Fournisseur de circuits imprimés à noyau en cuivre
South-Electronic
Optez pour South-Electronic pour la meilleure qualité, fiabilité et valeur dans vos besoins en circuits imprimés. Vous constaterez la différence avec nos services complets de circuits imprimés à noyau en cuivre – de la conception à la production, nous nous assurons que vous obteniez précision, durabilité et conformité avec les normes industrielles les plus strictes.
Votre fournisseur de confiance pour les circuits imprimés à noyau en cuivre
Bienvenue chez South-Electronic ! Nous sommes votre source incontournable pour des circuits imprimés à noyau en cuivre de haute qualité, connus pour leur excellente dissipation thermique et leurs performances robustes.
Nos circuits imprimés à noyau en cuivre sont conçus pour durer, ce qui les rend parfaits pour les applications haute puissance dans des secteurs exigeants. Nous proposons une variété de configurations, y compris des cartes à 2 couches, à 4 couches et même des cartes multicouches plus complexes, toutes conçues pour répondre à vos besoins électroniques spécifiques. Que vous cherchiez à améliorer la fonctionnalité des électroniques de puissance ou que vous ayez besoin de cartes haute performance pour des applications automobiles, nos circuits imprimés à noyau en cuivre sont éprouvés pour offrir fiabilité et précision. Comptez sur South-Electronic pour des produits constants et de haute qualité pour vos projets technologiques de pointe. Nos circuits imprimés à noyau en cuivre amélioreront la performance de vos appareils avec une gestion thermique exceptionnelle et une durabilité accrue. Partenariat avec nous pour atteindre l’innovation et le succès dans votre domaine.
Pourquoi choisir South-Electronic ?
-
Solutions personnalisées
Votre projet est unique, tout comme vos besoins.
Chez South-Electronic, nous le comprenons, c’est pourquoi nous proposons des solutions de circuits imprimés à noyau en cuivre sur mesure, spécifiquement conçues pour vous. Vous obtiendrez un produit qui répond exactement à vos spécifications, sans compromis. -
Assurance qualité
Vous vous souciez de la qualité, et nous aussi.
Avec la certification ISO9001 et des tests rigoureux tout au long du processus de production, vous pouvez être sûr que nos circuits imprimés à noyau en cuivre offriront la fiabilité et la longévité que votre projet exige. -
Commandes flexibles
Que vous ayez besoin d'un prototype ou d'une grande série de production, vous êtes maître du jeu.
Notre MOQ flexible vous permet de commander aussi peu qu'une pièce, vous permettant ainsi d'obtenir exactement ce dont vous avez besoin, quand vous en avez besoin, et à un prix qui correspond à la taille et au budget de votre projet. -
Professionnalisme et efficacité
Vous bénéficierez de l'expérience approfondie que notre équipe apporte.
Avec des années de connaissances dans l'industrie, nous sommes là pour résoudre vos défis les plus difficiles. Du design à la livraison, nous vous guiderons à chaque étape du processus. -
Capacités de production
Un délai rapide pour vous permettre de respecter vos échéances.
C’est pourquoi nous avons optimisé nos lignes de production pour vous garantir des circuits imprimés à noyau en cuivre rapidement, sans sacrifier la qualité. Vous recevrez ce dont vous avez besoin au moment où vous en avez besoin, permettant à votre projet de rester sur la bonne voie. -
Capacités de production
Vous bénéficierez d'une solution clé en main de notre part – de l'approvisionnement des composants à l'assemblage final.
Et que ce soit pour le support technique, les mises à jour de produits ou une communication en temps opportun, vous pouvez toujours compter sur nous pour être réactifs à vos besoins.
Projets connexes que nous avons réalisés
Avis des clients
Questions courantes
Questions les plus populaires
South-Electronic propose une variété de circuits imprimés à noyau en cuivre, y compris des circuits imprimés à un seul côté et multicouches conçus pour des applications à haute puissance telles que l'éclairage LED, l'électronique automobile, et les dispositifs de dissipation thermique.
South-Electronic offre des services complets et clé en main pour les circuits imprimés, y compris le prototypage, la fabrication de circuits imprimés, l'assemblage et l'approvisionnement en composants, couvrant l'ensemble du processus de la conception à la production.
South-Electronic suit un système de contrôle qualité strict, respectant les normes ISO 9001 et IPC pour garantir que chaque circuit imprimé respecte des exigences de qualité élevées. Des tests fonctionnels complets et des contrôles qualité sont effectués avant l'expédition.
Oui, South-Electronic propose une large gamme d'options de personnalisation, permettant aux clients d'ajuster l'épaisseur des cartes, le poids du cuivre, le nombre de couches et les matériaux spéciaux pour répondre aux exigences spécifiques du projet.
En général, le délai de production de South-Electronic varie de 7 à 15 jours ouvrés, en fonction de la complexité et de la taille de la commande. Des services accélérés sont également disponibles pour les projets urgents.
Envoyez-nous un message
Le guide complet des circuits imprimés à noyau en cuivre
Contenu
Chapitre 1
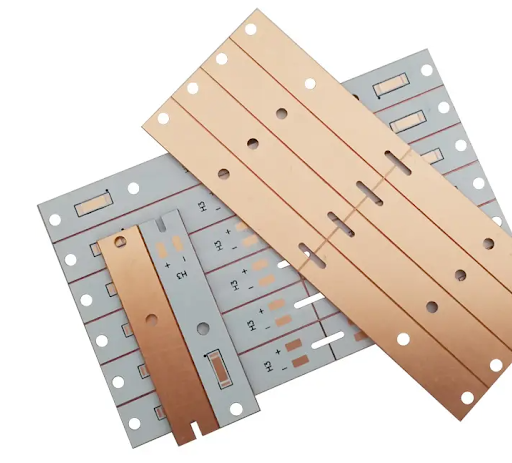
Introduction aux circuits imprimés à noyau en cuivre
Les circuits imprimés à noyau en cuivre, également connus sous le nom de circuits imprimés à base de cuivre, sont un type spécialisé de circuit imprimé qui utilise un substrat en cuivre pour fournir une meilleure conductivité thermique et des performances électriques améliorées. Contrairement aux circuits imprimés traditionnels qui utilisent de la fibre de verre ou d’autres matériaux non métalliques, les circuits imprimés à noyau en cuivre sont conçus pour gérer efficacement le dissipation thermique, ce qui les rend idéaux pour des applications haute puissance.
Avec l’évolution continue de l’industrie de l’électronique, il existe une demande croissante pour des circuits imprimés capables de gérer des densités de puissance plus élevées et des défis de gestion thermique. Les circuits imprimés à noyau en cuivre sont de plus en plus utilisés dans des applications telles que l’éclairage LED, l’électronique automobile et les alimentations électriques, où le dissipation thermique est essentielle pour maintenir les performances et prolonger la durée de vie des composants.
Les principaux avantages des circuits imprimés à noyau en cuivre par rapport aux circuits imprimés traditionnels incluent une meilleure gestion thermique, une plus grande durabilité et la capacité de supporter des courants plus élevés. Ces avantages font des circuits imprimés à noyau en cuivre le choix préféré pour les industries nécessitant des cartes de circuits fiables et haute performance capables de gérer des conditions d’exploitation exigeantes.
En incorporant du cuivre dans la conception du circuit imprimé, les fabricants peuvent obtenir une meilleure répartition de la chaleur, réduire les points chauds et améliorer la fiabilité globale du système, en particulier dans les environnements à haute fréquence et à courant élevé.
Chapitre 2
Qu'est-ce qu'un circuit imprimé à noyau en cuivre ?
Un circuit imprimé à noyau en cuivre est un type de circuit imprimé qui intègre un substrat en cuivre pour améliorer la dissipation thermique et améliorer les performances électriques globales de la carte. Ces circuits imprimés sont constitués d’un noyau en cuivre solide sandwiché entre des couches de matériau diélectrique et des couches de cuivre conducteur. Le noyau en cuivre sert à la fois de conducteur thermique et de fondation structurelle, offrant des capacités exceptionnelles de transfert de chaleur par rapport aux circuits imprimés traditionnels.
Structure d’un circuit imprimé à noyau en cuivre
La structure typique d’un circuit imprimé à noyau en cuivre comprend :
- Couche conductrice supérieure : C’est ici que les composants électroniques sont montés et connectés par des pistes en cuivre.
- Couche diélectrique : Située entre la couche conductrice supérieure et le noyau en cuivre, cette couche fournit une isolation électrique tout en permettant à la chaleur de passer efficacement.
- Noyau en cuivre : La couche centrale en cuivre agit comme un dissipateur thermique, absorbant et dissipant la chaleur générée par les composants haute puissance.
- Couche conductrice inférieure : Facultative dans certains designs, cette couche peut être utilisée pour la mise à la terre ou pour une dissipation thermique supplémentaire.
Différences entre les circuits imprimés à noyau en cuivre et les autres circuits imprimés à noyau métallique
Bien que les circuits imprimés à noyau en cuivre partagent des similitudes avec les autres circuits imprimés à noyau métallique (MCPCBs) tels que les circuits à noyau en aluminium ou en acier, il existe des différences distinctes :
- Conductivité thermique : Le cuivre a une conductivité thermique beaucoup plus élevée que l’aluminium ou l’acier, ce qui le rend plus efficace pour la gestion de la chaleur dans des applications haute puissance.
- Conductivité électrique : La conductivité électrique supérieure du cuivre permet une meilleure distribution de l’énergie et une résistance réduite, ce qui est crucial pour les circuits haute fréquence et à courant élevé.
- Coût : Les circuits imprimés à noyau en cuivre sont généralement plus chers que les circuits à noyau en aluminium ou en acier en raison du coût plus élevé du cuivre en tant que matière première. Cependant, les avantages en termes de performance justifient souvent l’investissement dans des applications où la dissipation thermique est cruciale.
- Poids : Le cuivre est plus dense et plus lourd que l’aluminium, de sorte que les circuits imprimés à noyau en cuivre ont tendance à être plus lourds. Cela peut être un facteur dans les applications où le poids est un critère, bien que cela soit souvent compensé par les besoins en performance.
Les circuits imprimés à noyau en cuivre sont le plus souvent utilisés dans des applications où une conductivité thermique élevée et des performances électriques fiables sont essentielles, telles que l’éclairage LED, l’électronique automobile et les dispositifs de puissance. Leur capacité à gérer efficacement la chaleur et à supporter des composants haute performance en fait une solution essentielle pour les industries ayant des exigences thermiques et électriques exigeantes.
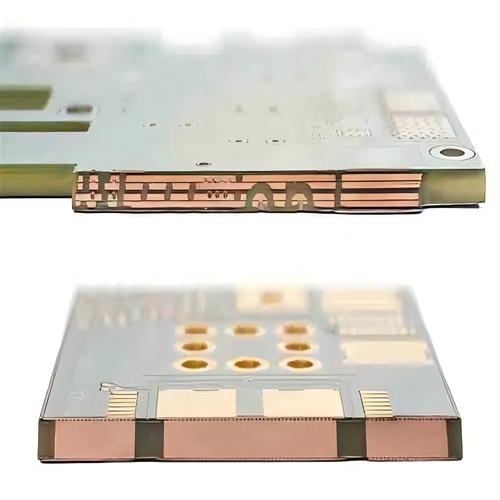
Chapitre 3

Avantages de l'utilisation des circuits imprimés à noyau en cuivre
Les circuits imprimés à noyau en cuivre offrent plusieurs avantages par rapport aux conceptions de circuits imprimés traditionnelles, ce qui en fait un choix préféré dans les applications exigeant une gestion thermique supérieure et une haute fiabilité. Voici les principaux avantages :
Conductivité thermique supérieure
L’un des principaux avantages des circuits imprimés à noyau en cuivre est leur conductivité thermique exceptionnelle. Le cuivre, étant l’un des matériaux les plus efficaces pour le transfert de chaleur, permet à ces circuits imprimés de dissiper la chaleur beaucoup plus rapidement que les circuits imprimés fabriqués à partir de fibre de verre standard ou de noyaux en aluminium. Cette caractéristique est cruciale dans les applications haute puissance, où une chaleur excessive peut entraîner une défaillance des composants, une réduction des performances ou une durée de vie plus courte du produit. La capacité des circuits imprimés à noyau en cuivre à gérer et à répartir la chaleur de manière uniforme aide à maintenir des températures de fonctionnement optimales pour les composants électroniques.
Meilleure dissipation de la chaleur pour les applications haute puissance
Dans des industries telles que l’électronique automobile, l’éclairage LED et l’électronique de puissance, la gestion de la chaleur est essentielle pour la longévité et l’efficacité des appareils. Les circuits imprimés à noyau en cuivre excellent dans la dissipation de la chaleur des composants critiques, réduisant ainsi le risque de surchauffe et améliorant la fiabilité globale du système. Cela rend les circuits imprimés à noyau en cuivre particulièrement adaptés aux applications haute puissance où les circuits imprimés traditionnels peuvent avoir des difficultés à gérer la chaleur générée. En répartissant efficacement la chaleur, les circuits imprimés à noyau en cuivre aident à maintenir l’intégrité des composants et à garantir des performances constantes au fil du temps.
Durabilité et fiabilité accrues
Les circuits imprimés à noyau en cuivre offrent non seulement des performances thermiques supérieures, mais améliorent également la durabilité et la fiabilité du design global du circuit. Le noyau en cuivre fournit une base structurelle solide, rendant le circuit imprimé plus résistant au stress thermique, à l’usure mécanique et aux facteurs environnementaux. Cette durabilité accrue se traduit par une durée de vie plus longue pour les appareils, une réduction des coûts de maintenance et moins de défaillances sur le terrain. De plus, la conductivité élevée du cuivre permet de meilleures performances électriques, réduisant ainsi les risques de perte de signal ou d’interférence, ce qui est essentiel dans les applications haute fréquence.
Dans l’ensemble, la combinaison d’une gestion thermique excellente, d’une durabilité et d’une performance électrique fiable fait des circuits imprimés à noyau en cuivre la solution idéale pour les industries nécessitant des cartes de circuits imprimés de haute qualité et durables, capables de résister à des conditions opérationnelles exigeantes.
Chapitre 4
Applications des circuits imprimés à noyau en cuivre
Les circuits imprimés à noyau en cuivre sont largement utilisés dans les industries où la gestion thermique et la performance électrique sont cruciales. Leurs propriétés uniques les rendent adaptées à une variété d’applications haute puissance et haute performance. Voici quelques-uns des principaux secteurs qui bénéficient de la technologie à noyau en cuivre :
Électronique automobile
Dans l’industrie automobile, de nombreux composants tels que les convertisseurs de puissance, les modules de commande et les phares LED génèrent des quantités importantes de chaleur. Les circuits imprimés à noyau en cuivre sont essentiels dans ces applications car ils dissipent efficacement la chaleur, garantissant que les composants électroniques sensibles fonctionnent de manière fiable même dans des conditions de température extrêmes. La capacité des circuits imprimés à noyau en cuivre à gérer des courants élevés et de la chaleur les rend idéaux pour les systèmes de véhicules électriques, les contrôleurs de moteurs et les unités de gestion de puissance.
Éclairage LED
L’une des applications les plus courantes des circuits imprimés à noyau en cuivre est dans les systèmes d’éclairage LED. Les LED génèrent une chaleur importante, et les circuits imprimés à noyau en cuivre sont utilisés pour gérer cette chaleur et prolonger la durée de vie des LED. En dissipant la chaleur de manière plus efficace, les circuits imprimés à noyau en cuivre aident à maintenir la luminosité et l’efficacité des LED, ce qui les rend idéaux pour des solutions d’éclairage haute performance dans les secteurs automobile, industriel et commercial.
Électronique de puissance
Les systèmes d’électronique de puissance, tels que les alimentations, les onduleurs et les convertisseurs, impliquent souvent des courants élevés et génèrent beaucoup de chaleur. Les circuits imprimés à noyau en cuivre sont cruciaux pour ces systèmes car ils fournissent une dissipation thermique efficace et maintiennent l’intégrité du circuit sous des charges électriques lourdes. Dans des dispositifs haute puissance tels que les machines industrielles et les systèmes de distribution d’énergie, la technologie à noyau en cuivre aide à prévenir la surchauffe et augmente la fiabilité et la longévité des équipements.
Circuits haute fréquence et applications à courant élevé
Dans les circuits haute fréquence, les circuits imprimés à noyau en cuivre offrent une meilleure intégrité du signal et réduisent l’interférence électromagnétique (EMI) grâce à la conductivité exceptionnelle du cuivre. Cela est particulièrement important dans les télécommunications, les systèmes radar et les dispositifs de communication sans fil. De plus, les circuits imprimés à noyau en cuivre sont idéaux pour les applications à courant élevé car ils peuvent supporter de plus grandes charges électriques sans dégradation des performances ou surchauffe.
Autres industries bénéficiant de la technologie à noyau en cuivre
Outre l’automobile, l’éclairage et l’électronique de puissance, d’autres industries bénéficient également des circuits imprimés à noyau en cuivre. Dans les secteurs aérospatial et de la défense, les circuits imprimés à noyau en cuivre sont utilisés dans des systèmes critiques où la fiabilité et la gestion thermique sont primordiales. L’industrie médicale utilise également des circuits imprimés à noyau en cuivre dans les systèmes d’imagerie et les équipements diagnostiques nécessitant des performances stables et durables. De plus, les électroniques grand public, y compris les systèmes informatiques haute performance et les jeux, dépendent de plus en plus de la technologie à noyau en cuivre pour gérer la chaleur et améliorer la longévité des appareils.
Résumé
Les circuits imprimés à noyau en cuivre jouent un rôle essentiel dans une large gamme d’industries, offrant la gestion thermique, la durabilité et les performances nécessaires pour des applications haute puissance et haute performance.
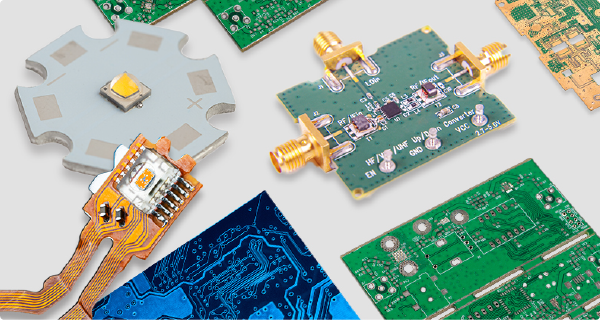
Chapitre 5

Processus de fabrication des circuits imprimés à noyau en cuivre
Le processus de fabrication des circuits imprimés à noyau en cuivre est plus complexe que celui des circuits imprimés traditionnels en raison des propriétés thermiques et électriques uniques du cuivre. Voici un guide étape par étape décrivant le processus de production, les matériaux clés impliqués et les défis auxquels sont confrontés les fabricants.
Guide étape par étape sur la production des circuits imprimés à noyau en cuivre
Préparation du noyau en cuivre Le processus commence par la sélection d’une feuille de cuivre de haute qualité, qui servira de noyau pour le circuit imprimé. Ce noyau en cuivre est généralement plus épais que les feuilles de cuivre utilisées dans les circuits imprimés standard afin de fournir une dissipation thermique améliorée. La feuille de cuivre est nettoyée pour éliminer toute impureté de surface, garantissant ainsi une bonne adhérence lors des étapes suivantes.
Stratification Une couche diélectrique, généralement constituée de matériaux thermiquement conducteurs et électriquement isolants, est stratifiée sur les deux côtés du noyau en cuivre. Cette couche sert d’isolant tout en permettant le transfert de chaleur. Le processus de stratification consiste à appliquer de la pression et de la chaleur pour lier solidement le matériau diélectrique au noyau en cuivre.
Perçage et gravure Une fois la couche diélectrique stratifiée, le circuit imprimé subit un perçage pour créer des trous et des vias permettant des connexions électriques entre les différentes couches du circuit. Après le perçage, les couches de cuivre sont gravées pour former les motifs du circuit. Cette étape utilise des solutions chimiques pour enlever le cuivre indésirable, ne laissant que les traces et les pastilles nécessaires.
Placage Après la gravure, les trous percés sont plaqués avec du cuivre pour créer des connexions électriques entre les couches supérieure et inférieure du circuit imprimé. Cette étape garantit que le courant peut circuler facilement à travers la carte. Des couches supplémentaires de cuivre ou d’autres métaux peuvent être ajoutées pour améliorer la conductivité et la durabilité.
Application du masque à souder et de la sérigraphie Un masque à souder est appliqué pour protéger les traces de cuivre de l’oxydation et prévenir les courts-circuits. Ce masque fournit également une isolation entre les composants. Après le masque à souder, une couche de sérigraphie est ajoutée pour marquer le circuit imprimé avec des désignations de composants et d’autres repères afin de faciliter l’assemblage et la résolution des problèmes.
Finition finale et test Le circuit imprimé subit une finition de surface finale, qui peut inclure l’application de matériaux tels que de l’or ou de l’argent pour améliorer la soudabilité. Ensuite, le circuit imprimé à noyau en cuivre est soumis à des tests électriques et fonctionnels rigoureux pour s’assurer qu’il répond aux spécifications requises. Toute défectuosité est corrigée avant l’expédition du produit final.
Matériaux et technologies clés impliqués
- Noyau en cuivre : Le composant principal qui offre une conductivité thermique supérieure et une intégrité structurelle.
- Couche diélectrique : Matériau isolant qui conduit également la chaleur loin des composants du circuit.
- Feuilles de cuivre : Utilisées pour créer les traces du circuit sur les couches extérieures.
- Matériaux de placage : Cuivre ou autres métaux utilisés pour plaquer les vias et les trous traversants afin de permettre les connexions électriques.
Des technologies avancées telles que le perçage laser et l’inspection optique automatisée (AOI) sont souvent utilisées pour garantir la précision pendant les processus de perçage, de gravure et de test. Les machines CNC sont également utilisées pour des formes et découpes de haute précision.
Défis courants et solutions lors de la fabrication
Gestion de la chaleur : L’un des défis majeurs dans la fabrication des circuits imprimés à noyau en cuivre est de maintenir un équilibre thermique approprié pendant les processus de stratification et de soudage. Une chaleur excessive peut entraîner un gauchissement ou une délamination. Les fabricants atténuent ce problème en utilisant un contrôle précis de la température et des matériaux de stratification de haute qualité.
Épaisseur du cuivre : Manipuler des noyaux en cuivre plus épais est plus difficile que de travailler avec des circuits imprimés standard. Le poids et la densité accrus du cuivre nécessitent des équipements spécialisés pour le perçage, la gravure et le placage. L’utilisation de machines CNC avec un couple élevé et une grande précision aide à gérer ces défis.
Problèmes d’adhésion : Il peut être difficile d’obtenir une forte adhésion entre le noyau en cuivre et la couche diélectrique. Toute impureté ou surface inégale peut entraîner une mauvaise adhésion. Un nettoyage minutieux des surfaces et l’utilisation de matériaux de stratification de haute qualité garantissent une adhésion plus fiable.
Précision de la gravure : Graver des couches de cuivre plus épaisses peut parfois entraîner des traces irrégulières ou une gravure excessive. Pour résoudre ce problème, les fabricants utilisent des processus chimiques avancés et une surveillance en temps réel pour contrôler le processus de gravure.
En conclusion, le processus de fabrication des circuits imprimés à noyau en cuivre implique des techniques et des matériaux avancés qui permettent de créer des cartes durables et efficaces. Malgré les défis, les fabricants ont développé des solutions permettant la production de circuits imprimés à noyau en cuivre offrant une performance précise pour des applications exigeantes.
Chapitre 6
Considérations de conception des circuits imprimés à noyau en cuivre
La conception des circuits imprimés à noyau en cuivre nécessite une planification minutieuse et le respect de règles de conception spécifiques pour maximiser leurs avantages thermiques et électriques. Voici quelques considérations clés de conception, meilleures pratiques et conseils pour garantir des performances optimales dans les conceptions de circuits imprimés à noyau en cuivre.
Règles de conception spécifiques et meilleures pratiques
Épaisseur du noyau en cuivre L’épaisseur du noyau en cuivre joue un rôle crucial dans la performance thermique et l’intégrité structurelle du circuit imprimé. Les concepteurs doivent sélectionner l’épaisseur de cuivre appropriée en fonction des besoins en énergie et des exigences de dissipation thermique de l’application. Les épaisseurs courantes des noyaux en cuivre varient de 1,0 mm à 3,0 mm, mais le choix idéal dépend de la charge thermique attendue et des contraintes mécaniques.
Choix du matériau diélectrique Le choix du bon matériau diélectrique entre le noyau en cuivre et les couches conductrices est essentiel pour équilibrer la conductivité thermique et l’isolation électrique. Des matériaux à haute conductivité thermique, tels que les époxydes conducteurs thermiquement ou les composés remplis de céramique, doivent être utilisés pour garantir un transfert thermique efficace. Le matériau diélectrique doit également maintenir d’excellentes propriétés d’isolation électrique pour éviter les courts-circuits.
Conception des vias et du placage Pour une dissipation thermique et des performances électriques optimales, la conception des vias (trous traversants) doit permettre un transfert thermique efficace de la surface vers le noyau en cuivre. Les concepteurs utilisent souvent des vias thermiquement conducteurs, qui sont plaqués de cuivre pour évacuer la chaleur des composants chauds. Il est important d’espacer correctement les vias et de s’assurer que les parois des vias sont entièrement plaquées pour améliorer la fiabilité et réduire la résistance.
Placement des composants Les composants à haute puissance, tels que les transistors de puissance ou les LED, doivent être placés aussi près que possible du noyau en cuivre pour maximiser la dissipation thermique. Le placement correct de ces composants garantit que la chaleur est transférée efficacement au noyau en cuivre, évitant ainsi les points chauds localisés qui pourraient affecter les performances. De plus, les composants sensibles doivent être placés stratégiquement pour éviter les zones de forte contrainte thermique.
Gestion thermique et distribution de l’énergie
Dissipation thermique efficace Les circuits imprimés à noyau en cuivre sont utilisés principalement pour leurs propriétés exceptionnelles de dissipation thermique. Pour en tirer le meilleur parti, les concepteurs doivent envisager l’utilisation de grandes zones de cuivre, de plans de cuivre épais et de dissipateurs thermiques directement fixés au noyau en cuivre. En maximisant la surface en contact avec le noyau en cuivre, plus de chaleur peut être distribuée uniformément, réduisant ainsi le risque de surchauffe des composants à haute puissance.
Couches de distribution de l’énergie La distribution de l’énergie est un autre aspect critique de la conception des circuits imprimés à noyau en cuivre. Pour minimiser la chute de tension et garantir une alimentation cohérente, les concepteurs doivent utiliser des traces larges et des couches de cuivre épaisses pour les plans d’alimentation et de masse. Ces couches aident à distribuer efficacement le courant sur la carte et à réduire l’impédance, ce qui est particulièrement important dans les applications à courant élevé.
Simulation thermique Les logiciels de simulation thermique peuvent être utilisés pendant la phase de conception pour prédire comment la chaleur circulera à travers la carte et où des points chauds potentiels pourraient se développer. En simulant diverses charges thermiques et placements de composants, les concepteurs peuvent apporter des ajustements avant la fabrication pour garantir des performances thermiques optimales. Cette étape est particulièrement importante dans les conceptions haute puissance où la gestion thermique incorrecte peut entraîner une défaillance prématurée des composants.
Conseils pour garantir des performances optimales dans les conceptions
Conception pour la fabricabilité (DFM): Lors de la conception d’un circuit imprimé à noyau en cuivre, il est essentiel de s’assurer que le design respecte les capacités du fabricant. Les noyaux en cuivre épais peuvent être difficiles à fabriquer, il est donc important de travailler en étroite collaboration avec le fabricant de PCB pour comprendre les contraintes de conception, afin d’assurer une production réussie.
Minimiser la longueur des traces: Des longueurs de traces plus courtes entre les composants à haute puissance réduisent la résistance et améliorent les performances électriques globales du circuit imprimé. De plus, minimiser la distance entre les composants sensibles à la chaleur et le noyau en cuivre améliore la dissipation thermique.
Utilisation de pads thermiques: Pour les composants générant une chaleur significative, l’utilisation de pads thermiques connectés au noyau en cuivre via des vias thermiques peut grandement améliorer le transfert thermique. Ces pads aident à dissiper la chaleur directement du composant vers le noyau en cuivre, maintenant ainsi un environnement de fonctionnement plus frais.
Blindage des composants: Pour les applications à signaux haute fréquence, les concepteurs peuvent avoir besoin de mettre en œuvre des techniques de blindage pour éviter les interférences électromagnétiques (EMI). Le noyau en cuivre peut également servir de bouclier naturel contre les EMI, à condition que le design intègre des techniques appropriées de mise à la terre et d’isolation.
Empilement des couches: Lors de la conception d’un circuit imprimé à noyau en cuivre multicouche, l’agencement des couches doit prendre en compte à la fois les facteurs thermiques et électriques. Les couches d’alimentation et de masse doivent être placées près du noyau en cuivre pour profiter de ses propriétés de dissipation thermique, tandis que les couches de signal doivent être isolées pour éviter les interférences.
Conclusion
La conception des circuits imprimés à noyau en cuivre nécessite une attention particulière à la gestion thermique, à la distribution de l’énergie et à la fabricabilité. En suivant ces règles de conception et meilleures pratiques, les concepteurs peuvent créer des circuits imprimés à noyau en cuivre efficaces et fiables qui offrent des performances optimales dans des environnements à haute puissance et haute température.
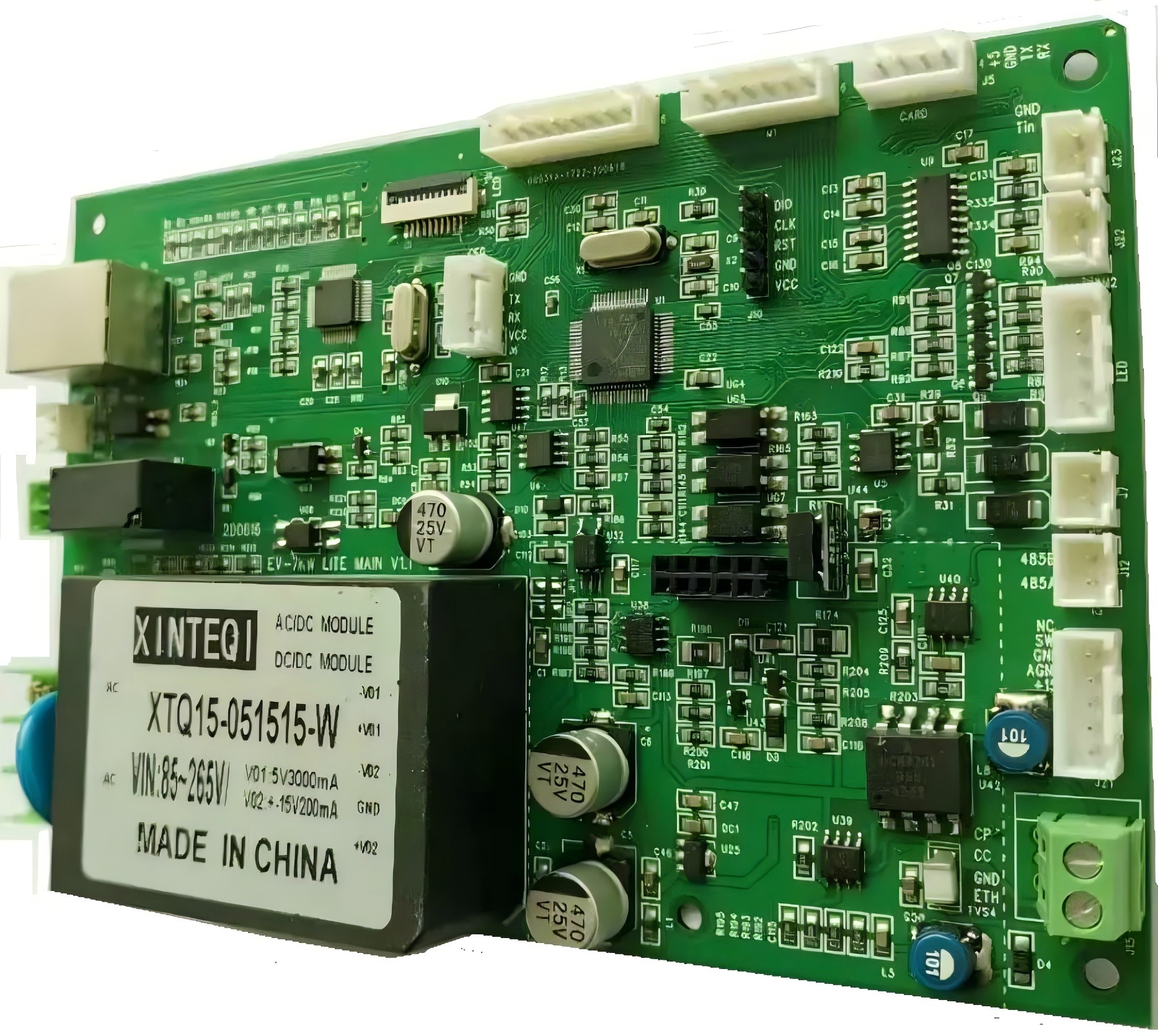
Chapitre 7
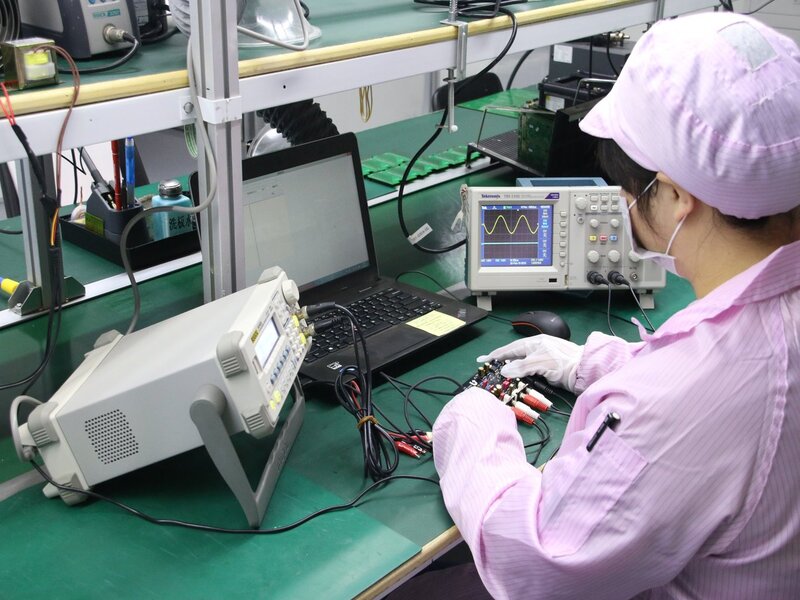
Circuits imprimés à noyau en cuivre vs. circuits à noyau en aluminium
es circuits imprimés à noyau en cuivre et à noyau en aluminium sont largement utilisés dans des applications nécessitant une excellente gestion thermique et une grande durabilité. Cependant, ils diffèrent considérablement en termes de propriétés des matériaux, de performance et de coût. Comprendre ces différences peut vous aider à choisir le bon type de circuit imprimé pour votre application spécifique.
Avantages et inconvénients de chaque matériau
Circuits imprimés à noyau en cuivre
Avantages :
- Conductivité thermique supérieure : Le cuivre offre une conductivité thermique plus élevée (environ 400 W/mK) par rapport à l’aluminium (205 W/mK), ce qui rend les circuits imprimés à noyau en cuivre plus efficaces pour dissiper la chaleur.
- Meilleure conductivité électrique : La conductivité électrique du cuivre est également beaucoup plus élevée, réduisant la résistance électrique et améliorant la distribution de la puissance dans les applications à haute fréquence et à courant élevé.
- Durabilité : Le cuivre est plus robuste et peut supporter des charges plus élevées et des contraintes thermiques sans se déformer ni perdre en performance.
Inconvénients :
- Coût : Le cuivre est nettement plus cher que l’aluminium, ce qui rend les circuits imprimés à noyau en cuivre plus coûteux à produire. Ce coût plus élevé peut ne pas être justifié dans des applications à faible puissance où l’aluminium fournit des performances suffisantes.
- Poids : Le cuivre est plus dense et plus lourd que l’aluminium, ce qui peut être un inconvénient dans les applications sensibles au poids, comme l’aérospatial et les appareils portables.
Circuits imprimés à noyau en aluminium
Avantages :
- Coût inférieur : L’aluminium est plus abordable que le cuivre, ce qui rend les circuits imprimés à noyau en aluminium une option économique pour une large gamme d’applications, en particulier dans l’électronique grand public et l’éclairage LED.
- Légèreté : L’aluminium est plus léger que le cuivre, ce qui en fait un choix privilégié dans les industries où le poids est un facteur critique, comme dans les applications automobiles et aérospatiales.
- Gestion thermique suffisante : Bien que la conductivité thermique de l’aluminium soit inférieure à celle du cuivre, elle reste bien supérieure à celle des substrats FR-4 traditionnels, ce qui rend les circuits imprimés en aluminium adaptés à de nombreuses applications sensibles à la chaleur, telles que les LED.
Inconvénients :
- Conductivité thermique inférieure : Bien que l’aluminium offre de bonnes propriétés de dissipation de la chaleur, il ne peut égaler les performances du cuivre dans les applications à haute puissance.
- Conductivité électrique : La conductivité électrique de l’aluminium est inférieure à celle du cuivre, ce qui le rend moins adapté aux circuits haute fréquence ou aux applications nécessitant une distribution efficace de l’énergie.
- Moins durable : L’aluminium est moins résistant aux contraintes thermiques et mécaniques extrêmes par rapport au cuivre, ce qui peut limiter son utilisation dans des applications à haute puissance et haute précision.
Coût, performance et adéquation des applications
Coût :
Les circuits imprimés à noyau en aluminium sont généralement plus rentables, ce qui les rend adaptés aux projets à budget limité ou aux applications où la performance thermique est importante mais pas cruciale. Les circuits imprimés à noyau en cuivre, en revanche, sont plus coûteux en raison du prix élevé du cuivre, mais offrent de meilleures performances en termes de conductivité thermique et électrique.Performance :
Les circuits imprimés à noyau en cuivre offrent une meilleure dissipation thermique, une conductivité électrique supérieure et une plus grande durabilité. Cela en fait le choix incontournable pour les applications à haute puissance, telles que les convertisseurs de puissance, l’électronique automobile et les systèmes LED haute performance. Les circuits imprimés à noyau en aluminium conviennent aux applications nécessitant une bonne gestion thermique mais sans besoin des performances haut de gamme que fournit le cuivre, comme l’électronique grand public, l’éclairage LED et certains systèmes automobiles.Adéquation des applications :
- Circuits imprimés à noyau en cuivre : Mieux adaptés aux applications à haute puissance où une dissipation thermique extrême et des performances électriques sont essentielles, comme les circuits à courant élevé, les dispositifs de puissance, l’électronique automobile et les machines industrielles.
- Circuits imprimés à noyau en aluminium : Idéaux pour les applications de gamme moyenne où le coût et le poids sont des considérations importantes, comme l’éclairage LED, l’électronique grand public et les systèmes intérieurs automobiles.
Quand choisir le cuivre plutôt que l’aluminium et vice versa
Choisissez les circuits imprimés à noyau en cuivre lorsque :
- Votre application nécessite une dissipation thermique supérieure, comme dans l’éclairage LED haute puissance, l’électronique automobile ou les alimentations.
- Vous avez besoin d’une conductivité électrique élevée pour des circuits haute fréquence ou à courant élevé, garantissant une perte d’énergie minimale.
- La durabilité et les performances à long terme sont cruciales, notamment dans des environnements difficiles où les composants sont soumis à des cycles thermiques et à des contraintes élevées.
Choisissez les circuits imprimés à noyau en aluminium lorsque :
- Le coût est un facteur clé, et l’application ne nécessite pas la dissipation thermique extrême et les performances électriques que fournit le cuivre.
- Le poids est une préoccupation, et vous avez besoin d’un circuit imprimé léger pour la portabilité ou pour réduire le poids global de l’appareil, comme dans les industries automobiles et aérospatiales.
- L’application implique des électroniques de puissance moyenne ou sensibles à la chaleur, telles que l’électronique grand public ou les systèmes LED de faible à moyenne puissance.
Résumé
Les circuits imprimés à noyau en cuivre excellent dans les environnements à haute performance et haute puissance où la gestion thermique et l’efficacité électrique sont essentielles. Les circuits imprimés à noyau en aluminium, bien que moins performants dans ces domaines, offrent une solution économique et légère pour les applications ne nécessitant pas les caractéristiques de performance extrême du cuivre. Le choix entre le cuivre et l’aluminium dépend des besoins spécifiques de votre projet en termes de coût, de performance et d’exigences d’application.
Chapitre 8
Comment tester les circuits imprimés à noyau en cuivre ?
Tester les circuits imprimés à noyau en cuivre est crucial pour garantir qu’ils respectent les normes de performance, notamment en termes de gestion thermique, de performance électrique et de durabilité. Voici les principales méthodes et processus pour tester ces circuits.
- Inspection visuelle
La première étape pour tester les circuits imprimés à noyau en cuivre consiste en une inspection visuelle approfondie pour identifier les défauts physiques tels que les couches mal alignées, les gravures incomplètes ou les problèmes liés aux vias et aux traces. Ce processus peut être effectué manuellement ou à l’aide de systèmes d’inspection optique automatisée (AOI).
Points à vérifier :
- Couches de cuivre mal alignées.
- Gravure incomplète ou inégale des traces.
- Défauts de surface tels que des rayures ou des fissures.
- Application incohérente du masque de soudure.
- Test de conductivité thermique
Étant donné que la gestion thermique est une caractéristique clé des circuits imprimés à noyau en cuivre, tester la conductivité thermique est essentiel pour vérifier l’efficacité de dissipation de la chaleur de la carte.
Fonctionnement :
Un capteur thermique est placé sur la carte pour surveiller la répartition de la chaleur lorsque la carte est soumise à des charges électriques. L’efficacité de dissipation thermique est évaluée en mesurant le taux de transfert de chaleur depuis les points chauds.
Indicateurs clés :
- Taux de transfert de chaleur.
- Répartition des températures sur la surface de la carte.
- Température maximale atteinte pendant le fonctionnement.
- Test de conductivité électrique
Les circuits imprimés à noyau en cuivre sont connus pour leur excellente conductivité électrique. Tester les performances électriques garantit que les traces et le noyau en cuivre supportent les charges de courant requises sans résistance excessive.
Méthodes de test :
- Mesure de la conductivité : Utilisation d’un multimètre ou d’équipements spécialisés pour mesurer la résistance sur les traces et les vias.
- Test de gestion des charges élevées : La carte est soumise à des charges de courant élevées pour évaluer sa capacité à gérer ces charges sans dégradation des performances.
Indicateurs clés :
- Résistance sur les traces et les vias.
- Chutes de tension et pertes de puissance sous charge.
- Intégrité des connexions électriques (notamment aux points de via).
- Test de cycles thermiques et de contraintes
Le test de cycles thermiques est essentiel pour s’assurer que les circuits imprimés à noyau en cuivre peuvent supporter les fluctuations de température répétées. Le test de contraintes simule des conditions opérationnelles extrêmes pour vérifier la résilience et la durabilité de la carte.
Fonctionnement :
La carte est soumise à une série de cycles thermiques alternant entre des températures élevées et basses. Cela permet d’identifier les problèmes liés à l’expansion des matériaux, à la délamination ou aux défaillances mécaniques dues au stress thermique.
Indicateurs clés :
- Taux d’expansion thermique.
- Résistance à la délamination ou aux fissures.
- Performances sous cycles thermiques répétés.
- Test fonctionnel
Le test fonctionnel garantit que la carte fonctionne comme prévu dans son application finale. Cela inclut l’alimentation de la carte et son fonctionnement dans des conditions opérationnelles typiques.
Configuration du test :
La carte est connectée à un banc d’essai où elle fonctionne sous des conditions simulées proches de la réalité. Les capteurs mesurent ses performances thermiques et électriques.
Indicateurs clés :
- Intégrité du signal et niveaux de bruit.
- Stabilité des tensions et courants sous charge.
- Températures de fonctionnement dans des conditions d’utilisation typiques.
- Test de charge élevée
Pour les circuits imprimés à noyau en cuivre conçus pour des applications à haute puissance, ce test est essentiel pour vérifier leur capacité à gérer des charges électriques importantes sans surchauffe ou défaillances électriques.
Configuration du test :
La carte est soumise à des charges de courant maximales tandis que des capteurs surveillent ses performances thermiques et électriques.
Indicateurs clés :
- Capacité de charge en courant maximale.
- Stabilité thermique à pleine puissance.
- Intégrité de la carte et des composants sous conditions de contrainte élevée.
- Test de soudabilité
Les tests de soudabilité vérifient que la surface de la carte permet une soudure correcte des composants, essentielle pour des connexions fiables.
Fonctionnement :
La carte est exposée à des températures de soudure, et la qualité des joints de soudure est évaluée.
Indicateurs clés :
- Résistance des joints de soudure.
- Propriétés de mouillage de la surface en cuivre.
- Absence de défauts de soudure.
- Test de fiabilité
Pour vérifier la durabilité et la fiabilité à long terme, les circuits imprimés à noyau en cuivre subissent des tests environnementaux et de fiabilité.
Tests inclus :
- Test d’humidité : La carte est exposée à des niveaux élevés d’humidité pour évaluer sa résistance à l’humidité et à la corrosion.
- Test de vibration : Des vibrations mécaniques sont appliquées pour évaluer l’intégrité structurelle de la carte.
- Test au brouillard salin : Pour évaluer la résistance à la corrosion dans des applications marines ou extérieures.
Indicateurs clés :
- Résistance à la corrosion.
- Intégrité structurelle sous vibrations.
- Résistance à l’humidité.
Résumé :
Les tests des circuits imprimés à noyau en cuivre incluent une combinaison de tests thermiques, électriques, mécaniques et environnementaux pour garantir que la carte respecte les normes de performance et de fiabilité. Ces tests approfondis sont essentiels pour vérifier que les circuits imprimés à noyau en cuivre peuvent fonctionner de manière optimale dans des applications exigeantes où la dissipation thermique et l’efficacité électrique sont cruciales.
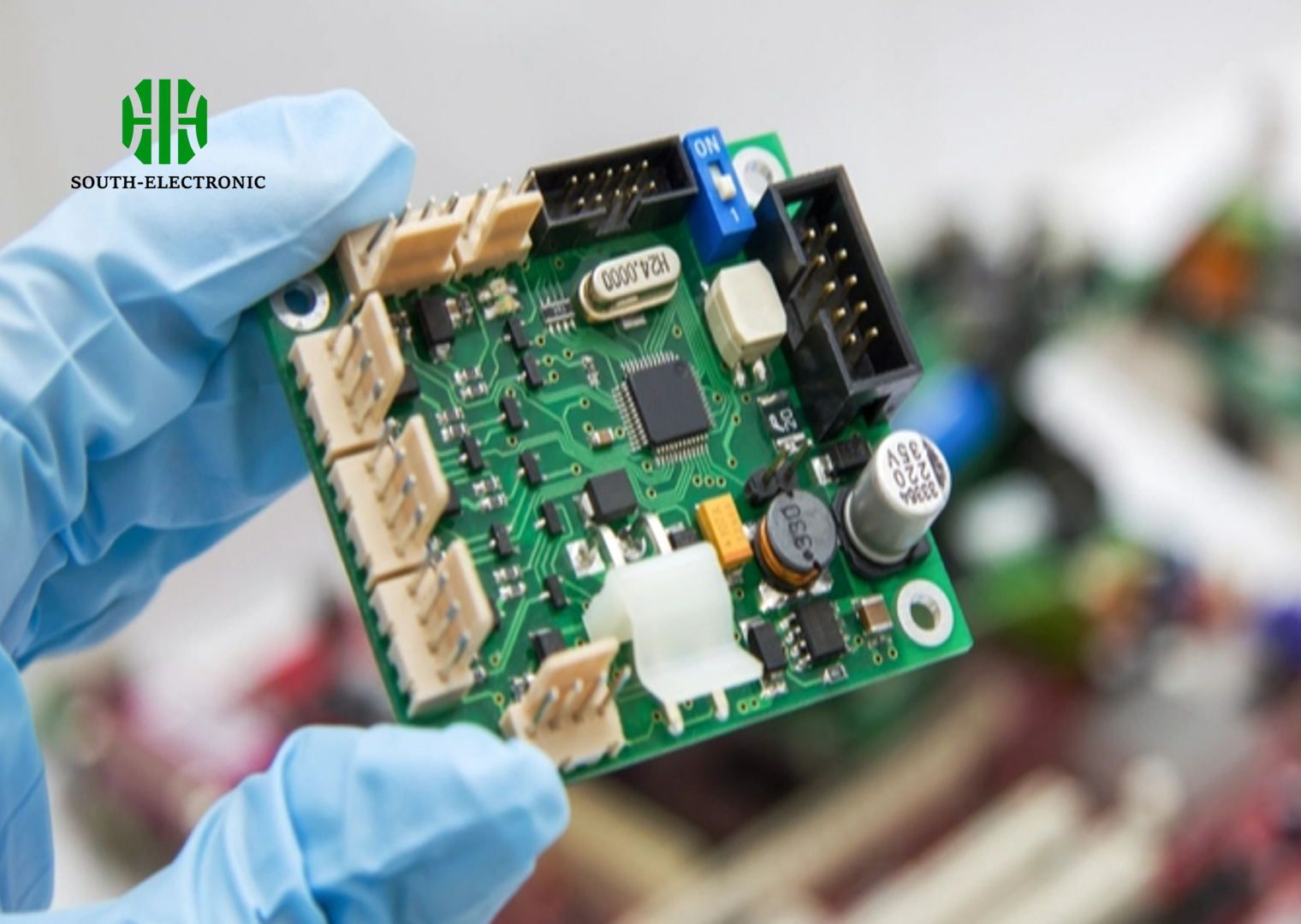
Chapitre 9

Comment choisir le bon fournisseur de circuits imprimés à noyau de cuivre ?
Choisir le bon fournisseur de circuits imprimés à noyau en cuivre est une décision cruciale qui peut impacter la qualité, la performance et la fiabilité de votre produit final. Voici les principaux facteurs à considérer lors de la sélection d’un fournisseur pour garantir qu’il réponde à vos exigences techniques et commerciales.
- Expérience et expertise
Un fournisseur avec une expérience étendue dans la fabrication de circuits imprimés à noyau en cuivre aura les connaissances et l’expertise technique nécessaires pour gérer les complexités de production de cartes de haute qualité. Recherchez des fournisseurs spécialisés dans la technologie du noyau en cuivre et ayant un historique éprouvé dans des applications haute performance comme l’électronique automobile, les alimentations ou l’éclairage LED.
Questions à poser :
- Depuis combien de temps produisent-ils des circuits imprimés à noyau en cuivre ?
- Ont-ils une expertise spécifique dans votre secteur ou application ?
- Normes de qualité et certifications
La qualité est essentielle, en particulier pour les applications haute puissance ou sensibles à la chaleur. Assurez-vous que le fournisseur respecte les normes internationales de qualité, telles que ISO 9001 et les normes IPC pour la fabrication de circuits imprimés.
Certifications à vérifier :
- ISO 9001 : Certification du système de gestion de la qualité.
- Normes IPC : IPC-6012 (Spécification de qualification et de performance pour les circuits rigides) et IPC-A-600 (Acceptabilité des circuits imprimés).
- Certification UL : Garantit que les circuits imprimés respectent les normes de sécurité pour les produits électriques.
- Capacités de fabrication
Évaluez les capacités de fabrication du fournisseur pour vous assurer qu’il peut répondre aux exigences spécifiques de votre projet de circuits imprimés à noyau en cuivre. Cela inclut la gestion des noyaux de cuivre épais, des laminés spécialisés et des équipements de production de haute précision.
Considérations clés de fabrication :
- Épaisseur maximale du cuivre qu’ils peuvent gérer.
- Techniques de laminage avancées pour les matériaux diélectriques.
- Capacités d’usinage CNC pour le perçage et le routage précis.
- Technologies de placage de haute qualité pour les vias et les trous traversants.
- Tests et contrôle qualité
Un fournisseur fiable aura des mesures strictes de test et de contrôle qualité en place. Cela inclut des inspections en cours de processus et des tests de produit final pour garantir que la carte répond aux spécifications thermiques, électriques et mécaniques requises.
Méthodes de test attendues :
- Inspection optique automatisée (AOI) pour détecter les défauts dans les traces de cuivre.
- Tests de conductivité thermique pour garantir une dissipation efficace de la chaleur.
- Tests électriques pour la conductivité, la gestion du courant et l’intégrité des signaux.
- Tests de contraintes environnementales, comme les cycles thermiques et les vibrations.
- Personnalisation et flexibilité
Votre projet peut avoir des exigences uniques en termes de conception ou de production. Le fournisseur idéal devrait offrir des options de personnalisation telles que l’épaisseur du cuivre, les dimensions de la carte, le nombre de couches et les matériaux diélectriques.
Options de personnalisation à considérer :
- Épaisseurs de noyau en cuivre personnalisées en fonction des besoins de dissipation thermique.
- Production flexible (de petites séries à des volumes élevés).
- Choix des finitions de surface (par ex., ENIG, OSP ou HASL) pour une meilleure soudabilité.
- Matériaux diélectriques spécialisés pour des performances accrues.
- Capacité de production et délais
La capacité de production du fournisseur est un autre facteur important, en particulier si vous devez augmenter la production ou respecter des délais serrés.
Ce qu’il faut évaluer :
- Capacités et capacités des lignes de production.
- Délais moyens pour les prototypes et la production en série.
- Performance de livraison à temps (vérifiez les avis ou études de cas).
- Support technique et communication
Une communication fiable et un support technique sont essentiels, surtout lorsque vous travaillez avec des conceptions complexes comme les circuits imprimés à noyau en cuivre.
Questions à poser :
- Proposent-ils des consultations en conception et des retours sur la fabricabilité (DFM) ?
- Quelle est la réactivité de leur équipe de support technique ?
- Offrent-ils des mises à jour en temps réel sur l’avancement de la production ?
- Prix et transparence des coûts
Bien que le coût ne doive pas être le seul facteur déterminant, il est important de trouver un fournisseur offrant des prix compétitifs sans compromettre la qualité.
Ce qu’il faut rechercher dans les prix :
- Décomposition claire des coûts (matériaux, main-d’œuvre, tests, etc.).
- Absence de frais cachés ou de charges supplémentaires.
- Flexibilité des prix pour différents volumes (prototypes versus production en série).
- Réputation et avis clients
Examinez la réputation du fournisseur dans l’industrie en consultant des témoignages clients, des études de cas et des évaluations.
Où vérifier :
- Avis en ligne sur des plateformes comme Google ou Alibaba.
- Études de cas ou références d’entreprises similaires dans votre secteur.
- Prix ou reconnaissances de l’industrie pour la qualité et la performance.
- Logistique et expédition internationale
Si vous travaillez avec un fournisseur international, assurez-vous qu’il dispose d’un réseau fiable de logistique et d’expédition.
Aspects logistiques à considérer :
- Options d’expédition mondiale et délais.
- Expérience dans le dédouanement et la documentation.
- Coûts et options d’expédition (par air, mer ou livraison express).
Conclusion :
Choisir le bon fournisseur de circuits imprimés à noyau en cuivre implique d’évaluer son expertise, ses normes de qualité, ses capacités de production et sa fiabilité. En prenant en compte des facteurs tels que les certifications, les options de personnalisation, le support technique et la transparence des coûts, vous pouvez sélectionner un fournisseur qui répond aux besoins de votre projet et livre des circuits imprimés à noyau en cuivre de haute qualité dans les délais impartis. Assurez-vous de mener des recherches approfondies, de vérifier les avis clients et de communiquer directement avec les fournisseurs potentiels pour prendre une décision éclairée.
Chapitre 10
Tendances futures des circuits imprimés à noyau en cuivre
Les circuits imprimés à noyau en cuivre (PCBs) jouent un rôle central dans l’électronique moderne grâce à leur capacité supérieure de dissipation thermique et de conductivité électrique. Voici quelques tendances à venir dans ce domaine en évolution :
Augmentation de la demande pour les applications haute puissance :
À mesure que les appareils deviennent plus puissants et plus compacts, la demande pour des circuits imprimés à noyau en cuivre capables de gérer efficacement la chaleur augmentera. Cela est particulièrement pertinent pour les applications dans les véhicules électriques, l’aérospatial et les télécommunications.Progrès dans la gestion thermique :
Les futurs circuits imprimés à noyau en cuivre intégreront probablement des technologies avancées de gestion thermique. Ces innovations pourraient inclure de nouveaux matériaux et des conceptions architecturales pour améliorer encore la dissipation de la chaleur.Miniaturisation et précision :
Avec la tendance de l’industrie à produire des appareils plus petits et plus efficaces, il y aura un développement accru de circuits imprimés à noyau en cuivre plus petits et plus précis. Cela nécessitera des avancées dans les technologies de fabrication pour maintenir les performances tout en réduisant la taille.Intégration avec l’électronique flexible :
Les circuits imprimés à noyau en cuivre pourraient être de plus en plus intégrés à l’électronique flexible, offrant durabilité et flexibilité dans la conception. Cette tendance est importante pour les technologies portables et les écrans flexibles.Processus de fabrication écologiques :
Avec un accent croissant sur la durabilité, il y aura une poussée vers des processus de fabrication plus respectueux de l’environnement. Cela inclut la réduction des déchets, le recyclage et l’utilisation de matériaux écologiques dans la production de circuits imprimés à noyau en cuivre.Amélioration des performances électriques :
Les futurs circuits imprimés à noyau en cuivre se concentreront sur l’amélioration des performances électriques, soutenant des taux de données plus élevés et une meilleure intégrité du signal, essentiels pour l’électronique moderne à haute vitesse.Stratégies de réduction des coûts :
Avec l’augmentation de la demande, l’accent sera mis sur le développement de processus de fabrication rentables qui maintiennent la qualité et les performances, rendant les circuits imprimés à noyau en cuivre plus accessibles pour diverses applications.
Ces tendances reflètent l’innovation continue et l’adaptation dans l’industrie électronique pour répondre aux demandes croissantes en termes d’efficacité, de durabilité et de performance dans les appareils modernes.
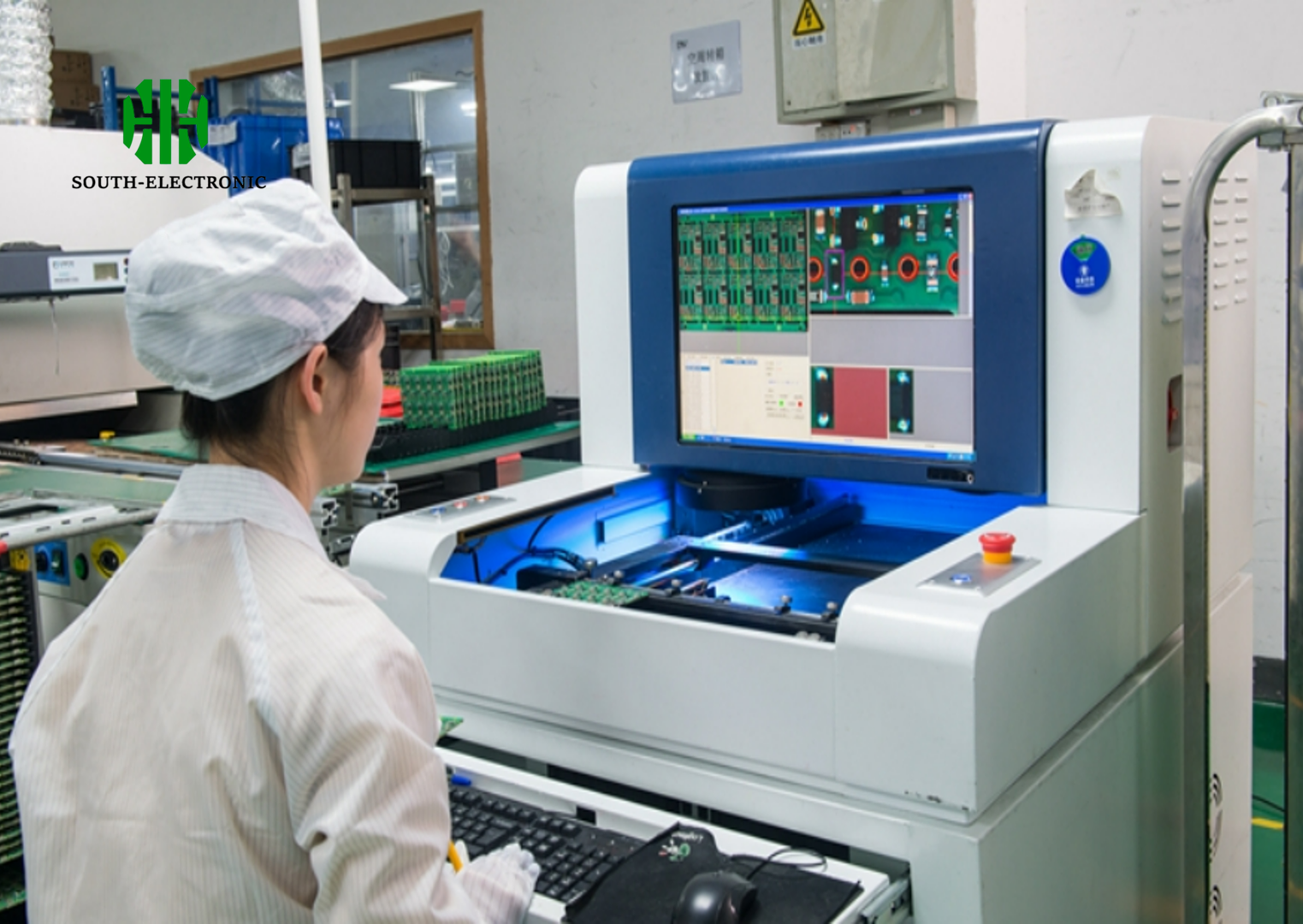
Contactez-Nous
Où Sommes-Nous ?
Parc Industriel, No. 438 Route Donghuan, No. 438, Shajing Donghuan Road, District Bao'an, Shenzhen, Guangdong, Chine
4ème étage, Bâtiment Zhihui Créatif, No. 2005 Route Xihuan, Shajing, District Baoan, Shenzhen, Chine
CHAMBRE A1-13, ÉTAGE 3, CENTRE INDUSTRIEL YEE LIM, 2-28 RUE KWAI LOK, KWAI CHUNG HK
service@southelectronicpcb.com
Téléphone : +86 400 878 3488
Envoyez-nous un message
Plus vous remplissez de détails, plus nous pourrons avancer rapidement à l’étape suivante.
