Fournisseurs de circuits imprimés de contrôle industriel
South-Electronic
Chez South-Electronic, nous sommes spécialisés dans la fourniture de circuits imprimés de contrôle industriel de haute qualité conçus pour garantir des performances stables et durables dans une variété d'environnements exigeants.
Pourquoi choisir South-Electronic pour votre PCB de contrôle industriel ?
Choisir South-Electronic, c’est travailler avec des experts qui produisent des PCB de contrôle industriel de qualité supérieure pour une large gamme d’applications.
Notre équipe possède une vaste expérience du secteur et fournit des PCB à des prix compétitifs sans compromettre la qualité. Nous nous engageons à fournir un service de qualité du début à la fin, garantissant votre satisfaction tout au long de votre projet.
-
Conformité mondiale
Votre portée mondiale exige qualité et conformité.
Notre circuit imprimé de contrôle industriel respecte les normes internationales, ce qui le rend adapté à une large gamme d'applications dans le monde entier, peu importe où votre entreprise opère. -
Assurance qualité supérieure
Votre confiance dans notre qualité est notre priorité absolue.
Grâce à des procédures de test avancées et des mesures strictes de contrôle de la qualité, nous garantissons que chaque PCB que vous recevez fonctionnera de manière fiable, même dans les conditions les plus exigeantes des environnements de contrôle industriel. -
Support complet
Avec nous, votre parcours sera fluide du début à la fin.
De la création du prototype à la production, notre équipe d'experts est là pour vous fournir un soutien continu, garantissant un processus fluide et efficace pour tous vos projets. -
Fabrication flexible
Vos besoins motivent notre flexibilité.
Nos capacités de fabrication sont très adaptables et peuvent gérer des commandes de toutes tailles, des petites séries à la production à grande échelle, tout en maintenant les normes de qualité les plus élevées. -
Efficacité stratégique de la chaîne d'approvisionnement
Votre satisfaction est renforcée par notre transparence.
Nos processus de chaîne d'approvisionnement optimisés incluent le suivi en temps réel et un service client dédié, améliorant ainsi la satisfaction globale des clients et la transparence opérationnelle.
Projet connexe que nous avons réalisé
Avis des clients
Questions courantes
Questions les plus populaires
Le circuit imprimé de contrôle industriel est un circuit imprimé spécialisé conçu pour répondre aux exigences des systèmes d'automatisation et de contrôle industriels. Il est conçu pour garantir fiabilité et durabilité dans des environnements industriels difficiles.
La gestion thermique est cruciale car elle empêche la surchauffe, assurant ainsi que le circuit imprimé fonctionne de manière fiable sous les charges thermiques typiquement rencontrées dans les environnements industriels, ce qui peut affecter la performance et la longévité.
Le circuit imprimé est largement utilisé dans l'automatisation, la robotique, les processus de fabrication et les systèmes de gestion de l'énergie dans les environnements industriels pour contrôler les machines et les processus de manière efficace.
La qualité est assurée grâce à des protocoles de test rigoureux, y compris des tests en circuit, des inspections optiques automatisées et des cycles thermiques, afin de garantir que chaque circuit imprimé répond aux normes les plus élevées de fiabilité et de fonctionnalité.
Le délai peut varier en fonction de la complexité et de la personnalisation du circuit imprimé, mais il est généralement compris entre 2 et 4 semaines pour la plupart des projets de circuits imprimés de contrôle industriel.
Vous pouvez commander en contactant notre équipe commerciale via notre site Web, où vous pourrez demander un devis, discuter de vos exigences spécifiques et en savoir plus sur nos capacités de production et nos délais de livraison.
Nous offrons un support complet après-vente comprenant le suivi des commandes en temps réel, un support technique et un service client dédié tout au long du cycle de vie du produit.
Envoyez-nous un message
Plus vous fournissez de détails, plus nous pourrons passer rapidement à l’étape suivante.
Le guide complet pour les circuits imprimés de contrôle industriel
contact
Chapitre 1
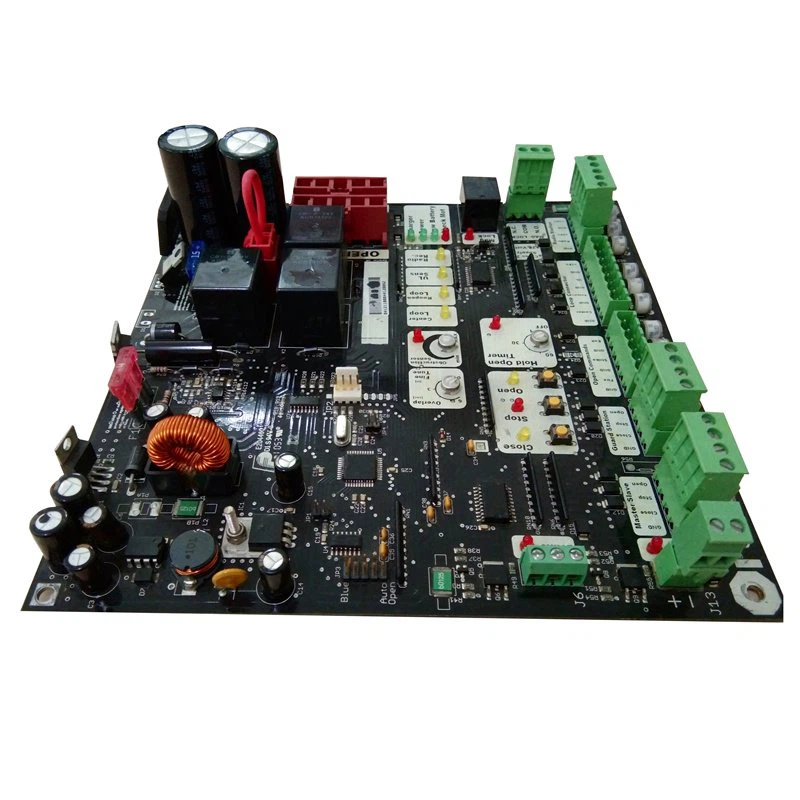
Introduction au PCB de contrôle industriel
Le PCB de contrôle industriel est la colonne vertébrale des systèmes industriels. Ce circuit imprimé spécialisé ne soutient pas seulement les fonctionnalités complexes des technologies d’automatisation et de contrôle actuelles, mais garantit également sa fiabilité opérationnelle dans des environnements difficiles. À mesure que l’industrie évolue vers des systèmes plus automatisés et technologiquement avancés, le besoin de PCB de contrôle industriel robustes et efficaces devient encore plus crucial.
Le PCB de contrôle industriel est différent du PCB standard, il est conçu pour gérer des puissances plus élevées et des exigences opérationnelles plus strictes. Il est conçu pour résister aux conditions extrêmes rencontrées dans les environnements industriels, comme les hautes températures, les vibrations et le fonctionnement continu. La fiabilité de ces systèmes est essentielle, car ils sont souvent la colonne vertébrale des opérations critiques telles que les processus de fabrication, la distribution d’énergie et l’automatisation.
Dans ce guide ultime, vous découvrirez toutes les différentes parties qui composent les cartes de contrôle industrielles, les matériaux utilisés, les considérations de conception, ainsi que les processus de fabrication rigoureux qui garantissent leur qualité supérieure et leur longue durée de vie. De plus, je vous donnerai des conseils pour choisir le bon fournisseur pour vos cartes de contrôle industrielles, une décision importante qui peut avoir un impact énorme sur l’efficacité et la fiabilité de vos opérations industrielles. En chemin, je parlerai également de South-Electronic, un leader dans le domaine, dont l’engagement envers la qualité et l’innovation établit vraiment la norme pour l’industrie.
Après avoir lu ce guide, vous en saurez plus sur les PCB de contrôle industriel que 99 % des personnes que vous rencontrerez. Vous serez en mesure de faire des choix plus éclairés pour aider votre système industriel à fonctionner de manière optimale et à ne jamais vous décevoir.
Chapitre 2
Les bases du PCB de contrôle industriel
Définition et importance
Qu’est-ce qu’un PCB de contrôle industriel ?
Le PCB de contrôle industriel (Circuit Imprimé) est une carte de circuit imprimé spécialement conçue pour fonctionner de manière fiable dans des environnements industriels difficiles. Le PCB est l’élément clé des systèmes de contrôle qui gèrent et automatisent les machines et processus industriels. Son rôle est essentiel pour garantir que ces systèmes fonctionnent efficacement, en toute sécurité et de manière continue, ce qui est crucial pour maintenir la productivité industrielle et l’intégrité opérationnelle.
Pourquoi est-il important ?
Le PCB de contrôle industriel joue un rôle clé dans divers secteurs, notamment la fabrication, l’automobile, l’énergie, et plus encore.
Précision et automatisation : Automatisation des tâches nécessitant une grande précision et répétabilité, réduisant ainsi les erreurs humaines et augmentant l’efficacité. Durabilité et fiabilité : Garantir que les systèmes peuvent fonctionner sans défaillance dans des conditions exigeantes, ce qui est crucial dans les environnements où les temps d’arrêt peuvent entraîner des pertes financières importantes. Adaptabilité : Faciliter les changements rapides dans les chaînes de production et les processus pour s’adapter aux nouvelles technologies ou aux demandes de production.
Principaux différenciateurs
En quoi le PCB de contrôle industriel se distingue-t-il ?
Durabilité améliorée
Matériaux : Le PCB de contrôle industriel utilise des matériaux capables de résister à des conditions environnementales extrêmes, telles que la chaleur, l’humidité et les produits chimiques corrosifs. Construction : Le PCB présente généralement des couches de cuivre plus épaisses et un substrat robuste pour résister aux contraintes des opérations industrielles.
Capacités de conception complexes
Intégration : Capable d’intégrer des conceptions de circuits complexes incluant des microprocesseurs avancés, des capteurs et d’autres composants critiques nécessaires au contrôle de machines industrielles sophistiquées. Disposition : Conçu pour maximiser l’espace et la fonctionnalité, souvent en utilisant des configurations multicouches qui supportent des densités élevées de composants tout en gérant efficacement la chaleur et l’intégrité des signaux.
Gestion thermique supérieure
Dissipation de la chaleur : Ils intègrent des technologies de refroidissement avancées telles que des dissipateurs de chaleur, des vias thermiques et parfois des systèmes de refroidissement actifs pour gérer la chaleur générée par les composants haute puissance. Stabilité thermique : Les matériaux et conceptions sont choisis pour garantir une stabilité à travers une gamme de températures opérationnelles, évitant ainsi les problèmes d’expansion thermique qui peuvent entraîner une défaillance du PCB.
Conformité réglementaire
Certifications : Conforme à des normes industrielles strictes telles que IPC-6012 Classe 3, garantissant qu’il répond à des critères élevés de fiabilité et de qualité. Normes de sécurité : Respect des normes de sécurité qui sont cruciales dans les applications industrielles, garantissant que le PCB ne présente aucun risque pendant son fonctionnement.
Tests avancés et assurance qualité
Tests rigoureux : Soumis à des protocoles de tests approfondis tels que des tests en circuit, des cycles thermiques et des tests de contrainte pour garantir qu’ils peuvent résister aux environnements industriels. Contrôle de qualité : Des normes élevées de contrôle de qualité sont maintenues tout au long du processus de fabrication pour éviter tout défaut pouvant entraîner des défaillances opérationnelles.
En résumé
Le PCB de contrôle industriel est conçu et fabriqué pour garantir qu’il peut fonctionner dans des conditions environnementales industrielles difficiles tout en maintenant sécurité, fiabilité et fonctionnalité. Comprendre ces bases est essentiel pour toute personne impliquée dans le développement, l’approvisionnement ou la gestion de systèmes électroniques industriels.
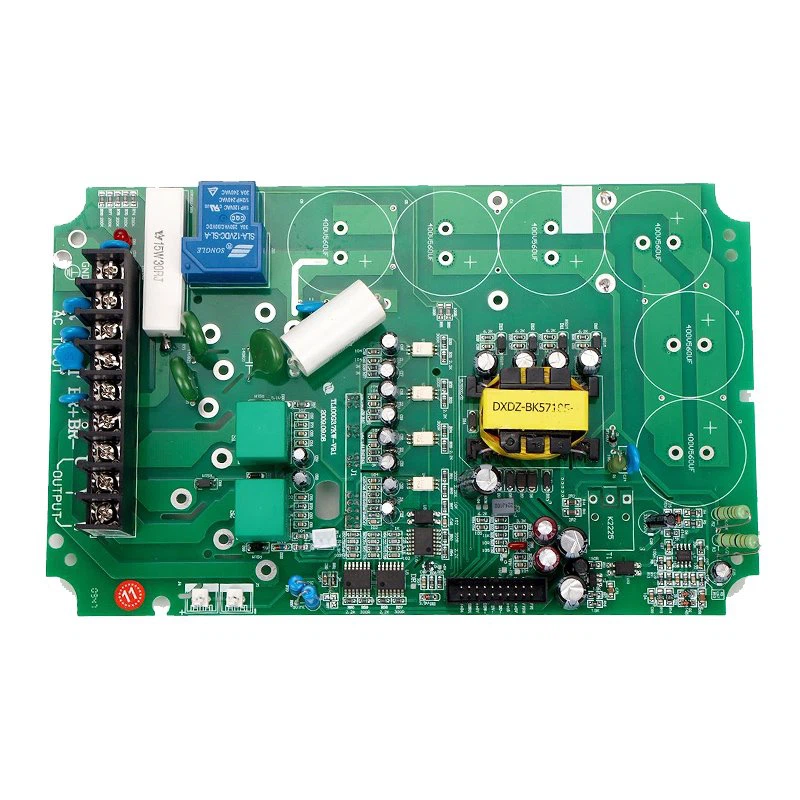
Chapitre 3
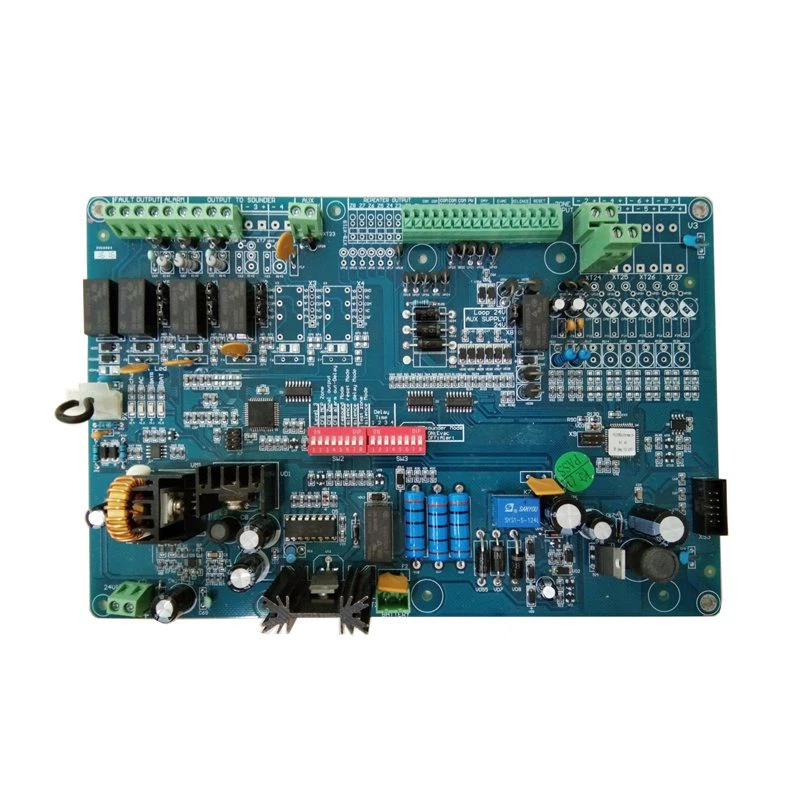
Composants et architecture du PCB de contrôle industriel
Le PCB de contrôle industriel est un assemblage complexe contenant une variété de composants spécialement conçus pour gérer des tâches industrielles exigeantes. Voici un aperçu détaillé des composants typiques présents sur le PCB et de la manière dont ils s’intègrent dans des systèmes de contrôle industriel puissants.
Composants clés du PCB de contrôle industriel
Microprocesseurs et microcontrôleurs
Fonctionnalité : Ils servent d’unité centrale de traitement (CPU) du PCB, exécutant le logiciel de contrôle qui gère les opérations des machines industrielles. Intégration : Connectés à diverses interfaces d’entrée/sortie qui leur permettent de recevoir des données de capteurs et d’envoyer des commandes aux actionneurs ou à d’autres composants de machines.
Modules d’interface
Types : Peuvent inclure des modules d’E/S numériques et analogiques, des modules de communication comme Ethernet ou CAN bus, et des modules d’interface utilisateur tels que des écrans tactiles ou des boutons. Rôle : Facilitent la communication entre le système de contrôle et les machines, capteurs ou systèmes de réseau, garantissant que les données sont échangées et traitées avec précision.
Régulateurs de puissance et convertisseurs
Objectif : Assurent que tous les composants du PCB reçoivent une alimentation stable et adaptée, indépendamment des fluctuations d’alimentation externes. Caractéristiques : Incluent souvent des caractéristiques d’isolation et de filtrage de l’alimentation pour protéger les composants sensibles des pics et du bruit dans les alimentations électriques industrielles.
Composants mémoire
Types : Incluent à la fois la RAM volatile pour le stockage temporaire des données et la mémoire non volatile pour stocker le firmware, les paramètres de configuration et les données d’application. Fonction : Crucial pour l’enregistrement des données, la rétention des configurations, et assurer que les logiciels de contrôle et les paramètres opérationnels peuvent être chargés rapidement au démarrage ou à la réinitialisation du système.
Interface des capteurs et actionneurs
Connectivité : Les circuits d’interface se connectent à une variété de capteurs (température, pression, etc.) et d’actionneurs (moteurs, vannes). Importance : Ces interfaces convertissent et conditionnent les signaux des capteurs et vers les actionneurs, assurant un flux de données et des actions de contrôle précis et fiables.
Circuits de conditionnement des signaux
Exigence : Nécessaires pour préparer les signaux des capteurs pour le traitement (amplification, filtrage et conversion des signaux analogiques en numériques). Conception : Conçus spécifiquement pour le type de capteur et les conditions environnementales attendues dans les environnements industriels.
Caractéristiques de sécurité et de fiabilité
Composants : Peuvent inclure des temporisateurs de surveillance, des circuits redondants et une logique de détection de panne pour surveiller l’intégrité du système et réagir aux pannes potentielles. Objectif : Renforcent la sécurité, la fiabilité et le temps de fonctionnement des systèmes de contrôle industriel, crucial dans les environnements où une défaillance peut entraîner des perturbations opérationnelles importantes.
Intégration dans des systèmes de contrôle industriel robustes
Disposition systématique : Les composants sont disposés de manière systématique pour optimiser l’intégrité des signaux et minimiser les interférences, crucial dans les environnements à forte interférence électromagnétique (EMI). Conception modulaire : De nombreux PCBs de contrôle industriel sont conçus de manière modulaire, permettant une maintenance plus facile et une évolutivité. Cette modularité permet de remplacer ou de mettre à niveau rapidement des modules sans perturber l’ensemble du système. Protection environnementale : Les composants et l’ensemble du PCB sont souvent enfermés dans des boîtiers robustes qui les protègent des défis environnementaux tels que la poussière, l’humidité et l’exposition chimique, garantissant une fiabilité et une fonctionnalité à long terme. Interconnectivité : Compte tenu de la complexité et de la nécessité d’une intégration avec d’autres systèmes industriels, le PCB est équipé de nombreuses options de connectivité pour assurer une communication fluide entre différentes plates-formes et systèmes au sein d’une installation.
Conclusion
Les composants et l’architecture du PCB de contrôle industriel sont conçus pour répondre aux défis uniques des environnements industriels. Comprendre ces éléments est essentiel pour concevoir, mettre en œuvre et maintenir des systèmes de contrôle industriel efficaces et fiables qui peuvent résister aux rigueurs des opérations industrielles tout en offrant des performances optimales.
Chapitre 4
Considérations matérielles pour les PCB de contrôle industriel
Les matériaux utilisés dans les PCB de contrôle industriel jouent un rôle essentiel dans la détermination de leur performance, durabilité et fiabilité dans les environnements industriels. Voici un aperçu approfondi des principaux choix de matériaux et de leur influence sur la fonctionnalité de ces PCB spécialisés.
Matériaux courants utilisés dans les PCB de contrôle industriel
FR4
Description : Le FR4 est le matériau standard pour la plupart des PCB, y compris ceux utilisés dans les systèmes de contrôle industriel. Il se compose d’un tissu en fibre de verre tissé avec une résine époxy. Caractéristiques : Il offre une bonne résistance mécanique, une résistance aux flammes et une excellente isolation électrique. Limitations : Bien que le FR4 soit suffisant pour de nombreuses applications, sa conductivité thermique est relativement faible, ce qui peut être un facteur limitant dans les environnements à haute température.
PCB à noyau métallique (MCPCB)
Matériaux : Généralement fabriqué avec un noyau en aluminium, mais peut également inclure du cuivre pour une conductivité thermique plus élevée. Avantages : Le MCPCB est excellent pour la gestion thermique, car le noyau métallique aide à dissiper la chaleur plus efficacement, protégeant ainsi les composants sensibles des défaillances dues à la chaleur. Applications : Idéal pour les applications à haute puissance où la chaleur est une préoccupation majeure, comme les convertisseurs de puissance ou les entraînements.
Stratifiés haute température
Types : Des matériaux comme le polyimide sont utilisés pour les PCB devant fonctionner dans des environnements à haute température, au-delà de ce que le FR4 peut supporter. Avantages : Le polyimide et des matériaux similaires peuvent résister à des températures plus élevées sans se dégrader, ce qui les rend adaptés aux applications industrielles impliquant des températures extrêmes.
Matériaux pour PCB flexibles
Matériaux : Le polyimide est également couramment utilisé pour les PCB flexibles en raison de sa durabilité et de sa flexibilité. Fonctionnalité : Les PCB flexibles sont utiles dans les applications industrielles où le PCB doit se conformer à une forme spécifique ou supporter des flexions et des mouvements sans défaillance.
Impact du choix des matériaux sur la performance et la durée de vie des PCB
Gestion thermique
Importance : Une gestion thermique appropriée est cruciale pour maintenir la fonctionnalité et la longévité des composants des PCB. Les matériaux ayant une meilleure conductivité thermique aident à dissiper la chaleur plus efficacement, réduisant ainsi le risque de surchauffe et prolongeant la durée de vie des composants. Choix des matériaux : L’aluminium et le cuivre dans les MCPCB sont préférés dans les scénarios où la dissipation de la chaleur est une préoccupation critique.
Résistance mécanique et durabilité
Considérations : Les environnements industriels posent souvent des contraintes physiques telles que des vibrations, des impacts ou des charges mécaniques constantes. Sélection des matériaux : Des matériaux robustes comme des couches de cuivre épaisses ou des stratifiés spécialisés à haute résistance peuvent fournir la durabilité nécessaire pour résister à ces conditions.
Résistance chimique et à l’humidité
Défis : L’exposition à des produits chimiques agressifs, des huiles ou de l’humidité est courante dans les environnements industriels. Solutions : L’utilisation de matériaux résistants aux produits chimiques et étanches à l’humidité peut prévenir la corrosion et les défaillances liées à l’humidité, améliorant ainsi la fiabilité du PCB.
Performance électrique
Exigence : Les PCB de contrôle industriel doivent souvent gérer des courants et des tensions plus élevés. Impact des matériaux : Les propriétés diélectriques du matériau du PCB influencent sa capacité à isoler entre les couches et les traces, empêchant les courts-circuits et garantissant un fonctionnement fiable.
Conclusion
Sélectionner les bons matériaux pour les PCB de contrôle industriel est crucial pour garantir qu’ils répondent aux normes de performance requises et résistent aux conditions difficiles typiques des environnements industriels. En comprenant les propriétés et les avantages des différents matériaux, les concepteurs peuvent adapter leurs PCB aux besoins spécifiques de l’application, améliorant à la fois la performance et la durée de vie. Cette approche centrée sur les matériaux est fondamentale pour concevoir des PCB non seulement fonctionnels, mais aussi durables et fiables sur le long terme.

Chapitre 5
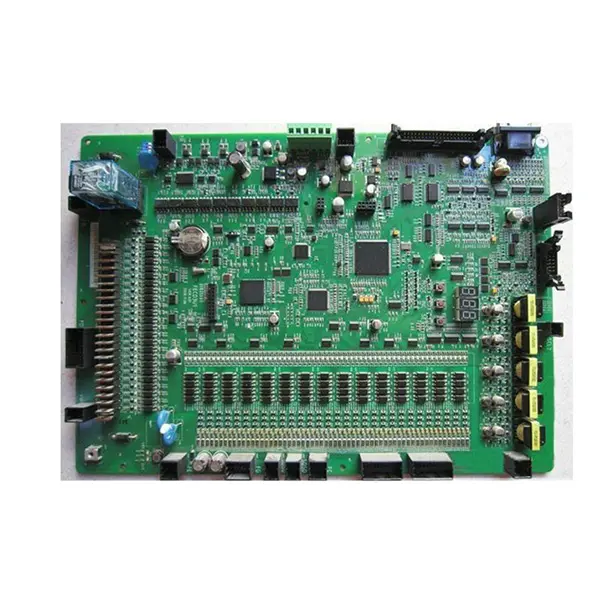
Stratégies de conception et d'agencement pour les PCB de contrôle industriel
Pour l’électronique industrielle, la conception et l’agencement des PCB sont essentiels pour garantir que les systèmes fonctionnent de manière fiable et efficace dans des conditions difficiles. Ci-dessous, nous explorerons les considérations de conception clés et les stratégies d’agencement qui sont vitales pour les PCB de contrôle industriel.
Principales considérations de conception
Sélection de composants robustes
Durabilité et qualité : Les composants doivent être choisis non seulement pour leur fonctionnalité, mais aussi pour leur capacité à résister aux températures extrêmes, aux vibrations et aux environnements corrosifs typiques des environnements industriels. Spécifications : Les composants de qualité industrielle, avec des plages de température étendues et une tolérance plus élevée aux contraintes physiques, sont préférés.
Gestion thermique améliorée
Dissipation de chaleur : Une gestion thermique efficace est essentielle pour éviter la surchauffe, qui peut entraîner une défaillance des composants. Cela comprend l’utilisation de dissipateurs thermiques, de vias thermiques et d’un espacement correct des composants générant de la chaleur. Soulagement thermique : L’incorporation de pads de soulagement thermique autour des composants sensibles à la chaleur peut prévenir le transfert de chaleur lors des processus de soudure qui pourraient endommager le composant.
Redondance
Systèmes de secours : L’intégration de redondances dans les chemins de signal critiques et les modules fonctionnels peut garantir que si un chemin échoue, un autre peut prendre le relais, maintenant l’intégrité opérationnelle du système. Test de la redondance : Des protocoles de test réguliers doivent être établis pour garantir que les redondances fonctionnent comme prévu lorsqu’elles sont requises.
Stratégies d’optimisation de l’agencement
Minimiser le bruit électrique
Intégrité du signal : Les stratégies d’agencement doivent donner la priorité à l’intégrité du signal, en particulier dans les environnements à forte interférence électromagnétique (EMI). Cela peut être géré par des techniques de routage, de blindage et de mise à la terre appropriées. Isolation : Séparer les composants bruyants ou à haute fréquence des signaux analogiques sensibles est crucial pour éviter les interférences croisées.
Utilisation efficace de l’espace
Placement des composants : Le placement stratégique des composants peut optimiser l’espace et améliorer l’efficacité générale de l’agencement. Cela inclut le fait de placer les composants connexes à proximité pour minimiser la longueur des traces et réduire les interférences potentielles. Gestion des couches : L’utilisation de PCB multicouches peut aider à gérer efficacement l’espace. Les plans d’alimentation et de masse peuvent être utilisés dans les couches internes pour fournir un blindage et réduire les interférences électromagnétiques.
Atténuation de l’accumulation de chaleur
Conception de l’agencement : Concevoir l’agencement pour répartir les composants générant de la chaleur peut prévenir l’accumulation de chaleur localisée. Outils de simulation : L’utilisation d’outils de conception assistée par ordinateur (CAO) et de simulation thermique peut aider à prédire le flux et la distribution de la chaleur, permettant aux concepteurs de prendre des décisions éclairées concernant le placement des composants et les mécanismes de refroidissement.
Renforcement
Revêtement de protection : L’application d’un revêtement protecteur peut protéger le PCB contre l’humidité, la poussière et l’exposition aux produits chimiques, courants dans les environnements industriels. Résistance aux vibrations : Les techniques de conception telles que le montage traversant et l’utilisation de raidisseurs peuvent fournir une résistance mécanique supplémentaire pour supporter les vibrations et les chocs.
Importance de la vérification de la conception
Prototypage et test : Un prototypage précoce et des tests rigoureux dans des conditions environnementales simulées peuvent aider à identifier les défauts potentiels de conception avant la production à grande échelle. Processus de conception itératif : La conception doit être un processus itératif, où les retours des phases de test sont utilisés pour améliorer continuellement la conception du PCB afin d’améliorer les performances et la fiabilité.
Conclusion
La conception et l’agencement des PCB de contrôle industriel nécessitent une attention méticuleuse aux détails et une compréhension approfondie des défis environnementaux auxquels ils seront confrontés. En adhérant à ces principes stratégiques de conception et à ces optimisations d’agencement, les ingénieurs peuvent améliorer considérablement la fiabilité et l’efficacité des systèmes de contrôle industriel, garantissant qu’ils fonctionnent de manière optimale même dans les conditions les plus exigeantes.
Chapitre 6
Fabrication et contrôle de qualité pour les PCB de contrôle industriel
La fabrication et l’assurance qualité des PCB de contrôle industriel sont essentielles pour garantir que ces composants puissent résister aux conditions exigeantes des environnements industriels tout en maintenant une fiabilité et une efficacité élevées. Voici un aperçu détaillé du processus de fabrication et des mesures de contrôle qualité mises en place pour répondre aux normes industrielles.
Processus de fabrication des PCB de contrôle industriel
Validation du design et ingénierie pré-production
Revue du design : Avant le début de la fabrication, le design du PCB fait l’objet d’une revue approfondie pour s’assurer qu’il respecte toutes les spécifications et qu’il est optimisé pour la fabrication. Vérifications DFM (Design for Manufacturability) : Cette étape consiste à analyser le design du PCB pour s’assurer qu’il est compatible avec les capacités de fabrication et qu’il adhère aux normes industrielles.
Sélection et approvisionnement des matériaux
Matériaux de haute qualité : Les matériaux utilisés dans les PCB de contrôle industriel, tels que les substrats à haute TG et le cuivre épais, sont sélectionnés pour leur capacité à résister aux conditions extrêmes. Évaluation des fournisseurs : Les fournisseurs de matières premières sont rigoureusement évalués pour s’assurer qu’ils fournissent des matériaux de haute qualité conformes aux spécifications industrielles.
Fabrication du PCB
Construction multicouche : Les PCB multicouches sont courants dans les systèmes de contrôle industriel en raison de leur fonctionnalité accrue et de leur taille compacte. Les couches sont soigneusement alignées et laminées sous haute pression et haute température. Gravure des circuits : Des techniques avancées comme l’imagerie directe par laser (LDI) sont utilisées pour un tracé précis des circuits, garantissant précision et cohérence.
Assemblage des composants
Technologie de montage en surface (SMT) : La plupart des PCB de contrôle industriel utilisent la technologie SMT pour le placement des composants, ce qui permet d’avoir plus de composants sur les deux faces du PCB et d’améliorer les performances. Technologie à trous traversants : Pour les composants nécessitant des connexions mécaniques plus solides, la technologie à trous traversants est utilisée, en particulier pour les connecteurs et les composants lourds.
Brasage et refusion
Brasage sans plomb : En conformité avec les normes RoHS (Restriction of Hazardous Substances), des matériaux de brasage sans plomb sont utilisés pour minimiser l’impact environnemental et améliorer la sécurité. Brasage par refusion : Assure une jonction de brasage fiable en contrôlant soigneusement le profil de température pendant le processus de brasage.
Mesures de contrôle qualité
Inspection optique automatisée (AOI)
Inspection après brasage : Immédiatement après le brasage, des systèmes AOI sont utilisés pour vérifier la qualité du brasage, l’alignement et la présence de tout défaut tel que des courts-circuits ou des circuits ouverts.
Inspection par rayons X
Inspection des couches : Pour les PCB multicouches, l’inspection par rayons X est cruciale pour identifier tout défaut interne potentiel tel que des désalignements ou des problèmes de brasage cachés.
Test en circuit (ICT)
Vérification fonctionnelle : Chaque PCB est testé pour vérifier son fonctionnement en simulant des conditions opérationnelles afin de s’assurer que tous les composants et circuits fonctionnent comme prévu.
Tests de stress environnemental
Tests thermiques et de vibration : Les PCB sont soumis à des tests de cycles thermiques et de vibration pour simuler les environnements industriels difficiles dans lesquels ils fonctionneront. Ces tests garantissent que le PCB peut résister aux variations de température et aux contraintes mécaniques.
Assurance qualité finale
Vérifications de qualité : Avant expédition, une série finale de vérifications de qualité est effectuée pour s’assurer que chaque PCB respecte toutes les spécifications techniques et fonctionnelles. Certifications : La conformité avec des certifications telles que ISO 9001 pour la gestion de la qualité et IPC-A-600 pour l’acceptabilité des PCB garantit que le PCB est fabriqué selon les normes les plus élevées.
Conclusion
Les processus de fabrication et de contrôle qualité pour les PCB de contrôle industriel sont conçus pour garantir que ces composants critiques non seulement respectent, mais dépassent les normes rigoureuses requises pour les applications industrielles. En mettant en œuvre des protocoles de fabrication stricts et des contrôles qualité complets, les fabricants peuvent fournir des PCB offrant une fiabilité et des performances inégalées dans tout environnement industriel.
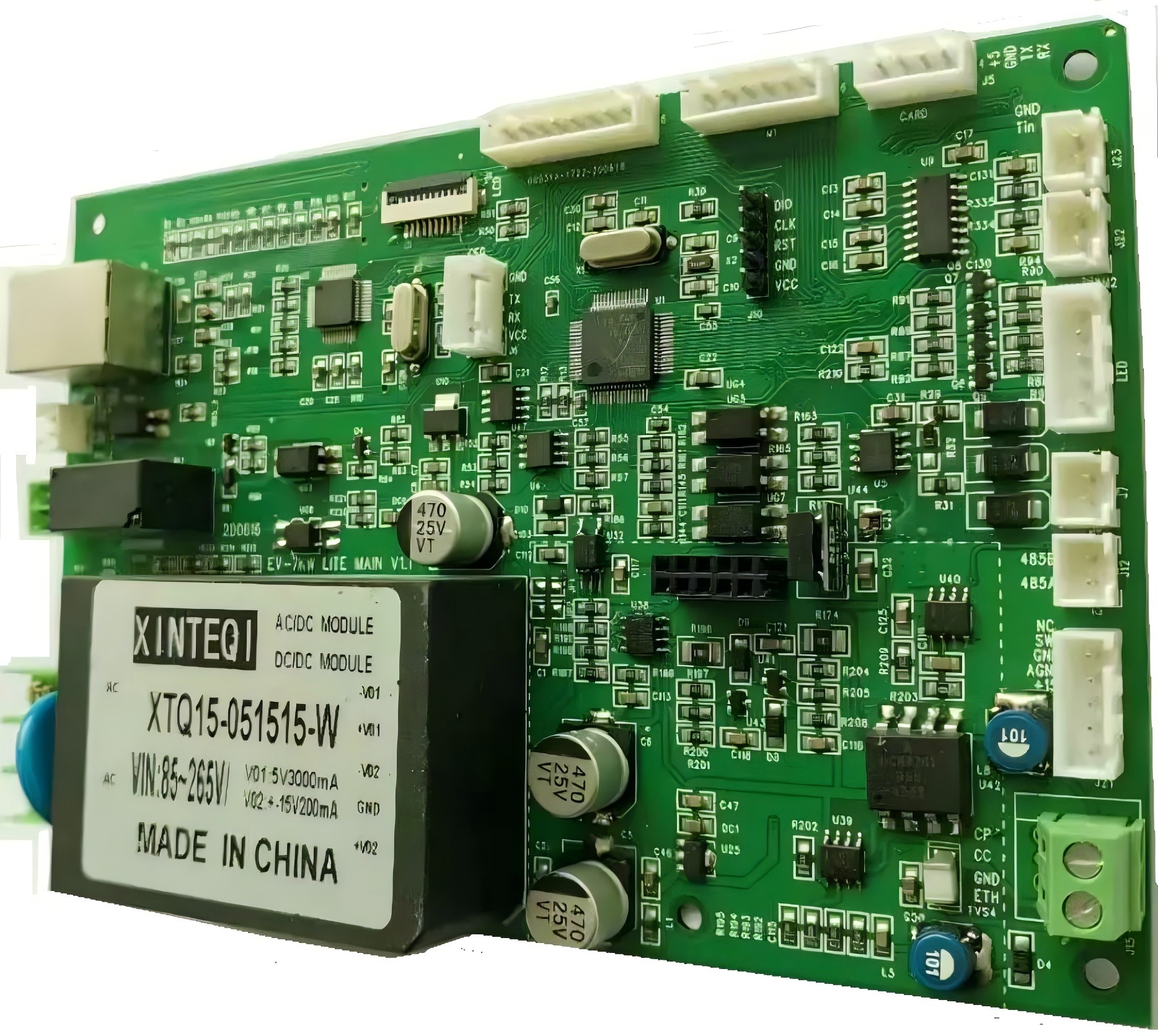
Chapitre 7
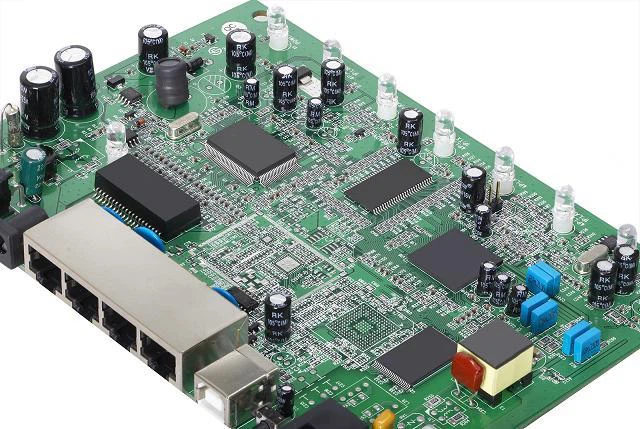
Comment choisir le bon fournisseur de PCB de contrôle industriel
Choisir un fournisseur de PCB de contrôle industriel implique plusieurs considérations critiques qui impactent directement la performance et la fiabilité de vos systèmes industriels. Voici ce qu’il faut rechercher et comment South-Electronic répond à ces critères :
Facteurs clés à considérer
Capacités de fabrication
Installations avancées : Assurez-vous que le fournisseur dispose d’installations de fabrication à la pointe de la technologie, capables de gérer la complexité des PCB de contrôle industriel. Adoption de la technologie : Vérifiez si le fournisseur utilise les dernières technologies de fabrication de PCB, essentielles pour produire des cartes de haute qualité répondant aux exigences modernes.
Conformité aux normes industrielles
Certifications : Recherchez des fournisseurs disposant de certifications industrielles pertinentes telles que ISO 9001 pour les systèmes de gestion de la qualité et IPC-A-600 pour les normes de fabrication et d’assemblage de PCB. Conformité réglementaire : Il est essentiel que le fournisseur respecte les normes internationales de sécurité et de qualité, garantissant que les PCB sont adaptés aux applications industrielles mondiales.
Processus d’assurance qualité
Protocoles de test : Vérifiez que le fournisseur dispose de protocoles de test robustes, des vérifications initiales de conception au contrôle qualité final, pour garantir que chaque PCB est conforme aux normes requises pour une utilisation industrielle. Cohérence : La cohérence dans la fabrication et l’assurance qualité est essentielle pour prévenir les défaillances sur le terrain. Une qualité cohérente signifie moins d’interruptions et des coûts de maintenance réduits.
Robustesse de la chaîne d’approvisionnement
Gestion de la chaîne d’approvisionnement : Évaluez la capacité du fournisseur à gérer une chaîne d’approvisionnement mondiale, ce qui est essentiel pour des livraisons en temps opportun et la gestion des perturbations de l’approvisionnement. Relations avec les fournisseurs : Des relations solides avec les fournisseurs de matières premières sont importantes pour garantir la qualité et la disponibilité des matériaux.
Support technique et service client
Support avant et après-vente : Les bons fournisseurs offrent un support complet, aidant à la conception, à la mise en œuvre et au dépannage après le déploiement. Communication : Des canaux de communication efficaces pour traiter rapidement les requêtes et les problèmes sont essentiels.
Ce qui distingue South-Electronic
Fabrication et technologie avancées
South-Electronic se distingue par ses installations de fabrication avancées équipées de technologies de production de PCB de pointe, garantissant une haute précision et une qualité supérieure dans chaque PCB.
Engagement envers les normes et la qualité
South-Electronic possède de nombreuses certifications, y compris ISO 9001 et IPC-A-600, démontrant son engagement envers les normes internationales de qualité et de sécurité. Des protocoles de test rigoureux sont en place pour s’assurer que chaque PCB expédié répond aux critères de qualité les plus exigeants.
Excellence de la chaîne d’approvisionnement
Avec une chaîne d’approvisionnement optimisée et de solides relations avec les fournisseurs, South-Electronic garantit une qualité de matériau fiable et des délais de livraison respectés, même dans des circonstances exigeantes.
Support client inégalé
South-Electronic offre un support technique complet, assistant les clients de la phase de conception à la phase post-vente, garantissant que chaque client trouve la solution parfaite à ses besoins.
Conclusion
Choisir le bon fournisseur de PCB pour les applications de contrôle industriel ne se résume pas à trouver le coût le plus bas ; il s’agit de trouver un partenaire capable de fournir des produits de haute qualité et un support robuste de manière constante. South-Electronic incarne ces attributs, ce qui en fait un choix de premier plan pour les entreprises cherchant des solutions de PCB de contrôle industriel fiables. En s’associant à des fournisseurs comme South-Electronic, vous vous assurez que vos opérations industrielles sont soutenues par la qualité, la fiabilité et un service exceptionnel.
Chapitre 8
Test et vérification des PCB de contrôle industriel
Aperçu
Les PCB de contrôle industriel sont soumis à des protocoles de test rigoureux pour garantir leur performance fiable dans des conditions industrielles réelles. Ces tests sont conçus pour vérifier à la fois la fonctionnalité et la durabilité des PCB, en insistant sur leur capacité à fonctionner en toute sécurité et efficacité dans des environnements difficiles.
Protocoles de test standards
Tests électriques
Test en circuit (ICT) : L’ICT est effectué pour vérifier les courts-circuits, les circuits ouverts, la résistance, la capacité et d’autres caractéristiques électriques afin de s’assurer que les composants sont correctement installés et fonctionnent. Test fonctionnel : Simule des conditions de fonctionnement pour vérifier que le PCB fonctionne comme prévu avec les entrées et sorties spécifiques qu’il rencontrera dans son utilisation réelle.
Tests environnementaux
Cyclage thermique : Le PCB est soumis à des températures extrêmes pour s’assurer qu’il peut résister aux contraintes thermiques. Ce test aide à identifier les pannes potentielles causées par la dilatation et la contraction des matériaux. Test de choc thermique : Des changements rapides de température sont utilisés pour tester la robustesse des joints de soudure des composants sous contrainte thermique.
Test de vibration et de choc
Test de vibration : Garantit que le PCB peut supporter les vibrations typiquement présentes dans les environnements industriels sans desserrer les composants ou provoquer des défaillances des joints de soudure. Test de choc : Teste la capacité du PCB à résister aux impacts soudains ou aux mouvements brusques, fréquents dans de nombreuses applications industrielles.
Test d’humidité
Exposition à une humidité élevée : Le PCB est exposé à des niveaux élevés d’humidité pour s’assurer que l’humidité ne provoque pas de corrosion ou d’autres défaillances, particulièrement important dans les environnements extérieurs ou industriels difficiles.
Test de résistance chimique
Exposition chimique : Le PCB est exposé aux produits chimiques qu’il pourrait rencontrer dans son environnement opérationnel pour vérifier qu’il ne se dégradera pas ou ne dysfonctionnera pas en raison d’interactions chimiques.
Rôle des tests rigoureux dans le maintien des normes
Assurance fiabilité
Prévention des pannes : Les tests rigoureux aident à identifier et atténuer les points de défaillance potentiels avant que le PCB ne soit déployé sur le terrain, garantissant qu’il est fiable tout au long de sa durée de vie prévue. Amélioration continue : Les retours des résultats des tests conduisent à des améliorations de conception, renforçant la fiabilité des futures versions des PCB.
Conformité aux normes de sécurité
Respect des réglementations : Les tests garantissent la conformité aux normes internationales de sécurité, telles que celles définies par l’IEEE, l’UL ou l’IPC, qui sont cruciales pour maintenir les normes légales et de sécurité dans les applications industrielles. Protection des biens et des personnes : En garantissant que les PCB peuvent résister aux contraintes environnementales et opérationnelles, les tests aident à prévenir les accidents et les défaillances du système qui pourraient mettre en danger des vies humaines et des actifs.
Contrôle de la qualité
Étalonnage : Les tests fixent des repères pour la qualité et les performances, fournissant une norme mesurable que les PCB doivent respecter pour être considérés comme viables pour une utilisation industrielle. Assurance qualité : Grâce à une approche systématique des tests, les fabricants peuvent garantir que chaque PCB expédié respecte des critères de qualité stricts, soutenant des processus de contrôle qualité robustes.
Conclusion
Le test et la validation sont essentiels au processus de fabrication des PCB de contrôle industriel, constituant la pierre angulaire de l’assurance qualité et de la fiabilité. Ces tests garantissent que les PCB peuvent non seulement répondre, mais aussi dépasser les exigences rigoureuses des environnements industriels, tout en maintenant une fiabilité élevée et des normes de sécurité strictes. Cette approche complète des tests permet aux systèmes de contrôle industriel de fonctionner efficacement, réduisant les temps d’arrêt et améliorant l’efficacité opérationnelle globale.
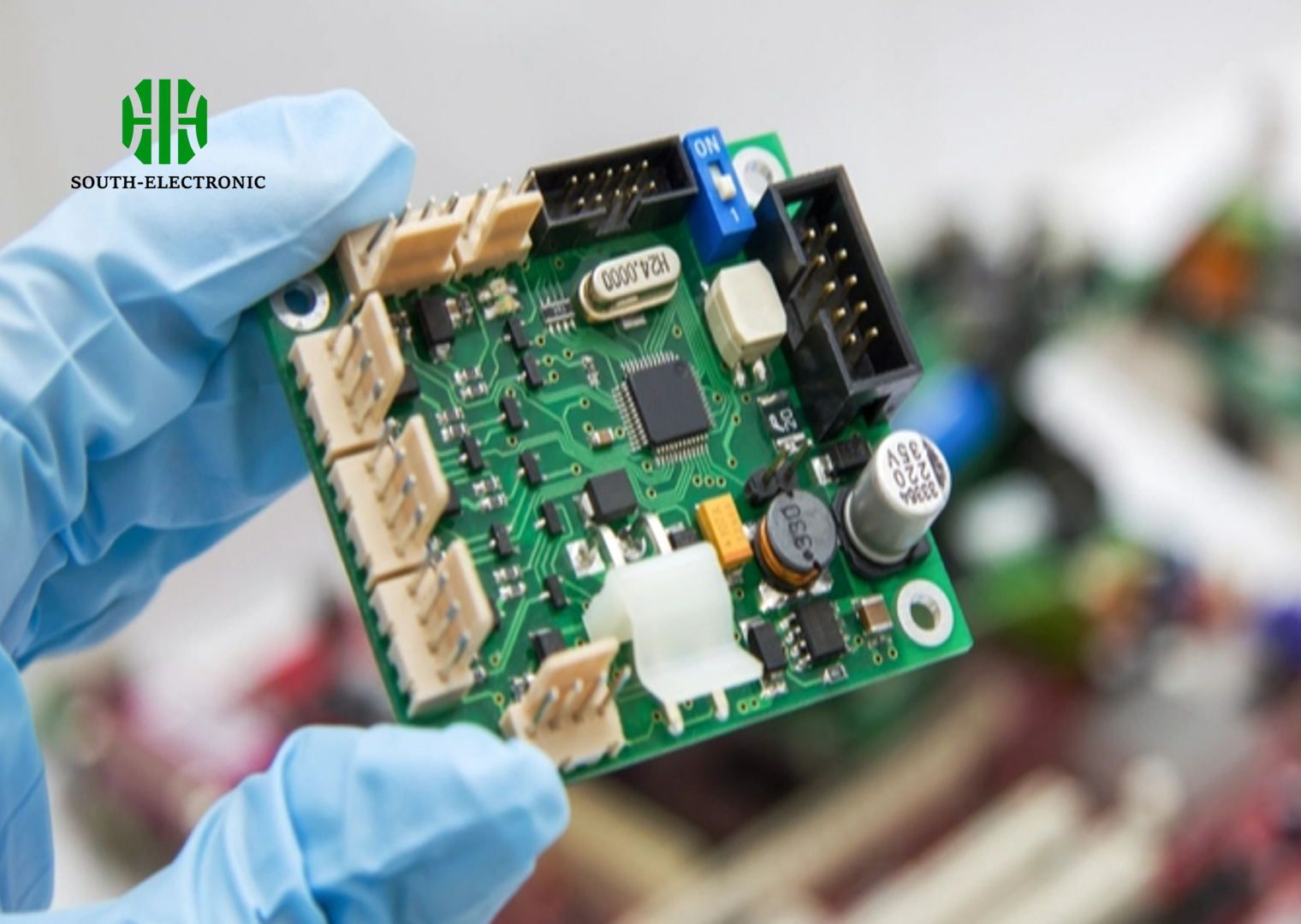
Chapitre 9

Maintenance et optimisation de la durée de vie des PCB de contrôle industriel
Maintenir efficacement les PCB de contrôle industriel est crucial pour maximiser leur durée de vie opérationnelle et garantir leur fiabilité dans des environnements industriels. Voici un guide complet sur les pratiques de maintenance et les conseils de dépannage.
Lignes directrices de maintenance
Nettoyage régulier
Objectif : Élimine la poussière, les débris et les substances corrosives qui peuvent s’accumuler sur le PCB et provoquer des courts-circuits ou de la corrosion. Méthode : Utilisez de l’air comprimé pour éliminer la poussière et des solvants de nettoyage non abrasifs et sûrs pour l’électronique pour enlever la saleté. Assurez-vous que le PCB est hors tension et bien sec avant de redémarrer les opérations.
Inspections de routine
Inspections visuelles : Vérifiez régulièrement les signes d’usure, tels que des composants décolorés, des condensateurs gonflés ou des zones brûlées, qui pourraient indiquer une surchauffe ou des problèmes électriques. Imagerie thermique : Utilisez des caméras thermiques pour détecter les points chauds sur le PCB, qui sont des signes avant-coureurs de défaillances potentielles.
Contrôle de l’environnement
Contrôle climatique : Maintenez un environnement contrôlé avec une température et une humidité régulées pour éviter les dommages dus au stress thermique et à l’humidité. Mesures de protection : Mettez en place des boîtiers et des barrières physiques appropriés pour protéger les PCB des dommages mécaniques et de l’exposition à des produits chimiques nocifs.
Vérification des connexions et des câblages
Vérification de l’intégrité : Inspectez régulièrement toutes les connexions et câblages pour détecter les desserrements ou les dommages, en particulier dans les environnements sujets aux vibrations. Resserrage : Assurez-vous que toutes les vis et connecteurs sont bien serrés et sécurisés pour éviter les pannes intermittentes.
Conseils de dépannage
Tests de diagnostic
Test de continuité : Utilisez un multimètre pour vérifier la continuité des pistes et connexions du PCB, ce qui peut aider à identifier les ruptures ou les courts-circuits. Mesures de tension et de courant : Mesurez régulièrement les tensions et les courants dans les parties critiques du circuit pour vous assurer qu’ils sont dans les limites spécifiées.
Test des composants
Condensateurs et résistances : Vérifiez les signes de vieillissement ou de défaillance des condensateurs et résistances, comme le gonflement, les fuites ou les changements drastiques de valeurs de résistance. Dispositifs à semi-conducteurs : Testez les transistors, diodes et circuits intégrés avec un multimètre ou un testeur de semi-conducteurs pour vous assurer qu’ils fonctionnent correctement.
Mises à jour du firmware et des logiciels
Mises à jour : Mettez régulièrement à jour les logiciels et firmwares pour corriger les bugs et améliorer les performances, ce qui peut également résoudre des problèmes liés aux logiciels qui se manifestent comme des problèmes matériels. Sauvegarde et restauration : Effectuez des sauvegardes régulières du firmware et des paramètres de configuration, qui peuvent être restaurés pour résoudre rapidement les problèmes liés à la corruption des logiciels.
Remplacement des pièces usées
Remplacement préventif : Identifiez et remplacez les composants ayant une durée de vie limitée avant leur défaillance, tels que les condensateurs et relais, en fonction des recommandations du fabricant. Pièces de rechange : Gardez des pièces de rechange critiques en stock pour minimiser les temps d’arrêt lors des opérations de maintenance ou des pannes imprévues.
Conclusion
Une maintenance efficace et un dépannage proactif sont essentiels pour prolonger la durée de vie et améliorer la fiabilité des PCB de contrôle industriel. En appliquant ces lignes directrices, les industries peuvent s’assurer que leurs systèmes de contrôle continuent de fonctionner efficacement sans interruption, protégeant ainsi la productivité et réduisant les coûts de maintenance liés aux arrêts non planifiés et aux réparations.
Chapitre 10
Innovations et perspectives futures des PCB de contrôle industriel
Le domaine des PCB de contrôle industriel évolue rapidement, poussé par les avancées technologiques et la demande croissante pour des systèmes plus efficaces, fiables et intelligents. Voici un aperçu des tendances émergentes et comment une entreprise leader comme South-Electronic se positionne à l’avant-garde de ces développements.
Tendances émergentes et avancées technologiques
Intégration de l’IoT et des technologies intelligentes
PCB intelligents : L’intégration des capacités de l’IoT dans les PCB de contrôle industriel permet la collecte de données en temps réel, la surveillance et le contrôle, ce qui améliore l’efficacité opérationnelle et les capacités de maintenance prédictive. Edge Computing : L’intégration de la puissance de calcul directement sur le PCB pour traiter les données en périphérie réduit la latence et la dépendance aux systèmes centraux, améliorant ainsi la réactivité des systèmes de contrôle.
Utilisation de matériaux avancés
Substrats haute performance : Des matériaux comme le polyimide, offrant une meilleure résistance à la chaleur et des propriétés mécaniques améliorées, deviennent de plus en plus courants pour répondre aux conditions exigeantes des applications industrielles. Innovations en gestion thermique : Le développement de substrats avec une meilleure conductivité thermique et l’intégration de canaux de refroidissement dans le PCB aident à mieux gérer la chaleur dans les applications à haute puissance.
Miniaturisation et interconnexion haute densité (HDI)
PCB plus petits et plus efficaces : Les avancées dans la technologie HDI permettent de fabriquer des PCB plus petits avec des composants plus densément intégrés, ce qui est crucial pour les applications industrielles modernes où l’espace est limité. Technologie Microvia : L’utilisation des microvias permet d’ajouter plus de couches dans les PCB, augmentant ainsi la fonctionnalité tout en réduisant la taille et le poids.
Flexibilité et conception modulaire
PCB flexibles : Avec la montée des applications industrielles dynamiques, les PCB flexibles capables de se conformer à diverses formes et de résister aux flexions et mouvements sont de plus en plus essentiels. PCB modulaires : Concevoir des PCB modulaires facilite les mises à niveau rapides et la maintenance, réduisant les temps d’arrêt et permettant une adaptation plus rapide aux changements technologiques.
Comment South-Electronic mène l’innovation
Adoption de technologies de pointe
Investissement en R&D : South-Electronic investit massivement dans la recherche et développement pour rester en avance sur les tendances technologiques, garantissant que leurs solutions PCB intègrent les dernières avancées en matière de conception et de fabrication électronique. Collaborations : En s’associant avec des leaders technologiques et des universités, South-Electronic reste connectée aux écosystèmes d’innovation pour intégrer des technologies novatrices dans ses PCB.
Personnalisation et évolutivité
Solutions sur mesure : South-Electronic se spécialise dans la fourniture de solutions PCB personnalisées répondant aux besoins industriels spécifiques, offrant une évolutivité allant des prototypes en petite série à la production à grande échelle, sans compromettre la précision ou la qualité. Fabrication agile : Grâce à des processus de fabrication agiles, South-Electronic s’adapte rapidement aux changements dans les exigences des clients et les avancées technologiques.
Durabilité et conformité
Matériaux écologiques : En mettant l’accent sur l’utilisation de matériaux et de processus durables, South-Electronic veille à ce que ses PCB soient non seulement performants mais aussi conformes aux normes environnementales mondiales. Conformité aux normes industrielles : Le maintien d’une adhésion stricte aux normes internationales de qualité et de sécurité est une priorité pour garantir que chaque PCB livré est prêt pour les rigueurs de l’utilisation industrielle.
Développements futurs à prévoir
À l’avenir, les tendances vers l’automatisation, la prise de décision basée sur les données et la durabilité environnementale continueront d’influencer le développement des PCB de contrôle industriel. Nous pouvons nous attendre à voir de nouvelles avancées dans les technologies des PCB intelligents, les sciences des matériaux et les techniques de fabrication qui amélioreront la connectivité, l’efficacité et l’éco-responsabilité de ces composants essentiels.
Conclusion
Le domaine des PCB de contrôle industriel est en pleine phase d’innovation et d’adaptation rapide. Des entreprises comme South-Electronic ne se contentent pas de suivre le rythme, mais façonnent activement l’avenir de ce secteur grâce à une innovation continue, un engagement envers la qualité et des stratégies tournées vers l’avenir. À mesure que la technologie progresse, les possibilités de systèmes de contrôle industriel plus intelligents, plus efficaces et plus flexibles semblent infinies.
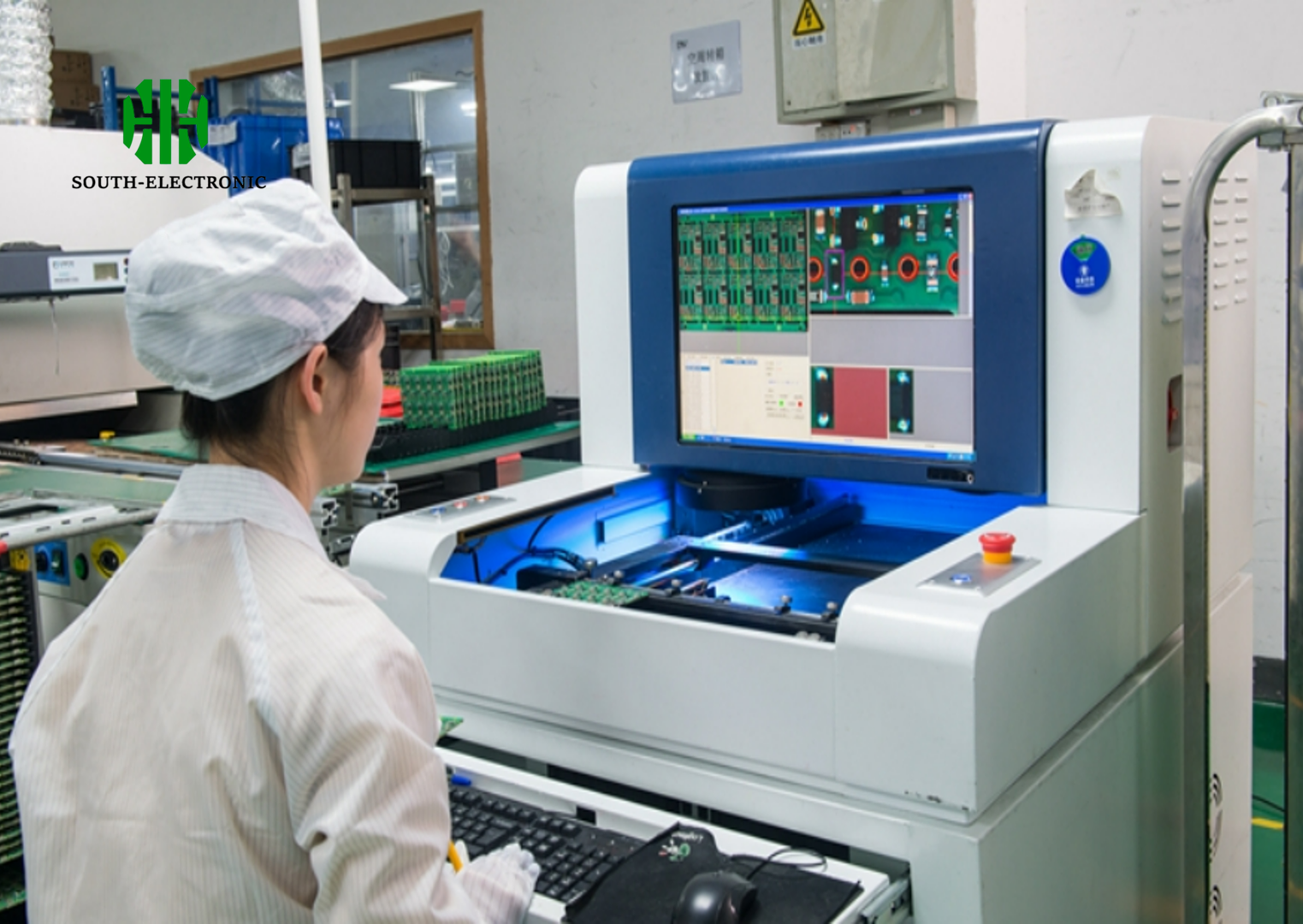
Contactez-nous
Où sommes-nous ?
Parc industriel, No. 438 Donghuan Road, No. 438, Shajing Donghuan Road, District de Bao'an, Shenzhen, Guangdong, Chine
4ème étage, bâtiment Zhihui Creative, No.2005 Xihuan Road, Shajing, district de Bao'an, Shenzhen, Chine
SALLE A1-13, 3ème étage, YEE LIM INDUSTRIAL CENTRE, 2-28 KWAI LOK STREET, KWAI CHUNG, HK
service@southelectronicpcb.com
Téléphone : +86 400 878 3488
Envoyez-nous un message
Plus vous fournissez de détails, plus nous pourrons passer rapidement à l’étape suivante.
