Multilayer PCB Supplier
South-Electronic
Choose South-Electronic for unparalleled quality, reliability, and exceptional value in your PCB solutions. Experience the difference with our comprehensive multilayer PCB service—from design to delivery, we ensure precision, durability, and compliance with the toughest industry standards.
Why Choose South-Electronic?
Get the best multilayer PCB solutions with South-Electronic. We customize your PCBs, make sure they’re top quality, get them to you fast, and give you a great price. Ask for a quote now and see how reliable we are.
-
Flexibility in Ordering
Customized to your specific needs, enjoy flexibility with us.
Whether you need a minimum order of just one piece or large-scale production, we offer flexible order quantities to meet your specific project requirements. -
Experienced Team
You benefit from the industry expertise of our professionals with over a decade of experience.
With more than ten years of experience, our dedicated team has deep industry knowledge to provide you with high-quality PCB solutions. -
Strict Quality Control
Every PCB you receive is manufactured to strict quality control standards.
With certifications such as UL, CE, IATF16949, and ISO13485, every PCB we produce undergoes rigorous quality control. -
Fast Turnaround
Save time and keep your project on track.
With our streamlined production process, you’ll enjoy fast delivery without any compromise on quality, helping you meet tight deadlines effortlessly. -
Lifetime Support
Feel confident with lifetime after-sales care.
Even after delivery, you can rely on us for ongoing support throughout the entire lifespan of your product, giving you long-term peace of mind.
Related Project We had Done
Customer Reviews
engineer
thank you, guys, the boards are really good, i am really happy to receive my boards, the components are perfect!
Operation Manager
South-Electronic is my first PCBA supplier in China. The service and quality are excellent, and the after-sales support is also very impressive. Good Job!
Common Questions
Most Popular Questions
Yes, South-Electronic offers fully customized multilayer PCB solutions, tailored to your specific requirements, ensuring the best fit for your applications.
Absolutely! South-Electronic provides prototyping services, allowing you to test and refine your designs before moving to mass production.
South-Electronic offers flexible ordering with a minimum order quantity (MOQ) starting from just one piece, making it ideal for both prototyping and large-scale production.
You can easily place an order by contacting South-Electronic through their website or email. Once your requirements are discussed, they’ll provide you with a quote and guide you through the entire process.
South-Electronic holds certifications like UL, CE, IATF16949, and ISO13485, ensuring that their PCBs meet the highest international quality standards.
Send us a message
The more detailed you fill out, the faster we can move to the next step.
The Complete Guide For Multilayer PCB
Contents
Chapter 1
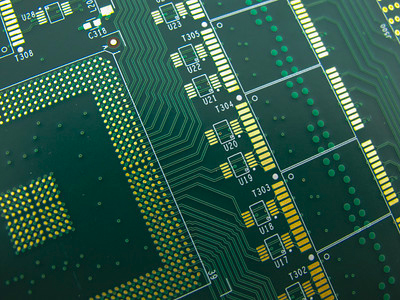
Introduction to Multilayer PCB
What is a Multilayer PCB?
A Multilayer PCB is a printed circuit board that has three or more layers of conductive material (usually copper) separated by insulating layers. These layers are stacked and laminated together, creating a compact, high-density board used for complex electronic circuits. Unlike single-layer or double-layer PCBs, which have limited space for routing, multilayer PCBs allow more intricate circuit designs by offering multiple conductive layers that interconnect through vias (vertical connections between the layers). This results in higher performance, greater functionality, and reduced space requirements in electronic devices.
History and Evolution of Multilayer PCBs
The concept of multilayer PCBs came about in the late 1960s as electronics became more advanced and miniaturization became a priority, particularly in the aerospace and telecommunications industries. Early PCBs only had one or two layers, which limited the complexity of circuits that could be designed. The need for greater circuit density, enhanced performance, and higher reliability led to the development of multilayer PCBs. Over time, innovations in materials, fabrication techniques, and design software have allowed multilayer PCBs to become mainstream in consumer electronics, medical devices, automotive systems, and more. Today, multilayer PCBs can have more than 50 layers in some high-end applications, allowing for incredibly complex and powerful designs.
Importance and Applications in Modern Electronics
Multilayer PCBs have become a cornerstone of modern electronic devices because they can accommodate high-density components and complex circuits in a compact form. Their importance lies in their ability to provide better performance in terms of signal integrity, noise reduction, and electromagnetic interference (EMI) shielding compared to single-layer or double-layer boards. This makes them essential in industries where precision, speed, and reliability are critical.
- Telecommunications: Used in routers, switches, and satellite systems where high-speed data transmission and reliability are crucial.
- Consumer Electronics: Found in smartphones, laptops, and wearables, where compact designs and enhanced functionality are required.
- Automotive: Used in advanced driver assistance systems (ADAS), infotainment, and power control systems that demand durability and performance.
- Medical Devices: Essential for devices like pacemakers, imaging equipment, and diagnostic tools that require high precision and reliability.
- Aerospace and Defense: Multilayer PCBs provide critical support in systems that require ruggedness, reliability, and performance under extreme conditions.
Overall, multilayer PCBs are vital for enabling the advancement of technology across various industries, supporting the growing demand for smaller, faster, and more efficient electronic devices.
Chapter 2
Structure of a Multilayer PCB
Layers in Multilayer PCBs
A multilayer PCB is made up of several layers of materials that work together to form a functional circuit board. The main layers in a multilayer PCB are:
- Copper Layers: These are the conductive layers that carry electrical signals. In a multilayer PCB, there are multiple copper layers stacked on top of each other, separated by insulating layers. These copper layers form the traces that connect various components and allow for signal transmission. The number of copper layers depends on the complexity of the PCB design, and they are typically very thin but highly conductive to ensure efficient signal flow.
- Substrate (Core): The substrate is the foundation of the PCB. It is usually made from materials like FR-4 (a composite material made from woven fiberglass and epoxy resin) or other specialized materials like polyimide for high-temperature applications. The substrate provides mechanical support to the board and acts as an insulating layer between the copper layers.
- Insulation (Dielectric Layers): These layers separate the copper layers and prevent electrical shorts between them. The insulation is usually made of materials like prepreg (pre-impregnated composite fibers) or other types of non-conductive epoxy. This insulating material not only separates the conductive layers but also contributes to the board’s durability and ability to withstand environmental factors like heat, moisture, and vibration.
The layering of copper and insulation continues throughout the PCB, creating a multilayer stackup that allows for complex routing of signals in a compact space.
Explanation of Inner and Outer Layers
In a multilayer PCB, the inner layers and outer layers serve different functions:
- Outer Layers: These are the top and bottom layers of the PCB. The outer layers typically contain the majority of the signal traces that connect to external components through solder pads and vias. They are usually protected by a solder mask that prevents unintentional contact with conductive materials. The outer layers are crucial for component placement, allowing for surface mount devices (SMDs) or through-hole components to be attached during assembly.
- Inner Layers: The inner layers are sandwiched between the outer layers and are primarily used for routing signals, providing power, and grounding. These layers play a critical role in managing signal integrity and power distribution. For example, one or more inner layers may be dedicated to power planes (which distribute power to different parts of the circuit) or ground planes (which reduce noise and electromagnetic interference by providing a reference point for signals). The inner layers allow for efficient routing of complex circuits without cluttering the outer layers, which is essential in high-density designs.
The combination of inner and outer layers in a multilayer PCB provides the flexibility needed to design complex circuits with multiple components, ensuring that signals are properly routed, and power is distributed effectively.
Via Types
Vias are small, plated holes that connect different layers in a multilayer PCB. Depending on how they are designed, vias can be classified into three main types:
- Through-Hole Vias: These are the most common type of vias. A through-hole via passes through all the layers of the PCB, connecting the top layer to the bottom layer, and all the internal layers in between. They are used when a connection is needed across the entire thickness of the PCB. While they are straightforward to manufacture, they can take up valuable real estate on the board, which could otherwise be used for component placement or signal routing.
- Blind Vias: Blind vias connect an outer layer to one or more inner layers but do not pass all the way through the board. They are used to increase the available routing area, especially in high-density designs, without occupying space on the opposite outer layer. Blind vias allow for more compact designs, as they enable connections between the surface and internal layers without interfering with the entire board.
- Buried Vias: Buried vias are used to connect two or more inner layers without extending to the outer layers. They are entirely hidden within the board’s structure and are typically used when complex routing is required, allowing the outer layers to be reserved for surface components. Buried vias increase the routing capabilities of the inner layers, but they can also add complexity to the PCB’s manufacturing process.
Each type of via plays a crucial role in ensuring that signals and power can move efficiently between the different layers in a multilayer PCB. The strategic use of these vias is vital to the overall design and performance of the board, especially in complex and high-speed circuits where signal integrity and space optimization are critical.
By understanding the structure and purpose of each layer and via type in a multilayer PCB, designers can optimize the board for performance, space efficiency, and durability in various applications.
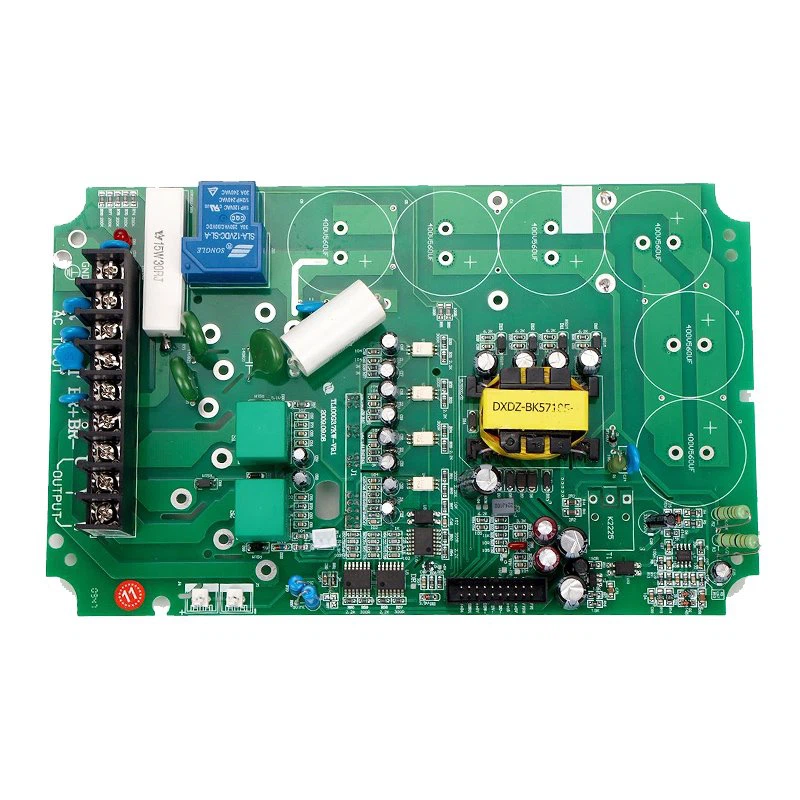
Chapter 3
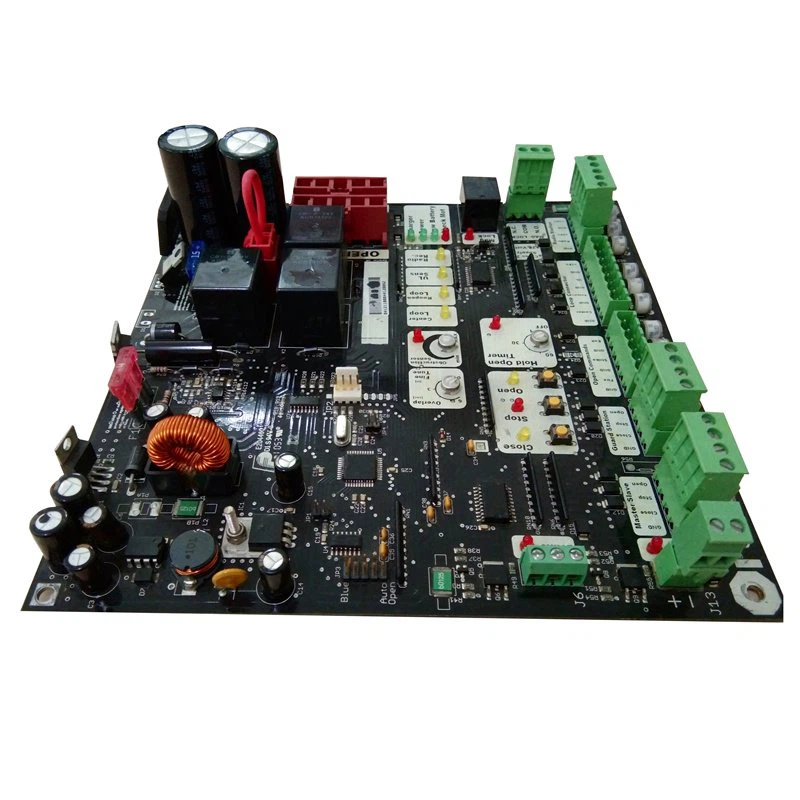
Benefits of Multilayer PCB
Multilayer PCBs offer numerous advantages over single-layer and double-layer boards, making them a preferred choice for complex electronic systems. Below are some key benefits:
Compact Design and Space Efficiency
One of the most significant benefits of multilayer PCBs is their compact design and efficient use of space. By stacking multiple layers of circuitry within the same board, multilayer PCBs significantly reduce the overall size of the device while maintaining or increasing its functionality. This compactness is essential in today’s technology landscape, where electronic devices are becoming increasingly smaller and more lightweight, particularly in industries like consumer electronics, aerospace, and medical devices.
- Optimized for Smaller Devices: Multilayer PCBs allow manufacturers to design products like smartphones, tablets, wearables, and laptops with high performance without increasing their physical size. These devices demand complex circuits, which can only be achieved efficiently through multilayer designs.
- Space-Saving Solution: By integrating multiple layers of circuitry into a single board, multilayer PCBs help reduce the need for larger boards or multiple PCBs in one device, saving space and minimizing the product’s overall footprint.
The ability to pack more functionality into a smaller space without compromising performance is a critical advantage of multilayer PCBs, especially in the modern electronics industry.
Improved Performance and Signal Integrity
Multilayer PCBs offer superior electrical performance compared to their single-layer and double-layer counterparts. This is primarily due to the use of dedicated inner layers for power and ground planes, as well as the careful design of signal routing paths across multiple layers. These design features help maintain signal integrity and minimize interference, crucial for high-speed, high-frequency applications.
- Reduced Electromagnetic Interference (EMI): Multilayer PCBs allow designers to incorporate ground planes between signal layers, which act as shields, reducing EMI and crosstalk between signals. This is particularly important in devices like telecommunications equipment, servers, and data centers, where high-speed data transmission requires clean, interference-free signals.
- Enhanced Signal Integrity: In multilayer designs, signals can be routed in such a way that impedance is controlled, minimizing signal degradation over long distances. This results in more accurate signal transmission, especially in high-frequency circuits used in communication devices, medical equipment, and automotive electronics.
- Lower Inductance and Capacitance: Multilayer PCBs have lower parasitic inductance and capacitance due to the close proximity of power and ground planes. This improves the overall performance of the circuit, making it ideal for applications requiring high-speed data processing or high-frequency signal transmission.
These improvements in performance and signal integrity make multilayer PCBs a superior choice for modern electronics, where speed, accuracy, and reliability are paramount.
Higher Component Density and Complexity Handling
Another major benefit of multilayer PCBs is their ability to handle higher component density and more complex circuit designs. With more layers available for routing, designers have greater flexibility to place components in optimal positions, improving the overall functionality and efficiency of the board.
- Increased Circuit Complexity: Multilayer PCBs are essential for supporting complex circuits with a large number of interconnections, which would be impossible to achieve with single-layer or double-layer boards. This is especially important in advanced applications such as aerospace systems, industrial machinery, and medical devices, where sophisticated functionalities are required.
- Efficient Component Placement: The multiple layers in a multilayer PCB allow for more efficient routing of traces, freeing up space on the surface of the board for more components. This is critical in compact devices where surface area is limited, but functionality requirements are high. For example, in smartphones or IoT devices, every square millimeter of space matters, and multilayer PCBs help maximize the use of available space.
- Better Heat Management: The increased number of layers in a multilayer PCB also aids in heat dissipation. Power planes and ground planes can act as heat sinks, distributing heat more evenly across the board and preventing hotspots. This results in a more reliable device with a longer lifespan, particularly in applications that generate significant heat, such as power electronics or automotive systems.
The ability to handle complex circuits and densely packed components makes multilayer PCBs ideal for advanced, high-performance electronic devices. This capability ensures that designers can continue to innovate and push the boundaries of what is possible in modern electronics.
In summary, multilayer PCBs offer clear advantages in terms of space efficiency, improved performance, and the ability to handle complex designs. These benefits make them essential in many high-tech applications, allowing for the creation of compact, powerful, and reliable electronic devices. Whether it’s in consumer electronics, telecommunications, medical devices, or automotive systems, multilayer PCBs provide the foundation for the sophisticated technology that powers modern life.
Chapter 4
Materials Used in Multilayer PCB
The materials used in multilayer PCBs play a critical role in their performance, durability, and suitability for various applications. The selection of these materials is based on factors such as the desired electrical performance, thermal resistance, and mechanical strength. Below is an overview of the common materials and how they are selected for specific applications:
Common Materials: FR4, Polyimide, and Rogers
Several materials are used in the construction of multilayer PCBs, with the most common being FR4, Polyimide, and Rogers. Each material has unique properties that make it suitable for different applications.
FR4 (Flame Retardant 4): FR4 is the most commonly used base material in PCB manufacturing due to its excellent balance of mechanical, electrical, and thermal properties. It is made from woven fiberglass cloth impregnated with an epoxy resin that has flame retardant properties. FR4 is widely used in general-purpose PCBs because of its durability, affordability, and decent performance in most electronic devices.
Key Characteristics:
- High mechanical strength
- Good insulation properties
- Low moisture absorption
- Flame retardant (meets UL94-V0 standards)
Applications: FR4 is ideal for consumer electronics, automotive systems, and general industrial applications. It is a go-to material for most multilayer PCB designs that do not require extremely high temperatures or specialized performance.
Polyimide: Polyimide is a high-performance material used for PCBs in demanding applications where heat resistance and flexibility are critical. Unlike FR4, polyimide is highly resistant to thermal degradation, making it suitable for applications that require high thermal stability. It is often used in flexible PCBs and rigid-flex boards, where its flexibility allows the board to bend without breaking.
Key Characteristics:
- Excellent thermal stability (can withstand high temperatures)
- Superior chemical resistance
- High flexibility and mechanical durability
- Good electrical insulation properties
Applications: Polyimide is commonly used in aerospace, military, medical devices, and high-temperature industrial equipment where exposure to extreme conditions is common. It is also used in flexible PCBs for compact devices like smartphones and wearable technology.
Rogers: Rogers is a brand name for a family of high-frequency, high-performance PCB materials. These materials are known for their low dielectric constant and loss tangent, making them ideal for high-frequency and microwave applications. Rogers materials also exhibit superior thermal management and stability, making them popular in RF (radio frequency) and microwave circuits.
Key Characteristics:
- Low dielectric constant and loss tangent for high-frequency signal integrity
- Excellent heat resistance
- Stable performance across a wide range of temperatures and frequencies
- Superior moisture resistance
Applications: Rogers materials are typically used in telecommunications, satellite systems, radar, and wireless communication devices, where signal integrity at high frequencies is paramount. These materials are essential in applications like 5G technology, where precision and low signal loss are critical.
Material Selection Based on Application
The choice of materials in multilayer PCBs depends heavily on the intended application and the specific requirements of the circuit. Designers must consider several factors when selecting the right material for their PCB:
Thermal Performance: For applications that generate a lot of heat or operate in high-temperature environments, materials like polyimide are preferred due to their superior thermal resistance. FR4 is suitable for general-purpose applications where thermal performance is less critical, while Rogers materials are ideal for high-frequency applications that also require good thermal management.
Signal Integrity: For high-speed, high-frequency circuits, signal integrity is crucial. Materials with low dielectric constants and loss tangents, like Rogers, are essential for minimizing signal loss and maintaining high performance. In contrast, FR4 may not be suitable for very high-frequency applications due to its relatively higher dielectric constant.
Mechanical Flexibility: For flexible or rigid-flex PCBs, polyimide is the material of choice due to its ability to withstand bending and mechanical stress without breaking. It is used in applications where the PCB must bend or flex during use, such as in wearables, foldable devices, and some automotive systems.
Cost Considerations: FR4 is the most cost-effective material, making it suitable for large-scale production and applications where budget constraints are a priority. In contrast, polyimide and Rogers materials are more expensive, but they offer enhanced performance in specialized applications.
Moisture and Chemical Resistance: In environments where moisture or chemicals are a concern, materials like polyimide and Rogers offer superior resistance. FR4, while generally durable, may absorb more moisture, which can affect its performance in humid or chemically aggressive environments.
Conductive and Non-Conductive Materials
A multilayer PCB is composed of both conductive and non-conductive materials, each playing a specific role in the board’s functionality.
Conductive Materials: The conductive layers in a PCB are typically made of copper. Copper is chosen for its excellent electrical conductivity, durability, and affordability. Each layer of copper in a multilayer PCB forms the circuit pathways or traces that transmit electrical signals between components. The thickness of the copper layers may vary depending on the current-carrying capacity required by the circuit.
Other Conductive Materials: For specialized applications, other conductive materials like gold, silver, or aluminum may be used in specific areas, such as connector pads or high-frequency signal paths.
Non-Conductive (Dielectric) Materials: The non-conductive layers, or dielectric layers, provide insulation between the conductive layers, preventing short circuits and ensuring that signals are routed correctly. These layers are usually made from materials like prepreg (fiberglass impregnated with resin), FR4, polyimide, or ceramic-based materials, depending on the thermal, mechanical, and electrical requirements of the PCB.
Dielectric materials play a critical role in controlling the impedance of the board, which is essential for high-speed signal transmission. The thickness and type of dielectric material affect the signal integrity and overall performance of the PCB.
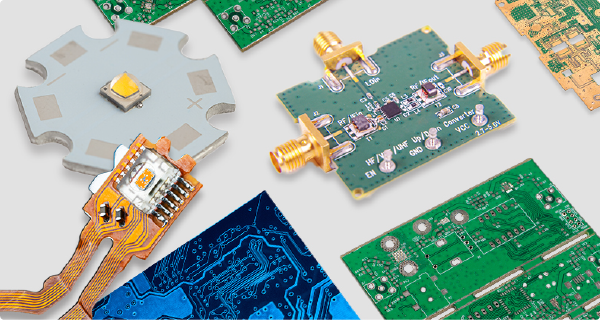
Chapter 5

Multilayer PCB Manufacturing Process
The manufacturing process of multilayer PCBs is a highly intricate and precise procedure, ensuring that the final product meets the desired performance standards and reliability. Below is a detailed breakdown of the key stages in multilayer PCB manufacturing:
PCB Design and Layout
The first step in the manufacturing process is the PCB design and layout. This phase involves using specialized software like CAD (Computer-Aided Design) tools to create a detailed blueprint of the multilayer PCB. The design includes the placement of all components, routing of signal traces, power planes, and ground layers, as well as the arrangement of vias and pads.
- Stackup Design: For multilayer PCBs, a crucial aspect of design is the stackup—the arrangement of conductive layers (copper) and insulating layers (dielectric). Designers choose the number of layers based on the circuit’s complexity and performance needs. Proper stackup design helps maintain signal integrity and minimize interference.
- Routing and Via Placement: Designers must route signals efficiently across layers, using vias (through-hole, blind, or buried) to connect traces across different layers. Signal integrity, impedance control, and electromagnetic interference (EMI) are key considerations in this phase.
Once the design is finalized, it is converted into Gerber files, which contain all the necessary information to guide the manufacturing process.
Lamination and Layer Buildup Process
The lamination and layer buildup process is where the multilayer structure of the PCB is physically created. This process involves alternating layers of copper and insulating materials (prepreg or core) being laminated together under heat and pressure to form a solid, compact PCB.
- Inner Layer Imaging: Each inner layer of the PCB is first etched with the circuit pattern. A photoresist is applied to the copper surface, and UV light is used to transfer the circuit design onto the layer. After the unwanted copper is etched away, the desired conductive pathways are left intact.
- Prepreg Layer Application: Prepreg (pre-impregnated composite fibers) serves as the insulating material between the copper layers. Sheets of prepreg are placed between each etched copper layer. These sheets bond the layers together during the lamination process.
- Lamination: The layers of copper and prepreg are carefully stacked in the required order to form the multilayer PCB structure. This stack is then placed in a press, where it is subjected to high temperature and pressure, causing the prepreg to melt and bond the layers together. Once cooled, this solidifies the structure into a single unified board.
The lamination process is critical in ensuring the durability, reliability, and mechanical stability of the PCB.
Drilling, Plating, and Etching
Once the layers are laminated, the next step is to create vias and holes that allow electrical connections between the various layers and for component mounting. This involves drilling, plating, and etching:
Drilling: Precision drilling machines create holes for through-hole vias, blind vias, and buried vias as specified in the design. These holes enable connections between the different layers of the PCB and provide pathways for components to be mounted on the board. High-precision drills, often laser-guided, are used to ensure the accuracy of these tiny holes, which can be as small as a few micrometers in diameter.
Plating: After drilling, the interior surfaces of the holes are plated with copper through a process called electroless copper plating. This ensures that the vias are conductive and can establish electrical connections between the different layers. The plating thickness is carefully controlled to ensure reliability and long-term durability, especially in high-performance applications.
Outer Layer Imaging and Etching: Similar to the inner layer imaging process, the outer layers are coated with a photoresist, exposed to UV light, and etched to create the circuit patterns on the outermost copper layers. The exposed copper is etched away, leaving behind the desired conductive traces that will connect components on the surface.
Final Assembly and Testing
Once the PCB structure is complete, the final assembly and testing phase begins. This phase ensures that the PCB is fully functional, free from defects, and ready for component mounting and end use.
Solder Mask Application: A solder mask is applied to the outer layers to protect the copper traces from oxidation, moisture, and contamination. The solder mask also helps prevent solder bridges from forming during the component assembly process. It is typically green but can be other colors based on customer specifications.
Silkscreen Printing: Important information, such as component labels, logos, or part numbers, is printed on the PCB using silkscreen printing. This helps during the assembly and maintenance of the PCB.
Surface Finish: To protect the exposed copper pads where components will be soldered, a surface finish like HASL (Hot Air Solder Leveling), ENIG (Electroless Nickel Immersion Gold), or OSP (Organic Solderability Preservative) is applied. This surface finish ensures good solderability during the component assembly process.
Electrical Testing: The completed PCB undergoes rigorous electrical testing to ensure that all connections are functioning correctly. Common tests include:
- Automated Optical Inspection (AOI): A camera scans the PCB to check for any missing traces, short circuits, or misalignments.
- Flying Probe Test: Probes touch the surface of the PCB to test the integrity of each connection and check for electrical shorts or open circuits.
- Functional Testing: The PCB is subjected to real-world conditions to ensure that it functions as intended in its target application.
Once the PCB passes all these tests, it is ready for the final assembly, where components will be mounted onto the board, or it can be shipped to the customer for further processing.
Chapter 6
Multilayer PCB Design Considerations
When designing a multilayer PCB, there are several important factors to consider in order to achieve optimal performance, reliability, and manufacturability. These factors include signal integrity, electromagnetic interference (EMI) control, power distribution, grounding, heat management, and layer stackup. Let’s take a closer look at each of these design considerations.
Signal Integrity and EMI/EMC Considerations
Signal integrity is critical in multilayer PCB design, especially in high-speed, high-frequency circuits. Poor signal integrity can result in data corruption, signal loss, or EMI, all of which can degrade the performance of the PCB. To maintain strong signal integrity and control EMI, designers must pay attention to the following elements:
- Controlled Impedance: High-speed signals require well-controlled impedance to avoid reflections and signal distortion. By using a carefully designed stackup, impedance can be controlled across specific layers. This often involves precise separation between signal layers and ground planes.
- Trace Length Matching: In high-speed designs, differences in trace lengths can result in timing mismatches between signals, known as signal skew. Designers must ensure that signal traces, especially those carrying critical clock or data signals, are properly matched in length to avoid timing issues.
- Minimizing Crosstalk: Crosstalk occurs when signal traces are placed too closely together, causing electrical interference between them. To minimize crosstalk, traces should be properly spaced and routed on different layers when necessary. Ground planes also help to shield signals from each other, reducing unwanted noise.
- Electromagnetic Compatibility (EMC): A well-designed multilayer PCB must comply with EMC standards to reduce electromagnetic radiation that could interfere with other devices. By using a dedicated ground plane and placing high-speed signals on inner layers between ground planes, designers can reduce EMI emissions. Shielding techniques, such as placing ground pours around sensitive traces, further improve EMC performance.
The goal is to create a design that ensures signals are transmitted with minimal distortion, noise, or loss, which is particularly important in telecommunications, aerospace, and automotive applications where signal integrity is critical.
Power Distribution and Grounding
Proper power distribution and grounding are essential in multilayer PCB designs to ensure stable voltage delivery and minimize power noise.
Dedicated Power and Ground Planes: In multilayer PCBs, it is common to dedicate entire layers to power and ground planes. These planes provide a low-impedance path for power distribution, reducing voltage drop and ensuring that all components receive stable power. A well-designed power plane also helps to distribute current evenly across the PCB, improving performance in high-power circuits.
- Grounding Techniques: A robust grounding system is crucial for minimizing noise and ensuring signal integrity. The ground plane acts as a reference for signals and reduces the return path impedance, which is important for maintaining signal quality. Using a single ground plane that spans the entire PCB is typically the best practice to avoid ground loops and ensure a consistent reference point for all signals.
- Decoupling Capacitors: To further improve power stability, decoupling capacitors are placed near critical components. These capacitors act as local energy storage units, smoothing out voltage fluctuations and reducing noise on the power rails. Proper placement and selection of these capacitors are essential to avoid power supply noise, especially in high-speed and high-frequency designs.
- Power Integrity: Maintaining power integrity in multilayer PCB designs ensures that the power distribution network delivers clean, noise-free power to all components. Poor power integrity can result in voltage drops, noise coupling, and unstable component behavior, leading to system failures.
By focusing on efficient power distribution and effective grounding, designers can ensure stable voltage levels across the entire PCB, which is critical for reliable performance.
Heat Dissipation and Thermal Management
As electronic devices become smaller and more powerful, thermal management has become a critical design consideration in multilayer PCBs. Without adequate heat dissipation, excessive heat can lead to component failure, reduced performance, and shorter product lifespan.
- Thermal Vias: One of the most effective ways to manage heat in a multilayer PCB is by using thermal vias. These vias transfer heat from one side of the PCB to another, spreading the heat across the board or directing it to a heatsink or thermal pad. Placing thermal vias under heat-generating components, such as processors or power regulators, helps in dissipating heat away from the component, preventing localized overheating.
- Heat Sinks and Pads: In some cases, passive cooling solutions like heat sinks or thermal pads are attached to specific components or areas of the PCB. These heat sinks absorb heat and radiate it away from the board, reducing the overall temperature of the system.
- Copper Weight: The thickness of the copper layers in the PCB, known as copper weight, also plays a role in heat dissipation. Increasing the copper weight allows the PCB to handle higher currents and spread heat more effectively across the board. However, thicker copper adds cost and complexity to the manufacturing process, so designers must balance thermal needs with cost constraints.
- Thermal Analysis: Thermal management is not just about adding cooling mechanisms but also about thermal analysis during the design phase. Thermal simulation tools allow designers to identify hot spots and optimize the layout to improve airflow and heat dissipation. Components that generate significant heat should be strategically placed near the edges of the board or near thermal vias for efficient cooling.
Effective thermal management ensures that the PCB can operate within safe temperature ranges, maintaining performance and prolonging the life of the device.
Stackup Design and Layer Arrangement
The stackup of a multilayer PCB refers to the arrangement and sequencing of the conductive and insulating layers. Stackup design is crucial in achieving the desired electrical performance, mechanical strength, and manufacturability of the PCB.
- Layer Symmetry: In multilayer PCB designs, symmetry is important for mechanical stability and minimizing warping during the manufacturing process. A balanced stackup with an equal number of copper and dielectric layers on either side of the PCB’s center helps to prevent mechanical stresses that can cause the board to bend or warp. This is particularly important in large or high-layer-count PCBs.
- Signal Layer Assignment: The placement of signal layers within the stackup is critical for maintaining signal integrity. High-speed signal layers should be placed close to ground planes to minimize the return path impedance and reduce the risk of signal distortion. Sensitive analog signals are typically routed on inner layers between ground planes to provide shielding from external noise sources.
- Power and Ground Planes: Power and ground planes are typically placed in the inner layers of the stackup, with signal layers arranged around them. This configuration helps to maintain a low-impedance path for both power and ground, improving signal integrity and EMI performance. Placing a ground plane directly adjacent to a power plane also creates a natural decoupling effect, which reduces noise on the power rails.
- Layer Count Optimization: The number of layers in a PCB is determined by the complexity of the circuit, the number of signals that need to be routed, and the performance requirements. More layers allow for greater flexibility in routing, improved signal integrity, and better power distribution, but they also increase manufacturing costs. Designers must strike a balance between performance and cost when deciding the optimal layer count for a multilayer PCB.
- Dielectric Thickness: The thickness of the insulating layers (dielectric) between copper layers affects both the electrical and mechanical properties of the PCB. Thinner dielectric layers are often used in high-speed designs to reduce signal propagation delays, while thicker dielectric layers may be used to improve structural integrity or provide insulation in high-voltage applications.
The stackup design and layer arrangement of a multilayer PCB play a pivotal role in determining the board’s overall performance, durability, and manufacturability. A well-optimized stackup helps achieve the desired balance between electrical performance, mechanical stability, and cost efficiency.
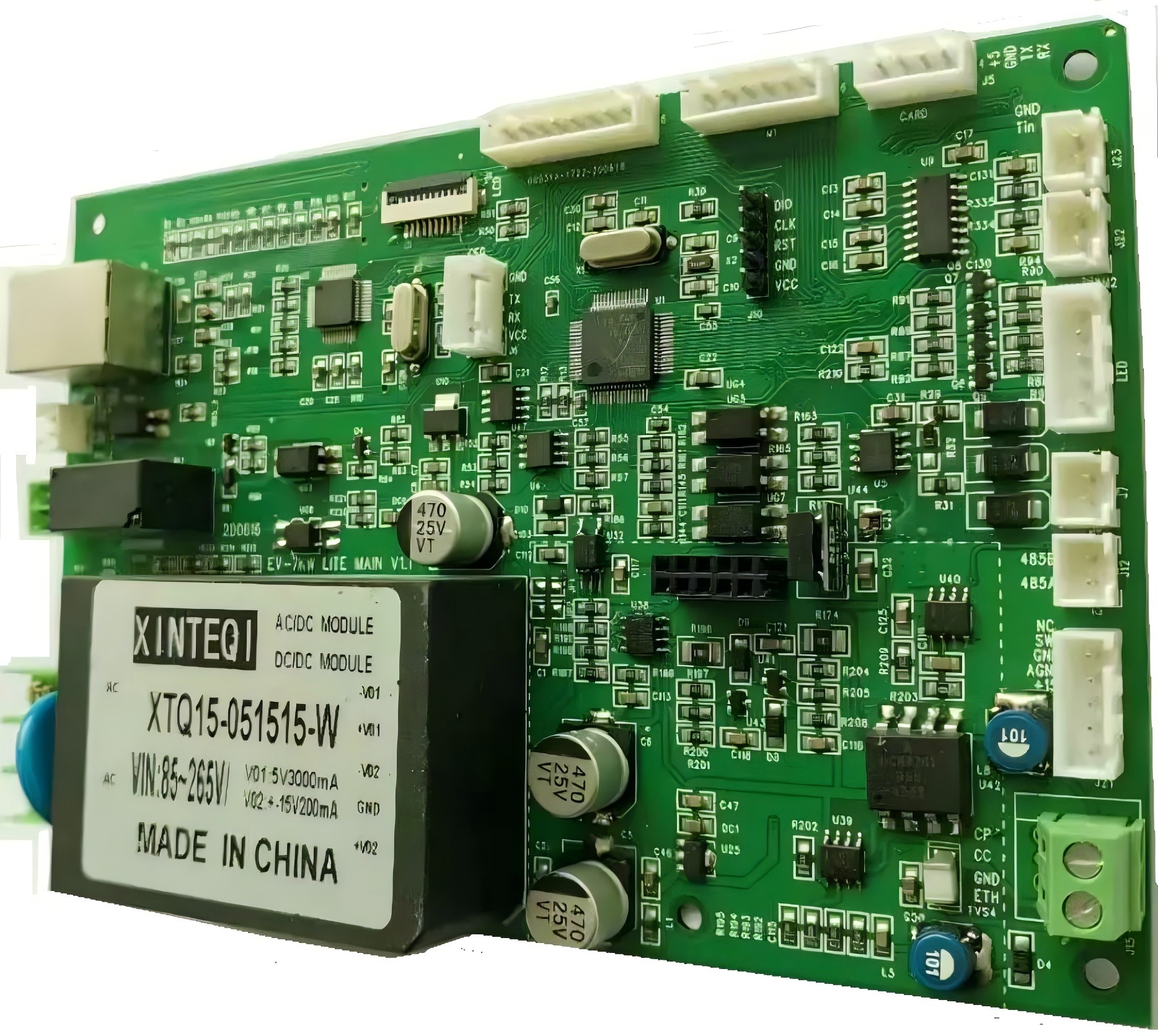
Chapter 7
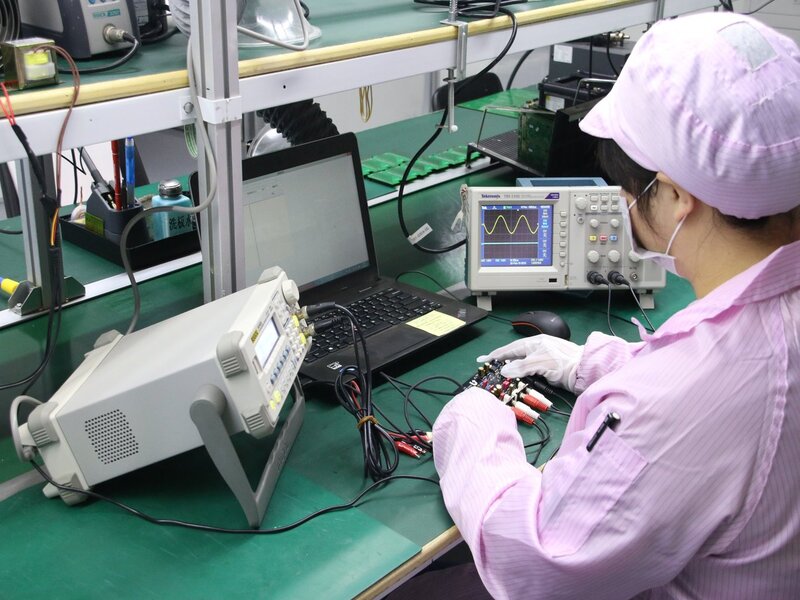
Common Applications of Multilayer PCB
Multilayer PCBs are indispensable in modern electronic devices due to their ability to handle complex circuits in a compact form factor, deliver high performance, and support a wide range of functionalities. Their unique advantages, such as higher component density, improved signal integrity, and efficient power distribution, make them suitable for a variety of high-tech industries. Below are some of the most common applications of multilayer PCBs:
Telecommunications and Networking Equipment
The telecommunications and networking industry relies heavily on multilayer PCBs to support high-speed data transmission, signal integrity, and reliability. As network infrastructure continues to evolve with the advent of technologies like 5G, the demand for high-performance, multilayer PCBs in this field is increasing.
Switches and Routers: Multilayer PCBs are critical in devices such as switches and routers, where high-speed signal processing and data routing are required. The multilayer design allows for the separation of power and ground planes from signal layers, reducing noise and electromagnetic interference (EMI), which is essential for maintaining signal integrity in these devices.
Base Stations and Antennas: In cellular base stations, multilayer PCBs are used to process and transmit data across networks, enabling seamless communication between mobile devices. The PCBs must handle high-frequency signals and maintain low signal loss, especially with the growing demands of 5G technology. The use of materials like Rogers, which are known for their low dielectric constant, ensures signal stability in these high-frequency environments.
Fiber Optic Transceivers: Fiber optic communication systems, which provide high-speed internet and data services, depend on multilayer PCBs for their signal processing units. These PCBs support data conversion between electrical and optical signals, requiring a compact design and the ability to handle high data rates efficiently.
Telecommunications and networking equipment require multilayer PCBs to deliver fast, reliable, and interference-free communication. Their ability to manage complex signals and minimize EMI makes them ideal for this industry.
Consumer Electronics (Smartphones, Laptops, etc.)
The consumer electronics sector is one of the largest markets for multilayer PCBs. Devices like smartphones, laptops, tablets, and wearables are becoming increasingly powerful while maintaining compact and lightweight designs, and this is only possible through the use of multilayer PCBs.
Smartphones: Multilayer PCBs are essential in smartphones due to their ability to accommodate the complex circuits required for a wide range of functionalities, such as wireless communication, touchscreens, cameras, and sensors. The compact design of a multilayer PCB allows for higher component density, enabling manufacturers to fit more features into increasingly smaller devices without compromising performance. Additionally, multilayer PCBs provide the necessary power distribution and signal integrity required for high-speed processors, memory chips, and wireless connectivity modules.
Laptops and Tablets: Multilayer PCBs are widely used in laptops and tablets, where performance and size constraints are critical. These devices require PCBs that can manage fast data transfer, handle multiple I/O ports, and support high-resolution displays. The flexibility in multilayer PCB design allows manufacturers to efficiently route signals across various components, such as processors, memory, and storage, ensuring that laptops and tablets meet modern performance standards.
Wearables: Wearable devices, such as smartwatches, fitness trackers, and health monitors, depend on multilayer PCBs to achieve their compact size while still delivering advanced functionality. In these applications, multilayer PCBs allow for the integration of sensors, wireless communication modules, and small processors, all within a miniature form factor. The flexibility of multilayer PCBs also enables the production of rigid-flex designs, which are ideal for devices that need to bend or conform to the user’s body.
The consumer electronics industry relies on multilayer PCBs for their ability to deliver high-performance, small form-factor designs. As consumer devices continue to advance, the demand for multilayer PCBs will only increase, enabling even more complex and compact devices in the future.
Aerospace, Automotive, and Medical Devices
Multilayer PCBs are used extensively in aerospace, automotive, and medical applications, where performance, reliability, and durability are paramount. These industries demand PCBs that can withstand extreme environments, deliver precise performance, and ensure the safety and effectiveness of the system.
Aerospace: In aerospace applications, multilayer PCBs are used in various systems such as avionics, radar systems, communication equipment, and navigation devices. These PCBs must be able to withstand extreme temperatures, pressure variations, and mechanical stresses. The use of materials like polyimide in multilayer PCBs allows them to perform reliably under these harsh conditions. Additionally, the compact design and high-performance characteristics of multilayer PCBs enable them to handle the complex signal processing required in aerospace systems.
Automotive: The automotive industry increasingly relies on multilayer PCBs to support advanced driver-assistance systems (ADAS), infotainment systems, engine control units (ECUs), and electric vehicle (EV) power management systems. In automotive applications, multilayer PCBs must deliver high reliability, withstand extreme temperatures and vibrations, and ensure efficient power distribution. They also need to handle high-speed data transmission for sensors, cameras, and communication modules used in ADAS and autonomous driving technologies. Additionally, electric vehicles (EVs) rely on multilayer PCBs for battery management systems, power inverters, and charging systems, making the PCB a critical component of the vehicle’s overall functionality.
Medical Devices: In the medical field, multilayer PCBs are essential for the design of devices like pacemakers, imaging equipment (such as MRI and CT scanners), and diagnostic tools. These devices demand extreme precision, reliability, and longevity, often requiring PCBs that can withstand sterilization processes and operate in environments with minimal noise and interference. Multilayer PCBs are used in medical devices to ensure accurate signal processing, manage power distribution, and deliver reliable performance over the device’s lifespan. The compact size and high functionality of multilayer PCBs allow medical devices to be portable, wearable, and, in some cases, implantable, improving patient care and diagnostic accuracy.
In aerospace, automotive, and medical applications, the reliability and performance of multilayer PCBs are critical to ensuring the safety, effectiveness, and efficiency of the systems they support. These industries require PCBs that can perform under extreme conditions while maintaining high precision and reliability.
Chapter 8
Challenges in Multilayer PCB Design
Designing multilayer PCBs is a complex task that requires careful planning and consideration. There are many challenges involved, from routing signals and managing impedance to dealing with the high costs and long lead times associated with multilayer boards. In this article, we will take a closer look at the main challenges faced in multilayer PCB design.
Design Complexity and Routing Challenges
One of the biggest challenges in multilayer PCB design is dealing with the increased complexity that comes with having multiple layers of circuitry. As the number of layers in a PCB increases, so does the difficulty of routing signals, managing power distribution, and maintaining signal integrity.
- Limited Space and Component Placement: With more layers and components packed into a small board, designers have to be strategic about where they place components. They need to make sure that components are placed in a way that avoids congestion and allows for efficient routing. This is especially important in designs where there is a need for dense component placement, such as in smartphones or wearable devices. Misplacing even one component can lead to inefficient routing and signal interference, which can cause design failures.
- Signal Routing Across Multiple Layers: Routing signals through multiple layers is challenging because you have to minimize the length of the signal paths while still maintaining a logical flow of connections. Designers have to carefully manage the signal paths to avoid unnecessary crossings and via placements, which can introduce noise or delays. Routing high-speed signals becomes even more challenging as the number of layers increases because you have to route each signal in a way that minimizes noise, signal reflection, and impedance mismatch.
- Via Management: Vias (through-hole, blind, and buried) are used to connect different layers in a multilayer PCB. While they are necessary for routing signals between layers, they also introduce challenges in terms of manufacturing and design. Using too many vias can lead to signal degradation and increased board complexity, while not using enough vias can make it difficult to route signals efficiently. Designers have to strike a balance, using vias strategically to maintain signal integrity without making the layout too complicated.
- Layer Stackup Optimization: As the number of layers increases, it becomes critical to optimize the stackup (the arrangement of layers). The stackup needs to accommodate power planes, ground planes, and signal layers in a way that maximizes performance while minimizing interference and noise. The layer stackup also affects the mechanical stability and manufacturability of the PCB, so it is an important consideration in the design process.
Addressing these design complexities requires a deep understanding of the overall system requirements and the use of advanced design tools that can simulate signal behavior and optimize routing.
Manufacturing Costs and Lead Times
Multilayer PCBs are typically more expensive and time-consuming to manufacture than single-layer or double-layer PCBs. This is because they require additional materials, processing steps, and quality control measures.
- Higher Manufacturing Costs: The increased complexity of multilayer PCBs directly affects manufacturing costs. Each additional layer adds to the material costs (such as copper and insulating materials), and the fabrication process becomes more involved. The lamination process, which involves pressing and bonding multiple layers of copper and insulating material together, is particularly expensive for multilayer designs. Precision drilling for vias, advanced etching techniques, and additional quality control measures also drive up costs. The use of specialized materials, such as high-frequency substrates like Rogers, further increases the overall expense.
- Extended Lead Times: The complexity of manufacturing multilayer PCBs means that they often have longer lead times compared to simpler boards. The multiple stages of lamination, drilling, plating, and testing extend the production cycle. Additionally, multilayer PCBs often require more detailed inspection and testing to ensure that they meet performance and reliability standards. If any issues arise during production, reworking or redesigning a multilayer PCB can be time-consuming, further delaying delivery. This makes lead time management a critical consideration, especially for projects with tight deadlines.
- Yield Challenges: Achieving high yield in multilayer PCB manufacturing can be difficult, especially for complex designs. Misalignments, via defects, and lamination issues can result in rejected boards, which increases the cost and time associated with production. Manufacturers need to implement strict quality control processes to ensure that each board meets the required specifications without sacrificing yield.
To mitigate these challenges, designers and manufacturers need to work closely together to optimize designs for manufacturability and balance performance with cost and production timelines.
Managing Impedance and Crosstalk
In high-speed and high-frequency multilayer PCBs, controlling impedance and minimizing crosstalk are critical challenges that can affect signal integrity and overall board performance.
- Impedance Control: Impedance refers to the resistance encountered by an electrical signal as it travels through a conductor. In multilayer PCB designs, maintaining consistent impedance is crucial, especially for high-speed signals. Variations in impedance can cause signal reflections, distortion, and data integrity loss. Designers have to carefully calculate and control the impedance of each trace, especially in high-frequency applications like telecommunications or radar systems. Factors like trace width, the distance between layers, and the type of dielectric material used all affect impedance. Proper impedance matching ensures that signals are transmitted smoothly across the board without degradation.
- Signal Integrity and Crosstalk: Crosstalk occurs when signals from adjacent traces interfere with each other, causing noise and data errors. In multilayer PCBs, the risk of crosstalk increases due to the proximity of traces and the high density of the routing. Crosstalk can significantly degrade signal integrity, especially in high-speed circuits where small disruptions can lead to major performance issues. To minimize crosstalk, designers have to carefully space out signal traces and use shielding techniques like ground planes to isolate signals. Routing high-speed signals on inner layers between ground planes also helps reduce crosstalk by providing a low-impedance return path.
- Differential Pair Routing: In many high-speed designs, differential pairs (two signal traces that carry opposite signals) are used to reduce noise and improve signal integrity. However, managing differential pairs across multiple layers and making sure that the two traces remain parallel and equidistant throughout the PCB can be challenging. Any deviation in trace length or spacing can lead to timing mismatches and impedance imbalances, which can affect the overall performance of the circuit.
- Via-Induced Impedance Changes: Vias introduce impedance discontinuities in signal paths, which can cause reflections and signal degradation. This is particularly problematic for high-speed signals that require a smooth, continuous impedance profile. Designers need to minimize the use of vias for high-frequency signals or use techniques like back-drilling to reduce the impact of via stubs on signal integrity.
Effectively managing impedance and crosstalk in multilayer PCB designs requires a combination of careful layout planning, advanced simulation tools, and adherence to best practices for high-speed design. By controlling these factors, designers can ensure that their multilayer PCBs deliver the required performance, even in the most demanding applications.
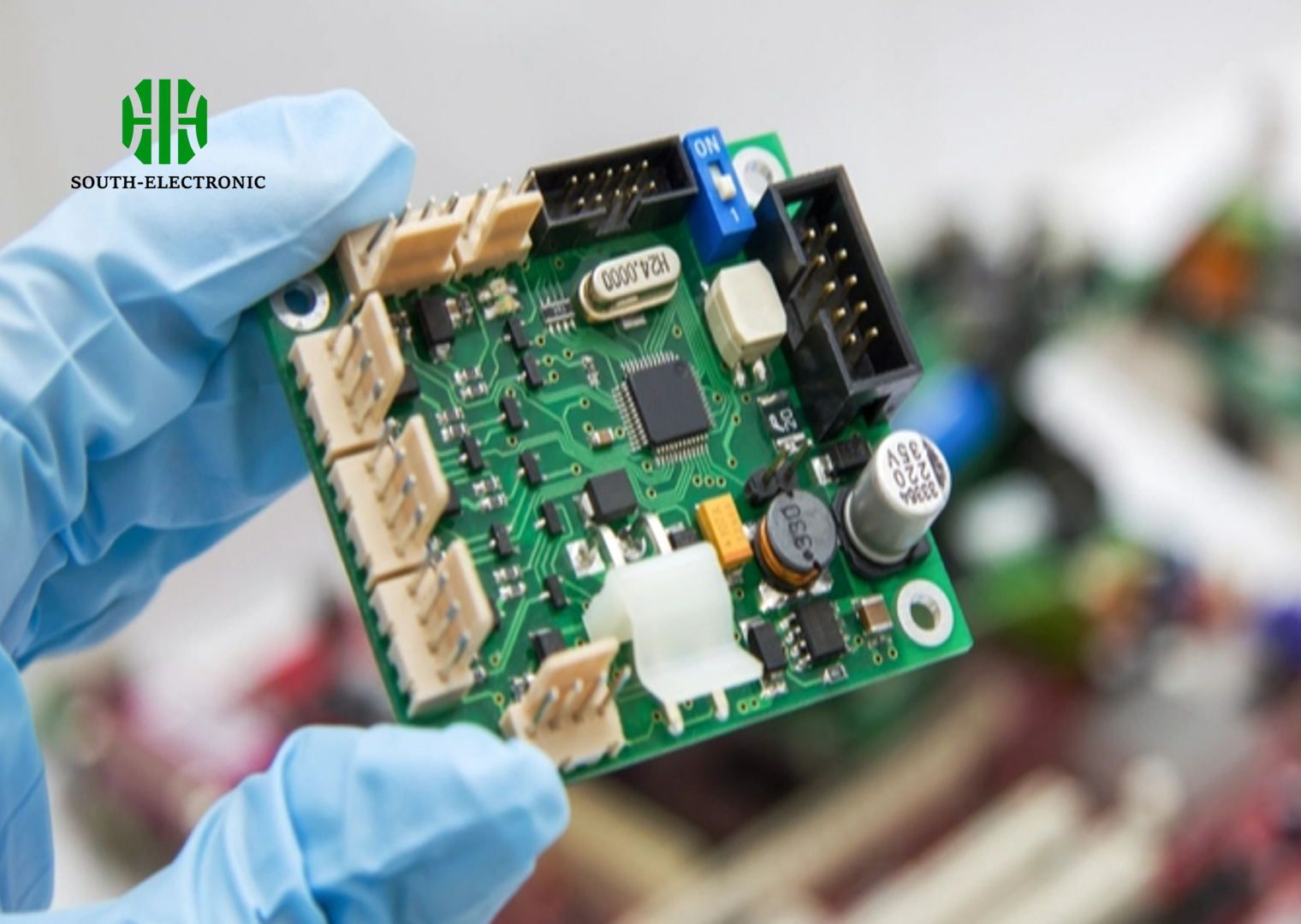
Chapter 9

Multilayer PCB Prototyping and Testing
Prototyping and testing are crucial stages in the development of multilayer PCBs, ensuring that the final product meets performance, reliability, and manufacturability requirements. Prototyping allows designers to identify and address issues early in the process, while thorough testing ensures the functionality and durability of the PCB before full-scale production. Below is a detailed explanation of the importance of prototyping, common testing techniques, and methods for avoiding common issues during the prototyping stage.
The Importance of Prototyping
Prototyping is an essential step in multilayer PCB design because it allows for the validation of the design before moving into mass production. Multilayer PCBs are often complex, and even the most carefully planned designs may have flaws or unexpected issues that only surface once a physical prototype is created. The primary benefits of prototyping include:
Design Validation: Prototyping allows engineers to verify that the PCB design performs as expected in real-world conditions. It ensures that all components are correctly placed and connected, and that signals are transmitted without interference. By creating a prototype, designers can validate key design elements such as signal integrity, power distribution, thermal management, and mechanical fit.
Early Detection of Issues: Prototyping helps catch design errors, manufacturing defects, or performance problems early in the development process. For instance, issues related to trace routing, impedance mismatches, or improper grounding can be identified during the prototyping phase, saving time and money compared to discovering these problems later in mass production.
Cost Savings: While creating prototypes involves some upfront costs, the investment is minimal compared to the potential costs of discovering a critical design flaw during production. By catching and addressing issues early, prototyping reduces the risk of expensive rework or delays in the production schedule.
Testing and Refinement: Prototyping also provides an opportunity to test different design variations or optimize the board layout for improved performance. This iterative process allows designers to refine the design, ensuring that the final PCB meets all performance and reliability requirements.
Given the complexity of multilayer PCBs, prototyping is not optional but rather an essential part of the design process, allowing for iterative improvements and reducing the risk of failure in the final product.
Testing Techniques: AOI, Flying Probe, Functional Testing
Once the prototype is created, several testing techniques are employed to verify its functionality and ensure that the board meets all design specifications. Common testing methods for multilayer PCBs include Automated Optical Inspection (AOI), Flying Probe Testing, and Functional Testing.
Automated Optical Inspection (AOI): AOI is a non-contact, automated inspection technique used to identify manufacturing defects on the surface of the PCB. The system uses high-resolution cameras to capture images of the PCB and compare them against the original design files (such as Gerber files). AOI can detect issues such as:
- Missing or misaligned components
- Solder bridge defects
- Open circuits or short circuits
- Incorrect component placement or orientation
AOI is particularly useful for inspecting densely populated multilayer PCBs where manual inspection would be difficult or time-consuming. It helps ensure that the board meets the required quality standards before more advanced testing techniques are applied.
Flying Probe Testing: The flying probe test is a versatile and effective method for testing multilayer PCBs, especially during the prototyping phase. Instead of using a traditional test fixture, flying probes use movable, precision-controlled probes to make electrical contact with the test points on the PCB. This method is ideal for small production runs or prototypes because it does not require a dedicated test fixture, which can be expensive to produce for one-off prototypes.
The flying probe test is used to:
- Verify electrical connections between layers
- Detect short circuits, open circuits, and miswiring
- Measure component values (resistance, capacitance)
This technique is flexible and can quickly adapt to design changes, making it a preferred method for early-stage testing of multilayer PCB prototypes.
Functional Testing: Functional testing involves testing the PCB under real operating conditions to ensure that it performs as expected. This type of testing verifies that all components work together as designed and that the PCB meets the desired performance criteria. Functional testing typically involves:
- Applying power to the PCB and verifying that voltage levels are correct
- Running software or firmware to check if the PCB behaves as expected
- Measuring signal integrity and power distribution under real-world conditions
Functional testing is critical because it simulates the actual environment in which the PCB will be used, allowing designers to ensure that the board will function properly in its final application.
By combining these testing methods, designers can thoroughly evaluate the prototype and ensure that it meets both functional and quality standards before proceeding to full-scale production.
How to Avoid Common Issues During Prototyping
The prototyping phase is where many potential issues in multilayer PCB designs can be identified and corrected. However, some common pitfalls can occur during this stage if not properly addressed. Here are strategies to avoid common issues:
Review the Design Thoroughly: Before sending the design for prototyping, perform a detailed review of the PCB layout, schematic, and bill of materials (BOM). Pay close attention to areas such as trace routing, via placement, and component selection to ensure that there are no obvious errors. Using Design Rule Check (DRC) software helps identify layout errors or violations of manufacturing constraints early in the process.
Ensure Proper Stackup and Impedance Calculations: In multilayer PCBs, the stackup (the arrangement of layers) plays a crucial role in signal integrity and overall board performance. Make sure that the stackup is optimized for the application, with the right combination of signal layers, power planes, and ground planes. For high-speed signals, impedance-controlled traces must be correctly calculated to avoid signal reflections or distortion.
Minimize Crosstalk and EMI: In multilayer designs, closely spaced signal traces can result in crosstalk, where signals interfere with each other. To avoid this issue, keep high-speed signal traces sufficiently spaced apart, use proper shielding techniques, and ensure that ground planes are in close proximity to signal layers. Similarly, pay attention to potential electromagnetic interference (EMI), especially in high-frequency designs.
Validate Power Distribution and Grounding: Multilayer PCBs often require complex power distribution networks. Ensure that power planes are properly designed to deliver stable voltage levels and that grounding is well-planned to avoid ground loops or high impedance return paths. Adding decoupling capacitors near power pins of critical components helps reduce noise and stabilize power distribution.
Test Early and Frequently: Start testing the prototype as early as possible in the development process. Use AOI and flying probe testing to quickly identify any defects or issues. Functional testing should be conducted in parallel to validate the design under real-world conditions. The earlier these tests are performed, the easier it is to correct any problems before they become more costly to fix in later production stages.
Work with a Trusted Manufacturer: Prototyping success depends not only on good design practices but also on working with a reliable and experienced PCB manufacturer. Manufacturers who specialize in multilayer PCBs can offer valuable advice on manufacturability, material selection, and design optimization, reducing the risk of errors during the prototyping process.
Chapter 10
Choosing the Right Multilayer PCB Manufacturer
Selecting the right manufacturer for your multilayer PCBs is crucial to ensuring that your design meets the highest standards of quality, reliability, and performance. The decision impacts not only the functionality of your final product but also the efficiency of the production process, costs, and lead times. Below are the key factors to consider when choosing a multilayer PCB manufacturer, along with an explanation of why South-Electronic stands out as an ideal choice.
Key Factors to Consider: Quality, Certifications, Lead Time
When evaluating a multilayer PCB manufacturer, several critical factors must be assessed to ensure the best results for your project:
Quality: The quality of a PCB is paramount, as it directly affects the performance and longevity of the final product. A high-quality manufacturer will have stringent quality control processes in place, including regular inspections and tests to detect any manufacturing defects. Look for a manufacturer that prioritizes precision in design and production, minimizing errors that could affect the PCB’s functionality.
Certifications: Certifications are a reliable indicator of a manufacturer’s commitment to quality and industry standards. Ensure that the manufacturer holds certifications such as ISO 9001 for quality management, UL, CE, IATF16949 for automotive applications, and ISO13485 for medical devices. These certifications ensure that the manufacturer complies with international standards and can produce PCBs suitable for specialized and high-performance applications.
Lead Time: Lead time is a critical consideration, especially in industries where time-to-market is crucial. A reliable manufacturer will have efficient production processes that allow for fast turnaround times without compromising quality. Ensure that the manufacturer is transparent about their lead times and can meet your project’s deadlines, whether you need a rapid prototype or full-scale production.
By prioritizing quality, certifications, and lead time, you can ensure that your PCB design is in the hands of a capable and dependable manufacturer.
Importance of Supplier Communication and Support
Effective communication and support from the supplier are essential for the success of any multilayer PCB project. A strong partnership with your PCB manufacturer can help ensure that your design is optimized for manufacturability and that any issues are resolved quickly. Key aspects to look for in terms of supplier communication and support include:
Proactive Communication: A good manufacturer will keep you informed at every stage of the production process, from initial design reviews to final delivery. They should be responsive to inquiries, provide regular updates, and communicate any potential delays or challenges in advance.
Design Support: Some manufacturers offer design for manufacturability (DFM) reviews, which can be incredibly helpful in ensuring that your PCB design is optimized for production. This can help prevent issues such as poor routing, misaligned layers, or improper via placements that could lead to production delays or performance issues.
Technical Assistance: Choose a manufacturer that offers technical support to address any concerns or questions you might have during the design, prototyping, or production stages. Having access to expert advice ensures that your PCB is produced to the highest standards.
After-Sales Support: A reliable manufacturer will also provide after-sales support, helping you troubleshoot any issues with the PCBs after delivery. This ensures that you receive assistance not only during production but throughout the entire lifecycle of the project.
Strong supplier communication and support are key to ensuring that your project runs smoothly and that any potential issues are addressed promptly.
Why Choose South-Electronic for Your Multilayer PCB Needs
South-Electronic is an experienced and highly qualified manufacturer that stands out as an excellent choice for your multilayer PCB needs. Here’s why:
Commitment to Quality: At South-Electronic, quality is a top priority. Every PCB undergoes rigorous quality control, including advanced testing methods to ensure that each board meets the highest standards of performance and reliability. South-Electronic holds certifications like ISO 9001, UL, CE, IATF16949, and ISO13485, ensuring compliance with international quality standards across various industries.
Fast Turnaround Times: South-Electronic understands the importance of meeting project deadlines. With efficient production processes and streamlined operations, the company offers fast lead times without compromising on quality. Whether you need rapid prototyping or full-scale production, South-Electronic can deliver on time, ensuring your projects stay on schedule.
Excellent Customer Support: South-Electronic places a strong emphasis on customer service, offering clear and proactive communication throughout the entire production process. The team provides comprehensive technical support, from DFM reviews to after-sales service, ensuring that your PCB design is optimized and any potential issues are swiftly resolved.
Customization and Flexibility: South-Electronic offers fully customizable PCB solutions tailored to your specific project needs. From prototyping to large-scale production, the company provides flexibility in terms of order quantities and design adjustments, making it easier to scale your production as required.
Proven Industry Expertise: With over a decade of experience, South-Electronic has established itself as a trusted partner for industries such as automotive, telecommunications, medical devices, and consumer electronics. Their deep industry knowledge ensures that they can handle even the most complex multilayer PCB designs with precision and reliability.
In conclusion, choosing South-Electronic for your multilayer PCB manufacturing needs ensures that you receive high-quality products, fast turnaround times, and exceptional customer support. Their expertise, commitment to quality, and dedication to customer satisfaction make them the ideal partner for your next project.
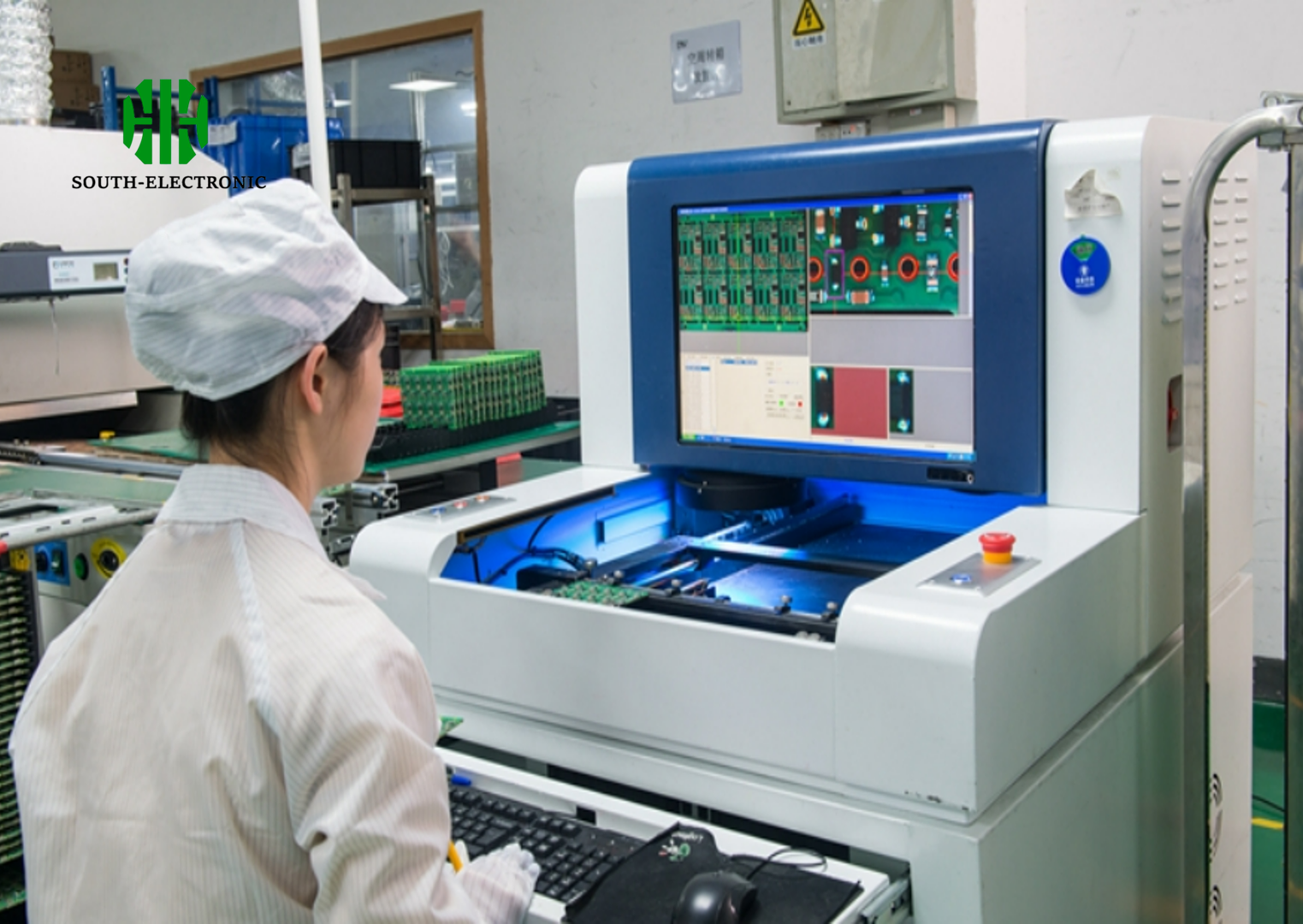
Get in touch
Where Are We?
Industrial Park, No. 438 Donghuan Road, No. 438, Shajing Donghuan Road, Bao'an District, Shenzhen, Guangdong, China
Floor 4, Zhihui Creative Building, No.2005 Xihuan Road, Shajing, Baoan District, Shenzhen, China
ROOM A1-13,FLOOR 3,YEE LIM INDUSTRIAL CENTRE 2-28 KWAI LOK STREET, KWAI CHUNG HK
service@southelectronicpcb.com
Phone : +86 400 878 3488
Send us a message
The more detailed you fill out, the faster we can move to the next step.
