What is the Characteristic Difference Between PCB and FPC?
As electronics get smaller and more flexible, engineers and designers have to decide whether to use a printed circuit board (PCB) or a flexible printed circuit (FPC). To make the right choice, you need to know the differences between the two.
What is the difference between PCB and FPC?
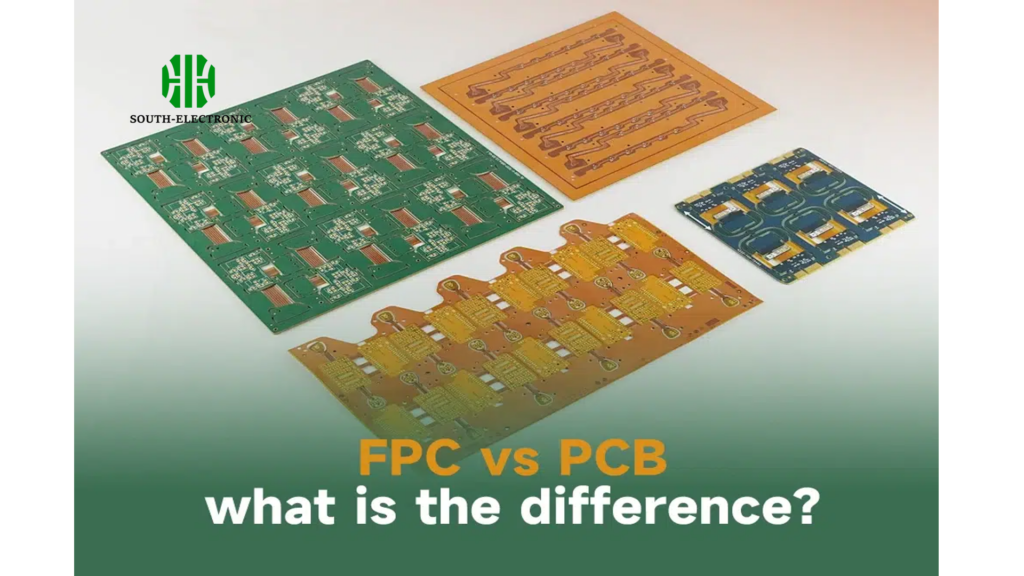
Definition of PCB
A PCB is a rigid board that uses copper tracks and pads to connect electronic components. These boards provide a stable foundation for mounting and soldering components, and they are used in everything from consumer electronics to industrial equipment.
Definition of FPC
A Flexible Printed Circuit (FPC), on the other hand, is a flexible and bendable version of the PCB. It allows electronic circuits to be integrated into devices where rigid boards are impractical. FPCs are made using flexible substrates, often polyimide, and can be bent or folded without breaking the circuit.
Key Differences Between PCB and FPC
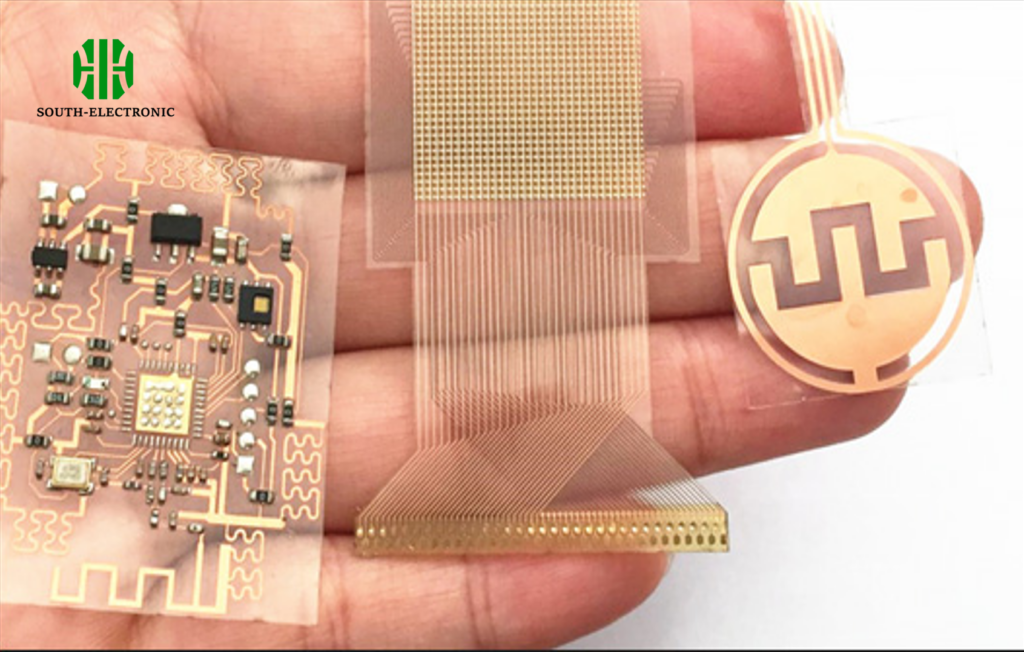
To visualize the distinction between PCB and FPC, let’s look at the table below, which outlines the fundamental differences:
Factor | PCB (Printed Circuit Board) | FPC (Flexible Printed Circuit) |
---|---|---|
Structure | Rigid, non-flexible | Flexible, bendable |
Material | Fiberglass or epoxy-based substrate | Polyimide or other flexible substrates |
Application Environment | Standard, fixed installations | Compact, dynamic environments |
Cost | Lower cost for mass production | Higher cost due to flexibility |
Design Complexity | Suitable for simple to complex designs | Suitable for complex, space-saving designs |
Durability | High rigidity ensures strength | Requires additional protection, prone to wear |
What are the Benefits of FPCs in Modern Electronics?
As the demand for smaller, more portable devices grows, Flexible Printed Circuits are becoming increasingly valuable. Let’s explore some of the key advantages of FPCs.
1. Flexibility
FPCs can bend, fold, and even twist without damaging the circuitry. This flexibility allows for more innovative designs in compact and portable devices. Devices like smartphones, tablets, and wearable electronics benefit from this property.
2. Space-Saving Design
Because FPCs can be shaped and bent, they allow manufacturers to design electronics that take up less space. FPCs are used in three-dimensional configurations, enabling designers to make thinner and lighter products.

3. Reduced Weight
FPCs are made from lighter materials than traditional PCBs, which helps reduce the overall weight of the device. This is particularly beneficial in aerospace and medical devices where every gram matters.
4. Durability in Dynamic Applications
FPCs are particularly useful in environments where the electronic components need to move or bend, such as in robotic arms, foldable smartphones, and other applications with moving parts.
Manufacturing Differences Between PCB and FPC
The manufacturing process of both PCBs and FPCs differs significantly. Let’s explore the key aspects:
PCB Manufacturing
- Substrate Material: Typically made from fiberglass-reinforced epoxy resin, which provides rigidity.
- Process: PCBs are manufactured using a subtractive method, where unwanted copper is removed to create conductive pathways.
- Layers: Multilayer PCBs can be produced, allowing for complex designs with multiple conductive layers.
- Design Limitations: Since PCBs are rigid, the layout must accommodate flat, two-dimensional designs.
FPC Manufacturing
- Substrate Material: Uses flexible materials like polyimide, which allow the circuit to bend.
- Process: Similar to PCB production, but with added complexities due to the need for flexibility.
- Layers: FPCs can also be multilayered, but the added flexibility introduces more design challenges.
- Complexity: The process of manufacturing FPCs is more expensive due to the materials used and the additional steps required to ensure flexibility without compromising electrical integrity.
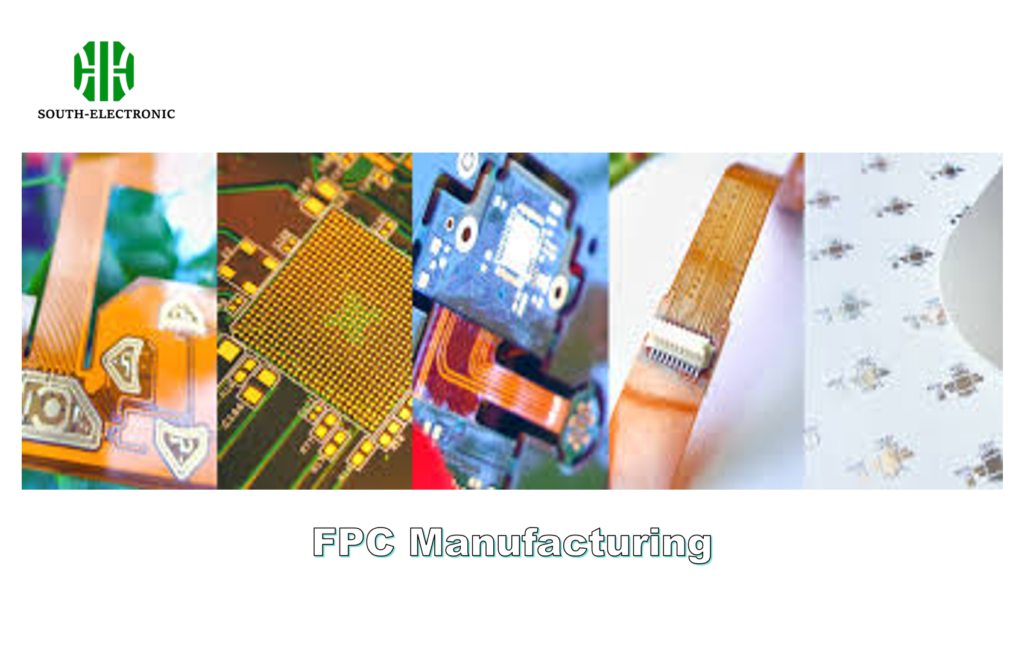
Here’s a table summarizing the differences in the manufacturing process:
Aspect | PCB | FPC |
---|---|---|
Substrate Material | Fiberglass-epoxy | Polyimide |
Process | Subtractive etching | Additive processes with flexibility in mind |
Design Consideration | Limited to 2D rigid applications | Supports 3D, flexible designs |
Cost | Lower for mass production | Higher due to complexity |
Applications of PCB and FPC in Electronics
PCBs and FPCs find their way into various industries, each having unique requirements that one or the other technology is better suited for.
Applications of PCBs
- Consumer Electronics: Devices such as televisions, desktop computers, and home appliances benefit from the cost-efficiency and reliability of PCBs.
- Industrial Equipment: In factories and other industrial settings, PCBs provide robust solutions for machinery and control systems.
- Automotive: PCBs are commonly used in automotive control systems, infotainment systems, and other electronics within vehicles.
Applications of FPCs
- Wearable Technology: FPCs are ideal for smartwatches, fitness trackers, and other wearable devices where space is limited and flexibility is essential.
- Medical Devices: In medical applications, such as pacemakers and implantable devices, FPCs are crucial for minimizing size and enhancing flexibility.
- Aerospace: FPCs are utilized in aerospace technologies where weight and space-saving designs are of utmost importance.
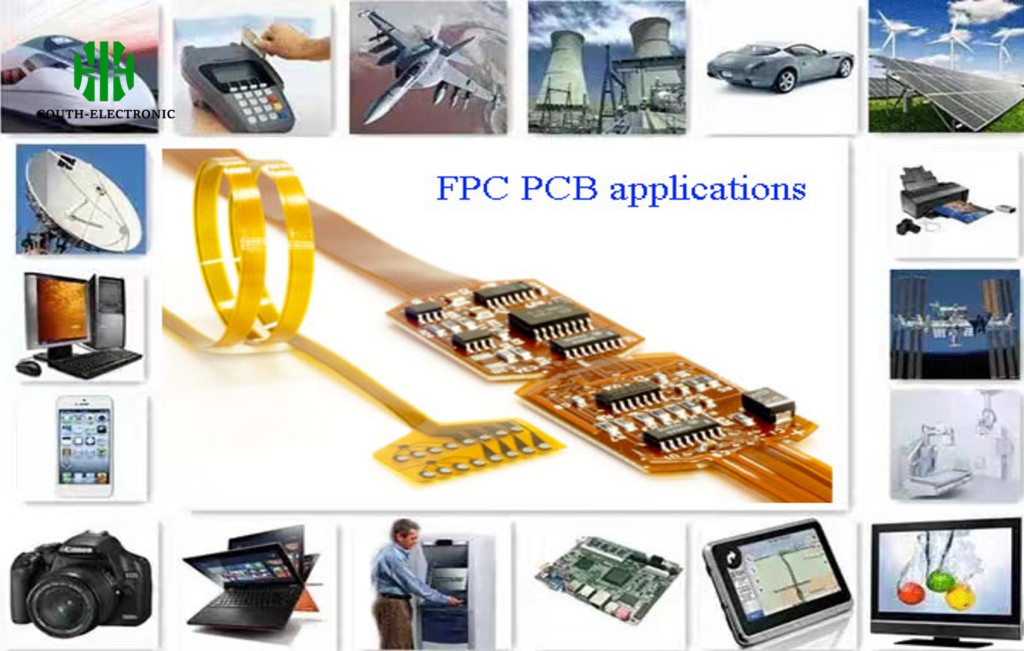
Deciding whether to use a PCB or FPC really depends on what you need for your device. If you don’t need flexibility, then a PCB is a good, stable, and cost-effective choice. But if you need flexibility and space savings, then an FPC is a better choice.
As technology gets smaller, more flexible, and more mobile, it’s important to understand the differences between these two options. By using the strengths of both PCBs and FPCs, you can create innovative solutions that meet the needs of today’s technology.