¿Qué es el material de PCB?
El material de PCB es el material del que están hechas las placas de circuito impreso. Es bueno manejando el calor, evitando fugas de electricidad y siendo resistente. Hay diferentes tipos de material de PCB, como FR4, Rogers, poliimida y otros. Cada tipo de material es bueno para diferentes cosas.
¿Qué es el material FR4 en PCB?
FR4 es un material de PCB popular porque es confiable y económico. Está hecho colocando tela de fibra de vidrio tejida en resina epoxi, por lo que no se incendia. Cumple con el estándar de seguridad contra incendios UL 94V-0, por lo que es seguro de usar en electrónicos.
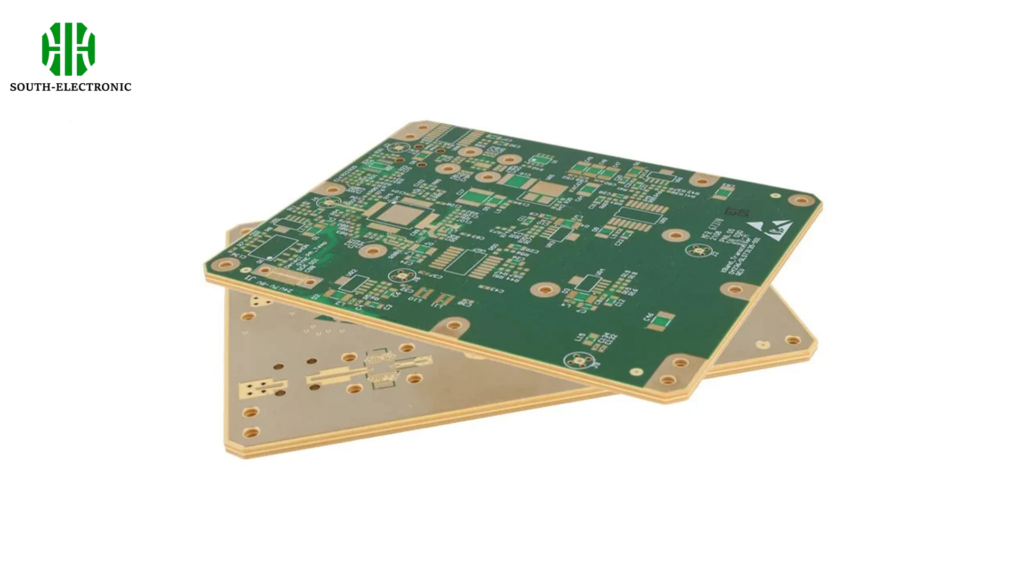
Propiedades del material FR4
- Aislamiento Eléctrico: Excelentes propiedades de aislamiento eléctrico.
- Resistencia Mecánica: Alta resistencia mecánica y rigidez.
- Estabilidad Térmica: Buena estabilidad térmica, adecuada para procesos de soldadura estándar.
- Resistencia a la Humedad: Baja absorción de humedad, asegurando un rendimiento estable en condiciones húmedas.
Aplicaciones de FR4
- Equipos de Comunicación: Routers, switches y antenas.
- Hardware de Computadora: Placas base, tarjetas gráficas y CPUs.
- Electrónica de Consumo: Smartphones, tabletas y consolas de juegos.
- Electrónica Industrial: Sistemas de control y equipos de automatización.
- Dispositivos Médicos: Equipos de diagnóstico y sistemas de imágenes médicas.
Consideraciones de diseño para FR4
- Espesor y Revestimiento de Cobre: El revestimiento de cobre estándar varía de 1 a 3 onzas por pie cuadrado.
- Acabados Superficiales: Los acabados comunes incluyen HASL, ENIG y OSP.
- Temperatura de Operación: Adecuado para aplicaciones hasta 150°C con variantes de alto rendimiento disponibles para temperaturas más altas.
¿Qué son los PCBs de Rogers?
Los materiales de Rogers son laminados de alta frecuencia conocidos por su rendimiento superior en aplicaciones de RF y microondas. Estos materiales se utilizan cuando el rendimiento eléctrico alto y la baja pérdida de señal son críticos.
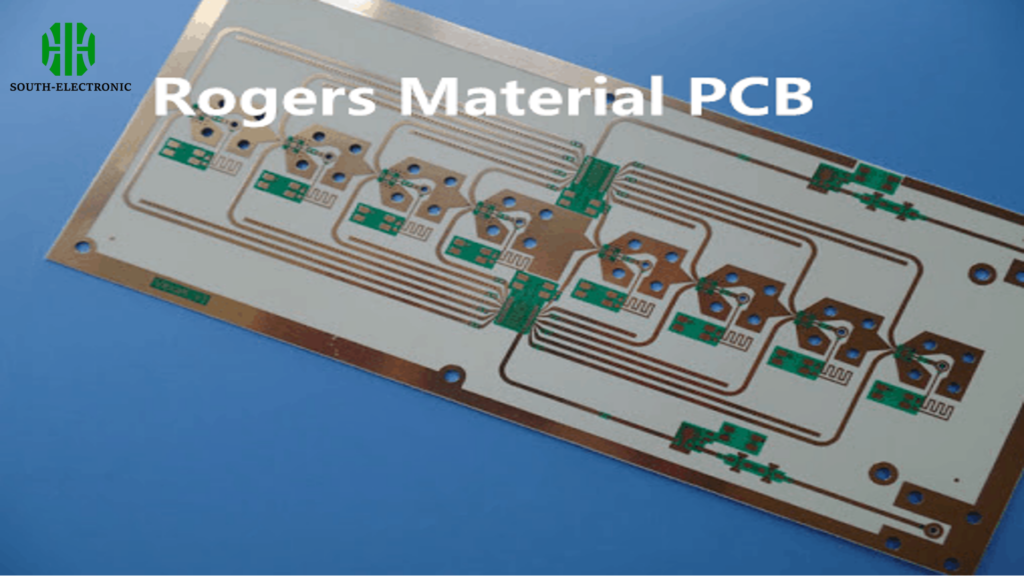
Propiedades del material Rogers
- Pérdida Dieléctrica Baja: Pérdida de señal mínima, lo que lo hace ideal para aplicaciones de alta frecuencia.
- Conductividad Térmica: Alta conductividad térmica, mejorando la gestión térmica.
- Constante Dieléctrica Estable: Propiedades dieléctricas consistentes en un amplio rango de frecuencias.
- Absorción de Humedad Baja: Mejor rendimiento en ambientes duros.
Aplicaciones de Rogers
- Circuitos de RF y Microondas: Adecuados para sistemas de comunicación y aplicaciones de radar.
- Aeroespacial y Defensa: Utilizados en aplicaciones críticas que requieren alta fiabilidad.
- Diseños Digitales de Alta Velocidad: Ideal para sistemas de transmisión de datos de alta velocidad.
Consideraciones de diseño para Rogers
- Diseño de Alta Frecuencia: Ideal para aplicaciones que requieren impedancia estable y baja pérdida de señal.
- Gestión Térmica: Efectivo para diseños con requerimientos significativos de disipación térmica.
- Sensibilidad a la Humedad: Más adecuado para entornos con alta humedad o exposición a la humedad.
FR4 vs Rogers PCB: ¿Cuál elegir?
Propiedad | FR4 | Rogers |
---|---|---|
Constante Dieléctrica (Dk) | ~4.5 | 2.5 a 11 |
Factor de Disipación (Df) | Mayor | Menor |
Conductividad Térmica | ~0.3 W/mK | 0.5 a 0.95 W/mK |
Absorción de Humedad | 0.1 a 0.2% | 0.02 a 0.08% |
Costo | Menor | Mayor |
Rango de Frecuencia | Hasta 10 MHz | Más de 500 MHz |
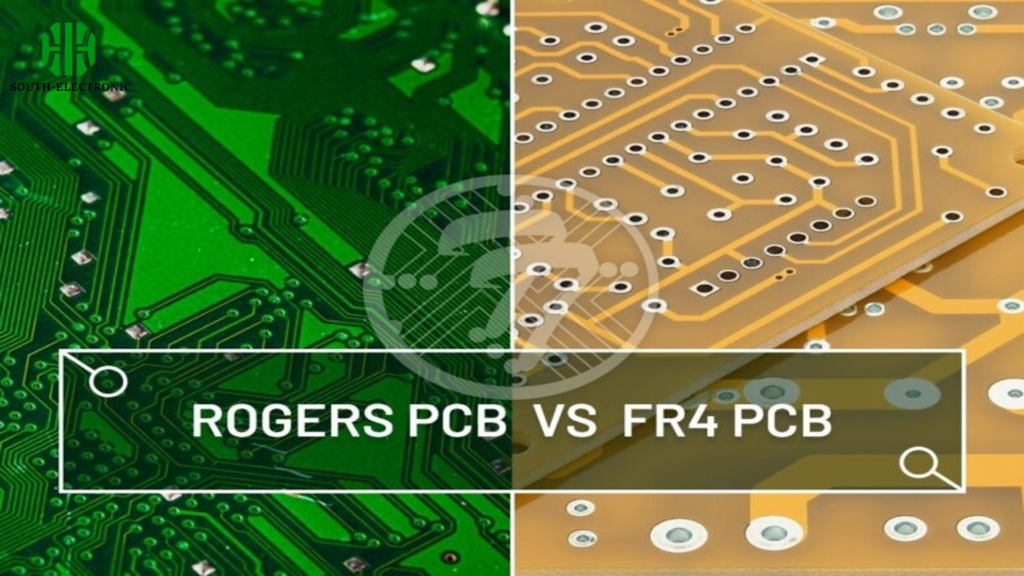
¿Por qué es importante la constante dieléctrica en los materiales de PCB?
La constante dieléctrica de los materiales de PCB es súper importante para asegurar que tus electrónicos funcionen correctamente. Afecta la velocidad a la que las señales atraviesan tu circuito, ayuda a mantener la impedancia bajo control para que tu circuito haga lo que se supone que debe hacer, te permite hacer tus dispositivos más pequeños al empaquetar más trazas juntas, e incluso afecta cómo se mueve el calor en tu circuito debido a cómo está relacionado con la conductividad térmica. Por lo tanto, elegir materiales con las propiedades dieléctricas adecuadas es realmente importante si quieres que tus electrónicos funcionen de la manera que deseas, especialmente cuando estás lidiando con cosas de alta frecuencia.