Why is PCB coating important for electronic devices?
PCB coating is a protective layer that gets put on printed circuit boards (PCBs) to keep them safe from stuff like moisture, dust, chemicals, and extreme temperatures. It helps electronic devices last longer and work better by stopping them from getting rusty, leaking electricity, or short-circuiting. Coatings are super important in places where stuff has to work all the time, like airplanes, medical devices, cars, and the military, because they get exposed to really bad conditions.
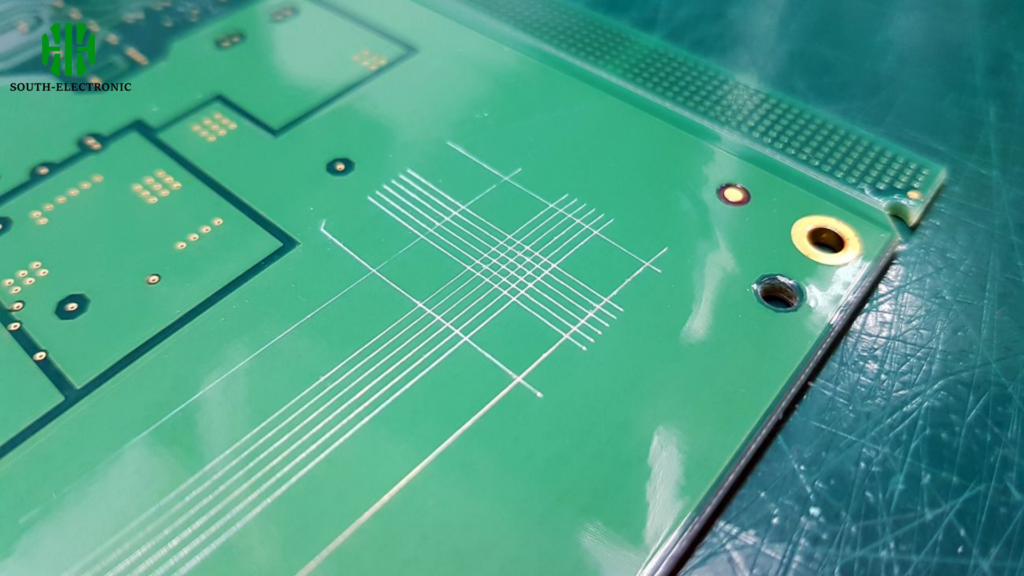
What are the industry standards and regulations for PCB coatings?
PCB coatings are super important for protecting circuit boards from things like moisture, dust, chemicals, and temperature extremes. The industry has standards and regulations to make sure coatings do their job well. Some of the main standards are:
- IPC-A-610: Acceptability of Electronic Assemblies - This standard outlines the criteria for acceptable coatings on electronic assemblies, focusing on the quality of the application.
- IPC-CC-830: Qualification and Performance of Electrical Insulating Compound for Printed Board Assemblies - This standard specifies the requirements for the quality and reliability of conformal coatings used on PCBs.
- MIL-I-46058C: This military standard is used for conformal coating materials, detailing the performance requirements and testing procedures.
- UL 746E: Standard for Polymeric Materials - Industrial Laminates, Filament Wound Tubing, Vulcanized Fiber, and Materials Used in Printed-Wiring Boards and Other Applications - It covers the safety and performance of polymeric coatings.

How can one ensure uniform coating coverage on a PCB?
Making sure you get even coverage involves techniques like spraying, dipping, or brushing. Each one has its pros and cons:
Method | Advantages | Challenges |
Spraying | Consistent coverage, fast | Requires masking |
Dipping | Thorough coverage | Handling excess coating |
Brushing | Precision application | Time-consuming, labor-intensive |
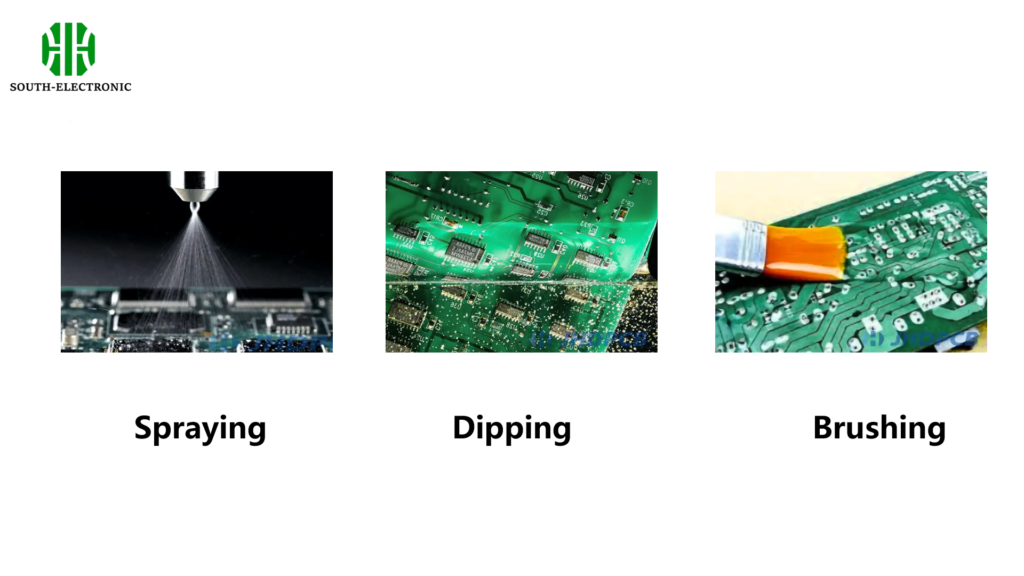
Is conformal coating necessary for PCB assembly?
You don't always need to use conformal coating on every PCB you make, but it's a good idea to use it if you're going to be putting your board in a tough environment. It helps protect your board from moisture, chemicals, dust, and extreme temperatures. It makes your board last longer and work better by stopping it from corroding, leaking electricity, or shorting out. If you're making a board for something like a plane, a medical device, a car, or the military, you usually have to use conformal coating because those things have to work right all the time. It costs more money to make a board with conformal coating, but it's worth it because your board will last longer and work better.