Assembly and High-Volume PCB Manufacturing
High Volume PCB assembly and mass production are crucial as long as our electrical needs depend significantly on PCBs. To satisfy these requirements, it's essential to choose a high-volume printed circuit board manufacturer that is perfect.
High-Volume PCB Manufacturing: High-volume PCB manufacturing refers to the industrial process of producing large quantities of printed circuit boards (PCBs), which are essential components in virtually all electronic devices. This manufacturing process involves the large-scale production of PCBs using sophisticated, automated machinery and technology to ensure efficiency, consistency, and lower per-unit costs.
High-Volume Assembly: High-volume assembly refers to the process of assembling numerous electronic components onto printed circuit boards to create functional electronic circuits. This stage follows PCB manufacturing and focuses on component placement and connection.

Benefits of High-Volume PCB Manufacturing
Production of High-Volume PCBs
The final stage of PCB manufacture before delivering to clients is high-volume printed circuit board fabrication. High numbers of PCB are produced by a linear process with no layout adjustments. The goal of this process is to generate high-quality printed circuit boards at the lowest cost while keeping up a rapid production rate to satisfy the demands of the client.
Large-Scale Assembly
High-volume printed circuit board assembly requires the creation of more than ten thousand PCB parts while taking Design for Manufacturing (DFM) and Design for Testing (DFT) into account (DFM). When hiring a printed circuit board firm for mass production, it is crucial to know the sort of printed circuit board that is needed. Otherwise, there is a chance that there will be a lot of high-quality PCBs that do not satisfy the particular requirements of the electronics. So, selecting the right PCB is crucial since it may greatly affect functioning.

Maximizing the High-Volume PCB Manufacturing Process
To maximize efficiency and effectiveness in high-volume PCB manufacturing, several strategies can be employed:
- Design for Manufacturability (DFM): This involves designing PCBs in a way that optimizes all the manufacturing processes. It includes selecting the right materials, minimizing the number of components, and ensuring that the design is easy to assemble. DFM helps in reducing waste, lowering costs, and speeding up production times.
- Automation and Technology Integration: Investing in the latest manufacturing technologies and automation systems can significantly enhance production efficiency. Automated testing, solder paste inspection, and assembly robots are examples of technologies that can improve throughput and quality.
- Supplier Relationships: Establishing strong relationships with component suppliers and material providers can ensure the steady availability of required inputs without delays. This also helps in negotiating better terms and prices, further lowering production costs.
- Lean Manufacturing Principles: Implementing lean manufacturing techniques can help in minimizing waste and improving overall efficiency. This includes just-in-time inventory practices, continuous improvement processes, and value stream mapping.
- Scalable Processes: Designing scalable processes that can be adjusted based on demand fluctuations is crucial for maintaining efficiency. This flexibility allows manufacturers to optimize production rates and avoid overproduction or stock shortages.
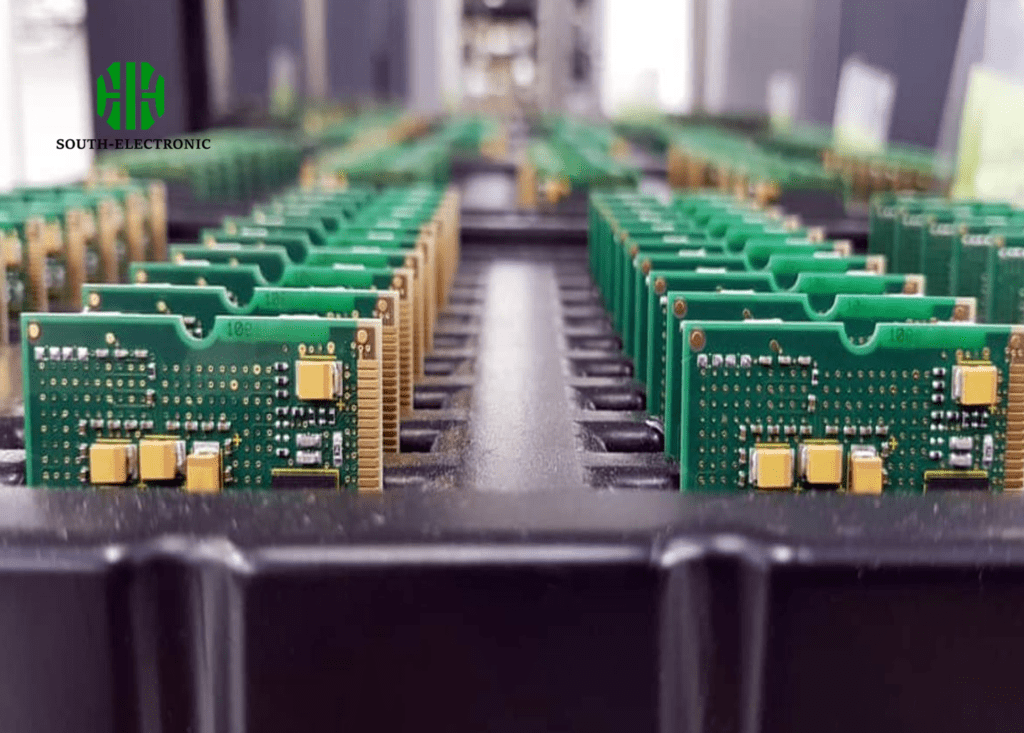
Prototype to High-Volume PCB Manufacturing
Ideally, the transition from PCB prototyping to manufacturing stage to mass or large volume creation should be simple and seamless. Nevertheless, difficulties might occur during this shift, such as the requirement to revise layout files in order to build PCBs of superior quality. Without the right design files, it may be more expensive to produce high-quality printed circuit boards, which would take more time and money.
Other serious issues, such the need to collect and transmit additional layout files from the prototype producer to the contract producer, may emerge as a result of a lack of layout data. Also, the contract producer might not be able to create your PCBs in accordance with the precise guidelines provided by the prototype maker. Components going missing during the printed circuit board fabrication phase are not unusual. Moreover, design modifications can be necessary, particularly if there are operational and performance shortcomings that call for re-prototyping and redesigning.