Rogers PCB Supplier
South-Electronic
Come to South-Electronic for top quality, reliability, and great value in your PCB needs. Experience the best with our complete Rogers PCB solutions—from design to production, we guarantee accuracy, strength, and compliance with strict industry standards.
Quality Rogers PCBs Delivered with Confidence
Welcome to South-Electronic, your one-stop shop for top-of-the-line Rogers PCBs known for their superior dielectric properties and thermal stability. Our Rogers PCBs offer exceptional performance, making them ideal for advanced applications in critical industries. Choose from single-layer, double-layer, and complex multi-layer configurations, all designed to meet your specific electronic requirements. Whether you’re pushing the boundaries of aerospace technology or need high-quality PCBs for telecommunications, our Rogers PCBs are engineered to provide reliability and accuracy. Count on South-Electronic for unparalleled quality and consistency in your high-tech projects. Our Rogers PCBs enhance the functionality of your devices with excellent signal integrity and reduced thermal concerns. Partner with us to drive innovation and success in your field.

Rogers RO4350B™ PCB
RO4350B™ PCB is known for its low-loss dielectric material, making it perfect for high-frequency applications. It is widely used in cellular base station antennas and power amplifiers because of its excellent thermal stability and cost-effectiveness.
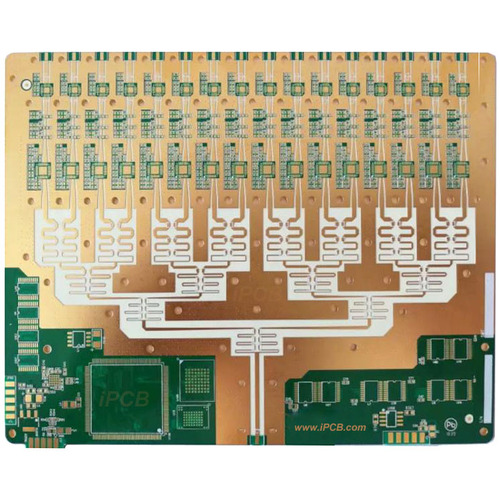
Rogers RO4003C™ PCB
RO4003C™ PCB has a low dielectric constant and low loss, making it suitable for high-speed digital and RF/microwave applications. It is commonly used in the aerospace and defense industries, especially for radar and sensor applications, because of its reliable performance.

Rogers RT/duroid® 5880 PCB
RT/duroid® 5880 PCB is famous for its extremely low dielectric constant and loss, making it ideal for critical microwave and millimeter-wave applications. It is used in automotive radar systems, satellite communications, and point-to-point wireless systems, where performance is everything.

Rogers TMM® PCB
TMM® PCB is made up of thermoset microwave materials that offer a range of dielectric constants. It is suitable for phased array antennas, microwave components, and aerospace electronics because it provides excellent thermal performance and mechanical rigidity.

Rogers ULTRALAM® 3000 PCB
ULTRALAM® 3000 PCB is made from liquid crystalline polymer (LCP) material, which is perfect for flexible and multilayer circuit constructions. It is excellent for high-frequency flexible circuits, making it ideal for telecommunications and high-reliability applications.

Rogers RO3003™ PCB
RO3003™ PCB is used in situations where high-frequency performance and low loss are crucial. It is commonly used in automotive radar applications, telecommunications, and precision instrumentation, ensuring reliable and efficient performance in demanding environments.
Why Choose South-Electronic?
Opt for South-Electronic for our expertise in bespoke, high-quality Rogers PCBs for diverse applications. Our team offers profound experience, ensuring premium quality at competitive rates and exceptional service from start to finish.
-
Quality Assurance
You want quality, and that's what we deliver.
At South-Electronic, we make sure every PCB is thoroughly checked, so you can trust that your products will work as expected. -
Cost Saving
Save more costs for you and get better quality
We offer competitive prices, so you can get high-quality PCBs without breaking your budget. -
Comprehensive Service
Provide you with simple and perfect solutions.
Our team is ready to answer your questions and provide support whenever you need it. You can count on us to help you through the process. -
Expert Support
You get to work with an experienced team.
With our one-stop service, we take care of everything from design to production and assembly. This way, you can focus on your business while we handle the details. -
Timely Delivery
Quickly delivered to your hands
Our efficient processes ensure that you get your PCBs when you need them, helping you stay on schedule.
Related Project We had Done
Customer Reviews
engineer
thank you, guys, the boards are really good, i am really happy to receive my boards, the components are perfect!
Operation Manager
South-Electronic is my first PCBA supplier in China. The service and quality are excellent, and the after-sales support is also very impressive. Good Job!
Common Questions
Most Popular Questions
South-Electronic offers expert consultation to help you select the most suitable Rogers material for your specific application. Our team evaluates your design requirements, performance criteria, and environmental factors to recommend the optimal material that balances cost and performance.
South-Electronic has a robust production capacity with multiple advanced manufacturing lines. We can handle a significant volume of orders per month, ensuring timely delivery without compromising quality, accommodating both small and large batch requests.
What are the typical lead times for production and delivery of
South-Electronic conducts comprehensive testing procedures, including electrical testing, thermal cycling, and mechanical stress tests, to ensure the reliability of our Rogers PCBs. Each batch undergoes rigorous quality checks to meet industry standards.
Yes, South-Electronic offers customization for Rogers PCBs, including specifications such as thickness, layer count, and material properties. Our engineering team works closely with you to tailor the PCBs to your exact needs.
South-Electronic's minimum order quantity for Rogers PCBs varies based on the specific product and complexity of the design. Generally, we accommodate both low and high volume orders, providing flexibility for different project sizes.
Send us a message
The more detailed you fill out, the faster we can move to the next step.
The Complete Guide for Rogers PCB
Contents
Chapter 1

Introduction to Rogers PCB
Brief Overview of Rogers PCBs
Rogers PCBs are specialized circuit boards crafted from high-frequency laminate materials developed by Rogers Corporation. Known for their exceptional thermal management and electrical performance, these PCBs are preferred in applications requiring reliable signal integrity and performance at high frequencies. Unlike traditional FR-4 PCBs, Rogers PCBs offer superior dielectric properties, making them ideal for advanced electronic applications.
Importance in the Electronics Industry
In the electronics industry, Rogers PCBs are heralded for their ability to meet the demanding requirements of modern devices, especially those operating in environments where high performance and reliability are crucial. Their unique properties support the miniaturization and functionality enhancement of components, making them indispensable in the production of cutting-edge electronics. This level of importance is driven by their capability to handle more complex circuits, higher speeds, and better overall performance compared to standard PCB materials.
Applications Across Various Sectors
Rogers PCBs are utilized across a diverse range of sectors, from telecommunications and aerospace to automotive and consumer electronics. In telecommunications, they facilitate high-speed data transmission and reliable network infrastructure. In aerospace and defense, Rogers PCBs are critical for crafting robust and dependable radar and navigation systems. The automotive industry leverages their performance for advanced driver-assistance systems and electric vehicle technologies. Moreover, consumer electronics benefit from their ability to enhance performance in gadgets requiring efficient heat management and high-frequency operation. As technology advances, the applications of Rogers PCBs continue to expand, pushing the boundaries of what’s possible in electronic design.
Chapter 2
Understanding Rogers Materials
Types of Materials Used in Rogers PCBs
Rogers PCBs are constructed using a variety of high-performance laminate materials specifically engineered by Rogers Corporation. These include PTFE (polytetrafluoroethylene) composites, hydrocarbon ceramics, and other specialized dielectric substrates. Each type of material is designed to meet the specific demands of high-frequency circuit applications. Common Rogers materials include RT/duroid®, RO4000®, RO3000®, and TMM® series, each offering distinct characteristics suited for different technological requirements and applications.
Comparison with Traditional FR-4 Materials
When compared to traditional FR-4 materials, Rogers materials offer superior electrical and thermal performance. FR-4 is a widely used material due to its cost-effectiveness and versatility in standard electronic applications, but it falls short in high-frequency scenarios where signal integrity and dielectric properties are critical. Rogers materials provide lower dielectric constant variability, reduced signal loss, and better thermal coefficient of expansion, which ensures consistent functionality even at high frequencies. Additionally, they offer improved thermal management capabilities, which are essential for the reliability and efficiency of complex electronic systems.
Key Benefits of Using Rogers Materials
The use of Rogers materials provides several key benefits:
Enhanced Signal Integrity: Rogers materials minimize signal loss and ensure greater reliability in high-speed and high-frequency applications.
Superior Thermal Management: Their excellent thermal properties help dissipate heat efficiently, reducing the risk of overheating and prolonging the lifespan of electronic components.
Consistency and Reliability: With stable dielectric properties over a wide range of temperatures and frequencies, Rogers materials deliver predictable performance, crucial for precision-driven applications.
Versatility in Applications: They are versatile enough to be used across various industries, offering tailored solutions for the specific needs of telecommunications, aerospace, automotive, and consumer electronics.
By integrating Rogers materials into PCBs, manufacturers can achieve the high performance and reliability required for today’s demanding electronic applications, making them a preferred choice for cutting-edge technology innovations.
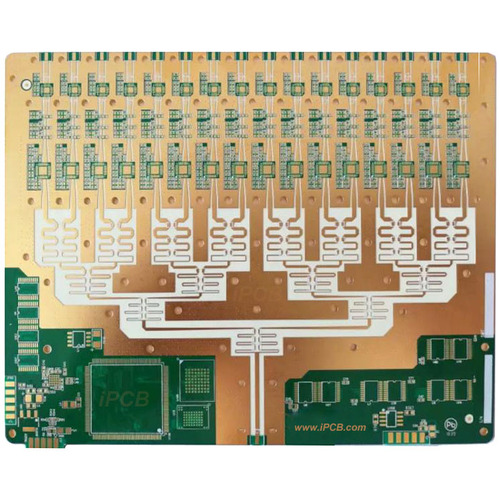
Chapter 3

Properties of Rogers PCBs
Thermal Management Capabilities
Rogers PCBs are renowned for their exceptional thermal management capabilities. These PCBs utilize advanced dielectric materials that effectively dissipate heat, critical for maintaining the performance and longevity of electronic components. The thermal conductivity of Rogers materials ensures that heat is quickly and efficiently channeled away from sensitive circuit elements, reducing the risk of thermal-related failures. This capability is particularly beneficial in applications involving high power and high frequency, where components can generate significant heat. As a result, Rogers PCBs are ideal for environments where temperature stability is crucial, such as in power amplifiers and high-frequency communication devices.
Electrical Performance Attributes
The electrical performance of Rogers PCBs is one of their most distinctive properties. They exhibit low dielectric constant and loss tangent, which minimize signal distortion and loss in high-frequency operations, leading to superior signal integrity. These materials provide excellent impedance control, essential for maintaining signal integrity at high speeds. Additionally, Rogers PCBs have a low coefficient of thermal expansion (CTE), which helps maintain stable electrical performance across a broad temperature range. These attributes make them suitable for advanced RF and microwave applications, where precision and performance cannot be compromised.
Durability and Reliability
Rogers PCBs offer outstanding durability and reliability, which are essential for high-performance and mission-critical applications. The inherent strength of Rogers materials provides resilience against mechanical stress and environmental conditions, such as moisture and chemical exposure. Their stability under varying thermal and electrical conditions ensures consistent performance over long periods, reducing the likelihood of failure and maintenance costs. This reliability is vital in industries like aerospace and defense, where equipment must operate flawlessly under intense conditions. Overall, the durability and reliability of Rogers PCBs make them a preferred choice for any application where performance and dependability are required over the lifespan of the product.
Chapter 4
Designing with Rogers PCB
Design Considerations and Best Practices
When designing with Rogers PCBs, several key considerations and best practices must be taken into account to fully leverage their advanced capabilities.
Material Selection: Choosing the appropriate Rogers material is critical based on the application’s frequency, thermal requirements, and environmental conditions. Each material offers unique characteristics that can significantly impact performance.
Impedance Control: Maintaining precise impedance is essential for high-frequency applications. Designers should carefully plan trace geometries and spacing to ensure consistent impedance throughout the design.
Thermal Management: Incorporating adequate heat dissipation techniques, such as thermal vias, copper planes, and heat sinks, can optimize thermal performance and maintain reliability.
Layer Stack-up Design: Properly planning the layer stack-up can enhance signal integrity and minimize issues such as crosstalk and electromagnetic interference (EMI). This involves considering the arrangement of signal, power, and ground layers.
Component Placement and Routing: Strategic component placement and efficient routing can reduce path lengths and minimize signal loss or delay, crucial in maintaining signal integrity in high-speed circuits.
Software Tools for Designing Rogers PCBs
Designing Rogers PCBs requires specialized software tools that can handle the complexities of high-frequency circuit design. Popular tools include:
Altium Designer: Offers comprehensive solutions for high-frequency and high-speed designs, with features that facilitate precise impedance matching and signal integrity analysis.
Cadence Allegro: Known for its advanced capabilities in RF and microwave design, it provides powerful simulation tools to predict electrical performance.
Mentor Graphics Xpedition: Provides robust simulation and verification tools focused on ensuring thermal and electrical performance in Rogers PCB designs.
ADS (Advanced Design System) by Keysight: Specifically tailored for RF, microwave, and high-speed digital applications, enabling accurate modeling and validation of complex circuits.
Challenges in Rogers PCB Design
Designing Rogers PCBs, while advantageous, presents several challenges:
Complexity in Material Handling: The unique properties of Rogers materials require careful handling during the manufacturing process to avoid defects and ensure performance.
Cost Considerations: Rogers materials can be significantly more expensive than traditional FR-4 materials, necessitating careful cost-benefit analysis, particularly for large-scale production.
Thermal and Mechanical Constraints: Designers must carefully manage the thermal and mechanical constraints to prevent warping or delamination, which can occur due to the different thermal expansion properties of the materials.
Precision in High-Frequency Design: Achieving precise impedance control and reducing EMI in high-frequency environments requires advanced design expertise and meticulous attention to detail.
Despite these challenges, adhering to best practices and leveraging specialized design tools can help overcome obstacles and maximize the benefits of Rogers PCBs in complex electronic applications.

Chapter 5

Manufacturing Processes for Rogers PCB
Key Steps in the Manufacturing Process
Manufacturing Rogers PCBs involves a series of precise and controlled steps to ensure the production of high-quality boards that meet specialized performance requirements.
Material Preparation: The process begins with selecting the appropriate Rogers laminate based on design specifications. Sheets are carefully prepared and cleaned to remove any contaminants that could affect adhesion and performance.
Image Transfer: The PCB design is transferred onto the copper-clad laminate using photolithography. This involves applying a photosensitive film (photoresist), exposing it to UV light through a photomask of the PCB design, and developing the image.
Etching: The exposed copper is etched away, leaving only the desired circuit patterns. This step must be tightly controlled to ensure dimensional accuracy and prevent over-etching or under-etching.
Drilling and Plating: Holes for vias and through-hole components are drilled using precision CNC machines. The drilled holes are then plated to ensure electrical connectivity throughout the layers of the PCB.
Lamination: For multilayer PCBs, individual layers are stacked and laminated under heat and pressure to form a single bonded structure. This step is crucial for ensuring mechanical stability and alignment.
Surface Finishing: A surface finish is applied to protect the exposed copper and provide a solderable surface. Common finishes include HASL (Hot Air Solder Leveling), ENIG (Electroless Nickel Immersion Gold), and others tailored for specific applications.
Solder Mask and Silkscreen: A solder mask is applied to prevent solder bridging between conductive traces. Silkscreen printing is used to add component labels and other identifiers to the board.
Technologies and Techniques Used
The manufacturing of Rogers PCBs employs advanced technologies and techniques:
Precision CNC Drilling: Ensures accurate hole placement and sizing, crucial for performance in high-frequency applications.
Laser Direct Imaging (LDI): Used in image transfer for fine-line PCB patterns, offering greater precision than traditional photolithography methods.
Automated Optical Inspection (AOI): Systems use high-resolution cameras and algorithms to inspect the board for defects during various stages of manufacturing, ensuring quality and consistency.
High-frequency Test Equipment: Used to evaluate electrical performance throughout manufacturing to ensure that the board meets specified high-frequency requirements.
Quality Control Measures
Rogers PCBs are subject to rigorous quality control measures to ensure they meet stringent standards necessary for their specialized applications.
Material Verification: Before production, materials are inspected and verified for compatibility with intended applications, focusing on dielectric properties and physical dimensions.
Dimensional Accuracy: Layers and traces are measured with high precision instruments to verify that they meet design specifications, avoiding any deviations that might affect performance.
Electrical Testing: Every PCB undergoes electrical testing to confirm continuity, impedance, and insulation resistance, validating that the board performs correctly under operational conditions.
Thermal Stress Testing: Boards are stress-tested to ensure they can withstand the thermal cycles experienced in their operational environments without degradation.
Final Inspection: A comprehensive final inspection is conducted, often incorporating both human and machine oversight, to ensure that boards are free from visual defects and meet all specified quality criteria before delivery.
By maintaining stringent controls at each stage of the manufacturing process, Rogers PCBs are produced with the reliability and performance required for demanding high-frequency and high-power applications.
Chapter 6
Applications of Rogers PCB
Use Cases in Telecommunications, Aerospace, and Automotive Industries
Rogers PCBs are highly regarded for their exceptional performance in several industry sectors, primarily due to their ability to handle complex electronic requirements effectively.
Telecommunications: In this industry, Rogers PCBs are used extensively in RF and microwave components, such as antennas, amplifiers, and transmitters. Their excellent dielectric properties and superior thermal management capabilities make them ideal for maintaining signal integrity and reducing losses in high-frequency communication systems.
Aerospace: The aerospace industry demands materials that can withstand extreme conditions, including high temperatures, humidity, and vibration. Rogers PCBs meet these challenges by offering outstanding durability and reliability. They are utilized in radar systems, aerospace sensors, and satellite communications, where precise performance is critical.
Automotive: As the automotive industry advances, especially with the development of electric vehicles and autonomous driving technologies, the demand for high-performance electronic systems has grown. Rogers PCBs are used in radar and sensor systems, power management systems, and infotainment systems due to their stability under variable conditions and excellent electrical performance.
Benefits in High-Frequency Applications
Rogers PCBs are particularly advantageous in high-frequency applications due to their specialized material properties:
Low Dielectric Loss: They exhibit minimal dielectric loss, which is crucial in preserving signal clarity and strength in high-frequency operations, reducing the potential for distortion or attenuation.
Consistent Dielectric Constant: Their stable dielectric constant across a wide range of frequencies and temperatures ensures predictable electrical performance, an essential requirement in sophisticated RF and microwave applications.
High Power Handling Capabilities: The materials used in Rogers PCBs can efficiently dissipate heat, allowing them to handle high power levels without compromising performance, making them suitable for use in high-power RF applications.
Emerging Applications and Trends
As technology advances, Rogers PCBs are at the forefront of several emerging applications and trends:
5G Technology: The rollout of 5G networks requires components that can operate at higher frequencies and with greater efficiency. Rogers PCBs are increasingly used in the development of 5G infrastructure, including base stations and small cells, where high performance at millimeter-wave frequencies is necessary.
IoT and Wearables: With the expansion of the Internet of Things and the demand for more compact and efficient devices, Rogers PCBs are being used in miniaturized sensors and communication modules, thanks to their lightweight construction and exceptional performance.
Advanced Automotive Electronics: As vehicles become more intelligent, using complex electronics systems for autonomous driving, ADAS (Advanced Driver-Assistance Systems) and vehicle-to-everything (V2X) communication systems, Rogers PCBs provide the necessary reliability and precision.
Military and Defense Applications: The need for sophisticated electronics in modern warfare has propelled the use of Rogers PCBs in military communication devices, radar, and guidance systems, where environmental stability and robust performance are paramount.
In summary, the diverse applications of Rogers PCBs in high-tech industries are driven by their unmatched performance attributes, making them a cornerstone for current and future technological advancements.

Chapter 7

Comparing Rogers PCBs with Other PCB Types
Differences and Similarities with Other PCBs
Rogers PCBs differ from traditional PCBs, such as those made from FR-4 material, in several ways:
Dielectric Properties: Rogers PCBs offer lower dielectric constant (DK) and loss tangent compared to FR-4, enhancing performance for high-frequency applications. This results in improved signal integrity and reduced signal losses.
Thermal Management: Rogers materials have superior thermal conductivity, allowing them to dissipate heat more effectively than standard FR-4 PCBs, which is crucial for applications with significant thermal demands.
Material Composition: Rogers PCBs are composed of hydrocarbon ceramic laminates, which provide better mechanical stability and electrical performance, whereas FR-4 is made from woven glass and epoxy resin.
Environmental Stability: Rogers materials tend to offer greater stability across a wide range of temperatures and environmental conditions, making them suitable for harsh environments.
Pros and Cons Compared to Traditional PCBs
Pros:
High-Frequency Performance: The main advantage of Rogers PCBs is their ability to perform exceptionally well at high frequencies, making them ideal for RF and microwave applications.
Thermal and Mechanical Robustness: They offer excellent thermal management and mechanical stability, which extends the lifespan of electronic components.
Low Signal Loss: Their low dielectric loss and consistent DK improve signal clarity and strength, reducing distortion and crosstalk.
Design Flexibility: Rogers materials support intricate designs, enabling complex multilayer configurations needed for advanced applications.
Cons:
Higher Cost: Rogers PCBs are more expensive than traditional FR-4 PCBs due to their specialized materials and manufacturing processes.
Complex Manufacturing Requirements: The precision manufacturing processes required for Rogers PCBs can be more complex, often necessitating specialized equipment and expertise.
Cost Implications and Performance Advantages
The cost implications of using Rogers PCBs are significant, primarily because of the higher price of raw materials and the specialized manufacturing techniques required. However, these costs can be justified in scenarios where performance gains are critical:
Performance Advantages: Rogers PCBs provide unparalleled performance in applications demanding high-frequency operation, precise impedance control, and thermal reliability, which are not feasible with standard PCBs.
Long-Term Value: Despite the higher upfront cost, the enhanced reliability and longevity of Rogers PCBs can lead to lower maintenance and replacement costs over the lifecycle of a product.
Cost-Benefit Analysis: For applications where the advantages of superior performance and reliability outweigh cost considerations, opting for Rogers PCBs provides significant benefits. Industries such as telecommunications, aerospace, and defense often perceive Rogers PCBs as an investment in quality and reliability.
In conclusion, while Rogers PCBs are more costly compared to traditional PCB types, their specialized capabilities make them indispensable in high-performance applications where precision, durability, and reliability are of utmost importance.
Chapter 8
Troubleshooting Common Issues with Rogers PCBs
Identifying and Addressing Common Problems
Even with the advanced capabilities of Rogers PCBs, designers and engineers may encounter various issues during design, manufacturing, or usage. Understanding and addressing these problems is crucial for maintaining the performance and reliability of the PCBs.
Impedance Variance: Variations in impedance can lead to signal integrity issues, especially in high-frequency applications.
- Solution: Ensure precise control over trace width and spacing during the design phase. Regularly calibrate manufacturing equipment to maintain consistency, and use simulation tools to predict impedance issues.
Delamination: This can occur if the PCB is subjected to inappropriate thermal stress or if there are voids in the laminate.
- Solution: Pay attention to thermal profiles during manufacturing. Ensure that the lamination process is carefully controlled with appropriate pressure and temperature settings to avoid delamination.
Via Failures: High-frequency and thermal stresses can lead to via failures.
- Solution: Use filled and capped vias for better mechanical stability and thermal performance. Opt for via-in-pad structures to reduce inductance and enhance heat dissipation.
Solderability Issues: Poor solderability can arise from the surface finish or contamination on the board’s surface.
- Solution: Use high-quality surface finishes like ENIG or immersion silver. Ensure thorough cleaning and proper handling throughout the manufacturing process to prevent contamination.
Tips for Ensuring Optimal Performance
Design Precision: Utilize advanced PCB design tools that provide detailed analysis for high-frequency layouts. Leverage 3D EM simulation to more accurately predict PCB performance.
Signal Integrity Checks: Regularly perform signal integrity analysis, especially when changes are made to the design, to ensure that the board maintains its performance specifications.
Thermal Management: Implement robust thermal management strategies, such as heat sinks, thermal vias, and copper pours, to manage heat distribution effectively.
Component Selection: Choose components that are compatible with high-frequency operations and can handle the thermal and mechanical stresses specific to your application.
Maintenance and Repair Strategies
Maintaining the integrity of Rogers PCBs over time involves both preventive and corrective measures:
Regular Inspections: Conduct visual and functional inspections to identify signs of wear, delamination, or thermal damage early. Use optical and X-ray inspection tools for thorough analysis.
Environmental Control: Store and operate PCBs in environments that adhere to specified temperature and humidity ranges to prevent moisture absorption and thermal expansion issues.
Repairs: For damaged boards, careful rework can be performed by trained technicians. This may include repairing damaged traces, replacing failed components, or even patching certain areas with new copper or dielectric material.
Cleaning: Use appropriate cleaning agents that do not leave residues and ensure that the PCBs are free from dust and debris, which can cause short circuits or impact performance.
By proactively addressing these challenges and implementing rigorous quality control and maintenance strategies, engineers can greatly enhance the reliability and functionality of Rogers PCBs in their applications.

Chapter 9
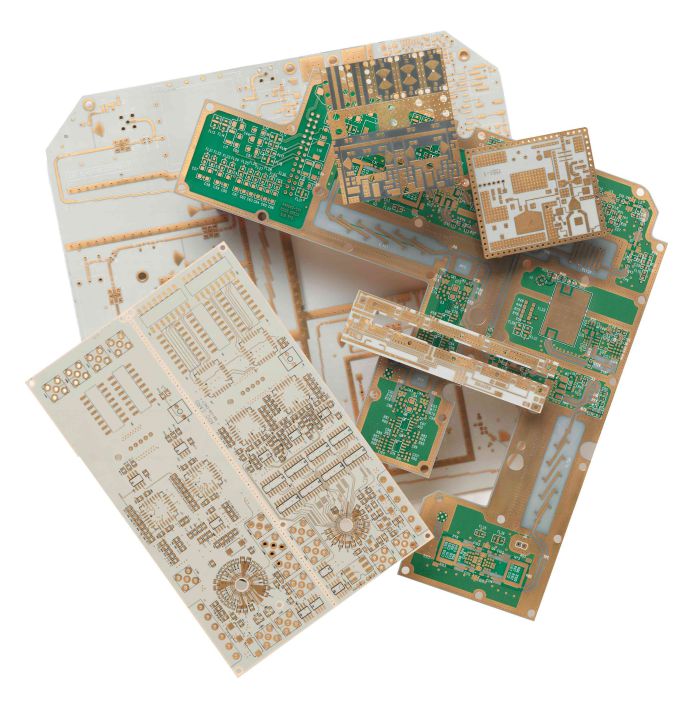
Future Trends in Rogers PCBs
Innovations and Advancements in Materials and Design
The future of Rogers PCBs is being shaped by ongoing innovations in materials and design techniques, responding to the evolving needs of high-frequency and high-performance applications.
Advanced Material Development: Future Rogers materials are expected to offer even lower dielectric constants and reduced loss tangents, enhancing high-frequency performance. Developments in composite and nano-materials might lead to laminates with improved thermal properties and mechanical strength.
Miniaturization and Integration: As electronics continue to shrink, Rogers PCBs will see advancements in miniaturization, enabling more compact designs with integrated components. Innovations such as embedded passive components and system-in-package (SiP) will become more prevalent.
Improved Thermal Management Solutions: The integration of new materials and designs focusing on thermal dissipation will be a priority, supporting electronics that operate at higher power densities without compromising reliability.
Impact of Emerging Technologies
Emerging technologies are set to significantly influence the development and application of Rogers PCBs:
5G and Beyond: As global 5G adoption accelerates and the groundwork for 6G begins, Rogers PCBs will be crucial in supporting infrastructure and devices that operate at increasingly higher frequencies.
Automotive Advancements: The rise of electric and autonomous vehicles necessitates advanced electronic systems that Rogers PCBs are well suited to support, from radar and lidar systems to power management and connectivity solutions.
IoT Expansion: The growth of IoT applications will drive demand for PCBs that can sustain reliable, long-range communication in compact formats. Rogers PCBs will play a vital role in providing the necessary performance characteristics.
AI and Machine Learning Interfaces: Advanced processing and connectivity requirements in AI-driven devices are creating a demand for PCBs that can manage complex data flows and real-time processing, areas where Rogers PCBs excel.
Predictions for Market Growth and Demand
The demand for Rogers PCBs is expected to grow substantially in the coming years, driven by several factors:
Increased Adoption in Telecommunications and Aerospace: Continued investment in telecommunications infrastructure and aerospace innovation will sustain demand for high-performance PCBs that can operate under stringent conditions.
Expanding Automotive Market: As modern vehicles integrate more sophisticated electronic systems, the demand for PCBs capable of handling high frequencies and robust electrical performance will increase.
Growth of Consumer Electronics: Innovations in consumer electronics that require efficient, high-speed connectivity will contribute to increased usage of Rogers PCBs.
Global Market Expansion: As technology development accelerates internationally, particularly in regions focused on industrial advancement (like Asia-Pacific), the market for Rogers PCBs is poised for significant expansion.
Overall, the future of Rogers PCBs looks promising, with technological advancements driving their integration into an ever-expanding range of applications. As industries continue to push the boundaries of what’s achievable with high-frequency electronics, Rogers PCBs will remain a cornerstone of innovation and development.
Chapter 10
Selecting the Right Supplier for Rogers PCB
Criteria for Choosing a Reliable Supplier
Selecting the right supplier for Rogers PCBs is crucial to ensure the quality, performance, and reliability of the final product. Here are some key criteria to consider:
Expertise and Experience: Look for suppliers with extensive experience in manufacturing Rogers PCBs. A proven track record in handling high-frequency and advanced materials is essential.
Quality Assurance Processes: Ensure that the supplier follows stringent quality control measures and complies with industry standards and certifications (e.g., ISO 9001, IPC standards).
State-of-the-Art Facilities: Advanced and well-maintained manufacturing facilities equipped with the latest technology and tools are vital for producing high-quality PCBs.
Customization Capabilities: The supplier should offer flexibility in customization to meet specific design requirements and accommodate complex multilayer PCBs.
Technical Support and Collaboration: A supplier who provides excellent technical support and is willing to collaborate closely during the design and manufacturing processes can significantly enhance the final product.
Case Studies of Successful Implementations
Here are a couple of examples of successful implementations of Rogers PCBs by major companies or in specific applications:
Telecommunications Infrastructure Company: A leading telecommunications firm partnered with a PCB manufacturer specializing in Rogers materials to develop advanced high-frequency circuit boards for their 5G network infrastructure. The boards, designed for optimal signal integrity and thermal management, contributed to higher network reliability and performance, setting a benchmark in 5G deployments.
Aerospace Defense Contractor: A top aerospace company required robust PCBs for their radar and communication systems used in military applications. Collaborating with an experienced Rogers PCB supplier, they successfully implemented multilayer boards with complex designs that withstood extreme environmental conditions, resulting in enhanced system reliability and mission success.
These case studies highlight the importance of selecting a capable supplier with specific expertise in Rogers PCBs to achieve optimal results in demanding applications. By carefully evaluating potential suppliers based on their experience, capabilities, and support offerings, companies can ensure their projects benefit from high-quality, high-performance PCBs.

Get in touch
Where Are We?
Industrial Park, No. 438 Donghuan Road, No. 438, Shajing Donghuan Road, Bao'an District, Shenzhen, Guangdong, China
Floor 4, Zhihui Creative Building, No.2005 Xihuan Road, Shajing, Baoan District, Shenzhen, China
ROOM A1-13,FLOOR 3,YEE LIM INDUSTRIAL CENTRE 2-28 KWAI LOK STREET, KWAI CHUNG HK
service@southelectronicpcb.com
Phone : +86 400 878 3488
Send us a message
The more detailed you fill out, the faster we can move to the next step.
