How Many Types of Special PCBs Are There?
There are a bunch of different types of special PCBs, like ceramic, aluminum, copper core, IC substrate, interposer boards, and heavy copper PCBs, each designed for specific applications that need special properties like better thermal conductivity, high-frequency performance, or high current-carrying capacity.
So, you want to know about special PCBs? Well, there are actually quite a few different types out there. Let me break it down for you.
Types of Special PCBs
1. Ceramic PCBs
Ceramic PCBs are known for their excellent thermal conductivity and stability, making them ideal for high-power applications. These PCBs are made from ceramic materials like aluminum oxide (Al2O3), aluminum nitride (AlN), or beryllium oxide (BeO). The high thermal conductivity of ceramic materials ensures efficient heat dissipation, which is crucial in power electronics and LED applications.
- Applications: Power modules, high-frequency circuits, automotive electronics, LED lighting.
- Key Features:
- High thermal conductivity.
- Superior stability in harsh environments.
- High-frequency performance.
Comparison of Ceramic Materials Used in PCBs
Material | Thermal Conductivity (W/mK) | Dielectric Constant | Application Areas |
---|---|---|---|
Aluminum Oxide (Al2O3) | 24-30 | 9.5 | General-purpose electronics |
Aluminum Nitride (AlN) | 170-200 | 8.5 | High-power LEDs, RF/microwave circuits |
Beryllium Oxide (BeO) | 200-300 | 6.7 | Specialized high-performance applications |
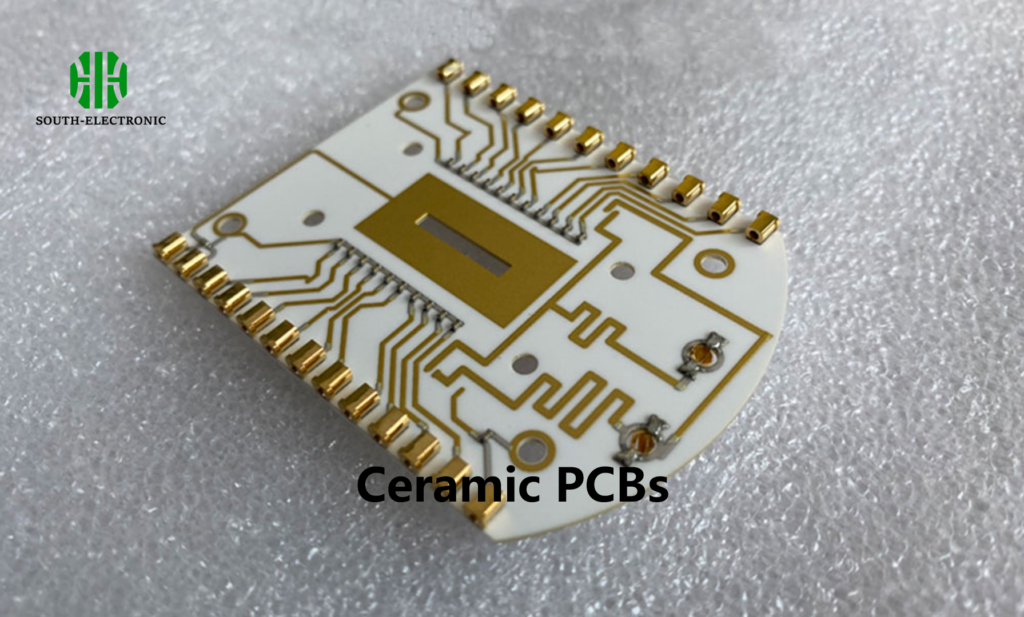
2. Aluminum PCBs
Aluminum PCBs are a subset of metal-core PCBs where the base material is aluminum. These boards are widely used in applications where heat dissipation is a primary concern, such as in LED lighting. Aluminum's excellent thermal conductivity allows the PCB to transfer heat away from critical components, preventing overheating and improving the lifespan of the product.
- Applications: LED lighting, power converters, motor controllers.
- Key Features:
- Excellent heat dissipation.
- Lightweight and durable.
- Cost-effective compared to other metal-core PCBs.
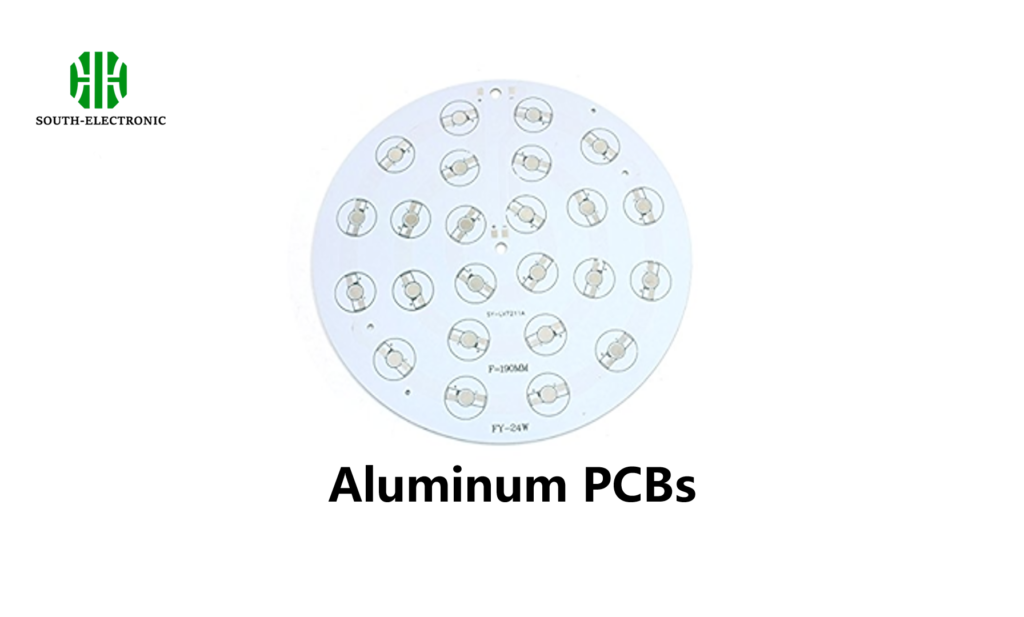
3. Copper Core PCBs
Copper core PCBs are another type of metal-core PCB, but with a copper base. Copper has even higher thermal conductivity than aluminum, making these PCBs suitable for the most demanding applications. Copper core PCBs are often used in high-frequency circuits and high-power LED systems where superior heat dissipation is required.
- Applications: High-frequency circuits, high-power LEDs, industrial power modules.
- Key Features:
- Superior heat dissipation.
- Excellent electrical conductivity.
- Robust mechanical strength.
Thermal Conductivity Comparison Between Aluminum and Copper Core PCBs
Material | Thermal Conductivity (W/mK) | Typical Applications |
---|---|---|
Aluminum | 200-240 | LED lighting, motor controllers |
Copper | 386 | High-power LEDs, RF circuits |

4. IC Substrate PCBs
Integrated Circuit (IC) substrate PCBs are specialized boards used to connect IC chips to larger circuit boards. These PCBs are designed with high precision and often include multiple layers to accommodate the complex wiring required for ICs. IC substrates are crucial in semiconductor packaging and are used in devices like smartphones, computers, and other high-tech electronics.
- Applications: Smartphones, computers, semiconductor devices.
- Key Features:
- High wiring density.
- Multi-layered structure.
- Precision manufacturing.
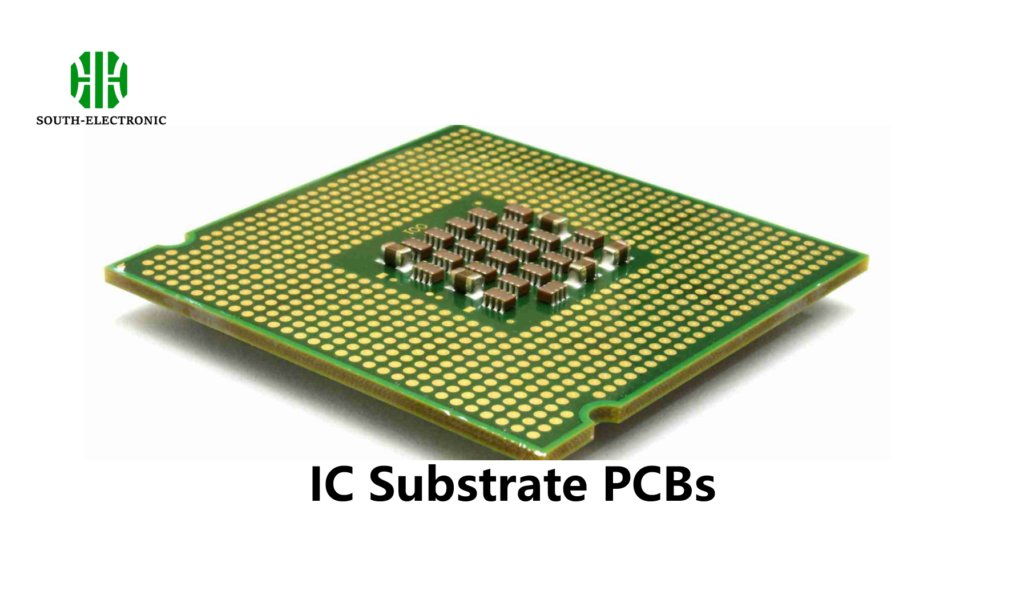
5. Interposer Boards
Interposer boards are used to connect two or more PCBs or ICs together, often in a stacked configuration. These boards are essential in high-density electronic assemblies, allowing for compact designs without compromising on functionality. Interposer boards are commonly used in advanced packaging technologies such as 2.5D and 3D ICs.
- Applications: 2.5D/3D ICs, high-density electronic assemblies, advanced packaging.
- Key Features:
- High-density interconnections.
- Enables compact designs.
- Supports advanced packaging technologies.
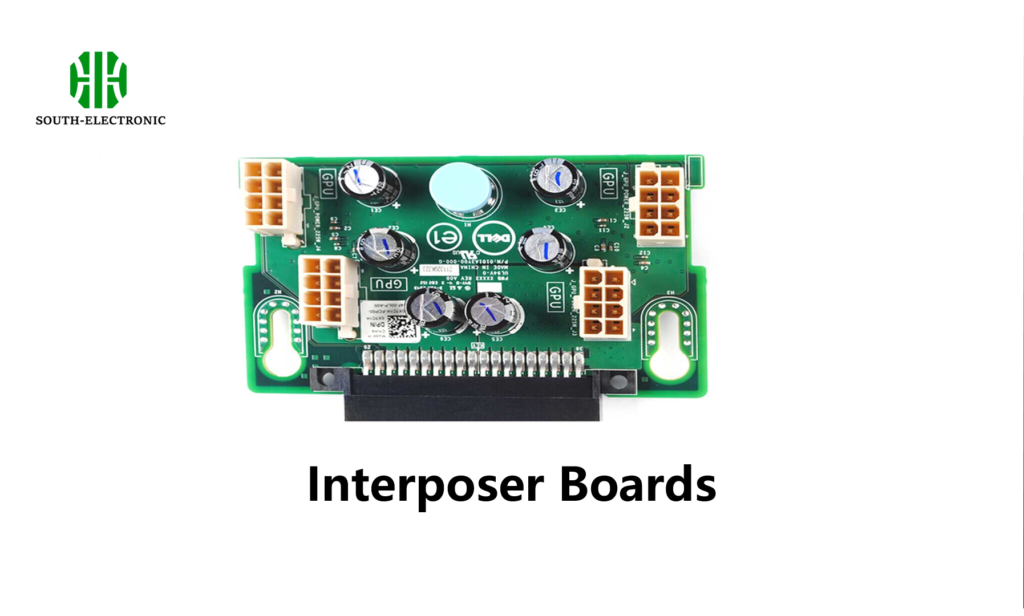
6. Heavy Copper PCBs
Heavy copper PCBs are designed with thicker copper layers, ranging from 3 ounces to over 20 ounces per square foot. These PCBs can handle higher currents and offer improved thermal management, making them ideal for power electronics and industrial applications where reliability is critical.
- Applications: Power distribution, automotive electronics, industrial controls.
- Key Features:
- High current-carrying capacity.
- Improved thermal management.
- Enhanced mechanical strength.

In conclusion, there are various types of special PCBs, each designed to meet specific requirements in different applications. From ceramic PCBs used in high-power applications to heavy copper PCBs for industrial controls, these specialized boards play a crucial role in modern electronics. Understanding the characteristics and applications of each type of special PCB helps in selecting the right one for your project, ensuring reliability and performance.