Proveedor de PCB Multicapa
South-Electronic
Elija South-Electronic para obtener calidad, fiabilidad y un valor excepcional sin igual en sus soluciones de PCB. Experimente la diferencia con nuestro servicio integral de PCB multicapa: desde el diseño hasta la entrega, garantizamos precisión, durabilidad y cumplimiento con los estándares más exigentes de la industria.
¿Por qué elegir South-Electronic?
Obtenga las mejores soluciones de PCB multicapa con South-Electronic. Personalizamos sus PCBs, aseguramos la máxima calidad, las entregamos rápidamente y ofrecemos un precio excelente. Solicite una cotización ahora y compruebe nuestra fiabilidad.
-
Flexibilidad en los Pedidos
Personalizado según sus necesidades específicas, disfrute de flexibilidad con nosotros.
Ya sea que necesite un pedido mínimo de solo una unidad o una producción a gran escala, ofrecemos cantidades flexibles para satisfacer los requisitos específicos de su proyecto. -
Equipo Experimentado
Usted se beneficia de la experiencia de nuestros profesionales con más de una década de trayectoria.
Con más de diez años de experiencia, nuestro equipo dedicado tiene un profundo conocimiento de la industria para ofrecerle soluciones de PCB de alta calidad. -
Control de Calidad Estricto
Cada PCB que reciba se fabrica bajo estrictos estándares de control de calidad.
Con certificaciones como UL, CE, IATF16949 e ISO13485, cada PCB que producimos pasa por un riguroso control de calidad. -
Entrega Rápida
Ahorre tiempo y mantenga su proyecto en marcha.
Con nuestro proceso de producción optimizado, disfrutará de entregas rápidas sin comprometer la calidad, ayudándole a cumplir con plazos ajustados sin esfuerzo. -
Soporte de por Vida
Siéntase seguro con nuestro servicio postventa de por vida.
Incluso después de la entrega, puede contar con nosotros para obtener soporte continuo durante toda la vida útil de su producto, brindándole tranquilidad a largo plazo.
Proyecto Relacionado que Hemos Realizado
Opiniones de los Clientes
Preguntas Frecuentes
Preguntas Más Populares
¡Sí! South-Electronic ofrece soluciones totalmente personalizadas de PCBs multicapa, adaptadas a sus requisitos específicos, asegurando el mejor ajuste para sus aplicaciones.
¡Por supuesto! South-Electronic proporciona servicios de prototipado, permitiéndole probar y perfeccionar sus diseños antes de pasar a la producción en masa.
South-Electronic ofrece pedidos flexibles con una cantidad mínima de pedido (MOQ) a partir de solo una unidad, lo que lo hace ideal tanto para prototipos como para producción a gran escala.
Puede realizar un pedido fácilmente contactando a South-Electronic a través de su sitio web o correo electrónico. Una vez discutidos sus requisitos, le proporcionarán una cotización y lo guiarán a lo largo de todo el proceso.
South-Electronic cuenta con certificaciones como UL, CE, IATF16949 e ISO13485, garantizando que sus PCBs cumplan con los más altos estándares internacionales de calidad.
Envíanos un mensaje
Cuanto más detallado completes, más rápido podremos avanzar al siguiente paso.
Guía Completa para PCB Multicapa
Contenido
Capítulo 1
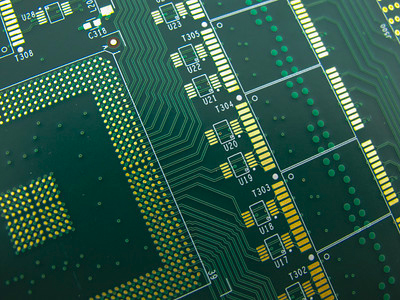
Introducción a los PCB Multicapa
¿Qué es un PCB Multicapa?
Un PCB Multicapa es una placa de circuito impreso que tiene tres o más capas de material conductor (generalmente cobre) separadas por capas aislantes. Estas capas se apilan y laminan juntas, creando una placa compacta y de alta densidad utilizada para circuitos electrónicos complejos. A diferencia de los PCB de una o dos capas, que tienen un espacio limitado para el ruteo, los PCB multicapa permiten diseños de circuitos más intrincados al ofrecer múltiples capas conductoras que se interconectan a través de vías (conexiones verticales entre las capas). Esto da como resultado un mayor rendimiento, una mayor funcionalidad y una reducción de los requisitos de espacio en los dispositivos electrónicos.
Historia y evolución de los PCB Multicapa
El concepto de los PCB multicapa surgió a finales de los años 60, cuando la electrónica se volvió más avanzada y la miniaturización se convirtió en una prioridad, especialmente en las industrias aeroespacial y de telecomunicaciones. Los primeros PCB solo tenían una o dos capas, lo que limitaba la complejidad de los circuitos que se podían diseñar. La necesidad de una mayor densidad de circuitos, un mejor rendimiento y una mayor fiabilidad llevó al desarrollo de los PCB multicapa. Con el tiempo, las innovaciones en materiales, técnicas de fabricación y software de diseño han permitido que los PCB multicapa se vuelvan comunes en la electrónica de consumo, dispositivos médicos, sistemas automotrices y más. Hoy en día, los PCB multicapa pueden tener más de 50 capas en algunas aplicaciones de alta gama, permitiendo diseños increíblemente complejos y potentes.
Importancia y aplicaciones en la electrónica moderna
Los PCB multicapa se han convertido en una piedra angular de los dispositivos electrónicos modernos porque pueden acomodar componentes de alta densidad y circuitos complejos en una forma compacta. Su importancia radica en su capacidad para ofrecer un mejor rendimiento en términos de integridad de señal, reducción de ruido y protección contra interferencias electromagnéticas (EMI) en comparación con las placas de una o dos capas. Esto los hace esenciales en industrias donde la precisión, la velocidad y la fiabilidad son críticas.
- Telecomunicaciones: Utilizados en routers, switches y sistemas satelitales donde la transmisión de datos a alta velocidad y la fiabilidad son cruciales.
- Electrónica de consumo: Presentes en smartphones, laptops y wearables, donde se requieren diseños compactos y funcionalidad mejorada.
- Automotriz: Utilizados en sistemas avanzados de asistencia al conductor (ADAS), sistemas de infoentretenimiento y sistemas de control de potencia que demandan durabilidad y rendimiento.
- Dispositivos médicos: Esenciales para dispositivos como marcapasos, equipos de imagen y herramientas de diagnóstico que requieren alta precisión y fiabilidad.
- Aeroespacial y defensa: Los PCB multicapa brindan soporte crítico en sistemas que requieren robustez, fiabilidad y rendimiento bajo condiciones extremas.
En resumen, los PCB multicapa son vitales para permitir el avance de la tecnología en diversas industrias, apoyando la creciente demanda de dispositivos electrónicos más pequeños, rápidos y eficientes.
Capítulo 2
Estructura de un PCB Multicapa
Capas en los PCB Multicapa
Un PCB multicapa está compuesto por varias capas de materiales que trabajan juntas para formar una placa de circuito funcional. Las principales capas en un PCB multicapa son:
- Capas de Cobre: Estas son las capas conductoras que transportan señales eléctricas. En un PCB multicapa, hay múltiples capas de cobre apiladas una sobre otra, separadas por capas aislantes. Estas capas de cobre forman las pistas que conectan varios componentes y permiten la transmisión de señales. El número de capas de cobre depende de la complejidad del diseño del PCB, y generalmente son muy delgadas pero altamente conductoras para garantizar un flujo de señal eficiente.
- Sustrato (Núcleo): El sustrato es la base del PCB. Generalmente está hecho de materiales como FR-4 (un material compuesto de fibra de vidrio tejida y resina epoxi) u otros materiales especializados como el poliimida para aplicaciones de alta temperatura. El sustrato proporciona soporte mecánico a la placa y actúa como una capa aislante entre las capas de cobre.
- Aislamiento (Capas Dieléctricas): Estas capas separan las capas de cobre y evitan cortocircuitos eléctricos entre ellas. El aislamiento generalmente está hecho de materiales como prepreg (fibras compuestas preimpregnadas) u otros tipos de epoxi no conductores. Este material aislante no solo separa las capas conductoras, sino que también contribuye a la durabilidad de la placa y a su capacidad de resistir factores ambientales como el calor, la humedad y la vibración.
La alternancia de capas de cobre y aislamiento continúa a lo largo del PCB, creando una estructura apilada que permite un enrutamiento complejo de señales en un espacio compacto.
Explicación de las Capas Internas y Externas
En un PCB multicapa, las capas internas y externas tienen funciones diferentes:
- Capas Externas: Son las capas superior e inferior del PCB. Las capas externas suelen contener la mayoría de las pistas de señal que se conectan a los componentes externos a través de almohadillas de soldadura y vías. Estas capas están generalmente protegidas por una máscara de soldadura que evita contactos no intencionales con materiales conductores. Las capas externas son cruciales para la colocación de componentes, permitiendo montar dispositivos de montaje superficial (SMD) o componentes de orificio pasante durante el ensamblaje.
- Capas Internas: Las capas internas están ubicadas entre las capas externas y se utilizan principalmente para enrutar señales, proporcionar energía y conexión a tierra. Estas capas desempeñan un papel fundamental en la gestión de la integridad de la señal y la distribución de energía. Por ejemplo, una o más capas internas pueden dedicarse a planos de alimentación (que distribuyen energía a diferentes partes del circuito) o planos de tierra (que reducen el ruido y las interferencias electromagnéticas al proporcionar un punto de referencia para las señales). Las capas internas permiten un enrutamiento eficiente de circuitos complejos sin saturar las capas externas, lo cual es esencial en diseños de alta densidad.
La combinación de capas internas y externas en un PCB multicapa proporciona la flexibilidad necesaria para diseñar circuitos complejos con múltiples componentes, garantizando que las señales se enruten correctamente y que la energía se distribuya de manera efectiva.
Tipos de Vías
Las vías son pequeños orificios metalizados que conectan diferentes capas en un PCB multicapa. Según su diseño, las vías se clasifican en tres tipos principales:
- Vías Pasantes: Son el tipo más común de vías. Una vía pasante atraviesa todas las capas del PCB, conectando la capa superior con la inferior y todas las capas internas intermedias. Se utilizan cuando se necesita una conexión a través de todo el grosor del PCB. Aunque son fáciles de fabricar, pueden ocupar espacio valioso en la placa que podría usarse para la colocación de componentes o el enrutamiento de señales.
- Vías Ciegas: Las vías ciegas conectan una capa externa con una o más capas internas, pero no atraviesan completamente la placa. Se utilizan para aumentar el área de enrutamiento disponible, especialmente en diseños de alta densidad, sin ocupar espacio en la capa externa opuesta. Las vías ciegas permiten diseños más compactos al conectar las capas superficiales con las internas sin interferir en toda la placa.
- Vías Enterradas: Las vías enterradas se utilizan para conectar dos o más capas internas sin extenderse a las capas externas. Están completamente ocultas dentro de la estructura de la placa y se emplean cuando se requiere un enrutamiento complejo, permitiendo que las capas externas se reserven para componentes superficiales. Las vías enterradas aumentan las capacidades de enrutamiento de las capas internas, pero también pueden añadir complejidad al proceso de fabricación del PCB.
Cada tipo de vía desempeña un papel crucial en garantizar que las señales y la energía se muevan eficientemente entre las diferentes capas de un PCB multicapa. El uso estratégico de estas vías es vital para el diseño y el rendimiento general de la placa, especialmente en circuitos complejos y de alta velocidad, donde la integridad de la señal y la optimización del espacio son fundamentales.
Al comprender la estructura y el propósito de cada capa y tipo de vía en un PCB multicapa, los diseñadores pueden optimizar la placa para rendimiento, eficiencia espacial y durabilidad en diversas aplicaciones.
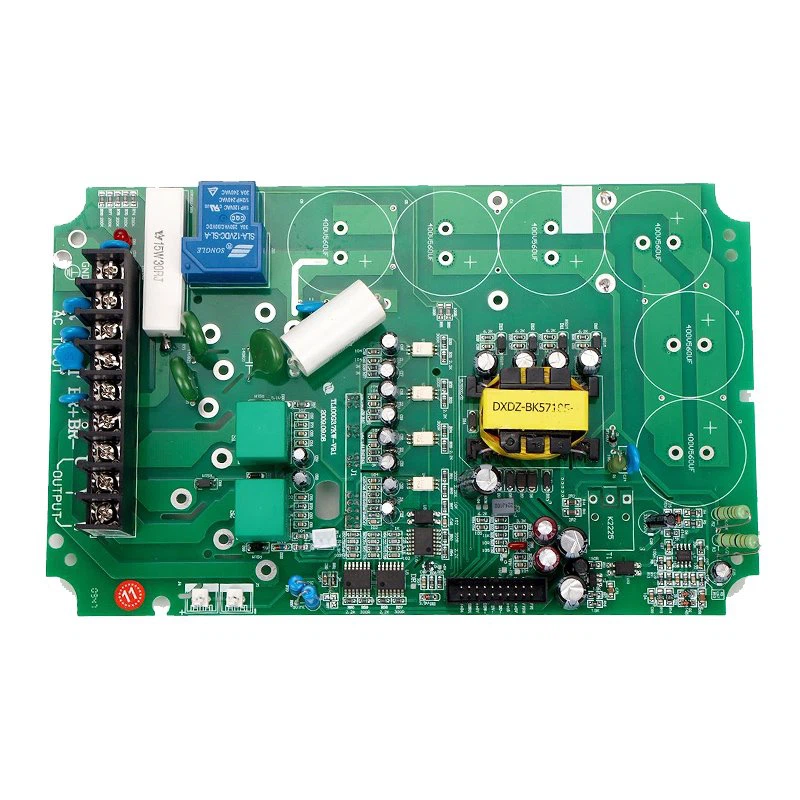
Capítulo 3
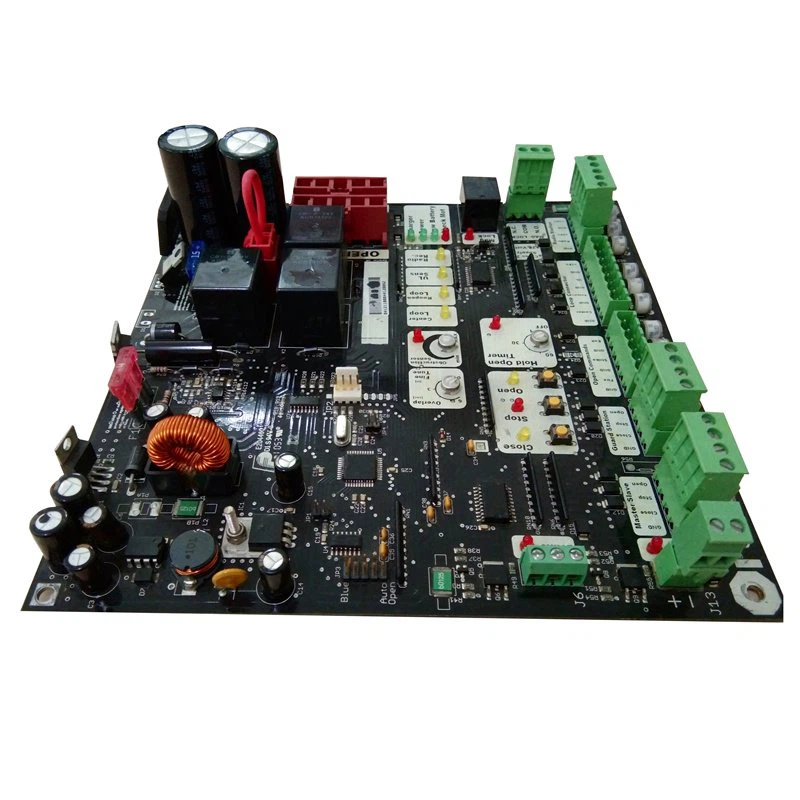
Beneficios de los PCB Multicapa
Los PCB multicapa ofrecen numerosas ventajas sobre las placas de una y dos capas, lo que los convierte en una opción preferida para sistemas electrónicos complejos. A continuación, se detallan algunos de sus principales beneficios:
Diseño Compacto y Eficiencia Espacial
Uno de los beneficios más significativos de los PCB multicapa es su diseño compacto y el uso eficiente del espacio. Al apilar múltiples capas de circuitos en la misma placa, los PCB multicapa reducen significativamente el tamaño general del dispositivo, manteniendo o incluso aumentando su funcionalidad. Esta compacidad es esencial en el panorama tecnológico actual, donde los dispositivos electrónicos son cada vez más pequeños y livianos, especialmente en industrias como la electrónica de consumo, la aeroespacial y la médica.
- Optimizado para Dispositivos Más Pequeños: Los PCB multicapa permiten a los fabricantes diseñar productos como smartphones, tabletas, wearables y laptops con un alto rendimiento sin aumentar su tamaño físico. Estos dispositivos requieren circuitos complejos que solo se pueden lograr eficientemente a través de diseños multicapa.
- Solución que Ahorra Espacio: Al integrar múltiples capas de circuitos en una sola placa, los PCB multicapa reducen la necesidad de placas más grandes o de múltiples PCB en un dispositivo, ahorrando espacio y minimizando la huella total del producto.
La capacidad de empaquetar más funcionalidad en un espacio reducido sin comprometer el rendimiento es una ventaja crítica de los PCB multicapa, especialmente en la industria electrónica moderna.
Mejor Rendimiento e Integridad de Señal
Los PCB multicapa ofrecen un rendimiento eléctrico superior en comparación con sus contrapartes de una o dos capas. Esto se debe principalmente al uso de capas internas dedicadas para planos de alimentación y tierra, así como al diseño cuidadoso de las rutas de señal a través de múltiples capas. Estas características de diseño ayudan a mantener la integridad de la señal y minimizar las interferencias, lo cual es crucial en aplicaciones de alta velocidad y alta frecuencia.
- Reducción de Interferencias Electromagnéticas (EMI): Los PCB multicapa permiten a los diseñadores incorporar planos de tierra entre las capas de señal, que actúan como escudos, reduciendo las EMI y el acoplamiento entre señales. Esto es particularmente importante en dispositivos como equipos de telecomunicaciones, servidores y centros de datos, donde la transmisión de datos a alta velocidad requiere señales limpias y libres de interferencias.
- Integridad de Señal Mejorada: En los diseños multicapa, las señales pueden ser enrutadas de manera que la impedancia se controle, minimizando la degradación de la señal a lo largo de largas distancias. Esto resulta en una transmisión de señales más precisa, especialmente en circuitos de alta frecuencia utilizados en dispositivos de comunicación, equipos médicos y electrónica automotriz.
- Baja Inductancia y Capacitancia: Los PCB multicapa tienen menor inductancia y capacitancia parasitaria debido a la proximidad de los planos de alimentación y tierra. Esto mejora el rendimiento general del circuito, haciéndolo ideal para aplicaciones que requieren procesamiento de datos a alta velocidad o transmisión de señales de alta frecuencia.
Estas mejoras en el rendimiento y la integridad de la señal hacen que los PCB multicapa sean una opción superior para la electrónica moderna, donde la velocidad, la precisión y la fiabilidad son fundamentales.
Mayor Densidad de Componentes y Manejo de la Complejidad
Otro beneficio importante de los PCB multicapa es su capacidad para manejar una mayor densidad de componentes y diseños de circuitos más complejos. Con más capas disponibles para el enrutamiento, los diseñadores tienen mayor flexibilidad para colocar componentes en posiciones óptimas, mejorando la funcionalidad y la eficiencia general de la placa.
- Mayor Complejidad de Circuitos: Los PCB multicapa son esenciales para soportar circuitos complejos con un gran número de interconexiones, lo que sería imposible de lograr con placas de una o dos capas. Esto es especialmente importante en aplicaciones avanzadas como sistemas aeroespaciales, maquinaria industrial y dispositivos médicos, donde se requieren funcionalidades sofisticadas.
- Colocación Eficiente de Componentes: Las múltiples capas en un PCB multicapa permiten un enrutamiento más eficiente de las pistas, liberando espacio en la superficie de la placa para más componentes. Esto es crucial en dispositivos compactos donde el área superficial es limitada, pero los requisitos de funcionalidad son elevados. Por ejemplo, en smartphones o dispositivos IoT, cada milímetro cuadrado de espacio es importante, y los PCB multicapa ayudan a maximizar el uso del espacio disponible.
- Mejor Gestión del Calor: El mayor número de capas en un PCB multicapa también ayuda a la disipación del calor. Los planos de alimentación y tierra pueden actuar como disipadores de calor, distribuyendo el calor de manera más uniforme en la placa y evitando puntos calientes. Esto resulta en un dispositivo más fiable y de mayor duración, especialmente en aplicaciones que generan una cantidad significativa de calor, como la electrónica de potencia o los sistemas automotrices.
La capacidad de manejar circuitos complejos y componentes densamente empaquetados hace que los PCB multicapa sean ideales para dispositivos electrónicos avanzados y de alto rendimiento. Esta capacidad garantiza que los diseñadores puedan seguir innovando y ampliando los límites de lo posible en la electrónica moderna.
En resumen, los PCB multicapa ofrecen claras ventajas en términos de eficiencia espacial, mejor rendimiento y capacidad para manejar diseños complejos. Estos beneficios los hacen esenciales en muchas aplicaciones de alta tecnología, permitiendo la creación de dispositivos electrónicos compactos, potentes y fiables. Ya sea en electrónica de consumo, telecomunicaciones, dispositivos médicos o sistemas automotrices, los PCB multicapa proporcionan la base para la sofisticada tecnología que impulsa la vida moderna.
Capítulo 4
Materiales Utilizados en PCB Multicapa
Los materiales utilizados en los PCB multicapa desempeñan un papel crucial en su rendimiento, durabilidad y adecuación para diversas aplicaciones. La selección de estos materiales se basa en factores como el rendimiento eléctrico deseado, la resistencia térmica y la resistencia mecánica. A continuación, se presenta una descripción general de los materiales comunes y cómo se seleccionan para aplicaciones específicas:
Materiales Comunes: FR4, Poliimida y Rogers
En la construcción de PCB multicapa se utilizan varios materiales, siendo los más comunes FR4, poliimida y Rogers. Cada material tiene propiedades únicas que lo hacen adecuado para diferentes aplicaciones.
- FR4 (Flame Retardant 4): FR4 es el material base más utilizado en la fabricación de PCB debido a su excelente equilibrio entre propiedades mecánicas, eléctricas y térmicas. Está compuesto por una tela de fibra de vidrio tejida impregnada con resina epoxi con propiedades ignífugas. FR4 se usa ampliamente en PCB de propósito general debido a su durabilidad, asequibilidad y buen rendimiento en la mayoría de los dispositivos electrónicos.
Características clave:
- Alta resistencia mecánica
- Buenas propiedades de aislamiento
- Baja absorción de humedad
- Ignífugo (cumple con los estándares UL94-V0)
Aplicaciones: FR4 es ideal para electrónica de consumo, sistemas automotrices y aplicaciones industriales generales. Es un material preferido para la mayoría de los diseños de PCB multicapa que no requieren temperaturas extremadamente altas o rendimiento especializado.
- Poliimida: La poliimida es un material de alto rendimiento utilizado en PCB para aplicaciones exigentes donde la resistencia al calor y la flexibilidad son críticas. A diferencia de FR4, la poliimida es altamente resistente a la degradación térmica, lo que la hace adecuada para aplicaciones que requieren alta estabilidad térmica. Se utiliza a menudo en PCB flexibles y placas rígido-flexibles, donde su flexibilidad permite que la placa se doble sin romperse.
Características clave:
- Excelente estabilidad térmica (puede soportar altas temperaturas)
- Resistencia química superior
- Alta flexibilidad y durabilidad mecánica
- Buenas propiedades de aislamiento eléctrico
Aplicaciones: La poliimida se usa comúnmente en las industrias aeroespacial, militar, dispositivos médicos y equipos industriales de alta temperatura, donde la exposición a condiciones extremas es frecuente. También se emplea en PCB flexibles para dispositivos compactos como smartphones y tecnología portátil.
- Rogers: Rogers es una marca de una familia de materiales para PCB de alto rendimiento y alta frecuencia. Estos materiales son conocidos por su baja constante dieléctrica y baja tangente de pérdida, lo que los hace ideales para aplicaciones de alta frecuencia y microondas. Los materiales Rogers también ofrecen una gestión térmica y estabilidad superiores, siendo populares en circuitos de RF (radiofrecuencia) y microondas.
Características clave:
- Baja constante dieléctrica y tangente de pérdida para integridad de señal de alta frecuencia
- Excelente resistencia al calor
- Rendimiento estable en un amplio rango de temperaturas y frecuencias
- Resistencia superior a la humedad
Aplicaciones: Los materiales Rogers se utilizan típicamente en telecomunicaciones, sistemas satelitales, radares y dispositivos de comunicación inalámbrica, donde la integridad de la señal en altas frecuencias es fundamental. Estos materiales son esenciales en aplicaciones como la tecnología 5G, donde la precisión y la baja pérdida de señal son críticas.
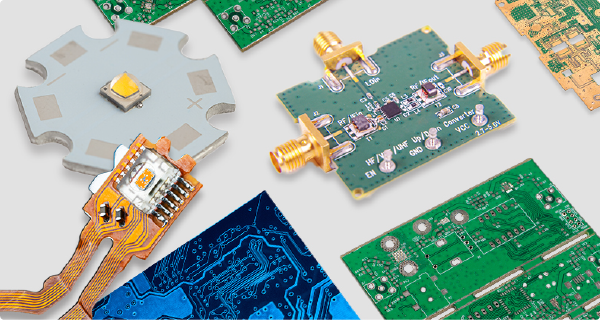
Capítulo 5

Proceso de Fabricación de PCB Multicapa
El proceso de fabricación de PCB multicapa es un procedimiento altamente intrincado y preciso, que asegura que el producto final cumpla con los estándares deseados de rendimiento y fiabilidad. A continuación, se detalla cada una de las etapas clave del proceso de fabricación:
Diseño y Disposición del PCB
El primer paso en el proceso de fabricación es el diseño y la disposición del PCB. Esta fase implica el uso de software especializado, como herramientas CAD (Diseño Asistido por Computadora), para crear un plano detallado del PCB multicapa. El diseño incluye la colocación de todos los componentes, el trazado de las pistas de señal, los planos de alimentación y tierra, así como la disposición de las vías y las almohadillas.
- Diseño de Stackup: Para los PCB multicapa, un aspecto crucial del diseño es el stackup, la disposición de las capas conductoras (cobre) y las capas aislantes (dieléctrico). Los diseñadores eligen el número de capas en función de la complejidad y las necesidades de rendimiento del circuito. Un diseño de stackup adecuado ayuda a mantener la integridad de la señal y minimizar las interferencias.
- Trazado y Colocación de Vías: Los diseñadores deben trazar las señales de manera eficiente a través de las capas, utilizando vías (pasantes, ciegas o enterradas) para conectar las pistas entre diferentes capas. La integridad de la señal, el control de impedancia y las interferencias electromagnéticas (EMI) son consideraciones clave en esta fase.
Una vez finalizado el diseño, se convierte en archivos Gerber, que contienen toda la información necesaria para guiar el proceso de fabricación.
Laminación y Proceso de Construcción de Capas
La laminación y el proceso de construcción de capas es donde se crea físicamente la estructura multicapa del PCB. Este proceso implica la laminación de capas alternadas de cobre y materiales aislantes (prepreg o núcleo) bajo calor y presión para formar un PCB compacto y sólido.
- Impresión de Capas Internas: Cada capa interna del PCB se graba primero con el patrón del circuito. Se aplica un fotorresistente a la superficie de cobre y se utiliza luz UV para transferir el diseño del circuito a la capa. Después de grabar el cobre no deseado, quedan intactas las rutas conductoras deseadas.
- Aplicación de Prepreg: El prepreg (fibras compuestas preimpregnadas) actúa como material aislante entre las capas de cobre. Se colocan hojas de prepreg entre cada capa de cobre grabada. Estas hojas unen las capas durante el proceso de laminación.
- Laminación: Las capas de cobre y prepreg se apilan cuidadosamente en el orden requerido para formar la estructura del PCB multicapa. Este apilamiento se coloca en una prensa, donde se somete a alta temperatura y presión, lo que hace que el prepreg se derrita y una las capas. Una vez enfriado, se solidifica la estructura en una placa unificada.
El proceso de laminación es crucial para garantizar la durabilidad, fiabilidad y estabilidad mecánica del PCB.
Perforación, Recubrimiento y Grabado
Después de laminar las capas, el siguiente paso es crear vías y orificios que permitan conexiones eléctricas entre las diferentes capas y el montaje de componentes. Esto implica perforación, recubrimiento y grabado:
- Perforación: Máquinas de perforación de alta precisión crean orificios para vías pasantes, ciegas y enterradas según lo especificado en el diseño. Estos orificios permiten conexiones entre las diferentes capas del PCB y proporcionan vías para montar componentes en la placa. Se utilizan taladros de alta precisión, a menudo guiados por láser, para garantizar la exactitud de estos pequeños orificios, que pueden tener un diámetro de solo unos pocos micrómetros.
- Recubrimiento: Después de la perforación, las superficies interiores de los orificios se recubren con cobre mediante un proceso llamado recubrimiento químico de cobre. Esto asegura que las vías sean conductoras y puedan establecer conexiones eléctricas entre las diferentes capas. El grosor del recubrimiento se controla cuidadosamente para garantizar la fiabilidad y durabilidad a largo plazo, especialmente en aplicaciones de alto rendimiento.
- Impresión y Grabado de Capas Externas: Similar al proceso de impresión de capas internas, las capas externas se recubren con un fotorresistente, se exponen a luz UV y se graban para crear los patrones de circuito en las capas externas de cobre. El cobre expuesto se graba, dejando las rutas conductoras deseadas para conectar los componentes en la superficie.
Montaje Final y Pruebas
Una vez que la estructura del PCB está completa, comienza la fase final de montaje y pruebas. Esta fase asegura que el PCB sea completamente funcional, esté libre de defectos y esté listo para el montaje de componentes y su uso final.
Aplicación de Máscara de Soldadura: Se aplica una máscara de soldadura a las capas externas para proteger las pistas de cobre de la oxidación, la humedad y la contaminación. La máscara de soldadura también ayuda a evitar puentes de soldadura durante el proceso de montaje de componentes. Generalmente es de color verde, aunque puede ser de otros colores según las especificaciones del cliente.
Impresión de Serigrafía: Se imprime información importante, como etiquetas de componentes, logotipos o números de pieza, en el PCB mediante serigrafía. Esto facilita el montaje y mantenimiento del PCB.
Acabado Superficial: Para proteger las almohadillas de cobre expuestas donde se soldarán los componentes, se aplica un acabado superficial como HASL (Nivelación de Soldadura por Aire Caliente), ENIG (Oro Inmerso en Níquel Electrolítico) o OSP (Preservativo de Soldabilidad Orgánica). Este acabado superficial asegura una buena soldabilidad durante el proceso de montaje de componentes.
Pruebas Eléctricas: El PCB terminado se somete a rigurosas pruebas eléctricas para garantizar que todas las conexiones funcionen correctamente. Las pruebas comunes incluyen:
- Inspección Óptica Automatizada (AOI): Una cámara escanea el PCB para verificar si faltan pistas, hay cortocircuitos o desalineaciones.
- Prueba con Sonda Volante: Sondas tocan la superficie del PCB para comprobar la integridad de cada conexión y verificar si hay cortocircuitos o circuitos abiertos.
- Pruebas Funcionales: El PCB se somete a condiciones reales para garantizar que funcione según lo previsto en su aplicación final.
Una vez que el PCB pasa todas estas pruebas, está listo para el montaje final, donde se montarán los componentes en la placa, o puede ser enviado al cliente para su posterior procesamiento.
Capítulo 6
Consideraciones en el Diseño de PCB Multicapa
Al diseñar un PCB multicapa, es importante tener en cuenta varios factores para lograr un rendimiento óptimo, fiabilidad y facilidad de fabricación. Estos factores incluyen integridad de señal, control de interferencias electromagnéticas (EMI), distribución de energía, puesta a tierra, gestión térmica y diseño del stackup. A continuación, se analizan en detalle estas consideraciones de diseño.
Integridad de Señal y Consideraciones de EMI/EMC
La integridad de señal es crucial en el diseño de PCB multicapa, especialmente en circuitos de alta velocidad y alta frecuencia. Una mala integridad de señal puede provocar corrupción de datos, pérdida de señal o EMI, lo que degrada el rendimiento del PCB. Para mantener una buena integridad de señal y controlar las EMI, los diseñadores deben prestar atención a los siguientes elementos:
- Impedancia Controlada: Las señales de alta velocidad requieren una impedancia bien controlada para evitar reflexiones y distorsiones de señal. Mediante un diseño de stackup cuidadosamente elaborado, se puede controlar la impedancia en capas específicas. Esto generalmente implica una separación precisa entre capas de señal y planos de tierra.
- Igualación de Longitudes de Trazas: En diseños de alta velocidad, las diferencias en las longitudes de las trazas pueden provocar desajustes de temporización entre señales, conocidos como skew. Los diseñadores deben asegurarse de que las trazas de señal, especialmente aquellas que transportan señales críticas de reloj o datos, estén correctamente igualadas en longitud para evitar problemas de temporización.
- Minimización de Crosstalk: El crosstalk ocurre cuando las trazas de señal están demasiado cerca unas de otras, causando interferencia eléctrica entre ellas. Para minimizar el crosstalk, las trazas deben espaciarse adecuadamente y, cuando sea necesario, enrutarse en diferentes capas. Los planos de tierra también ayudan a proteger las señales entre sí, reduciendo el ruido no deseado.
- Compatibilidad Electromagnética (EMC): Un PCB multicapa bien diseñado debe cumplir con los estándares de EMC para reducir la radiación electromagnética que podría interferir con otros dispositivos. Al usar un plano de tierra dedicado y colocar señales de alta velocidad en capas internas entre planos de tierra, se pueden reducir las emisiones de EMI. Las técnicas de blindaje, como el uso de planos de tierra alrededor de trazas sensibles, mejoran aún más el rendimiento de EMC.
El objetivo es crear un diseño que garantice la transmisión de señales con mínima distorsión, ruido o pérdida, lo cual es particularmente importante en aplicaciones de telecomunicaciones, aeroespaciales y automotrices.
Distribución de Energía y Puesta a Tierra
Una distribución de energía y un sistema de puesta a tierra adecuados son esenciales en los diseños de PCB multicapa para garantizar una entrega de voltaje estable y minimizar el ruido eléctrico.
- Planos Dedicados de Energía y Tierra: En los PCB multicapa, es común dedicar capas enteras a planos de energía y tierra. Estos planos proporcionan un camino de baja impedancia para la distribución de energía, reduciendo la caída de voltaje y asegurando que todos los componentes reciban energía estable. Un plano de energía bien diseñado también ayuda a distribuir la corriente de manera uniforme en el PCB, mejorando el rendimiento en circuitos de alta potencia.
- Técnicas de Puesta a Tierra: Un sistema de puesta a tierra robusto es crucial para minimizar el ruido y garantizar la integridad de la señal. El plano de tierra actúa como referencia para las señales y reduce la impedancia del camino de retorno, lo cual es importante para mantener la calidad de la señal. Usar un solo plano de tierra que abarque todo el PCB es la mejor práctica para evitar bucles de tierra y garantizar un punto de referencia consistente para todas las señales.
- Condensadores de Desacoplo: Para mejorar aún más la estabilidad de la energía, se colocan condensadores de desacoplo cerca de los componentes críticos. Estos condensadores actúan como pequeñas unidades de almacenamiento de energía, suavizando las fluctuaciones de voltaje y reduciendo el ruido en los rieles de energía. Su correcta colocación y selección son esenciales para evitar el ruido en la fuente de alimentación, especialmente en diseños de alta velocidad y alta frecuencia.
- Integridad de Energía: Mantener la integridad de energía en los diseños de PCB multicapa asegura que la red de distribución de energía entregue energía limpia y sin ruido a todos los componentes. Una mala integridad de energía puede resultar en caídas de voltaje, acoplamiento de ruido y un comportamiento inestable de los componentes, lo que puede llevar a fallas del sistema.
Centrarse en una distribución eficiente de energía y una puesta a tierra efectiva garantiza niveles de voltaje estables en todo el PCB, lo cual es crítico para un rendimiento fiable.
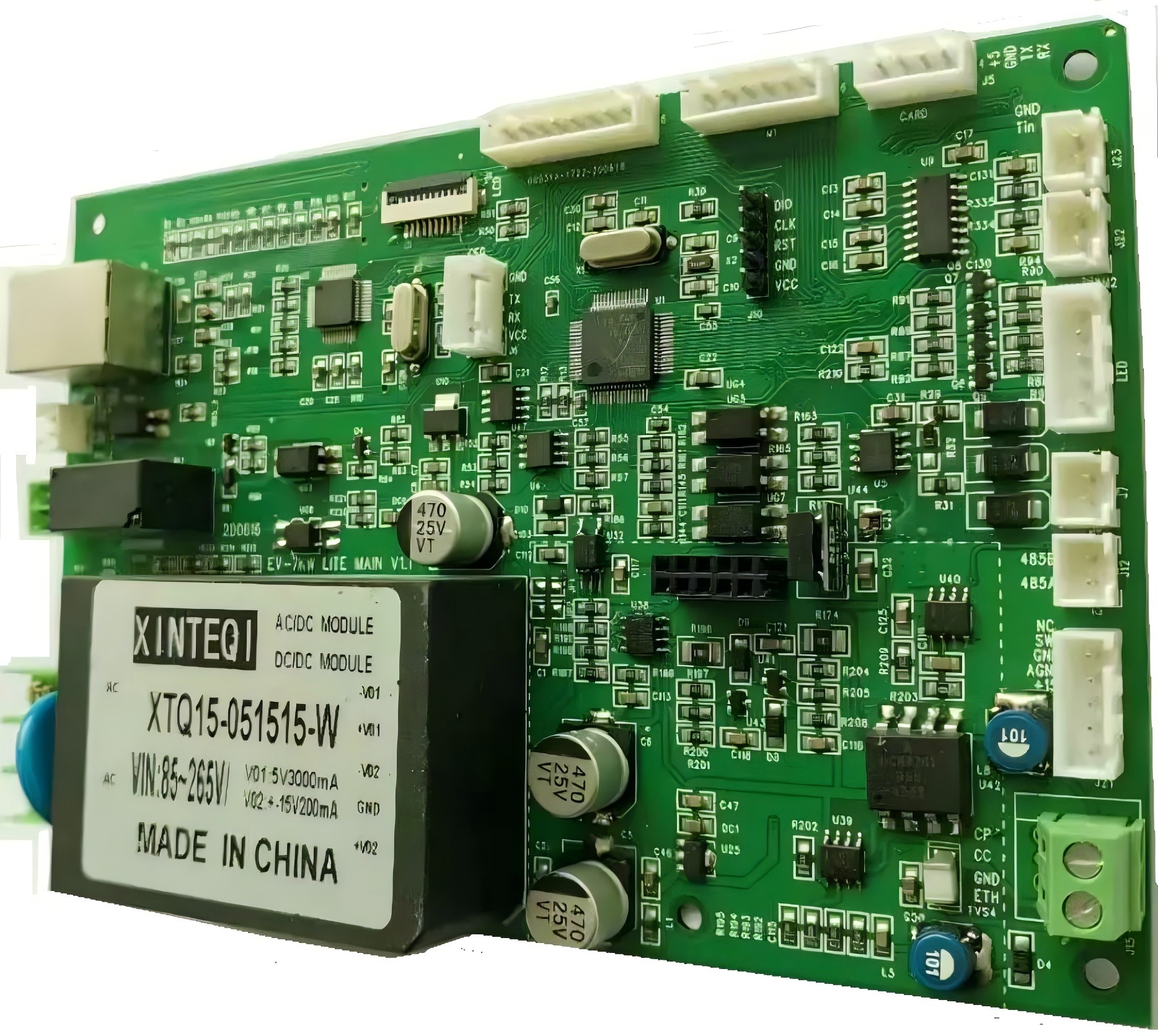
Capítulo 7
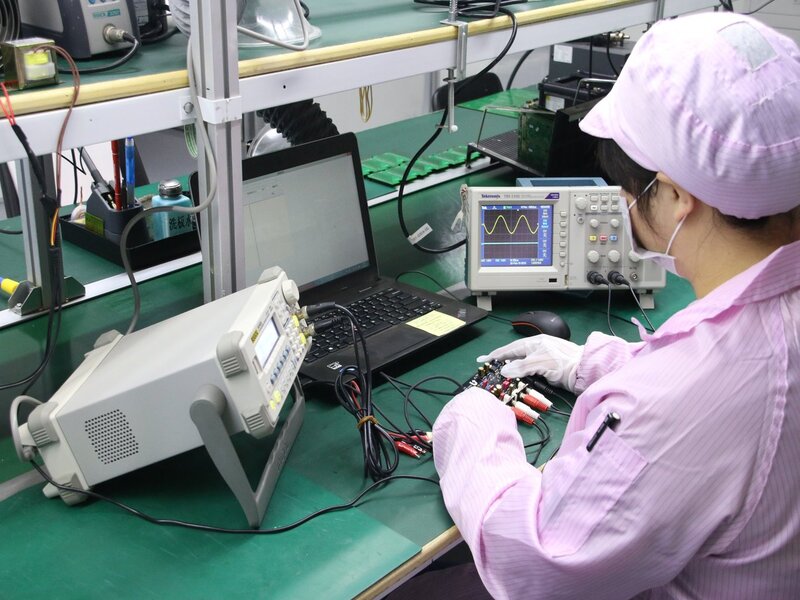
Aplicaciones Comunes de las PCB Multicapa
Las PCB multicapa son indispensables en los dispositivos electrónicos modernos debido a su capacidad para manejar circuitos complejos en un formato compacto, ofrecer un alto rendimiento y soportar una amplia gama de funcionalidades. Sus ventajas únicas, como mayor densidad de componentes, mejor integridad de señal y eficiente distribución de energía, las hacen ideales para una variedad de industrias de alta tecnología. A continuación, se describen algunas de las aplicaciones más comunes de las PCB multicapa:
Equipos de Telecomunicaciones y Redes
La industria de las telecomunicaciones y redes depende en gran medida de las PCB multicapa para garantizar la transmisión de datos a alta velocidad, la integridad de señal y la fiabilidad. A medida que la infraestructura de redes evoluciona con tecnologías como el 5G, la demanda de PCB multicapa de alto rendimiento en este campo sigue aumentando.
- Conmutadores y Enrutadores: Las PCB multicapa son fundamentales en dispositivos como conmutadores y enrutadores, donde se requiere procesamiento de señales y enrutamiento de datos a alta velocidad. El diseño multicapa permite separar los planos de alimentación y tierra de las capas de señal, reduciendo el ruido y las interferencias electromagnéticas (EMI), lo cual es esencial para mantener la integridad de señal en estos dispositivos.
- Estaciones Base y Antenas: En las estaciones base celulares, las PCB multicapa se utilizan para procesar y transmitir datos a través de las redes, permitiendo una comunicación fluida entre dispositivos móviles. Estas PCB deben manejar señales de alta frecuencia y mantener bajas pérdidas de señal, especialmente con las crecientes demandas de la tecnología 5G. El uso de materiales como Rogers, conocidos por su baja constante dieléctrica, asegura la estabilidad de la señal en estos entornos de alta frecuencia.
- Transceptores de Fibra Óptica: Los sistemas de comunicación por fibra óptica, que proporcionan servicios de internet y datos de alta velocidad, dependen de las PCB multicapa para sus unidades de procesamiento de señales. Estas PCB soportan la conversión de datos entre señales eléctricas y ópticas, requiriendo un diseño compacto y la capacidad de manejar eficientemente altas tasas de transmisión de datos.
Los equipos de telecomunicaciones y redes requieren PCB multicapa para ofrecer una comunicación rápida, fiable y sin interferencias. Su capacidad para gestionar señales complejas y minimizar las EMI las hace ideales para esta industria.
Electrónica de Consumo (Smartphones, Portátiles, etc.)
El sector de la electrónica de consumo es uno de los mayores mercados para las PCB multicapa. Dispositivos como smartphones, portátiles, tabletas y wearables son cada vez más potentes, manteniendo un diseño compacto y ligero, lo que solo es posible gracias a las PCB multicapa.
- Smartphones: Las PCB multicapa son esenciales en los smartphones debido a su capacidad para acomodar los circuitos complejos necesarios para una amplia gama de funciones, como la comunicación inalámbrica, pantallas táctiles, cámaras y sensores. El diseño compacto de una PCB multicapa permite una mayor densidad de componentes, lo que permite a los fabricantes incluir más funciones en dispositivos cada vez más pequeños sin comprometer el rendimiento. Además, las PCB multicapa proporcionan la distribución de energía y la integridad de señal necesarias para procesadores de alta velocidad, chips de memoria y módulos de conectividad inalámbrica.
- Portátiles y Tabletas: Las PCB multicapa se utilizan ampliamente en portátiles y tabletas, donde el rendimiento y las limitaciones de tamaño son críticos. Estos dispositivos requieren PCB capaces de gestionar la transferencia rápida de datos, soportar múltiples puertos de entrada/salida y admitir pantallas de alta resolución. La flexibilidad en el diseño de PCB multicapa permite a los fabricantes enrutar eficientemente las señales entre diversos componentes, como procesadores, memoria y almacenamiento, asegurando que los portátiles y tabletas cumplan con los estándares modernos de rendimiento.
- Wearables: Los dispositivos wearables, como relojes inteligentes, rastreadores de actividad y monitores de salud, dependen de las PCB multicapa para lograr su tamaño compacto sin dejar de ofrecer funcionalidades avanzadas. En estas aplicaciones, las PCB multicapa permiten la integración de sensores, módulos de comunicación inalámbrica y pequeños procesadores, todo dentro de un formato miniaturizado. La flexibilidad de las PCB multicapa también permite la producción de diseños rígido-flexibles, ideales para dispositivos que deben doblarse o adaptarse al cuerpo del usuario.
La industria de la electrónica de consumo depende de las PCB multicapa por su capacidad para ofrecer un alto rendimiento en diseños compactos. A medida que los dispositivos de consumo siguen evolucionando, la demanda de PCB multicapa continuará creciendo, permitiendo dispositivos aún más complejos y compactos en el futuro.
Capítulo 8
Desafíos en el Diseño de PCB Multicapa
El diseño de PCB multicapa es una tarea compleja que requiere una planificación cuidadosa. Desde el enrutamiento de señales y la gestión de la impedancia hasta los altos costos y largos tiempos de entrega asociados con estas placas, hay muchos desafíos involucrados. A continuación, se analizan los principales retos en el diseño de PCB multicapa.
Complejidad del Diseño y Desafíos de Enrutamiento
Uno de los mayores desafíos en el diseño de PCB multicapa es lidiar con la mayor complejidad que implica tener múltiples capas de circuitos. A medida que aumenta el número de capas, también lo hacen las dificultades para enrutar señales, gestionar la distribución de energía y mantener la integridad de la señal.
- Espacio Limitado y Colocación de Componentes: Con más capas y componentes en una placa pequeña, los diseñadores deben ser estratégicos en la colocación de los componentes. Deben asegurarse de que los componentes se ubiquen de manera que eviten la congestión y permitan un enrutamiento eficiente. Esto es especialmente importante en diseños que requieren alta densidad de componentes, como los smartphones o dispositivos wearables. Una mala colocación de los componentes puede generar enrutamientos ineficientes e interferencias, lo que podría ocasionar fallos en el diseño.
- Enrutamiento de Señales a Través de Múltiples Capas: Enrutar señales a través de múltiples capas es un desafío, ya que se debe minimizar la longitud de las rutas de señal mientras se mantiene un flujo lógico de conexiones. Los diseñadores deben gestionar cuidadosamente las rutas de señal para evitar cruces innecesarios y el uso excesivo de vías, que pueden introducir ruido o retrasos. En diseños de alta velocidad, el enrutamiento se complica aún más, ya que es necesario minimizar el ruido, las reflexiones de señal y los desajustes de impedancia.
- Gestión de Vías: Las vías (pasantes, ciegas y enterradas) se utilizan para conectar diferentes capas en una PCB multicapa. Aunque son esenciales para enrutar señales entre capas, también presentan desafíos en términos de fabricación y diseño. El uso excesivo de vías puede degradar las señales y aumentar la complejidad de la placa, mientras que un número insuficiente de vías dificulta el enrutamiento eficiente. Los diseñadores deben encontrar un equilibrio, utilizando vías de manera estratégica para mantener la integridad de la señal sin complicar demasiado el diseño.
- Optimización del Stackup: A medida que aumenta el número de capas, se vuelve crucial optimizar el stackup (la disposición de las capas). El stackup debe incluir planos de alimentación, planos de tierra y capas de señal de manera que maximicen el rendimiento y minimicen las interferencias y el ruido. La disposición de las capas también afecta la estabilidad mecánica y la facilidad de fabricación de la PCB, por lo que es una consideración clave en el proceso de diseño.
Abordar estas complejidades de diseño requiere un profundo conocimiento de los requisitos del sistema y el uso de herramientas avanzadas de diseño que puedan simular el comportamiento de las señales y optimizar el enrutamiento.
Costos de Fabricación y Tiempos de Entrega
Las PCB multicapa suelen ser más caras y requieren más tiempo de fabricación en comparación con las placas de una o dos capas. Esto se debe a la necesidad de materiales adicionales, pasos de procesamiento y medidas de control de calidad.
- Altos Costos de Fabricación: La complejidad adicional de las PCB multicapa impacta directamente en los costos de fabricación. Cada capa adicional aumenta los costos de materiales (como cobre y materiales aislantes), y el proceso de fabricación se vuelve más complicado. El proceso de laminación, que implica prensar y unir múltiples capas de cobre y material aislante, es particularmente costoso en los diseños multicapa. La perforación de alta precisión para las vías, las técnicas avanzadas de grabado y las medidas de control de calidad adicionales también incrementan los costos. El uso de materiales especializados, como los sustratos de alta frecuencia (por ejemplo, Rogers), aumenta aún más el gasto total.
- Tiempos de Entrega Prolongados: La complejidad de la fabricación de PCB multicapa significa que a menudo tienen tiempos de entrega más largos en comparación con las placas más simples. Las múltiples etapas de laminación, perforación, recubrimiento y pruebas prolongan el ciclo de producción. Además, las PCB multicapa suelen requerir inspecciones y pruebas más detalladas para garantizar que cumplan con los estándares de rendimiento y fiabilidad. Si surgen problemas durante la producción, la reelaboración o el rediseño de una PCB multicapa puede ser un proceso largo, lo que retrasa aún más la entrega. Por esta razón, la gestión de los tiempos de entrega es una consideración crítica, especialmente en proyectos con plazos ajustados.
- Retos de Rendimiento (Yield): Lograr un alto rendimiento en la fabricación de PCB multicapa puede ser difícil, especialmente en diseños complejos. Los desalineamientos, defectos en las vías y problemas de laminación pueden resultar en placas rechazadas, lo que incrementa el costo y el tiempo asociados a la producción. Los fabricantes deben implementar procesos estrictos de control de calidad para garantizar que cada placa cumpla con las especificaciones requeridas sin sacrificar el rendimiento.
Para mitigar estos desafíos, los diseñadores y fabricantes deben trabajar en estrecha colaboración para optimizar los diseños en función de la fabricabilidad y equilibrar el rendimiento con los costos y los plazos de producción.
Gestión de Impedancia y Crosstalk
En las PCB multicapa de alta velocidad y alta frecuencia, el control de la impedancia y la minimización del crosstalk son desafíos críticos que pueden afectar la integridad de la señal y el rendimiento general de la placa.
- Control de Impedancia: La impedancia se refiere a la resistencia que encuentra una señal eléctrica al viajar a través de un conductor. En los diseños de PCB multicapa, mantener una impedancia consistente es crucial, especialmente para señales de alta velocidad. Las variaciones en la impedancia pueden causar reflexiones de señal, distorsión y pérdida de integridad de los datos. Los diseñadores deben calcular y controlar cuidadosamente la impedancia de cada traza, especialmente en aplicaciones de alta frecuencia como telecomunicaciones o sistemas de radar. Factores como el ancho de la traza, la distancia entre capas y el tipo de material dieléctrico utilizado afectan la impedancia. Un adecuado ajuste de impedancia asegura que las señales se transmitan de manera fluida sin degradación.
- Integridad de la Señal y Crosstalk: El crosstalk ocurre cuando las señales de trazas adyacentes interfieren entre sí, causando ruido y errores de datos. En las PCB multicapa, el riesgo de crosstalk aumenta debido a la proximidad de las trazas y la alta densidad del enrutamiento. El crosstalk puede degradar significativamente la integridad de la señal, especialmente en circuitos de alta velocidad, donde pequeñas interrupciones pueden ocasionar grandes problemas de rendimiento. Para minimizar el crosstalk, los diseñadores deben espaciar adecuadamente las trazas de señal y usar técnicas de blindaje, como planos de tierra para aislar las señales. Enrutar señales de alta velocidad en capas internas entre planos de tierra también ayuda a reducir el crosstalk al proporcionar un camino de retorno de baja impedancia.
- Enrutamiento de Pares Diferenciales: En muchos diseños de alta velocidad, se utilizan pares diferenciales (dos trazas que llevan señales opuestas) para reducir el ruido y mejorar la integridad de la señal. Sin embargo, gestionar estos pares diferenciales a través de múltiples capas y asegurarse de que las dos trazas permanezcan paralelas y equidistantes a lo largo del PCB puede ser un desafío. Cualquier desviación en la longitud o el espaciamiento de las trazas puede generar desajustes de temporización y desequilibrios de impedancia, lo que afecta el rendimiento general del circuito.
- Cambios de Impedancia Inducidos por Vías: Las vías introducen discontinuidades de impedancia en las rutas de señal, lo que puede causar reflexiones y degradación de señal. Esto es particularmente problemático para señales de alta velocidad, que requieren un perfil de impedancia suave y continuo. Los diseñadores deben minimizar el uso de vías en señales de alta frecuencia o utilizar técnicas como perforaciones de retroceso (back-drilling) para reducir el impacto de los residuos de las vías en la integridad de la señal.
Gestionar eficazmente la impedancia y el crosstalk en los diseños de PCB multicapa requiere una combinación de planificación cuidadosa del diseño, herramientas avanzadas de simulación y la adopción de mejores prácticas para diseños de alta velocidad. Controlando estos factores, los diseñadores pueden garantizar que sus PCB multicapa ofrezcan el rendimiento requerido incluso en las aplicaciones más exigentes.
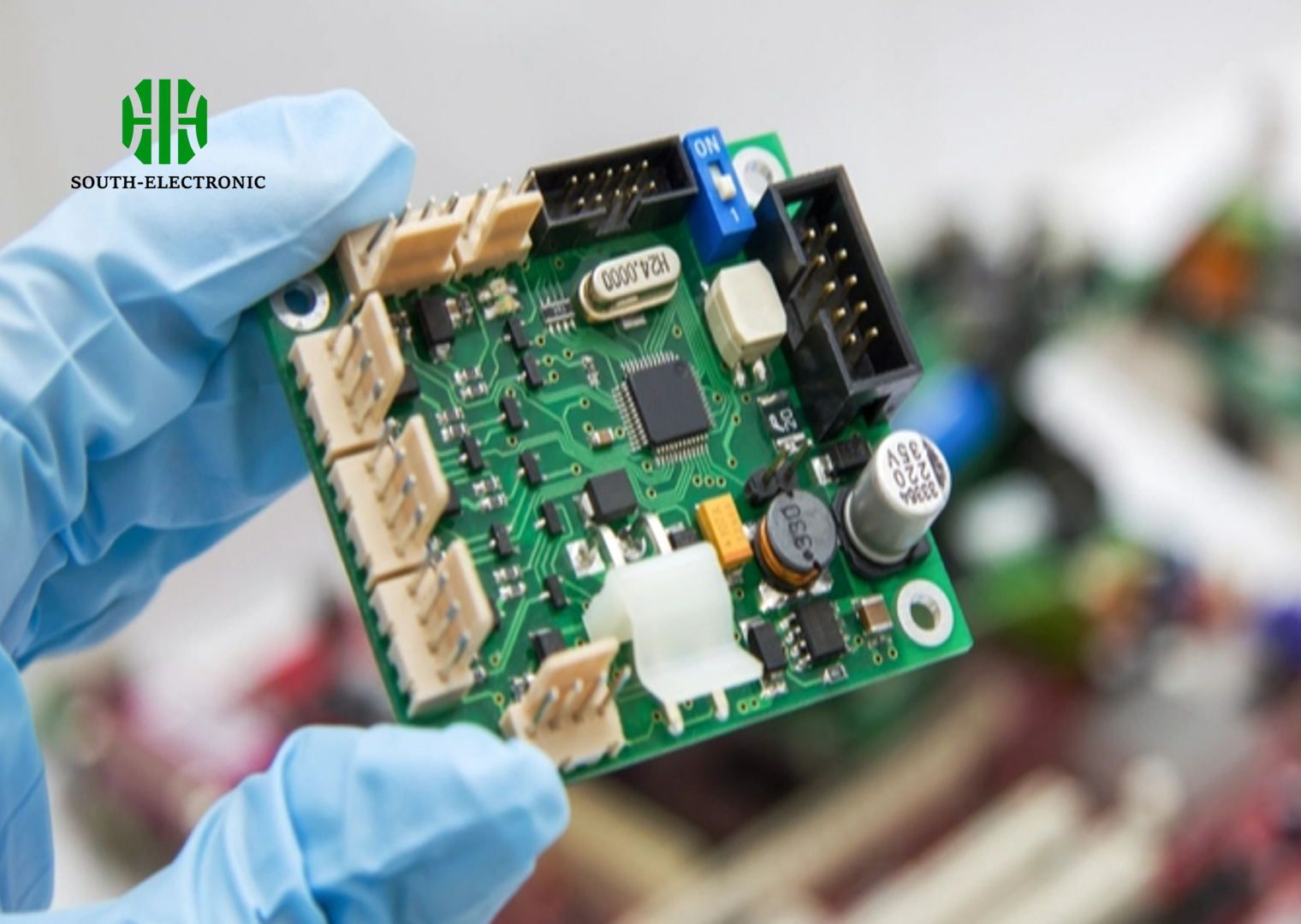
Capítulo 9

Prototipado y Pruebas de PCB Multicapa
El prototipado y las pruebas son etapas cruciales en el desarrollo de PCB multicapa, ya que garantizan que el producto final cumpla con los requisitos de rendimiento, fiabilidad y fabricabilidad. El prototipado permite a los diseñadores identificar y solucionar problemas en las primeras fases del proceso, mientras que las pruebas exhaustivas aseguran la funcionalidad y durabilidad de la PCB antes de la producción a gran escala. A continuación, se detalla la importancia del prototipado, las técnicas comunes de prueba y los métodos para evitar problemas durante esta etapa.
La Importancia del Prototipado
El prototipado es un paso esencial en el diseño de PCB multicapa, ya que permite validar el diseño antes de pasar a la producción masiva. Las PCB multicapa suelen ser complejas, y incluso los diseños más meticulosamente planeados pueden presentar fallos o problemas inesperados que sólo se evidencian al crear un prototipo físico. Los principales beneficios del prototipado incluyen:
- Validación del Diseño: El prototipado permite a los ingenieros verificar que el diseño de la PCB funcione como se espera en condiciones reales. Garantiza que todos los componentes estén correctamente colocados y conectados, y que las señales se transmitan sin interferencias. Mediante un prototipo, los diseñadores pueden validar elementos clave del diseño, como la integridad de la señal, la distribución de energía, la gestión térmica y el ajuste mecánico.
- Detección Temprana de Problemas: El prototipado ayuda a identificar errores de diseño, defectos de fabricación o problemas de rendimiento en las primeras etapas del desarrollo. Por ejemplo, problemas relacionados con el enrutamiento de trazas, desajustes de impedancia o una puesta a tierra incorrecta pueden detectarse durante la fase de prototipado, ahorrando tiempo y dinero en comparación con descubrir estos problemas más adelante en la producción en masa.
- Ahorro de Costos: Aunque crear prototipos implica ciertos costos iniciales, la inversión es mínima en comparación con los costos potenciales de descubrir un fallo crítico en la etapa de producción. Detectar y solucionar problemas a tiempo reduce el riesgo de retrabajos costosos o retrasos en el cronograma de producción.
- Pruebas y Optimización: El prototipado también ofrece la oportunidad de probar diferentes variantes de diseño u optimizar la disposición de la placa para mejorar el rendimiento. Este proceso iterativo permite a los diseñadores refinar el diseño, asegurando que la PCB final cumpla con todos los requisitos de rendimiento y fiabilidad.
Dada la complejidad de las PCB multicapa, el prototipado no es opcional, sino una parte esencial del proceso de diseño, que permite mejoras iterativas y reduce el riesgo de fallos en el producto final.
Técnicas de Prueba: AOI, Flying Probe, Pruebas Funcionales
Una vez creado el prototipo, se emplean varias técnicas de prueba para verificar su funcionalidad y garantizar que la placa cumpla con todas las especificaciones de diseño. Las técnicas comunes de prueba para PCB multicapa incluyen Inspección Óptica Automatizada (AOI), Prueba con Sonda Voladora y Pruebas Funcionales.
- Inspección Óptica Automatizada (AOI): La AOI es una técnica de inspección automatizada y sin contacto que se utiliza para identificar defectos de fabricación en la superficie de la PCB. El sistema utiliza cámaras de alta resolución para capturar imágenes de la PCB y compararlas con los archivos de diseño originales (como los archivos Gerber). La AOI puede detectar problemas como:
- Componentes faltantes o mal alineados
- Defectos en los puentes de soldadura
- Circuitos abiertos o cortocircuitos
- Colocación u orientación incorrecta de los componentes
La AOI es especialmente útil para inspeccionar PCB multicapa densamente pobladas, donde la inspección manual sería difícil o llevaría mucho tiempo. Garantiza que la placa cumpla con los estándares de calidad requeridos antes de aplicar técnicas de prueba más avanzadas.
Prueba con Sonda Voladora (Flying Probe): La prueba con sonda voladora es un método versátil y efectivo para probar PCB multicapa, especialmente durante la fase de prototipado. En lugar de utilizar un banco de pruebas tradicional, las sondas voladoras utilizan puntas de prueba controladas con precisión para hacer contacto eléctrico con los puntos de prueba de la PCB. Este método es ideal para pequeñas series de producción o prototipos, ya que no requiere un banco de pruebas dedicado, cuyo coste puede ser elevado para prototipos únicos.
La prueba con sonda voladora se utiliza para:
- Verificar conexiones eléctricas entre capas
- Detectar cortocircuitos, circuitos abiertos y errores de cableado
- Medir valores de componentes (resistencia, capacitancia)
Esta técnica es flexible y puede adaptarse rápidamente a cambios en el diseño, lo que la convierte en un método preferido para pruebas iniciales de prototipos de PCB multicapa.
Pruebas Funcionales: Las pruebas funcionales consisten en evaluar la PCB en condiciones reales de funcionamiento para garantizar que se desempeñe según lo esperado. Este tipo de prueba verifica que todos los componentes funcionen conjuntamente según lo diseñado y que la PCB cumpla con los criterios de rendimiento deseados. Las pruebas funcionales suelen incluir:
- Aplicar energía a la PCB y verificar que los niveles de voltaje sean correctos
- Ejecutar software o firmware para comprobar si la PCB se comporta como se espera
- Medir la integridad de la señal y la distribución de energía en condiciones reales
Las pruebas funcionales son críticas porque simulan el entorno real en el que se utilizará la PCB, permitiendo a los diseñadores garantizar que la placa funcionará correctamente en su aplicación final.
Combinando estas técnicas de prueba, los diseñadores pueden evaluar exhaustivamente el prototipo y asegurarse de que cumpla con los estándares funcionales y de calidad antes de proceder a la producción a gran escala.
Cómo Evitar Problemas Comunes Durante el Prototipado
La fase de prototipado es crucial para identificar y corregir posibles problemas en los diseños de PCB multicapa. Sin embargo, pueden surgir algunos errores comunes si no se abordan adecuadamente. A continuación, se presentan estrategias para evitar estos problemas:
- Revisar Minuciosamente el Diseño: Antes de enviar el diseño para prototipado, realice una revisión detallada del diseño de la PCB, el esquema y la lista de materiales (BOM). Preste especial atención a áreas como el enrutamiento de trazas, la colocación de vías y la selección de componentes para asegurarse de que no haya errores evidentes. Utilizar software de verificación de reglas de diseño (DRC) ayuda a identificar errores de diseño o violaciones de restricciones de fabricación en las primeras etapas.
- Asegurar un Stackup y Cálculos de Impedancia Correctos: En las PCB multicapa, el stackup (la disposición de las capas) juega un papel crucial en la integridad de la señal y el rendimiento general de la placa. Asegúrese de que el stackup esté optimizado para la aplicación, con la combinación correcta de capas de señal, planos de alimentación y planos de tierra. Para señales de alta velocidad, las trazas con impedancia controlada deben calcularse correctamente para evitar reflexiones o distorsiones de señal.
- Minimizar Crosstalk y EMI: En diseños multicapa, las trazas de señal muy juntas pueden causar crosstalk, donde las señales interfieren entre sí. Para evitar este problema, mantenga suficiente espacio entre las trazas de señal de alta velocidad, utilice técnicas de blindaje adecuadas y asegúrese de que los planos de tierra estén cerca de las capas de señal. Del mismo modo, preste atención a las posibles interferencias electromagnéticas (EMI), especialmente en diseños de alta frecuencia.
- Validar la Distribución de Energía y Puesta a Tierra: Las PCB multicapa a menudo requieren redes complejas de distribución de energía. Asegúrese de que los planos de alimentación estén diseñados adecuadamente para entregar niveles de voltaje estables y que la puesta a tierra esté bien planificada para evitar bucles de tierra o caminos de retorno de alta impedancia. Añadir condensadores de desacoplo cerca de los pines de alimentación de los componentes críticos ayuda a reducir el ruido y estabilizar la distribución de energía.
- Probar Temprano y Frecuentemente: Comience a probar el prototipo lo antes posible durante el proceso de desarrollo. Utilice AOI y pruebas con sonda voladora para identificar rápidamente defectos o problemas. Las pruebas funcionales deben realizarse en paralelo para validar el diseño en condiciones reales. Cuanto antes se realicen estas pruebas, más fácil será corregir cualquier problema antes de que se conviertan en costosos de solucionar en etapas posteriores de producción.
- Trabajar con un Fabricante Confiable: El éxito del prototipado depende no solo de buenas prácticas de diseño, sino también de colaborar con un fabricante de PCB confiable y experimentado. Los fabricantes especializados en PCB multicapa pueden ofrecer valiosos consejos sobre fabricabilidad, selección de materiales y optimización del diseño, reduciendo el riesgo de errores durante el proceso de prototipado.
Capítulo 10
Cómo Elegir el Fabricante Adecuado de PCB Multicapa
Seleccionar al fabricante adecuado para tus PCB multicapa es crucial para garantizar que tu diseño cumpla con los más altos estándares de calidad, fiabilidad y rendimiento. Esta decisión afecta no solo la funcionalidad del producto final, sino también la eficiencia del proceso de producción, los costos y los tiempos de entrega. A continuación, se describen los factores clave a considerar al elegir un fabricante de PCB multicapa y las razones por las que South-Electronic destaca como una elección ideal.
Factores Clave a Considerar: Calidad, Certificaciones, Tiempos de Entrega
Al evaluar a un fabricante de PCB multicapa, es fundamental analizar varios factores para garantizar los mejores resultados para tu proyecto:
- Calidad: La calidad de una PCB es primordial, ya que afecta directamente el rendimiento y la durabilidad del producto final. Un fabricante de alta calidad tendrá procesos estrictos de control de calidad, incluyendo inspecciones y pruebas regulares para detectar defectos de fabricación. Busca un fabricante que priorice la precisión en el diseño y la producción, minimizando errores que puedan afectar la funcionalidad de la PCB.
- Certificaciones: Las certificaciones son un indicador confiable del compromiso de un fabricante con la calidad y los estándares de la industria. Asegúrate de que el fabricante cuente con certificaciones como ISO 9001 para la gestión de calidad, UL, CE, IATF16949 para aplicaciones automotrices, e ISO13485 para dispositivos médicos. Estas certificaciones garantizan que el fabricante cumple con estándares internacionales y puede producir PCB adecuadas para aplicaciones especializadas y de alto rendimiento.
- Tiempos de Entrega: Los tiempos de entrega son un aspecto crítico, especialmente en industrias donde el tiempo de comercialización es esencial. Un fabricante confiable tendrá procesos de producción eficientes que permitan tiempos de entrega rápidos sin comprometer la calidad. Asegúrate de que el fabricante sea transparente sobre sus tiempos de entrega y pueda cumplir con los plazos de tu proyecto, ya sea para un prototipo rápido o una producción a gran escala.
Al priorizar la calidad, las certificaciones y los tiempos de entrega, puedes asegurarte de que tu diseño de PCB esté en manos de un fabricante competente y confiable.
Importancia de la Comunicación y el Soporte del Proveedor
Una comunicación y soporte efectivos por parte del proveedor son esenciales para el éxito de cualquier proyecto de PCB multicapa. Una sólida colaboración con tu fabricante de PCB puede ayudar a garantizar que tu diseño esté optimizado para la fabricación y que cualquier problema se resuelva rápidamente. Los aspectos clave a considerar en términos de comunicación y soporte incluyen:
- Comunicación Proactiva: Un buen fabricante te mantendrá informado en cada etapa del proceso de producción, desde las revisiones iniciales del diseño hasta la entrega final. Deberían ser receptivos a las consultas, proporcionar actualizaciones regulares y comunicar cualquier posible retraso o desafío con anticipación.
- Soporte en el Diseño: Algunos fabricantes ofrecen revisiones de diseño para fabricación (DFM), que pueden ser de gran ayuda para garantizar que el diseño de tu PCB esté optimizado para la producción. Esto puede prevenir problemas como un enrutamiento deficiente, capas desalineadas o una colocación inadecuada de vías que podrían causar retrasos en la producción o problemas de rendimiento.
- Asistencia Técnica: Elige un fabricante que ofrezca soporte técnico para resolver cualquier duda o preocupación que puedas tener durante las etapas de diseño, prototipado o producción. Tener acceso a asesoramiento experto garantiza que tu PCB se produzca con los más altos estándares.
- Soporte Postventa: Un fabricante confiable también proporcionará soporte postventa, ayudándote a resolver cualquier problema con las PCB después de la entrega. Esto asegura que recibirás asistencia no solo durante la producción, sino a lo largo de todo el ciclo de vida del proyecto.
Una sólida comunicación y soporte del proveedor son clave para garantizar que tu proyecto se desarrolle sin problemas y que cualquier problema potencial se aborde de manera oportuna.
Por Qué Elegir South-Electronic para Tus Necesidades de PCB Multicapa
South-Electronic es un fabricante experimentado y altamente calificado que se destaca como una excelente opción para tus necesidades de PCB multicapa. Estas son las razones:
- Compromiso con la Calidad: En South-Electronic, la calidad es una prioridad. Cada PCB pasa por rigurosos controles de calidad, incluyendo métodos avanzados de prueba para garantizar que cada placa cumpla con los más altos estándares de rendimiento y fiabilidad. South-Electronic cuenta con certificaciones como ISO 9001, UL, CE, IATF16949 e ISO13485, garantizando el cumplimiento de estándares internacionales de calidad en diversas industrias.
- Tiempos de Entrega Rápidos: South-Electronic comprende la importancia de cumplir con los plazos del proyecto. Con procesos de producción eficientes y operaciones optimizadas, la empresa ofrece tiempos de entrega rápidos sin comprometer la calidad. Ya sea que necesites prototipos rápidos o producción a gran escala, South-Electronic puede entregar a tiempo, asegurando que tus proyectos se mantengan dentro del cronograma.
- Excelente Soporte al Cliente: South-Electronic pone un fuerte énfasis en el servicio al cliente, ofreciendo una comunicación clara y proactiva durante todo el proceso de producción. El equipo proporciona un completo soporte técnico, desde revisiones de DFM hasta servicio postventa, asegurando que el diseño de tu PCB esté optimizado y que cualquier problema potencial se resuelva rápidamente.
- Personalización y Flexibilidad: South-Electronic ofrece soluciones de PCB completamente personalizables, adaptadas a las necesidades específicas de tu proyecto. Desde el prototipado hasta la producción a gran escala, la empresa proporciona flexibilidad en términos de cantidades de pedido y ajustes de diseño, facilitando la ampliación de tu producción según sea necesario.
- Experiencia Probada en la Industria: Con más de una década de experiencia, South-Electronic se ha establecido como un socio confiable para industrias como la automotriz, las telecomunicaciones, los dispositivos médicos y la electrónica de consumo. Su profundo conocimiento de la industria garantiza que puedan manejar incluso los diseños de PCB multicapa más complejos con precisión y fiabilidad.
En conclusión, elegir a South-Electronic para la fabricación de tus PCB multicapa garantiza que recibirás productos de alta calidad, tiempos de entrega rápidos y un soporte al cliente excepcional. Su experiencia, compromiso con la calidad y dedicación a la satisfacción del cliente los convierten en el socio ideal para tu próximo proyecto.
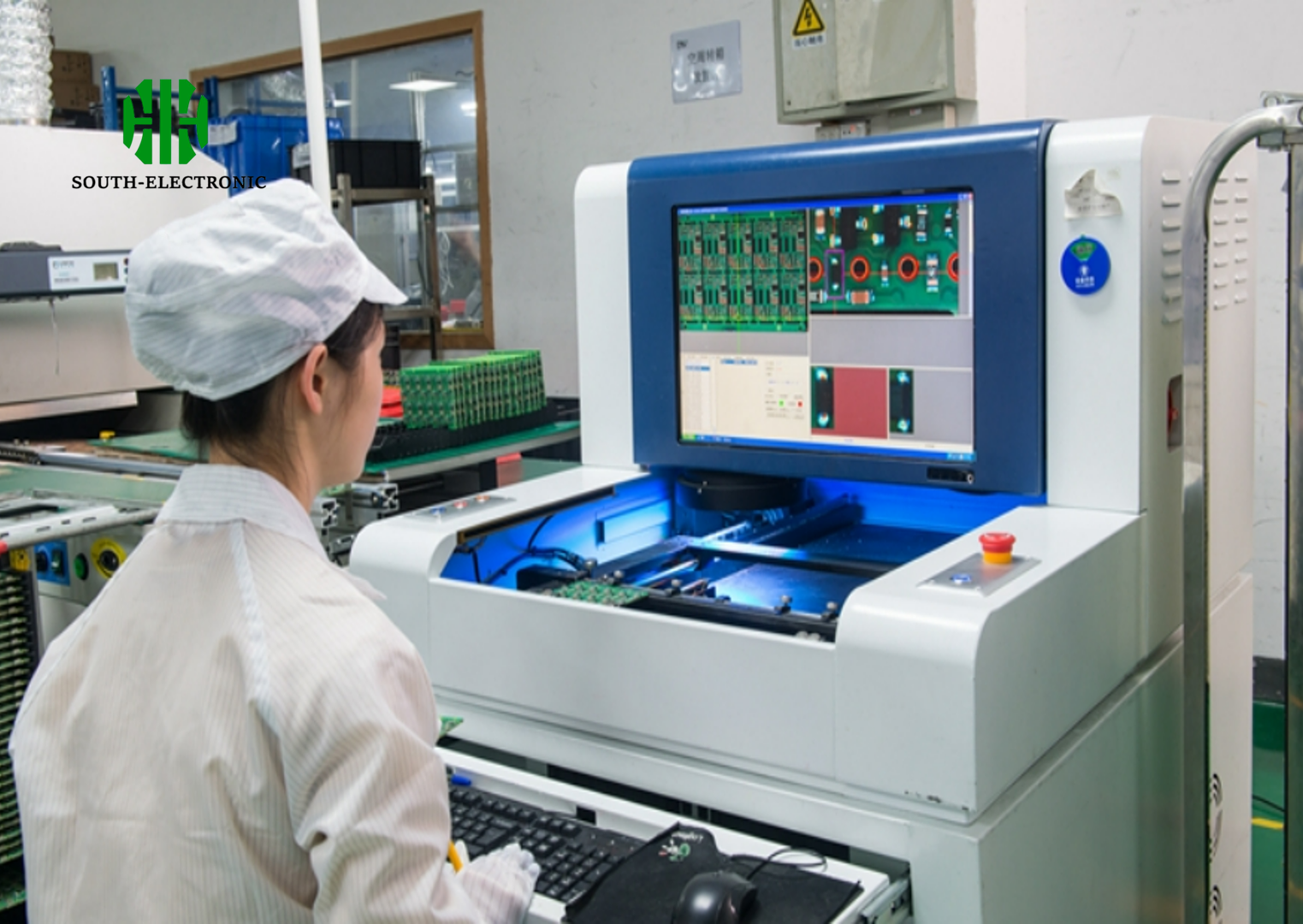
Póngase en Contacto
¿Dónde Estamos?
Parque Industrial, No. 438 Donghuan Road, No. 438, Shajing Donghuan Road, Distrito de Bao'an, Shenzhen, Guangdong, China
Cuarto Piso, Edificio Creativo Zhihui, No.2005 Xihuan Road, Shajing, Distrito de Baoan, Shenzhen, China
Habitación A1-13, Tercer Piso, Centro Industrial Yee Lim, 2-28 Calle Kwai Lok, Kwai Chung, HK
service@southelectronicpcb.com
Teléfono: +86 400 878 3488
Envíanos un mensaje
Cuanto más detallado completes, más rápido podremos avanzar al siguiente paso.
