Top Flex PCB
South-Electronic
Level up your projects with South-Electronic’s high-quality flex PCBs! We’re all about quality, customization, and innovation, so you can use our boards in anything from consumer electronics to aerospace. Let us help you make your ideas real—get a quote today!
Elevate Your Projects with Flex PCBs
Welcome to South-Electronic, where we guarantee excellence in flex PCBs.
Whether you’re innovating in wearable tech or demanding robustness in aerospace, our flexible PCBs are engineered to deliver reliability and adaptability. Let South-Electronic be your partner in driving success and excellence in your field.

Single-Sided Flex PCB
Single-Sided Flex PCB have one layer of conductive material, which makes them perfect for simple, low-density applications where flexibility is key. They're great for projects that need few electrical connections but still need to be lightweight and flexible.
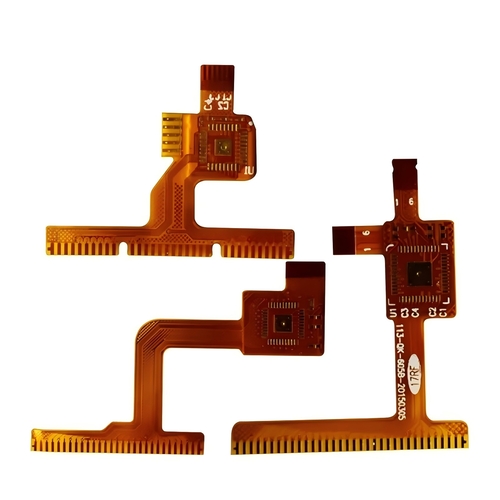
Double-Sided Flex PCB
Double-Sided Flex PCB have conductive material on both sides, which allows for more complex designs in a small space. They increase circuit density without sacrificing flexibility, so they're great for applications that need both complexity and space efficiency.
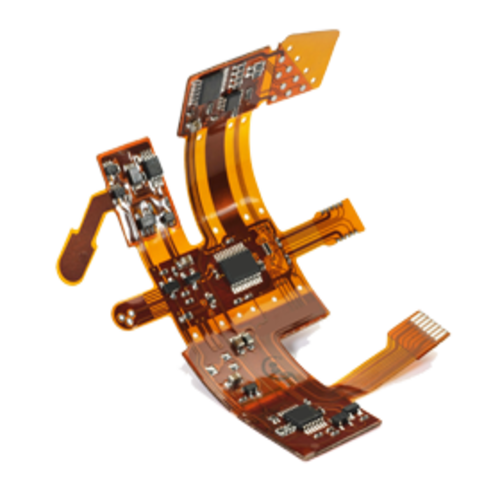
Multilayer Flex PCB
Multilayer flex PCBs have three or more layers of conductive material, which makes them perfect for high-complexity applications that need advanced electronic functions. They're extremely flexible and space efficient, so they're great for complex designs in many different industries.

Rigid-Flex PCB
Rigid-flex PCBs combine the structural stability of rigid circuit boards with the flexibility of flexible circuits. They're perfect for complex electronic assemblies, because they provide strong but flexible connections that meet strict performance requirements.
Why Choose South-Electronic?
-
High-Quality Manufacturing
When you choose South-Electronic, you’re choosing excellence.
Our commitment to top-quality manufacturing ensures that every Flex PCB is produced with precision and care, meeting the highest industry standards for reliability and performance. -
Customization Options
Your project is unique, and your PCBs should be too.
With our wide range of customization options, you can design Flex PCBs that are tailored to your specific needs. This means you can create innovative products that stand out from the competition. -
Extensive Industry Experience
That’s why we offer rapid prototyping services that allow you to test your designs quickly. This way, you can iterate and refine your designs faster, so you can get your products to market sooner.
-
Global Shipping and Support
No matter where your business takes you, we’ve got your back.
We offer reliable global shipping, so you can trust that your PCBs will arrive on time. And if you have any questions or concerns, our support team is always here to help.
Related Project We had Done
Customer Reviews
engineer
thank you, guys, the boards are really good, i am really happy to receive my boards, the components are perfect!
Operation Manager
South-Electronic is my first PCBA supplier in China. The service and quality are excellent, and the after-sales support is also very impressive. Good Job!
Common Questions
Most Popular Questions
South-Electronic offers a wide range of flexible PCBs to meet the needs of different industries. Our product line includes single-sided, double-sided, and multi-layer flex circuits that perform well in tight spaces. Whether you need standard designs or custom configurations, our flexible PCBs are designed to support your innovative applications.
Quality is our top priority at South-Electronic. We have strict quality control measures in place throughout the production process, including advanced inspection techniques and compliance with international standards such as ISO and IPC. Our experienced team tests all flexible PCBs to ensure they meet your specifications and exceed your expectations.
Absolutely! At South-Electronic, we understand that every project is unique. We offer full customization options for the shapes and sizes of flexible PCBs to fit your specific needs. Our engineering team works closely with you to develop the perfect solution that seamlessly integrates into your design.
We strive to deliver your products in a timely manner. Our standard lead time for flexible PCBs is typically [insert typical lead time, e.g., 4-6 weeks], depending on the complexity of your order. If you have urgent requirements, we also offer expedited options to ensure you get your products when you need them.
At South-Electronic, we offer flexible solutions to meet your business needs. The minimum order quantity for our flexible PCBs is [insert minimum order quantity, e.g., 10 units], so you can place orders that work for both small-scale prototypes and larger production runs.
Yes, we provide comprehensive support throughout the shipping process. Our team at South-Electronic is knowledgeable about customs and import/export documentation, so we can handle all the paperwork efficiently. This allows you to focus on your business while we take care of the logistics.
Send us a message
The more detailed you fill out, the faster we can move to the next step.
The Complete Guide for Flex PCB
Contents
Chapter 1

Introduction to Flex PCB
Flex PCBs are electrical circuits that can bend and conform to the shape of various devices. They’re different from traditional rigid PCBs because they use flexible substrates, which makes them lightweight and adaptable. These circuits can have multiple layers, which allows for complex designs while still maintaining flexibility.
This is important because it lets you fit more stuff into a smaller space, which is a big deal in electronics these days. Flex PCBs are used in all kinds of things, like phones, medical devices, and cars. As technology gets better and better, people are going to want more and more from their electronics, and flex PCBs are going to be the way to give it to them. That’s why they’re so popular with engineers and manufacturers.
Chapter 2
Advantages of Flex PCBs
Flex PCBs offer numerous advantages that make them a preferred choice in many applications. Here are some key benefits:
Space Savings
One of the most significant advantages of flex PCBs is their ability to save space. Their flexible nature allows them to be routed through tight spaces and around obstacles within a device. This space-saving capability is particularly beneficial in compact electronic devices, where every millimeter counts, enabling designers to create sleeker and more efficient products.
Lightweight Design
Flex PCBs are inherently lighter than traditional rigid circuit boards. The use of flexible materials not only reduces the overall weight of the assembly but also contributes to a lower shipping cost and improved energy efficiency in portable devices. This lightweight design is crucial for industries such as aerospace and automotive, where weight reduction can lead to significant performance improvements.
Enhanced Durability
Flex PCBs are designed to withstand mechanical stress and vibration, making them more durable in demanding environments. Their ability to bend and twist without breaking reduces the risk of damage from movement and impacts, ensuring a longer lifespan for electronic devices. This durability is particularly important in applications like medical devices and automotive systems, where reliability is paramount.
Flexibility in Design
The versatility of flex PCBs allows for innovative design solutions that are not possible with rigid boards. Designers can create complex geometries and integrate multiple components into a single board, reducing the number of interconnections needed. This flexibility facilitates more compact designs and allows for greater creativity in product development, making flex PCBs ideal for cutting-edge technologies.
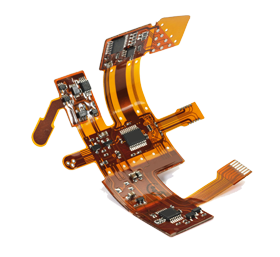
Chapter 3
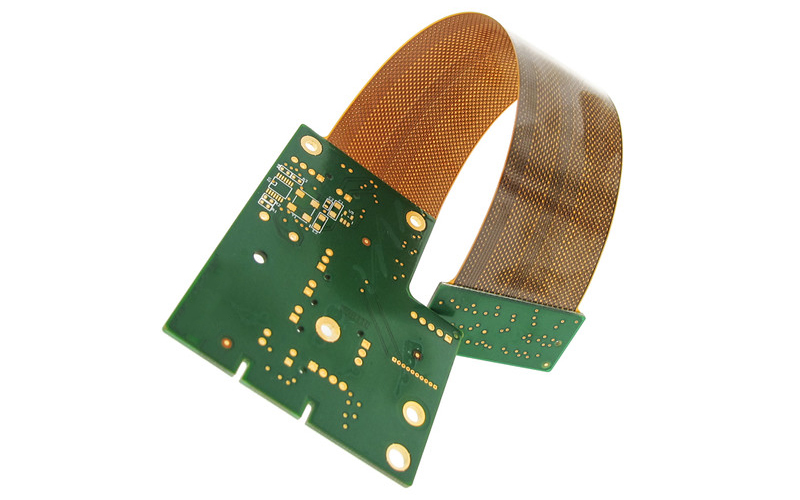
Common Applications of Flex PCBs
Consumer Electronics
Flex PCBs are widely used in consumer electronics due to their compact size and adaptability. They can be found in devices such as smartphones, tablets, and wearables, where space constraints are critical. The ability to conform to different shapes allows for innovative designs, enhancing functionality while maintaining aesthetic appeal.
Medical Devices
In the medical field, flex PCBs play a vital role in the development of advanced diagnostic and monitoring equipment. They are commonly used in devices like portable ECG monitors, insulin pumps, and imaging systems. The durability and reliability of flex PCBs ensure that they can withstand the rigorous demands of medical applications, where precision and performance are essential.
Automotive Industry
The automotive industry increasingly relies on flex PCBs for various applications, including infotainment systems, sensor arrays, and electronic control units. Their lightweight and flexible nature contribute to improved fuel efficiency and performance. Additionally, flex PCBs are used in safety systems, such as airbags and anti-lock braking systems, where reliability and durability are critical.
Aerospace and Defense
In aerospace and defense applications, flex PCBs are essential for lightweight, compact, and reliable electronic systems. They are used in satellite communication systems, avionics, and military equipment, where performance in extreme conditions is required. The ability to endure harsh environments while maintaining functionality makes flex PCBs a preferred choice for these high-stakes applications.
Chapter 4
Types of Flex PCBs
Flex PCBs come in different types, each designed for specific applications. Knowing these types can help you choose the right one for your project. Here are the main types of flex PCBs:
1. Single-Sided Flex PCBs
Single-sided flex PCBs have one conductive layer on one side of a flexible substrate. They are typically used in simpler applications where space is limited, such as in sensors and compact devices. They are cost-effective and easy to manufacture.
2. Double-Sided Flex PCBs
Double-sided flex PCBs have conductive layers on both sides of the substrate, allowing for more complex circuitry. They are ideal for applications that require more connections and functionality, such as in displays and consumer electronics. They also offer more flexibility in routing electrical signals.
3. Multi-Layer Flex PCBs
Multi-layer flex PCBs have multiple layers of conductive pathways separated by insulating materials. They enable intricate designs and higher circuit density, making them suitable for advanced applications like medical devices and high-speed electronics. They improve signal integrity and reduce electromagnetic interference.
4. Rigid-Flex PCBs
Rigid-flex PCBs combine rigid and flexible sections within one circuit board. They are perfect for applications that require stability in certain areas while maintaining flexibility in others. They are commonly found in complex devices like smartphones and aerospace equipment.
5. Flex Circuits with Additional Features
Some flex PCBs come with special features, such as embedded components, via holes, or additional protective layers. These enhancements can improve performance, reliability, and thermal management, making them suitable for demanding applications.
In conclusion, the different types of flex PCBs—single-sided, double-sided, multi-layer, rigid-flex, and those with additional features—offer unique benefits for specific needs. By choosing the right type, you can optimize performance and functionality in your electronic designs.

Chapter 5
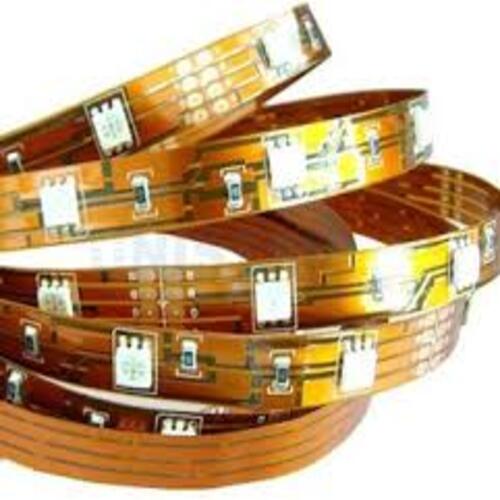
Materials Used in Flex PCBs
Flex PCBs are made up of a variety of materials that affect their performance and reliability. To choose the right flex PCB for your application, you need to know about these materials. Here are the main ones:
1. Substrate Materials
- Polyimide (PI):This is the most common substrate material for flex PCBs because it can handle high temperatures, resists chemicals, and is flexible. It is great for applications in tough environments.
- Polyester (PET):Polyester is cheaper than polyimide, but not as tough. It is used for simpler applications that don’t need to handle extreme heat. It is flexible and is used in consumer electronics.
2. Conductive Materials
- Copper:Copper is the standard material for conductive traces in flex PCBs. It is highly conductive and easy to work with during manufacturing. You can use different thicknesses of copper depending on the current you need for your application.
- Silver:In some high-frequency or high-performance applications, silver is used because it is even more conductive than copper. However, it is more expensive, so it is not as common.
3. Adhesives and Bonding Agents
- Acrylic Adhesives:These are used to bond the conductive layers to the substrate. They provide good adhesion and flexibility. They are used in multi-layer flex PCBs.
- Epoxy Adhesives:Epoxy adhesives are strong and can handle high temperatures. They are used in applications that need a lot of strength and thermal resistance.
4. Protective Coatings
- Conformal Coatings:These coatings protect the PCB from moisture, dust, and chemicals. They make the PCB more durable. You can add them as an extra layer to flex PCBs to make sure they work well in different environments.
- Surface Finishes: You can add ENIG (Electroless Nickel Immersion Gold) or HASL (Hot Air Solder Leveling) to copper traces to make them easier to solder and more resistant to corrosion.
In summary, the materials you choose for your flex PCB—like polyimide or polyester substrates, copper or silver conductors, and the right adhesives—make a big difference in how well it works and how long it lasts. By knowing about these materials, you can make smart choices that meet your needs.
Chapter 6
Design Considerations for Flex PCBs
Designing flexible printed circuit boards (Flex PCBs) is different from designing traditional rigid PCBs. By following some key design guidelines, you can ensure optimal performance and reliability in your applications. Here are some important things to consider:
1. Bend Radius
The bend radius is a critical aspect of flex PCB design. It refers to the minimum radius a flex PCB can bend without risking damage. A larger bend radius is recommended to prevent stress on the circuitry. As a general rule, the bend radius should be at least 10 times the thickness of the substrate material.
2. Trace Width and Spacing
Proper trace width and spacing are important for electrical performance. Wider traces can handle higher currents, while narrower traces save space. However, you need to have enough spacing to avoid short circuits and ensure manufacturability. Consider using design software to simulate trace performance under different conditions.
3. Layer Stacking
When designing multi-layer flex PCBs, you need to carefully plan the layer stack-up. Make sure that the flexible layers are placed in a way that provides the necessary flexibility while maintaining mechanical integrity. Balance the design to optimize electrical performance and physical characteristics.
4. Component Placement
Strategic component placement is important for efficient signal routing and minimizing interference. Avoid placing components in areas that will experience a lot of bending. Also, consider using surface-mounted devices (SMDs) to save space and improve reliability.
5. Stress Relief Features
Including stress relief features, such as cut-outs or slots, can help mitigate mechanical stress during bending and movement. These features are especially important in high-flex applications, as they can significantly improve the lifespan of the flex PCB.
6. Design Software Tools
Use advanced design software that is specifically tailored for flex PCB applications. Tools like Altium Designer, Eagle, or KiCAD can help you create precise designs while allowing you to simulate and analyze the circuit performance in real time. These tools also make it easier to implement design rules and guidelines, ensuring manufacturability.
7. Prototyping and Testing
Before going into production, create prototypes to test the functionality and durability of your design. Test your design under real-world conditions to identify any potential issues early on. Iterating on your design based on testing feedback can lead to improved performance and reliability.
In conclusion, paying attention to the bend radius, trace width, layer stacking, component placement, stress relief features, and using specialized design software is important when designing flex PCBs. By considering these things, you can create effective and reliable flexible circuits that are tailored to your specific applications.

Chapter 7
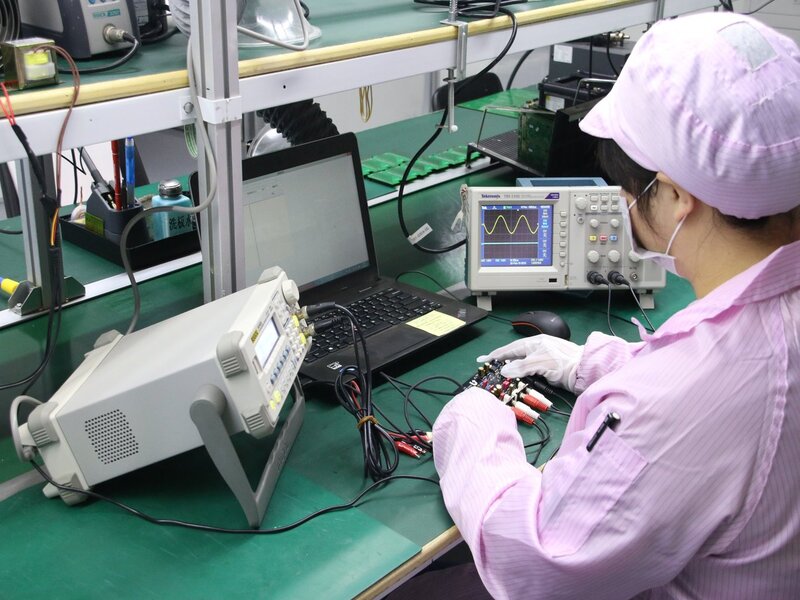
Manufacturing Process of Flex PCBs
Making flexible printed circuit boards (Flex PCBs) involves several critical steps that ensure high-quality production. Understanding these processes can help you appreciate the complexity and precision required to create reliable flex PCBs. Here’s an overview of the key stages in manufacturing flex PCBs:
1. Design and Layout
The first step in making flex PCBs is the design and layout phase. Designers create the PCB layout using specialized software, ensuring that all components, traces, and layers are optimized for performance and flexibility. This stage also includes defining the specifications for materials and dimensions.
2. Material Preparation
Once the design is finalized, the next step is to prepare the substrate materials. Common substrates like polyimide or polyester are cut to the required dimensions. Copper foils are then laminated onto the substrate using adhesives, forming the basis for the conductive pathways.
3. Photolithography
In this stage, a photoresist layer is applied to the copper-clad substrate. The PCB design is then transferred onto the substrate using photolithography techniques, where ultraviolet (UV) light exposes the photoresist according to the circuit pattern. After exposure, the substrate is developed, removing the unexposed photoresist and leaving the desired copper pattern.
4. Etching
The exposed copper areas are subjected to an etching process, where chemicals remove the unwanted copper, leaving only the desired circuitry. This step is crucial for creating precise conductive paths on the flex PCB.
5. Layer Lamination (for Multi-Layer PCBs)
For multi-layer flex PCBs, multiple layers of substrate and circuitry are aligned and laminated together under heat and pressure. This process ensures that the layers bond effectively, creating a robust multi-layer structure that maintains flexibility.
6. Drilling and Plating
Next, holes for vias and component mounting are drilled into the flex PCB. These holes are then plated with copper to create electrical connections between layers. This step is essential for ensuring signal integrity across multiple layers.
7. Surface Finish
After drilling, a surface finish is applied to protect the copper traces and enhance solderability. Common surface finishes include Electroless Nickel Immersion Gold (ENIG) and Hot Air Solder Leveling (HASL), both of which provide excellent protection against oxidation.
8. Testing and Inspection
Quality control is critical in making flex PCBs. Various tests, including electrical testing and visual inspection, are performed to ensure that the PCBs meet specified performance criteria. This stage helps identify any defects early in the process, reducing the risk of issues during deployment.
9. Cutting and Packaging
Once testing is complete, the flex PCBs are cut to their final shapes and sizes. They are then packaged appropriately to protect them during shipping and handling, ensuring they reach customers in perfect condition.
In summary, making flex PCBs involves several critical steps, including design, material preparation, photolithography, etching, lamination, drilling, plating, surface finishing, testing, and packaging. Each stage requires precision and attention to detail to produce high-quality flex PCBs that meet the demands of modern electronic applications.
Chapter 8
Challenges and Limitations of Flex PCBs
Flex PCBs offer a range of benefits, but they also present challenges and limitations that designers and manufacturers need to consider. Understanding these issues will help you make informed decisions when you choose to use flex PCBs. Here are some of the key challenges:
1. Manufacturing Complexity
Manufacturing flex PCBs is more complex than manufacturing rigid PCBs. This complexity can lead to longer lead times and higher production costs, especially for low-volume orders. Manufacturers need specialized equipment and expertise to handle the unique requirements of flex PCB production.
2. Cost Considerations
While flex PCBs can be cost-effective for high-volume applications, the initial costs can be much higher than those for traditional rigid PCBs. For small production runs or prototypes, the cost of materials and manufacturing may not justify the benefits of using flex technology.
3. Limited Component Options
Not all electronic components are suitable for use with flex PCBs. Some components may be too large or rigid to integrate easily. This limitation can restrict your design options and require careful component selection to ensure compatibility.
4. Handling and Assembly Challenges
Flex PCBs are more delicate than rigid boards and can be easily damaged during handling and assembly. Proper care and handling procedures are essential to prevent issues like cracking or delamination, which can affect performance and reliability.
5. Environmental Sensitivity
Certain materials used in flex PCBs, such as polyimide, may have limitations on exposure to extreme environmental conditions. While flex PCBs are designed to be durable, they can still be affected by factors like humidity and temperature fluctuations if not managed properly.
6. Testing and Validation Difficulties
Testing flex PCBs can be more challenging than testing rigid boards because of their flexibility and the complexity of their designs. Ensuring consistent quality and performance requires rigorous testing protocols, which can add to the overall project timeline.
7. Limited Repairability
Once a flex PCB is assembled into a device, repairing it can be difficult. The flexibility and integration of components can make it challenging to replace or repair individual parts without compromising the entire board.
In summary, while flex PCBs offer significant advantages, you need to consider challenges like manufacturing complexity, cost considerations, limited component options, handling issues, environmental sensitivity, testing difficulties, and limited repairability. By understanding these limitations, you can make informed choices and effectively address potential issues in your projects.
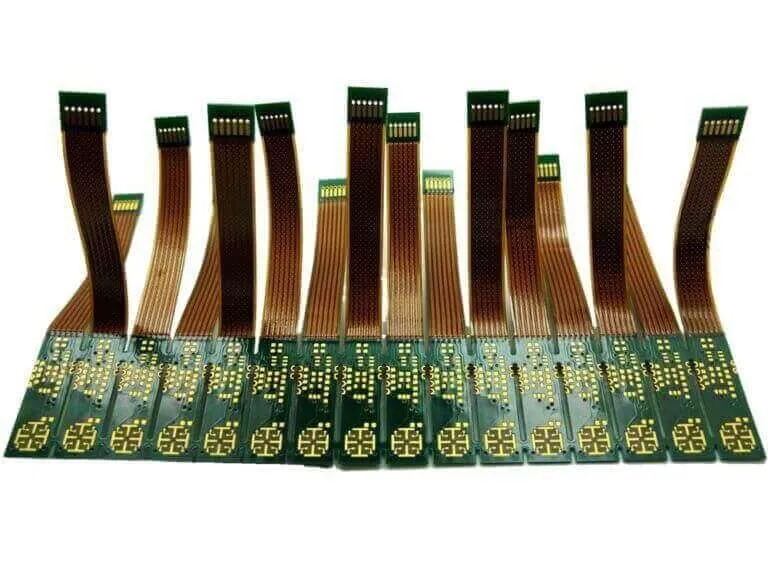
Chapter 9

Best Practices for Flex PCB Assembly
Assembling flex PCBs requires attention to detail to ensure reliability and performance. Here are some best practices to follow during the assembly process:
Soldering Techniques
- Choose the Right Solder: Use low-temperature soldering techniques to prevent damage to the flexible substrate. Lead-free solders are often preferred.
- Reflow Soldering: This technique is commonly used for surface-mounted devices (SMDs) on flex PCBs. Ensure that the temperature profile is carefully controlled to avoid overheating the flexible materials.
- Wave Soldering: For through-hole components, wave soldering can be effective. However, it’s crucial to select a gentle wave to minimize stress on the flex PCB.
- Manual Soldering: When hand soldering, use a soldering iron with a fine tip to ensure precision. Avoid excessive heat exposure to the flex material, and keep soldering times as short as possible.
- Flux Application: Use an appropriate flux to improve solder wetting and ensure good connections. Avoid excessive flux, which can lead to residue buildup and affect performance.
Testing and Quality Assurance
- Electrical Testing: Conduct thorough electrical testing to verify that all connections are functional. Common methods include in-circuit testing (ICT) and functional testing.
- Visual Inspection: Implement a visual inspection process to identify any defects, such as misaligned components, solder bridges, or damaged traces. High-resolution cameras can aid in this process.
- Flex Testing: Perform flex testing to assess the mechanical integrity of the PCB. Bending tests should simulate the expected usage conditions to ensure reliability over time.
- Thermal Cycling: Subject the assembled flex PCBs to thermal cycling tests to evaluate their performance under varying temperature conditions. This helps identify potential weaknesses in the design.
- Documentation and Traceability: Maintain detailed documentation throughout the assembly process, including test results and inspection records. This practice ensures traceability and accountability.
Packaging and Handling
- Use Appropriate Packaging: Flex PCBs should be packaged in anti-static materials to prevent electrostatic discharge (ESD) damage. Use cushioning materials to protect against physical stress during transport.
- Labeling: Clearly label all packaging with handling instructions and any specific requirements for storage conditions (e.g., temperature and humidity).
- Training for Handling: Provide training for personnel involved in handling and assembling flex PCBs. Emphasize the importance of careful handling to prevent damage.
- Storage Conditions: Store flex PCBs in controlled environments to avoid exposure to extreme temperatures and humidity. Use moisture barrier bags if necessary to protect against moisture absorption.
- Avoiding Mechanical Stress: Handle flex PCBs gently to prevent mechanical stress. Avoid bending or twisting the boards excessively during assembly or packaging.
In conclusion, following best practices for soldering techniques, testing and quality assurance, and proper packaging and handling can significantly enhance the reliability and performance of flex PCBs. By prioritizing these practices, manufacturers can ensure that their flex PCBs meet the demands of modern electronic applications.
Chapter 10
Future Trends in Flex PCB Technology
Innovations in Materials
In the future, flex PCBs will be made from materials that are even more flexible, durable, and thermally conductive. Researchers are developing new materials, such as super-thin polyimide and biodegradable materials, to meet sustainability goals. They are also improving conductive inks and flexible components to enable even more complex designs.
Emerging Applications
Flex PCBs are being used in new applications, such as wearable technology, flexible displays, and the Internet of Things (IoT). As the demand for smaller, lighter products grows, industries such as healthcare, automotive, and consumer electronics will increasingly rely on flex PCBs to create innovative products. This will drive further research and development in the field.
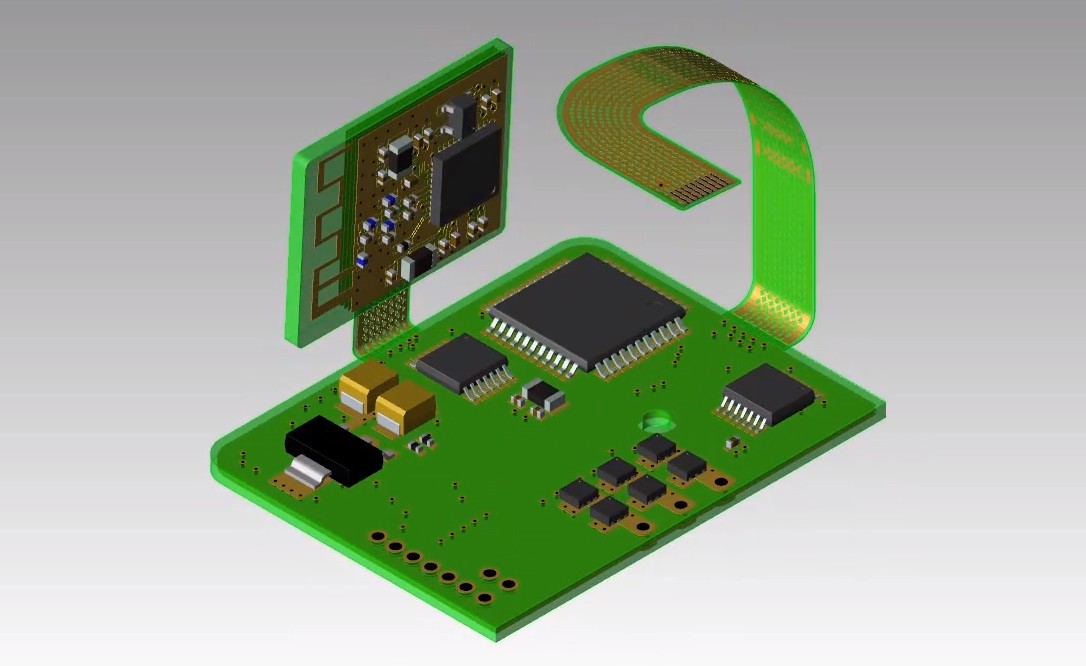
Get in touch
Where Are We?
Industrial Park, No. 438 Donghuan Road, No. 438, Shajing Donghuan Road, Bao'an District, Shenzhen, Guangdong, China
Floor 4, Zhihui Creative Building, No.2005 Xihuan Road, Shajing, Baoan District, Shenzhen, China
ROOM A1-13,FLOOR 3,YEE LIM INDUSTRIAL CENTRE 2-28 KWAI LOK STREET, KWAI CHUNG HK
service@southelectronicpcb.com
Phone : +86 400 878 3488
Send us a message
The more detailed you fill out, the faster we can move to the next step.
