What Is BGA Rework?
When you need to remove, replace, or repair a BGA component on a PCB, that's called BGA rework. A BGA is a component that has a bunch of solder balls (or "bumps") that connect it to the board. Unlike traditional components, BGAs are hard to rework because the solder joints are hidden under the package, so you can't get to them or see them.
When is BGA Rework Necessary?
- Faulty Solder Joints: If the solder joints between the BGA and the PCB are compromised, rework becomes necessary to restore electrical connectivity.
- Damaged Components: Physical or thermal stress can damage the BGA package, requiring replacement.
- Upgrades or Modifications: In some cases, upgrading a component or modifying the circuit requires BGA removal and replacement.
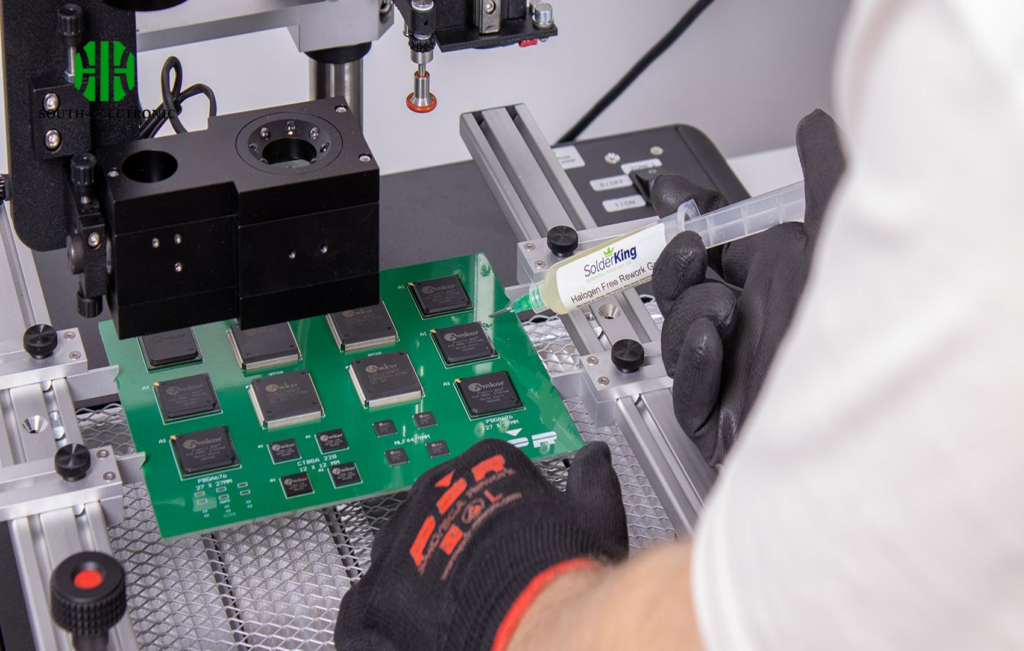
How to Do BGA Rework?
Tools Needed for BGA Rework:
- BGA Rework Station (includes hot air gun, soldering station, and reflow oven)
- ESD Protection (anti-static mat, wrist strap)
- Flux (for cleaning and facilitating solder reflow)
- Solder Paste or Pre-formed Solder Balls
- Vacuum Pickup Tool (for safely removing and placing the BGA)
- Tweezers and Cleaning Materials (to clean the PCB pads)
1. Site Preparation
Before reworking the BGA, proper preparation is critical. Ensure your workspace is clean, static-free, and organized.
- Clean the Area: Use isopropyl alcohol to remove any debris, dirt, or old flux from the area around the BGA.
- Apply ESD Protection: Wear an ESD wrist strap and place the board on an ESD-safe mat to prevent static discharge from damaging sensitive components.
- Apply Flux: Use a no-clean flux to the BGA area to promote proper solder reflow during the heating process.
2. BGA Removal
Removing the BGA is a delicate step that requires precise control over temperature and time.
- Preheat the PCB: Use the BGA rework station to preheat the PCB to ensure even temperature distribution and avoid warping the board.
- Heat the BGA: Position the hot air nozzle above the BGA and apply heat evenly until the solder joints reflow. The BGA should start to lift from the board as the solder melts.
- Remove the BGA: Carefully use a vacuum pickup tool or tweezers to lift the BGA off the board. Be sure not to apply excessive force, as this could damage the pads underneath.
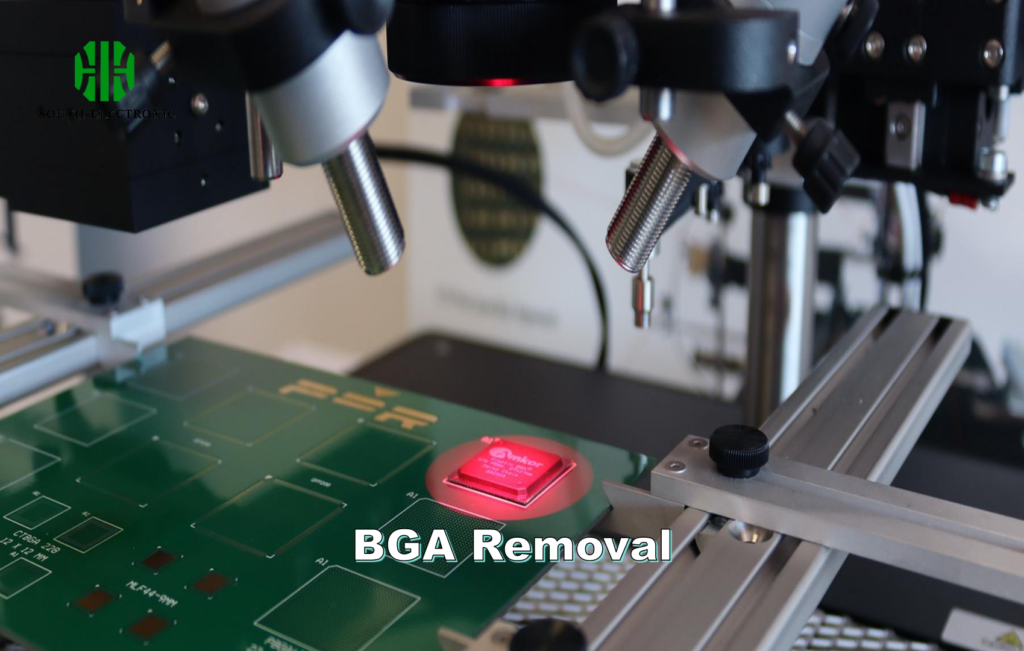
3. Cleaning the Site (Site Redressing)
After removing the BGA, it’s essential to clean the pads on the PCB to prepare for re-soldering.
- Remove Residual Solder: Use a solder wick or soldering iron to remove old solder from the pads. This ensures that the new BGA will make proper contact with the PCB.
- Clean with Alcohol: Clean the site again with isopropyl alcohol to remove any flux or residue left behind during solder removal.
4. Reballing the BGA
Reballing is the process of applying new solder balls to the BGA if needed. This step is essential if the original BGA is being reused.
- Align the BGA: Place the BGA in a reballing jig or stencil designed to hold it in place.
- Apply Solder Balls or Paste: Using a fine solder stencil, apply solder paste or pre-formed solder balls to the BGA.
- Reflow the Solder Balls: Use the reflow station to melt the solder balls onto the BGA. Ensure even heat distribution to avoid warping the BGA.
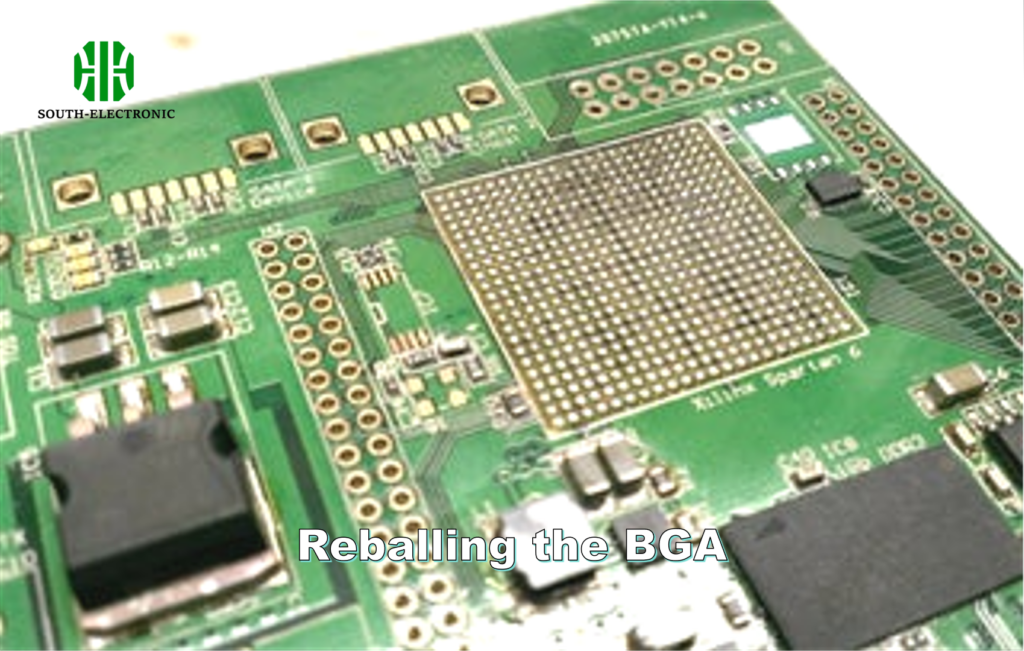
5. Re-soldering the BGA
After the BGA is properly reballed, it’s time to reattach it to the PCB.
- Position the BGA: Carefully align the BGA on the PCB pads using tweezers or a vacuum tool.
- Reflow the BGA: Use the rework station's hot air or reflow oven to melt the solder balls, ensuring the BGA is securely attached to the PCB.
- Inspect the Solder Joints: After cooling, inspect the joints under a microscope or using X-ray equipment to ensure proper connections.
How Many Times Can a BGA Be Reworked?
You can only rework a BGA so many times. Usually, you can rework a BGA two or three times before you start to risk damaging the pads on the board or the component itself.
Rework Cycle | Expected Outcome |
---|---|
1st Cycle | Optimal rework; minimal pad damage |
2nd Cycle | Pads may weaken; moderate risk |
3rd Cycle | High risk of pad or component failure |
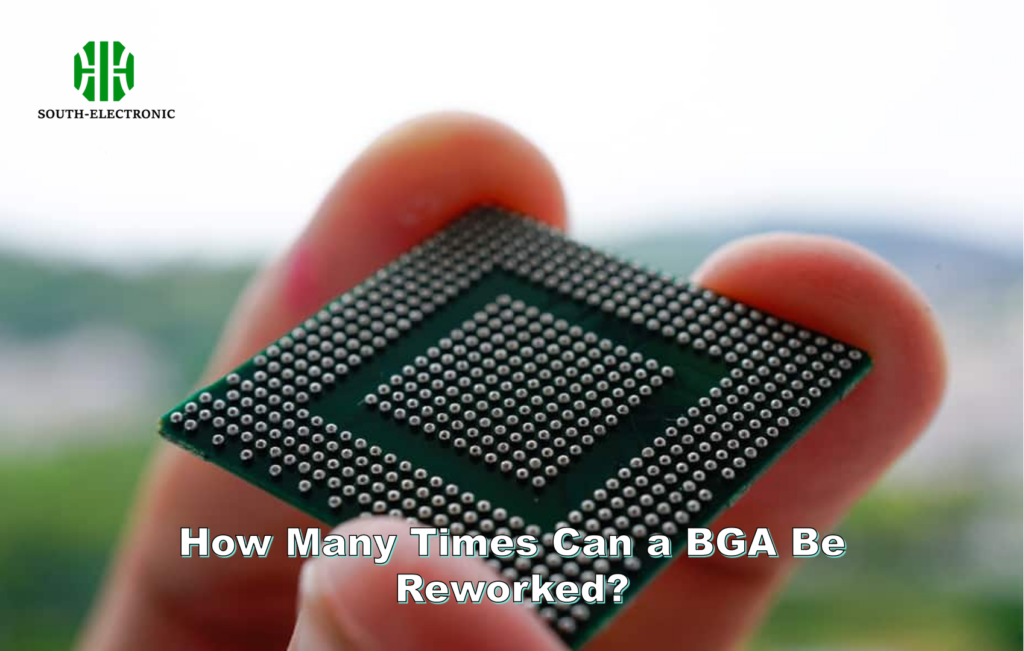
Common BGA Rework Mistakes and How to Avoid Them
When reworking BGAs, several common errors can occur. Below are the most common issues and how to prevent them:
1. Uneven Heating
- Mistake: Applying uneven heat during removal or reflow can warp the PCB or damage the BGA.
- Solution: Always use a preheating station and evenly distribute heat across the BGA.
2. Insufficient Flux
- Mistake: Not using enough flux can lead to poor solder flow, causing weak joints.
- Solution: Always apply a sufficient amount of no-clean flux to ensure proper solder reflow.
Doing a BGA rework is a precise job that you have to pay attention to, have the right tools, and know how to do it right. If you follow the steps I outline in this guide—site preparation, BGA removal, cleaning, reballing, and re-soldering—you’ll be able to do BGA rework with confidence. Just make sure you don’t make the common mistakes like not heating it evenly or not using enough flux, and always inspect your work after reflow.