Do You Need Separate Flux with Rosin Core Solder?
When you're using rosin flux core solder, it usually has enough flux to solder most electronics. But sometimes it's helpful to add more flux, like when you're working with big, oxidized surfaces or you're doing rework on complicated assemblies. If you know what flux does and what kinds there are, you can make better choices and get stronger, more reliable solder joints.
What is Flux and How Does It Work?
The Role of Flux in Soldering
Flux is like a cleaning agent that you use when you're soldering. It gets rid of all the crud and junk on the metal surfaces so that you can get a good connection. When you heat up metal, it oxidizes, and that can stop the solder from sticking. Flux cleans the metal surfaces so that the solder sticks better.
Types of Flux
There are several types of flux used in soldering, each with specific characteristics and applications:
Type of Flux | Characteristics | Common Applications |
---|---|---|
Rosin Flux | Non-corrosive, mild, often used in electronics. | PCB assembly, wire soldering. |
No-Clean Flux | Minimal residue, does not require cleaning. | Surface-mount technology (SMT). |
Water-Soluble Flux | Strong cleaning action, requires cleaning after use. | Critical electronic applications. |
Acid Flux | Aggressive cleaning, highly corrosive, not for electronics. | Plumbing, metal repair. |
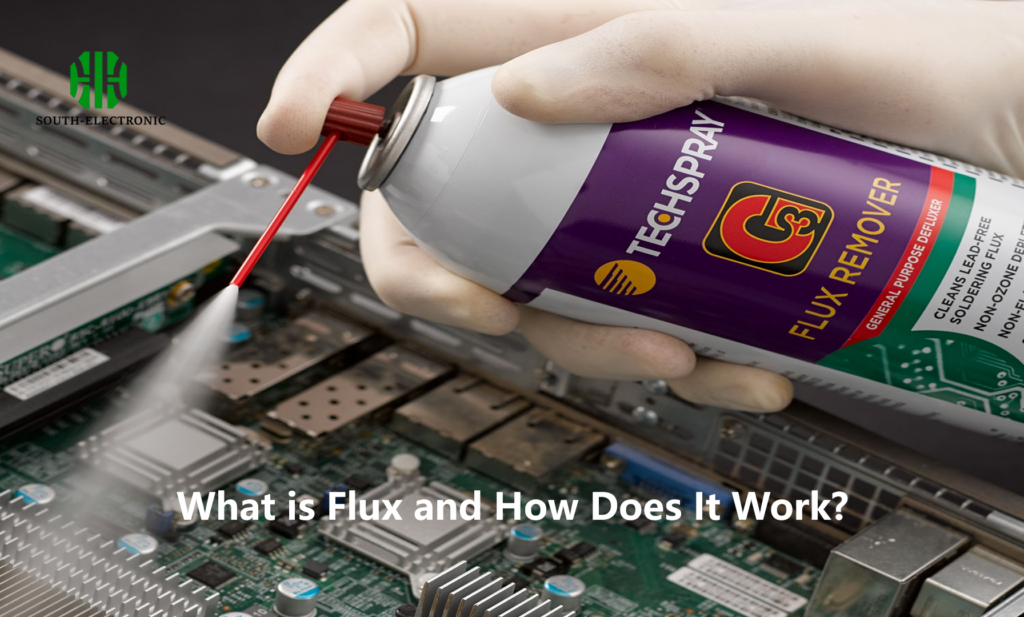
What is Rosin Core Solder and How Does It Work?
Composition of Rosin Core Solder
Rosin core solder is made up of a metal alloy (usually tin and lead, or tin and silver) with a core that contains rosin flux. When the solder melts, the flux is released and cleans the surfaces to create a strong bond.
Advantages of Rosin Core Solder
Rosin core solder is particularly favored in electronics for its ease of use and effectiveness. The main advantages include:
- Non-corrosive: Rosin flux does not corrode metal surfaces, making it safe for sensitive electronic components.
- Self-cleaning: As the solder melts, the rosin flux cleans the metal surfaces, eliminating the need for a separate flux application in many cases.
- Heat resistance: Rosin core solder can withstand the high temperatures used in soldering without degrading, ensuring durable joints.
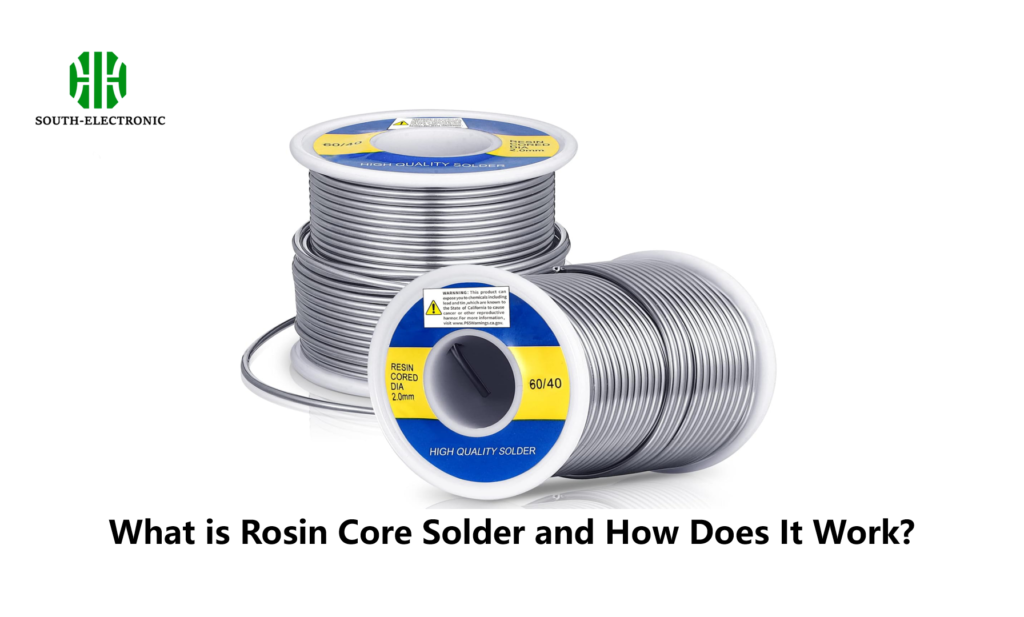
Do You Always Need Additional Flux?
When Additional Flux May Not Be Necessary
For many electronics applications, the flux within rosin core solder is sufficient. Here’s why:
- Pre-cleaned Components: If the components and PCB are already clean, the flux in the rosin core will typically be enough to ensure a good connection.
- Small or Standard Joints: For standard soldering tasks, such as connecting wires or small components, the rosin core’s flux should provide adequate cleaning and bonding.
Scenarios Where Additional Flux is Beneficial
However, there are situations where adding extra flux can improve the soldering process:
- Large or Heavily Oxidized Surfaces: If you’re working with larger components or surfaces that have oxidized significantly, applying additional flux can enhance solder flow and improve the strength of the joint.
- Rework or Repair Jobs: When desoldering or reworking joints, additional flux can help by reactivating the existing solder and ensuring a clean reflow.
- Complex Assemblies: For intricate or high-density boards, extra flux can help ensure that solder reaches all necessary connections, especially in tight spaces.
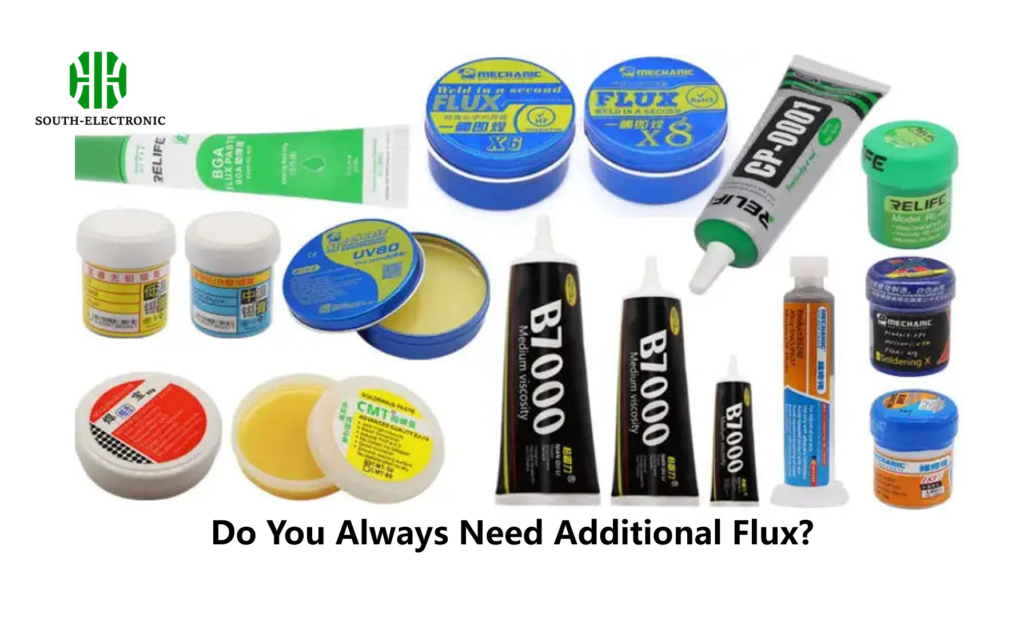
Rosin Core vs. Other Types of Flux: What’s the Difference?
Comparison of Flux Types
It’s important to understand the differences between rosin flux and other types of flux to decide whether additional flux is necessary. Here’s a table comparing the most commonly used fluxes in electronics:
Flux Type | Benefits | Drawbacks |
---|---|---|
Rosin Flux | Safe for electronics, no cleaning required. | Not as effective on heavily oxidized metals. |
No-Clean Flux | Leaves minimal residue, easy to use. | Residue might still affect sensitive circuits. |
Water-Soluble Flux | Strong cleaning action, excellent for critical joints. | Requires thorough cleaning to prevent corrosion. |
Acid Flux | Effective for non-electronics applications. | Highly corrosive, unsuitable for electronics. |