As modern electronics evolve, there is a growing need for efficient heat dissipation. Traditional PCBs, made with FR4 or other materials, often struggle with thermal management, especially in high-power applications. Aluminum PCBs offer a solution by integrating materials designed for superior heat conduction, making them ideal for use in LED lighting and other high-power electronics.
Structure of Aluminum Printed Circuit Boards
The structure of aluminum PCBs is composed of four main layers, each contributing to the board's overall performance, especially in terms of heat management.
1. Copper Foil Layer
The top layer is copper foil, which is thicker than in traditional FR4 boards, typically ranging from 1oz to 10oz. This layer serves as the conductive path for electrical signals and also contributes to the board's ability to carry higher current loads due to the increased thickness.
2. Dielectric Layer
Underneath the copper foil is the dielectric layer. This layer is super important for thermal management because it insulates the conductive copper from the aluminum base while also providing high thermal conductivity and low thermal resistance.
Properties of the Dielectric Layer
- Thermal Conductivity: 1W/mK to 3W/mK
- Thickness: 50 μm to 200 μm
- Electrical Insulation: High electrical insulation capacity.
Property | Value |
---|---|
Thermal Conductivity | 1W/mK to 3W/mK |
Thickness | 50 μm to 200 μm |
Electrical Insulation | High |
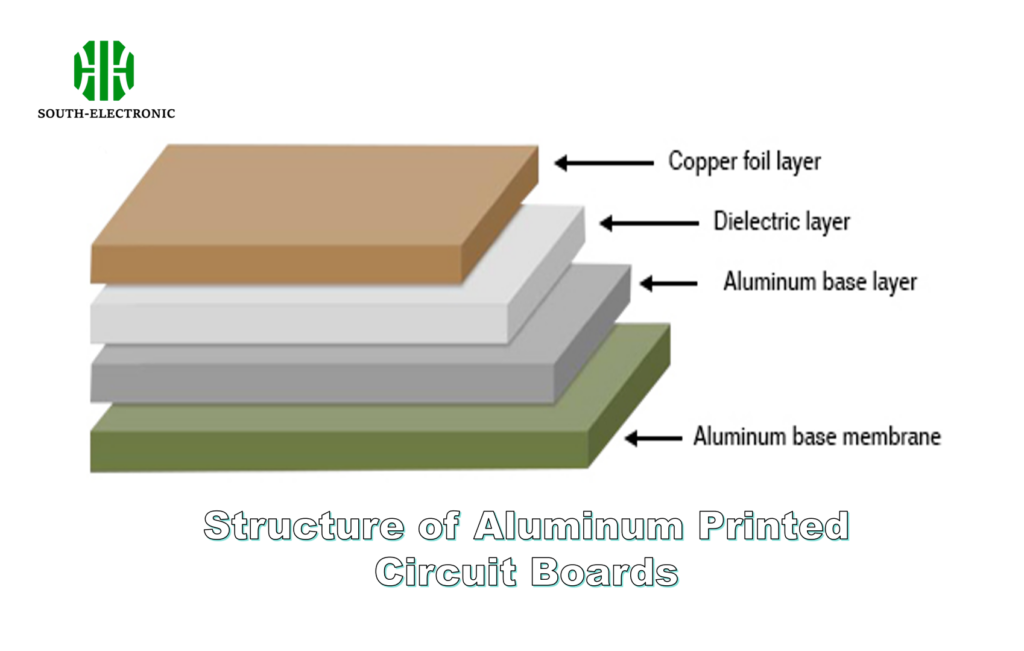
3. Aluminum Base Layer
What makes this PCB different from others is the aluminum base layer. This base provides excellent heat dissipation by transferring the heat generated by components into the aluminum core, where it can be dissipated more effectively.
Benefits of the Aluminum Base
- Heat Dissipation: Aluminum conducts heat away from components more efficiently than FR4.
- Strength and Durability: Provides a rigid foundation for the PCB, enhancing its mechanical properties.
4. Aluminum Base Membrane
The last layer is the aluminum base membrane. It protects the aluminum core from things like moisture and corrosion. This layer makes sure the PCB lasts a long time and works well even in tough conditions.
Layer | Function |
---|---|
Copper Foil | Conducts electricity; thicker for more current |
Dielectric Layer | Insulates and dissipates heat |
Aluminum Base | Provides heat dissipation and mechanical stability |
Aluminum Membrane | Protects from corrosion and environmental damage |
Comparison Between Aluminum PCBs and FR4 PCBs

One of the things that sets aluminum PCBs apart from the more traditional FR4 PCBs is their ability to handle heat and current.
Feature | Aluminum PCBs | FR4 PCBs |
---|---|---|
Thermal Conductivity | 1W/mK to 3W/mK | 0.3W/mK |
Dielectric Layer | Thicker, with better heat dissipation | Thinner, poorer heat management |
Heat Dissipation | Excellent | Moderate |
Applications | High-power devices, LEDs | General electronics |
Applications of Aluminum PCBs

- LED Lighting:Aluminum PCBs are frequently used in LED lighting systems. LEDs generate significant amounts of heat, and aluminum PCBs help dissipate this heat effectively, preventing premature failure of the LEDs.
- Power Converters:In power conversion electronics, where high voltage and current are involved, aluminum PCBs ensure efficient thermal management, increasing the longevity and reliability of the system.
- Automotive Industry:Due to their robust structure and thermal properties, aluminum PCBs are commonly used in automotive electronics, such as power modules, headlight systems, and charging systems for electric vehicles.
Aluminum PCBs are the new hotness when it comes to high-power applications where thermal management is key. They're way better than those old-school FR4 boards because they've got this four-layer structure that's all about heat dissipation, durability, and reliability. That's why all the cool kids in industries like LED lighting, power electronics, and cars are using them.