistemas Avanzados de Asistencia al Conductor), sistemas de infoentretenimiento, controles de navegación y módulos de gestión de energía. Su pequeño tamaño, alta fiabilidad y capacidad para manejar transmisión de datos de alta velocidad los hacen esenciales para los vehículos modernos, especialmente para los vehículos eléctricos y autónomos.
- Sistemas Aeroespaciales: En la industria aeroespacial, los PCB HDI se despliegan en sistemas de aviónica, equipos de comunicación por satélite y controles de navegación. Estas placas deben soportar temperaturas extremas, variaciones de presión y vibraciones, y la tecnología HDI garantiza alta fiabilidad y rendimiento en estas condiciones exigentes. Además, la ligereza de los PCB HDI ayuda a reducir el peso total de las aeronaves y naves espaciales, lo cual es un factor crítico en el diseño aeroespacial.
Telecomunicaciones y Hardware de Redes
El sector de las telecomunicaciones es otra área donde los PCB HDI tienen un impacto significativo. Con el auge de la tecnología 5G, la necesidad de transmisión de datos de alta velocidad y alta frecuencia se ha vuelto fundamental, y los PCB HDI proporcionan el rendimiento y la miniaturización necesarios para satisfacer estas demandas.
- Estaciones Base 5G: Los PCB HDI se utilizan en la infraestructura central de las redes 5G, permitiendo velocidades de transferencia de datos más rápidas, menor latencia y mayor ancho de banda. Ayudan a lograr los diseños de celdas pequeñas necesarios para el despliegue de 5G.
- Enrutadores y Conmutadores de Red: En el hardware de redes, los PCB HDI permiten un enrutamiento eficiente de señales de alta velocidad, minimizando la diafonía y la pérdida de señal. Esto asegura que los enrutadores, conmutadores y centros de datos operen con un rendimiento óptimo, facilitando la comunicación y transferencia de datos en redes de gran escala.
- Sistemas de Comunicación por Fibra Óptica: Los PCB HDI son esenciales en transceptores ópticos y procesadores de señal, que son componentes críticos en los sistemas de comunicación por fibra óptica. Sus diseños de alta densidad aseguran un procesamiento de datos eficiente y velocidades de transmisión rápidas.
Automatización Industrial y Robótica
El creciente campo de la automatización industrial y la robótica también se beneficia de los PCB HDI. Los sistemas de automatización dependen de un procesamiento de datos preciso y rápido para controlar máquinas, sensores y actuadores en tiempo real.
- Robótica: Los PCB HDI se utilizan en robots para sistemas de navegación, controladores de motor y unidades de procesamiento, donde el espacio es limitado y el rendimiento es crucial. Estos sistemas a menudo requieren transferencia de datos de alta velocidad, bajo consumo de energía y alta fiabilidad, todos los cuales pueden ser proporcionados por los PCB HDI.
- Controladores de Automatización: Los PCB HDI se utilizan en controladores lógicos programables (PLC) e interfaces hombre-máquina (HMI) que controlan maquinaria industrial, asegurando que operen de manera eficiente y precisa en entornos de manufactura complejos.
Militar y Defensa
En los sectores militar y de defensa, los PCB HDI son indispensables debido a su alta fiabilidad, forma compacta y capacidad para soportar condiciones extremas. Los sistemas de defensa a menudo requieren electrónica robusta para aplicaciones como comunicación, vigilancia, radar y sistemas de armamento.
- Sistemas de Radar y Comunicación: Los PCB HDI aseguran un procesamiento de datos rápido y una comunicación fiable en sistemas militares críticos, donde el tiempo de inactividad o el fallo no son una opción.
- Sistemas de Control de Armas: Los PCB HDI se utilizan en sistemas de guía para misiles y drones, donde el tamaño compacto y la alta precisión son esenciales.
En conclusión, los PCB HDI se encuentran en una amplia variedad de industrias y aplicaciones, desde la electrónica de consumo y la salud hasta la automoción, la aeroespacial, las telecomunicaciones y la defensa. Su capacidad para ofrecer diseños compactos, de alta densidad y alto rendimiento los hace esenciales para las tecnologías avanzadas y sistemas electrónicos complejos de hoy en día. A medida que crece la demanda de dispositivos electrónicos más pequeños, rápidos y eficientes, el uso de PCB HDI continuará expandiéndose en estas industrias.
Capítulo 6
Diseño de PCB HDI
Diseñar un PCB HDI es una tarea compleja que requiere una consideración cuidadosa de varios factores para maximizar el rendimiento, garantizar la fiabilidad y cumplir con los requisitos específicos de las aplicaciones electrónicas de alta densidad y alta velocidad. En este capítulo, presentaremos algunas pautas para ayudarle a diseñar PCBs HDI que cumplan con estos requisitos.
Mejores Prácticas para el Diseño de PCBs HDI
Diseñar PCBs HDI es más complejo que el diseño de PCB tradicional debido a la mayor densidad y al uso de técnicas de fabricación avanzadas. Seguir las mejores prácticas puede ayudar a asegurar un diseño óptimo:
- Definir Objetivos Claros de Diseño: Comience definiendo claramente los requisitos de rendimiento del producto, como la velocidad de la señal, la densidad de componentes y las restricciones mecánicas. Esto le ayudará a elegir la configuración HDI adecuada, incluyendo el número de capas y estructuras de vías.
- Colaborar Temprano con los Fabricantes: El diseño de PCB HDI está estrechamente vinculado a las capacidades de fabricación. Colaborar con el fabricante desde el principio del proceso de diseño garantiza que el diseño pueda producirse de manera rentable y dentro de los límites técnicos del fabricante, evitando iteraciones de diseño costosas.
- Usar Software de Diseño Avanzado: Los PCBs HDI modernos requieren herramientas de diseño sofisticadas que soporten diseños de alta densidad, trazos finos y microvías. Utilizar software estándar de la industria como Altium Designer o Cadence Allegro asegura mayor precisión y cumplimiento de los estándares de fabricación.
- Implementar Diseño para Fabricabilidad (DFM): Considere la fabricabilidad a lo largo del proceso de diseño evitando estructuras excesivamente complejas que puedan llevar a mayores costos o menores tasas de rendimiento. Las pautas de DFM incluyen mantener los tamaños de las vías dentro de las tolerancias de fabricación, minimizar el número de perforaciones y garantizar suficiente separación de cobre.
Consideraciones de Disposición: Ancho de Trazo, Colocación de Vías y Diseño de Apilamiento
La disposición de un PCB HDI es crucial para lograr un alto rendimiento, especialmente en términos de integridad de la señal, gestión térmica y colocación de componentes. Varios elementos de diseño requieren una planificación cuidadosa:
- Ancho y Espaciado de los Trazos: Dado que los PCBs HDI a menudo manejan señales de alta velocidad, el ancho y espaciado de los trazos deben calcularse cuidadosamente para minimizar la pérdida de señal y evitar diafonía. Es fundamental mantener un control adecuado de la impedancia en función de la velocidad de la señal y el tipo de línea de transmisión (como microstrip o stripline). Para aplicaciones de ultra alta frecuencia, el ancho de trazo puede ser tan pequeño como 3-5 mils, y el espaciado debe optimizarse para la reducción de ruido.
- Colocación y Tipos de Vías: La colocación adecuada de las vías es clave para mantener la integridad de las señales entre capas. Las microvías se utilizan comúnmente en los PCBs HDI debido a su pequeño tamaño, lo que permite una colocación densa de componentes. Es importante colocar las vías cerca de los componentes para acortar las rutas de señal, mejorando la velocidad de transmisión y reduciendo la degradación de la señal. Las vías ciegas y enterradas deben usarse estratégicamente para mantener la compacidad de la placa y evitar capas innecesarias. Además, las vías apiladas pueden proporcionar una conectividad mejorada entre capas, aunque deben usarse con moderación para controlar costos y garantizar estabilidad mecánica.
- Diseño de Apilamiento: El apilamiento de un PCB HDI se refiere a la disposición de sus capas, incluyendo señales, planos de energía y de tierra. Un apilamiento bien optimizado ayuda a lograr un control adecuado de impedancia, mejora la integridad de la señal y minimiza la interferencia electromagnética (EMI). Por lo general, se utilizan capas alternas de señales y tierra para proporcionar un apantallamiento adecuado y mantener una impedancia constante en las trazas de alta velocidad. También se prefieren los apilamientos simétricos para evitar deformaciones durante el proceso de fabricación.
Cómo Minimizar la Interferencia de Señal y Mejorar la Gestión Térmica
Los PCBs HDI se utilizan a menudo en aplicaciones de alta velocidad donde es crucial gestionar la integridad de la señal y la disipación de calor. Los diseñadores deben considerar posibles interferencias y desafíos térmicos para asegurar un funcionamiento fiable.
Minimización de la Interferencia de Señal (EMI/Diafonía): La interferencia de señal, o interferencia electromagnética (EMI), y la diafonía pueden degradar la calidad de la señal en los PCBs HDI. Para minimizar estos efectos:
- Uso de Planos de Tierra: Un plano de tierra sólido adyacente a las capas de señales de alta velocidad ayuda a reducir la EMI al proporcionar un camino de retorno de baja impedancia para las señales.
- Optimización del Enrutamiento de Trazos: Evite enrutar trazos de alta velocidad en paralelo a lo largo de distancias prolongadas, ya que esto puede llevar a la diafonía entre señales adyacentes. En su lugar, use enrutamiento ortogonal entre capas para reducir el acoplamiento.
- Emparejamiento de Impedancia: Asegúrese de que la impedancia del trazo coincida con la impedancia característica de los componentes conectados.
- Uso de Pares Diferenciales: Para señales de datos de alta velocidad, se recomiendan pares diferenciales, que ayudan a cancelar la EMI y reducir la pérdida de señal.
Mejora de la Gestión Térmica: Los PCBs HDI pueden generar considerable calor que, si no se maneja adecuadamente, puede degradar el rendimiento y acortar la vida útil de los componentes. Las estrategias efectivas de gestión térmica incluyen:
- Vías Térmicas: Colocar vías térmicas debajo de componentes que generan calor ayuda a disipar el calor dirigiéndolo a otras capas o a un disipador de calor externo.
- Disipadores de Calor y Almohadillas Térmicas: Incorporar disipadores de calor o almohadillas térmicas puede retirar el calor eficientemente de componentes críticos.
- Grosor del Cobre: Aumentar el grosor del cobre en las capas de potencia y tierra ayuda a distribuir el calor de manera más efectiva.
- Colocación de Componentes: Distribuya los componentes que generan calor uniformemente en la placa para evitar puntos calientes localizados.
En conclusión, diseñar PCBs HDI requiere una atención cuidadosa a los detalles y un enfoque estratégico para la disposición, integridad de la señal y gestión térmica. Siguiendo estas pautas y utilizando herramientas avanzadas de diseño, los ingenieros pueden crear PCBs HDI de alto rendimiento y fiabilidad.
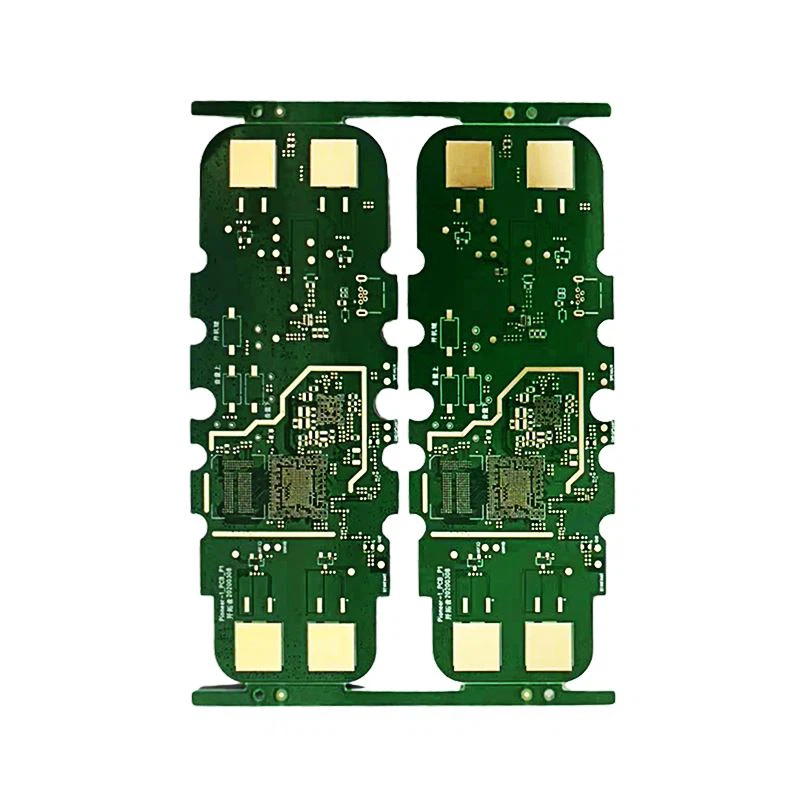
Capítulo 7
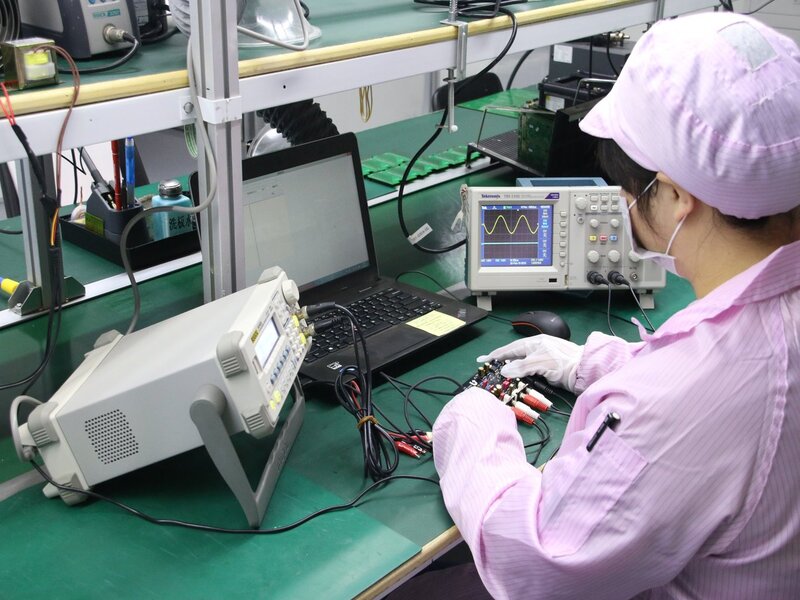
Control de Calidad y Pruebas para PCB HDI
El control de calidad y las pruebas son aspectos críticos de la producción de PCB HDI, ya que garantizan que el producto final cumpla con los altos estándares requeridos para el rendimiento, la fiabilidad y la durabilidad. Debido a la complejidad y densidad de los diseños HDI, son necesarios rigurosos protocolos de prueba para detectar y abordar cualquier defecto en las primeras etapas del proceso de fabricación. Esto ayuda a prevenir fallos costosos y asegura que el PCB funcione como se espera en aplicaciones exigentes como telecomunicaciones, aeroespacial y dispositivos médicos. A continuación, se describen los procesos esenciales de control de calidad y los métodos de prueba en la producción de PCB HDI.
Procesos Esenciales de Control de Calidad en la Producción de PCB HDI
La producción de PCB HDI implica múltiples etapas, cada una de las cuales requiere un estricto control de calidad para mantener alta precisión y consistencia. Las principales medidas de control de calidad incluyen:
- Revisión de Diseño para Fabricabilidad (DFM): Antes de comenzar la producción, una revisión exhaustiva de DFM garantiza que el diseño del PCB esté optimizado para la fabricación. Esta revisión identifica elementos de diseño que podrían ser difíciles o costosos de producir, ayudando a prevenir retrasos o errores en la producción.
- Control de Calidad en Proceso: Durante el proceso de fabricación, se realizan controles de calidad en diversas etapas para detectar problemas antes de que se agraven. Esto incluye inspecciones durante los procesos de perforación, laminado, grabado y recubrimiento para garantizar que las vías, trazos y capas estén alineados correctamente y cumplan con las especificaciones requeridas.
- Aseguramiento de la Calidad de los Materiales: Los materiales utilizados en la producción de PCB HDI, como el cobre, los laminados y el prepreg, se prueban cuidadosamente para asegurar su calidad. Esto garantiza que cumplan con los estándares necesarios para el rendimiento eléctrico, la estabilidad térmica y la resistencia mecánica.
Tipos de Pruebas
Se emplean varios métodos avanzados de prueba en la fabricación de PCB HDI para verificar su funcionalidad, detectar defectos y asegurar la calidad general. Algunos de los métodos de prueba más comunes incluyen:
- Prueba Eléctrica (ET): La prueba eléctrica garantiza que el PCB HDI funcione como se espera, verificando la continuidad de todas las conexiones eléctricas y detectando cortocircuitos o circuitos abiertos.
- Inspección Óptica Automatizada (AOI): AOI utiliza cámaras de alta resolución para inspeccionar automáticamente la superficie del PCB y detectar defectos.
- Inspección por Rayos X: La inspección por rayos X es especialmente importante para los PCB HDI, ya que permite ver las conexiones ocultas dentro de las capas de la placa, como las vías enterradas.
- Prueba de Soldabilidad: Garantiza que el acabado de la superficie del PCB HDI, como ENIG o OSP, proporcione la soldabilidad adecuada para el ensamblaje de componentes.
- Pruebas de Ciclos Térmicos y Resistencia al Estrés: Los PCB HDI a menudo se someten a ciclos térmicos para simular las variaciones de temperatura que experimentarán en aplicaciones reales.
Cómo Garantizar la Fiabilidad y Durabilidad de los PCB HDI
Dada la importancia de los PCB HDI, asegurar su fiabilidad y durabilidad es esencial. Los fabricantes emplean varias técnicas para mejorar la longevidad de los PCB HDI y minimizar el riesgo de fallos durante la operación:
- Materiales de Primera Calidad: El uso de materiales de alta calidad, como poliimida, laminados de alto rendimiento y capas de cobre más gruesas, mejora la durabilidad de los PCB HDI.
- Integridad de las Vías: Asegurar la formación adecuada de las vías es crucial para la fiabilidad de los PCB HDI. Procesos como el relleno de vías y el recubrimiento de cobre mejoran la resistencia mecánica de las microvías.
- Diseño de Gestión Térmica: Los PCB HDI con alta densidad de componentes son propensos a acumular calor, lo que puede degradar el rendimiento. Diseñar el PCB con características adecuadas de gestión térmica ayuda a disipar el calor de manera eficiente y previene puntos calientes.
- Pruebas Ambientales: Los PCB HDI diseñados para aplicaciones críticas a menudo se someten a pruebas ambientales para asegurar que puedan soportar las condiciones en el mundo real.
- Monitoreo Continuo y Retroalimentación: Muchos fabricantes implementan sistemas de monitoreo continuo que recogen datos de cada lote de producción.
En conclusión, el control de calidad y las pruebas son esenciales para asegurar la funcionalidad, fiabilidad y durabilidad de los PCB HDI.
Capítulo 8
Consideraciones de Costos para PCB HDI
Cuando planea producir PCB HDI, es necesario considerar el costo. El costo puede variar dependiendo de la complejidad del diseño, los materiales que utilice y los procesos de fabricación. Si comprende estos factores, puede tomar decisiones informadas sobre cómo equilibrar el costo y la calidad.
Factores que afectan el costo de los PCB HDI
El costo de los PCB HDI depende de varios factores, muchos de los cuales están relacionados con la complejidad del diseño y los procesos necesarios para fabricarlos. Estos son los principales factores que afectan el costo:
- Número de capas: Cuantas más capas tenga un PCB HDI, más costoso será de fabricar.
- Tecnología de vías: El tipo y la cantidad de vías que use afectan el costo. Las microvías, vías ciegas y vías enterradas requieren procesos avanzados.
- Materiales: Los materiales de alta calidad, como poliimida, laminados con cerámica o sustratos de alta temperatura, son más costosos.
- Acabados de superficie avanzados: Los PCB HDI a menudo necesitan acabados especiales para facilitar la soldadura.
- Tamaño y forma de la placa: Las placas pequeñas pueden ser más costosas por unidad de área.
- Pruebas y garantía de calidad: Los PCB HDI requieren métodos avanzados de prueba, como inspección por rayos X, AOI y pruebas eléctricas.
Cómo los PCB HDI pueden ahorrar dinero en producción a gran escala
Aunque inicialmente la producción de PCB HDI puede ser más costosa debido a la tecnología avanzada, se pueden obtener ahorros significativos en la producción en masa:
- Economías de escala: A medida que se fabrican más unidades, el costo por unidad disminuye.
- Menos componentes: Los PCB HDI permiten integrar más componentes en una sola placa, lo que reduce la necesidad de conexiones.
- Tamaño más pequeño: Con PCB HDI, se pueden hacer dispositivos más pequeños, lo cual puede ahorrar costos.
- Mayor fiabilidad: Los PCB HDI son más confiables, lo que reduce los fallos.
Cómo equilibrar el costo y la calidad al comprar PCB HDI
Encontrar el equilibrio adecuado entre costo y calidad es fundamental:
- Trabaje con el fabricante: Colabore con el fabricante desde el principio.
- Diseñe correctamente: Optimice el diseño de su PCB HDI.
- Encuentre un buen proveedor: Busque un proveedor con experiencia en PCB HDI.
- Compre en volumen: Comprar grandes cantidades puede reducir el costo por unidad.
- Realice prototipos: Antes de producir en masa, haga prototipos para verificar el diseño.
En conclusión, aunque los PCB HDI pueden ser costosos al principio, pueden ahorrar dinero a largo plazo debido a su fiabilidad, tamaño compacto y costo reducido en grandes cantidades. Para equilibrar costo y calidad, diseñe correctamente, trabaje con un buen fabricante y tome decisiones inteligentes sobre materiales y cantidades.
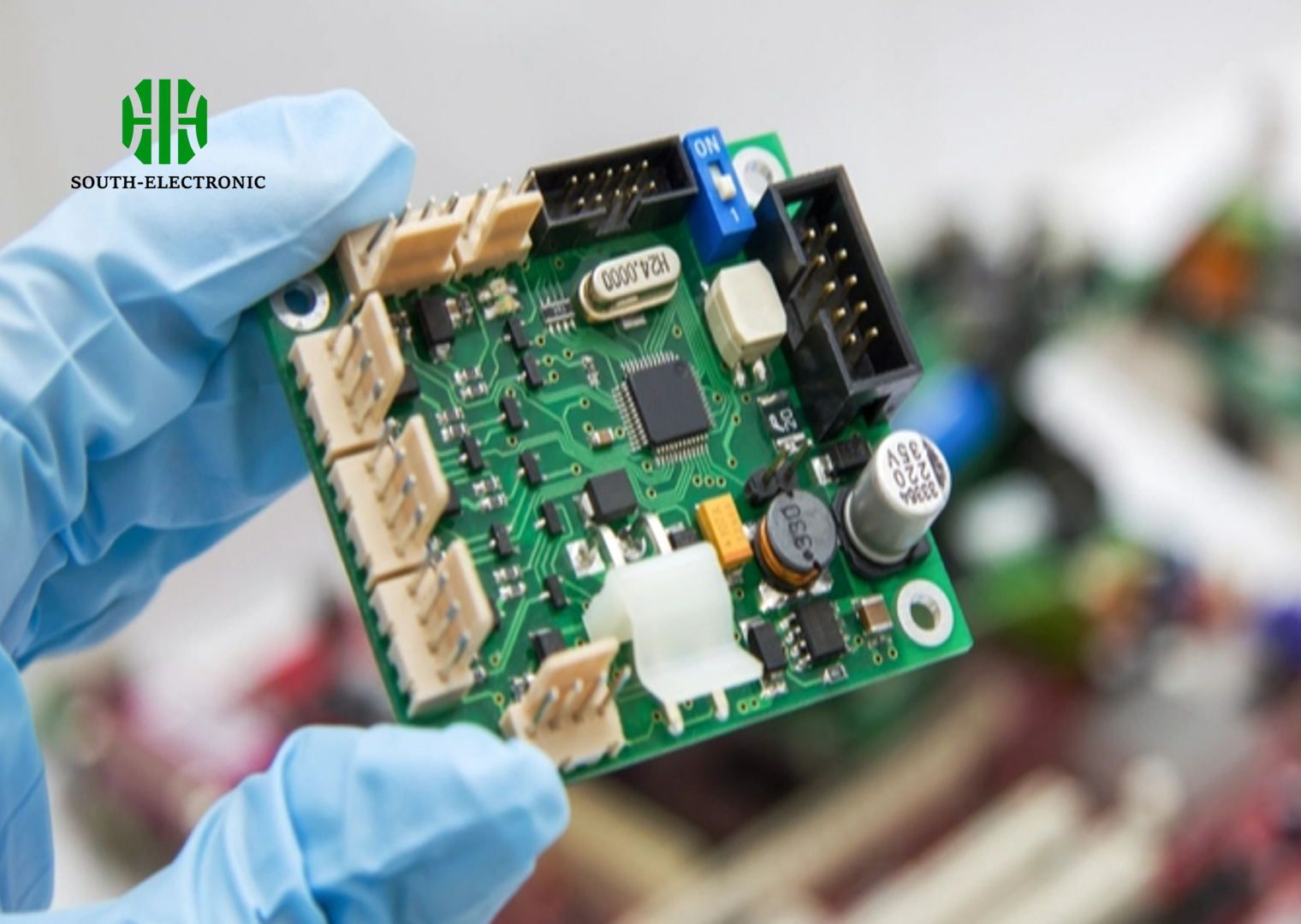
Capítulo 9

Ventajas de los PCB HDI sobre los PCB Convencionales
Los PCB HDI (Interconexión de Alta Densidad) son mejores que los PCB tradicionales en muchos aspectos, especialmente cuando se necesita más rendimiento, un tamaño más pequeño y mayor fiabilidad.
- Más Componentes: Los PCB HDI permiten colocar más componentes en un espacio más reducido mediante el uso de microvías, vías ciegas y vías enterradas, lo que facilita diseños más complejos y compactos en comparación con los PCB convencionales. Esto es muy importante para dispositivos con espacio limitado.
- Más Pequeños: Los PCB HDI permiten fabricar placas más pequeñas y ligeras. Esto es esencial en dispositivos como smartphones, wearables y en el sector aeroespacial, donde el tamaño y el peso son cruciales.
- Mejores Señales: Los PCB HDI mejoran la señal ya que los caminos de las señales son más cortos, reduciendo la interferencia electromagnética (EMI) y la diafonía. Esto es vital en aplicaciones de alta velocidad, como 5G, centros de datos y telecomunicaciones.
- Mejor Gestión Térmica: Los PCB HDI disipan mejor el calor gracias a las vías térmicas y mejores diseños, lo que permite que soporten aplicaciones de alta potencia sin calentarse demasiado y aumentando su durabilidad.
- Mayor Fiabilidad: Los PCB HDI son más fiables gracias a sus vías apiladas y materiales de alta calidad, lo que los hace menos propensos a fallar en automóviles, aviones y aplicaciones militares.
- Más Rápidos: Los PCB HDI permiten velocidades mayores, ya que las señales tienen que recorrer menos distancia. Esto los hace ideales para telecomunicaciones, redes y computadoras de alta velocidad.
- Más Opciones: Los PCB HDI ofrecen más opciones ya que se pueden apilar más capas y utilizar diferentes tipos de vías, lo cual es útil para diseños complejos y personalizados en el sector médico y de consumo.
- Más Económicos: Aunque los PCB HDI son más costosos al inicio, se vuelven más económicos en producción masiva, ya que permiten una mayor eficiencia y pueden integrar más componentes en una sola placa, reduciendo los costos del sistema completo.
En conclusión, los PCB HDI son mejores porque son más pequeños, rápidos y fiables, y se pueden utilizar en muchos sectores, como telecomunicaciones, aeroespacial, automoción y consumo.
Capítulo 10
El Futuro de la Tecnología de PCB HDI
A medida que la tecnología sigue avanzando, los PCB HDI continuarán haciéndose más pequeños, rápidos y potentes. A continuación, algunos de los cambios que podemos esperar ver:
- La Tecnología HDI Está Evolucionando: Los PCB HDI se están volviendo más complejos, con diseños de múltiples pasos, empaques 3D y tecnología de sistema en paquete (SiP). Esto nos permite incluir más funciones en un espacio más pequeño y mejorar el rendimiento.
- Nuevos Materiales y Técnicas: Estamos comenzando a usar nuevos materiales como sustratos flexibles y laminados de alta frecuencia (como PTFE). También estamos usando técnicas como la imagen directa por láser (LDI) y tecnologías avanzadas de vías. Esto nos permite hacer trazos más pequeños, gestionar mejor el calor e integrar más en un espacio reducido.
- PCB HDI en el Internet de las Cosas (IoT), Inteligencia Artificial (IA) y 5G: Los PCB HDI serán clave para los dispositivos IoT, ya que necesitan ser pequeños y consumir poca energía. También serán importantes para sistemas de IA y computación en el borde, que necesitan procesar datos rápidamente. Además, jugarán un papel importante en redes 5G, ya que pueden manejar señales de alta frecuencia y hacer que las estaciones base sean más compactas.
- PCB HDI y Empaque de Semiconductores: Los PCB HDI comenzarán a trabajar con nuevos tipos de empaques de semiconductores, como el empaquetado de nivel de oblea de abanico (FO-WLP) y sistema en paquete (SiP). Esto permitirá fabricar dispositivos más pequeños y rápidos.
- Sostenibilidad: Cada vez nos importa más el medio ambiente, por lo que estamos usando soldadura sin plomo, laminados sin halógenos y materiales reciclables. Queremos asegurarnos de no dañar el planeta.
En conclusión, los PCB HDI seguirán impulsando las revoluciones de IoT, IA y 5G. Y continuarán mejorando con nuevos materiales, empaques y métodos para cuidar el planeta.
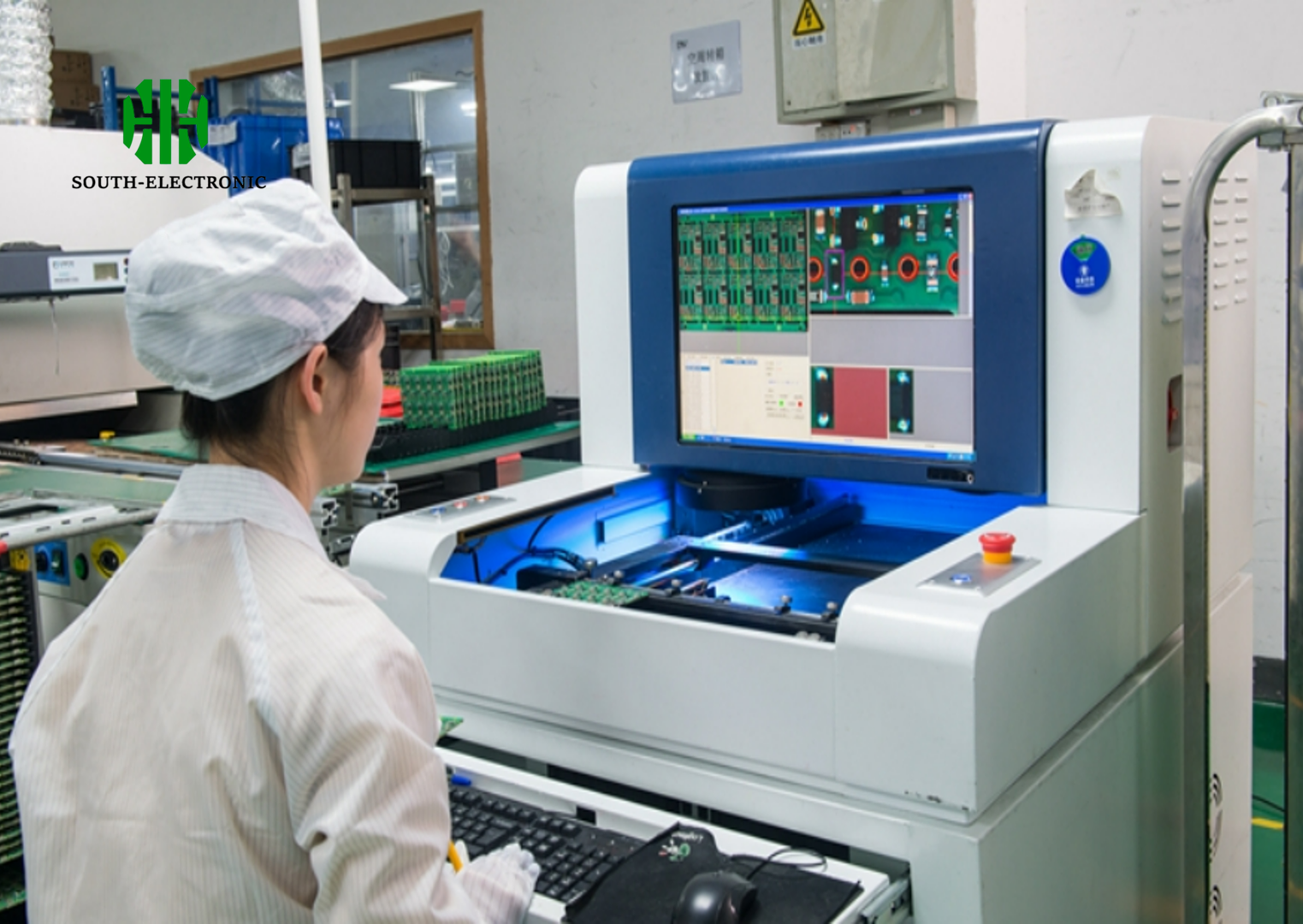
Póngase en Contacto
¿Dónde Estamos?
Parque Industrial, No. 438 Donghuan Road, No. 438, Shajing Donghuan Road, Distrito de Bao'an, Shenzhen, Guangdong, China
Cuarto Piso, Edificio Creativo Zhihui, No.2005 Xihuan Road, Shajing, Distrito de Baoan, Shenzhen, China
Habitación A1-13, Tercer Piso, Centro Industrial Yee Lim, 2-28 Calle Kwai Lok, Kwai Chung, HK
service@southelectronicpcb.com
Teléfono: +86 400 878 3488
Envíanos un mensaje
Cuanto más detallado completes, más rápido podremos avanzar al siguiente paso.
