Aluminum PCB Supplier
South-Electronic
Choose South-Electronic for unparalleled quality, reliability, and extraordinary value in your PCB solutions. We do it all, from design to delivery, with precision and compliance to the highest industry standards. Whether you need custom solutions or rapid prototyping, we're here to help you succeed.
Elevate Your Products with High-Quality Aluminum PCB
Welcome to South-Electronic, we’re the go-to place for top-notch Aluminum PCBs that are built to last and designed to keep things cool. Our state-of-the-art solutions are perfect for even the toughest jobs. Whether you need something super precise or you just need a prototype in a hurry, we’ve got you covered.
When you work with us, you’re partnering with a team that’s dedicated to making your products better, your production process smoother, and your business more successful. Let’s do this!
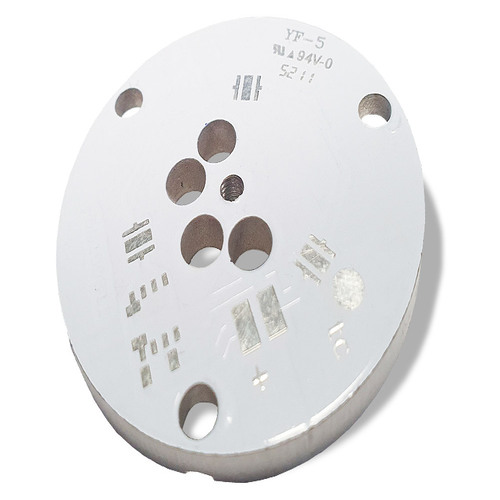
Single layer Aluminum PCB
This type of PCB has copper cladding on one side only and is used for simple single-layer circuit designs. It is widely used in LED lighting and consumer electronics because it is cost-effective and easy to manufacture.
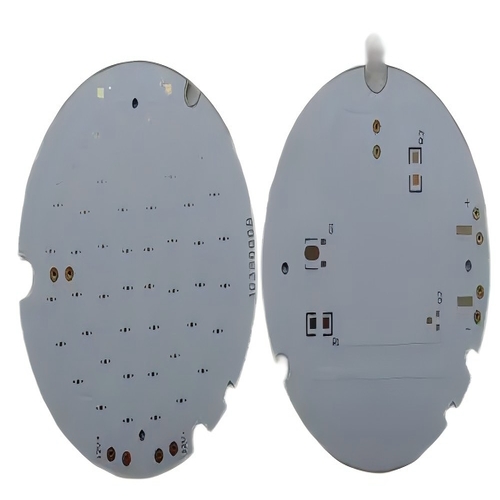
Double layer Aluminum PCB
This PCB has copper layers on both sides and is suitable for slightly more complex circuits that require thermal management on both sides of the board. It is commonly used in electronic devices that handle moderate power levels.
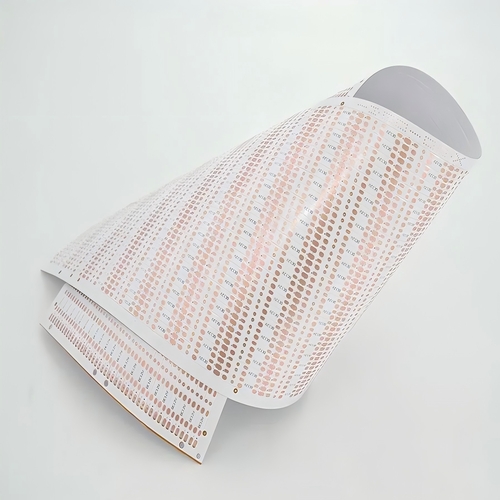
Flexible Aluminum PCB
Made with flexible materials, these PCBs can be bent or folded and are ideal for wearable devices and mobile technology. They combine the thermal advantages of aluminum with the flexibility of a flexible design.
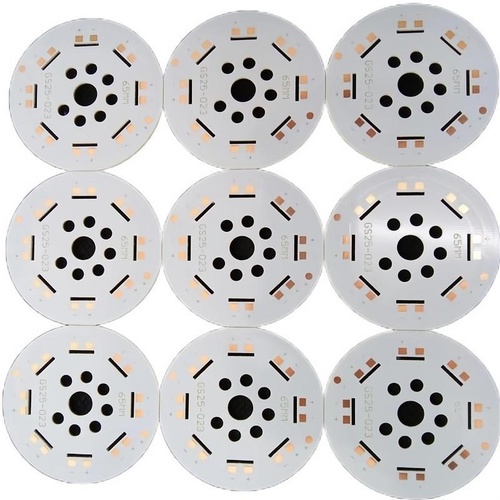
IMS PCB
IMS PCBs have excellent thermal conductivity and are ideal for applications that require rapid heat dissipation. They are commonly used in power converters, LED lighting systems, and automotive electronics, benefiting from a metal base that effectively dissipates heat from critical components.
Why Choose South-Electronic?
-
Custom Solutions
Tailor-Made for your project.
Work closely with South-Electronic to customize your PCB solution to ensure it precisely meets your specific requirements. Whether it's a specialized component or a complex design, you can rely on us to provide the products you need. -
Premium Quality
You deserve the best, and quality is our top priority.
With our rigorous quality control processes, including thorough inspections and testing, we guarantee that your products will meet the highest standards. Our PCBs are defect-free, so you can count on them to perform reliably in your production. -
Clear Communication
Provide you with responsive, clear and efficient service.
That’s why we provide clear, responsive support throughout the entire process. Whether you have a question or need an update, we’re here to keep you informed and make sure your project stays on track. -
Competitive Pricing
You want the best quality at the best price.
That’s why we offer top-quality PCBs at competitive prices. You can maximize your profit margins without sacrificing the high standards you require. We offer cost-effective solutions without cutting corners on quality, so you can stay ahead of the competition. -
Fast Global Shipping
You need a partner who can keep up with your fast-paced business.
We offer global shipping with fast turnaround times, so your PCBs arrive when you need them. With our reliable logistics, you don’t have to worry about delays. You can stay on schedule and keep your production running smoothly.
Related Project We had Done
Customer Reviews
engineer
thank you, guys, the boards are really good, i am really happy to receive my boards, the components are perfect!
Operation Manager
South-Electronic is my first PCBA supplier in China. The service and quality are excellent, and the after-sales support is also very impressive. Good Job!
Common Questions
Most Popular Questions
South-Electronic offers an extensive selection of aluminum PCBs, including single-sided, double-sided, and multilayer configurations. These options cater to a wide array of electronic applications, ensuring you find the perfect fit for your project.
South-Electronic excel in providing tailored solutions, using our advanced manufacturing techniques to precisely match your specific design needs. Whether it's a unique shape, size, or performance specification, South-Electronic has you covered.
At South-Electronic, we prioritize quality and reliability. Our aluminum PCBs undergo strict quality checks and are backed by a five-year warranty. We are proud to be ROHS, UL, and ISO certified, underscoring our commitment to excellence.
Time is often of the essence. That's why we offer expedited service options to help you meet tight deadlines without sacrificing quality.
We take environmental responsibility seriously. Our manufacturing processes are designed to be as eco-friendly as possible, ensuring our aluminum PCBs are both high-performance and environmentally sustainable.
At South-Electronic, we make sure you get your stuff fast. We know you need it, so we get it to you as quick as we can. We don't mess around with your time.
Send us a message
The more detailed you fill out, the faster we can move to the next step.
The Complete Guide for Aluminum PCB
Contents
Chapter 1
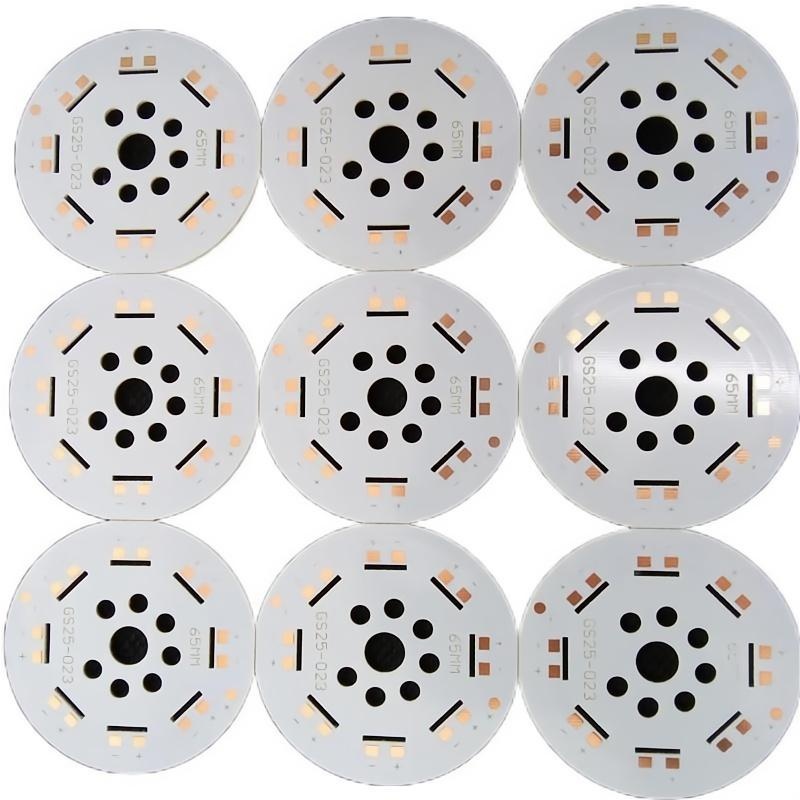
Introduction to Aluminum PCB
Definition and Overview
Aluminum PCBs, also known as Metal Core Printed Circuit Boards (MCPCBs), are specialized circuit boards that use a metal substrate, usually aluminum, to improve heat dissipation. Unlike traditional PCBs made mostly from FR-4 materials, aluminum PCBs have a base metal layer that acts as a heat spreader, which is important for high-power applications. This construction makes the boards more durable and better at managing heat, making them ideal for electronic devices that operate at high temperatures.
Advantages Over Traditional PCBs
- Enhanced Thermal Conductivity:Aluminum PCBs have better heat conductivity than traditional PCBs, which means they can effectively move heat away from important components to prevent overheating and ensure stability.
- Improved Dimensional Stability:The metal substrate makes aluminum PCBs more dimensionally stable, so they can perform well over a wide range of temperatures.
- Higher Mechanical Durability:These PCBs are stronger and more resistant to mechanical stress, so they’re good for environments with vibrations or impacts.
- Lightweight Yet Sturdy: Despite their metal base, aluminum PCBs remain relatively lightweight, providing an excellent strength-to-weight ratio.
- Cost-Effective Heat Management: By eliminating the need for additional heat sinks or cooling devices, aluminum PCBs reduce both system costs and space requirements.
Common Applications and Industries
Aluminum PCBs are widely used across various industries due to their outstanding thermal management and mechanical properties. Some common applications include:
LED Lighting: Aluminum PCBs are important in LED applications because they help dissipate heat, which improves performance and extends the lifespan of the LEDs.
Power Converters: Used in power supply and regulation modules where managing heat is important.
Automotive: Used in automotive electronics like brake and throttle systems, where durability and heat management are important.
Consumer Electronics: Used in audio-frequency devices and high-density circuit designs that need materials that can handle high temperatures.
Telecommunications: Used in routers and transmission boards that deal with high-frequency signals and heat.
By leveraging the unique properties of aluminum PCBs, these industries achieve enhanced performance, reliability, and longevity for their electronic devices, paving the way for innovative solutions and applications.
Chapter 2
Types of Aluminum PCB
1. Single-Sided Aluminum PCBs
Single-sided aluminum PCBs are the simplest type of these boards, with a single conductive layer of copper on one side of the aluminum substrate. They are typically used in applications where only one layer of circuitry is needed. The aluminum base provides excellent heat dissipation from the circuit layer to the environment. These PCBs are cost-effective and great for simple designs like LED lighting and general power applications, where you need to manage heat but don’t have a lot of circuit complexity.
2. Double-Sided Aluminum PCBs
Double-sided aluminum PCBs have conductive copper layers on both sides of the aluminum core. This allows for more complex circuitry compared to single-sided boards, giving you the ability to connect between the two sides through plated holes or vias. They are commonly used in more advanced power supply systems, automotive applications, and industrial controls where you need more layout options and better performance without sacrificing the heat dissipation benefits.
3. Multilayer Aluminum PCBs
Multilayer aluminum PCBs have multiple layers of circuitry stacked together, with insulating material in between. This lets you have really complex circuit designs while still getting great thermal performance because of the aluminum core in the stack. These PCBs are typically used in high-end applications like telecommunications and complex automotive electronics, where you need to save space and manage heat really well for the system to work right.
4. Hybrid Aluminum PCBs
Hybrid aluminum PCBs combine the benefits of aluminum substrates with dielectric materials or other metal cores to get the thermal and electrical properties you need for your PCB. This lets you mix different materials together, so you can get electrical insulation along with great thermal conductivity. Hybrid PCBs are especially useful in applications that need a custom balance of performance, like RF applications, precision power electronics, and advanced lighting systems, where traditional PCB materials might not be good enough.
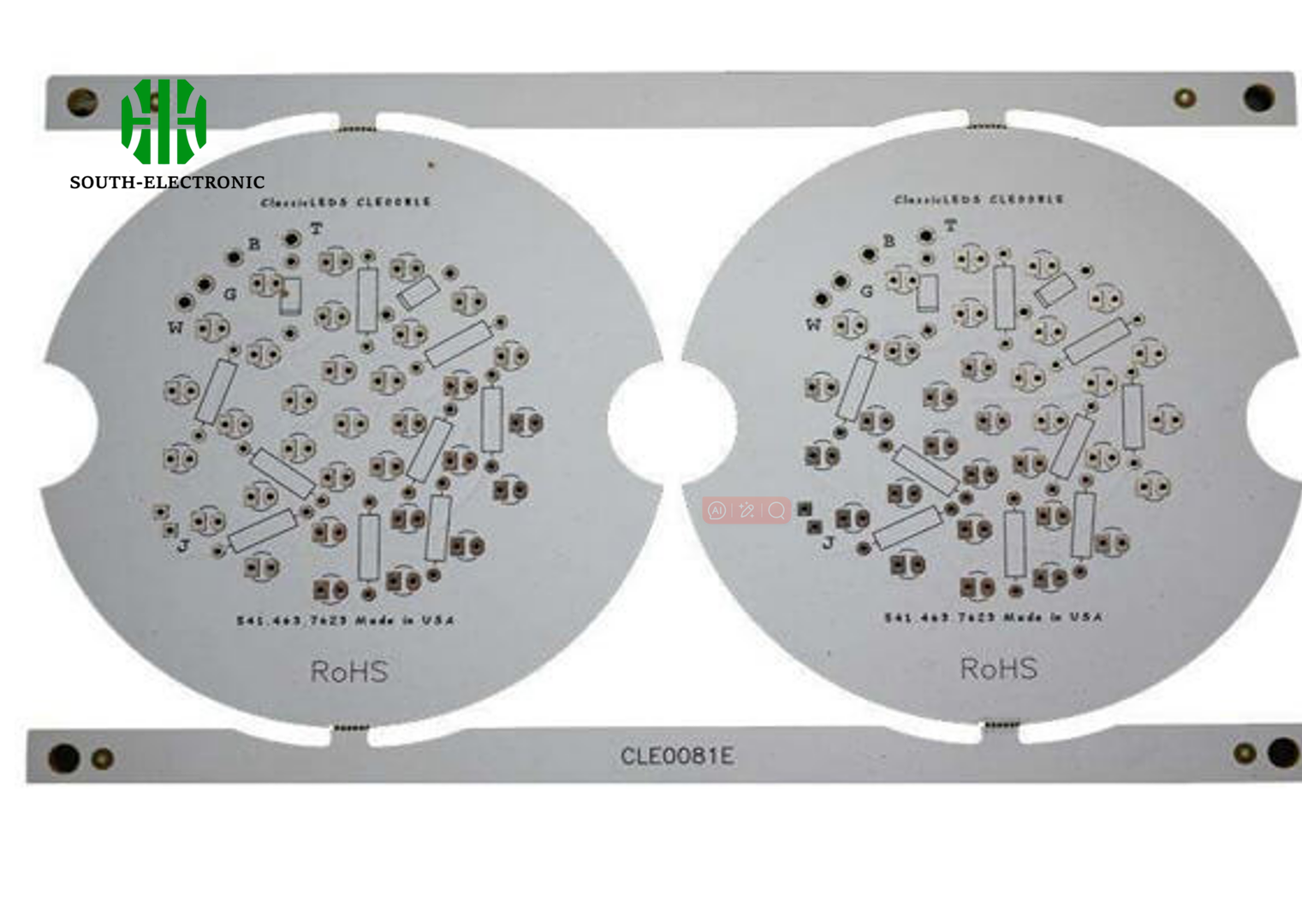
Chapter 3
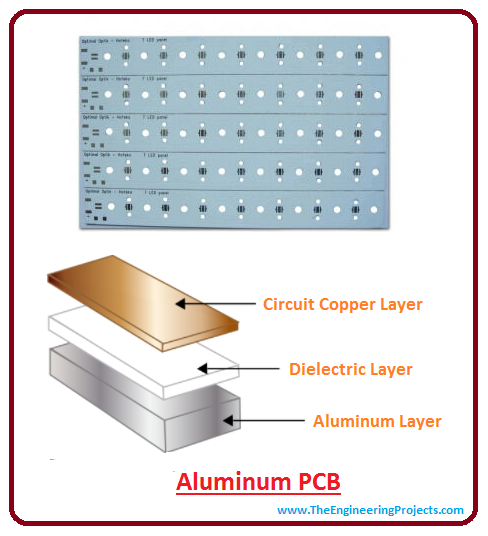
Materials and Construction of Aluminum PCB
Composition of Aluminum PCBs
Aluminum PCBs are unique because they have a metal substrate, usually aluminum, that is chosen for its great thermal conductivity and lightweight properties. Aluminum PCBs have three main components:
- Aluminum Base: This is the main part that provides the structure and also helps with heat dissipation. This is especially important for applications that generate a lot of heat.
- Dielectric Layer: This is a material that is thermally conductive but electrically insulating. It separates the aluminum base from the circuit layer. It helps transfer heat from the circuitry to the aluminum base while keeping the electricity separate.
- Circuit Layer: This is usually a layer of copper foil that is etched to create the circuitry. The thickness of this layer depends on the electrical needs of the application.
Layer Structure
The construction of aluminum PCBs usually consists of three main layers, each serving a distinct purpose:
Base Layer (Aluminum Substrate):
- Provides the foundational structure of the PCB.
- Offers mechanical rigidity and robustness.
- Acts as a heat sink, conducting heat away from the circuit components.
Dielectric Layer:
- A thin, thermally conductive material placed between the circuit layer and the base.
- Its primary function is to conduct heat from the circuit layer to the aluminum base efficiently.
- It also acts as an electrical insulator, preventing electrical currents from passing to the aluminum layer.
Circuit Layer:
- Comprised of a copper foil that is etched to create the desired circuit pattern.
- Supports the flow of electrical signals across the PCB.
This layered structure is engineered to optimize thermal performance while maintaining electrical integrity, making aluminum PCBs suitable for applications requiring reliable thermal management.
Comparison with Other Metal Core PCB
Aluminum PCBs are part of the broader category of Metal Core PCBs (MCPCBs), which include other metal options such as copper and steel. Here are some comparisons:
Thermal Conductivity: Aluminum PCBs generally offer better thermal conductivity compared to steel-core PCBs, though copper-core PCBs have even higher thermal conductivity levels. However, aluminum strikes a balance between performance and cost.
Cost-Effectiveness: Aluminum is more cost-effective than copper, making aluminum PCBs an economical choice for applications that require good thermal management without incurring the higher costs associated with copper.
Weight: Aluminum is significantly lighter than other metals like copper and steel, making aluminum PCBs preferable for applications where weight is a consideration, such as in aerospace and portable electronics.
Manufacturability: Aluminum PCBs are easier to process and more versatile in design compared to their copper and steel counterparts. This ease of manufacturing often translates into shorter lead times and lower production costs.
By understanding the materials and construction of aluminum PCBs, industries can better choose the right PCB type that aligns with their specific needs, ensuring efficient performance and reliability.
Chapter 4
Manufacturing Process of Aluminum PCBs
How to Make an Aluminum PCB?
- Design and Layout:The first step in making an aluminum PCB is designing the circuit board using PCB design software. This design includes all the details about how the circuit paths will be laid out and routed.
- Material Preparation:Next, the aluminum substrate is prepared to the required dimensions and cleanliness standards. This is the base of the board and everything else will be built on top of it.
- Lamination:A dielectric layer is applied to the aluminum substrate. This layer is thermally conductive but electrically insulating, and it’s what the conductive copper layer will sit on top of.
- Copper Patterning:A layer of copper foil is laminated on top of the dielectric. This copper layer is then patterned using processes like photoengraving or laser etching to create the circuit paths.
- Etching:The unprotected areas of the copper layer are etched away using chemical solutions, leaving behind the actual circuit patterns.
- Drilling and Plating:Holes are drilled into the board as needed for through-hole components or mounting purposes. Depending on the design, these holes may be plated to create electrical connections between different layers.
- Solder Mask Application:A solder mask is applied over the board to protect the circuit from oxidation and prevent solder bridges during component assembly. Openings are left where components will be soldered.
- Surface Finishing:The surfaces of the board are finished to improve solderability and protect exposed copper. Common finishes include HASL (Hot Air Solder Leveling) and ENIG (Electroless Nickel Immersion Gold).
- Testing and Quality Control:The finished PCBs are tested to ensure they work properly and meet the required quality standards before being shipped to the customer or moving on to assembly.
Key Technologies and Machines Used
- CNC Machines:These machines are used for precise drilling and milling operations to ensure the holes and cutouts are accurate.
- Photo Imaging Equipment:This equipment is used during the copper patterning stage to transfer the circuit design onto the copper layer using UV light or lasers.
- Etching Machines:Automated etching tanks are used to remove unwanted copper and refine the circuit paths on the boards.
- Lamination Presses:These are used to create multilayer constructions or press the dielectric and copper layers onto the aluminum substrate.
- Solder Mask Application Systems:Machines or manual processes are used to apply the protective solder mask over the circuit.
Challenges and Considerations in Manufacturing
- Thermal Management:It’s important to manage heat effectively without compromising the integrity of the circuit, which requires careful material selection and process controls.
- Precision and Accuracy:Aligning the layers and accurately etching and drilling are critical to avoid short circuits and connectivity issues. This requires high-precision machines and strong quality control processes.
- Material Characteristics:Working with aluminum requires special handling and tooling to prevent the metal from warping and to maintain dimensional stability.
- Cost Management:Balancing material costs and manufacturing expenses while maintaining quality is an important consideration for cost-effective production.
By understanding these manufacturing steps, technologies, and challenges, manufacturers can optimize their processes to produce high-quality aluminum PCBs for demanding applications.
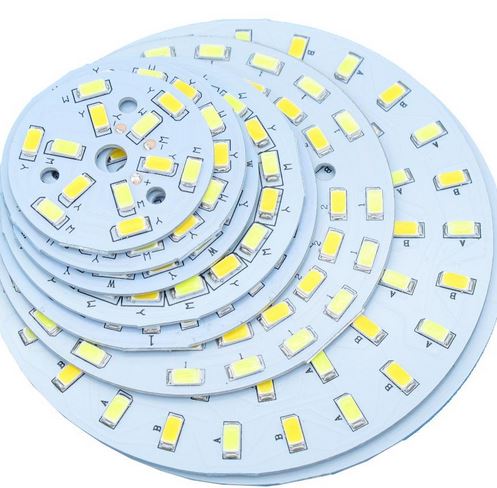
Chapter 5
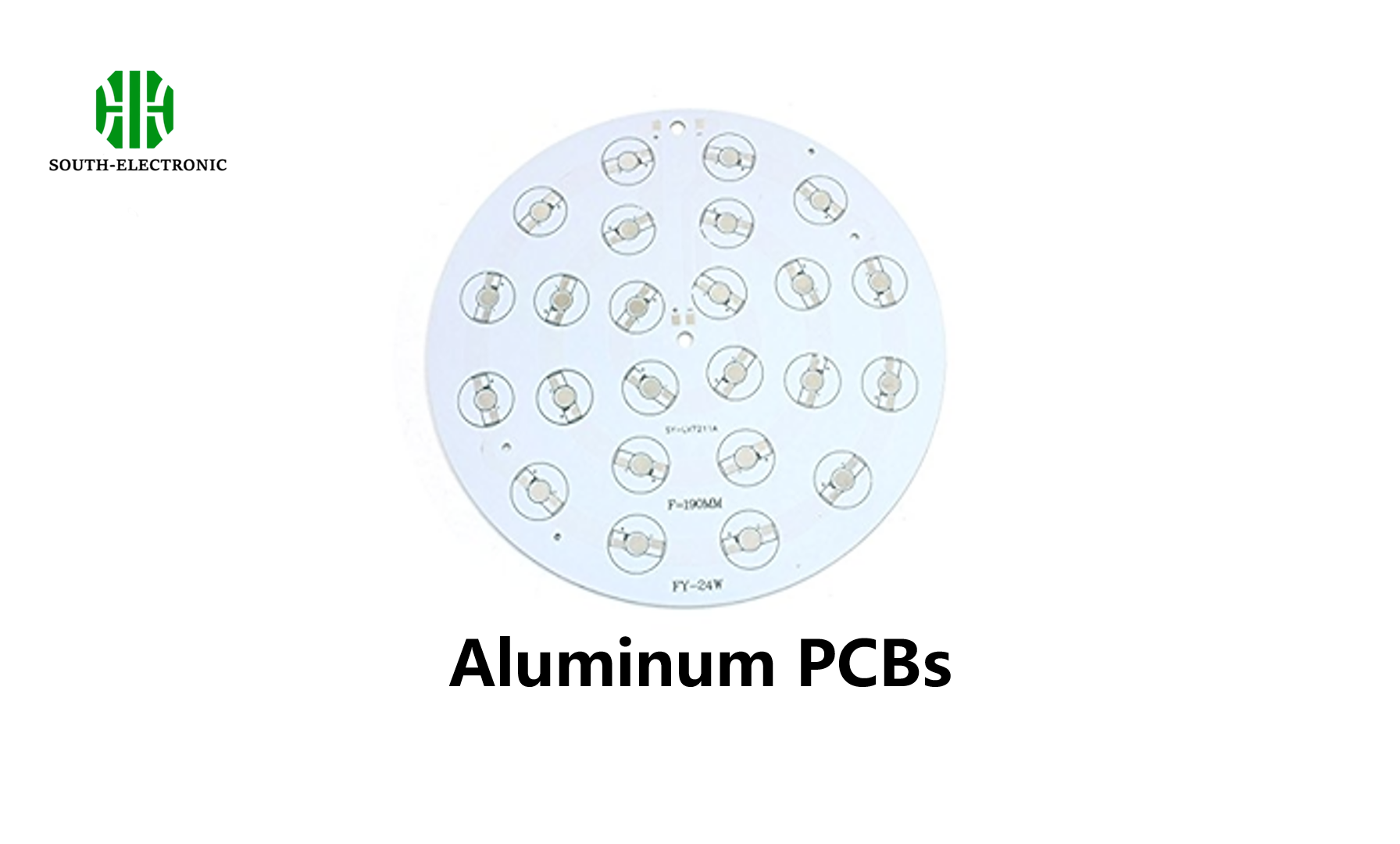
Designing Aluminum PCB
Design Guidelines and Best Practices
- Choosing the Right Materials:Choose the dielectric material that will work best for your design based on its thermal conductivity and electrical insulation properties. This is key to making sure that heat is transferred efficiently and that your circuit performs reliably.
- Deciding on the Number of Layers:Decide whether you need a single layer, a double-sided board, or a multilayer board based on the complexity and functionality of your circuit. Make sure that the layer stack-up supports good thermal management.
- Optimizing Trace Widths and Spacing:Make sure that your trace widths and spacing are optimized so that they can handle the current loads without causing a lot of heat to build up. Follow the IPC standards to make sure that your board is reliable and performs well.
- Placing Components:Place your components strategically so that you minimize thermal gradients and make sure that heat is distributed evenly. Make sure that components that generate heat have a direct thermal pathway to the aluminum substrate.
- Using Thermal Vias:Use thermal vias to help dissipate heat vertically, especially if you have a multilayer board. This is important for getting the heat from the heat source to the aluminum base.
- Considering Solder Mask and Silkscreen:Use solder masks to prevent solder bridges and to protect your circuitry. Make sure that the silkscreen layer that you use for component designation doesn’t interfere with the exposed metal areas that you need for heat dissipation.
- Design for Manufacturability (DFM):Work closely with your manufacturer to make sure that your design aligns with their manufacturing capabilities. This will help you minimize the risk of errors and make sure that your board is produced efficiently.
Thermal Management and Heat Dissipation Considerations
- Efficient Heat Pathways:Design pathways that allow direct thermal transfer from components to the aluminum substrate. This includes minimizing obstruction in heat flow paths.
- Thermal Simulation:Use thermal simulation software to predict and optimize heat dissipation performance. Identifying hotspots through simulation helps in effective thermal management planning.
- Component Heat Sinking:Include built-in heat sinks where possible or consider additional heat sink attachments to support major heat-generating components.
- Environmental Testing:Validate thermal performance under operational conditions through rigorous testing. This ensures the PCB will operate reliably within the intended thermal envelope.
- Ventilation and Convection:Design PCBs considering the system’s overall ventilation. Proper airflow and placement within the enclosure can significantly enhance thermal performance.
Designing aluminum PCBs involves a comprehensive understanding of material properties, electrical performance, and thermal management. By following best practices and using advanced design tools, engineers can create efficient, reliable PCBs for demanding applications.
Chapter 6
Quality Standards and Certifications
Why ROHS, UL, and ISO Certifications Matter?
1.ROHS (Restriction of Hazardous Substances)
- Why it matters: ROHS compliance ensures that the aluminum PCBs are free from hazardous materials such as lead, mercury, cadmium, and certain brominated flame retardants. This is important for the health and safety of both consumers and the environment, especially in consumer electronics.
- What it means: Meeting ROHS standards helps to reduce the environmental impact and build consumer trust by assuring that the products are environmentally friendly.
2.UL (Underwriters Laboratories)
- Why it matters: UL certification indicates that the aluminum PCBs meet specific safety standards, with a focus on fire safety and product reliability.
- What it means: UL certification adds credibility to the product and demonstrates that it has undergone rigorous testing for safety and performance. This gives manufacturers and end-users confidence in the safety of the electronic components.
3.ISO (International Organization for Standardization)
- Why it matters: Specifically, ISO 9001 and ISO 14001 relate to quality management systems and environmental management systems, respectively. These certifications ensure that PCB manufacturers follow systematic quality assurance practices and are environmentally responsible.
- What it means: ISO certifications drive continuous improvement in processes, increase efficiency, and provide customers with confidence in consistent product quality and the organization’s commitment to sustainability.
How Certifications Impact Performance and Reliability?
- Better Quality Products:Complying with standards means using good materials and processes, which reduces defects and makes aluminum PCBs work better.
- More Market Acceptance:Certified products are more likely to be accepted in global markets because they meet international standards for safety and quality.
- Safer and More Reliable:Certified products have been tested a lot, so they are safer and more reliable. You can trust them to work the same way every time, no matter what.
- Last Longer:Standards and certifications help aluminum PCBs last longer because they are made from better materials and tested to make sure they can handle different conditions.
Better Quality Control
- Check the Materials:Make sure all the materials coming in are what they are supposed to be. This includes checking for ROHS and other things that are important.
- Control the Process:Keep a close eye on how you make things so they are always the same and always good. Use machines to help you make things the same way every time.
- Test and Test Again:Test everything to make sure it works and will keep working. Test the electricity, test the heat, and test it some more. Make sure it works right.
- Fix It:Use things like Six Sigma to find and fix problems. When you find a problem, fix it right away.
- Write It Down:Write down everything you do so you can look at it later. This helps you get better and makes sure you are doing things the right way.
When you follow the rules and get the right certifications, you can make aluminum PCBs that work well, are safe, and last a long time. This makes the people who make the rules happy and makes the people who buy your stuff happy too.
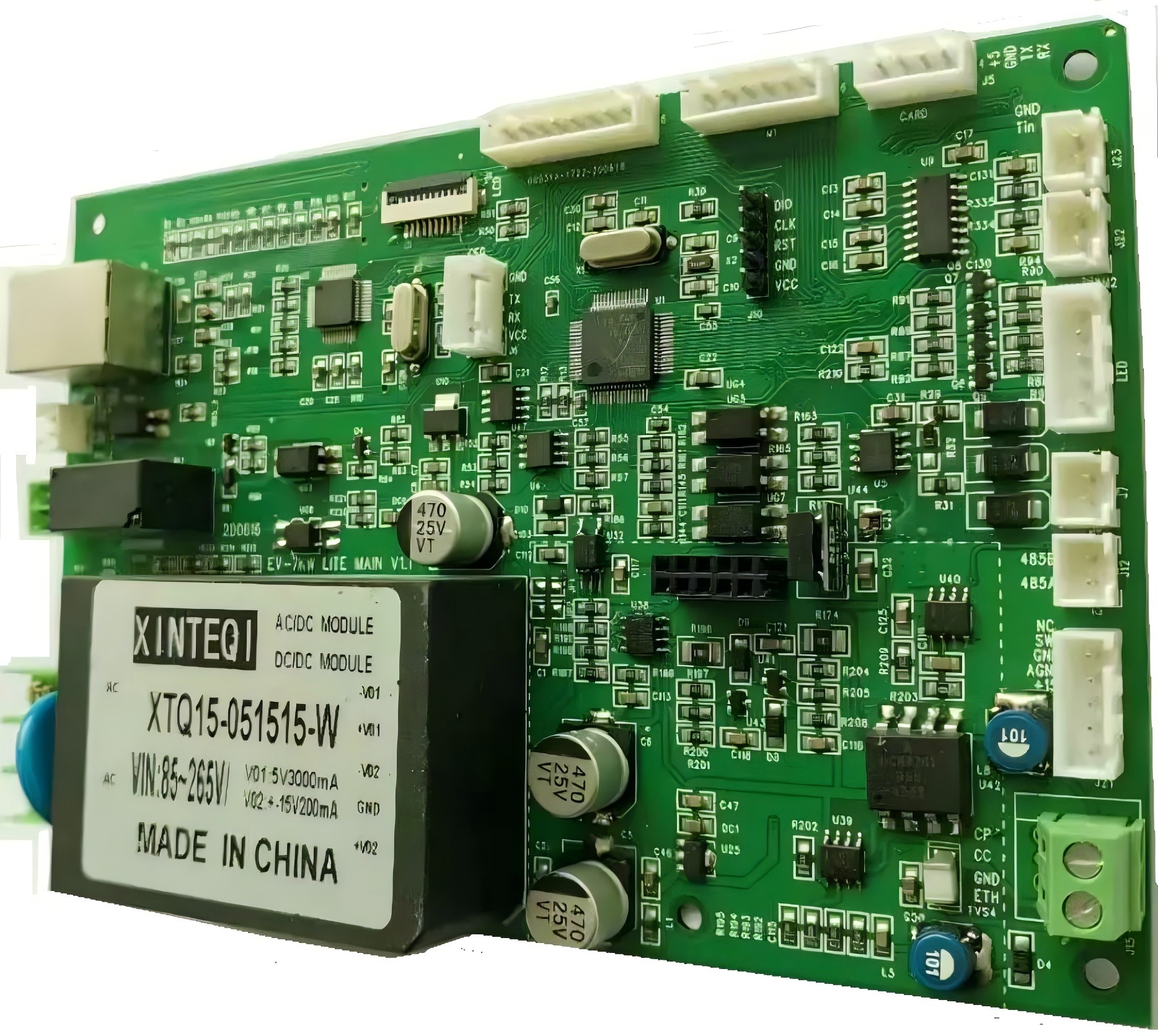
Chapter 7
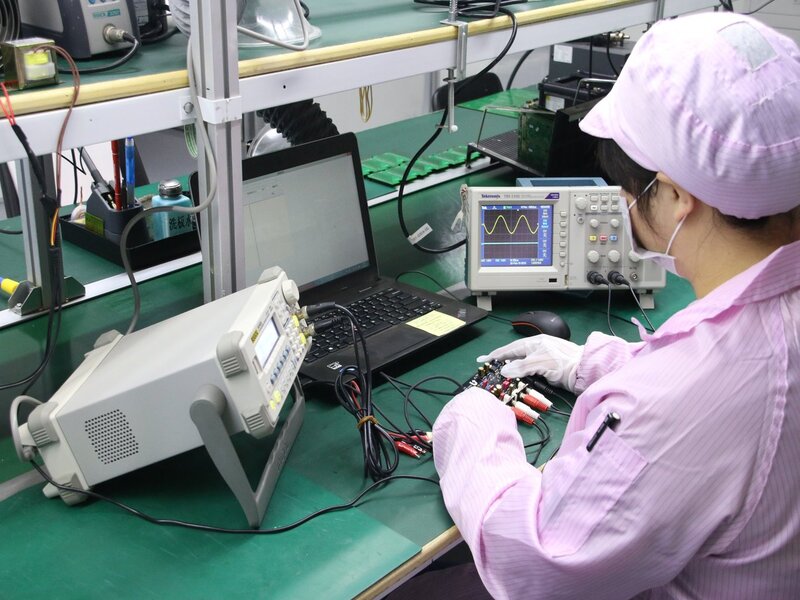
Environmental Impact and Sustainability
Eco-Friendly Manufacturing Practices
- Green Material Sourcing:Make sure all the stuff you use is eco-friendly, and that you get it from places that don’t mess up the environment. You should also use materials that don’t have any bad stuff in them.
- Waste Management and Reduction:Figure out ways to make less trash when you’re making stuff. You can also recycle the stuff you don’t use so you don’t have to throw it away.
- Water and Energy Conservation:Use machines that don’t use as much water and power. This will help you not mess up the environment as much when you’re making stuff.
- Emission Control:Use machines that don’t let out bad stuff into the air. You should also follow the rules about not messing up the environment.
Lifecycle and Recyclability of Aluminum PCBs
- Durability and Longevity:Make stuff that lasts a long time so people don’t have to throw it away and get new stuff. This will help the environment because people won’t have to make as much stuff.
- Recyclability:You should use materials that can be used again after you’re done with them. This will help the environment because people won’t have to make as much stuff.
- End-of-Life Management:You should tell people to recycle the stuff they don’t want anymore. You can also help people recycle the stuff they don’t want anymore.
Initiatives for Reducing Carbon Footprint
- Sustainable Supply Chain:Work with people who don’t mess up the environment. This will help the environment because people won’t have to make as much stuff.
- Renewable Energy Integration:Use power from the sun or wind to make stuff. This will help the environment because people won’t have to use as much stuff that messes up the environment.
- Transportation Optimization:Figure out ways to get stuff to people without using as much gas. This will help the environment because people won’t have to use as much stuff that messes up the environment.
- Innovative Design Strategies:Make stuff that doesn’t use as much stuff. This will help the environment because people won’t have to use as much stuff that messes up the environment.
- Stakeholder Engagement:Work with other people to make stuff that doesn’t mess up the environment. This will help the environment because people won’t have to use as much stuff that messes up the environment.
Chapter 8
Cost Factors and Considerations
Cost Comparison with Other PCB Types
Material Costs:Aluminum PCBs generally have higher material costs compared to traditional FR-4 PCBs due to the use of metal substrates and specialized dielectric materials aimed at enhancing thermal management.
Manufacturing Complexity:The manufacturing process for aluminum PCBs can be more complex, often involving additional steps such as precise thermal management features, which can increase production costs compared to standard rigid or flexible PCBs.
Thermal Management Benefits:Despite higher initial costs, aluminum PCBs offer superior thermal performance, reducing the need for external cooling mechanisms in electronic devices and potentially lowering overall system costs.
Factors Influencing Pricing
Volume:Higher production volumes typically lead to reduced costs per unit due to economies of scale. Bulk orders spread fixed costs over many units, thus decreasing individual unit cost.
Design Complexity:The complexity of the PCB design, including the number of layers, presence of vias, and intricate routing, directly impacts the pricing. More complex designs require more time and resources to produce.
Material Selection:The choice of dielectric materials and aluminum grade influences costs. High-performance materials designed for specific applications or enhanced features (e.g., better thermal conductivity) tend to be more expensive.
Customization and Special Features:Custom PCB designs with unique features or custom shapes often demand specialized production techniques, affecting overall costs. Features like additional thermal vias or complex component footprints can increase the price.
Tips for Cost-Effective Manufacturing
Optimize Design for Manufacturing (DFM):Simplify designs where possible to avoid unnecessary complexity. Collaborate with manufacturers early in the design process to align on capabilities and cost-saving strategies.
Material Efficiency:Select materials that offer the best compromise between performance and cost. Evaluate the specific thermal and electrical needs of your application to avoid over-specifying materials.
Batch Production:Group orders or consolidate similar designs into one production run to take advantage of the cost savings associated with large-scale production.
Supplier Relationships:Build strong relationships with suppliers to negotiate better pricing, leverage their expertise for cost reduction, and ensure a stable supply chain that can lead to more favorable terms.
Iterative Prototyping:Employ iterative prototyping and testing to refine designs. Identifying and addressing potential issues during prototyping can prevent costly revisions and delays in full-scale production.
Streamline Processes:Invest in efficient manufacturing processes and automation to reduce labor costs and increase throughput. This not only cuts costs but also helps ensure consistent quality.
By understanding and addressing the cost implications associated with aluminum PCBs, manufacturers can effectively manage expenses while delivering efficient, high-quality products that cater to the needs of their customers.
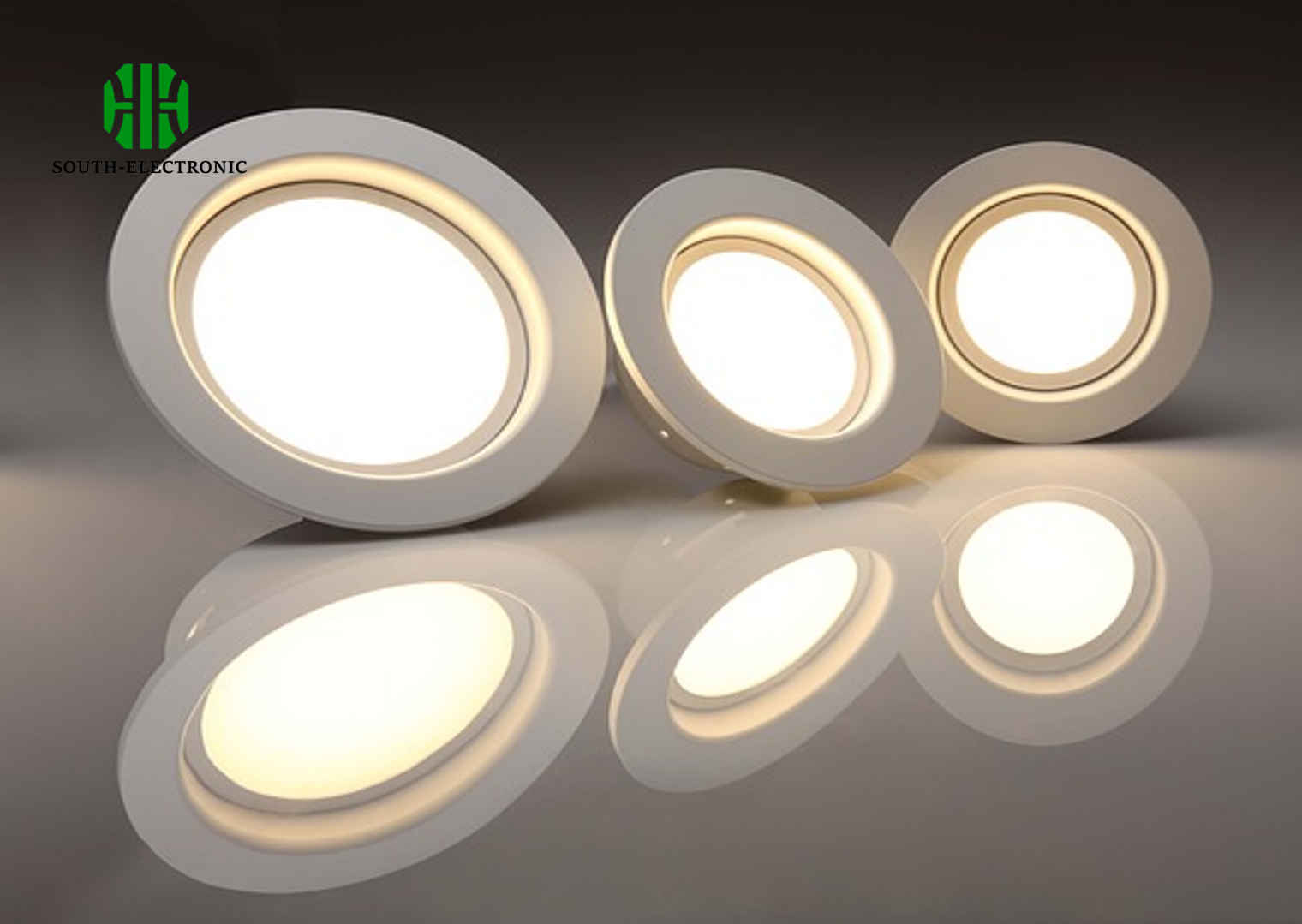
Chapter 9
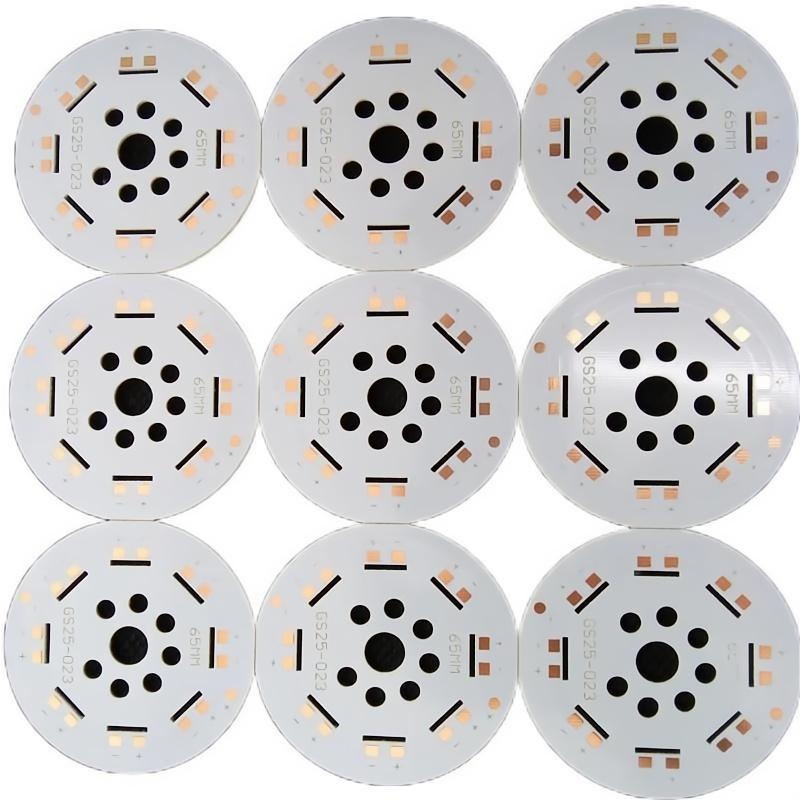
Market Trends and Innovations
Recent Advances in Aluminum PCB Technology
- Better Heat Management Materials:New materials have been developed that have better thermal conductivity and electrical insulation properties. This allows for better heat dissipation and performance in high-power applications.
- Integration with Advanced Components:Components can now be embedded directly into aluminum PCBs, allowing for slimmer designs and more efficient thermal pathways. This is being used more and more in applications like automotive and high-performance computing.
- Flexible Aluminum PCBs:Flexible aluminum PCBs have been developed that combine the thermal management benefits of aluminum substrates with the flexibility of flexible circuits. This is being driven by the demand for wearable technology and compact consumer electronics.
- Automated Manufacturing Techniques:Advances in manufacturing automation, such as precision laser cutting and automated optical inspection (AOI), have increased production efficiency and reduced defect rates in aluminum PCB manufacturing.
Trends Driving the Growth of Aluminum PCBs
- Demand for Efficient Thermal Solutions:As electronics become more powerful and compact, the need for effective thermal management solutions has driven the growth of aluminum PCBs, especially in LED lighting, automotive, and renewable energy sectors.
- Rise of Electric Vehicles (EVs):The shift towards electric vehicles, which require efficient power electronics and battery management systems, has significantly increased the demand for aluminum PCBs due to their superior thermal properties.
- Expansion of Consumer Electronics:As consumer electronics continue to evolve towards more powerful and compact designs, aluminum PCBs are increasingly being adopted for their ability to handle higher thermal loads and provide better reliability.
- Sustainability and Eco-Friendliness:With an increased emphasis on sustainability, the recyclability and natural abundance of aluminum have made aluminum PCBs an attractive choice for manufacturers looking to adopt more eco-friendly practices.
Future Outlook and Emerging Opportunities
- Growth in 5G and IoT Applications:The proliferation of 5G technology and IoT devices presents significant opportunities for aluminum PCBs due to their ability to manage high frequencies and heat dissipation in these advanced technologies.
- Advancements in Renewable Energy Solutions:As the renewable energy sector grows, the demand for reliable and efficient power management systems using aluminum PCBs in solar panels and wind turbines is expected to rise.
- Miniaturization and High-Performance Computing:The push towards miniaturization and the development of high-performance computing applications open new avenues for aluminum PCBs, which are ideal for environments requiring compact, efficient thermal management.
- Collaborative Innovations:Industry collaborations and partnerships are likely to spur new innovations and applications for aluminum PCBs, benefiting from shared expertise and technological advancements.
The market for aluminum PCBs is set to continue growing as technology evolves, driven by the need for enhanced performance and sustainability in a wide range of applications.
Chapter 10
How to Choose a Reliable Aluminum PCB Supplier?
Quality Standards and Certifications
Make sure the supplier meets industry-standard quality certifications such as ISO 9001, ISO 14001, UL, and ROHS compliance. These certifications show that the supplier follows strict quality management and environmental standards, ensuring high-quality products.
Technical Expertise and Capabilities
Evaluate the supplier’s technical expertise and manufacturing capabilities, including their ability to handle complex designs, multilayer PCBs, and custom specifications. A supplier with advanced technological capabilities can meet diverse and challenging project requirements.
Experience and Track Record
Consider the supplier’s experience in the industry. A well-established supplier with a proven track record of delivering aluminum PCBs to various industries increases reliability and trust in their products and services.
Customization and Flexibility
Choose a supplier that offers customization options and demonstrates flexibility in production processes. The ability to accommodate unique designs and varying production volumes is crucial to support specific project needs.
Quality Assurance Measures
Look into the supplier’s quality assurance practices, including their inspection and testing procedures. Suppliers that use advanced testing techniques and equipment, such as automated optical inspection (AOI) and X-ray testing, ensure product quality and reliability.
Supply Chain Management and Reliability
Evaluate the supplier’s supply chain management practices. A reliable supplier should ensure consistent availability of raw materials, timely delivery, and minimal disruptions to production timelines.
Customer Support and Service
Superior customer support is essential, including clear communication, responsiveness to inquiries, and willingness to address issues. A supplier that prioritizes customer satisfaction can become a valuable partner in your success.
Cost Competitiveness
While cost should not be the only factor, it is important to find a supplier that offers competitive pricing without compromising quality. Transparent pricing and a clear understanding of cost factors can help with budgeting and financial planning.
Sustainability Practices
Given the increasing importance of sustainable practices, choose suppliers that prioritize environmental responsibility and sustainability. This includes efforts to reduce waste, optimize energy usage, and promote recyclable materials.
References and Reviews
Seek references and reviews from previous clients to gain insight into the supplier’s reliability and performance history. Positive feedback from reputable sources is often a good indication of the supplier’s reputation in the industry.
Choosing the right supplier for aluminum PCBs requires careful consideration of various factors that ensure high-quality production, reliability, and a productive partnership focused on achieving your project goals.
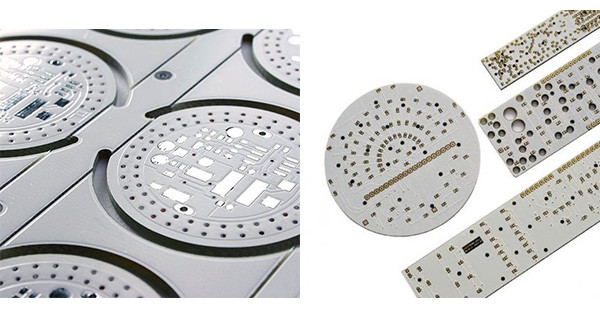
Get in touch
Where Are We?
Industrial Park, No. 438 Donghuan Road, No. 438, Shajing Donghuan Road, Bao'an District, Shenzhen, Guangdong, China
Floor 4, Zhihui Creative Building, No.2005 Xihuan Road, Shajing, Baoan District, Shenzhen, China
ROOM A1-13,FLOOR 3,YEE LIM INDUSTRIAL CENTRE 2-28 KWAI LOK STREET, KWAI CHUNG HK
service@southelectronicpcb.com
Phone : +86 400 878 3488
Send us a message
The more detailed you fill out, the faster we can move to the next step.
