PCB flexible Supérieu
South-Electronic
Améliorez vos projets avec les flex PCBs de haute qualité de South-Electronic ! Nous nous consacrons à la qualité, la personnalisation et l'innovation, pour que vous puissiez utiliser nos circuits dans tout, de l'électronique de consommation à l'aérospatial. Laissez-nous vous aider à concrétiser vos idées—demandez un devis dès aujourd'hui !
Élevez vos projets avec des flex PCB
Bienvenue chez South-Electronic, où nous garantissons l’excellence en flex PCBs.
Que vous innoviez dans la technologie portable ou recherchiez la robustesse dans l’aérospatiale, nos PCBs flexibles sont conçus pour offrir fiabilité et adaptabilité. Laissez South-Electronic être votre partenaire pour stimuler le succès et l’excellence dans votre domaine.

PCB Flex simple face
Les PCB Flex simple face ont une couche de matériau conducteur, ce qui les rend parfaits pour les applications simples et à faible densité où la flexibilité est essentielle. Ils sont idéaux pour les projets nécessitant peu de connexions électriques mais restant légers et flexibles.
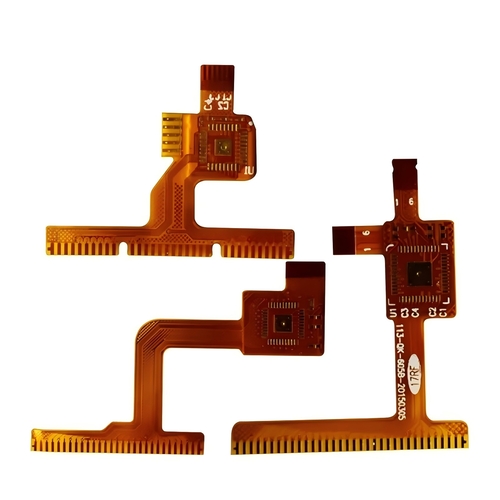
PCB Flex double face
Les PCB Flex double face possèdent du matériau conducteur des deux côtés, ce qui permet des conceptions plus complexes dans un espace réduit. Ils augmentent la densité des circuits sans compromettre la flexibilité, ce qui les rend idéaux pour des applications nécessitant à la fois complexité et efficacité spatiale.
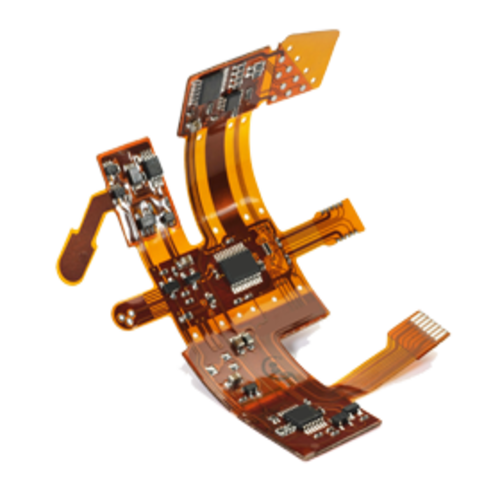
PCB Flex multicouche
Les PCB Flex multicouches ont trois couches ou plus de matériau conducteur, ce qui les rend parfaits pour les applications de haute complexité nécessitant des fonctions électroniques avancées. Ils sont extrêmement flexibles et économes en espace, parfaits pour les conceptions complexes dans de nombreuses industries.

PCB Rigide-Flexible
Les PCB rigides-flexibles combinent la stabilité structurelle des circuits rigides avec la flexibilité des circuits flexibles. Ils sont parfaits pour les assemblages électroniques complexes, car ils offrent des connexions solides mais flexibles répondant à des exigences de performance strictes.
Pourquoi choisir South-Electronic ?
-
Fabrication de Haute Qualité
En choisissant South-Electronic, vous choisissez l'excellence.
Notre engagement envers la fabrication de haute qualité garantit que chaque Flex PCB est produit avec précision et soin, respectant les normes les plus élevées de l'industrie en matière de fiabilité et de performance. -
Options de Personnalisation
Votre projet est unique, et vos PCB doivent l'être aussi.
Avec notre large gamme d'options de personnalisation, vous pouvez concevoir des Flex PCBs adaptés à vos besoins spécifiques. Cela signifie que vous pouvez créer des produits innovants qui se démarquent de la concurrence. -
Expérience Étendue dans l'Industrie
C'est pourquoi nous offrons des services de prototypage rapide qui vous permettent de tester rapidement vos conceptions.
De cette manière, vous pouvez itérer et affiner vos conceptions plus rapidement, pour mettre vos produits sur le marché plus tôt. -
Expédition et Support Mondial
Peu importe où votre entreprise vous emmène, nous sommes là pour vous soutenir.
Nous offrons une expédition mondiale fiable, vous permettant de faire confiance à l'arrivée de vos PCB dans les délais. Et si vous avez des questions ou des préoccupations, notre équipe de support est toujours là pour vous aider.
Projet Connexe que Nous Avons Réalisé
Avis des Clients
Questions Fréquemment Posées
Questions les Plus Populaires
South-Electronic propose une large gamme de PCBs flexibles pour répondre aux besoins de différentes industries. Notre gamme de produits inclut des circuits flexibles simple face, double face et multicouche qui fonctionnent bien dans des espaces restreints. Que vous ayez besoin de conceptions standard ou de configurations personnalisées, nos PCBs flexibles sont conçus pour soutenir vos applications innovantes.
La qualité est notre priorité chez South-Electronic. Nous avons des mesures de contrôle de qualité strictes tout au long du processus de production, incluant des techniques d'inspection avancées et le respect des normes internationales comme ISO et IPC. Notre équipe expérimentée teste tous les PCBs flexibles pour s'assurer qu'ils répondent à vos spécifications et dépassent vos attentes.
Absolument ! Chez South-Electronic, nous comprenons que chaque projet est unique. Nous offrons des options complètes de personnalisation pour les formes et tailles des PCBs flexibles afin de répondre à vos besoins spécifiques. Notre équipe d'ingénierie travaille en étroite collaboration avec vous pour développer la solution parfaite qui s'intègre parfaitement à votre design.
Nous nous efforçons de livrer vos produits en temps voulu. Notre délai de livraison standard pour les PCBs flexibles est généralement de [insérez le délai de livraison typique, par ex., 4-6 semaines], selon la complexité de votre commande. Si vous avez des exigences urgentes, nous proposons également des options accélérées pour garantir que vous receviez vos produits à temps.
Chez South-Electronic, nous offrons des solutions flexibles pour répondre à vos besoins commerciaux. La quantité minimale de commande pour nos PCBs flexibles est de [insérez la quantité minimale de commande, par ex., 10 unités], ce qui vous permet de passer des commandes adaptées aux prototypes à petite échelle et aux grandes séries de production.
Oui, nous fournissons un soutien complet tout au long du processus d'expédition. Notre équipe chez South-Electronic est bien informée sur la documentation douanière et d'import/export, nous pouvons donc gérer efficacement toutes les formalités administratives. Cela vous permet de vous concentrer sur votre activité pendant que nous nous occupons de la logistique.
Envoyez-nous un message
Plus vous remplissez de détails, plus nous pourrons avancer rapidement à l’étape suivante.
Guide Complet pour PCB Flexible
Contenu
Chapitre 1

Introduction au PCB Flexible
Les PCB flexibles sont des circuits électriques capables de se plier et de s’adapter à la forme de différents appareils. Ils se distinguent des PCB rigides traditionnels car ils utilisent des substrats flexibles, ce qui les rend légers et adaptables. Ces circuits peuvent comporter plusieurs couches, permettant ainsi des conceptions complexes tout en maintenant la flexibilité.
C’est important car cela permet d’intégrer plus de composants dans un espace réduit, ce qui est essentiel dans l’électronique actuelle. Les PCB flexibles sont utilisés dans de nombreux appareils, tels que les téléphones, les dispositifs médicaux et les voitures. À mesure que la technologie progresse, la demande pour des produits électroniques plus performants va croître, et les PCB flexibles seront la solution pour répondre à ces besoins. C’est pourquoi ils sont si populaires auprès des ingénieurs et des fabricants.
Chapitre 2
Avantages des PCBs Flexibles
Les PCBs flexibles offrent de nombreux avantages qui en font un choix privilégié dans de nombreuses applications. Voici quelques avantages clés :
Gain d’Espace
L’un des principaux avantages des PCBs flexibles est leur capacité à économiser de l’espace. Leur nature flexible leur permet d’être acheminés dans des espaces restreints et autour d’obstacles au sein d’un appareil. Cette capacité de gain d’espace est particulièrement bénéfique dans les appareils électroniques compacts, où chaque millimètre compte, permettant aux concepteurs de créer des produits plus élégants et efficaces.
Conception Légère
Les PCBs flexibles sont intrinsèquement plus légers que les circuits imprimés rigides traditionnels. L’utilisation de matériaux flexibles réduit non seulement le poids global de l’assemblage, mais contribue également à réduire les coûts de transport et à améliorer l’efficacité énergétique dans les appareils portables. Ce design léger est essentiel pour des secteurs comme l’aérospatiale et l’automobile, où la réduction de poids peut entraîner des améliorations significatives des performances.
Durabilité Accrue
Les PCBs flexibles sont conçus pour résister au stress mécanique et aux vibrations, les rendant plus durables dans les environnements exigeants. Leur capacité à se plier et à se tordre sans se casser réduit le risque de dommages dus aux mouvements et aux chocs, assurant une durée de vie plus longue pour les appareils électroniques. Cette durabilité est particulièrement importante dans des applications comme les dispositifs médicaux et les systèmes automobiles, où la fiabilité est primordiale.
Flexibilité dans la Conception
La polyvalence des PCBs flexibles permet des solutions de conception innovantes qui ne sont pas possibles avec des circuits rigides. Les concepteurs peuvent créer des géométries complexes et intégrer plusieurs composants sur une seule carte, réduisant ainsi le nombre de connexions nécessaires. Cette flexibilité facilite des conceptions plus compactes et permet une plus grande créativité dans le développement de produits, faisant des PCBs flexibles un choix idéal pour les technologies de pointe.
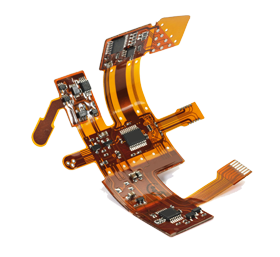
Chapitre 3

Applications Courantes des PCBs Flexibles
Électronique Grand Public
Les PCBs flexibles sont largement utilisés dans l’électronique grand public en raison de leur taille compacte et de leur adaptabilité. On les trouve dans des appareils tels que les smartphones, les tablettes et les appareils portables, où les contraintes d’espace sont cruciales. Leur capacité à s’adapter à différentes formes permet des conceptions innovantes, améliorant la fonctionnalité tout en conservant un attrait esthétique.
Dispositifs Médicaux
Dans le domaine médical, les PCBs flexibles jouent un rôle essentiel dans le développement d’équipements de diagnostic et de surveillance avancés. Ils sont couramment utilisés dans des appareils comme les moniteurs ECG portables, les pompes à insuline et les systèmes d’imagerie. La durabilité et la fiabilité des PCBs flexibles garantissent leur capacité à supporter les exigences rigoureuses des applications médicales, où la précision et la performance sont essentielles.
Industrie Automobile
L’industrie automobile repose de plus en plus sur les PCBs flexibles pour diverses applications, y compris les systèmes d’infodivertissement, les matrices de capteurs et les unités de commande électroniques. Leur nature légère et flexible contribue à une meilleure efficacité énergétique et à de meilleures performances. De plus, les PCBs flexibles sont utilisés dans les systèmes de sécurité, tels que les airbags et les systèmes de freinage antiblocage, où la fiabilité et la durabilité sont essentielles.
Aérospatiale et Défense
Dans les applications aérospatiales et de défense, les PCBs flexibles sont essentiels pour des systèmes électroniques légers, compacts et fiables. Ils sont utilisés dans les systèmes de communication par satellite, l’avionique et les équipements militaires, où la performance dans des conditions extrêmes est requise. La capacité à résister aux environnements difficiles tout en maintenant la fonctionnalité fait des PCBs flexibles un choix privilégié pour ces applications à haut risque.
Chapitre 4
Types de PCBs Flexibles
Les PCBs flexibles existent en différents types, chacun conçu pour des applications spécifiques. Connaître ces types peut vous aider à choisir celui qui convient à votre projet. Voici les principaux types de PCBs flexibles :
- PCBs Flex Simple Face
Les PCBs flex simple face ont une couche conductrice sur un côté d’un substrat flexible. Ils sont généralement utilisés dans des applications plus simples où l’espace est limité, comme dans les capteurs et les appareils compacts. Ils sont économiques et faciles à fabriquer.
- PCBs Flex Double Face
Les PCBs flex double face ont des couches conductrices sur les deux côtés du substrat, permettant des circuits plus complexes. Ils sont idéaux pour les applications nécessitant plus de connexions et de fonctionnalités, comme dans les écrans et l’électronique grand public. Ils offrent également plus de flexibilité dans le routage des signaux électriques.
- PCBs Flex Multicouche
Les PCBs flex multicouches ont plusieurs couches de chemins conducteurs séparées par des matériaux isolants. Ils permettent des conceptions complexes et une plus grande densité de circuits, ce qui les rend adaptés aux applications avancées comme les dispositifs médicaux et l’électronique haute vitesse. Ils améliorent l’intégrité du signal et réduisent les interférences électromagnétiques.
- PCBs Rigide-Flexible
Les PCBs rigide-flexible combinent des sections rigides et flexibles dans un même circuit. Ils sont parfaits pour les applications nécessitant de la stabilité dans certaines zones tout en maintenant de la flexibilité dans d’autres. On les retrouve couramment dans des appareils complexes comme les smartphones et les équipements aérospatiaux.
- Circuits Flex avec des Caractéristiques Supplémentaires
Certains PCBs flexibles sont dotés de caractéristiques spéciales, telles que des composants intégrés, des trous traversants ou des couches protectrices supplémentaires. Ces améliorations peuvent améliorer les performances, la fiabilité et la gestion thermique, ce qui les rend adaptés aux applications exigeantes.
En conclusion, les différents types de PCBs flexibles—simple face, double face, multicouche, rigide-flexible et ceux avec des caractéristiques supplémentaires—offrent des avantages uniques pour des besoins spécifiques. En choisissant le bon type, vous pouvez optimiser les performances et la fonctionnalité de vos conceptions électroniques.

Chapitre 5

Matériaux Utilisés dans les PCBs Flexibles
Les PCBs flexibles sont constitués de divers matériaux qui influencent leur performance et leur fiabilité. Pour choisir le bon PCB flexible pour votre application, il est essentiel de connaître ces matériaux. Voici les principaux :
- Matériaux de Substrat
- Polyimide (PI) : C’est le matériau de substrat le plus courant pour les PCBs flexibles car il supporte des températures élevées, résiste aux produits chimiques et est flexible. Il est idéal pour les applications en environnements difficiles.
- Polyester (PET) : Le polyester est moins cher que le polyimide, mais moins résistant. Il est utilisé dans les applications plus simples qui ne nécessitent pas de supporter des températures extrêmes. Il est flexible et utilisé dans l’électronique grand public.
- Matériaux Conducteurs
- Cuivre : Le cuivre est le matériau standard pour les traces conductrices dans les PCBs flexibles. Il est hautement conducteur et facile à travailler lors de la fabrication. Vous pouvez utiliser différentes épaisseurs de cuivre en fonction du courant nécessaire pour votre application.
- Argent : Dans certaines applications à haute fréquence ou haute performance, l’argent est utilisé car il est encore plus conducteur que le cuivre. Cependant, il est plus coûteux et donc moins courant.
- Adhésifs et Agents de Liaison
- Adhésifs Acryliques : Ils sont utilisés pour lier les couches conductrices au substrat. Ils offrent une bonne adhérence et flexibilité. Ils sont utilisés dans les PCBs flexibles multicouches.
- Adhésifs Époxy : Les adhésifs époxy sont solides et peuvent supporter des températures élevées. Ils sont utilisés dans les applications nécessitant une grande résistance et une haute résistance thermique.
- Revêtements Protecteurs
- Revêtements Conformes : Ces revêtements protègent le PCB de l’humidité, de la poussière et des produits chimiques, le rendant plus durable. Vous pouvez les ajouter comme couche supplémentaire aux PCBs flexibles pour qu’ils fonctionnent bien dans différents environnements.
- Finitions de Surface : Vous pouvez ajouter une finition ENIG (Nickel Chimique Immersion Or) ou HASL (Nivellement de Soudure à l’Air Chaud) aux traces de cuivre pour les rendre plus faciles à souder et plus résistantes à la corrosion.
En résumé, les matériaux que vous choisissez pour votre PCB flexible—tels que les substrats en polyimide ou polyester, les conducteurs en cuivre ou argent, et les adhésifs appropriés—font une grande différence dans leur fonctionnement et leur durabilité. En connaissant ces matériaux, vous pouvez faire des choix judicieux qui répondent à vos besoins.
Chapitre 6
Considérations de Conception pour les PCBs Flexibles
La conception des circuits imprimés flexibles (PCBs flexibles) est différente de celle des PCBs rigides traditionnels. En suivant quelques lignes directrices essentielles de conception, vous pouvez garantir des performances et une fiabilité optimales dans vos applications. Voici quelques points importants à considérer :
- Rayon de Courbure
Le rayon de courbure est un aspect crucial dans la conception des PCBs flexibles. Il fait référence au rayon minimum qu’un PCB flexible peut atteindre sans risque de dommage. Il est recommandé d’utiliser un rayon de courbure plus grand pour éviter le stress sur le circuit. En règle générale, le rayon de courbure doit être d’au moins 10 fois l’épaisseur du matériau du substrat.
- Largeur et Espacement des Traces
Une largeur et un espacement appropriés des traces sont importants pour les performances électriques. Des traces plus larges peuvent supporter des courants plus élevés, tandis que des traces plus étroites économisent de l’espace. Cependant, un espacement suffisant est nécessaire pour éviter les courts-circuits et garantir la fabricabilité. Envisagez d’utiliser un logiciel de conception pour simuler les performances des traces dans différentes conditions.
- Empilage des Couches
Lors de la conception de PCBs flexibles multicouches, il est nécessaire de planifier soigneusement l’empilement des couches. Assurez-vous que les couches flexibles sont placées de manière à fournir la flexibilité nécessaire tout en maintenant l’intégrité mécanique. Équilibrez le design pour optimiser les performances électriques et les caractéristiques physiques.
- Placement des Composants
Le placement stratégique des composants est important pour un routage efficace des signaux et une minimisation des interférences. Évitez de placer des composants dans des zones qui subiront beaucoup de flexion. Envisagez également d’utiliser des dispositifs montés en surface (SMD) pour économiser de l’espace et améliorer la fiabilité.
- Caractéristiques de Détente de Contrainte
L’inclusion de caractéristiques de détente de contrainte, comme des découpes ou des fentes, peut aider à atténuer le stress mécanique lors de la flexion et des mouvements. Ces caractéristiques sont particulièrement importantes dans les applications nécessitant une flexibilité élevée, car elles peuvent améliorer considérablement la durée de vie du PCB flexible.
- Outils de Logiciel de Conception
Utilisez des logiciels de conception avancés spécifiquement adaptés aux applications de PCBs flexibles. Des outils comme Altium Designer, Eagle ou KiCAD peuvent vous aider à créer des conceptions précises, vous permettant de simuler et d’analyser les performances des circuits en temps réel. Ces outils facilitent également la mise en œuvre des règles et des lignes directrices de conception, garantissant la fabricabilité.
- Prototypage et Tests
Avant de passer en production, créez des prototypes pour tester la fonctionnalité et la durabilité de votre conception. Testez votre conception dans des conditions réelles pour identifier les problèmes potentiels dès le départ. Répéter la conception en fonction des retours de test peut conduire à des améliorations en termes de performance et de fiabilité.
En conclusion, prêter attention au rayon de courbure, à la largeur des traces, à l’empilement des couches, au placement des composants, aux caractéristiques de détente de contrainte et à l’utilisation de logiciels de conception spécialisés est essentiel lors de la conception de PCBs flexibles. En tenant compte de ces éléments, vous pouvez créer des circuits flexibles efficaces et fiables adaptés à vos applications spécifiques.
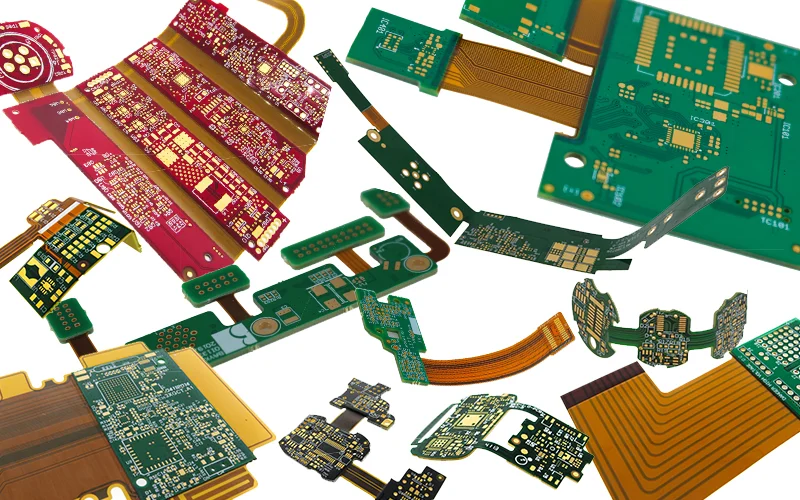
Chapitre 7
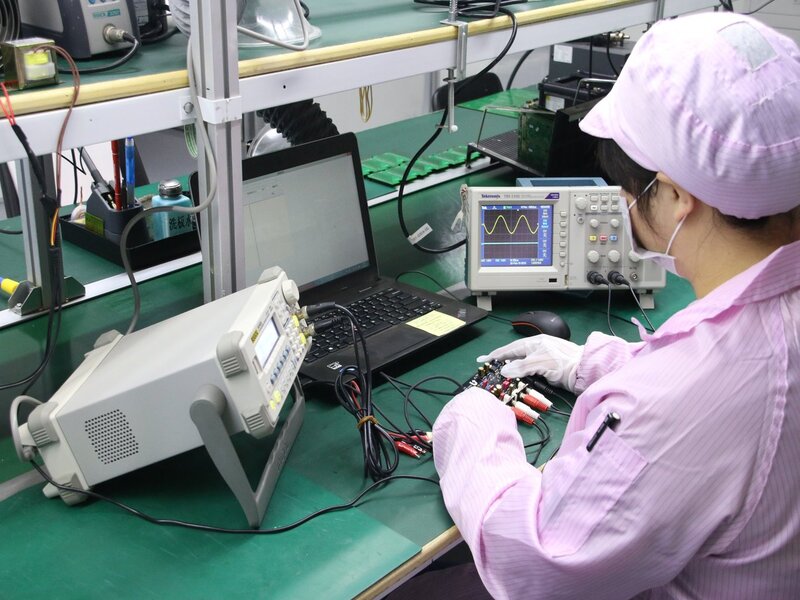
Processus de Fabrication des PCBs Flexibles
La fabrication des circuits imprimés flexibles (PCBs flexibles) implique plusieurs étapes essentielles qui garantissent une production de haute qualité. Comprendre ces processus vous aidera à apprécier la complexité et la précision nécessaires pour créer des PCBs flexibles fiables. Voici un aperçu des étapes clés de la fabrication des PCBs flexibles :
- Conception et Mise en Page
La première étape de la fabrication des PCBs flexibles est la phase de conception et de mise en page. Les concepteurs créent la mise en page du circuit imprimé à l’aide de logiciels spécialisés, en veillant à ce que tous les composants, les traces et les couches soient optimisés pour la performance et la flexibilité. Cette étape comprend également la définition des spécifications pour les matériaux et les dimensions.
- Préparation des Matériaux
Une fois la conception finalisée, l’étape suivante consiste à préparer les matériaux du substrat. Des substrats courants comme le polyimide ou le polyester sont découpés aux dimensions requises. Les feuilles de cuivre sont ensuite laminées sur le substrat à l’aide d’adhésifs, formant la base des chemins conducteurs.
- Photolithographie
À cette étape, une couche de résine photosensible est appliquée sur le substrat plaqué de cuivre. Le design du PCB est ensuite transféré sur le substrat par des techniques de photolithographie, où la lumière ultraviolette (UV) expose la résine photosensible selon le motif du circuit. Après exposition, le substrat est développé, enlevant la résine non exposée et laissant le motif en cuivre souhaité.
- Gravure
Les zones de cuivre exposées sont soumises à un processus de gravure, où des produits chimiques enlèvent le cuivre indésirable, ne laissant que les circuits souhaités. Cette étape est cruciale pour créer des chemins conducteurs précis sur le PCB flexible.
- Lamination des Couches (pour les PCBs Multicouches)
Pour les PCBs flexibles multicouches, plusieurs couches de substrat et de circuit sont alignées et laminées ensemble sous pression et chaleur. Ce processus garantit l’adhérence efficace des couches, créant une structure multicouche robuste tout en maintenant la flexibilité.
- Perçage et Placage
Ensuite, des trous pour les vias et le montage des composants sont percés dans le PCB flexible. Ces trous sont ensuite plaqués avec du cuivre pour créer des connexions électriques entre les couches. Cette étape est essentielle pour garantir l’intégrité du signal entre les couches.
- Finition de Surface
Après le perçage, une finition de surface est appliquée pour protéger les traces de cuivre et améliorer la soudabilité. Les finitions de surface courantes incluent le nickel chimique à immersion d’or (ENIG) et le nivellement de soudure à air chaud (HASL), offrant une excellente protection contre l’oxydation.
- Tests et Inspection
Le contrôle qualité est essentiel dans la fabrication des PCBs flexibles. Divers tests, y compris des tests électriques et des inspections visuelles, sont effectués pour s’assurer que les PCBs répondent aux critères de performance spécifiés. Cette étape permet d’identifier les défauts tôt dans le processus, réduisant le risque de problèmes lors de l’utilisation.
- Découpe et Emballage
Une fois les tests terminés, les PCBs flexibles sont découpés dans leurs formes finales. Ils sont ensuite emballés de manière appropriée pour les protéger lors du transport et de la manipulation, garantissant leur arrivée en parfait état.
En résumé, la fabrication des PCBs flexibles implique plusieurs étapes critiques, y compris la conception, la préparation des matériaux, la photolithographie, la gravure, la lamination, le perçage, le placage, la finition de surface, les tests et l’emballage. Chaque étape nécessite précision et attention aux détails pour produire des PCBs flexibles de haute qualité répondant aux exigences des applications électroniques modernes.
Chapitre 8
Défis et Limitations des PCBs Flexibles
Les PCBs flexibles offrent de nombreux avantages, mais ils présentent également des défis et des limitations que les concepteurs et les fabricants doivent prendre en compte. Comprendre ces aspects vous aidera à prendre des décisions éclairées lors du choix d’utiliser des PCBs flexibles. Voici certains des principaux défis :
- Complexité de la Fabrication
La fabrication des PCBs flexibles est plus complexe que celle des PCBs rigides. Cette complexité peut entraîner des délais de production plus longs et des coûts de production plus élevés, surtout pour les commandes de faible volume. Les fabricants ont besoin d’équipements spécialisés et d’une expertise pour répondre aux exigences uniques de la production de PCBs flexibles.
- Considérations de Coût
Bien que les PCBs flexibles puissent être rentables pour les applications de grande production, les coûts initiaux peuvent être bien plus élevés que ceux des PCBs rigides traditionnels. Pour les petites séries de production ou les prototypes, le coût des matériaux et de la fabrication peut ne pas justifier les avantages de la technologie flexible.
- Options de Composants Limitées
Tous les composants électroniques ne sont pas adaptés aux PCBs flexibles. Certains composants peuvent être trop grands ou rigides pour s’intégrer facilement. Cette limitation peut restreindre vos options de conception et nécessiter une sélection minutieuse des composants pour garantir la compatibilité.
- Défis de Manipulation et d’Assemblage
Les PCBs flexibles sont plus délicats que les cartes rigides et peuvent être facilement endommagés lors de la manipulation et de l’assemblage. Des procédures de manipulation et de soin appropriées sont essentielles pour éviter des problèmes comme les fissures ou le délaminage, qui peuvent affecter les performances et la fiabilité.
- Sensibilité Environnementale
Certains matériaux utilisés dans les PCBs flexibles, comme le polyimide, peuvent avoir des limites en matière d’exposition aux conditions environnementales extrêmes. Bien que les PCBs flexibles soient conçus pour être durables, ils peuvent être affectés par des facteurs tels que l’humidité et les fluctuations de température s’ils ne sont pas correctement gérés.
- Difficultés de Test et de Validation
Tester les PCBs flexibles peut être plus difficile que tester des cartes rigides en raison de leur flexibilité et de la complexité de leurs conceptions. Assurer une qualité et des performances cohérentes nécessite des protocoles de test rigoureux, ce qui peut prolonger le délai global du projet.
- Réparabilité Limitée
Une fois qu’un PCB flexible est assemblé dans un appareil, il peut être difficile de le réparer. La flexibilité et l’intégration des composants peuvent rendre difficile le remplacement ou la réparation de pièces individuelles sans compromettre l’ensemble de la carte.
En résumé, bien que les PCBs flexibles offrent des avantages significatifs, il est important de prendre en compte les défis tels que la complexité de fabrication, les considérations de coût, les options de composants limitées, les défis de manipulation, la sensibilité environnementale, les difficultés de test et la réparabilité limitée. En comprenant ces limitations, vous pouvez faire des choix éclairés et traiter efficacement les problèmes potentiels dans vos projets.
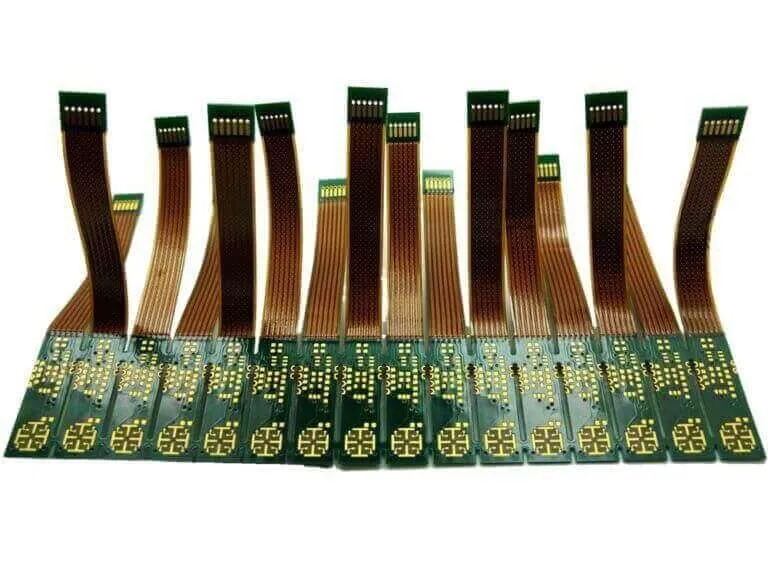
Chapitre 9

Meilleures Pratiques pour l'Assemblage des PCBs Flexibles
L’assemblage des PCBs flexibles nécessite une attention aux détails pour garantir la fiabilité et la performance. Voici quelques meilleures pratiques à suivre lors du processus d’assemblage :
Techniques de Soudure
- Choisir le Bon Alliage de Soudure : Utilisez des techniques de soudure à basse température pour éviter d’endommager le substrat flexible. Les soudures sans plomb sont souvent préférées.
- Soudure par Refusion : Cette technique est couramment utilisée pour les dispositifs montés en surface (SMD) sur les PCBs flexibles. Assurez-vous que le profil de température est soigneusement contrôlé pour éviter de surchauffer les matériaux flexibles.
- Soudure Vague : Pour les composants traversants, la soudure vague peut être efficace. Cependant, il est crucial de choisir une vague douce pour minimiser les contraintes sur le PCB flexible.
- Soudure Manuelle : Lors de la soudure manuelle, utilisez un fer à souder à pointe fine pour assurer la précision. Évitez une exposition excessive à la chaleur et réduisez le temps de soudure autant que possible.
- Application de Flux : Utilisez un flux approprié pour améliorer l’adhésion de la soudure et garantir de bonnes connexions. Évitez un excès de flux, ce qui pourrait entraîner une accumulation de résidus et affecter la performance.
Tests et Assurance Qualité
- Tests Électriques : Réalisez des tests électriques approfondis pour vérifier la fonctionnalité de toutes les connexions. Les méthodes courantes incluent les tests en circuit (ICT) et les tests fonctionnels.
- Inspection Visuelle : Mettez en place un processus d’inspection visuelle pour identifier les défauts tels que les composants mal alignés, les ponts de soudure ou les traces endommagées. Les caméras haute résolution peuvent aider dans ce processus.
- Tests de Flexion : Effectuez des tests de flexion pour évaluer l’intégrité mécanique du PCB. Les tests de flexion doivent simuler les conditions d’utilisation prévues pour garantir la fiabilité dans le temps.
- Cyclage Thermique : Soumettez les PCBs flexibles assemblés à des tests de cycles thermiques pour évaluer leur performance sous des conditions de température variables. Cela aide à identifier les faiblesses potentielles dans la conception.
- Documentation et Traçabilité : Maintenez une documentation détaillée tout au long du processus d’assemblage, y compris les résultats des tests et les enregistrements d’inspection. Cette pratique garantit la traçabilité et la responsabilité.
Emballage et Manipulation
- Utiliser un Emballage Approprié : Les PCBs flexibles doivent être emballés dans des matériaux antistatiques pour éviter les dommages dus aux décharges électrostatiques (ESD). Utilisez des matériaux de rembourrage pour les protéger des contraintes physiques pendant le transport.
- Étiquetage : Étiquetez clairement tous les emballages avec des instructions de manipulation et toute exigence spécifique de stockage (par ex., température et humidité).
- Formation pour la Manipulation : Fournissez une formation au personnel impliqué dans la manipulation et l’assemblage des PCBs flexibles. Soulignez l’importance d’une manipulation soigneuse pour éviter les dommages.
- Conditions de Stockage : Stockez les PCBs flexibles dans des environnements contrôlés pour éviter l’exposition à des températures et à une humidité extrêmes. Utilisez des sacs à barrière d’humidité si nécessaire pour protéger contre l’absorption d’humidité.
- Éviter les Contraintes Mécaniques : Manipulez les PCBs flexibles avec précaution pour éviter les contraintes mécaniques. Évitez de plier ou de tordre excessivement les cartes pendant l’assemblage ou l’emballage.
En conclusion, suivre les meilleures pratiques en techniques de soudure, tests et assurance qualité, et emballage et manipulation appropriés peut améliorer considérablement la fiabilité et la performance des PCBs flexibles. En priorisant ces pratiques, les fabricants peuvent s’assurer que leurs PCBs flexibles répondent aux exigences des applications électroniques modernes.
Chapitre 10
Tendances Futures de la Technologie des PCBs Flexibles
Innovations dans les Matériaux
À l’avenir, les PCBs flexibles seront fabriqués à partir de matériaux encore plus flexibles, durables et conducteurs thermiques. Les chercheurs développent de nouveaux matériaux, tels que le polyimide ultra-fin et les matériaux biodégradables, pour répondre aux objectifs de durabilité. Ils améliorent également les encres conductrices et les composants flexibles pour permettre des conceptions encore plus complexes.
Applications Émergentes
Les PCBs flexibles sont utilisés dans de nouvelles applications, telles que la technologie portable, les écrans flexibles et l’Internet des objets (IoT). À mesure que la demande de produits plus petits et plus légers augmente, des industries comme la santé, l’automobile et l’électronique grand public dépendront de plus en plus des PCBs flexibles pour créer des produits innovants. Cela stimulera davantage la recherche et le développement dans ce domaine.
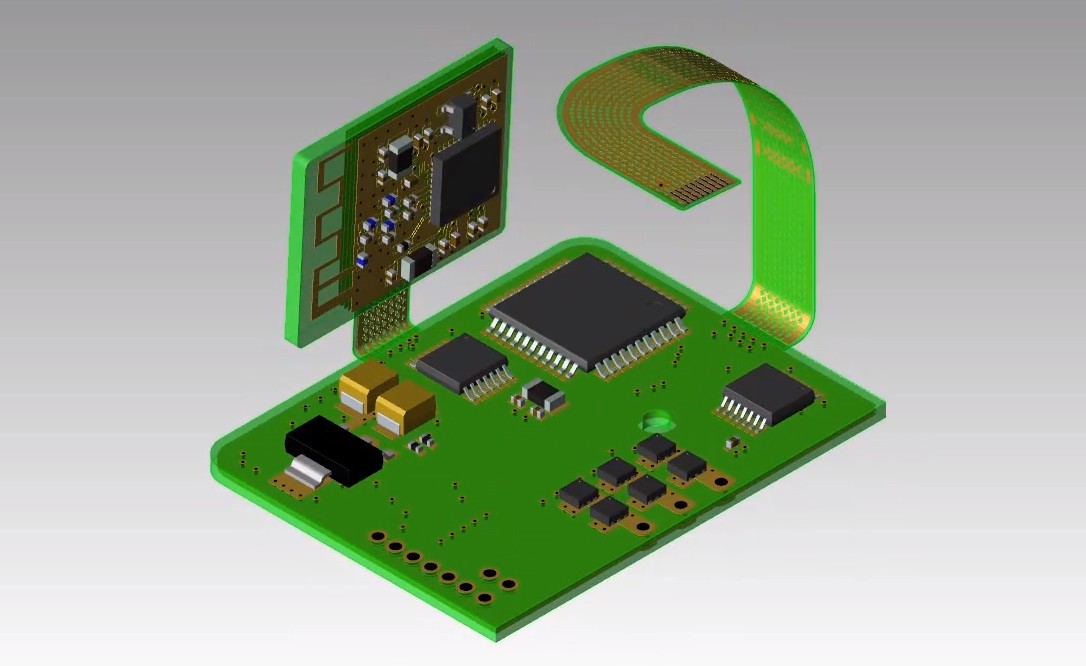
Contactez-Nous
Où Sommes-Nous ?
Parc Industriel, No. 438 Route Donghuan, No. 438, Shajing Donghuan Road, District Bao'an, Shenzhen, Guangdong, Chine
4ème étage, Bâtiment Zhihui Créatif, No. 2005 Route Xihuan, Shajing, District Baoan, Shenzhen, Chine
CHAMBRE A1-13, ÉTAGE 3, CENTRE INDUSTRIEL YEE LIM, 2-28 RUE KWAI LOK, KWAI CHUNG HK
service@southelectronicpcb.com
Téléphone : +86 400 878 3488
Envoyez-nous un message
Plus vous remplissez de détails, plus nous pourrons avancer rapidement à l’étape suivante.
