LED PCB Supplier
South-Electronic
At South-Electronic, we specialize in providing high-quality LED PCBs that deliver bright, consistent lighting and superior performance, helping your lighting projects shine brighter and last longer.
Experience the Best with Our LED PCB
Welcome to the world of South-Electronic, your reliable source for LED PCB designed to optimize light efficiency and lifespan.
Our PCB can meet your custom lighting needs, from commercial applications to state-of-the-art lighting systems.
Team up with us to light up your industry.
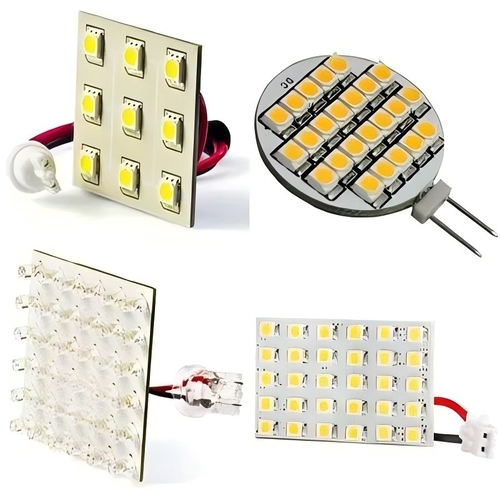
General Lighting LED PCB
Made for lighting up homes and businesses. These circuit boards work with all kinds of light fixtures to give you good light all the time.
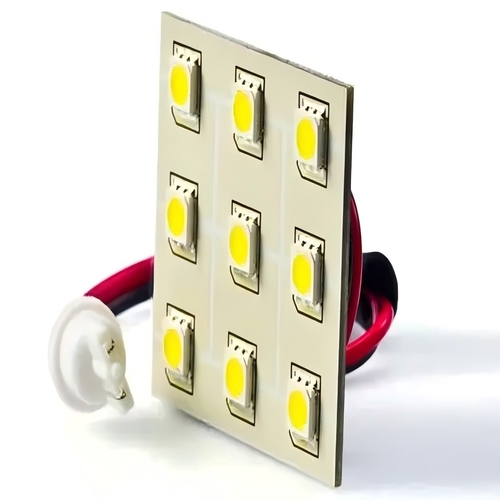
High-Power LED PCB
Designed to handle the high currents required by high power LEDs. These PCB are ideal for industrial and high intensity lamps.
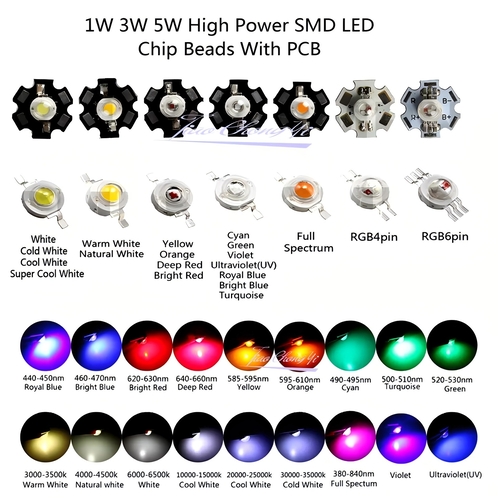
UV LED PCB
Made for UV. The PCB is used for medical, disinfection and treatment. UV LED requires special materials and technology to work properly and last a long time.

Automotive LED PCB
Made for cars. These circuit boards have to be really tough and work all the time, even when the car is really hot or really cold.
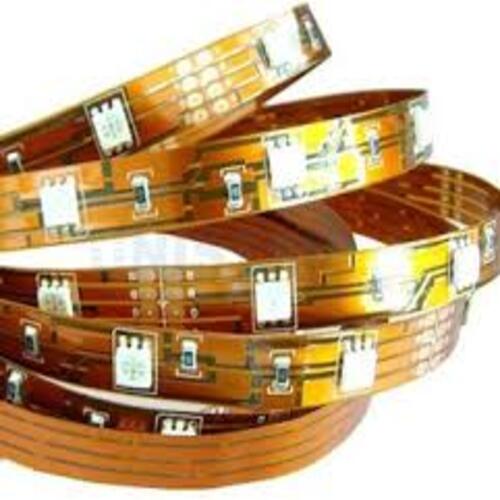
Flexible LED PCB
They are flexible so you can use them in a variety of shapes. You can put the LED FPC in any shapes.
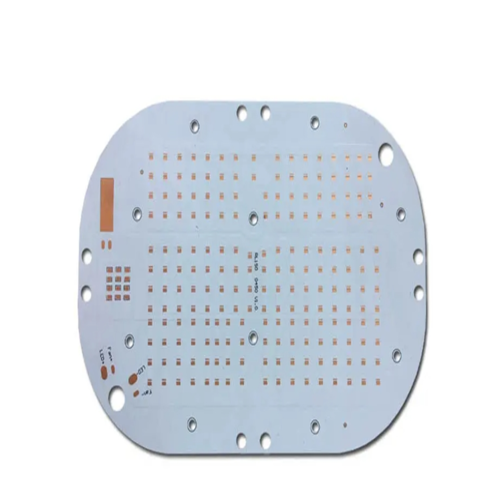
Backlight LED PCB
The PCB is mainly used for backlighting in consumer electronics. It's designed to distribute light evenly and use little energy.
Why Choose South-Electronic?
Choose South-Electronic and you’re working with experts in making high-quality LED PCB for all kinds of lights.
Our team of experts, with years of industry experience, delivers top-of-the-line PCB at prices that can’t be beat. We’re committed to providing you with exceptional service from start to finish, making sure you’re happy every step of the way.
-
Lifetime Support
Your success is our priority.
When you choose our LED PCB, you’re not just getting a product—you’re getting lifetime support. We’ll be here whenever you need help, guiding you every step of the way, long after your purchase. -
Quality Assurance with Extended Warranty
Your peace of mind matters to us.
That’s why we guarantee the highest quality in every LED PCB you order from us, backed by a five-year warranty. If anything goes wrong during that time, you can count on us to fix it for free, ensuring your projects stay on track. -
Quick Response and Delivery
Your time is valuable, and we respect that.
We promise to process your order swiftly and provide optimized logistics solutions so you can expect your projects to be completed on time without sacrificing quality or speed. -
Global Service Network
Your location shouldn’t limit your access to quality products.
No matter where you are, our global supply chain and service network are here to support you. With major markets in Europe and America, you can easily access our products and services wherever you are. -
Flexible Order Quantities
Your project is our priority, no matter the size.
Whether you need 1pc samples or a mass rproduction, we offer the flexibility to meet your specific requirements. With us, you get truly flexible ordering that adapts to your needs.
Related Project We had Done
Customer Reviews
engineer
thank you, guys, the boards are really good, i am really happy to receive my boards, the components are perfect!
Operation Manager
South-Electronic is my first PCBA supplier in China. The service and quality are excellent, and the after-sales support is also very impressive. Good Job!
Common Questions
Most Popular Questions
LED PCB, or Light Emitting Diode Printed Circuit Board, is a specialized PCB used to operate and manage LED lighting solutions. It provides electrical connections and mechanical support to the LED components, ensuring efficient heat dissipation and reliable performance.
The most common material used in LED PCB is ALU, known for its excellent heat conductivity and durability. Other materials like copper and FR4 are also used depending on the specific requirements of the application.
UV LED PCB is used for applications requiring ultraviolet light, such as sterilization, curing, and medical analysis. Benefits include high energy efficiency, long lifespan, and the ability to operate at lower temperatures compared to traditional UV solutions.
The lifespan of an LED PCB can vary based on the quality of materials and the operational environment, but typically, LED PCBs can last between 25,000 to 100,000 hours with proper design and thermal management.
Yes, LED PCB i considered environmentally friendly due to their energy efficiency and the absence of toxic materials like mercury, which are often found in other types of lighting technologies.
At South-Electronic, we insisit to a strict quality control process that includes automated inspections and rigorous testing. We are committed to using high-quality materials and advanced manufacturing techniques to ensure that each LED PCB meets the highest standards.
We provide lifetime after-sales support, including technical assistance and maintenance services. Our extended 5 years warranty covers free repairs for any issues that arise during the warranty period, giving you peace of mind for the long term.
Send us a message
The more detailed you fill out, the faster we can move to the next step.
The Complete Guide For LED PCB
Content
Chapter 1
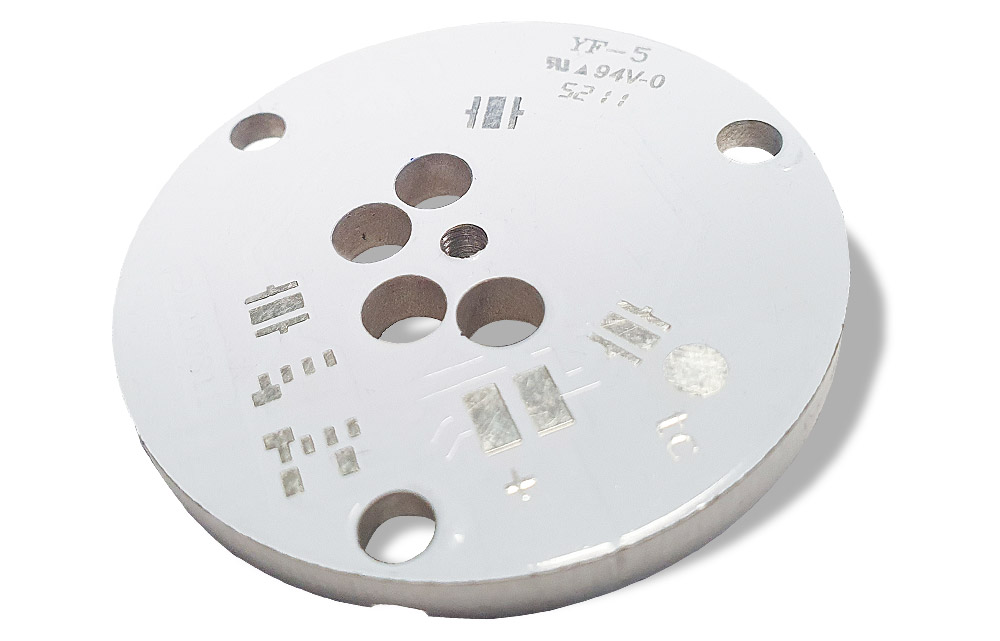
Introduction For LED PCB
Overview of LED PCB and Its Applications in Various Industries
LED PCB, or Light Emitting Diode Printed Circuit Board, is specialized PCB support LEDs, known for its efficiency and longevity, across a diverse range of applications. From automotive to medical devices, LED PCB is crucial for effective thermal management, ensuring optimal performance and extended lifespan of LED.
LED PCB is critical to improving performance and functionality in industries like automotive, consumer electronics, medical devices, and industrial lightings. LED PCB is essential in automotive applications, where it illuminate everything from headlights to dashboard backlights. It also enhance the usability and aesthetics of consumer electronics like smartphones and televisions with superior backlighting. In the medical field, it is used in diagnostic and treatment tools, highlighting their reliability and versatility.
The Evolution of LED Technology and Its Integration with PCB
From simple indicator lights to complex lighting systems: The journey of LED technology began in the early 20th century and reached a major milestone in the 1960s when the first practical LED was developed. Since then, LED had evolved from basic indicator lights to sophisticated components that drive major lighting applications across multiple industries.
Adapting to the Needs: The Rise of Metal-Core PCB
As LED applications become more widespread, the need for advanced thermal management solutions has driven innovation in Metal Core PCB (MCPCB), especially aluminum backplanes. Specialized PCB is designed to efficiently dissipate heat, protecting LED from thermal failure and improving their performance.
More Than Function: Making Your PCB Looks Nicer with LED
In today’s world, using LED on your PCB is about more than just its lighting function. It’s about making them look nice. That’s especially true when it comes to consumer and architectural lighting. The LED PCB we use today are designed to not only perform well and last a long time, but also looks great. They’re designed to make the end products look as good as they work.
Driving Innovation Across Industries
This ongoing integration has sparked a ton of cool innovations in the field:
- Material Advancements:
Using conductive materials like aluminum and copper in the PCB core allows it to dissipate heat better.
- Design Innovations:
Modern LED PCB has special design that can make the light brighter and the heat dissipate faster through reflective coatings and built-in heat sinks, etc.
- Technological Integration:
Connecting LED PCB to smart technology allows it to control lighting systems that can change based on events happening around it or people’s behavior, making them smarter and more responsive.
As we continue to explore the uses of LED PCB, from different types and materials to manufacturing methods, we will find all sorts of new ways to use them. This will enable many different industries to grow further.
Chapter 2
Types of LED PCB
LED PCB is essential components in a wide range of applications, each tailored to meet specific operational demands and environmental conditions. Let’s explore the different types of LED PCB designed to cater to various needs, from general lighting to specialized industrial applications.
General Lighting LED PCB
It is perfect for residential, commercial and industrial use. The PCB is made of aluminum so it dissipates heat very well. This means your LEDs will work well and last a long time. Whether you light up your office with ceiling lights, illuminate the street with lamps, or add ambiance to your home with wall lights, the PCB is reliable and can provide you with the light you need.
High-Power LED PCB
High-Power LED PCB is designed to handle big electrical loads and a lot of heat, which makes they’re perfect for your high-intensity lighting needs. They have advanced thermal management systems, like thicker copper layers and built-in heat sinks, to keep your setups cool and working well, even in tough conditions. The LED PCB is great for powering floodlights, stadium lighting, or any industrial applications that need a lot of light.
UV LED PCB
UV LED PCB is PCB specifically designed to work with ultraviolet light emitting diodes (UV LEDs). These PCBs are often used in applications that require UV light, such as curing inks and coatings, medical phototherapy, sterilization, and UV exposure for chemical processes.
UV LED PCB is often made of materials that can withstand high-intensity UV light without degradation, such as certain types of fiberglass or ceramic substrates. They may also have enhanced cooling capabilities to manage the heat generated by UV LEDs, which is critical to maintaining the efficiency and life of the LEDs. The PCB is valued for its energy efficiency, long service life, and compact design, which makes it suitable for a variety of industrial and medical applications.
Automotive LED PCB
Automotive LED PCB is printed circuit board designed specifically for automotive lighting applications, such as headlights, taillights, interior lights, and dashboard indicators.
The PCB is typically made of materials that can withstand the harsh conditions of the automotive environment, including vibration, temperature fluctuations, and exposure to moisture. Aluminum-based PCB is widely used due to its excellent heat dissipation properties, which is essential to maintaining the performance and life of LEDs in the high-heat environment of the vehicle.
Automotive LED PCB is carefully designed for high reliability and often feature advanced circuit designs to effectively manage power and ensure consistent light output. They play a key role in enhancing the safety and aesthetics of modern vehicles, providing brighter, more energy-efficient lighting solutions compared to traditional automotive lighting technologies.
Flexible LED PCB
Flexible LED PCB is innovative PCB made from materials such as polyimide or polyester film that can bend and conform to unconventional shapes. This flexibility makes it ideal for a variety of applications such as wearable technology, automotive interior lighting, and curved displays. The PCB is extremely thin and light, which is critical for compact and weight-sensitive applications. Despite its flexibility, it’s durable and can withstand vibration and mechanical stress, making it ideal for harsh environments. In addition, it is designed to dissipate heat efficiently, ensuring the lifespan and performance of the LED.
Backlight LED PCB
Backlight LED PCB is a critical component in consumer electronics, making sure that devices like smartphones, televisions, laptops, and more have even light distribution behind their screens. The PCB is carefully designed to be thin and efficient, using multiple LEDs to maintain consistent brightness across large areas. Perfect for improving the visibility and clarity of displays, our Backlight LED PCB provide the performance and reliability you need to enhance user experience and device functionality.
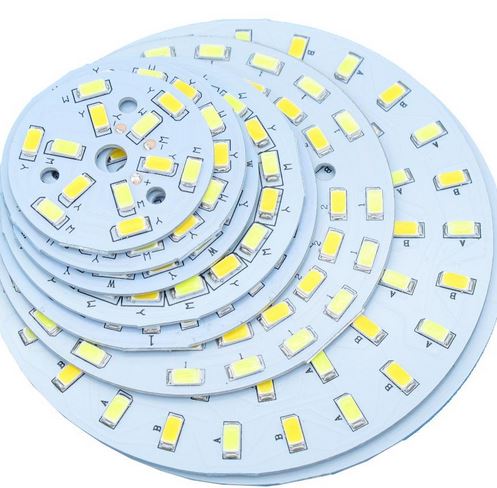
Chapter 3
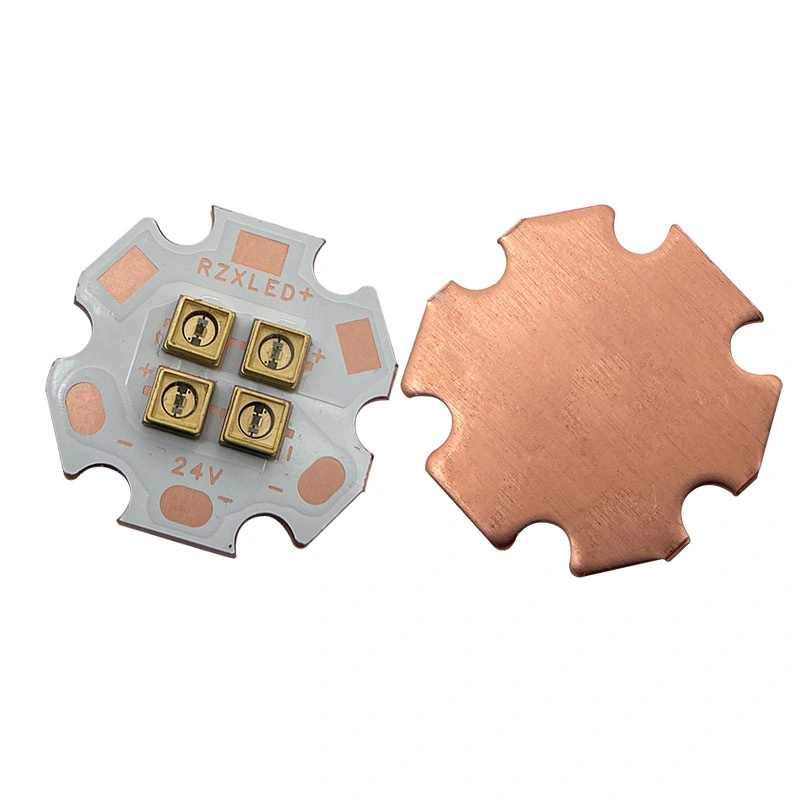
Materials Used in LED PCB
The material you choose for manufacturing your LED PCB is crucial to the overall performance of your boards. Factors like heat dissipation, durability, and electrical conductivity are heavily influenced by this decision. Aluminum, copper, and their alloys are some of the most commonly used materials in LED PCB because of their excellent properties that are perfectly suited for LED applications. Whether you want to improve the longevity, efficiency, or functionality of your LED PCB, understanding the advantages of each material will help you make the best choices for your specific needs.
Aluminum
Aluminum is the go-to material for LED PCB manufacturing. It’s cheap and does a great job of managing heat. Aluminum PCBs have a thin layer of thermally conductive dielectric material that bridges the gap between the IC components and the metal backing plate, which makes your device work better.
Benefits:
- Thermal Conductivity:
Aluminum is really good at getting rid of heat from your LEDs. This not only makes them work better, but it also makes them last longer.
- Durability: Aluminum is really strong and tough, so it doesn’t break or warp under normal conditions. That means you can use it for all kinds of lighting projects and know they’ll last.
- Lightweight:
Aluminum is lightweight, which is great for things like portable or wearable devices. It makes it easy to handle and fit into different designs without losing quality or function.
Copper
Copper is the way to go for LED PCB, especially if you need really good thermal conductivity. Copper PCB is better at pulling heat away from LED components than aluminum, which is important if you want your high-power LEDs to keep working right.
Benefits:
- Superior Thermal Conductivity: Copper has almost double the thermal conductivity of aluminum, making it perfect for applications that generate a lot of heat. This enhanced ability to dissipate heat ensures your high-power LEDs run smoothly and reliably.
- High Electrical Conductivity:
Known for its excellent electrical conductivity, copper is especially beneficial for high-frequency applications or those where minimal signal loss is critical. This guarantees optimal performance when precision is everything.
- Flexibility: Copper’s adaptability allows it to be used in both rigid and flexible PCB designs, offering you a wide range of possibilities in PCB construction. Whether your project requires the robustness of a rigid PCB or the adaptability of a flexible one, copper is an excellent material choice.
Copper-Aluminum Alloys
When you need to find the right balance between cost, weight, and performance for your LED PCB, copper and aluminum alloys are often the materials of choice. These alloys combine the best features of both metals, providing a moderate level of thermal and electrical conductivity that is ideal for a wide range of LED applications.
Benefits:
- Balanced Conductivity: Compared to aluminum alone, these alloys offer improved thermal performance. They are also more cost-effective than pure copper, giving you a budget-friendly option that doesn’t sacrifice efficiency and heat management.
- Versatility: Customize these alloys to fit your specific project needs. The adjustable copper-to-aluminum ratio lets you tailor the thermal and electrical properties to make sure your LED PCB perform exactly as you need them to in a variety of environments.
- Durability and Lightweight: Copper-aluminum alloys are the perfect blend of toughness and lightness, which makes them great for applications where you need something that’s both strong and easy to move around. That’s why they’re so good for things like portable devices and other things where you don’t want them to be too heavy.
FR4
FR4 is a staple material in traditional PCB manufacturing and is also applicable in certain LED scenarios where intense heat dissipation is not a primary concern. This composite material, made of woven fiberglass cloth and an epoxy resin binder, offers a flame-resistant, self-extinguishing feature that ensures safety across various applications.
Benefits:
- Cost-Effectiveness:
FR4 is generally less expensive than metal-based PCB, making it an excellent choice for projects where budget constraints are a key consideration.
- Insulation and Rigidity:
It provides superb electrical insulation and rigidity, making it suitable for LED applications that do not generate high heat, ensuring stable and reliable performance.
- Versatility:
FR4 is a great choice for LED lighting and a wide range of other electronic applications because it has good electrical properties.
Each material has its own advantages for different LED PCB applications. By understanding what you need for your project—like how much heat and electricity you need, what the environment is like, and how much money you have—you can pick the best material for your LED PCB. This will make your lighting solutions work better and last longer.
Chapter 4
Design Considerations for LED PCB
When you’re designing LED PCB, you’ve got to plan carefully and optimize everything to meet your performance expectations and reliability standards. In this article, we’ll look at some of the key design considerations and common challenges you’ll face when you’re creating LED lighting solutions that work.
Layout
To make your LED PCB looks nice, distribute light evenly, and not wasted electricity, you need to plan your layout carefully.
Key Considerations:
- Spacing:Make sure you leave enough space between your LEDs so they don’t get too hot and so the light looks even across the PCB.
- Path of Electricity:Make the electricity flow through your PCB in the most efficient way possible so you don’t lose voltage and waste energy.
- Placement:even Layout, concentrated layout, combined layout.
Even layout is to achieve uniform light distribution, LEDs can be arranged in a regular grid or linear pattern. This layout is suitable for general lighting and backlighting applications.
Concentrated layout is to achieve a stronger beam and higher light intensity by concentrating the LEDs in a smaller area. This layout is suitable for applications such as flashlights and spotlights.
Combined layout is to combine two or more of the above layout methods to meet specific lighting needs, such as stage lighting or multi-functional lamps.
Thermal Management
Description: Effective thermal management is critical to LED PCB design because LEDs generate heat, if not managed properly, can affect the performance and life of the LEDs.
Key Considerations:
- Material Choice:
Choose materials like aluminum or copper for their high thermal conductivity, which helps dissipate heat quickly.
- Thermal Vias:
Incorporate thermal vias to significantly improve heat transfer from the LEDs to the heat sink.
- Heat Sinks and Cooling:
Consider adding heat sinks and exploring active cooling options such as fans, especially important in high-power LED applications.
Component Placement
Description: Strategic placement of components on an LED PCB is crucial not only for aesthetic purposes but also for functionality and heat managemen
Key Considerations:
- Balanced Placement: Distribute components evenly on the PCB to balance thermal loads and improve stability.
- Accessibility: Arrange components to make assembly, maintenance, and possible future upgrades or repairs easier.
- Integration of Drivers and Controllers: Place drivers and controllers near their respective LEDs to minimize energy losses and reduce interference.
Common Design Challenges and Solutions
1.Heat Accumulation
Use materials with higher thermal conductivity, implement thermal vias, and design effective cooling mechanisms like heat sinks or fans to prevent LED failure.
2.Electrical Noise and Interference
Ground properly, shield, and route high-frequency signals carefully to avoid affecting LED performance.
3.Power Distribution
Design power paths with minimal resistance and ensure voltage regulators and capacitors are properly sized and placed to provide a stable power supply.
4.Physical Durability
In harsh environments, increase durability by using tough materials and PCB design techniques such as through-hole components and conformal coatings.
By carefully considering these design aspects and addressing potential challenges, you can greatly improve the performance, reliability, and usefulness of your LED PCBs in a variety of lighting applications, ensuring they meet the stringent requirements of modern lighting systems.
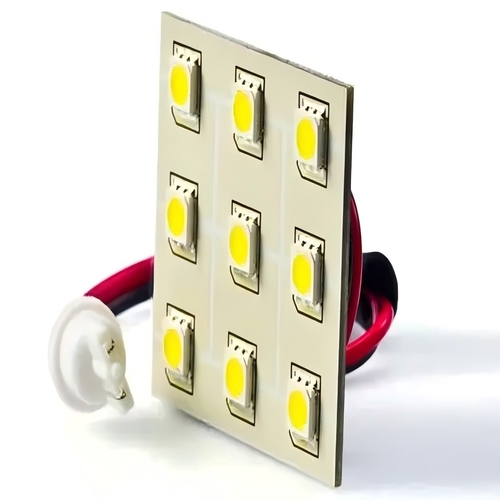
Chapter 5

Manufacturing Processes for LED PCB
The manufacturing process of LED PCBs is simple compared to other types PCB,but still process that requires precision and expertise to make sure each board meets your exact specifications for performance and durability. Here’s a step-by-step guide to understanding how is LED PCB made, from imaterial choose to final shipment.
Step-by-Step Manufacturing Process
Material Selection
- Thermal Management: LED PCB always use materials with high thermal conductivity, such as aluminum or copper substrates, to help dissipate heat generated by LEDs.
PCB Fabrication
- Substrate Preparation: The chosen substrate material is prepared for the deposition of circuit layers.
- Circuit Pattern Transfer: Apply a layer of photoresist, expose it to a pattern using ultraviolet light, and develop the pattern to prepare for etching.
- Etching: Remove unwanted metal to create the circuit traces.
- Layer Stacking: For multilayer PCB, stack and press layers together with prepreg and core materials.
Surface Finish
- Applying Surface Finish: Apply a surface finish to protect the copper traces and ensure good solderability. Common finishes include ENIG (Electroless Nickel Immersion Gold) and HASL (Hot Air Solder Leveling).
Components Mounting
- Solder Paste Stenciling: Apply solder paste to the areas where components will be placed.
- Pick and Place: Automatically place LED components and other electronics on the PCB.
- Reflow Soldering: Pass the PCB through a reflow oven where the solder paste melts and solidifies, creating electrical connections.
Inspection and Testing
- Automated Optical Inspection: (AOI): Inspect the PCB for any soldering or placement defects using optical systems.
- Electrical Testing: Perform functionality tests to ensure the circuit performs as designed.
- Thermal Testing:Check thermal performance to ensure heat is managed effectively.
Assembly and Finishing:
- Conformal Coating: Apply a protective coating to protect the LED and other components from environmental factors like moisture and dust.
- Final Assembly: Assemble additional mechanical or optical components, such as lenses or heat sinks.
Quality Control
- Visual Inspection: Manually check the PCB for any obvious defects.
- Performance Testing: Test the LED PCB under operational conditions to ensure it meets the required specifications.
Each step is critical for ensuring the functionality and reliability of LED PCB, particularly because of the heat and power management needs inherent to LED applications. The manufacturing process may vary slightly depending on the specific type of LED PCB, such as rigid, flexible, or hybrid designs.
Chapter 6
Applications of LED PCB
LED PCB has become an integral component in various fields due to their efficiency, longevity and versatility. Its applications range from everyday lighting solutions to specialized industrial uses, highlighting their wide adaptability and importance.
This section explores the applications in depth and includes case studies illustrating the innovative uses of LED PCB in different projects.CBs in different projects.
General Lighting
- Residential Lighting: LED bulbs, spotlights, and ambient lighting in houses.
- Commercial Lighting: Office lighting, shop lighting, and signage that require long operational hours and consistent performance.
- Public Lighting: Street lamps and public area lighting that benefit from LED’s durability and low maintenance requirements.
Automotive Lighting
- Headlights: More automakers are adopting LED headlights for their superior brightness and energy efficiency compared to traditional bulbs.
- Interior Lighting: Dashboard lighting, cabin lights, and display backlighting that enhance functionality and driver experience.
Industrial Applications
- Machinery Lighting: Providing bright, directional light for industrial machines and workstations.
- Safety Signaling: LED indicators and emergency lighting systems that require high reliability.
Medical Devices
- Surgical Lighting: High-intensity, focused lights used in operating rooms.
- Therapeutic Devices: Devices using UV LEDs for skin treatments and sterilization processes.
Portable Electronics
- Smartphones and Tablets: Backlighting for screens and buttons.
- Wearable Devices: Fitness trackers and smartwatches that use LEDs for displays and indicators.
Case Study
1: Smart City Lighting Project
Project Overview: A major city implemented a smart lighting system using LED PCBs across its public infrastructure to reduce energy consumption and maintenance costs.
Technology Used: LED PCBs equipped with sensors and connected to an IoT network that allowed for dynamic control based on environmental conditions.
Outcome: The project resulted in a 40% reduction in energy usage and significantly lower maintenance costs due to the longevity of LEDs.
2: Automotive LED Retrofit
Project Overview: A leading automotive manufacturer retrofitted its vehicles with LED lighting to enhance nighttime visibility and reduce energy usage.
Technology Used: High-power LED PCBs designed for automotive headlights that provided brighter and more efficient lighting than traditional halogen lamps.
Outcome: Improved driver visibility and reduced load on the vehicle’s electrical system, enhancing battery life and reducing emissions.
3: High-Efficiency Industrial Lighting
Project Overview: An industrial facility upgraded its lighting systems to LED technology to improve visibility and reduce operational costs.
Technology Used: Robust LED PCBs with high lumens-per-watt efficiency, designed to withstand the rigorous conditions of industrial environments.
Outcome: Enhanced lighting quality improved worker safety and productivity, while the energy-efficient LEDs significantly cut down on electricity costs.
These case studies show the versatility and effectiveness of LED PCBs in a variety of settings, highlighting their impact on improving performance, safety, and efficiency across multiple industries. By implementing LED technology, these projects not only achieve immediate benefits but also contribute to long-term sustainability and operational excellence.

Chapter 7
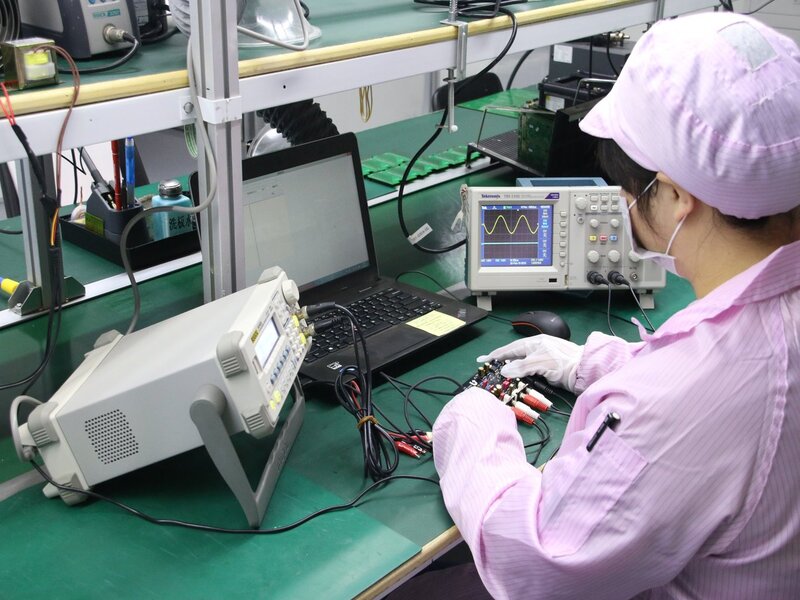
What is UV LED?Advantages and Disadvantages
UV LED is diode that emit ultraviolet light.
Advantages of UV LED:
Longer Lifespan: UV LED can last up to 10,000 hours or more, reducing replacement costs.
Compact Size: Its small size allows for more compact designs in devices.
Instant On/Off: Unlike traditional bulbs, UV LEDs do not require warm-up time.
Environmentally Friendly: They do not contain mercury, making them safer and more eco-friendly.
Disadvantages of UV LED
Initial Cost: Higher upfront costs compared to traditional UV sources.
Thermal Management: UV LED generates a lot of heat and require an efficient cooling system.
Limited Wavelength Options: The availability of specific wavelengths can be limited, affecting their application in certain fields.
Intensity Degradation:UV output can decrease over time, impacting performance.
Applications of UV LED
- Sterilization and Disinfection:UV LED is used in water purification, air sterilization, and surface disinfection.
- Medical Applications: It is use in phototherapy and dental procedures.
Industrial Curing: In curing inks, coatings, and adhesives in manufacturing, for example 3D Printing Industrial.
Chapter 8
Choosing the Right LED PCB for Your Needs
Selecting the right LED PCB for a specific application is critical to ensuring optimal performance, efficiency and cost-effectiveness. This section outlines the key criteria to consider when selecting an LED PCB and provides advice on sourcing from manufacturers and ensuring compatibility with existing systems.
Standard for selecting suitable LED PCB
Thermal Management Requirements
- Consideration: Assess the heat output of the LED application. High-power LEDs or densely packed arrays will require PCBs with excellent thermal conductivity and heat dissipation features such as aluminum or copper substrates.
- Guideline: For applications with high thermal demands, opt for metal-core PCBs (MCPCBs), especially aluminum-backed or copper-backed PCBs.
Electrical Requirements
- Considerations: Evaluate the voltage and current requirements of the LEDs. The PCB should be able to handle the electrical load without performance degradation.
- Guideline: Ensure the PCB layout, conductive layer thickness, and trace width are appropriate for the current level to prevent voltage drops and overheating.
Environmental Conditions
- Consideration: Consider environmental factors, such as extreme temperatures, humidity, and exposure to chemicals or UV rays, which can affect the performance and lifespan of a PCB.
- Guideline: For harsh environments, consider using PCB with additional protective coatings, or choose materials known for their durability and resistance to environmental stress.
Size and Shape Limitations
- Consideration: The physical space available for the PCB in your product design will determine the size and shape of the PCB.
- Guideline: For applications that require unique shapes or bends, use a flexible LED PCB. Ensure the layout is optimized to fit the available space while maintaining functionality.
Cost Considerations
- Consideration: Budget constraints influence the choice of materials and technologies used in PCB.
- Guideline: Balance cost and performance requirements, considering long-term savings from reduced maintenance and energy consumption versus initial investment.
Sourcing and Compatibility
Choosing a Manufacturer
- Advice: Choose a manufacturer that has experience with LED PCB, especially one that has a strong quality assurance process. Look for certifications and standards compliance, such as ISO certification, to ensure quality and reliability.
Ensuring Compatibility
- Advice: rovide the manufacturer with detailed specifications of the existing system, including mechanical and electrical interfaces. Request prototypes to test compatibility before full production.
- Consideration: Compatibility with the existing system involves not only physical assembly but also electrical integration. Ensure the PCB operates within the same voltage and current range as other system components.
Long-term Supplier Relationships
- Advice: Building a good relationship with your PCB supplier can result in better service, more favorable terms, and faster responses to custom requests. Consider suppliers that offer additional services, such as on-time delivery, inventory management, and end-to-end customer support.
Evaluating Prototypes
- Advice: Always order prototypes before committing to volume production. This will allow you to test the LED PCB under realistic conditions and make any necessary adjustments based on performance.
By carefully considering these criteria and following strategic sourcing practices, you can ensure that you select an LED PCB that is correct for your specific needs, thereby maximizing the performance and longevity of your LED application.
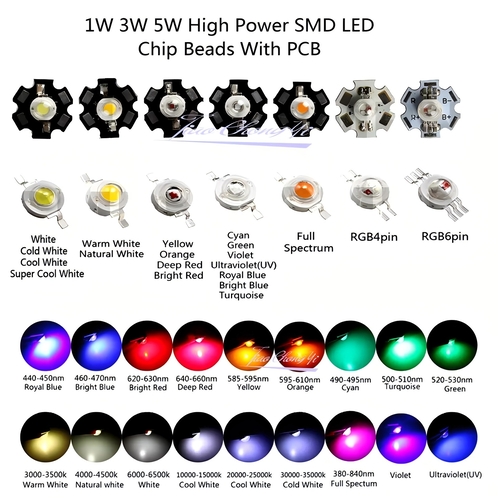
Chapter 9

Maintenance and Troubleshooting for LED PCB
Proper maintenance and effective troubleshooting are essential to maximizing the life and performance of your LED PCB. The following is practical tips and strategies for maintaining your LED PCB, as well as a guide to diagnosing and resolving common problems that may arise during use.
Maintenance Tips for LED PCBs
Regular Cleaning
- Tip: Dust and debris can accumulate on the PCB, which can block heat dissipation and cause overheating. Clean the PCB surface regularly with a soft brush or compressed air. For more stubborn dirt, use isopropyl alcohol and a soft cloth.
- Frequency: Clean every three to six months, depending on the environment in which the LED PCB is used.
Check for Loose Connections
- Tip: Loose connections can lead to increased resistance and potential failure points. Check and secure all connections and terminals regularly.
- Frequency: Check connections during routine maintenance checks or every time you perform cleaning.
Inspect for Physical Damage
- Tip: Check for signs of wear, such as cracked solder joints, which can be caused by thermal cycling. Also, check the LED itself for any physical damage. themselves.
- Frequency: Perform a physical inspection annually or more frequently if the PCB is used in a high-vibration environment.
Monitor Heat Dissipation
- Tip: Make sure any radiator or cooling device is functioning properly. A clogged or dirty radiator can significantly reduce cooling efficiency.
- Frequency: Checking the thermal management system is part of a regular maintenance schedule.
Performance Testing
- Tip: Use a multimeter to check voltage and current at various points in the circuit to ensure everything is operating within specified limits.
- Frequency: Perform electrical testing semi-annually or after any major system changes or repairs.
Troubleshooting Common Issues
Dimming or Flickering LEDs
- Cause: This may be caused by a power supply problem, a faulty component (such as a capacitor), or a bad connection.
- Solution: Check and replace the defective power supply or component. Make sure all connections are secure and free of corrosion.
Overheating
- Cause: Overheating can be caused by inadequate thermal management, excessive current, or environmental factors.
- Solution: Confirm that current settings are within safe ranges. Clean heat sink or upgrade heat sink as needed to improve thermal management. If ambient temperature is too high, consider environmental control solutions.
LED Is Not On
- Cause: This can be caused by a failed LED, a broken (open) circuit, or a power supply problem.
- Solution: Test individual LED using a multimeter set to diode mode. Check for breaks or bad soldering in the circuit. Make sure the power supply is functioning properly and providing the correct voltage.
Uneven Lighting
- Cause: Uneven lighting can be caused by inconsistent LED bins, changes in current distribution, or LED aging.
- Solution: Replace old LEDs with new LEDs from the same bin to ensure uniformity. Check and adjust current drivers to equalize power distribution on the PCB.
Color Shift in LEDs
- Cause: olor change can be caused by aging or overheating.
- Solution: If overheating is the cause, enhance the cooling system. If due to aging, consider replacing older LEDs to maintain color consistency.
By following these maintenance tips and using troubleshooting guidelines, users can significantly improve the reliability and lifespan of their LED PCB, ensuring they continue to operate efficiently in their applications.
Chapter 10
Future Trends and Innovations in LED PCB Technology
The LED PCB industry is poised for significant advancements as innovations in materials, manufacturing processes, and integration with emerging technologies such as the Internet of Things (IoT) and smart technology continue. Below, we explore these future trends and consider how they will shape the next generation of LED PCB.
New Materials and Manufacturing Techniques
Advanced Thermal Management Materials
- Insight: As the density of LEDs on PCB increases, thermal management becomes more critical. Future developments include the use of new materials with higher thermal conductivity, such as graphene and improved ceramic-based substrates, which can greatly enhance the ability to dissipate heat.
- Impact: Enhanced thermal management will increase the lifetime and reliability of LEDs, enabling smaller, more powerful devices.
Eco-Friendly Materials
- Insight: There is a growing trend towards sustainability in the electronics manufacturing industry. Biodegradable PCB substrates and lead-free solders are being developed to reduce environmental impact.
- Impact: These materials will help reduce the ecological footprint of LED PCB and comply with global regulations and consumer preferences for more environmentally friendly products.
Additive Manufacturing (3D Printing)
- Insight: 3D printing of PCB is emerging as a technique that allows for rapid prototyping and complex multi-layer structures without the need for extensive tooling or high setup costs.
- Impact: This could lead to more customized LED PCB designs and quicker iteration cycles in the design process, especially for niche applications.
Integration with IoT and Smart Technology
Smart Lighting Systems
- Insight: LED PCB is increasingly being integrated with sensors and wireless communication technologies, enabling them to be part of IoT-enabled smart lighting systems. These systems can adjust lighting based on environmental conditions, presence detection, or user preferences.
- Impact: This integration enhances energy efficiency and user experience, providing personalized lighting environments and contributing to smart home and smart city ecosystems.
Data-Driven Functionality
- Insight: In addition to lighting, LED PCB can be equipped with sensors to collect data about the environment in which they operate, such as temperature, humidity, and light levels. This data can be used for diagnostics and predictive maintenance.
- Impact: Enhanced data collection capabilities will make LED systems smarter, reducing maintenance costs and downtime by predicting conditions before failures occur.
Interconnectivity and Control
- Insight: Future LED PCB is likely to have enhanced connectivity using protocols such as Zigbee, Bluetooth, and Wi-Fi. This will allow for seamless integration with other smart devices and systems.
- Impact: Enhanced connectivity will enable centralized control and automation of lighting systems, further improving convenience and energy efficiency.
Adaptive and Responsive Lighting
Dynamic Adjustments
- Insight: Future LED PCB is expected to support dynamic adjustments in real-time, responding to multimedia content, audio signals, or interactive installations.
- Impact: This will open new avenues in entertainment, advertising, and ambient environment creation, providing immersive and adaptive user experiences.
Human-Centric Lighting
- Insight: There is growing interest in developing lighting solutions that can mimic natural light patterns to align with human circadian rhythms, i.e. human centric lighting.
- Impact: LED PCB designed for this purpose will help improve health and productivity, especially in environments such as offices and hospitals.
The future of LED PCB technology is full of potential, characterized by technological integration and innovation. As new materials and smarter technologies continue to develop, LED PCB will play a key role in lighting solutions and the way we interact with our environment, making them more responsive, efficient, and more aligned with human needs.
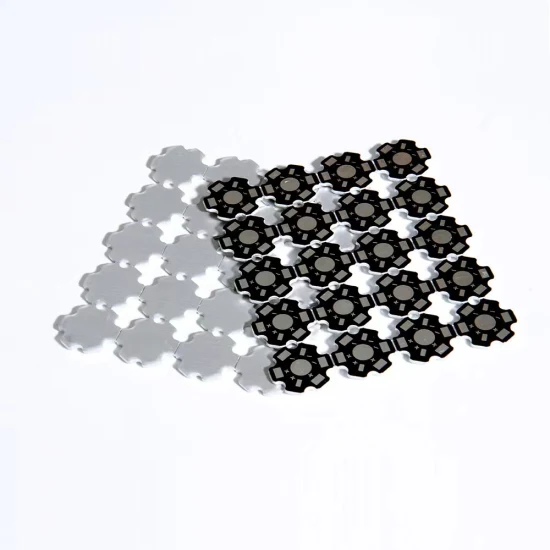
Get in touch
Where Are We?
Industrial Park, No. 438 Donghuan Road, No. 438, Shajing Donghuan Road, Bao'an District, Shenzhen, Guangdong, China
Floor 4, Zhihui Creative Building, No.2005 Xihuan Road, Shajing, Baoan District, Shenzhen, China
ROOM A1-13,FLOOR 3,YEE LIM INDUSTRIAL CENTRE 2-28 KWAI LOK STREET, KWAI CHUNG HK
service@southelectronicpcb.com
Phone : +86 400 878 3488
Send us a message
The more detailed you fill out, the faster we can move to the next step.
