Telecom PCB Providers
South-Electronic
At South-Electronic, we specialize in providing top-quality telecom PCB that ensure durability, reliability, and excellent performance, making your communication systems run more smoothly and efficiently.
Optimize Your Network Systems with South-Electronic’s Telecom PCB
Your telecom projects deserve the best, and South-Electronic’s PCB delivers. Designed to meet the rigorous demands of telecom environments, our PCB ensure your network systems—from data centers to communications satellites—operate at peak efficiency.
Your success in communications starts with reliability. South-Electronic provides you with the highest quality telecom PCB to enhance your systems with consistent, powerful performance. Partner with us to take your telecom projects to the next level with reliability you can trust.
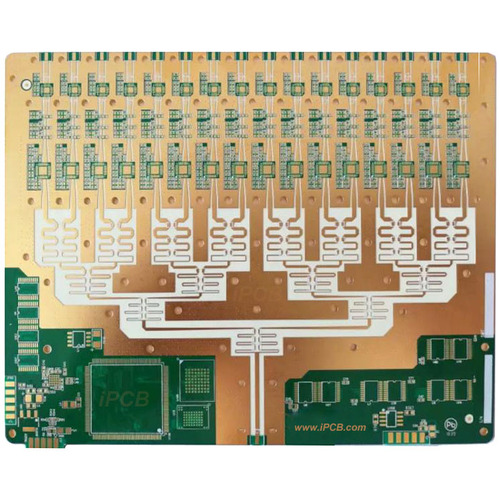
High Frequency PCB
Designed for applications requiring high signal integrity. The PCB is used in advanced communication systems like 5G networks and satellite communications.
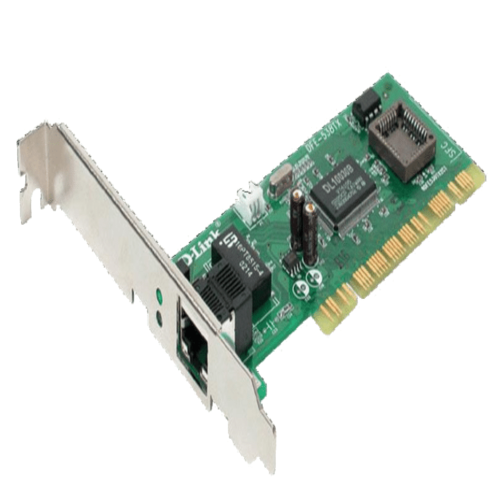
Network Interface Card (NIC)
Responsible for connecting computers or servers to a network, NICs require high-speed interfaces and robust design to handle large volumes of data traffic.
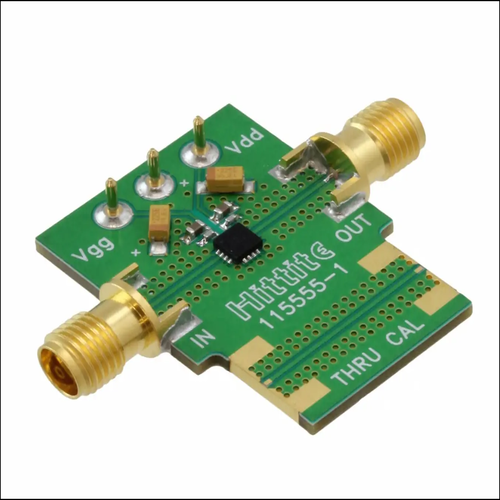
Signal Boosters PCB
This enhance signal strength and coverage in extensive telecommunication networks, ensuring reliable and extended connectivity.
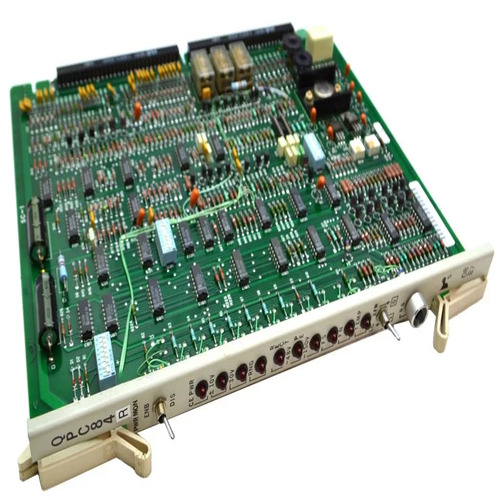
Server System
Involved in data storage and processing for telecom operations, requiring high reliability and data integrity, especially in server farms and cloud storage facilities.
Why Choose South-Electronic?
When you choose South-Electronic, you’re partnering with a specialist in high-quality telecom PCB.
Your project deserves the best, and our experienced team ensures you receive top-tier PCB at competitive prices. From start to finish, we are committed to providing exceptional service, making sure your satisfaction is our priority every step of the way.
-
Quality Assurance with Extended Warranty
Your telecom projects demand the best .
Every telecom PCB you receive from us is backed by our commitment to the highest quality, supported by a five-year warranty. If any issues arise, you can count on free repair. -
Lifetime After-Sales Support
Your peace of mind is our priority.
With our telecom PCB, you’re not just making a purchase—you’re securing lifetime after-sales support. We’re here to assist you at every stage, offering ongoing service and assistance. -
Flexible Ordering Quantity
Your needs drive our flexibility.
Whether you need just one piece or mass production, we offer flexible solutions tailored to your specific demands, without any order size limitations. -
Rapid Response and Delivery
Your deadlines matter to us.
With our efficient production processes and optimized logistics, we guarantee timely delivery, ensuring that your projects stay on schedule without compromising on quality. -
Transparent and Communicative Client Relations
Your experience with us is built on trust.
Our end-to-end supply chain visibility allows you to track your orders in real time. This transparency ensures smoother transactions and better communication.
Related Project We had Done
Customer Reviews
engineer
thank you, guys, the boards are really good, i am really happy to receive my boards, the components are perfect!
Operation Manager
South-Electronic is my first PCBA supplier in China. The service and quality are excellent, and the after-sales support is also very impressive. Good Job!
Common Questions
Most Popular Questions
South-Electronic provides a wide range of telecom PCB including Standard & Flex, High-Frequency & HDI, Power Management & Thermal, and Server & Data Systems PCB.
Reduced Signal Loss: made with materials that have lower dielectric losses, such as Rogers or Teflon. These materials help in reducing the loss of signal strength as the frequency of the signal increases.
Improved Signal Integrity: designed to manage better propagation of electromagnetic waves. By minimizing issues like signal skew and crosstalk, high-frequency PCBs ensure clearer and more reliable communication.
Higher Frequency Operation: can operate at frequencies in the GHz range. This ability makes them ideal for use in radio frequency (RF) applications, microwave transmission, and faster data transmission technologies.
Design Flexibility: can be shaped and bent to fit into unconventional and compact spaces. This flexibility is particularly beneficial in telecommunications devices like smartphones, smartwatches, and other wearable technology.
Reduced Space and Weight: typically require fewer interconnects and can replace multiple rigid boards and connectors, reducing the overall weight and space needed for the same functionality.
Enhanced Reliability: have fewer solder joints and mechanical connectors, which are often the weak points in electronic circuits. This reduction in potential failure points enhances the reliability of telecommunications device.
1. Material Selection
: Select materials with appropriate dielectric properties, thermal stability, and mechanical strength to meet the demands of high-frequency and high-speed applications, like Rogers, Teflon.
2. Manufacturing Controls
Strict Process Control: Ensure that the manufacturing process adheres to industry standards such as IPC.
3. Testing and Inspection
AOI: Use AOI systems during the manufacturing process to catch any potential defects in the traces or pads early.
Electrical Testing: Conduct comprehensive electrical tests, such as (ICT) or flying probe test.
Environmental and Stress Testing: Implement tests like thermal cycling, shock, and vibration testing.
4. Quality Assurance
Implement ISO Standards: Adhere to ISO 9001 standards for quality management system.
South-Electronic offers lifetime after-sales support and a comprehensive warranty for all our telecom PCB. Our support includes technical assistance, free repairs for any issues during the warranty period, and ongoing maintenance advice.
Yes, with eight production lines and advanced manufacturing technologies, South-Electronic is equipped to handle large-scale production without compromising on quality or efficiency. We can meet high volume demands while ensuring each PCB is manufactured to our exacting standards.
Send us a message
The more detailed you fill out, the faster we can move to the next step.
The Complete Guide for Telecom PCB
Content
Chapter 1

Introduction to Telecom PCB
Overview of PCB in Telecommunications
Printed circuit board (PCB) is the backbone of the telecommunications industry. These boards provide the essential circuitry required for all telecommunications equipment to function, from the simplest devices like routers and switches to complex infrastructure like data centers and satellite communications systems. Essentially, every piece of telecommunications equipment relies on PCB to operate efficiently and effectively.
PCB in telecommunications is uniquely designed to handle a wide array of functionalities including signal transmission, power distribution, and data processing, all of which are crucial for maintaining robust communication channels. They support various technologies such as optical transmission systems, microwave links, and cellular base stations, all integral to the network that forms the global communications infrastructure.
Importance of PCB in the Modern Telecom Industry
The growth of the modern telecommunications industry is driven by the ongoing need for faster data transfer, greater connectivity, and more reliable networks. This is where PCB really matter. As technology evolves, so does the complexity of the PCB that support it. For example, the advent of 5G technology requires the development of high-frequency PCB that can operate efficiently on the millimeter wave spectrum and manage increased data loads.
Moreover, with the rise of the Internet of Things (IoT) and the expansion of networks of smart devices, telecom PCB must also evolve to manage more connections, process larger data volumes, and ensure energy efficiency. The quality, design, and functionality of PCB directly impact the performance and reliability of telecom services, which in turn impacts everything from consumer satisfaction to the implementation of critical communications infrastructure in healthcare, defense, and more.
In an era of heightened environmental concern, the telecommunications industry is under pressure to reduce its carbon footprint. Advanced PCB can help address this by improving energy efficiency and reducing waste through smarter design and more durable materials.
Chapter 2
Types of Telecom PCB
The telecommunications industry relies on various types of PCB to meet the diverse needs of its technologies and applications. Each type of PCB has unique characteristics and advantages that can be tailored for specific functions within telecommunications systems. Below, we will explore the different types of telecommunications PCB and their main use cases.
Standard & Flex PCB
Description:
Rigid PCB is the most common type used in telecommunications equipment and have multiple layers to accommodate the circuitry required for complex operation.
Flexible (Flex) and Rigid-Flex PCB combine a rigid board with flexible interconnects. They are designed to flex to a certain degree, which is beneficial in telecommunications applications that require tight packaging or need to withstand vibration and other physical stresses.
Use Cases:
- Mobile Devices: Flex and Rigid-Flex PCB are ideal for smartphones, tablets, and other portable telecom devices where space is limited, and durability is crucial.
- Base Stations: Standard PCB are used in base stations for cellular networks, where they support various functions such as signal processing and power distribution.
High-Frequency & HDI PCB
Description:
High-Frequency PCB is designed to operate at high signal frequencies, typically in the gigahertz range, which is essential for high-speed data transmission technologies like 5G. HDI (High-Density Interconnect) PCB feature a higher density of components and interconnects than traditional PCB, allowing for more functionality in a smaller size, which enhances the performance of telecom devices.
Use Cases:
- 5G Networks: High-Frequency PCB is crucial in 5G applications where high-speed and reliable data transmission are required.
- Satellite Communications: Both High-Frequency and HDI PCBs are used in satellite modems and communication devices that need to operate effectively in the harsh conditions of space.
Power Management & Thermal PCB
Description:
The PCB is specially designed to handle power distribution and thermal management within telecom devices. Efficient power management is crucial to prevent overheating and to ensure that all components receive the correct voltage levels for optimal performance. Thermal PCB often incorporate materials and designs that help dissipate heat more efficiently.
Use Cases:
- Data Centers: Power Management PCB is used extensively in data centers to manage and distribute power across servers and storage units efficiently.
- High-Performance Routers and Switches: These devices use Thermal Management PCB to maintain optimal operating temperatures and prevent system failures.
Server & Data Systems PCB
Description:
ThePCB is tailored for server and data storage applications within the telecom industry. It’s designed to support large-scale, high-speed data processing and storage, with robust data integrity and uptime guarantees.
Use Cases:
- Cloud Storage Facilities: Server PCB is used in cloud storage systems where high data integrity, speed, and availability are crucial.
- Enterprise Servers: The systems rely on Data Systems PCB to process and store vast amounts of data that flow through corporate networks, ensuring smooth and efficient operations.

Chapter 3

Design Considerations for Telecom PCB
Designing PCB for telecommunications requires meticulous attention to several critical factors. The design choices made can significantly impact the performance, durability, and overall effectiveness of the PCB in its final application. Below, we explore the key design considerations for telecom PCB.
Key Design Factors
Material Selection:
- Conductivity and Signal Integrity: aterials used in telecom PCB must have excellent electrical properties to maintain signal integrity, especially at high frequencies typical of modern telecom applications. Materials like FR-4 are commonly used for standard applications, but more advanced materials such as PTFE (Teflon) are chosen for high-frequency PCB to reduce signal loss and dispersion.
- Thermal Management: The material must also have good thermal properties to dissipate heat effectively. For example, materials with higher thermal conductivity can prevent hot spots and reduce thermal stress on the components.
- Mechanical Durability: The physical properties of the material, such as flexibility and strength, are crucial, especially in PCB designed for mobile or outdoor telecom equipment where environmental stressors like temperature changes and physical impacts are prevalent.
Layout:
- Component Placement: Strategic placement of components can influence a PCB’s performance by minimizing signal path lengths and reducing potential interference. This is particularly important in the design of High-Density Interconnect (HDI) PCB where space is limited.
- Signal Integrity: Careful routing of traces, especially for high-frequency signals, is essential to avoid cross-talk and electromagnetic interference (EMI), which can degrade the performance of telecom systems.
- Power Integrity: Adequate distribution of power and ground planes ensures stable operation and reduces noise, which is crucial for maintaining the reliability of communication systems.
Thickness:
- Stack-up Configuration: The thickness of PCB and its layers can affect both its electrical and mechanical properties. Thicker PCB may offer better mechanical strength but can complicate the routing of high-frequency signals due to increased parasitic capacitance and inductance.
- Impedance Control: Controlling the impedance of PCB tracks is crucial for high-frequency telecom applications, and the thickness of the dielectric layer plays a key role in this. A well-designed stack-up can help maintain consistent impedance across the PCB.
Impact of Design on Performance and Durability
Performance:
- The choice of materials and layout directly impacts the PCB’s ability to perform under high-frequency conditions, which are common in telecom applications. Better materials and optimized layouts enhance signal integrity and reduce latency, crucial for high-speed data transmission.
- Efficient power distribution designs ensure that all components on the PCB operate within their optimal power range, thereby enhancing the performance and stability of the system.
Durability:
- Durability in telecom PCB is influenced by the ability to withstand physical and thermal stress. Materials that can endure harsh environmental conditions and layouts that optimize thermal management contribute to a longer lifespan of the PCB.
- The mechanical design, including thickness and material flexibility, also determines how well a PCB can withstand vibrations, impacts, and bending, which are particularly important in mobile or field-deployed telecom equipment.
Chapter 4
Manufacturing Processes for Telecom PCB
The manufacturing of printed circuit boards (PCB) for telecommunications is a complex and nuanced process that involves multiple precise steps. Each stage must be carefully controlled to ensure the highest quality and performance of the final PCB. Here is a step-by-step explanation of the PCB manufacturing process.
Step-by-Step Explanation of the PCB Manufacturing Process
Design and Pre-Production Engineering:
- Process: The manufacturing process begins with PCB design, which includes layout creation using CAD (Computer-Aided Design) software. The design is then converted into manufacturing data.
- Quality Control: Engineering team meticulously reviews the design for any potential issues that could affect manufacturing or performance, such as signal integrity, impedance mismatches, or thermal hotspots, DFM (Design for Manufacturability) checks to ensure that the PCB design adheres to manufacturing capabilities and standards.
Material Selection and Preparation:
- Process: Based on the specific requirements of the telecom PCB, materials are selected and prepared. This includes cutting the base material to size and preparing it for the layer stack-up.
- Quality Control : Sourcing materials from trusted suppliers and conduct material quality tests to ensure they meet our stringent standards for electrical and thermal performance.
Layer Stack-Up and Lamination:
- Process: Different layers of materials, including copper foil and prepreg (pre-impregnated with resin) layers, are stacked together. The stack is then subjected to heat and pressure in a lamination press to bond the layers into a single structure.
- Quality Control: During lamination, parameters like temperature, pressure, and time are closely monitored and controlled to avoid delamination and to ensure a uniform bond.
Drilling and Plating:
- Process: Post-lamination, holes are drilled to create vias that electrically connect different layers of the PCB. The inner walls of the drilled holes are then plated with copper to establish these connections.
- Quality Control : Using precision drilling equipment to maintain exact hole dimensions and placements. The plating process is tightly controlled to ensure a consistent and reliable layer of copper is deposited inside each via.
Pattern Imaging and Etching:
- Process: A photosensitive film is applied to the PCB, exposed to light through a mask that outlines the circuit patterns, and then developed to remove unexposed areas. The exposed copper surfaces are then etched away, leaving the desired copper traces.
- Quality Control : Imaging processes are calibrated for precision to ensure that the patterns align correctly across all layers. The etching process is monitored to achieve clean and accurate line widths and spacing.
Solder Mask Application:
- Process: A solder mask is applied over the copper traces, except where soldering components are required, to prevent accidental solder bridging during component placement.
- Quality Control :
- We apply solder masks uniformly and cure them under controlled conditions to ensure they adhere properly and protect the copper traces effectively.
- Process: A solder mask is applied over the copper traces, except where soldering components are required, to prevent accidental solder bridging during component placement.
Surface Finish Application:
- Process: Various surface finishes, such as HASL (Hot Air Solder Leveling), ENIG (Electroless Nickel Immersion Gold), or OSP (Organic Solderability Preservatives), are applied to prepare the exposed copper pads for soldering components.
- Quality Control : The choice of surface finish and its application are carefully controlled to ensure good solderability and long-term reliability of the connections.
Assembly and Soldering:
- Process: Components are placed on the PCB and soldered, either through reflow soldering or wave soldering, depending on component types and density.
- Quality Control : Assembly lines are equipped with automated optical inspection (AOI) and x-ray inspection systems to check for correct component placement, orientation, and soldering quality.
Testing and Inspection:
- Process: Finished PCB is tested for functionality and inspected for any defects. This can include electrical testing, such as in-circuit tests or flying probe tests, and visual inspections.
- Quality Control : We employ comprehensive testing procedures to ensure each PCB meets the specific functional requirements of telecommunications applications. Each batch is subjected to rigorous quality checks to ensure high reliability and performance.
Packaging and Shipping:
- Process: Once approved, PCB is carefully packaged to prevent damage during transport and shipped to customers.
- Quality Control : Packaging standards are designed to protect the delicate electronics during transit. We use anti-static packaging and moisture barrier bags to ensure PCB arrive in pristine condition.
South-Electronic’s commitment to quality at every step of the manufacturing process ensures that our telecom PCB meet the highest standards, suitable for the demanding environments of the telecommunications industry. This meticulous approach helps us maintain reliability, performance, and customer satisfaction.
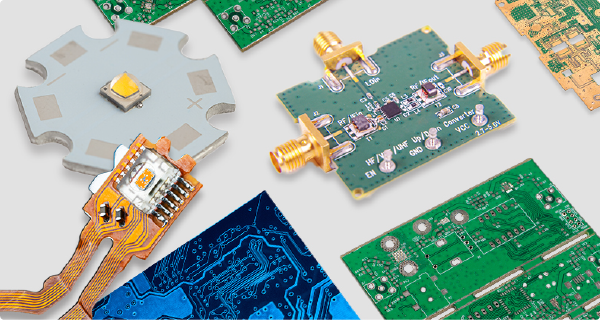
Chapter 5
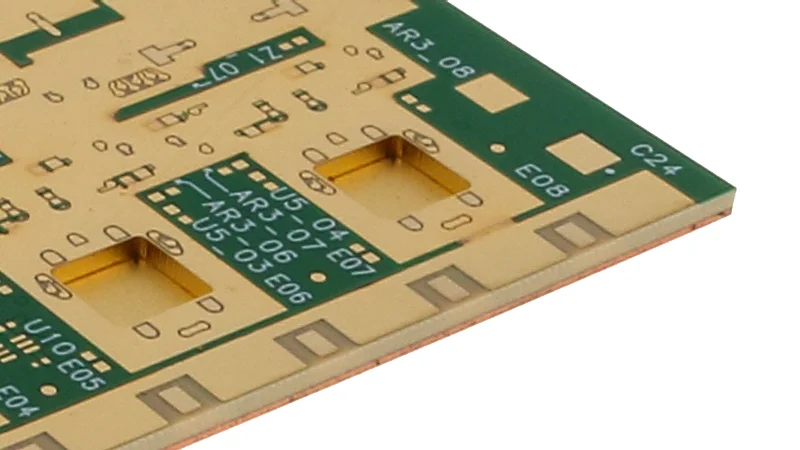
High Frequency and HDI PCB Description
Learn more about high frequency and HDI PCB
High-Frequency PCB: designed to operate at the microwave and millimeter-wave frequencies required by modern communication systems. The PCB is typically made from materials that have low dielectric constant and low loss tangent values to minimize signal attenuation and maintain signal integrity over high-frequency transmission. Common materials used include Rogers, Taconic, and PTFE (Teflon). High-frequency PCB require precise control over PCB features like trace widths and spacing, to ensure impedance matching and reduce signal loss.
HDI (High-Density Interconnect) PCB: is a significant advancement in PCB technology, enabling more compact and efficient designs by incorporating finer lines and spaces, smaller vias, and higher density of connection pads. HDI PCB typically employ advanced technologies such as micro vias, multi-layer structures, and high-performance thin materials. These features enable HDI PCB to support more components on a smaller board, thereby reducing size and weight while increasing the functionality of the device.
Their Role in 5G and Advanced Telecom Systems
Role in 5G Systems: 5G technology requires extremely high data rates and ultra-low latency, which can only be achieved through the use of high-frequency PCB. The PCB is critical to the development and deployment of 5G infrastructure, such as base stations, routers, and antennas that operate in the gigahertz frequency range. High-frequency PCB in 5G systems ensure efficient signal transmission with minimal losses, which is essential to maintaining the integrity and speed of communications.
HDI PCB plays a key role in 5G because they can accommodate the higher component density required for 5G’s enhanced broadband capabilities. Using HDI technology in 5G devices enables faster signal transmission speeds and improves signal integrity in complex circuit designs. This is especially important for 5G smartphones and other consumer electronics with limited space and high functionality requirements.
Role in Advanced Telecom Systems: In addition to 5G, high-frequency and HDI PCB are integral to various advanced telecom systems such as satellite communications, high-speed servers, and complex network systems. High-frequency PCB facilitate these applications by supporting the necessary high-speed data transfer and high signal frequencies with reduced interference and enhanced reliability.
For satellite communication systems, which operate at high frequencies and require robust environmental resistance, high-frequency PCB ensure reliable performance under extreme conditions. HDI PCB contribute by allowing more technology to be packed into tighter spaces, crucial for aerospace applications where weight and space are at a premium.
HDI PCB is also the foundation for the development of advanced routers and switches, which are essential for managing data flows in complex network infrastructures. These devices often require densely packed multi-layer HDI PCB to handle high-speed signals and implement multiple functions within limited space.
Overall, high-frequency and HDI PCB is essential to pushing the limits of modern telecommunications. As telecommunications systems continue to evolve with technologies such as 5G, these specialized PCB will continue to play a critical role in meeting the industry’s increasingly stringent performance standards.
Chapter 6
Flex and Rigid-Flex PCB in Telecommunications
Benefits of Using Flexible PCB in Telecom
Flexibility and Adaptability: Flexible PCB (FPCB) offers flexibility, making them particularly well suited for telecommunications devices that require complex assembly within tight spaces. Inherent flexibility enables these boards to adapt to unconventional shapes and configurations, seamlessly fitting into the design of the device rather than dictating it. This adaptability is critical for modern telecommunications devices such as smartphones and wearable technology, where space is at a premium and components must conform to a specific design aesthetic.
Reduced Weight and Size: One of the primary advantages of flexible PCB is their lightweight and thin profile, which significantly reduces the overall weight and size of the devices. This reduction is vital for portable and handheld telecom devices, where every fraction of an inch and ounce matters. Flex PCB uses lighter materials and eliminate the need for connectors and multiple rigid boards, contributing to a more compact device design.
Enhanced Reliability: Flexible PCB enhance reliability by reducing the number of interconnects and potential failure points within the device. Since they can be designed as a single continuous piece that accommodates all necessary circuitry, there are fewer solder joints and connectors, which are often the weak points in electronic devices. The reduced mechanical stress on solder joints and fewer rigid interfaces lead to lower rates of failure under conditions of thermal cycling and mechanical stress.
Improved Impedance Control: he construction of flexible PCB allows for consistent impedance control, which is critical in telecommunications for maintaining signal integrity, especially in high-frequency applications. The uniform electrical characteristics achieved through the continuous nature of flexible circuits help in managing signal loss and cross-talk, crucial for the quality and reliability of communication.
Applications and Advantages Over Traditional PCB
Applications in Telecommunications:
- Smartphones and Tablets: Flexible and rigid-flex PCB are widely used in mobile devices to connect various components such as cameras, buttons, and displays in a compact form factor.
- Wearable Technology: Devices such as smart watches and fitness trackers benefit from the lightweight and conformable capabilities of flexible PCB.
- Advanced Communication Equipment: In satellite communications equipment and base station antennas, flexible PCB can be used to create designs that meet aerodynamic and compact space requirements, thereby improving performance and durability.
Advantages Over Traditional PCB:
- Durability in Harsh Environments: Flexible PCB is more resistant to vibrations and thermal stress, making them ideal for use in field equipment and other telecommunications gear exposed to harsh environmental conditions.
- Cost-Effective Assembly: By reducing the complexity of the device assembly, flexible PCB can lower overall manufacturing costs. Fewer components and assembly steps are required, which simplifies the production process and reduces labor and error rates.
- Innovative Design Possibilities: The use of flexible PCB opens up new design possibilities that are not feasible with rigid boards. Designers can integrate components into unique configurations and develop products that stand out in the competitive telecom market.
In summary, flex and rigid-flex PCB brings several significant benefits and innovative possibilities to telecommunications, making them essential components in the development of both current and future telecom technologies. Their ability to combine form and function effectively makes them a preferred choice for many advanced applications in the industry.
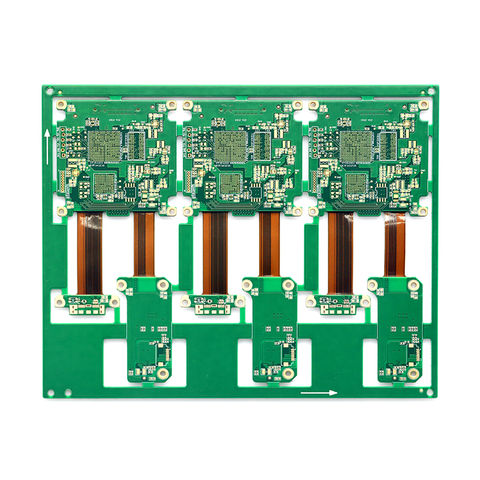
Chapter 7
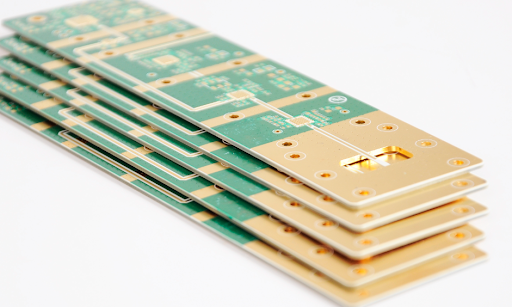
Power Management in Telecom PCB
Importance of Efficient Power Management
Effective power management in telecom PCB is critical and can significantly impact the overall performance, reliability, and sustainability of telecom systems. Efficient power management is critical for the following reasons:
System Reliability and Performance:
- Stability: Efficient power management ensures stable voltage and current levels across all components of a telecom system, which is vital for maintaining system reliability and avoiding unexpected shutdowns or failures.
- Performance: Proper power distribution directly influences the performance of high-speed telecom devices by reducing noise and voltage drop, which can affect data transmission speeds and signal integrity.
Energy Efficiency:
- Reduced Power Consumption: Effective power management techniques help in minimizing power waste through heat dissipation and inefficient power conversion, which is essential in large-scale operations like data centers where energy costs contribute significantly to operational expenses.
- Sustainability: As the telecom industry moves towards greener practices, improving energy efficiency through better power management in PCB design helps reduce the environmental impact.
Thermal Management:
- Heat Reduction: Efficient power management also plays a critical role in thermal management by reducing the amount of heat generated by electronic components. This is particularly important in densely packed devices where excessive heat can lead to component failure and reduce the lifespan of the device.
Overview of PCB Designs that Enhance Power Efficiency
Designing PCB for enhanced power efficiency involves several strategies aimed at optimizing the power distribution system and minimizing energy loss. Here are some of the key design approaches:
Power Integrity Simulation:
- Simulation Tools: Using advanced simulation tools to model and analyze the power distribution network (PDN) of a PCB allows designers to identify potential issues like impedance mismatches and voltage drops before the board is manufactured. This preemptive analysis helps in optimizing the PDN for minimal power loss and noise.
Layer Stack Design:
- Dedicated Power and Ground Layers: Designing PCB with dedicated power and ground layers can significantly improve power distribution. These layers help reduce resistance and inductance, which minimizes voltage drops across the PCB and improves overall power efficiency.
- Thick Copper Layers: Using thicker copper for power planes can also help in reducing resistance and improving current carrying capacity, which is beneficial for high-power applications.
Component Placement and Routing:
- Strategic Placement: Careful placement of components to minimize the length of power traces can reduce voltage drops and power losses. Placing power-hungry components closer to the power source can also help in achieving more efficient power distribution.
- Wide Power Traces: Designing wider power traces or using multiple parallel traces can decrease resistance and improve the distribution of power across the PCB.
Voltage Regulators and Converters:
- Efficient Regulators: Incorporating efficient voltage regulators and power converters directly on the PCB can help in stepping down voltages closer to the point of load, which reduces power loss in distribution and improves conversion efficiency.
- Switching Regulators: Switching regulators are more efficient than linear regulators, especially in applications where a significant voltage drop is required. They convert excess voltage into frequency rather than heat, thus enhancing overall energy efficiency.
Thermal Management Integration:
- Heat Sinks and Thermal Vias: Integrating heat sinks and using thermal vias to connect heat-generating components to ground or dedicated heat layers can help in dissipating heat more effectively, which indirectly improves power efficiency by reducing thermal stress on electrical components.
By integrating these power management strategies into the PCB design, telecom equipment manufacturers can enhance the efficiency, reliability, and sustainability of their products, meeting the demanding requirements of modern telecommunications systems. Efficient power management not only ensures optimal performance but also contributes to longer device lifespans and reduced operational costs.
Chapter 8
Testing and Quality Assurance in Telecom PCB Production
Quality Standards in PCB Production
Adherence to strict quality standards is critical to PCB production, especially for the telecommunications industry where reliability and performance are critical. These standards ensure that PCB meet the stringent requirements of the telecommunications industry, including signal integrity, power management, and environmental suitability. Key quality standards commonly adhered to by the industry include:
IPC Standards:
- IPC-A-600: Known as the Acceptability of Printed Boards, this standard sets the visual quality acceptability criteria for PCB, covering topics such as laminate conditions, hole and conductor plating, and assembly.
- IPC-6012: This standard provides the qualification and performance specifications for rigid PCB, including detailed criteria for testing electronic properties, structural integrity, and thermal reliability.
ISO 9001:
- This international standard specifies requirements for a quality management system (QMS) where an organization needs to demonstrate its ability to consistently provide products that meet customer and regulatory requirements. It emphasizes customer satisfaction and continual improvement.
UL Certification:
- UL (Underwriters Laboratories) certification ensures that PCB is manufactured in compliance with safety standards, particularly regarding their flammability and the materials used in production. This is crucial for ensuring the safety of telecom equipment.
Testing Methods to Ensure Reliability and Performance
To verify that PCB comply with these standards and meet the high expectations of telecom applications, a series of rigorous testing methods are employed:
Electrical Testing:
- In-Circuit Testing (ICT): This method involves checking for shorts, opens, resistance, capacitance, and other basic quantities to ensure each component is correctly installed and functional.
- Flying Probe Testing: Unlike ICT, flying probe tests do not require a test fixture and use moving probes to rapidly test PCB on small production runs. This method is flexible and can test a wide range of electrical parameters.
Thermal Stress Testing:
- Thermal Cycling: By exposing the PCB to extreme temperatures in rapid succession, this test checks the board’s ability to withstand thermal expansion and contraction, which could lead to failure in solder joints and other components.
- Thermal Shock Testing: This involves subjecting PCB to sudden and severe changes in temperature to assess their reliability under stressful environmental conditions.
Mechanical Testing:
- Vibration Testing: This test simulates the conditions that a PCB might encounter during shipping or in its operational environment, ensuring that it can withstand physical disturbances.
- Bend and Flex Testing: Particularly important for flex and rigid-flex PCB, these tests evaluate the mechanical endurance and robustness of the board under bending stresses.
Environmental Testing:
- Humidity Testing: Exposes the PCB to high humidity levels to check for potential failures caused by moisture absorption, which can lead to short circuits and corrosion.
- Salt Spray Test: This test is used to check corrosion resistance of metal surfaces and plating on PCB, which is crucial for devices exposed to harsh environments.
Functional Testing:
- After all individual components and connections are verified, functional tests are performed to check the PCB’s operation under conditions that mimic actual use. This ensures that the PCB not only meets manufacturing standards but also performs as expected in real-world applications.
By implementing these comprehensive testing and quality assurance measures, manufacturers can ensure that the PCB provide the high reliability and performance required in the telecommunications field. These processes not only help identify and correct problems before PCB is deployed, but also help extend the life and success of the products that use the PCB.

Chapter 9
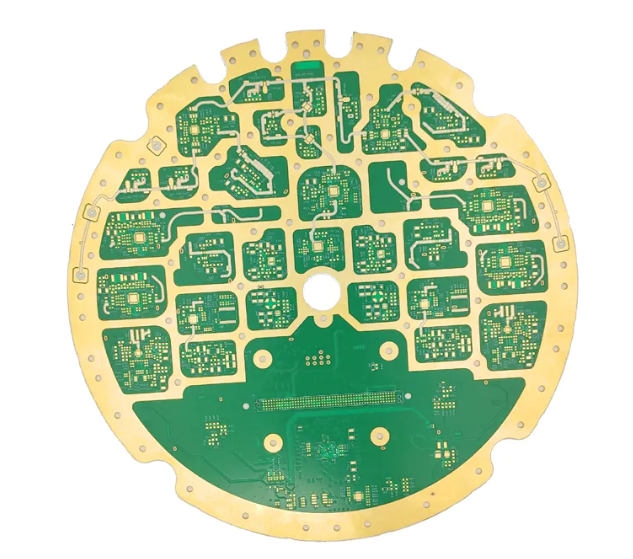
Challenges and Solutions in Telecom PCB Design
The design and manufacturing of PCB for telecommunications present unique challenges due to the complexity and high-performance requirements of modern telecom systems. Here, we explore common issues faced during the PCB design and manufacturing process.
Common Issues Faced During PCB Design and Manufacturing
Signal Integrity Problems:
- Issue: As telecommunications systems operate at higher frequencies, maintaining signal integrity becomes increasingly challenging. Issues such as crosstalk, signal loss, and electromagnetic interference (EMI) can severely degrade performance.
- Solution: Using advanced design techniques such as differential signaling, controlled impedance, and proper routing practices to mitigate these issues, also utilize high-quality materials with low dielectric constants and loss tangent values to enhance high-frequency signal integrity.
Thermal Management:
- Issue: High-density and high-power telecom applications generate significant heat, which can lead to overheating if not properly managed. This can affect the reliability and lifespan of the components.
- Solution: Design PCB with efficient heat dissipation methods, including thermal vias, heat sinks, and thermal pads. Additionally, PCB constructed with materials that have good thermal conductivity to help spread and dissipate heat more effectively.
Component Placement and Density:
- Issue: As devices miniaturize and demand more functionality, managing component placement and density becomes a complex task that can impact manufacturability and performance.
- Solution: Employing advanced software tools for layout and design to optimize component placement and routing. This ensures our designs maximize space while maintaining manufacturability and accessibility for testing and assembly.
Manufacturing Yield and Consistency:
- Issue: Ensuring high yields and consistency in manufacturing high-quality PCB is challenging, especially when dealing with complex designs and high volumes.
- Solution: Implemening strictquality control measures and continuous monitoring throughout the manufacturing process. This includes automated optical inspection (AOI) and x-ray inspection systems to detect and correct any defects early in the production cycle.
Environmental and Mechanical Durability:
- Issue: elecom equipment often operates in harsh environmental conditions, which can strain PCB mechanically and environmentally.
- Solution: Useing ruggedized design principles, such as using materials that are resistant to moisture, corrosion, and thermal variations. Design PCB to meet specific standards like IPC-6012 Class 3, which ensures high reliability under tough conditions.
Innovative Solutions Employed by South-Electronic
Use of HDI Technology:
- Innovation: key strategies we use to meet miniaturization needs and increase the functionality of telecom PCB. HDI boards feature finer spaces and lines, smaller vias, and higher density of connection pads than traditional PCB.
- Benefits: This allows for faster signal transmission, more functionality in a smaller area, and better electrical performance, which is critical for advanced telecom applications.
Embedded Passive and Active Components:
- Innovation: Integrating passive and active components directly into the PCB substrate, which is another innovative solution to improve performance and reduce PCB size.
- Benefits: This integration helps reduce signal paths and improves reliability by minimizing the number of solder joints and external connections, which are potential points of failure.
By addressing these challenges with innovative solutions, South-Electronic not only meets but exceeds the stringent demands of the telecom industry, ensuring that our PCB deliver the highest levels of performance and reliability.
Chapter 10
Future Trends and Innovations in Telecom PCB
The telecommunications industry continues to evolve, driven by rapid technological advancements and a growing demand for better connectivity and performance. Emerging technologies such as the Internet of Things (IoT), artificial intelligence (AI), and next-generation wireless networks are reshaping the telecommunications PCB design landscape. Below, we explore how these technologies are impacting PCB design and predict future developments in this area.
Emerging Technologies Affecting PCB Design
Internet of Things (IoT):
- Impact: IoT devices require PCB to be small, efficient, and capable of operating with minimal power consumption while handling multiple sensor inputs and connectivity options. This demand pushes the development of multifunctional, highly integrated PCB.
- PCB Design Innovations: IoT is accelerating the adoption of flex and rigid-flex PCB that can fit into unconventional spaces and shapes required by various IoT devices. Additionally, the integration of energy-harvesting components onto PCB is becoming more prevalent to extend the battery life of IoT devices.
Artificial Intelligence (AI):
- Impact: AI applications in telecommunications, such as predictive maintenance, network optimization, and intelligent routing, require processing vast amounts of data in real-time. This necessitates PCB that can support high-speed data processing hardware and high-density interconnects.
- PCB Design Innovations: To meet these needs, there is an increasing use of HDI PCB with enhanced thermal management capabilities. AI also drives the development of PCB that can integrate more powerful processors and GPU chips efficiently.
5G and Beyond:
- Impact: The rollout of 5G technology and research into 6G and beyond requires PCB that can handle higher frequencies and higher data rates. This requires materials and designs that minimize high-frequency signal loss and interference.
- PCB Design Innovations: Using advanced materials such as low-loss laminates and employing improved signal integrity design techniques are critical. In addition, 5G drives miniaturization while increasing the need for effective thermal solutions.
Predictions for Future Developments in Telecom PCB
Advanced Material Use:
- Prediction: Continued development and adoption of new materials that offer better high-frequency performance, thermal management, and environmental resistance. Materials such as liquid crystal polymer (LCP) are expected to become more common for their excellent electrical properties and reliability.
Greater Integration:
- Prediction: The trend towards more integrated systems will likely continue, with an increase in the use of System-on-Chip (SoC) and System-in-Package (SiP) solutions. These integrations can reduce the overall footprint of telecom PCBs while boosting their functionality and efficiency.
Sustainability Focus:
- Prediction: As environmental concerns become more pressing, there will be a stronger emphasis on designing PCB that are not only efficient but also made from sustainable or recyclable materials. Additionally, energy-efficient designs that consume less power and reduce electronic waste will be prioritized.
Automation and AI in PCB Manufacturing:
- Prediction: The use of AI and machine learning in the manufacturing process will become more prevalent. These technologies can help optimize manufacturing processes, reduce defects, and improve the overall quality and yield of telecom PCB.
Smart PCB:
- Prediction: Development of ‘smart’ PCB that incorporate built-in sensors to monitor performance and environmental conditions in real-time, providing data for predictive maintenance and system optimizations.
These trends and innovations reflect a dynamic shift in the telecom industry towards more intelligent, efficient, and integrated PCB solutions. As new technologies continue to emerge, the role of advanced PCB design and manufacturing will become even more critical in delivering the next generation of telecommunications infrastructure.
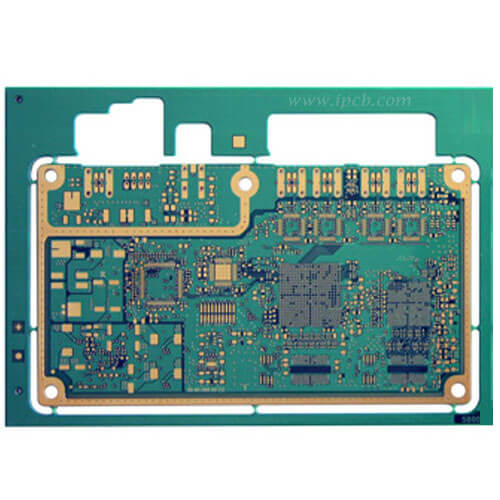
Get in touch
Where Are We?
Industrial Park, No. 438 Donghuan Road, No. 438, Shajing Donghuan Road, Bao'an District, Shenzhen, Guangdong, China
Floor 4, Zhihui Creative Building, No.2005 Xihuan Road, Shajing, Baoan District, Shenzhen, China
ROOM A1-13,FLOOR 3,YEE LIM INDUSTRIAL CENTRE 2-28 KWAI LOK STREET, KWAI CHUNG HK
service@southelectronicpcb.com
Phone : +86 400 878 3488
Send us a message
The more detailed you fill out, the faster we can move to the next step.
