Услуга По Разработке Печатных Плат
South-Electronic
В South-Electronic мы специализируемся на предоставлении услуг по разработке печатных плат высокого качества, обеспечивая надежность, долговечность и улучшение производительности вашей продукции. Наши индивидуальные проекты адаптированы под ваши уникальные потребности, тщательно разработаны для оптимизации производительности и надежности. Благодаря восьми современным производственным линиям мы гарантируем быструю обработку и своевременную доставку, независимо от объема заказа.
Почему выбирают South-Electronic?
В South-Electronic мы придерживаемся строгих процессов контроля качества, гарантируя, что каждая печатная плата соответствует самым высоким отраслевым стандартам, помогая вам снизить расходы на обслуживание и повысить удовлетворенность клиентов. От разработки и прототипирования до массового производства South-Electronic предлагает комплексные решения, упрощая вашу цепочку поставок и снижая затраты.
-
Индивидуальный Дизайн
Индивидуальный Дизайн для Удовлетворения Ваших Уникальных Потребностей.
В South-Electronic мы понимаем, что каждый проект уникален. Именно поэтому наши услуги по разработке печатных плат настраиваются в соответствии с вашими конкретными требованиями, гарантируя, что каждая деталь будет выполнена в точном соответствии с вашими спецификациями. Это улучшит производительность и надежность вашей продукции. -
Гарантированное Удовлетворение
Вы оцените уверенность, которую дает работа с сертифицированной по ISO9001 компанией.
Мы уделяем приоритетное внимание четкому и прозрачному общению и придерживаемся самых высоких стандартов, гарантируя, что ваши 8-слойные печатные платы не только соответствуют, но и превосходят ваши ожидания по производительности, долговечности и точности. -
Услуга "Под Ключ"
Выбирая нас, вы получаете полное решение для печатных плат, от проектирования и прототипирования до массового производства.
Мы предлагаем услугу "под ключ", устраняя сложности и затраты, связанные с работой с несколькими поставщиками. -
Комплексное Обслуживание
Вы получите полное удовлетворение благодаря нашему широкому ассортименту оборудования.
У нас есть широкий спектр возможностей для обработки печатных плат. От разработки до доставки мы обладаем всем необходимым оборудованием и процессами, чтобы гарантировать качественное выполнение вашего заказа. -
Быстрая Доставка
Оставайтесь в графике благодаря нашим быстрым срокам выполнения заказов.
Оптимизированное производство обеспечивает быструю обработку, чтобы вы получали свою продукцию вовремя, без задержек.
Связанные Проекты, Которые Мы Выполнили
Отзывы Клиентов
Часто Задаваемые Вопросы
Самые Популярные Вопросы
В South-Electronic вы получите непрерывную техническую поддержку от наших опытных инженеров и технических специалистов. Они готовы консультировать и решать любые возникающие вопросы в процессе проектирования и производства. Мы поддерживаем связь через регулярные обновления и прямой доступ, чтобы вы были уверены, что ваш проект идет по плану.
Да, South-Electronic прекрасно справляется с разработкой индивидуальных проектов, соответствующих уникальным спецификациям вашего проекта. Мы работаем с вами в тесном сотрудничестве, чтобы настроить каждый аспект макета печатной платы, гарантируя, что он полностью соответствует вашим требованиям и улучшает производительность и надежность вашей продукции.
В South-Electronic мы обычно выполняем заказы в сжатые сроки благодаря нашим эффективным процессам и современным производственным линиям. Хотя сроки могут варьироваться в зависимости от сложности вашего проекта и объема заказа, мы стремимся соблюдать строгие графики и обеспечивать своевременную доставку.
Мы внедрили строгие процедуры контроля качества на всех этапах производственного процесса. South-Electronic придерживается лучших отраслевых стандартов, проводя тщательные тесты и проверки на каждом этапе, чтобы каждая печатная плата была максимально качественной и надежной.
В South-Electronic мы обладаем высокой производственной мощностью с восьмью современными производственными линиями, которые позволяют нам обрабатывать как небольшие, так и крупные заказы. Наши операции гибкие и могут быть масштабированы в зависимости от потребностей вашего проекта, поэтому мы можем справляться с большими объемами.
Наши производственные линии оснащены новейшими технологиями и передовым оборудованием, что обеспечивает точность и эффективность. Это включает в себя автоматизированные машины и современные инструменты, которые позволяют нам поддерживать высокое качество и сокращать сроки производства.
Отправьте нам сообщение
Чем подробнее вы заполните, тем быстрее мы сможем перейти к следующему шагу.
Полное Руководство по Разработке Печатных Плат
Содержание
Глава 1
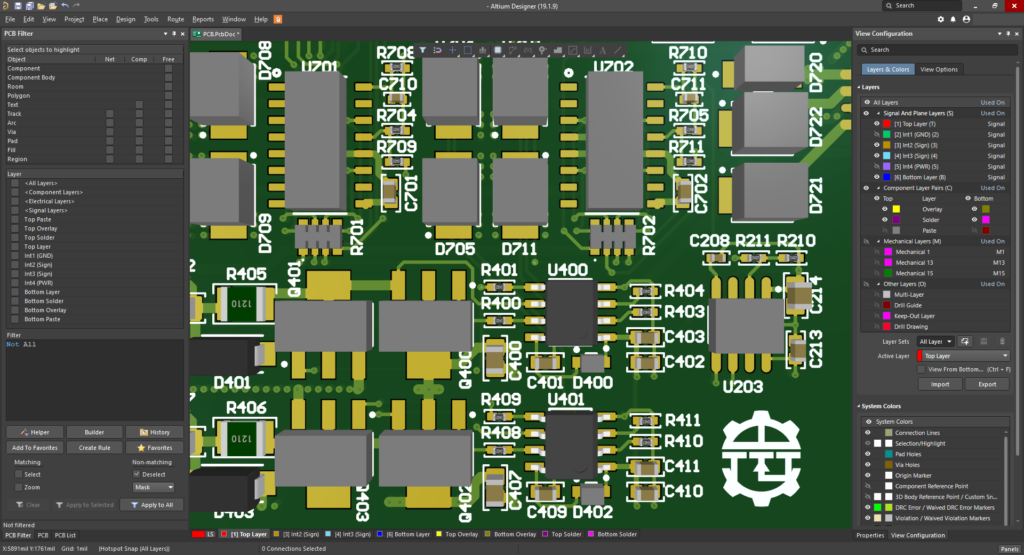
Введение в Разработку Печатных Плат
Разработка печатных плат играет важную роль в мире электроники. Это основа почти всех электронных устройств — от простых гаджетов до сложных механизмов. Если вы инженер или любитель, стремящийся создавать эффективные и надежные электронные системы, вам необходимо знать о разработке печатных плат.
Что Такое Разработка Печатных Плат?
Разработка печатных плат — это процесс проектирования физического расположения компонентов и электрических соединений на печатной плате. Это включает в себя логичное и эффективное размещение электронных компонентов и прокладку электрических соединений между ними.
Печатная плата обычно состоит из нескольких слоев, включая:
- Медные слои для токопроводящих дорожек,
- Подложку для изоляции,
- Слой паяльной маски для защиты.
Многослойность позволяет миниатюризировать схемы, что дает возможность размещать сложную электронику в небольших корпусах.
Ключевые аспекты разработки печатных плат:
- Размещение Компонентов: Определение местоположения компонентов для их оптимальной работы и компактного размещения.
- Прокладка Дорожек: Проектирование путей, по которым будут проходить электрические сигналы.
- Проверка Правил Проектирования (DRC): Проверка соответствия проектирования производственным возможностям и стандартам.
- Целостность Сигнала: Обеспечение высокого качества электрических сигналов при их прохождении через плату.
- Тепловое Управление: Эффективное управление выделяемым теплом, чтобы предотвратить повреждения компонентов.
Почему Разработка Печатных Плат Важна в Электронике
Разработка печатных плат важна по ряду причин:
- Надежность и Функциональность: Хорошо разработанная печатная плата обеспечивает стабильную работу электронных устройств, минимизируя возможные ошибки и повышая надежность.
- Компактность: Грамотная разработка позволяет размещать электронные компоненты на меньшей площади, создавая компактные устройства, такие как смартфоны и носимая электроника.
- Экономическая Эффективность: Оптимизация разработки печатных плат снижает затраты на производство за счет уменьшения использования материалов и увеличения количества плат в одной партии.
- Оптимизация Производительности: Продуманная разработка минимизирует задержки и помехи сигналов, что важно для высокоскоростных и высокочастотных приложений.
- Тепловое Управление: Хороший дизайн способствует эффективному рассеиванию тепла, размещая компоненты в правильных местах.
- Масштабируемость и Гибкость: Качественная разработка упрощает внесение изменений и масштабирование производства.
Итак, разработка печатных плат — это важнейший аспект создания электронных устройств. Она влияет на их производительность, стоимость и размеры. Чтобы создавать инновационные и надежные продукты, необходимо овладеть искусством разработки печатных плат.
Глава 2
Основы Проектирования Печатных Плат
Проектирование печатных плат является основой создания эффективных и надежных электронных систем. Освоив основы проектирования печатных плат, инженеры и дизайнеры могут создавать схемы, соответствующие заданным критериям производительности, размера и стоимости.
Компоненты Проектирования Печатных Плат
При проектировании печатной платы необходимо учитывать несколько ключевых компонентов и концепций для обеспечения эффективного макета:
Подложка:
Подложка — это базовый материал печатной платы, обеспечивающий механическую поддержку всей платы. Обычно она изготовлена из стекловолокна (FR4) и служит изолирующим слоем между платой и её компонентами.
Медные Слои:
На медных слоях травятся электрические цепи. Печатная плата может иметь несколько медных слоев для сложных схем, где дорожки формируют пути для электрических сигналов.
Паяльная Маска:
Это защитное покрытие, наносимое на медные слои для предотвращения коротких замыканий и защиты от воздействия окружающей среды. Она придает печатным платам характерный зеленый цвет, хотя доступны и другие цвета.
Шелкография:
Шелкографический слой добавляет текст и символы на печатную плату для обозначения компонентов, точек тестирования и других индикаторов. Это облегчает процессы сборки и отладки.
Дорожки и Площадки:
Дорожки — это проводящие пути, аналогичные проводам, которые соединяют различные компоненты на плате. Площадки предоставляют поверхности для пайки компонентов на плату.
Виас:
Виасы — это небольшие отверстия, обеспечивающие электрические соединения между слоями многослойной печатной платы. Они заполнены проводящим материалом для облегчения межслойной связи.
Компоненты:
Включают все электронные элементы, припаянные к печатной плате, такие как резисторы, конденсаторы, микросхемы и разъемы. Правильное размещение и ориентация этих компонентов имеют ключевое значение для работы схемы.
Правила и Ограничения Проектирования:
Это набор рекомендаций, которые обеспечивают возможность производства и правильное функционирование при заданных условиях эксплуатации. Они включают ограничения по расстояниям, размерам и электрическим параметрам.
Типы Печатных Плат
Печатные платы бывают различных типов, каждый из которых подходит для разных приложений и требований к дизайну. Вот некоторые из них:
Односторонние Печатные Платы:
Имеют один медный слой и являются самым простым типом печатных плат. Они экономичны и просты в производстве, идеально подходят для схем низкой плотности, таких как калькуляторы и блоки питания.
Двусторонние Печатные Платы:
С медными слоями с обеих сторон они позволяют создавать более сложные схемы, так как компоненты и маршруты могут размещаться с обеих сторон. Обычно используются в системах мониторинга энергии, промышленных контроллерах и автомобильной электронике.
Многослойные Печатные Платы:
Состоят из трех и более медных слоев, которые чередуются с изоляционными. Подходят для сложных технологий, таких как компьютеры и аэрокосмическое оборудование, благодаря способности размещать сложные схемы в ограниченном пространстве.
Жесткие Печатные Платы:
Имеют твердую подложку, которая не гнется. Используются в тех случаях, когда плата должна оставаться стабильной и сохранять форму, например, в настольных компьютерах и сетевом оборудовании.
Гибкие Печатные Платы:
Изготовлены из гибких пластиковых подложек, которые можно сгибать и помещать в компактные или неправильные формы. Часто применяются в носимой электронике, мобильных устройствах и гибкой электронике.
Жестко-Гибкие Печатные Платы:
Объединяют свойства жестких и гибких печатных плат, позволяя сгибаться отдельным секциям, в то время как основная плата остается жесткой. Идеальны для приложений, требующих как гибкости, так и долговечности.
Высокочастотные Печатные Платы:
Разработаны для управления сигналами в диапазоне гигагерц, применяются в спутниковых и коммуникационных системах, где важна целостность сигнала на высоких частотах.
Понимание этих компонентов и типов является жизненно важным для каждого, кто занимается проектированием печатных плат, так как это открывает путь к созданию эффективных, экономичных и высокопроизводительных электронных систем.
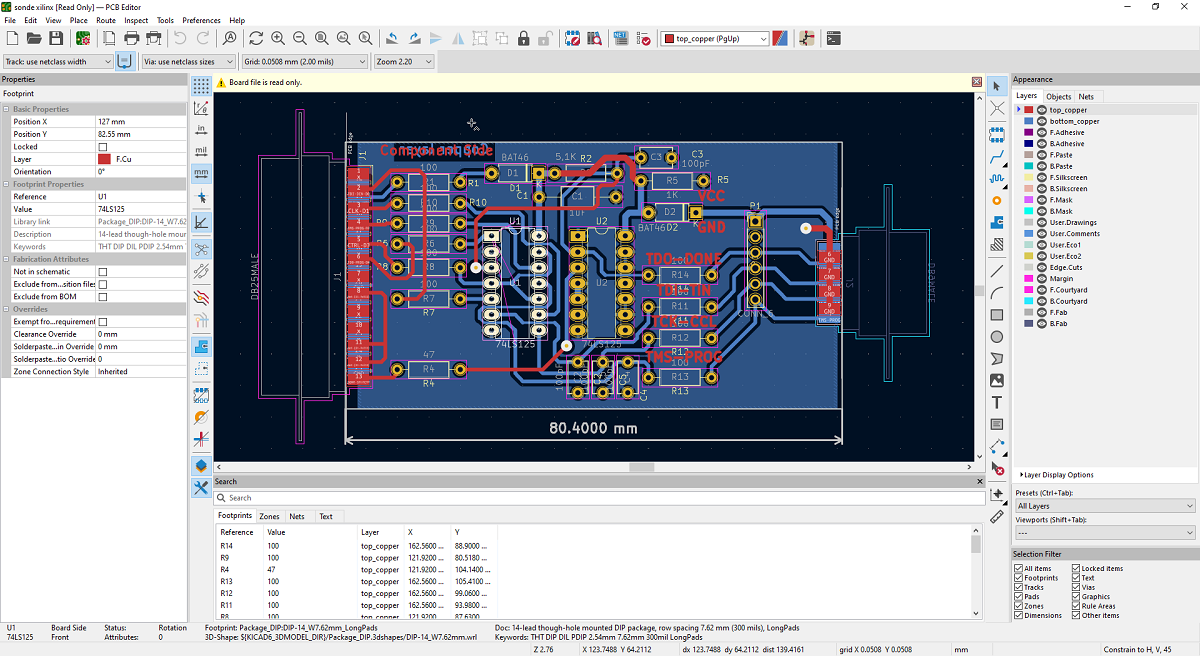
Глава 3

Основное Программное Обеспечение для Проектирования Печатных Плат
В процессе проектирования печатных плат наличие правильных программных инструментов крайне важно. Эти инструменты не только упрощают процесс разработки, но и позволяют проводить симуляцию и тестирование дизайна перед фактическим производством. Использование подходящего программного обеспечения может значительно повысить точность, эффективность и креативность ваших проектов.
Обзор Популярных Инструментов Для Проектирования Печатных Плат
Существует множество программ для проектирования печатных плат, каждая из которых подходит для различных требований и уровней подготовки. Вот обзор наиболее популярных программ:
Altium Designer:
Известен своим обширным набором функций, Altium Designer пользуется популярностью среди профессиональных инженеров для сложных и крупных проектов. Предоставляет мощные инструменты для управления библиотеками и продвинутые средства симуляции, что делает его идеальным для высокотехнологичных разработок.
Eagle (Простой Графический Редактор Макетов):
Один из самых популярных инструментов среди любителей и профессионалов, Eagle известен своим удобным интерфейсом и гибкостью. Обладает мощными функциями редактирования и широкой библиотекой компонентов. В настоящее время принадлежит Autodesk, что улучшает его интеграцию с другими инструментами для проектирования.
KiCad:
Бесплатное и открытое программное обеспечение для проектирования печатных плат, KiCad набирает популярность благодаря своим возможностям, сопоставимым с коммерческими программами. Поддерживает сложные проекты с множеством слоев и имеет активную поддержку сообщества для дополнительных библиотек и модулей.
OrCAD:
Подходит для широкого спектра проектов, от простых до сложных. Известен своими мощными возможностями симуляции, OrCAD востребован в учебных и промышленных средах, где требуется высокая точность электрических разработок.
Proteus:
Proteus прост в использовании и особенно популярен в обучении, образовательных целях и для проектов начального уровня. Позволяет визуально симулировать работу схем наряду с проектированием печатных плат, что помогает лучше понять поведение схемы до её реального внедрения.
DipTrace:
Подходит для создания как простых, так и сложных проектов, DipTrace предлагает интуитивно понятный интерфейс и упрощенный рабочий процесс. Поддерживает 3D-визуализацию, что помогает дизайнерам точнее представить конечный продукт.
DesignSpark PCB:
Предназначен как для начинающих, так и для опытных разработчиков. DesignSpark бесплатен и предлагает неограниченное количество площадок и узлов. Имеет обширную библиотеку и простой для освоения интерфейс, что делает его идеальным выбором для менее сложных проектов.
Глава 4
Лучшие Практики Разработки Печатных Плат
Если вы хотите создавать дизайны, которые работают эффективно, надежны и легко поддаются производству, вам необходимо знать лучшие практики проектирования печатных плат (PCB). Два ключевых аспекта проектирования, которые влияют на эти параметры, — это целостность сигнала и распределение питания.
Проектирование для Целостности Сигнала
Целостность сигнала связана с поддержанием чистоты электрических сигналов при их прохождении через печатную плату. Плохая целостность сигнала может привести к потере данных, шуму и неисправности схем. Вот несколько лучших практик для обеспечения хорошей целостности сигнала:
- Держите Дорожки Короткими: Короткие дорожки имеют меньшую сопротивляемость, индуктивность и меньше шансов для деградации сигналов. Держите высокоскоростные сигналы как можно короче.
- Контролируйте Импеданс: Проектируйте дорожки с контролируемым импедансом, особенно для высокочастотных схем, чтобы избежать отражений и потерь. Согласование импеданса обеспечивает эффективную передачу сигналов.
- Правильно Используйте Планы Земли: Сплошные планы земли обеспечивают сигналы точкой отсчета, снижают шум и улучшают работу всей системы. Они также помогают уменьшить электромагнитные помехи (EMI).
- Разделяйте Сигналы: Держите высокоскоростные сигналы подальше от низкоскоростных или высокотоковых сигналов, чтобы избежать их взаимного влияния. Используйте дорожки земли или медные зоны между разными типами сигналов.
- Избегайте Пересечения Виасов: Чрезмерное количество виасов может нарушить поток сигналов и увеличить индуктивность. Используйте меньше виасов для важных сигналов и старайтесь прокладывать дорожки прямо.
- Правильно Маршрутизируйте Дифференциальные Пары: Для сигналов, передающихся в виде дифференциальных пар, сохраняйте одинаковое расстояние и длину пар, чтобы сигналы оставались сбалансированными и чистыми.
- Правильно Завершайте Сигналы: Используйте правильные методы завершения (например, параллельные или последовательные резисторы) для согласования импеданса линии и предотвращения отражений.
- Следите за Возвратными Путями Сигналов: Убедитесь, что возвратные пути сигналов прямые и непрерывные. Размещайте виасы земли рядом с виасами сигналов для улучшения возвратных путей.
Рекомендации по Распределению Питания
Хороший дизайн распределения питания важен для обеспечения стабильного питания всех компонентов, снижения падений напряжения и уменьшения нагрева. Вот несколько рекомендаций:
- Используйте Широкие Дорожки Питания: Широкие дорожки или медные заливки могут пропускать больший ток с меньшим сопротивлением, что снижает падение напряжения и нагрев.
- Используйте Отдельный Питательный План: Отдельный план питания позволяет равномерно распределять напряжение и снижает его колебания. Это также обеспечивает низкоиндуктивный путь по всей схеме.
- Используйте Конденсаторы Развязки: Размещайте конденсаторы развязки рядом с выводами питания микросхем, чтобы фильтровать всплески напряжения и обеспечивать мгновенное питание во время быстрых изменений.
- Используйте Топологию «Звезда» для Ветвлений: Применяйте топологию «звезда» для ветвления линий питания из центральной точки, чтобы уменьшить площадь токовых петель и снизить шум на линиях питания и земли.
- Соединяйте Питание и Землю Виасами: Используйте виасы для соединения планов питания и земли, снижая индуктивность петель и обеспечивая надежные пути земли.
- Избегайте Колебаний Земли: Не допускайте, чтобы разные части платы с высоким током использовали общий путь земли. Это предотвратит динамические изменения напряжения, влияющие на землю.
- Учитывайте Тепло: Размещайте компоненты питания таким образом, чтобы эффективно отводить тепло. Используйте радиаторы или термовиасы для компонентов, выделяющих много тепла.
- Проверяйте Целостность Питания: Используйте инструменты симуляции для проверки целостности питания, чтобы убедиться, что напряжение нигде на плате не выходит за допустимые пределы.
Применяя эти лучшие практики в своих разработках печатных плат, вы сможете обеспечить хорошую целостность сигналов и эффективное распределение питания, что сделает ваши электронные устройства надежными и эффективными в различных условиях.
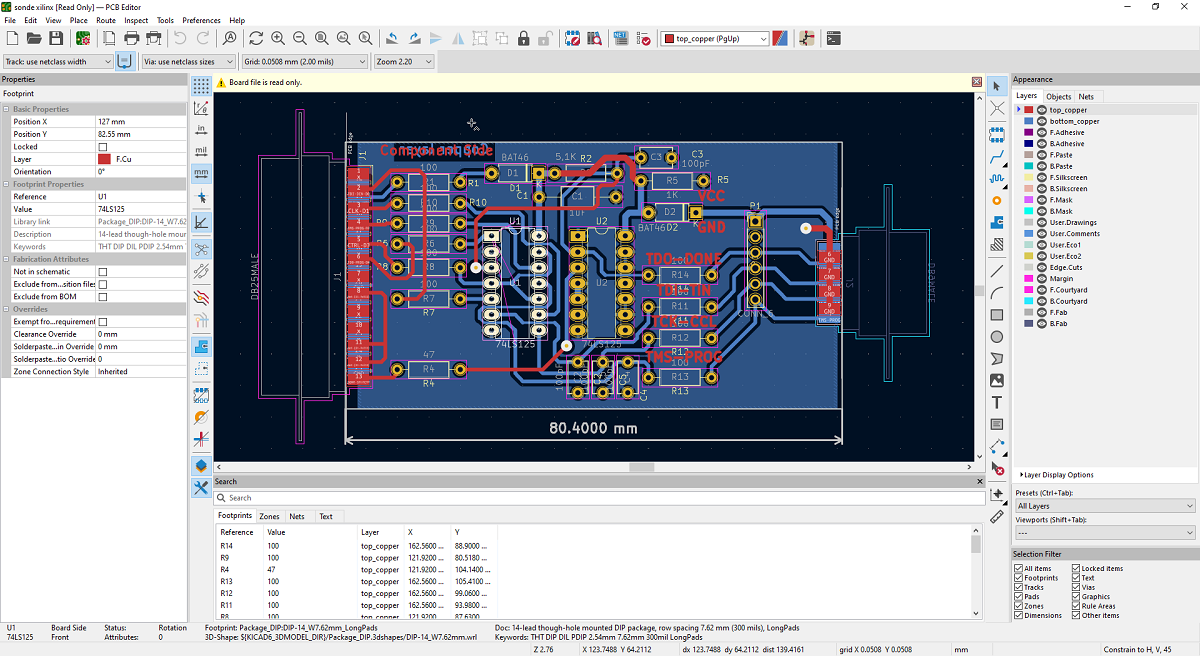
Глава 5
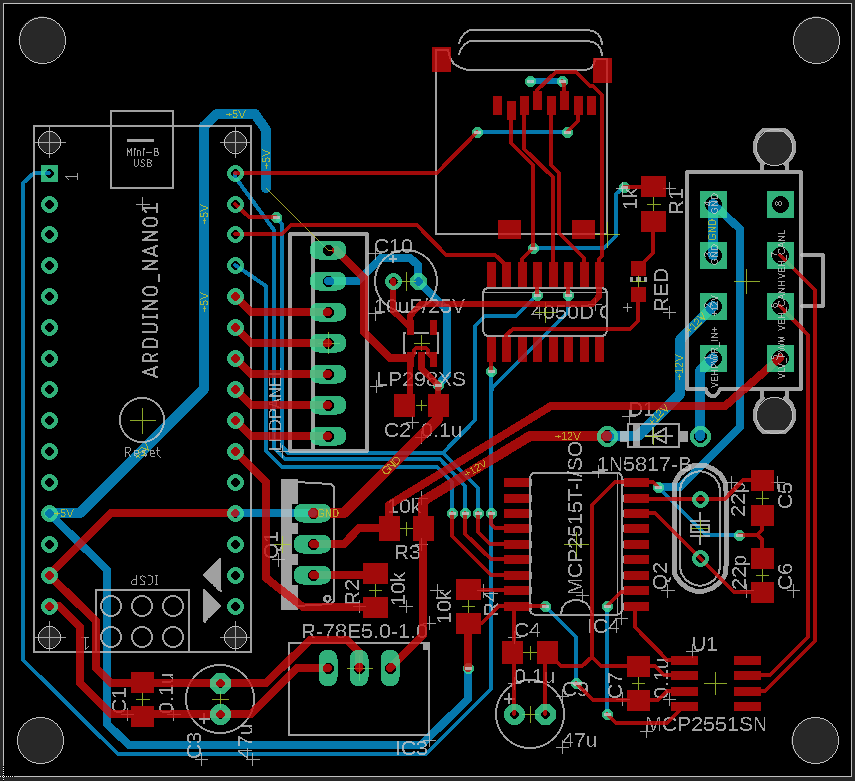
Стратегии Размещения Компонентов
Правильное размещение компонентов — это ключевой шаг в проектировании печатных плат, который напрямую влияет на электрическую производительность, управление теплом и удобство производства. Применение стратегического размещения компонентов улучшает общую функциональность и надежность схемы.
Важность Стратегического Размещения Компонентов
Целостность Сигнала:
Стратегическое размещение минимизирует длину путей сигналов, снижая потенциальные задержки, отражения и шум, что улучшает целостность и производительность сигнала.Тепловое Управление:
Эффективное размещение компонентов способствует рассеиванию тепла. Правильная компоновка предотвращает перегрев, обеспечивает работу компонентов в безопасных температурных диапазонах и продлевает срок службы платы.Упрощение Сборки:
Организованное размещение компонентов упрощает процесс сборки, снижает количество ошибок и уменьшает производственные затраты. Четкое разделение и логичное расположение позволяют автоматическим сборочным линиям работать эффективно.Снижение Электромагнитных Помех (EMI):
Тщательное размещение минимизирует перекрестные помехи и электромагнитные помехи, поддерживая оптимальные расстояния между компонентами и обеспечивая эффективные пути заземления.Обслуживание и Тестирование:
Проектирование с учетом обслуживания облегчает доступ к критически важным компонентам для тестирования и ремонта, что особенно важно для сложных или высоконадежных приложений.Оптимизация Пространства:
Стратегическое размещение максимально использует доступное пространство, позволяя уменьшить размеры электронных устройств без потери функциональности.
Советы по Эффективному Размещению Компонентов
Приоритет для Ключевых Компонентов:
Начните с размещения ключевых компонентов, таких как микроконтроллеры, процессоры или разъемы, так как они часто определяют компоновку остальных компонентов.Группируйте Связанные Компоненты:
Группируйте компоненты по функциям (например, аналоговые цепи, цифровая логика) для упрощения маршрутизации и сокращения расстояний сигналов. Эта стратегия также помогает эффективно распределять питание.Соблюдайте Единую Ориентацию:
Размещайте компоненты в единой ориентации для упрощения инспекции и сборки. Единая ориентация также снижает вероятность ошибок при пайке.Оптимизируйте Маршрутизацию Трасс Сигналов:
Расположите компоненты так, чтобы минимизировать длину трасс для высокоскоростных сигналов. Размещайте компоненты таким образом, чтобы избежать ненужных изгибов или виасов.Учитывайте Теплочувствительные Компоненты:
Держите теплочувствительные компоненты вдали от мощных устройств. Обеспечьте достаточно места или используйте радиаторы для улучшения рассеивания тепла.Следуйте Рекомендациям Производителя:
Соблюдайте рекомендации по проектированию из технической документации компонентов, особенно в отношении термоплощадок и развязывающих конденсаторов для интегральных схем.Оставьте Место для Итераций Дизайна:
Оставьте место для возможных изменений дизайна и добавления компонентов, чтобы внести корректировки без значительной перестройки.Соблюдайте Электрические Зазоры:
Обеспечьте достаточные электрические зазоры между контактами и дорожками в соответствии с правилами проектирования, чтобы предотвратить короткие замыкания и электрические дуги.Физические Ограничения:
Учитывайте окончательную механическую сборку, оставляя области для монтажных отверстий, краевых разъемов и других конструктивных требований.Ревизия и Симуляция:
Используйте программное обеспечение для симуляции влияния размещения компонентов. Это помогает выявить потенциальные проблемы до этапа производства.
Применяя эти стратегии, дизайнеры могут повысить эффективность своих макетов печатных плат, обеспечивая их надежность, производительность и удобство производства.
Глава 6
Техники Маршрутизации для Эффективного Проектирования Печатных Плат
Маршрутизация — это критически важный этап в проектировании печатных плат, на котором устанавливаются физические соединения между компонентами через сеть трасс. Эффективные техники маршрутизации необходимы для оптимизации производительности, снижения шума и обеспечения целостности сигналов.
Различные Методы Маршрутизации
Ручная Маршрутизация:
- Описание: При ручной маршрутизации дизайнер вручную прокладывает каждую трассу на печатной плате. Этот метод позволяет лучше контролировать пути сигналов, что особенно важно для высокоскоростных и чувствительных сигналов.
- Применение: Используется там, где требуется высокая точность, например, в радиочастотных (RF) схемах или на платах с высокой плотностью компонентов.
Автоматическая Маршрутизация (Автомат):
- Описание: Алгоритмы программного обеспечения автоматически определяют оптимальные пути для трасс. Автоматическая маршрутизация быстра и подходит для менее сложных схем.
- Применение: Идеально для простых схем или как предварительный этап для последующей ручной доработки.
Маршрутизация Дифференциальных Пар:
- Описание: Включает прокладку пары комплементарных сигналов с постоянным расстоянием и длиной для обеспечения целостности сигналов. Используется для минимизации шума и перекрестных помех.
- Применение: Критически важно для высокоскоростных интерфейсов, таких как HDMI, USB и Ethernet.
Согласование Длин:
- Описание: Обеспечивает равную длину трасс, по которым должны одновременно поступать сигналы. Это важно для избежания проблем синхронизации в высокочастотных схемах.
- Применение: Необходимо в системах шины памяти, таких как схемы DDR.
Маршрутизация с Контролируемым Импедансом:
- Описание: Обеспечивает определенные значения импеданса трасс за счет контроля их ширины, расстояния до других трасс и близости к планам земли.
- Применение: Используется в радиочастотных (RF) и высокочастотных линиях сигналов.
Via Stitching:
- Описание: Включает размещение нескольких виасов вдоль трассы для соединения планов земли или распределения тепловых нагрузок, что помогает снизить EMI и эффекты земляных петель.
- Применение: Часто используется в многослойных печатных платах с высокой электромагнитной интерференцией.
Как Избежать Ошибок в Маршрутизации
Избегайте Острых Углов:
- Ошибка: Использование острых углов (меньше 90 градусов) может привести к отражению сигналов и проблемам при производстве.
- Решение: Используйте углы 45 градусов для поворотов трасс, чтобы обеспечить плавный поток сигналов.
Минимизируйте Использование Виасов:
- Ошибка: Чрезмерное количество виасов увеличивает индуктивность и сопротивление, ухудшая целостность сигналов.
- Решение: Планируйте маршрутизацию так, чтобы минимизировать количество виасов, особенно в высокочастотных линиях.
Избегайте Параллельных Трасс:
- Ошибка: Параллельные трассы могут вызвать перекрестные помехи, особенно в высокоскоростных схемах.
- Решение: Увеличьте расстояние между параллельными трассами или используйте дифференциальные пары, если это возможно.
Плохое Заземление:
- Ошибка: Неправильное заземление приводит к увеличению шума и EMI.
- Решение: Используйте сплошные планы земли и обеспечьте адекватное количество виасов для заземления.
Игнорирование Теплового Управления:
- Ошибка: Невнимание к тепловым проблемам при маршрутизации может привести к перегреву.
- Решение: Используйте трассы достаточной ширины для токовых путей и применяйте термические развязки для виасов.
Несогласование Длин Трасс:
- Ошибка: Разная длина трасс приводит к несоответствиям времени в синхронизированных сигналах.
- Решение: Используйте змейку (serpentine routing) для согласования длин в критических парах сигналов.
Перегруженность Трасс:
- Ошибка: Слишком большое количество трасс в одной области затрудняет пайку и обслуживание.
- Решение: Планируйте макет так, чтобы трассы распределялись равномерно, и обеспечьте достаточные зазоры в соответствии с правилами проектирования.
Применяя эти техники маршрутизации, дизайнеры могут улучшить производительность и надежность своих печатных плат, снизив риск проблем на этапе производства и обеспечив оптимальную работу схемы.
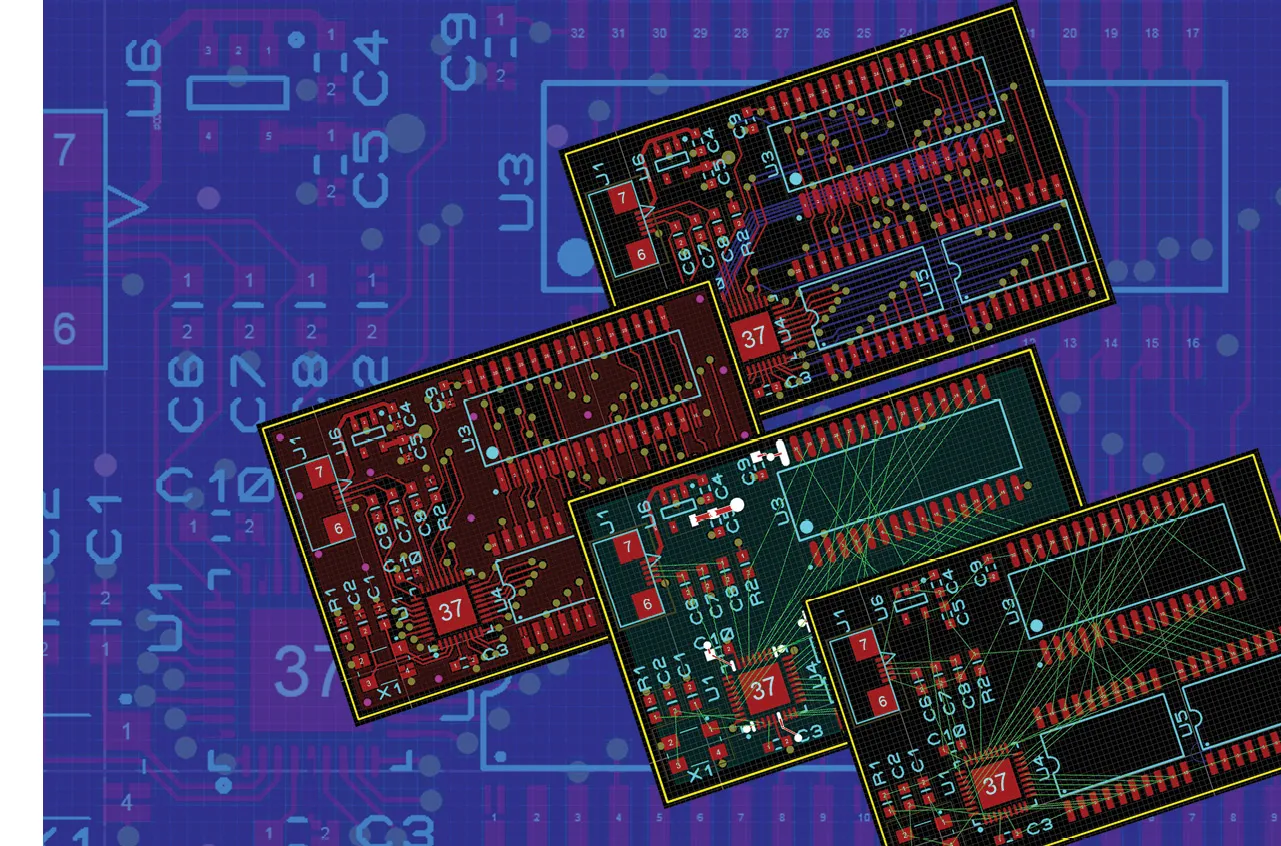
Глава 7

Учет Планов Земли и Питания
Планы земли и питания являются неотъемлемой частью проектирования печатных плат, обеспечивая эффективное распределение питания и целостность сигналов. Их правильная реализация имеет решающее значение для оптимизации работы схемы и снижения электромагнитных помех (EMI).
Роль Планов Земли и Питания
Целостность Сигнала:
Планы земли обеспечивают непрерывный путь возврата для сигналов, что помогает минимизировать площади сигнальных петель и снижает индуктивность, сохраняя при этом качество сигналов.Снижение Шума:
Планы земли и питания выступают в качестве экранов от электромагнитных помех (EMI). Сплошной план земли может поглощать и рассеивать EMI, создаваемые различными компонентами.Тепловое Управление:
Планы питания могут эффективно распределять тепло по печатной плате, способствуя управлению теплом и выполняя роль радиаторов для компонентов.Стабильность Напряжения:
Планы питания обеспечивают равномерное распределение напряжения по всей плате, предотвращая падения напряжения и обеспечивая стабильное питание компонентов.Упрощение Маршрутизации:
Выделяя слои для питания и земли, маршрутизация сигналов становится проще, снижая сложность дизайна и улучшая производственный процесс.
Как Эффективно Использовать Планы Земли и Питания
Используйте Выделенные Слои:
Для многослойных печатных плат выделяйте целые слои под сплошные планы земли и питания. Это упрощает управление слоями и оптимизирует производительность.Минимизируйте Разрывы:
Избегайте ненужного разделения планов земли. Разрывы могут прерывать пути возврата и увеличивать индуктивные петли, что ухудшает качество сигналов и увеличивает EMI.Эффективное Использование Соединительных Виасов:
Используйте соединительные виасы для связи планов земли и питания на разных слоях. Это помогает поддерживать стабильный потенциал и снижать индуктивность.Оптимизируйте Форму и Размер Планов:
Убедитесь, что планы питания и земли достаточно широки, чтобы выдерживать ожидаемые токовые нагрузки. Правильные размеры предотвращают перегрев и обеспечивают низкоимпедансные пути.Размещение Развязочных Конденсаторов:
Устанавливайте развязочные конденсаторы рядом с выводами питания микросхем, подключая их напрямую к планам питания и земли. Это фильтрует шумы питания и стабилизирует подачу напряжения.Разделение Аналоговой и Цифровой Земли:
Если на плате есть аналоговые и цифровые компоненты, используйте отдельные планы земли, чтобы предотвратить влияние цифрового шума на чувствительные аналоговые сигналы. Соединяйте их в одной точке, чтобы избежать земляных петель.Разделение Планов Земли с Осторожностью:
Если разделение необходимо (например, для различных доменов питания), убедитесь, что разделы четко определены, и внимательно следите за путями возврата, пересекающими разделы.Регулярные Проверки и Симуляции:
Используйте инструменты симуляции для проверки целостности и производительности планов земли и питания. Эти инструменты помогают выявить потенциальные слабые места или проблемы с помехами.
Понимая и тщательно проектируя планы земли и питания, можно значительно улучшить производительность и надежность печатных плат. Такой подход обеспечивает эффективную целостность сигналов, снижает риски, связанные с EMI, и повышает общую стабильность схемы.
Глава 8
Тепловое Управление в Проектировании Печатных Плат
Эффективное тепловое управление имеет решающее значение в проектировании печатных плат для обеспечения их надежной и стабильной работы, особенно в высокомощных приложениях. Понимание способов управления теплом помогает предотвратить перегрев, улучшить производительность и продлить срок службы электронных компонентов.
Понимание Теплового Управления
Значение Теплового Управления:
По мере того как электронные устройства становятся более компактными, плотность компонентов на печатных платах увеличивается, что приводит к повышенному потреблению энергии и генерации тепла. Эффективное тепловое управление обеспечивает правильное рассеивание тепла, предотвращая повреждение компонентов.Источники Тепла на Печатных Платах:
Тепло в основном генерируется силовыми компонентами, такими как процессоры, силовые транзисторы и светодиоды. Плохое управление теплом может привести к тепловому напряжению, что отрицательно скажется на физической целостности и производительности платы.Последствия Плохого Теплового Управления:
Без эффективного рассеивания тепла компоненты могут превысить свои максимальные рабочие температуры, что приведет к проблемам, таким как тепловой разгон, снижение эффективности и выход компонентов из строя.
Методы Улучшения Рассеивания Тепла на Печатных Платах
Использование Тепловых Виасов:
Интегрируйте тепловые виасы в областях с высоким выделением тепла, чтобы перенести его с верхнего слоя на внутренние слои или на противоположную сторону платы. Это увеличивает площадь для рассеивания тепла.Медные Заливки и Радиаторы:
Используйте медные заливки на печатной плате для равномерного распределения тепла. Для критически важных компонентов устанавливайте радиаторы для быстрого отвода тепла с поверхности.Оптимальное Размещение Компонентов:
Размещайте компоненты, генерирующие значительное количество тепла, в зонах с хорошей вентиляцией. Избегайте плотного группирования горячих компонентов, если не используются эффективные методы охлаждения.Многослойные Печатные Платы:
Используйте многослойные конструкции для интеграции внутренних тепловых распределителей, эффективно распределяющих тепло по разным слоям.Теплопроводящие Подложки и Изоляторы:
Применяйте теплопроводящие интерфейсные материалы, такие как теплопроводящие подложки, для улучшения передачи тепла от компонентов к радиаторам или слоям платы.Выбор Материала Платы:
Выбирайте материалы подложки для печатных плат с высокой теплопроводностью. Материалы, такие как печатные платы с металлическим сердечником или керамические подложки, могут улучшить рассеивание тепла.Установка Вентиляторов и Принудительного Охлаждения:
Для высокомощных приложений рассмотрите использование активных решений для охлаждения, таких как вентиляторы, чтобы улучшить воздушный поток через печатную плату.Тепловое Моделирование:
Применяйте программное обеспечение для теплового анализа на этапе проектирования, чтобы предсказать распределение тепла и выявить горячие точки. Это позволяет внести коррективы в макет или стратегию охлаждения до начала производства.
Применяя эти методы, разработчики могут эффективно управлять тепловыми проблемами при проектировании печатных плат. Это не только обеспечивает надежную работу, но и оптимизирует производительность и срок службы электронных устройств.
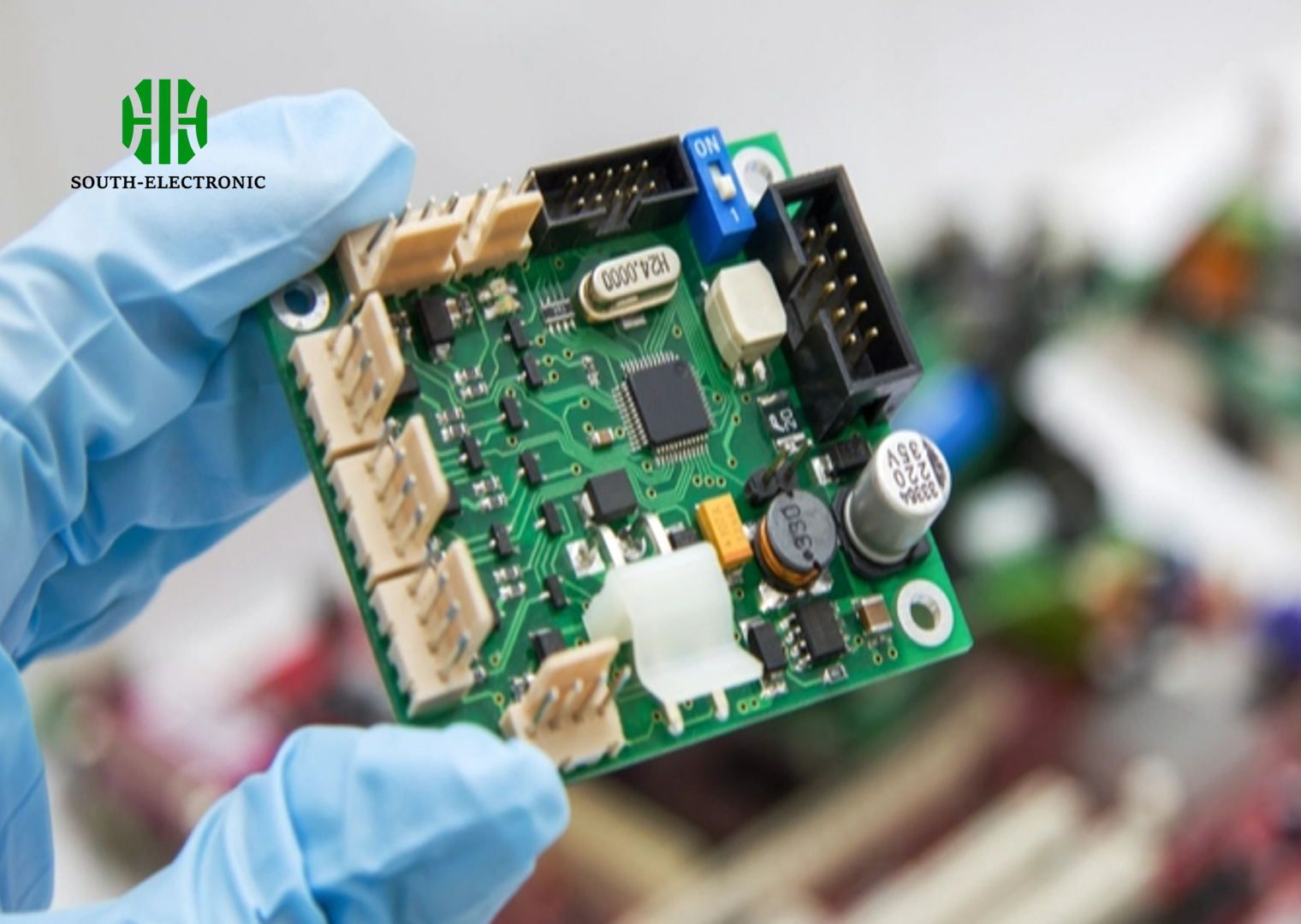
Глава 9
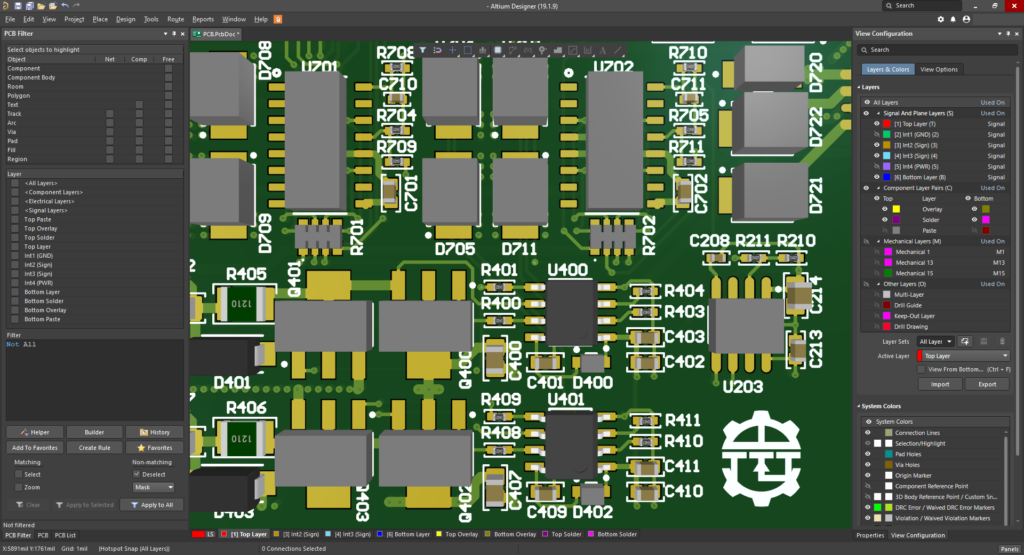
Тестирование и Отладка Проекта Печатной Платы
Методы Тестирования Проектов Печатных Плат Перед Массовым Производством
Прежде чем ваш проект печатной платы перейдет к массовому производству, необходимо тщательно протестировать и отладить макет, чтобы убедиться, что он соответствует всем спецификациям и работает, как задумано. Вот несколько эффективных методов, которые следует учитывать:
Электрическое Тестирование:
Включает использование автоматизированного оборудования для проверки на наличие коротких замыканий, разрывов цепи и правильных значений сопротивления по всей плате. Этот вид тестирования важен для подтверждения правильности электрических соединений и их функциональности.Функциональное Тестирование:
Симулируйте реальные условия работы печатной платы, чтобы убедиться, что все компоненты взаимодействуют корректно, а плата выполняет свои функции.Тестирование в Схеме (ICT):
ICT предполагает проверку компонентов печатной платы непосредственно на самой плате с использованием специализированных устройств и оборудования для выполнения прямых измерений. Это помогает выявить неисправности компонентов и убедиться, что каждая часть работает корректно в составе схемы.
Распространенные Проблемы, Обнаруживаемые При Тестировании Печатных Плат, и Способы Их Решения
При тестировании ваших макетов печатных плат вы, вероятно, столкнетесь с рядом распространенных проблем. Вот как их можно решить:
Проблемы Целостности Сигнала:
Проблемы, такие как перекрестные помехи, шум и интерференция, могут ухудшить работу печатной платы. Эти проблемы можно устранить, пересмотрев макет для увеличения расстояния между дорожками, улучшив заземление или применив методы экранирования.Проблемы Распределения Питания:
Могут возникать падения напряжения и нестабильное питание. Решить их можно, добавив дополнительные планы питания, улучшив развязку или переработав сеть распределения питания.Сбой Компонентов:
Дефектные или неправильно установленные компоненты могут привести к сбоям. Замена компонентов и проверка процедур установки на этапе сборки помогут устранить эти проблемы.
Инструменты для Эффективной Отладки Проектов Печатных Плат
Эффективные инструменты отладки необходимы для выявления и устранения проблем в макетах печатных плат. Вот некоторые основные инструменты, которые помогут ускорить процесс отладки:
Осциллографы:
Используйте осциллограф для визуального наблюдения за электрическими сигналами в цепи. Это особенно важно для выявления проблем с целостностью сигнала и синхронизацией.Мультиметры:
Необходимы для измерения напряжения, тока и сопротивления, мультиметры помогают убедиться, что каждая часть печатной платы работает в ожидаемых пределах.Логические Анализаторы:
Для более сложных цифровых схем логические анализаторы позволяют захватывать и отображать цифровые сигналы на печатной плате, что помогает выявить проблемы в цифровых потоках данных и интерфейсах.Тепловизоры:
Эти устройства позволяют визуально обнаруживать горячие точки на печатной плате, указывая на области, где электрические компоненты могут перегреваться или где может протекать чрезмерный ток.
Используя эти методы тестирования и отладки, вы можете убедиться, что макет вашей печатной платы оптимизирован для производительности и достаточно надежен для выполнения предполагаемых задач. Такой тщательный подход к тестированию и отладке не только повышает надежность конечного продукта, но и упрощает переход от прототипа к производству, экономя время и ресурсы в долгосрочной перспективе.
Глава 10
Будущие Тренды в Проектировании Печатных Плат
С развитием технологий проектирование печатных плат постоянно совершенствуется, чтобы соответствовать новым требованиям в производительности, миниатюризации и функциональности. Следить за новыми тенденциями помогает инженерам и дизайнерам предвидеть будущие вызовы и разрабатывать инновационные решения.
Перспективные Технологии в Проектировании Печатных Плат
Гибкая и Растяжимая Электроника:
Гибкие печатные платы, изготовленные из таких материалов, как полиимид, могут сгибаться и изгибаться без потери функциональности. Растяжимая электроника — это следующая ступень, позволяющая интеграцию в носимые устройства и медицинское оборудование.Встроенные Компоненты:
Встраивание пассивных (резисторы, конденсаторы) и активных (микросхемы) компонентов в слои печатной платы экономит пространство, улучшает электрические характеристики и повышает механическую прочность.Платы с Высокой Плотностью Межсоединений (HDI):
По мере уменьшения размеров устройств платы HDI, с более тонкими дорожками и микровиасами, обеспечивают большую плотность компонентов и улучшают маршрутизацию, что важно для современных гаджетов.3D-Печать и Аддитивное Производство:
Аддитивное производство позволяет создавать сложные 3D-структуры внутри печатной платы, открывая новые возможности для миниатюризации и многослойных схем.Современные Материалы:
Новые материалы для подложек, такие как керамика или передовые композиты, обладают превосходными термическими и электрическими свойствами, что улучшает производительность в приложениях с высокой частотой и мощностью.
Прогнозы для Будущих Инноваций в Проектировании Печатных Плат
Интеграция с IoT и ИИ:
В будущем печатные платы будут более тесно интегрироваться с устройствами IoT и алгоритмами ИИ, встраивая датчики и интеллектуальные функции непосредственно в плату для повышения связности и вычислительной мощности.Увеличение Использования Машинного Обучения:
Алгоритмы машинного обучения смогут оптимизировать процессы проектирования печатных плат, от размещения компонентов до маршрутизации, автоматически предсказывая узкие места и предлагая оптимальные конфигурации.Фокус на Экологичность:
С ростом экологических проблем будущие печатные платы будут уделять больше внимания экологически чистым материалам и производственным процессам, включая перерабатываемость и сокращение отходов.Интеграция с Квантовыми Вычислениями:
С развитием квантовых вычислений печатные платы должны будут адаптироваться к уникальным требованиям, таким как криогенные условия и точная целостность сигналов для кубитов.Биоразлагаемые и Экологически Чистые Печатные Платы:
Исследования в области биоразлагаемых подложек могут привести к созданию плат, которые разлагаются после окончания срока службы, снижая количество электронных отходов и облегчая их утилизацию.Развитие Многофункциональных Плат:
Печатные платы станут более универсальными, сочетая несколько функций и интегрируя возможности, такие как антенны и модули беспроводной связи, непосредственно в плату.Использование Дополненной Реальности (AR) в Проектировании:
AR может революционизировать проектирование печатных плат, предоставляя возможность в реальном времени визуализировать и изменять макеты в 3D-пространстве, что упростит и сделает процесс проектирования менее ошибочным.Улучшенные Решения для Управления Теплом:
Инновации в управлении теплом будут решать проблемы, связанные с увеличением плотности мощности, с использованием передовых материалов с фазовым переходом и жидкостного охлаждения, интегрированного непосредственно в печатные платы.
Изучая эти перспективные технологии и будущие тренды, разработчики печатных плат могут оставаться впереди, обеспечивая, чтобы их проекты были не только надежными, но и инновационными и соответствующими будущим потребностям рынка.
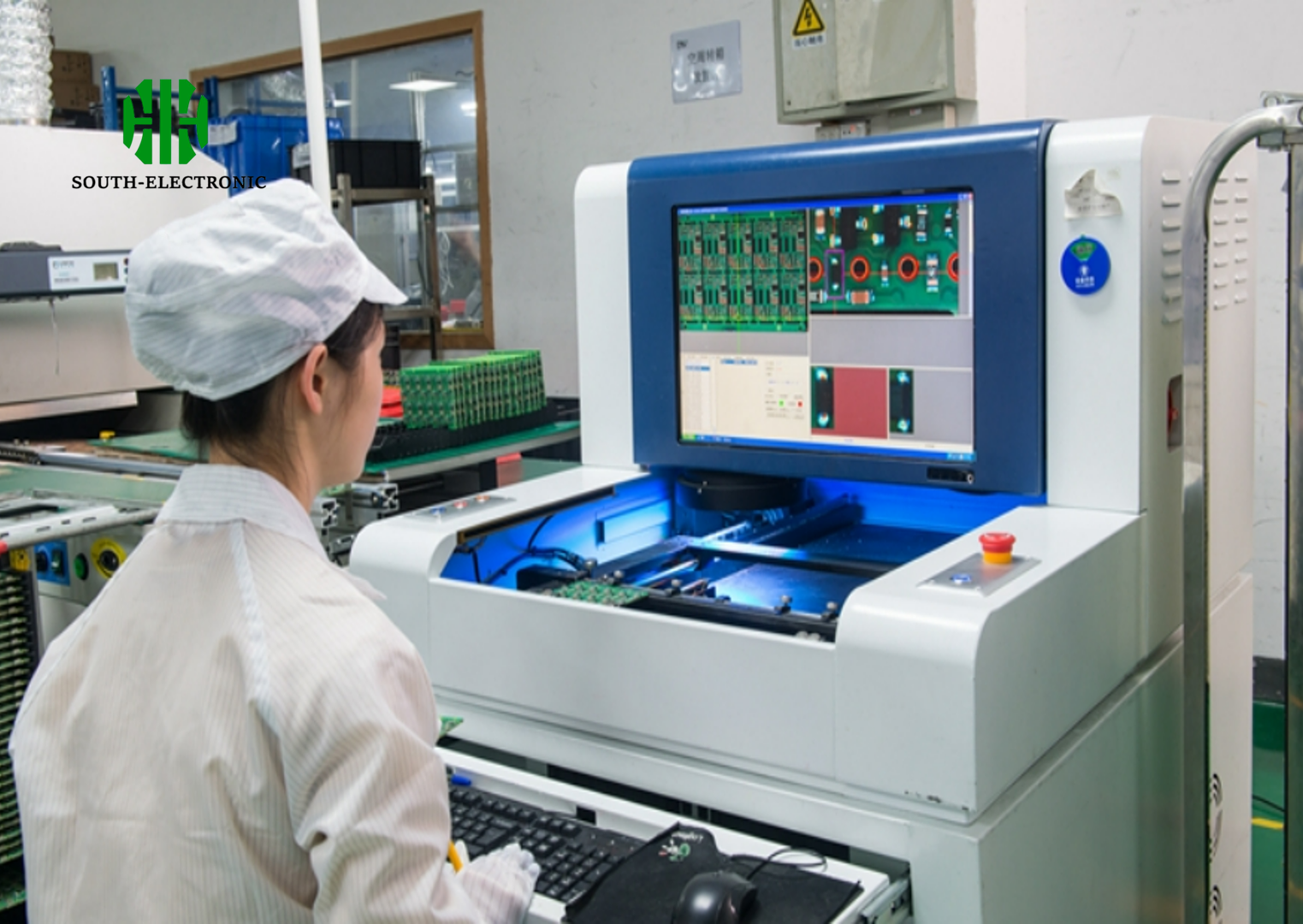
Связаться с Нами
Где Мы Находимся?
Промышленный Парк, № 438 Донхуан Роад, № 438, Шадзин Донхуан Роад, Район Баоань, Шэньчжэнь, Гуандун, Китай
4-й Этаж, Креативное Здание Жихуй, №2005 Сихуан Роад, Шадзин, Район Баоань, Шэньчжэнь, Китай
Комната A1-13, 3-й Этаж, Промышленный Центр Йи Лим, 2-28 Улица Kвай Лок, Квай Чунг, Гонконг
service@southelectronicpcb.com
Телефон: +86 400 878 3488
Отправьте нам сообщение
Чем подробнее вы заполните, тем быстрее мы сможем перейти к следующему шагу.
