PCB 6 couches de haute qualité
South-Electronic
Choisissez South-Electronic pour la meilleure qualité, fiabilité et valeur pour vos besoins en PCB. Découvrez la différence avec notre service complet de PCB 6 couches – du début à la fin, nous vous garantissons précision, durabilité et conformité aux normes industrielles les plus strictes.
Pourquoi choisir South-Electronic ?
Chez South-Electronic, nous comprenons l’importance d’avoir les bonnes solutions pour vos projets de PCB 6 couches. Nous sommes les meilleurs dans le domaine de l’innovation en PCB, et nous pouvons personnaliser et fournir la précision dont vous avez besoin pour assurer le succès de votre projet. Nous sommes déterminés à vous offrir les meilleures technologies et solutions pour garantir votre réussite.
-
Flexibilité dans les commandes
Rendez vos commandes simples et efficaces.
Que vous ayez besoin d'un seul PCB ou d'une grande série, sans minimum de commande strict, vous pouvez commencer dès une pièce. Cela vous offre la flexibilité d'expérimenter, de prototyper ou de produire en fonction de vos besoins spécifiques. -
Équipe expérimentée
Vous bénéficierez de l’expertise d’une équipe expérimentée.
Avec des années d'expérience pratique, notre équipe comprend vos défis et est prête à fournir des solutions adaptées à votre vision. Des recommandations de conception aux idées de fabrication, nous sommes là pour vous accompagner à chaque étape. Ce niveau d'expertise garantit des résultats optimaux dans les délais et le budget impartis. -
Contrôle qualité strict
Vous méritez les meilleurs produits, et c'est exactement ce que nous offrons.
Chaque PCB 6 couches fabriqué par South-Electronic est soumis à des contrôles de qualité rigoureux pour s'assurer qu'il répond à vos normes exactes. Avec des certifications telles que UL, CE, IATF16949 et ISO13485, vous pouvez être certain que vos produits sont fabriqués selon les normes mondiales les plus élevées. Nous nous engageons à dépasser vos attentes en matière de performance et de fiabilité avec chaque carte que nous produisons. -
Service complet
Vous bénéficierez d’un partenaire de service complet.
Notre large gamme d’équipements de traitement avancés nous permet de gérer chaque étape de la production, vous évitant ainsi de devoir sous-traiter auprès de plusieurs fournisseurs. Qu'il s'agisse de cartes multicouches complexes ou de prototypage rapide, nous disposons des outils et de l'expertise nécessaires pour garantir que chaque aspect de votre projet soit géré avec fluidité et efficacité. -
Livraison rapide
Vous bénéficierez d’un partenaire de service complet.
Notre large gamme d’équipements de traitement avancés nous permet de gérer chaque étape de la production, vous évitant ainsi de devoir sous-traiter auprès de plusieurs fournisseurs. Qu'il s'agisse de cartes multicouches complexes ou de prototypage rapide, nous disposons des outils et de l'expertise nécessaires pour garantir que chaque aspect de votre projet soit géré avec fluidité et efficacité. -
Satisfaction garantie
Votre satisfaction est au cœur de tout ce que nous faisons.
En tant qu'usine certifiée ISO9001, South-Electronic s'engage à fournir des produits de haute qualité avec une communication claire et proactive. Nous veillons à ce que chaque commande respecte vos normes et vous tenons informé tout au long du processus. Cet engagement envers la qualité et le service signifie que vous pouvez compter sur nous pour livrer exactement ce dont vous avez besoin, à chaque fois.
Projets connexes que nous avons réalisés
Avis des clients
Questions fréquentes
Questions les plus populaires
Absolument ! Nous offrons des options de personnalisation complètes pour les PCB 6 couches. Vous pouvez spécifier l'épaisseur de la carte, le poids du cuivre, la largeur des pistes et les types de vias pour répondre précisément aux besoins de votre projet.
Le délai typique est de 5 à 10 jours ouvrables, selon la complexité et la quantité de votre commande. Nous proposons également des options accélérées pour les projets urgents.
Le MOQ de South-Electronic est très flexible, commençant à partir d'une seule pièce. Cela vous permet de commander tout, des prototypes aux productions à grande échelle.
South-Electronic détient des certifications telles que UL, ISO9001, CE, IATF16949 et ISO13485, garantissant une qualité supérieure et la conformité aux normes internationales.
Oui, South-Electronic propose une expédition internationale pour assurer une livraison rapide à ses clients dans le monde entier. Leurs solutions logistiques sont conçues pour offrir une livraison sécurisée et efficace.
South-Electronic fournit un solide service après-vente, offrant des garanties sur ses produits. Elle respecte des mesures strictes de contrôle de la qualité, telles que les certifications ISO et RoHS, garantissant une fiabilité à long terme et une satisfaction client.
Envoyez-nous un message
Plus vous remplissez de détails, plus nous pourrons avancer rapidement à l’étape suivante.
Le guide complet pour PCB 6 couches
Sommaire
Chapitre 1

Introduction au PCB 6 couches
Un PCB 6 couches (Printed Circuit Board) est un type de carte qui comporte six couches de cuivre et de matériaux isolants. Ces cartes sont utilisées dans des appareils électroniques plus complexes qui doivent accomplir davantage de tâches, améliorer les signaux et fonctionner plus efficacement. Les couches supplémentaires permettent une meilleure circulation des signaux et de l’énergie, ce qui les rend adaptées aux nouvelles technologies nécessitant gain d’espace, rapidité et faible consommation d’énergie.
Aujourd’hui, les PCB 6 couches sont utilisés dans de nombreux domaines. Ils se trouvent dans les téléphones, les ordinateurs, les équipements médicaux et les voitures. Ils sont parfaits pour des applications nécessitant des dispositifs compacts, multifonctionnels et rapides. Ils peuvent gérer des signaux à haute fréquence et empêcher les interférences d’autres signaux, ce qui les rend idéaux pour des performances élevées.
Chapitre 2
Pourquoi utiliser un PCB 6 couches ?
Il existe plusieurs raisons de choisir un PCB 6 couches, notamment :
Amélioration de l’intégrité du signal : Avec des couches supplémentaires dédiées aux plans d’alimentation et de masse, un PCB 6 couches permet de minimiser les interférences et d’assurer une transmission stable des signaux. Cela est particulièrement important dans les dispositifs utilisant des signaux haute fréquence, car cela réduit la dégradation des signaux et les interférences entre les couches. Les couches supplémentaires permettent également un meilleur contrôle de l’impédance, ce qui est crucial pour maintenir une qualité de signal cohérente dans les circuits à haute vitesse.
Réduction accrue du bruit : Un PCB 6 couches aide à réduire les interférences électromagnétiques (EMI) et les interférences radiofréquences (RFI) en offrant des couches de masse supplémentaires qui agissent comme des écrans entre les couches de signal. Cet effet de blindage réduit le risque de bruit et d’interférences indésirables affectant les performances de la carte. En améliorant la réduction du bruit, les PCB 6 couches contribuent à un fonctionnement plus fiable et stable, notamment dans les applications sensibles comme les dispositifs médicaux et les systèmes de communication.
Amélioration de la dissipation thermique et de la durabilité : À mesure que les composants électroniques deviennent plus puissants, la gestion de la dissipation thermique devient essentielle pour garantir leur longévité et leur performance. Le design à 6 couches offre une gestion thermique améliorée en répartissant la chaleur sur plusieurs couches, permettant une meilleure distribution de la chaleur à travers le PCB. Cela aide à éviter les points chauds, qui peuvent endommager les composants ou réduire leur durée de vie. De plus, la structure épaisse et multicouche des PCB 6 couches renforce leur résistance mécanique, les rendant plus durables et résistants aux contraintes physiques.
Soutien aux applications à haute vitesse : De nombreuses électroniques modernes nécessitent un traitement des signaux et un transfert de données à haute vitesse, en particulier dans des industries comme les télécommunications, l’informatique et l’électronique automobile. Les PCB 6 couches conviennent parfaitement aux applications à haute vitesse car ils maintiennent l’intégrité du signal et réduisent le bruit. Les couches supplémentaires assurent une meilleure séparation des chemins de signal, réduisant les interférences croisées et garantissant une transmission précise des signaux haute vitesse. Cela fait des PCB 6 couches un excellent choix pour les appareils comme les smartphones, les systèmes de stockage de données, et les commandes automobiles avancées, où la vitesse et la fiabilité sont primordiales.
En résumé, un PCB 6 couches offre des avantages significatifs pour les dispositifs électroniques avancés, améliorant les performances, la fiabilité et la durabilité. Ces avantages en font le choix préféré des ingénieurs et des fabricants travaillant sur des applications haute performance et haute fréquence.

Chapitre 3
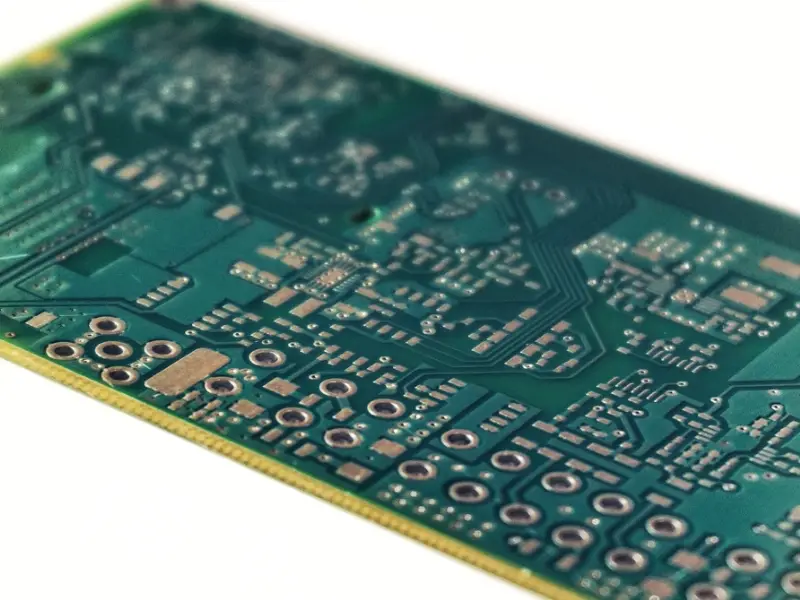
Comment sont construits les PCB 6 couches ?
La fabrication d’un PCB 6 couches est un processus minutieux nécessitant planification et exécution pour garantir les performances. Cela commence par définir l’empilement des couches, choisir les matériaux et déterminer le type de vias nécessaires pour connecter les couches. Examinons chacun de ces aspects :
1. Empilement des couches (Layer Stack-Up)
L’empilement des couches d’un PCB 6 couches est l’agencement des couches conductrices en cuivre et des couches de matériau isolant qui composent la carte. Un empilement typique comprend deux couches de signal internes, deux plans d’alimentation (un pour l’alimentation et un pour la masse), et deux couches extérieures pour le routage des signaux. Les configurations les plus courantes sont :
Signal 1 / Ground / Signal 2 / Power / Ground / Signal 3
Signal 1 / Ground / Power / Signal 2 / Ground / Signal 3
Ces configurations protègent les couches de signal avec des couches de masse et d’alimentation pour réduire les interférences électromagnétiques (EMI). Les couches d’alimentation distribuent l’énergie et réduisent le bruit. Cette approche permet de contrôler l’impédance et d’améliorer l’intégrité du signal pour les applications à haute vitesse et haute fréquence.
2. Choix des matériaux (Material Selection)
Les matériaux utilisés dans un PCB 6 couches influencent les performances, la durabilité et le coût. Le matériau le plus courant est le FR4, un stratifié en époxy renforcé de fibres de verre, qui offre un équilibre entre isolation électrique, stabilité thermique et coût. Pour des applications hautes performances ou haute température, des matériaux avec des températures de transition vitreuse (Tg) plus élevées peuvent être nécessaires.
- FR4 standard : Pour les PCB à usage général avec des exigences de performance modérées. Tg autour de 130°C.
- FR4 à haut Tg : Pour les applications nécessitant une meilleure résistance thermique. Les matériaux High-Tg (Tg de 170°C ou plus) sont plus stables à des températures élevées, ce qui les rend adaptés aux circuits haute puissance ou haute fréquence.
- Rogers ou Polyimide : Pour les applications spécialisées telles que les circuits RF et micro-ondes nécessitant de meilleures propriétés électriques.
Le choix du bon matériau garantit que la carte peut gérer les charges thermiques, maintenir l’intégrité du signal et rester fiable.
3. Types de vias (Via Types)
Les vias sont des trous qui connectent différentes couches dans un PCB. Dans un PCB 6 couches, il existe différents types de vias selon la conception :
- Vias traversants (Through-Hole Vias) : Ces vias traversent l’ensemble du PCB. Ils sont les plus courants et connectent toutes les couches dans des conceptions plus simples. Cependant, ils occupent de l’espace sur les couches internes, ce qui peut limiter les options de routage dans des PCB complexes.
- Vias borgnes (Blind Vias) : Ces vias connectent les couches extérieures à une ou plusieurs couches internes sans traverser la carte. Ils sont utiles pour les conceptions haute densité où l’espace est limité, offrant plus d’options de routage sans occuper de place sur les couches internes.
- Vias enterrés (Buried Vias) : Ces vias se trouvent entièrement à l’intérieur des couches internes et ne touchent pas les couches extérieures. Ils sont utilisés dans les cartes multicouches pour connecter des couches internes spécifiques sans affecter les couches de surface. Les vias enterrés maximisent la surface pour le routage sur les couches supérieure et inférieure.
Le type de via dépend de la complexité du design, de l’espace disponible et de la nécessité d’optimiser le routage tout en minimisant les interférences et la perte de signal.
Chapitre 4
Considérations de conception pour les PCB 6 couches
La conception d’un PCB 6 couches nécessite une planification minutieuse et la prise en compte de divers facteurs qui influencent ses performances, sa fiabilité et sa fabricabilité. Les principaux aspects de la conception d’un PCB 6 couches incluent l’agencement optimal des couches, la largeur et l’espacement appropriés des pistes, ainsi que le contrôle de l’impédance pour maintenir l’intégrité du signal. Voici une analyse détaillée de ces considérations de conception :
1. Agencement optimal des couches pour le routage des signaux et les plans d’alimentation
L’empilement et l’agencement des couches dans un PCB 6 couches jouent un rôle crucial dans les performances globales de la carte. L’objectif est d’équilibrer les couches de signal et les plans d’alimentation pour garantir un routage efficace, réduire le bruit et améliorer l’intégrité du signal. Un PCB 6 couches typique se compose de trois paires de couches : deux couches de signal, un plan d’alimentation, un plan de masse et des couches supplémentaires pour le signal ou la masse. Voici un empilement de couches courant et efficace :
- Couche de signal supérieure (Signal 1)
- Plan de masse (GND)
- Couche de signal interne (Signal 2)
- Plan d’alimentation (VCC)
- Couche de signal interne (Signal 3)
- Couche de signal inférieure (Signal 4)
Dans cet agencement, le plan de masse est placé à côté de la couche de signal supérieure, et le plan d’alimentation est proche de la deuxième couche de signal interne. Cette structure réduit les interférences électromagnétiques (EMI) et permet une meilleure protection des signaux. La combinaison des plans d’alimentation et de masse offre également un découplage pour les couches de signal, minimisant les interférences croisées et le bruit entre les couches.
Les concepteurs doivent également envisager de placer des signaux haute vitesse sur les couches internes pour réduire les radiations et les interférences. De plus, séparer les plans d’alimentation et de masse sur différentes couches améliore la distribution de l’alimentation et minimise les fluctuations de tension.
2. Directives pour la largeur et l’espacement des pistes
La largeur des pistes sur un PCB et l’espacement entre elles sont des considérations essentielles qui influencent la capacité de la carte à gérer le courant et à maintenir l’intégrité du signal. La largeur des pistes est généralement déterminée en fonction de la capacité de transport de courant requise pour le circuit, ainsi que des contraintes thermiques et de fabricabilité. Les pistes plus larges sont nécessaires pour transporter des courants plus élevés, tandis que les pistes plus étroites sont utilisées pour des signaux nécessitant un contrôle précis, tels que les lignes de données à haute vitesse.
Pour les applications haute vitesse ou haute fréquence, l’espacement entre les pistes est tout aussi important que leur largeur. Un espacement serré entre les pistes peut entraîner un couplage et des interférences de signal, il est donc crucial de suivre les règles de conception appropriées pour éviter les interférences croisées. Une règle générale pour l’espacement des pistes est de maintenir un écart au moins égal à la largeur de la piste elle-même, bien que cela varie selon la conception.
La norme IPC-2221 fournit des directives pour la largeur et l’espacement des pistes en fonction de l’utilisation prévue de la carte. Par exemple, une piste en cuivre de 1 oz transportant 1 ampère de courant nécessite généralement une largeur d’environ 0,015 pouce (15 mils). Cependant, pour les conceptions haute densité avec un espace limité, les concepteurs peuvent avoir besoin d’optimiser soigneusement à la fois la largeur et l’espacement des pistes.
3. Contrôle de l’impédance et conseils pour l’intégrité du signal
Le contrôle de l’impédance est un facteur crucial dans les PCB 6 couches, en particulier pour les conceptions haute vitesse et haute fréquence. Lorsque les signaux se déplacent à travers les pistes du PCB, l’impédance de ces pistes peut affecter la qualité du signal. Si l’impédance n’est pas contrôlée, cela peut entraîner des réflexions de signal, une dégradation et une distorsion, ce qui peut nuire aux performances du circuit.
Pour maintenir une impédance correcte, les concepteurs de PCB doivent prendre en compte la largeur des pistes, l’espacement entre la piste et son plan de référence (généralement un plan de masse ou d’alimentation) et la constante diélectrique du matériau de la carte (par exemple, FR4). Une impédance contrôlée est obtenue en ajustant soigneusement ces paramètres pour répondre aux spécifications requises pour les signaux haute vitesse. Par exemple, une impédance de 50 ohms est souvent l’objectif pour les signaux asymétriques, tandis que les paires différentielles (utilisées pour la transmission de données haute vitesse) nécessitent généralement une impédance de 100 ohms.
Voici quelques conseils clés pour maintenir l’intégrité du signal dans les conceptions de PCB 6 couches :
- Gardez les pistes de signal courtes et directes : Plus une piste est longue, plus le risque de dégradation du signal est élevé. Gardez les chemins des signaux haute vitesse aussi courts que possible.
- Utilisez des plans de masse pour la protection : Placez les signaux sensibles ou haute vitesse près des plans de masse pour minimiser les EMI et le bruit. Cet effet de blindage aide à maintenir des signaux propres.
- Maintenez une géométrie de piste cohérente : Pour éviter les incompatibilités d’impédance, assurez-vous que la largeur des pistes, l’espacement et les transitions de couche restent cohérents tout au long du chemin du signal.
- Utilisez des paires différentielles si nécessaire : Pour les signaux numériques haute vitesse ou les conceptions RF, le routage en paires différentielles (avec impédance contrôlée) aide à réduire le bruit et à améliorer l’intégrité du signal.
- Conception des vias : Un autre aspect du contrôle de l’impédance est la conception des vias. Les vias peuvent introduire des discontinuités dans le chemin du signal, causant potentiellement des réflexions. Utiliser moins de vias et maintenir une transition de via contrôlée peut aider à préserver l’intégrité du signal. Les vias borgnes et enterrés peuvent également être utilisés pour réduire la longueur du chemin du signal et minimiser la dégradation du signal dans les conceptions multicouches.
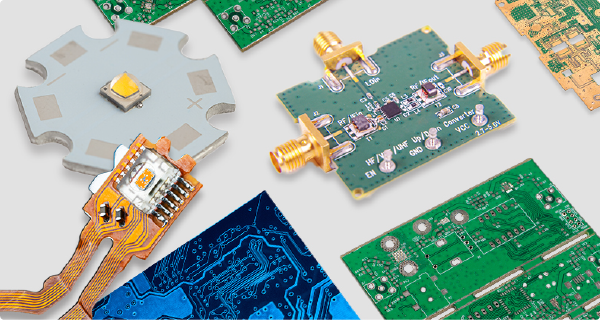
Chapitre 5

Processus de Fabrication des PCB à 6 Couches
La fabrication d’un PCB à 6 couches est un processus complexe et hautement contrôlé qui comprend plusieurs étapes cruciales, chacune nécessitant une grande précision et une attention minutieuse pour garantir que le produit final répond aux spécifications requises. Cette section fournit un aperçu des principales étapes de fabrication, des méthodes d’inspection et de test, ainsi que des mesures de contrôle qualité visant à assurer les plus hauts standards de performance et de fiabilité pour les PCB à 6 couches.
Aperçu des Étapes de Fabrication :
Préparation des Matériaux et Stratification des Couches :
Le processus de fabrication commence par le choix du matériau de base, généralement le FR4 ou d’autres matériaux à haute température de transition vitreuse (High Tg), qui servira de fondation au PCB. Un prepreg (matériau constitué de fibres de verre imprégnées de résine) est utilisé pour lier ensemble les couches de cuivre.
Pour un PCB à 6 couches, des stratifiés revêtus de cuivre sont empilés dans un ordre spécifique pour former la structure interne de la carte. Cela inclut l’alternance de couches de feuilles de cuivre et de matériaux isolants. La conception de l’empilage est essentielle pour l’intégrité du signal, la distribution de l’énergie et la gestion thermique.
Les couches sont stratifiées ensemble sous haute chaleur et pression, ce qui fait fondre le prepreg et lie les couches pour former une carte solide et cohésive. Ce processus, appelé pressage, est l’une des étapes les plus critiques dans la fabrication des PCB multicouches, car il détermine l’alignement et l’adhérence des couches.
Perçage :
Une fois les couches stratifiées, des trous, ou vias, sont percés dans la carte. Ces vias permettent des connexions électriques entre les différentes couches du PCB.
Selon la conception, un PCB à 6 couches peut comporter des vias traversants, des vias aveugles ou des vias enterrés. Ces trous sont percés à l’aide de machines CNC de haute précision, garantissant la précision et l’alignement avec les motifs des circuits.
Placage et Dépôt Autocatalytique de Cuivre :
Après le perçage, les parois internes des vias sont plaquées de cuivre pour établir une connexion électrique entre les couches. Cela se fait par un processus appelé dépôt autocatalytique de cuivre, où une fine couche de cuivre est déposée chimiquement sur la surface des trous percés.
Ensuite, un processus d’électrodéposition épaissit le revêtement de cuivre, rendant les vias conducteurs et prêts pour la transmission des signaux.
Imagerie et Gravure :
À cette étape, une couche de photorésist (matériau photosensible) est appliquée sur les couches extérieures du PCB. Le photorésist est exposé à la lumière UV à l’aide d’un masque qui définit les motifs des circuits.
Une fois exposée, la carte subit un processus de développement qui élimine le photorésist non exposé, ne laissant que les traces de cuivre souhaitées.
Ensuite, la carte passe par un processus de gravure chimique, où le cuivre indésirable est retiré, ne laissant que les chemins de circuits définis. Cette étape est cruciale pour créer les voies électriques qui connectent les composants sur le PCB.
Application du Masque de Soudure et Finition de Surface :
Après la gravure, un masque de soudure est appliqué sur la surface du PCB pour protéger les traces de cuivre et prévenir les courts-circuits. Le masque de soudure couvre toutes les zones de la carte sauf les pastilles de composants, où la soudure sera appliquée.
Différentes finitions de surface peuvent être appliquées, telles que HASL (nivellement à l’air chaud), ENIG (dépôt chimique de nickel et d’or), ou OSP (conservateurs de soudabilité organiques). Ces finitions protègent les pastilles de cuivre exposées et assurent une bonne soudabilité lors du processus d’assemblage.
Impression Sérigraphique :
À cette étape, des marques d’identification telles que les étiquettes de composants, les numéros de pièces et les logos de l’entreprise sont imprimées sur le PCB à l’aide d’un processus de sérigraphie. Cela facilite l’assemblage et le dépannage de la carte.
Profilage et Découpe Finale :
Le PCB est ensuite découpé à sa forme finale à l’aide de routeurs CNC ou de machines de découpe laser. Si plusieurs cartes sont produites sur un seul panneau, elles sont séparées à ce stade.
Méthodes d’Inspection et de Test :
Inspection Optique Automatisée (AOI) :
L’AOI est utilisée pour inspecter visuellement le PCB à la recherche de défauts tels que des désalignements, des traces manquantes ou des motifs incorrects. Des caméras capturent des images haute résolution de la carte, et le système les compare automatiquement aux fichiers de conception pour détecter toute déviation.
L’AOI est particulièrement efficace pour vérifier l’intégrité du processus de gravure et s’assurer que toutes les traces sont correctement formées.
Inspection par Rayons X :
L’inspection par rayons X est utilisée pour vérifier les couches internes et les connexions, en particulier les vias, pour détecter les défauts invisibles à l’œil nu. Cette méthode est essentielle pour les PCB multicouches, car les défauts dans les vias enterrés ou aveugles peuvent affecter considérablement les performances de la carte.
L’inspection par rayons X aide également à détecter les éventuels problèmes dans les joints de soudure lors de la phase d’assemblage.
Tests Électriques :
Des tests électriques sont effectués pour garantir que tous les circuits du PCB sont correctement connectés et exempts de courts-circuits ou de circuits ouverts. Des testeurs à sondes volantes ou des testeurs à lit de clous sont couramment utilisés à cet effet.
Les tests électriques vérifient la continuité des traces et la fonctionnalité du PCB avant qu’il ne passe à l’étape d’assemblage.
Mesures de Contrôle Qualité :
Conformité aux Certifications :
South-Electronic veille à ce que tous les PCB à 6 couches respectent les normes et certifications industrielles telles que ISO9001, UL, CE, IATF16949 et ISO13485. Ces certifications garantissent que les PCB sont fabriqués selon les normes de qualité et de sécurité les plus élevées.
Inspections en Cours de Processus :
Tout au long du processus de fabrication, des inspections en cours sont effectuées pour détecter les défauts à un stade précoce et prévenir les retouches coûteuses ultérieurement. Ces inspections comprennent la vérification de l’alignement des couches, de la qualité des vias percés et de la précision du dépôt de cuivre.
Assurance Qualité Finale (QA) :
Avant l’expédition, les PCB finis subissent une dernière série d’inspections et de tests pour garantir qu’ils respectent toutes les spécifications de conception et les normes de qualité. Tout défaut ou problème détecté à ce stade est corrigé avant que les cartes ne soient emballées pour la livraison.
L’assurance qualité finale garantit que les clients reçoivent des PCB pleinement fonctionnels et de haute qualité, assurant une fiabilité optimale dans leurs applications prévues.
Chapitre 6
Défis Courants dans la Conception de PCB à 6 Couches
La conception d’un PCB à 6 couches présente une série de défis, notamment la gestion des interférences entre signaux, le contrôle des signaux à haute vitesse, et la gestion thermique dans des conceptions densément peuplées. Ces défis nécessitent une attention particulière à la disposition, au choix des matériaux, et à l’application de techniques de conception adaptées pour garantir des performances optimales. Explorons les défis les plus courants et comment les relever.
- Gestion des interférences entre signaux :
Les interférences entre signaux se produisent lorsque les signaux d’une trace interfèrent avec ceux d’une trace voisine, provoquant des bruits ou des distorsions indésirables. Ce problème est particulièrement critique dans les PCB multicouches où la densité des traces est élevée.
Pour gérer efficacement les interférences entre signaux :
- Optimiser la superposition des couches : Placer les plans de masse à proximité des couches de signaux.
- Augmenter l’espacement des traces : Réduire le couplage électromagnétique.
- Utiliser des traces de garde : Absorbent les interférences avant qu’elles n’affectent les signaux adjacents.
- Gestion des signaux à haute vitesse :
Les signaux à haute vitesse nécessitent un contrôle précis pour éviter les distorsions.
- Contrôle de l’impédance : Éviter les dégradations des signaux.
- Utilisation de paires différentielles : Réduire les EMI.
- Minimiser les transitions via les vias : Limiter les pertes de signal.
- Gestion thermique dans des conceptions denses :
Une gestion thermique efficace est cruciale pour éviter la surchauffe.
- Utilisation de vias thermiques : Pour dissiper la chaleur.
- Plans en cuivre pour dissipation thermique : Renforcer les couches internes.
- Placement et espacement des composants : Répartir les sources de chaleur.
En intégrant ces techniques, les ingénieurs peuvent assurer des performances optimales même dans des PCB à 6 couches densément peuplés.
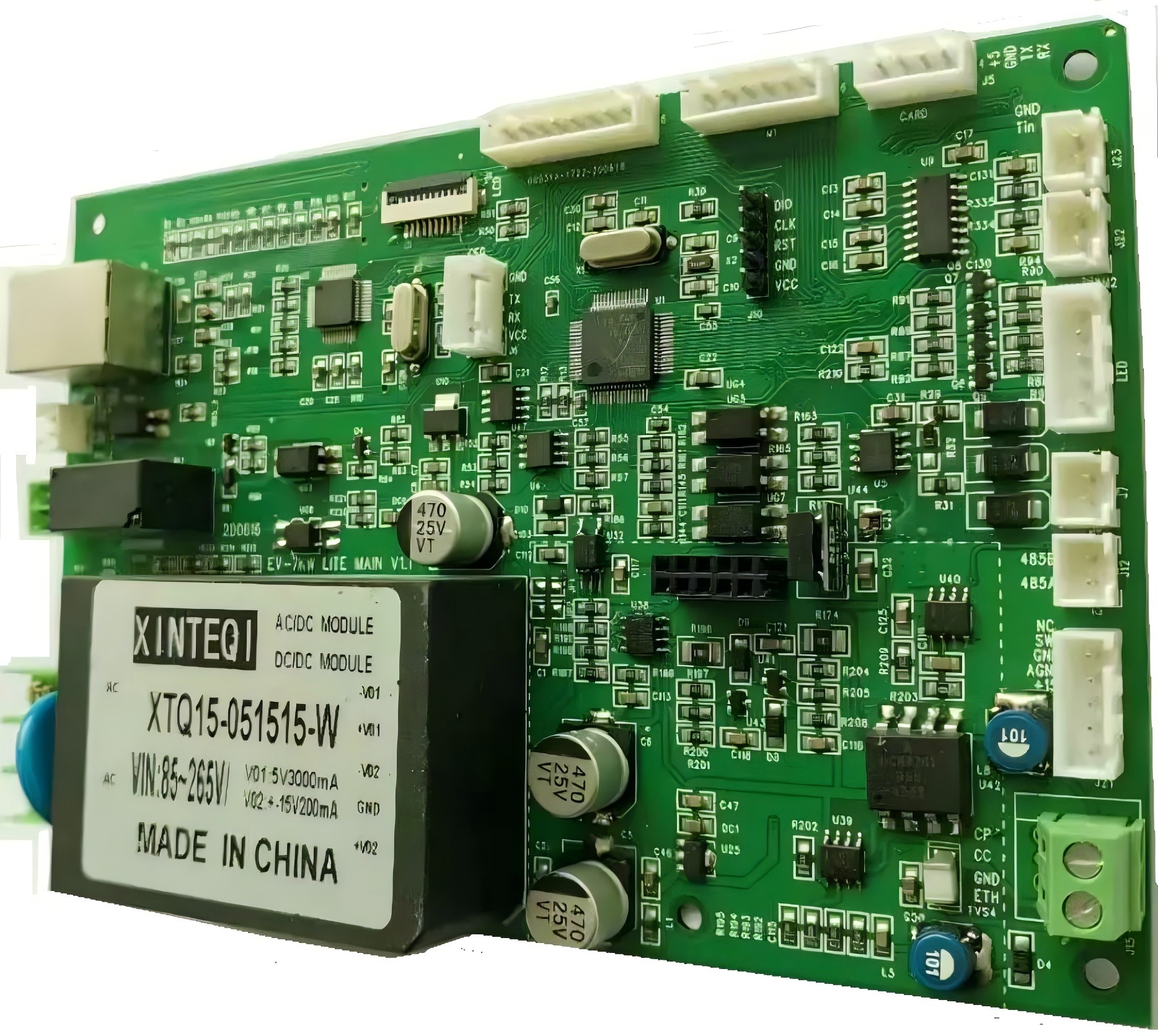
Chapitre 7
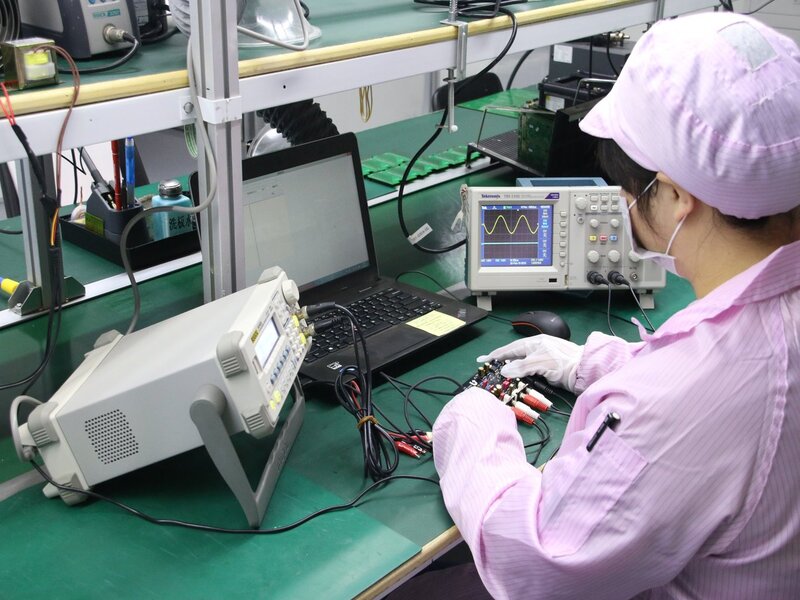
Choix des Matériaux pour un PCB à 6 Couches
Le choix des matériaux pour un PCB à 6 couches est crucial car il influence les performances, la durabilité, et le coût de la carte. Différentes applications nécessitent des matériaux de substrat spécifiques en fonction de leurs propriétés électriques, de leur stabilité thermique, et de leur résistance mécanique. Dans cette section, je vous présenterai les matériaux de substrat les plus courants, leur impact sur les performances et le coût, et comment choisir le meilleur matériau pour votre application.
1. Différences entre les Matériaux de Substrat
Le matériau de substrat d’un PCB est la couche isolante qui sépare et soutient les couches conductrices en cuivre. Les matériaux les plus courants pour les PCB à 6 couches incluent FR4, FR4 à haute Tg, et polyimide, bien que d’autres matériaux avancés puissent être utilisés pour des applications spécifiques.
FR4 (Flame Retardant 4) :
FR4 est le matériau standard de l’industrie pour la plupart des PCB.
Avantages :
- Bon rapport coût/performance.
Inconvénients : - Limité pour les environnements à haute température ou les fréquences élevées.
FR4 à Haute Tg :
Ce matériau peut supporter des températures élevées sans se dégrader.
Avantages :
- Meilleure stabilité thermique.
Inconvénients : - Plus cher que le FR4 standard.
Polyimide :
Matériau performant, idéal pour les environnements à très haute température.
Avantages :
- Excellente durabilité et flexibilité.
Inconvénients : - Coût élevé.
Laminés Rogers :
Utilisés dans les applications RF et micro-ondes.
Avantages :
- Faible perte diélectrique.
Inconvénients : - Très coûteux.
2. Impact des Matériaux sur les Performances et les Coûts
Performances Thermiques :
Les matériaux à haute conductivité thermique sont préférables pour éviter les problèmes liés à la chaleur.
Performances Électriques :
- Constante diélectrique (Dk) : Une faible valeur Dk réduit les délais de propagation.
- Facteur de dissipation (Df) : Un faible Df assure une meilleure intégrité du signal.
Résistance Mécanique et Flexibilité :
Les substrats comme le polyimide conviennent aux PCB flexibles.
Facteurs Environnementaux :
Les environnements difficiles nécessitent des matériaux résistants à l’humidité et aux produits chimiques.
Choisir le Bon Matériau pour Votre Application
Température de Fonctionnement :
Optez pour du FR4 à haute Tg ou du polyimide si la carte est soumise à des températures élevées.
Fréquence du Signal :
Pour des applications à haute fréquence, choisissez des matériaux comme les laminés Rogers.
Considérations de Coût :
Le FR4 est une option économique, mais pour des performances accrues, le coût supplémentaire peut être justifié.
Chapitre 8
Finitions de Surface pour un PCB à 6 Couches
Les finitions de surface jouent un rôle crucial dans la fabrication des PCB à 6 couches en protégeant les plots de cuivre exposés contre l’oxydation et la contamination tout en améliorant la soudabilité lors de l’assemblage. Le choix de la finition appropriée est essentiel pour garantir une fiabilité à long terme et des performances optimales. Dans cette section, nous explorerons les types de finitions les plus courants, leur impact sur la soudabilité et la fiabilité, et comment choisir la meilleure finition pour votre application.
1. Types de Finitions de Surface
Plusieurs finitions sont couramment utilisées dans l’industrie des PCB, chacune avec ses avantages et limitations. Le choix dépend de facteurs tels que la méthode d’assemblage, les conditions environnementales, et les considérations de coût. Voici les options les plus populaires :
HASL (Nivellement à l’Air Chaud):
Très répandu en raison de son faible coût et de sa facilité d’application.
- Avantages : Économique, bonne soudabilité, longue durée de vie.
- Inconvénients : Surface inégale, peu adaptée aux composants à pas fin.
- Applications : Assemblages généraux.
ENIG (Nickel Chimique Immersion Or):
Populaire pour les PCB complexes.
- Avantages : Surface plane, excellente résistance à la corrosion.
- Inconvénients : Coût élevé, risque de « pads noirs ».
- Applications : Circuits HDI, BGA.
OSP (Préservatif Organique de Soudabilité):
Protège le cuivre de l’oxydation.
- Avantages : Respectueux de l’environnement, économique.
- Inconvénients : Durée de vie limitée.
- Applications : Électronique grand public.
Argent et Étain Immersion:
Fournissent une excellente performance électrique mais sont sensibles à l’oxydation.
2. Impact des Finitions sur la Soudabilité et la Fiabilité
- Soudabilité : ENIG et OSP offrent une excellente soudabilité.
- Résistance à l’oxydation : ENIG est supérieur.
- Durabilité en cycles de refusion : ENIG et HASL sont robustes.
3. Choisir la Meilleure Finition pour Vos Besoins
- Pour les conceptions complexes : ENIG ou OSP sont recommandés.
- Pour les productions économiques : HASL ou OSP.
- Pour une fiabilité accrue : ENIG est idéal.
- Pour des environnements difficiles : ENIG ou argent immersion.
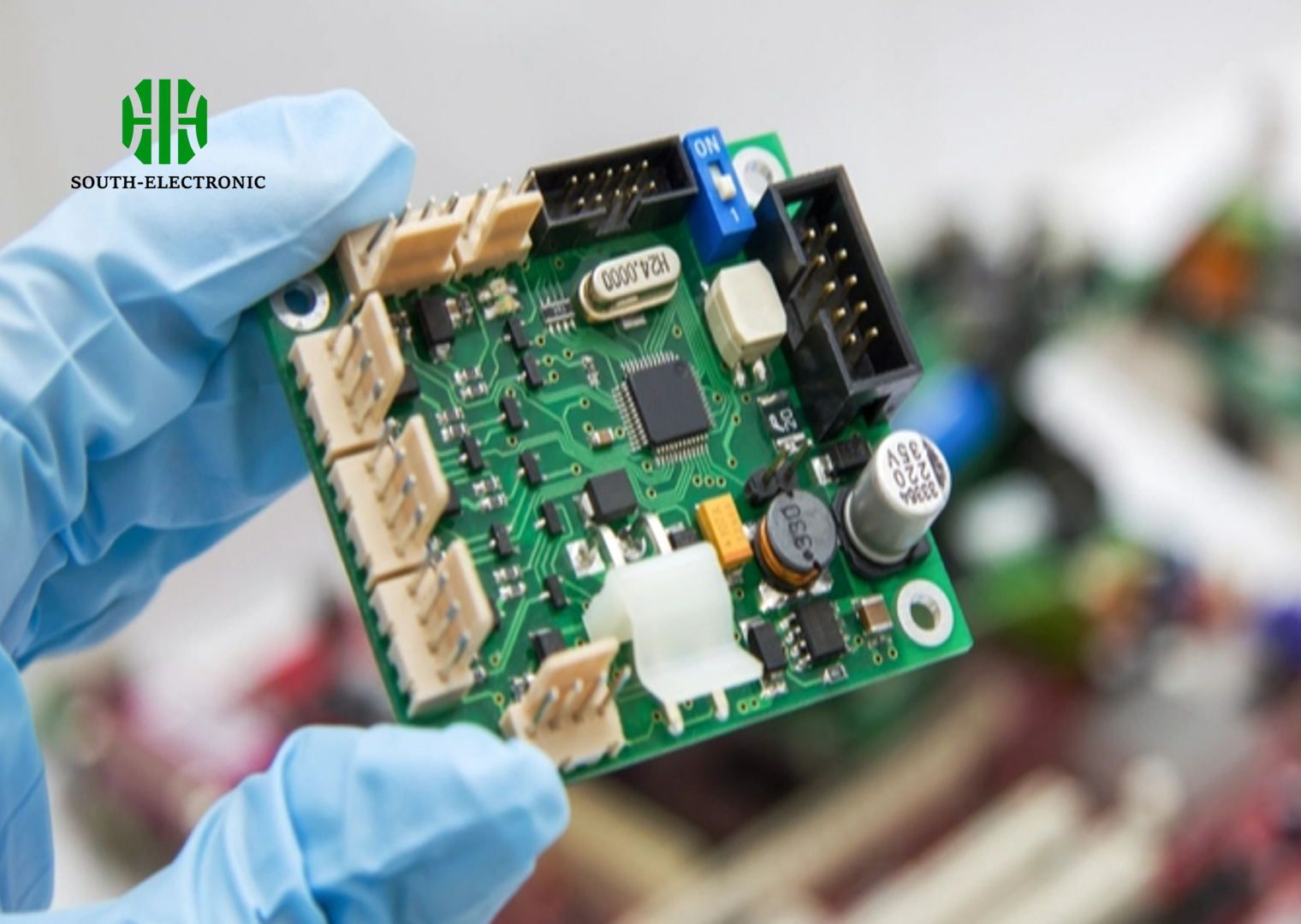
Chapitre 9

Considérations de Coût
La fabrication d’un PCB à 6 couches implique plusieurs facteurs pouvant considérablement influencer le coût total de production. Comprendre ces facteurs est essentiel pour prendre des décisions éclairées concernant les matériaux, la complexité du design, et le volume de commande tout en respectant les exigences de performance. Dans cette section, nous examinerons les principaux facteurs de coût, fournirons des conseils pour équilibrer coût et performance, et proposerons des stratégies pratiques pour réduire les coûts.
1. Facteurs Clés de Coût dans la Fabrication de PCB à 6 Couches
Matériaux :
Le choix des matériaux est l’un des principaux facteurs de coût.
- Matériaux de Substrat : Le FR4 standard est le plus économique. Cependant, des matériaux comme le FR4 à haute Tg, le polyimide ou les laminés Rogers augmentent considérablement le coût.
- Épaisseur du Cuivre : Une épaisseur standard de 1 oz est courante, mais des épaisseurs plus importantes augmentent le coût.
- Finitions de Surface : Les finitions comme HASL sont plus abordables, tandis que ENIG et Immersion Silver sont plus coûteuses.
Complexité du Design :
- Nombre de Couches : Plus il y a de couches, plus les coûts de fabrication augmentent.
- Composants à Pas Fin et Dispositions Denses : Nécessitent plus de précision, augmentant ainsi les coûts.
- Types de Vias : Les vias aveugles et enterrés augmentent la complexité et le coût.
Volume de Commande :
- Prototypes ou Petites Séries : Coût plus élevé par unité en raison des frais fixes.
- Production à Grande Échelle : Réduction significative des coûts unitaires grâce aux économies d’échelle.
2. Comment Équilibrer Coût et Performance
- Choisir le Matériau Approprié : Le FR4 standard est le choix le plus économique, mais optez pour des matériaux haut de gamme si nécessaire.
- Optimiser l’Empilement des Couches : Ne pas ajouter de couches inutiles.
- Équilibrer Épaisseur du Cuivre et Design des Traces : Utiliser uniquement l’épaisseur nécessaire pour éviter les surcoûts.
- Simplifier le Design : Réduire les vias complexes et les tracés compliqués.
3. Conseils pour Réduire les Coûts des PCB à 6 Couches
- Utiliser des Matériaux Standards : Préférez le FR4 pour les applications générales.
- Choisir des Finitions Économiques : Optez pour HASL ou OSP pour réduire les coûts.
- Minimiser les Types de Vias : Utilisez des vias traversants standard pour économiser.
- Commander en Grandes Quantités : Profitez des réductions de volume pour réduire le coût unitaire.
- Design pour la Fabrication : Simplifiez le design en suivant les recommandations du fabricant pour réduire les coûts liés à la production.
Chapitre 10
Choisir le Bon Fabricant pour un PCB à 6 Couches
Lors de l’évaluation des fabricants de PCB, notamment pour des conceptions multicouches et à haute performance comme les PCBs à 6 couches, tenez compte des facteurs suivants :
Capacités de Fabrication :
Il est essentiel de vérifier que le fabricant dispose des technologies nécessaires pour gérer des conceptions multicouches complexes. Cela inclut des techniques avancées de perçage de vias (vias aveugles et enterrés), le contrôle d’impédance, et des finitions de surface de haute qualité comme ENIG ou l’argent immersion. Assurez-vous également que le fabricant possède des équipements modernes pour les composants à pas fin et les interconnexions haute densité (HDI).
Expérience avec les PCBs Multicouches :
L’expérience est cruciale lorsqu’il s’agit de PCBs multicouches comme ceux à 6 couches. Les fabricants spécialisés dans ce domaine seront mieux équipés pour gérer les défis liés à l’intégrité du signal, à l’optimisation de l’empilement des couches, et aux techniques de routage avancées. Recherchez un fournisseur ayant un historique éprouvé dans la production de PCBs à 6 couches pour des applications similaires aux vôtres.
Délais d’Exécution :
La rapidité est souvent un facteur important dans la production de PCBs, notamment lors du prototypage ou pour respecter des délais serrés. Un fournisseur fiable doit offrir des options de délais flexibles, y compris une production rapide pour les prototypes et des délais raisonnables pour les commandes en grande quantité. Toutefois, la rapidité ne doit pas se faire au détriment de la qualité.
Options de Personnalisation :
Un bon fabricant de PCB doit offrir une flexibilité dans la personnalisation pour répondre aux exigences spécifiques de votre projet. Cela inclut des options pour le choix des matériaux, l’épaisseur du cuivre, les finitions de surface, et les types de vias. Un fabricant proposant un large éventail d’options de personnalisation vous aidera à obtenir la carte exacte dont vous avez besoin pour votre application.
Support Client et Communication :
Une communication claire est essentielle tout au long des étapes de conception, de production, et de livraison. Choisissez un fabricant qui offre un support technique solide, des réponses rapides aux questions, et une communication transparente sur les mises à jour de production, les expéditions, et tout problème potentiel.
Efficacité des Coûts :
Bien que le coût ne doive pas être le seul facteur déterminant, il est important de travailler avec un fournisseur offrant des prix compétitifs sans compromettre la qualité. Les remises sur les commandes en gros, la flexibilité dans le choix des matériaux, et des processus de fabrication économiques sont des considérations importantes pour gérer les contraintes budgétaires.
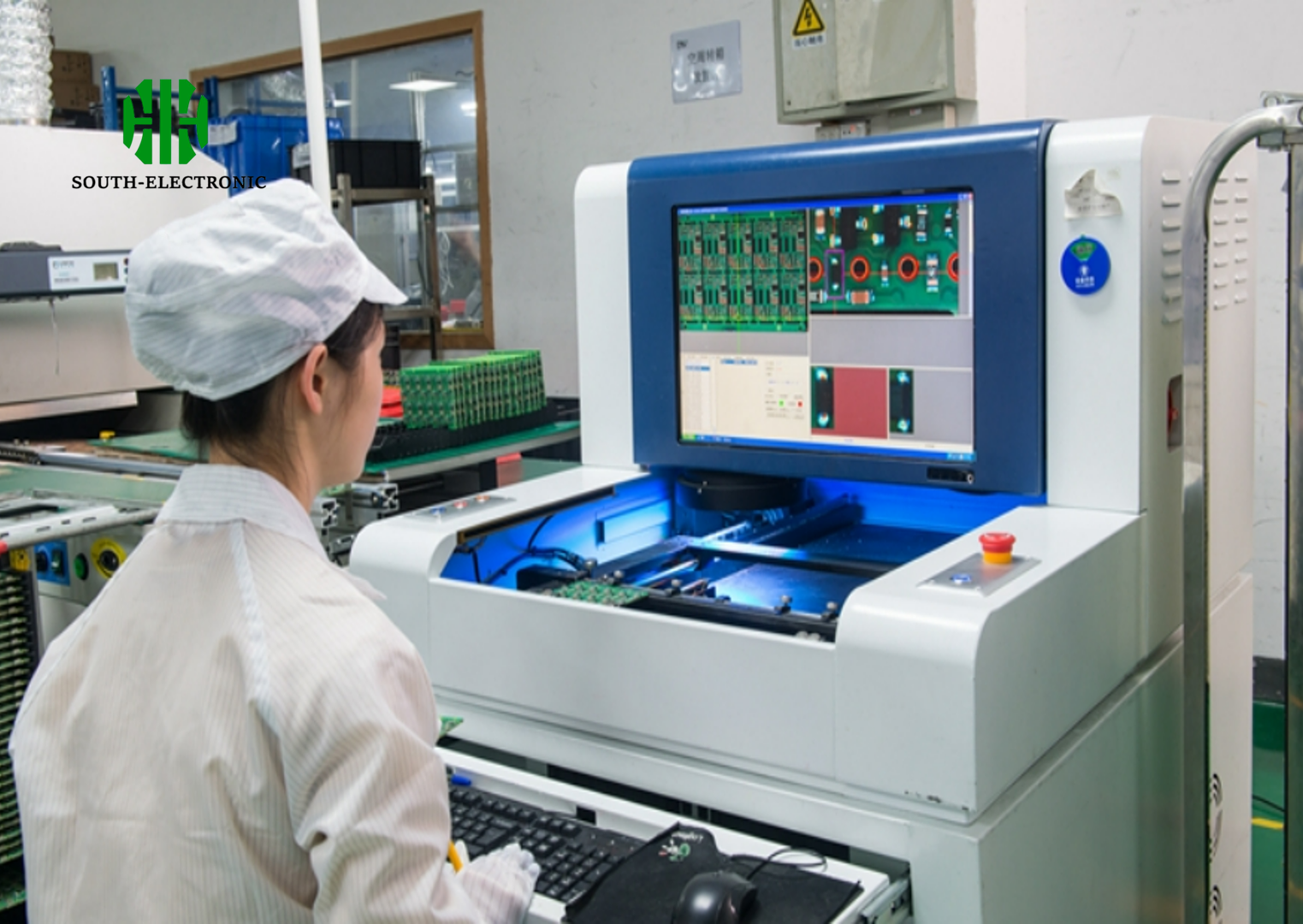
Contactez-Nous
Où Sommes-Nous ?
Parc Industriel, No. 438 Route Donghuan, No. 438, Shajing Donghuan Road, District Bao'an, Shenzhen, Guangdong, Chine
4ème étage, Bâtiment Zhihui Créatif, No. 2005 Route Xihuan, Shajing, District Baoan, Shenzhen, Chine
CHAMBRE A1-13, ÉTAGE 3, CENTRE INDUSTRIEL YEE LIM, 2-28 RUE KWAI LOK, KWAI CHUNG HK
service@southelectronicpcb.com
Téléphone : +86 400 878 3488
Envoyez-nous un message
Plus vous remplissez de détails, plus nous pourrons avancer rapidement à l’étape suivante.
