Your computer suddenly shuts down. Your phone feels unusually hot and stops charging. These everyday problems might be caused by short circuits on the circuit boards inside these devices. Short circuits occur when electrical pathways that should remain separated come into contact, causing unexpected power flow. In this article, we'll explore the common causes of these short circuits, how to spot them, and the steps you can take to prevent such frustrating malfunctions in the electronics you rely on every day.
What is PCB Short Circuit?
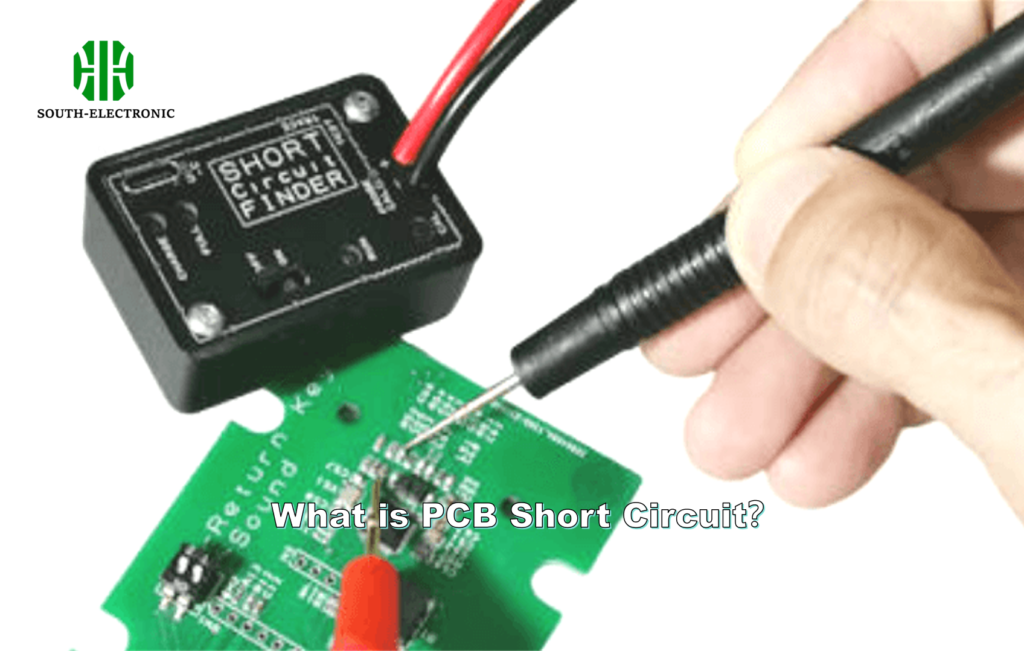
Short circuits on PCBs are a major cause of electronic device failures. A short circuit occurs when two points in a circuit that should not be connected come into contact with each other, causing a surge of current that can damage the circuit. For manufacturers, it is important to detect and address these issues early to prevent device failures, protect components, and reduce expensive repairs.
Common Causes of PCB Short Circuits
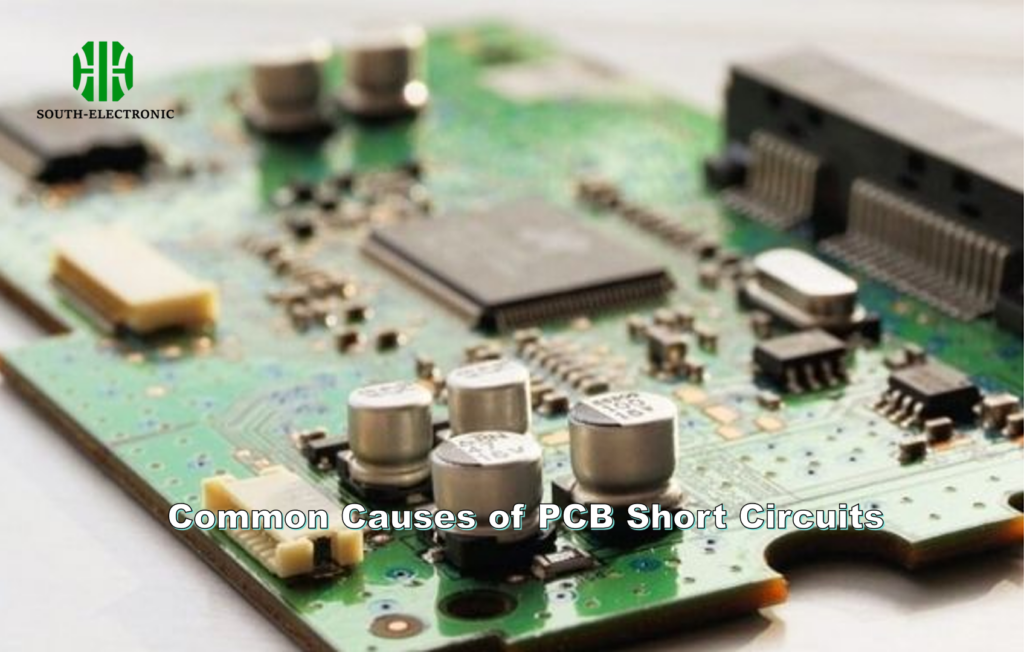
Understanding the root causes of PCB short circuits is vital to avoid them in the first place. Here are some of the most prevalent reasons:
- Contamination: Contaminants such as dust, moisture, and flux residue can cause conductive bridges betweenDust, moisture, and flux residue can cause conductive bridges between tracks, which can short out a circuit. In humid environments, moisture can accumulate on the PCB, leading to shorts over time, especially in high-voltage circuits.
- Design Flaws: Improper PCB layout is a common cause of short circuits. If you don't leave enough space between conductive traces, don't give vias enough clearance, or put components in the wrong place, you can cause shorts. High-density PCBs are especially prone to this if you don't follow design rules to the letter.
- Soldering Defects: Bad soldering practices, like using too much solder or putting components on crooked, can create solder bridges, which short out pins. Bad solder joints are especially common in manual soldering processes or reflow ovens that aren't calibrated well.
- Overheating: f a PCB gets too hot during operation or because of poor thermal management, the materials can break down. This can cause solder to melt or the PCB to delaminate, both of which increase the risk of shorts.
- Mechanical Stress: If a PCB gets bent, vibrated, or cycled through hot and cold temperatures, it can develop micro-cracks or outright breaks, which can cause shorts. This is especially common in environments where devices get moved around a lot or are exposed to high temperatures.
Advanced Detection Techniques
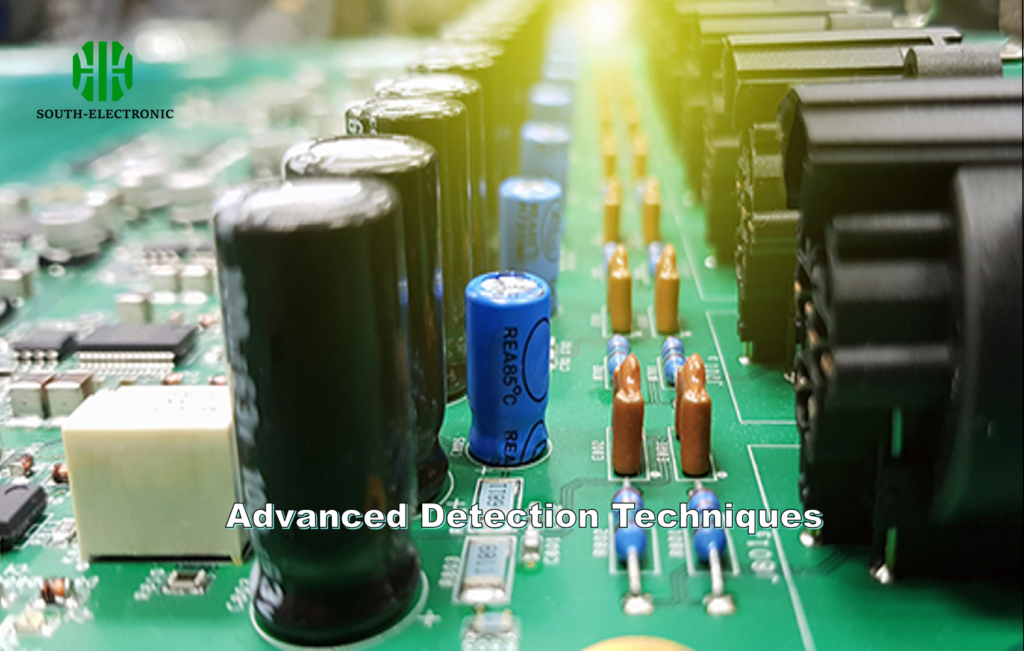
Detecting PCB short circuits early in the design or manufacturing process is crucial to ensure the long-term reliability of the device. Here are the most effective methods for detecting shorts:
- Visual Inspection: The first step is to look at the board. You can use a magnifying glass to look at the traces, components, and solder joints for obvious problems. This is a time-consuming method and may not find shorts that are hidden inside multilayer boards.
- Multimeter Testing: You can use a multimeter to check for continuity between points on the board. By measuring the resistance between two points, you can tell if there is a short. If the resistance is close to zero, there is a short. This method works well for simple boards but can be difficult for complex boards.
- Thermal Imaging: Shorts often produce heat as the current flows through a smaller path. You can use a thermal camera to scan the board and find hot spots. This will help you find the short.
- Automated Optical Inspection (AOI): AOI systems are used in manufacturing environments. They use high-resolution cameras to scan the board for problems like solder bridges, misaligned components, and trace spacing issues. AOI is good for finding surface-level shorts but may not find problems inside the board.
- In-Circuit Testing (ICT): ICT applies electrical probes to the PCB's test points, checking for shorts, opens, and component failures. This method is highly effective for mass production, allowing for quick identification of defects in both assembly and soldering.
- X-ray Inspection: For multilayer PCBs or cases where shorts occur within internal layers, X-ray inspection is the go-to method. It allows manufacturers to inspect the internal structure of the PCB and locate hidden shorts caused by manufacturing issues like via misalignments or internal trace breaks.
How to Prevent PCB Short Circuits?
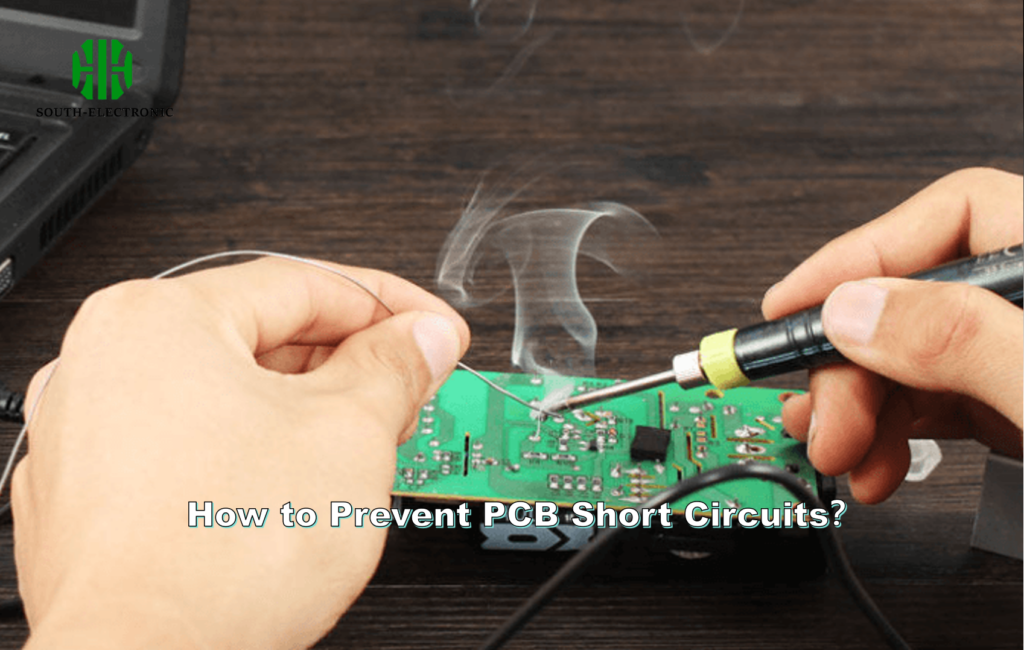
Preventing short circuits starts with a robust design and continues through careful manufacturing and testing. Here are some effective preventive measures:
- Proper Design Practices:Make sure to space out your traces and components properly during the design phase. You need to follow IPC standards for clearance and track width. If you’re designing a multilayer board, you need to think about isolation between layers to avoid internal shorts.
- Controlled Manufacturing Environments:It’s super important to keep your manufacturing environment clean during the PCB assembly process. You need to make sure that your manufacturing environment is free from dust, humidity, and other contaminants that could mess up your board. You also need to store your PCBs properly and clean your equipment regularly to keep your assembly line clean.
- Thorough Testing Procedures:You need to test your boards at multiple stages of production, including pre-soldering and post-soldering tests. You should use a combination of manual inspection and automated testing like AOI and ICT to make sure you catch any defects before you ship your boards.
- Use of High-Quality Materials:If you use cheap or wrong materials, your board could fail under thermal stress or mechanical strain. You need to choose the right substrate material and high-temperature resistant solder to make sure your board is reliable for a long time, especially if your board is going to be in extreme conditions.
- Regular Maintenance and Inspection:You need to clean and inspect your boards that are in operation on a regular basis to keep them from getting contaminated and shorting out. If you have high-performance systems, you should do periodic checks with thermal imaging or visual inspection to catch shorts before they cause a failure.
Short circuits on PCBs are a big problem in the electronics industry, but you can minimize their impact by understanding, detecting, and preventing them. By following good design practices, using advanced detection methods, and sticking to strict manufacturing standards, you can make sure your PCBs last a long time and work reliably. Regular testing and maintenance are important to avoid short circuits and prevent failures, whether you're making a few boards or a lot of them.