Why Do Circuit Boards Use Potting?
Potting is a process that protects a circuit board by covering it with a solid or gelatinous compound. This protective layer keeps out moisture, dust, and corrosive agents and provides shock resistance. This article looks at why potting is so popular in the electronics industry and what makes it a great way to protect sensitive components.
What is the Purpose of Potting in Electronics?
Potting in electronics involves encasing a circuit board or electronic assembly in a protective material, which is typically a resin or silicone compound. This method serves several key purposes:
- Moisture Exclusion: Potting prevents water or moisture from reaching sensitive electrical components.
- Shock and Vibration Resistance: The protective compound shields the PCB from mechanical damage caused by vibrations or impacts.
- Corrosion Prevention: Potting prevents corrosive agents like chemicals or salt from coming into contact with the circuit.
- Electrical Insulation: It acts as an insulator, reducing the risk of electrical failures or short circuits.
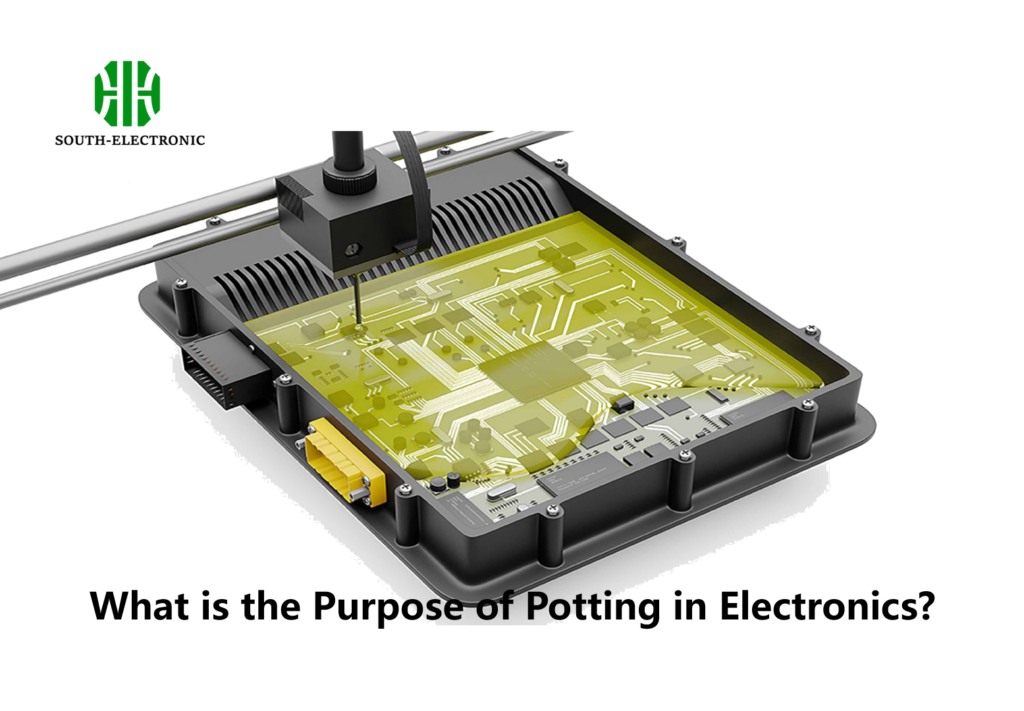
Why Choose Potting Instead of Conformal Coating?
Both potting and conformal coating are common methods used to protect PCBs, but they serve different purposes and environments.
Differences Between Potting and Conformal Coating
Feature | Potting | Conformal Coating |
---|---|---|
Level of Protection | High (shock, vibration, moisture) | Moderate (moisture, mild vibration) |
Application Areas | Harsh environments (automotive, aerospace) | Consumer electronics, less severe conditions |
Material Cost | Higher due to thicker compound | Lower due to thinner application |
Removal Difficulty | Difficult to remove without damage | Easier to remove or rework |
To sum it up, potting gives you more protection, but it’s more expensive and harder to get rid of. Conformal coating is great for less demanding environments where cost and flexibility are important. But if you need maximum protection, especially in industries like aerospace and automotive, potting is the way to go.
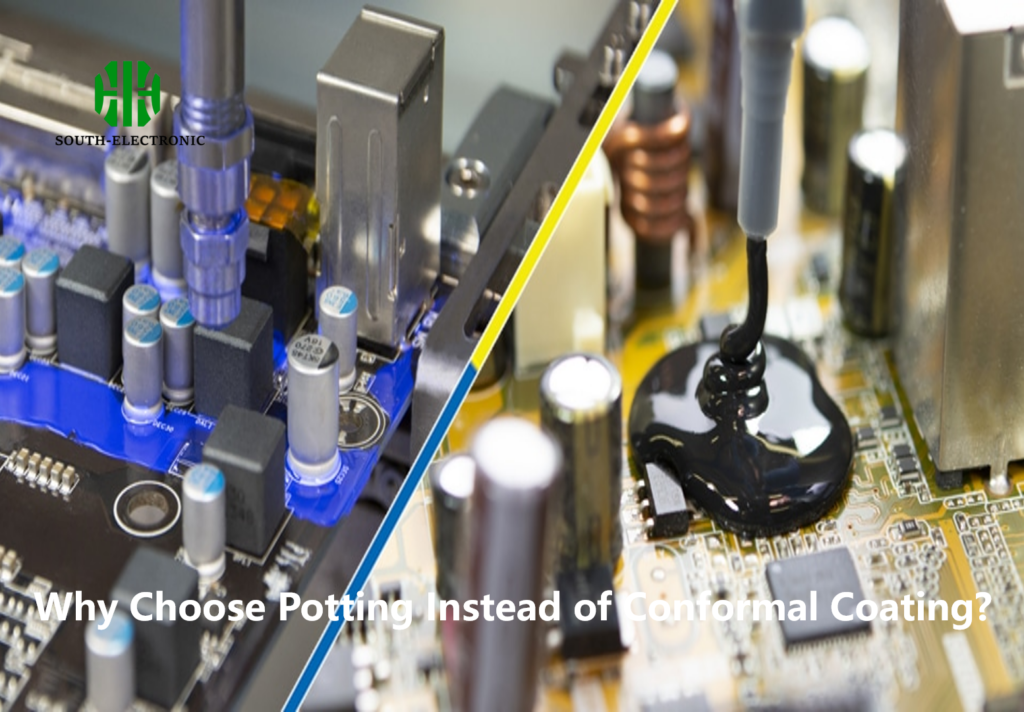
Types of Potting Compounds
There are various types of potting materials, each with different properties suited for specific applications. Here’s a look at the most commonly used potting compounds:
1. Epoxy Potting Compound
Epoxy is one of the most commonly used potting materials due to its excellent durability and adhesion. It is ideal for high-temperature applications and provides excellent electrical insulation.
- Pros: High mechanical strength, excellent adhesion to a variety of surfaces.
- Cons: Once cured, it is very difficult to remove and is prone to cracking in high-temperature fluctuations.
2. Silicone Potting Compound
Silicone compounds are flexible and resistant to both high and low temperatures, making them ideal for electronics that experience temperature variations.
- Pros: High flexibility, good thermal stability, excellent moisture resistance.
- Cons: Less mechanically strong than epoxy.
3. Polyurethane Potting Compound
Polyurethane is another widely used material, known for its flexibility and resistance to chemicals. It’s often chosen for applications where the PCB may experience a wide range of temperatures or mechanical stresses.
- Pros: Excellent chemical resistance, flexible, suitable for outdoor applications.
- Cons: Lower thermal stability compared to epoxy.
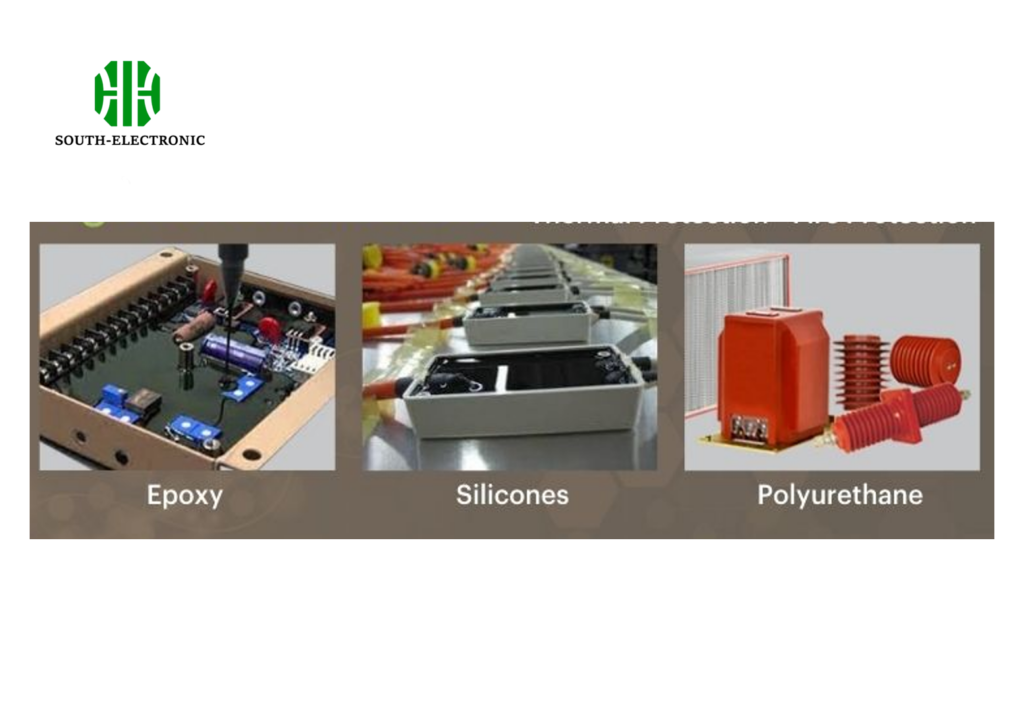
Environmental Considerations for Potting
Potting is highly effective in protecting PCBs from environmental factors like temperature fluctuations, moisture, and chemical exposure. Here are the key considerations when choosing potting for your circuit boards:
- Temperature Resistance:Certain potting compounds, like silicone, can withstand a wide range of temperatures, making them suitable for both extreme heat and cold environments.
- Moisture Protection:Potting materials offer excellent moisture resistance, preventing corrosion and electrical short circuits in wet environments.
- Chemical Resistance:Polyurethane and epoxy provide excellent protection against chemicals, making them ideal for industrial and automotive applications where exposure to oils and solvents is common.
Potting is a must for keeping sensitive electronic components safe from moisture, vibrations, shocks, and corrosive agents. Although it can be more expensive and difficult to rework, the protection and durability it provides make it the best choice for industries like automotive, aerospace, and industrial electronics.
For electronics that require maximum protection in harsh environments, potting is a superior solution compared to conformal coatings.