Turnkey PCB Assembly
South-Electronic
You can count on South-Electronic for unmatched quality, dependability, and exceptional value. We handle everything—from design and procurement to final assembly and testing—so you can focus on what matters most. Your projects will benefit from precision, durability, and compliance with the highest industry standards, ensuring peace of mind every step of the way.
Your Trusted Partner in Turnkey PCB Assembly
Our assemblies are designed to deliver top performance, suitable for a wide range of applications. We offer flexible solutions including single-layer, double-layer, and multi-layer boards, all customized to meet your specific electronic needs. Whether improving efficiency in consumer electronics or ensuring reliable operations in industrial controls, our Turnkey PCB Assembly services are your best bet for ensuring project success with speed and accuracy.
Why Choose South-Electronic?
-
Flexibility in Ordering
You get exactly what you need, no matter the order size.
Whether it’s a single piece or thousands, we’re ready to fulfill your order with the same dedication to quality and precision -
Experienced Team
You gain from our decade of industry expertise..
Leverage over a decade of industry expertise with a team that's as experienced as they are dedicated. We're here to help you navigate any PCB challenges with ease. -
Comprehensive Service
You get complete satisfaction with our wide range of equipment..
We have a wide range of PCB processing capabilities. From design to delivery, we have the equipment and processes to make sure your order is done right. -
Fast Delivery
You stay on schedule with our fast turnaround times..
Our streamlined production ensures fast turnaround times, so you get your products when you need them, without delays. -
Guaranteed Satisfaction
You’ll appreciate the confidence that comes with working with an ISO9001 certified company..
We prioritize clear, transparent communication and hold ourselves to the highest standards, ensuring that your 8-layer PCBs not only meet but exceed your expectations for performance, durability, and precision.
Related Project We had Done
Customer Reviews
engineer
thank you, guys, the boards are really good, i am really happy to receive my boards, the components are perfect!
Operation Manager
South-Electronic is my first PCBA supplier in China. The service and quality are excellent, and the after-sales support is also very impressive. Good Job!
Common Questions
Most Popular Questions
South-Electronic specializes in assembling various types of PCBs, including rigid, flexible, and rigid-flex PCBs, serving industries from consumer electronics to automotive.
They implement stringent quality control measures, including automated optical inspection (AOI), in-circuit testing (ICT), and adherence to industry standards to ensure high-quality assembly.
Yes, they support both small and large batch orders, providing flexibility to cater to prototyping needs as well as large-scale production.
They are ISO9001 certified, ensuring compliance with international quality management standards, and possibly hold additional certifications relevant to specific industries.
Yes, they often welcome visits from clients to tour their facilities, provided you schedule in advance to ensure accommodations for your visit.
Send us a message
The more detailed you fill out, the faster we can move to the next step.
The Complete Guide For Turnkey PCB Assembly
Contents
Chapter 1
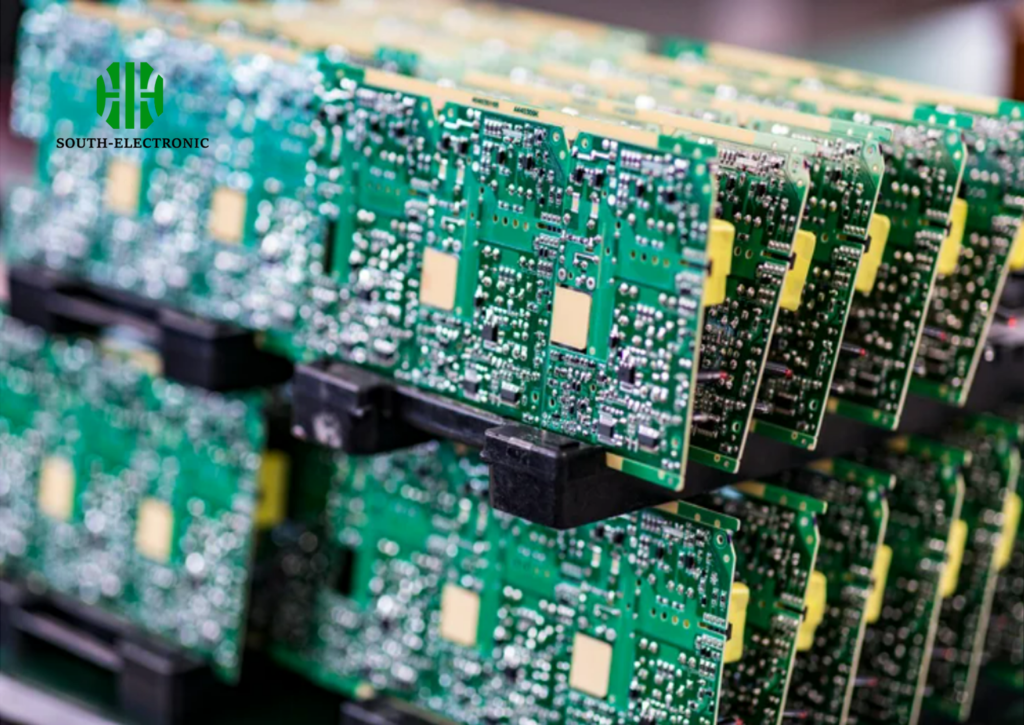
Introduction to Turnkey PCB Assembly
In this section, we will talk about turnkey PCB assembly, why it matters, why it’s better than the old way of doing things, and give you a quick overview of the whole process.
1. What is Turnkey PCB Assembly?
Turnkey PCB assembly is a complete end-to-end service where the provider handles everything from the design and sourcing of components to the assembly, testing, and delivery of the finished product. Turnkey means you get a finished and tested product without having to deal with multiple suppliers or a bunch of logistical headaches.
2.Why Turnkey PCB Assembly Matters
Turnkey PCB assembly is a game changer for companies that want to streamline their production process. Here’s why it’s so important:
- Efficiency and Speed: By consolidating everything under one roof, you can get your products to market faster.
- Cost Savings: By controlling every aspect of the process, from sourcing materials to final assembly, you can save money by taking advantage of economies of scale and reducing logistical expenses.
- Quality Control: With complete control over the entire process, turnkey providers can implement strict quality control measures to make sure every product meets industry standards.
3.Why Turnkey Services Are Better Than the Old Way
Here are some of the advantages of using turnkey PCB assembly over the old way of doing things:
Simplified Management: You have one point of contact, which makes things a lot easier than dealing with multiple suppliers and contractors.
Reduced Risk: Because the provider takes care of everything, there’s less chance for errors or miscommunication between different parties, which can happen in a traditional setup.
Better Focus: By outsourcing the assembly process, you can focus on what you’re good at, like product design, marketing, and strategy.
Chapter 2
The PCB Assembly Process Explained
In this section, we will take a closer look at the detailed steps involved in the PCB assembly process, the differences between full turnkey and partial turnkey services, and how these processes integrate with design and manufacturing.
1.Detailed Steps of PCB Assembly
The PCB assembly process consists of several steps that ensure electronic components are accurately placed and soldered onto printed circuit boards. Here is a breakdown of the process:
Design and Preparation:
- Schematic Capture: The first step is to create a schematic diagram that defines the electrical connections and components.
- PCB Layout Design: Using CAD software, designers convert the schematic into a precise board layout, determining the placement of components and routing of traces.
Component Sourcing:
- Bill of Materials (BOM) Generation: A comprehensive list of all components is created, specifying part numbers, quantities, and preferred suppliers.
- Procurement: Components are purchased from approved vendors, ensuring quality and compatibility with the PCB design.
PCB Fabrication:
- Substrate Preparation: The base material, typically made from fiberglass or similar composites, is prepared.
- Layering and Etching: Multiple layers of copper are etched onto the substrate to create the circuit traces.
- Drilling and Plating: Holes or vias are drilled and plated for component leads and inter-layer connections.
Solder Paste Application:
- Using a stencil, solder paste is precisely applied to solder pads on the PCB to facilitate component attachment.
Component Placement:
- Surface Mount Technology (SMT): Automated pick-and-place machines position surface-mounted components onto the board.
- Through-Hole Technology (THT): Components with leads are manually or automatically inserted into drilled holes.
Reflow Soldering:
- The PCB is heated in a reflow oven, melting the solder paste to secure surface-mounted components.
Inspection and Quality Control:
- Automated Optical Inspection (AOI): High-resolution cameras check for misalignment, excess solder, and component defects.
- In-Circuit Testing (ICT): Electrical tests ensure circuit integrity and functionality.
Final Assembly and Testing:
- The board undergoes additional testing, such as functional testing, to verify performance under real-life conditions.
Packaging and Shipping:
- Completed PCBs are securely packaged and prepared for shipment to the customer.
2.Differences Between Full Turnkey and Partial Turnkey
Full Turnkey: This encompasses the entire PCB assembly process, where the provider handles everything from design and component sourcing to manufacturing and testing.
Partial Turnkey: This allows customers to choose which parts of the process they want the provider to handle, such as only assembly or testing, while maintaining control over other aspects like component sourcing or design.
3.Integration with Design and Manufacturing
The PCB assembly process is closely tied to design and manufacturing, creating a seamless workflow:
Design Integration: A collaborative approach between designers and assembly teams ensures that PCB layouts are optimized for manufacturing (DFM), reducing potential issues during production.
Manufacturing Alignment: Effective communication between design, sourcing, and assembly phases ensures that manufacturing processes are efficient, cost-effective, and adaptable to design changes.
By understanding these detailed steps and integration strategies, customers can gain a better understanding of the complexities of PCB assembly and the value that turnkey services provide in simplifying and enhancing product development.
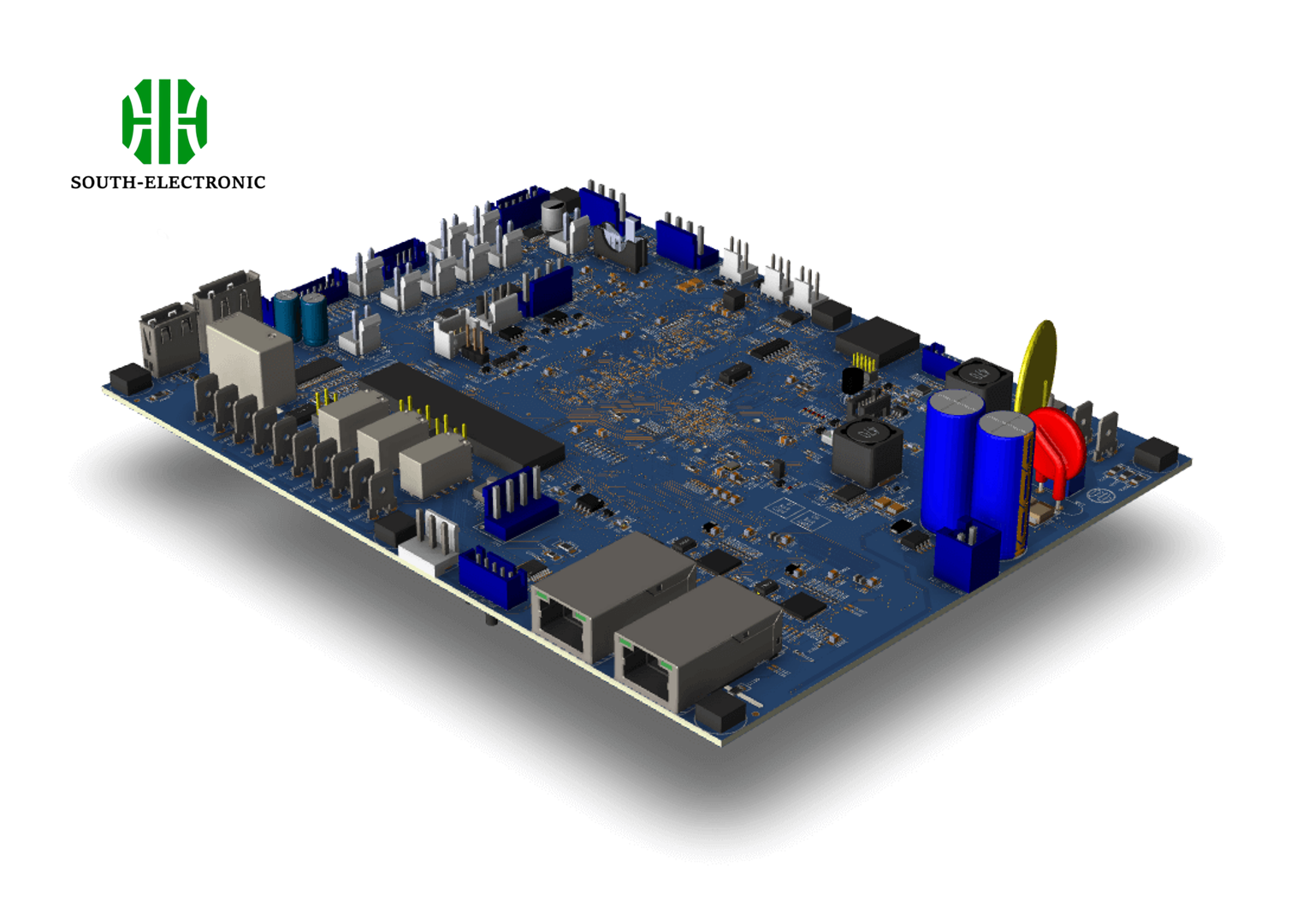
Chapter 3
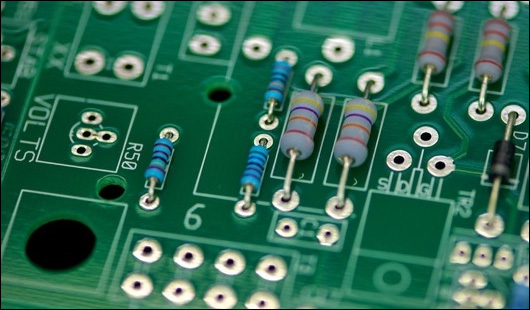
Choosing the Right Turnkey Provider
Choosing the right turnkey provider is critical to the success of your PCB assembly projects. In this section, we will discuss the key factors to consider, important questions to ask potential partners, and provide an overview of some of the top industry players.
1.Key Factors to Consider When Selecting a Provider
There are several important factors to consider when choosing a turnkey provider to ensure your project requirements are met:
Experience and Expertise:
Look for providers with extensive experience in the industry and a proven track record of handling projects similar to yours.
Assess their technical expertise in handling complex designs, high-density boards, and different types of PCBs (rigid, flexible, rigid-flex).
Quality Assurance:
Ensure the provider has rigorous quality control processes and certifications such as ISO9001, IPC standards, or other relevant industry compliances.
Check for robust testing methods like AOI, ICT, and functional testing to ensure product reliability.
Supply Chain Management:
Evaluate their component sourcing capabilities and relationships with reputable suppliers to ensure availability and quality of parts.
Consider their inventory management solutions to avoid delays and ensure timely delivery.
Customization and Flexibility:
The provider should offer customization options to accommodate specific needs regarding design modifications, component selections, and production volumes.
Assess their ability to scale production to meet growing demands or accommodate prototyping and small-batch requirements.
Cost-effectiveness:
Compare cost structures across providers and ensure transparency regarding pricing components, including any hidden fees associated with the turnkey process.
Consider the overall value offered, balancing cost with quality and service comprehensiveness.
Technology and Infrastructure:
Ensure the provider uses advanced equipment and up-to-date technology to deliver precise assembly and handle contemporary design complexities.
Assess their production capacity and facilities for handling projects at varying scales.
Chapter 4
Design Considerations for Turnkey PCB Assembly
Designing PCBs for turnkey assembly is all about efficiency. Efficient design ensures that boards can be manufactured quickly, cost-effectively, and with minimal errors. In this section, we’ll talk about the importance of Design for Manufacturing (DFM), give you tips for optimizing your PCB designs for assembly, and highlight some common design pitfalls to avoid.
1.The Importance of Design for Manufacturing (DFM)
Design for Manufacturing (DFM) is a strategy in PCB design that focuses on simplifying the manufacturing process and improving product quality. DFM is important for a few reasons:
- Cost Reduction: By minimizing complexity and potential errors, DFM helps reduce manufacturing costs. It eliminates unnecessary features that add to production expense without enhancing functionality.
- Efficiency Improvement: Streamlined designs with DFM considerations are easier to manufacture, which speeds up production times and reduces resource consumption.
- Enhanced Quality: DFM emphasizes simplifying interfaces, components, and workflows, leading to fewer chances of defects during assembly and higher reliability.
- Risk Mitigation: By anticipating potential manufacturing challenges during the design phase, designers can proactively address issues that might lead to costly redesigns or delays.
2. Tips for Designing PCBs Optimized for Assembly
To ensure your PCB designs are optimized for assembly, consider the following tips:
Component Placement:
- Place components on one side of the PCB to reduce assembly complexity.
- Group components by type to make assembly processes like stencil printing and pick-and-place more efficient.
Pad and Hole Sizes:
- Use standard pad sizes and shapes to ensure compatibility with automated assembly machinery.
- Make sure vias and through-holes are correctly sized and plated to facilitate reliable connections.
Trace and Spacing Considerations:
- Leave enough space between traces to prevent short circuits.
- Follow industry standards for trace width and spacing in terms of current capacity and signal integrity.
Orientations and Silkscreen:
- Standardize component orientation to simplify inspection and soldering.
- Use clear and concise silkscreen labeling for component identification and orientation.
Thermal Management:
- Consider thermal reliefs and heat dissipation requirements to prevent overheating.
- Leave enough space for components that generate heat to achieve better thermal performance.
Panelization:
- Design boards with panelization in mind, optimizing for assembly lines that may handle multiple boards simultaneously.
3.Common Design Pitfalls to Avoid
When designing PCBs for turnkey assembly, be aware of common pitfalls that can complicate the process:
- Ignoring DFM Guidelines: Not following standard manufacturing guidelines leads to higher costs and longer lead times due to potential redesigns.
- Complex Layer Stacks: Avoid overly complex layer stacks that increase fabrication difficulty and error likelihood.
- Inadequate Testing Considerations: Not including test points and adequate grounding can hinder testing, leading to costly error discovery post-production.
- Skipping Design Reviews: Not doing thorough design reviews and simulations can result in undetected errors that propagate to the assembly stage.
- Incorrect Parts Library: Using incorrect component libraries or outdated parts may lead to mismatches and procurement challenges.
By keeping these design considerations in mind, you can create PCBs that are easier and more cost-effective to assemble, reducing time-to-market and improving overall product quality.
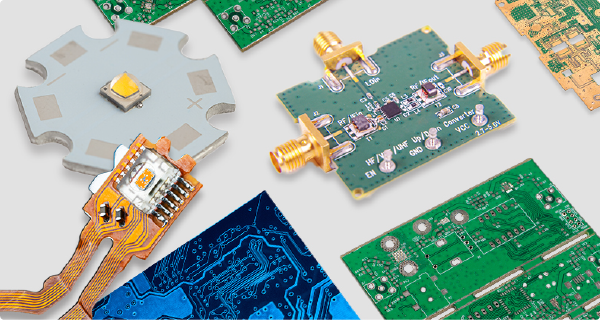
Chapter 5
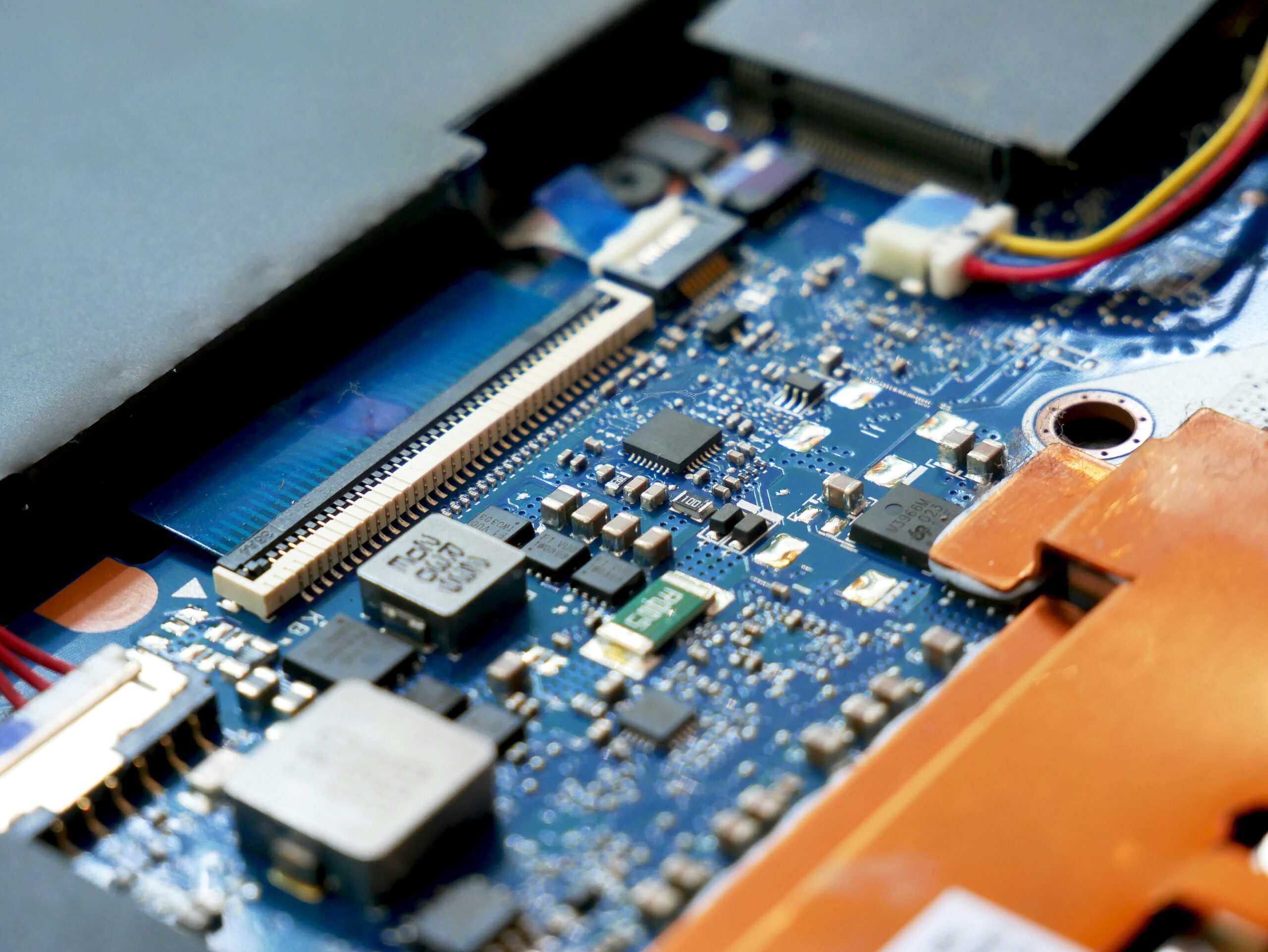
Component Sourcing and Management
Getting the right components and managing them well is crucial to the success of turnkey PCB assembly. In this section, we’ll look at how turnkey providers get components, why it’s important to have good relationships with suppliers, and how to manage your component inventory.
1.How Turnkey Providers Get Components
Turnkey providers have a lot of ways to get components quickly and at a good price. Here are some of the things they do:
- Supplier Networks: Turnkey providers have a lot of suppliers they can buy from. They know who to trust and where to get the best parts.
- Global Sourcing: Turnkey providers can buy parts from all over the world. They can get the best prices and find parts that are hard to get in one place.
- Automated Buying: Turnkey providers use software to keep track of what parts they have, what they need, and how much they cost. They can order parts automatically and make sure they get them on time.
- Planning: Turnkey providers work with their customers to know what parts they need and when. They make sure they have the parts they need when they need them.
- Alternatives: Sometimes, the parts you want aren’t available. Turnkey providers can find other parts that work just as well.
2.Why Good Supplier Relationships Matter
Turnkey providers need good relationships with their suppliers. Here’s why:
- Consistency: When you have a good relationship with your suppliers, you know you’re going to get good parts. You don’t have to worry about getting fake or broken parts.
- Priority: If you have a good relationship with your suppliers, they’ll make sure you get the parts you need, even if they’re hard to get.
- Savings: When you’ve been working with a supplier for a long time, you can get better prices and better terms. You can pass those savings on to your customers.
- Help and Advice: Suppliers can help you with technical problems and work with you to make your products better.
- Faster Solutions: If you have a problem with a supplier, it’s easier to fix it if you have a good relationship with them.
3.How to Manage Your Inventory
You need to manage your inventory well if you want to make your products on time. Here’s how:
- Just-In-Time (JIT) Inventory: You don’t want to have too many parts sitting around. You want to have just enough to make your products. That way, you don’t waste money on parts you don’t need and you don’t have to store them.
- Inventory Tracking: You need to know how many parts you have, how many you need, and when you need to order more. Good software can help you keep track of your inventory and make sure you always have enough parts.
- Risk Management: Sometimes, you can’t get the parts you need. That’s why you need to have extra parts on hand. That way, you won’t have to stop making your products if you can’t get the parts you need.
- Lifecycle Management: You need to know how long your parts are going to be available. That way, you can plan ahead and make sure you have enough parts to make your products.
Supplier Audits: You need to make sure your suppliers are doing a good job. You need to check on them regularly and make sure they’re doing what they’re supposed to be doing.
By getting the right parts and managing them well, turnkey providers can make their products on time and make sure they’re good quality. That’s how they keep their customers happy and make money.
Chapter 6
Ensuring Quality in Turnkey PCB Assembly
When it comes to turnkey PCB assembly, achieving high quality is crucial to ensure that electronic products are functional, reliable, and long-lasting. In this section, we will discuss the quality assurance techniques used during assembly, the importance of certifications and compliance standards, and the role of testing and inspections in the process.
1.Quality Assurance Techniques Used in Assembly
Quality assurance in PCB assembly involves various techniques to ensure that each product meets the specified standards and customer expectations:
- Standard Operating Procedures (SOPs): Establishing detailed procedures for each stage of the assembly process ensures consistency and minimizes errors.
- Automated Optical Inspection (AOI): This technology uses cameras to automatically inspect PCBs for issues such as misaligned components, solder paste application inconsistencies, and missing parts.
- Statistical Process Control (SPC): Monitoring assembly processes with real-time data helps identify deviations and maintain consistent quality during production.
- Process Control and Documentation: Rigorous process documentation and control checks help track compliance with design and manufacturing standards.
- Feedback Loops: Continuous feedback from testing and customer reviews is used to refine assembly techniques and improve quality assurance processes over time.
2.Importance of Certifications and Compliance Standards
Adhering to industry-standard certifications and compliance standards is crucial to guarantee the quality and safety of PCBs:
- ISO 9001 Certification: Recognized worldwide, ISO 9001 sets the standard for quality management systems, helping providers ensure consistency and improve customer satisfaction.
- IPC Standards: The Institute for Printed Circuits (IPC) provides standards for PCB manufacturing and assembly, ensuring that components meet performance and reliability requirements.
- RoHS Compliance: Ensures that products meet environmental standards by restricting the use of specific hazardous materials found in electronic products.
- UL Certification: Ensures the safety and electrical integrity of components and processes, indicating conformity to industry safety standards.
- CE Marking: Required for products sold within the European Economic Area, indicating that a product meets EU safety, health, and environmental requirements.
3.Role of Testing and Inspections
Testing and inspections play a critical role in ensuring the quality of turnkey PCB assembly:
- In-Circuit Testing (ICT): Checks electrical performance and functionality by probing individual circuits on the board to ensure there are no shorts or opens.
- Functional Testing: Simulates the operating environment to ensure that the PCB performs as expected under real-world conditions.
- X-ray Inspection: Non-destructive testing method that allows for the inspection of solder joints and internal traces, particularly useful for detecting faults with complex assemblies.
- Thermal Cycling and Environmental Stress Testing: Examines how PCBs perform under varying temperature and environmental conditions, ensuring reliability over the product’s lifecycle.
- Final Quality Control Inspections: Thorough visual inspections that check for assembly defects such as incorrect component placement or finished surface inconsistencies.
By integrating these quality assurance techniques, maintaining compliance with industry standards, and employing comprehensive testing and inspections, turnkey providers can ensure the highest quality standards in PCB assembly, fostering customer trust and long-term success.
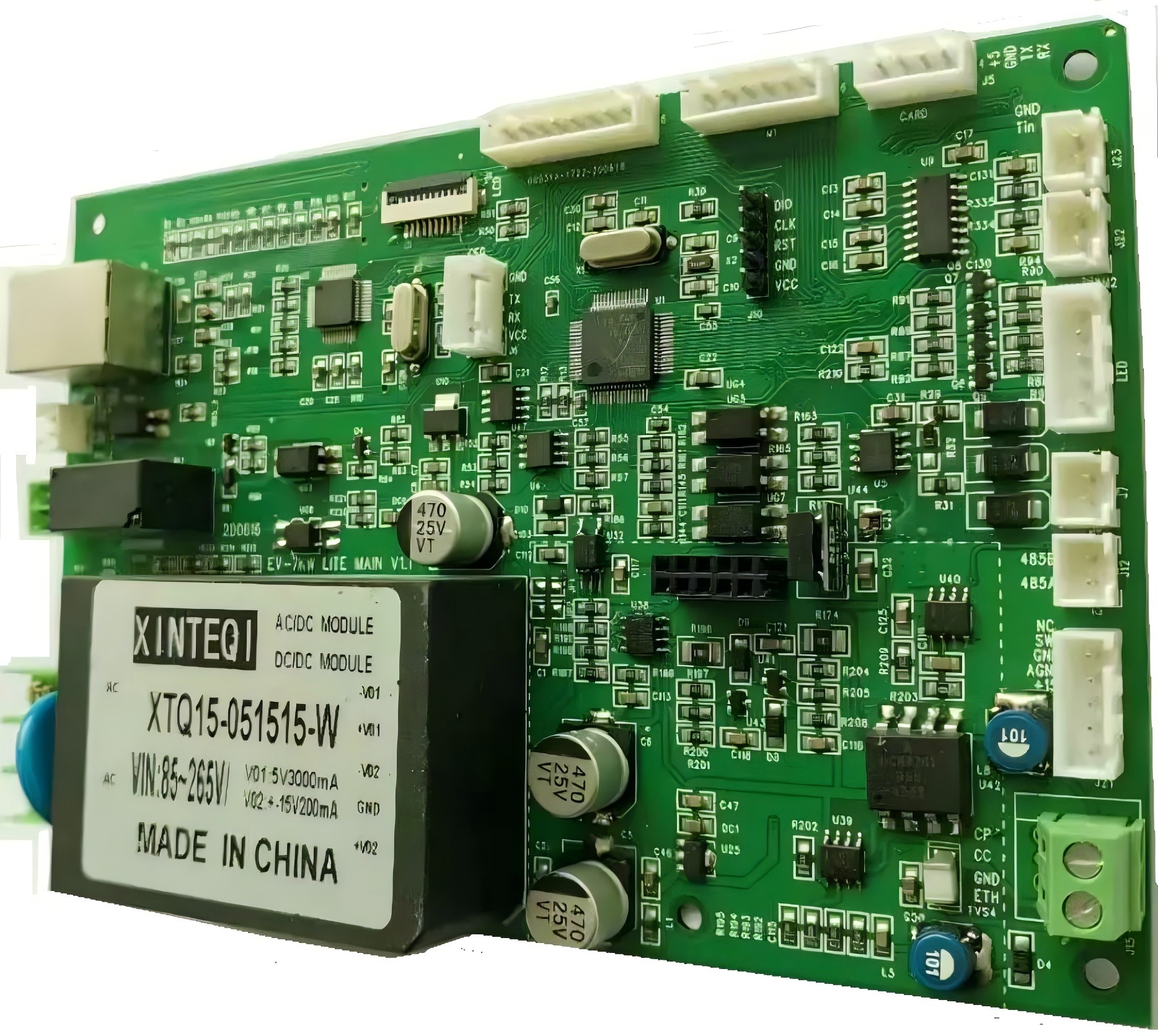
Chapter 7
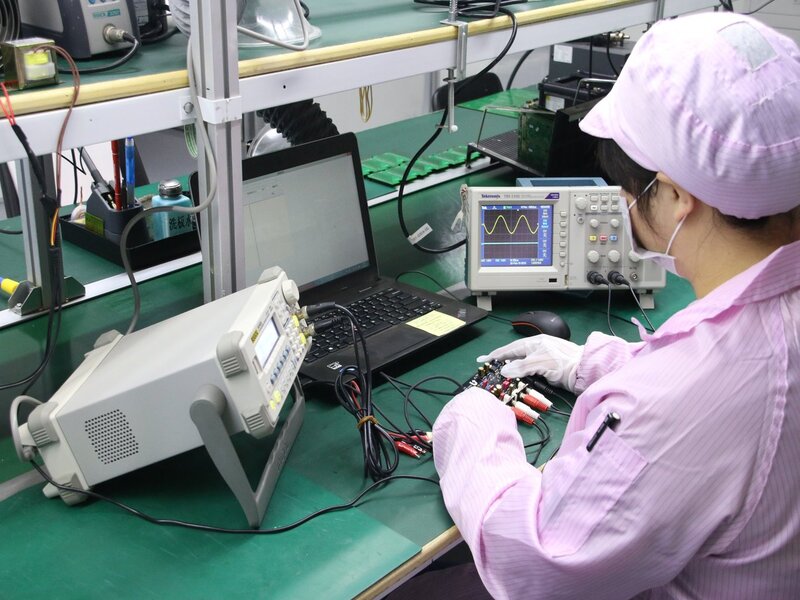
Cost Considerations and Budgeting
Understanding the cost dynamics in turnkey PCB assembly is essential for effective budgeting and cost management. This section delves into the key cost factors involved in turnkey assembly, strategies for cost reduction, and a comparison between turnkey and non-turnkey costs.
1.Understanding Cost Factors in Turnkey Assembly
Several factors contribute to the overall cost of turnkey PCB assembly:
Component Costs: A significant portion of the budget goes to sourcing components. Prices can vary based on the component type, quantity needed, market fluctuations, and supplier relationships.
Manufacturing Complexity: More complex designs with higher layer counts, specialized technologies, or dense components can increase manufacturing costs due to the need for advanced techniques and longer production times.
Labor and Overhead: Labor costs can vary based on geographical location, the level of expertise required, and the efficiency of manual versus automated processes. Overheads like energy, facility maintenance, and administrative expenses also contribute.
Quality Assurance and Testing: Implementing extensive testing and quality assurance processes is cost-intensive but necessary to ensure product reliability and minimize future failures.
Logistics and Shipping: Shipping costs for components and finished products, especially if sourcing globally, can be substantial and affect the overall budget.
2.Strategies for Cost Reduction
To manage and reduce costs in turnkey PCB assembly, consider the following strategies:
Design for Cost Efficiency: Implement Design for Manufacturability (DFM) principles early to simplify designs, reduce unnecessary features, and choose cost-effective components and production techniques.
Optimize Component Selection: Use alternative components that offer similar performance at lower costs. Bulk purchasing and negotiating with suppliers can also result in cost savings.
Automate Where Possible: Leveraging automation in assembly and testing can reduce labor costs and improve efficiency.
Consolidate Suppliers: Working with fewer suppliers for components can leverage better pricing, reduce shipping costs, and streamline logistics.
Lifecycle Cost Analysis: Consider total lifecycle costs, including potential redesigns and maintenance, to make cost-effective choices initially that save money over the long term.
3.Comparison of Turnkey vs. Non-turnkey Costs
Understanding the cost implications of selecting a turnkey provider versus managing assembly in-house (non-turnkey) is crucial:
Turnkey Costs:
- Pros: Turnkey solutions often bundle component sourcing, manufacturing, assembly, and testing into a single service, potentially reducing the overall costs via economies of scale, streamlined processes, and expert management. Additionally, they minimize the need for a large in-house team and complex logistics management.
- Cons: Upfront costs may appear higher compared to single-service providers, but they often offer better value through efficiency and reduced errors.
Non-turnkey Costs:
- Pros: Greater control over individual processes and potentially lower upfront costs if some stages are insourced or directly managed.
- Cons: Separate management of component sourcing, assembly, and testing can lead to higher cumulative costs due to inefficiencies, increased overheads, and potential for higher error rates without specialized expertise.
In conclusion, while initial turnkey costs may seem higher, the consolidated management, reduced complexity, and time-saving benefits often result in lower overall expenses and better value for most projects.
Chapter 8
Customization and Flexibility
Customization and flexibility in turnkey PCB assembly are critical for meeting diverse client needs and adapting to specific project requirements. This section explores the options available for custom PCB assembly, how services can be tailored to specific needs, and presents case studies highlighting successful customized solutions.
1.Options for Custom PCB Assembly
Turnkey providers offer a range of customization options to cater to unique project specifications:
Design Flexibility: Custom PCB designs allow clients to specify parameters such as board size, shape, layer count, trace width, and material types to suit specialized applications.
Component Selection: Customers can choose specific components based on performance criteria, brand preferences, or cost considerations, tailoring the PCBs to their required specifications.
Prototype and Iteration Services: Providers offer rapid prototyping services that enable clients to test and refine their designs across multiple iterations before finalizing production.
Specialized Mounting and Assembly Techniques: Turnkey services can accommodate non-standard mounting techniques, such as through-hole, surface mount technology (SMT), or mixed technology assembly, providing flexibility in assembly methods.
Customization of Testing Protocols: Clients can specify custom testing and inspection protocols to ensure that the PCBs meet specialized functionality and reliability criteria.
2.Tailoring Services to Meet Specific Needs
Tailoring services in PCB assembly involves a collaborative approach between the turnkey provider and the client to ensure alignment with project goals:
Consultative Approach: Providers work closely with clients to understand their requirements, offering expert advice on design optimization, component selection, and cost-effective manufacturing methodologies.
Scalable Solutions: Turnkey providers adjust their capabilities to handle projects of varying scales, from small-scale prototype runs to high-volume production, ensuring flexibility in meeting demand.
Integration with Existing Systems: Custom PCBs are designed to integrate seamlessly with existing systems and products, ensuring compatibility and enhancing overall system performance.
Adaptable Supply Chain Management: Providers can tailor supply chain solutions to align with client-specific requirements, whether it’s sourcing niche components or managing precise delivery schedules.
3.Case Studies of Customized Solutions
Case Study 1: Medical Device PCB Customization
- Challenge: A medical device company needed customized PCB assemblies that adhered to stringent medical standards and featured compact, multi-layer designs with rare, high-quality components.
- Solution: The turnkey provider collaborated with the client’s engineering team to refine the board design for DFM and sourced specialized components through their extensive supplier network. They also implemented strict quality control measures to meet medical compliance standards.
Case Study 2: Automotive Industry Adaptation
- Challenge: An automotive manufacturer required PCBs capable of withstanding extreme temperatures and vibrations for use in electric vehicles.
- Solution: Custom PCBs were designed with robust, heat-resistant materials and reinforced connections. The turnkey provider conducted environmental stress testing to ensure reliability and longevity in harsh operating conditions.
Case Study 3: IoT Start-up Scale-Up
- Challenge: A start-up developing IoT devices needed a scalable production plan to increase output from pilot prototypes to mass production without compromising design innovation.
- Solution: The turnkey partner provided rapid prototyping for initial product iterations, followed by a tailored scaling strategy that optimized production efficiency while maintaining the flexibility for design adjustments.
These case studies illustrate the value of customization and flexibility in turnkey PCB assembly, showcasing how tailored solutions can address specific challenges and requirements across different industries.
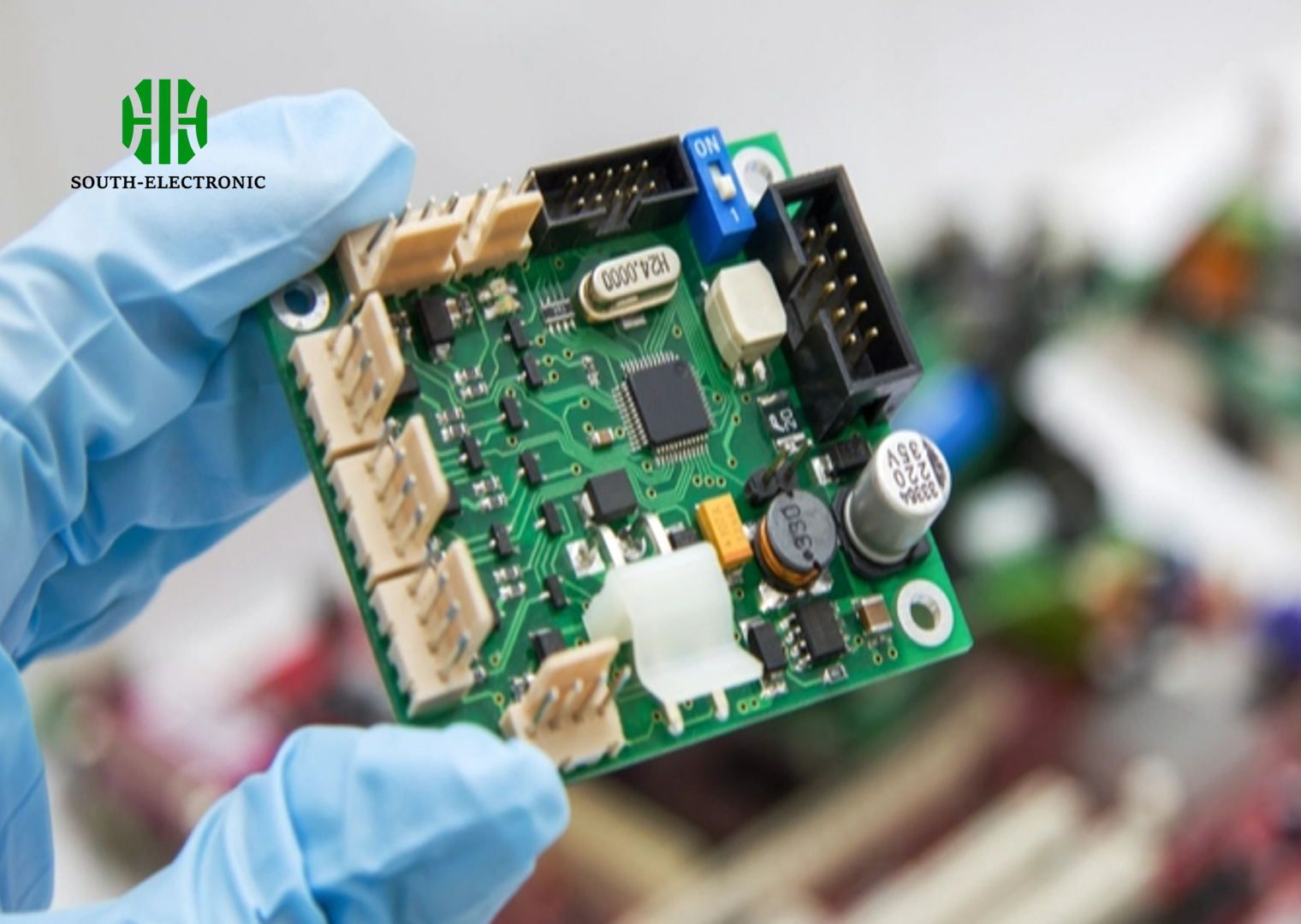
Chapter 9

Turnkey PCB Assembly for Different Industries
Turnkey PCB assembly is pivotal across multiple industries, each with its unique requirements and challenges. This section explores the applications in various sectors, the industry-specific challenges and solutions, as well as current trends and innovations.
1.Applications in Various Sectors
Turnkey PCB assembly services are utilized in numerous industries due to their comprehensive nature:
Automotive:
- Applications include engine control units, infotainment systems, advanced driver-assistance systems (ADAS), and battery management systems for electric vehicles.
- Turnkey providers support the high reliability and performance standards necessary for automotive applications.
Healthcare:
- PCBs are used in medical devices such as diagnostic equipment, wearable health monitors, and imaging systems.
- Providers ensure compliance with stringent regulatory standards, critical for patient safety and product reliability.
Consumer Electronics:
- Common in smartphones, tablets, computers, and home automation systems.
- Emphasis is on rapid production cycles and high-quality manufacturing to meet consumer demand and competitive pressures.
Aerospace and Defense:
- PCBs are integral to avionics, communication systems, and navigation equipment.
- Turnkey services ensure robust performance under extreme conditions, meeting rigorous defense specifications and standards.
Industrial and IoT:
- Used in factory automation, sensors, control systems, and smart devices.
- Providers focus on reliability and long-term operational stability in diverse environmental conditions.
2.Industry-Specific Challenges and Solutions
Each industry presents unique challenges that turnkey PCB assembly services address with targeted solutions:
Automotive Challenges:
- Challenge: Need for high durability and safety standards.
- Solution: Use of high-quality materials, rigorous testing, and compliance with automotive standards like IATF 16949.
Healthcare Challenges:
- Challenge: Strict regulatory compliance and precision.
- Solution: Adherence to standards such as ISO 13485 and FDA regulations, with thorough testing and quality assurance.
Consumer Electronics Challenges:
- Challenge: Rapid product life cycles and miniaturization.
- Solution: Advanced manufacturing techniques, efficient supply chain management, and flexible production capabilities.
Aerospace and Defense Challenges:
- Challenge: Extreme reliability and performance in harsh environments.
- Solution: Specialized materials and testing processes, compliance with MIL-SPEC standards.
Chapter 10
Future Trends and Innovations in PCB Assembly
The evolving landscape of PCB assembly is marked by emerging technologies, increased automation, and the integration of artificial intelligence (AI). These advancements are set to redefine the capabilities and efficiencies of turnkey services. This section explores these trends and offers predictions for the future of PCB assembly.
1.Emerging Technologies in PCB Assembly
New technologies are revolutionizing PCB assembly, enabling highly sophisticated electronic innovations:
Flexible and Rigid-Flex PCBs: These advanced PCBs allow for more versatile applications, particularly in wearables, medical devices, and compact consumer electronics, where space and flexibility are crucial.
3D Printing and Additive Manufacturing: 3D printing allows for rapid prototyping and the creation of complex board geometries that were previously difficult to achieve through traditional manufacturing methods.
Nano-Technology Integration: As components continue to shrink, the integration of nano-technologies promises higher performance and smaller footprints, pushing the boundaries of what’s possible in electronic miniaturization.
2.The Role of Automation and AI
Automation and AI are transforming manufacturing processes in PCB assembly:
Automated Assembly Lines: The implementation of robotic arms and conveyor systems speeds up production, reduces human error, and minimizes labor costs, leading to more consistent quality outputs.
AI-driven Testing and Inspection: AI algorithms enhance inspection processes by analyzing vast amounts of data to detect defects and optimize testing protocols, leading to higher accuracy and reliability.
Predictive Maintenance and Analytics: AI technologies are used to predict equipment failures and optimize machinery maintenance schedules, enhancing uptime and reducing operational costs.
Smart Supply Chain Management: AI facilitates more efficient supply chain operations by predicting demand fluctuations, optimizing inventory levels, and improving logistics routing.
3.Predictions for the Future of Turnkey Services
As these technologies advance, they will reshape the future of turnkey PCB assembly services:
Increased Customization and Personalization: With advanced manufacturing technologies, turnkey services will offer even greater customization, tailoring products precisely to client specifications across various industries.
Greater Integration of Eco-Friendly Practices: Future turnkey solutions will likely adopt more sustainable practices, driven by consumer demand and regulatory pressures, to minimize environmental impact.
Enhanced Collaboration and Communication Platforms: Digital platforms will facilitate real-time collaboration between clients and manufacturers, streamlining design adjustments, order processing, and production feedback loops.
Expansion of Global Access and Collaboration: The global nature of turnkey services will be further enhanced by advancements in communication technology, enabling seamless international collaborations and market expansions.
Overall, the future of turnkey PCB assembly promises exciting innovations, improved efficiencies, and enhanced adaptability to meet the growing demands of technology-driven industries.
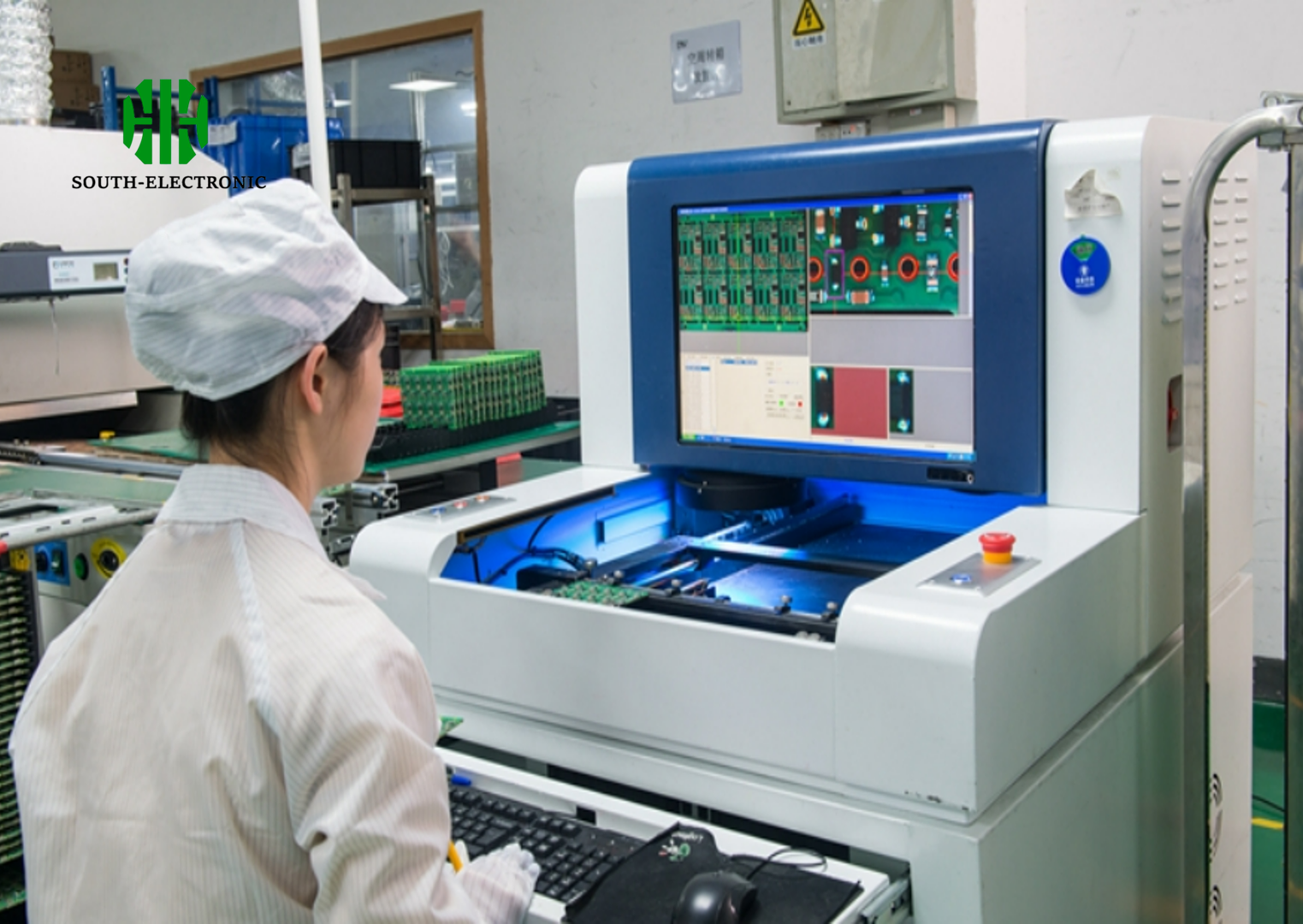
Get in touch
Where Are We?
Industrial Park, No. 438 Donghuan Road, No. 438, Shajing Donghuan Road, Bao'an District, Shenzhen, Guangdong, China
Floor 4, Zhihui Creative Building, No.2005 Xihuan Road, Shajing, Baoan District, Shenzhen, China
ROOM A1-13,FLOOR 3,YEE LIM INDUSTRIAL CENTRE 2-28 KWAI LOK STREET, KWAI CHUNG HK
service@southelectronicpcb.com
Phone : +86 400 878 3488
Send us a message
The more detailed you fill out, the faster we can move to the next step.
