Fournisseur de PCB HDI
South-Electronic
Choisissez South-Electronic pour la meilleure qualité, fiabilité et valeur ajoutée dans vos besoins en PCB. Faites l'expérience de la différence avec nos services complets pour PCB HDI – de la conception à la production, nous garantissons précision, durabilité et conformité aux normes les plus strictes de l'industrie.
Votre partenaire fiable pour des PCB HDI de haute qualité
Bienvenue chez South-Electronic, votre source de PCB HDI de haute qualité, réputée pour sa technologie de connexion haute densité et ses capacités de miniaturisation.
Faites confiance à South-Electronic pour une qualité et une constance de haut niveau dans vos projets technologiques. Nos PCB HDI améliorent les performances de vos appareils grâce à une connectivité exceptionnelle et un espace réduit. Collaborez avec nous pour atteindre l’innovation et le succès dans votre domaine.

Type I PCB HDI
Celui-ci possède des microvias ultra-fines avec des diamètres inférieurs à 75 microns et des largeurs/isolation de conducteur inférieures à 50 microns. Il est parfait pour les dispositifs électroniques de nouvelle génération, comme les équipements médicaux avancés et les télécommunications à haute fréquence.

Type II PCB HDI
Celui-ci est basé sur le Type I en ajoutant des vias borgnes et enterrés pour un meilleur routage. Il convient aux dispositifs électroniques avancés nécessitant des connexions multicouches complexes et une densité plus élevée.
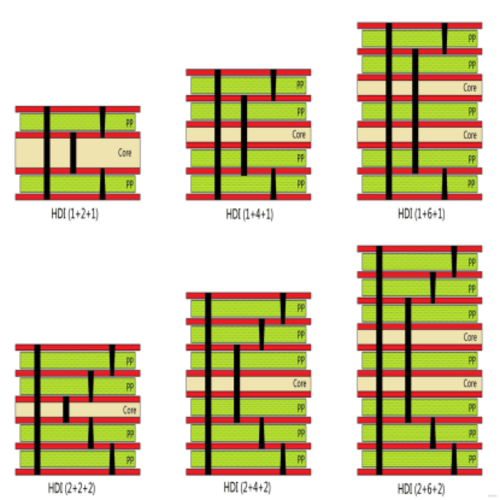
Type III PCB HDI
Celui-ci comporte au moins deux couches de microvias sur un ou les deux côtés du noyau, en utilisant des vias borgnes et enterrés. Il est idéal pour les applications haute performance, comme les smartphones et l'informatique avancée, car il offre un routage supérieur.
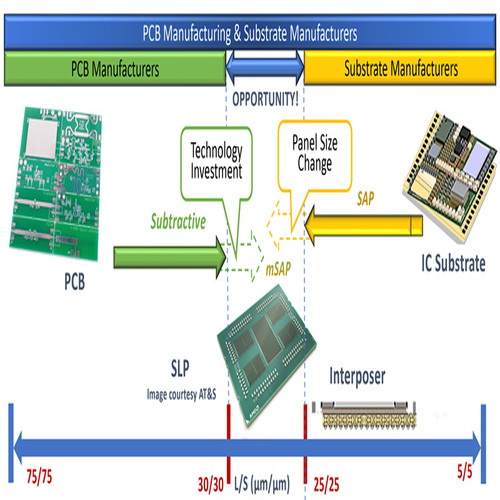
PCB Ultra HDI
Celui-ci possède des microvias ultra-fines avec des diamètres inférieurs à 75 microns et des largeurs/isolation de conducteur inférieures à 50 microns. Il est parfait pour les dispositifs électroniques de nouvelle génération, comme les équipements médicaux avancés et les télécommunications à haute fréquence.
Pourquoi choisir South-Electronic ?
Choisissez South-Electronic pour notre expertise dans les PCB HDI personnalisés et de haute qualité pour une gamme d’applications. Notre équipe possède une vaste expérience, garantissant une qualité supérieure à des prix compétitifs et un service exceptionnel du début à la fin.
-
Flexibilité dans les commandes
Vous pouvez commander à partir d’une seule pièce pour répondre exactement à vos besoins en PCB HDI.
Profitez de la flexibilité pour tester de nouveaux designs ou répondre aux exigences de petites séries sans tracas. -
Équipe expérimentée
Vous bénéficiez de notre décennie d’expertise dans l’industrie.
Nous comprenons vos défis et vous proposons des solutions expertes et un soutien fiable à chaque étape. -
Service complet
Vous obtenez une satisfaction complète avec notre large gamme d'équipements.
Notre service complet garantit que vous recevez tout ce dont vous avez besoin pour une expérience sans accroc. -
Livraison rapide
Vous profitez de nos délais de production rapides et efficaces.
Nous priorisons la livraison ponctuelle pour respecter vos délais et garder vos projets sur la bonne voie. -
Satisfaction garantie
Nous vous assurons qualité et communication claire avec notre certification ISO9001.
Votre satisfaction est notre priorité, et nous nous engageons à dépasser vos attentes à chaque commande.
Projet similaire que nous avons réalisé
Avis des clients
Questions fréquentes
Questions les plus populaires
South-Electronic propose une large gamme de configurations de PCB HDI, y compris des conceptions multicouches, des microvias, des vias borgnes et enterrés, ainsi que des trous percés au laser. Nous sommes spécialisés dans la fourniture de solutions de haute densité adaptées aux besoins spécifiques de votre projet, assurant des performances optimales pour les dispositifs électroniques complexes.
Chez South-Electronic, nous appliquons des mesures strictes de contrôle de qualité tout au long du processus de fabrication. Nos PCB HDI subissent des tests électriques complets, une inspection optique automatisée (AOI) et une inspection aux rayons X pour détecter d'éventuels défauts. Nous sommes également certifiés ISO et UL, garantissant que tous les produits respectent les normes internationales de qualité.
Oui, nous prenons en charge les commandes de petits lots pour les prototypes. Nous comprenons l'importance des tests et de la validation dans la phase de développement et offrons des options de fabrication flexibles pour répondre à vos besoins de prototypage sans exigences minimales importantes.
Le délai de production standard pour les PCB HDI chez South-Electronic est généralement de 10 à 20 jours, en fonction de la complexité du design et de la quantité de la commande. Nous proposons également des options pour les projets urgents avec des délais de livraison plus rapides.
Oui, nous proposons des services de prototypage rapide et des commandes en urgence. Pour les projets sensibles au temps, nous offrons des options de fabrication rapide pour garantir que vos prototypes et commandes de production soient terminés dans les plus brefs délais, sans compromettre la qualité.
Envoyez-nous un message
Plus vous remplissez de détails, plus nous pourrons avancer rapidement à l’étape suivante.
Le Guide Complet du PCB HDI
Contenu
Chapitre 1
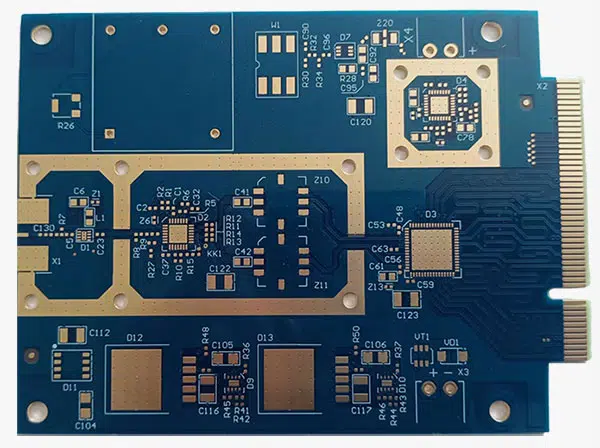
Introduction au PCB HDI
Qu’est-ce qu’un PCB HDI ?
Les PCB HDI (High-Density Interconnect) sont des cartes de circuit imprimé avancées conçues pour accueillir une densité de câblage plus élevée par unité de surface, utilisant des traces plus fines et des microvias. Cela permet un routage plus complexe et une intégration de composants dans un design compact, rendant la technologie HDI idéale pour les applications à haute performance.
Pourquoi est-ce important et où est-ce utilisé ?
Les PCB HDI sont essentiels dans l’électronique moderne, alimentant les appareils nécessitant un traitement plus rapide, une efficacité accrue et des formats plus compacts. Ils sont largement utilisés dans les smartphones, ordinateurs portables, dispositifs médicaux, systèmes automobiles et équipements de télécommunications avancés. Alors que les exigences technologiques continuent de croître, les PCB HDI permettent aux fabricants de répondre aux besoins de solutions électroniques plus compactes, efficaces et fiables.
Chapitre 2
Types de Configurations de PCB HDI
Différents Types de Configurations de PCB HDI
Il existe différentes manières de configurer les PCB HDI, en fonction de la complexité et des fonctionnalités nécessaires. La configuration de base est un design HDI à 1 étape, qui comporte une seule couche de microvias offrant une connectivité efficace pour des applications moins exigeantes, comme les petits appareils électroniques grand public. Un design HDI à 2 étapes se construit sur cette base en ajoutant une autre couche de microvias ou des vias décalés, augmentant la densité de la carte et permettant un routage des signaux plus complexe. La configuration la plus avancée est un design HDI multi-étapes, utilisant des vias empilés ou décalés sur plusieurs couches pour atteindre une densité maximale et gérer des circuits hautement complexes. Ces configurations sont essentielles pour des applications avancées telles que l’informatique haute vitesse, les télécommunications et les équipements militaires, où la performance, la fiabilité et l’optimisation de l’espace sont cruciales.
Explication des Microvias, Vias Borgnes et Vias Enterrés
La technologie HDI utilise des types de vias avancés pour augmenter considérablement les options de routage et la connectivité entre les couches du PCB. Les microvias sont de très petits trous percés au laser, généralement inférieurs à 0,15 mm de diamètre. Ils connectent les couches adjacentes et permettent un placement dense des composants ainsi qu’une intégrité élevée des signaux. Les vias borgnes connectent la couche extérieure du PCB à une ou plusieurs couches internes sans traverser toute la carte, ce qui économise de l’espace sur la surface du PCB tout en maintenant une efficacité de routage. Les vias enterrés ne connectent que les couches internes et sont complètement cachés de l’extérieur, permettant aux concepteurs de créer des dispositions plus complexes sans sacrifier l’espace de surface pour des composants supplémentaires.
Avantages des Différentes Configurations de HDI
La configuration que vous choisissez pour votre PCB HDI dépend de l’application spécifique et des exigences de performance. Les designs HDI à 1 étape sont économiques et parfaits pour des produits nécessitant des performances modérées, comme les appareils portables ou les appareils électroniques grand public d’entrée de gamme. Les configurations HDI à 2 étapes et multi-étapes permettent une densité de composants beaucoup plus élevée et des circuits plus sophistiqués, nécessaires pour des applications de pointe comme les smartphones, les tablettes, les appareils médicaux et l’électronique automobile. De plus, l’utilisation des microvias, vias borgnes et vias enterrés optimise l’espace de la carte, réduit les interférences de signal, améliore la gestion thermique et augmente les performances globales, en particulier dans les appareils nécessitant un transfert de données à haute vitesse et une miniaturisation, comme les équipements de télécommunications, les systèmes aérospatiaux et les appareils informatiques haut de gamme. Grâce à l’utilisation de ces différentes configurations et technologies de vias, les PCB HDI offrent une flexibilité de conception inégalée, des performances améliorées et des avantages en matière d’économie d’espace, essentiels pour l’électronique moderne.
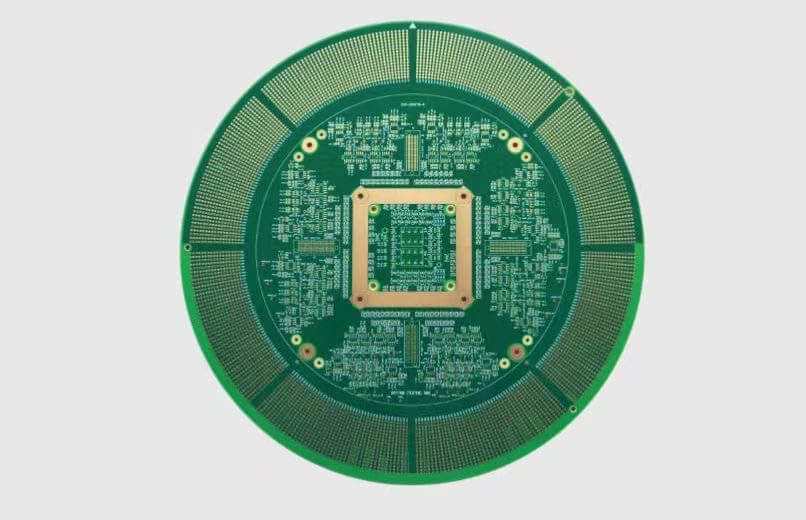
Chapitre 3

Processus de Fabrication de PCB HDI
La fabrication de PCB HDI est un processus complexe qui comprend de nombreuses étapes et des technologies avancées. L’objectif est de créer un design haute densité multicouche capable de répondre aux exigences croissantes de miniaturisation, de vitesse et de performance des électroniques modernes. Voici un aperçu détaillé des étapes et des technologies clés utilisées pour fabriquer des PCB HDI.
Processus de Fabrication Étape par Étape
Le processus de fabrication des PCB HDI commence par la formation d’une couche de base, qui constitue la fondation des autres couches. Des couches supplémentaires sont ajoutées par laminage et gravure pour créer des chemins de circuits complexes. Ensuite, des technologies avancées de vias, comme les microvias, les vias borgnes et les vias enterrés, sont utilisées pour connecter les couches. Une fois les vias créés, la carte passe par des étapes de perçage, de dépôt de cuivre et de finition de surface. Elle est ensuite inspectée et testée pour s’assurer qu’elle répond aux spécifications et aux normes de qualité avant d’être envoyée au client.
- Formation de la couche de base : Le processus commence par la création des couches de base du PCB, où les couches de cuivre et de diélectrique sont laminées ensemble.
- Perçage au laser : Les microvias sont réalisées par perçage au laser de haute précision. Il s’agit d’une étape cruciale dans la fabrication des PCB HDI, car elle permet de créer des trous très petits (généralement inférieurs à 150 microns) reliant les couches internes et externes.
- Dépôt de cuivre et placage : Après le perçage des vias, la carte passe par un dépôt de cuivre, où une fine couche de cuivre est appliquée sur les parois des vias percés. Cette étape garantit la conductivité électrique entre les couches. Ensuite, toute la surface est recouverte de cuivre par électroplacage pour former les pistes conductrices.
- Laminage : Les multiples couches du PCB sont empilées et collées ensemble par laminage. Cela implique l’application de chaleur et de pression pour lier les différentes couches de cuivre et de matériau isolant, formant une structure multicouche essentielle aux designs haute densité.
- Gravure et Formation des Circuits : Les couches de cuivre sont gravées sélectivement pour créer le motif de circuit souhaité. Il s’agit d’une étape cruciale pour créer les chemins de signal sur le PCB.
- Finition de Surface et Application du Masque de Soudure : Un masque de soudure est appliqué pour protéger les pistes de cuivre et éviter les courts-circuits lors de la soudure des composants. Ensuite, une finition de surface, comme ENIG (Nickel Immersion Or) ou HASL (Nivellement à l’air chaud), est appliquée pour améliorer la soudabilité et prévenir l’oxydation.
- Inspection et Test : Le produit final est soigneusement testé, incluant une inspection optique automatisée (AOI), des tests électriques et parfois une inspection aux rayons X, pour s’assurer que toutes les connexions fonctionnent et que le PCB respecte les spécifications de conception.
Technologies Utilisées
La fabrication de PCB HDI repose sur plusieurs technologies avancées permettant une haute précision :
- Perçage au laser : Utilisé pour créer des microvias, essentiels à la conception HDI haute densité. Le perçage au laser permet de créer des vias extrêmement petits que les perceuses mécaniques ne peuvent pas réaliser.
- Laminage : Ce processus lie les multiples couches de cuivre et de matériau isolant, créant les structures multicouches des PCB HDI. Le laminage garantit que la carte est mécaniquement solide et stable.
- Placage : Le placage électrolytique est utilisé pour appliquer du cuivre sur les vias et les pistes, garantissant une bonne connexion électrique entre les couches. De plus, des finitions de surface spéciales, comme ENIG ou OSP (Conservateur de Soudabilité Organique), sont appliquées pour rendre la carte plus durable et plus facile à souder.
Matériaux Clés Utilisés dans la Fabrication de PCB HDI
Le choix des matériaux est important pour la performance et la fiabilité des PCB HDI :
- Feuille de cuivre : Le cuivre est utilisé pour créer les pistes conductrices et les vias dans le PCB. Sa haute conductivité électrique en fait un excellent choix pour assurer un bon fonctionnement des signaux.
- Matériaux diélectriques : Des matériaux comme le FR-4 (un stratifié en époxy renforcé de verre) sont couramment utilisés comme couches isolantes entre les couches de cuivre. Pour des designs plus avancés, des matériaux ayant une stabilité thermique plus élevée, comme le polyimide, peuvent être utilisés.
- Préimprégné et Stratifiés : Ils sont importants pour lier les couches ensemble. Le préimprégné (un tissu en verre enduit de résine) est placé entre les couches de cuivre lors du laminage pour garantir la solidité mécanique de la carte et l’isolation électrique.
- Masque de Soudure : Une couche de protection est appliquée sur les pistes de cuivre pour éviter l’oxydation et les courts-circuits pendant l’assemblage.
- Finitions de Surface : Des finitions courantes comme ENIG, HASL ou OSP sont utilisées pour protéger le cuivre exposé et faciliter la soudure des composants.
En conclusion, la fabrication des PCB HDI est un processus hautement sophistiqué nécessitant un contrôle minutieux de chaque étape et l’utilisation de matériaux et de technologies avancés. La combinaison de perçage au laser, de laminage multicouche et de matériaux haute performance permet de fabriquer des cartes compactes et haute densité essentielles pour les dispositifs électroniques modernes.
Chapitre 4
Avantages des PCB HDI
Les PCB HDI offrent de nombreux avantages par rapport aux conceptions de PCB traditionnelles, les rendant essentielles dans l’électronique moderne où l’espace, la performance et l’efficacité sont cruciaux. Voici les principaux avantages qui font de la technologie HDI le choix préféré pour des dispositifs haute performance, compacts et fiables :
Augmentation de la Densité et Intégration des Composants
L’un des principaux avantages des PCB HDI est leur capacité à prendre en charge une densité de composants beaucoup plus élevée que les PCB standard. En utilisant des microvias, des vias borgnes et des vias enterrés, les PCB HDI peuvent intégrer davantage de composants dans un espace réduit. Cela permet un routage complexe, surtout dans les conceptions multicouches, permettant aux ingénieurs de créer des circuits complexes sans sacrifier l’espace ou la fonctionnalité. Cette densité accrue est cruciale pour des applications avancées telles que les smartphones, les dispositifs portables et l’électronique automobile, où l’espace disponible est limité, mais la demande en fonctionnalités est élevée.
Amélioration des Performances Électriques et de l’Intégrité du Signal
Les PCB HDI sont conçus pour gérer des signaux haute vitesse avec une perte de signal et des interférences minimales. L’utilisation de traces plus courtes et de microvias réduit la longueur du trajet du signal, minimisant les interférences électromagnétiques (EMI) et le couplage. Cela améliore l’intégrité du signal, ce qui est essentiel pour les applications haute fréquence telles que la communication 5G, les appareils IoT et les systèmes informatiques. De plus, la capacité à placer les composants plus près les uns des autres réduit les chemins électriques, diminuant la latence du signal et améliorant les performances globales. Cela est particulièrement avantageux dans les applications intensives en données, où la vitesse et la précision sont essentielles.
Format Plus Petit et Conceptions Plus Compactes
La miniaturisation des électroniques est une force motrice derrière l’adoption généralisée de la technologie HDI. Les PCB HDI permettent aux fabricants de créer des dispositifs plus petits, plus fins et plus légers sans compromettre la fonctionnalité ou la performance. En maximisant l’utilisation de l’espace disponible avec un routage à haute densité et des structures multicouches, les PCB HDI aident à réduire la taille globale des appareils. Cela est particulièrement important dans l’électronique grand public portable, comme les smartphones, les tablettes et les dispositifs portables, où les formats compacts sont non seulement souhaitables, mais nécessaires pour une utilisation pratique.
Fiabilité et Durabilité Accrues
La construction avancée des PCB HDI contribue à une fiabilité et une durabilité accrues par rapport aux PCB traditionnels. Les vias plus petits et le nombre accru de connexions permettent une meilleure gestion thermique, car la chaleur est distribuée plus uniformément sur la carte. Cela réduit le risque de points chauds et de défaillance des composants en raison de la chaleur excessive. De plus, les matériaux utilisés dans les PCB HDI, tels que les laminés haute performance et le cuivre, offrent une meilleure résistance aux contraintes mécaniques, assurant l’intégrité de la carte même dans des conditions environnementales difficiles. Cela rend les PCB HDI idéaux pour des industries comme l’automobile, l’aérospatiale et le militaire, où la durabilité et la fiabilité sont primordiales.
Transmission Plus Rapide des Signaux et Performance Améliorée
En plus d’une meilleure intégrité du signal, les PCB HDI offrent une transmission plus rapide des signaux grâce à leur conception avancée. Les trajets de signal plus courts, les délais de signal réduits et le routage optimisé contribuent à des vitesses de transmission des données plus rapides, ce qui est crucial dans les applications nécessitant une puissance de traitement élevée et un transfert de données rapide. Les PCB HDI sont largement utilisés dans des secteurs comme les télécommunications, l’informatique et l’automatisation industrielle, où le traitement des données et la communication à haute vitesse sont essentiels pour la performance du système.
Flexibilité dans le Design et Personnalisation
La flexibilité des conceptions de PCB HDI permet aux ingénieurs de créer des cartes sur mesure adaptées aux besoins spécifiques d’une application. Avec des configurations de vias en plusieurs étapes et la possibilité d’empiler les couches de différentes manières, les PCB HDI offrent plus de liberté de conception par rapport aux PCB traditionnels. Cela les rend idéaux pour créer des solutions personnalisées pour des industries spécialisées comme les dispositifs médicaux, où des conceptions uniques sont souvent nécessaires pour répondre à des normes strictes de taille et de performance. La capacité à combiner des conceptions de PCB rigides-flexibles renforce encore cette flexibilité, permettant des agencements tridimensionnels complexes pouvant s’intégrer dans des dispositifs compacts ou de formes irrégulières.
Efficacité des Coûts en Production de Gros Volume
Bien que le coût initial de production des PCB HDI puisse être plus élevé en raison des techniques de fabrication avancées, ces coûts sont compensés lors des séries de production en gros volume. La capacité à intégrer plus de fonctionnalités dans un espace réduit peut réduire le besoin de PCB, composants et interconnexions multiples, abaissant le coût global du produit final. De plus, la fiabilité et la performance accrues des PCB HDI entraînent moins de défaillances, réduisant les coûts associés aux réparations, aux retours et aux temps d’arrêt, ce qui fait de la technologie HDI une solution rentable à long terme pour les fabricants en gros volume.
En conclusion, les PCB HDI offrent une gamme d’avantages qui en font la solution de choix pour les fabricants souhaitant créer des produits électroniques haute performance, compacts et fiables. Leur capacité à prendre en charge une densité de composants accrue, à améliorer l’intégrité des signaux, à offrir des vitesses plus rapides et à renforcer la flexibilité du design les a rendus indispensables dans des secteurs tels que l’électronique grand public, les télécommunications, l’automobile, l’aérospatiale et les dispositifs médicaux. À mesure que la technologie continue d’évoluer, la demande pour les PCB HDI ne fera qu’augmenter, stimulant l’innovation et permettant le développement de systèmes électroniques plus avancés et compacts.

Chapitre 5
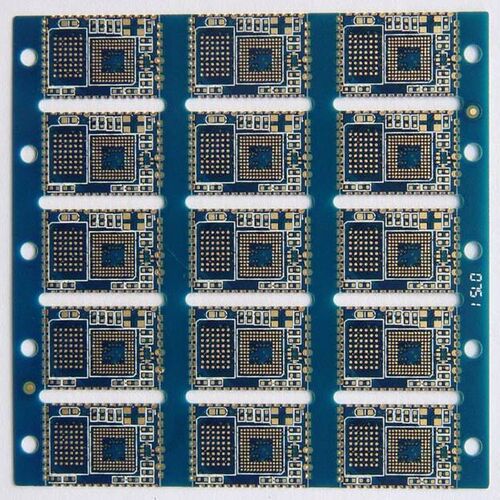
Applications Courantes des PCB HDI
Les PCB HDI sont devenus essentiels dans une large gamme d’industries en raison de leur capacité à supporter des conceptions haute densité, une performance électrique améliorée et des formats plus compacts. Leur polyvalence et leurs caractéristiques avancées les rendent idéaux pour de nombreuses applications dans divers secteurs de haute technologie. Voici quelques-unes des applications les plus courantes des PCB HDI :
Électronique Grand Public
Le marché de l’électronique grand public, en particulier pour les dispositifs tels que les smartphones, tablettes, ordinateurs portables et appareils portables, dépend fortement des PCB HDI. Avec la demande croissante pour des dispositifs plus petits, plus puissants et remplis de fonctionnalités, la technologie HDI permet aux fabricants de maximiser la fonctionnalité tout en minimisant la taille.
- Smartphones : Les PCB HDI permettent l’intégration de fonctionnalités avancées telles que les caméras haute résolution, les processeurs rapides, la connectivité 5G et une meilleure autonomie de batterie dans un espace extrêmement compact.
- Tablettes et Ordinateurs Portables : Ces dispositifs bénéficient des PCB HDI en offrant une meilleure gestion de l’espace, une meilleure gestion de l’énergie et une conception plus fine et légère.
- Appareils Portables : Des dispositifs comme les montres intelligentes et les trackers de fitness utilisent les PCB HDI pour intégrer de nombreux capteurs, processeurs et modules de communication sans fil dans un format petit et léger, offrant un confort d’utilisation avec une fonctionnalité robuste.
Dispositifs Médicaux et Équipements de Santé
Les PCB HDI jouent un rôle crucial dans le développement des dispositifs médicaux, où la précision, la fiabilité et la taille compacte sont essentielles. Avec l’adoption de technologies avancées comme les dispositifs de diagnostic portables, les équipements médicaux implantables et les systèmes de surveillance, l’utilisation des PCB HDI a considérablement augmenté.
- Dispositifs Implantables : Les PCB HDI sont utilisés dans les pacemakers, les neurostimulateurs et les appareils auditifs, où la petite taille et la fiabilité sont essentielles pour un usage sûr et de longue durée à l’intérieur du corps humain.
- Équipements de Diagnostic : Des dispositifs tels que les échographes, les scanners IRM et les outils de diagnostic portables bénéficient de la puissance de traitement élevée et de la transmission de données efficace des PCB HDI, garantissant des résultats précis et rapides.
- Moniteurs de Santé Portables : Les trackers de fitness et les dispositifs médicaux portables qui surveillent la fréquence cardiaque, la pression artérielle et d’autres signes vitaux nécessitent des PCB HDI compacts et légers pour offrir une performance fiable tout en étant confortables pour le patient.
Industries Automobile et Aéronautique
Dans les secteurs de l’automobile et de l’aéronautique, les PCB HDI sont essentiels pour créer des systèmes performants et fiables capables de résister à des environnements exigeants tout en offrant des fonctionnalités avancées.
- Électronique Automobile : Les PCB HDI sont utilisés dans les systèmes avancés d’aide à la conduite (ADAS), les systèmes d’infodivertissement, les commandes de navigation et les modules de gestion de l’énergie. Leur petite taille, leur grande fiabilité et leur capacité à gérer une transmission de données rapide en font un élément essentiel des véhicules modernes, en particulier des véhicules électriques et autonomes.
- Systèmes Aéronautiques : Dans l’industrie aérospatiale, les PCB HDI sont déployés dans les systèmes avioniques, les équipements de communication par satellite et les commandes de navigation. Ces cartes doivent supporter des températures extrêmes, des variations de pression et des vibrations, et la technologie HDI garantit une fiabilité et une performance élevées dans de telles conditions exigeantes. De plus, la légèreté des PCB HDI contribue à réduire le poids global des avions et des engins spatiaux, un facteur essentiel dans la conception aérospatiale.
Matériel de Télécommunications et Réseaux
Le secteur des télécommunications est un autre domaine où les PCB HDI ont un impact significatif. Avec l’essor de la technologie 5G, le besoin de transmission de données rapide et à haute fréquence est devenu primordial, et les PCB HDI fournissent les performances et la miniaturisation nécessaires pour répondre à ces exigences.
- Stations de Base 5G : Les PCB HDI sont utilisés dans l’infrastructure de base des réseaux 5G, permettant des vitesses de transfert de données plus rapides, une latence réduite et une bande passante plus élevée. Ils aident à réaliser les conceptions de petites cellules requises pour le déploiement de la 5G.
- Routeurs et Commutateurs Réseaux : Dans le matériel de réseau, les PCB HDI permettent un routage efficace des signaux à haute vitesse tout en minimisant le couplage et la perte de signal. Cela garantit que les routeurs, commutateurs et centres de données fonctionnent à des performances optimales, facilitant la communication et le transfert de données dans les réseaux à grande échelle.
- Systèmes de Communication par Fibre Optique : Les PCB HDI sont essentiels dans les émetteurs-récepteurs optiques et les processeurs de signal, qui sont des composants clés des systèmes de communication par fibre optique. Leurs conceptions haute densité assurent un traitement de données efficace et des taux de transmission rapides.
Automatisation Industrielle et Robotique
Le domaine croissant de l’automatisation industrielle et de la robotique bénéficie également des PCB HDI. Les systèmes d’automatisation dépendent d’un traitement rapide et précis des données pour contrôler les machines, les capteurs et les actionneurs en temps réel.
- Robotique : Les PCB HDI sont utilisés dans les robots pour les systèmes de navigation, les contrôleurs de moteur et les unités de traitement, où l’espace est limité et la performance est cruciale. Ces systèmes nécessitent souvent un transfert de données rapide, une faible consommation d’énergie et une grande fiabilité, que les PCB HDI peuvent offrir.
- Contrôleurs d’Automatisation : Les PCB HDI sont utilisés dans les contrôleurs logiques programmables (PLC) et les interfaces homme-machine (HMI) qui contrôlent les machines industrielles, garantissant qu’elles fonctionnent de manière efficace et précise dans des environnements de fabrication complexes.
6. Systèmes Militaires et de Défense
Dans les secteurs militaire et de défense, les PCB HDI sont indispensables en raison de leur grande fiabilité, de leur forme compacte et de leur capacité à supporter des conditions extrêmes. Les systèmes de défense nécessitent souvent des électroniques robustes pour des applications telles que la communication, la surveillance, le radar et les systèmes d’armement.
- Systèmes de Radar et de Communication : Les PCB HDI assurent un traitement rapide des données et une communication fiable dans les systèmes militaires critiques, où les pannes ne sont pas envisageables.
- Systèmes de Contrôle des Armes : Les PCB HDI sont utilisés dans les systèmes de guidage pour les missiles et les drones, où la taille compacte et la haute précision sont essentielles.
En conclusion, les PCB HDI se retrouvent dans une large gamme d’industries et d’applications, de l’électronique grand public et de la santé à l’automobile, l’aéronautique, les télécommunications et la défense. Leur capacité à offrir des conceptions compactes, haute densité et haute performance les rend essentiels pour les technologies de pointe et les systèmes électroniques complexes d’aujourd’hui. Alors que la demande pour des électroniques plus petites, plus rapides et plus efficaces augmente, l’utilisation des PCB HDI continuera de s’étendre dans ces industries.
Chapitre 6
Conception de PCB HDI
La conception d’un PCB HDI est une tâche complexe nécessitant une prise en compte minutieuse de divers facteurs pour maximiser les performances, assurer la fiabilité et répondre aux exigences spécifiques des applications électroniques haute densité et haute vitesse. Dans cet article, nous présenterons quelques lignes directrices pour vous aider à concevoir des PCB HDI répondant à ces exigences.
Bonnes Pratiques pour la Conception de PCB HDI
La conception des PCB HDI est plus complexe que celle des PCB traditionnels en raison de la densité accrue et de l’utilisation de techniques de fabrication avancées. Suivre les bonnes pratiques peut aider à garantir une conception optimale :
- Définir des Objectifs de Conception Clairs : Commencez par définir clairement les exigences de performance du produit, telles que la vitesse du signal, la densité des composants et les contraintes mécaniques. Cela vous aidera à choisir la configuration HDI appropriée, y compris le nombre de couches et les structures de vias.
- Collaborer Tôt avec les Fabricants : La conception de PCB HDI est étroitement liée aux capacités de fabrication. Collaborer avec le fabricant dès le début du processus de conception garantit que la conception peut être produite de manière rentable et dans les limites techniques du fabricant, en évitant les itérations coûteuses.
- Utiliser un Logiciel de Conception Avancé : Les PCB HDI modernes nécessitent des outils de conception sophistiqués prenant en charge les dispositions multicouches et haute densité, les microvias et les traces fines. Utiliser des logiciels de pointe comme Altium Designer ou Cadence Allegro garantit une plus grande précision et conformité aux normes de fabrication.
- Mettre en Œuvre la Conception pour la Fabrication (DFM) : Considérez la fabricabilité tout au long du processus de conception en évitant les structures trop complexes qui pourraient entraîner des coûts plus élevés ou des rendements plus faibles. Les lignes directrices DFM incluent le maintien des tailles de vias dans les tolérances de fabrication, la minimisation du nombre de trous de perçage et l’assurance d’une distance suffisante entre les couches de cuivre.
Considérations de Disposition : Largeur des Traces, Placement des Vias et Conception de l’Empilage
La disposition d’un PCB HDI est cruciale pour atteindre des performances élevées, notamment en matière d’intégrité des signaux, de gestion thermique et de placement des composants. Plusieurs éléments de disposition nécessitent une planification minutieuse :
- Largeur des Traces et Espacement : Les PCB HDI traitant souvent des signaux haute vitesse, la largeur et l’espacement des traces doivent être calculés avec soin pour minimiser la perte de signal et éviter le couplage. Il est essentiel de maintenir un contrôle de l’impédance en fonction de la vitesse du signal et du type de ligne de transmission (comme le microstrip ou le stripline). Dans les applications ultra-haute fréquence, la largeur des traces peut être aussi petite que 3-5 mils, et l’espacement doit être optimisé pour réduire le bruit.
- Placement des Vias et Types : Un placement approprié des vias est essentiel pour maintenir l’intégrité des signaux voyageant entre les couches. Les microvias sont couramment utilisées dans les PCB HDI en raison de leur petite taille, permettant un placement dense des composants. Il est important de placer les vias près des composants pour raccourcir les trajets des signaux, améliorer la vitesse de transmission et réduire la dégradation du signal. Les vias borgnes et enterrés doivent être utilisés stratégiquement pour maintenir la compacité de la carte et éviter les couches inutiles. De plus, les vias empilés peuvent fournir une connectivité améliorée entre les couches, mais doivent être utilisés avec parcimonie pour contrôler les coûts et assurer la stabilité mécanique.
- Conception de l’Empilage : L’empilage d’un PCB HDI fait référence à l’agencement de ses couches, y compris les couches de signal, d’alimentation et de masse. Un empilage bien optimisé aide à obtenir un contrôle de l’impédance, améliore l’intégrité du signal et minimise les interférences électromagnétiques (EMI). Typiquement, des couches alternées de signal et de masse sont utilisées pour fournir un blindage adéquat et maintenir une impédance cohérente sur les traces haute vitesse. Les empilages symétriques sont également préférés pour éviter le gauchissement pendant le processus de fabrication. Pour les conceptions HDI complexes, des couches supplémentaires avec vias borgnes ou enterrés sont utilisées pour réduire le nombre de couches nécessaires pour le routage, améliorant ainsi la qualité du signal tout en réduisant l’épaisseur de la carte.
Comment Minimiser les Interférences de Signal et Améliorer la Gestion Thermique
Les PCB HDI sont souvent utilisés dans des applications haute vitesse où la gestion de l’intégrité du signal et de la dissipation thermique est cruciale. Les concepteurs doivent tenir compte des interférences potentielles et des défis thermiques pour garantir un fonctionnement fiable.
Minimisation des Interférences de Signal (EMI/Couplage) : Les interférences électromagnétiques (EMI) et le couplage peuvent dégrader la qualité du signal dans les PCB HDI. Pour minimiser ces effets :
- Utiliser des Plans de Masse : Un plan de masse solide adjacent aux couches de signal haute vitesse aide à réduire l’EMI en fournissant un chemin de retour à faible impédance pour les signaux.
- Optimiser le Routage des Traces : Évitez de router les traces haute vitesse en parallèle sur de longues distances, car cela peut entraîner un couplage entre les signaux adjacents. Utilisez plutôt un routage orthogonal entre les couches pour réduire le couplage.
- Correspondance d’Impédance : Assurez-vous que l’impédance de la trace est adaptée à l’impédance caractéristique des composants connectés. Les incohérences d’impédance peuvent provoquer des réflexions de signal, entraînant du bruit et une corruption des données dans les systèmes haute vitesse.
- Utiliser des Paires Différentielles : Pour les signaux de données haute vitesse, les paires différentielles sont recommandées. Ces paires portent des signaux complémentaires, ce qui aide à annuler l’EMI et à réduire la perte de signal, les rendant idéales pour les chemins de signaux critiques comme USB, HDMI ou Ethernet.
Améliorer la Gestion Thermique : En raison de leur nature compacte, les PCB HDI peuvent générer une chaleur considérable, qui, si elle n’est pas correctement gérée, peut dégrader les performances et réduire la durée de vie des composants. Les stratégies de gestion thermique efficaces incluent :
- Vias Thermiques : Le placement de vias thermiques sous les composants générant de la chaleur aide à dissiper la chaleur en la dirigeant vers d’autres couches ou vers un dissipateur thermique externe.
- Dissipateurs de Chaleur et Pads Thermiques : Incorporer des dissipateurs de chaleur ou des pads thermiques dans la conception permet de retirer la chaleur des composants critiques, réduisant le risque de surchauffe.
- Épaisseur du Cuivre : Augmenter l’épaisseur du cuivre dans les couches d’alimentation et de masse aide à distribuer la chaleur plus efficacement. Des traces de cuivre plus épaisses peuvent également réduire les chutes de tension et améliorer la capacité de courant.
- Placement des Composants : Distribuez uniformément les composants générant de la chaleur sur la carte pour éviter les points chauds. Les composants nécessitant une puissance élevée, tels que les processeurs et les amplificateurs de puissance, doivent être placés dans des zones avec une bonne circulation d’air ou à proximité de dispositifs de gestion thermique.
En conclusion, concevoir des PCB HDI nécessite une attention minutieuse aux détails et une approche stratégique de la disposition, de l’intégrité du signal et de la gestion thermique. En suivant ces lignes directrices et en utilisant des outils de conception avancés, les ingénieurs peuvent créer des PCB HDI haute performance et fiables qui répondent aux exigences rigoureuses des applications électroniques modernes, allant des dispositifs de consommation aux systèmes industriels et militaires.
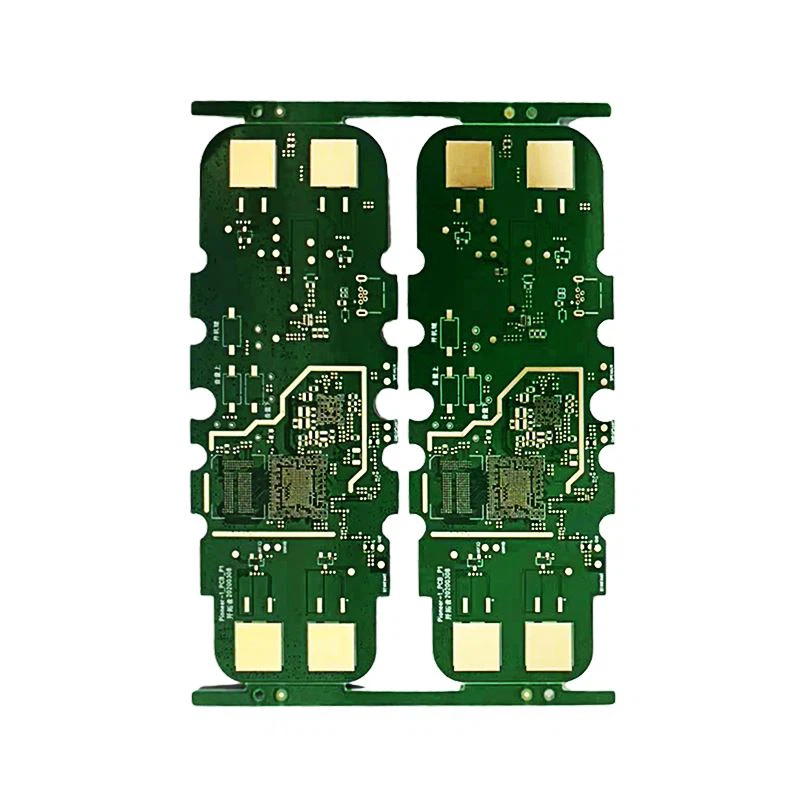
Chapitre 7
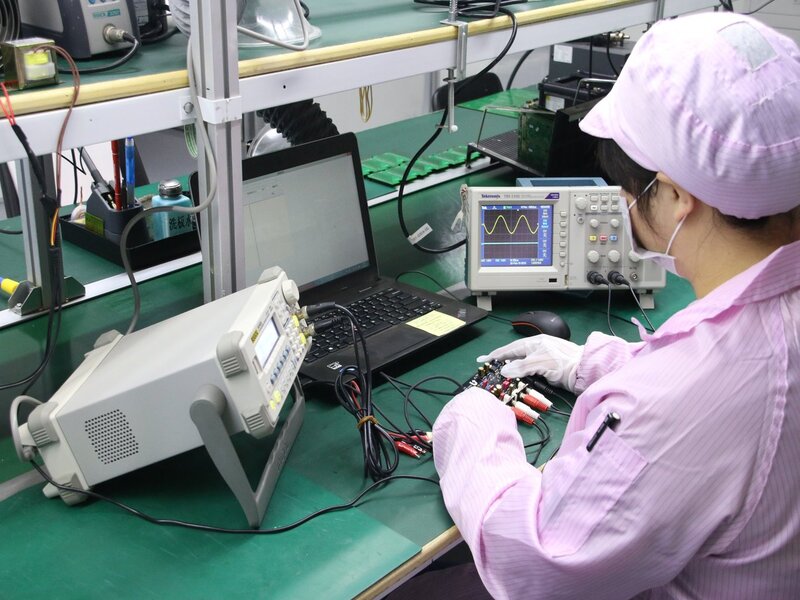
Contrôle de Qualité et Tests pour les PCB HDI
Le contrôle de qualité et les tests sont des aspects essentiels de la production de PCB HDI, garantissant que le produit final répond aux normes élevées nécessaires pour la performance, la fiabilité et la durabilité. En raison de la complexité et de la densité des conceptions HDI, des protocoles de test rigoureux sont nécessaires pour détecter et corriger tout défaut dès les premières étapes de la fabrication. Cela aide à prévenir les défaillances coûteuses et garantit que le PCB peut fonctionner comme prévu dans des applications exigeantes telles que les télécommunications, l’aérospatiale et les dispositifs médicaux. Voici les processus de contrôle de qualité essentiels et les méthodes de test utilisés dans la production des PCB HDI.
Processus Essentiels de Contrôle de Qualité dans la Production de PCB HDI
La production de PCB HDI implique plusieurs étapes, chacune nécessitant un contrôle de qualité strict pour maintenir une haute précision et une constance. Les principales mesures de contrôle de qualité incluent :
- Revue de Conception pour la Fabricabilité (DFM) : Avant le début de la production, une revue DFM approfondie garantit que la conception du PCB est optimisée pour la fabrication. Cette revue identifie les éléments de conception qui pourraient être difficiles ou coûteux à produire, aidant à éviter les retards de production ou les erreurs.
- Contrôle de Qualité en Cours de Processus : Pendant le processus de fabrication, des vérifications de qualité sont effectuées à différentes étapes pour détecter tout problème avant qu’il ne s’aggrave. Celles-ci incluent des inspections lors des processus de perçage, de laminage, de gravure et de placage pour s’assurer que les vias, les traces et les couches sont correctement alignés et répondent aux spécifications requises.
- Assurance Qualité des Matériaux : Les matériaux utilisés dans la production de PCB HDI, tels que la feuille de cuivre, les laminés et les préimprégnés, sont soigneusement testés pour garantir leur qualité. Cela garantit qu’ils répondent aux normes requises pour la performance électrique, la stabilité thermique et la résistance mécanique.
Types de Tests
Plusieurs méthodes de test avancées sont utilisées dans la fabrication des PCB HDI pour vérifier leur fonctionnalité, détecter les défauts et assurer la qualité globale. Les techniques de test les plus couramment utilisées incluent :
- Test Électrique (ET) : Le test électrique garantit que le PCB HDI fonctionne comme prévu en vérifiant la continuité de toutes les connexions électriques et en détectant tout court-circuit, circuit ouvert ou autre problème électrique.
- Inspection Optique Automatisée (AOI) : L’AOI utilise des caméras haute résolution pour inspecter automatiquement la surface du PCB pour détecter des défauts tels que des composants mal alignés, des largeurs de trace incorrectes.
- Inspection aux Rayons X : L’inspection aux rayons X est particulièrement importante pour les PCB HDI, car de nombreuses caractéristiques, comme les vias enterrés et les microvias empilés, sont cachées sous des couches de matériau et ne peuvent pas être inspectées optiquement.
En conclusion, le contrôle de qualité et les tests sont essentiels pour garantir la fonctionnalité, la fiabilité et la durabilité des PCB HDI.
Chapitre 8
Considérations de Coût pour les PCB HDI
Lorsque vous planifiez la production de PCB HDI, il est essentiel de prendre en compte les coûts. Le coût peut varier en fonction de la complexité du design, des matériaux utilisés et des processus de fabrication. En comprenant ces facteurs de coût, vous pouvez faire des choix éclairés pour équilibrer coût et qualité.
Facteurs qui Influencent le Coût des PCB HDI
Le coût des PCB HDI dépend de plusieurs facteurs, dont beaucoup sont liés à la complexité du design et aux processus nécessaires pour les fabriquer. Voici les principaux facteurs influençant le coût :
- Nombre de couches : Plus un PCB HDI comporte de couches, plus il coûte cher à produire.
- Technologie des vias : Le type et le nombre de vias utilisés influencent également le coût.
- Matériaux : Les matériaux de haute qualité, comme le polyimide et les laminés remplis de céramique, sont plus coûteux.
Comment Équilibrer Coût et Qualité Lors de l’Achat de PCB HDI
Vous devez trouver le bon équilibre entre coût et qualité lors de l’achat de PCB HDI. Voici quelques conseils :
- Travailler avec le fabricant : Discutez avec le fabricant pour optimiser le design et réduire les coûts.
- Conception adéquate : Concevez les PCB HDI correctement pour économiser.
- Choisir un bon fournisseur : Trouvez un fournisseur expérimenté dans la fabrication des PCB HDI.
Conclusion
Bien que les PCB HDI puissent être plus coûteux au départ, ils peuvent vous faire économiser à long terme grâce à leur fiabilité, leur petite taille, et leur compatibilité avec la production de masse.
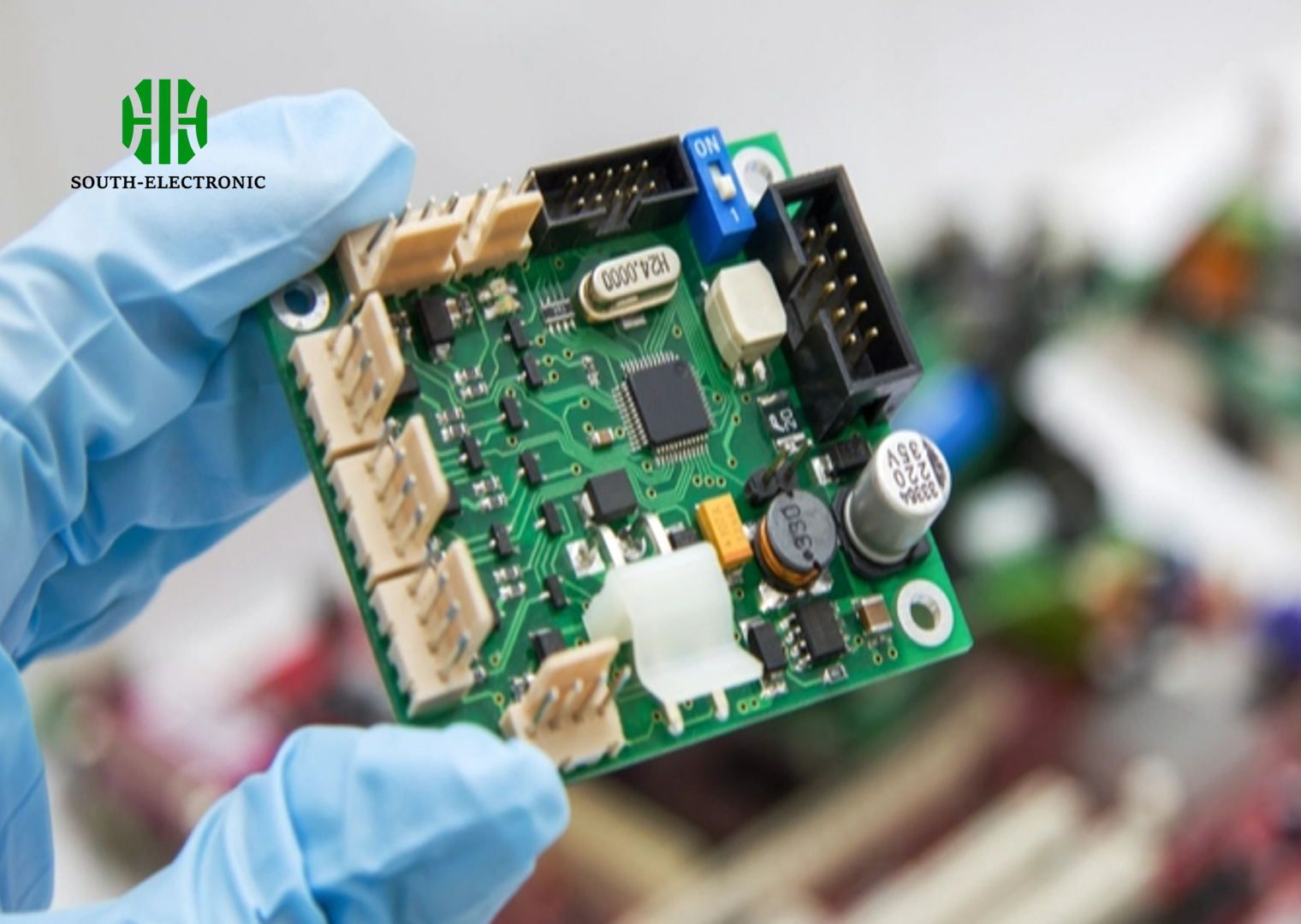
Chapitre 9

Avantages des PCB HDI par Rapport aux PCB Conventionnels
Les PCB HDI (High-Density Interconnect) sont supérieurs aux PCB traditionnels à bien des égards, notamment lorsque vous avez besoin de plus de performance, d’une taille plus petite et d’une fiabilité accrue.
- Plus de composants : Les PCB HDI permettent d’intégrer plus de composants dans un espace réduit en utilisant des microvias, vias aveugles et enterrés, ce qui permet des conceptions plus complexes et compactes que les PCB classiques. Ceci est particulièrement important pour les appareils où l’espace est limité.
- Taille réduite : Les PCB HDI permettent de concevoir des cartes plus petites et plus légères, ce qui est essentiel pour les smartphones, les appareils portables et l’aérospatiale, où la petite taille et la légèreté sont primordiales.
- Meilleure transmission de signal : Les PCB HDI offrent de meilleures performances en matière de signal en réduisant les chemins de transmission, ce qui diminue les interférences électromagnétiques (EMI) et les interférences entre signaux (crosstalk). Ceci est crucial pour les applications à haute vitesse telles que la 5G, les centres de données et les télécommunications.
- Meilleure gestion thermique : Les PCB HDI dissipent mieux la chaleur grâce aux vias thermiques et à un agencement optimisé, ce qui réduit la chaleur et augmente leur durabilité dans les applications à forte puissance.
- Plus de fiabilité : Les PCB HDI sont plus fiables grâce aux vias empilés et aux matériaux de meilleure qualité, ce qui les rend moins susceptibles de s’endommager dans les secteurs de l’automobile, de l’aviation et de la défense.
- Plus de rapidité : Les PCB HDI permettent des vitesses plus élevées car les signaux ont des trajets plus courts, ce qui les rend idéaux pour les télécommunications, les réseaux et les ordinateurs rapides.
- Plus d’options : Les PCB HDI offrent plus d’options en permettant d’empiler plus de couches et d’optimiser l’usage des vias, ce qui permet des conceptions plus complexes et personnalisées dans les secteurs médical et grand public.
- Moins chers à grande échelle : Bien que les PCB HDI soient plus coûteux au départ, ils deviennent moins chers en grande quantité, car ils peuvent être produits plus rapidement et intégrer plus de composants sur une seule carte, ce qui réduit les coûts du système complet.
En somme, les PCB HDI sont meilleurs car ils sont plus compacts, plus rapides et plus fiables, et ils peuvent être utilisés dans de nombreux secteurs tels que les télécommunications, l’aérospatiale, l’automobile et les produits de consommation.
Chapitre 10
L'Avenir de la Technologie des PCB HDI
À mesure que la technologie continue de progresser, les PCB HDI vont devenir de plus en plus petits, plus rapides et plus puissants. Voici quelques tendances que nous pouvons anticiper :
- Évolution de la Technologie HDI : Les PCB HDI deviennent de plus en plus complexes, avec des conceptions multi-étapes, des emballages 3D, et la technologie système dans un boîtier (SiP). Cela nous permet d’intégrer davantage de composants dans un espace réduit et d’améliorer les performances.
- Nouveaux Matériaux et Techniques : Nous commençons à utiliser de nouveaux matériaux comme les substrats flexibles et les laminés haute fréquence (comme le PTFE). Nous utilisons également de nouvelles techniques telles que l’imagerie directe par laser (LDI) et des technologies de vias avancées. Cela nous permet de créer des traces plus fines, de mieux gérer la chaleur, et d’intégrer davantage de composants dans un espace plus restreint.
- Les PCB HDI, l’Internet des Objets (IoT), l’Intelligence Artificielle (IA) et la 5G : Les PCB HDI seront cruciaux pour les appareils IoT car ils doivent être petits et économes en énergie. Ils seront également importants pour les systèmes d’IA et de calcul en périphérie, car ils doivent traiter les données très rapidement. Enfin, ils seront essentiels pour les réseaux 5G car ils peuvent gérer des signaux haute fréquence et réduire la taille des stations de base.
- Les PCB HDI et l’Emballage des Semi-conducteurs : Les PCB HDI vont commencer à intégrer de nouveaux types d’emballage pour semi-conducteurs, comme l’emballage au niveau de la tranche (FO-WLP) et le système dans un boîtier (SiP). Cela nous permettra de créer des dispositifs plus petits et plus rapides.
- Durabilité : Nous commençons à accorder plus d’importance à l’environnement, nous utilisons donc des soudures sans plomb, des laminés sans halogène et des matériaux recyclables. Nous voulons nous assurer que nous ne nuisons pas à la planète.
Ainsi, les PCB HDI vont continuer à alimenter les révolutions de l’IoT, de l’IA et de la 5G. Ils vont également continuer de s’améliorer avec de nouveaux matériaux, de nouveaux emballages, et de nouvelles méthodes pour prendre soin de la planète.
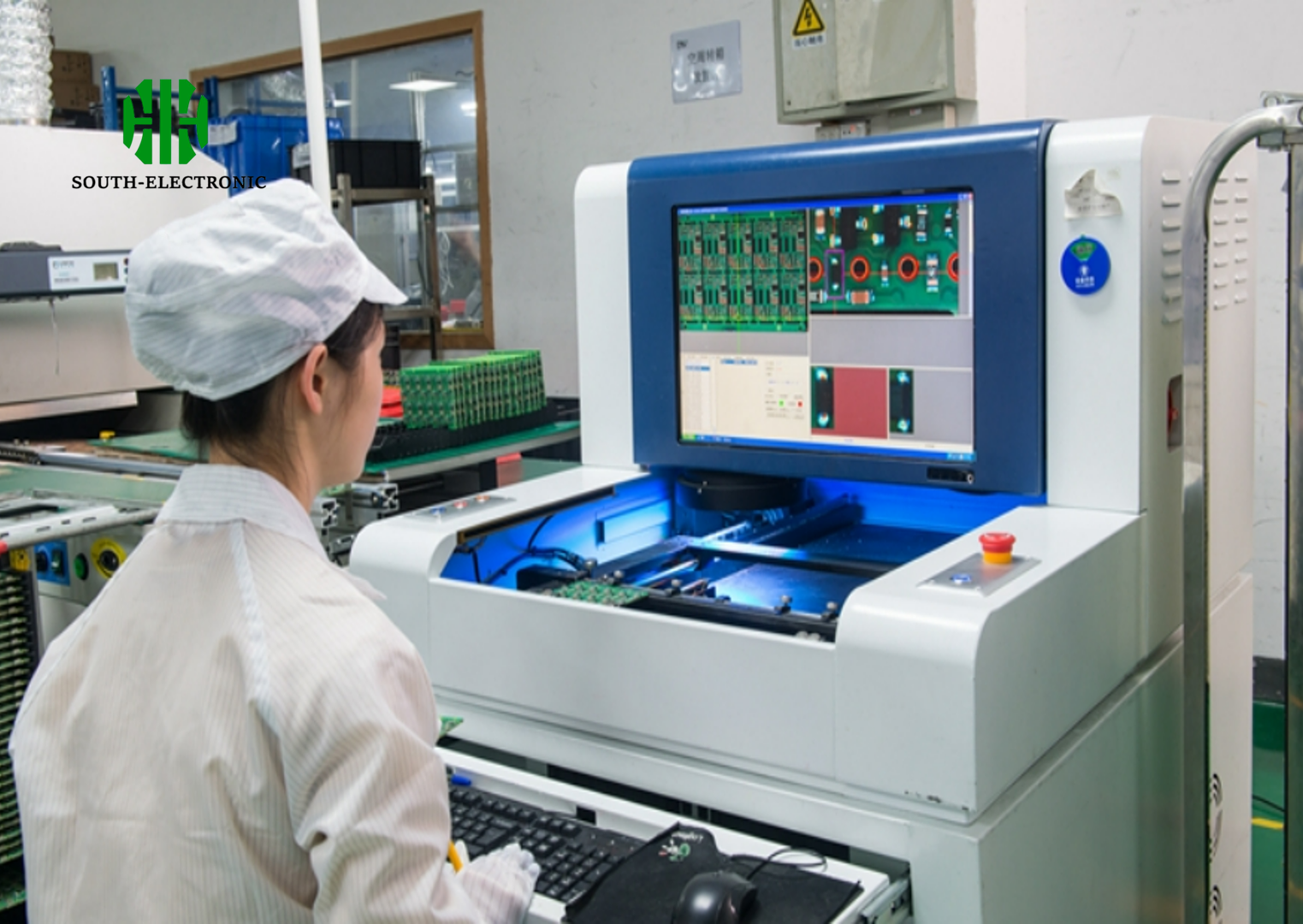
Contactez-Nous
Où Sommes-Nous ?
Parc Industriel, No. 438 Route Donghuan, No. 438, Shajing Donghuan Road, District Bao'an, Shenzhen, Guangdong, Chine
4ème étage, Bâtiment Zhihui Créatif, No. 2005 Route Xihuan, Shajing, District Baoan, Shenzhen, Chine
CHAMBRE A1-13, ÉTAGE 3, CENTRE INDUSTRIEL YEE LIM, 2-28 RUE KWAI LOK, KWAI CHUNG HK
service@southelectronicpcb.com
Téléphone : +86 400 878 3488
Envoyez-nous un message
Plus vous remplissez de détails, plus nous pourrons avancer rapidement à l’étape suivante.
