PCB de haute qualité à 8 couches
South-Electronic
Optez pour South-Electronic pour la meilleure qualité, fiabilité et valeur pour vos besoins en PCB. Découvrez la différence avec notre service tout-en-un de PCB à 8 couches – de la conception à la livraison, nous garantissons précision, durabilité et conformité aux normes les plus élevées de l'industrie.
Votre partenaire de confiance pour des PCB à 8 couches de haute qualité
Pourquoi choisir South-Electronic ?
South-Electronic est votre solution de choix. Avec plus d’une décennie d’expertise, nous livrons des PCB à 8 couches conçus avec précision pour respecter les normes les plus élevées de l’industrie. Que vous ayez besoin d’une seule pièce ou d’une commande en gros, nous proposons des solutions sur mesure avec un délai de réponse rapide.
-
Flexibilité de Personnalisation
Vous aurez la liberté de commander exactement ce dont vous avez besoin, que ce soit un prototype unique ou des volumes de production importants.
Nos capacités avancées de personnalisation garantissent que votre PCB à 8 couches est conçu et fabriqué pour répondre même aux spécifications les plus complexes, vous offrant des solutions sur mesure qui s’alignent parfaitement avec les exigences de votre projet. -
Équipe Expérimentée
Vous pouvez faire confiance à notre équipe d'experts chevronnés, avec plus d'une décennie d'expérience pratique dans la fabrication de PCB.
Des conceptions complexes à la résolution de défis techniques, nos ingénieurs sont bien informés des dernières tendances et innovations de l'industrie, garantissant que vos PCBs à 8 couches sont de la plus haute qualité et précision. -
Contrôle de Qualité Stricte
Vous bénéficierez d'un processus véritablement transparent, du moment où vous partagez votre conception jusqu'à la livraison finale de vos circuits imprimés à 8 couches.
Nous gérons chaque étape de la production en interne, du prototypage à l'assemblage, en utilisant des équipements de pointe qui garantissent précision, rapidité et cohérence. Votre satisfaction est notre priorité, et nous sommes là pour vous accompagner à chaque étape. -
Service Complet
Vous vivrez un processus véritablement fluide dès le moment où vous partagez votre conception jusqu'à la livraison finale de vos PCBs à 8 couches.
Nous gérons chaque étape de la production en interne, de la prototypage à l’assemblage, en utilisant des équipements à la pointe de la technologie qui garantissent précision, rapidité et cohérence. Votre satisfaction est notre priorité, et nous sommes là pour vous soutenir à chaque étape. -
Livraison Rapide
Vous bénéficierez de nos processus de production rationalisés et de machines avancées qui nous permettent de respecter des délais serrés sans sacrifier la qualité.
Que ce soit pour un projet sensible au temps ou une commande en gros, vous pouvez compter sur nous pour une livraison rapide et fiable qui maintient votre projet dans les délais. -
Satisfaction Garanti
Vous apprécierez la confiance qui vient de travailler avec une entreprise certifiée ISO9001.
Nous priorisons une communication claire et transparente et nous nous tenons à des normes élevées, assurant que vos PCBs à 8 couches non seulement répondent mais dépassent vos attentes en matière de performance, de durabilité et de précision.
Projets Connus que Nous Avons Réalisés
Avis des Clients
Questions Fréquentes
Questions les Plus Populaires
South-Electronic offre un fort soutien après-vente, proposant des garanties sur ses produits. Ils adhèrent à des mesures strictes de contrôle de qualité telles que les certifications ISO et RoHS, assurant fiabilité à long terme et satisfaction client.
South-Electronic est certifié UL, CE, IATF16949, ISO13485 et ISO9001, vous pouvez donc être confiant que leurs PCB à 8 couches répondent aux normes internationales les plus élevées en matière de qualité, de sécurité et de performance.
Le délai de traitement typique pour les PCB à 8 couches se situe entre 7 et 15 jours ouvrables, selon la complexité et la quantité de votre commande. Si vous avez besoin d'une livraison plus rapide, ils proposent également des options d'expédition accélérée.
Pour obtenir un devis, vous pouvez visiter le site de South-Electronic et soumettre vos spécifications de conception via leur formulaire de contact ou envoyer un e-mail directement à leur équipe de vente. Ils répondront rapidement avec un devis détaillé basé sur vos exigences.
Oui, South-Electronic propose une expédition mondiale pour garantir une livraison rapide aux clients du monde entier. Leurs solutions logistiques sont conçues pour fournir une livraison sécurisée et efficace.
South-Electronic offre un fort soutien après-vente, proposant des garanties sur ses produits. Ils adhèrent à des mesures strictes de contrôle de qualité telles que les certifications ISO et RoHS, assurant fiabilité à long terme et satisfaction client.
Envoyez-nous un message
Plus vous remplissez de détails, plus nous pourrons avancer rapidement à l’étape suivante.
Le Guide Complet pour les PCB à 8 Couches
Table des Matières
Chapitre 1
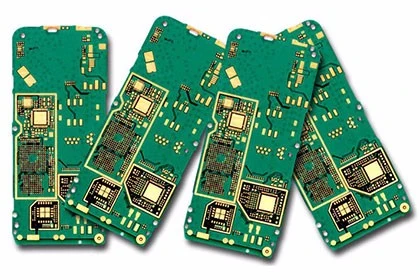
Introduction au PCB à 8 Couches
Qu’est-ce qu’un PCB à 8 Couches ?
Un PCB à 8 couches est un type de carte de circuit imprimé multicouche qui comporte huit couches de matériau conducteur, généralement du cuivre, séparées par des matériaux isolants (également appelés dielectrics). Ces couches sont laminées ensemble à l’aide de chaleur et de pression pour créer une structure compacte, robuste et efficace. Les couches conductrices permettent un routage complexe des signaux électriques, tandis que les couches isolantes préviennent les interférences entre différents signaux sur la carte.
En résumé, les PCB à 8 couches sont essentiels pour créer des systèmes électroniques avancés et haute performance, ce qui en fait une pierre angulaire de nombreuses industries, y compris les télécommunications, l’automobile, la médecine et les applications industrielles.
Importance et Utilisations Courantes des PCB à 8 Couches dans l’Électronique
Les PCB à 8 couches jouent un rôle crucial dans l’électronique moderne, en particulier dans les applications où l’espace est limité mais où les exigences de performance sont élevées. Les couches supplémentaires permettent une meilleure intégrité des signaux, une meilleure compatibilité électromagnétique (EMC) et une distribution de puissance améliorée. Ces avantages font des PCB à 8 couches des choix idéaux pour des applications nécessitant des performances robustes et une fiabilité.
Importance Clé :
Intégrité des Signaux : Avec plus de couches, les traces de signal peuvent être mieux séparées, réduisant ainsi les interférences et le bruit. Cela conduit à des signaux plus clairs et à de meilleures performances, en particulier pour les transmissions de données à haute vitesse.
Distribution de Puissance : Les couches supplémentaires permettent une distribution plus efficace des plans d’alimentation, minimisant les chutes de tension et garantissant une alimentation stable à tous les composants.
Miniaturisation : Les PCB à 8 couches permettent aux concepteurs de compacter davantage de fonctionnalités dans des appareils plus petits, ce qui est essentiel pour l’électronique moderne comme les smartphones et les dispositifs portables.
Gestion Thermique : Les couches supplémentaires peuvent aider à gérer la chaleur de manière plus efficace, ce qui est crucial pour les composants haute performance.
Utilisations Courantes :
Télécommunications : Les PCB à 8 couches sont couramment utilisés dans les dispositifs de mise en réseau comme les routeurs, les commutateurs et l’équipement de télécommunications, où un transfert de données haute vitesse est essentiel.
Électronique Automobile : Dans les véhicules modernes, les PCB à 8 couches sont utilisés pour des systèmes avancés comme les unités de contrôle moteur (ECUs), les modules GPS et les systèmes d’infodivertissement qui nécessitent des conceptions compactes et des performances fiables.
Dispositifs Médicaux : La précision et la fiabilité des PCB à 8 couches les rendent adaptés aux dispositifs médicaux, y compris les appareils de diagnostic et les équipements d’imagerie, où la précision est critique.
Automatisation Industrielle : Les PCB à 8 couches sont utilisés dans les systèmes de contrôle industriel et l’équipement d’automatisation, où la durabilité, l’intégrité des signaux et des performances élevées sont nécessaires.
En résumé, les PCB à 8 couches sont essentiels pour créer des systèmes électroniques avancés et haute performance, faisant d’eux une pierre angulaire de nombreuses industries, y compris les télécommunications, l’automobile, la médecine et les applications industrielles.
Chapitre 2
Avantages d'Utiliser un PCB à 8 Couches
1. Intégrité des Signaux Améliorée et Réduction des Interférences
Un des plus grands avantages d’utiliser un PCB à 8 couches est l’amélioration significative de l’intégrité des signaux. L’intégrité des signaux fait référence à la qualité des signaux électriques lors de leur transit à travers le PCB. Dans des conceptions avec moins de couches, les chemins de signal peuvent être plus longs, ce qui peut entraîner des problèmes potentiels comme la perte de signal, le crosstalk, et les interférences électromagnétiques (EMI). Ces problèmes peuvent dégrader les performances de l’appareil, en particulier dans les applications à haute vitesse.
Avec un PCB à 8 couches, les couches supplémentaires permettent une meilleure séparation entre les chemins de signal, réduisant ainsi la probabilité d’interférence entre eux. De plus, des couches spécialisées peuvent être désignées pour la mise à la terre ou la distribution de l’énergie, aidant à protéger les traces de signal sensibles contre les interférences. En conséquence, cette séparation accrue et la mise à la terre améliorent la qualité globale des signaux, rendant le PCB adapté pour des applications haute fréquence comme les télécommunications, le traitement des données, et les circuits RF.
Bénéfices Clés :
- Réduction du crosstalk entre les signaux grâce à une meilleure gestion des couches.
- Amélioration du blindage avec des plans de mise à la terre et d’énergie dédiés.
- Adapté aux applications à haute vitesse et haute fréquence où l’intégrité des signaux est critique.
2. Densité de Composants Plus Élevée et Efficacité Spatiale
Alors que les appareils électroniques continuent de se réduire tout en augmentant en fonctionnalités, le besoin de PCBs compacts et à haute densité devient de plus en plus important. Un PCB à 8 couches offre un avantage significatif en permettant aux concepteurs d’accommoder plus de composants et un routage complexe dans un espace plus petit. Ceci est particulièrement bénéfique pour les appareils où l’espace est précieux, telles que les smartphones, les tablettes, et les électroniques portables.
Les multiples couches d’un PCB à 8 couches permettent un routage plus efficace des signaux, réduisant le besoin de longues traces sinueuses sur les couches de surface. Cela permet non seulement de gagner de l’espace, mais raccourcit également les chemins de signal, ce qui contribue à de meilleures performances. De plus, le nombre plus élevé de couches permet plus de flexibilité dans le placement des composants, permettant aux concepteurs de maximiser les fonctionnalités dans un espace plus petit sans compromettre les performances ou l’intégrité du circuit.
Bénéfices Clés :
- Une densité de composants plus élevée permet plus de fonctionnalités dans des appareils compacts.
- Un routage efficace avec des chemins de signal plus courts améliore les performances générales.
- L’efficacité spatiale permet la production d’électroniques plus petites et plus puissantes.
3. Amélioration de la Dissipation Thermique
La gestion thermique est une considération critique dans la conception de PCB, en particulier pour les applications à forte puissance ou les dispositifs fonctionnant en continu pendant de longues périodes. Une chaleur excessive peut dégrader les performances et la durée de vie des composants, rendant la dissipation de la chaleur efficace essentielle.
Un PCB à 8 couches offre une meilleure dissipation thermique que les cartes avec moins de couches, car les couches supplémentaires peuvent aider à répartir la chaleur de manière plus uniforme sur la carte. Dans les PCBs multicouches, des vias thermiques – petits trous remplis de matériau conducteur – peuvent être utilisés pour transférer la chaleur des couches de surface vers les couches internes, où elle peut être dissipée plus efficacement. Cela réduit la concentration de chaleur dans une zone particulière, aidant à protéger les composants sensibles des dommages thermiques.
De plus, les couches ajoutées permettent l’inclusion de plans de cuivre plus épais dédiés à la distribution de puissance, ce qui aide à conduire la chaleur loin des zones critiques. Ceci est particulièrement important dans des applications telles que les machines industrielles, l’électronique automobile, et les alimentations, où une chaleur excessive peut compromettre la fiabilité et les performances.
Bénéfices Clés :
- Meilleure gestion thermique grâce à une distribution uniforme de la chaleur sur les couches.
- Les vias thermiques améliorent la dissipation thermique, protégeant les composants de la surchauffe.
- Adapté aux applications à forte puissance et aux environnements où la chaleur est un problème.
Conclusion
En résumé, les avantages des PCBs à 8 couches en font un choix idéal pour des applications haute performance, limitées en espace, et sensibles à la chaleur. L’amélioration de l’intégrité des signaux, une plus grande densité de composants, et une meilleure dissipation thermique garantissent que ces PCBs sont bien adaptés aux technologies avancées dans des secteurs tels que les télécommunications, l’automobile, et l’automatisation industrielle.

Chapitre 3
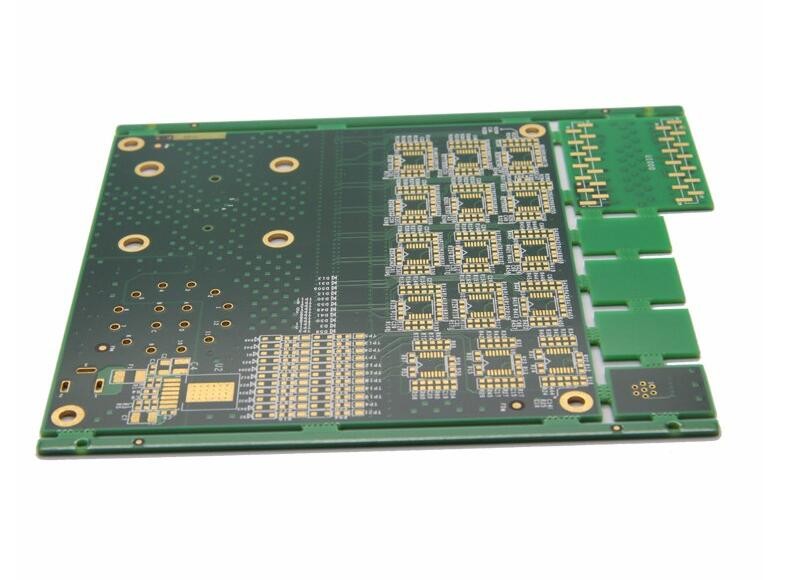
Conception de l'Empilement de PCB à 8 Couches
Explication de la Structure de l’Empilement
La conception de l’empilement d’un PCB se réfère à la manière dont les couches de cuivre (utilisées pour le routage des signaux et de l’énergie) et les matériaux isolants (connus sous le nom de diélectriques) sont disposés dans la carte. Dans un PCB à 8 couches, il y a huit couches conductrices, généralement en cuivre, qui sont séparées par des couches de matériau isolant. La conception de l’empilement est cruciale car elle impacte directement les performances électriques de la carte, sa fabricabilité, et son coût.
Dans un PCB à 8 couches standard, les couches sont disposées dans un ordre spécifique, généralement avec les couches de signal sur les couches extérieures et les plans d’alimentation et de mise à la terre entre elles. Cet arrangement aide à maintenir l’intégrité du signal, réduire le bruit, et fournir un réseau stable de distribution d’énergie. L’objectif d’un empilement bien conçu est de créer une structure optimisée qui minimise les interférences électromagnétiques (EMI), soutient les signaux à haute vitesse, et gère efficacement la distribution de l’énergie.
Un empilement typique à 8 couches se compose de couches alternées de signal et de plans d’alimentation/de terre :
- Couches de Signal : Utilisées pour le routage des signaux électriques entre les composants.
- Plans de Terre : Fournissent un point de référence pour les signaux, aidant à réduire le bruit et l’EMI.
- Plans d’Alimentation : Distribuent l’énergie aux composants tout en minimisant les chutes de tension et les interférences.
Comment Optimiser l’Arrangement des Couches pour l’Intégrité du Signal, la Distribution de l’Énergie, et la Mise à la Terre
L’arrangement des couches dans un PCB à 8 couches joue un rôle crucial dans l’atteinte d’une intégrité du signal optimale, d’une bonne distribution de l’énergie, et d’une mise à la terre efficace. Voici des stratégies clés pour optimiser l’empilement :
Intégrité du Signal :
Couches de Signal et Plans de Terre Alternés : Placer les couches de signal adjacentes aux plans de terre (ou d’alimentation) aide à protéger les signaux et réduit les interférences électromagnétiques. Cette configuration diminue les chances de crosstalk entre les signaux, surtout dans les circuits à haute vitesse.
Minimiser les Longueurs de Chemin de Signal : Garder les traces de signal courtes et placer des signaux connexes sur les mêmes couches ou des couches adjacentes peut réduire le retard de signal et la perte, améliorant ainsi les performances globales.
Routage de Paires Différentielles : Pour des signaux à haute vitesse, utilisez des paires différentielles (deux traces étroitement espacées portant des signaux égaux et opposés) sur les couches de signal pour améliorer l’immunité au bruit.
Distribution de l’Énergie :
Plans d’Alimentation Dédiés : Placer un plan d’alimentation adjacent à un plan de terre crée un chemin de faible inductance pour la distribution d’énergie, ce qui réduit les fluctuations de tension et assure une livraison d’énergie stable. Ceci est particulièrement important dans les circuits à haute puissance.
Optimiser le Placement des Couches d’Alimentation et de Terre : Les couches d’alimentation et de terre devraient être étroitement jumelées pour créer un « sandwich d’énergie », minimisant l’impédance et fournissant un flux d’énergie plus fluide vers les composants.
Mise à la Terre :
Multiples Couches de Terre : Avoir plusieurs couches de terre dans l’empilement améliore le blindage, réduit le bruit, et fournit un référentiel stable pour les signaux. Les couches de terre sont essentielles pour maintenir l’intégrité du signal, en particulier dans les applications haute fréquence.
Vias et Connexions de Terre : Ajouter de nombreux vias de terre (connexions verticales entre les couches) aide à garantir une mise à la terre appropriée à travers toutes les couches, réduisant ainsi le risque de dégradation du signal.
Chapitre 4
Choix des Matériaux pour les PCB à 8 Couches
Choisir les bons matériaux pour un PCB à 8 couches est crucial pour atteindre les performances, la durabilité et le rapport coût-efficacité souhaités pour votre application spécifique. Le matériau influence principalement les propriétés électriques, thermiques et mécaniques du PCB, ce qui affecte à son tour l’intégrité des signaux, la dissipation thermique et la fiabilité globale. Dans cette section, nous allons explorer les meilleurs matériaux pour les PCB à 8 couches, leurs utilisations spécifiques et comment le choix du matériau impacte la performance, le coût et la durabilité.
Meilleurs Matériaux pour Différentes Applications
FR4 (Ignifuge 4)
Aperçu : Le FR4 est l’un des matériaux les plus couramment utilisés pour les substrats de PCB. Il s’agit d’un stratifié en époxy renforcé de verre qui offre une excellente isolation électrique, une résistance mécanique et une résistance à l’humidité et à la chaleur.
Applications : Le FR4 est largement utilisé dans l’électronique grand public, les télécommunications, l’électronique automobile et les équipements industriels. Il est adapté aux applications à basse et moyenne fréquence où le coût est un facteur significatif.
Avantages :
- Coût bas et largement disponible.
- Bonne résistance mécanique et isolation électrique.
- Adapté aux applications générales, y compris les conceptions multicouches comme les PCB à 8 couches.
Inconvénients :
- Performance limitée à haute fréquence en raison de pertes diélectriques plus élevées comparées à des matériaux spécialisés comme Rogers.
- Conductivité thermique inférieure, ce qui la rend moins idéale pour les applications générant une chaleur significative.
Rogers (Stratifiés Haute Fréquence)
Aperçu : Rogers est un matériau haute performance connu pour ses excellentes propriétés diélectriques et sa faible perte de signal à haute fréquence. Il est couramment utilisé dans des applications nécessitant une intégrité du signal supérieure, telles que les circuits RF et micro-ondes.
Applications : Les stratifiés Rogers sont utilisés dans les systèmes numériques à haute vitesse, RF, micro-ondes et de communication, où la perte de signal doit être minimisée. Il est idéal pour des applications avancées telles que les systèmes radar, les réseaux 5G et les communications par satellite.
Avantages :
- Constante diélectrique faible et faible perte de signal, ce qui le rend idéal pour les applications haute fréquence et haute vitesse.
- Haute conductivité thermique, permettant une meilleure dissipation de la chaleur.
- Stabilité supérieure dans des environnements à forte humidité ou avec des fluctuations de température.
Inconvénients :
- Plus coûteux que le FR4, ce qui peut augmenter considérablement le coût de production.
- Peut être plus difficile à traiter, nécessitant des équipements et des techniques spécialisées.
Polyimide
Aperçu : Le polyimide est un matériau flexible à haute température connu pour ses excellentes propriétés thermiques et mécaniques. Il est souvent utilisé dans des applications nécessitant à la fois flexibilité et durabilité, telles que les PCB flexibles et rigides-flexibles.
Applications : Le polyimide est couramment utilisé dans l’aérospatiale, le militaire et les applications médicales où les cartes doivent résister à des environnements extrêmes ou à des flexions fréquentes.
Avantages :
- Excellente stabilité thermique et peut résister à des températures extrêmes.
- Grande flexibilité mécanique, ce qui le rend idéal pour les PCBs flexibles et les applications nécessitant mouvement ou flexion.
- Bonnes propriétés d’isolation électrique et résistance chimique.
Inconvénients :
- Coût plus élevé que le FR4, en particulier dans les conceptions de PCB rigides-flexibles.
- Légèrement plus complexe à fabriquer, nécessitant des techniques avancées pour la production.
PTFE (Polytétrafluoroéthylène)
Aperçu : Le PTFE est un matériau fluoropolymère synthétique connu pour sa faible constante diélectrique et ses capacités de haute fréquence. Il est souvent utilisé dans les applications de micro-ondes et RF en raison de ses excellentes propriétés électriques.
Applications : Le PTFE est utilisé dans les systèmes de communication à haute fréquence, les antennes et les dispositifs RF où la moindre perte de signal et les interférences sont critiques.
Avantages :
- Constante diélectrique extrêmement faible, le rendant parfait pour les circuits à haute fréquence.
- Chimiquement inerte et résistant à des températures élevées et à des environnements difficiles.
- Excellent pour minimiser la perte de signal dans des applications sensibles RF et micro-ondes.
Inconvénients :
- Difficile à traiter et à fabriquer, nécessitant des techniques et des outils spécialisés.
L’Impact du Choix des Matériaux sur la Performance, le Coût et la Durabilité
Performance
Intégrité des Signaux : Le choix du matériau a un impact direct sur la performance électrique du PCB. Les applications haute fréquence, telles que les circuits RF et micro-ondes, nécessitent des matériaux avec de faibles constantes diélectriques et de faibles pertes de signal (comme Rogers ou PTFE). Pour les applications générales où les signaux à haute fréquence ne posent pas de problème, le FR4 offre une option rentable tout en fournissant une bonne intégrité des signaux pour des fréquences faibles à modérées.
Gestion Thermique : Des matériaux tels que Rogers et le polyimide ont une meilleure conductivité thermique que le FR4, ce qui les rend plus adaptés aux applications avec des exigences de puissance élevées ou celles qui génèrent une chaleur significative. Choisir un matériau avec de meilleures propriétés de dissipation de chaleur garantit une durée de vie plus longue des composants et réduit le risque de dommages thermiques.
Propriétés Mécaniques : Les applications nécessitant de la flexibilité, comme dans l’aérospatiale ou les dispositifs médicaux, profitent de matériaux comme le polyimide, qui offrent flexibilité mécanique et durabilité dans des environnements dynamiques. Les matériaux plus rigides comme le FR4 conviennent mieux aux conceptions rigides où la flexibilité mécanique n’est pas nécessaire.
Coût
Coût des Matériaux : Le FR4 est généralement le matériau le plus abordable et est largement disponible, ce qui en fait le choix privilégié pour de nombreuses applications générales. Les matériaux comme Rogers, le polyimide et le PTFE sont des options plus coûteuses, généralement utilisés dans des applications spécialisées ou hautes performances où les avantages d’une meilleure intégrité des signaux, d’une gestion thermique ou de flexibilité justifient les coûts plus élevés.
Complexité de Fabrication : Certains matériaux, comme le PTFE et Rogers, nécessitent des processus de fabrication spécialisés, ce qui peut ajouter au coût de production total. Par exemple, les matériaux Rogers peuvent nécessiter un équipement plus avancé pour le stratification et le forage, rendant leur production plus coûteuse que celle des plaques FR4. De plus, des empilements complexes et des conceptions avec plusieurs couches à haute fréquence peuvent également augmenter les coûts en raison de la précision requise.
Durabilité
Résistance Thermique et Chimique : Les matériaux comme le polyimide et le PTFE offrent une résistance supérieure à des températures élevées et à des environnements difficiles par rapport au FR4, les rendant plus durables dans les applications où le stress environnemental est une préoccupation. Par exemple, dans les applications aéronautiques ou industrielles, les matériaux capables de résister à des températures extrêmes, à l’humidité ou à l’exposition chimique sont essentiels pour assurer la fiabilité à long terme du PCB.
Résistance Mécanique : Pour les applications requérant des performances mécaniques robustes, comme dans l’électronique automobile ou industrielle, des matériaux comme le FR4 et le polyimide fournissent la rigidité ou la flexibilité nécessaires. Le polyimide, en particulier, est bien adapté aux circuits flexibles qui doivent se plier sans perdre leur intégrité structurelle.
Conclusion
Le choix des matériaux est l’une des décisions les plus critiques dans la conception de PCB à 8 couches, car il impacte directement les performances, les coûts et la durabilité du produit final. Bien que le FR4 soit un choix rentable pour les applications générales, des matériaux plus avancés comme Rogers, le polyimide et le PTFE sont idéaux pour des applications haute fréquence, haute thermique et flexibles. Comprendre les exigences spécifiques de votre projet vous aidera à choisir le bon matériau, équilibrant les besoins de performance avec le coût et la fabricabilité.
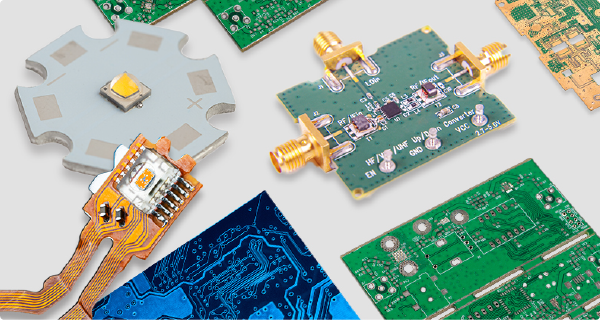
Chapitre 5

Applications
Les PCBs à 8 couches jouent un rôle clé dans de nombreux systèmes électroniques avancés, surtout dans les secteurs où les performances élevées, l’intégrité des signaux et l’efficacité de l’espace sont importants. Les couches supplémentaires offrent plus de flexibilité dans la conception de circuits, ce qui signifie que vous pouvez réaliser des choses plus complexes, optimiser la gestion thermique et améliorer l’intégrité des signaux. Voici quelques-uns des endroits les plus courants et importants où vous utiliseriez un PCB à 8 couches.
1. Communications à Haute Vitesse
Aperçu : L’industrie des télécommunications est l’un des principaux utilisateurs des PCB à 8 couches en raison de la demande de transmission de données à haute vitesse et de l’intégrité des signaux. À mesure que les taux de données augmentent et que les dispositifs deviennent plus complexes, maintenir l’intégrité des signaux sur de longues distances et à haute vitesse devient crucial. Les couches supplémentaires dans un PCB à 8 couches permettent un meilleur routage des signaux, un meilleur mise à la terre et une minimisation des interférences électromagnétiques (EMI), tous essentiels pour les systèmes de communication.
Utilisations clés :
Équipements Réseau : Des dispositifs comme les routeurs, les commutateurs et les modems s’appuient sur des PCB à 8 couches pour gérer de grandes quantités de données à haute vitesse. Les couches supplémentaires aident à séparer les chemins de signaux, réduisant ainsi le crosstalk et fournissant une distribution stable de l’énergie, garantissant des performances fiables dans les environnements de réseau.
Technologie 5G : Alors que le monde se tourne vers la 5G, le besoin de PCBs pouvant supporter des signaux haute fréquence et maintenir l’intégrité des signaux augmente. Les PCB à 8 couches jouent un rôle important dans l’infrastructure derrière la technologie 5G, des stations de base aux dispositifs portables.
Fibres Optiques : Les systèmes de communication par fibre optique, qui nécessitent une latence extrêmement faible et un traitement de données à haute vitesse, bénéficient de l’intégrité des signaux et de la gestion efficace de l’énergie offertes par les PCBs à 8 couches.
Avantages pour les Communications à Haute Vitesse :
- Réduction des interférences de signaux et du crosstalk grâce à une meilleure séparation des couches.
- Amélioration de l’intégrité des signaux à haute fréquence, essentielle pour une transmission rapide des données.
- Plus de flexibilité de routage pour intégrer des circuits complexes dans les systèmes de communication.
2. Électronique Automobile
Aperçu : L’industrie automobile s’appuie de plus en plus sur des systèmes électroniques pour gérer tout, des unités de contrôle du moteur (ECUs) aux systèmes d’assistance avancée au conducteur (ADAS). Les PCBs à 8 couches sont essentiels pour gérer la complexité des véhicules modernes, car ils permettent une densité de composants plus élevée et des circuits plus sophistiqués dans un espace compact. L’électronique automobile doit également résister à des conditions environnementales difficiles, y compris des températures extrêmes et des vibrations, ce qui rend la durabilité d’un PCB à 8 couches critique.
Utilisations clés :
Unités de Contrôle du Moteur (ECUs) : Les ECUs sont responsables de la gestion de diverses fonctions du moteur d’un véhicule, telles que l’injection de carburant, le timing de l’allumage et le contrôle des émissions. Ces systèmes nécessitent des PCBs fiables avec plusieurs couches pour gérer les données complexes et les systèmes de contrôle qui garantissent l’efficacité et les performances du moteur.
Systèmes d’Assistance Avancée au Conducteur (ADAS) : Les ADAS incluent des fonctionnalités comme les avertissements de départ de voie, l’évitement de collision et le régulateur de vitesse adaptatif. Ces systèmes dépendent de nombreux capteurs, caméras et technologies radar, tous nécessitant des PCBs haute performance pour traiter les données rapidement et avec précision.
Systèmes Infodivertissement dans le Véhicule (IVI) : Les systèmes infodivertissement allient les fonctions audio, vidéo et de navigation. L’intégration de ces diverses caractéristiques nécessite des PCBs capables de gérer le transfert de données à haute vitesse et de fournir une distribution d’énergie stable afin d’assurer un fonctionnement fluide.
Avantages pour l’Électronique Automobile :
- Durabilité et fiabilité accrues pour résister aux environnements automobiles difficiles.
- Prise en charge de circuits complexes à haute densité requis par les systèmes automobiles modernes.
- Amélioration de la gestion thermique, essentielle pour prévenir la surchauffe dans l’électronique automobile.
3. Dispositifs Médicaux
Aperçu : Les dispositifs médicaux nécessitent souvent des PCBs qui peuvent offrir une grande précision, fiabilité et longévité. De nombreuses applications médicales impliquent un traitement de données sensibles, où même la moindre interférence de signal pourrait affecter les performances. Les PCBs à 8 couches sont largement utilisés dans l’équipement médical pour leur capacité à gérer des circuits complexes tout en maintenant l’intégrité des signaux et en garantissant une fiabilité à long terme.
Utilisations clés :
Systèmes d’Imagerie Diagnostique : Les dispositifs médicaux tels que les IRM, les scanners CT et les appareils à ultrasons dépendent de circuits complexes nécessitant une transmission précise des signaux. La conception multicouche des PCBs à 8 couches aide à garantir que ces signaux sont clairs et sans interférence, ce qui est crucial pour des diagnostics précis.
Dispositifs Médicaux Portables : Des dispositifs portables tels que les moniteurs cardiaques, les pompes à insuline et les outils de diagnostic portables nécessitent des PCBs compacts et légers avec une haute fiabilité. Les PCBs à 8 couches permettent d’inclure plus de composants dans un format réduit, ce qui les rend idéales pour les applications médicales portables.
Équipement Chirurgical : Les outils chirurgicaux de haute précision impliquent souvent des composants électroniques qui aident les chirurgiens pendant les procédures. Ces dispositifs doivent être extrêmement fiables, car toute défaillance pourrait avoir des conséquences graves. Les PCBs à 8 couches fournissent la complexité et la durabilité requises pour un tel équipement à enjeux élevés.
Avantages pour les Dispositifs Médicaux :
- Haute fiabilité et durabilité pour les applications vitales.
- Conception compacte permettant une intégration dans des dispositifs médicaux portables ou peu invasifs.
- Réduction de l’interférence de signal, essentielle pour des outils de diagnostic et de surveillance précis.
4. Contrôle Industriel
Aperçu : Les systèmes de contrôle industriel, tels que ceux utilisés dans l’automatisation, la robotique et la gestion de l’énergie, nécessitent des PCBs capables de gérer des charges puissantes, des algorithmes de contrôle complexes et des environnements de fonctionnement difficiles. Les PCBs à 8 couches offrent le nombre de couches nécessaires pour accueillir le routage extensif et la gestion de l’énergie requise par l’électronique industrielle moderne. De plus, leurs capacités améliorées de gestion thermique les rendent bien adaptés aux applications haute puissance.
Utilisations clés :
Systèmes d’Automatisation : Les usines et les installations industrielles s’appuient sur des systèmes d’automatisation pour contrôler les processus et les machines. Ces systèmes doivent traiter de grandes quantités de données en temps réel et fonctionnent souvent dans des environnements difficiles. Les PCBs à 8 couches fournissent la durabilité, l’intégrité des signaux et la gestion de l’énergie nécessaires pour de telles applications.
Robotique : Les robots utilisés dans la fabrication, la santé et la recherche nécessitent des systèmes de contrôle complexes pour gérer le mouvement, les capteurs et le traitement des données. Les PCBs à 8 couches aident à intégrer plusieurs sous-systèmes tout en maintenant l’intégrité des signaux nécessaire pour un fonctionnement précis.
Alimentations Électriques : Les alimentations électriques industrielles nécessitent des PCBs capables de gérer des courants et des tensions élevés tout en garantissant une dissipation efficace de la chaleur. Les couches supplémentaires dans un PCB à 8 couches permettent une meilleure distribution des plans d’alimentation et aident à gérer efficacement les charges thermiques.
Avantages pour le Contrôle Industriel :
- Amélioration de la distribution d’énergie et gestion thermique pour des applications à courant élevé.
- Capacité à soutenir des conceptions de circuits complexes à haute densité dans les systèmes industriels.
- Robustesse et durabilité pour résister à des environnements industriels difficiles.
5. Autres Applications
Les PCBs à 8 couches se trouvent également dans plusieurs autres domaines avancés :
Électroniques Aéronautiques : Dans l’aéronautique, le poids et l’espace sont des facteurs cruciaux. Les PCBs à 8 couches permettent une haute densité de composants dans un design compact tout en garantissant une fiabilité élevée dans des conditions extrêmes.
Électroniques Grand Public : Les appareils électroniques grand public haut de gamme comme les smartphones, les tablettes et les consoles de jeux nécessitent des PCBs avec des capacités de routage avancées et la capacité de gérer des données à haute vitesse. Les PCBs à 8 couches répondent à ces exigences tout en gardant les appareils compacts et légers.
Technologie Portable : À mesure que les dispositifs portables deviennent plus avancés, ils nécessitent des PCBs pouvant s’adapter à des formats petits et flexibles. Les PCBs à 8 couches permettent une plus grande fonctionnalité dans un espace réduit, les rendant idéaux pour des applications portables telles que les montres connectées et les traqueurs de fitness.
Conclusion
Les PCBs à 8 couches sont une part importante de la manière dont nous concevons et fabriquons des dispositifs électroniques modernes dans divers secteurs. Ils permettent de transférer les données rapidement, de réaliser des tâches complexes et de gérer l’énergie de manière efficace, ce qui est essentiel dans les domaines des telecom, de l’automobile, de la médecine, de l’industrie et plus encore. Que vous développiez la prochaine génération de réseaux 5G ou fabriquiez des dispositifs médicaux vitaux, les PCBs à 8 couches vous offrent la performance et la fiabilité nécessaires pour les applications les plus exigeantes.
Chapitre 6
Processus de Fabrication des PCB à 8 Couches
Le processus de fabrication des PCB à 8 couches est complexe et nécessite un contrôle précis à chaque étape pour garantir des performances élevées et une fiabilité optimale. Du design initial à l’assemblage final, chaque étape implique une planification, une exécution et des tests minutieux. Cette section fournit une répartition détaillée des étapes clés impliquées dans la fabrication d’un PCB à 8 couches, des défis communs rencontrés et des contrôles de qualité critiques qui garantissent que le produit fini répond aux normes de l’industrie.
Étape 1 : Conception et Mise en Page
La première étape du processus de fabrication est la conception du PCB à 8 couches, qui consiste à créer un schéma et à le traduire en une mise en page physique à l’aide d’un logiciel de conception de PCB. Le processus de conception inclut :
- Capture du schéma : Le design du circuit est capturé sous forme de schéma, représentant les connexions électriques entre les composants.
- Conception de la pile de couches : L’arrangement des 8 couches est déterminé, en optimisant le placement des couches de signal, d’alimentation et de terre pour l’intégrité des signaux et la distribution d’énergie.
- Routage : Les signaux sont routés entre les composants sur les différentes couches à l’aide de vias (interconnexions verticales), garantissant une interférence minimale et des chemins de signal optimisés.
- Conception pour la Fabricabilité (DFM) : La mise en page est optimisée pour répondre aux contraintes de fabrication, garantissant que le design peut être produit de manière fiable et rentable.
Au cours de la phase de conception, il est crucial de tenir compte de facteurs tels que la largeur des pistes, l’espacement et le placement des vias pour minimiser la perte de signal et s’assurer que le PCB final répond aux spécifications de performance.
Étape 2 : Sélection des Matériaux
Une fois le design finalisé, l’étape suivante consiste à sélectionner les matériaux qui seront utilisés pour le PCB à 8 couches. Le choix des matériaux est basé sur les exigences de l’application, y compris :
- Matériau de Substrat : Le matériau de base (souvent FR4, Rogers ou Polyimide) est choisi en fonction des facteurs tels que l’intégrité des signaux, la performance thermique et le coût.
- Épaisseur de Feuille de Cuivre : L’épaisseur des couches de cuivre est choisie pour gérer la capacité de transport de courant requise.
- Matériaux Pré-imprégnés et Cœur : Les matériaux pré-imprégnés (fibres de verre imprégnées de résine) et les matériaux de cœur sont utilisés pour lier les couches ensemble et fournir une isolation entre les couches conductrices.
L’étape de sélection des matériaux est cruciale pour atteindre les propriétés électriques, thermiques et mécaniques souhaitées du PCB.
Étape 3 : Préparation des Couches et Stratification
Avec le design et les matériaux sélectionnés, le processus de fabrication commence par la préparation des couches individuelles :
- Imagerie des Couches Internes : Une couche de photo-résine est appliquée sur le substrat plaqué cuivre, et le motif de circuit pour chaque couche est imprimé à l’aide de lumière UV. Ce processus crée les chemins qui transporteront les signaux électriques.
- Gravure : Après l’imagerie, le cuivre non désiré est gravé, ne laissant que les traces conçues sur la couche.
- Alignement des Couches : Chacune des 8 couches est soigneusement alignée à l’aide d’un système de registration optique pour s’assurer que les vias et les traces se connectent correctement à travers les couches.
- Stratification : Les couches sont ensuite empilées ensemble, avec des couches isolantes (pré-imprégnées) entre elles. L’empilement est placé dans une presse à stratification, où la chaleur et la pression sont appliquées pour lier les couches ensemble en un seul panneau solide.
Étape 4 : Perçage et Formation de Vias
Après la stratification des couches, l’étape suivante consiste à percer des trous pour créer des vias, qui relient les différentes couches du PCB :
- Perçage : Des perceuses de précision sont utilisées pour créer des trous à travers l’empilement, ciblant des points spécifiques où des connexions doivent être établies entre les couches. Ces trous peuvent aller des simples trous traversants à des microvias ou vias enfouis plus complexes.
- Placage : Après le perçage, les trous sont plaqués avec une fine couche de cuivre pour créer une connexion électrique entre les couches.
Cette étape est particulièrement difficile pour les PCBs à 8 couches en raison de la nécessité d’un alignement précis des vias et du risque d’endommager les couches internes pendant le perçage.
Étape 5 : Imagerie des Couches Externes et Placage
Une fois les vias formés, les couches extérieures du PCB sont imagées et gravées :
- Imagerie des Couches Externes : Une couche de photo-résine est appliquée sur les couches de cuivre les plus extérieures, et le motif de circuit est imprimé à l’aide de lumière UV. Les zones quitransporteront des signaux sont protégées, tandis que le reste estexposé à la gravure.
- Placage : Une couche de cuivre est électroplaquée sur les zones exposées, y compris les trous percés, pour créer les connexions nécessaires. Des couches supplémentaires d’étain ou de soudure peuvent être appliquées pour protéger les traces de cuivre et les vias pendant le processus de gravure final.
- Gravure : Le cuivre excédentaire est enlevé, laissant derrière lui les motifs de circuit souhaités sur les couches externes.
À ce stade, le PCB commence à prendre sa forme finale, avec toutes les connexions nécessaires en place.
Étape 6 : Application du Masque à Souder et Sérigraphie
Pour protéger le PCB et le préparer à l’assemblage des composants, les étapes suivantes sont réalisées :
- Application du Masque à Souder : Une couche de masque à souder est appliquée sur le PCB pour protéger les traces de cuivre de l’oxydation et prévenir les ponts de soudure lors de l’assemblage. Le masque à souder est généralement de couleur verte, mais d’autres couleurs comme le bleu, le rouge et le noir peuvent également être utilisées.
- Impression Sérigraphique : La couche de sérigraphie est appliquée pour ajouter du texte, des étiquettes de composants et des repères de référence sur le PCB, facilitant ainsi l’assemblage et le dépannage.
Les couches de masque à souder et de sérigraphie sont essentielles pour garantir que le PCB soit durable et facile à manipuler lors du processus d’assemblage.
Étape 7 : Tests Électriques
Avant l’assemblage, le PCB à 8 couches subit des tests rigoureux pour s’assurer qu’il répond aux spécifications de conception :
- Tests Électriques : Des systèmes de test automatisés vérifient la continuité (en s’assurant que toutes les connexions sont correctement établies) et l’isolement (en s’assurant qu’il n’y a pas de connexions ou de courts-circuits indésirables entre les différentes parties du circuit). Des tests par sonde volante ou des tests par lit de broches sont couramment utilisés.
- Tests d’Impédance : Pour les conceptions haute vitesse, les tests d’impédance garantissent que le PCB maintienne les valeurs d’impédance correctes entre les différentes couches, ce qui est essentiel pour l’intégrité des signaux.
Les tests sont une étape critique pour garantir que le PCB fonctionne correctement et répond aux normes de performance avant que les composants soient ajoutés.
Étape 8 : Assemblage
Une fois que le PCB a passé tous les tests, il passe à la phase d’assemblage, où les composants sont montés sur la carte :
- Technologie de Montage de Surface (SMT) : Les composants sont placés à la surface du PCB à l’aide de machines automatiques de prise et de placement. Les composants sont ensuite soudés en place à l’aide d’un four de refusion, qui fait fondre la soudure et crée une connexion sécurisée.
- Assemblage par Passage de Trou : Pour les composants nécessitant un montage par trou traversant, les pattes sont insérées dans les trous pré-percés et soudées, soit manuellement soit à l’aide de machines à souder à onde.
- Inspection : Le PCB assemblé subit une inspection visuelle, une inspection optique automatisée (AOI) et une inspection par rayons X pour garantir que tous les composants sont correctement placés et soudés.
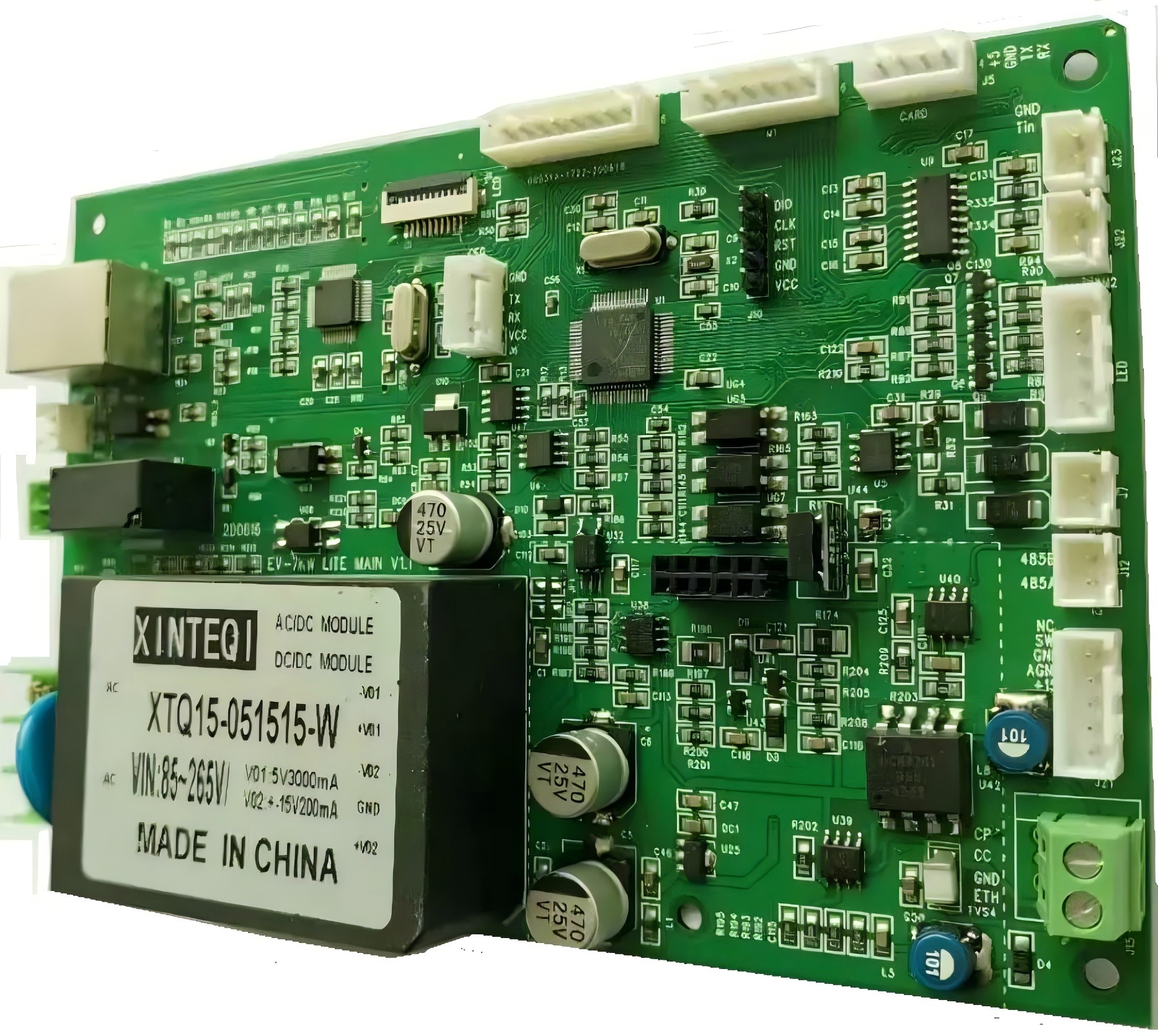
Chapitre 7
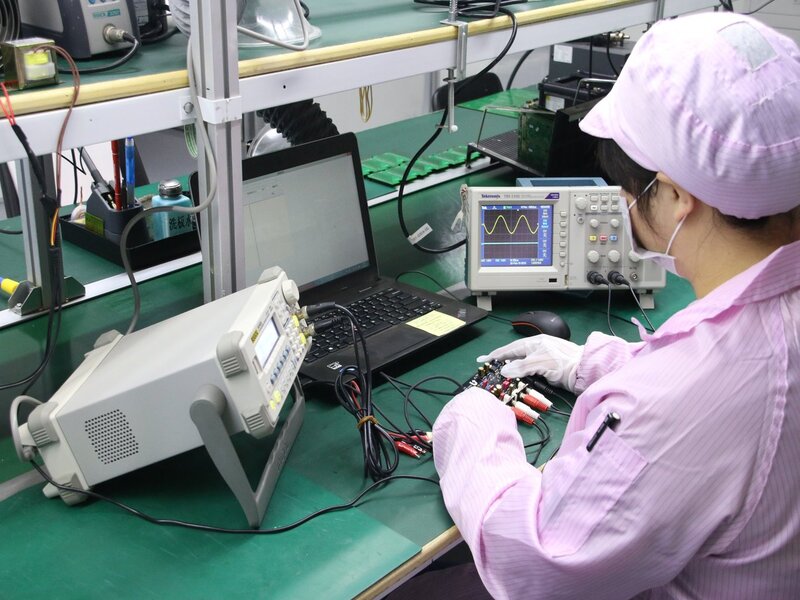
Facteurs de Coût dans la Production de PCB à 8 Couches
Le coût de production d’un PCB à 8 couches peut varier considérablement en fonction de plusieurs facteurs. Des matériaux utilisés à la complexité du design, chaque élément joue un rôle dans la détermination du prix final de la planche. Dans cette section, nous allons décomposer les principaux moteurs de coût dans la production de PCB à 8 couches et fournir des conseils pour réduire les coûts sans sacrifier la qualité.
Analyse des Facteurs Affectant le Coût
Matériaux
Matériau de Substrat : Le type de matériau de substrat utilisé dans un PCB à 8 couches a un impact majeur sur le coût. Les matériaux couramment utilisés comprennent le FR4, qui est relativement peu coûteux et largement disponible, et des stratifiés hautes performances comme Rogers ou Polyimide, qui sont nettement plus chers en raison de leurs propriétés électriques supérieures et de leur stabilité thermique. Le choix du matériau dépend des exigences de l’application, telles que l’intégrité du signal, la fréquence et les conditions environnementales.
Épaisseur du Cuivre : L’épaisseur des couches de cuivre affecte également le prix. Du cuivre plus épais est souvent requis pour les cartes qui doivent gérer des courants plus élevés ou fournir une meilleure dissipation de la chaleur, mais cela augmente les coûts des matériaux. Les couches de cuivre plus épaisses (par exemple, 2 oz/ft² ou plus) sont plus coûteuses que le standard de 1 oz/ft².
Finitions de Surface : Le type de finition de surface utilisée sur le PCB (tel que HASL, ENIG ou OSP) affecte à la fois les performances et le coût. Par exemple, l’ENIG (Nickel Électrolytique Immersion Or) offre une excellente résistance à la corrosion et est idéal pour les applications à haute fiabilité mais est plus coûteux que l’HASL (Nivellement de Soudure par Air Chaud).
Nombre de Couches
Nombre de Couches Plus Élevé Équivaut à des Coûts Plus Élevés : Chaque couche supplémentaire augmente la complexité du PCB, nécessitant plus de matériaux, des conceptions de pile plus complexes, et des étapes de fabrication supplémentaires. Un PCB à 8 couches est naturellement plus coûteux qu’un PCB à 4 ou 6 couches en raison des couches intérieures supplémentaires et du processus de stratification plus sophistiqué. Plus il y a de couches nécessaires, plus le coût de fabrication est élevé en raison de la main-d’œuvre accrue et de la nécessité d’équipements spécialisés pour aligner et stratifier correctement les couches.
Processus de Stratification : À mesure que le nombre de couches augmente, la complexité du processus de stratification augmente également. Dans un PCB à 8 couches, plusieurs couches de pré-imprégné (isolantes) et de cœur doivent être soigneusement alignées et stratifiées sous des conditions précises pour éviter des défauts comme le désalignement ou la délamination, ce qui augmente le coût.
Complexité du Design
- Routage Avancé et Types de Vias : Des stratégies de routage complexes telles que l’interconnexion à haute densité (HDI), les vias aveugles, les vias enfouis, et les microvias peuvent considérablement augmenter les coûts. Ces technologies nécessitent des équipements avancés et plus de temps pour les fabriquer. De plus, les designs avec des composants à pas fin oudes exigences de signal haute vitesse nécessitent un contrôle précis des largeurs de trace et des espacements, ce qui augmente également le coût de production.
Contrôle de l’Impédance : Les PCB avec impédance contrôlée, souvent requis pour des applications haute vitesse ou haute fréquence, sont plus chers à fabriquer car ils nécessitent des tolérances plus strictes pendant la fabrication et une attention particulière au design des traces et à la configuration de la pile.
Gestion Thermique : Certaines applications nécessitent des techniques avancées de gestion thermique, comme l’utilisation de vias thermiques, de dissipateurs de chaleur, ou de stratifiés spéciaux avec une conductivité thermique élevée. Ces mesures ajoutent de la complexité et du coût au processus de production.
Volume de Production
Prototype contre Production de Masse : Le volume de production impacte significativement le coût unitaire d’un PCB à 8 couches. Les petites séries ou les prototypes sont beaucoup plus coûteux par carte, car les coûts de configuration (comme la préparation des outils et la réalisation de tests) se répartissent sur moins d’unités. En revanche, la production de masse permet d’obtenir des économies d’échelle, réduisant le coût par unité.
Coûts de Configuration : Chaque série de production implique des coûts de configuration pour créer les outils nécessaires, configurer les équipements et préparer les matériaux. Pour les commandes à faible volume, ces coûts de configuration peuvent représenter une part importante du prix global. Des productions plus importantes permettent d’amortir ces coûts fixes sur de nombreuses unités, conduisant à un coût par carte inférieur.
Conseils pour Réduire les Coûts Sans Compromettre la Qualité
Choisissez le Matériau Adéquat pour l’Application
Optimisez la Sélection des Matériaux : Bien que des matériaux de haute performance comme Rogers ou Polyimide offrent d’excellentes propriétés électriques et thermiques, ils ne sont pas nécessaires pour toutes les applications. Si votre design ne requiert pas les caractéristiques avancées de ces matériaux, choisir un matériau moins coûteux comme le FR4 peut réduire les coûts sans affecter les performances de la carte pour des applications à fréquences plus basses ou moins exigeantes.
Évaluez l’Épaisseur du Cuivre : Utilisez l’épaisseur de cuivre standard de 1 oz/ft², sauf si votre design nécessite une gestion de courant plus élevée ou une meilleure dissipation thermique. N’augmentez l’épaisseur du cuivre que si c’est absolument nécessaire, car cela peut augmenter considérablement les coûts des matériaux.
Simplifiez le Design Quand C’est Possible
Minimisez les Types de Vias : Les vias aveugles, enfouis, et microvias sont essentiels pour certains designs à haute densité, mais peuvent être coûteux. Si votre design permet l’utilisation de vias standard traversants, optez pour ceux-ci à la place afin de réduire la complexité et le coût de fabrication.
Limitez le Contrôle de l’Impédance : Si votre application ne nécessite pas un contrôle strict de l’impédance, simplifier le design des traces peut réduire les coûts de production. Le contrôle de l’impédance nécessite des tolérances plus rigoureuses lors de la fabrication, ce qui augmente les coûts, donc ne l’utilisez que lorsque cela est nécessaire pour les designs à haute vitesse ou RF.
Optimisez l’Utilisation des Couches : Assurez-vous que votre design à 8 couches utilise efficacement les couches pour le routage des signaux, la distribution d’énergie et la mise à la terre. Évitez d’ajouter des couches inutiles, car chaque couche supplémentaire augmente les coûts à la fois matériels et de fabrication. En optimisant la conception de la pile et en tirant le meilleur parti des couches disponibles, vous pouvez atteindre une meilleure efficacité de coût.
Tirez Parti des Remises sur Volume
Planifiez pour la Production de Masse : Si possible, consolidez les commandes pour tirer parti des économies d’échelle offertes par des productions plus importantes. Commander en vrac réduit considérablement le coût par unité, car les coûts de configuration sont répartis sur un plus grand nombre de cartes. Si vous prévoyez avoir besoin de plus de pièces dans un avenir proche, il est souvent plus efficace de passer une plus grande commande en amont.
Prototype avec un Nombre de Couches Moins Élevé : Si vous êtes au stade du prototypage et que votre design ne requiert pas l’ensemble des fonctionnalités d’un PCB à 8 couches, envisagez d’utiliser une carte plus simple avec moins de couches pour les tests initiaux. Cela peut aider à réduire les coûts durant le développement tout en vous permettant de valider la fonctionnalité de base de votre design.
Travaillez avec des Fabricants de PCB Expérimentés
Choisissez un Fabricant avec une Expertise Prouvée : Travailler avec un fabricant spécialisé dans les PCB multicouches peut vous aider à éviter des erreurs coûteuses durant la production. Un fabricant expérimenté peut vous guider sur la façon d’optimiser votre design pour la fabricabilité (DFM), ce qui peut vous faire économiser du temps et de l’argent en identifiant des problèmes potentiels dès le début du processus.
Demandez des Avis sur la Fabricabilité (DFM) : Avant de finaliser votre design, demandez un avis DFM à votre fabricant. Cet avis aidera à identifier des défis de fabrication potentiels ou des inefficacités dans votre design, telles que des complexités inutiles, des caractéristiques difficiles à produire ou des tolérances trop strictes, tout en suggérant des améliorations pour rendre le processus de production plus rentable sans compromettre la qualité.
Réduisez le Nombre de Personnalisations
- Standardisez les Spécifications de la Carte : Évitez d’utiliser des caractéristiques hautement personnalisées, à moins que cela ne soit nécessaire. Par exemple, respectez des épaisseurs de carte, des tailles de trous, et des finitions de surface standard pour réduire les coûts. Les spécifications personnalisées nécessitent souvent des étapes de traitement supplémentaires et des matériaux spécialisés, augmentant à la fois le temps de fabrication et le coût.
Conclusion
Le coût de production d’un PCB à 8 couches est influencé par divers facteurs, y compris la sélection des matériaux, le nombre de couches, la complexité du design, et le volume de production. Bien que les PCB multicouches soient intrinsèquement plus coûteux en raison de leur complexité, il existe plusieurs stratégies que vous pouvez employer pour optimiser les coûts sans compromettre la qualité. En sélectionnant les matériaux appropriés pour votre application, en simplifiant votre design, en tirant parti des remises sur volume, et en collaborant avec un fabricant expérimenté, vous pouvez atteindre un équilibre entre efficacité de coût et haute performance dans votre production de PCB à 8 couches.
Chapitre 8
Considérations Clés pour la Conception de PCB à 8 Couches
Lorsque vous concevez un PCB à 8 couches, plusieurs facteurs critiques doivent être pris en compte pour garantir une performance optimale. Ceux-ci incluent l’intégrité du signal, la gestion thermique, la distribution d’énergie, et le placement approprié des vias et des stratégies de routage. Chacun de ces éléments joue un rôle crucial dans la détermination de l’efficacité, de la fiabilité et de la fonctionnalité de votre produit final.
Intégrité du Signal
L’intégrité du signal est particulièrement importante, notamment dans les applications à haute vitesse ou haute fréquence. Avec 8 couches à utiliser, vous pouvez consacrer des couches spécifiques à l’acheminement des signaux et les placer à côté des plans de masse, ce qui aide à réduire le crosstalk et l’interférence électromagnétique (EMI). En maintenant les longueurs de traces courtes et en contrôlant soigneusement l’impédance, vous pouvez maintenir l’intégrité du signal, en veillant à ce que vos signaux soient transmis avec précision et fiabilité à travers la carte.
Gestion Thermique
La gestion thermique est une autre considération clé lors de la conception d’un PCB à 8 couches. À mesure que vous entassez davantage de composants et de couches dans un espace plus réduit, votre carte génère plus de chaleur. Pour éviter la surchauffe et garantir une fiabilité à long terme, vous pouvez utiliser des techniques telles que les vias thermiques, qui aident à transférer la chaleur entre les couches, et des plans de cuivre plus épais pour une meilleure dissipation thermique. Gérer correctement la charge thermique garantit que votre carte fonctionne dans des plages de température sûres, même dans des applications à haute puissance.
Distribution de l’Énergie
Assurer une distribution d’énergie stable à travers tous les composants est crucial, en particulier dans des conceptions complexes à haute densité. En consacrant des couches spécifiques aux plans d’alimentation et de terre, les concepteurs peuvent créer un chemin à faible impédance pour la distribution d’énergie, réduisant ainsi les fluctuations de tension et le bruit. Le placement approprié des plans d’alimentation améliore également l’intégrité du signal et la gestion thermique, car les plans d’alimentation peuvent aider à protéger les signaux sensibles et distribuer la chaleur plus uniformément sur la carte.
Placement des Vias et Stratégies de Routage
Les vias, qui assurent des connexions électriques entre les couches, sont essentiels dans la conception de PCB à 8 couches. Un placement correct des vias est crucial pour maintenir l’intégrité du signal et assurer une distribution d’énergie efficace. Les concepteurs doivent placer des vias avec soin pour minimiser les réflexions et les pertes de signal, en particulier dans les conceptions haute vitesse. De plus, l’utilisation de vias aveugles ou enfouis peut aider à économiser de l’espace et à réduire l’interférence du signal, permettant un routage plus efficace des circuits complexes. Les stratégies de routage optimales, telles que le routage par paires différentielles pour les signaux haute vitesse et la planification soigneuse des chemins de traces, aident à éviter la dégradation du signal et garantissent un fonctionnement fiable.
Conclusion
En résumé, la conception d’un PCB à 8 couches nécessite une attention particulière à l’intégrité du signal, à la gestion thermique, à la distribution d’énergie, et au placement des vias. En abordant ces considérations clés, les concepteurs peuvent s’assurer que leurs cartes répondent aux exigences de performance tout en maintenant la fiabilité et l’efficacité, même dans des applications complexes et exigeantes.
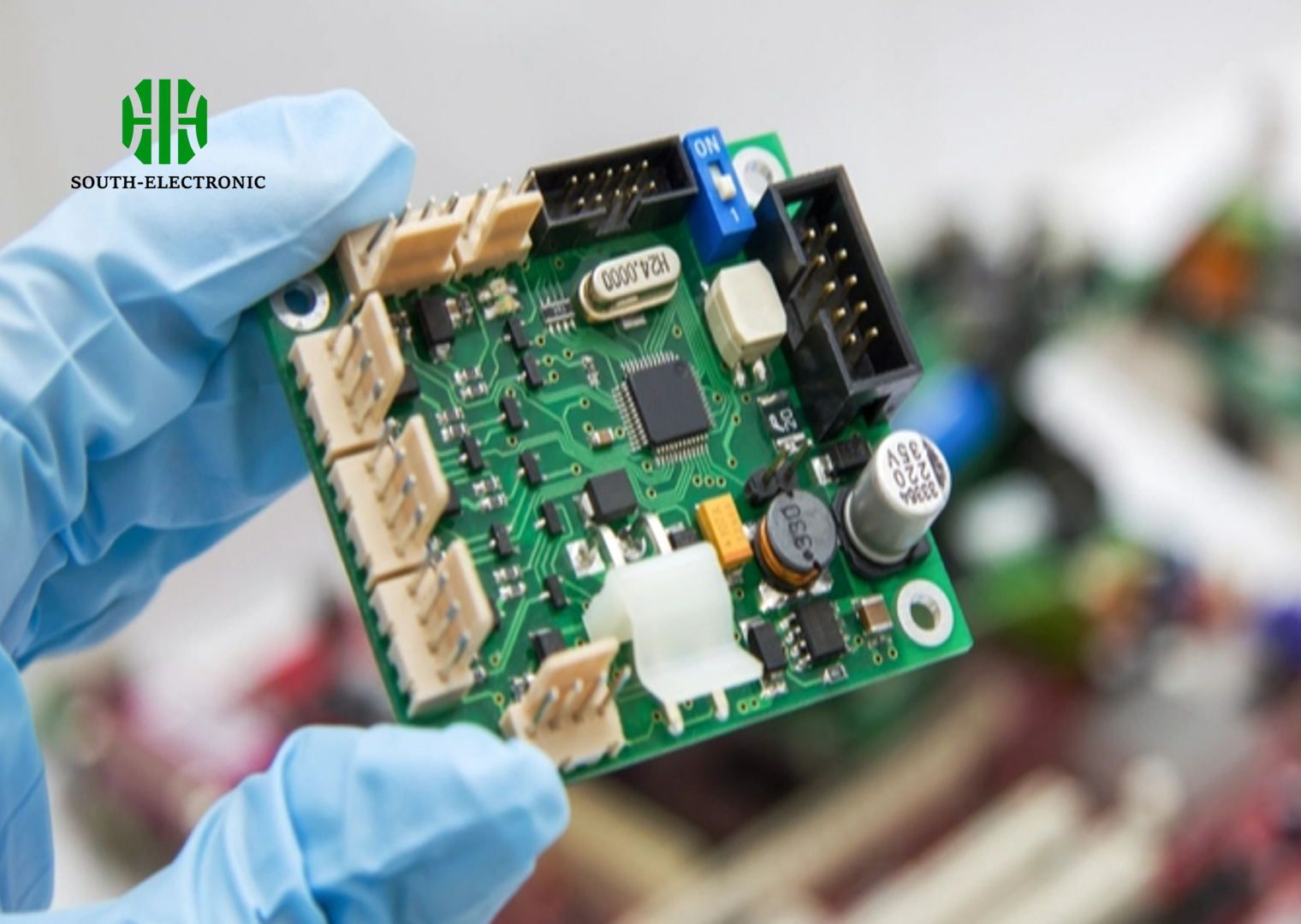
Chapitre 9

Tests et Assurance Qualité pour le PCB à 8 Couches
Assurer la qualité et la fiabilité des PCB à 8 couches nécessite un processus rigoureux de tests et d’assurance qualité. Plusieurs méthodes de test sont employées pour vérifier que le PCB respecte les spécifications de conception et fonctionne de manière fiable dans son application prévue.
Méthodes de Test Courantes
Tests Électriques : Cela inclut des tests de continuité et d’isolation pour s’assurer que toutes les connexions sont correctement effectuées et qu’il n’y a pas de courts-circuits ou de circuits ouverts. Ces tests sont souvent réalisés à l’aide d’équipements de test automatiques tels que des testeurs de sonde volante ou un lit de clous pour vérifier l’intégrité des voies électriques à travers les multiples couches.
Tests de Signal : Pour les PCB à haute vitesse et haute fréquence, les tests d’intégrité des signaux sont cruciaux. Cela implique de vérifier l’impédance des pistes, d’évaluer la qualité du signal et de vérifier qu’il n’y a pas de perte de signal excessive ou d’interférence. Les tests de signal garantissent que la carte peut gérer des taux de données élevés sans dégradation des performances.
Contrôles de Durabilité : Des tests environnementaux, tels que le cyclage thermique et les tests de stress mécanique, sont effectués pour s’assurer que le PCB peut résister aux conditions du monde réel. Ces tests évaluent la capacité du PCB à fonctionner sous des fluctuations de température, d’humidité et de stress mécanique, garantissant une fiabilité à long terme.
Importance des Certifications
Les certifications comme UL, CE, et ISO sont vitales pour établir la qualité et la sécurité des PCB à 8 couches :
Certification UL (Underwriters Laboratories) : Assure que le PCB respecte des normes de sécurité spécifiques, notamment en matière d’inflammabilité et de performance électrique, ce qui est essentiel pour les applications où la sécurité est une priorité.
Marquage CE : Indique que le PCB est conforme aux normes de santé, de sécurité et environnementales requises pour les produits vendus dans l’Espace Économique Européen (EEE), garantissant que la carte répond aux exigences réglementaires strictes.
Certifications ISO (Organisation Internationale de Normalisation) : Comme ISO 9001, démontrent que le fabricant suit des systèmes de gestion de la qualité, assurant une qualité de production constante et le respect des normes industrielles.
Conclusion
Les tests et l’assurance qualité sont essentiels pour garantir que les PCB à 8 couches sont à la fois fiables et sûrs pour une utilisation dans des applications exigeantes. Les tests électriques, les contrôles d’intégrité des signaux et les évaluations de durabilité garantissent que les cartes fonctionnent comme prévu, tandis que les certifications comme UL, CE et ISO garantissent qu’elles répondent aux normes industrielles reconnues en matière de performance et de sécurité.
Chapitre 10
Choisir le Bon Fournisseur
Sélectionner le bon fournisseur pour vos besoins en PCB à 8 couches est essentiel pour garantir une production de haute qualité, des délais de livraison respectés et un excellent service client. Plusieurs facteurs doivent être pris en considération lors de l’évaluation des fournisseurs potentiels.
Facteurs Clés à Considérer
Expérience : L’expérience du fournisseur dans la production de PCB à 8 couches et d’autres PCB multicouches est cruciale. Un fournisseur ayant un solide parcours dans la fabrication de cartes complexes et performantes est plus susceptible de livrer des produits fiables. Recherchez un fournisseur ayant une historique prouvée dans des secteurs tels que les télécommunications, l’automobile et les dispositifs médicaux, où les PCB à 8 couches sont couramment utilisés.
Certifications : Assurez-vous que le fournisseur possède des certifications clés de l’industrie, telles que UL, ISO9001 et IATF16949 (pour les applications automobiles). Ces certifications indiquent que le fournisseur respecte des normes strictes de contrôle qualité et de sécurité. Les certifications telles que CE sont également importantes si votre produit est destiné au marché européen.
Support Client : Un support client réactif et compétent est essentiel, surtout lors de la gestion de conceptions de PCB complexes. Choisissez un fournisseur qui offre une communication claire, des mises à jour en temps utile sur l’état de production et un support après-vente pour résoudre rapidement tout problème potentiel.
Vitesse de Livraison : La capacité à respecter des délais serrés est souvent cruciale dans le développement de produit. Évaluez la capacité de production et le parcours du fournisseur en matière de livraison ponctuelle. Les fournisseurs qui offrent des services de prototypage rapide ou des options de production accélérées peuvent être particulièrement précieux lors des premières étapes du développement du produit.
Comment Évaluer la Qualité et la Fiabilité d’un Fournisseur
Demander des Échantillons ou des Études de Cas : Un fournisseur fiable devrait être en mesure de fournir des exemples de travaux précédents, soit par des échantillons, soit par des études de cas de projets similaires de PCB à 8 couches. Cela vous donnera une idée de leurs capacités de production et de la qualité de leur rendement.
Vérifier les Avis et Références : Recherchez des avis ou des témoignages d’autres clients qui ont travaillé avec le fournisseur. Des retours positifs de clients dans votre secteur sont un indicateur fort de la fiabilité et de la qualité du fournisseur.
Effectuer un Audit de l’Usine : Si possible, visitez l’installation du fournisseur ou demandez une visite virtuelle pour évaluer ses processus de fabrication, son équipement et ses procédures de contrôle qualité. Une usine bien entretenue et correctement équipée est un bon signe que le fournisseur peut livrer des PCB de haute qualité.
Conclusion
Lors de la sélection d’un fournisseur pour des PCB à 8 couches, il est essentiel de prendre en compte des facteurs tels que l’expérience, les certifications, le support client et la vitesse de livraison. L’évaluation de ces éléments et la révision des échantillons ou des références vous aideront à trouver un fournisseur qui répond à vos normes de qualité et à vos délais de projet, garantissant un partenariat réussi et un produit final performant.
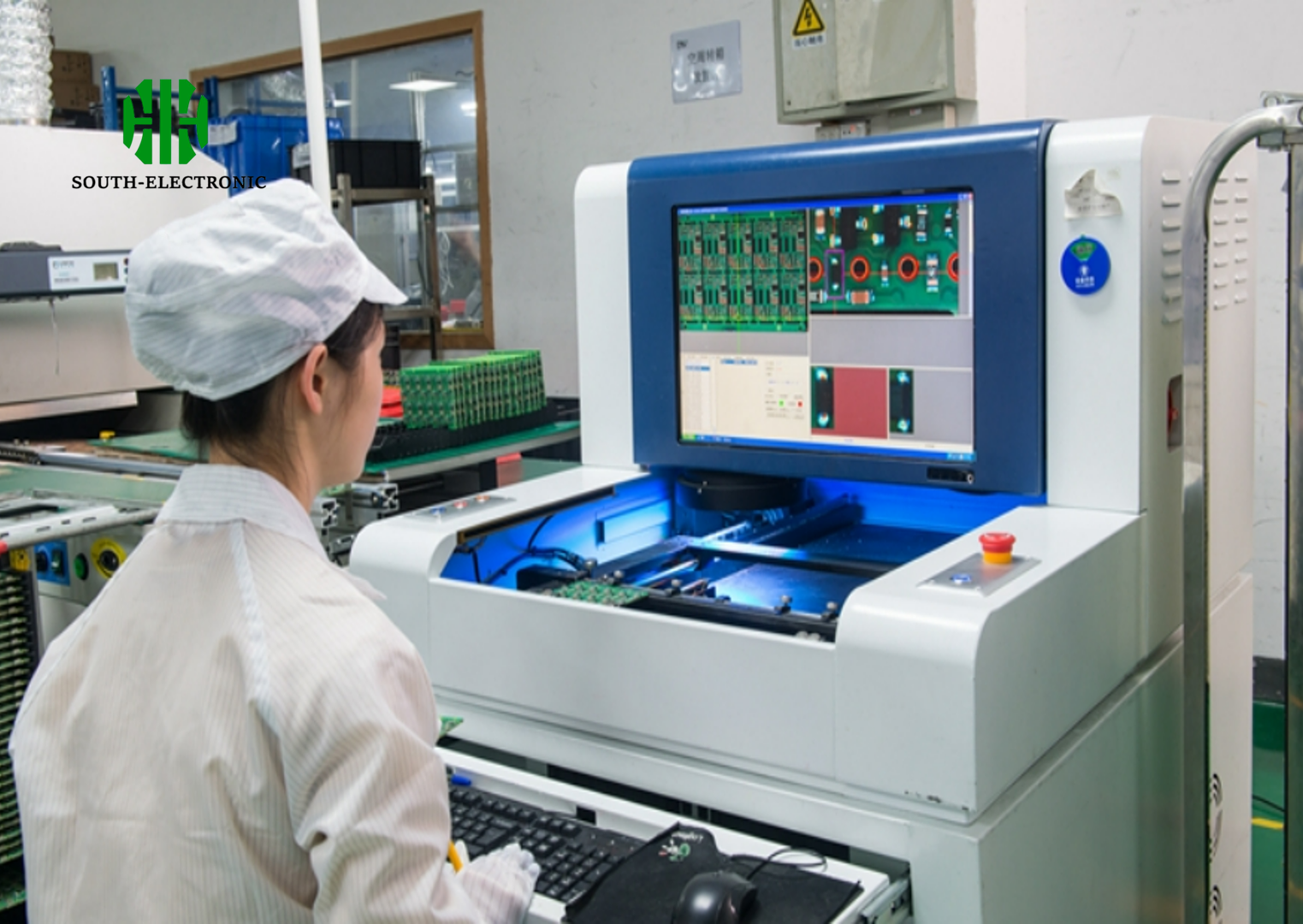
Contactez-Nous
Où Sommes-Nous ?
Parc Industriel, No. 438 Route Donghuan, No. 438, Shajing Donghuan Road, District Bao'an, Shenzhen, Guangdong, Chine
4ème étage, Bâtiment Zhihui Créatif, No. 2005 Route Xihuan, Shajing, District Baoan, Shenzhen, Chine
CHAMBRE A1-13, ÉTAGE 3, CENTRE INDUSTRIEL YEE LIM, 2-28 RUE KWAI LOK, KWAI CHUNG HK
service@southelectronicpcb.com
Téléphone : +86 400 878 3488
Envoyez-nous un message
Plus vous remplissez de détails, plus nous pourrons avancer rapidement à l’étape suivante.
