HDI PCB Design Service
South-Electronic
At South-Electronic, we've got the advanced High-Density Interconnect (HDI) technology to make sure every PCB design we do is as precise and efficient as possible. If you want to make sure your PCB is reliable and performs well, our HDI PCBs are what you need.
Why Choose South-Electronic?
-
Customized Design
Customized Design to Meet Your Unique Needs.
At South-Electronic, we understand that every project is unique. That's why our PCB layout services are customized to meet your specific requirements, ensuring that every detail is executed to your exact specifications. This will improve the performance and reliability of your products. -
Guaranteed Satisfaction
You’ll appreciate the confidence that comes with working with an ISO9001 certified company.
We prioritize clear, transparent communication and hold ourselves to the highest standards, ensuring that your PCBs not only meet but exceed your expectations for performance, durability, and precision. -
One-Stop Service
When you choose us, you get a complete PCB solution from design and prototyping to mass production.
We offer a one-stop service, eliminating the complexity and cost of dealing with multiple suppliers. -
Comprehensive Service
You get complete satisfaction with our wide range of equipment.
We have a wide range of PCB processing capabilities. From design to delivery, we have the equipment and processes to make sure your order is done right. -
Fast Delivery
You stay on schedule with our fast turnaround times.
Our streamlined production ensures fast turnaround times, so you get your products when you need them, without delays.
Related Project We had Done
Customer Reviews
engineer
thank you, guys, the boards are really good, i am really happy to receive my boards, the components are perfect!
Operation Manager
South-Electronic is my first PCBA supplier in China. The service and quality are excellent, and the after-sales support is also very impressive. Good Job!
Common Questions
Most Popular Questions
technologies, including microvias, stacked and staggered vias, and via-in-pad. These technologies allow for more design flexibility, higher component density, and compact PCB layouts that are crucial for high-performance electronics.
Yes, South-Electronic is equipped to manufacture high-layer HDI PCBs, which allow for complex interconnects and denser circuitry that are ideal for advanced applications. This capability ensures that even highly complex designs meet both performance and reliability standards.
To ensure reliability, South-Electronic employs rigorous quality control processes, including automated optical inspection (AOI), electrical testing, and functional testing. These steps ensure that each HDI PCB meets strict quality and performance criteria, reducing risks and improving longevity.
South-Electronic holds important industry certifications, including ISO and IPC standards, which ensure compliance with international quality and reliability standards for HDI PCB production.
South-Electronic offers comprehensive after-sales support, including troubleshooting assistance, repair services, and warranty options. Their team is available to address any post-production needs, ensuring that each customer receives ongoing support to maintain optimal performance of their HDI PCBs.
Send us a message
The more detailed you fill out, the faster we can move to the next step.
The Complete Guide for HDI PCB Design
Contents
Chapter 1
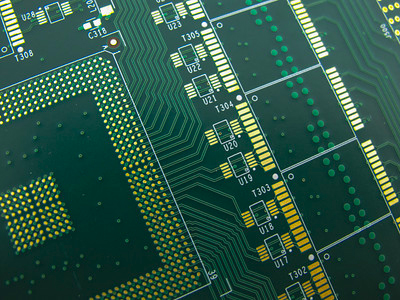
Introduction to HDI PCB Design
Overview of HDI Technology in PCBs
High Density Interconnect (HDI) technology is a game-changer in the world of printed circuit board (PCB) design. It enables you to pack more components into a smaller space than ever before. How? By using thinner lines, smaller vias, and placing components closer together. Understanding HDI technology will help you design smaller, more efficient, higher-performing devices as you dive into the world of electronics. HDI PCBs use advanced techniques like microvias, built-up multilayer boards, and high-frequency signal integrity to push your product’s capabilities beyond the limits of traditional designs.
Importance and Evolution of HDI PCBs in Modern Electronics
HDI PCBs are a big deal in today’s electronics industry. As devices get smaller and more complex, there’s a growing demand for boards that can support high component density without sacrificing performance. HDI technology has stepped up to meet that demand. It’s gone from being a way to make consumer electronics look and work better to a critical part of high-stakes applications like medical devices, automotive systems, and aerospace engineering. That’s because HDI PCBs keep getting better, thanks to advances in fabrication techniques and materials science. That means you can keep pushing the boundaries of what’s possible in your electronic designs.
Key Terms and Definitions
As you start working with HDI PCBs, knowing these key terms will help you understand and master the field faster:
Microvias: Little holes that a laser drills to connect different layers of a PCB. They’re a big deal because they save space and make HDI boards perform better:
- Microvias: Small holes drilled by a laser to connect different layers of a PCB, crucial for reducing space and enhancing the performance of HDI boards.
- Build-up Multilayer Boards: A method where additional layers are sequentially added to base copper layers, allowing for a more compact board design.
- Signal Integrity: The measure of the quality of an electrical signal, which is paramount in HDI PCBs to ensure functionality and performance.
- Pad Density: Refers to the number of component pads per unit area on a board, which is typically higher in HDI PCBs compared to conventional ones.
Chapter 2
Benefits of HDI PCBs
Enhanced Electrical Performance
When you choose HDI PCBs, you’re opting for superior electrical performance that is pivotal for today’s high-speed electronics. The use of microvias and densely packed interconnects in HDI boards results in shorter electrical paths, reduced cross-talk, and improved signal integrity. This means that you can expect faster signal transmission rates and better reliability in the function of your electronic devices. Whether you’re designing for consumer electronics, telecommunications, or high-frequency applications, HDI PCBs provide the performance enhancements you need to stay competitive.
Increased Circuit Density and Its Advantages
The hallmark of HDI technology is its ability to increase circuit density. This means more functionality in a smaller space, a critical advantage as electronic devices continue to shrink in size while growing in complexity. For you, this translates into the ability to design more compact devices without sacrificing performance—think smartphones, smartwatches, and medical implants. The increased circuit density also facilitates better thermal management and energy efficiency, which are essential for the longevity and sustainability of your products.
Reliability and Durability in Demanding Environments
Choosing HDI PCBs means investing in reliability and durability, especially critical in demanding environments like automotive, aerospace, and industrial electronics. The robust nature of HDI boards, characterized by their enhanced material selection and innovative layering techniques, ensures that they can withstand harsh conditions including high temperatures, vibration, and humidity. This durability not only extends the lifespan of the electronic components but also ensures consistent performance under stress, giving you peace of mind that your product will perform as expected, no matter the conditions.
In summary, HDI PCBs offer you a triple advantage: unmatched electrical performance, increased circuit density for miniaturization, and exceptional reliability and durability. These benefits are indispensable in today’s fast-evolving technological landscape, where the demands on electronic devices are greater than ever. By integrating HDI PCBs into your designs, you’re not just keeping up with the industry standards—you’re setting them.
Increased Circuit Density and Its Advantages
The key advantage of HDI technology is that it increases circuit density. This means more functionality in a smaller space, which is important as electronic devices continue to get smaller and more complex. This allows you to design smaller devices without sacrificing performance—think smartphones, smartwatches, and medical implants. The increased circuit density also allows for better thermal management and energy efficiency, which are critical for the long-term reliability and sustainability of your products.
Reliability and Durability in Demanding Environments
When you choose HDI PCBs, you’re investing in reliability and durability, especially important in harsh environments like automotive, aerospace, and industrial electronics. HDI boards are built to be robust, with advanced material selection and innovative layering techniques that allow them to withstand harsh conditions like high temperatures, vibration, and humidity. This durability not only extends the life of the electronic components, but also ensures consistent performance under stress, giving you confidence that your product will perform as expected, no matter the conditions.
When you choose HDI PCBs, you’re investing in reliability and durability, especially important in harsh environments like automotive, aerospace, and industrial electronics. HDI boards are built to be robust, with advanced material selection and innovative layering techniques that allow them to withstand harsh conditions like high temperatures, vibration, and humidity. This durability not only extends the life of the electronic components, but also ensures consistent performance under stress, giving you confidence that your product will perform as expected, no matter the conditions.
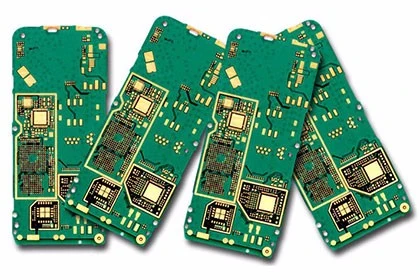
Chapter 3

Design Considerations for HDI PCBs
Material Selection for HDI PCBs
PCBs. The materials you select directly impact the performance and reliability of your electronic devices. You need to choose substrate materials that support fine line etching and provide excellent thermal stability and low dielectric loss, especially for high-frequency applications. High-performance materials like high-TG FR-4, polyimide, and BT resin are popular choices that meet these needs. Each material offers different benefits, such as improved heat resistance or better mechanical properties, allowing you to tailor the PCB to your project’s specific requirements. By selecting the right materials, you ensure that your HDI PCBs can support dense component layouts and are durable enough to handle the operational challenges they will face.
Layer Configuration and Stack-Up Considerations
Layer configuration and stack-up are critical to maximizing the benefits of HDI technology. As you design your HDI PCB, consider how the arrangement of layers can affect both the electrical performance and manufacturability of the board. The right layer configuration can reduce signal integrity issues by minimizing the distances that signals need to travel between components, reducing potential delays and interference. A well-planned stack-up can also improve the thermal management of the board, which is crucial for high-density circuits. Common configurations include using buried vias and via-in-pad designs to free up surface space for additional components. This strategic layering not only optimizes electrical performance but also helps miniaturize the device, allowing you to push the boundaries of what your products can do.
Via Types Used in HDI PCBs
Vias are a fundamental component of HDI PCBs and play a critical role in layer-to-layer interconnectivity. Understanding the types of vias available and how to use them effectively is essential to your design process. Microvias, which are small diameter vias drilled with a laser, are a hallmark of HDI design. They enable very high-density routing but can only be used for a few layers. Buried vias, which are hidden within the PCB, and blind vias, which connect an external layer to one or more internal layers, help achieve more compact and efficient designs. By effectively using these various via types, you can significantly improve the performance of your HDI PCBs by minimizing the path length for electrical signals and optimizing the real estate available on each layer.
By thoughtfully considering materials, layer configurations, and via types, you ensure that your HDI PCBs are cutting edge and provide the robustness and efficiency needed to meet today’s technological demands. By focusing on these key aspects, you position your electronic products to excel in both performance and reliability.
Chapter 4
HDI PCB Design Process
Step-by-Step Guide from Conceptualization to Final Design
Designing an HDI PCB starts with your vision. You need to conceptualize what you want your electronic device to do and what it needs to be able to do. Here’s a breakdown of the design process:
Requirement Analysis: Start by defining the performance requirements, size constraints, and environmental conditions your PCB must withstand. Understanding these will dictate the complexities involved in the layout and fabrication.
Schematic Design: Next, create a detailed schematic diagram that represents all the electrical connections between components. This is a critical step where you map out your circuit and make decisions about component placement, which significantly impacts the performance and manufacturability of your HDI PCB.
Board Layout: With your schematic in hand, begin the layout process. Here, the placement of components and routing of traces are done in accordance with HDI guidelines to optimize space and improve signal integrity.
Layer Stack-Up Planning: Decide on the number of layers and their arrangement based on the circuit complexity and power integrity needs. This includes choosing the right type of vias (microvias, buried vias) to interconnect layers effectively.
Simulation and Testing: Before finalizing the design, perform simulations to check for electrical performance, including signal integrity and thermal characteristics. Address any issues that arise to avoid costly revisions later.
Prototype Fabrication: Once your design is finalized, manufacture a prototype to test the design physically. This stage often requires adjustments based on the prototype’s performance.
Final Design Iteration and Production: After thorough testing and refinement, finalize your design for mass production. Ensure that all specifications are met to provide optimal performance in the intended applications.
Tools and Software Recommended for HDI PCB Design
Effective HDI PCB design requires sophisticated tools capable of handling the intricacies of high-density layouts:
CAD Software: Utilize advanced CAD (Computer-Aided Design) software like Altium Designer, Cadence Allegro, or Mentor Graphics PADS for detailed and precise design work. These tools offer robust features for layer management, auto-routing, and 3D visualization of your PCB stack-up.
Simulation Tools: Software like ANSYS or HyperLynx can be invaluable for signal integrity and thermal analysis, helping you predict and mitigate issues before physical prototypes are developed.
Tips for Effective Schematic Capture and Layout Planning
Keep Components Close: Place related components near each other to minimize trace lengths, which reduces potential signal degradation and interference.
Utilize HDI Techniques: Make full use of microvias and via-in-pad technologies to maximize space and improve the performance of your PCBs.
Plan for Heat: Consider thermal paths in your design to ensure that heat is managed effectively, especially in densely packed boards.
Test Routinely: Integrate testing into every stage of the design process. Early detection of problems can save significant time and resources.
By following these steps and using the right tools, you can effectively navigate the complexities of HDI PCB design, ensuring that your end product not only meets but exceeds expectations. This process not only requires technical know-how but also a visionary approach to integrating form, function, and future-readiness into your electronics.
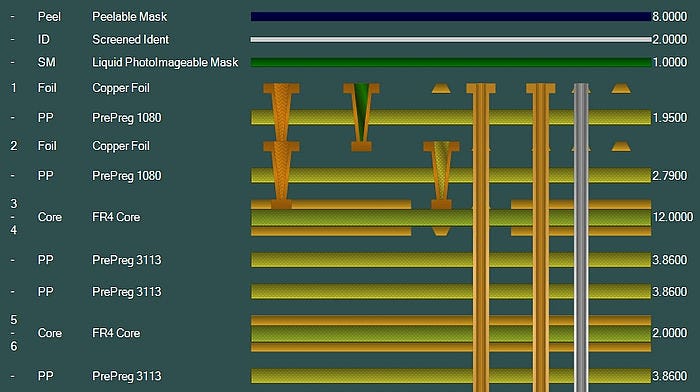
Chapter 5
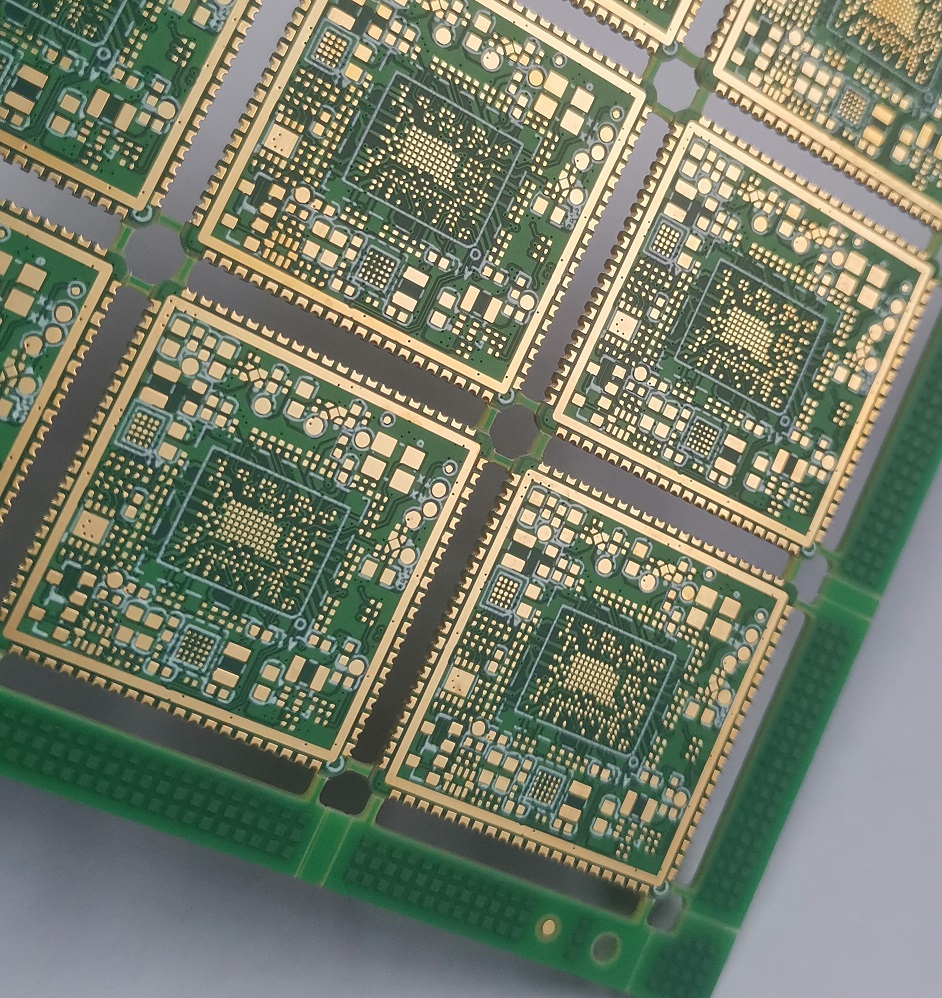
HDI PCB Manufacturing Techniques
Overview of Manufacturing Processes Unique to HDI PCBs
Manufacturing High Density Interconnect (HDI) PCBs involves sophisticated techniques that cater to their unique requirements for higher component density and finer lines. As you venture into manufacturing these advanced boards, you’ll encounter processes such as microvia formation, sequential lamination, and direct laser drilling, all essential to achieving the compact and efficient designs characteristic of HDI technology. These processes are designed to reduce layer counts while increasing functionality, crucial for modern electronic devices that demand minimized size without sacrificing performance.
Key Manufacturing Challenges and Solutions
Manufacturing HDI PCBs presents several challenges, but with the right strategies, you can overcome them effectively:
Microvia Formation: One of the most significant challenges is the formation of microvias, which are tiny holes drilled into the PCB to connect different layers. These require precise control to avoid defects like incomplete drilling or plating voids. Using advanced laser drilling equipment ensures accuracy and consistency in microvia formation.
Layer Alignment: As the number of layers increases, maintaining perfect alignment becomes crucial and challenging. Misalignment can lead to connection failures and reduced reliability. Employing optical inspection methods during the lamination process can help ensure that each layer aligns correctly.
Signal Integrity: Maintaining signal integrity in densely packed circuits is crucial. Using simulation tools during the design phase can predict potential issues that might arise from signal interactions. Additionally, careful planning of trace routing and shielding techniques during manufacturing can mitigate these effects.
Equipment and Technology Used in Production
To meet the demands of HDI PCB manufacturing, your facility needs to be equipped with state-of-the-art technology:
Laser Drilling Machines: Essential for creating microvias, laser drilling machines allow for high precision and control, making them ideal for the small dimensions required in HDI PCBs.
Automated Optical Inspection (AOI) Systems: These systems are crucial for ensuring that each layer of the PCB is free from defects and correctly aligned before proceeding to the next step in the manufacturing process.
Electroplating Equipment: Proper plating of vias and traces is vital for the functionality of HDI PCBs. Modern electroplating systems provide the control needed to achieve consistent and reliable plating, especially in the case of microvias and fine trace widths.
Sequential Lamination Presses: These are used to bond multiple layers of HDI PCBs under controlled temperature and pressure, ensuring strong adhesion and accurate layer registration.
By mastering these techniques and utilizing the right equipment, you can ensure the production of high-quality HDI PCBs that meet the exacting standards required by advanced electronic applications. This will not only enhance the reliability and performance of the products you create but also position your manufacturing operations at the forefront of the electronics industry.
Chapter 6
Testing and Quality Assurance for HDI PCBs
Common Testing Methods
To ensure that your HDI PCBs perform reliably under all conditions, a comprehensive suite of tests is critical. Here are the primary testing methods you’ll want to implement:
Electrical Testing: This involves checking for shorts, opens, and proper impedance values to ensure electrical functionality. Using a Flying Probe tester or a Bed of Nails tester, you can conduct these tests quickly and effectively without needing direct contact with each circuit component, which is ideal for the dense layouts of HDI PCBs.
Thermal Testing: Given the compact nature of HDI PCBs, managing heat is crucial. Thermal testing helps verify that your boards can operate efficiently under various thermal conditions without performance degradation. Techniques such as thermal cycle testing, where the PCB is subjected to varying temperatures to simulate operational environments, are commonly used.
Signal Integrity Testing: As frequencies increase, maintaining signal integrity becomes more challenging. Signal integrity tests ensure that the PCB can transmit signals without undue distortion or loss, crucial for maintaining functionality in high-speed applications.
Quality Standards Applicable to HDI PCBs
Adhering to recognized quality standards is not just about compliance; it’s about ensuring the longevity and reliability of your HDI PCBs. Here are some standards to consider:
IPC-6012: This standard governs the qualification and performance specifications for rigid printed boards, including those used in HDI designs. Adhering to IPC-6012 ensures that your PCBs meet rigorous reliability and quality requirements.
ISO 9001: While not specific to PCBs, ISO 9001 certification in your manufacturing processes ensures that you have a robust quality management system in place, leading to higher consistency and customer satisfaction.
IPC-A-600: Known as the “Acceptability of Printed Boards,” this standard helps in visually evaluating PCB quality, focusing on criteria such as material quality, surface conditions, and hole quality, which are critical in HDI PCBs.
Handling and Inspection During the QA Process
Handling and inspection are pivotal stages in the QA process, especially for HDI PCBs where even minor imperfections can lead to significant issues:
Automated Optical Inspection (AOI): Before and after assembly, use AOI systems to check for surface defects such as scratches or etching errors. This method is particularly effective at early stages to prevent faulty boards from moving further in the production process.
X-ray Inspection: This is crucial for inspecting microvias and other hidden features that are not visible to the naked eye. X-ray inspection allows you to check the integrity of internal layers and interconnections, ensuring that they are free from defects such as voids or misalignments.
Manual Inspection: While automated methods are effective, manual inspections by trained personnel can be invaluable, especially for final checks. It allows for the identification of issues that machines might miss and adds an additional layer of assurance before your product ships out.
By implementing these testing methods and adhering to stringent quality standards, you provide your customers with HDI PCBs that not only meet but exceed expectations in terms of performance and reliability. This commitment to quality assurance is what sets you apart in the competitive landscape of electronics manufacturing.
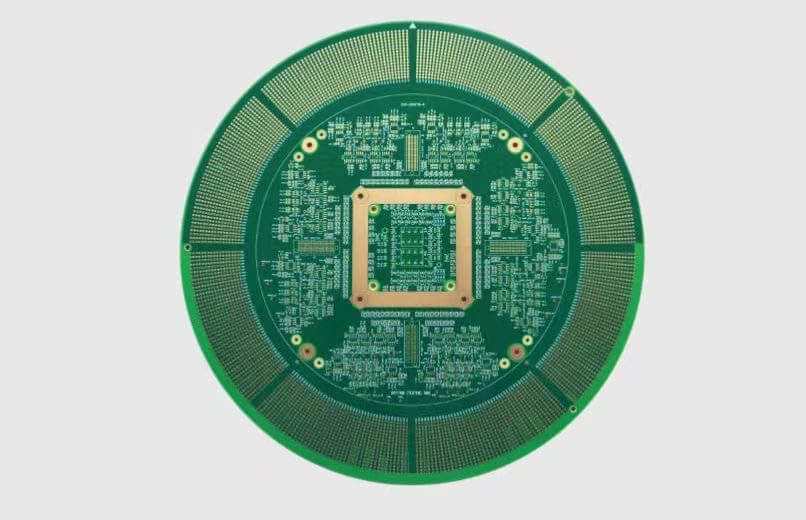
Chapter 7

Applications of HDI PCBs
Use Cases in Various Industries
HDI PCBs are integral to numerous industries, each benefiting from the unique capabilities of these high-density interconnect solutions:
Automotive: In the automotive sector, HDI PCBs are crucial for supporting the advanced electronics found in modern vehicles. From infotainment systems to safety features like airbag controllers and anti-lock braking systems, HDI PCBs provide the necessary reliability and performance in environments that are subject to vibration and temperature extremes.
Aerospace: Aerospace applications demand the utmost in reliability and precision, and HDI PCBs deliver just that. They are used in cockpit instrumentation, communication systems, and satellite navigations, where their ability to handle high-frequency signals is indispensable.
Consumer Electronics: In consumer electronics, HDI PCBs enable the miniaturization of devices such as smartphones, tablets, and wearables. They allow more functions to be packed into tighter spaces without compromising performance, leading to sleeker, more powerful devices.
Medical Devices: HDI PCBs are also widely used in medical equipment, including imaging systems and handheld diagnostic instruments. Their high reliability and compact size make them ideal for critical medical applications where precision and durability are essential.
Case Studies Showcasing the Impact of HDI PCBs
Smartphone Innovation: One leading smartphone manufacturer used HDI PCBs to revolutionize their latest model. By integrating HDI technology, they managed to double the battery life and improve the camera functionality without increasing the phone size, offering consumers a much more robust device.
Automotive Safety Improvements: An automotive company incorporated HDI PCBs into their safety systems, significantly enhancing the responsiveness and reliability of their vehicles’ emergency response features. This innovation contributed to the company receiving higher safety ratings, which boosted customer trust and sales.
Future Trends in Applications
The future of HDI PCBs promises even broader applications and innovations:
Internet of Things (IoT): As IoT devices become more prevalent, the demand for small, high-performance PCBs will increase. HDI PCBs are perfectly suited to meet these needs, providing the ability to connect multiple sensors and actuators in compact spaces.
Wearable Technology: The wearable tech industry is expanding, and HDI PCBs are at the heart of this growth. Their ability to fit into small, sometimes irregular spaces while maintaining functionality makes them ideal for this application.
Artificial Intelligence (AI): As AI continues to evolve, the electronics that support it must manage increasing amounts of data at higher speeds. HDI PCBs with their superior signal integrity and density capabilities are essential to making AI more accessible in everyday devices.
By integrating HDI PCBs into your products, you’re not just keeping pace with current technological trends; you’re staying ahead of them, ready to meet the challenges of tomorrow’s electronics landscape. This commitment to innovation ensures that your designs will continue to push the boundaries of what’s possible, making a significant impact across various industries.
Chapter 8
Challenges and Solutions in HDI PCB Design
Addressing Signal Integrity Issues
Signal integrity is a paramount concern in HDI PCB design due to the high density and compactness of the boards. When you’re crafting designs that involve high-speed signals, you may encounter issues like cross-talk, impedance mismatches, and signal reflections, which can degrade the performance of your electronics.
Solutions:
- Careful Routing and Shielding: Implement differential signaling where possible, and use ground planes to shield high-speed traces. This reduces cross-talk and electromagnetic interference, preserving the integrity of your signals.
- Impedance Control: Maintain consistent impedance across your PCB by using controlled impedance lines. This involves precise calculations and adjustments in the PCB layout phase to ensure that the impedance matches the requirements of your components and signals.
- Utilizing Advanced Materials: Consider using materials with lower dielectric constants and loss tangents, which can help in maintaining signal integrity at higher frequencies.
Managing Heat in Dense Layouts
As component density increases, so does the thermal challenge. HDI PCBs often house more active components in a smaller area, which can lead to significant heat accumulation, affecting the reliability and lifespan of the components.
Solutions:
- Thermal Via Placement: Incorporate thermal vias near heat-generating components to help dissipate heat more effectively. These vias act as thermal conduits, transferring heat away from sensitive components towards heat sinks or the outer layers of the PCB.
- Material Selection: Use substrates with higher thermal conductivity. Materials like aluminum-backed PCBs or copper can help manage heat better than standard materials.
- Effective Component Layout: Strategize the placement of components to distribute heat evenly across the PCB. Avoid clustering heat-sensitive components together unless absolutely necessary.
Overcoming Design Complexities with Innovative Solutions
The intricate nature of HDI PCBs brings several design challenges, including achieving the necessary connectivity and maintaining manufacturability without compromising on performance.
Solutions:
- Advanced Design Software: Use state-of-the-art PCB design software that features auto-routing, impedance calculators, and thermal analysis tools. These software solutions can help you visualize and optimize layouts before prototype manufacturing.
- Prototyping and Iteration: Engage in rapid prototyping to test and refine your PCB designs. This allows you to identify and resolve issues early in the design process, saving time and reducing costs in the long run.
- Collaborative Design Approach: Work closely with your manufacturing partners from the outset. Their insights can help adapt your designs to better fit manufacturing capabilities, ensuring a smoother transition from design to production.
By addressing these challenges with targeted solutions, you empower your HDI PCB designs to meet the demanding requirements of modern electronics, ensuring that your products perform reliably and efficiently. This proactive approach to problem-solving in HDI PCB design not only enhances the quality of your final products but also positions you as a leader in the field, capable of tackling the complexities of next-generation electronics.

Chapter 9

Cost Considerations and Optimization
Analyzing the Cost Factors in HDI PCB Production
Understanding the cost factors involved in HDI PCB production is crucial for managing budgets and expectations. When you’re planning an HDI PCB project, several elements can drive up costs significantly:
- Material Costs: HDI PCBs often require specialized materials that can handle higher frequencies and densities, such as advanced resin systems and copper foils, which are more expensive than those used in standard PCBs.
- Complex Manufacturing Processes: Techniques like laser drilling, sequential lamination, and fine line etching are integral to HDI PCBs but are more complex and time-consuming, leading to higher production costs.
- Design Complexity: More intricate designs that include numerous layers, microvias, and compact layouts demand more precise and labor-intensive work, increasing the overall cost.
Strategies for Cost-Effective HDI PCB Design and Manufacturing
To manage and optimize costs without compromising quality, consider these strategies:
- Efficient Design Practices: Minimize the use of unnecessary layers and microvias. Plan your design efficiently to use the least complex structure possible while meeting performance requirements. Tools like design for manufacturability (DFM) checks can help identify cost-saving opportunities in your designs.
- Material Selection: Evaluate the cost versus performance benefits of different materials. Sometimes, less expensive materials can meet the required specifications, especially if the device isn’t subjected to extreme environmental conditions.
- Volume Considerations: Larger production volumes can reduce the cost per unit. If you anticipate ongoing needs, bulk manufacturing might offer significant savings. Engaging with suppliers for long-term contracts can also lead to better pricing and terms.
Balancing Performance with Cost
Balancing the high performance required by HDI PCBs with cost constraints is a key challenge. Here’s how you can maintain this balance effectively:
- Prioritize Key Features: Identify which features of your PCB are critical to performance and which can be adjusted or removed without significant impact. Focus your budget on high-priority areas that contribute directly to the essential functionality of your product.
- Iterative Testing and Validation: Implement a robust testing regime early in the design phase. Catching and correcting design flaws early can prevent costly revisions and reworks later in the production process.
- Collaboration with Manufacturers: Work closely with your PCB manufacturer to understand their capabilities and limitations. They can offer insights into cost-effective practices and might suggest alternative manufacturing techniques or materials that reduce costs while achieving desired results.
By adopting these strategies, you can effectively manage the costs associated with HDI PCB production while ensuring that your products meet the high standards required for performance. This not only keeps your projects financially viable but also competitive in the market, ensuring that you deliver high-quality, cost-effective solutions to your customers.
Chapter 10
Future of HDI PCB Technology
Emerging Trends and Technologies in HDI PCB Design
As you look towards the future, HDI PCB technology is poised to evolve with the integration of increasingly sophisticated technologies that enhance design capabilities and functionalities:
- 3D PCBs: Emerging 3D printing technologies are starting to be applied to HDI PCBs, allowing for the creation of three-dimensional structures. This innovation can significantly increase the density and complexity of PCB designs, opening up new possibilities in electronic device architecture.
- Flexible HDIs: There’s growing interest in flexible HDI PCBs, which are crucial for wearable technology, medical devices, and embedded electronics. These flexible circuits can conform to unusual shapes and move without breaking, expanding the design possibilities beyond traditional flat boards.
- Integrated Passive Devices (IPD): The integration of passive components directly onto the PCB substrate is another trend gaining traction. This approach saves space and reduces the number of components, leading to thinner, lighter boards with fewer points of failure.
Predictions for the Evolution of HDI Applications
The scope of HDI technology applications is expected to broaden significantly, driven by demands for higher performance and miniaturization:
- Automotive and Aerospace: As both sectors push for more advanced electronic systems for navigation, safety, and performance monitoring, HDI PCBs will become even more critical. Their ability to handle high-density configurations reliably makes them ideal for the complex electronic systems used in these industries.
- Smart Cities and Infrastructure: HDI PCBs will play a vital role in the development of smart infrastructure by enabling the integration of IoT devices into everyday objects and systems, enhancing urban living with smarter solutions for energy management, traffic control, and environmental monitoring.
Impact of Advancements like AI and IoT on HDI PCB Designs
The influence of Artificial Intelligence (AI) and the Internet of Things (IoT) on HDI PCB design is profound and far-reaching:
- AI Integration: As AI becomes more embedded in devices, the demand for PCBs that can handle intensive data processing and real-time decision-making increases. HDI PCBs with their high component density and efficient signal handling are perfect for AI applications, requiring robust, high-speed processing capabilities.
- IoT Expansion: The explosion of IoT devices in the market necessitates PCBs that can connect multiple sensors and actuaries in a compact space. HDI technology facilitates the development of small, powerful PCBs capable of supporting the connectivity needs of millions of IoT devices.
As you navigate the future of electronics, staying ahead in HDI PCB technology means continually adapting to these advancements. Embracing new design paradigms and manufacturing techniques will ensure that your products remain at the cutting edge, meeting the evolving demands of technology and consumers alike. The future of HDI PCBs is not just about keeping up with trends but setting them, driving innovation that shapes the next generation of electronic devices.
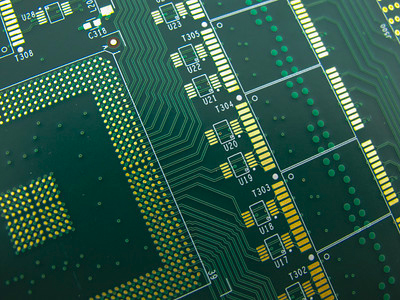
Get in touch
Where Are We?
Industrial Park, No. 438 Donghuan Road, No. 438, Shajing Donghuan Road, Bao'an District, Shenzhen, Guangdong, China
Floor 4, Zhihui Creative Building, No.2005 Xihuan Road, Shajing, Baoan District, Shenzhen, China
ROOM A1-13,FLOOR 3,YEE LIM INDUSTRIAL CENTRE 2-28 KWAI LOK STREET, KWAI CHUNG HK
service@southelectronicpcb.com
Phone : +86 400 878 3488
Send us a message
The more detailed you fill out, the faster we can move to the next step.
