What is Metal 3D Printing?
Metal 3D printing is a type of additive manufacturing that builds parts from metal powders or filaments by adding material layer by layer under computer control. There are several different processes for metal 3D printing, including Direct Metal Laser Sintering (DMLS), Selective Laser Melting (SLM), and Electron Beam Melting (EBM).
How Metal 3D Printing Works?
1. Design Stage
- 3D Modeling: Begin with a CAD model, which is then sliced digitally into layers, preparing it for printing.
2. Setup
- Prepare Equipment: Ready the printer by loading metal powder and setting up the machine parameters.
3. Printing Process
- Build Layers: A laser or electron beam selectively melts the metal powder layer by layer, forming the part based on the digital model.
4. Post-Processing
- Clean and Refine: Remove the part from the machine, eliminate supports, and perform finishing processes like sanding or heat treatment for desired properties and appearance.
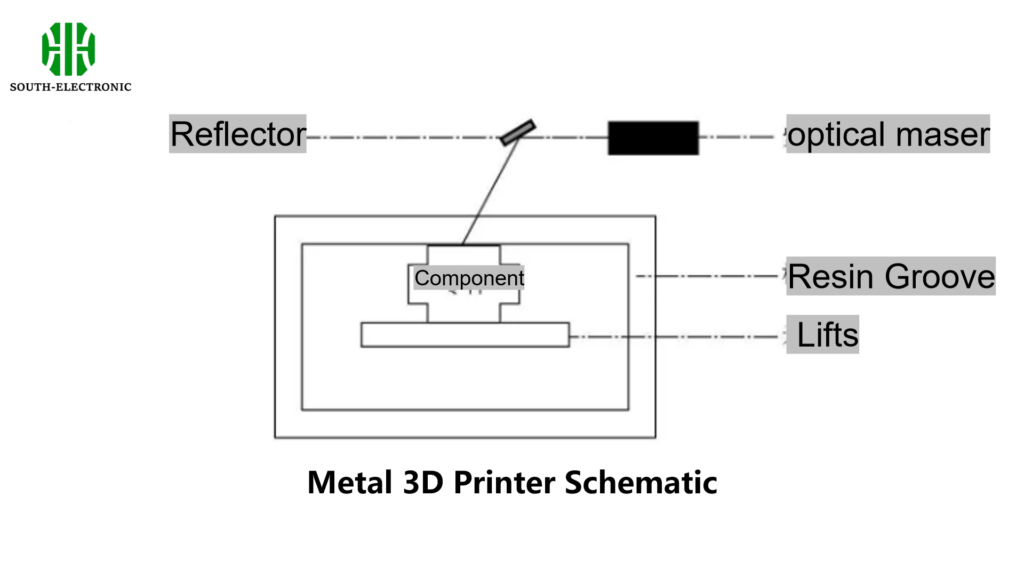
What is the Most Common Metal 3D Printing?
The most common method of metal 3D printing is Selective Laser Melting (SLM). SLM is widely used due to its ability to produce high-density, complex metal components suitable for various industries, including aerospace, automotive, and healthcare.
Another method to 3D print metal is called Direct Metal Laser Sintering (DMLS) and Electron Beam Melting (EBM). These methods can work with different metals, like stainless steel, aluminum, titanium, and nickel alloys. That makes them good choices for 3D printing metal.

What is the strongest Metal 3D Printing Material?
There are different metals and alloys for different applications in 3D printing. The most common materials are titanium, stainless steel, and aluminum. The strongest metal 3D printing material is usually considered to be titanium, specifically Titanium 6AL-4V (Ti6Al4V). It's an alloy that's used a lot because it's strong, lightweight, and doesn't corrode.
Comparison of Metal Materials in 3D Printing:
Material | Properties | Common Uses | Cost Effectiveness |
Titanium | High strength, lightweight | Aerospace, medical implants | Expensive |
Stainless Steel | Corrosion resistant, durable | Automotive, tools | Moderate |
Aluminum | Lightweight, good conductivity | Consumer goods, electronics | Relatively cheap |
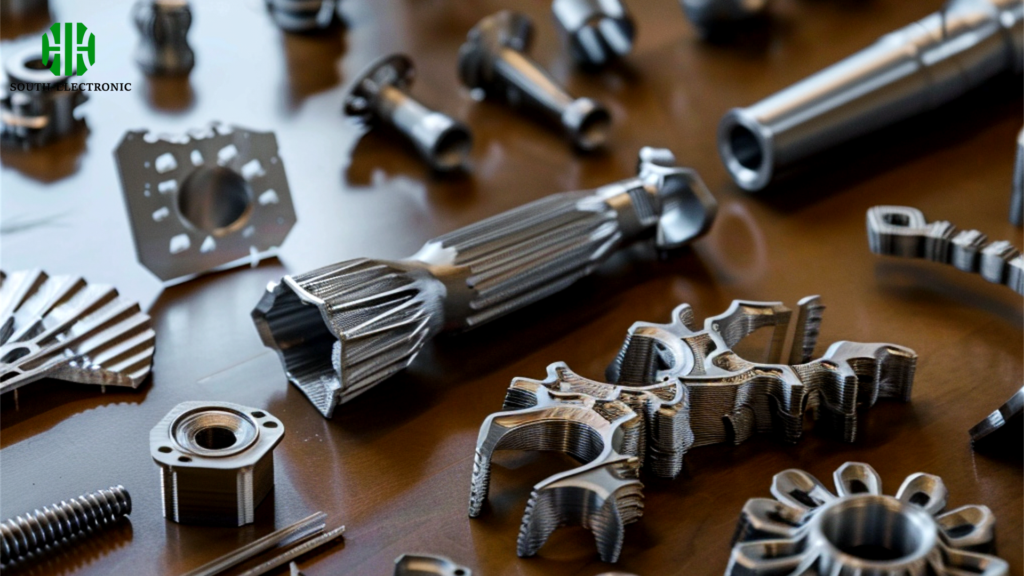
What are the Current Limitations of Metal 3D Printing Technology?
- Metal 3D Print Cost: The technology is often too expensive. This includes the high costs of the printers themselves, the metal powders used as raw materials, and the operational and maintenance expenses associated with running the equipment.
- Material Limitations: Although metal 3D printing can use a range of metals, the variety of metal 3D print materials is still narrower than those available in traditional manufacturing. Also, the properties of materials can change after printing, affecting how they perform in application-specific environments.
- Production speed: It's usually slower than traditional manufacturing methods, especially for larger or more complex parts.
- Size Limitations: The size of parts that can be produced is generally limited by the size of the metal 3D printer. While there are large-format printers available, they are much more expensive and less common, which restricts the feasible size of parts that can be produced.