Fournisseur d'assemblage par trou traversant
South-Electronic
Ne cherchez pas plus loin que South-Electronic pour une qualité, une fiabilité et une valeur inégalées dans vos besoins d'assemblage de PCB. Voyez la différence avec notre service d'assemblage de PCB par trou traversant tout-en-un - de la conception à l'assemblage, nous garantissons la précision, la longévité et la conformité aux normes les plus élevées de l'industrie.
Votre fournisseur de confiance pour l'assemblage de PCB par trou traversant
Bienvenue chez South-Electronic, où vous découvrirez des services d’assemblage de PCB par trou traversant de haut niveau connus pour leur excellente précision et fiabilité.
Que vous ayez besoin de cartes simples, doubles ou multichouches, nous adaptons nos services pour améliorer vos entreprises électroniques, améliorer les performances des appareils et garantir une valeur exceptionnelle. Profitez d’une commande flexible avec un minimum d’une pièce, bénéficiez de l’expérience de notre équipe d’experts et profitez d’une livraison rapide avec nos lignes de production optimisées.
Pourquoi choisir South-Electronic ?
-
Commande flexible
Vous pouvez commander aussi peu que 1 pièce pour répondre à vos besoins HDI exacts.
Profitez de la flexibilité pour tester de nouveaux designs ou répondre à des besoins de petites quantités sans aucun problème. -
Équipe d'experts
Vous bénéficiez de notre décennie d'expertise dans l'industrie.
Nous comprenons vos défis et fournissons des solutions d'experts et un soutien fiable à chaque étape. -
Service complet
Vous obtenez une satisfaction complète avec notre large gamme d'équipements.
Notre service complet vous assure d'obtenir tout ce dont vous avez besoin pour une expérience sans accroc. -
Livraison rapide
Vous bénéficiez de nos temps de production rapides et efficaces.
Nous donnons la priorité à la livraison rapide pour respecter vos délais et maintenir vos projets sur la bonne voie. -
Satisfaction garantie
Vous êtes assuré de la qualité et d'une communication claire avec notre certification ISO9001.
Votre satisfaction est notre priorité, et nous nous engageons à dépasser vos attentes à chaque commande.
Projets liés que nous avons réalisés
Avis des clients
Questions fréquentes
Questions les plus populaires
South-Electronic propose de nombreuses options de personnalisation. Vous pouvez commander une seule unité ou un grand nombre d'unités. Vous pouvez également leur demander d'ajouter des fonctionnalités spéciales ou d'apporter des modifications de conception dont vous avez besoin.
L'équipe de South-Electronic possède une grande expérience. Ils savent effectuer toutes les tâches d'assemblage avec précision et qualité. Ils savent ce qu'ils font, donc ils peuvent réaliser votre projet correctement et s'assurer qu'il est parfait.
L'équipe de South-Electronic possède une grande expérience. Ils savent effectuer toutes les tâches d'assemblage avec précision et qualité. Ils savent ce qu'ils font, donc ils peuvent réaliser votre projet correctement et s'assurer qu'il est parfait.
Les composants qui nécessitent des liaisons mécaniques solides et peuvent supporter des tensions et des courants plus élevés, tels que les condensateurs, les transformateurs et les connecteurs, sont généralement utilisés dans l'assemblage par trou traversant en raison de leur plus grande taille et de leur durabilité renforcée.
Oui, ils le peuvent. Si vous avez besoin de quelque chose rapidement, ils peuvent le faire. Ils peuvent accélérer les choses pour vous si vous en avez besoin. Ils s'assureront que vous obteniez ce dont vous avez besoin lorsque vous en avez besoin.
South-Electronic a un processus de contrôle qualité très strict. Ils suivent toutes les règles et les normes pour s'assurer que tout ce qu'ils fabriquent est parfait. Ils vérifient tout à chaque étape pour s'assurer que tout est en ordre.
Oui, ils le font. Ils vous aideront avec tout ce dont vous avez besoin après avoir acheté des produits chez eux. Ils veulent s'assurer que vous êtes satisfait de ce que vous avez obtenu et ils vous aideront avec tout ce dont vous avez besoin.
Envoyez-nous un message
Le guide complet pour l'assemblage par trous traversants
Contenu
Chapitre 1
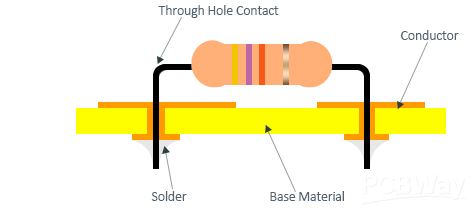
Introduction à l'assemblage par trou traversant
La technologie par trou traversant est une méthode classique dans le domaine de la fabrication d’équipements électroniques. Elle consiste à monter des composants électroniques sur des cartes de circuit imprimé (PCI) en insérant leurs broches dans des trous percés dans la carte. Cette technique traditionnelle était la principale méthode d’assemblage électronique avant l’avènement de méthodes plus modernes comme la technologie de montage en surface (SMT).
Dans l’assemblage par trou traversant, une fois que les broches des composants sont insérées dans les trous, elles sont soudées à des pads sur le côté opposé de la carte. Cela crée une connexion mécanique solide qui sert également de lien électrique entre les composants et la PCI. Cette méthode est connue pour sa fiabilité et sa durabilité, ce qui en fait un choix préféré dans les applications où les contraintes mécaniques ou les facteurs environnementaux, tels que la chaleur ou les vibrations, sont des préoccupations.
Importance et avantages dans la fabrication d’équipements électroniques
La technologie par trou traversant continue de jouer un rôle important dans certains scénarios de fabrication malgré les progrès réalisés dans d’autres techniques d’assemblage. Voici quelques-uns des principaux avantages :
- Résistance mécanique : La méthode de broche à travers le trou offre des liaisons mécaniques supérieures par rapport au montage en surface. Cela la rend idéale pour les composants qui peuvent être soumis à des contraintes mécaniques ou avoir besoin d’un support physique solide, tels que les connecteurs ou les composants lourds.
- Facilité de prototypage et de test : Les composants par trou traversant sont souvent plus faciles à manipuler et à modifier pendant les phases de prototypage et de test, permettant des modifications et des ajustements plus faciles.
- Résistance environnementale : En raison des joints de soudure robustes, les assemblages par trou traversant sont plus résistants aux facteurs environnementaux, tels que les chocs et les vibrations. Cela les rend adaptés aux industries aérospatiale, militaire et automobile où de telles conditions sont courantes.
- Capacité de gestion de puissance : Les composants qui dissipent plus de puissance ou nécessitent des capacités de gestion de courant plus élevées sont mieux adaptés à l’assemblage par trou traversant en raison des plus grandes surfaces de contact fournies par les broches.
Introduction comparative à la technologie de montage en surface (SMT)
Alors que la technologie par trou traversant était autrefois la norme dans l’assemblage électronique, le développement de la technologie de montage en surface (SMT) a fourni une alternative compacte et efficace. Contrairement à l’assemblage par trou traversant, les composants SMT sont montés directement sur la surface de la PCI sans percer de trous, ce qui permet des conceptions de PCI plus compactes et une densité de composants plus élevée.
Points forts de la comparaison :
- Taille et poids : Le SMT permet des conceptions plus compactes car il élimine le besoin de trous et utilise des composants plus petits, ce qui le rend idéal pour les équipements électroniques grand public modernes et miniaturisés comme les smartphones et les ordinateurs portables.
- Vitesse d’assemblage : Le SMT permet des processus d’assemblage automatisés plus rapides car il simplifie la phase de placement des composants, permettant une production à grande échelle avec une intervention manuelle minimale.
- Efficacité coûts : La capacité à automatiser davantage les processus et les coûts de matériaux réduits en raison des tailles de composants plus petites conduisent souvent à des économies dans le SMT.
Cependant, la technologie par trou traversant reste indispensable pour des applications spécifiques où la durabilité, la flexibilité des tests et la capacité de gestion de puissance sont prioritaires. Par conséquent, de nombreux assemblages électroniques modernes utilisent une combinaison des deux techniques, chacune servant son rôle distinct dans la conception finale du produit. Grâce à ce mélange, les fabricants exploitent les forces de ces deux méthodologies pour produire des équipements électroniques robustes et efficaces qui répondent à des exigences d’application diverses.
Chapitre 2
Histoire et Évolution de la Technologie des Troues de Passage
Contexte Historique et Développement
L’origine de la technologie des trous de passage remonte au milieu du 20e siècle, coïncidant avec la croissance rapide de l’industrie électronique. Au fur et à mesure que les appareils électroniques évoluaient en complexité tout au long des années 1950 et 1960, il est devenu urgent de disposer d’une méthode fiable pour fixer solidement les composants électroniques aux cartes de circuit. Cela a conduit au développement et à l’adoption généralisée de la technologie des trous de passage.
Initialement, les circuits électroniques étaient construits à l’aide d’un câblage point à point, qui était fastidieux et sujet aux erreurs. L’introduction de la carte de circuit imprimé (PCI) a révolutionné ce processus. Avec les PCI, les composants pouvaient être soudés sur une carte pré-imprimée avec des trajets conducteurs, ce qui a rationalisé l’assemblage et amélioré considérablement la fiabilité.
La technologie des trous de passage est devenue la norme à cette époque pour plusieurs raisons :
- Fabilité : La soudure des broches de composant à travers des trous perforés a fourni une connexion électrique et mécanique robuste, essentielle à la fiabilité des appareils électroniques.
- Facilité de Prototypage : La capacité d’insérer et de remplacer facilement les composants a facilité le prototypage et les tests, ce qui a permis une innovation et un développement de produits rapides.
Transition de l’Électronique Ancienne aux Applications Modernes
À mesure que la technologie avançait et que la demande augmentait pour des appareils électroniques plus compacts et plus efficaces, les méthodes d’assemblage ont évolué. À la fin du 20e siècle, la technologie de montage en surface (SMT) est apparue, offrant des avantages considérables en termes de réduction de taille et d’efficacité de fabrication. Cependant, la technologie des trous de passage a persisté – en particulier dans les applications qui nécessitaient une plus grande résistance mécanique et une durabilité des composants.
L’électronique d’aujourd’hui intègre à la fois la technologie des trous de passage et la SMT pour capitaliser sur les avantages de chacune :
Applications Modernes : La technologie des trous de passage est toujours activement utilisée dans la production de composants à haute contrainte ou critiques en puissance, tels que les connecteurs, les transformateurs et les grands condensateurs. Sa durabilité reste inégalée dans les applications soumises à des contraintes mécaniques ou à des environnements extrêmes, tels que les technologies militaires ou aérospatiales.
Approche Combinée : De nombreux appareils électroniques contemporains utilisent une approche d’assemblage mixte, en exploitant la SMT pour la miniaturisation et les trous de passage pour la force, optimisant ainsi les performances du produit. Cette hybridation permet l’innovation dans des appareils complexes tels que les systèmes de contrôle automobile, les machines industrielles et les appareils électroniques grand public sophistiqués.
Héritage et Avenir : Malgré l’essor de la SMT, l’héritage de la technologie des trous de passage perdure car elle continue de fournir une fiabilité inégalée dans les applications critiques. L’évolution continue de cette technologie démontre son adaptabilité, garantissant sa pertinence dans un secteur en constante évolution, en maintenant son rôle fondamental dans le paysage de l’assemblage électronique pour les décennies à venir.
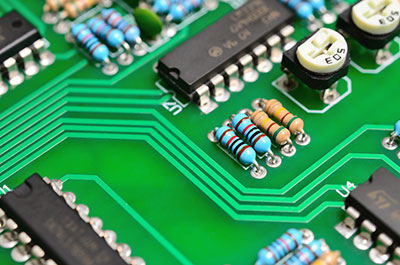
Chapitre 3
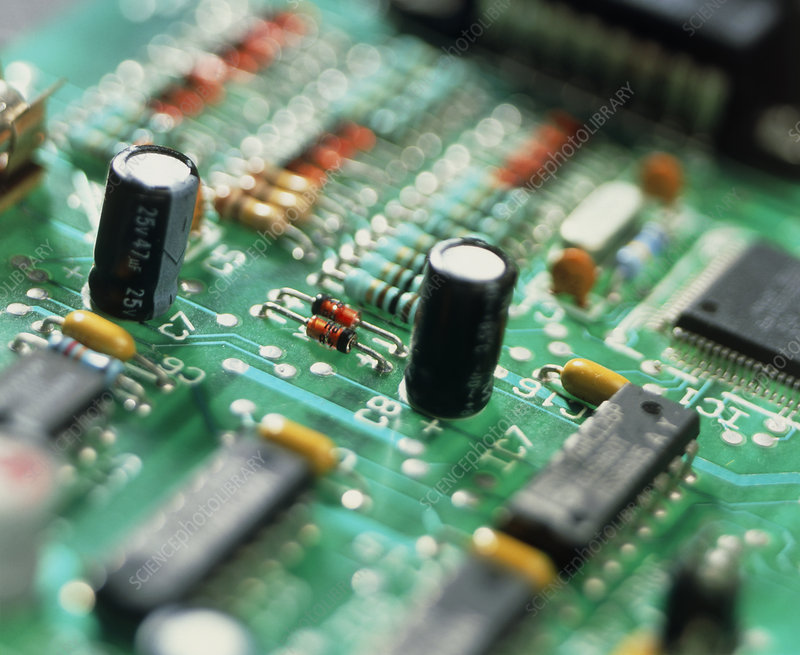
Composants utilisés dans l'assemblage à travers les trous
Types de composants
L’assemblage à travers les trous implique principalement des composants connus pour leur forme à broches, où les broches ou les pins du composant sont insérés à travers des trous percés sur une carte de circuit imprimé (PCB). Voici quelques types courants de composants utilisés dans la technologie à trous :
Résistances : ces composants contrôlent le flux de courant électrique à l’intérieur des circuits. Ils sont généralement cylindriques avec des broches axiales s’étendant des deux extrémités, appelées résistances à broches.
Condensateurs : utilisés pour stocker et libérer de l’énergie électrique, les condensateurs sous forme de trous sont souvent radiaux ou axiaux. Les condensateurs radiaux ont deux broches sortant d’une extrémité, ce qui les rend compacts, tandis que les condensateurs axiaux ont des broches s’étendant des deux extrémités.
Diodes : ces composants permettent au courant de circuler dans une seule direction, agissant comme une vanne de contrôle pour l’électricité. Les diodes, comme les redresseurs et les LED, sont couramment trouvées avec des broches pour insertion à travers les trous.
Transistors : utilisés pour amplifier et commuter les signaux électroniques, les transistors sous forme de trous sont généralement livrés comme des dispositifs uniques et verticaux avec trois broches.
Inductances : comme de petites bobines, ces composants stockent de l’énergie dans un champ magnétique lorsque le courant les traverse. Les inductances à broches sont souvent utilisées lorsque une plus grande puissance est nécessaire.
Circuits intégrés (IC) : ils peuvent aller de simples portes à des processeurs complexes, généralement dans un format de package à broches doubles (DIP) pour le montage à trous, offrant une meilleure dissipation de puissance par rapport à leurs homologues SMT.
Connecteurs : essentiels pour relier les différentes parties d’un système, les connecteurs à trous offrent une stabilité mécanique solide et sont capables de supporter des contraintes environnementales et physiques importantes.
Explication détaillée des composants à broches par rapport aux composants SMT
<p-La distinction clé entre les composants à broches (à travers les trous) et les composants SMT réside dans leur conception et leur application :Composants à broches : ces composants sont caractérisés par leurs broches filaires, qui s’étendent du corps du composant à travers des trous dans la carte de circuit imprimé. Cette méthode permet de former des connexions mécaniques plus solides, les rendant adaptées aux applications où la durabilité est essentielle. La plus grande taille des composants à broches facilite une manipulation manuelle plus facile pendant l’assemblage et les tests, en particulier utile pour les prototypes et la fabrication à faible volume.
Composants SMT : en revanche, les composants SMT sont conçus pour être placés directement sur la surface de la carte de circuit imprimé sans nécessité de trous. Cela permet d’augmenter la densité des circuits et de réduire l’espace sur la carte, essentiel pour les appareils électroniques modernes qui exigent une conception compacte. Les broches SMT sont généralement plus courtes et plus plates, facilitant l’assemblage automatisé mais rendant souvent la réparation manuelle plus difficile.
Différenciation des avantages :
- Stabilité mécanique : les composants à broches excellent dans les applications où les composants doivent résister aux contraintes mécaniques, aux chocs et aux vibrations.
- Efficacité d’espace : les composants SMT sont idéaux pour les appareils nécessitant une densité de composants élevée et une miniaturisation.
Les deux types jouent des rôles intégraux dans l’électronique moderne. Les composants à trous offrent fiabilité et robustesse là où cela est nécessaire, tandis que les composants SMT fournissent une taille compacte et des coûts de production plus bas, permettant aux fabricants de répondre efficacement aux demandes technologiques diverses. Le choix entre les deux dépend souvent des exigences spécifiques de l’application, des capacités de fabrication et des objectifs de conception de produit.
Chapitre 4
Le Processus d'Assemblage par Trou de Passage
Le processus d’assemblage par trou de passage est une procédure minutieuse qui garantit que les composants sont fixés de manière sécurisée et fiable à une carte de circuit imprimé (PCB). Ce processus implique plusieurs étapes critiques, chacune jouant un rôle essentiel dans la qualité et la fonctionnalité du produit final. Voici une décomposition étape par étape du processus d’assemblage par trou de passage :
Décomposition Étape par Étape du Processus d’Assemblage
Préparation et Fabrication de la PCB
- Commencez par la conception et la fabrication de la PCB selon la conception de circuit spécifique. Cela implique la création de la carte avec des trous pré-percés pour accueillir les broches des composants et des chemins conducteurs imprimés pour les connexions électriques.
Tri et Préparation des Composants
- Les composants sont triés et préparés conformément aux exigences de la conception de circuit. Cela inclut la collecte de résistances, de condensateurs, de diodes et d’autres composants à broches nécessaires à l’assemblage.
Insertion des Composants
- Des techniciens qualifiés insèrent manuellement les broches de chaque composant dans les trous désignés sur la PCB. Ce processus nécessite de la précision pour garantir que chaque composant est placé correctement pour correspondre au schéma de circuit.
Techniques de Soudage
- Une fois les composants placés, la carte subit un processus de soudage pour créer une connexion électrique et mécanique fiable. Il existe deux techniques de soudage principales utilisées :
a. Soudage à la Vague : Pour une production à grande échelle, les PCB sont passés au-dessus d’une vague de soudure fondue. La soudure adhère aux zones métalliques exposées et aux broches des composants, formant des joints à mesure qu’elle refroidit.
b. Soudage Manuel : Pour de petites quantités ou des composants délicats, les techniciens utilisent des fer à souder pour souder chaque connexion individuellement, permettant une précision et un contrôle.
Coupure des Broches Excédentaires
- Après le soudage, les broches de composant qui dépassent sont coupées pour prévenir les courts-circuits et les interférences avec d’autres parties de l’appareil.
Inspection et Contrôle de la Qualité
- Les cartes assemblées subissent des processus d’inspection rigoureux pour garantir que tous les composants sont correctement placés et solidement soudés. Cela inclut des vérifications visuelles et des inspections optiques automatisées (AOI) pour détecter tout défaut de soudage ou d’erreur de placement.
Tests Fonctionnels
- Les assemblages terminés sont soumis à des tests électriques pour vérifier que le circuit fonctionne comme prévu. Cela peut impliquer des tests de puissance, des vérifications d’intégrité des signaux et d’autres mesures de diagnostic pour identifier tout problème potentiel.
Réparation et Révision (si nécessaire)
- Tout défaut détecté pendant l’inspection et les tests est corrigé par des processus de réparation et de révision. Cela peut inclure la resoudure des connexions, le remplacement de composants défectueux ou d’autres mesures correctives.
Assemblage Final et Conditionnement
- Une fois que tous les composants sont correctement assemblés et testés, la PCB peut être enfermée dans un boîtier ou un coffret, l’intégrant dans la conception du produit final. Les produits assemblés sont ensuite conditionnés pour l’expédition et la distribution.
Examen Approfondi de l’Insertion des Composants, des Techniques de Soudage et de l’Inspection
Insertion des Composants : Cette étape est fondamentale car elle détermine les processus ultérieurs. La précision et la cohérence dans le placement de chaque composant garantissent un soudage efficace et minimisent les problèmes post-soudage.
Techniques de Soudage : Le soudage à la vague est efficace pour la production de masse, garantissant une application de soudure uniforme sur plusieurs cartes. Le soudage manuel, cependant, permet un travail d’artisanat méticuleux, essentiel pour la prototypage et les travaux détaillés.
Inspection : Le contrôle de la qualité est intégré à différentes étapes de l’assemblage. Les inspections non seulement garantissent la conformité aux spécifications de conception mais également contribuent à maintenir la fiabilité et la sécurité du produit électronique. Des techniques comme l’AOI et les tests dans le circuit (ICT) sont souvent employées pour améliorer la précision de l’inspection.
Grâce à ces processus systématiques, l’assemblage par trou de passage offre des connexions électroniques robustes et fiables, garantissant l’excellence opérationnelle et la durabilité dans une large gamme de produits électroniques.

Chapitre 5
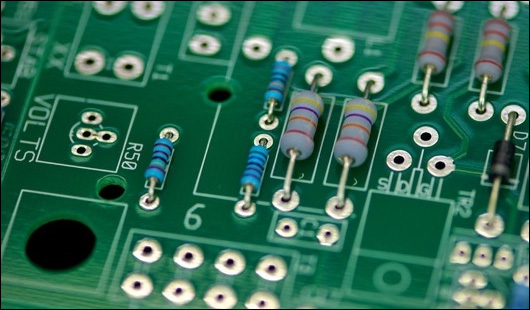
Advantages of Through-Hole Assembly
Le processus d’assemblage par trou traversant repose sur une gamme diversifiée d’équipement et d’outils pour assurer l’attachement efficace et efficient de composants électroniques aux cartes de circuits imprimés (PCI). Ici, nous explorons les outils essentiels traditionnellement utilisés dans l’assemblage par trou traversant et mettons en évidence les dernières technologies qui transforment ces processus.
Présentation des outils essentiels
Stations de soudage :
- Ces outils sont fondamentaux dans l’assemblage par trou traversant, en particulier pour le soudage manuel. Les stations de soudage comprennent généralement un fer à souder, un support et des commandes de température, permettant aux opérateurs de manipuler des composants délicats avec précision et une application de chaleur constante.
Machines de soudage à vague :
- Elles sont essentielles pour la production à grande échelle, les machines de soudage à vague automatisent le processus de soudage en créant une vague de soudure fondue. Les PCI sont convoyés au-dessus de cette vague, souder de manière sécurisée tous les composants par trou traversant en un seul mouvement rapide, améliorant considérablement la productivité et l’uniformité.
Machines d’insertion de composants :
- Bien que de nombreux composants par trou traversant soient placés manuellement, des machines d’insertion automatisées peuvent être utilisées pour certaines applications. Ces machines offrent rapidité et précision dans le placement des composants, réduisant ainsi les erreurs humaines.
Outils de désoudage :
- Les stations et les pompes de désoudage sont utilisées pour retirer la soudure des composants et des PCI, ce qui est crucial lors des processus de réparation ou de reprise. Ces outils aident à désengager efficacement les composants sans endommager la carte.
Outils d’inspection :
- Les lampes de grossissement, les microscopes et les systèmes d’inspection optique automatisés (AOI) sont indispensables pour vérifier les joints de soudure et le placement des composants. Ces outils garantissent que l’assemblage répond aux normes et spécifications nécessaires.
Instruments de découpe :
- Les coupe-fils sont utilisés pour couper les excédents de pattes de composant après soudage, aidant à prévenir les courts-circuits et les interférences avec la carte de circuit imprimé.
Dernières technologies transformant les processus d’assemblage
Technologies de soudage automatisées :
- Les machines de soudage robotisées avancées offrent une précision et une reproductibilité qui dépassent considérablement les capacités de soudage manuel. Ces robots peuvent être programmés pour des tâches spécifiques, optimisant ainsi le débit et garantissant une qualité constante sur des assemblages complexes.
Soudage au laser de précision :
- Utilisé pour des applications délicates ou à haute précision, le soudage au laser fournit une application de chaleur ciblée, minimisant ainsi le stress thermique sur les composants et permettant un contrôle précis dans le soudage de pattes délicates.
Systèmes d’inspection intelligents :
- Les technologies d’inspection pilotées par l’IA sont de plus en plus intégrées dans les lignes d’assemblage. Ces systèmes utilisent l’apprentissage automatique pour identifier les défauts avec une plus grande précision et rapidité que les méthodes d’inspection traditionnelles, fournissant des informations en temps réel et des commentaires rapides.
Systèmes de contrôle environnemental :
- Les innovations dans les équipements de protection contre les décharges électrostatiques (ESD) et les systèmes de contrôle climatique améliorent l’environnement de fonctionnement, garantissant ainsi la fiabilité élevée des processus de soudage en minimisant les impacts environnementaux et en améliorant la sécurité des opérateurs.
Fours de refusion avancés :
- Bien que principalement utilisés dans le SMT, les technologies de refusion avancées sont parfois appliquées dans des environnements d’assemblage hybride. L’intégration avec le trou traversant peut se produire dans des conceptions de cartes de technologie mixte, reflétant la flexibilité des lignes d’assemblage.
Ces progrès illustrent l’évolution continue de l’équipement et des outils dans l’assemblage par trou traversant, garantissant que cette méthode d’assemblage fiable s’adapte aux demandes modernes de rapidité, de précision et de qualité dans la fabrication d’électronique. Grâce à l’intégration de technologies de pointe, les fabricants continuent d’améliorer la fiabilité et l’efficacité des processus de trou traversant, suivant ainsi les changements dynamiques de l’industrie électronique.
Chapitre 6
Disadvantages and Limitations
L’assemblage par trous traversants est une méthode éprouvée pour monter des composants électroniques sur une carte de circuit imprimé (PCB). Même si elle a été partiellement remplacée par la technologie de montage en surface (SMT) dans de nombreuses applications, l’assemblage par trous traversants conserve encore des avantages distincts dans des scénarios spécifiques. Ici, nous fournissons une comparaison complète avec la SMT et détaillons les scénarios dans lesquels l’assemblage par trous traversants est préférable.
Avantages de l’assemblage par trous traversants
Résistance mécanique et durabilité :
- Connexions solides : Les broches des composants à trous traversants s’étendent à travers la PCB, créant un lien mécanique solide qui est très résistant aux contraintes physiques, aux vibrations et aux facteurs environnementaux. Cela rend les assemblages par trous traversants idéaux pour les applications dans des environnements robustes.
Facilité de prototypage et de test :
- Maniement manuel simple : Les composants à trous traversants sont plus grands et plus faciles à manipuler, ce qui simplifie l’insertion et le soudage manuels pendant le prototypage. Cette facilité d’utilisation permet de construire et de tester plus rapidement les prototypes avec des composants à trous traversants.
Fiabilité dans les applications à haute puissance :
- Performances thermiques améliorées : Les composants à trous traversants offrent généralement une meilleure dissipation de la chaleur en raison de leur taille plus grande et de leurs connexions robustes, les rendant adaptés aux applications à haute puissance et à haute tension.
Facilite la réalisation de joints de soudure de haute qualité :
- Consistance : La nature simple du soudage des broches à travers la carte entraîne souvent des joints de soudure de meilleure qualité par rapport à la SMT, où les composants reposent sur la surface de la PCB.
Inconvénients de l’assemblage par trous traversants
Espace de carte et densité :
- Moins compact : Les composants à trous traversants nécessitent plus d’espace sur la PCB, limitant la densité des composants et les rendant inadaptés aux produits où la miniaturisation est une priorité.
Temps d’assemblage plus long :
- Procédures manuelles : La nature manuelle de l’insertion des composants et du soudage peut augmenter le temps de production et les coûts de main-d’œuvre par rapport aux processus automatisés utilisés dans la SMT.
Applicabilité limitée dans l’électronique moderne :
- Non adapté aux petits composants : De nombreuses applications électroniques modernes utilisent des composants très petits qui ne sont pas disponibles sous forme de trous traversants, nécessitant la SMT pour de tels assemblages.
Comparaison complète avec la SMT
Automatique vs manuel : La SMT est bien adaptée aux processus d’assemblage automatisés, réduisant les coûts de main-d’œuvre et augmentant la vitesse de production. L’assemblage par trous traversants, en revanche, repose souvent sur le placement et le soudage manuels, qui peuvent être plus lents mais offrent une flexibilité dans le prototypage et la réparation.
Durabilité vs miniaturisation : La SMT excelle dans les applications où la miniaturisation et la densité de paquetage sont cruciales, telles que les smartphones et les tablettes. L’assemblage par trous traversants reste avantageux lorsque la durabilité et les connexions mécaniques solides sont requises, comme dans les applications automobiles, aérospatiales et industrielles.
Scénarios dans lesquels l’assemblage par trous traversants est préférable
Applications à haute fiabilité :
- Aérospatiale et défense : Ces secteurs requièrent souvent des connecteurs et des composants à haute fiabilité qui maintiennent les performances dans des conditions extrêmes, un scénario dans lequel la robustesse de l’assemblage par trous traversants est avantageuse.
Composants grands et lourds :
- Transformateurs et inductances : Les composants grands et lourds bénéficient de la stabilité mécanique fournie par l’assemblage par trous traversants, garantissant un montage sécurisé dans le boîtier du produit.
Prototypage et développement :
- Facilité de modification : La simplicité de la substitution de composants à trous traversants pour les tests les rend idéaux pour le développement de prototypes où des changements fréquents et des tests sont nécessaires.
Applications à haute tension et à haute puissance :
- Alimentations et convertisseurs : Les composants à trous traversants peuvent mieux gérer la taille, les contraintes thermiques et les exigences électriques typiques des applications à haute puissance.
Réparation et maintenance :
- Facilité de réparation : La taille plus grande et la nature robuste des composants à trous traversants les rendent plus faciles à retirer et à remplacer lors de la maintenance ou de la réparation.
En conclusion, même si l’assemblage par trous traversants a été largement dépassé par la SMT dans l’électronique grand public en raison de la nécessité de conceptions compactes et de production automatisée, il demeure une technologie vitale dans de nombreuses applications de niche et exigeantes où la fiabilité de pointe et la résistance mécanique sont non négociables. Comprendre les forces inhérentes à l’assemblage par trous traversants aide les concepteurs et les ingénieurs à sélectionner la technologie la plus appropriée pour leurs besoins d’application spécifiques.
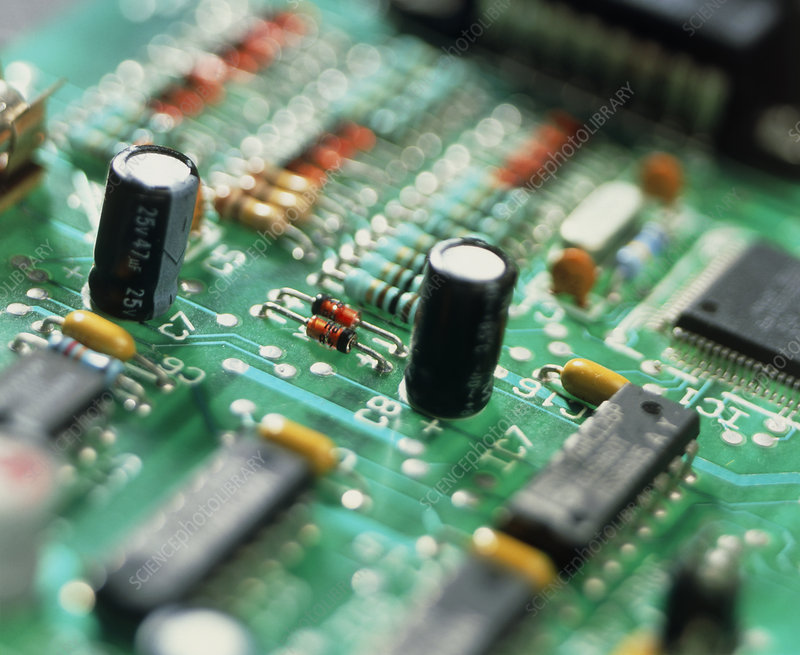
Chapitre 7
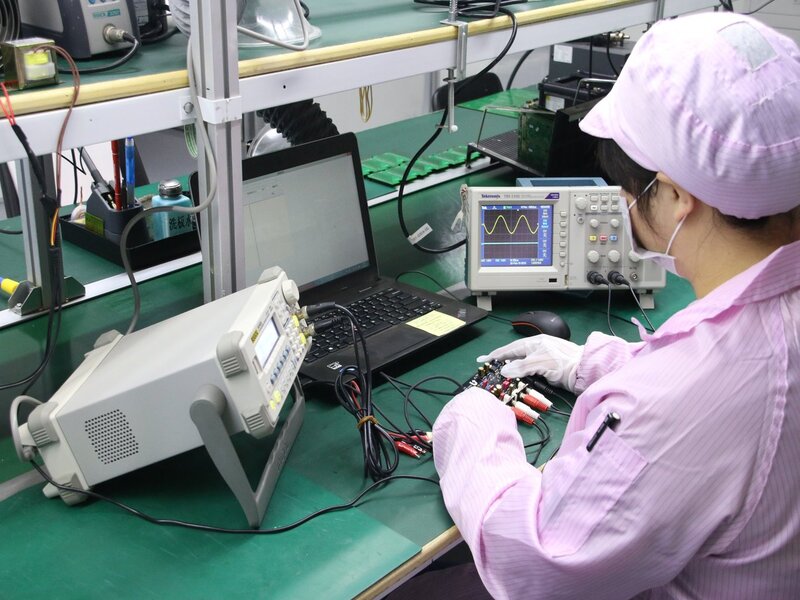
Avantages et Inconvénients de l'Assemblage par Trou
L’assemblage par trou est une méthode éprouvée pour monter des composants électroniques sur une carte de circuit imprimé (CI). Bien qu’il ait été partiellement supplanté par la technologie de montage en surface (SMT) dans de nombreuses applications, l’assemblage par trou conserve des avantages distincts dans des scénarios spécifiques. Nous fournissons ici une comparaison complète avec la SMT et détaillons les scénarios où l’assemblage par trou est préférable.
Avantages de l’Assemblage par Trou
Résistance Mécanique et Durabilité :
- Connexions Solides : Les broches des composants par trou s’étendent à travers la CI, créant un lien mécanique solide qui est très résistant aux contraintes physiques, aux vibrations et aux facteurs environnementaux. Cela rend les assemblages par trou idéaux pour les applications dans des environnements robustes.
Facilité de Prototypage et de Test :
- Manipulation Manuelle Simple : Les composants par trou sont plus grands et plus faciles à manipuler, ce qui simplifie l’insertion et le soudage manuels pendant le prototypage. Cette facilité d’utilisation permet de construire et de tester plus rapidement des prototypes avec des composants par trou.
Fiable dans les Applications à Haute Puissance :
- Performances Thermiques Améliorées : Les composants par trou offrent généralement une meilleure dissipation de chaleur en raison de leur plus grande taille et de leurs connexions robustes, les rendant adaptés aux applications à haute puissance et haute tension.
Facilite la Création de Joints de Soudure de Haute Qualité :
- Consistance : La nature simple du soudage des broches à travers la carte résulte souvent en des joints de soudure de meilleure qualité par rapport à la SMT, où les composants reposent sur la surface de la CI.
Inconvénients de l’Assemblage par Trou
Espace de la Carte et Densité :
- Moins Compact : Les composants par trou nécessitent plus d’espace sur la CI, limitant la densité des composants et les rendant inadaptés aux produits où la miniaturisation est une priorité.
Temps d’Assemblage Plus Long :
- Processus Manuels : La nature manuelle de l’insertion des composants et du soudage peut augmenter le temps de production et les coûts de main-d’œuvre par rapport aux processus automatisés utilisés dans la SMT.
Applicabilité Limitée dans l’Électronique Moderne :
- Non Adapté aux Petits Composants : De nombreuses applications électroniques modernes utilisent des composants très petits qui ne sont pas disponibles sous forme de composants par trou, nécessitant la SMT pour de tels assemblages.
Comparaison Complète avec la SMT
Automatisé vs. Manuel : La SMT est bien adaptée aux processus d’assemblage automatisés, réduisant les coûts de main-d’œuvre et augmentant la vitesse de production. L’assemblage par trou, en revanche, repose souvent sur la pose et le soudage manuels, qui peuvent être plus lents mais offrent une flexibilité dans le prototypage et la réparation.
Durabilité vs. Miniaturisation : La SMT excelle dans les applications où la miniaturisation et la densité de packaging sont cruciales, comme dans les smartphones et les tablettes. L’assemblage par trou reste avantageux lorsque la durabilité et les connexions mécaniques solides sont requises, comme dans les applications automobiles, aérospatiales et industrielles.
Scénarios où l’Assemblage par Trou est Préférable
Applications à Haute Fiabilité :
- Aérospatiale et Défense : Ces secteurs nécessitent souvent des connecteurs et des composants à haute fiabilité qui maintiennent les performances dans des conditions extrêmes, un scénario où la robustesse de l’assemblage par trou est avantageuse.
Composants Grands et Lourds :
- Transformateurs et Inductances : Les composants grands et lourds bénéficient de la stabilité mécanique fournie par l’assemblage par trou, assurant un montage sécurisé dans le boîtier du produit.
Prototypage et Développement :
- Facilité de Modification : La simplicité de remplacer des composants par trou pour les tests les rend idéaux pour le développement de prototypes où des changements et des tests fréquents sont nécessaires.
Applications à Haute Tension et Haute Puissance :
- Alimentations et Convertisseurs : Les composants par trou peuvent mieux gérer la taille, les contraintes thermiques et les exigences électriques typiques des applications à haute puissance.
Réparation et Maintenance :
- Facilité de Réparation : La plus grande taille et la nature robuste des composants par trou les rendent plus faciles à retirer et à remplacer pendant la maintenance ou la réparation.
En conclusion, bien que l’assemblage par trou ait été en grande partie supplanté par la SMT dans l’électronique grand public en raison de la nécessité de conceptions compactes et de production automatisée, il reste une technologie vitale dans de nombreuses applications de niche et exigeantes où la fiabilité et la résistance mécanique sont non négociables. Comprendre les forces inhérentes à l’assemblage par trou aide les concepteurs et les ingénieurs à sélectionner la technologie la plus adaptée à leurs besoins d’application spécifiques.
Chapitre 8
Défis courants dans l'assemblage par perçage
L’assemblage par perçage, malgré ses avantages en termes de durabilité et de fiabilité élevée, présente plusieurs défis de fabrication. Ces défis peuvent affecter la qualité, l’efficacité et la rentabilité du processus d’assemblage si ils ne sont pas traités de manière adéquate. Ci-dessous, nous décrivons certains problèmes typiques qui surviennent pendant la fabrication par perçage et proposons des solutions et des bonnes pratiques pour atténuer ces pièges courants.
Problèmes typiques rencontrés pendant la fabrication
Mauvaise alignment des composants :
- Problème : Les composants peuvent être mal alignés lors de l’insertion manuelle, ce qui peut entraîner des défauts de soudure ou des défaillances fonctionnelles.
- Impact : Les composants mal alignés peuvent causer des problèmes de connectivité électrique et affecter les performances du produit final.
Formation de joints de soudure de mauvaise qualité :
- Problème : Une quantité insuffisante de soudure, des températures incorrectes ou des paramètres de vague de soudure inappropriés peuvent entraîner des joints de soudure de mauvaise qualité.
- Impact : Les joints de soudure faibles peuvent causer des connexions intermittentes ou des défaillances de circuit complètes.
Ponts de soudure excessifs :
- Problème : Lorsque les composants sont trop proches les uns des autres ou que la soudure est imprécise, des ponts de soudure peuvent se former entre les connexions adjacentes.
- Impact : Cela peut entraîner des courts-circuits et endommager potentiellement la carte ou les composants.
Problèmes d’intégrité des pads et des trous :
- Problème : Un perçage incorrect, un placage de mauvaise qualité ou une chaleur excessive peuvent endommager les pads et les trous de la carte de circuit imprimé.
- Impact : Les pads et les trous endommagés peuvent entraîner des connexions mécaniques et des chemins électriques peu fiables.
Endommagement des composants due à la chaleur :
- Problème : Les composants sensibles à la chaleur peuvent être endommagés pendant les processus de soudure, affectant leur fonctionnalité.
- Impact : Les composants endommagés peuvent entraîner des défaillances dans le circuit et nécessiter des réparations ou des remplacements coûteux.
Incohérences de soudure par vague :
- Problème : Les variations des conditions de soudure par vague peuvent entraîner une couverture et une qualité de soudure incohérentes sur la carte.
- Impact : Cela entraîne une qualité de produit variable, nécessitant une inspection et une réparation accrues.
Solutions et bonnes pratiques pour éviter les pièges courants
Placement précis des composants :
- Solution : Utiliser des guides d’insertion de composants et des machines d’insertion automatisées lorsque cela est possible pour assurer un placement précis. Le marquage clair des orientations des composants sur les cartes de circuit imprimé peut aider les insertions manuelles.
- Bonne pratique : Formez rigoureusement les techniciens d’assemblage aux techniques de placement et à l’importance de maintenir l’alignement.
Optimisation des processus de soudure :
- Solution : Contrôlez soigneusement les températures et les durées de soudure pour assurer un écoulement de soudure optimal et une résistance des joints.
- Bonne pratique : Mettez en place un régime de contrôle de processus robuste pour les machines de soudure par vague, en vérifiant régulièrement la cohérence de la température et le maintien du niveau de soudure.
Gestion des ponts de soudure :
- Solution : Assurez un espacement approprié entre les composants et utilisez des masques de soudure pour minimiser les risques de ponts de soudure. Ajustez les paramètres de soudure par vague pour contrôler la profondeur et la propagation du dépôt de soudure.
- Bonne pratique : Conceptionnez les cartes avec un espacement de pad plus grand lorsque cela est possible et effectuez des tests réguliers de ponts de soudure pendant les cycles de production.
Assurance de la qualité des pads et des trous :
- Solution : Utilisez des processus de fabrication de cartes de circuit imprimé précis et fiables pour maintenir la qualité des trous et des pads. Effectuez un contrôle qualité pour vérifier les défauts tels que le sous-perçage ou le décollement.
- Bonne pratique : Intégrez des contrôles de qualité stricts dans le processus de fabrication de la carte de circuit imprimé, y compris des audits et des vérifications réguliers à des stades de production clés.
Gestion de la chaleur :
- Solution : Utilisez des phases de préchauffage avant la soudure pour minimiser les chocs thermiques, et sélectionnez des soldes avec des points de fusion appropriés pour les composants délicats.
- Bonne pratique : Conceptionnez les cartes pour inclure des soulages thermiques ou des dissipateurs de chaleur pour les composants particulièrement sensibles à la chaleur. Réexaminez régulièrement les profils de soudure pour s’adapter à de nouveaux composants.
Soudure par vague cohérente :
- Solution : Calibrez et maintenez régulièrement les équipements de soudure par vague pour assurer une hauteur et une température de vague cohérentes.
- Bonne pratique : Effectuez des vérifications de calibration et des activités de maintenance régulières pour les machines de soudure par vague et maintenez des journaux détaillés pour identifier et traiter les fluctuations rapidement.
En comprenant et en se préparant à ces défis courants, les fabricants peuvent non seulement améliorer la qualité et la fiabilité des assemblages par perçage, mais également renforcer l’efficacité globale et réduire les coûts de fabrication. La mise en œuvre de bonnes pratiques et de solutions dans les procédures opérationnelles standard garantira un processus de fabrication robuste capable de produire des assemblages par perçage de haute qualité à plusieurs reprises.
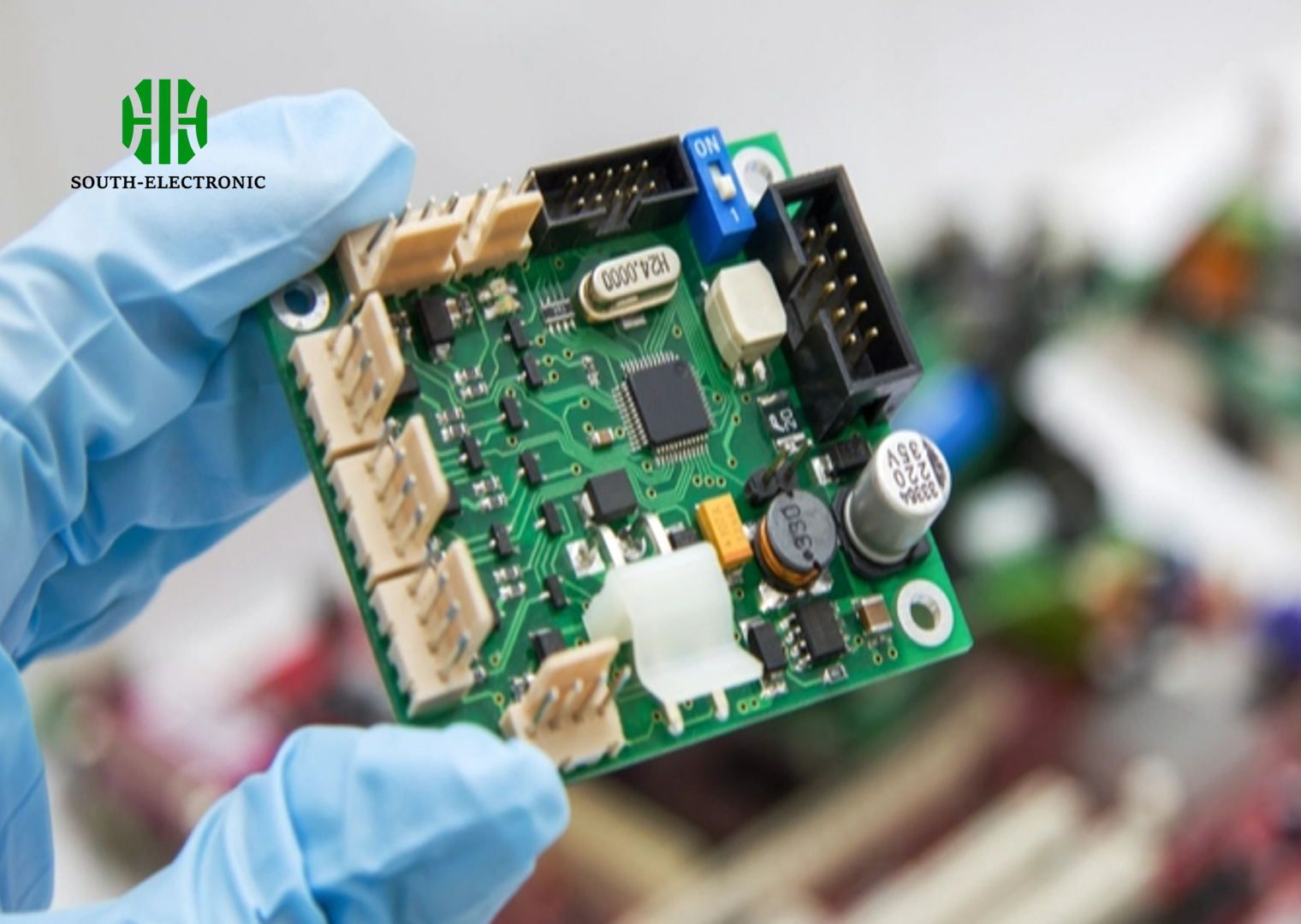
Chapitre 9

Assurance de la qualité et tests des assemblages à trous traversants
Assurer la qualité des assemblages à trous traversants est crucial pour maintenir la fiabilité et les performances des produits électroniques. L’assurance de la qualité englobe une large gamme de méthodologies et de techniques de test conçues pour identifier et rectifier les problèmes potentiels tout au long du processus de fabrication. Ici, nous explorons des méthodes efficaces pour l’assurance de la qualité et mettons en évidence des techniques de test clés telles que les tests in-circuit (ICT) et les tests fonctionnels.
Méthodes pour assurer la qualité des assemblages à trous traversants
Examen de conception robuste :
- Validation de la conception : Effectuer des examens de conception approfondis pour garantir que les conceptions de PCB sont conformes aux meilleures pratiques pour l’assemblage à trous traversants. Cela inclut la vérification des empreintes de composants, des tailles de trous et des considérations de disposition.
- Simulation et analyse : Utiliser des outils de simulation pour anticiper les problèmes potentiels tels que les contraintes thermiques et la fiabilité des joints de soudure avant d’entrer dans la phase de production.
Contrôle de processus :
- Procédures standardisées : Mettre en œuvre des procédures d’assemblage standardisées pour minimiser la variabilité dans les processus tels que le placement de composants et la soudure.
- Surveillance continue : Utiliser des capteurs et des outils de surveillance pour suivre en continu les paramètres clés pendant l’assemblage, tels que la température de soudure et le niveau de soudure à vague.
Inspection des matériaux :
- Vérification des composants : Inspecter les composants entrants pour garantir leur conformité aux spécifications, en vérifiant les défauts ou les dommages qui pourraient affecter la qualité de l’assemblage.
- Qualité de la soudure et des matériaux : Garantir la qualité des soudures et des autres matériaux en les achetant à des fournisseurs fiables et en effectuant des audits réguliers de la qualité des matériaux.
Formation des opérateurs :
- Développement des compétences : Fournir des programmes de formation complets aux travailleurs de la ligne d’assemblage pour garantir une manipulation compétente des composants à trous traversants et le respect des procédures de qualité.
- Certification et recertification : Certifier les opérateurs dans les processus clés et effectuer des recertifications régulières pour maintenir les compétences à jour et les aligner sur les normes de l’industrie.
Techniques de test pour les assemblages à trous traversants
Test in-circuit (ICT) :
- Objectif : L’ICT est utilisé pour vérifier les performances électriques et les connexions au sein d’un circuit. Il vérifie les courts-circuits, les ouvertures, la résistance, la capacité et d’autres paramètres directement sur la carte.
- Méthode : Utilise un support de test à clous pour accéder aux points de test sur la PCB, permettant un test complet de chaque nœud du circuit.
- Avantages : Fournit des commentaires rapides et précis sur les défauts d’assemblage tels que les valeurs de composants incorrectes, les problèmes de joints de soudure et d’autres erreurs d’assemblage, permettant une identification et une correction rapides.
Test fonctionnel :
- Objectif : Le test fonctionnel évalue les performances de la PCB dans des conditions réelles, en garantissant que l’ensemble de l’assemblage fonctionne selon les spécifications de la conception.
- Méthode : Les cartes sont connectées à un système de test qui simule leur environnement de fonctionnement, en évaluant comment l’assemblage PCB fonctionne correctement.
- Avantages : Vérifie que le produit final fonctionnera comme prévu dans l’application finale, en fournissant l’assurance que les composants interagissent correctement et que le système atteint les niveaux de performance souhaités.
Inspection visuelle :
- Objectif : Pour vérifier visuellement le placement et la qualité de soudure des composants sur la PCB, en détectant les problèmes d’assemblage évidents avant les tests fonctionnels.
- Méthode : Effectuée manuellement par des inspecteurs formés ou à l’aide de systèmes d’inspection optique automatisés (AOI) pour évaluer rapidement et avec précision la carte.
- Avantages : Permet une détection précoce des composants mal alignés, d’une soudure insuffisante et d’autres défauts visuels, en réduisant le besoin de réparation.
Test environnemental et de contrainte :
- Objectif : Pour évaluer comment l’assemblage réalisé fonctionne dans diverses conditions environnementales telles que les extrêmes de température, l’humidité et les chocs physiques.
- Méthode : Exposer les cartes à des conditions qui simulent les contraintes du monde réel et mesurer leur capacité à résister à ces contraintes sans dégradation des performances ou de la fiabilité.
- Avantages : Garantit que le produit maintiendra sa fonctionnalité et sa fiabilité dans diverses conditions de fonctionnement, crucial pour les applications à haute sollicitation comme l’automobile et l’aérospatiale.
En utilisant ces méthodes d’assurance de la qualité et ces techniques de test, les fabricants peuvent garantir que les assemblages à trous traversants répondent à des normes de qualité strictes. Cette approche globale non seulement améliore la fiabilité et la fonctionnalité des produits électroniques, mais atténue également les risques associés aux défauts d’assemblage, soutenant ainsi la satisfaction à long terme des clients et la réputation de la marque.
Chapitre 10
Tendances et innovations futures dans l'assemblage par trou traversant
Alors que l’industrie électronique continue d’évoluer, l’assemblage par trou traversant est sur le point de subir des avancées significatives impulsées par les technologies émergentes et les méthodes innovantes. Ces tendances futures ne promettent pas seulement d’améliorer l’efficacité et la qualité des assemblages par trou traversant, mais offrent également des solutions novatrices aux défis de longue date. Ci-dessous, nous explorons les tendances à venir et comment elles pourraient redessiner le paysage de l’assemblage par trou traversant.
Automation et robotique :
- Automatisation avancée : L’intégration de solutions de robotique et d’automatisation sophistiquées dans les lignes d’assemblage par trou traversant est susceptible d’augmenter la précision et la vitesse. Les robots d’insertion de composants et de soudage automatisés peuvent minimiser les erreurs humaines et améliorer la cohérence des processus d’assemblage.
- Robots collaboratifs (Cobots) : Les cobots sont conçus pour travailler aux côtés des opérateurs humains, fournissant une assistance pour les tâches complexes qui nécessitent une combinaison de précision mécanique et d’intuition humaine. Cette approche hybride peut considérablement améliorer la productivité et la qualité.
Impression 3D et fabrication additive :
- Fabrication de composants : À mesure que la technologie d’impression 3D progresse, elle a le potentiel de révolutionner la façon dont les composants sont fabriqués et intégrés dans les assemblages par trou traversant, en particulier pour les productions personnalisées ou à faible volume.
- Développement de prototypes : La fabrication additive peut accélérer les processus de prototypage, permettant aux concepteurs de tester et d’affiner rapidement les conceptions par trou traversant avant la production à grande échelle.
Matériaux avancés et revêtements :
- Alliages haute performance : Le développement de nouveaux alliages métalliques et de revêtements peut améliorer les performances thermiques et électriques, rendant les composants par trou traversant plus robustes et fiables.
- Revêtements environnementaux : Les innovations dans les revêtements protecteurs peuvent améliorer la durabilité des assemblages par trou traversant contre les facteurs environnementaux tels que l’humidité, la chaleur et la corrosion.
<strong:Intégration de l'IoT et de l'IA :
- Fabrication intelligente : Les appareils Internet des objets (IoT) peuvent être utilisés pour surveiller et contrôler divers aspects du processus d’assemblage en temps réel, fournissant des analyses et des insights détaillés qui peuvent améliorer l’efficacité et la qualité.
- Contrôle qualité basé sur l’IA : L’intelligence artificielle peut être employée pour analyser les données des processus de test et d’inspection, en identifiant les modèles et en prédisant les défauts potentiels avant qu’ils ne se manifestent, permettant ainsi des actions correctives préventives.
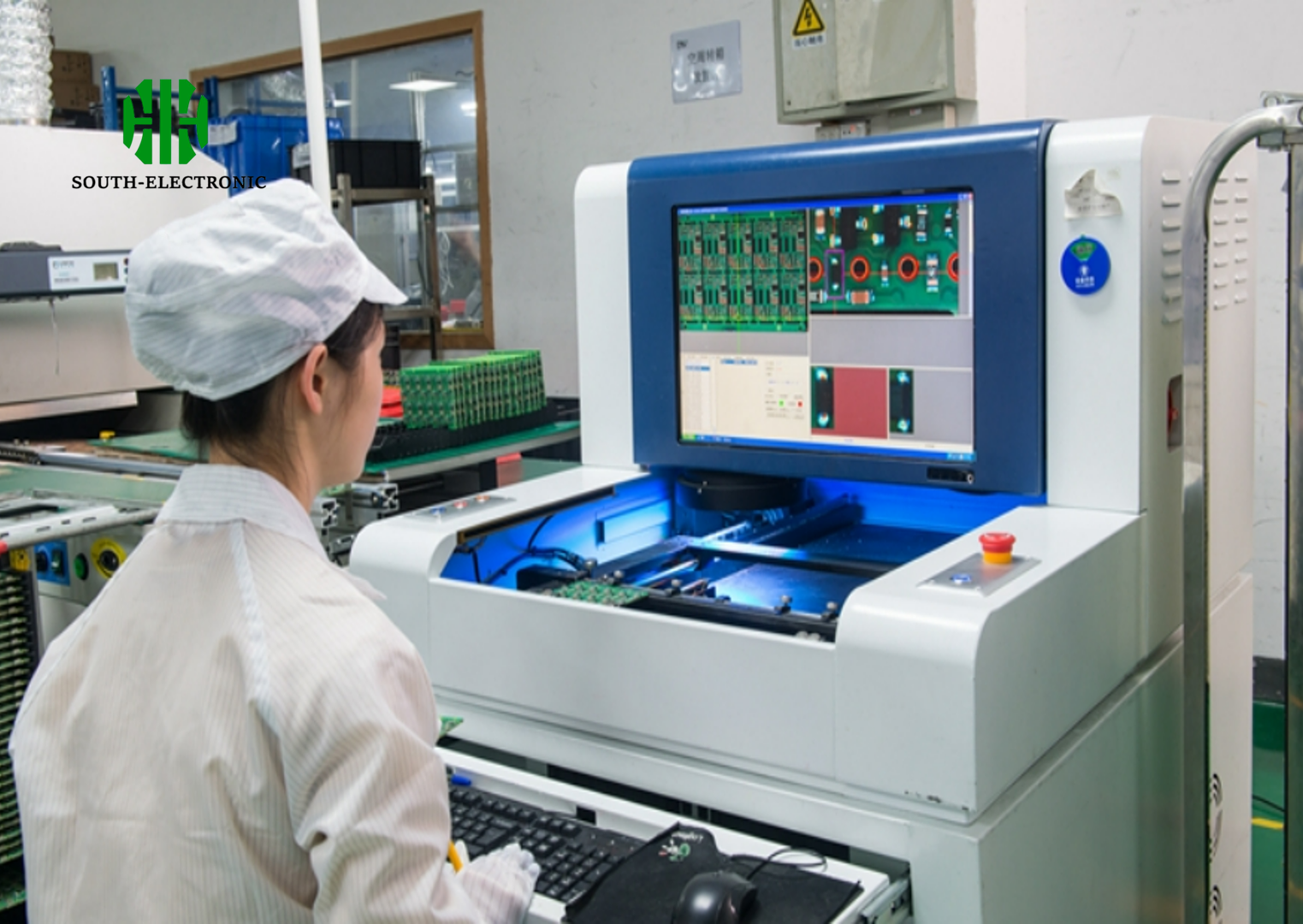
Contactez-Nous
Où Sommes-Nous ?
Parc Industriel, No. 438 Route Donghuan, No. 438, Shajing Donghuan Road, District Bao'an, Shenzhen, Guangdong, Chine
4ème étage, Bâtiment Zhihui Créatif, No. 2005 Route Xihuan, Shajing, District Baoan, Shenzhen, Chine
CHAMBRE A1-13, ÉTAGE 3, CENTRE INDUSTRIEL YEE LIM, 2-28 RUE KWAI LOK, KWAI CHUNG HK
service@southelectronicpcb.com
Téléphone : +86 400 878 3488
Envoyez-nous un message
