Поставщик алюминиевых печатных плат
South-Electronic
Выбирайте South-Electronic для непревзойденного качества, надежности и исключительной ценности в решениях для печатных плат. Мы делаем всё: от проектирования до доставки с точностью и в соответствии с высочайшими отраслевыми стандартами. Будь то индивидуальные решения или быстрые прототипы, мы готовы помочь вам достичь успеха.
Улучшите свои продукты с высококачественными алюминиевыми печатными платами
Добро пожаловать в South-Electronic! Мы – ваш лучший выбор для премиальных алюминиевых печатных плат, которые создаются на долгий срок и эффективно охлаждают устройства. Наши современные решения подходят даже для самых сложных задач. Нужна высокая точность или прототип в короткие сроки? Мы вам поможем!
Сотрудничая с нами, вы получаете партнёра, который стремится сделать ваши продукты лучше, производственный процесс – эффективнее, а бизнес – успешнее. Давайте работать вместе!
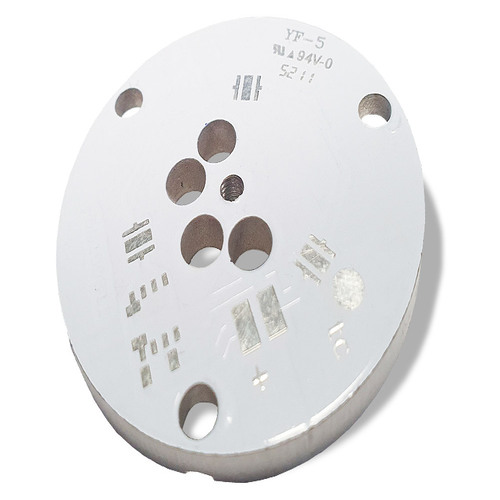
Однослойная алюминиевая печатная плата
Этот тип печатной платы имеет медное покрытие только с одной стороны и используется для простых однослойных схем. Широко применяется в светодиодном освещении и потребительской электронике благодаря своей экономичности и простоте производства.
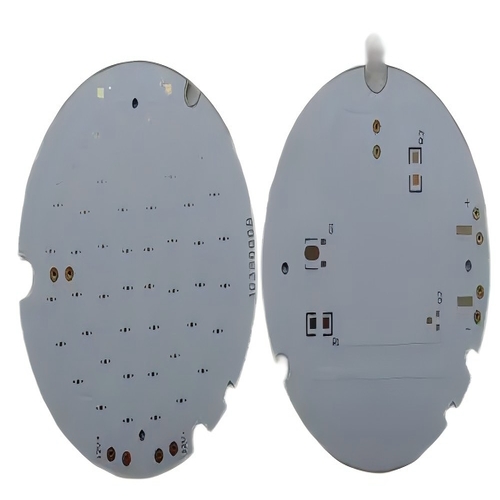
Двухслойная алюминиевая печатная плата
Эта плата имеет медные слои с обеих сторон и подходит для более сложных схем, требующих теплового управления с обеих сторон платы. Обычно используется в электронных устройствах, работающих с умеренными уровнями мощности.
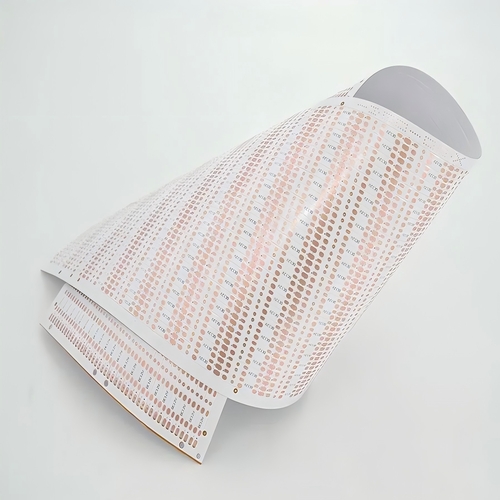
Гибкая алюминиевая печатная плата
Изготовленные из гибких материалов, эти печатные платы могут сгибаться или складываться, что делает их идеальными для носимых устройств и мобильных технологий. Они сочетают в себе тепловые преимущества алюминия с гибкостью конструкции.
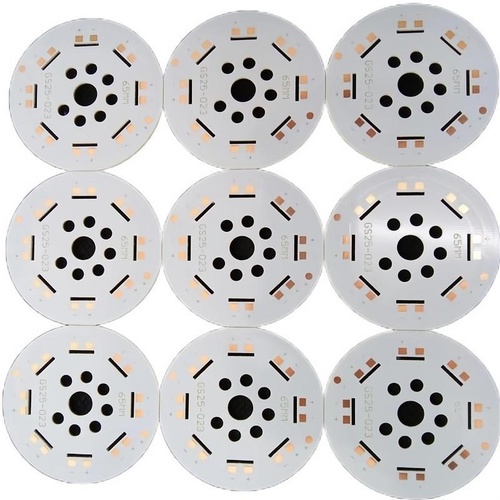
IMS печатная плата
IMS печатные платы обладают отличной теплопроводностью и идеально подходят для приложений, требующих быстрого отвода тепла. Обычно используются в преобразователях мощности, системах светодиодного освещения и автомобильной электронике, эффективно отводя тепло от критических компонентов благодаря металлическому основанию.
Почему выбирают South-Electronic?
-
Индивидуальные решения
Создано специально для вашего проекта.
Работайте в тесном сотрудничестве с South-Electronic, чтобы адаптировать решение для вашей печатной платы, которое будет точно соответствовать вашим специфическим требованиям. Будь то специализированный компонент или сложный дизайн, вы можете рассчитывать на нас в предоставлении нужной продукции. -
Премиальное качество
Вы заслуживаете лучшего, и качество — наш главный приоритет.
Благодаря нашим строгим процессам контроля качества, включая тщательные проверки и тестирование, мы гарантируем, что ваша продукция будет соответствовать самым высоким стандартам. Наши печатные платы без дефектов, поэтому вы можете быть уверены в их надежности в процессе производства. -
Прозрачная коммуникация
Мы предоставляем ясное, оперативное и эффективное обслуживание.
Именно поэтому мы обеспечиваем четкую и оперативную поддержку на протяжении всего процесса. Если у вас есть вопрос или вам нужно обновление, мы всегда держим вас в курсе и следим за успешным ходом вашего проекта. -
Конкурентные цены
Вы хотите получить лучшее качество по лучшей цене.
Именно поэтому мы предлагаем печатные платы высшего качества по конкурентоспособным ценам. Вы можете максимизировать свою прибыль, не жертвуя высокими стандартами, которых вы требуете. Мы предлагаем экономически эффективные решения без ущерба качеству, чтобы вы могли опережать конкурентов. -
Быстрая международная доставка
Вам нужен партнер, который будет успевать за вашим динамичным бизнесом.
Мы предлагаем международную доставку с быстрым временем выполнения заказов, чтобы ваши печатные платы прибывали вовремя. С нашей надежной логистикой вам не придется беспокоиться о задержках. Вы сможете соблюдать сроки и поддерживать бесперебойное производство.Вам нужен партнер, который будет успевать за вашим динамичным бизнесом. Мы предлагаем международную доставку с быстрым временем выполнения заказов, чтобы ваши печатные платы прибывали вовремя. С нашей надежной логистикой вам не придется беспокоиться о задержках. Вы сможете соблюдать сроки и поддерживать бесперебойное производство.
Связанные проекты, которые мы реализовали
Отзывы клиентов
Часто задаваемые вопросы
Самые популярные вопросы
South-Electronic предлагает широкий выбор алюминиевых печатных плат, включая однослойные, двусторонние и многослойные конфигурации. Эти варианты подходят для широкого спектра электронных приложений, обеспечивая идеальное решение для вашего проекта.
South-Electronic специализируется на предоставлении индивидуальных решений, используя наши передовые методы производства для точного соответствия вашим требованиям дизайна. Будь то уникальная форма, размер или спецификация производительности, South-Electronic обеспечит нужный результат.
В South-Electronic мы уделяем первостепенное внимание качеству и надежности. Наши алюминиевые печатные платы проходят строгий контроль качества и имеют пятилетнюю гарантию. Мы гордимся тем, что сертифицированы по стандартам ROHS, UL и ISO, что подтверждает нашу приверженность к совершенству.
Время часто играет ключевую роль. Поэтому мы предлагаем услуги ускоренной обработки, чтобы помочь вам уложиться в сжатые сроки без потери качества.
Мы серьезно относимся к экологической ответственности. Наши производственные процессы спроектированы таким образом, чтобы быть максимально экологичными, гарантируя, что наши алюминиевые печатные платы обладают высокой производительностью и экологической устойчивостью.
В South-Electronic мы делаем все, чтобы вы получили свои товары быстро. Мы знаем, что это важно, поэтому стараемся доставить их как можно быстрее. Мы не теряем вашего времени.
Отправьте нам сообщение
Чем подробнее вы заполните, тем быстрее мы сможем перейти к следующему шагу.
Полное руководство по алюминиевым печатным платам
Содержание
Глава 1
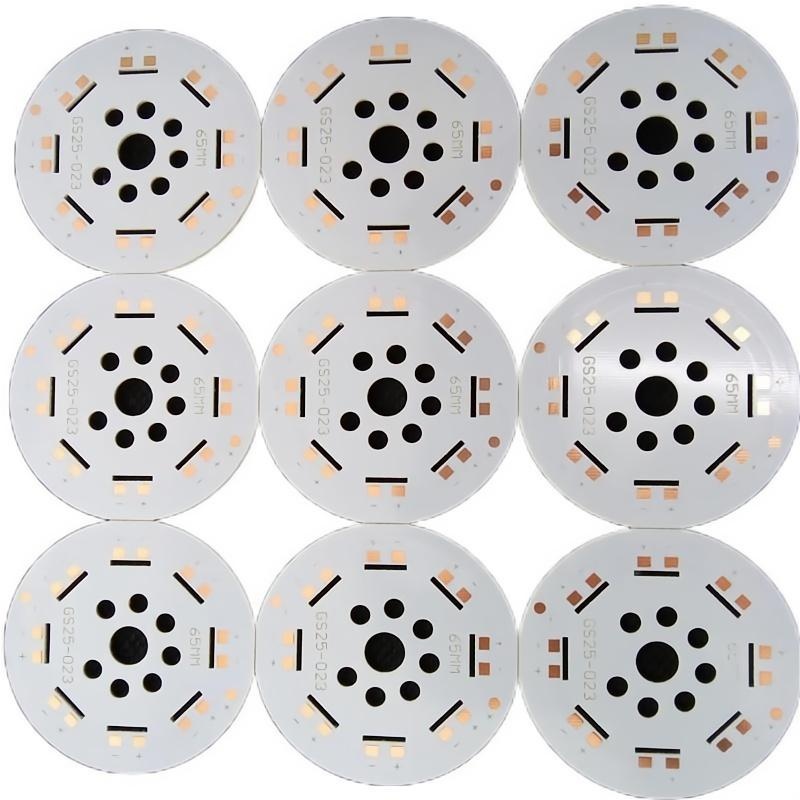
Введение в алюминиевые печатные платы
Определение и обзор
Алюминиевые печатные платы, также известные как печатные платы с металлическим основанием (MCPCBs), представляют собой специализированные платы, которые используют металлический субстрат, обычно алюминий, для улучшения отвода тепла. В отличие от традиционных печатных плат, изготовленных в основном из материалов FR-4, алюминиевые печатные платы имеют металлический базовый слой, который действует как теплоотвод, что особенно важно для приложений с высокой мощностью. Такая конструкция делает платы более прочными и эффективными в управлении теплом, что делает их идеальными для электронных устройств, работающих при высоких температурах.
Преимущества по сравнению с традиционными печатными платами
- Повышенная теплопроводность: Алюминиевые печатные платы обладают лучшей теплопроводностью, чем традиционные платы, что позволяет эффективно отводить тепло от важных компонентов, предотвращая перегрев и обеспечивая стабильность.
- Улучшенная стабильность размеров: Металлический субстрат обеспечивает лучшую стабильность размеров, позволяя алюминиевым платам работать в широком диапазоне температур.
- Высокая механическая прочность: Эти печатные платы более устойчивы к механическим нагрузкам, что делает их подходящими для использования в условиях вибрации или ударов.
- Легкие, но прочные: Несмотря на металлическую основу, алюминиевые печатные платы остаются относительно легкими, обеспечивая отличное соотношение прочности и веса.
- Экономичное управление теплом: Благодаря устранению необходимости в дополнительных радиаторах или охлаждающих устройствах, алюминиевые платы сокращают как системные затраты, так и требования к пространству.
Основные области применения и индустрии
Алюминиевые печатные платы широко применяются в различных отраслях благодаря их выдающимся термическим и механическим характеристикам. Основные области применения включают:
- Светодиодное освещение: Алюминиевые печатные платы играют ключевую роль в светодиодных приложениях, так как способствуют рассеиванию тепла, улучшая производительность и продлевая срок службы светодиодов.
- Преобразователи мощности: Используются в модулях питания и регулирования, где важно управление теплом.
- Автомобильная промышленность: Применяются в автомобильной электронике, такой как системы торможения и акселерации, где важны прочность и управление теплом.
- Потребительская электроника: Используются в аудиочастотных устройствах и схемах высокой плотности, требующих материалов, устойчивых к высоким температурам.
- Телекоммуникации: Применяются в маршрутизаторах и передающих платах, работающих с высокочастотными сигналами и тепловыми нагрузками.
Используя уникальные свойства алюминиевых печатных плат, эти отрасли достигают повышения производительности, надежности и долговечности своих электронных устройств, открывая путь для инновационных решений и приложений.
Глава 2
Типы алюминиевых печатных плат
Односторонние алюминиевые печатные платы
Односторонние алюминиевые печатные платы – это самый простой тип таких плат, с одним проводящим слоем меди на одной стороне алюминиевого субстрата. Обычно они используются в приложениях, где требуется только один слой схемы. Алюминиевая основа обеспечивает отличное рассеивание тепла от слоя схемы в окружающую среду. Эти платы являются экономичными и подходят для простых конструкций, таких как светодиодное освещение и общие энергосистемы, где требуется управление теплом без высокой сложности схем.Двухсторонние алюминиевые печатные платы
Двухсторонние алюминиевые печатные платы имеют проводящие медные слои с обеих сторон алюминиевого ядра. Это позволяет создавать более сложные схемы по сравнению с односторонними платами, предоставляя возможность соединения между двумя сторонами через металлизированные отверстия или переходные отверстия. Они обычно используются в более сложных системах питания, автомобильной электронике и промышленных системах управления, где требуются больше вариантов компоновки и повышенная производительность без ущерба для отвода тепла.Многослойные алюминиевые печатные платы
Многослойные алюминиевые печатные платы имеют несколько слоев схем, уложенных друг на друга с изолирующим материалом между ними. Это позволяет создавать очень сложные конструкции схем, сохраняя при этом отличную тепловую производительность благодаря алюминиевому ядру в составе. Эти платы обычно используются в высокотехнологичных приложениях, таких как телекоммуникации и сложная автомобильная электроника, где важно экономить пространство и эффективно управлять теплом для нормальной работы системы.Гибридные алюминиевые печатные платы
Гибридные алюминиевые печатные платы сочетают преимущества алюминиевых подложек с диэлектрическими материалами или другими металлическими ядрами для достижения необходимых тепловых и электрических характеристик платы. Это позволяет комбинировать различные материалы, обеспечивая электрическую изоляцию вместе с отличной теплопроводностью. Гибридные платы особенно полезны в приложениях, требующих индивидуального баланса характеристик, таких как радиочастотные приложения, прецизионная силовая электроника и усовершенствованные системы освещения, где традиционные материалы для плат могут быть недостаточно хороши.
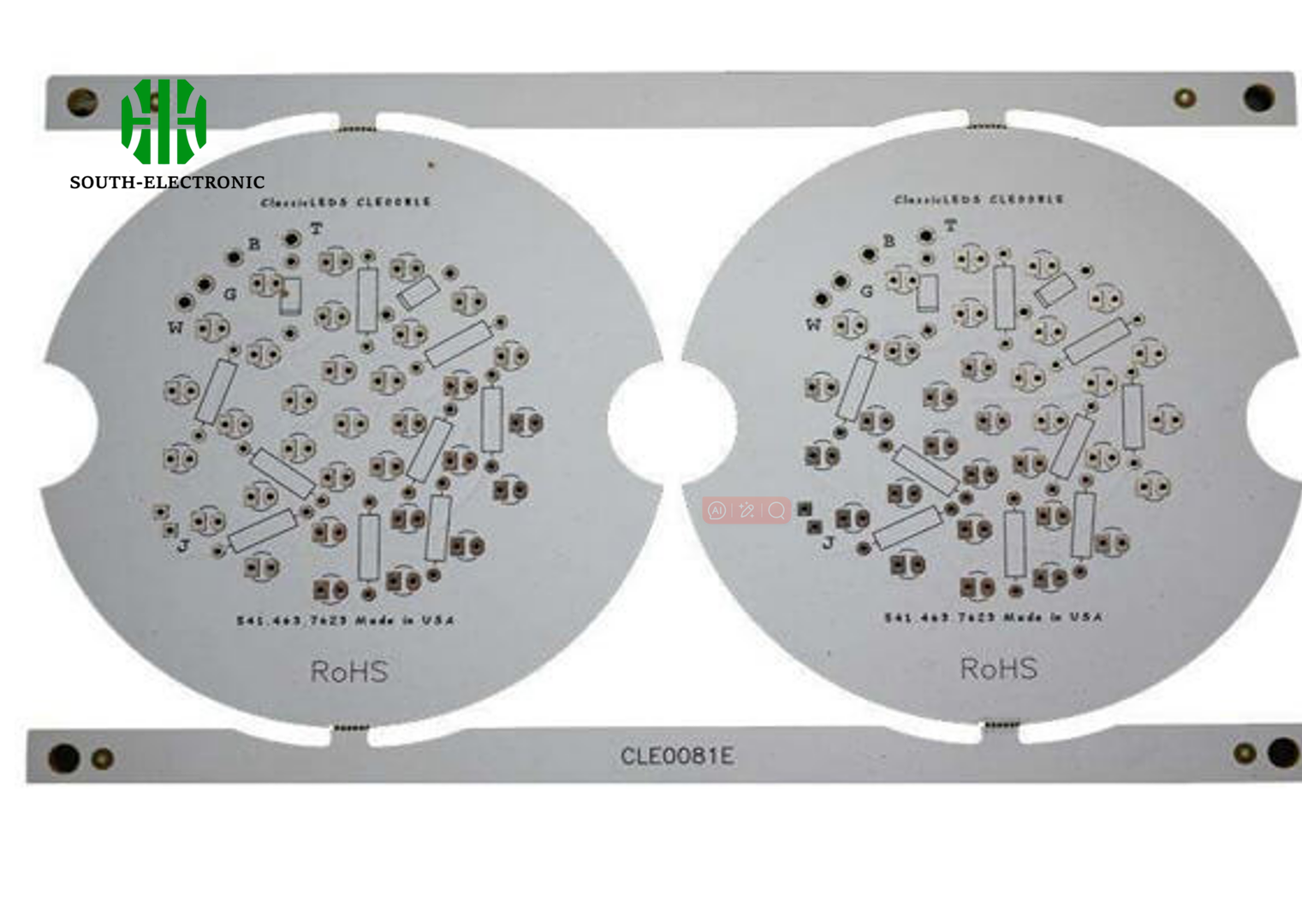
Глава 3
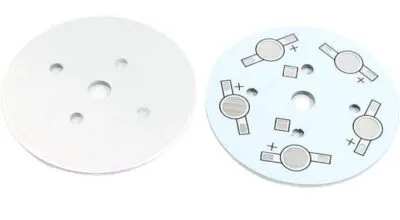
Материалы и конструкция алюминиевых печатных плат
Состав алюминиевых печатных плат
Алюминиевые печатные платы уникальны благодаря использованию металлического субстрата, обычно алюминия, который обладает отличной теплопроводностью и легкостью. Алюминиевые печатные платы состоят из трех основных компонентов:
- Алюминиевое основание: Основная часть платы, обеспечивающая структуру и способствующая отводу тепла. Это особенно важно для приложений с высокой тепловой нагрузкой.
- Диэлектрический слой: Материал, проводящий тепло, но электрически изолирующий. Он отделяет алюминиевое основание от слоя схемы. Помогает передавать тепло от схемы к алюминиевому основанию, сохраняя электрическую изоляцию.
- Слой схемы: Обычно представляет собой слой медной фольги, выгравированной для создания схемы. Толщина этого слоя зависит от электрических требований приложения.
Слоистая структура
Конструкция алюминиевых печатных плат обычно включает три основных слоя, каждый из которых выполняет свою задачу:
Базовый слой (алюминиевый субстрат):
- Обеспечивает основу платы.
- Предоставляет механическую жесткость и прочность.
- Действует как радиатор, отводящий тепло от компонентов схемы.
Диэлектрический слой:
- Теплопроводный материал, расположенный между слоем схемы и основанием.
- Основная функция – эффективно передавать тепло от слоя схемы к алюминиевому основанию.
- Также выполняет роль электрического изолятора, предотвращая прохождение электрического тока к алюминиевому слою.
Слой схемы:
- Состоит из медной фольги, выгравированной для создания необходимой схемы.
- Поддерживает передачу электрических сигналов по плате.
Эта слоистая структура оптимизирована для улучшения тепловой производительности при сохранении электрической целостности, что делает алюминиевые печатные платы подходящими для приложений, требующих надежного управления теплом.
Сравнение с другими печатными платами на металлической основе
Алюминиевые печатные платы входят в более широкую категорию печатных плат на металлической основе (MCPCBs), включающую другие варианты металлов, такие как медь и сталь. Вот некоторые сравнения:
- Теплопроводность: Алюминиевые платы обычно обеспечивают лучшую теплопроводность, чем платы на стальной основе, хотя платы на медной основе имеют еще более высокие показатели. Однако алюминий предлагает баланс между производительностью и стоимостью.
- Экономичность: Алюминий дешевле меди, что делает алюминиевые платы экономичным выбором для приложений, требующих хорошего управления теплом без высоких затрат, связанных с медью.
- Вес: Алюминий значительно легче других металлов, таких как медь и сталь, что делает алюминиевые платы предпочтительными для приложений, где важен вес, например, в аэрокосмической и портативной электронике.
- Производительность: Алюминиевые платы проще в обработке и более универсальны в дизайне по сравнению с медными и стальными аналогами. Эта простота производства часто сокращает сроки выполнения заказов и снижает производственные затраты.
Понимание материалов и конструкции алюминиевых печатных плат позволяет промышленности более точно выбирать тип платы, соответствующий их специфическим требованиям, обеспечивая эффективную работу и надежность.
Глава 4
Процесс производства алюминиевых печатных плат
Как изготавливают алюминиевые печатные платы?
Дизайн и проектирование:
Первый шаг в производстве алюминиевой печатной платы — это разработка схемы с использованием программного обеспечения для проектирования. В дизайн включаются все детали прокладки и маршрутизации цепей.Подготовка материала:
Затем алюминиевый субстрат подготавливается до требуемых размеров и уровня чистоты. Это основа платы, на которую будут наноситься остальные слои.Ламинирование:
На алюминиевый субстрат наносится диэлектрический слой. Этот слой теплопроводный, но электрически изолирующий, и на него накладывается проводящий медный слой.Создание медного рисунка:
Слой медной фольги ламинируется на диэлектрический слой. Затем медный слой обрабатывается с помощью фотогравировки или лазерного травления для создания дорожек схемы.Травление:
Незащищенные участки медного слоя удаляются с помощью химических растворов, оставляя окончательный рисунок схем.Сверление и металлизация:
В плате сверлятся отверстия для монтажа компонентов или крепления платы. В зависимости от дизайна эти отверстия могут быть металлизированы для создания электрических соединений между слоями.Нанесение паяльной маски:
На плату наносится паяльная маска для защиты схемы от окисления и предотвращения появления мостиков припоя при сборке компонентов. В местах пайки оставляются открытые участки.Финишная обработка:
Поверхности платы обрабатываются для улучшения паяемости и защиты открытых медных участков. Наиболее распространенные покрытия — HASL (горячее олово) и ENIG (химический никель-золото).Тестирование и контроль качества:
Готовые печатные платы тестируются для проверки их работоспособности и соответствия стандартам качества перед отправкой заказчику или переходом к сборке.
Ключевые технологии и используемые машины
- Станки с ЧПУ:
Используются для точного сверления и фрезеровки, обеспечивая точность отверстий и вырезов. - Оборудование для фотогравировки:
Применяется на этапе создания медного рисунка для переноса схемы на медный слой с использованием УФ-света или лазеров. - Травильные машины:
Автоматизированные травильные установки для удаления ненужной меди и уточнения дорожек схем. - Прессы для ламинирования:
Используются для создания многослойных конструкций или прессования диэлектрических и медных слоев на алюминиевый субстрат. - Системы нанесения паяльной маски:
Машины или ручные процессы для нанесения защитной паяльной маски на схему.
Сложности и особенности производства
Тепловое управление:
Важно эффективно управлять теплом, не нарушая целостность схемы, что требует тщательного выбора материалов и контроля процессов.Точность и аккуратность:
Выровнять слои, точно выполнить травление и сверление — критические моменты, чтобы избежать коротких замыканий и проблем с соединением. Для этого требуются высокоточные машины и строгий контроль качества.Свойства материала:
Работа с алюминием требует специального обращения и инструментов, чтобы предотвратить деформацию металла и сохранить стабильность размеров.Управление затратами:
Важно сбалансировать стоимость материалов и производственные расходы, сохраняя при этом качество, для достижения экономически эффективного производства.
Понимание этих этапов, технологий и сложностей позволяет производителям оптимизировать процессы и выпускать высококачественные алюминиевые печатные платы для сложных приложений.
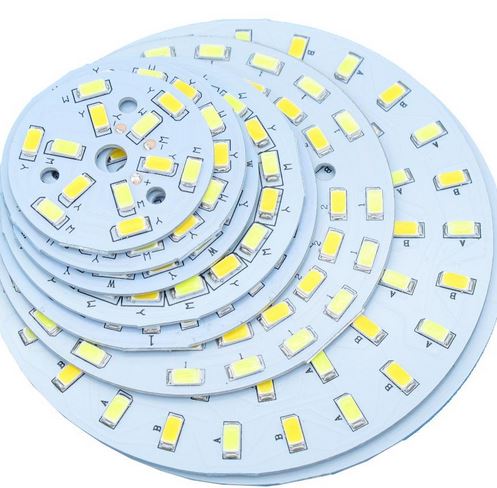
Глава 5

Проектирование алюминиевых печатных плат
Руководства по проектированию и лучшие практики
Выбор подходящих материалов:
Выберите диэлектрический материал, который лучше всего подходит для вашего проекта, основываясь на его теплопроводности и электрической изоляции. Это ключ к эффективной передаче тепла и надежной работе схемы.Определение количества слоев:
Решите, нужна ли вам однослойная, двусторонняя или многослойная плата, в зависимости от сложности и функциональности вашей схемы. Убедитесь, что структура слоев поддерживает эффективное управление теплом.Оптимизация ширины и расстояния дорожек:
Убедитесь, что ширина и расстояние дорожек оптимизированы для обработки токовых нагрузок без значительного нагрева. Следуйте стандартам IPC для обеспечения надежности и производительности платы.Размещение компонентов:
Размещайте компоненты так, чтобы минимизировать термические градиенты и обеспечить равномерное распределение тепла. Убедитесь, что компоненты, генерирующие тепло, имеют прямой тепловой путь к алюминиевому субстрату.Использование тепловых переходных отверстий:
Используйте тепловые переходные отверстия для вертикальной передачи тепла, особенно в многослойных платах. Это важно для отвода тепла от источника к алюминиевой основе.Учёт паяльной маски и шелкографии:
Применяйте паяльную маску для предотвращения перемычек припоя и защиты схемы. Убедитесь, что слой шелкографии для обозначения компонентов не перекрывает открытые металлические области, необходимые для отвода тепла.Проектирование с учётом производственных возможностей (DFM):
Тесно сотрудничайте с производителем, чтобы ваш проект соответствовал его возможностям. Это поможет минимизировать риск ошибок и обеспечить эффективное производство платы.
Управление теплом и отвод тепла
Эффективные тепловые пути:
Проектируйте пути, которые позволяют прямую передачу тепла от компонентов к алюминиевому субстрату. Минимизируйте препятствия на тепловых потоках.Тепловое моделирование:
Используйте программное обеспечение для теплового моделирования, чтобы предсказать и оптимизировать отвод тепла. Идентификация горячих точек помогает в планировании эффективного управления теплом.Теплоотводы компонентов:
Включите встроенные теплоотводы, где это возможно, или рассмотрите возможность добавления внешних теплоотводов для основных источников тепла.Экологические испытания:
Проверьте тепловую производительность платы в реальных условиях эксплуатации с помощью строгих испытаний. Это гарантирует, что плата будет работать надёжно в заданных тепловых пределах.Вентиляция и конвекция:
Учитывайте общую вентиляцию системы при проектировании плат. Правильный воздушный поток и размещение внутри корпуса могут значительно улучшить тепловую производительность.
Проектирование алюминиевых печатных плат требует глубокого понимания свойств материалов, электрической производительности и управления теплом. Следуя лучшим практикам и используя современные инструменты проектирования, инженеры могут создавать эффективные и надёжные печатные платы для сложных приложений.
Глава 6
Стандарты качества и сертификации
Почему важны сертификации ROHS, UL и ISO?
- ROHS (Ограничение опасных веществ)
- Почему это важно: Соответствие стандарту ROHS гарантирует, что алюминиевые печатные платы не содержат опасных материалов, таких как свинец, ртуть, кадмий и некоторые бромированные огнестойкие добавки. Это важно для здоровья и безопасности потребителей и окружающей среды, особенно в потребительской электронике.
- Что это значит: Соответствие стандартам ROHS помогает снизить воздействие на окружающую среду и укрепить доверие потребителей, подтверждая экологичность продукции.
- UL (Underwriters Laboratories)
- Почему это важно: Сертификация UL подтверждает, что алюминиевые печатные платы соответствуют определённым стандартам безопасности, с акцентом на пожаробезопасность и надёжность продукта.
- Что это значит: Сертификация UL добавляет продукту доверие и демонстрирует, что он прошёл строгие испытания на безопасность и производительность. Это даёт производителям и конечным пользователям уверенность в безопасности электронных компонентов.
- ISO (Международная организация по стандартизации)
- Почему это важно: В частности, стандарты ISO 9001 и ISO 14001 относятся к системам управления качеством и экологическим системам управления. Эти сертификации гарантируют, что производители печатных плат соблюдают систематические практики обеспечения качества и экологической ответственности.
- Что это значит: Сертификации ISO способствуют непрерывному улучшению процессов, повышают эффективность и дают клиентам уверенность в стабильном качестве продукции и приверженности компании устойчивому развитию.
Как сертификации влияют на производительность и надёжность?
- Продукты лучшего качества: Соответствие стандартам означает использование качественных материалов и процессов, что снижает количество дефектов и улучшает работу алюминиевых печатных плат.
- Более широкое признание на рынке: Сертифицированные продукты с большей вероятностью принимаются на международных рынках благодаря соответствию глобальным стандартам безопасности и качества.
- Более безопасные и надёжные: Сертифицированные продукты проходят множество испытаний, что делает их более безопасными и надёжными. Вы можете быть уверены, что они будут работать стабильно.
- Долговечность: Стандарты и сертификации продлевают срок службы алюминиевых печатных плат благодаря использованию качественных материалов и тестированию в различных условиях.
Лучший контроль качества
- Проверка материалов: Убедитесь, что все поступающие материалы соответствуют заявленным спецификациям. Это включает проверку на соответствие стандарту ROHS и другим важным требованиям.
- Контроль процесса: Внимательно следите за производственным процессом, чтобы обеспечить стабильность и качество. Используйте машины для стандартизации и повторяемости процессов.
- Испытания и повторные испытания: Тестируйте всё, чтобы убедиться, что оно работает правильно и продолжает работать. Проверяйте электрические и тепловые параметры.
- Исправление проблем: Используйте методы, такие как Six Sigma, чтобы находить и устранять проблемы.
- Документирование: Записывайте всё, что вы делаете, чтобы иметь возможность анализировать и улучшать процессы в будущем.
Следование стандартам и получение необходимых сертификаций позволяет производить алюминиевые печатные платы, которые работают эффективно, безопасны и долговечны. Это удовлетворяет как регуляторов, так и клиентов.
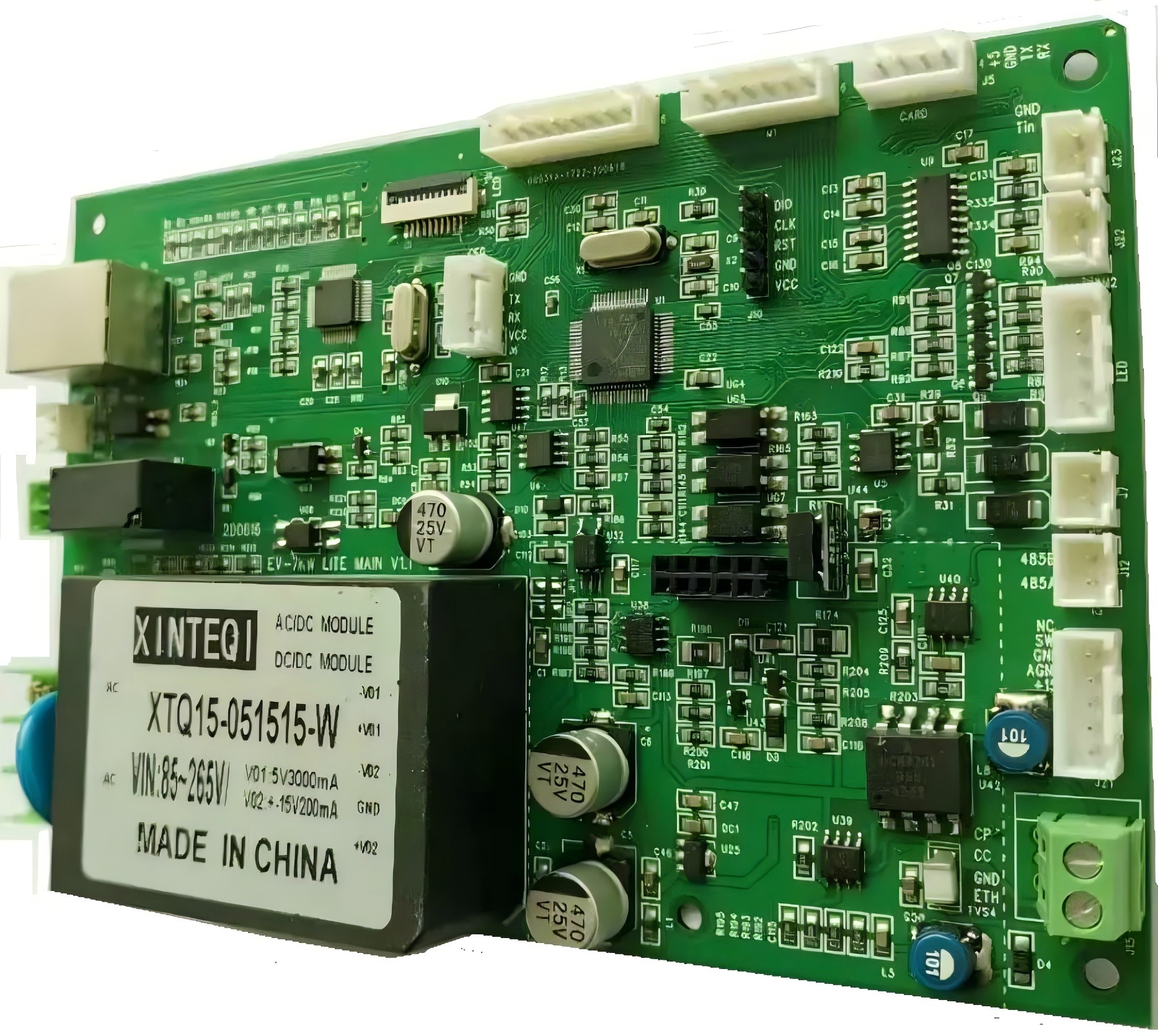
Глава 7
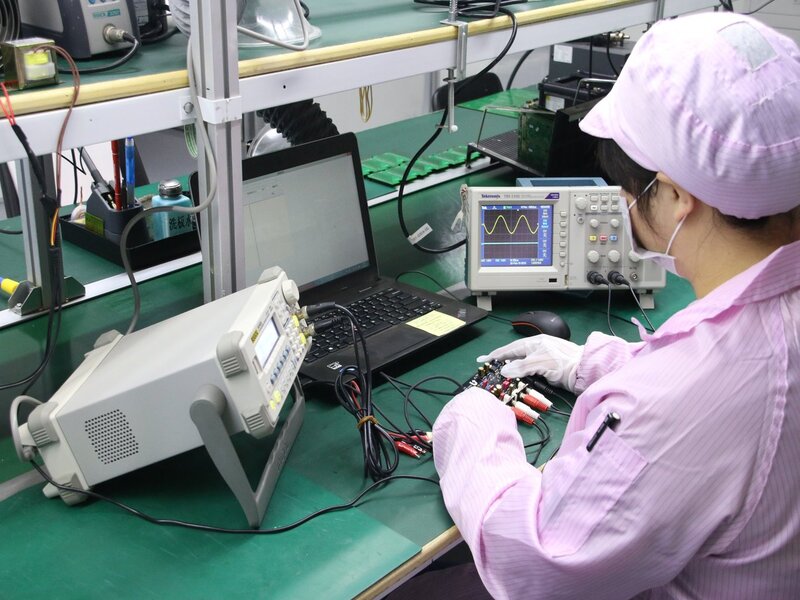
Экологическое воздействие и устойчивость
Экологически чистые методы производства
Использование экологически чистых материалов:
Убедитесь, что используемые материалы безопасны для окружающей среды и поставляются от ответственных производителей. Используйте материалы, не содержащие опасных веществ.Управление и сокращение отходов:
Найдите способы уменьшить количество отходов во время производства. Перерабатывайте материалы, чтобы минимизировать количество выбрасываемого мусора.Сохранение воды и энергии:
Используйте оборудование и процессы, которые требуют меньше воды и энергии. Это уменьшит воздействие на окружающую среду.Контроль выбросов:
Используйте машины, которые минимизируют выбросы в атмосферу, и соблюдайте экологические нормы для предотвращения загрязнения.
Жизненный цикл и возможность переработки алюминиевых печатных плат
Прочность и долговечность:
Производите продукты, которые служат дольше, чтобы уменьшить количество отходов и снизить потребность в частых заменах.Возможность переработки:
Используйте материалы, которые можно перерабатывать после окончания срока службы. Это снижает необходимость производства новых материалов.Управление в конце срока службы:
Поощряйте переработку отслуживших изделий и помогайте клиентам правильно утилизировать отходы.
Инициативы по сокращению углеродного следа
Устойчивая цепочка поставок:
Сотрудничайте с поставщиками, которые придерживаются экологически чистых методов работы. Это снижает воздействие на окружающую среду на всех этапах производства.Интеграция возобновляемых источников энергии:
Используйте солнечную или ветровую энергию в производственных процессах. Это уменьшает зависимость от загрязняющих источников энергии.Оптимизация транспорта:
Разработайте более эффективные способы доставки продукции, чтобы сократить расход топлива и выбросы углерода.Инновационные стратегии проектирования:
Разрабатывайте изделия, которые требуют меньше материалов и энергии для производства. Это снижает экологический след на стадии разработки.Вовлечение заинтересованных сторон:
Сотрудничайте с другими компаниями, организациями и сообществами, чтобы разрабатывать экологически чистую продукцию и процессы.
Глава 8
Факторы и соображения стоимости
Сравнение стоимости с другими типами печатных плат
Стоимость материалов:
Алюминиевые печатные платы обычно имеют более высокую стоимость материалов по сравнению с традиционными платами FR-4 из-за использования металлических подложек и специализированных диэлектрических материалов, улучшающих управление теплом.Сложность производства:
Процесс производства алюминиевых печатных плат может быть более сложным и включать дополнительные этапы, такие как создание точных тепловых характеристик, что увеличивает производственные затраты по сравнению со стандартными жёсткими или гибкими платами.Преимущества управления теплом:
Несмотря на более высокие начальные затраты, алюминиевые платы обеспечивают превосходные тепловые характеристики, уменьшая необходимость во внешних механизмах охлаждения, что потенциально снижает общую стоимость системы.
Факторы, влияющие на ценообразование
Объём:
Чем больше объём производства, тем ниже стоимость за единицу благодаря экономии на масштабе. Массовые заказы распределяют фиксированные затраты на большее количество единиц, снижая индивидуальную стоимость.Сложность дизайна:
Сложность дизайна платы, включая количество слоёв, наличие переходных отверстий и сложность разводки, напрямую влияет на цену. Более сложные проекты требуют больше времени и ресурсов.Выбор материалов:
Выбор диэлектрических материалов и типа алюминия влияет на стоимость. Материалы с высокой производительностью, предназначенные для конкретных приложений или улучшенных характеристик (например, высокая теплопроводность), стоят дороже.Индивидуальные решения и специальные функции:
Индивидуальные проекты с уникальными функциями или специальной формой требуют специализированных технологий производства, что увеличивает общую стоимость. Дополнительные тепловые переходы или сложные компоненты также повышают цену.
Советы по снижению затрат на производство
Оптимизация дизайна для производства (DFM):
Упрощайте дизайн, где это возможно, чтобы избежать ненужной сложности. Сотрудничайте с производителями на ранних стадиях разработки для согласования стратегий экономии.Рациональное использование материалов:
Выбирайте материалы, которые обеспечивают лучший баланс между производительностью и стоимостью. Оцените тепловые и электрические требования приложения, чтобы избежать избыточных спецификаций.Производство партиями:
Объединяйте заказы или комбинируйте схожие проекты в одной производственной серии для получения экономии от крупномасштабного производства.Отношения с поставщиками:
Устанавливайте прочные отношения с поставщиками для получения лучших цен, использования их опыта в сокращении затрат и обеспечения стабильности цепочки поставок.Итеративное прототипирование:
Используйте итеративные прототипы и тестирование для доработки дизайна. Выявление и устранение потенциальных проблем на этапе прототипирования предотвращает дорогостоящие исправления и задержки в массовом производстве.Оптимизация процессов:
Инвестируйте в эффективные производственные процессы и автоматизацию, чтобы снизить затраты на рабочую силу и увеличить производительность. Это не только снижает затраты, но и гарантирует стабильное качество.
Понимание и управление затратами на производство алюминиевых печатных плат позволяет производителям эффективно контролировать расходы, одновременно предоставляя эффективные и качественные продукты, соответствующие потребностям клиентов.
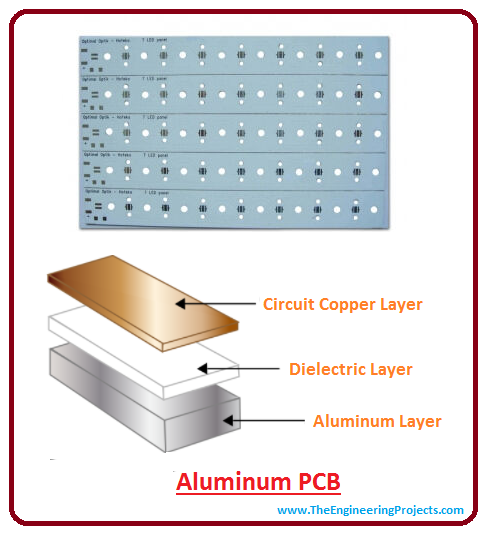
Глава 9
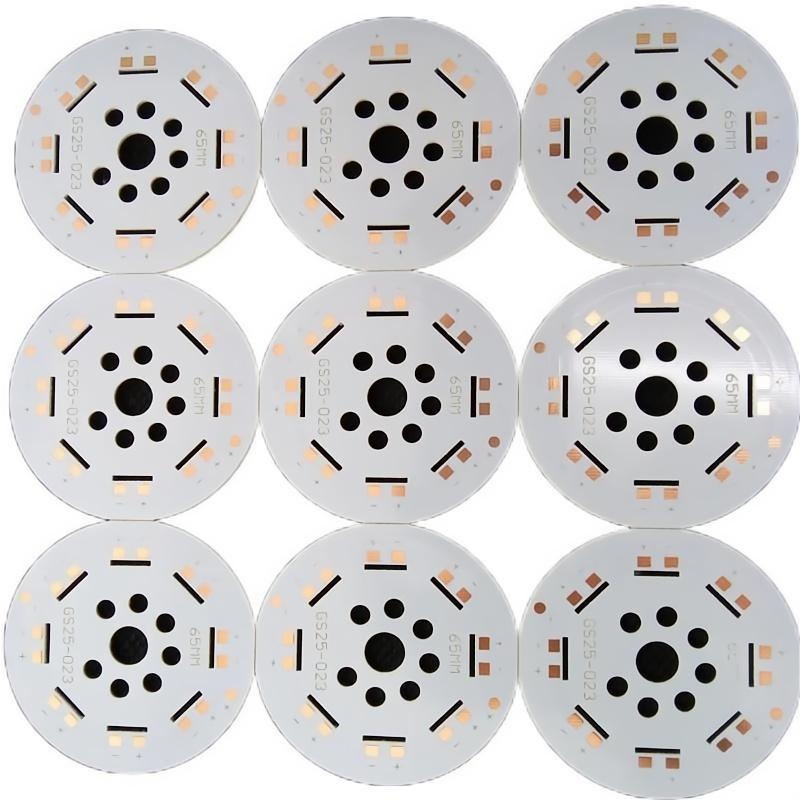
Рыночные тенденции и инновации
Последние достижения в технологии алюминиевых печатных плат
Улучшенные материалы для теплового управления:
Разработаны новые материалы с улучшенной теплопроводностью и электрической изоляцией, что позволяет лучше отводить тепло и повышать производительность в приложениях с высокой мощностью.Интеграция с современными компонентами:
Теперь компоненты могут быть встроены непосредственно в алюминиевые печатные платы, что позволяет создавать более тонкие конструкции и эффективные тепловые пути. Это всё чаще используется в автомобильной промышленности и высокопроизводительных вычислениях.Гибкие алюминиевые печатные платы:
Созданы гибкие алюминиевые платы, которые объединяют преимущества теплового управления алюминиевых подложек с гибкостью гибких схем. Это обусловлено растущим спросом на носимую электронику и компактные устройства.Автоматизация производственных процессов:
Прогресс в автоматизации, такой как точная лазерная резка и автоматическая оптическая инспекция (AOI), увеличил эффективность производства и снизил уровень дефектов в изготовлении алюминиевых печатных плат.
Тенденции, стимулирующие рост алюминиевых печатных плат
Спрос на эффективные тепловые решения:
По мере того как электроника становится мощнее и компактнее, необходимость в эффективных тепловых решениях стимулирует рост алюминиевых плат, особенно в освещении LED, автомобилестроении и возобновляемой энергетике.Рост электромобилей (EV):
Переход на электромобили, требующие эффективной силовой электроники и систем управления батареями, значительно увеличил спрос на алюминиевые платы благодаря их превосходным тепловым свойствам.Расширение рынка потребительской электроники:
По мере того как потребительская электроника становится мощнее и компактнее, алюминиевые платы всё чаще используются благодаря их способности справляться с высокими тепловыми нагрузками и обеспечивать надёжность.Экологичность и устойчивость:
С увеличением внимания к экологической устойчивости перерабатываемость и природная доступность алюминия делают алюминиевые платы привлекательным выбором для производителей, стремящихся внедрять экологичные практики.
Будущие перспективы и новые возможности
Рост 5G и IoT приложений:
Распространение технологий 5G и устройств IoT открывает значительные возможности для алюминиевых плат благодаря их способности управлять высокими частотами и тепловыми нагрузками.Прогресс в области возобновляемой энергии:
Рост возобновляемой энергетики увеличивает спрос на надёжные и эффективные системы управления энергией, использующие алюминиевые платы в солнечных панелях и ветряных турбинах.Миниатюризация и высокопроизводительные вычисления:
Стремление к миниатюризации и развитие высокопроизводительных вычислений открывают новые горизонты для алюминиевых плат, которые идеально подходят для компактного и эффективного теплового управления.Коллаборативные инновации:
Сотрудничество и партнёрства в отрасли, вероятно, будут стимулировать новые инновации и применения для алюминиевых плат, опираясь на совместный опыт и технологические достижения.
Рынок алюминиевых печатных плат продолжит расти по мере развития технологий, что обусловлено необходимостью повышения производительности и устойчивости в различных приложениях.
Глава 10
Как выбрать надёжного поставщика алюминиевых печатных плат
Стандарты качества и сертификации
Убедитесь, что поставщик соответствует отраслевым стандартам качества, таким как ISO 9001, ISO 14001, UL и ROHS. Эти сертификации подтверждают, что поставщик соблюдает строгие стандарты управления качеством и охраны окружающей среды, обеспечивая продукцию высокого качества.
Техническая экспертиза и возможности
Оцените технические знания и производственные возможности поставщика, включая его способность работать с сложными дизайнами, многослойными платами и индивидуальными спецификациями. Поставщик с современными технологическими возможностями сможет удовлетворить разнообразные и сложные требования проектов.
Опыт и послужной список
Обратите внимание на опыт поставщика в отрасли. Хорошо зарекомендовавший себя поставщик с подтверждённым опытом поставки алюминиевых плат для различных отраслей повышает надёжность и доверие к его продукции и услугам.
Индивидуальные решения и гибкость
Выберите поставщика, который предлагает варианты индивидуальной настройки и демонстрирует гибкость в производственных процессах. Способность адаптироваться к уникальным дизайнам и различным объёмам производства имеет ключевое значение для поддержки специфических нужд проекта.
Меры обеспечения качества
Изучите меры обеспечения качества у поставщика, включая процедуры инспекции и тестирования. Поставщики, использующие передовые методы тестирования, такие как автоматическая оптическая инспекция (AOI) и рентгеновское тестирование, обеспечивают качество и надёжность продукции.
Управление цепочкой поставок и надёжность
Оцените практики управления цепочкой поставок поставщика. Надёжный поставщик должен гарантировать постоянную доступность сырья, своевременную доставку и минимальные сбои в производственных графиках.
Поддержка и обслуживание клиентов
Отличная поддержка клиентов включает чёткую коммуникацию, оперативные ответы на запросы и готовность решать возникающие проблемы. Поставщик, который уделяет приоритетное внимание удовлетворению клиентов, может стать ценным партнёром в достижении успеха.
Конкурентоспособность цен
Хотя цена не должна быть единственным фактором, важно найти поставщика, который предлагает конкурентные цены без ущерба для качества. Прозрачное ценообразование и чёткое понимание факторов стоимости помогут в бюджетировании и финансовом планировании.
Экологические практики
С учётом растущего внимания к устойчивому развитию, выбирайте поставщиков, которые уделяют приоритетное внимание экологической ответственности. Это включает сокращение отходов, оптимизацию энергопотребления и использование перерабатываемых материалов.
Рекомендации и отзывы
Ищите рекомендации и отзывы от предыдущих клиентов, чтобы получить представление о надёжности и производительности поставщика. Положительные отзывы от авторитетных источников часто являются хорошим индикатором репутации поставщика в отрасли.
Выбор подходящего поставщика алюминиевых печатных плат требует внимательного анализа множества факторов, которые обеспечат высокое качество производства, надёжность и продуктивное сотрудничество для достижения целей вашего проекта.
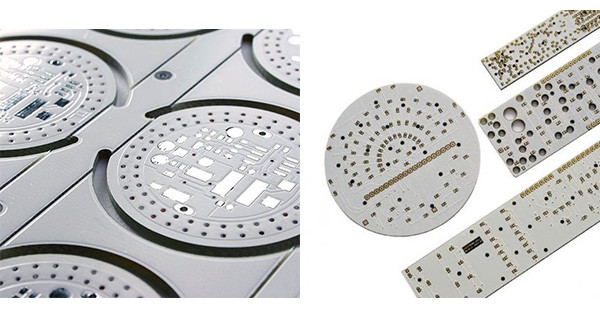
Связаться с Нами
Где Мы Находимся?
Промышленный Парк, № 438 Донхуан Роад, № 438, Шадзин Донхуан Роад, Район Баоань, Шэньчжэнь, Гуандун, Китай
4-й Этаж, Креативное Здание Жихуй, №2005 Сихуан Роад, Шадзин, Район Баоань, Шэньчжэнь, Китай
Комната A1-13, 3-й Этаж, Промышленный Центр Йи Лим, 2-28 Улица Kвай Лок, Квай Чунг, Гонконг
service@southelectronicpcb.com
Телефон: +86 400 878 3488
Отправьте нам сообщение
Чем подробнее вы заполните, тем быстрее мы сможем перейти к следующему шагу.
