Servicios de ensamblaje SMT
South-Electronic
Elige South-Electronic, experimentarás una calidad y precisión incomparables desde el principio hasta el final. Asocíate con South-Electronic hoy y déjanos ayudarte a llevar tus proyectos al siguiente nivel con innovaciones de alta calidad.
Su proveedor de confianza de ensamblaje de PCB SMT
Bienvenido a South-Electronic, donde encontrarás servicios de ensamblaje de PCB SMT de alta calidad conocidos por su precisión y confiabilidad.
Nuestros ensamblajes de PCB SMT ofrecen un rendimiento excelente, lo que los hace perfectos para una amplia gama de aplicaciones. Elige entre placas de una capa, dos capas y multi-capas, todas personalizadas para satisfacer tus necesidades electrónicas específicas. Ya sea que estés mejorando la eficiencia en electrónica de consumo o necesites una operación fiable en controles industriales, nuestros servicios de ensamblaje de PCB SMT destacan por ofrecer eficiencia y precisión. Confía en South-Electronic para una calidad y consistencia excepcionales en tus emprendimientos electrónicos. Nuestros ensamblajes de PCB SMT mejoran la funcionalidad de tus dispositivos con una confiabilidad y rendimiento superiores. Asocíate con nosotros para la excelencia y la innovación en tu campo.

Ensamblaje SMT de un solo lado
El ensamblaje SMT de un solo lado es cuando se colocan componentes en un solo lado de la placa. Es bueno para diseños más simples y económicos donde no se necesitan tantos componentes. Se utiliza mucho en dispositivos electrónicos básicos porque es barato y fácil de fabricar.
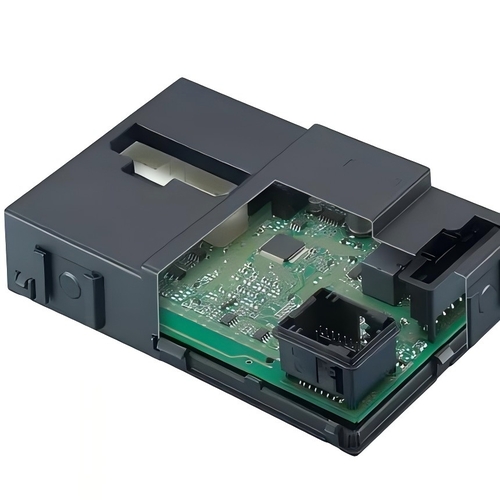
Double-Sided SMT Assembly
El ensamblaje SMT de doble lado es cuando se colocan componentes en ambos lados de la placa. Esto te permite colocar más componentes en la placa y hacer más cosas con ella. Es bueno para diseños más complicados que necesitan más espacio para componentes y es mejor para electrónica más avanzada.
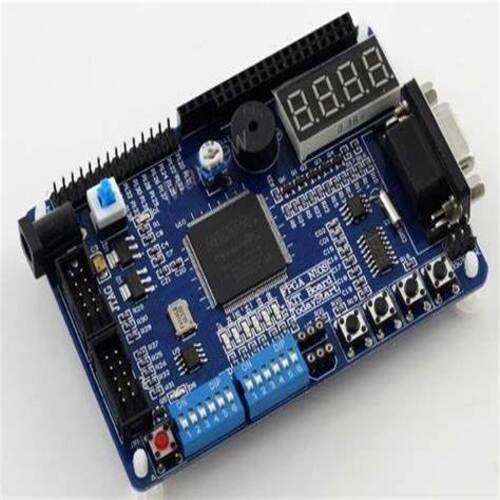
Ensamblaje de matriz de bolas (BGA)
El ensamblaje BGA es cuando se utiliza una cuadrícula de bolas de soldadura para conectar componentes a la placa. Es bueno para circuitos de alta densidad y alto rendimiento como CPUs y GPUs. BGA ofrece un mejor rendimiento eléctrico y una mejor disipación de calor, por lo que es bueno para dispositivos de tecnología avanzada que necesitan conexiones pequeñas y fiables.
¿Por qué elegir South-Electronic?
Elige South-Electronic por nuestra experiencia en servicios de ensamblaje SMT personalizados y de alta calidad para una amplia gama de aplicaciones. Nuestro equipo tiene una amplia experiencia, lo que significa que podemos ofrecer una calidad superior a precios competitivos y un servicio excepcional desde el principio hasta el final.
-
Precisión y Calidad
Su proyecto merece nada más que los estándares más altos.
En South-Electronic, nos aseguramos de que cada ensamblaje SMT que producimos tenga precisión y confiabilidad, garantizando que sus productos sean impecables y funcionen exactamente como se espera. -
Personalización Flexible
Adaptamos nuestros servicios a sus necesidades específicas, ya sea que necesite ensamblaje de un solo lado, doble lado o BGA.
Independientemente de lo que necesite, puede escalar sus pedidos con flexibilidad, manteniendo al mismo tiempo una calidad inquebrantable. -
Entrega Rápida
Entendemos que el tiempo es crucial para su negocio.
Por eso, nuestras líneas de producción altamente eficientes le permiten recibir sus pedidos rápidamente, lo que le ayuda a mantenerse por delante de sus plazos y a mantener sus proyectos en marcha. -
Equipo Experimentado
Al trabajar con nosotros, cuenta con el apoyo de un equipo con años de experiencia en ensamblaje de PCB.
Se beneficiará de la confianza de trabajar con profesionales que entienden su industria y saben cómo satisfacer sus necesidades específicas. -
Solución de un solo punto de contacto
Desde el diseño inicial hasta el ensamblaje final, nos encargamos de cada paso del proceso.
Con nosotros, obtiene la comodidad de un socio de servicio completo que puede manejar todas sus necesidades de PCB de manera fluida, lo que le da tranquilidad y simplifica su flujo de trabajo. -
No hay requisitos de pedido mínimo
Tiene la libertad de pedir exactamente lo que necesita, sin importar la cantidad.
Incluso si solo es una unidad, estamos aquí para satisfacer sus necesidades sin restricciones de pedido mínimo, lo que le da una flexibilidad total en sus decisiones de compra.
Proyecto relacionado que hemos realizado
Reseñas de clientes
Preguntas comunes
Preguntas más populares
South-Electronic se especializa en ensamblar una amplia gama de PCB, incluyendo tableros de un solo lado, de doble lado y de varias capas, así como ensamblajes de matriz de bolas (BGA). Atienden a diversas industrias y pueden manejar tanto diseños simples como complejos.
South-Electronic sigue estrictos procesos de control de calidad en todo el ensamblaje SMT. Utilizan equipo avanzado y realizan inspecciones exhaustivas en cada etapa, asegurando que cada ensamblaje cumpla con los estándares precisos. También están certificados ISO9001, lo que agrega otra capa de garantía en términos de calidad y confiabilidad.
El plazo de entrega típico varía según la complejidad y la cantidad del pedido. Sin embargo, South-Electronic se enorgullece de ofrecer tiempos de entrega rápidos, completando la mayoría de los proyectos en unas pocas semanas, mientras también ofrece servicios de urgencia para pedidos urgentes.
Para obtener un presupuesto preciso, debes proporcionar información detallada como tus archivos de diseño de PCB (archivos Gerber), lista de materiales (BOM), cantidad y cualquier requisito de ensamblaje específico. Cuanto más precisa sea tu información, más personalizado será el presupuesto.
South-Electronic tiene la certificación ISO9001, lo que demuestra su compromiso con la gestión de la calidad y los estándares de producción. Garantiza la precisión y la confiabilidad a través de pruebas rigurosas, equipo de última generación y técnicos experimentados que supervisan todos los aspectos del proceso de ensamblaje.
South-Electronic ofrece un completo soporte después de la venta, incluyendo una garantía sobre sus ensamblajes SMT. Por lo general, ofrecen una garantía de hasta cinco años, asegurando que los clientes estén cubiertos por cualquier defecto o problema potencial. Su equipo de servicio al cliente siempre está disponible para ayudar con cualquier inquietud después de la venta.
Envíanos un mensaje
La guía completa para el ensamblaje SMT
Contenido
Capítulo 1
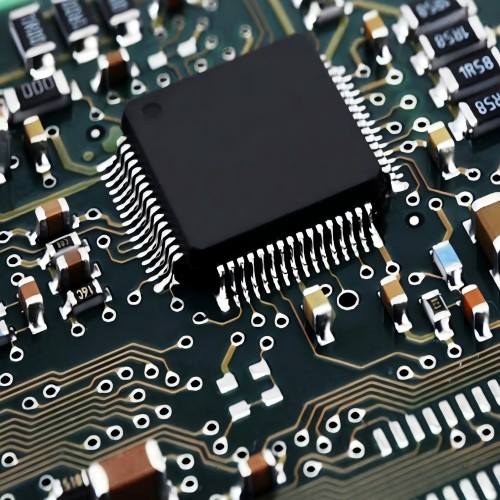
Introducción a la ensambladura SMT
La tecnología de montaje en superficie (SMT) es una forma de hacer circuitos electrónicos. En lugar de colocar las piezas a través de agujeros en la tarjeta de circuito, las piezas se colocan en la superficie de la tarjeta. Esto hace que la tarjeta de circuito sea más pequeña y mejor. La SMT se utiliza para hacer todo tipo de electrónica, como teléfonos, computadoras y otras cosas que usamos todos los días. Es la mejor manera de hacer electrónica porque la hace más pequeña, más rápida y más barata.
La SMT es mejor que la forma antigua de hacer electrónica porque hace que las piezas sean más pequeñas. Las piezas en SMT se llaman Dispositivos de Montaje en Superficie (SMD). Son mucho más pequeños que las piezas antiguas. Esto significa que la electrónica puede ser más pequeña. La SMT también hace que las piezas sean más rápidas. Las piezas se colocan en la tarjeta por una máquina, por lo que es más rápido que hacerlo a mano. La SMT también hace que las piezas sean más baratas. La máquina puede colocar las piezas en la tarjeta más rápido y más veces que una persona puede. Esto hace que las piezas sean más baratas. La SMT es la mejor manera de hacer electrónica porque la hace más pequeña, más rápida y más barata.
La SMT es la mejor manera de hacer electrónica porque la hace más pequeña. Las piezas en SMT son más pequeñas que las piezas antiguas. Esto significa que la electrónica puede ser más pequeña. La SMT es la mejor manera de hacer electrónica porque la hace más rápida. Las piezas se colocan en la tarjeta por una máquina, por lo que es más rápido que hacerlo a mano. La SMT es la mejor manera de hacer electrónica porque la hace más barata. La máquina puede colocar las piezas en la tarjeta más rápido y más veces que una persona puede. Esto hace que las piezas sean más baratas. La SMT es la mejor manera de hacer electrónica porque la hace más pequeña, más rápida y más barata.
Capítulo 2
Cómo funciona la ensambladura SMT
La ensambladura SMT es un proceso altamente automatizado utilizado para conectar dispositivos de montaje en superficie (SMD) directamente a la superficie de una placa de circuito impreso (PCB). A continuación, se explica paso a paso cómo funciona la ensambladura SMT y los componentes clave involucrados:
Paso 1: Aplicar pasta de soldadura
El proceso comienza con la aplicación de pasta de soldadura a la PCB. Se coloca una plantilla sobre la placa para asegurarse de que la pasta se aplique solo en las áreas donde se montarán los componentes. La pasta de soldadura, una combinación de pequeñas bolas de soldadura y flux, actúa como un adhesivo para mantener los componentes en su lugar antes de la soldadura y crea conexiones eléctricas entre las patas del componente y las almohadillas de la PCB.
Paso 2: Máquinas de colocación y recogida
Una vez aplicada la pasta de soldadura, la PCB se pasa a una máquina de colocación y recogida. Esta máquina de alta precisión recoge los pequeños componentes de montaje en superficie de carretes o bandejas y los coloca en la PCB según el diseño de la disposición. Las máquinas de colocación y recogida modernas pueden colocar miles de componentes por hora, lo que garantiza la velocidad y la precisión.
Paso 3: Soldadura de reflujo
Después de colocar los componentes en la placa, el ensamblado se mueve al horno de reflujo. Aquí, la PCB se calienta a una temperatura específica, lo que hace que la pasta de soldadura se derrita y forme uniones de soldadura sólidas. El proceso de reflujo se controla cuidadosamente para asegurarse de que la soldadura se derrita y se solidifique sin dañar los componentes o la propia PCB. Una vez que la placa se enfría, los componentes están firmemente sujetos y se establecen las conexiones eléctricas.
Paso 4: Inspección y prueba
Una vez que se completa el proceso de soldadura, la PCB se somete a inspección para asegurarse de que esté correctamente ensamblada. Las máquinas de inspección óptica automatizada (AOI) escanean la placa para comprobar la presencia de componentes faltantes, defectos de soldadura y desalineaciones. En algunos casos, también se puede utilizar la inspección por rayos X, especialmente para ensamblados complejos como los paquetes de matriz de bolas (BGA), donde las uniones de soldadura están ocultas bajo el componente.
Componentes clave involucrados en la ensambladura SMT
- Pasta de soldadura: Una combinación de flux y partículas de soldadura finas que mantiene temporalmente los componentes en su lugar y eventualmente crea las uniones de soldadura durante el reflujo.
- Máquina de colocación y recogida: Equipo automatizado que coloca componentes en la PCB con alta precisión, manejando incluso los SMD más pequeños.
- Horno de reflujo: Un horno especializado que calienta la PCB para derretir la pasta de soldadura y sujetar firmemente los componentes a la placa.
- Plantilla: Una plantilla utilizada para aplicar la pasta de soldadura con precisión en áreas específicas de la PCB.
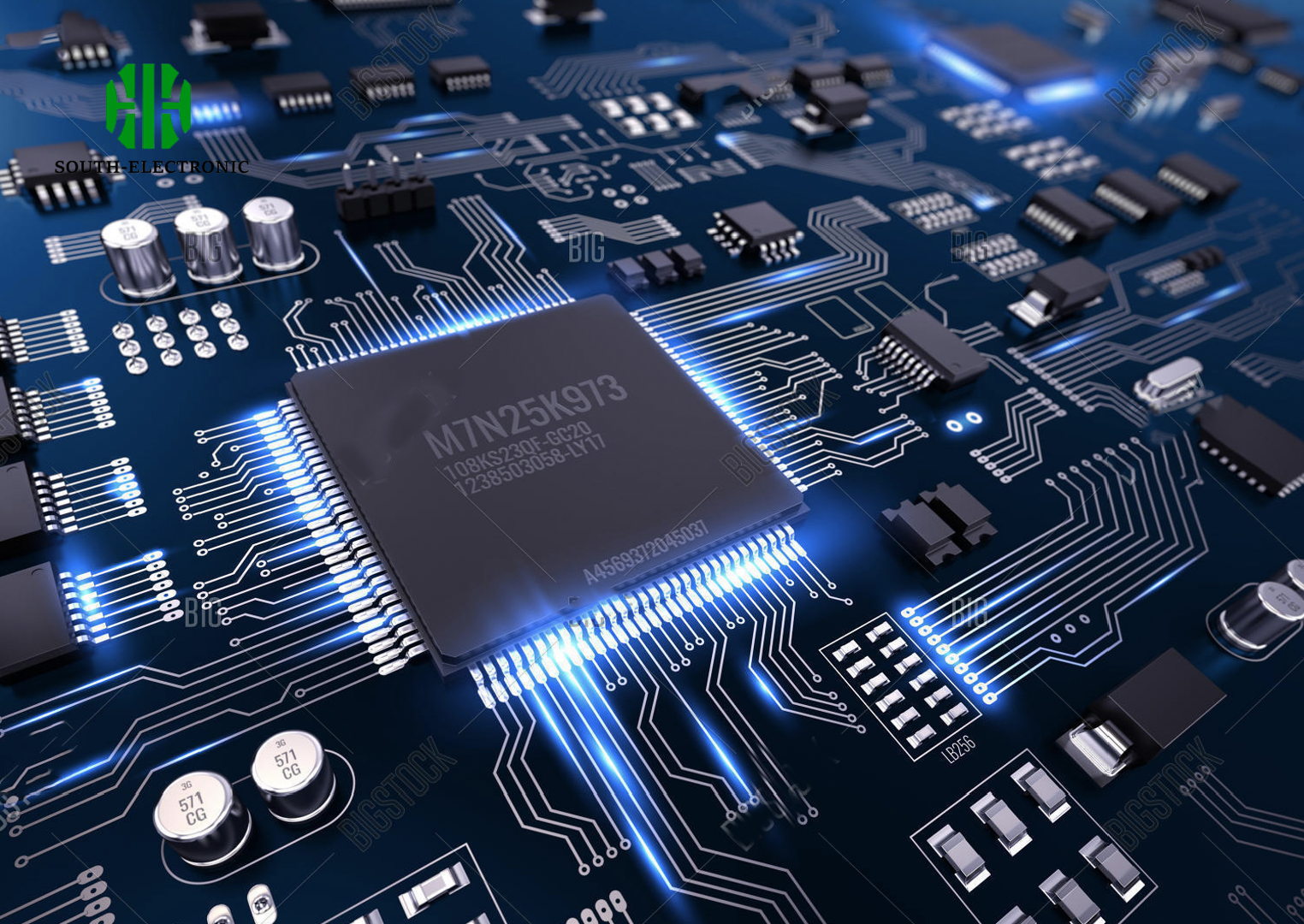
Capítulo 3

Tipos de montaje SMT
El montaje SMT se presenta en diferentes formas dependiendo de la complejidad y los requisitos del diseño de la tarjeta de circuito impreso. Los principales tipos incluyen montajes SMT de un solo lado, de doble lado y de varias capas, cada uno ofreciendo ventajas únicas en términos de utilización del espacio, funcionalidad y rendimiento. Además, las técnicas de montaje avanzadas como la Matriz de Bola de Soldadura (BGA) y el Chip sobre la Tarjeta (COB) proporcionan soluciones especializadas para electrónica de alto rendimiento.
Montaje SMT de un solo lado
El montaje SMT de un solo lado implica montar todos los componentes en un lado de la tarjeta de circuito impreso. Este tipo de montaje se utiliza generalmente en diseños más simples y rentables donde se necesitan menos componentes, lo que lo hace ideal para electrónica básica. Se utiliza ampliamente en productos de consumo como electrodomésticos, controles remotos y dispositivos electrónicos básicos. El montaje SMT de un solo lado es preferido cuando el diseño es sencillo, el espacio no es una restricción importante y los requisitos de funcionalidad son relativamente bajos.
- Ventajas: Bajo costo, fabricación más fácil, adecuado para diseños simples.
- Aplicaciones: Electrónica básica, dispositivos de nivel de entrada y circuitos de baja densidad.
Montaje SMT de doble lado
En el montaje SMT de doble lado, los componentes se montan en ambos lados de la tarjeta de circuito impreso, lo que permite una mayor densidad de componentes y una mayor funcionalidad. Este tipo de montaje es ideal para electrónica más compleja donde se necesitan más componentes pero el espacio es limitado. El montaje SMT de doble lado permite a los diseñadores utilizar de manera eficiente ambos lados de la tarjeta de circuito impreso, optimizando el diseño y mejorando el rendimiento general del producto.
- Ventajas: Mayor densidad de componentes, mayor funcionalidad, uso eficiente del espacio.
- Aplicaciones: Dispositivos de telecomunicación, equipo médico, sistemas de control industrial y otros productos electrónicos compactos y de alto rendimiento.
Montaje SMT de varias capas
El montaje SMT de varias capas implica el uso de tarjetas de circuito impreso con varias capas de vías conductoras apiladas, separadas por capas aislantes. Esto permite una mayor densidad de componentes y diseños más complejos, permitiendo un mayor rendimiento sin aumentar el tamaño de la tarjeta. El montaje SMT de varias capas es esencial para dispositivos que requieren funcionalidad avanzada, procesamiento de datos de alta velocidad o alta integridad de señal en un factor de forma compacto.
- Ventajas: Soporta diseños complejos y de alto rendimiento, reduce la interferencia electromagnética y permite una transmisión de datos más rápida.
- Aplicaciones: Teléfonos inteligentes, portátiles, sistemas de comunicación avanzados y electrónica aeroespacial.
Montaje de Matriz de Bola de Soldadura (BGA)
El montaje BGA es una forma especializada de SMT donde los componentes se montan utilizando una cuadrícula de pequeñas bolas de soldadura en la parte inferior del componente. BGA ofrece varias ventajas sobre los métodos SMT tradicionales, incluyendo un mejor rendimiento eléctrico, una mejor disipación térmica y la capacidad de manejar una alta densidad de conexiones en un área compacta. BGA se utiliza comúnmente para componentes como procesadores, GPU y chips de memoria, donde el rendimiento y la confiabilidad son fundamentales.
- Ventajas: Rendimiento eléctrico mejorado, disipación de calor mejorada, soporta conexiones de alta densidad.
- Aplicaciones: CPU, GPU, módulos de memoria y otros componentes de computación de alto rendimiento.
Tecnología de Chip sobre la Tarjeta (COB)
El Chip sobre la Tarjeta (COB) es un método de empaquetado avanzado donde los chips de semiconductor desnudos se montan directamente en la tarjeta de circuito impreso y se soldan a la circuitería de la tarjeta. Los chips luego se encapsulan con una capa protectora, generalmente una resina epoxi, para protegerlos de factores ambientales. La tecnología COB es ventajosa para aplicaciones que requieren diseños compactos y características de alto rendimiento, ya que reduce el número de pasos de empaquetado intermedios, lo que reduce el costo y el tamaño del montaje.
- Ventajas: Huella más pequeña, menor costo y mayor confiabilidad debido a menos conexiones.
- Aplicaciones: Iluminación LED, sensores, módulos electrónicos compactos y electrónica de consumo.
Resumen
Cada tipo de montaje SMT, ya sea de un solo lado, de doble lado o de varias capas, sirve a diferentes necesidades de diseño según la complejidad, el tamaño y los requisitos de rendimiento del producto. Las tecnologías BGA y COB son métodos avanzados que mejoran el rendimiento en aplicaciones de alta densidad y alta velocidad. Estos varios tipos de montaje SMT permiten a los fabricantes construir productos electrónicos cada vez más compactos, potentes y confiables en una amplia gama de industrias.
Capítulo 4
Ventajas de SMT sobre la tecnología de agujeros pasantes
SMT y la tecnología de agujeros pasantes son los dos métodos principales para ensamblar componentes electrónicos en tarjetas de circuito impreso (PCB). La tecnología de agujeros pasantes, que implica insertar los terminales de los componentes en agujeros preperforados en la PCB, era anteriormente el estándar, pero ha sido reemplazada en gran medida por SMT debido a sus muchas ventajas en términos de eficiencia, rendimiento y costo. A continuación, se presenta una comparación detallada de SMT versus ensamblaje de agujeros pasantes, junto con los beneficios clave que ofrece SMT.
Comparación de SMT vs. Ensamblaje de agujeros pasantes
1. Montaje de componentes
- Ensamblaje de agujeros pasantes: Los componentes en la tecnología de agujeros pasantes tienen terminales que se insertan en agujeros perforados en la PCB y luego se soldan en el lado opuesto de la tarjeta. Esto crea una conexión mecánica fuerte, lo que hace que la tecnología de agujeros pasantes sea ideal para componentes que experimentarán estrés mecánico o están sujetos a movimientos frecuentes.
- Ensamblaje SMT: En contraste, los componentes SMT se colocan directamente en la superficie de la PCB sin necesidad de perforación. Estos dispositivos de montaje en superficie (SMD) son más pequeños, ligeros y fáciles de manejar en procesos de ensamblaje automatizados.
2. Utilización del espacio
- Ensamblaje de agujeros pasantes: La tecnología de agujeros pasantes requiere más espacio en la PCB debido al tamaño de los componentes y la necesidad de agujeros perforados. Esto limita la densidad de componentes y hace que sea más difícil crear diseños compactos.
- Ensamblaje SMT: SMT permite una mayor densidad de componentes porque los componentes se pueden colocar directamente en la superficie de la tarjeta y se pueden montar en ambos lados de la PCB. Esto es especialmente importante para la electrónica moderna que requiere diseños compactos y ligeros.
3. Velocidad de ensamblaje
- Ensamblaje de agujeros pasantes: El ensamblaje de agujeros pasantes tiende a ser más lento y laborioso, ya que cada componente debe insertarse en la PCB a mano o mediante máquinas semiautomatizadas. El proceso de perforación también agrega tiempo extra al ciclo de fabricación.
- Ensamblaje SMT: SMT está altamente automatizado, utilizando máquinas de colocación para posicionar componentes con alta velocidad y precisión. Esta automatización reduce significativamente el tiempo de ensamblaje y aumenta la producción, lo que hace que SMT sea el método preferido para la fabricación de alto volumen.
4. Eficiencia de costo
- Ensamblaje de agujeros pasantes: Los pasos adicionales requeridos en el ensamblaje de agujeros pasantes, como la perforación de agujeros y la colocación manual de componentes, llevan a costos de producción más altos. Además, los componentes de agujeros pasantes suelen ser más grandes y más caros que los componentes de montaje en superficie.
- Ensamblaje SMT: SMT es más rentable debido a su automatización, tiempos de ensamblaje más rápidos y el uso de componentes más pequeños y económicos. Con menos procesos manuales involucrados y la capacidad de manejar la producción de alto volumen de manera eficiente, SMT reduce los costos de fabricación generales.
5. Resistencia mecánica
- Ensamblaje de agujeros pasantes: Los componentes de agujeros pasantes proporcionan una mejor resistencia mecánica porque los terminales pasan a través de la tarjeta y se soldan en el otro lado. Esto lo hace adecuado para conectores o componentes que están sujetos a estrés físico o requieren durabilidad, como transformadores o condensadores grandes.
- Ensamblaje SMT: Si bien los componentes SMT son más compactos, no proporcionan la misma resistencia mecánica que los componentes de agujeros pasantes. Sin embargo, para la mayoría de las aplicaciones electrónicas, donde se prioriza el tamaño, la velocidad y la eficiencia, la resistencia mecánica de SMT es suficiente.
Beneficios clave de SMT sobre la tecnología de agujeros pasantes
1. Eficiencia de espacio
Una de las principales ventajas de SMT es su capacidad para alojar más componentes en una sola tarjeta debido al tamaño más pequeño de los dispositivos de montaje en superficie (SMD). Esto permite diseños de mayor densidad y más funcionalidad en espacios más pequeños. Dispositivos como teléfonos inteligentes, dispositivos portátiles y tabletas se benefician de la naturaleza compacta de los ensamblajes SMT, donde el espacio es un lujo.
2. Eficiencia de espacio
Velocidad de ensamblaje más alta SMT permite una velocidad de ensamblaje más rápida porque el proceso estáalmostamente completamente automatizado. Máquinas como los sistemas de colocación pueden posicionar componentes rápidamente y con precisión, manejando miles de componentes por hora. Esto resulta en tiempos de producción más cortos y la capacidad de satisfacer la demanda de alto volumen, lo cual es esencial para la electrónica de consumo y otros productos producidos en masa.
3. Eficiencia de espacio
Ahorro de costos El ensamblaje SMT generalmente cuesta menos que el ensamblaje de agujeros pasantes por varias razones:
- Sin perforación: SMT elimina la necesidad de perforar agujeros en la PCB, lo que reduce los costos de producción y acelera el proceso de fabricación.
- Componentes más pequeños: Los SMD son típicamente más pequeños y más baratos que los componentes de agujeros pasantes, lo que permite a los fabricantes ahorrar en materiales.
- Automatización: El alto nivel de automatización en SMT conduce a menores costos laborales y ciclos de producción más rápidos, lo que reduce los costos generales por unidad.
4. Flexibilidad de diseño
Con SMT, los componentes se pueden montar en ambos lados de la PCB, lo que permite a los diseñadores crear tarjetas más complejas y multifuncionales. Esta flexibilidad es especialmente útil para dispositivos electrónicos avanzados que requieren altos niveles de funcionalidad dentro de un espacio limitado. SMT también permite diseños más innovadores y productos más pequeños y ligeros, lo que lo hace la tecnología de elección para la electrónica portátil.
5. Rendimiento mejorado
Los ensamblajes SMT tienden a tener un mejor rendimiento eléctrico porque los terminales más cortos utilizados en los SMD reducen los efectos parásitos como la inductancia y la resistencia. Esto conduce a velocidades de operación más altas y una mejor integridad de señal, lo cual es crucial para circuitos de alta frecuencia y alta velocidad.
6. Disipación térmica mejorada
Los SMD son más eficientes para disipar el calor en comparación con los componentes de agujeros pasantes. El contacto cercano entre el componente y la superficie de la PCB permite una mejor transferencia térmica, lo que es especialmente beneficioso en aplicaciones que generan mucho calor, como la electrónica de potencia y los procesadores.
Conclusión
Si bien la tecnología de agujeros pasantes todavía tiene aplicaciones específicas, particularmente para componentes que necesitan resistencia mecánica o están expuestos a estrés físico, SMT ofrece ventajas claras en términos de eficiencia de espacio, velocidad de ensamblaje, ahorro de costos y rendimiento general. Como resultado, SMT se ha convertido en la elección preferida para la mayoría de la electrónica moderna, desde gadgets de consumo hasta dispositivos industriales y médicos, gracias a su capacidad para ofrecer soluciones de alta densidad, alto rendimiento y costo efectivo.
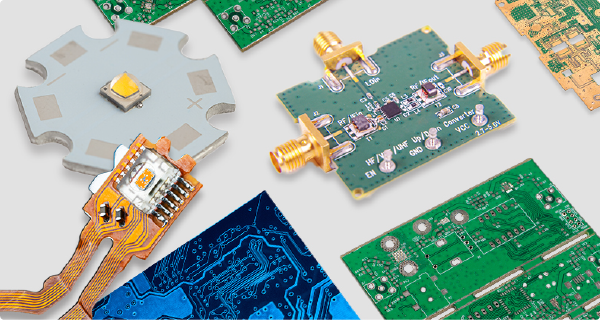
Capítulo 5

Equipo y herramientas de montaje SMT
El montaje SMT es un proceso altamente automatizado y preciso que requiere equipo especializado para garantizar la eficiencia, la precisión y los resultados de alta calidad. La clave para un montaje SMT exitoso radica en el uso de tecnología avanzada, que permite la colocación rápida y precisa de componentes pequeños en la superficie de una placa de circuito impreso (PCB). En esta sección, exploraremos el equipo y las herramientas esenciales utilizados en el proceso de montaje SMT y cómo contribuyen a mejorar la precisión y la eficiencia.
1. Impresora de pasta de soldadura
La impresora de pasta de soldadura es la primera pieza de equipo utilizada en el proceso de montaje SMT. Aplica pasta de soldadura, una mezcla de partículas de soldadura de metal fino y flux, sobre la superficie de la PCB donde se colocarán los componentes. Se utiliza una plantilla, que es una delgada lámina de metal con aberturas que corresponden a los pads de la PCB, para controlar la colocación exacta y el grosor de la pasta de soldadura.
- Propósito: Asegura la aplicación precisa de pasta de soldadura en áreas específicas de la PCB donde se montarán los componentes.
- Importancia: Una aplicación precisa y uniforme de pasta de soldadura es fundamental para crear uniones de soldadura fuertes y confiables durante el proceso de reflujo.
2. Máquina de colocación y sujeción
La máquina de colocación y sujeción es una de las piezas de equipo más cruciales en el montaje SMT. Esta máquina altamente automatizada es responsable de recoger componentes de montaje en superficie de bobinas o bandejas y colocarlos con precisión en la PCB. Las máquinas de colocación y sujeción modernas utilizan brazos robóticos con succión o pinzas para manejar incluso los componentes más pequeños, colocándolos con alta precisión a velocidades increíblemente rápidas.
- Propósito: Coloca DMS (Dispositivos de Montaje en Superficie) en la PCB en sus ubicaciones designadas según el archivo de diseño.
- Importancia: La velocidad y la precisión de la máquina de colocación y sujeción son clave para la eficiencia general del proceso SMT. Con máquinas modernas capaces de colocar miles de componentes por hora, reducen significativamente el tiempo de ensamblaje mientras mantienen una precisión excepcional.
3. Horno de reflujo
Después de que los componentes se colocan en la PCB, el conjunto completo pasa por un horno de reflujo. Este horno especializado calienta la placa a una temperatura lo suficientemente alta como para derretir la pasta de soldadura, permitiendo que fluya y cree conexiones eléctricas y mecánicas fuertes entre los componentes y la PCB. El horno de reflujo utiliza perfiles de temperatura cuidadosamente controlados para asegurarse de que la soldadura se derrita y se enfríe de manera uniforme sin dañar componentes sensibles.
- Propósito: Calienta la PCB para derretir la pasta de soldadura y formar uniones de soldadura sólidas entre los componentes y los pads de la PCB.
- Importancia: La soldadura de reflujo es un paso crítico en el proceso SMT, asegurando que los componentes estén firmemente sujetos y conectados eléctricamente. El control adecuado de la temperatura en el horno de reflujo es esencial para prevenir problemas como puentes de soldadura o daños a los componentes.
4. Inspección óptica automatizada (AOI)
Los sistemas de inspección óptica automatizada (AOI) se utilizan para inspeccionar la PCB después de la soldadura de reflujo. Las máquinas AOI utilizan cámaras de alta resolución y algoritmos avanzados para escanear la PCB y detectar defectos como componentes faltantes, desalineaciones, uniones de soldadura deficientes o otras inconsistencias. Este proceso de inspección ayuda a identificar problemas temprano en el ciclo de producción, reduciendo la necesidad de costosos reworks.
- Propósito: Inspecciona las PCB en busca de defectos, como componentes desalineados o problemas de soldadura, después del proceso de reflujo.
- Importancia: La AOI proporciona un método eficiente y sin contacto para garantizar la calidad de las ensambladuras SMT, minimizando las posibilidades de que se envíen tarjetas defectuosas a los clientes.
5. Sistema de inspección de rayos X
Para ensamblados complejos, como aquellos que involucran componentes de matriz de bola (BGA), se utiliza comúnmente un sistema de inspección de rayos X. Dado que las uniones de soldadura en los componentes BGA están ocultas bajo el paquete, los métodos de inspección óptica tradicionales son insuficientes. La inspección de rayos X permite a los fabricantes examinar la estructura interna de las uniones de soldadura, identificando defectos ocultos como vacíos o grietas.
- Propósito: Inspecciona las uniones de soldadura ocultas, particularmente en componentes BGA y otros donde no es posible la inspección visual.
- Importancia: La inspección de rayos X garantiza que incluso las uniones de soldadura ocultas estén formadas correctamente, proporcionando una mayor garantía de la confiabilidad y funcionalidad de la ensambladura.
6. Impresora de plantilla
La impresora de plantilla se utiliza en las primeras etapas del montaje SMT para aplicar la pasta de soldadura con precisión en la PCB. La plantilla es una delgada lámina de metal con cortes que corresponden a los pads de la PCB donde se necesita aplicar la pasta de soldadura. La impresora de plantilla garantiza que la pasta de soldadura se aplica en cantidades precisas en cada pad, lo que es esencial para formar uniones de soldadura fuertes y confiables durante el reflujo.
- Propósito: Aplica la pasta de soldadura en la PCB de manera controlada utilizando una plantilla.
- Importancia: Asegura que la pasta de soldadura se deposita solo donde se necesita, en las cantidades adecuadas, garantizando uniones de soldadura óptimas en el producto final.
7. Sistema de inspección de pasta de soldadura (SPI)
Un sistema de inspección de pasta de soldadura (SPI) se utiliza para verificar la calidad y la consistencia de la pasta de soldadura aplicada en la PCB. Esta máquina mide la altura, el volumen y la alineación de la pasta de soldadura para asegurarse de que cumpla con las especificaciones requeridas antes de que se coloquen los componentes en la placa.
- Propósito: Verifica la calidad y la consistencia de la aplicación de la pasta de soldadura.
- Importancia: Garantiza una soldadura adecuada confirmando que se ha aplicado la cantidad correcta de pasta de soldadura en cada pad, reduciendo los defectos causados por una cobertura de soldadura deficiente.
8. Estación de rework
Incluso con altos niveles de automatización, pueden ocurrir errores o defectos. Una estación de rework se utiliza para eliminar y reemplazar manualmente componentes defectuosos o reparar problemas de soldadura. Está equipada con herramientas como pistolas de aire caliente, pinzas y soldadores para permitir que los técnicos corrijan errores sin dañar la PCB o otros componentes.
- Propósito: Permite la corrección manual de errores, como reemplazar componentes defectuosos o reparar problemas de soldadura.
- Importancia: Proporciona una forma de abordar defectos menores sin desechar toda la placa, mejorando la eficiencia en cuanto a costos y reduciendo el desperdicio.
Cómo la tecnología mejora la precisión y la eficiencia en el montaje SMT
La tecnología moderna juega un papel fundamental en la precisión y la eficiencia del montaje SMT. El uso de equipo altamente automatizado, como máquinas de colocación y sujeción y hornos de reflujo, garantiza que incluso los componentes más pequeños y complejos se coloquen y solden con precisión extrema. Esta automatización no solo acelera el proceso de fabricación, sino que también reduce el riesgo de error humano, lo que conduce a productos de mayor calidad y menos defectos.
Además, sistemas de inspección avanzados como AOI y máquinas de rayos X ayudan a detectar defectos temprano en el proceso de producción, asegurando que solo se entreguen PCB completamente funcionales y confiables a los clientes. Al integrar tecnología de vanguardia, las líneas de montaje SMT pueden producir ensamblados de alta calidad y volumen a una fracción del tiempo y el costo en comparación con los métodos manuales.
Conclusión
El proceso de montaje SMT depende de una variedad de equipo y herramientas sofisticadas que trabajan juntos para lograr una producción rápida, precisa y rentable. Desde las impresoras de pasta de soldadura y las máquinas de colocación y sujeción hasta los hornos de reflujo y los sistemas de inspección, cada pieza de equipo juega un papel crucial en el éxito del montaje SMT. A medida que la tecnología continúa evolucionando, la precisión y la eficiencia del montaje SMT solo mejorarán, lo que lo convierte en la opción preferida para la fabricación de electrónica moderna.
Capítulo 6
Desafíos comunes en la ensambladura SMT
Mientras que la tecnología de montaje en superficie (SMT) ha revolucionado la industria de la fabricación de electrónica al mejorar la eficiencia, reducir los costos y permitir diseños más compactos, el proceso no está exento de desafíos. Varios problemas pueden surgir durante la ensambladura SMT que pueden afectar la calidad, funcionalidad y confiabilidad del producto final. Aquí, discutiremos algunos de los problemas típicos que se encuentran durante el proceso SMT, como los defectos de soldadura y el mal alineamiento de componentes, y exploraremos soluciones y mejores prácticas para superar estos desafíos.
1. Defectos de soldadura
La soldadura es una de las etapas más críticas en el proceso de ensambladura SMT, ya que forma la conexión eléctrica y mecánica entre los componentes de montaje en superficie y la placa de circuito impreso (PCB). Sin embargo, pueden ocurrir varios defectos de soldadura durante el proceso de reflujo, lo que puede comprometer la calidad de la ensambladura.
Defectos de soldadura comunes:
- Puente de soldadura: Ocurre cuando el exceso de soldadura crea un puente entre dos pads o pistas de componentes adyacentes, lo que lleva a cortocircuitos.
- Soldadura insuficiente: Cuando se aplica demasiada poca soldadura, puede resultar en uniones de soldadura débiles, lo que puede causar fallos intermitentes o completos de la conexión eléctrica.
- Voides de soldadura: Las burbujas de aire atrapadas dentro de la unión de soldadura, conocidas como voides, pueden reducir la resistencia mecánica y la conductividad térmica de la unión, lo que potencialmente puede llevar a fallos de componentes.
- Effecto tombstone: Cuando un extremo de un componente pequeño se levanta durante el reflujo, forma una forma de «tombstone», dejando un lado del componente desconectado.
Soluciones y mejores prácticas para defectos de soldadura:
- Aplicación de pasta de soldadura: Asegurarse de que la aplicación de pasta de soldadura sea consistente y precisa es crucial para prevenir defectos. Utilizar plantillas de alta calidad y mantener una alineación adecuada entre la plantilla y la PCB puede ayudar a evitar problemas como el puente de soldadura y la soldadura insuficiente.
- Perfil del horno de reflujo: Controlar adecuadamente el perfil de temperatura del horno de reflujo es clave para reducir defectos como el efecto tombstone y los voides de soldadura. La temperatura debe aumentarse y disminuirse cuidadosamente para asegurar la fusión y enfriamiento uniformes de la soldadura sin causar estrés térmico a los componentes.
- Cualidad de la pasta de soldadura: Utilizar pasta de soldadura de alta calidad con la viscosidad y composición correctas asegura una mejor adhesión, reduce los voides y mejora la calidad general de las uniones de soldadura.
2. Mal alineamiento de componentes
El mal alineamiento de componentes ocurre cuando los componentes de montaje en superficie no se colocan correctamente en sus pads designados. Este problema puede llevar a fallos eléctricos, conexiones mecánicas deficientes o problemas durante la soldadura de reflujo.
Causas del mal alineamiento de componentes:
- Errores de colocación y recogida: La máquina automática de colocación y recogida puede colocar incorrectamente los componentes debido a problemas de calibración, configuración incorrecta o problemas mecánicos.
- Deformación de la PCB: Si la PCB está deformada o doblada, los componentes pueden no alinearse correctamente con los pads, lo que lleva a conexiones deficientes.
- Mala alineación de la pasta de soldadura: La pasta de soldadura mal alineada puede desplazar la colocación del componente, lo que resulta en defectos de soldadura o conexiones débiles.
Soluciones y mejores prácticas para el mal alineamiento de componentes:
- <strong-Calibración de la máquina de colocación y recogida: Calibrar y mantener regularmente la máquina de colocación y recogida para asegurar una colocación precisa de los componentes. Asegurarse de que la máquina esté programada correctamente y que las boquillas y ventosas funcionen adecuadamente puede reducir errores.
- Planitud de la PCB: Asegurarse de que la PCB esté plana y libre de deformaciones antes de la ensambladura es crucial. Utilizar materiales de PCB de alta calidad y almacenarlos en condiciones adecuadas puede ayudar a prevenir la deformación.
- Inspección visual: Antes del reflujo, realizar una inspección visual o una inspección óptica automática (AOI) para detectar cualquier componente mal alineado. Esto permite realizar correcciones antes del proceso de soldadura, ahorrando tiempo y reduciendo la necesidad de rework.
3. Efecto tombstone
El efecto tombstone ocurre cuando un componente pasivo pequeño, como un resistor o un condensador, se levanta de un extremo durante el proceso de reflujo. Esto deja un lado del componente desconectado de la PCB, lo que causa un circuito abierto. El efecto tombstone es más común con componentes más pequeños, como los paquetes 0201 o 0402.
Causas del efecto tombstone:
- Calentamiento desigual: Si un lado del componente se calienta más rápido que el otro durante el reflujo, la soldadura del lado más caliente se fundirá primero y tirará del componente hacia arriba.
- Desequilibrio de la pasta de soldadura: Si la pasta de soldadura no se aplica de manera uniforme, puede causar fuerzas desiguales durante el reflujo, lo que lleva al efecto tombstone.
Soluciones y mejores prácticas para el efecto tombstone:
- Optimización del perfil de reflujo: Asegurarse de que el perfil de temperatura del horno de reflujo sea uniforme y caliente ambos extremos del componente al mismo tiempo, reduciendo el riesgo de efecto tombstone.
- Diseño de la plantilla: Utilizar una plantilla bien diseñada que aplique cantidades uniformes de pasta de soldadura a ambos pads puede prevenir desequilibrios que llevan al efecto tombstone.
4. Formación de bolas de soldadura
La formación de bolas de soldadura ocurre cuando se forman pequeñas bolas de soldadura en la PCB en lugar de fluir uniformemente para formar una unión de soldadura adecuada. Estas bolas de soldadura pueden causar cortocircuitos o llevar a uniones de soldadura poco confiables.
Causas de la formación de bolas de soldadura:
- Pasta de soldadura excesiva: Aplicar demasiada pasta de soldadura puede resultar en un exceso de soldadura que se extiende y forma bolas durante el reflujo.
- Humedad en la PCB o la pasta de soldadura: Si la PCB o la pasta de soldadura contienen humedad, puede causar salpicaduras de soldadura durante el reflujo, lo que lleva a la formación de bolas de soldadura.
Soluciones y mejores prácticas para la formación de bolas de soldadura:
- Control de la cantidad de pasta de soldadura: Utilizar la cantidad correcta de pasta de soldadura, aplicada con una plantilla adecuadamente diseñada. Asegurarse de que las aberturas de la plantilla estén correctamente dimensionadas para evitar una aplicación excesiva de pasta.
- <strong-Almacenamiento en seco: Almacenar las PCB y la pasta de soldadura en condiciones secas para prevenir la absorción de humedad. El precalentamiento de las PCB antes del reflujo también puede ayudar a eliminar cualquier humedad que podría causar salpicaduras de soldadura.
5. Insuficiente humectación de la soldadura
La humectación de la soldadura se refiere a la capacidad de la soldadura para fluir y adherirse a las pistas de los componentes y los pads de la PCB. Una humectación insuficiente puede resultar en uniones de soldadura débiles, que pueden fallar bajo estrés mecánico o térmico.
Causas de la insuficiente humectación de la soldadura:
- Contaminación de la PCB o los componentes: La oxidación o la contaminación en los pads de la PCB o las pistas de los componentes pueden prevenir una adhesión de soldadura adecuada.
- Temperatura de soldadura baja: Si la temperatura del horno de reflujo es demasiado baja, la soldadura puede no fundirse completamente, lo que lleva a una mala humectación.
Soluciones y mejores prácticas para la insuficiente humectación de la soldadura:
- Limpieza de la superficie: Asegurarse de que tanto la PCB como los componentes estén libres de contaminantes como polvo, aceite u oxidación. Utilizar un recubrimiento protector en las PCB durante el almacenamiento puede ayudar a prevenir la oxidación.
- Temperatura de reflujo óptima: Asegurarse de que el horno de reflujo esté configurado a la temperatura correcta para permitir que la soldadura se funda completamente y humedezca las superficies de manera efectiva.
6. Daño a los componentes
Durante la ensambladura SMT, los componentes pueden dañarse debido al calor excesivo, el manejo físico o el almacenamiento inadecuado. Los componentes dañados pueden llevar a fallos de ensambladura o a una reducción de la confiabilidad del producto.
Causas del daño a los componentes:
- Calor de reflujo excesivo: Si la temperatura del horno de reflujo es demasiado alta o la placa pasa demasiado tiempo en el horno, los componentes sensibles pueden dañarse.
- Manejo mecánico: Un manejo inadecuado de los componentes durante el proceso de colocación y recogida o durante el almacenamiento puede resultar en daños físicos.
Soluciones y mejores prácticas para el daño a los componentes:
- Control del perfil de reflujo: Utilizar un perfil de temperatura de reflujo cuidadosamente controlado para evitar sobrecalentar los componentes.
- Procedimientos de manejo adecuados: Implementar las mejores prácticas para el manejo de componentes, incluyendo el almacenamiento adecuado en entornos seguros contra descargas electrostáticas (ESD) y el uso de equipos automatizados para minimizar el contacto físico.
Conclusión
La ensambladura SMT es un proceso altamente eficiente, pero puede presentar varios desafíos, incluyendo defectos de soldadura, mal alineamiento de componentes y otros problemas que pueden afectar la calidad del producto final. Al entender las causas de estos desafíos comunes y implementar las mejores prácticas, como la aplicación adecuada de pasta de soldadura, el mantenimiento del equipo y la optimización de los perfiles de reflujo, los fabricantes pueden reducir significativamente los defectos y mejorar la confiabilidad de sus ensambladuras SMT. La inspección regular y el manejo cuidadoso de los componentes a lo largo del proceso de ensambladura también son esenciales para asegurar resultados de alta calidad.
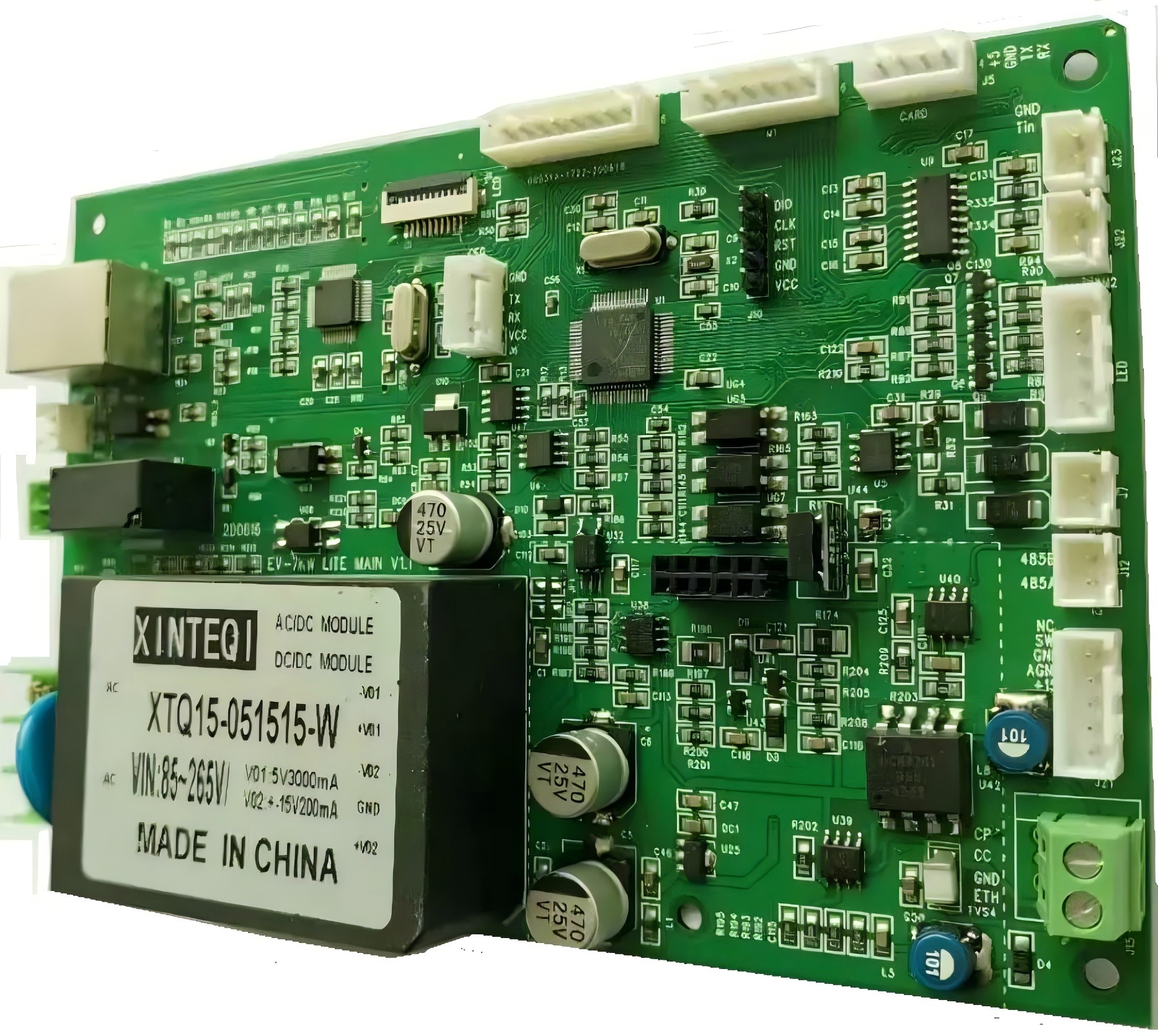
Capítulo 7
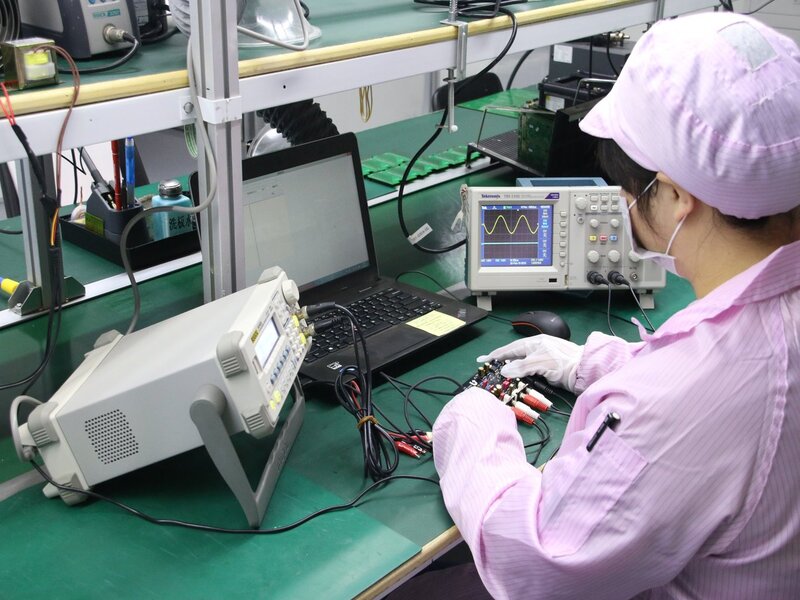
Consideración de Diseño de Ensamblaje SMT
Diseñar tarjetas de circuito impreso (PCB) para el ensamblaje de tecnología de montaje en superficie (SMT) requiere una atención cuidadosa al detalle para garantizar que el proceso de fabricación sea eficiente, rentable y produzca resultados de alta calidad. Un diseño adecuado puede reducir significativamente la probabilidad de problemas de ensamblaje y aumentar el rendimiento y la confiabilidad del producto final. Esta sección cubrirá las pautas de diseño clave para optimizar sus PCB para el ensamblaje SMT y explicará cómo evitar errores de diseño que pueden complicar el proceso de ensamblaje.
1. Colocación y Orientación de Componentes
La colocación adecuada de los componentes es uno de los aspectos más críticos del diseño de ensamblaje SMT. La mala colocación de los componentes puede generar problemas como la mala alineación, el «tombstoning» o la formación de puentes de soldadura durante el proceso de reflujo.
Consideraciones clave:
- Colocación Uniforme: Asegúrese de que los componentes estén colocados en una dirección uniforme siempre que sea posible. Alinear los componentes en la misma orientación no solo simplifica el proceso de colocación y recogida, sino que también reduce los errores durante la colocación automatizada.
- Minimizar la Sombra de los Componentes: Coloque los componentes más altos, como conectores o condensadores, lejos de los componentes más pequeños para evitar la «sombra» durante la soldadura o la inspección, lo que puede resultar en una soldadura o inspección incorrecta.
- Evitar el Agrupamiento Excesivo: Aunque la eficiencia del espacio es importante, agrupar los componentes demasiado juntos puede generar dificultades en la aplicación de la pasta de soldadura, la formación de puentes de soldadura o problemas de inspección. Asegúrese de que haya un espacio adecuado entre los componentes.
Mejor Práctica:
- Utilice software de diseño con reglas de diseño integradas para comprobar la distancia y alineación adecuadas de los componentes. Siga las pautas del fabricante para las distancias de colocación para optimizar el equipo de colocación y recogida automatizado.
2. Diseño de Pads de Soldadura
Los pads de soldadura son cruciales para garantizar una conexión sólida entre la PCB y los dispositivos de montaje en superficie (SMD). Un diseño adecuado de los pads de soldadura puede prevenir problemas como la soldadura insuficiente, la formación de puentes de soldadura y la mala alineación de los componentes.
Consideraciones clave:
- Tamaño y Forma del Pad: Asegúrese de que los pads de soldadura sean del tamaño y la forma correctos para los componentes que se están utilizando. Los pads que son demasiado grandes o demasiado pequeños pueden causar problemas de soldadura, como un enfriamiento desigual o una unión de soldadura débil. Para componentes con un paso fino, utilice pads más pequeños con un espaciado preciso.
- Máscara de Soldadura: Asegúrese de que haya un espacio suficiente entre los pads de soldadura y la máscara de soldadura para evitar la formación de puentes de soldadura. La máscara de soldadura define el área donde no debe fluir la soldadura, por lo que su diseño es fundamental para prevenir cortocircuitos.
- Pads Térmicos: Para componentes que requieren disipación de calor, como transistores de potencia o BGAs, los pads térmicos son esenciales. Estos pads deben estar diseñados para permitir una transferencia de calor eficiente y, al mismo tiempo, proporcionar una conectividad eléctrica adecuada.
Mejor Práctica:
- Utilice huellas recomendadas por el fabricante para cada componente y realice comprobaciones de reglas de diseño (DRC) para verificar que los tamaños y formas de los pads se ajusten a los estándares.
3. Colocación de Vías
Las vías son esenciales para crear conexiones eléctricas entre diferentes capas de la PCB, pero su colocación puede afectar el proceso de ensamblaje. La mala colocación de las vías puede interferir con la colocación de los componentes y la soldadura.
Consideraciones clave:
- Evitar Vías en Pads de Soldadura: Colocar vías directamente en los pads de soldadura, también conocido como «vía en el pad», puede hacer que la soldadura se filtre a través del agujero de la vía, reduciendo la cantidad de soldadura disponible para el componente. Esto puede debilitar la unión de soldadura y provocar problemas de confiabilidad.
- Espaciado de Vías: Asegúrese de que las vías estén colocadas a una distancia segura de los componentes y otras trazas. Un gran número de vías muy juntas puede generar una concentración de calor durante el reflujo, lo que puede afectar la calidad de la soldadura.
Mejor Práctica:
- Si las vías necesitan colocarse en los pads de soldadura (debido a limitaciones de espacio), utilice vías «cubiertas» o «rellenadas» para evitar que la soldadura fluya a través de ellas.
4. Gestión Térmica
La gestión térmica es fundamental para componentes que generan calor, como circuitos integrados de potencia y procesadores. Un diseño adecuado garantiza que el calor se disipe de manera efectiva y no cause daños a los componentes o afecte el rendimiento de la PCB.
Consideraciones clave:
- Vías Térmicas: Utilice vías térmicas para disipar el calor lejos de componentes sensibles al calor. Estas vías deben conectarse a grandes planos de cobre que puedan distribuir el calor de manera uniforme en toda la PCB.
- Disipadores de Calor y Vierte de Cobre: Para componentes de alta potencia, considere utilizar disipadores de calor o vierte de cobre (grandes áreas de cobre en la PCB) para ayudar a disipar el calor. Estos pueden conectarse al plano de tierra u otras capas para mejorar la transferencia de calor.
Mejor Práctica:
- Diseñe la PCB con patrones de alivio térmico adecuados para garantizar que el calor se distribuya de manera uniforme en toda la placa. Considere utilizar software de simulación para modelar el comportamiento térmico durante la operación.
5. Ancho y Espaciado de Trazas
El ancho y el espaciado de las trazas en la PCB son fundamentales para garantizar que la placa pueda manejar la corriente y las señales que se requieren sin causar sobrecalentamiento o interferencia eléctrica.
Consideraciones clave:
- Ancho de Traza Adecuado: Asegúrese de que las trazas sean lo suficientemente anchas como para manejar la corriente requerida sin sobrecalentarse. La capacidad de llevar corriente de una traza depende de su ancho y el grosor de la capa de cobre.
- Claridad para Señales de Alta Tensión: Para aplicaciones de alta tensión, asegúrese de que las trazas estén lo suficientemente separadas como para evitar arcos o cortocircuitos entre ellas. Siga las normas de la industria (como IPC-2221) para las pautas de claridad.
- Impedancia Controlada: Para trazas de señales de alta velocidad, la impedancia controlada es fundamental. Esto garantiza que las señales se transmitan sin distorsión o reflexión, lo que puede degradar el rendimiento en aplicaciones como RF o transmisión de datos.
Mejor Práctica:
- Utilice calculadoras en línea o software de diseño de PCB para calcular el ancho y el espaciado de trazas óptimos para su aplicación específica. Para diseños de alta velocidad, utilice pautas de impedancia controlada y evite esquinas afiladas en las trazas.
6. Acceso a Componentes y Puntos de Prueba
Para garantizar que la PCB pueda probarse y repararse de manera eficiente, es esencial incluir puntos de prueba y proporcionar acceso adecuado a componentes críticos.
Consideraciones clave:
- Puntos de Prueba Accesibles: Incluya puntos de prueba para señales y rieles de potencia clave para facilitar las pruebas durante el ensamblaje y la depuración. Estos puntos deben ser fácilmente accesibles para sondas de prueba o equipo de prueba automatizado.
- No Obstruir Componentes: Asegúrese de que los componentes no estén colocados en áreas donde se necesiten puntos de prueba o conectores. Esto ayudará durante la fase de prueba y el mantenimiento o reparaciones futuras.
Mejor Práctica:
- Planifique los puntos de prueba temprano en el proceso de diseño y verifique que estén colocados en lugares donde puedan ser fácilmente accesados por equipo de inspección o sondas de prueba.
7. Evitar el «Tombstoning»
El «tombstoning» ocurre cuando componentes pasivos pequeños, como resistores o condensadores, se levantan por un lado durante el proceso de reflujo. Esto generalmente resulta en un circuito abierto y es más común con componentes más pequeños.
Consideraciones clave:
- Diseño de Pad Simétrico: Asegúrese de que los pads para componentes pequeños como 0201 o 0402 estén diseñados simétricamente para que ambos extremos del componente se calienten de manera uniforme durante el proceso de reflujo. Un calentamiento desigual puede hacer que un extremo se levante.
- Aplicación Adecuada de Pasta de Soldadura: Asegúrese de que la pasta de soldadura se aplique de manera uniforme en ambos pads. Volúmenes de soldadura desiguales pueden causar un desequilibrio en las fuerzas durante el reflujo, lo que puede provocar el «tombstoning».
Mejor Práctica:
- Utilice el grosor de esténcil correcto y asegúrese de que las aberturas del esténcil estén bien diseñadas para aplicar una cantidad uniforme de pasta de soldadura a componentes pequeños.
8. Consideraciones de Panelización
La panelización es el proceso de agrupar múltiples PCB en un solo panel para la fabricación, lo que facilita su manejo durante el ensamblaje. Una panelización incorrecta puede generar problemas de ensamblaje y defectos.
Consideraciones clave:
- Diseño de Panel Consistente: Asegúrese de que el diseño del panel permita un manejo eficiente durante el proceso de ensamblaje. Incluya marcadores de alineación para la alineación y asegúrese de que no haya puntos débiles en el panel que puedan causar deformaciones.
- Ruta y Colocación de Pestañas: Si utiliza V-score o ruta de pestañas para la despanelización, asegúrese de que las líneas de ruta no interfieran con componentes o trazas cerca de los bordes de la PCB.
Mejor Práctica:
- Trabaje con el fabricante para diseñar el diseño del panel, asegurándose de que cumpla con los requisitos del equipo de ensamblaje y pueda ser fácilmente despanelizado sin dañar las placas.
9. Minimizar la Interferencia Electromagnética (EMI)
A medida que las PCB se vuelven más compactas, el riesgo de interferencia electromagnética (EMI) aumenta. Un diseño adecuado puede ayudar a mitigar los problemas de EMI, que pueden degradar el rendimiento de circuitos de alta velocidad o dispositivos inalámbricos.
Consideraciones clave:
- Planos de Tierra: Utilice planos de tierra sólidos para reducir la EMI y mejorar la integridad de la señal. El plano de tierra debe cubrir toda la PCB, con mínimas brechas o divisiones.
- Blindaje: Para circuitos particularmente sensibles, considere utilizar latas de blindaje o jaulas de Faraday para proteger los componentes de fuentes externas de EMI.
Mejor Práctica:
- Utilice buenas prácticas de diseño como separar circuitos de alta velocidad y baja velocidad, routear trazas de señal perpendiculares a los planos de potencia y minimizar la longitud de las trazas para señales de alta velocidad.
10. Serigrafía y Etiquetado
La serigrafía proporciona información vital sobre la colocación y orientación de los componentes, y una etiquetado adecuado puede prevenir errores de ensamblaje.
Consideraciones clave:
- Marcas de Serigrafía Claras: Asegúrese de que todos los componentes, especialmente los polarizados, tengan marcas de serigrafía claras y precisas para indicar la orientación correcta. Esto es particularmente importante para diodos, condensadores e IC con orientaciones de pin específicas.
- No Colocar Serigrafía en Pads: Asegúrese de que la serigrafía no se superponga con los pads de soldadura, ya que esto puede afectar la calidad de la soldadura durante el reflujo.
Mejor Práctica:
- Verifique la capa de serigrafía antes de finalizar el diseño para asegurarse de que todos los componentes estén claramente etiquetados y no haya superposiciones de serigrafía en áreas críticas de soldadura.
Conclusión
Diseñar para el ensamblaje SMT requiere una atención cuidadosa a la colocación de los componentes, el diseño de los pads de soldadura, la gestión térmica y el diseño de las trazas para garantizar un proceso de fabricación exitoso. Siguiendo estas pautas de diseño y evitando errores comunes, los diseñadores pueden reducir los defectos, mejorar la eficiencia de la producción y garantizar la confiabilidad del producto final. La implementación de las mejores prácticas en el diseño de PCB para el ensamblaje SMT no solo simplifica el proceso de ensamblaje, sino que también mejora el rendimiento y la durabilidad de los productos electrónicos que se producen.
Capítulo 8
Control de Calidad en la Asamblea SMT
Garantizar resultados de alta calidad en la asamblea SMT es crucial para el rendimiento y la confiabilidad del producto final. Se emplean varios métodos de control de calidad a lo largo del proceso SMT para detectar defectos temprano, prevenir problemas de asamblea y asegurar la integridad de la tarjeta de circuito impreso (PCB). Dos técnicas clave, Inspección Óptica Automatizada (AOI) e Inspección de Rayos X, se utilizan ampliamente para mantener altos estándares en el proceso de asamblea. Además, la adhesión a certificaciones de calidad como ISO9001 garantiza que todos los procesos estén rigurosamente controlados y cumplan con los estándares internacionales.
1. Inspección Óptica Automatizada (AOI)
La Inspección Óptica Automatizada (AOI) es un método de inspección visual sin contacto que escanea las PCB ensambladas para identificar cualquier defecto, como componentes faltantes, desalineaciones o problemas de soldadura. Las máquinas AOI utilizan cámaras de alta resolución y software de reconocimiento de patrones para detectar problemas en una etapa muy temprana de la producción. El sistema compara el colocación y la soldadura real de los componentes con el diseño y el diseño previstos.
Cómo AOI garantiza la calidad:
- Detecta desalineaciones: AOI identifica rápidamente cualquier componente mal colocado o inclinado, evitando problemas adicionales durante el proceso de reflujo.
- Revisa defectos de soldadura: Examina las uniones de soldadura para detectar problemas comunes como soldadura insuficiente, soldadura puente o uniones de soldadura frías.
- Rápido y preciso: Los sistemas AOI ofrecen un método rápido y muy preciso para inspeccionar grandes volúmenes de PCB, lo que reduce significativamente el riesgo de productos defectuosos que llegan a la siguiente etapa de producción.
2. Inspección de Rayos X
La inspección de rayos X es particularmente útil para inspeccionar PCB complejos que utilizan componentes avanzados como Matrices de Bola (BGAs), donde las uniones de soldadura están ocultas bajo el componente. Dado que estas uniones no pueden ser inspeccionadas visualmente, las máquinas de rayos X permiten a los fabricantes ver dentro de la PCB y examinar la calidad de las uniones de soldadura y las conexiones.
Cómo la inspección de rayos X garantiza la calidad:
- Detecta defectos ocultos: La inspección de rayos X revela problemas como vacíos en las uniones de soldadura, grietas o soldadura insuficiente bajo componentes BGA y otros componentes ocultos.
- Garantiza una soldadura adecuada: Ayuda a garantizar que cada unión de soldadura esté segura y esté formada correctamente, incluso cuando no se puede inspeccionar visualmente.
- Crítico para diseños de alta densidad: A medida que los componentes se vuelven más pequeños y más densamente empaquetados, la inspección de rayos X se vuelve esencial para verificar que todas las conexiones funcionen correctamente.
3. Estándares de calidad ISO9001
La certificación ISO9001 es un estándar de gestión de la calidad reconocido internacionalmente que garantiza que la empresa sigue un proceso consistente y confiable en la fabricación. Para la asamblea SMT, adherirse a los estándares ISO9001 significa que cada paso del proceso, desde el diseño hasta el ensamblaje final, está cuidadosamente monitoreado y controlado.
Cómo ISO9001 contribuye a la calidad:
- Control de proceso: ISO9001 requiere que todos los procesos estén documentados, controlados y mejorados continuamente, lo que reduce la probabilidad de errores y garantiza una calidad consistente.
- Gestión de riesgos: Al seguir los estándares ISO9001, los fabricantes implementan prácticas de gestión de riesgos que identifican problemas potenciales temprano, lo que conduce a menos defectos y una tasa más alta de producción exitosa.
- Satisfacción del cliente: ISO9001 garantiza que se cumplan los requisitos del cliente, ya que los fabricantes están obligados a cumplir con estrictos estándares de calidad, lo que resulta en productos confiables que cumplen o superan las expectativas del cliente.
Conclusión
El control de calidad en la asamblea SMT se logra a través de una combinación de técnicas de inspección avanzadas como AOI y la inspección de rayos X, así como la adhesión a estándares de calidad reconocidos por la industria como ISO9001. Estos métodos garantizan que se identifiquen y corrijan los defectos temprano en el proceso, reduciendo el riesgo de productos defectuosos y asegurando la confiabilidad de los ensamblajes finales. Al implementar medidas de control de calidad estrictas, los fabricantes pueden producir consistentemente PCB de alto rendimiento y sin defectos que cumplen con los más altos estándares de calidad.
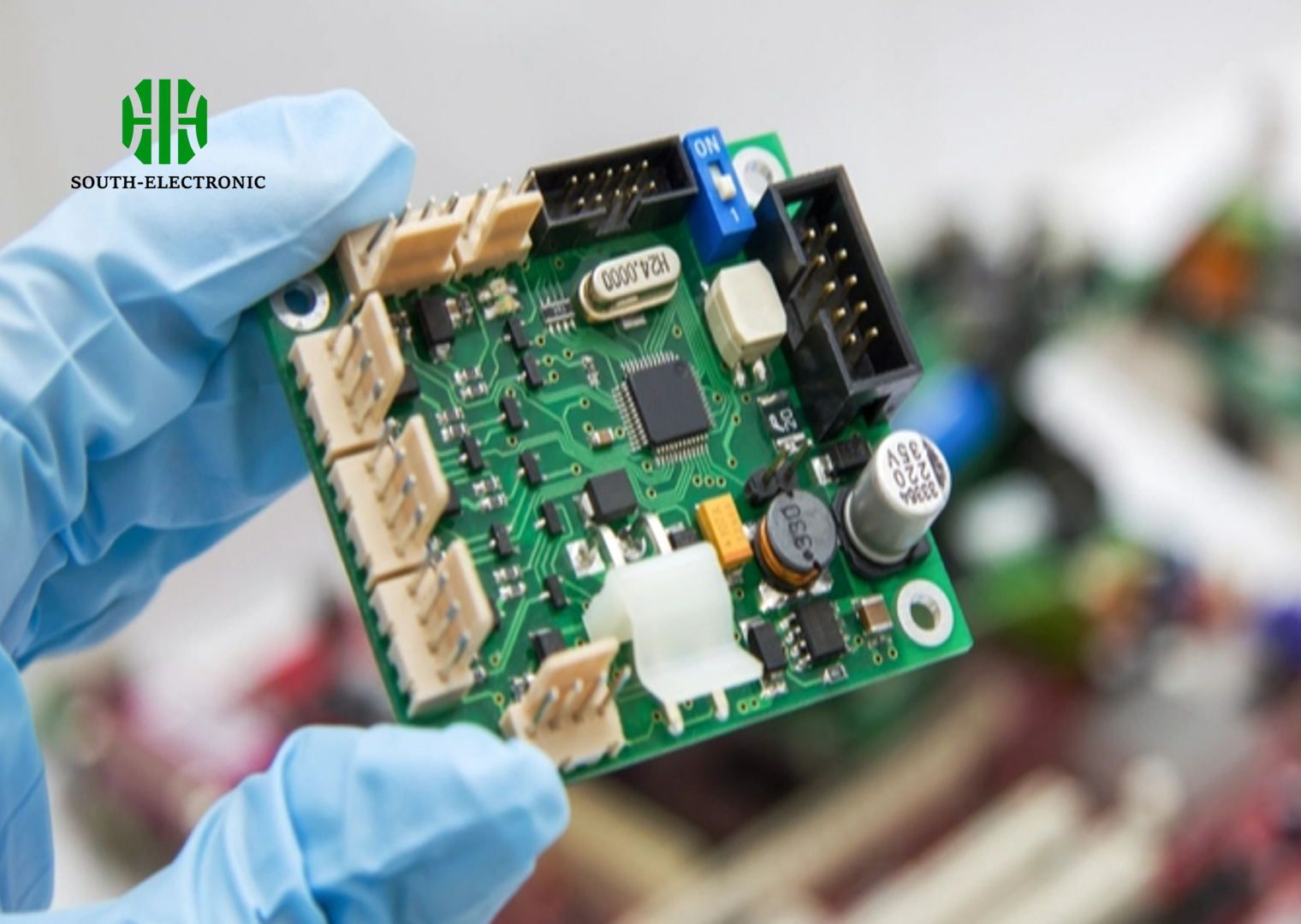
Capítulo 9

Aplicaciones de la ensambladura SMT en diferentes industrias
La tecnología de montaje en superficie (SMT) ha revolucionado la industria de fabricación de electrónica, convirtiéndose en un elemento clave para la producción de dispositivos electrónicos complejos, de alto rendimiento y compactos en diversos sectores. La ensambladura SMT se utiliza ampliamente en una amplia gama de industrias debido a su capacidad para respaldar la miniaturización, mejorar el rendimiento y reducir los costos de producción. En esta sección, exploraremos cómo la ensambladura SMT beneficia a diferentes industrias, junto con ejemplos del mundo real de su aplicación.
1. Electrónica de consumo
La industria de la electrónica de consumo es quizás la mayor beneficiaria de la ensambladura SMT. Con la creciente demanda de dispositivos más pequeños, más rápidos y más potentes, SMT permite a los fabricantes producir tarjetas de circuito impreso altamente compactas que admiten funcionalidades avanzadas mientras mantienen la asequibilidad.
Aplicaciones en electrónica de consumo:
- Teléfonos inteligentes y tabletas: La ensambladura SMT se utiliza para empaquetar cientos de componentes diminutos en tarjetas de circuito impreso en dispositivos como teléfonos inteligentes y tabletas. Estos dispositivos dependen de la precisión de SMT para integrar procesadores, chips de memoria y módulos de comunicación en diseños pequeños y ligeros.
- Dispositivos wearables: Desde rastreadores de actividad hasta relojes inteligentes, SMT permite la miniaturización de componentes, lo que hace posible crear tecnología wearable elegante y ligera.
Ejemplo: Los iPhones de Apple dependen en gran medida de la ensambladura SMT para integrar circuitos complejos que alimentan todo, desde los procesadores de la serie A hasta la pantalla táctil y los sistemas de gestión de baterías.
2. Industria automotriz
A medida que los vehículos se vuelven más avanzados tecnológicamente, la industria automotriz utiliza cada vez más la ensambladura SMT para construir los complejos sistemas electrónicos necesarios para los automóviles modernos. Estos sistemas incluyen todo, desde unidades de infoentretenimiento y navegación hasta funciones de seguridad críticas como sistemas de frenos antibloqueo (ABS) y sistemas de asistencia al conductor avanzados (ADAS).
Aplicaciones en la industria automotriz:
- Unidades de control electrónicas (ECU): SMT se utiliza para ensamblar las tarjetas de circuito impreso altamente densas en las ECU, que controlan diversas funciones del vehículo, como la gestión del motor, los frenos y el control de estabilidad.
- ADAS y conducción autónoma: Características avanzadas como el asistente de mantenimiento de carril, el control de crucero adaptativo y los sensores de estacionamiento dependen de SMT para crear circuitos compactos y confiables para el procesamiento de sensores.
Ejemplo: Los vehículos eléctricos de Tesla hacen un uso extensivo de la ensambladura SMT para sus ECU, sistemas de gestión de baterías y tecnologías de conducción autónoma, lo que ayuda a la empresa a reducir el tamaño y el peso de componentes críticos.
3. Aeroespacio y defensa
En las industrias aeroespacial y de defensa, donde la confiabilidad, el rendimiento y la reducción de peso son fundamentales, la ensambladura SMT es fundamental para producir sistemas electrónicos avanzados utilizados en aeronaves, satélites y aplicaciones de defensa. Estos sistemas deben cumplir con estrictos estándares de rendimiento y durabilidad mientras operan en entornos extremos.
Aplicaciones en aeroespacio y defensa:
- Aviónica: La ensambladura SMT se utiliza para crear tarjetas de circuito impreso compactas y ligeras para sistemas de aviónica, incluyendo comunicaciones, navegación y sistemas de control de vuelo.
- Satélites y exploración espacial: SMT permite la producción de electrónica ligera y altamente confiable utilizada en satélites y sondas espaciales, donde las limitaciones de espacio y las condiciones ambientales extremas son factores clave.
Ejemplo: El rover de Marte, lanzado por la NASA, depende de circuitos ensamblados con SMT para controlar su navegación, sistemas de energía e instrumentos científicos, todos diseñados para soportar las condiciones extremas del espacio.
4. Dispositivos médicos
En el campo médico, la ensambladura SMT es esencial para crear electrónica miniaturizada, precisa y confiable utilizada en equipo de diagnóstico, dispositivos de monitoreo y dispositivos médicos implantables. Estos dispositivos a menudo requieren estrictos estándares de rendimiento, confiabilidad y seguridad.
Aplicaciones en dispositivos médicos:
- Dispositivos médicos wearables: Dispositivos como monitores de ritmo cardíaco, sensores de glucosa y máquinas de ECG portátiles dependen de la ensambladura SMT para la miniaturización y la confiabilidad, lo que los hace cómodos y fáciles de usar para los pacientes.
- Dispositivos implantables: Los marcapasos y los implantes cocleares utilizan la tecnología SMT para crear circuitos compactos y eficientes que pueden implantarse en el cuerpo humano y funcionar de manera confiable durante períodos prolongados.
Ejemplo: Los marcapasos y las bombas de insulina de Medtronic son ejemplos de dispositivos médicos que utilizan la ensambladura SMT para crear sistemas compactos y altamente confiables que son fundamentales para la salud y el bienestar de los pacientes.
5. Telecomunicaciones
Los sistemas de telecomunicaciones, que son responsables de transmitir y procesar datos a alta velocidad, se benefician significativamente de la ensambladura SMT. Con la creciente demanda de comunicación más rápida y confiable, SMT se utiliza para crear las tarjetas de circuito impreso densamente empaquetadas y de alto rendimiento necesarias para el equipo de red moderno.
Aplicaciones en telecomunicaciones:
- Estaciones base celulares: SMT se utiliza para construir las tarjetas de circuito impreso en las estaciones base que manejan la comunicación celular, lo que apoya la expansión de las redes 5G.
- Comunicaciones de fibra óptica: El equipo de transmisión de datos de alta velocidad, como transceptores de fibra óptica y conmutadores de red, utiliza SMT para ensamblar circuitos compactos y eficientes que garantizan la transmisión de señales de manera confiable.
Ejemplo: Los enrutadores de alta velocidad y el equipo de red de Cisco utilizan la ensambladura SMT para cumplir con las demandas de alto rendimiento de las redes de telecomunicaciones modernas, incluidas las redes 5G y de fibra óptica.
6. Automatización industrial y de fabricación
En la automatización industrial y de fabricación, la ensambladura SMT es fundamental para producir los sistemas de control que alimentan a los robots, los sistemas de transporte y el equipo de monitoreo. Estos sistemas deben ser altamente confiables y a menudo operan en entornos hostiles.
Aplicaciones en automatización industrial:
- Controladores lógicos programables (PLC): SMT se utiliza para crear las tarjetas de circuito impreso para los PLC, que controlan la maquinaria y los procesos en fábricas y entornos industriales.
- Robótica: Las tarjetas de control ensambladas con SMT son esenciales para los movimientos y operaciones precisos de los robots industriales utilizados en la automatización.
Ejemplo: Los sistemas de control industrial y el equipo de automatización de Siemens utilizan la ensambladura SMT para crear tarjetas de circuito impreso confiables y compactas que gestionan procesos de fábrica complejos.
Conclusión
La ensambladura SMT es una tecnología esencial en una amplia gama de industrias, desde la electrónica de consumo hasta el sector aeroespacial. Su capacidad para crear tarjetas de circuito impreso compactas, confiables y de alto rendimiento ha hecho que se convierta en el estándar para la fabricación de electrónica moderna. Ya sea permitiendo la miniaturización de teléfonos inteligentes o garantizando la confiabilidad de los sistemas aeroespaciales, la ensambladura SMT juega un papel fundamental en el mundo tecnológico avanzado de hoy en día.
Capítulo 10
Elegir al socio de ensamblaje SMT adecuado
Seleccionar al proveedor de servicios de ensamblaje de tecnología de montaje en superficie (SMT) adecuado es una decisión crítica que puede tener un impacto significativo en la calidad, el costo y el plazo de su proyecto. Ya sea que esté trabajando en prototipos a pequeña escala o en producciones de gran volumen, elegir a un socio que se alinee con sus necesidades técnicas y comerciales es esencial para garantizar el éxito de su ensamblaje de electrónica. A continuación, se presentan algunos de los factores clave a considerar al seleccionar un proveedor de ensamblaje SMT, junto con información sobre por qué la calidad, el tiempo de entrega y el soporte técnico son cruciales para proyectos exitosos.
1. Estándares y certificaciones de calidad
La calidad es fundamental en el ensamblaje SMT, ya que cualquier defecto en el producto final puede provocar fallos en el campo, aumentar los costos y dañar su reputación. Es esencial asegurarse de que su socio de ensamblaje SMT cumpla con altos estándares de calidad y tenga certificaciones relevantes.
Factores a considerar:
- Certificación ISO9001: Busque proveedores que estén certificados ISO9001. Esta certificación demuestra que la empresa sigue estrictos estándares de gestión de la calidad, lo que garantiza resultados consistentes y confiables en el proceso de fabricación.
- Control de calidad interno: Asegúrese de que el proveedor tenga procesos de control de calidad robustos, como inspección óptica automática (AOI), inspección de rayos X y pruebas en circuito, para detectar defectos temprano y mantener altos estándares en todo el proceso de ensamblaje.
- Calidad de la fuente de componentes: Asegúrese de que el proveedor obtenga componentes de alta calidad y confiables de proveedores de confianza para prevenir problemas como componentes falsificados o de baja calidad que ingresen a su cadena de suministro.
Por qué es importante: El ensamblaje de alta calidad minimiza los defectos y el retrabajo, lo que resulta en un producto más confiable y menores costos generales a largo plazo.
2. Tiempo de entrega y confiabilidad
Para muchos proyectos de electrónica, el tiempo de lanzamiento al mercado es un factor crítico. Un socio de ensamblaje SMT confiable debe ser capaz de cumplir con los plazos del proyecto sin comprometer la calidad. Los tiempos de entrega rápidos pueden darle una ventaja competitiva, especialmente en industrias en constante evolución como la electrónica de consumo y las telecomunicaciones.
Factores a considerar:
- Tiempo de entrega: Pregunte sobre el tiempo de entrega promedio del proveedor para corridas de prototipos y pedidos de producción completos. Los proveedores con procesos optimizados y líneas de producción eficientes pueden ofrecer tiempos de entrega más rápidos.
- Registro de entrega a tiempo: Asegúrese de que el proveedor tenga un historial comprobado de entrega de proyectos a tiempo. Los retrasos en el proceso de ensamblaje pueden tener un efecto dominó en todo su cronograma de producción.
- Capacidad de escalabilidad: Si espera escalar su producción en el futuro, asegúrese de que el socio tenga la capacidad y la flexibilidad para manejar volúmenes más grandes sin retrasos significativos.
Por qué es importante: La entrega rápida y confiable le permite llevar sus productos al mercado rápidamente, lo que le da una ventaja competitiva y le ayuda a cumplir con las demandas de los clientes a tiempo.
3. Pericia técnica y soporte
Un socio de ensamblaje SMT competente debe ofrecer más que solo servicios de ensamblaje; debe ofrecer pericia técnica y soporte para ayudarlo a navegar los desafíos en el diseño, la selección de componentes y la fabricación. El socio adecuado podrá ofrecer ideas y soluciones que pueden mejorar la calidad y la fabricabilidad de su producto.
Factores a considerar:
- Soporte de ingeniería: Busque un socio con un equipo de ingeniería experimentado que pueda revisar su diseño de PCB y ofrecer sugerencias para mejoras, como la optimización para la fabricación (DFM) o la minimización de posibles problemas de ensamblaje.
- Asistencia para prototipos: Para nuevos productos, es importante trabajar con un proveedor que pueda girar rápidamente prototipos y ofrecer comentarios sobre posibles defectos de diseño o áreas de mejora antes de pasar a la producción en masa.
- Soporte posterior a la venta: El soporte técnico no termina una vez que las placas están ensambladas. Asegúrese de que su socio ofrezca asistencia técnica posterior a la venta para abordar cualquier problema que surja después de la entrega.
Por qué es importante: Trabajar con un proveedor de ensamblaje SMT que ofrece un fuerte soporte técnico puede ayudarlo a evitar errores costosos, garantizar corridas de producción sin problemas y mejorar la calidad general de su producto.
4. Flexibilidad y opciones de personalización
No todos los proyectos de ensamblaje SMT son iguales, y su socio de ensamblaje debe ofrecer flexibilidad para adaptarse a sus necesidades únicas. Ya sea un prototipo de bajo volumen o una producción de gran volumen, su socio debe ser capaz de adaptar sus servicios para satisfacer sus requisitos específicos.
Factores a considerar:
- Capacidad de bajo volumen y alto volumen: Asegúrese de que el proveedor pueda manejar tanto corridas de prototipos pequeñas como lotes de producción más grandes. Algunos proveedores se especializan en producciones de gran volumen, mientras que otros destacan en producciones flexibles de bajo volumen.
- Personalización: Si su proyecto requiere materiales, componentes o procesos específicos, asegúrese de que el proveedor pueda cumplir con estas solicitudes personalizadas. Esto es especialmente importante para industrias como la médica o la aeroespacial, donde el cumplimiento de estrictos estándares puede ser necesario.
- No hay requisitos de pedido mínimo: Para startups o empresas que desarrollan prototipos, es importante encontrar un socio que esté dispuesto a trabajar en proyectos a pequeña escala sin imponer cantidades de pedido mínimas altas.
Por qué es importante: La flexibilidad garantiza que pueda adaptarse a los requisitos cambiantes del proyecto y aún así recibir servicios de ensamblaje de alta calidad adaptados a sus necesidades exactas.
5. Rentabilidad
Si bien el costo nunca debe ser el único factor de decisión al elegir un socio de ensamblaje SMT, es importante encontrar un proveedor que ofrezca precios competitivos sin sacrificar la calidad. Evalúe el valor general ofrecido por el proveedor, considerando factores como la calidad, el servicio y el soporte, en lugar de centrarse únicamente en el precio más bajo.
Factores a considerar:
- Precios transparentes: Asegúrese de que el proveedor ofrezca precios transparentes sin costos ocultos. Solicite cotizaciones detalladas que incluyan todos los aspectos del proceso de ensamblaje, desde la fuente de componentes hasta las pruebas.
- Optimización de costos: Busque socios que ofrezcan opciones de ahorro de costos, como descuentos por volumen para pedidos más grandes o sugerencias para alternativas de componentes más asequibles sin comprometer la calidad.
Por qué es importante: Los precios competitivos lo ayudan a mantenerse dentro de su presupuesto, pero es importante equilibrar el costo con el nivel de calidad y soporte que recibe. Una opción más barata que resulta en ensamblajes de mala calidad puede generar problemas más costosos a largo plazo.
6. Envío y logística global
Si opera en diferentes países o regiones, considere un socio de ensamblaje SMT con capacidades de envío global y una red de logística comprobada. La capacidad de enviar productos de manera confiable a varios lugares y gestionar aduanas y otros problemas logísticos internacionales es crucial para las empresas que operan a escala global.
Factores a considerar:
- Alcance global: Asegúrese de que el socio pueda enviar internacionalmente y tenga experiencia en la gestión de regulaciones aduaneras, aranceles y derechos en sus mercados objetivo.
- Embalo y manipulación: El proveedor debe ofrecer un embalaje adecuado para proteger las PCB sensibles durante el envío, así como sistemas de seguimiento confiables para mantenerlo informado durante todo el proceso de entrega.
Por qué es importante: La gestión eficiente del envío y la logística ayuda a evitar retrasos, reduce los riesgos de daños y garantiza que sus productos lleguen a sus destinos a tiempo.
Conclusión
Al elegir al socio de ensamblaje SMT adecuado, es esencial evaluar factores clave como los estándares de calidad, el tiempo de entrega, el soporte técnico, la flexibilidad y la rentabilidad. Asegurarse de que su socio pueda cumplir con sus requisitos específicos y entregar resultados confiables y de alta calidad marcará una gran diferencia en el éxito de su proyecto. Priorizar estos factores garantiza un proceso de fabricación sin problemas, un tiempo de lanzamiento al mercado más rápido y un producto final que cumpla con los más altos estándares de calidad y rendimiento.
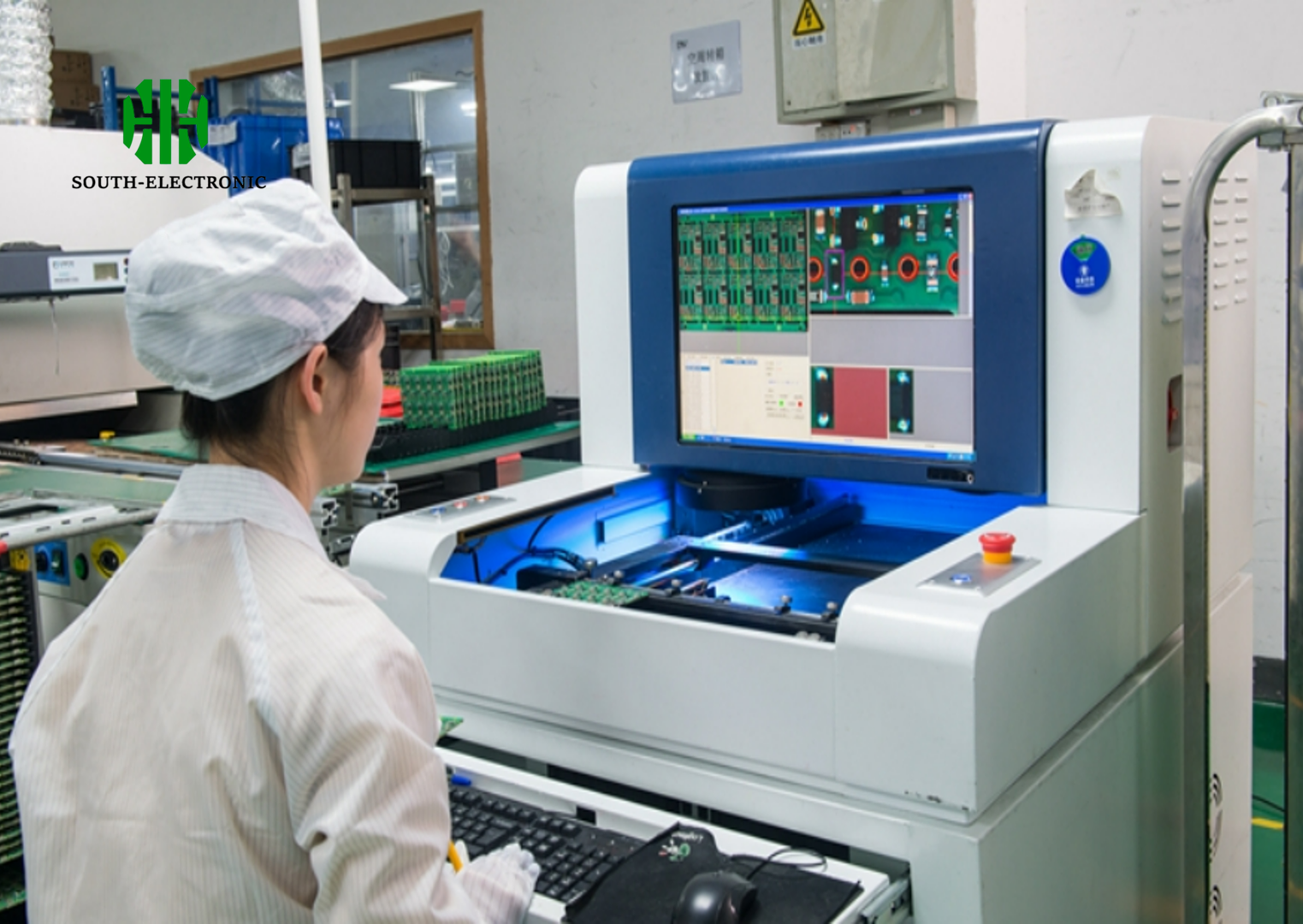
Póngase en Contacto
¿Dónde Estamos?
Parque Industrial, No. 438 Donghuan Road, No. 438, Shajing Donghuan Road, Distrito de Bao'an, Shenzhen, Guangdong, China
Cuarto Piso, Edificio Creativo Zhihui, No.2005 Xihuan Road, Shajing, Distrito de Baoan, Shenzhen, China
Habitación A1-13, Tercer Piso, Centro Industrial Yee Lim, 2-28 Calle Kwai Lok, Kwai Chung, HK
service@southelectronicpcb.com
Teléfono: +86 400 878 3488
Envíanos un mensaje
