PCB Manufacturing Supplier
South-Eelctronic
Choose South-Electronic for unmatched quality, reliability, and value. We offer a complete one-stop PCB Manufacturing service, from initial design to final delivery, ensuring accuracy, speed, and adherence to the highest industry standards.
Your Trusted PCB Manufacturing Partner
Welcome to South-Electronic, where you’ll find all the PCB solutions you need for today’s electronics industry. We make high-quality PCBs that work great and are perfect for your projects.
You can count on South-Electronic for consistent, high-quality PCBs. They’re not only reliable, but they’re also small and fit into tight spaces. You can use them for all kinds of things. Work with us and you’ll be successful.

Rigid PCB
Rigid PCBs are great for standard electronics. They're strong and durable, so they'll last a long time and work reliably in all sorts of everyday applications. They're also a cost-effective option for devices that need tough circuit boards.

Flexible PCB
Flexible PCBs are super adaptable, so they're perfect for situations where space is tight or the design is really complex. They can bend, which means you can come up with all sorts of cool, space-saving layouts without sacrificing electrical performance.
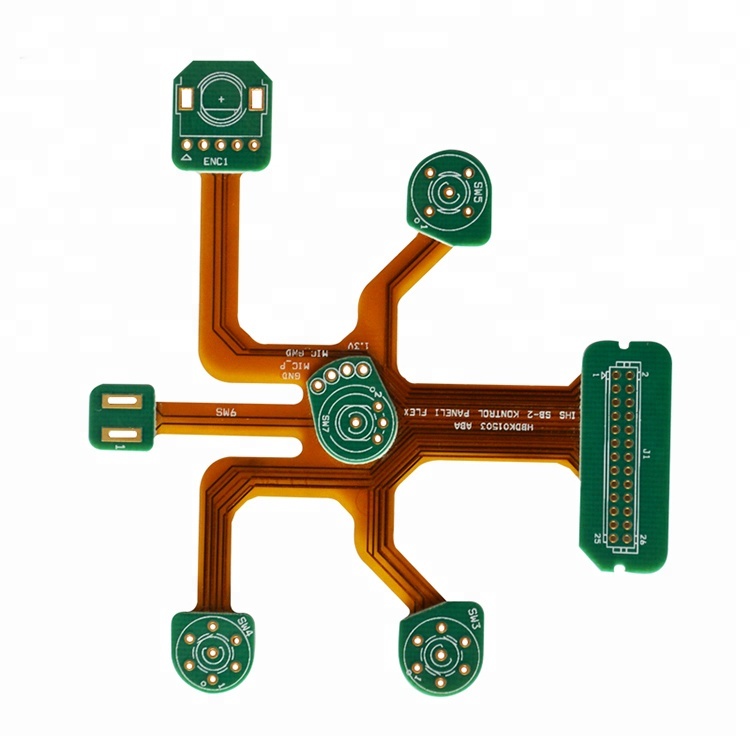
Rigid-Flex PCB
Rigid-Flex PCBs are a mix of hard boards and flexible circuits. They're great for advanced applications where you need both flexible connections and stable components. You get the best of both worlds.

High-Frequency PCB
High-frequency PCBs are made to work really well in high-frequency environments, like RF and microwave circuits. They make sure signals stay strong and don't get lost, so they're perfect for things like telecom, radar systems, and other demanding applications.
Why Choose South-Electronic?
-
Dedicated Support
You have our support from start to finish.
From your initial inquiry to the final product delivery, our team of experts ensures a smooth process with personalized support. -
Flexibility in Ordering
You get exactly what you need, no matter the order size
Whether it’s a single piece or thousands, we’re ready to fulfill your order with the same dedication to quality and precision -
Experienced Team
You benefit from decades of expertise.
Our team of industry veterans ensures your PCB needs are met with innovative solutions and top-tier production. -
Comprehensive Service
Get everything you need in one place.
From design to delivery, our advanced technology and manufacturing capabilities guarantee that your order is completed to the highest standards. -
Fast Delivery
YYou stay on schedule with our fast turnaround times.
Our streamlined production ensures fast turnaround times, so you get your products when you need them, without delays.
Related Project We had Done
Customer Reviews
engineer
thank you, guys, the boards are really good, i am really happy to receive my boards, the components are perfect!
Operation Manager
South-Electronic is my first PCBA supplier in China. The service and quality are excellent, and the after-sales support is also very impressive. Good Job!
Common Questions
Most Popular Questions
South-Electronic manufactures a wide range of PCBs to suit various project needs, including FR4 PCBs , Flexible PCBs (FPC), Rigid-Flex PCBs, Aluminum PCBs (ALU PCB), Copper Core PCBs, and Rogers PCBs. If you need a simple single-layer board or a complex multilayer design, we got you covered. We make high-quality boards for all kinds of industries.
At South-Electronic, we take quality seriously. We have a strict quality control process that we follow at every step of production, from selecting the materials to doing the final inspection. Our factory is certified with ISO, RoHS, and UL, and we test every PCB that we make. We do electrical tests and functional tests on every board.
Yep, we offer a 5-year warranty from the date you get your stuff, covering any manufacturing defects or quality issues. If anything comes up during that time, we'll work with you to fix it, including offering repairs or replacements to make sure you're happy.
South-Electronic accept a wide range of file formats for PCB design submissions, including Gerber files, Eagle, Altium, and CAD formats. If you have your design in another format, please contact us, and we’ll help you with compatibility to make sure everything goes smoothly.
Sure, you can ask for samples to test before you place a big order. That way, you can make sure our PCBs are good quality and work the way you want them to.
You bet! South-Electronic is a specialist in handling complex PCB projects and offers full customization to meet your specific requirements. Whether you need multilayer boards, HDI, or flexible PCB solutions, our experienced team and advanced technology are fully equipped to bring your vision to life. We provide tailored solutions that meet both your technical and commercial needs.
Send us a message
The more detailed you fill out, the faster we can move to the next step.
The Complete Guide For PCB Manufacturing
Contents
Chapter 1

Introduction to PCB Manufacturing
PCBs are the backbone of modern electronics. They’re the platform that connects and supports electronic components. The process of PCB manufacturing turns raw materials into intricate circuits that make devices work. From smartphones and computers to medical devices and automotive systems, PCBs are in almost every electronic product we use today.
The manufacturing process has several stages. Design, fabrication, assembly, and testing all contribute to the final quality and performance of the PCB. Understanding PCB manufacturing is important for engineers, designers, and businesses because it affects how reliable a product is, how much it costs to make, and how long it takes to get to market. As technology gets better, we want better PCBs. Manufacturers are using new techniques and materials to meet the higher standards of the industry. This guide will tell you about PCB manufacturing. It will explain the processes, applications, and future trends that are changing the industry.
Chapter 2
Types of PCB Manufacturing
When it comes to PCB manufacturing, it’s important to understand the different types so you can choose the right one for your specific application. The main categories of PCBs include:
- Rigid PCBs: These are the most common type of PCB and are made from solid substrates that provide structural support. They’re typically used in devices where space and weight are critical, such as smartphones and computers. They’re durable and reliable, making them ideal for high-volume production.
- Flexible PCBs: These boards are made from flexible materials, so they can bend and conform to different shapes. Flexible PCBs are often used in wearable devices, medical equipment, and small electronic products where space is at a premium. They’re lightweight, which can help reduce the overall weight of the product.
- Rigid-Flex PCBs: These boards combine the benefits of both rigid and flexible PCBs. They have both rigid and flexible sections and are used in complex applications that require high reliability and lower assembly costs, such as aerospace and military electronics. They’re versatile and allow for innovative designs without sacrificing performance.
- Multilayer PCBs: These boards have multiple layers of circuitry stacked together, separated by insulating material. Multilayer PCBs allow for higher circuit density and are commonly found in advanced electronics like servers, routers, and high-performance computing devices. They help minimize space while maximizing functionality.
- High-Frequency PCBs: These PCBs are specifically designed to handle high-frequency signals and are essential in applications like telecommunications and RF devices. They require specialized materials and manufacturing techniques to ensure signal integrity and minimize loss.
- Aluminum PCBs: These PCBs have a metal substrate and are great for heat dissipation, making them ideal for LED applications and high-power devices. Their thermal management capabilities help extend the life of components and improve performance.
By understanding the different types of PCB manufacturing, you can make informed decisions based on your specific needs. Whether you prioritize durability, flexibility, or high-frequency performance, each type of PCB offers unique advantages for different applications, enhancing the overall functionality and reliability of your product.

Chapter 3

Manufacturing Processes of PCB Manufacturing
The manufacturing of printed circuit boards (PCBs) involves several critical stages, each essential for ensuring the quality and functionality of the final product. Here’s a comprehensive overview of the main processes involved:
1. Design and Layout
Engineers use advanced PCB design software, such as Altium Designer or Eagle, to create the schematic diagram and layout, define electrical connections, component placements, and routing paths. Thorough simulations and design rule checks (DRCs) are conducted to identify potential issues before moving to production.
2. Printing the Design
The design is transferred to a copper-clad laminate using photolithography. A photosensitive film is applied to the laminate, then exposed to ultraviolet (UV) light. This process hardens the film in areas where the circuit design is present, creating a mask for the subsequent etching.
3. Etching
Unexposed copper is chemically removed, leaving only the desired copper traces. This process defines the circuitry and ensures electrical connectivity. Etching can be done through various methods, including chemical or laser etching, depending on the design’s complexity.
4. Drilling
Holes are drilled into the PCB for component leads and vias. Automated drilling machines ensure precision and efficiency. Vias are especially important for multilayer boards, enabling electrical connections between different layers.
5. Plating
The PCB undergoes electroplating, where a thin layer of copper is deposited into the drilled holes and over the surface. This step enhances conductivity and strengthens connections between layers. Additional finishes, such as nickel or gold, may also be included.
6. Solder Mask Application
A solder mask is applied to protect the copper traces from oxidation and prevent solder bridges during assembly. This green epoxy layer ensures that only designated areas are soldered, enhancing PCB reliability and functionality.
7. Silkscreen Printing
A silkscreen layer is printed onto the PCB to add component designators, logos, and other critical information. This step aids assembly personnel in identifying components quickly, reducing the risk of errors during assembly.
8. Surface Finish
The final surface finish is applied to enhance solderability and protect exposed copper pads from oxidation. Common finishes include Hot Air Solder Leveling (HASL), Electroless Nickel Immersion Gold (ENIG), and Organic Solderability Preservative (OSP).
9. Testing
The PCBs undergo extensive testing to identify defects. Electrical tests, visual inspections, and automated optical inspections (AOI) ensure compliance with stringent quality standards.
10. Assembly
Components are placed and soldered onto the PCB, accomplished through surface mount technology (SMT) or through-hole technology. Automated pick-and-place machines are commonly used for SMT assembly, allowing for high-speed and accurate component placement.
By understanding these manufacturing processes, businesses can appreciate the complexity involved in PCB production. Each stage requires meticulous attention to detail and adherence to industry standards, ultimately contributing to the reliability and performance of the final product. Continuous advancements in technology and manufacturing techniques enhance the efficiency and capabilities of PCB manufacturing, meeting the ever-growing demands of the electronics industry.
Chapter 4
PCB Manufacturing Testing and Quality Assurance
Testing and quality assurance are super important in the PCB manufacturing process. They make sure that the final products meet the required specifications and work well in their intended applications. Here’s a detailed look at the types of testing involved and the importance of reliability testing.
Types of Testing
Functional Testing
- Purpose: This test makes sure that the PCB works as intended under normal operating conditions. It checks the functionality of each circuit and component on the board.
- Process: Functional testing can involve applying power to the PCB and measuring the output to make sure it matches expected values. You can simulate various conditions to see how the board performs in real-world scenarios, like voltage levels, timing, and signal integrity.
- Tools Used: Automated test equipment (ATE), oscilloscopes, and multimeters are commonly used to do these tests accurately and efficiently.
In-Circuit Testing (ICT)
- Purpose: ICT checks individual components and interconnections while the PCB is still being made. This helps you find defects early.
- Process: Test probes connect to specific points on the PCB to measure resistance, capacitance, and inductance. This method can quickly find issues like shorts, opens, and incorrect component values.
- Advantages: ICT is super efficient, so you can find problems before you assemble the boards, saving time and money.
Automated Optical Inspection (AOI)
- Purpose: AOI looks at the PCB visually to find defects in soldering, alignment, and component placement.
- Process: High-resolution cameras take pictures of the PCBs and compare them to predefined templates. If there are any differences, you get an alert to look closer.
- Benefits: AOI is good at catching surface defects that might not show up in electrical testing, so you know the boards are both visually and functionally good.
X-ray Inspection
- Purpose: This method is mostly used for multilayer PCBs and components with hidden solder joints, like BGA (Ball Grid Array) packages.
- Process: X-ray machines take pictures that show the inside of the PCB, so you can look at solder joints and component integrity without taking the board apart.
- Importance: It helps you find possible reliability problems caused by hidden defects that could cause the board to fail when it’s being used.
Environmental Testing
- Purpose: Environmental tests check how the PCB performs under different environmental conditions, like extreme temperatures, humidity, and vibration.
- Process: You subject the boards to thermal cycling, humidity tests, and vibration tests to see how they do in conditions they might see in their application.
- Significance: This testing is really important for applications in harsh environments, so you know the PCB can handle the conditions without losing performance.
Importance of Reliability Testing
Reliability testing is super important to make sure that PCBs will work right for the whole time they’re supposed to, especially in critical applications like aerospace, automotive, and medical devices.
For products that have to work in tough environments or that are going to be used for a long time, reliability testing makes sure that they’ll keep working. This is especially important in industries like automotive and aerospace, where failures can be really bad.
In summary, you have to do a lot of testing and quality assurance to make PCBs. By using different testing methods and making reliability a priority, you can make sure that your products work and that people can depend on them, which is what you need to do in the electronics business today.
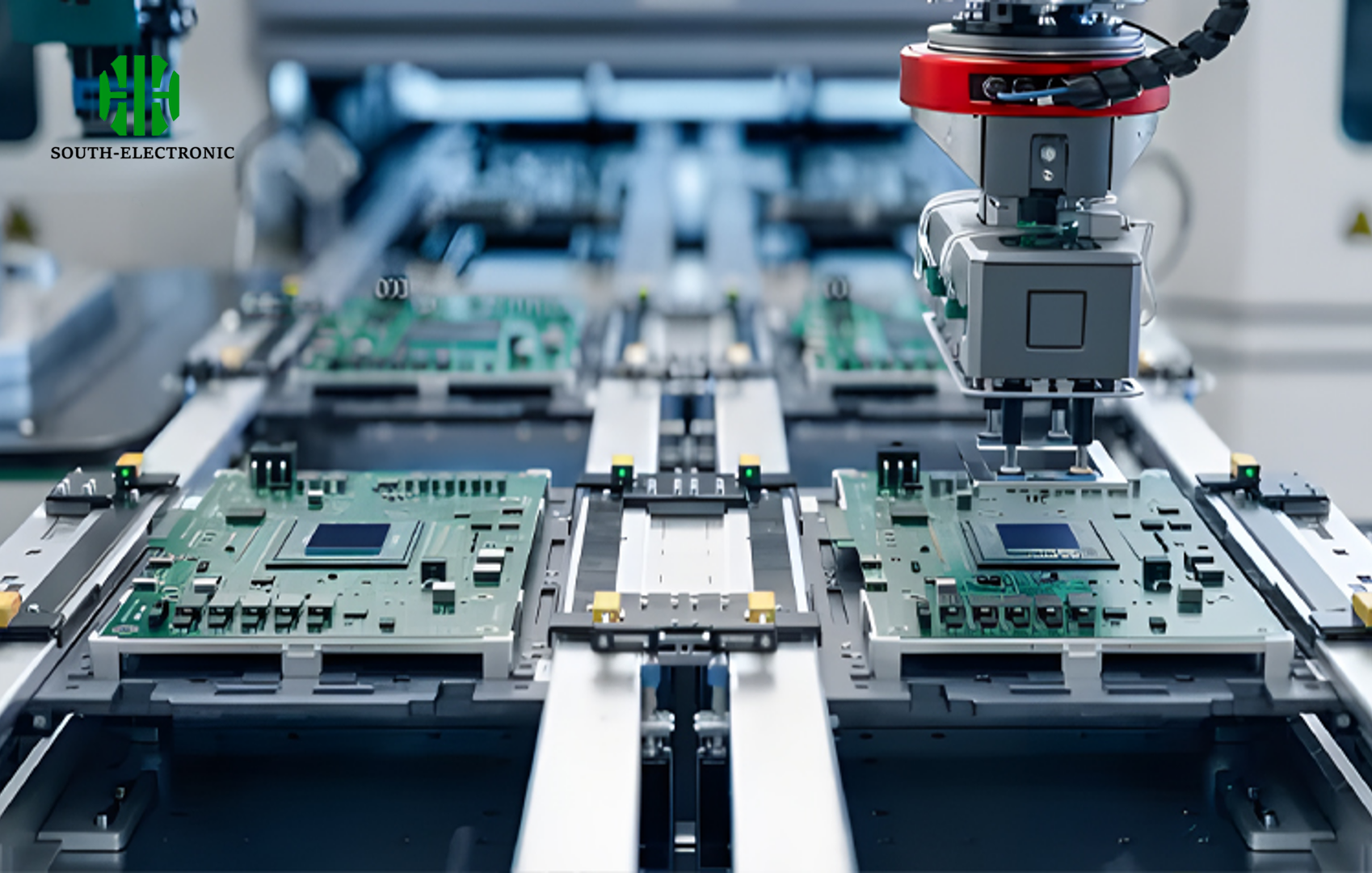
Chapter 5

Design Considerations for PCB Manufacturing
When it comes to PCB manufacturing, design is key. A well-designed PCB ensures functionality and enhances manufacturability and reliability. Here are the key aspects of PCB design, including software options and design considerations.
Software Options
Altium Designer:
- Overview: Altium Designer is a comprehensive PCB design software widely used in the industry. It offers an integrated environment for schematic capture, PCB layout, and component management.
- Features: Its advanced features include real-time design rule checks, 3D visualization, and extensive libraries for components. This software is particularly beneficial for complex designs and multilayer boards.
Eagle:
- Overview: Autodesk’s Eagle is a popular choice among hobbyists and professionals alike due to its user-friendly interface and powerful features.
- Features: Eagle includes schematic capture, PCB layout tools, and a rich library of components. Its affordability makes it an excellent option for small-scale projects and startups.
KiCad:
- Overview: KiCad is an open-source PCB design tool that has gained traction for its robustness and zero cost.
- Features: It provides a complete set of tools for PCB design, including 3D modeling and an extensive library manager. KiCad is suitable for both beginners and experienced designers looking for a free alternative.
OrCAD:
- Overview: OrCAD is a suite of tools designed for professional electronic design automation (EDA). It’s particularly strong in circuit simulation and analysis.
- Features: With its advanced simulation capabilities and comprehensive library management, OrCAD is favored for high-complexity designs and industries that require extensive verification.
PADS:
- Overview: PADS from Mentor Graphics is tailored for professional PCB design, focusing on high-speed and complex applications.
- Features: It offers advanced routing capabilities, signal integrity analysis, and a strong focus on manufacturability, making it ideal for engineers working on sophisticated electronic systems.
Design Considerations
Layer Count:
- Importance: The number of layers in a PCB impacts its complexity, cost, and performance. Designers must carefully determine the appropriate layer count based on the circuit’s requirements and available budget.
- Recommendation: Aim for the minimum number of layers necessary to achieve design goals, as more layers can increase manufacturing costs and complexity.
Component Placement:
- Overview: Strategic placement of components is essential for optimizing performance and manufacturability. Components should be arranged to minimize trace lengths and avoid interference.
- Consideration: High-frequency components should be placed close to their respective connections to reduce inductance and improve signal integrity.
Trace Width and Spacing:
- Guidelines: The width of traces affects current-carrying capacity and resistance. Designers must adhere to guidelines based on the anticipated current load and ensure adequate spacing between traces to prevent short circuits.
- Tools: Use online calculators or design software features to determine appropriate trace widths according to IPC standards.
Via Types and Placement:
- Types: Different via types, such as through-hole, blind, and buried vias, have unique implications for PCB design. Designers should choose the type that best suits the layout and manufacturing process.
- Consideration: Minimize via usage when possible, as each via introduces additional cost and can affect signal integrity.
Thermal Management:
- Importance: PCBs must dissipate heat effectively to prevent component failure. Proper thermal management strategies, such as thermal vias, heat sinks, and adequate spacing, should be implemented.
- Recommendation: Analyze thermal profiles during the design phase to identify potential hotspots and adjust layouts accordingly.
Signal Integrity:
- Considerations: For high-speed designs, maintaining signal integrity is crucial. Designers should consider factors such as impedance control, differential signaling, and proper grounding techniques.
- Simulation: Utilize simulation tools to analyze signal behavior and identify potential issues before manufacturing.
- Design Rule Checks (DRCs):
- Overview: Running DRCs within design software helps identify violations of manufacturing constraints, such as spacing and width discrepancies.
- Importance: Conducting thorough DRCs minimizes the risk of manufacturing defects, ensuring that the design is viable for production.
Documentation and BOM (Bill of Materials):
- Overview: Comprehensive documentation, including a detailed BOM, is essential for successful manufacturing. The BOM should include part numbers, specifications, and sourcing information for each component.
- Consideration: Clear documentation aids in assembly, troubleshooting, and future design revisions.
In summary, effective PCB design involves selecting the right software and considering various design elements. By paying attention to these considerations, designers can create PCBs that are not only functional but also optimized for manufacturing and long-term reliability.
Chapter 6
Applications of PCB Manufacturing
Printed Circuit Boards (PCBs) are the backbone of modern electronics, used in countless devices across a range of industries. Their versatility and reliability enable a wide range of applications, as outlined below.
1. Consumer Electronics
- Overview: PCBs are the foundation of consumer electronics, powering devices such as smartphones, tablets, laptops, and televisions.
- Applications: They enable connections between components like processors, memory, and displays, ensuring efficient operation and user experience.
2. Automotive Industry
- Overview: The automotive industry increasingly relies on PCBs to support advanced electronic systems.
- Applications: PCBs are used in various applications, including engine control units (ECUs), infotainment systems, safety features like airbags and anti-lock braking systems, and electric vehicle components. Their reliability is critical for enhancing vehicle performance and safety.
3. Medical Devices
- Overview: In the medical field, PCBs are essential for a range of diagnostic and therapeutic equipment.
- Applications: They are found in devices such as MRI machines, ultrasound equipment, patient monitoring systems, and wearable health trackers. The high standards of quality and reliability in medical applications ensure patient safety and effective treatment.
4. Telecommunications
- Overview: PCBs play a vital role in the telecommunications industry, supporting the infrastructure for communication networks.
- Applications: They are used in routers, switches, cell towers, and satellite systems, enabling seamless data transmission and connectivity. The need for high-speed and reliable communication drives innovation in PCB design for this sector.
5. Industrial Equipment
- Overview: Many industrial applications depend on PCBs for automation and control systems.
- Applications: PCBs are used in robotics, manufacturing machinery, process control systems, and instrumentation. Their durability and performance are essential for efficient operations in demanding environments.
6. Aerospace and Defense
- Overview: The aerospace and defense industries require high-performance PCBs for critical applications.
- Applications: PCBs are used in avionics, navigation systems, radar equipment, and missile guidance systems. The reliability and precision of these boards are paramount in ensuring mission success and safety.
7. IoT Devices
- Overview: The Internet of Things (IoT) has driven the development of a wide range of connected devices, heavily reliant on PCBs.
- Applications: Smart home devices, wearable technology, and industrial IoT applications use PCBs for communication, processing, and sensor integration. The compact design and energy efficiency of PCBs support the growing demand for IoT solutions.
8. Renewable Energy
- Overview: The shift towards renewable energy sources has increased the demand for PCBs in this sector.
- Applications: PCBs are used in solar inverters, wind turbine controllers, and energy storage systems. Their ability to handle high currents and operate in various environmental conditions is vital for efficient energy conversion and management.
9. Computing and Networking
- Overview: PCBs are crucial in the computing and networking sectors, where high performance is essential.
- Applications: They are integral to servers, data centers, and networking equipment, facilitating data processing and transmission. Advanced PCB designs help meet the demands for speed, capacity, and reliability.
10. Agricultural Technology
- Overview: PCBs are increasingly used in agricultural technology to enhance productivity and efficiency.
- Applications: Smart farming solutions, including automated irrigation systems, drone technology, and precision agriculture sensors, rely on PCBs for their electronic functions. These innovations help optimize resource use and improve crop yields.
In conclusion, the applications of PCB manufacturing are vast and diverse, spanning numerous industries and technologies. As electronics continue to evolve, the demand for innovative PCB designs will grow, enabling even more advanced functionalities across various sectors. The adaptability and reliability of PCBs make them essential components in the modern technological landscape.
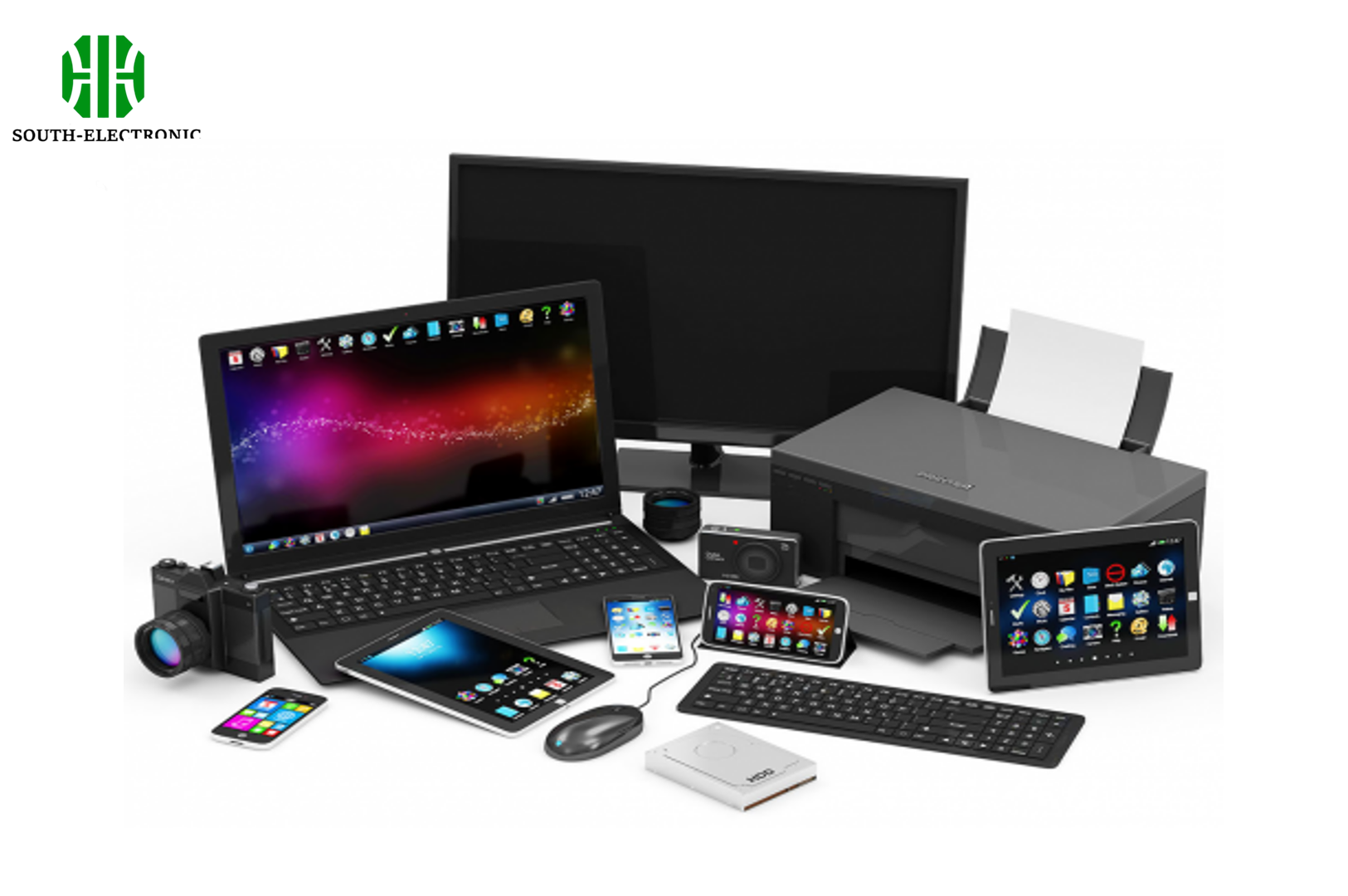
Chapter 7
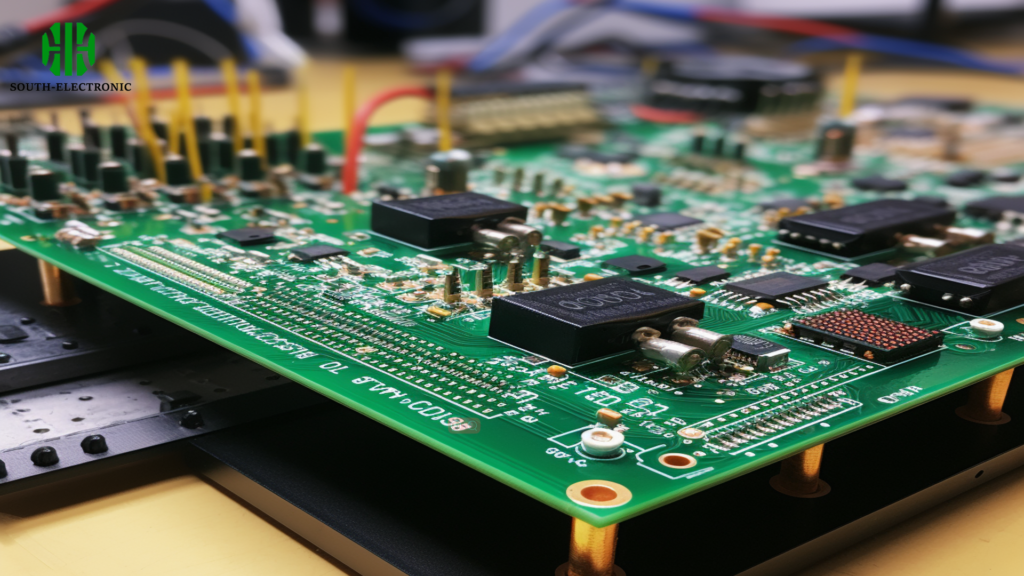
Advantages of PCB Manufacturing
PCBs are important in electronic devices because they make them work better, last longer, and cost less. Here are some reasons why:
1. Smaller is better
- Space Efficiency: PCBs let us make electronic products smaller and lighter. This is important in consumer electronics, where people want things to be small.
- Layering: We can make PCBs with lots of layers. This lets us put more parts in a smaller space. It also lets us make things that do more stuff.
2. They last longer
- Durability: PCBs are made from tough materials. They can take a lot of abuse and still work. This is important in cars and medical devices.
- Consistency: We make PCBs the same way every time. This means they always work the way they are supposed to. This is important in things that have to work right all the time.
3. They cost less
- We can make a lot of PCBs at once. This makes them cost less. This lets us make a lot of electronic devices without spending a lot of money.
- We can put a lot of parts on a PCB. This makes it easier to put things together. It also makes it faster and cheaper to make electronic devices.
4. They are easy to fix
- PCBs are easy to look at and see how they work. This makes it easy to fix them when they break. This is important in factories and stores.
- We can take parts off of a PCB and put new ones on. This makes it easy to fix them. This is important in factories and stores.
5. They can change
- We can change a PCB to make it do new things. This is important in electronics because things change all the time.
- We can make a lot of PCBs or just a few. This is important because sometimes we need a lot of something and sometimes we don’t.
6. They work better
- PCBs let us make electronic devices that work better. This is important in things like phones and computers.
- PCBs let us make electronic devices that send signals better. This is important in things like phones and computers.
7. They stay cool
- PCBs can be made to stay cool. This is important because heat can make electronic devices stop working.
- PCBs can be made from materials that can take a lot of heat. This is important because heat can make electronic devices stop working.
8. They can be different
- We can make a PCB that does what we want it to do. This is important because different things need different PCBs.
- We can put a lot of different parts on a PCB. This is important because different things need different parts.
9. They are made by machines
- Machines can make PCBs better than people can. This is important because we want electronic devices to work right.
- Machines can make PCBs without making mistakes. This is important because we want electronic devices to work right.
PCBs are important in electronic devices because they make them work better, last longer, and cost less. This is why we use them in everything from cars to phones to computers.
Chapter 8
Understanding PCB Manufacturing Costs
Understanding the costs associated with PCB manufacturing is crucial for businesses looking to optimize their production processes and improve profit margins. There are a lot of things that go into the cost of making a PCB, like materials, labor, overhead, and other things that are specific to your design and how you’re going to use the PCB.
Material Costs
- Base Materials: The primary material used in PCBs is typically fiberglass epoxy resin (FR-4), which is relatively inexpensive. However, the choice of substrate can significantly affect costs. For instance, high-frequency PCBs may require materials like Rogers or Taconic, which are more expensive.
- Copper Foil: Copper is a critical component of PCBs, used for the conductive pathways. The cost of copper can fluctuate based on market conditions, impacting overall manufacturing costs.
- Solder Mask and Silkscreen: The application of solder masks (which protect the copper traces) and silkscreen layers (which provide labeling) also adds to material costs. Specialty colors or finishes may increase expenses further.
- Component Costs: The type and quantity of electronic components mounted on the PCB play a significant role in overall costs. High-quality components or those with specific performance requirements tend to be more expensive.
- Additional Materials: Other materials, such as adhesives, thermal management materials (like thermal pads), and protective coatings, can add to costs, especially in high-performance applications.
Labor and Overhead Expenses
- Labor Costs: Labor expenses include wages for skilled workers involved in PCB design, manufacturing, and assembly. Skilled labor, particularly in high-tech areas like surface mount technology (SMT) assembly, commands higher wages due to the expertise required.
- Training and Expertise: Continuous training for workers to keep up with evolving technologies and manufacturing processes is another labor-related cost that companies must consider.
- Overhead Costs: These encompass all indirect expenses related to the manufacturing process, including facility rent, utilities, equipment maintenance, and administrative expenses. A well-maintained facility with advanced machinery will incur higher overhead costs but can lead to greater efficiency and quality.
- Equipment and Technology: The investment in manufacturing equipment, such as pick-and-place machines, soldering systems, and testing equipment, also contributes to costs. High-quality, automated systems can lead to long-term savings despite higher initial investments.
- Quality Assurance: Implementing quality control measures, such as testing and inspection, incurs additional costs but is essential for ensuring the reliability of the PCBs. Investing in quality assurance can reduce costs associated with defective products and rework.
Additional Cost Factors
- Design Complexity: More complex PCB designs, including multilayer boards, intricate routing, and specialized components, can increase manufacturing costs due to the need for advanced design tools and more intensive labor.
- Volume of Production: The scale of production plays a significant role in cost per unit. Larger production runs typically reduce the cost per PCB due to economies of scale, while small batch productions can be significantly more expensive on a per-unit basis.
- Lead Time and Urgency: Rush orders may incur higher costs due to expedited manufacturing and shipping processes. Businesses must weigh the benefits of quicker delivery against increased expenses.
- Supply Chain Factors: Fluctuations in the supply chain, including shortages of raw materials or components, can affect pricing and lead times, impacting overall manufacturing costs.
If you need your PCBs right away, it’s going to cost more money to make them and ship them to you faster. You have to decide if it’s worth it to get them faster or if you can wait and save some money.
Sometimes, you can’t get the stuff you need to make your PCBs. That can make it cost more money and take longer to make your PCBs.
So, if you want to know how much it costs to make a PCB, you have to look at all the stuff I just talked about. If you do a good job with all of it, you’ll be able to make more PCBs and make more money.
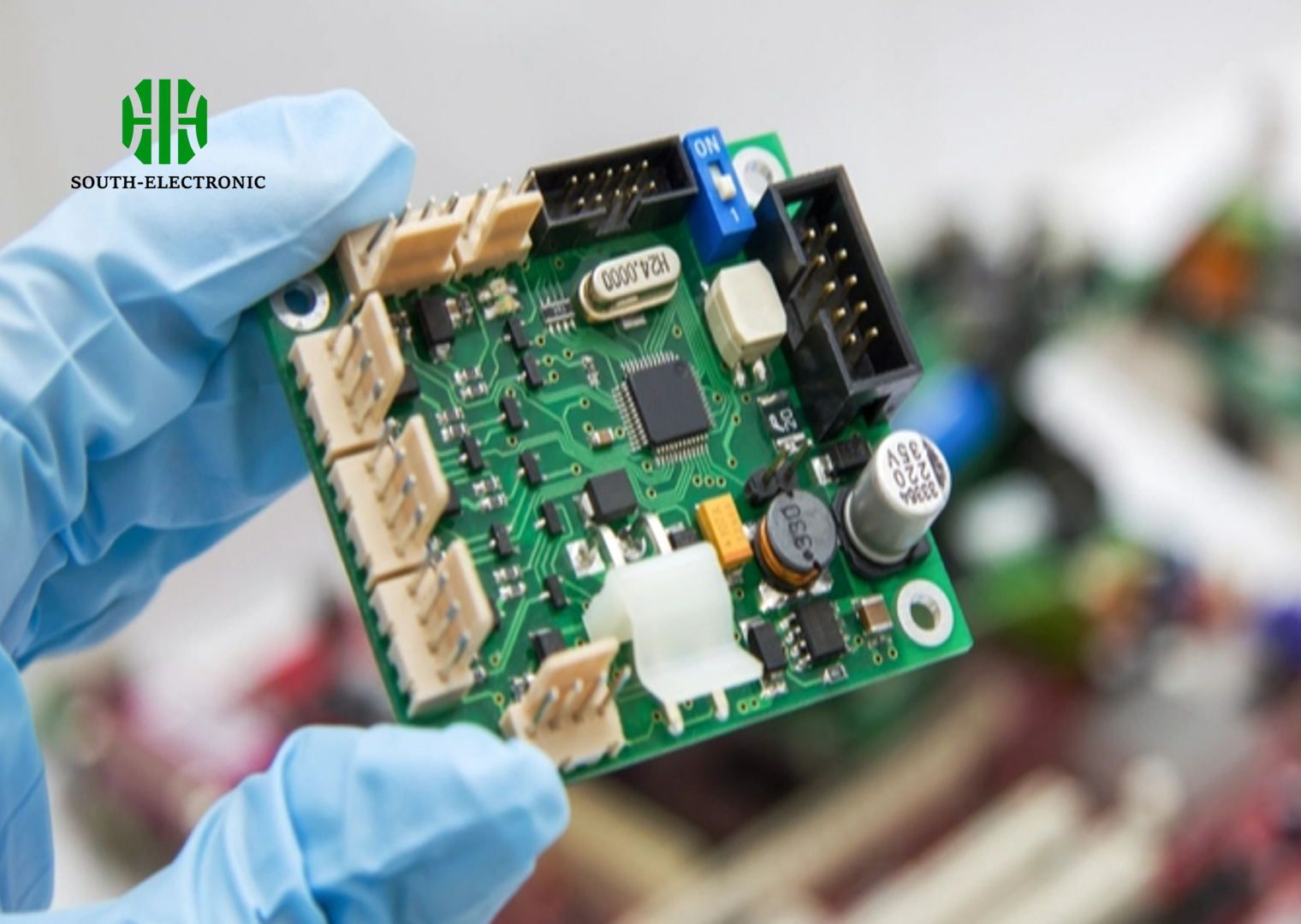
Chapter 9

Future Trends in PCB Manufacturing Technology
The PCB manufacturing industry is poised for significant advancements driven by innovations in materials and technology, as well as a growing emphasis on sustainability. Here are the key trends shaping the future:
Innovations in Materials and Technology
- Advanced Materials: The development of new materials, such as high-frequency substrates and flexible materials, will enhance PCB performance, especially for 5G and IoT applications. These materials can improve signal integrity and thermal management.
- 3D Printing: Additive manufacturing techniques are emerging as a viable option for producing PCBs, allowing for rapid prototyping and customized designs without the need for traditional manufacturing processes.
- Smart PCBs: Integration of sensors and intelligence into PCBs will enable real-time monitoring and adaptive functionalities, supporting the growing demand for smart devices and automation in various industries.
- Embedded Components: The trend of embedding components within the PCB itself, such as capacitors and resistors, will continue to grow. This reduces assembly time and enhances reliability by minimizing interconnections.
Sustainability in PCB Production
- Eco-Friendly Materials: The industry is increasingly focusing on biodegradable and recyclable materials to reduce environmental impact. This includes alternatives to traditional FR-4 substrates and lead-free solder materials.
- Waste Reduction Practices: Manufacturers are adopting lean manufacturing techniques to minimize waste throughout the production process. This includes optimizing designs to reduce material usage and implementing recycling programs for scrap materials.
- Energy-Efficient Processes: The adoption of energy-efficient manufacturing technologies will reduce the carbon footprint of PCB production. This includes using renewable energy sources and optimizing energy consumption in facilities.
- Regulatory Compliance: As environmental regulations become stricter, PCB manufacturers will need to comply with standards such as RoHS (Restriction of Hazardous Substances) and WEEE (Waste Electrical and Electronic Equipment) to ensure sustainable practices.
In summary, the future of PCB manufacturing will be characterized by innovative materials and technologies that enhance performance, alongside a strong focus on sustainability to meet environmental challenges and regulatory requirements. These trends will not only improve product quality but also contribute to a more sustainable electronics industry.
Chapter 10
Choosing the Right PCB Manufacturing Supplier
Selecting the right PCB manufacturing supplier is crucial for ensuring quality, reliability, and efficiency in your production process. A successful partnership can significantly impact your product’s performance and your business’s bottom line. Here are key factors to consider when making this important decision:
1. Quality Standards
- Certifications: Look for suppliers with industry-standard certifications, such as ISO 9001 or IPC-A-600. These certifications indicate a commitment to quality management and adherence to manufacturing standards.
- Quality Control Processes: Investigate the supplier’s quality assurance processes, including testing methods and inspection protocols. A robust quality control system helps prevent defects and ensures reliable performance.
2. Experience and Expertise
- Industry Experience: Choose a supplier with a proven track record in PCB manufacturing for your specific industry. Experience in handling similar projects can provide insights into best practices and potential challenges.
- Technical Expertise: Assess the supplier’s engineering capabilities and design support. A knowledgeable partner can offer valuable input during the design phase, improving manufacturability and reducing costs.
3. Production Capabilities
- Technology and Equipment: Evaluate the supplier’s manufacturing technology and equipment. Advanced machinery and processes can lead to higher precision and better quality.
- Capacity: Ensure the supplier can meet your production volume needs, whether you require small batches or large-scale production. Flexibility to scale production as needed is essential.
4. Lead Times and Reliability
- Turnaround Times: Consider the supplier’s lead times for production and delivery. Reliable timelines are crucial for maintaining your project schedules and meeting market demands.
- Consistency: Research the supplier’s reputation for consistency in delivery and product quality. Customer reviews and testimonials can provide insights into their reliability.
5. Cost and Pricing Structure
- Transparent Pricing: Request detailed quotes that outline all costs, including tooling, setup, and additional fees. This transparency helps avoid unexpected expenses later in the process.
- Value for Money: While cost is important, prioritize suppliers that offer the best value rather than simply the lowest price. Consider the total cost of ownership, including quality and potential rework costs.
6. Customer Support and Communication
- Responsive Communication: A good supplier should have a responsive communication channel for addressing inquiries and issues promptly. Effective communication helps build trust and facilitates collaboration.
- Technical Support: Assess the level of technical support offered. Suppliers that provide design assistance and troubleshooting can help streamline the manufacturing process.
In summary, choosing the right PCB manufacturing supplier involves careful consideration of quality standards, experience, production capabilities, and customer support. By evaluating these key factors, you can establish a successful partnership that enhances your production efficiency and product quality, ultimately leading to greater business success.

Get in touch
Where Are We?
Industrial Park, No. 438 Donghuan Road, No. 438, Shajing Donghuan Road, Bao'an District, Shenzhen, Guangdong, China
Floor 4, Zhihui Creative Building, No.2005 Xihuan Road, Shajing, Baoan District, Shenzhen, China
ROOM A1-13,FLOOR 3,YEE LIM INDUSTRIAL CENTRE 2-28 KWAI LOK STREET, KWAI CHUNG HK
service@southelectronicpcb.com
Phone : +86 400 878 3488
Send us a message
The more detailed you fill out, the faster we can move to the next step.
