What is Flip Chip Assembly?
Flip chip assembly, also known as direct chip attach (DCA), involves attaching a semiconductor die face-down onto a substrate or carrier. This method eliminates the need for traditional wire bonding, offering a more compact and efficient connection. It has evolved significantly since its inception in the 1960s, becoming a preferred choice for modern electronic devices.
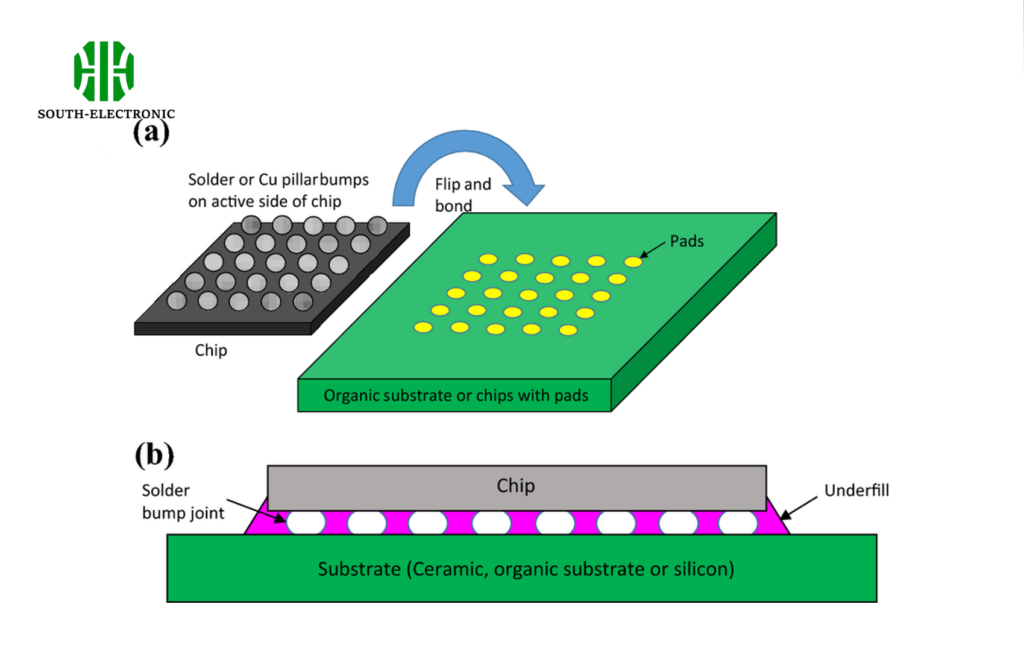
Comparison of Flip Chip Assembly and Other Methods
Feature | Flip Chip Assembly | Wire Bonding |
---|---|---|
Connection Type | Face-down | Side connection |
Space Efficiency | High | Moderate |
Signal Integrity | Excellent | Good |
Thermal Performance | Superior | Moderate |
Complexity | High | Moderate |
How Flip Chip Assembly Works?
The flip chip assembly process involves several key steps:
- Wafer Preparation:The semiconductor wafer is prepared, and individual chips are cut from it.
- Bumping Techniques:Solder bumps are applied to the pads on the chip. These bumps serve as the connection points between the chip and the substrate.
- Die Attachment:The chip is flipped over and aligned with the substrate, allowing the solder bumps to contact the corresponding pads.
- Interconnection Methods:The solder bumps are melted (typically using hot air reflow) to create a strong electrical connection. After cooling, the connection is mechanically and electrically secure.
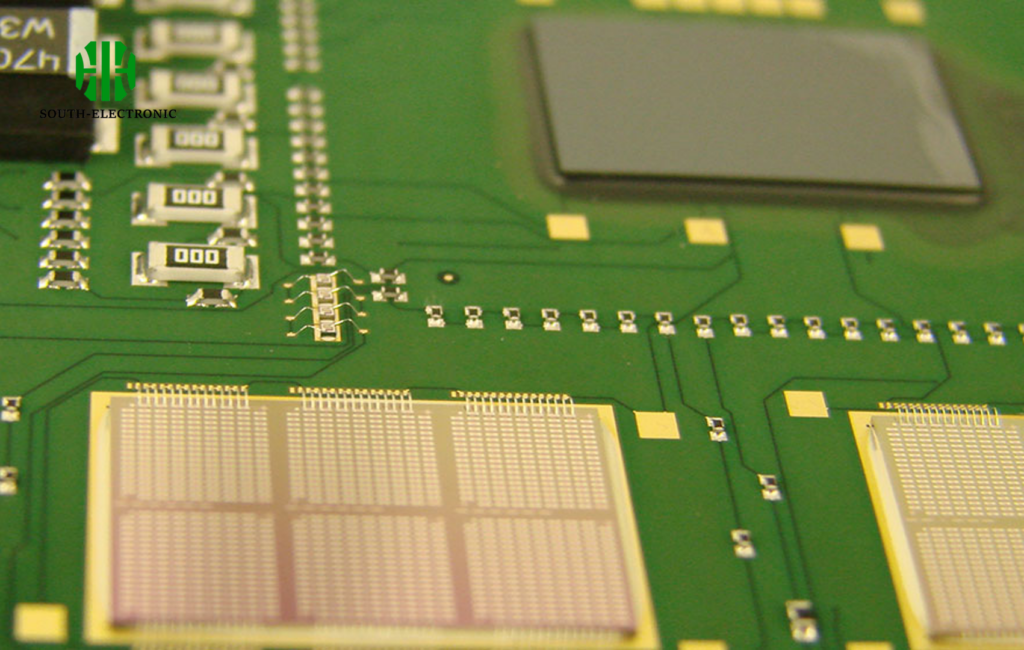
Benefits of Flip Chip Assembly
Flip chip assembly offers several advantages:
- Higher Performance: The direct connection reduces signal paths, enhancing electrical performance and reducing inductance.
- Space Efficiency: The compact nature of flip chip assembly allows for smaller device footprints, making it ideal for portable electronics.
- Better Thermal Management: Improved thermal conduction is achieved due to the face-down connection, which allows heat to dissipate more effectively.
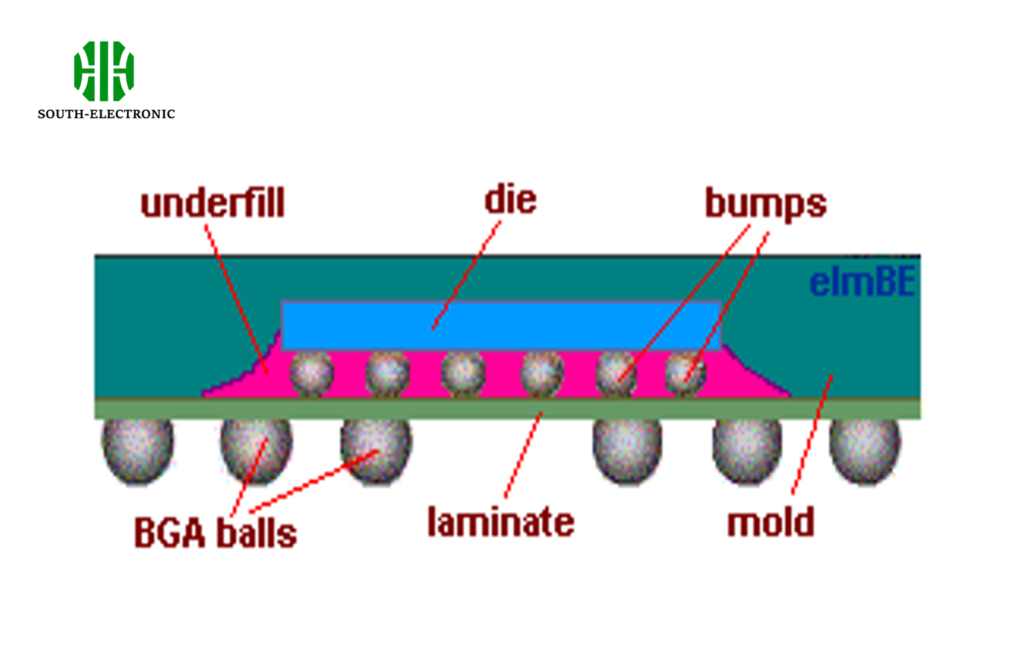
Applications of Flip Chip Assembly
Flip chip technology is widely used across various industries, including:
- Consumer Electronics: Smartphones, tablets, and laptops utilize flip chip assembly for high-performance chips.
- Automotive: Advanced driver-assistance systems (ADAS) and infotainment systems rely on flip chip technology for reliability and performance.
- Telecommunications: High-speed networking equipment benefits from the compact design and efficiency of flip chip assemblies.

Challenges in Flip Chip Assembly
Despite its advantages, flip chip assembly faces some challenges:
- Manufacturing Complexity: The process requires precision alignment and control, making it more complex than traditional methods.
- Cost Factors: Initial setup and production costs can be higher, though these may be offset by performance gains.
Future Trends in Flip Chip Assembly
The future of flip chip assembly is promising, with ongoing innovations aimed at improving performance and reducing costs. Trends include:
- Advanced Materials: Research into new materials for bumps and substrates is expected to enhance performance.
- Integration with 3D Packaging: Combining flip chip assembly with 3D packaging techniques will enable even more compact designs.
Flip chip assembly is a revolutionary technology in the semiconductor industry, offering significant advantages in performance, efficiency, and design. As technology advances, it will continue to play a vital role in the future of electronics. If you have any questions or insights, feel free to share.