Services d'assemblage SMT
South-Electronic
Choisissez South-Electronic, vous bénéficierez d'une qualité et d'une précision inégalées du début à la fin. Associez-vous à South-Electronic aujourd'hui et laissez-nous vous aider à faire passer vos projets au niveau supérieur avec des solutions innovantes et de haute qualité !
Votre fournisseur de confiance pour l'assemblage de PCB SMT
Bienvenue chez South-Electronic, où vous trouverez des services d’assemblage de PCB SMT de haute qualité, réputés pour leur précision et leur fiabilité.
Nos assemblages de PCB SMT offrent des performances excellentes, ce qui les rend parfaits pour une large gamme d’applications. Choisissez parmi des cartes à une couche, à deux couches et à plusieurs couches, toutes personnalisées pour répondre à vos besoins électroniques spécifiques. Que vous amélioriez l’efficacité des appareils électroniques grand public ou que vous ayez besoin d’une opération fiable dans les contrôles industriels, nos services d’assemblage de PCB SMT excellent dans la livraison de l’efficacité et de la précision. Comptez sur South-Electronic pour une qualité et une constance exceptionnelles dans vos entreprises électroniques. Nos assemblages de PCB SMT améliorent la fonctionnalité de vos appareils avec une fiabilité et des performances supérieures. Associez-vous à nous pour l’excellence et l’innovation dans votre domaine.

Assemblage SMT à face unique
L'assemblage SMT à face unique est lorsque vous placez des composants sur une face de la carte. C'est idéal pour les conceptions plus simples et moins chères où vous n'avez pas besoin de tant de composants. Il est beaucoup utilisé dans les appareils électroniques de base parce qu'il est abordable et facile à fabriquer.
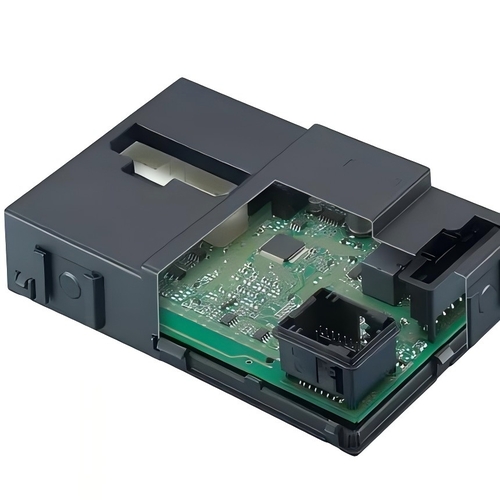
Assemblage SMT à double face
L'assemblage SMT à double face est lorsque vous placez des composants sur les deux faces de la carte. Cela vous permet de placer plus de composants sur la carte et de réaliser plus de choses avec. C'est idéal pour les conceptions plus complexes qui nécessitent plus d'espace pour les composants et c'est mieux pour les appareils électroniques plus avancés.
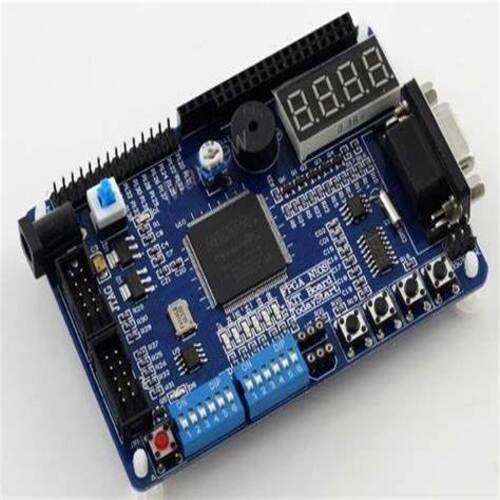
Assemblage à matrice de billes (BGA)
L'assemblage BGA est lorsque vous utilisez une grille de billes de soudure pour connecter les composants à la carte. C'est idéal pour les circuits de haute densité et de haute performance comme les CPU et les GPU. Le BGA offre de meilleures performances électriques et une meilleure dissipation de la chaleur, ce qui le rend idéal pour les appareils de technologie avancée qui nécessitent des connexions petites et fiables.
Pourquoi choisir South-Electronic ?
Choisissez South-Electronic pour notre expertise dans les services d’assemblage SMT personnalisés et de haute qualité pour une large gamme d’applications. Notre équipe a une expérience étendue, ce qui signifie que nous pouvons offrir une qualité supérieure à des prix compétitifs et un service exceptionnel du début à la fin.
-
Précision et Qualité
Votre projet mérite rien de moins que les normes les plus élevées.
Chez South-Electronic, nous nous assurons de la précision et de la fiabilité dans chaque assemblage SMT que nous produisons, en garantissant que vos produits soient parfaits et fonctionnent exactement comme prévu. -
Personnalisation flexible
Nous adaptons nos services pour répondre à vos exigences spécifiques, que vous ayez besoin d'un assemblage simple face, double face ou BGA.
Quels que soient vos besoins, vous pouvez adapter vos commandes avec flexibilité, tout en maintenant une qualité incompromissable. -
Délai de réalisation rapide
Nous comprenons que le temps est crucial pour votre entreprise.
C'est pourquoi nos lignes de production très efficaces vous permettent de recevoir vos commandes rapidement, ce qui vous aide à respecter vos délais et à maintenir vos projets sur la bonne voie. -
Équipe expérimentée
Lorsque vous travaillez avec nous, vous êtes soutenu par une équipe ayant des années d'expérience dans l'assemblage de PCB.
Vous bénéficierez de la confiance de travailler avec des professionnels qui comprennent votre industrie et savent répondre à vos besoins spécifiques. -
Solution tout-en-un
De la conception initiale à l'assemblage final, nous prenons en charge chaque étape du processus.
Avec nous, vous bénéficiez de la commodité d'un partenaire de services complets qui peut gérer tous vos besoins en PCB de manière transparente, ce qui vous donne la tranquillité d'esprit et simplifie votre flux de travail. -
Aucune exigence de commande minimale
Vous avez la liberté de commander exactement ce dont vous avez besoin, quelle que soit la quantité.
Même si cela ne concerne qu'une seule unité, nous sommes là pour répondre à vos exigences sans contraintes de commande minimale, ce qui vous donne une flexibilité complète dans vos décisions d'achat.
Projets liés que nous avons réalisés
Avis des clients
Questions fréquentes
Questions les plus populaires
South-Electronic est spécialisé dans l'assemblage d'une large gamme de PCB, notamment des cartes à face unique, des cartes à face double et des cartes multi-couches, ainsi que des assemblages de matrice de balles (BGA). Ils répondent aux besoins de diverses industries et peuvent gérer à la fois des conceptions simples et complexes.
South-Electronic suit des processus de contrôle de qualité stricts tout au long de l'assemblage SMT. Ils utilisent des équipements avancés et effectuent des inspections approfondies à chaque étape, garantissant que chaque assemblage répond à des normes précises. Ils sont également certifiés ISO 9001, ce qui ajoute une autre couche de garantie en termes de qualité et de fiabilité.
Le délai de livraison typique varie en fonction de la complexité et de la quantité de la commande. Cependant, South-Electronic se targue d'offrir des délais de réalisation rapides, achevant la plupart des projets en quelques semaines, tout en proposant des services accélérés pour les commandes urgentes.
Pour obtenir un devis précis, vous devrez fournir des informations détaillées telles que vos fichiers de conception de PCB (fichiers Gerber), votre liste de matériel (BOM), la quantité et tout spécification d'assemblage particulière. Plus vos informations sont précises, plus le devis sera personnalisé.
South-Electronic détient la certification ISO 9001, démontrant son engagement envers la gestion de la qualité et les normes de production. Ils assurent la précision et la fiabilité grâce à des tests rigoureux, des équipements de pointe et des techniciens expérimentés qui surveillent tous les aspects du processus d'assemblage.
South-Electronic propose un support après-vente complet, y compris une garantie sur ses assemblages SMT. Ils proposent généralement une garantie de cinq ans, garantissant aux clients qu'ils sont couverts contre tout défaut ou problème potentiel. Leur équipe de service client est toujours disponible pour aider à résoudre tout problème après-vente.
Envoyez-nous un message
Le Guide Complet pour l'Assemblage SMT
Contenu
Chapitre 1
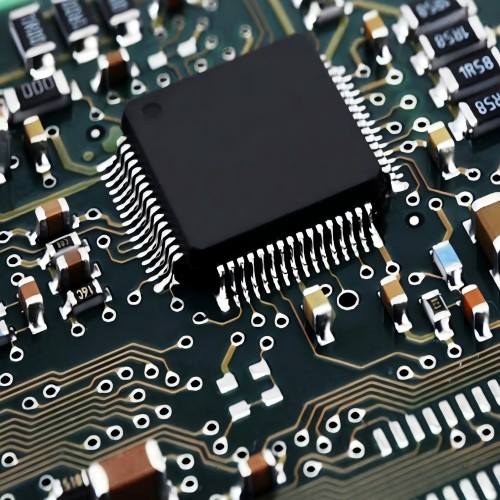
Introduction à l'assemblage SMT
La technologie de montage en surface (SMT) est un moyen de réaliser des circuits électroniques. Au lieu de mettre les composants à travers des trous dans la carte de circuit, les composants sont placés sur la surface de la carte. Cela rend la carte de circuit plus petite et meilleure. La SMT est utilisée pour fabriquer tous les types d’électronique, comme les téléphones, les ordinateurs et d’autres choses que nous utilisons tous les jours. C’est la meilleure façon de fabriquer des électroniques car cela les rend plus petites, plus rapides et moins chères.
La SMT est meilleure que l’ancienne méthode de fabrication d’électroniques car elle rend les composants plus petits. Les composants de la SMT sont appelés dispositifs de montage en surface (SMD). Ils sont beaucoup plus petits que les anciens composants. Cela signifie que les électroniques peuvent être plus petites. La SMT rend également les composants plus rapides. Les composants sont placés sur la carte par une machine, donc c’est plus rapide que de le faire à la main. La SMT rend également les composants moins chers. La machine peut placer les composants sur la carte plus rapidement et plus souvent qu’une personne ne le peut. Cela rend les composants moins chers. La SMT est la meilleure façon de fabriquer des électroniques car elle les rend plus petites, plus rapides et moins chères.
La SMT est la meilleure façon de fabriquer des électroniques car elle les rend plus petites. Les composants de la SMT sont plus petits que les anciens composants. Cela signifie que les électroniques peuvent être plus petites. La SMT est la meilleure façon de fabriquer des électroniques car elle les rend plus rapides. Les composants sont placés sur la carte par une machine, donc c’est plus rapide que de le faire à la main. La SMT est la meilleure façon de fabriquer des électroniques car elle les rend moins chères. La machine peut placer les composants sur la carte plus rapidement et plus souvent qu’une personne ne le peut. Cela rend les composants moins chers. La SMT est la meilleure façon de fabriquer des électroniques car elle les rend plus petites, plus rapides et moins chères.
Chapitre 2
Comment fonctionne l'assemblage SMT
L’assemblage SMT est un processus hautement automatisé utilisé pour fixer directement des dispositifs de montage en surface (SMD) à la surface d’une carte de circuit imprimé (PCB). Voici une explication étape par étape de la façon dont fonctionne l’assemblage SMT et des principaux composants impliqués :
Étape 1 : Appliquer la pâte de soudure
Le processus commence par l’application de pâte de soudure sur la PCB. Un pochoir est placé sur la carte pour s’assurer que la pâte est appliquée uniquement aux zones où les composants seront montés. La pâte de soudure, un mélange de petites billes de soudure et de flux, agit comme un adhésif pour maintenir les composants en place avant la soudure et crée des connexions électriques entre les bornes du composant et les pads de la PCB.
Étape 2 : Machines de prise et de pose
Une fois la pâte de soudure appliquée, la PCB est passée à une machine de prise et de pose. Cette machine très précise prend les petits composants de montage en surface sur des bobines ou des plateaux et les place sur la PCB selon le découpage de conception. Les machines de prise et de pose modernes sont capables de placer des milliers de composants par heure, garantissant rapidité et précision.
Étape 3 : Soudage par refusion
Après la pose des composants sur la carte, l’assemblage passe dans le four de refusion. Ici, la PCB est chauffée à une température spécifique, faisant fondre la pâte de soudure et formant des joints de soudure solides. Le processus de refusion est soigneusement contrôlé pour s’assurer que la soudure fonde et se solidifie sans endommager les composants ou la PCB elle-même. Une fois que la carte a refroidi, les composants sont solidement fixés et les connexions électriques sont établies.
Étape 4 : Inspection et test
Une fois le processus de soudage terminé, la PCB subit une inspection pour garantir un assemblage correct. Les machines d’inspection optique automatisées (AOI) analysent la carte pour vérifier la présence de composants manquants, de défauts de soudure et de désalignements. Dans certains cas, une inspection aux rayons X peut également être utilisée, en particulier pour des assemblages complexes comme les packages à grille de billes (BGA) où les joints de soudure sont cachés sous le composant.
Composants clés impliqués dans l’assemblage SMT
- Pâte de soudure : Un mélange de flux et de particules de soudure fines qui maintient temporairement les composants en place et crée finalement les joints de soudure pendant la refusion.
- Machine de prise et de pose : Équipement automatisé qui place les composants sur la PCB avec une grande précision, gérant même les plus petits SMD.
- Four de refusion : Un four spécialisé qui chauffe la PCB pour faire fondre la pâte de soudure et fixer solidement les composants à la carte.
- Pochoir : Un gabarit utilisé pour appliquer avec précision la pâte de soudure à des zones spécifiques de la PCB.
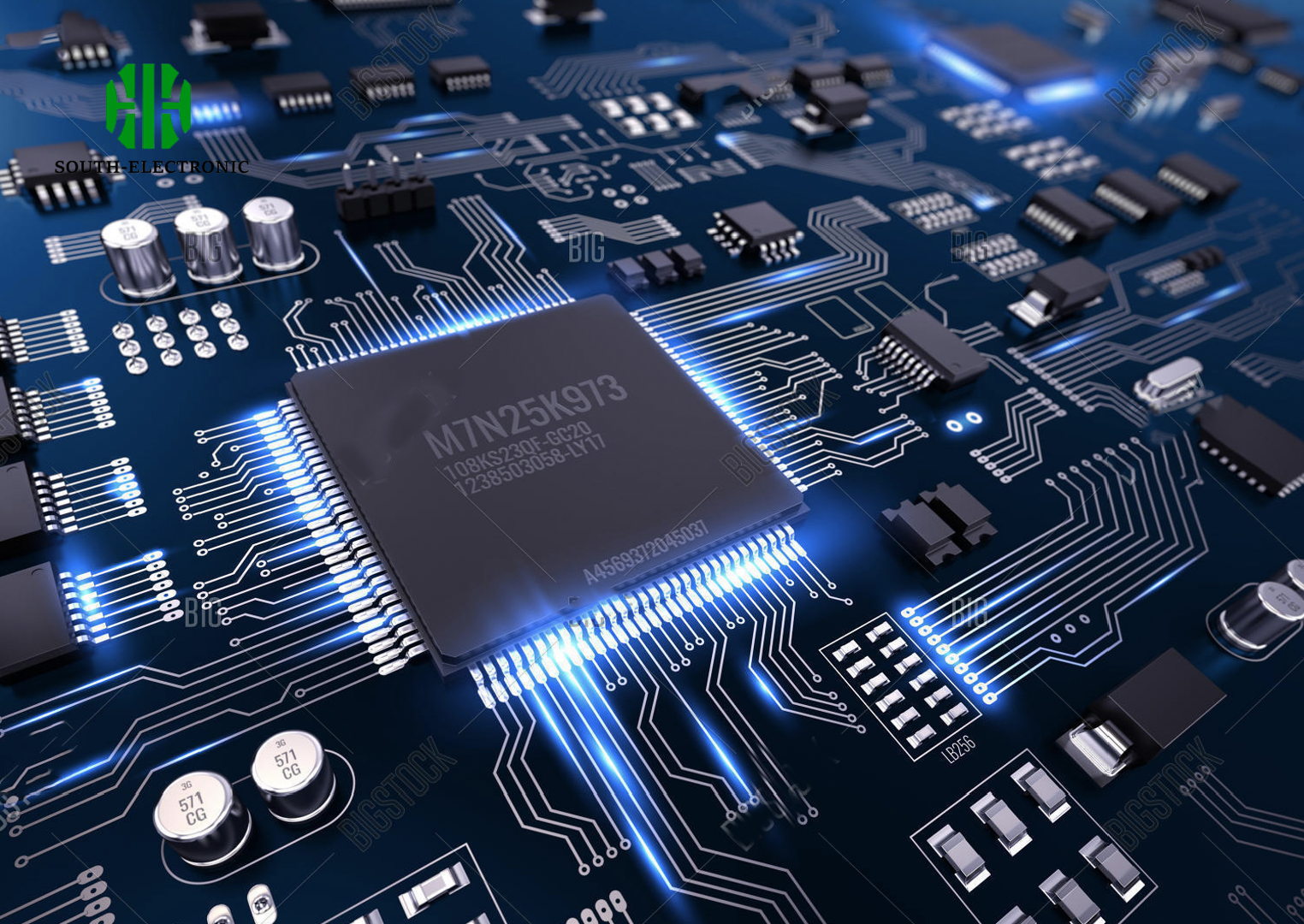
Chapitre 3

The SMT Assembly Process
Le montage SMT existe sous différentes formes en fonction de la complexité et des exigences de la conception de la carte de circuit imprimé (PCB). Les principaux types comprennent les montages SMT à face unique, à double face et multi-couches, chacun offrant des avantages uniques en termes d’utilisation de l’espace, de fonctionnalité et de performance. De plus, des techniques de montage avancées telles que le Ball Grid Array (BGA) et le Chip-on-Board (COB) fournissent des solutions spécialisées pour les électroniques hautes performances.
Montage SMT à face unique
Le montage SMT à face unique implique le montage de tous les composants sur une face de la carte de circuit imprimé. Ce type de montage est généralement utilisé dans des conceptions plus simples et rentables où moins de composants sont nécessaires, ce qui le rend idéal pour les électroniques de base. Il est largement utilisé dans les produits grand public tels que les appareils électroménagers, les télécommandes et les gadgets électroniques de base. Le montage SMT à face unique est préféré lorsque la conception est simple, que l’espace n’est pas une contrainte majeure et que les exigences de fonctionnalité sont relativement faibles.
- Avantages : faible coût, fabrication plus facile, convient aux conceptions simples.
- Applications : électronique de base, appareils d’entrée de gamme et circuits à faible densité.
Montage SMT à double face
Dans le montage SMT à double face, les composants sont montés des deux côtés de la carte de circuit imprimé, ce qui permet une plus grande densité de composants et une fonctionnalité accrue. Ce type de montage est idéal pour des électroniques plus complexes où plus de composants sont nécessaires, mais où l’espace est limité. Le montage SMT à double face permet aux concepteurs d’utiliser efficacement les deux faces de la carte de circuit imprimé, en optimisant le layout et en améliorant les performances globales du produit.
- Avantages : plus grande densité de composants, plus de fonctionnalités, utilisation efficace de l’espace.
- Applications : appareils de télécommunication, équipements médicaux, systèmes de contrôle industriels et autres électroniques compactes hautes performances.
Montage SMT multi-couches
Le montage SMT multi-couches implique l’utilisation de cartes de circuit imprimé avec plusieurs couches de chemins conducteurs empilés, séparés par des couches isolantes. Cela permet une densité de composants encore plus grande et des conceptions plus complexes, permettant de meilleures performances sans augmenter la taille de la carte. Le montage SMT multi-couches est essentiel pour les appareils qui nécessitent une fonctionnalité avancée, un traitement de données haute vitesse ou une intégrité de signal élevée dans un facteur de forme compact.
- Avantages : prend en charge les conceptions complexes hautes performances, réduit les interférences électromagnétiques et permet une transmission de données plus rapide.
- Applications : smartphones, ordinateurs portables, systèmes de communication avancés et électronique aérospatiale.
Montage Ball Grid Array (BGA)
Le montage BGA est un type spécialisé de montage SMT où les composants sont montés à l’aide d’une grille de petites billes de soudure sur le dessous du composant. Le BGA offre plusieurs avantages par rapport aux méthodes SMT traditionnelles, notamment de meilleures performances électriques, une meilleure dissipation thermique et la possibilité de gérer une grande densité de connexions dans une zone compacte. Le BGA est couramment utilisé pour des composants tels que les processeurs, les GPU et les puces de mémoire, où les performances et la fiabilité sont critiques.
- Avantages : performances électriques améliorées, dissipation thermique améliorée, prend en charge des connexions à haute densité.
- Applications : CPU, GPU, modules de mémoire et autres composants informatiques hautes performances.
Technologie Chip-on-Board (COB)
La technologie Chip-on-Board (COB) est une méthode de conditionnement avancée dans laquelle les puces de semi-conducteurs nues sont montées directement sur la carte de circuit imprimé et reliées par des fils à la connectique de la carte. Les puces sont ensuite encapsulées dans une couche protectrice, généralement de la résine époxyde, pour les protéger des facteurs environnementaux. La technologie COB est avantageuse pour des applications nécessitant des conceptions compactes et des caractéristiques hautes performances, car elle réduit le nombre d’étapes de conditionnement intermédiaires, réduisant ainsi le coût et la taille du montage.
- Avantages : empreinte plus petite, coût plus faible et fiabilité améliorée en raison de moins de connexions.
- Applications : éclairage LED, capteurs, modules électroniques compacts et électronique grand public.
Résumé
Chaque type de montage SMT, que ce soit à face unique, à double face ou multi-couches, répond à des besoins de conception différents en fonction de la complexité, de la taille et des exigences de performance du produit. Les technologies BGA et COB sont des méthodes avancées qui améliorent les performances dans les applications à haute densité et à grande vitesse. Ces différents types de montage SMT permettent aux fabricants de construire des produits électroniques de plus en plus compacts, puissants et fiables dans un large éventail d’industries.
Chapitre 4
Solder Paste and Its Importance
La SMT et la technologie à travers les trous sont les deux principales méthodes d’assemblage de composants électroniques sur des cartes de circuit imprimé (PCI). La technologie à travers les trous, qui consiste à insérer les pattes de composant dans des trous pré-percés sur la PCI, était autrefois la norme, mais a été en grande partie remplacée par la SMT en raison de ses nombreux avantages en termes d’efficacité, de performance et de coût. Voici une comparaison détaillée de la SMT et de l’assemblage à travers les trous, ainsi que les principaux avantages offerts par la SMT.
Comparaison de la SMT et de l’assemblage à travers les trous
1.Montage de composants
- Assemblage à travers les trous : Les composants de la technologie à travers les trous ont des pattes qui sont insérées dans des trous percés sur la PCI et ensuite soudées sur le côté opposé de la carte. Cela crée une connexion mécanique solide, ce qui rend la technologie à travers les trous idéale pour les composants qui subiront des contraintes mécaniques ou qui seront soumis à des mouvements fréquents.
- Assemblage SMT : En revanche, les composants SMT sont placés directement sur la surface de la PCI sans nécessité de perçage. Ces dispositifs à montage de surface (SMD) sont plus petits, plus légers et plus faciles à manipuler dans les processus d’assemblage automatisés.
2.Utilisation de l’espace
- Assemblage à travers les trous : La technologie à travers les trous nécessite plus d’espace sur la PCI en raison de la taille des composants et de la nécessité de trous percés. Cela limite la densité des composants et rend plus difficile la création de conceptions compactes.
- Assemblage SMT : La SMT permet une densité de composants beaucoup plus élevée car les composants peuvent être placés directement sur la surface de la carte et peuvent être montés des deux côtés de la PCI. C’est particulièrement important pour les électroniques modernes qui nécessitent des conceptions compactes et légères.
3.Vitesse d’assemblage
- Assemblage à travers les trous : L’assemblage à travers les trous tend à être plus lent et plus fastidieux, car chaque composant doit être inséré dans la PCI à la main ou par des machines semi-automatiques. Le processus de perçage ajoute également du temps au cycle de fabrication.
- Assemblage SMT : La SMT est fortement automatisée, utilisant des machines de placement pour positionner les composants avec une grande vitesse et une grande précision. Cette automatisation réduit considérablement le temps d’assemblage et augmente le débit de production, ce qui fait de la SMT la méthode préférée pour la fabrication à grande échelle.
4.Efficacité coûts
- Assemblage à travers les trous : Les étapes supplémentaires requises dans l’assemblage à travers les trous, telles que le perçage de trous et le placement manuel des composants, conduisent à des coûts de production plus élevés. De plus, les composants à travers les trous sont généralement plus grands et plus chers que les composants à montage de surface.
- Assemblage SMT : La SMT est plus rentable en raison de son automatisation, de ses temps d’assemblage plus rapides et de l’utilisation de composants plus petits et moins chers. Avec moins de processus manuels impliqués et la capacité de gérer une production à grande échelle de manière efficace, la SMT réduit les coûts de fabrication globaux.
5.Résistance mécanique
- Assemblage à travers les trous : Les composants à travers les trous offrent une meilleure résistance mécanique car les pattes traversent la carte et sont soudées de l’autre côté. Cela les rend adaptés aux connecteurs ou aux composants soumis à des contraintes physiques ou nécessitant une durabilité, tels que les transformateurs ou les grands condensateurs.
- Assemblage SMT : Bien que les composants SMT soient plus compacts, ils n’offrent pas la même résistance mécanique que les composants à travers les trous. Cependant, pour la plupart des applications électroniques, où la taille, la vitesse et l’efficacité sont privilégiées, la résistance mécanique de la SMT est suffisante.
Principaux avantages de la SMT par rapport à la technologie à travers les trous
1.Efficacité de l’espace
L’efficacité de l’espace est l’un des principaux avantages de la SMT, car elle permet de loger plus de composants sur une seule carte en raison de la plus petite taille des dispositifs à montage de surface (SMD). Cela permet des conceptions à plus haute densité et plus de fonctionnalités dans des espaces plus petits. Des appareils tels que les smartphones, les wearables et les tablettes tirent tous parti de la nature compacte des assemblages SMT, où l’espace est un facteur primordial.
2.Vitesse d’assemblage
La SMT permet une vitesse d’assemblage plus rapide car le processus est presque entièrement automatisé. Des machines telles que les systèmes de placement peuvent positionner les composants rapidement et avec précision, traitant des milliers de composants par heure. Cela se traduit par des temps de production plus courts et la capacité de répondre à des demandes à grande échelle, ce qui est essentiel pour les produits électroniques grand public et autres produits fabriqués en masse.
3.Économies de coûts
L’assemblage SMT est généralement moins coûteux que l’assemblage à travers les trous pour plusieurs raisons :
- Aucun perçage : La SMT élimine la nécessité de percer des trous dans la PCI, ce qui réduit les coûts de production et accélère le processus de fabrication.
- Composants plus petits : Les SMD sont généralement plus petits et moins chers que les composants à travers les trous, permettant aux fabricants de faire des économies sur les matériaux.
- Automatisation : Le niveau élevé d’automatisation de la SMT conduit à des coûts de main-d’œuvre plus bas et à des cycles de production plus rapides, réduisant ainsi les coûts globaux par unité.
4.Flexibilité de conception
La SMT offre une flexibilité de conception avec la possibilité de monter des composants des deux côtés de la PCI, permettant aux concepteurs de créer des cartes plus complexes et multifonctionnelles. Cette flexibilité est particulièrement utile pour les appareils électroniques avancés qui nécessitent des niveaux élevés de fonctionnalité dans des espaces limités. La SMT permet également des conceptions plus innovantes et des produits plus petits et plus légers, ce qui en fait la technologie de choix pour les électroniques portables.
5.Amélioration des performances
Les assemblages SMT tendent à avoir de meilleures performances électriques car les pattes plus courtes utilisées dans les SMD réduisent les effets parasites tels que l’inductance et la résistance. Cela conduit à des vitesses de fonctionnement plus élevées et à une meilleure intégrité des signaux, ce qui est crucial pour les circuits à haute fréquence et à grande vitesse.
6.Amélioration de la dissipation thermique
Les SMD sont plus efficaces pour dissiper la chaleur par rapport aux composants à travers les trous. Le contact étroit entre le composant et la surface de la PCI permet une meilleure transfert thermique, ce qui est particulièrement bénéfique pour les applications qui génèrent beaucoup de chaleur, telles que les électroniques de puissance et les processeurs.
Conclusion
Alors que la technologie à travers les trous conserve encore des applications spécifiques, notamment pour les composants qui nécessitent une résistance mécanique ou sont exposés à des contraintes physiques, la SMT offre des avantages clairs en termes d’efficacité de l’espace, de vitesse d’assemblage, d’économies de coûts et de performances globales. En conséquence, la SMT est devenue le choix préféré pour la plupart des électroniques modernes, des gadgets grand public aux appareils industriels et médicaux, grâce à sa capacité à offrir des solutions à haute densité, à haute performance et rentables.
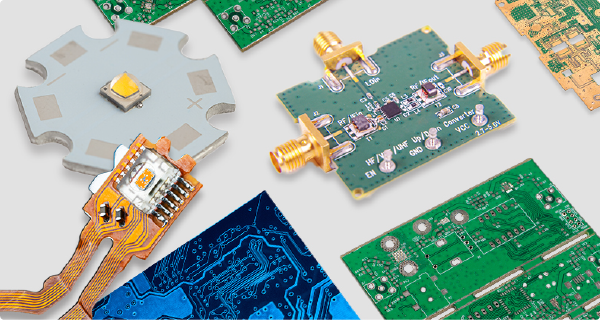
Chapitre 5

Équipement et outils d'assemblage SMT
L’assemblage SMT est un processus hautement automatisé et précis qui nécessite un équipement spécialisé pour assurer l’efficacité, la précision et des résultats de haute qualité. La clé d’un assemblage SMT réussi réside dans l’utilisation de la technologie avancée, qui permet le placement rapide et précis de petits composants sur la surface d’une carte de circuit imprimé (PCI). Dans cette section, nous allons explorer les équipements et outils essentiels utilisés dans le processus d’assemblage SMT et comment ils contribuent à améliorer la précision et l’efficacité.
1. Imprimeur de pâte de soudure
L’imprimeur de pâte de soudure est le premier équipement utilisé dans le processus d’assemblage SMT. Il applique une pâte de soudure – un mélange de particules de soudure métallique fines et de flux – sur la surface de la PCI où les composants seront placés. Un pochoir, qui est une fine feuille de métal avec des ouvertures correspondant aux pads de la PCI, est utilisé pour contrôler l’application exacte et l’épaisseur de la pâte de soudure.
- Objectif : Assure une application précise de la pâte de soudure dans les zones spécifiques de la PCI où les composants seront montés.
- Importance : Une application précise et uniforme de la pâte de soudure est critique pour créer des joints de soudure solides et fiables pendant le processus de refusion.
2. Machine de placement
La machine de placement est l’un des équipements les plus critiques dans l’assemblage SMT. Cette machine hautement automatisée est responsable du prélèvement de composants de montage en surface à partir de bobines ou de plateaux et de leur placement précis sur la PCI. Les machines de placement modernes utilisent des bras robotisés avec aspiration ou pinces pour manipuler même les plus petits composants, les positionnant avec une grande précision à des vitesses incroyablement élevées.
- Objectif : Place les DMS (dispositifs de montage en surface) sur la PCI à leurs emplacements désignés selon le fichier de conception.
- Importance : La vitesse et la précision de la machine de placement sont clés pour l’efficacité globale du processus SMT. Avec les machines modernes capables de placer des milliers de composants par heure, elles réduisent considérablement le temps d’assemblage tout en maintenant une précision exceptionnelle.
3. Four de refusion
Après le placement des composants sur la PCI, l’ensemble de l’assemblage passe par un four de refusion. Ce four spécial chauffe la carte à une température suffisamment élevée pour faire fondre la pâte de soudure, lui permettant de s’écouler et de créer des liaisons électriques et mécaniques solides entre les composants et la PCI. Le four de refusion utilise des profils de température soigneusement contrôlés pour assurer que la soudure fonde et se refroidit de manière uniforme sans endommager les composants sensibles.
- Objectif : Chauffe la PCI pour faire fondre la pâte de soudure et former des joints de soudure solides entre les composants et les pads de la PCI.
- Importance : La soudure de refusion est une étape critique dans le processus SMT, assurant que les composants sont solidement attachés et connectés électriquement. Un contrôle de température approprié dans le four de refusion est essentiel pour prévenir des problèmes tels que le pontage de soudure ou l’endommagement des composants.
4. Inspection optique automatisée (AOI)
Les systèmes d’inspection optique automatisée (AOI) sont utilisés pour inspecter la PCI après la soudure de refusion. Les machines AOI utilisent des caméras à haute résolution et des algorithmes avancés pour scanner la PCI et détecter les défauts tels que des composants manquants, des désalignements, des joints de soudure de mauvaise qualité ou d’autres incohérences. Ce processus d’inspection aide à identifier les problèmes tôt dans le cycle de production, réduisant ainsi le besoin de réparation coûteuse.
- Objectif : Inspecte les PCI pour les défauts, tels que des composants mal alignés ou des problèmes de soudure, après le processus de refusion.
- Importance : L’AOI fournit une méthode efficace et non invasive pour assurer la qualité des assemblages SMT, minimisant ainsi les chances de cartes défectueuses être livrées aux clients.
5. Système d’inspection aux rayons X
Pour les assemblages complexes, tels que ceux impliquant des composants BGA (Ball Grid Array), un système d’inspection aux rayons X est souvent utilisé. Puisque les joints de soudure dans les composants BGA sont cachés sous le paquet, les méthodes d’inspection optique traditionnelles sont insuffisantes. L’inspection aux rayons X permet aux fabricants d’examiner la structure interne des joints de soudure, en identifiant les défauts cachés tels que des vides ou des fissures.
- Objectif : Inspecte les joints de soudure cachés, en particulier dans les composants BGA et d’autres composants où l’inspection visuelle n’est pas possible.
- Importance : L’inspection aux rayons X garantit que même les joints de soudure cachés sont correctement formés, offrant ainsi une plus grande assurance de la fiabilité et de la fonctionnalité de l’assemblage.
6. Imprimeur de pochoir
L’imprimeur de pochoir est utilisé dans les premières étapes de l’assemblage SMT pour appliquer la pâte de soudure de manière précise sur la PCI. Le pochoir est une fine feuille de métal avec des découpes correspondant aux pads de la PCI où la pâte de soudure doit être appliquée. L’imprimeur de pochoir assure que la pâte de soudure est appliquée en quantités précises sur chaque pad, ce qui est essentiel pour former des joints de soudure solides et fiables pendant la refusion.
- Objectif : Applique la pâte de soudure sur la PCI de manière contrôlée à l’aide d’un pochoir.
- Importance : Garantit que la pâte de soudure est déposée uniquement là où elle est nécessaire, en quantités optimales, pour assurer des joints de soudure optimaux dans le produit final.
7. Système d’inspection de la pâte de soudure (SPI)
Un système d’inspection de la pâte de soudure (SPI) est utilisé pour vérifier la qualité et la cohérence de l’application de la pâte de soudure sur la PCI. Cette machine mesure la hauteur, le volume et l’alignement de la pâte de soudure pour s’assurer qu’elle répond aux spécifications requises avant que les composants soient placés sur la carte.
- Objectif : Vérifie la qualité et la cohérence de l’application de la pâte de soudure.
- Importance : Garantit une soudure appropriée en confirmant que la quantité correcte de pâte de soudure a été appliquée sur chaque pad, réduisant les défauts causés par une mauvaise couverture de soudure.
8. Station de réparation
Même avec des niveaux élevés d’automatisation, des erreurs ou des défauts peuvent survenir occasionnellement. Une station de réparation est utilisée pour supprimer manuellement les composants défectueux et les remplacer ou réparer les problèmes de soudure. Elle est équipée d’outils tels que des pistolets à air chaud, des pinces et des fer à souder pour permettre aux techniciens de corriger les erreurs sans endommager la PCI ou d’autres composants.
- Objectif : Permet une correction manuelle des erreurs, telles que le remplacement de composants défectueux ou la réparation des problèmes de soudure.
- Importance : Fournit un moyen de traiter les défauts mineurs sans jeter la carte entière, améliorant ainsi l’efficacité coûts et réduisant les déchets.
Comment la technologie améliore la précision et l’efficacité dans l’assemblage SMT
La technologie moderne joue un rôle essentiel dans la précision et l’efficacité de l’assemblage SMT. L’utilisation d’équipements hautement automatisés, tels que les machines de placement et les fours de refusion, assure que même les plus petits et les composants les plus complexes soient placés et soudés avec une extrême précision. Cette automatisation non seulement accélère le processus de fabrication, mais réduit également le risque d’erreur humaine, conduisant ainsi à des produits de haute qualité et à moins de défauts.
En outre, les systèmes d’inspection avancés comme l’AOI et les machines aux rayons X aident à détecter les défauts tôt dans le processus de production, garantissant que seules des cartes PCI entièrement fonctionnelles et fiables soient livrées aux clients. En intégrant la technologie de pointe, les lignes d’assemblage SMT peuvent produire des assemblages de haute qualité et de grande quantité à une fraction du temps et du coût comparés aux méthodes manuelles.
Conclusion
Le processus d’assemblage SMT repose sur une variété d’équipements et d’outils sophistiqués qui travaillent ensemble pour atteindre une production rapide, précise et rentable. Des imprimeurs de pâte de soudure et des machines de placement aux fours de refusion et aux systèmes d’inspection, chaque pièce d’équipement joue un rôle crucial pour assurer le succès de l’assemblage SMT. À mesure que la technologie continue d’évoluer, la précision et l’efficacité de l’assemblage SMT ne feront qu’améliorer, en faisant de celui-ci le choix préféré pour la fabrication d’électronique moderne.
Chapitre 6
Conception de l'assemblage SMT
La conception de cartes de circuit imprimé (PCI) pour l’assemblage de la technologie de montage en surface (SMT) nécessite une attention scrupuleuse aux détails pour garantir que le processus de fabrication soit efficace, rentable et produise des résultats de haute qualité. Une conception appropriée peut considérablement réduire la probabilité de problèmes d’assemblage et améliorer les performances et la fiabilité du produit final. Cette section couvrira les principaux conseils de conception pour optimiser vos PCI pour l’assemblage SMT et expliquera comment éviter les défauts de conception qui peuvent compliquer le processus d’assemblage.
1. Placement et orientation des composants
Le placement approprié des composants est l’un des aspects les plus critiques de la conception de l’assemblage SMT. Un placement de composant incorrect peut entraîner des problèmes tels que des problèmes d’alignement, du tombstoning ou un pont de soudure pendant le processus de refusion.
Considérations clés :
- Placement uniforme : Assurez-vous que les composants soient placés dans une direction uniforme chaque fois que cela est possible. L’alignement des composants dans la même orientation ne simplifie pas seulement le processus de prise et de placement, mais réduit également les erreurs pendant le placement automatisé.
- Minimiser l’ombrage des composants : Placez les composants plus hauts, tels que les connecteurs ou les condensateurs, loin des composants plus petits pour éviter l’« ombrage » pendant la soudure ou l’inspection, ce qui peut entraîner des erreurs de soudure ou d’inspection.
- Éviter un regroupement serré : Bien que l’efficacité de l’espace soit importante, regrouper les composants trop étroitement peut entraîner des difficultés dans l’application de la pâte de soudure, le pont de soudure ou les problèmes d’inspection. Assurez-vous qu’il y a un espacement suffisant entre les composants.
Meilleure pratique :
- Utilisez des logiciels de conception avec des règles de conception intégrées pour vérifier l’espacement et l’alignement des composants. Suivez les directives du fabricant pour les distances de placement afin d’optimiser l’équipement de placement automatisé.
2. Conception des pads de soudure
Les pads de soudure sont essentiels pour assurer une connexion solide entre la carte de circuit imprimé et les dispositifs de montage en surface (SMD). Une conception de pad de soudure appropriée peut prévenir des problèmes tels que le manque de soudure, le pont de soudure et le mauvais alignement des composants.
Considérations clés :
- Taille et forme du pad : Assurez-vous que les pads de soudure soient de la taille et de la forme correctes pour les composants utilisés. Les pads qui sont trop grands ou trop petits peuvent causer des problèmes de soudure, tels que le mouillage inégal ou les joints de soudure faibles. Pour les composants à pas fin, utilisez des pads plus petits avec un espacement précis.
- Dégagement de la masque de soudure : Assurez-vous qu’il y a un dégagement suffisant entre les pads de soudure et la masque de soudure pour éviter le pont de soudure. La masque de soudure définit la zone où la soudure ne doit pas s’écouler, donc sa conception est critique pour prévenir les courts-circuits.
- Pads thermiques : Pour les composants qui nécessitent une dissipation de chaleur, tels que les transistors de puissance ou les BGA, les pads thermiques sont essentiels. Ces pads devraient être conçus pour permettre une transfert de chaleur efficace tout en fournissant une connectivité électrique suffisante.
Meilleure pratique :
- Utilisez les empreintes recommandées par le fabricant pour chaque composant et exécutez des vérifications de règles de conception (DRC) pour vérifier que les tailles et les formes de pad sont conformes aux normes.
3. Placement des vias
Les vias sont essentiels pour créer des connexions électriques entre les différentes couches de la carte de circuit imprimé, mais leur placement peut avoir un impact sur le processus d’assemblage. Un mauvais placement des vias peut interférer avec le placement des composants et la soudure.
Considérations clés :
- Éviter les vias sur les pads de soudure : Placer des vias directement sur les pads de soudure, également connu sous le nom de « via-in-pad », peut entraîner la pénétration de la soudure dans le trou de via, réduisant la quantité de soudure disponible pour le composant. Cela peut affaiblir le joint de soudure et entraîner des problèmes de fiabilité.
- Espacement des vias : Assurez-vous que les vias soient placés à une distance sûre des composants et des autres traces. Trop de vias rapprochés peuvent entraîner une concentration de chaleur pendant la refusion, ce qui peut affecter la qualité de la soudure.
Meilleure pratique :
- Si les vias doivent être placés sur les pads de soudure (en raison de contraintes d’espace), utilisez des vias « tendus » ou « remplis » pour empêcher la soudure de s’écouler à travers eux.
4. Gestion thermique
La gestion thermique est critique pour les composants qui génèrent de la chaleur, tels que les circuits intégrés de puissance et les processeurs. Une conception appropriée garantit que la chaleur est dissipée efficacement et ne cause pas de dommages aux composants ou n’affecte pas les performances de la carte de circuit imprimé.
Considérations clés :
- Vias thermiques : Utilisez des vias thermiques pour dissiper la chaleur loin des composants sensibles à la chaleur. Ces vias devraient être connectés à de grandes plaques de cuivre qui peuvent répartir la chaleur uniformément sur la carte de circuit imprimé.
- Dispositifs de refroidissement et coulées de cuivre : Pour les composants à haute puissance, envisagez d’utiliser des dispositifs de refroidissement ou des coulées de cuivre (grandes zones de cuivre sur la carte de circuit imprimé) pour aider à dissiper la chaleur. Ceux-ci peuvent être connectés au plan de masse ou à d’autres couches pour une meilleure transfert de chaleur.
Meilleure pratique :
- Concevez la carte de circuit imprimé avec des modèles de soulagement thermique appropriés pour garantir que la chaleur est répartie uniformément sur la carte. Envisagez d’utiliser des logiciels de simulation pour modéliser le comportement thermique pendant l’exploitation.
5. Largeur et espacement des traces
La largeur et l’espacement des traces sur la carte de circuit imprimé sont critiques pour garantir que la carte peut gérer le courant et les signaux requis sans causer de surchauffe ou d’interférences électriques.
Considérations clés :
- Largeur de trace suffisante : Assurez-vous que les traces soient suffisamment larges pour gérer le courant requis sans surchauffer. La capacité de transport de courant d’une trace dépend de sa largeur et de l’épaisseur de la couche de cuivre.
- Dégagement pour les signaux à haute tension : Pour les applications à haute tension, assurez-vous que les traces soient espacées suffisamment pour éviter les arcs ou les courts-circuits entre elles. Suivez les normes de l’industrie (telles que IPC-2221) pour les lignes directrices de dégagement.
- Impédance contrôlée : Pour les traces de signaux à haute vitesse, une impédance contrôlée est cruciale. Cela garantit que les signaux sont transmis sans distorsion ou réflexion, ce qui peut dégrader les performances dans des applications telles que la RF ou la transmission de données.
Meilleure pratique :
- Utilisez des calculateurs en ligne ou des logiciels de conception de carte de circuit imprimé pour calculer la largeur et l’espacement de trace optimaux pour votre application spécifique. Pour les conceptions à haute vitesse, utilisez des lignes directrices d’impédance contrôlée et évitez les coins pointus dans les traces.
6. Accès aux composants et points de test
Pour garantir que la carte de circuit imprimé peut être testée et réparée efficacement, il est essentiel d’inclure des points de test et de fournir un accès suffisant aux composants critiques.
Considérations clés :
- Points de test accessibles : Incluez des points de test pour les signaux clés et les rails d’alimentation pour faciliter les tests pendant l’assemblage et le dépannage. Ces points devraient être facilement accessibles pour les sondes de test ou les équipements de test automatisés.
- Aucun obstacle de composant : Assurez-vous que les composants ne soient pas placés dans des zones où des points de test ou des connecteurs doivent être accessibles. Cela aidera pendant les phases de test et de maintenance ou de réparation futures.
Meilleure pratique :
- Planifiez les points de test au début du processus de conception et vérifiez qu’ils sont placés dans des endroits où ils peuvent être facilement accessibles par l’équipement d’inspection ou les sondes de test.
7. Évitement du tombstoning
Le tombstoning se produit lorsque de petits composants passifs, tels que des résistances ou des condensateurs, se soulèvent d’un côté pendant le processus de refusion. Cela entraîne généralement un circuit ouvert et est plus courant avec les composants plus petits.
Considérations clés :
- Conception de pad symétrique : Assurez-vous que les pads pour les petits composants comme 0201 ou 0402 soient conçus de manière symétrique de sorte que les deux extrémités du composant chauffent uniformément pendant le processus de refusion. Un chauffage inégal peut causer le soulèvement d’une extrémité.
- Application appropriée de la pâte de soudure : Assurez-vous que la pâte de soudure soit appliquée uniformément sur les deux pads. Des volumes de soudure inégaux peuvent causer un déséquilibre des forces pendant la refusion, entraînant le tombstoning.
Meilleure pratique :
- Utilisez l’épaisseur de pochoir correcte et assurez-vous que les ouvertures du pochoir soient bien conçues pour appliquer uniformément la pâte de soudure aux petits composants.
8. Considérations de panneau
La panéisation est le processus de regroupement de plusieurs cartes de circuit imprimé dans un seul panneau pour la fabrication, ce qui facilite la manipulation pendant l’assemblage. Une panéisation incorrecte peut entraîner des problèmes d’assemblage et des défauts.
Considérations clés :
- Conception de panneau cohérente : Assurez-vous que la conception du panneau permet une manipulation efficace pendant le processus d’assemblage. Incluez des repères pour l’alignement et assurez-vous qu’il n’y a pas de point faible dans le panneau qui pourrait causer des déformations.
- Routing et placement des onglets : Si vous utilisez V-score ou le routage d’onglet pour le dépannage, assurez-vous que les lignes de routage n’interfèrent pas avec les composants ou les traces près des bords de la carte de circuit imprimé.
Meilleure pratique :
- Travaillez avec le fabricant pour concevoir le plan de panneau, en veillant à ce qu’il réponde aux exigences de l’équipement d’assemblage et puisse être facilement dépanné sans endommager les cartes.
9. Minimisation des interférences électromagnétiques (EMI)
À mesure que les cartes de circuit imprimé deviennent plus compactes, le risque d’interférences électromagnétiques (EMI) augmente. Une conception appropriée peut aider à atténuer les problèmes d’EMI, qui peuvent dégrader les performances des circuits à haute vitesse ou des dispositifs sans fil.
Considérations clés :
- Planes de masse : Utilisez des plans de masse solides pour réduire les EMI et améliorer l’intégrité des signaux. Le plan de masse devrait couvrir toute la carte de circuit imprimé, avec des lacunes ou des coupures minimales.
- Blindage : Pour les circuits particulièrement sensibles, envisagez d’utiliser des boîtiers de blindage ou des cages de Faraday pour protéger les composants des sources d’EMI externes.
Meilleure pratique :
- Utilisez de bonnes pratiques de disposition telles que la séparation des circuits à haute vitesse et à basse vitesse, le routage des traces de signal perpendiculairement aux plans d’alimentation et la minimisation des longueurs de trace pour les signaux sensibles.
10. Silkscreen et étiquetage
Le silkscreen fournit des informations essentielles sur le placement et l’orientation des composants, et un étiquetage approprié peut prévenir les erreurs d’assemblage.
Considérations clés :
- Marquages de silkscreen clairs : Assurez-vous que tous les composants, en particulier les composants polarisés, aient des marquages de silkscreen clairs et précis pour indiquer l’orientation correcte. C’est particulièrement important pour les diodes, les condensateurs et les circuits intégrés avec des orientations de broche spécifiques.
- Aucun silkscreen sur les pads : Assurez-vous que le silkscreen ne chevauche pas les pads de soudure, car cela peut affecter la qualité de la soudure pendant la refusion.
Meilleure pratique :
- Vérifiez à deux reprises la couche de silkscreen avant de finaliser la conception pour vous assurer que tous les composants sont étiquetés clairement et qu’il n’y a pas de chevauchement de silkscreen sur les zones de soudure critiques.
Conclusion
La conception pour l’assemblage SMT nécessite une attention particulière au placement des composants, à la conception des pads, à la gestion thermique et au tracé pour garantir un processus de fabrication réussi. En suivant ces lignes directrices de conception et en évitant les défauts courants, les concepteurs peuvent réduire les défauts, améliorer l’efficacité de production et garantir la fiabilité du produit final. La mise en œuvre des meilleures pratiques de conception de carte de circuit imprimé pour l’assemblage SMT ne simplifie pas seulement le processus d’assemblage, mais améliore également les performances et la durabilité des produits électroniques fabriqués.
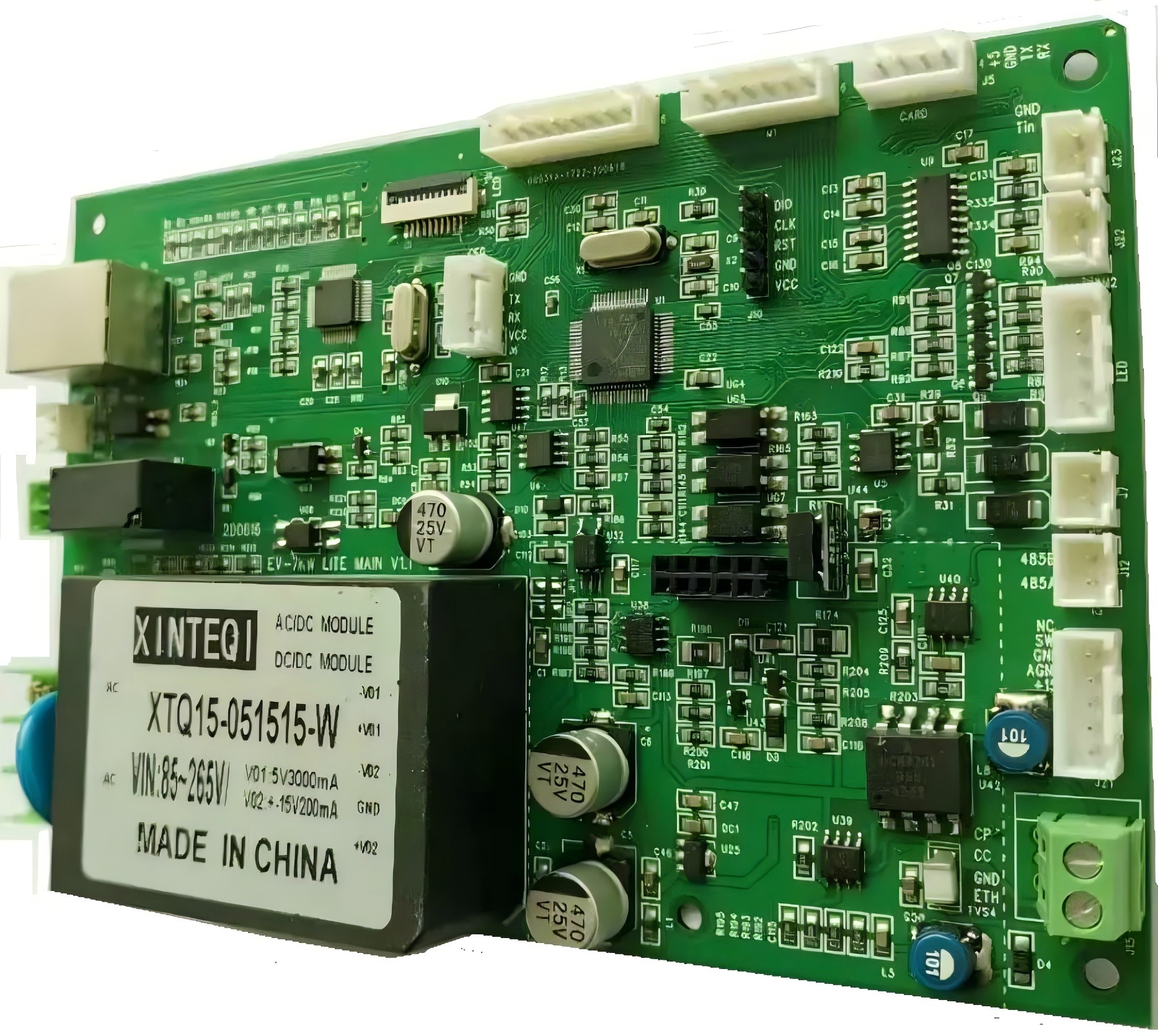
Chapitre 7
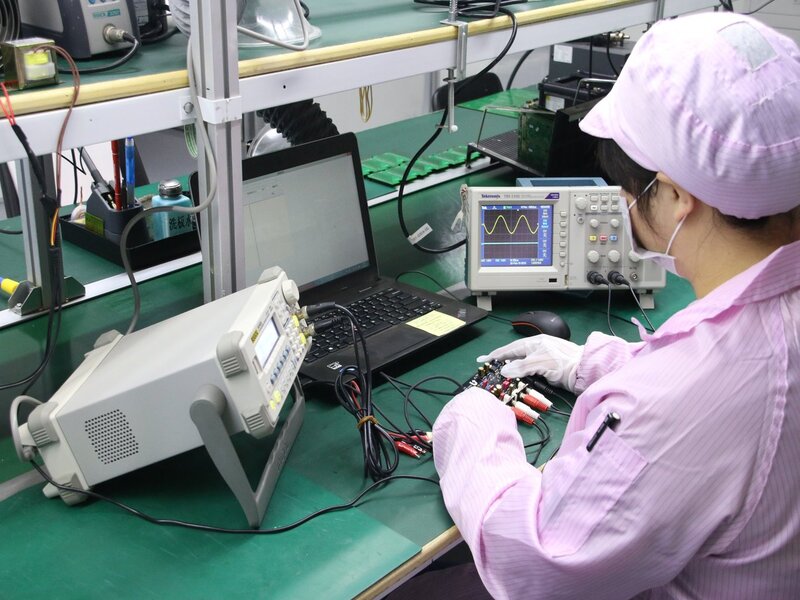
Défis courants dans l'assemblage SMT
Alors que la technologie de montage en surface (SMT) a révolutionné l’industrie de la fabrication électronique en améliorant l’efficacité, en réduisant les coûts et en permettant des conceptions plus compactes, le processus n’est pas sans défis. Divers problèmes peuvent survenir lors de l’assemblage SMT qui peuvent affecter la qualité, la fonctionnalité et la fiabilité du produit final. Ici, nous allons discuter de certains des problèmes typiques rencontrés lors du processus SMT, tels que les défauts de soudure et le désalignement des composants, et explorer des solutions et des meilleures pratiques pour surmonter ces défis.
1. Défauts de soudure
La soudure est l’une des étapes les plus critiques du processus d’assemblage SMT, car elle forme la connexion électrique et mécanique entre les composants de surface et la carte de circuit imprimé (PCB). Cependant, divers défauts de soudure peuvent se produire pendant le processus de refusion, ce qui peut compromettre la qualité de l’assemblage.
Défauts de soudure courants :
- Ponts de soudure : Se produisent lorsque l’excès de soudure crée un pont entre deux pads ou des pistes de composant adjacentes, entraînant des courts-circuits.
- Soudure insuffisante : Lorsque trop peu de soudure est appliquée, elle peut entraîner des joints de soudure faibles, qui peuvent provoquer des défaillances électriques intermittentes ou complètes.
- Vides de soudure : Les bulles d’air piégées dans le joint de soudure, appelées vides, peuvent réduire la résistance mécanique et la conductivité thermique du joint, pouvant entraîner une défaillance du composant.
- Tombstoning : Lorsqu’une extrémité d’un petit composant se soulève pendant la refusion, elle forme une forme de « tombeau », laissant un côté du composant déconnecté.
Solutions et meilleures pratiques pour les défauts de soudure :
- Application de pâte de soudure : Assurer une application de pâte de soudure cohérente et précise est crucial pour prévenir les défauts. L’utilisation de pochoirs de haute qualité et le maintien d’un alignement approprié entre le pochoir et la carte de circuit imprimé peuvent aider à éviter des problèmes tels que les ponts de soudure et la soudure insuffisante.
- Profil du four de refusion : Contrôler correctement le profil de température du four de refusion est essentiel pour réduire les défauts tels que le tombstoning et les vides de soudure. La température doit être soigneusement rampée pour garantir une fusion et un refroidissement uniformes de la soudure sans causer de contraintes thermiques aux composants.
- Qualité de la pâte de soudure : L’utilisation d’une pâte de soudure de haute qualité avec la viscosité et la composition correctes garantit une meilleure adhérence, réduit les vides et améliore la qualité globale des joints de soudure.
2. Désalignement des composants
Le désalignement des composants se produit lorsque les composants de surface ne sont pas placés correctement sur leurs pads désignés. Ce problème peut entraîner des défaillances électriques, de mauvaises connexions mécaniques ou des problèmes pendant la solderie de refusion.
Causes du désalignement des composants :
- Erreurs de prise et de placement : La machine automatique de prise et de placement peut placer incorrectement les composants en raison de problèmes de calibration, de réglages incorrects ou de problèmes mécaniques.
- Gauchissement de la carte de circuit imprimé : Si la carte de circuit imprimé est gauchie ou pliée, les composants peuvent ne pas s’aligner correctement sur les pads, entraînant de mauvaises connexions.
- Désalignement de la pâte de soudure : La pâte de soudure mal alignée peut déplacer le placement du composant, aboutissant à des défauts de soudure ou à des connexions faibles.
Solutions et meilleures pratiques pour le désalignement des composants :
- Calibration de la machine de prise et de placement : Calibrer et maintenir régulièrement la machine de prise et de placement pour garantir un placement précis des composants. S’assurer que la machine est programmée correctement et que les buses et les ventouses fonctionnent correctement peut réduire les erreurs.
- Platitude de la carte de circuit imprimé : S’assurer que la carte de circuit imprimé est plate et exempte de gauchissement avant l’assemblage est crucial. L’utilisation de matériaux de haute qualité pour la carte de circuit imprimé et les stocker dans des conditions appropriées peut aider à prévenir le gauchissement.
- Inspection visuelle : Effectuer une inspection visuelle ou une inspection optique automatisée (AOI) avant la refusion pour détecter tout composant mal aligné. Cela permet des corrections avant le processus de soudure, ce qui économise du temps et réduit les reprises.
3. Tombstoning
Le tombstoning se produit lorsqu’un petit composant passif, tel qu’une résistance ou un condensateur, se soulève d’une extrémité pendant le processus de refusion. Cela laisse un côté du composant non connecté à la carte de circuit imprimé, provoquant un circuit ouvert. Le tombstoning est plus courant avec de petits composants, comme les packages 0201 ou 0402.
Causes du tombstoning :
- Chauffage inégal : Si une extrémité du composant chauffe plus vite que l’autre pendant la refusion, la soudure du côté le plus chaud fond en premier et tire le composant vers le haut.
- Déséquilibre de la pâte de soudure : Si la pâte de soudure n’est pas appliquée uniformément, elle peut provoquer des forces inégales pendant la refusion, aboutissant au tombstoning.
Solutions et meilleures pratiques pour le tombstoning :
- Optimisation du profil de refusion : Assurer un profil de température uniforme du four de refusion qui chauffe les deux extrémités du composant simultanément, réduisant ainsi le risque de tombstoning.
- Conception du pochoir : Utiliser un pochoir bien conçu qui applique des quantités égales de pâte de soudure sur les deux pads peut prévenir les déséquilibres qui aboutissent au tombstoning.
4. Formation de boules de soudure
La formation de boules de soudure se produit lorsque de petites boules de soudure se forment sur la carte de circuit imprimé au lieu de s’écouler uniformément pour former un joint correct. Ces boules de soudure peuvent causer des courts-circuits ou entraîner des connexions de soudure non fiables.
Causes de la formation de boules de soudure :
- Excès de pâte de soudure : Appliquer trop de pâte de soudure peut entraîner un excès de soudure qui se répand et forme des boules pendant la refusion.
- Humidité dans la carte de circuit imprimé ou la pâte de soudure : Si la carte de circuit imprimé ou la pâte de soudure contient de l’humidité, elle peut provoquer des éclaboussures de soudure pendant la refusion, aboutissant à la formation de boules de soudure.
Solutions et meilleures pratiques pour la formation de boules de soudure :
- Contrôle de la quantité de pâte de soudure : Utiliser la quantité correcte de pâte de soudure, appliquée avec un pochoir bien conçu. S’assurer que les ouvertures du pochoir sont correctement dimensionnées pour éviter une application excessive de pâte.
- Stockage à sec : Stocker les cartes de circuit imprimé et la pâte de soudure dans des conditions sèches pour prévenir l’absorption d’humidité. Le pré-chauffage des cartes de circuit imprimé avant la refusion peut également aider à éliminer toute humidité qui pourrait causer des éclaboussures de soudure.
5. Mauvaise humidification de la soudure
L’humidification de la soudure fait référence à la capacité de la soudure à s’écouler et à adhérer aux pistes de composant et aux pads de la carte de circuit imprimé. Une mauvaise humidification peut entraîner des joints de soudure faibles, qui peuvent défaillir sous contrainte mécanique ou thermique.
Causes d’une mauvaise humidification de la soudure :
- Contamination de la carte de circuit imprimé ou des composants : L’oxydation ou la contamination sur les pads de la carte de circuit imprimé ou les pistes de composant peuvent empêcher une adhérence de soudure correcte.
- Température de soudage trop basse : Si la température du four de refusion est trop basse, la soudure peut ne pas fondre complètement, entraînant une mauvaise humidification.
Solutions et meilleures pratiques pour une mauvaise humidification de la soudure :
- Nettoyage de surface : S’assurer que la carte de circuit imprimé et les composants sont exempts de contaminants tels que la poussière, l’huile ou l’oxydation. L’utilisation d’un revêtement protecteur sur les cartes de circuit imprimé pendant le stockage peut aider à prévenir l’oxydation.
- Température de refusion optimale : S’assurer que le four de refusion est réglé sur le profil de température correct pour permettre à la soudure de fondre complètement et d’humidifier efficacement les surfaces.
6. Endommagement des composants
Pendant l’assemblage SMT, les composants peuvent être endommagés en raison d’une chaleur excessive, d’une manipulation physique ou d’un stockage inapproprié. Les composants endommagés peuvent entraîner des défaillances d’assemblage ou une fiabilité réduite du produit.
Causes de l’endommagement des composants :
- Chaleur de refusion excessive : Si la température du four de refusion est trop élevée ou si la carte de circuit imprimé passe trop de temps dans le four, les composants sensibles peuvent être endommagés.
- Manipulation mécanique : Une manipulation incorrecte des composants pendant le processus de prise et de placement ou pendant le stockage peut entraîner des dommages physiques.
Solutions et meilleures pratiques pour l’endommagement des composants :
- Contrôle du profil de refusion : Utiliser un profil de température de refusion soigneusement contrôlé pour éviter de surchauffer les composants.
- Procédures de manipulation appropriées : Mettre en œuvre les meilleures pratiques pour la manipulation des composants, y compris un stockage approprié dans des environnements anti-électrostatiques et l’utilisation d’équipements automatisés pour minimiser les contacts physiques.
Conclusion
L’assemblage SMT est un processus très efficace, mais il peut présenter plusieurs défis, notamment les défauts de soudure, le désalignement des composants et d’autres problèmes qui peuvent avoir un impact sur la qualité du produit final. En comprenant les causes de ces défis courants et en mettant en œuvre les meilleures pratiques telles que l’application correcte de la pâte de soudure, la maintenance de l’équipement et l’optimisation des profils de refusion, les fabricants peuvent considérablement réduire les défauts et améliorer la fiabilité de leurs assemblages SMT. L’inspection régulière et la manipulation soigneuse des composants tout au long du processus d’assemblage sont également essentielles pour garantir des résultats de haute qualité.
Chapitre 8
Contrôle de la qualité dans l'assemblage SMT
Assurer des résultats de haute qualité dans l’assemblage SMT est crucial pour les performances et la fiabilité du produit final. Plusieurs méthodes de contrôle de la qualité sont employées tout au long du processus SMT pour détecter les défauts dès le départ, prévenir les problèmes d’assemblage et assurer l’intégrité du PCB. Deux techniques clés, l’inspection optique automatisée (AOI) et l’inspection aux rayons X, sont largement utilisées pour maintenir des normes élevées dans le processus d’assemblage. En outre, le respect des certifications de qualité telles que ISO 9001 garantit que tous les processus sont rigoureusement contrôlés et répondent aux normes internationales.
1. Inspection optique automatisée (AOI)
L’inspection optique automatisée (AOI) est une méthode d’inspection visuelle sans contact qui scanne les PCB assemblés pour identifier tout défaut, tels que des composants manquants, des décalages ou des problèmes de soudure. Les machines AOI utilisent des caméras à haute résolution et des logiciels de reconnaissance de motifs pour détecter les problèmes à un stade très précoce de la production. Le système compare le placement et la soudure réels des composants avec la conception et la disposition prévues.
Comment l’AOI assure la qualité :
- Détecte les décalages : l’AOI identifie rapidement tout composant déplacé ou incliné, prévenant ainsi d’autres problèmes lors du processus de refusion.
- Vérifie les défauts de soudure : il examine les joints de soudure pour détecter des problèmes courants tels que la soudure insuffisante, le pontage de soudure ou les joints de soudure froids.
- Rapide et précis : les systèmes AOI offrent une méthode rapide et très précise pour inspecter de grands volumes de PCB, ce qui réduit considérablement le risque de produits défectueux atteignant le stade suivant de la production.
2. Inspection aux rayons X
L’inspection aux rayons X est particulièrement utile pour inspecter des PCB complexes qui utilisent des composants avancés comme les matrices de balles de grille (BGAs), où les joints de soudure sont cachés sous le composant. Puisque ces joints ne peuvent pas être inspectés visuellement, les machines à rayons X permettent aux fabricants de voir à l’intérieur du PCB et d’examiner la qualité des joints de soudure et des connexions.
Comment l’inspection aux rayons X assure la qualité :
- Détecte les défauts cachés : l’inspection aux rayons X révèle des problèmes tels que des vides dans les joints de soudure, des fissures ou une soudure insuffisante sous les BGA et les autres composants cachés.
- Assure une soudure appropriée : elle aide à garantir que chaque joint de soudure est sécurisé et correctement formé, même lorsqu’il ne peut pas être inspecté visuellement.
- Essentiel pour les conceptions à haute densité : à mesure que les composants deviennent plus petits et plus densément emballés, l’inspection aux rayons X devient essentielle pour vérifier que toutes les connexions fonctionnent correctement.
3. Normes de qualité ISO 9001
La certification ISO 9001 est une norme de gestion de la qualité reconnue à l’échelle internationale qui garantit que l’entreprise suit un processus cohérent et fiable dans la fabrication. Pour l’assemblage SMT, le respect des normes ISO 9001 signifie que chaque étape du processus, de la conception à l’assemblage final, est soigneusement surveillée et contrôlée.
Comment l’ISO 9001 contribue à la qualité :
- Contrôle des processus : l’ISO 9001 exige que tous les processus soient documentés, contrôlés et améliorés en continu, ce qui réduit la probabilité d’erreurs et garantit une qualité constante.
- Gestion des risques : en suivant les normes ISO 9001, les fabricants mettent en œuvre des pratiques de gestion des risques qui identifient les problèmes potentiels dès le départ, ce qui entraîne moins de défauts et un taux de production réussie plus élevé.
- Satisfaction client : l’ISO 9001 garantit que les exigences des clients sont satisfaites, car les fabricants sont tenus à des normes de qualité strictes, ce qui donne lieu à des produits fiables qui répondent ou dépassent les attentes des clients.
Conclusion
Le contrôle de la qualité dans l’assemblage SMT est réalisé grâce à une combinaison de techniques d’inspection avancées comme l’AOI et l’inspection aux rayons X, ainsi que le respect des normes de qualité reconnues par l’industrie comme l’ISO 9001. Ces méthodes garantissent que les défauts sont identifiés et corrigés dès le début du processus, réduisant ainsi le risque de produits défectueux et assurant la fiabilité des assemblages finaux. En mettant en œuvre des mesures de contrôle de la qualité strictes, les fabricants peuvent produire de manière constante des PCB haute performance et sans défaut qui répondent aux normes les plus élevées de qualité.
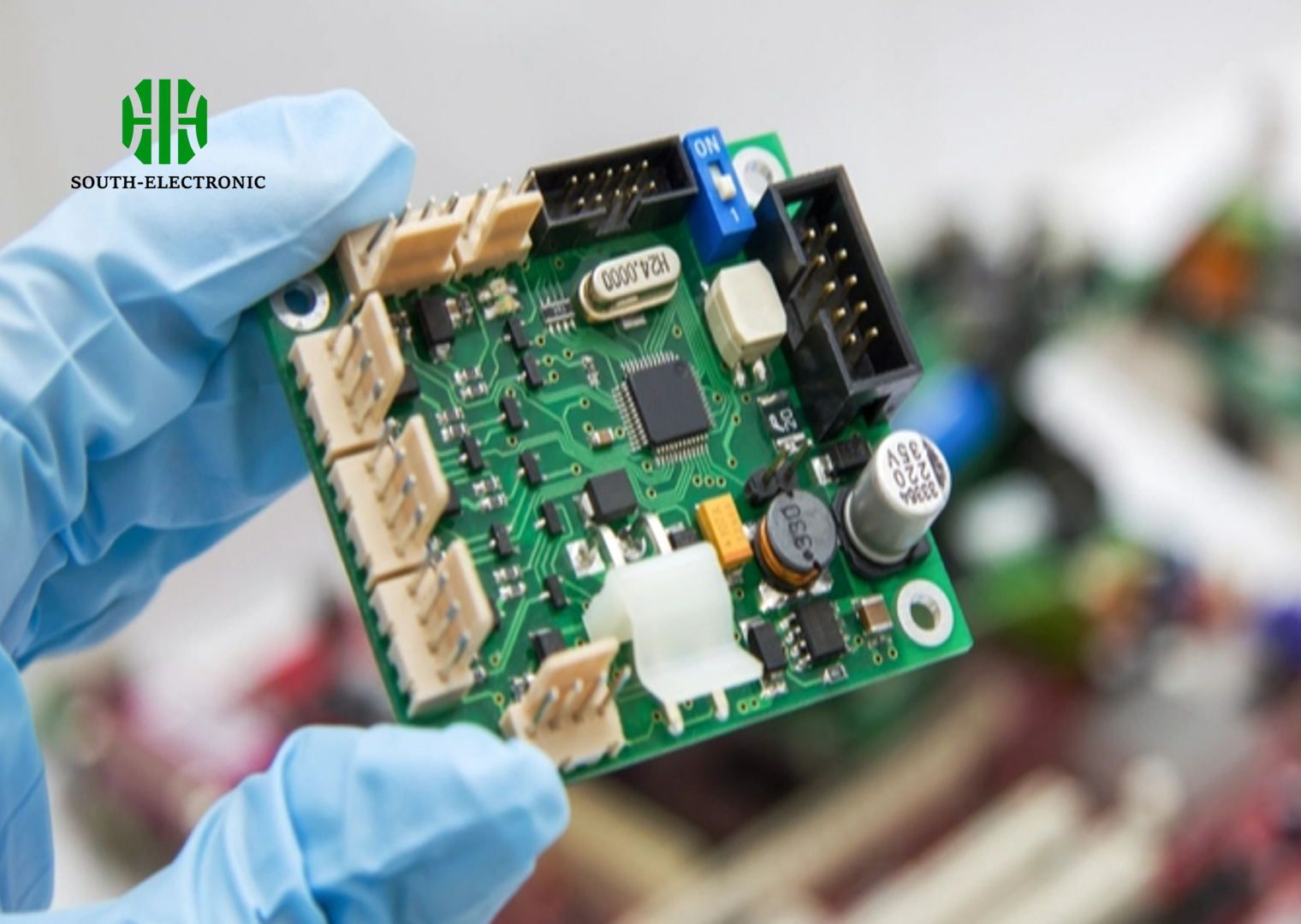
Chapitre 9

Applications de l'assemblage SMT dans différents secteurs
La technologie de montage en surface (SMT) a révolutionné l’industrie de la fabrication électronique, en la rendant essentielle pour la production d’appareils électroniques complexes, hautes performances et compacts dans divers secteurs. L’assemblage SMT est largement utilisé dans une vaste gamme d’industries en raison de sa capacité à supporter la miniaturisation, améliorer les performances et réduire les coûts de production. Dans cette section, nous allons explorer comment l’assemblage SMT bénéficie à différents secteurs, ainsi que des exemples concrets de son application.
1. Électronique grand public
L’industrie de l’électronique grand public est probablement le plus grand bénéficiaire de l’assemblage SMT. Avec la demande croissante de dispositifs plus petits, plus rapides et plus puissants, SMT permet aux fabricants de produire des cartes de circuit imprimé hautement compactes qui soutiennent des fonctionnalités avancées tout en maintenant l’abordabilité.
Applications dans l’électronique grand public :
- Téléphones intelligents et tablettes : L’assemblage SMT est utilisé pour emballer des centaines de petits composants sur des cartes de circuit imprimé dans des appareils tels que les téléphones intelligents et les tablettes. Ces appareils reposent sur la précision de SMT pour intégrer des processeurs, des puces de mémoire et des modules de communication dans des conceptions compactes et légères.
- Appareils portables : Des traceurs de fitness aux montres intelligentes, SMT permet la miniaturisation des composants, ce qui rend possible la création de technologies portables élégantes et légères.
Exemple : Les iPhones d’Apple reposent lourdement sur l’assemblage SMT pour l’intégration de circuits complexes qui alimentent tout, des processeurs de série A aux écrans tactiles et aux systèmes de gestion de la batterie.
2. Industrie automobile
À mesure que les véhicules deviennent plus avancés sur le plan technologique, l’industrie automobile utilise de plus en plus l’assemblage SMT pour construire les systèmes électroniques complexes nécessaires aux voitures modernes. Ces systèmes comprennent tout, des unités d’infodivertissement et de navigation aux fonctionnalités de sécurité essentielles comme les systèmes antiblocage des roues (ABS) et les systèmes avancés d’aide à la conduite (ADAS).
Applications dans l’industrie automobile :
- Unités de contrôle électroniques (ECU) : SMT est utilisé pour assembler les cartes de circuit imprimé hautement denses dans les ECU, qui contrôlent diverses fonctions du véhicule, telles que la gestion du moteur, les freins et le contrôle de stabilité.
- ADAS et conduite autonome : Des fonctionnalités avancées comme l’assistance de maintien de voie, le contrôle de vitesse adaptatif et les capteurs de stationnement reposent sur SMT pour créer des circuits compacts et fiables pour le traitement des capteurs.
Exemple : Les véhicules électriques de Tesla font un usage intensif de l’assemblage SMT pour leurs ECU, leurs systèmes de gestion de batterie et leurs technologies de conduite autonome, ce qui aide l’entreprise à réduire la taille et le poids des composants essentiels.
3. Aérospatiale et défense
Dans les industries aérospatiale et de défense, où la fiabilité, les performances et la réduction de poids sont primordiales, l’assemblage SMT est critique pour la production de systèmes électroniques avancés utilisés dans les avions, les satellites et les applications de défense. Ces systèmes doivent répondre à des normes de performance et de durabilité strictes tout en fonctionnant dans des environnements extrêmes.
Applications dans l’aérospatiale et la défense :
- Avionique : L’assemblage SMT est utilisé pour créer des cartes de circuit imprimé compactes et légères pour les systèmes avioniques, y compris les systèmes de communication, de navigation et de contrôle de vol.
- Satellites et exploration spatiale : SMT permet la production d’électronique légère et hautement fiable utilisée dans les satellites et les sondes spatiales, où les contraintes de volume et les conditions environnementales extrêmes sont des facteurs clés.
Exemple : Le rover Mars lancé par la NASA repose sur des circuits assemblés SMT pour contrôler sa navigation, ses systèmes d’alimentation et ses instruments scientifiques, tous conçus pour résister aux conditions extrêmes de l’espace.
4. Appareils médicaux
Dans le domaine médical, l’assemblage SMT est essentiel pour créer des électroniques miniaturisées, précises et fiables utilisées dans l’équipement de diagnostic, les appareils de surveillance et les dispositifs médicaux implantables. Ces appareils nécessitent souvent des normes strictes pour les performances, la fiabilité et la sécurité.
Applications dans les appareils médicaux :
- Appareils médicaux portables : Des dispositifs comme les montres cardiaques, les capteurs de glucose et les appareils de surveillance ECG portable reposent sur l’assemblage SMT pour la miniaturisation et la fiabilité, les rendant confortables et faciles à utiliser pour les patients.
- Dispositifs implantables : Les pacemakers et les implants cochléaires utilisent la technologie SMT pour créer une connectique compacte et efficace qui peut être implantée dans le corps humain et fonctionner de manière fiable sur de longues périodes.
Exemple : Les pacemakers et les pompes à insuline de Medtronic sont des exemples d’appareils médicaux qui utilisent l’assemblage SMT pour créer des systèmes compacts et hautement fiables qui sont essentiels pour la santé et le bien-être des patients.
5. Télécommunications
Les systèmes de télécommunication, qui sont responsables de la transmission et du traitement de données à haute vitesse, bénéficient considérablement de l’assemblage SMT. Avec la demande croissante de communication plus rapide et plus fiable, SMT est utilisé pour créer les cartes de circuit imprimé haute densité et hautes performances nécessaires à l’équipement de réseau moderne.
Applications dans les télécommunications :
- Stations de base cellulaires : SMT est utilisé pour construire les cartes de circuit imprimé des stations de base qui gèrent la communication cellulaire, soutenant l’expansion des réseaux 5G.
- Communications optiques par fibre : L’équipement de transmission de données haute vitesse, tel que les transceivers optiques par fibre et les commutateurs de réseau, utilise SMT pour assembler des circuits compacts et efficaces qui assurent une transmission de signal fiable.
Exemple : Les routeurs haute vitesse et l’équipement de réseau de Cisco utilisent l’assemblage SMT pour répondre aux exigences de performances élevées des réseaux de télécommunication modernes, y compris les réseaux 5G et la fibre optique.
6. Automatisation industrielle et de fabrication
Dans l’automatisation industrielle et de fabrication, l’assemblage SMT est critique pour produire les systèmes de contrôle qui alimentent les robots, les systèmes de convoyage et l’équipement de surveillance. Ces systèmes doivent être hautement fiables et fonctionner souvent dans des environnements difficiles.
Applications dans l’automatisation industrielle :
- Contrôleurs logiques programmables (PLC) : SMT est utilisé pour créer les cartes de circuit imprimé pour les PLC, qui contrôlent les machines et les processus dans les usines et les environnements industriels.
- Robotique : Les cartes de contrôle assemblées SMT sont essentielles pour les mouvements précis et les opérations des robots industriels utilisés dans l’automatisation.
Exemple : Les systèmes de contrôle industriels et l’équipement d’automatisation de Siemens utilisent l’assemblage SMT pour créer des cartes de circuit imprimé fiables et compactes qui gèrent des processus de fabrication complexes.
Conclusion
L’assemblage SMT est une technologie essentielle dans une large gamme d’industries, allant de l’électronique grand public à l’aérospatiale. Sa capacité à créer des cartes de circuit imprimé compactes, fiables et hautes performances en a fait la norme pour la fabrication électronique moderne. Que ce soit pour permettre la miniaturisation des téléphones intelligents ou assurer la fiabilité des systèmes aérospatiaux, l’assemblage SMT joue un rôle critique dans le monde technologique avancé d’aujourd’hui.
Chapitre 10
Choosing the Right SMT Assembly Partner
La sélection du bon fournisseur de services d’assemblage de technologie de montage en surface (SMT) est une décision critique qui peut avoir un impact significatif sur la qualité, le coût et le délai de votre projet. Que vous travailliez sur des prototypes à petite échelle ou des productions à grande échelle, choisir un partenaire qui correspond à vos besoins techniques et commerciaux est essentiel pour assurer le succès de votre assemblage électronique. Voici quelques-uns des facteurs clés à considérer lors de la sélection d’un fournisseur de services d’assemblage SMT, ainsi que des informations sur pourquoi la qualité, le délai de réalisation et le support technique sont cruciaux pour les projets réussis.
1. Normes de qualité et certifications
La qualité est primordiale dans l’assemblage SMT, car tout défaut dans le produit final peut entraîner des défaillances sur le terrain, des coûts accrus et des dommages à votre réputation. Il est essentiel de s’assurer que votre partenaire d’assemblage SMT respecte des normes de qualité élevées et détient les certifications pertinentes.
Facteurs à considérer :
- Certification ISO9001 : Recherchez des fournisseurs certifiés ISO9001. Cette certification démontre que l’entreprise suit des normes de gestion de la qualité strictes, garantissant des résultats constants et fiables dans le processus de fabrication.
- Contrôle qualité interne : Assurez-vous que le fournisseur dispose de processus de contrôle qualité robustes, tels que l’inspection optique automatisée (AOI), l’inspection aux rayons X et les tests en circuit, pour détecter les défauts en amont et maintenir des normes élevées tout au long du processus d’assemblage.
- Qualité de la source de composants : Assurez-vous que le fournisseur source des composants de haute qualité et fiables auprès de fournisseurs de confiance pour prévenir des problèmes tels que des composants contrefaits ou de mauvaise qualité qui pourraient entrer dans votre chaîne d’approvisionnement.
Pourquoi cela est important : Un assemblage de haute qualité minimise les défauts et les reprises, ce qui se traduit par un produit plus fiable et des coûts globaux plus bas à long terme.
2. Délai de réalisation et fiabilité de la livraison
Pour de nombreux projets électroniques, le temps de mise sur le marché est un facteur critique. Un partenaire d’assemblage SMT fiable devrait être en mesure de respecter les délais de votre projet sans compromettre la qualité. Des délais de réalisation rapides peuvent vous donner un avantage concurrentiel, en particulier dans des industries en évolution rapide comme l’électronique grand public et les télécommunications.
Facteurs à considérer :
- Délai de livraison : Demandez le délai de livraison moyen du fournisseur pour les lots de prototypes et les commandes de production complète. Les fournisseurs disposant de processus rationalisés et de lignes de production efficaces peuvent offrir des délais de réalisation plus rapides.
- Historique de livraison à temps : Assurez-vous que le fournisseur a un historique de livraison à temps prouvé. Les retards dans le processus d’assemblage peuvent avoir un effet d’entraînement sur votre calendrier de production global.
- Capacité d’adaptation : Si vous prévoyez d’accroître votre production à l’avenir, assurez-vous que le partenaire a la capacité et la flexibilité pour gérer des volumes plus importants sans retards significatifs.
Pourquoi cela est important : Une livraison rapide et fiable vous permet de mettre vos produits sur le marché rapidement, vous donnant un avantage concurrentiel et vous aidant à répondre aux demandes des clients à temps.
3. Expertise technique et support
Un partenaire d’assemblage SMT compétent devrait offrir plus que des services d’assemblage – il devrait offrir une expertise technique et un support pour vous aider à surmonter les défis de conception, de sélection de composants et de fabrication. Le bon partenaire devrait être en mesure d’offrir des insights et des solutions qui peuvent améliorer la qualité et la fabriquabilité de votre produit.
Facteurs à considérer :
- Support d’ingénierie : Recherchez un partenaire disposant d’une équipe d’ingénieurs expérimentés qui peut examiner votre conception de PCB et offrir des suggestions d’amélioration, telles que l’optimisation de la fabriquabilité (DFM) ou la minimisation des problèmes potentiels d’assemblage.
- Aide à la réalisation de prototypes : Pour les nouveaux produits, il est important de travailler avec un fournisseur capable de réaliser rapidement des prototypes et d’offrir des commentaires sur les défauts potentiels de conception ou les domaines d’amélioration avant de passer à la production de masse.
- Support après-vente : Le support technique ne s’arrête pas une fois les cartes assemblées. Assurez-vous que votre partenaire offre un support technique après-vente pour résoudre tout problème qui pourrait survenir après la livraison.
Pourquoi cela est important : Travailler avec un fournisseur de services d’assemblage SMT qui offre un solide support technique peut vous aider à éviter des erreurs coûteuses, à assurer des lots de production sans heurts et à améliorer la qualité globale de votre produit.
4. Flexibilité et options de personnalisation
Tous les projets d’assemblage SMT ne sont pas les mêmes, et votre partenaire d’assemblage devrait offrir de la flexibilité pour répondre à vos besoins uniques. Que ce soit un prototype à faible volume ou une production à grande échelle, votre partenaire devrait être en mesure de personnaliser ses services pour répondre à vos exigences spécifiques.
Facteurs à considérer :
- Capacité à bas et à haut volume : Assurez-vous que le fournisseur peut gérer à la fois les lots de prototypes et les lots de production plus importants. Certains fournisseurs se spécialisent dans les productions à grande échelle, tandis que d’autres excellent dans la production flexible à faible volume.
- Personnalisation : Si votre projet nécessite des matériaux, des composants ou des processus spécifiques, assurez-vous que le fournisseur peut répondre à ces demandes de personnalisation. C’est particulièrement important pour les industries comme les soins de santé ou l’aérospatiale, où la conformité à des normes strictes peut être requise.
- Pas de exigences de commande minimum : Pour les startups ou les entreprises en développement de prototypes, il est important de trouver un partenaire qui est prêt à travailler sur des projets à petite échelle sans imposer des quantités de commande minimum élevées.
Pourquoi cela est important : La flexibilité vous permet de vous adapter à des exigences de projet changeantes et de recevoir toujours des services d’assemblage de haute qualité adaptés à vos besoins exacts.
5. Rentabilité
Si le coût ne devrait jamais être le seul facteur de décision lors du choix d’un partenaire d’assemblage SMT, il est important de trouver un fournisseur qui offre des tarifs compétitifs sans sacrifier la qualité. Évaluez la valeur globale offerte par le fournisseur, en tenant compte de facteurs tels que la qualité, le service et le support, plutôt que de vous concentrer uniquement sur le prix le plus bas.
Facteurs à considérer :
- Prix transparents : Assurez-vous que le fournisseur offre des prix transparents sans frais cachés. Demandez des devis détaillés qui incluent tous les aspects du processus d’assemblage, de la source de composants aux tests.
- Optimisation des coûts : Recherchez des partenaires qui offrent des options d’économie, telles que des remises pour les commandes plus importantes ou des suggestions pour des alternatives de composants plus abordables sans compromettre la qualité.
Pourquoi cela est important : Des tarifs compétitifs vous aident à rester dans votre budget, mais il est important d’équilibrer le coût avec le niveau de qualité et de support que vous recevez. Une option moins chère qui entraîne une assemblage de mauvaise qualité peut conduire à des problèmes plus coûteux à long terme.
6. Expédition et logistique mondiales
Si vous opérez dans différents pays ou régions, envisagez un partenaire d’assemblage SMT ayant des capacités d’expédition mondiales et un réseau logistique éprouvé. La capacité à expédier des produits de manière fiable vers diverses destinations tout en gérant les douanes et les autres problèmes logistiques internationaux est cruciale pour les entreprises opérant à l’échelle mondiale.
Facteurs à considérer :
- Portée mondiale : Assurez-vous que le partenaire peut expédier à l’international et a de l’expérience dans la gestion des réglementations douanières, des tarifs et des droits de douane dans vos marchés cibles.
- Emballage et manutention : Le fournisseur devrait offrir un emballage approprié pour protéger les PCB sensibles pendant le transport, ainsi que des systèmes de suivi fiables pour vous tenir informé tout au long du processus de livraison.
Pourquoi cela est important : Une gestion efficace de l’expédition et de la logistique aide à éviter les retards, à réduire les risques de dommages et à garantir que vos produits arrivent à destination à temps.
Conclusion
Lors du choix du bon partenaire d’assemblage SMT, il est essentiel d’évaluer des facteurs clés tels que les normes de qualité, le délai de réalisation, le support technique, la flexibilité et la rentabilité. S’assurer que votre partenaire peut répondre à vos besoins spécifiques et fournir des résultats fiables et de haute qualité fera une grande différence dans le succès de votre projet. Donner la priorité à ces facteurs garantit un processus de fabrication fluide, un temps de mise sur le marché plus rapide et un produit final qui répond aux normes les plus élevées de qualité et de performance.
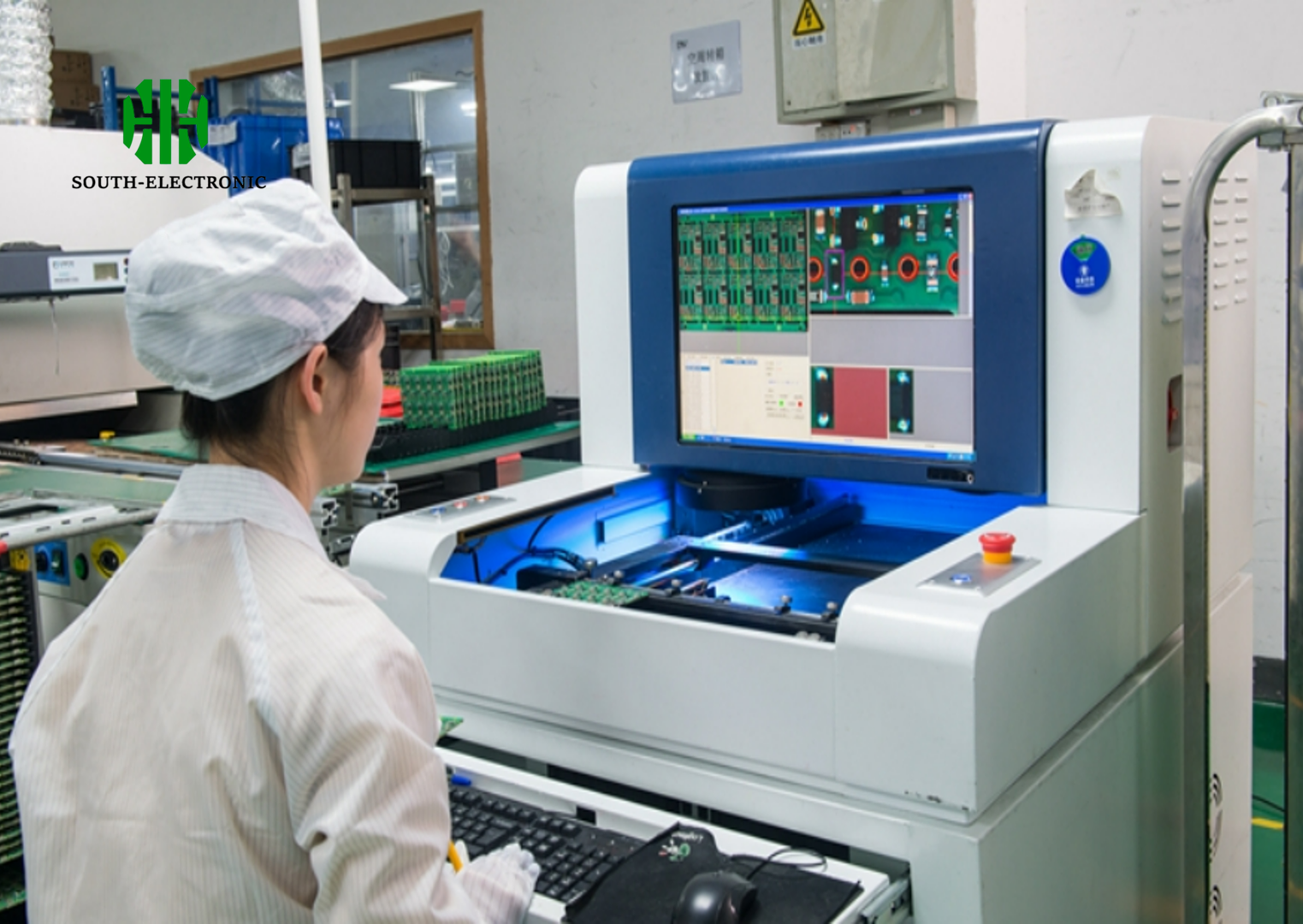
Contactez-Nous
Où Sommes-Nous ?
Parc Industriel, No. 438 Route Donghuan, No. 438, Shajing Donghuan Road, District Bao'an, Shenzhen, Guangdong, Chine
4ème étage, Bâtiment Zhihui Créatif, No. 2005 Route Xihuan, Shajing, District Baoan, Shenzhen, Chine
CHAMBRE A1-13, ÉTAGE 3, CENTRE INDUSTRIEL YEE LIM, 2-28 RUE KWAI LOK, KWAI CHUNG HK
service@southelectronicpcb.com
Téléphone : +86 400 878 3488
Envoyez-nous un message
