Introduction
Dans le monde dynamique de la production électronique, la recherche de méthodes qui équilibrent coût, efficacité et performances de premier ordre est incessante. Au milieu de ce paysage regorgeant d’innovations, la technologie jet d’encre pour la création de substrats de circuits imprimés (PCB) s’est imposée comme une redoutable rivale, bousculant la suprématie de longue date des approches semi-additives et soustractives conventionnelles.
Techniques traditionnelles : procédés semi-additifs et soustractifs
La fabrication traditionnelle de PCB utilise principalement deux méthodes : les processus semi-additifs et soustractifs.
Procédés semi-additifs (SAP)
Le processus semi-additif est une méthode dans laquelle le motif de circuit est ajouté au substrat non conducteur plutôt que d’être retiré d’une couche conductrice. Étapes clés :
- Nettoyage et préparation du support.
- Dépôt d’une fine couche de cuivre sur l’ensemble du substrat.
- Application d’une couche de photorésist.
- Exposition à la lumière à travers un masque à motif.
- Développement de la couche de photorésist pour éliminer les parties non exposées.
- Galvanoplastie pour augmenter l’épaisseur du cuivre uniquement dans les zones souhaitées.
- Enlever la résine photosensible restante et graver pour éliminer tout cuivre indésirable.
Processus soustractifs
Le processus soustractif commence par une couche de cuivre conductrice pré-appliquée sur toute la surface du substrat. Le motif de circuit souhaité est transféré sur cette couche de cuivre à l’aide d’un masque de résistance, après quoi le cuivre exposé est chimiquement gravé, laissant derrière lui le motif de circuit. Étapes clés :
- Application d’une couche de cuivre sur le substrat.
- Application d’une couche de photorésist sur le cuivre.
- Exposition à la lumière à travers un masque à motif, durcissant la réserve là où le cuivre doit rester.
- Gravure chimique pour éliminer le cuivre non protégé.
- Enlever la réserve durcie pour révéler le circuit de cuivre final.
Les deux processus ont leurs avantages et leurs défis uniques. Le procédé semi-additif est de plus en plus privilégié pour les PCB avancés à haute densité où la précision et la miniaturisation sont primordiales. Le processus soustractif, quant à lui, reste un incontournable pour un large spectre d’applications en raison de sa simplicité et de son efficacité pour la production de circuits imprimés standard. Le choix entre SAP et les processus soustractifs dépend des exigences spécifiques du PCB, notamment de sa densité, de sa complexité et des contraintes de coût du projet.
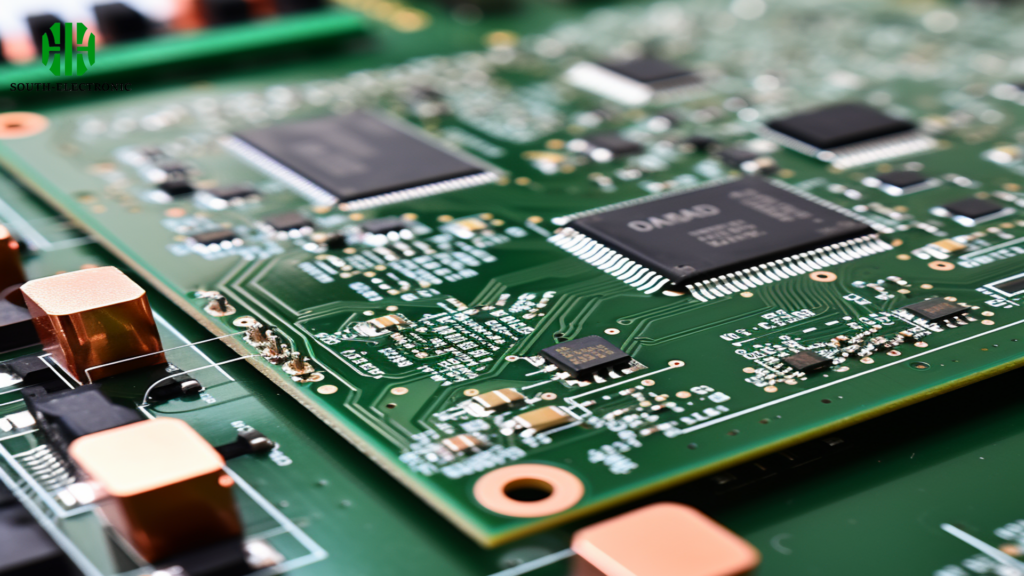
Fabrication de PCB à jet d’encre
À la base, la fabrication de PCB à jet d’encre utilise un processus d’impression numérique similaire à celui des imprimantes à jet d’encre standard utilisées pour le papier. Cependant, au lieu d’encre, il utilise des encres ou des pâtes conductrices spécialement formulées. L’impression à jet d’encre applique le matériau uniquement là où cela est nécessaire, minimisant ainsi les déchets. Étapes clés :
- Conception et disposition : tout comme la fabrication traditionnelle de circuits imprimés, le processus commence par la création d’une conception de circuit à l’aide d’un logiciel de conception assistée par ordinateur (CAO). Cette conception numérique dicte le dépôt de l’encre conductrice.
- Préparation du substrat : Le matériau du substrat, qui peut varier des matériaux rigides traditionnels aux plastiques flexibles, est préparé et placé dans l’imprimante à jet d’encre.
- Impression jet d’encre : l’imprimante dépose ensuite avec précision l’encre conductrice sur le substrat, en suivant le plan CAO. Selon la complexité du circuit et les besoins spécifiques, cette phase peut nécessiter une ou plusieurs itérations.
- Durcissement/Séchage : Après l’impression, le substrat subit un processus de durcissement ou de séchage. Les spécificités de cette étape dépendent du type d’encre utilisé, certaines encres nécessitant de la chaleur ou de la lumière UV pour se solidifier et adhérer correctement au substrat.
- Inspection et tests : La dernière étape consiste à inspecter le PCB imprimé pour déceler tout défaut et à effectuer des tests électriques pour garantir la fonctionnalité.
La fabrication de PCB à jet d’encre incarne un changement de paradigme dans la fabrication de PCB, offrant un mélange d’efficacité, de flexibilité et d’innovation. À mesure que la technologie mûrit et surmonte ses limites actuelles, elle promet d’avoir un impact significatif sur le paysage de la fabrication électronique, en particulier dans les domaines nécessitant des délais d’exécution rapides et une flexibilité dans la conception et les matériaux.
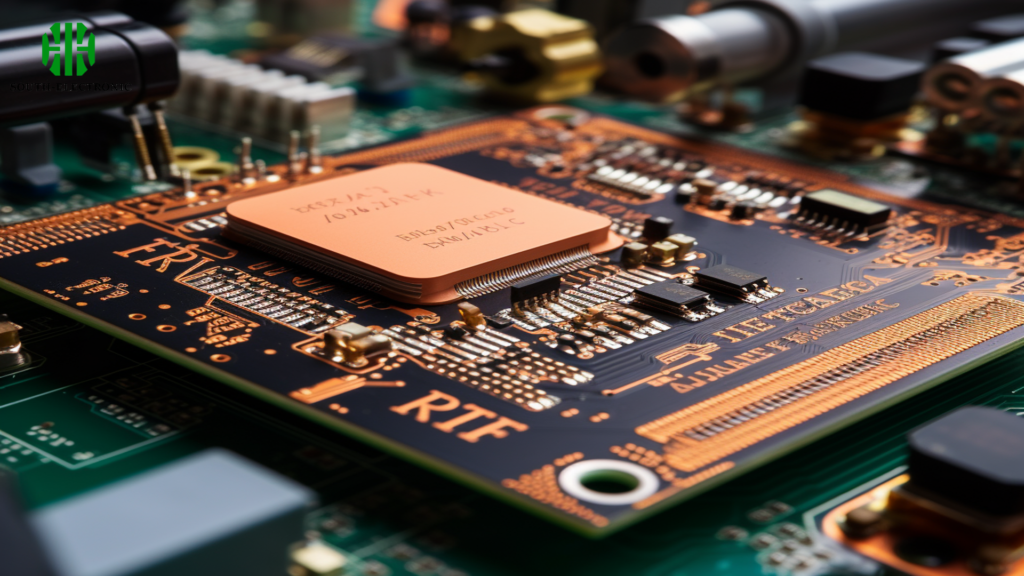
Quel est le meilleur?
La détermination de la « meilleure » méthode de fabrication entre le jet d’encre et les techniques traditionnelles dépend des critères spécifiques les plus importants pour le projet en cours, qu’il s’agisse du coût, de la flexibilité, de l’impact environnemental ou des performances. Bien que les techniques traditionnelles aient actuellement l’avantage en termes de performances et de fiabilité, en particulier pour les applications RF, la fabrication à jet d’encre apporte des avantages notables en termes de réduction des coûts, de polyvalence et de durabilité environnementale. Concernant les technologies naissantes, bien qu’elles soient au stade expérimental, elles ont le potentiel de surpasser à la fois les méthodes à jet d’encre et les méthodes traditionnelles en termes d’efficacité RF et de productivité de fabrication.
Conclusion
L’avènement de la fabrication de circuits imprimés à jet d’encre offre un aperçu alléchant de l’avenir de la fabrication électronique, promettant des réductions de coûts et potentiellement révolutionnant la production de composants RF. Cependant, la transition des méthodes traditionnelles semi-additives et soustractives ne se fait pas sans défis. En explorant plus en détail les performances comparatives des RF, le choix entre adopter l’innovation ou adhérer à la tradition implique de peser des facteurs tels que le coût, l’efficacité, les considérations environnementales et les capacités technologiques.