Rigid-Flex PCB
South-Electronic
Opt for South-Electronic for unmatched quality, dependability, and outstanding value in your PCB requirements. Embrace the benefits of our comprehensive Rigid-Flex PCB solutions – from initial design to final production. We ensure precision, durability, and strict conformity to the highest industry standards. Experience the difference with South-Electronic.
Your Trusted Partner for Rigid-Flex PCB Solutions!
Welcome to South-Electronic, your destination for top-quality Rigid-Flex PCBs known for their flexible design and robust performance.
Our Rigid-Flex PCBs deliver exceptional performance, ideal for advanced applications in challenging environments. Explore a variety of configurations, including dual-layer, multi-layer, and complex custom designs, all meticulously crafted to meet your unique electronic requirements. Whether you’re seeking durable boards for aerospace or innovative designs for wearable technology, you’ll discover the perfect solution with us. Enjoy personalized service, rapid delivery, and a satisfaction guarantee that prioritizes your needs. Collaborate with us to foster innovation and attain success in your field.
Why Choose South-Electronic?
-
Manufacturing Capabilitie
At South-Electronic, you tap into our state-of-the-art facility equipped with 8 production lines.
This means you can rely on us to handle everything from simple to complex multi-layer PCB designs, giving you the flexibility to innovate and stay ahead in your market. -
Quality Assurance
You can’t afford to compromise on quality, and neither can we.
Our ISO9001 certified factory ensures that every product goes through rigorous quality checks. You can trust that each PCB will meet the highest standards of excellence, freeing you from worries about defects and ensuring reliable performance. -
Expertise and Experience
You deserve a partner who truly understands the complexities of Rigid-Flex PCBs.
With South-Electronic, you're gaining over a decade of industry expertise. We equip you with invaluable insights and the latest trends, ensuring your products remain at the forefront of technology. -
Rapid Response and Delivery
Your deadlines are important to us.
Choosing South-Electronic means selecting a partner dedicated to meeting tight schedules. Our streamlined processes ensure that your Rigid-Flex PCBs are manufactured with precision and delivered swiftly, keeping your projects on track -
Lifetime After-Sales Support
Your peace of mind is our priority.
By choosing us, you’re not just making a purchase—you’re securing lifetime after-sales support. We stand by you at every stage, ensuring your experience with South-Electronic is seamless, dependable, and worry-free.
Related Project We had Done
Customer Reviews
engineer
thank you, guys, the boards are really good, i am really happy to receive my boards, the components are perfect!
Operation Manager
South-Electronic is my first PCBA supplier in China. The service and quality are excellent, and the after-sales support is also very impressive. Good Job!
Common Questions
Most Popular Questions
South-Electronic certifications, including ISO 9001 and UL listings, ensure that every Rigid-Flex PCB we produce meets rigorous international standards, providing you with products that exemplify reliability and excellence.
South-Electronic Rigid-Flex PCBs undergo a meticulous quality control process, encompassing advanced testing and inspection at every stage of production. By leveraging cutting-edge technology and adhering to rigorous quality management systems, we ensure that each PCB performs optimally in your applications.
Absolutely. South-Electronic excels in providing customized solutions to meet your specific application requirements. We offer bespoke Rigid-Flex PCB designs tailored to your exact specifications, ensuring seamless integration and enhanced performance and reliability for your projects.
South-Electronic expansive production facilities, featuring eight state-of-the-art production lines, empower us to efficiently manage complex, large-volume orders. South-Electronic is fully equipped to scale production to meet your demands without compromising on quality, ensuring timely delivery and satisfaction for all your projects.
With decades of experience in manufacturing Rigid-Flex PCBs, South-Electronic blends seasoned expertise with innovative practices. Our long-standing presence in the industry reflects our dedication to continual improvement and our ability to adapt to technological advancements, ensuring we provide high-quality solutions tailored to your needs.
South-Electronic offers comprehensive technical support and robust after-sales services. Our dedicated team of experts is committed to providing you with the guidance necessary to maximize the effectiveness of your Rigid-Flex PCBs. From initial consultation to after-sales assistance, we ensure you have the support needed for seamless integration and optimal performance.
Send us a message
The more detailed you fill out, the faster we can move to the next step.
The Complete Guide for Rigid-flex PCB
Contents
Chapter 1
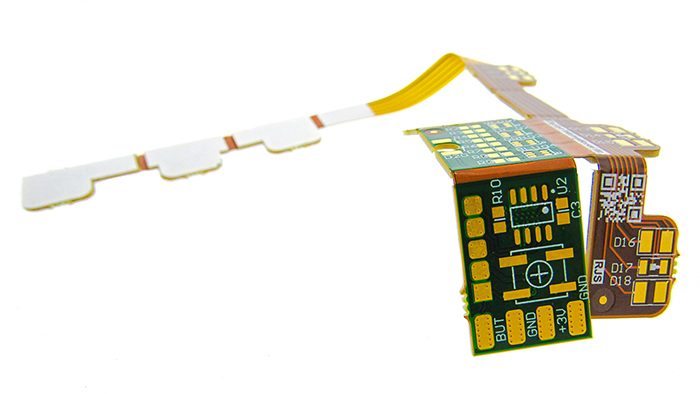
Introduction to Rigid-Flex PCB
What are Rigid-Flex PCBs?
Rigid-Flex PCBs are composed of multiple layers of flexible circuit substrates attached to one or more rigid boards. This unique construction allows for a range of complex and compact configurations that traditional PCBs cannot achieve. The flexible layers enable dynamic bending and folding, providing design engineers with the ability to fit circuits into tight spaces without compromising on electronic performance.
The significance of Rigid-Flex PCBs goes beyond their structural and mechanical benefits. They provide enhanced resistance to vibrations and mechanical stresses, making them an ideal choice for applications in challenging environments such as aerospace, medical devices, and automotive industries. Their ability to reduce connector and interface needs also enhances signal reliability and reduces the risk of common connection issues found in traditional PCB assemblies.As electronics continue to evolve, the role of Rigid-Flex PCBs becomes increasingly critical in pushing the boundaries of device capabilities.
Chapter 2
Benefits of Using Rigid-Flex PCB
Rigid-Flex PCBs offer a range of compelling advantages that address the ever-changing needs of modern electronic design. By combining the strengths of rigid and flexible circuit technologies, they provide solutions that are both innovative and practical. Here are some of the key benefits:
1. Enhanced Mechanical Stability and Flexibility
One of the most significant benefits of Rigid-Flex PCBs is their ability to withstand a wide range of mechanical stresses. The flexible layers allow the circuit to be bent and twisted without damaging the electronic components, which is especially beneficial in applications where movement and vibration are common. This flexibility also enables more complex three-dimensional assembly configurations, leading to greater design freedom and efficiency.
2. Space and Weight Reduction
Rigid-Flex PCBs are instrumental in achieving more compact and lightweight electronic devices. By eliminating the need for connectors and cables between separate rigid sections, these PCBs reduce the overall space and weight required for the circuitry. This reduction is crucial in industries like aerospace and consumer electronics, where every gram counts, and space is at a premium.
3. Improved Reliability and Durability
The integration of rigid and flexible layers into a single circuit board reduces the need for solder joints and connectors, which are often points of failure in traditional PCBs. This unified solution enhances the overall reliability of the device by minimizing potential failure points, resulting in a longer lifespan and reduced maintenance needs.
4. Simplified Assembly and Connection
With fewer interconnections and components needed to connect multiple boards, Rigid-Flex PCBs simplify the assembly process. This not only reduces the risk of errors during manufacturing but also enhances signal integrity by decreasing the number of potential interference sources.
5. Superior Electrical Performance
The seamless design of Rigid-Flex PCBs allows for optimized routing, which can improve electrical performance. Shorter interconnect paths can enhance signal integrity and reduce latency, making them ideal for applications requiring high-speed data transfer.
6. Cost Efficiency in the Long Run
While initial production costs for Rigid-Flex PCBs might be higher compared to traditional PCBs, the long-term benefits often lead to cost savings. The increased reliability, reduced need for connectors, and simplified assembly process can lower manufacturing and maintenance expenses over time.
Rigid-Flex PCBs have become an indispensable tool in advanced electronic design, offering benefits that address the critical demands of various industries. Their ability to provide flexibility, reliability, and efficiency makes them a preferred choice for engineers striving for excellence in their innovative products.
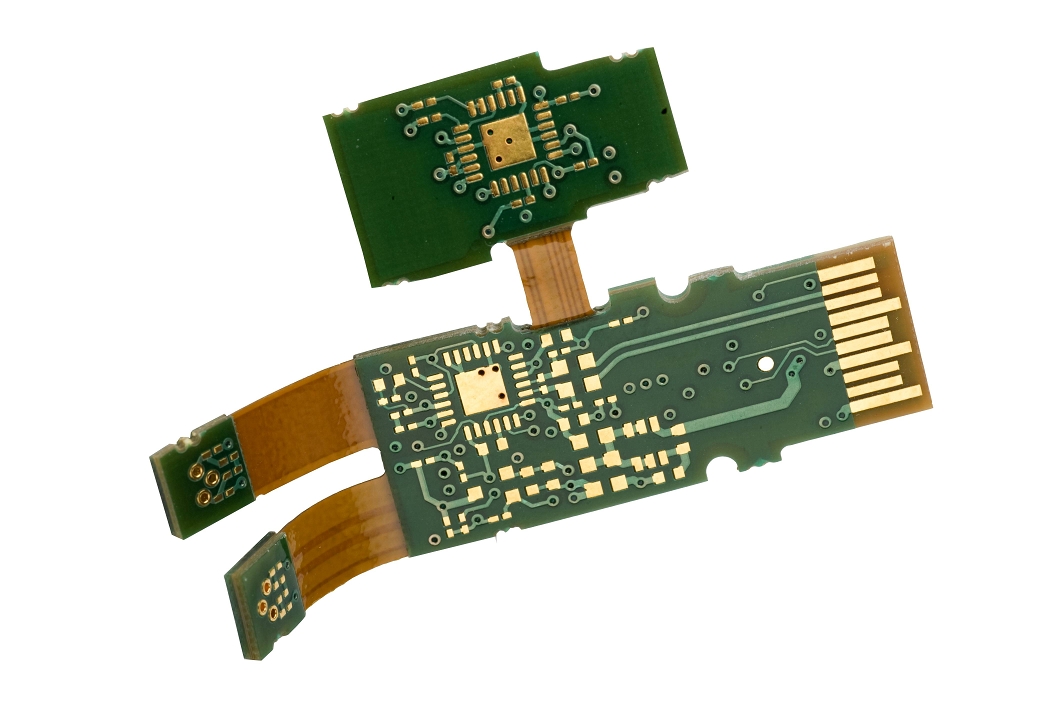
Chapter 3
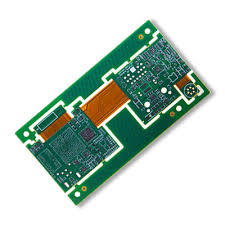
Design Considerations for Rigid-Flex PCB
Designing Rigid-Flex PCBs demands meticulous planning to exploit their unique capabilities fully and ensure optimal functionality and reliability. Here are the key factors to consider during the design process:
1. Understanding the Application Requirements
The initial step in designing Rigid-Flex PCBs is to thoroughly grasp the specific requirements of the application. This includes considering environmental conditions, mechanical stress, electrical performance, and space constraints. A clear understanding of these requirements will guide the design process, ensuring the final product meets the necessary standards.
2. Layer Stackup and Flex Layer Arrangement
Determining the correct layer stackup is crucial in Rigid-Flex PCB design. The arrangement of rigid and flexible layers should be optimized for both mechanical and electrical performance. Properly balancing the layers is essential to avoid mechanical failures and ensure signal integrity. Designers should also consider the bending requirements, ensuring that the flex layers are situated to accommodate these movements without failure.
3. Bending Requirements and Flexibility
One of the main advantages of Rigid-Flex PCBs is their flexibility, but excessive bending can lead to stress and potential damage. It’s essential to define the bending regions and ensure that bending stress is minimized. Implementing appropriate bend radii and accommodating for dynamic or static flexing needs can prevent damage and prolong the lifespan of the PCB.
4. Component Placement and Routing
Strategic component placement is essential in maximizing the performance and reliability of Rigid-Flex PCBs. Rigid sections should house the heavier components and connectors, while the flexible areas should be kept clear of components to allow for bending. Additionally, careful routing helps maintain signal integrity and minimize electromagnetic interference.
5.Thermal Management*
Effective thermal management is crucial in Rigid-Flex PCB design, particularly for applications involving high power densities. Ensuring proper heat dissipation through materials, layer arrangement, and potentially incorporating thermal vias or heatsinks can prevent overheating and maintain performance.
6. Material Selection
Selecting the appropriate materials for both the rigid and flexible layers is fundamental to the success of the design. Material choices affect the electrical, thermal, and mechanical properties of the PCB. Designers should choose materials that meet the specific application requirements and environmental conditions.
7. Compliance with Standards and Regulations
Ensure that the design complies with relevant industry standards and regulations, which can vary depending on the application and geographical location. This compliance is crucial for ensuring the safety, reliability, and marketability of the product.
By carefully considering these design aspects, engineers can fully harness the potential of Rigid-Flex PCBs, leading to innovative solutions that meet the complex demands of current and future electronic applications.
Chapter 4
Manufacturing Process of Rigid-Flex PCB
The manufacturing process of Rigid-Flex PCBs is a meticulous journey, demanding precision and expertise to yield high-quality results. Grasping these steps is crucial for designing PCBs that are not only robust but also manufacturable with efficiency and minimal errors. Here’s a breakdown of the essential stages in the manufacturing process:
1. Design and Pre-Production Planning
The journey begins with meticulous design and planning. Engineers employ advanced software tools to craft detailed schematics, layer stack-ups, and layout designs. This phase encompasses:
- Verifying design rules and constraints
- Establishing material requirements and configurations
- Preparing CAD files for production
The design undergoes thorough review and validation to ensure it meets all specifications and performance criteria.
2. Material Selection and Preparation
Choosing the right materials for both rigid and flexible sections is paramount. Common materials include FR4 for rigid boards and polyimide for flexible circuits. These materials are prepared and cut according to design specifications, considering factors like thermal resistance, dielectric properties, and flexibility.
3. Layer Fabrication
Both flexible and rigid circuit layers are fabricated individually:
- Flexible Layers:Polyimide sheets are laminated with copper foil, which is then etched to reveal the desired circuit pattern.
- Rigid Layers: This involves copper cladding, photoresist coating, exposure, developing, and etching processes to create circuit patterns, similar to traditional PCB manufacturing.
4. Layer Lamination and Bonding
Once individual layers are fabricated, they are laminated together with precision. This involves:
- Arranging layers in the correct order and sequence
- Using adhesives and bonding films to attach flexible and rigid layers
- Applying heat and pressure to laminate the stack securely, avoiding any misalignment or air gaps
5. Drilling and Plating
Drilled holes serve as vias and mounting points, enabling electrical connections between layers. Post-drilling, these holes are plated with conductive material, typically copper, to ensure reliable electrical connectivity throughout the PCB.
6. Solder Mask and Surface Finishing
A solder mask is applied to protect the circuit and identify soldering points. This is followed by adding surface finishes like ENIG (Electroless Nickel Immersion Gold) to enhance solderability and guard against oxidation.
7. Testing and Quality Inspection
Rigorous testing and inspections are conducted to ensure the PCB meets all specifications:
- -Electrical Testing:Verifies circuit continuity and insulation.
- Visual Inspection:Checks for physical defects and cosmetic flaws.
- Functional Testing:Tests the PCB in simulated real-world conditions.
8. Cutting and Final Assembly
The final shape of the PCB is cut using routers or lasers to achieve precise dimensions. Any connectors or additional components are then assembled onto the board as specified in the design.
Manufacturing Rigid-Flex PCBs is a complex process that necessitates state-of-the-art technology and skilled expertise. Each step must be executed with precision to ensure the resulting PCBs are capable of high performance and reliability in their designated applications.
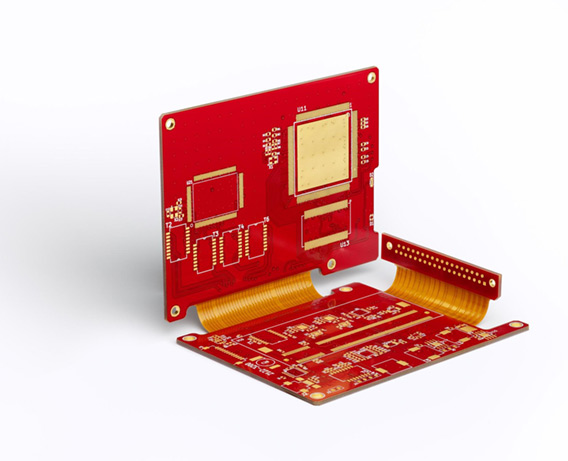
Chapter 5

Applications of Rigid-Flex PCB
Rigid-Flex PCBs have become indispensable in modern electronics, celebrated for their versatility and reliability. Their unique blend of rigid and flexible components makes them ideal across a spectrum of industries and technological frontiers. Here are some pivotal areas where Rigid-Flex PCBs shine:
1. Aerospace and Defense
The aerospace and defense sectors demand electronics that can endure extreme conditions—high temperatures, intense vibrations, and significant pressure. Rigid-Flex PCBs excel in:
- Avionics systems
- Satellites and space equipment
- Military communication devices
- Navigation and control systems
Their resilience in harsh environments, coupled with weight and space efficiency, sets them apart.
2. Medical Devices
Precision, reliability, and compactness are paramount in medical technology. Rigid-Flex PCBs are pivotal in:
- Diagnostic imaging systems (e.g., MRI, CT scanners)
- Wearable health monitors
- Implantable devices, such as pacemakers
- Surgical instrumentation
Their biocompatibility and flexibility foster the creation of compact, dependable, and safe medical devices.
3. Consumer Electronics
The consumer electronics landscape is ever-evolving, driven by the quest for smaller, more powerful gadgets. Rigid-Flex PCBs facilitate innovations in:
- Smartphones and tablets
- Wearable technology, such as smartwatches and fitness trackers
- Flexible displays and foldable screens
- Cameras and audio equipment
Their ability to support intricate designs without sacrificing functionality makes them a cornerstone of contemporary consumer tech.
4. Automotive Industry
Automotive electronics must withstand constant movement and challenging environments. Rigid-Flex PCBs are integral to:
- Infotainment systems
- Advanced Driver Assistance Systems (ADAS)
- Engine management systems
- Sensors and control modules
Their durability and adaptability meet the rigorous demands of automotive electronics, enduring vibrations and temperature shifts with ease.
5. Industrial Applications
Industrial automation and robotics depend on robust and reliable electronic systems. Rigid-Flex PCBs are crucial in:
- Robotic arms and machinery
- Control systems and sensors
- Power distribution networks
- Industrial IoT devices
Their ability to streamline assembly and enhance reliability in tough industrial settings makes them invaluable.
Rigid-Flex PCBs are at the heart of numerous technological advancements, thanks to their versatility, reliability, and capacity to meet complex design needs. As industries continue to push the boundaries of innovation, the demand for Rigid-Flex PCBs will only escalate, driving progress across a multitude of fields with their groundbreaking capabilities.
Chapter 6
Challenges and Considerations in Designing Rigid-Flex PCB
Rigid-Flex PCBs bring a host of advantages, yet their design and manufacturing processes come with distinct challenges that must be meticulously managed to guarantee peak performance and reliability. Grasping these challenges is key to crafting more effective design and production strategies. Here are the primary challenges and considerations when dealing with Rigid-Flex PCBs:
- Complexity and Cost: The design and production of Rigid-Flex PCBs involve an array of sophisticated technologies, often leading to elevated initial design and manufacturing costs. Balancing design complexity with product requirements during the design phase is essential to control expenses. Partnering with seasoned manufacturers can help mitigate costs while maintaining quality.
- Material Selection: Choosing the right materials is pivotal to the PCB’s performance. Different materials may be required for the rigid and flexible sections, and their compatibility, electrical performance, thermal stability, and mechanical strength must be carefully evaluated. Materials in the flexible sections need to endure repeated bending and flexing without compromising functionality.
- Mechanical Stress Management: Managing mechanical stress, particularly in the flexible regions, is crucial. Design considerations should account for bend radius and bend cycles to prevent excessive stress that could lead to component failure. Minimizing vias and solder joints in bending areas is vital to reduce stress concentration.
- Thermal Management: Effective thermal management is critical, especially as Rigid-Flex PCBs may operate in high-power and high-temperature environments. Poor thermal management can cause PCB warping or component damage. Design solutions might include heat sinks, thermal vias, and thermal interface materials to efficiently dissipate heat.
- Manufacturing and Assembly Requirements: The manufacturing and assembly of Rigid-Flex PCBs demand more stringent processes compared to standard rigid PCBs. Complex lamination and layering structures require specialized manufacturing techniques and skilled operators. When choosing a manufacturing partner, ensure they have the necessary experience and technical expertise to navigate diverse production challenges.
- Design Rule Checking and Validation: Given the unique characteristics of Rigid-Flex PCBs, meticulous attention is needed during design rule checking (DRC) and validation. Ensuring designs comply with electrical, mechanical, and reliability specifications, as well as industry standards and certification requirements, is essential. This process helps identify and rectify potential issues before production.
By proactively tackling these challenges, engineers can ensure their Rigid-Flex PCB designs meet technical requirements while optimizing cost, reliability, and manufacturability.
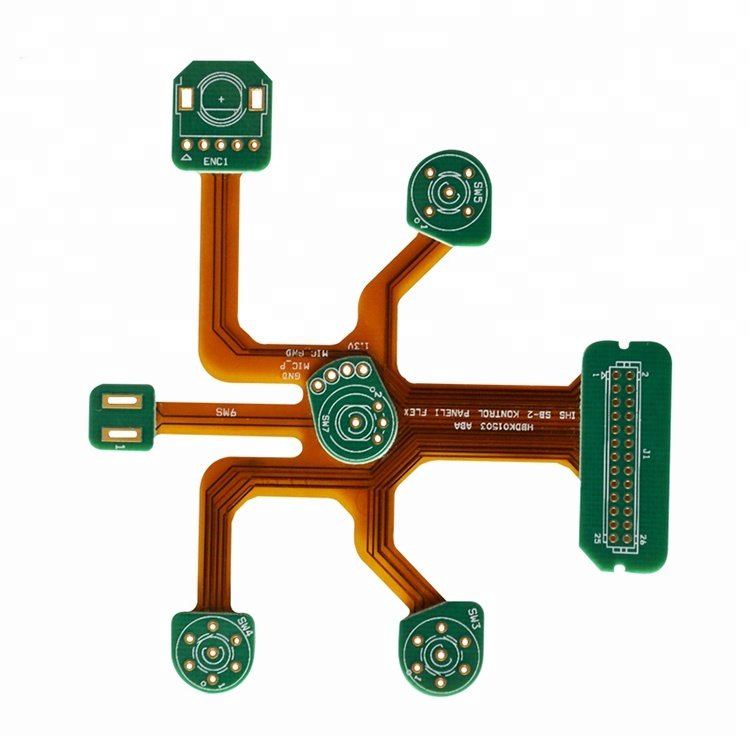
Chapter 7

Tips for Designing Rigid-Flex PCBs
Designing Rigid-Flex PCBs requires careful planning and execution to get the most out of them. By following best practices, designers can optimize performance, reliability, and manufacturability. Here are some key tips for designing Rigid-Flex PCBs:
1. Work with Manufacturers Early
Get manufacturers involved early in the design process. They can help you make key decisions about material selection, layer stack-up, and manufacturing techniques. Early collaboration ensures that your design is feasible and can often lead to cost savings and performance improvements in the final product.
2. Get the Layer Stack-Up Right
Plan the layer stack-up carefully to balance flexibility and rigidity. Consider using symmetric stack-ups to prevent warping and ensure mechanical stability. Your stack-up should also account for impedance control, thermal management, and electrical performance.
3. Design for Flex and Bend Areas
Design your flexible areas to handle mechanical stress:
- Make sure you have an adequate bend radius; a good rule of thumb is to make the bend radius at least ten times the thickness of the flex section.
- Avoid placing vias, pads, or components in flex and bend areas to reduce stress concentration.
- Use hatched polygons instead of solid copper in the flexible region to increase flexibility and reduce weight without sacrificing electrical performance.
4. Pay Attention to Trace Layout and Routing
Optimize your trace layout and routing for signal integrity and mechanical performance:
- Keep your trace widths and spacing consistent, especially in bend areas, to avoid stress points and electrical issues.
- Route your traces perpendicular to the bending line to minimize stress.
- Use curved traces instead of 90-degree angles to reduce mechanical stress during bending.
5. Choose the Right Adhesive and Materials
Select adhesive materials that provide strong interlayer bonds and can withstand environmental stresses. Your materials should have thermal and mechanical properties that match the rigid and flexible circuits to maintain performance under different conditions.
6. Consider Signal Integrity and EMI
Think about signal integrity and electromagnetic interference (EMI) during the design phase:
- Use controlled impedance routing techniques for high-speed signals.
- Implement proper grounding strategies and ground planes to reduce EMI.
- Carefully place decoupling capacitors and shielding to maintain signal integrity.
7. Prototype and Test
Build prototypes to validate your design assumptions and performance. Test your design thoroughly, including mechanical stress tests, thermal cycling, and electrical performance evaluations, to find any design flaws. Use your testing data to iterate and refine your design as needed.
By following these tips, you can improve the performance and reliability of your Rigid-Flex PCBs and make the manufacturing process smoother. Thoughtful design and planning are key to creating a robust and successful Rigid-Flex PCB product.
Chapter 8
Testing and Quality Assurance for Rigid-Flex PCBs
When it comes to Rigid-Flex PCBs, reliability and performance are everything. You can’t afford to have these boards fail in the field. That’s why testing and quality assurance (QA) are so critical throughout the entire manufacturing process. Let’s take a closer look at the key testing methods, standards, and the role of QA in delivering high-quality Rigid-Flex PCBs.
Key Testing Methods and Standards
Electrical Testing:
- Continuity Testing: This ensures that all the electrical paths on the PCB are complete, with no opens that could disrupt signal flow.
- Isolation Testing: This verifies that there are no short circuits between conductive traces, which could cause things to go haywire.
- Impedance Testing: This is especially important for high-frequency applications. It ensures that the impedance is within the specified range to maintain signal integrity.
Thermal Testing:
- This is all about how the PCB performs under different temperature conditions. This is especially important for applications in harsh environments where you might have thermal cycling.
- Thermography: This uses infrared imaging to detect hotspots and ensure even heat distribution across the board during operation.
Mechanical Testing:
- Bend and Flex Tests: These are all about making sure that Rigid-Flex PCBs can withstand repeated bending and flexing without performance degradation.
- Vibration and Shock Testing: This is done to simulate real-world conditions, especially for automotive and aerospace applications where there’s a lot of mechanical stress.
Environmental Testing (Continued):
- Humidity and Moisture Resistance: This is all about making sure the board performs well in high-humidity conditions or when it’s exposed to moisture. You don’t want anything to degrade or corrode or have electrical failures.
- Thermal Shock Testing: This is all about making sure the board can handle rapid changes in temperature. This is especially important for boards used in environments where the temperature fluctuates a lot.
Chemical Testing:
- This is all about making sure that the PCB materials can resist chemical exposure. This is especially important in industrial applications where the board might come into contact with solvents or corrosive substances.
Visual and Optical Inspection:
- Automated optical inspection (AOI) systems can detect defects like misaligned components, poor solder joints, or trace defects. This is just another way to make sure that everything is good to go.
Industry Standards Compliance:
- Adhering to industry standards like IPC-6013 (Qualification and Performance Specification for Flexible Printed Boards) and IPC-2223 (Sectional Design Standard for Flexible Printed Boards) is all about making sure that your boards meet recognized performance and quality benchmarks.
Why Quality Assurance Matters in the Manufacturing Process
Quality assurance is critical to the manufacturing of Rigid-Flex PCBs. It’s all about making sure that every board you build meets the specifications and performance standards you’ve set. Here are some key aspects of quality assurance in this context:
Proactive Quality Management:
Quality assurance starts with a thorough design review. You want to identify and address any potential issues early in the development process. This includes DFM (Design for Manufacturability) and DFT (Design for Testability) assessments to make production and testing as smooth as possible.
Process Control:
You want to have robust process controls throughout the manufacturing process to make sure that everything is consistent and repeatable. This means carefully monitoring things like temperature, humidity, and pressure at each step of fabrication.
Supplier Quality Management:
Rigid-Flex PCBs rely on high-performance materials and components. You need to make sure that your suppliers are adhering to quality standards so you can maintain the overall quality of your final product. Supplier audits and material certifications are common practices.
Continuous Improvement:
A strong quality assurance program includes feedback loops and data analysis to drive continuous improvement. This means comparing your test results to your benchmarks and investigating any variances so you can make your processes and materials better over time.
End-of-Line Testing and Inspection:
You want to have rigorous testing and inspection at the end of your production line to make sure that every PCB you ship meets your quality and performance standards. This final check helps you reduce the risk of defects reaching your customers.
Documentation and Traceability:
You need to keep detailed records of every manufacturing batch you produce so you have traceability. This is important for addressing any issues that come up after production. Your documentation should cover everything from material usage to test results.
In short, a strong quality assurance framework not only ensures that you deliver a reliable, durable product, but it also helps you build your reputation and keep your customers happy. By investing in comprehensive testing and quality assurance mechanisms, you can mitigate risks and reinforce the performance integrity of Rigid-Flex PCBs across a wide range of applications.
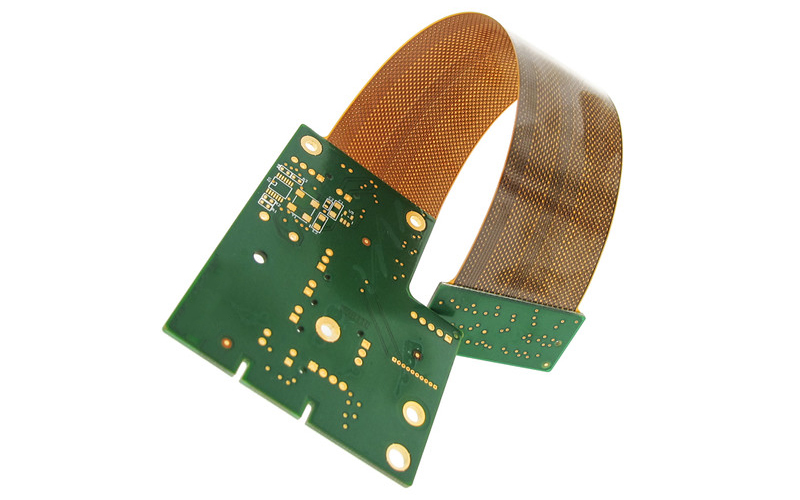
Chapter 9
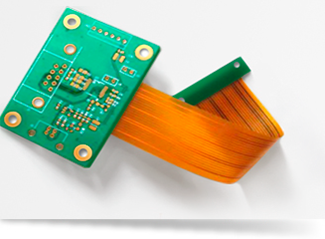
Future Trends in Rigid-Flex PCB Technology
The evolution of electronics continues to push the boundaries of what is possible, and Rigid-Flex PCB technology is at the forefront of these advancements. As industries strive for smaller, more powerful devices, the future of Rigid-Flex PCBs is shaped by several emerging trends:
1. Miniaturization and Increased Complexity
The demand for smaller, more powerful devices drives the trend toward further miniaturization. Rigid-Flex PCBs allow for tight integration of components, accommodating more features within a limited space. Advances in fabrication technology will enable finer lines and spaces, supporting even more compact designs with increased functionality.
2. Advanced Materials
The development of new materials with improved properties will enhance the capabilities of Rigid-Flex PCBs. These materials will offer better thermal management, greater flexibility, and increased durability, enabling PCBs to perform reliably in extreme conditions. Innovations in conductive materials and substrates will also support higher electrical performance and efficiency.
3. Integration with IoT and Wearable Technologies
As the Internet of Things (IoT) and wearable technologies continue to expand, Rigid-Flex PCBs will play a critical role. Their ability to conform to various shapes and integrate multiple components makes them ideal for wearable devices, smart textiles, and connected sensors. This trend will lead to new applications in health monitoring, smart home devices, and industrial automation.
4. Hybrid and Multi-Board Systems
The future will see an increase in hybrid systems that combine Rigid-Flex PCBs with other types of PCBs to optimize performance and cost. These multi-board systems will take advantage of the strengths of different board types, creating more efficient and tailored solutions for complex applications in industries such as aerospace, automotive, and telecommunications.
5. Sustainable Manufacturing Practices
As environmental concerns grow, the industry will adopt more sustainable manufacturing practices. This includes the use of eco-friendly materials, reducing waste during production, and improving energy efficiency. The recyclability and lifecycle management of Rigid-Flex PCBs will become more significant, with an emphasis on minimizing environmental impact.
6. Enhanced Design and Simulation Software
Advances in design software and simulation tools will revolutionize how engineers create Rigid-Flex PCB layouts. Improved tools will allow for more accurate modeling of mechanical and electrical performance, facilitating better optimization and faster prototyping. Virtual prototyping and digital twins will further streamline the design process, reducing time-to-market and development costs.
As these trends develop, Rigid-Flex PCBs will increasingly become essential to meeting the growing demands of modern electronics. By adapting to these changes, manufacturers and designers can leverage Rigid-Flex technology to innovate and excel in their respective fields.
Chapter 10
Choosing the Right Rigid-Flex PCB Solution
Selecting the right Rigid-Flex PCB solution involves careful consideration of multiple factors to ensure the final product meets your specific performance, reliability, and cost requirements. Here are some key aspects to consider when choosing the optimal Rigid-Flex PCB solution for your project:
1. Define Application Requirements
Begin by clearly outlining the requirements of your application. Consider factors such as electrical performance, mechanical stress, operating environment, space constraints, and thermal conditions. Understanding these requirements helps in specifying the necessary characteristics and features of the Rigid-Flex PCB.
2. Material Selection
Select appropriate materials that match the application’s environmental and performance needs. Consider factors like flexibility, thermal stability, and dielectric properties. The choice of substrates, adhesives, and conductive materials can significantly impact the durability and functionality of the PCB.
3. Collaborate with Experienced Manufacturers
Partner with manufacturers who have extensive experience in Rigid-Flex PCB production. Their expertise can guide you in making informed decisions regarding design optimization, material choices, and cost-effective manufacturing techniques. A knowledgeable manufacturer can also help navigate potential challenges in the fabrication process.
4. Evaluate Design Capabilities
Ensure that your design can be manufactured easily and effectively. This includes confirming the feasibility of your layout, considering impedance control, and evaluating the bend radius to ensure mechanical stability. Advanced design software and simulation tools can assist in validating these elements before production.
5. Prototype and Test
Create prototypes to test your design in real-world conditions. Prototyping allows for the identification and mitigation of issues that may not be apparent in the design phase. Conduct thorough mechanical, thermal, and electrical testing to ensure that the PCB meets all performance criteria.
6. Consider Lifecycle and Maintenance
Account for the lifecycle of the product and potential maintenance needs. Choose Rigid-Flex solutions that offer long-term reliability to reduce the frequency of repairs or replacements. This is particularly important in applications where maintenance access is limited or costly.
7. Cost vs. Performance Balance
Strike a balance between cost and performance. While it might be tempting to prioritize cost savings, it’s crucial to ensure that performance and reliability are not compromised, especially in demanding applications. Evaluate the total cost of ownership over time to make informed financial decisions.
By thoughtfully considering these factors, you can choose a Rigid-Flex PCB solution that not only meets the technical demands of your project but also aligns with your budgetary constraints and manufacturing timelines. A well-chosen solution can provide significant advantages, driving success and innovation in your electronic products
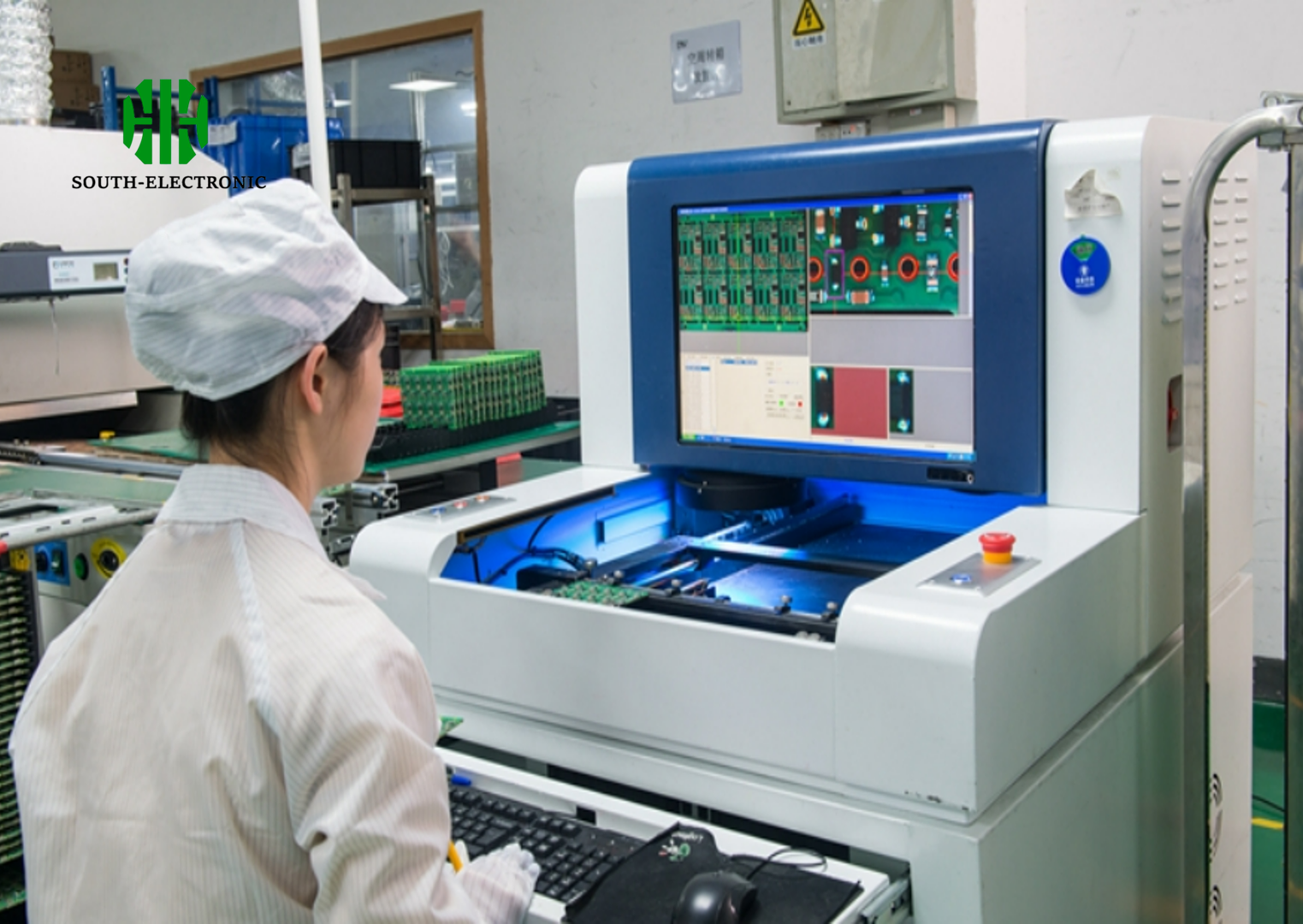
Get in touch
Where Are We?
Industrial Park, No. 438 Donghuan Road, No. 438, Shajing Donghuan Road, Bao'an District, Shenzhen, Guangdong, China
Floor 4, Zhihui Creative Building, No.2005 Xihuan Road, Shajing, Baoan District, Shenzhen, China
ROOM A1-13,FLOOR 3,YEE LIM INDUSTRIAL CENTRE 2-28 KWAI LOK STREET, KWAI CHUNG HK
service@southelectronicpcb.com
Phone : +86 400 878 3488
Send us a message
The more detailed you fill out, the faster we can move to the next step.
