What is Solder Wicking?
Solder wick is a tool that you use to remove extra solder from a joint, usually after you've done some solder wicking. It's made of braided copper. Solder wicking is when the solder moves away from where it's supposed to be during soldering, usually ending up in via holes, traces, or other places. This usually happens because the component terminal gets hot enough to melt the solder before the solder pad does, so the solder gets "wicked" or pulled away from the solder pad.
Why is Solder Wicking a Problem?
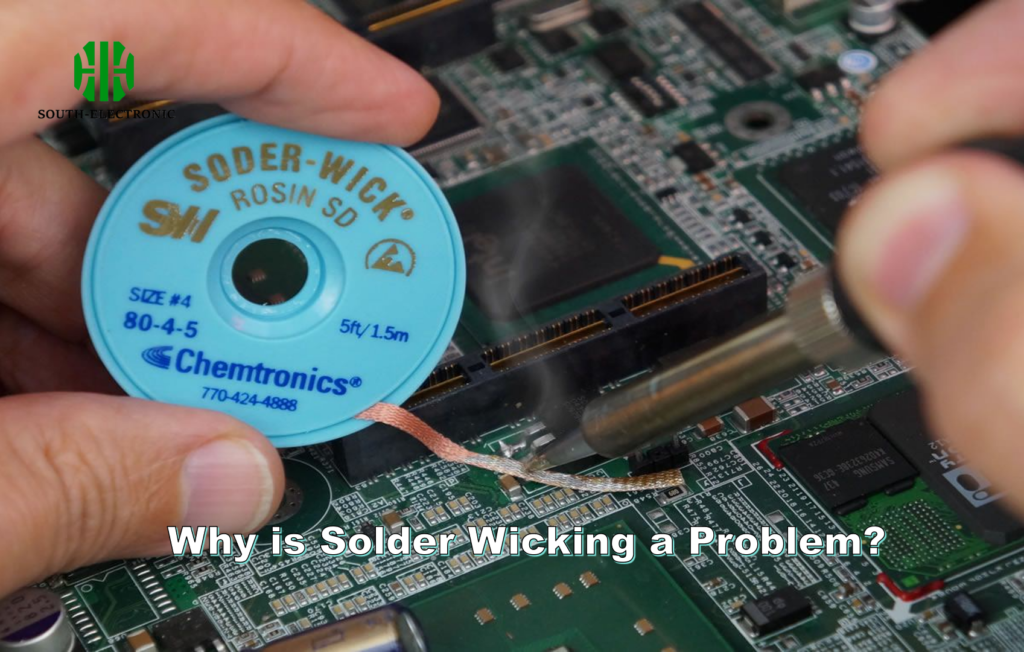
Solder wicking results in insufficient solder on the solder pad, causing weak or unreliable solder joints. This can lead to a number of problems:
- Defective components
- Unreliable electrical connections
- Potential failures in circuit functionality
Wicking also makes future repairs difficult, as components may be soldered in place with insufficient or uneven solder.
Causes of Solder Wicking:
Factor | Description |
---|---|
Uneven Heating | When the component terminal heats up faster than the pad, solder tends to move toward the hotter area. |
Improper Pad Design | Pads that are too small or improperly shaped can cause wicking. |
Excess Solder | Using too much solder can cause it to flow into unwanted areas. |
Component Leads | Some components have leads that naturally encourage solder wicking. |
How to Prevent Solder Wicking?

Preventing solder wicking is critical to achieving high-quality solder joints. Here are some key strategies:
1. Use Solder Masks
One of the most effective ways to prevent solder wicking is by using a solder mask to cover large copper areas or via holes connected to the pad. This prevents solder from wicking into those areas and ensures that it stays where it is needed.
2. Optimize Pad Design
Ensure that the solder pads are designed with the correct size and shape for the components being soldered. Poor pad design can make wicking more likely, especially if the pad is too small or lacks thermal balance.
3. Control Heating
To prevent uneven heating, use a controlled reflow process. Ensure that the soldering iron or reflow oven heats both the pad and the component lead evenly, so the solder doesn't flow away from the joint.
4. Apply the Right Amount of Solder
Using the correct amount of solder is critical. Too much solder can overflow and lead to wicking, while too little will result in weak joints.
Prevention Method | Description |
---|---|
Solder Masks | Cover large copper areas or vias connected to pads to keep solder in place. |
Proper Pad Design | Ensure correct pad sizing to balance thermal dissipation. |
Even Heating | Control heating to prevent lead or pad from reaching melting points first. |
Correct Solder Amount | Avoid excess solder to prevent overflow and wicking. |
Common Applications of Solder Wicking
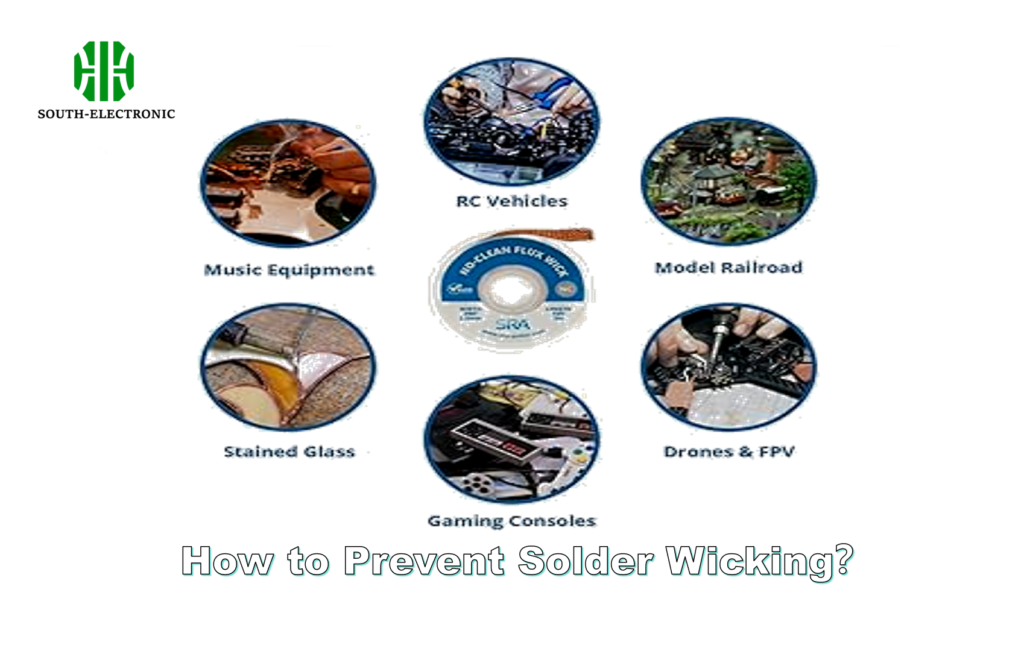
Solder wicking is most commonly encountered in the following scenarios:
- PCB Assembly: Wicking is a frequent issue in the manufacturing process when components are soldered onto PCBs.
- Rework and Repair: Solder wick is used to remove excess solder and correct wicking defects during rework.
- Component Replacement: During repairs or component upgrades, wicking can make it challenging to remove old components cleanly.
Solder wicking is a big problem in electronics assembly and repair. But you can stop it if you know how. You need to heat things right, use solder masks, and put on the right amount of solder. Then you won't have solder wicking and you'll have good solder joints. But if you do get wicking, you can use solder wick to take off the extra solder and fix things.