HDI PCB Supplier
South-Electronic
Choose South-Electronic for the highest quality, reliability, and best value in your PCB needs. Experience the difference with our complete HDI PCB services – from design to production, we guarantee precision, durability, and compliance with the toughest industry standards.
Your Reliable Partner for High-Quality HDI PCB
Welcome to South-Electronic, your source for high-quality HDI PCBs known for their high-density interconnect technology and miniaturization capabilities.
Trust South-Electronic for top-notch quality and consistency in your high-tech projects. Our HDI PCBs enhance your devices’ performance through exceptional connectivity and reduced space requirements. Partner with us to achieve innovation and success in your field.

Type I HDI PCB
This one has ultra-fine microvias with diameters less than 75 microns and conductor widths/isolation below 50 microns. It's perfect for next-generation electronic devices, like advanced medical equipment and high-frequency telecommunications.

Type II HDI PCB
This one builds on Type I by adding both blind and buried vias for better routing. It's good for advanced electronic devices that need complex multi-layer connections and higher density.
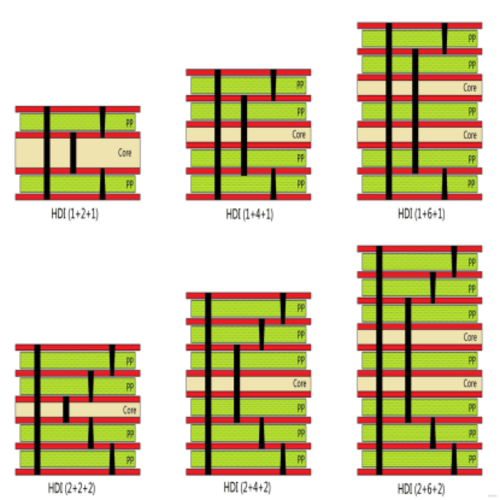
Type III HDI PCB
This one has at least two layers of microvias on one or both sides of the core, using both blind and buried vias. It's great for high-performance applications like smartphones and advanced computing because it offers superior routing
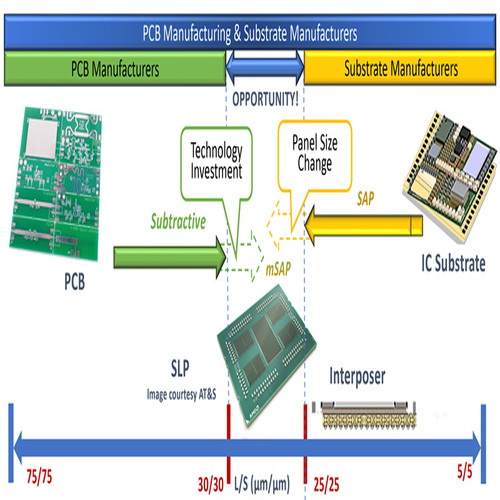
Ultra HDI PCB
This one has ultra-fine microvias with diameters less than 75 microns and conductor widths/isolation below 50 microns. It's perfect for next-generation electronic devices, like advanced medical equipment and high-frequency telecommunications.
Why Choose South-Electronic?
Choose South-Electronic for our expertise in custom, high-quality HDI PCBs for a range of applications. Our team has extensive experience, ensuring superior quality at competitive prices and exceptional service from start to finish.
-
Flexibility in Ordering
You can order as few as 1 piece to fit your exact HDI needs.
Enjoy the flexibility to test new designs or meet small batch requirements without any hassle. -
Experienced Team
You gain from our decade of industry expertise.
We understand your challenges and provide expert solutions and reliable support every step of the way. -
Comprehensive Service
You get complete satisfaction with our wide range of equipment.
Our comprehensive service ensures you get everything you need for a seamless experience. -
Fast Delivery
You benefit from our quick and efficient production times.
We prioritize timely delivery to meet your deadlines and keep your projects on track. -
Guaranteed Satisfaction
You’re assured of quality and clear communication with our ISO9001 certification.
Your satisfaction is our priority, and we’re dedicated to exceeding your expectations with every order.
Related Project We had Done
Customer Reviews
engineer
thank you, guys, the boards are really good, i am really happy to receive my boards, the components are perfect!
Operation Manager
South-Electronic is my first PCBA supplier in China. The service and quality are excellent, and the after-sales support is also very impressive. Good Job!
Common Questions
Most Popular Questions
South-Electronic has a wide range of HDI PCB configurations, including multi-layer designs, microvias, blind and buried vias, and laser-drilled holes. We specialize in delivering high-density interconnect solutions tailored to your specific project needs, ensuring optimal performance for complex electronic devices.
At South-Electronic, we have rigorous quality control measures throughout the manufacturing process. Our HDI PCBs undergo comprehensive electrical testing, Automated Optical Inspection (AOI), and X-ray inspection to detect any defects. We are also ISO and UL certified, ensuring that all products meet international quality standards.
Yes, we support small batch orders for prototyping. We understand the importance of testing and validation in the development phase, and we offer flexible manufacturing options to meet your prototyping needs without large minimum order requirements.
The standard production lead time for HDI PCBs at South-Electronic is typically 10 to 20 days, depending on the complexity of the design and the order quantity. We also offer options to accommodate urgent projects with faster turnaround times.
Yes, we provide rapid prototyping and expedited order services. For time-sensitive projects, we offer quick-turn manufacturing options to ensure your prototypes and production orders are completed within the shortest possible timeframe, without compromising on quality.
Send us a message
The more detailed you fill out, the faster we can move to the next step.
The Complete Guide For HDI PCB
Contents
Chapter 1
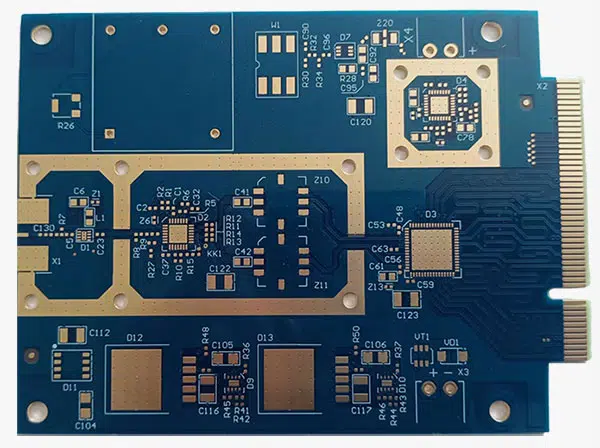
Introduction to HDI PCB
What’s HDI PCB?
HDI (High-Density Interconnect) PCBs are advanced circuit boards designed to accommodate higher wiring density per unit area, utilizing finer traces and microvias. This allows for more complex routing and integration of components in a compact design, making HDI technology ideal for high-performance applications.
Why is it important and where is it used?
HDI PCBs are crucial in modern electronics, powering devices that require faster processing, higher efficiency, and smaller form factors. They are widely used in smartphones, laptops, medical devices, automotive systems, and advanced telecommunications equipment. As technology demands continue to grow, HDI PCBs enable manufacturers to meet the needs for more compact, efficient, and reliable electronic solutions.
Chapter 2
Types of HDI PCB Configurations
Different Types of HDI PCB Configurations
There are different ways to configure HDI PCBs, depending on how complex and functional you need them to be. The most basic configuration is a 1-step HDI design, which has a single layer of microvias that provide efficient connectivity for less demanding applications, like smaller consumer electronics. A 2-step HDI design builds on this by adding another layer of microvias or staggered vias, which increases the board’s density and allows for more complex signal routing. The most advanced configuration is a multi-step HDI design, which uses multiple stacked or staggered vias across multiple layers to achieve maximum density and handle highly intricate circuit designs. These configurations are important for advanced applications like high-speed computing, telecommunications, and military equipment, where performance, reliability, and space optimization are critical.
Microvias, Blind Vias, and Buried Vias Explained
HDI technology uses advanced types of vias to greatly increase the routing options and connectivity between PCB layers. Microvias are very small, laser-drilled holes that are typically less than 0.15mm in diameter. They connect adjacent layers and allow for dense component placement and high signal integrity. Blind vias connect the outer layer of the PCB to one or more inner layers without going through the entire board, which saves space on the PCB surface while still maintaining routing efficiency. Buried vias only connect the inner layers and are completely hidden from the outside. This allows designers to create more complex layouts without sacrificing surface space for additional components.
Benefits of Different HDI Configurations
The configuration you choose for your HDI PCB depends on the specific application and performance requirements. 1-step HDI designs are cost-effective and great for products with moderate performance needs, like wearable devices or entry-level consumer electronics. 2-step and multi-step HDI configurations allow for much higher component density and more sophisticated circuitry, which is necessary for cutting-edge applications like smartphones, tablets, medical devices, and automotive electronics. Additionally, using microvias, blind vias, and buried vias optimizes the board’s space, reduces signal interference, improves thermal management, and boosts overall performance, especially in devices that require high-speed data transfer and miniaturization, like telecommunications equipment, aerospace systems, and high-end computing devices.
By using these different configurations and via technologies, HDI PCBs offer unmatched design flexibility, improved performance, and space-saving benefits, which are essential for modern electronics.
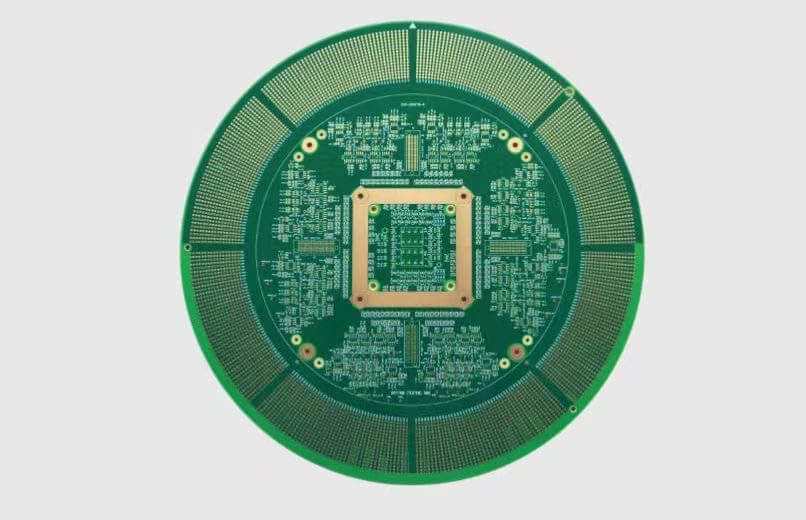
Chapter 3

HDI PCB Manufacturing Process
Making HDI PCBs is a complex process that involves many steps and advanced technologies. The goal is to make a high-density, multi-layered design that can handle the increasing demands of modern electronics for miniaturization, speed, and performance. Here’s a detailed breakdown of the key steps and technologies used to make HDI PCBs.
Step-by-Step Manufacturing Process
The process of making HDI PCBs starts with making a core layer, which is the base for the other layers. Additional layers are added by lamination and etching to make the complex circuit paths. Then advanced via technologies, like microvias, blind vias, and buried vias, are used to connect the layers. After the vias are made, the board goes through drilling, copper plating, and surface finishing. It’s then inspected and tested to make sure it meets the specifications and quality standards before it’s sent to the customer.
- Core Layer Formation: The process starts by making the core PCB layers, where copper and dielectric layers are laminated together.
- Laser Drilling: Microvias are made using high-precision laser drilling. This is a critical step in making HDI PCBs because it allows for very small holes (usually less than 150 microns) that connect the inner and outer layers.
- Copper Deposition and Plating: After the vias are drilled, the board goes through copper deposition, where a thin layer of copper is put on the walls of the drilled vias. This step makes sure there’s electrical conductivity between the layers. Then the whole surface is coated with copper through electroplating to make the conductive traces.
- Lamination: The PCB’s multiple layers are stacked and bonded together by lamination. This involves applying heat and pressure to bond the different layers of copper and insulating material, making a multilayer structure that’s important for high-density designs.
- Etching and Circuit Formation: The copper layers are selectively etched away to make the desired circuit pattern. This is a critical step in making the signal paths on the PCB.
- Surface Finish and Solder Mask Application: A solder mask is put on to protect the copper traces and prevent short circuits when the components are soldered. Then a surface finish, like ENIG (Electroless Nickel Immersion Gold) or HASL (Hot Air Solder Leveling), is put on to improve solderability and prevent oxidation.
- Inspection and Testing: The final product is thoroughly tested, including Automated Optical Inspection (AOI), electrical testing, and sometimes X-ray inspection, to make sure all the connections work and the PCB meets the design specifications.
Technologies Involved
Technologies Used Making HDI PCBs relies on several advanced technologies that allow for high precision and accuracy:
- Laser Drilling: Used to make microvias, which are key to HDI’s high-density design. Laser drilling allows for making extremely small vias that mechanical drills can’t make.
- Lamination: This process bonds the multiple layers of copper and insulating material together, making the multi-layer HDI PCB structures. Lamination makes sure the board is mechanically strong and stable.
- Plating: Electroplating is used to put copper on the vias and traces, making sure there’s good electrical connection between the layers. Also, special surface finishes like ENIG or OSP (Organic Solderability Preservative) are put on to make the board more durable and easier to solder.
Key Materials Used in HDI PCB Fabrication
The choice of materials is important in making HDI PCBs for both performance and reliability:
- Copper Foil: Copper is used to make the conductive traces and vias in the PCB. Its high electrical conductivity makes it good for making sure the signals work well.
- Dielectric Materials: Materials like FR-4 (a glass-reinforced epoxy laminate) are commonly used as insulating layers between the copper layers. For more advanced designs, materials with higher thermal stability, like polyimide, can be used.
- Prepreg and Laminates: These are important for bonding the layers together. Prepreg (a resin-coated glass fabric) is put between the copper layers during lamination to make sure the board is mechanically strong and electrically insulated.
- Solder Mask: A protective layer is put on top of the copper traces to prevent oxidation and short circuits during assembly.
- Surface Finishes: Common finishes like ENIG, HASL, or OSP are used to protect the exposed copper and make it easier to solder the components.
In conclusion, making HDI PCBs is a highly sophisticated process that requires careful control of each step and the use of advanced materials and technologies. The combination of laser drilling, multi-layer lamination, and high-performance materials allows for making compact, high-density boards that are important for modern electronic devices.
Chapter 4
Advantages of HDI PCBs
HDI PCBs offer numerous advantages over traditional PCB designs, making them essential in modern electronics where space, performance, and efficiency are critical. Here are the key benefits that make HDI technology the preferred choice for high-performance, compact, and reliable devices:
Increased Density and Component Integration
One of the primary advantages of HDI PCBs is their ability to support a much higher component density than standard PCBs. By utilizing microvias, blind vias, and buried vias, HDI PCBs can integrate more components in a smaller space. This allows for complex routing, especially in multilayer designs, enabling engineers to create intricate circuits without sacrificing space or functionality. This increased density is crucial for advanced applications such as smartphones, wearables, and automotive electronics, where the available board space is limited but the demand for functionality is high.
Enhanced Electrical Performance and Signal Integrity
HDI PCBs are designed to handle high-speed signals with minimal signal loss and interference. The use of shorter traces and microvias reduces the signal path length, minimizing electromagnetic interference (EMI) and crosstalk. This results in improved signal integrity, which is vital for high-frequency applications like 5G communication, IoT devices, and computing systems. Additionally, the ability to place components closer together shortens the electrical paths, reducing signal latency and improving overall performance. This is particularly beneficial in data-intensive applications, where speed and accuracy are critical.
Smaller Form Factor and More Compact Designs
The miniaturization of electronics is a driving force behind the widespread adoption of HDI technology. HDI PCBs allow manufacturers to create smaller, thinner, and lighter devices without compromising functionality or performance. By maximizing the use of available board space with high-density trace routing and multi-layered structures, HDI PCBs help reduce the overall size of devices. This is especially important in portable consumer electronics, such as smartphones, tablets, and wearables, where compact form factors are not only desirable but necessary for practical usability.
Higher Reliability and Durability
The advanced construction of HDI PCBs contributes to greater reliability and durability compared to traditional PCBs. The smaller vias and increased number of interconnections allow for better thermal management, as heat is distributed more evenly across the board. This reduces the risk of hot spots and component failure due to excessive heat. Furthermore, the materials used in HDI PCBs, such as high-performance laminates and copper, provide better resistance to mechanical stress, ensuring the board’s integrity even under harsh environmental conditions. This makes HDI PCBs ideal for industries like automotive, aerospace, and military, where durability and reliability are paramount.
Faster Signal Transmission and Improved Performance
In addition to better signal integrity, HDI PCBs offer faster signal transmission due to their advanced design. Shorter signal paths, reduced signal delays, and optimized routing contribute to faster data transmission speeds, which are crucial in applications requiring high processing power and rapid data transfer. HDI PCBs are widely used in sectors like telecommunications, computing, and industrial automation, where high-speed data processing and communication are critical for system performance.
Flexibility in Design and Customization
The flexibility of HDI PCB designs allows engineers to create custom boards tailored to specific application needs. With multi-step via configurations and the ability to stack layers in various ways, HDI PCBs provide more design freedom compared to traditional PCBs. This makes them ideal for creating custom solutions for specialized industries such as medical devices, where unique designs are often required to meet stringent size and performance standards. The ability to combine rigid-flex PCB designs further enhances this flexibility, allowing for complex, three-dimensional layouts that can fit into compact or irregularly shaped devices.
Cost Efficiency in High-Volume Production
While the initial cost of HDI PCB production can be higher due to the advanced manufacturing techniques involved, these costs are offset in high-volume production runs. The ability to integrate more functionality into a smaller space can reduce the need for multiple PCBs, components, and interconnections, lowering the overall cost of the final product. Additionally, the enhanced reliability and performance of HDI PCBs lead to fewer failures, reducing the costs associated with repairs, returns, and downtime, making HDI technology a cost-effective solution in the long term for high-volume manufacturers.
In conclusion, HDI PCBs offer a range of advantages that make them the go-to solution for manufacturers aiming to create high-performance, compact, and reliable electronic products. Their ability to support greater component density, improve signal integrity, offer faster speeds, and enhance design flexibility has made them indispensable in sectors such as consumer electronics, telecommunications, automotive, aerospace, and medical devices. As technology continues to evolve, the demand for HDI PCBs will only increase, driving innovation and enabling the development of more advanced and compact electronic systems.

Chapter 5
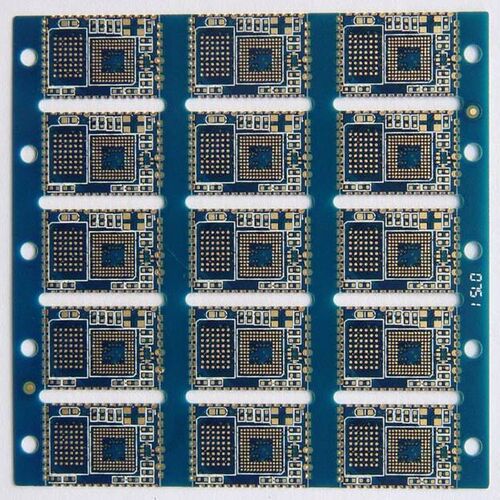
Common Applications of HDI PCBs
HDI PCBs have become essential in a wide range of industries due to their ability to support high-density designs, enhanced electrical performance, and smaller form factors. Their versatility and advanced features make them ideal for numerous applications across various high-tech sectors. Below are some of the most common applications of HDI PCBs:
Consumer Electronics
The consumer electronics market, particularly for devices such as smartphones, tablets, laptops, and wearables, heavily relies on HDI PCBs. With the growing demand for smaller, more powerful, and feature-packed devices, HDI technology allows manufacturers to maximize functionality while minimizing size.
- Smartphones: HDI PCBs enable the integration of advanced features like high-resolution cameras, fast processors, 5G connectivity, and enhanced battery life in an extremely compact space.
- Tablets and Laptops: These devices benefit from HDI PCBs by offering faster data processing, better power management, and more efficient use of space, resulting in slimmer designs and lighter products.
- Wearables: Devices like smartwatches and fitness trackers use HDI PCBs to incorporate multiple sensors, processors, and wireless communication modules in a tiny, lightweight package, making them comfortable to wear while still offering robust functionality.
Medical Devices and Healthcare Equipment
HDI PCBs play a crucial role in the development of medical devices, where precision, reliability, and compact size are critical. As the healthcare industry adopts more advanced technologies, such as portable diagnostic devices, implantable medical equipment, and monitoring systems, the use of HDI PCBs has increased significantly.
- Implantable Devices: HDI PCBs are used in pacemakers, neurostimulators, and hearing aids, where small size and reliability are essential for safe, long-term use inside the human body.
- Diagnostic Equipment: Devices like ultrasound machines, MRI scanners, and handheld diagnostic tools benefit from the high processing power and efficient data transmission provided by HDI PCBs, ensuring accurate and timely results.
- Wearable Health Monitors: Fitness trackers and wearable medical devices that monitor heart rate, blood pressure, and other vital signs require compact, lightweight HDI PCBs to offer reliable performance while being comfortable for the patient.
Automotive and Aerospace Industries
In the automotive and aerospace sectors, HDI PCBs are critical for creating reliable, high-performance systems that can withstand harsh environments while offering advanced functionality.
- Automotive Electronics: HDI PCBs are used in ADAS (Advanced Driver Assistance Systems), infotainment systems, navigation controls, and power management modules. Their small size, high reliability, and ability to handle high-speed data transmission make them essential for modern vehicles, especially electric and autonomous vehicles.
- Aerospace Systems: In the aerospace industry, HDI PCBs are deployed in avionics systems, satellite communication equipment, and navigation controls. These boards must endure extreme temperatures, pressure variations, and vibrations, and HDI technology ensures high reliability and performance in such demanding conditions. Additionally, the lightweight nature of HDI PCBs helps reduce the overall weight of aircraft and spacecraft, which is a critical factor in aerospace design.
Telecommunications and Networking Hardware
The telecommunications sector is another area where HDI PCBs have a significant impact. With the rise of 5G technology, the need for high-speed, high-frequency data transmission has become paramount, and HDI PCBs provide the necessary performance and miniaturization to meet these demands.
- 5G Base Stations: HDI PCBs are used in the core infrastructure of 5G networks, enabling faster data transfer rates, lower latency, and higher bandwidth. They help achieve the small cell designs required for 5G deployment.
- Networking Routers and Switches: In networking hardware, HDI PCBs allow for efficient routing of high-speed signals while minimizing crosstalk and signal loss. This ensures that routers, switches, and data centers operate at optimal performance, facilitating seamless communication and data transfer across large-scale networks.
- Fiber Optic Communication Systems: HDI PCBs are essential in optical transceivers and signal processors, which are critical components in fiber optic communication systems. Their high-density designs ensure efficient data processing and fast transmission rates.
Industrial Automation and Robotics
The growing field of industrial automation and robotics also benefits from HDI PCBs. Automation systems rely on precise and fast processing of data to control machines, sensors, and actuators in real time.
- Robotics: HDI PCBs are used in robots for navigation systems, motor controllers, and processing units, where space is limited, and performance is crucial. These systems often require high-speed data transfer, low power consumption, and high reliability, all of which HDI PCBs can provide.
- Automation Controllers: HDI PCBs are used in programmable logic controllers (PLCs) and human-machine interfaces (HMIs) that control industrial machinery, ensuring they operate efficiently and accurately in complex manufacturing environments.
6. Military and Defense Systems
In the military and defense sectors, HDI PCBs are indispensable due to their high reliability, compact form, and ability to handle extreme conditions. Defense systems often require robust electronics for applications such as communication, surveillance, radar, and weaponry systems.
- Radar and Communication Systems: HDI PCBs ensure fast data processing and reliable communication in critical military systems, where downtime or failure is not an option.
- Weapon Control Systems: HDI PCBs are used in guidance systems for missiles and drones, where compact size and high precision are essential.
In conclusion, HDI PCBs are found in a wide range of industries and applications, from consumer electronics and healthcare to automotive, aerospace, telecommunications, and defense. Their ability to offer high-density, high-performance, and compact designs makes them essential for today’s cutting-edge technologies and complex electronic systems. As the demand for smaller, faster, and more efficient electronics grows, the use of HDI PCBs will continue to expand across these industries.
Chapter 6
HDI PCB Design
Designing an HDI PCB is a complex task that requires careful consideration of various factors to maximize performance, ensure reliability, and meet the specific requirements of high-density and high-speed electronic applications. In this article, we will outline some guidelines to help you design HDI PCBs that meet these requirements.
Best Practices for Designing HDI PCBs
Designing HDI PCBs is more complex than traditional PCB design due to the increased density and the use of advanced manufacturing techniques. Following best practices can help ensure an optimal design:
- Define Clear Design Objectives: Start by clearly defining the product’s performance requirements, such as signal speed, component density, and mechanical constraints. This will help you choose the appropriate HDI configuration, including the number of layers and via structures.
- Collaborate Early with Manufacturers: HDI PCB design is tightly linked to manufacturing capabilities. Collaborating with the manufacturer early in the design process ensures that the design can be produced cost-effectively and within the manufacturer’s technical limits, avoiding costly design iterations.
- Use Advanced Design Software: Modern HDI PCBs require sophisticated design tools that support multi-layer, high-density layouts, microvias, and fine trace width. Using industry-standard software like Altium Designer or Cadence Allegro ensures greater precision and compliance with manufacturing standards.
- Implement Design for Manufacturability (DFM): Consider manufacturability throughout the design process by avoiding overly complex structures that may lead to higher costs or lower yield rates. DFM guidelines include keeping via sizes within manufacturing tolerances, minimizing the number of drill hits, and ensuring enough copper clearance.
Layout Considerations: Trace Width, Via Placement, and Stack-Up Design
The layout of an HDI PCB is critical for achieving high performance, especially in terms of signal integrity, thermal management, and component placement. Several layout elements require careful planning:
- Trace Width and Spacing: Since HDI PCBs often handle high-speed signals, the trace width and spacing must be carefully calculated to minimize signal loss and avoid crosstalk. It’s crucial to maintain proper impedance control based on the signal speed and the type of transmission line (such as microstrip or stripline). For ultra-high-frequency applications, trace width may be as small as 3-5 mils, and spacing must be optimized for noise reduction.
- Via Placement and Types: Proper via placement is key to maintaining the integrity of signals traveling between layers. Microvias are commonly used in HDI PCBs due to their small size, which allows for dense component placement. It’s important to place vias close to components to shorten signal paths, improving transmission speed and reducing signal degradation. Blind vias and buried vias should be used strategically to maintain board compactness and avoid unnecessary layers. Additionally, stacked vias can provide enhanced connectivity between layers but should be used sparingly to control costs and ensure mechanical stability.
- Stack-Up Design: The stack-up of an HDI PCB refers to the arrangement of its layers, including signal, power, and ground planes. A well-optimized stack-up helps achieve proper impedance control, improves signal integrity, and minimizes electromagnetic interference (EMI). Typically, alternating signal and ground layers are used to provide adequate shielding and to maintain consistent impedance across high-speed traces. Symmetrical stack-ups are also preferred to prevent warping during the manufacturing process. For complex HDI designs, additional layers with blind or buried vias are used to reduce the number of layers needed for routing, thus enhancing signal quality while reducing board thickness.
How to Minimize Signal Interference and Enhance Thermal Management
HDI PCBs are often used in high-speed applications where managing signal integrity and heat dissipation is critical. Designers must account for potential interference and thermal challenges to ensure reliable operation.
Minimizing Signal Interference (EMI/Crosstalk): Signal interference, or electromagnetic interference (EMI), and crosstalk can degrade signal quality in HDI PCBs. To minimize these effects:
- Use Ground Planes: A solid ground plane adjacent to high-speed signal layers helps reduce EMI by providing a low-impedance return path for signals. It’s also important to ensure consistent grounding across all layers.
- Optimize Trace Routing: Avoid routing high-speed traces in parallel over long distances, as this can lead to crosstalk between adjacent signals. Instead, use orthogonal routing between layers to reduce coupling.
- Impedance Matching: Ensure that the trace impedance is matched to the characteristic impedance of the connected components. Impedance mismatches can cause signal reflection, leading to noise and data corruption in high-speed systems.
- Use Differential Pairs: For high-speed data signals, differential pairs are recommended. These pairs carry complementary signals, which help cancel out EMI and reduce signal loss, making them ideal for critical signal paths like USB, HDMI, or Ethernet.
Enhancing Thermal Management: Due to their compact nature, HDI PCBs can generate considerable heat, which, if not properly managed, can degrade performance and shorten the lifespan of components. Effective thermal management strategies include:
- Thermal Vias: Placing thermal vias beneath heat-generating components helps dissipate heat by directing it to other layers or an external heat sink. These vias improve thermal conductivity and prevent hotspots.
- Heat Sinks and Thermal Pads: Incorporating heat sinks or thermal pads into the design can efficiently pull heat away from critical components, reducing the risk of overheating. Heat sinks should be placed in areas with high thermal activity, such as near processors or power regulators.
- Copper Thickness: Increasing the copper thickness in power and ground layers helps distribute heat more effectively. Thicker copper traces can also reduce voltage drops and improve current-carrying capacity.
- Component Placement: Distribute heat-generating components evenly across the board to prevent localized hotspots. Components that require high power, such as processors and power amplifiers, should be placed in areas with good airflow or near thermal management features.
In conclusion, designing HDI PCBs requires careful attention to detail and a strategic approach to layout, signal integrity, and thermal management. By following these guidelines and leveraging advanced design tools, engineers can create high-performance, reliable HDI PCBs that meet the stringent demands of modern electronics applications, ranging from consumer devices to industrial and military systems.
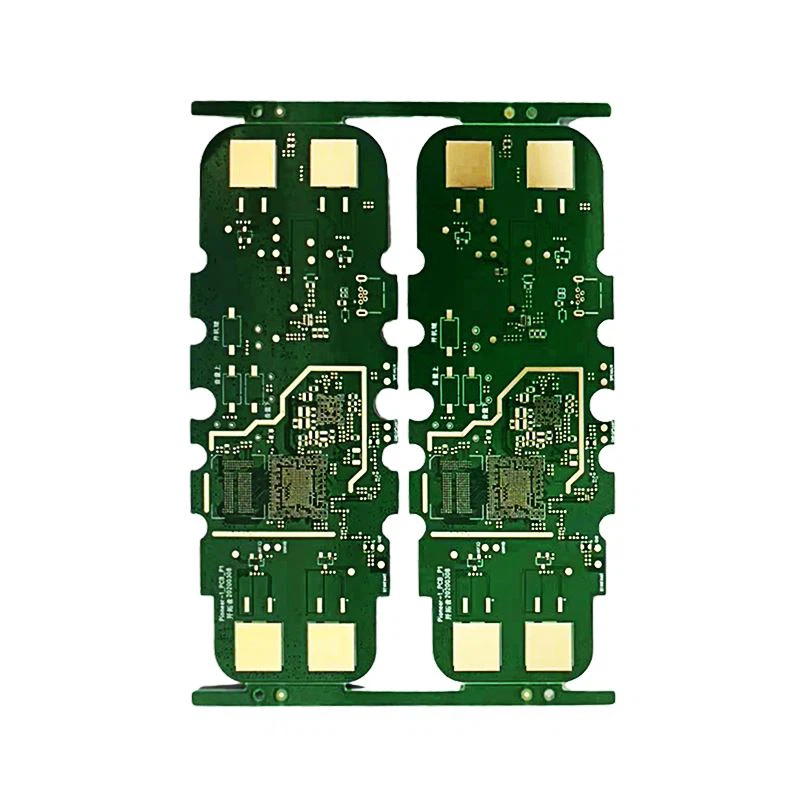
Chapter 7
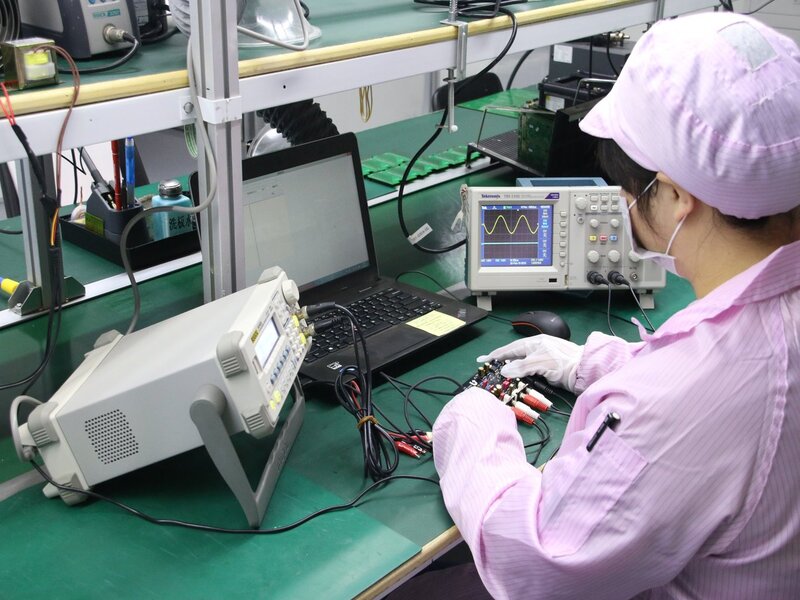
Quality Control and Testing for HDI PCBs
Quality control and testing are critical aspects of HDI PCB production, ensuring that the final product meets the high standards required for performance, reliability, and durability. Due to the complexity and density of HDI designs, rigorous testing protocols are necessary to detect and address any defects early in the manufacturing process. This helps to prevent costly failures and ensures that the PCB can function as intended in demanding applications such as telecommunications, aerospace, and medical devices. Below are the essential quality control processes and testing methods involved in HDI PCB production.
Essential Quality Control Processes in HDI PCB Production
The production of HDI PCBs involves multiple stages, each requiring strict quality control to maintain high precision and consistency. Key quality control measures include:
- Design for Manufacturability (DFM) Review: Before production begins, a thorough DFM review ensures that the PCB design is optimized for manufacturing. This review identifies any design elements that may be difficult or costly to produce, helping to prevent production delays or errors.
- In-Process Quality Control: During the manufacturing process, quality checks are performed at various stages to catch any issues before they escalate. These include inspections during drilling, lamination, etching, and plating processes to ensure that vias, traces, and layers are aligned correctly and meet the required specifications.
- Material Quality Assurance: The materials used in HDI PCB production, such as copper foil, laminates, and prepreg, are carefully tested for quality. This ensures that they meet the required standards for electrical performance, thermal stability, and mechanical strength. Ensuring the consistency and quality of these materials is crucial to avoid issues like delamination or trace defects.
Types of Testing
Several advanced testing methods are employed in HDI PCB manufacturing to verify functionality, detect defects, and ensure overall quality. Some of the most commonly used testing techniques include:
- Electrical Testing (ET): Electrical testing ensures that the HDI PCB performs as expected by verifying the continuity of all electrical connections and detecting any shorts, open circuits, or other electrical issues. Flying probe testing or bed-of-nails testing is often used to probe each net of the PCB, ensuring that all traces and vias are correctly connected and functioning without errors. For HDI PCBs, which typically have complex and dense designs, this type of testing is critical to confirm that all the high-density interconnects are correctly formed.
- Automated Optical Inspection (AOI): AOI uses high-resolution cameras to automatically inspect the surface of the PCB for defects such as misaligned components, incorrect trace widths, missing or incorrect components, and other visual anomalies. In HDI PCBs, where trace widths and spacing are extremely fine, AOI is particularly useful for detecting defects that may not be visible to the naked eye. AOI systems use pattern recognition algorithms to compare the actual PCB with the original design files, identifying any discrepancies.
- X-ray Inspection: X-ray inspection is especially important for HDI PCBs, as many of their features, such as buried vias and stacked microvias, are hidden beneath layers of material and cannot be inspected using optical methods. X-ray testing allows manufacturers to see inside the layers of the PCB and verify the integrity of these hidden connections. It is commonly used to inspect for voids in vias, misalignment of layers, and any internal defects that could compromise the board’s reliability.
- Solderability Testing: Ensures that the surface finish of the HDI PCB, such as ENIG (Electroless Nickel Immersion Gold) or OSP (Organic Solderability Preservative), provides proper solderability for component assembly. Poor solderability can lead to weak solder joints, causing performance issues or failure.
- Thermal Cycling and Stress Testing: HDI PCBs are often subjected to thermal cycling to simulate the temperature variations they will experience in real-world applications. This test helps identify any potential issues related to thermal expansion and contraction, which could cause vias to crack or delaminate. Mechanical stress testing is also conducted to evaluate the board’s ability to withstand physical stress, such as bending or vibration, without compromising performance.
How to Ensure the Reliability and Durability of HDI Boards
Given the critical applications of HDI PCBs, ensuring their reliability and durability is essential. Manufacturers employ several techniques to enhance the longevity of HDI boards and minimize the risk of failure during operation:
- Top-Notch Materials: Using high-quality, dependable materials like polyimide, high-performance laminates, and thicker copper layers can improve the durability of HDI boards, especially in tough environments where thermal and mechanical stress is common. Materials with low thermal expansion coefficients help reduce the risk of delamination or warping over time.
- Via Integrity: Ensuring the proper formation of vias is crucial to the reliability of HDI PCBs. Processes like via filling and copper plating improve the mechanical strength of microvias, preventing cracking or failures during thermal cycling or vibration. Stacked vias should be carefully manufactured and inspected, as improper alignment or poor filling can lead to weak points that might fail under stress.
- Thermal Management Design: HDI PCBs with dense component placement are prone to heat buildup, which can degrade performance over time. Designing the PCB with proper thermal management features, such as thermal vias, thicker copper layers for power and ground planes, and appropriate component spacing, helps to dissipate heat efficiently and prevents hotspots that could damage the board.
- Environmental Testing: HDI PCBs designed for critical applications, such as aerospace, automotive, or medical devices, often undergo environmental testing, which exposes them to extreme temperatures, humidity, and corrosive atmospheres. These tests ensure that the boards can withstand the environmental conditions they will be exposed to in real-world scenarios, increasing their operational reliability.
- Continuous Monitoring and Feedback: Many manufacturers implement continuous monitoring systems that collect data from each production batch, identifying trends or potential weaknesses over time. This feedback loop allows manufacturers to continuously improve their processes and maintain the highest levels of quality in HDI PCB production.
In conclusion, quality control and testing are essential to ensuring the functionality, reliability, and durability of HDI PCBs. By employing rigorous testing methods like electrical testing, AOI, and X-ray inspection, and adhering to strict quality control standards, manufacturers can deliver HDI PCBs that meet the high-performance demands of modern electronic devices. Ensuring the integrity of materials, via structures, and thermal management will help improve the long-term reliability of HDI boards, making them suitable for critical applications across a wide range of industries.
Chapter 8
Cost Considerations for HDI PCBs
When you’re planning to produce HDI PCBs, you need to consider the cost. The cost can vary depending on the complexity of the design, the materials you use, and the manufacturing processes you go through. If you understand these cost drivers, you can make informed decisions about how to balance cost and quality.
Factors that affect the cost of HDI PCBs
The cost of HDI PCBs depends on several factors, many of which are related to the complexity of the design and the processes needed to make them. Here are the main things that affect the cost:
- Number of layers: The more layers an HDI PCB has, the more it costs to make. This is because it’s more complicated to align and laminate multiple layers, and you need more materials and labor. A six, eight, or ten-layer HDI board is much more expensive than a two or four-layer board.
- Via technology: The type and number of vias you use affect the cost. Microvias, blind vias, and buried vias all require advanced processes like laser drilling and precise plating, which makes them more expensive to produce. Stacked vias are especially expensive because you have to be very precise when you align the stacked layers and make sure the connections are good.
- Materials: High-quality materials like polyimide, ceramic-filled laminates, or high-temperature substrates cost more. You need these materials for applications that need high thermal stability, flexibility, or durability, like aerospace, medical devices, or automotive electronics. The thickness of the copper you use for the conductive layers can also affect the cost. Thicker copper lets you carry more current and dissipate more heat, but it costs more.
- Advanced surface finishes: You often need special surface finishes on HDI PCBs to make them easier to solder and keep them from oxidizing. There are different options, like ENIG (Electroless Nickel Immersion Gold) or HASL (Hot Air Solder Leveling), and they cost different amounts. ENIG is more expensive than other finishes like OSP (Organic Solderability Preservative), but people like it because it’s flat and doesn’t have lead.
- Board size and shape: Smaller HDI PCBs can cost more per square unit because it’s harder to route them and you have to put more components in a smaller space. If your board has an irregular shape or cutouts or if it’s not a standard size, it can cost more because you need special tools and more complicated manufacturing processes.
- Testing and quality assurance: HDI PCBs need advanced testing methods like X-ray inspection, Automated Optical Inspection (AOI), and electrical testing. These tests make sure the board is reliable, but they add to the cost. The more complicated the design, the more rigorous and expensive the testing you need to do to make sure all the connections and components work right.
How HDI PCBs can save you money in high-volume production
Even though it can cost more to make HDI PCBs at first because you need advanced technology and materials, you can save a lot of money if you make a lot of them. Here’s how:
- Economies of scale: When you make a lot of HDI PCBs, the cost per unit goes down because you spread the fixed costs, like setup, tooling, and machine calibration, over more units. This can save you a lot of money, especially if you’re making a lot of consumer electronics, automotive systems, or telecommunications equipment.
- Fewer components: HDI PCBs let you put more stuff on one board, so you don’t need as many boards or connectors. This makes the whole system simpler and cheaper because you don’t have to spend as much on components, assembly, or shipping.
- Smaller size: You can make smaller devices with HDI PCBs, and that can save you money, especially if you’re in an industry where size and weight are important. For example, if you make electronics for cars or airplanes, using smaller, lighter electronics can make the vehicles lighter, so they use less fuel and cost less to make.
- Better reliability: HDI PCBs are more reliable because they’re made better. They handle heat and signals better, so the final product is more reliable. This means you have fewer failures and don’t have to spend as much on warranties. This is especially important if you make things like medical devices or airplane parts.
How to balance cost and quality when you buy HDI PCBs
You need to find the right balance between cost and quality when you buy HDI PCBs. If you try to save money by buying cheap boards, they might not work right, and that could be a big problem, especially if you’re making cars, airplanes, or medical devices. Here are some things you can do to get the right balance:
- Work with the manufacturer: Talk to the people who are going to make your HDI PCBs before you start. They can help you design the boards so they’re easier to make and cost less. For example, they might be able to help you change the size of your vias or make the stack-up simpler, and that could save you a lot of money without hurting how the boards work.
- Design it right: If you design your HDI PCBs the right way, you can save money. Make sure you stack them up right, route them right, and don’t use more layers or vias than you need. Also, think about what materials you really need. You don’t always have to use the most expensive stuff. You can use regular materials most of the time and only use the fancy stuff where you really need it.
- Find a good supplier: Make sure you find a supplier that knows how to make HDI PCBs. You don’t want to work with someone who doesn’t know what they’re doing because they might make mistakes that cost you a lot of money. Also, make sure the supplier has the right certifications, like ISO 9001, UL, or IPC-6012. That means they’re serious about quality.
- Buy a lot: If you can, buy a lot of HDI PCBs at once. You’ll get a better price if you buy a lot, and you won’t have to pay extra to get them made fast.
- Make prototypes: Before you make a lot of HDI PCBs, make a few prototypes. That way, you can make sure your design works and you don’t have to fix anything when you’re making a lot of boards. Fixing things when you’re making a lot of boards can cost a lot of money.
In conclusion, even though HDI PCBs can cost more at first because they’re complicated and you need fancy technology and materials, they can save you money in the long run because they’re more reliable, smaller, and cheaper to make in large quantities. To get the right balance between cost and quality, you need to design your boards right, work with a good manufacturer, and make smart choices about materials and how many boards you buy. If you do these things, you can get HDI PCBs that are good and don’t cost too much.
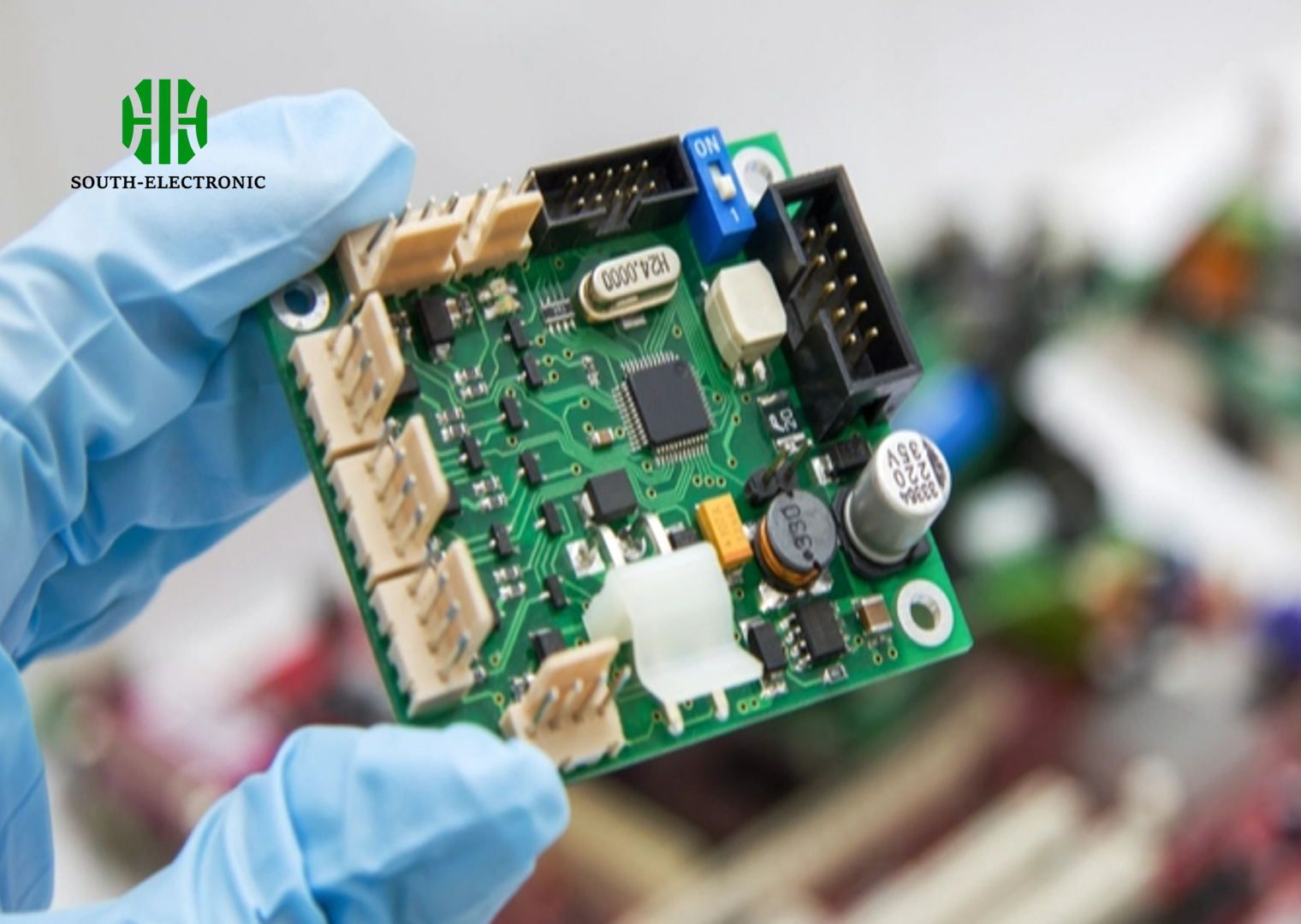
Chapter 9

Advantages of HDI PCBs Over Conventional PCBs
HDI (High-Density Interconnect) PCBs are better than traditional PCBs in many ways, especially when you need more performance, a smaller size, and more reliability.
- More Components HDI PCBs let you put more components in a smaller space using microvias, blind vias, and buried vias, so you can make more complex and compact layouts than you can with regular PCBs. This is really important for devices that don’t have a lot of space.
- Smaller HDI PCBs let you make smaller, lighter boards. This is really important for smartphones, wearables, and aerospace, where you need to be small and light.
- Better Signals HDI PCBs give you better signals because you have fewer paths for the signals to go through, so you don’t get as much electromagnetic interference (EMI) and crosstalk. This is really important for high-speed stuff like 5G, data centers, and telecom.
- Better Heat HDI PCBs are better at getting rid of heat because they have thermal vias and better layouts, so they don’t get as hot and they last longer in high-power stuff.
- More Reliable HDI PCBs are more reliable because they have stacked vias and better materials, so they don’t break as easily in cars, planes, and the military.
- Faster HDI PCBs let you go faster because the signals don’t have to go as far, so they’re good for telecom, networking, and fast computers.
- More Options HDI PCBs give you more options because you can stack up more layers and do more with the vias, so you can do more complex and custom stuff in medical and consumer.
- Cheaper HDI PCBs are more expensive at first, but they get cheaper when you make a lot of them because you can make them faster and you can put more stuff on one board, so you save money on the whole system.
So, HDI PCBs are better because they’re smaller, faster, and more reliable, and you can use them in a lot of different places like telecom, aerospace, auto, and consumer.
Chapter 10
The Future of HDI PCB Technology
As technology keeps getting better, HDI PCBs are going to keep getting smaller, faster, and more powerful. Here are a few of the trends we can expect to see:
- HDI Technology is Evolving HDI PCBs are getting more complicated, with multi-step designs, 3D packaging, and system-in-package (SiP) technology. This lets us pack more stuff into a smaller space and get better performance.
- New Materials and Techniques We’re starting to use new materials like flexible substrates and high-frequency laminates (like PTFE). We’re also using new techniques like laser direct imaging (LDI) and advanced via technologies. These let us make smaller traces, manage heat better, and pack more stuff into a smaller space.
- HDI PCBs and the Internet of Things (IoT), Artificial Intelligence (AI), and 5G HDI PCBs are going to be really important for IoT devices because they need to be small and use less power. They’re also going to be important for AI and edge computing systems because they need to process data really fast. And they’re going to be important for 5G networks because they can handle high-frequency signals and make base stations smaller.
- HDI PCBs and Semiconductor Packaging HDI PCBs are going to start working with new kinds of semiconductor packaging, like fan-out wafer-level packaging (FO-WLP) and system-in-package (SiP). This is going to let us make smaller, faster devices.
- Sustainability We’re starting to care more about the environment, so we’re using lead-free solder, halogen-free laminates, and recyclable materials. We want to make sure we’re not hurting the planet.
So, HDI PCBs are going to keep driving the IoT, AI, and 5G revolutions. And they’re going to keep getting better with new materials, new packaging, and new ways to take care of the planet.
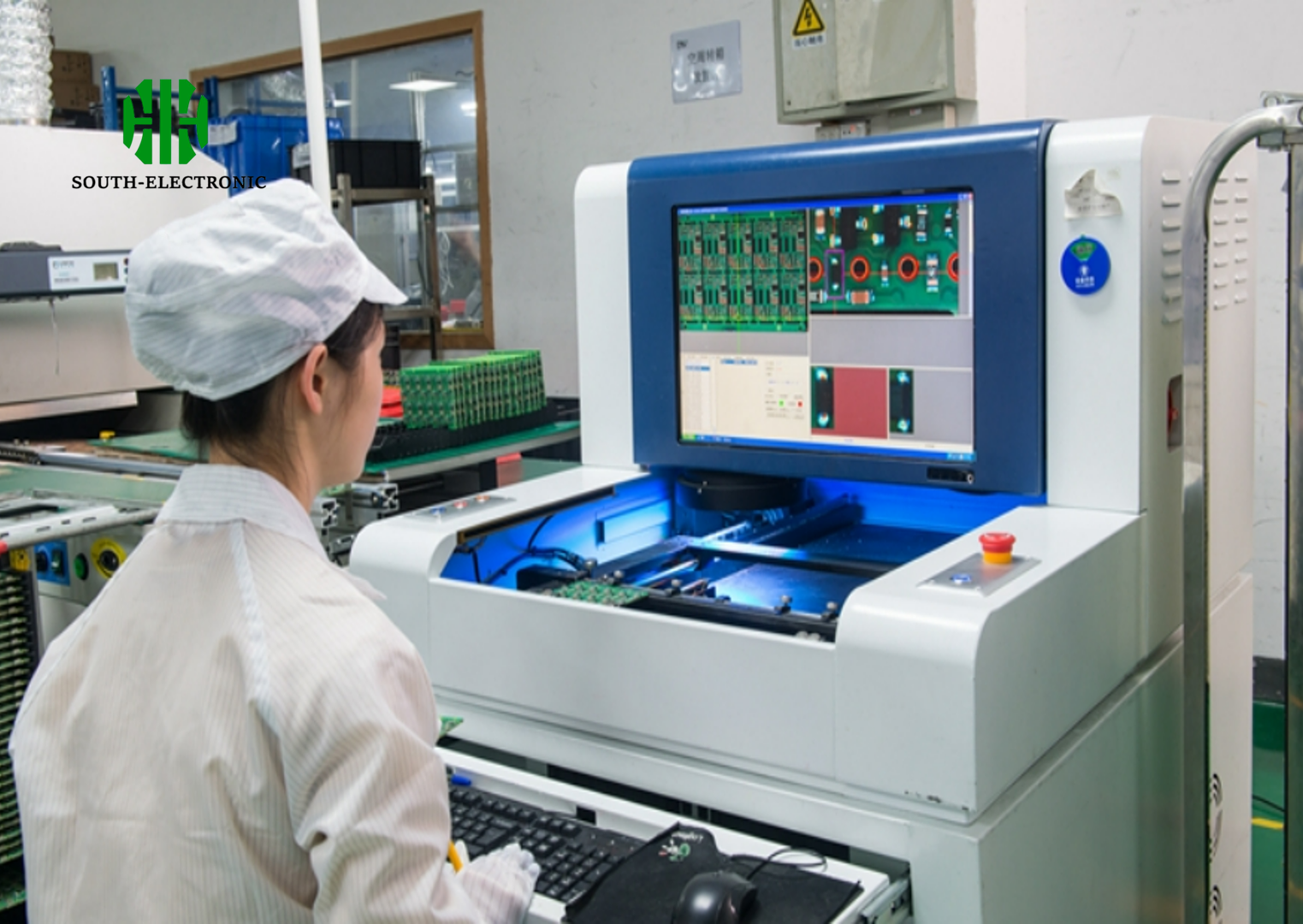
Get in touch
Where Are We?
Industrial Park, No. 438 Donghuan Road, No. 438, Shajing Donghuan Road, Bao'an District, Shenzhen, Guangdong, China
Floor 4, Zhihui Creative Building, No.2005 Xihuan Road, Shajing, Baoan District, Shenzhen, China
ROOM A1-13,FLOOR 3,YEE LIM INDUSTRIAL CENTRE 2-28 KWAI LOK STREET, KWAI CHUNG HK
service@southelectronicpcb.com
Phone : +86 400 878 3488
Send us a message
The more detailed you fill out, the faster we can move to the next step.
