Premier PCB Assembly Partner
South-Electronic
At South-Electronic, we understand the critical importance of precision and reliability in PCB assembly, which is why we offer advanced solutions tailored to meet the specific needs of your projects.
Your Go-To Partner for Reliable PCB Assembly Solutions
Welcome to South-Electronic, we deliver tailored solutions that fit your unique project requirements. Whether you’re looking for a single prototype or full-scale production, you’ll benefit from our decade of experience, fast delivery, and ISO9001-certified quality.
When it comes to your PCB assembly needs, you deserve a partner who understands the importance of precision and reliability.You can count on us to bring your ideas to life with efficiency and care. Let us help you take your electronics manufacturing to the next level!
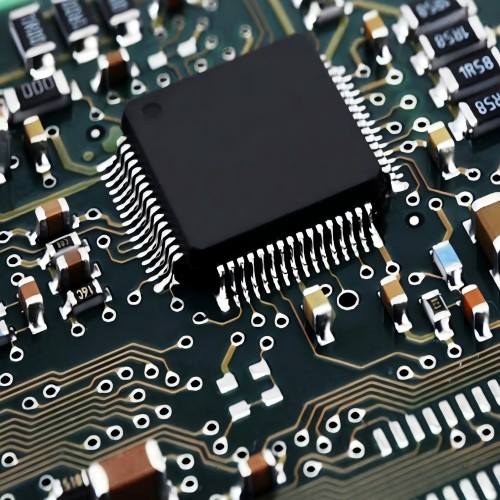
Surface Mount Technology (SMT)
SMT is key for engine management systems like fuel injection, ignition timing, and emissions control. These PCBs are designed to be reliable and durable, withstanding tough environmental conditions.

Through-Hole Technology (THT)
THT is used for body functions such as lighting, power windows, and central locking. It's vital for Body Control Modules (BCMs), which connect sensors and actuators throughout the vehicle.
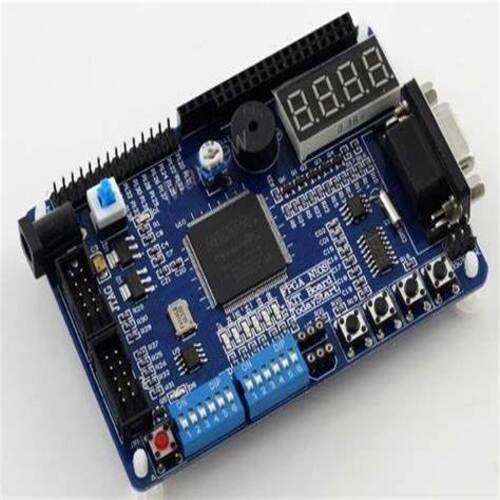
Mixed Technology Assembly
This combines SMT and THT to manage entertainment, navigation, and connectivity systems like Bluetooth and Wi-Fi. These assemblies handle high-speed data and advanced user interfaces.

Prototype Assembly
Prototype PCBs are used in safety systems like airbags and antitheft devices, ensuring quick response times and reliable, fail-safe operation.
Why Choose South-Electronic?
Choose South-Electronic for our expertise in delivering custom, high-quality PCB assemblies for a wide range of applications. Our team has extensive experience, ensuring superior quality at competitive prices and exceptional service from start to finish.
-
Flexibility in Ordering
No matter the size of your order, we offer flexible options that fit your production requirements.
Whether you need a small batch or large-scale production, you can expect the same level of care and quality in every order. -
Experienced Team
With over a decade of experience, you benefit from the extensive industry knowledge we have built.
Our dedicated team works closely with you to provide insights and solutions that drive the success of your project from start to finish. -
Comprehensive Service
From PCB design to manufacturing, assembly, and delivery, we offer a complete one-stop service.
By letting us handle your project from concept to completion, you save time and effort, ensuring a seamless and efficient execution. -
Fast Delivery
Your deadlines are important to us. .
Our efficient production and operations ensure quick turnaround times, allowing you to meet tight schedules without sacrificing quality. -
Rapid Response and Delivery
Your deadlines are important, and we meet them.
With our efficient production processes and optimized logistics, we ensure timely delivery of your orders. -
Guaranteed Satisfaction
Your peace of mind is guaranteed..
As an ISO9001 certified factory, we are committed to delivering top-quality products and maintaining clear communication.
Related Project We had Done
Customer Reviews
engineer
thank you, guys, the boards are really good, i am really happy to receive my boards, the components are perfect!
Operation Manager
South-Electronic is my first PCBA supplier in China. The service and quality are excellent, and the after-sales support is also very impressive. Good Job!
Common Questions
Most Popular Questions
South-Electronic provides Surface Mount Technology (SMT), Through-Hole Technology (THT), Mixed Technology Assembly, and Prototype Assembly, ensuring solutions for a wide range of electronic products.
Absolutely! We provide single PCB assembly samples with fast turnaround and expert support to launch your project smoothly.
The typical delivery time depends on the project size, but South-Electronic is known for its fast turnaround, often completing orders in as little as 5 to 10 business days.
Absolutely. South-Electronic can handle orders ranging from small prototype batches to large-scale production, with the same commitment to quality and precision.
South-Electronic follows strict quality control processes, including ISO9001 certification, multiple inspection stages, and thorough testing to ensure that each assembly meets the highest standards of reliability.
Send us a message
The more detailed you fill out, the faster we can move to the next step.
The Complete Guide For PCB Assembly
Contents
Chapter 1
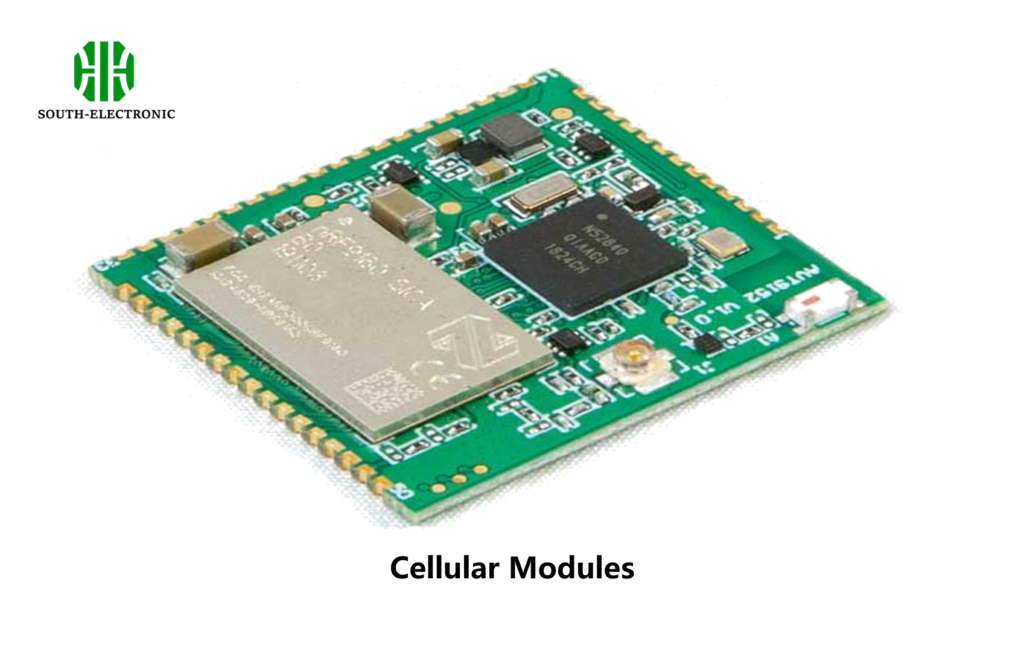
Introduction to PCB Assembly
PCB Assembly: A Brief Overview
PCB (Printed Circuit Board) assembly is the process of mounting and soldering electronic components onto a blank circuit board. This involves placing components like resistors, capacitors, integrated circuits (ICs), and other devices onto a board, connecting them via conductive pathways to create functional electronic circuits. PCB assembly is the backbone of all electronic devices, from everyday gadgets like smartphones and laptops to complex systems in automotive, medical, and aerospace industries.
There are two primary methods for PCB assembly: Surface Mount Technology (SMT), where components are placed directly onto the surface of the board, and Through-Hole Technology (THT), where components are placed through pre-drilled holes on the PCB. Depending on the complexity of the project, these methods can be combined, known as Mixed Technology Assembly.
Why PCB Assembly Matters in Electronics Manufacturing
PCB assembly is crucial because it transforms a plain circuit board into a fully functional electronic device. Without proper assembly, even the best-designed PCB cannot operate. The efficiency, durability, and functionality of electronic products rely heavily on the quality of PCB assembly. Key reasons why PCB assembly is essential in electronics manufacturing include:
- Precision and Functionality: PCB assembly ensures that each component is placed accurately to form circuits that perform specific functions.
- Reliability: Well-assembled PCBs are designed to withstand different environmental conditions, ensuring that devices function as intended over time.
- Scalability: PCB assembly makes it possible to produce both small prototypes and large-scale products with consistent quality, enabling mass production.
- Innovation: Advances in PCB assembly allow for the development of more sophisticated electronic devices with higher functionality in smaller, more compact forms.
In modern electronics manufacturing, PCB assembly is a vital step that bridges the gap between design and the finished product, making it possible to deliver high-performance, reliable devices to market.
Key Terms and Concepts Related to PCB Assembly
To fully understand PCB assembly, it’s important to be familiar with some key terms and concepts:
- Bill of Materials (BOM): A comprehensive list of all the components needed for the PCB assembly process, including part numbers and quantities.
- Stencil: A thin sheet used during the PCB assembly process to apply solder paste to the board’s surface, ensuring accurate placement of the solder.
- Pick and Place Machine: Automated equipment that precisely places components onto the PCB based on the design layout.
- Reflow Soldering: A process in which solder paste is melted to secure SMT components in place.
- Wave Soldering: A process mainly used for THT assembly, where the board is passed over a wave of molten solder to attach components.
- Automated Optical Inspection (AOI): A method of visually inspecting assembled PCBs to detect issues like soldering errors, misalignment, and missing components.
- X-Ray Inspection: A non-destructive testing method used to check for hidden defects in the solder joints, especially for BGA (Ball Grid Array) components.
- Electrostatic Discharge (ESD): The transfer of static electricity, which can damage sensitive components during the assembly process. Proper ESD protection is critical in PCB assembly environments.
Understanding these basics sets the foundation for diving deeper into the intricate processes of PCB assembly, which we’ll explore in the following sections of this guide.
Chapter 2
Types of PCB Assembly
Explanation of Surface Mount Technology (SMT)
SMT, or Surface Mount Technology, is one of the most widely used methods for PCB assembly today. In SMT, components are mounted directly onto the surface of the PCB, without the need for drilled holes. This technique uses tiny, lightweight components known as Surface Mount Devices (SMDs) that are placed onto the board’s surface with precision. The board and components are then passed through a reflow oven, where solder paste is melted, creating secure connections between the components and the board.
Advantages of SMT:
- Compact Design: SMT allows for high-density component placement, which means more components can fit on smaller boards, resulting in more compact and lightweight designs.
- Cost-Effective for Mass Production: The automated nature of SMT is well-suited for high-volume production, reducing labor costs and production time.
- High-Speed Assembly: Using pick-and-place machines, SMT components can be placed quickly and accurately, allowing for faster assembly times compared to manual processes.
- Enhanced Performance: SMT assemblies can handle high frequencies and signals due to their smaller size, which minimizes the parasitic capacitance and inductance.
Typical Applications: SMT is ideal for consumer electronics like smartphones, laptops, and tablets, where miniaturization, speed, and cost-efficiency are critical.
Explanation of Through-Hole Technology (THT)
THT, or Through-Hole Technology, is a traditional method where components have long leads that pass through pre-drilled holes in the PCB. Once the leads are inserted, they are soldered to pads on the opposite side of the board. This method provides a strong mechanical bond between the component and the PCB, making it highly durable and reliable for certain applications.
Advantages of THT:
- Strong Mechanical Bonds: Because the components are physically soldered through the board, THT is known for its durability and is ideal for products that undergo mechanical stress, such as industrial and automotive applications.
- Easier for Prototyping and Testing: Components can be easily inserted and replaced during the design and testing phases, making THT popular for prototyping and small-scale production.
- Heat Resistance: THT components can often withstand higher heat levels, making them suitable for products that will be exposed to harsh environments or high-power applications.
Typical Applications: THT is commonly used in military, aerospace, and industrial equipment, where the reliability of mechanical connections is essential.
Overview of Mixed Technology Assembly
Mixed Technology Assembly involves the combination of both Surface Mount Technology (SMT) and Through-Hole Technology (THT) on a single PCB. This approach is used when a design requires the benefits of both SMT’s compactness and THT’s mechanical durability.
For instance, high-frequency components or fine-pitch devices may be mounted using SMT for their space-saving benefits, while larger or heat-sensitive components like connectors, transformers, and capacitors may be mounted using THT for their robustness.
Advantages of Mixed Technology Assembly:
- Design Flexibility: Mixed assembly offers the best of both worlds, allowing for greater design versatility and the ability to meet the specific requirements of complex devices.
- Optimized Performance: By combining SMT and THT, you can create designs that are both compact and mechanically strong, improving the overall performance of the device.
- Cost-Effective for Specialized Products: Mixed technology is often the solution for industries like automotive or telecommunications, where both miniaturization and reliability are critical, and the extra cost of combining techniques is justified by the performance needs.
Typical Applications: Mixed technology is frequently used in products like automotive control systems, power supplies, and communication devices, where both high-density components and robust mechanical strength are required.
In conclusion, by understanding the differences between SMT, THT, and Mixed Technology Assembly, you can make informed decisions about which method is best suited for your project. Each type of assembly offers unique advantages, whether you’re looking for compact, high-speed solutions or strong, reliable connections. At South-Electronic, we offer expertise in all three assembly types, ensuring that your PCB designs meet the highest standards of performance and quality.

Chapter 3

PCB Assembly Process: Step-by-Step Guide
From Idea to Product
The PCB assembly process takes a well-designed circuit board from concept to a fully functional product. It involves several precise steps to ensure each component is placed accurately and that the connections are secure. Below is a step-by-step walkthrough of the entire process, highlighting each critical stage involved in transforming a bare PCB into a complete electronic product.
Key Stages of PCB Assembly
Solder Paste Application
- Purpose: The first step in the PCB assembly process is applying solder paste to the board. This paste, a mixture of powdered solder and flux, acts as an adhesive for the components.
- Process: A stencil, customized to the PCB design, is placed over the board. The solder paste is then spread across the stencil, filling the exposed areas on the PCB where components will be placed. The stencil is removed, leaving solder paste in precise locations on the board’s pads.
- Importance: Accurate solder paste application is essential to ensure that components will bond correctly to the board and that the soldering process creates strong connections.
Component Placement
- Purpose: This step involves placing all the components on the PCB in their designated locations.
- Process: Automated machines called pick-and-place machines are used to place Surface Mount Devices (SMDs) onto the board, aligning them with the solder paste. These machines work with incredible speed and accuracy, positioning thousands of components in just a few minutes. For Through-Hole Technology (THT), components are inserted manually or by automated machines into pre-drilled holes.
- Importance: Precise placement of components is critical for the PCB to function properly. Misaligned components can lead to poor connections, electrical shorts, or even malfunctioning circuits.
Soldering
- Purpose: Soldering is the process of securing components to the PCB by melting the solder paste and forming electrical connections.
- Reflow Soldering (for SMT): Once the components are placed, the PCB goes through a reflow oven where controlled heat melts the solder paste, creating strong electrical connections between the components and the board. The board is then cooled, allowing the solder to solidify and secure the components in place.
- Wave Soldering (for THT): For Through-Hole components, the PCB is passed over a wave of molten solder. The solder attaches to the component leads that protrude through the board, forming a durable mechanical and electrical bond.
- Importance: Proper soldering ensures a reliable connection between the components and the board. Poor soldering can lead to weak joints, which can fail over time, especially under stress or high temperatures.
Inspection and Quality Control
Purpose: Inspection ensures that the PCB is free from defects and functions as intended.
- Process: After soldering, the PCB undergoes a variety of inspection methods:
- Automated Optical Inspection (AOI): A camera scans the board, comparing it to a predefined model to detect issues like misplaced components, soldering defects, or missing parts.
- X-Ray Inspection: This is used to inspect solder joints beneath components that are difficult to see, like Ball Grid Arrays (BGAs). It helps detect hidden soldering issues like voids or misaligned connections.
- Functional Testing: In this final stage, the PCB is powered on and tested for functionality. Specialized equipment simulates the board’s operating conditions to ensure it performs as expected.
- Importance: Rigorous inspection is vital for catching potential problems early and ensuring the product is reliable and meets quality standards before shipping.
Conclusion
The PCB assembly process involves multiple precise steps, each critical to ensuring that the finished product functions reliably. From the careful application of solder paste to the automated placement of components and various forms of soldering, every stage contributes to the overall quality and performance of the board. Inspection and quality control serve as the final safeguard, ensuring that only fully functional, defect-free PCBs are delivered to customers.
Chapter 4
Common Materials and Components Used in PCB Assembly
When you’re putting together a printed circuit board (PCB), the materials and components you use are critical to the functionality and durability of the final product. The right materials will ensure your PCB can handle the environment and electrical requirements it’s designed for. In this article, we’ll look at the types of boards and components you’ll commonly use, the differences between materials, and what you need to consider when you’re selecting components for your PCB.
Types of Boards and Components
1. Types of PCBs
The base material, or substrate, of your PCB is key to its performance. There are several types of boards depending on what they’re made of and what they’re used for:
- Single-Sided PCBs: These have only one conductive layer and are used for simple, low-density designs.
- Double-Sided PCBs: These have conductive layers on both sides and are good for more complex circuits.
- Multilayer PCBs: These have three or more layers and are used in advanced applications like computers, telecommunications, and medical devices.
2. Common Components in PCB Assembly
There are several key components that you’ll mount on your PCB during the assembly process. Each of these components has a specific purpose:
- Resistors: These control current flow by providing resistance to the circuit.
- Capacitors: These store and release electrical energy. They filter out interference and stabilize voltage.
- Inductors: These store energy in a magnetic field when current passes through them. They’re often used in power supply circuits.
- Integrated Circuits (ICs): These are miniaturized circuits that perform a variety of tasks, from basic logic operations to complex computing functions.
- Diodes: These allow current to flow in one direction. They protect circuits from reverse current.
- Transistors: These switch or amplify electrical signals. They’re commonly used in switching applications.
- Connectors: These provide a physical interface for power or signal input/output. They connect your PCB to other devices or systems.
Differences Between Materials (FR4, Polyimide, etc.)
1. FR4
FR4 is the most common material used for PCBs. It’s a fiberglass-reinforced epoxy laminate known for its durability, moisture resistance, and cost-effectiveness. It’s stable over a wide range of temperatures, so it’s good for most general-purpose PCBs.
- Key Characteristics: Strong mechanical properties, good electrical insulation, affordable.
- Typical Applications: Consumer electronics, telecommunications, and industrial devices.
2. Polyimide
Polyimide is a flexible, heat-resistant material used in high-performance applications. It can be bent and folded, so it’s good for flexible PCBs used in wearable electronics or compact devices.
- Key Characteristics: High-temperature resistance, flexible, chemically stable.
- Typical Applications: Aerospace, automotive, medical devices, and flexible electronics.
3. Metal-Core PCBs
Instead of a traditional non-conductive fiberglass core, these PCBs use a metal core (usually aluminum or copper). They’re great for high-power applications because they dissipate heat really well.
- Key Characteristics: Excellent heat management, high thermal conductivity, durable.
- Typical Applications: LED lighting, power supplies, and automotive electronics.
4. Rogers Material
Rogers is a high-frequency laminate material that’s often used in RF (Radio Frequency) and microwave circuits. It has excellent dielectric properties and low signal loss, which is important for high-speed and high-frequency designs.
- Key Characteristics: Low dielectric loss, stable performance at high frequencies, high thermal conductivity.
- Typical Applications: Telecommunications, aerospace, and high-frequency communication systems.
Considerations for Choosing Components
When you’re choosing components for your PCB assembly, there are several factors you need to consider to make sure your final product performs well and lasts a long time:
1.Thermal Tolerance
Your components need to be able to handle the temperatures they’ll be exposed to during soldering, especially during the reflow soldering process. Make sure your components can handle the heat without degrading.
2.Electrical Requirements
Each component needs to meet the electrical specifications of your circuit, like voltage, current, and frequency requirements. If you over-specify your components, you’ll drive up costs. If you under-specify them, your circuit might not work right.
3.Component Size and Form Factor
Component size is really important, especially for compact or high-density PCBs. You’ll want to use Surface Mount Devices (SMDs) for smaller, more compact designs. You might need Through-Hole components for mechanical strength in larger designs.
4.Environmental Factors
You need to choose components based on the environment your device will be operating in. For example, if your device will be in a high-temperature or high-humidity environment, you’ll need components with higher heat resistance or moisture protection.
5.Cost vs. Performance
High-performance components will be more reliable and last longer, but they’ll also increase the overall cost of your PCB. You need to find the right balance between cost and performance so your project stays within budget and still works right.
Conclusion
Choosing the right materials and components for your PCB assembly is critical to making sure your final product works, lasts, and performs well. Whether you’re using FR4 for its cost-effectiveness, polyimide for its flexibility, or specific components like resistors and ICs, every decision you make affects how your PCB performs. By understanding your options and what you need to think about, you can optimize your PCB designs for your specific application.
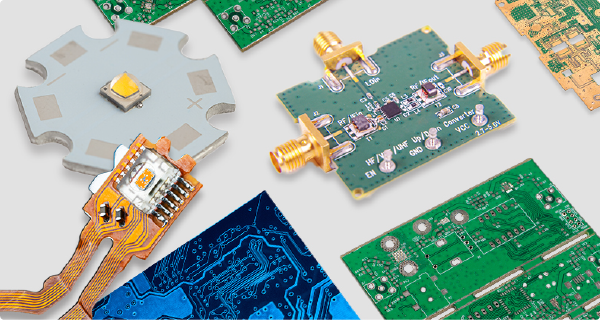
Chapter 5

Prototype PCB Assembly
Why Prototyping is Important in Product Development
Prototype PCB assembly is a critical part of the product development process because it allows designers and engineers to test and validate their designs before moving into full-scale production. By creating a functional prototype, companies can evaluate the performance of the circuit, identify potential issues, and make necessary adjustments early on. This reduces the risk of costly design flaws being discovered after mass production has already begun. Prototyping is important for:
- Design Validation: Prototyping ensures that the design functions as intended and meets all performance requirements before committing to large-scale manufacturing.
- Testing and Evaluation: It allows engineers to test the PCB under real-world conditions to ensure it performs reliably under various operational stresses.
- Iterative Improvements: Prototyping allows the development team to iterate on the design, refining it until it achieves the desired results.
In short, without a robust prototyping phase, there’s a higher risk of failures and unexpected costs during full production.
How PCB Prototyping Reduces Risks
By investing time and resources into prototyping, companies can significantly reduce the risks associated with launching new products. Here are some key ways PCB prototyping helps mitigate risks:
- Identifying Design Flaws Early: Prototyping allows engineers to discover any design flaws before the product reaches the manufacturing stage, avoiding costly recalls, redesigns, or delays in production.
- Cost-Effective Iterations: Prototyping allows companies to make incremental changes to the design without the financial burden of reworking large production batches. The ability to quickly test and modify designs reduces the likelihood of expensive mistakes during full-scale production.
- Ensuring Compatibility with Other Components: A prototype provides the opportunity to test the PCB’s interaction with other system components, ensuring compatibility and reducing the risk of integration problems later in the process.
- Real-World Performance Testing: Prototypes allow for real-world testing of the board’s durability, performance, and resistance to various environmental conditions such as heat, humidity, and vibration. This ensures that the final product will function reliably in its intended environment.
- Streamlining the Manufacturing Process: Prototyping also helps to refine the manufacturing process itself. By understanding how the design performs in small batches, manufacturers can optimize the production workflow for efficiency and cost savings when it comes time for full production.
Rapid Prototyping Services at South-Electronic
At South-Electronic, we understand the critical role prototyping plays in your product’s success, which is why we offer rapid PCB prototyping services designed to meet your tight deadlines. Whether you’re developing a new product or improving an existing one, our prototyping services provide the speed, flexibility, and accuracy you need to move from concept to reality.
- Fast Turnaround: We prioritize rapid delivery of your prototypes so you can stay on track with your project timeline. Our efficient production processes allow us to deliver fully assembled prototypes in as little as 5-10 business days.
- Custom Solutions: We tailor our prototyping services to match your specific needs, offering both Surface Mount Technology (SMT) and Through-Hole Technology (THT) assembly options.
- High Precision: With our state-of-the-art equipment and experienced team, we ensure that each prototype meets the highest standards of quality, allowing you to confidently test your designs.
- Support for Iteration: Whether you need a single prototype or multiple iterations, we offer flexible services that allow you to make incremental changes to your design before moving into full production.
By partnering with South-Electronic for your prototyping needs, you ensure that your PCB designs are fully validated, tested, and ready for mass production.
Conclusion
Prototype PCB assembly is a critical step in product development, offering a low-risk, cost-effective way to test and refine designs before full-scale production. By leveraging prototyping, companies can avoid costly mistakes, ensure compatibility, and optimize their products for real-world performance. With South-Electronic’s rapid prototyping services, you get the speed and quality you need to bring your designs to life—faster and more efficiently.
Chapter 6
Challenges and Solutions in PCB Assembly
PCB assembly is a complicated process, and even small problems can cause big issues in the final product. Knowing the common challenges and implementing effective solutions is key to making sure you get high-quality PCBs. In this section, we’ll look at some of the most common assembly issues—like shorts, solder bridges, and misalignment—and talk about best practices for avoiding these problems.
Common Assembly Issues
1.Short Circuits
What It Is: A short circuit happens when unintended connections are made between two or more points in a circuit, allowing current to flow along an unplanned path. This can cause components to not work, generate too much heat, or even permanently damage the PCB.
Causes: Shorts are often caused by bad soldering, where too much solder connects two pins that are next to each other, or by traces on the board that aren’t routed correctly.
2.Solder Bridges
What It Is: A solder bridge is a type of short circuit that happens when solder connects two or more pads or pins that it shouldn’t. This can make the board not work or work incorrectly.
Causes: Solder bridges usually happen because too much solder was put on or because the spacing between the leads of the component wasn’t enough when the board was assembled.
3.Component Misalignment
What It Is: Misalignment happens when components aren’t put in the right place on the PCB. Even small misalignments can cause problems with the board’s performance, especially in circuits that are complex or have high frequencies.
Causes: Misalignment can happen because the solder paste wasn’t put on right, the components weren’t placed correctly, or the components moved around during the reflow soldering process.
4.Cold Solder Joints
What It Is: Cold solder joints happen when the solder doesn’t melt all the way during the soldering process, which makes a weak or brittle connection. These joints can cause the board to work sometimes and not work other times.
Causes: Cold solder joints usually happen because the soldering iron didn’t get hot enough, the person soldering didn’t do it right, or low-quality solder paste was used.
5.Component Shifting During Reflow
What It Is: During reflow soldering, components can move out of place if the solder paste melts too fast or if the reflow profile isn’t set up right. This can make bad connections and cause short circuits.
Causes: Component shifting usually happens because the reflow temperature wasn’t set right or the solder paste wasn’t the right thickness.
Solutions and Best Practices to Avoid These Problems
1.Preventing Short Circuits
Solution: The best way to stop short circuits is to design the PCB right so that they don’t happen. Making sure there’s enough space between traces and components will lower the chance of unintended connections. During assembly, using the right amount of solder paste and using a machine to look at the board (automated optical inspection, or AOI) can help find shorts early.
Best Practice: Use software to check the design and make sure the traces are set up right and don’t overlap. Use strict quality control measures, like looking at the board and using AOI, to find shorts before the board is finished.
2.Avoiding Solder Bridges
Solution: One way to stop solder bridges is to use stencils that control how much solder paste is put on the board. Making sure the pads are designed right and have enough space between the pins is also important. Also, making sure the reflow process is set up right and using the right reflow profile will keep too much solder from spreading.
Best Practice: Use good stencils and keep the paste application equipment clean so the solder paste is spread out evenly. Make sure the components you use are designed right and have enough space between the pins so you don’t get solder bridges.
3.Correcting Component Misalignment
Solution: Using machines to put the components on the board will make sure they go in the right place. Making sure the machines are set up right will put the components in the right place. If you have to put the components on by hand, use tools that let you put them in the right place.
Best Practice: Keep the machines set up right so they put the components in the right place. Use AOI to check the board and make sure the components are in the right place before the last soldering step. Put marks on the board to help the machines put the components in the right place.
4.Preventing Cold Solder Joints
Solution: To stop cold solder joints, you have to make sure you use enough heat when you solder. Using good solder paste and making sure the reflow process is set up right will make sure the solder melts all the way and sticks to the board.
Best Practice: Check the temperature in the reflow oven to make sure it’s right for the solder paste. Use good flux and solder materials to make sure the solder sticks to the board and you don’t get cold joints. Check all the solder joints by looking at them or using AOI to find any weak connections.
5.Preventing Component Shifting
Solution: Make sure the temperature in the reflow oven is set up right so the solder paste doesn’t melt too fast and make the components move. Use solder paste that’s the right thickness so the components stay in place when the solder melts.
Best Practice: Set up the reflow process to match the components and solder paste you’re using. Make sure the machine puts enough pressure on the components when it puts them on the board so they don’t move around when you solder them.
Conclusion
Even though PCB assembly is hard, knowing about common issues like short circuits, solder bridges, and misalignment helps you use the right solutions to keep these problems from happening. By designing the board right, being careful when you put the components on, and checking everything before you finish, you can make sure you get good, reliable PCBs. At South-Electronic, we use the best technology and practices to make sure your PCB assemblies meet the highest standards and don’t have any problems with assembly or defects.
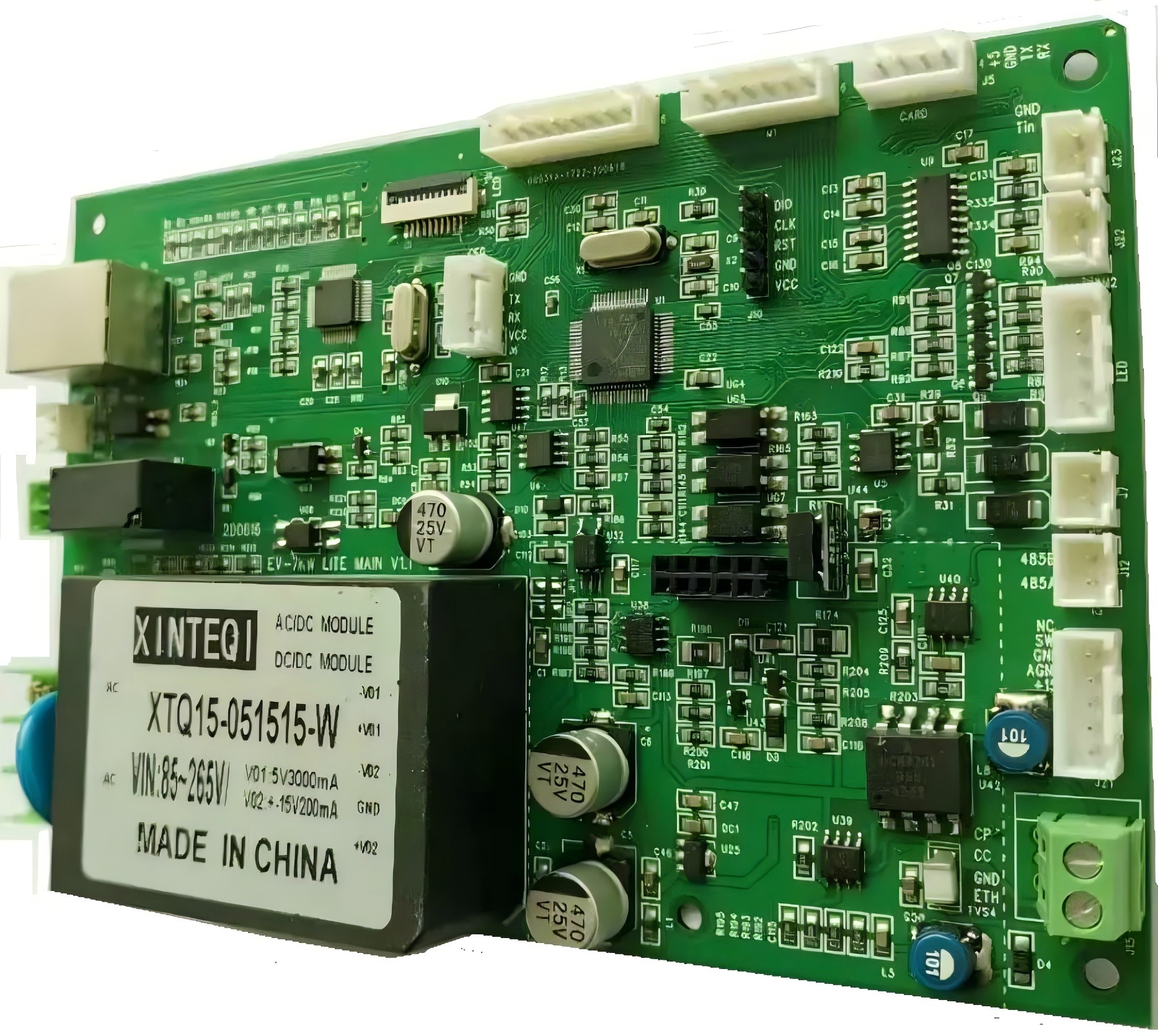
Chapter 7
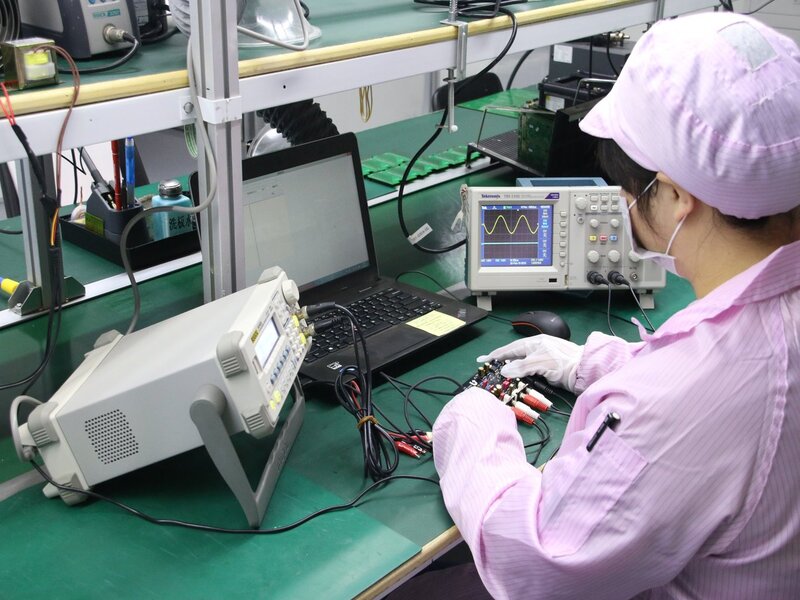
Quality Control in PCB Assembly
Why Quality Control Processes are Important
Quality control (QC) is a critical part of PCB assembly. It ensures that the final product meets the design specifications and performance requirements. Even small defects in the assembly process can cause circuits to malfunction, reduce reliability, or completely fail. That’s why it’s important to have strong quality control processes in place to identify and address any issues early in the production cycle.
Quality control not only improves the overall reliability and performance of the PCB, but it also reduces costs associated with product returns, repairs, and recalls. By investing in thorough QC procedures, manufacturers can deliver consistent, high-quality products that meet industry standards and customer expectations.
Different Testing Methods
1.Visual Inspection
What it is: Visual inspection is the first step in identifying visible defects like misaligned components, solder bridges, missing components, or surface damage.
How it works: Trained technicians manually inspect the PCB to look for obvious assembly errors. They may also use magnification tools to get a closer look at fine-pitch components and solder joints.
Why it’s important: Visual inspection is good for catching surface-level defects, but it may not catch hidden issues, especially in complex, high-density PCBs. That’s why it’s often used in combination with automated methods.
2.Automated Optical Inspection (AOI)
What it is: AOI is an automated method used to inspect PCBs for defects like incorrect component placement, poor solder joints, or missing parts.
How it works: AOI uses high-resolution cameras to take images of the PCB. The system then compares these images to a predefined reference model to look for discrepancies. AOI systems can inspect PCBs much faster than manual inspection, making it ideal for high-volume production.
Why it’s important: AOI reduces the risk of human error and ensures that defects are caught early in the assembly process. It’s especially useful for complex boards with a lot of components.
3.X-Ray Inspection
What it is: X-ray inspection is used to detect hidden defects in solder joints and components that aren’t visible to the naked eye, like those under Ball Grid Arrays (BGAs).
How it works: An X-ray machine scans the PCB, providing images of the internal structure. This allows technicians to inspect the quality of solder joints, check for voids, and make sure all connections are properly made, even under components.
Why it’s important: X-ray inspection is critical for ensuring the reliability of PCBs with advanced packaging, like BGAs or multi-layer boards, where defects can be hard to detect with other methods.
Certifications to Look For
When choosing a PCB assembly partner, it’s important to make sure they follow recognized industry standards and certifications. These certifications are a sign of quality and reliability. Here are some key certifications to look for:
1.ISO9001 Certification
What it is: ISO9001 is an internationally recognized standard for quality management systems (QMS). It ensures that a company follows consistent, repeatable processes to meet customer requirements and improve quality over time.
Why it’s important: ISO9001 certification means the PCB manufacturer has a high level of process control, documentation, and continuous improvement, which translates to higher product quality and customer satisfaction.
2.IPC Standards
What they are: IPC standards define the quality criteria for electronic assemblies. IPC-A-610, for example, sets the acceptability standards for PCB workmanship, covering things like soldering, component placement, and rework.
Why they’re important: A manufacturer that follows IPC standards builds PCBs to a high level of quality, minimizing defects and improving overall reliability.
3.RoHS Compliance
What it is: The Restriction of Hazardous Substances (RoHS) directive restricts the use of certain hazardous materials (like lead, mercury, and cadmium) in electronic products.
Why it’s important: RoHS compliance means the PCBs are environmentally friendly and meet regulatory requirements, which is especially important for products that will be sold in markets like the European Union.
Conclusion
Effective quality control processes are the foundation of reliable PCB assembly. From manual visual inspections to advanced techniques like AOI and X-ray inspection, these methods ensure that defects are caught early and resolved before final production. Additionally, certifications like ISO9001 and IPC standards show a manufacturer’s commitment to quality. At South-Electronic, we follow these rigorous standards, so you can be confident that every PCB we produce meets the highest levels of quality and reliability.
Chapter 8
Choosing the Right PCB Assembly Partner
When you’re looking for a company to handle your PCB assembly, you need to make sure you’re choosing the right one. The right company will make sure your boards are put together correctly, delivered on time, and meet the quality standards you need. To make the right choice, you need to consider several factors when you’re looking at different companies.
What to Look for in a PCB Assembly Company
Experience
- Why It’s Important: A company that has a lot of experience will know the industry, the assembly process, and the problems that can come up with your project. They’ve worked with a lot of different industries and know how to make the assembly process work for you.
- What to Look for: Look for a company that has a lot of experience doing PCB assembly for your industry. Look for case studies or testimonials that show they’ve done a good job for other people.
Flexibility
- Why It’s Important: Not every project is the same, so you need a company that can be flexible. Whether you need a small batch for a prototype or a big order for a production run, the company you choose should be able to handle it.
- What to Look for: Make sure the company can do a lot of different things, like Surface Mount Technology (SMT) and Through-Hole Technology (THT), and that they can handle small orders and big ones.
Certifications
- Why It’s Important: Certifications like ISO9001 and IPC standards show that the company is serious about quality. They show that the company has a good quality control system and that they follow the rules that the industry has set up. You want to make sure you get boards that are good quality and that you can trust.
- What to Look for: Make sure the company has the right certifications, like ISO9001 for quality management and IPC-A-610 for assembly standards. Certifications show that the company is serious about quality and that they do a good job.
How to Choose a PCB Assembly Company
Look at What They Can Do
Look at the company’s equipment, technology, and the things they can do. Do they have the latest technology, like automated pick-and-place machines, AOI, and X-ray inspection? If they do, they can handle complicated designs and big orders.
Ask About Lead Times
You need to get your boards fast, so ask the company how long it takes them to do a job. Can they do it fast if you need it? If they can do rapid prototyping and get things done fast, they’re a good choice if you need something quickly.
Read Reviews and Case Studies
A good company will have good reviews. Look for reviews, testimonials, or case studies that show the company does a good job and delivers on time and on budget. This will give you a good idea of what the company is like and if they’re good to work with.
Get a Quote and Compare Prices
You don’t want to pay too much, but you also don’t want to get bad boards. Look at the prices from different companies, but make sure you’re comparing the same things. Make sure the price matches what the company can do and the quality they offer.
Why South-Electronic Is the Right Choice
At South-Electronic, we know that quality, flexibility, and reliability are important to you. Here’s why we’re the right choice for your project:
- We Know What We’re Doing: We’ve been doing PCB assembly for more than ten years, and we’ve worked with a lot of different industries, like automotive, medical, and consumer electronics. We know how to do the job right and make sure your boards are good quality.
- We Can Do It All: We can handle small orders and big ones, and we can do everything from rapid prototyping to big orders. We can do whatever you need for your project.
- We Do It Right: We’re ISO9001 certified, and we follow IPC-A-610 standards to make sure your boards are good quality. We check them with Automated Optical Inspection (AOI) and X-ray testing to make sure they’re good before we send them to you.
- We Do It Fast: We know you need your boards fast, so we have a system that gets them to you on time. We can do rapid prototyping so you can test your design before you make a big order.
When you choose South-Electronic, you’re choosing a company that will help you get your project done right.
Conclusion
Choosing the right company to do your PCB assembly is important. You need to look at things like experience, flexibility, and certifications, and you need to look at different companies to see who’s the best. When you choose South-Electronic, you’re not just getting a company that does PCB assembly—you’re getting a partner who will help you get your project done right, on time, and with good quality.
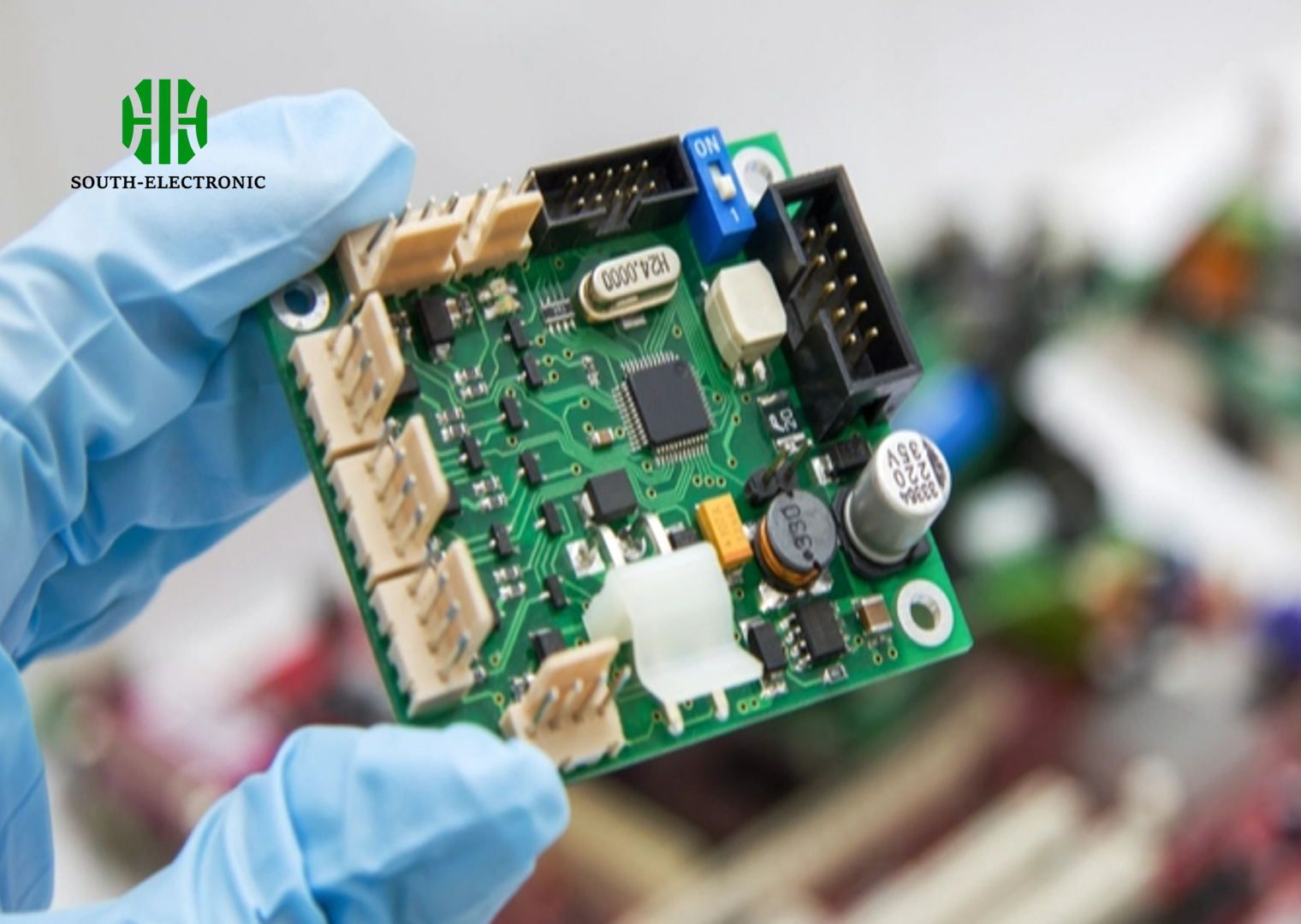
Chapter 9

PCB Assembly for Different Industries
PCB assembly is a versatile process that can be tailored to meet the unique needs of various industries. Different sectors, such as automotive, medical, and consumer electronics, require distinct design considerations, quality standards, and performance criteria. Below, we explore how PCB assembly varies across these industries and the specific requirements each sector demands.
Automotive Industry
PCBs play a critical role in modern vehicles, powering everything from engine management systems to advanced driver assistance systems (ADAS). The automotive industry requires highly reliable PCBs that can withstand harsh environmental conditions, including extreme temperatures, vibrations, and exposure to moisture.
Specific Requirements for Automotive PCBs:
- High Reliability and Durability: Automotive PCBs must operate flawlessly in tough environments, making durability a top priority.
- Heat Resistance: The ability to withstand high temperatures is essential, especially in engine control units (ECUs) and powertrain systems.
- Electromagnetic Compatibility (EMC): Automotive electronics must meet strict EMC standards to avoid interference with other electronic systems in the vehicle.
- Compliance with Automotive Standards: PCBs must comply with industry-specific standards, such as ISO/TS 16949 and AEC-Q100, which ensure the highest levels of quality and reliability.
Medical Industry
In the medical field, PCBs are used in a wide range of devices, from diagnostic machines to life-saving equipment like pacemakers and defibrillators. PCBs for medical applications must meet stringent quality and reliability standards, as even minor malfunctions can have serious consequences.
Specific Requirements for Medical PCBs:
- High Precision and Reliability: Medical devices demand precision and reliability, as they directly affect patient care and safety.
- Biocompatibility and Sterilization: PCBs used in implants or devices that interact with the human body must be biocompatible and capable of withstanding sterilization processes.
- Miniaturization: Many medical devices require compact PCBs to fit into small, portable devices without sacrificing performance.
- Compliance with Medical Standards: Medical PCBs must adhere to certifications such as ISO 13485, which outlines specific standards for quality management in the medical device industry.
Consumer Electronics Industry
In consumer electronics, such as smartphones, tablets, and wearable devices, PCBs need to balance high performance with cost-efficiency. Consumer electronics demand rapid innovation and constant upgrades, making flexible, scalable PCB assembly solutions essential.
Specific Requirements for Consumer Electronics PCBs:
- Miniaturization and High-Density Components: Devices like smartphones and wearables require PCBs with small form factors and high component density to support advanced features in compact designs.
- Cost-Effectiveness: Given the competitive nature of the consumer electronics market, manufacturers must optimize PCB production to minimize costs without compromising quality.
- High-Speed and High-Frequency Capability: With the growing demand for faster, more powerful devices, PCBs must support high-speed data transmission and efficient power management.
- Rapid Prototyping and Time-to-Market: Consumer electronics require quick iterations and fast production cycles to stay ahead of market trends, making rapid prototyping services crucial.
Conclusion
Each industry has unique demands that shape how PCBs are designed, assembled, and tested. Whether it’s the extreme durability required in automotive electronics, the high precision needed for medical devices, or the compact designs demanded by consumer electronics, PCB assembly must be tailored to meet these specific requirements. At South-Electronic, we have the expertise and capabilities to deliver PCB assemblies that meet the strict standards of various industries, ensuring reliability, performance, and compliance with industry-specific regulations.
Chapter 10
The Future of PCB Assembly
Trends and Innovations in PCB Assembly
The PCB assembly industry is always changing, driven by technology and market demands. One of the biggest trends is miniaturization. As electronics get smaller and more powerful, the need for high-density, compact PCB designs is growing. This is especially true in consumer electronics, medical devices, and wearables, where space-saving innovations like flexible PCBs and multilayer designs are essential.
Another trend is environmentally friendly manufacturing. As regulations get stricter, more companies are using eco-friendly materials, lead-free processes (RoHS compliance), and sustainable production methods to reduce the environmental impact of PCB assembly.
Finally, high-speed data transmission and 5G technology are shaping the future of PCBs, especially in telecommunications, automotive, and industrial applications. These innovations require PCBs with excellent signal integrity, high-frequency performance, and improved thermal management.
Impact of Automation and AI in PCB Manufacturing
Automation and artificial intelligence (AI) are changing PCB assembly, making it more efficient, accurate, and scalable. Automated pick-and-place machines, soldering systems, and inspection technologies like AOI (Automated Optical Inspection) reduce human error and speed up production. This level of automation allows manufacturers to produce complex, high-volume orders with precision and low costs.
AI is also important in PCB design and defect detection. Machine learning algorithms optimize board layouts, predict potential issues, and streamline testing. AI-powered inspection systems detect defects, like solder bridges or misaligned components, faster than human inspectors, leading to higher yields and fewer production delays.
These advancements make it easier for companies to meet the demand for faster time-to-market, increased product complexity, and more affordable solutions—without sacrificing quality.
Final Thoughts on Choosing the Right PCB Assembly Service
As PCB assembly changes with new trends and technology, it’s important to choose the right assembly partner. When selecting a PCB assembly provider, look for a company that offers advanced manufacturing capabilities, like automated assembly, AI-driven testing, and the flexibility to handle small and large production runs.
Your partner should also have industry experience, a commitment to quality (with certifications like ISO9001 and IPC standards), and the ability to meet your industry’s requirements, whether you’re in automotive, medical, or consumer electronics.
At South-Electronic, we stay ahead of industry trends and innovations to meet your PCB assembly needs. Whether you need rapid prototyping, high-volume production, or advanced testing solutions, we can help with precision, speed, and reliability.
Conclusion
The future of PCB assembly is influenced by miniaturization, environmental sustainability, and advancements in automation and AI. These trends make the industry more efficient and precise, allowing manufacturers to meet the demands of complex and compact electronics. By choosing the right PCB assembly partner—one that embraces innovation and prioritizes quality—you can ensure your products are built to meet the challenges of tomorrow’s market.
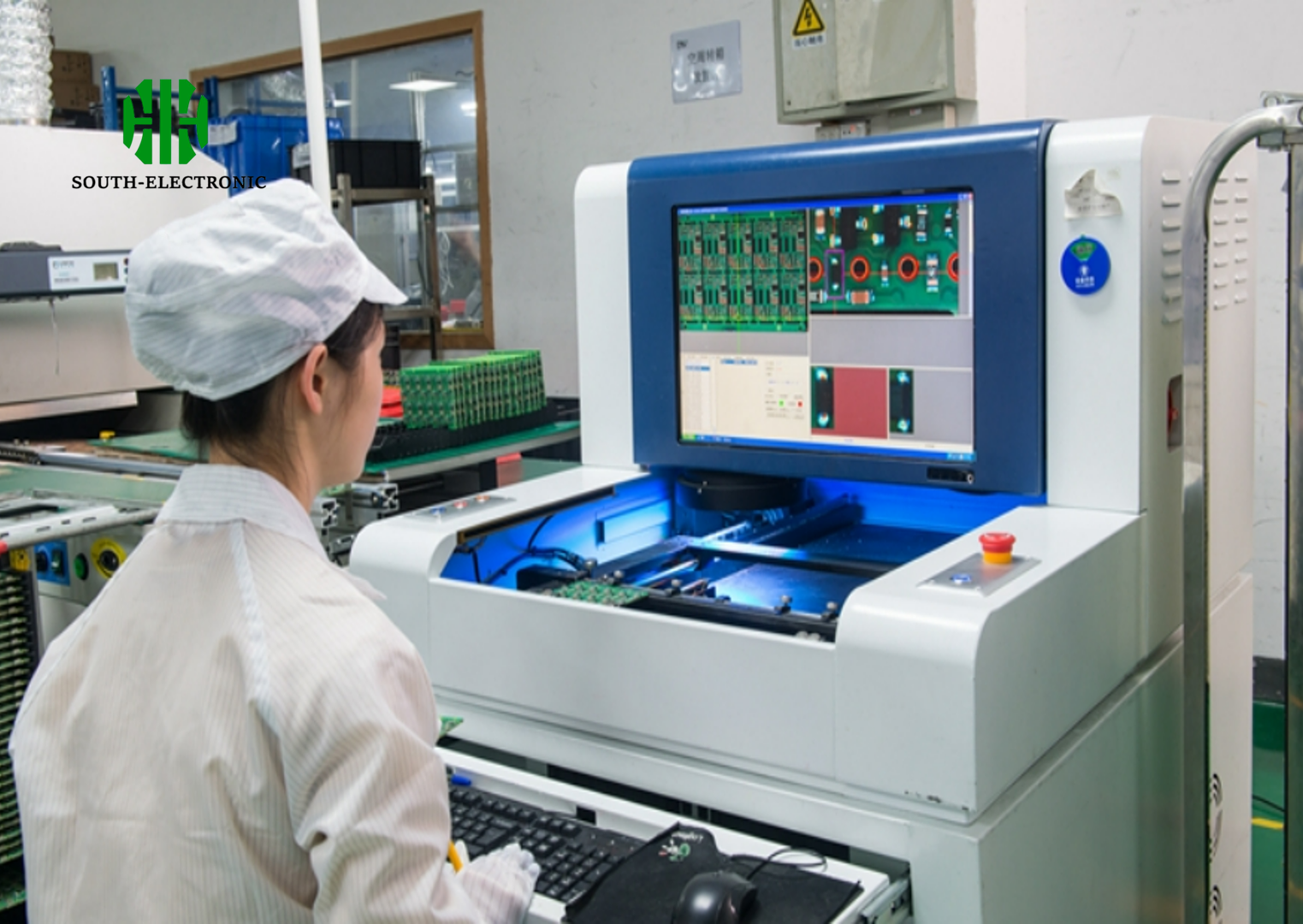
Get in touch
Where Are We?
Industrial Park, No. 438 Donghuan Road, No. 438, Shajing Donghuan Road, Bao'an District, Shenzhen, Guangdong, China
Floor 4, Zhihui Creative Building, No.2005 Xihuan Road, Shajing, Baoan District, Shenzhen, China
ROOM A1-13,FLOOR 3,YEE LIM INDUSTRIAL CENTRE 2-28 KWAI LOK STREET, KWAI CHUNG HK
service@southelectronicpcb.com
Phone : +86 400 878 3488
Send us a message
The more detailed you fill out, the faster we can move to the next step.
